Metalworks PM30V2 User manual

v1.0 22052012
GB
MANUAL
Motorized presses
Please read and keep for future reference
PM30V2(757161603)
PM60V1(757161605), PM60B1(757161606), PM60B2(757161608), PM60BD2(757161609)
PM100V1(757161611), PM100B1(757161612), PM100B2(757161614),
PM100B2D(757161615), PM100B2XL(757161616), PM100B2XLD(757161617)
PM160V1(757161618), PM160B1(757161619), PM160B2(757161621),
PM160B2D(757161622), PM160B2XL(757161623), PM160B2XLD(757161624)
PM200B2(757161625)
copyrighted document - all rights reserved by FBC

v1.0 22052012 2
GB
Contents
1 Description ..............................................................................................3
1.1 General information .............................................................................................. 3
1.2 Technical data...................................................................................................... 3
1.3 Dimensions .......................................................................................................... 5
2 General safety advice..............................................................................6
2.1 User’s responsibility............................................................................................... 6
2.2 Basic safety advice ............................................................................................... 6
2.3 Special risks......................................................................................................... 7
2.4 The press must not be used when :.......................................................................... 8
3 Installation ..............................................................................................8
3.1 Transporting the press ........................................................................................... 8
3.2 Environmental conditions for the installation.............................................................. 8
4 Before first use ........................................................................................9
4.1 Mounting the oil tank............................................................................................. 9
4.2 Filling the oil tank ................................................................................................. 9
4.3 Electrical connection ........................................................................................... 10
4.4 Direction valve control......................................................................................... 10
4.5 Checks before first installation ............................................................................... 10
5 Using the press...................................................................................... 11
5.1 First use ..............................................................................................................11
5.2 Regular use.........................................................................................................11
5.3 Adjustment of the working table............................................................................ 12
5.4 Emergency stop button ........................................................................................ 12
5.5 Hand pump ....................................................................................................... 13
5.6 Moving cylinder ................................................................................................. 13
5.7 Pressure regulation valve...................................................................................... 13
5.8 Two speed pump................................................................................................ 14
5.9 Protective screen controlled by a limit switch ........................................................... 14
5.10 Working time.................................................................................................... 14
6 Maintenance.......................................................................................... 14
6.1 Daily maintenance .............................................................................................. 14
6.2 Six monthly maintenance ..................................................................................... 14
7 Circuit diagrams .................................................................................... 15
7.1 Hydraulic diagram .............................................................................................. 15
7.2 Electrical circuit................................................................................................... 17
8 EC Declaration of conformity.................................................................. 19
copyrighted document - all rights reserved by FBC

v1.0 22052012 3
GB
1 Description
1.1 General information
The Hydraulic Workshop Press is designed for:
• Beams, profiles, pivots, shaft bending and straightening,
• Bearings, bushings, the assembly and disassembly of pivots,
• Stamping, punching, forming.
This machine can be used in car repair shops, workshops etc. and is also suitable for home use. To enable
more options, the machine can be fitted with special equipment, like “V blocks” and an inner table. Proper use
of the machine is strongly recommended at all times to reduce the risk of damage.
1.2 Technical data
1.2.1 Single speed press
General specification 60 T 100 T 160 T
Pressing force [kN] 588 981 1570
Pressure max. [bar] 235 266 283
Stroke [mm] 400 400 400
Weight [kg] 685 955 1575
Electric motor 60 T 100 T 160 T
Power [kW] 3 4 6
Voltage [V] 400 / 3~ 400 / 3~ 400 / 3~
Frequency [Hz] 50 / 60 50 / 60 50 / 60
Rated speed [RPM] 3000 3000 3000
Insulation Protection [IP] 54 55 55
Insulation Class I I I
Oil type HL 46 HL 46 HL 46
Hydraulic system 60 T 100 T 160 T
Delivery flow [Lt/min] 9,6 11,4 17,7
Oil tank capacity [dm
3
] 20 20 20
System capacity [dm
3
] 8 12 17
Operating conditions 60 T 100 T 160 T
Pressing speed [mm/s] 6 4,8 5,1
Return speed [mm/s] 8,25 6,4 6,95
copyrighted document - all rights reserved by FBC

v1.0 22052012 4
GB
1.2.2 Double speed press
The given parameters of stamp travel speed are maximum values and can be 25% lower.
The given parameters of stamp travel speed regard the press operation at oil temperature above 30°C.
General specification 30 T 60 T 80 T 100 T 100 T-1200 100 T-1500 160 T 200 T
Pressing force [kN] 294 588 785 981 981 981 1570 1960
Pressure max. [bar] 166 235 250 266 266 266 283 277,5
Stroke [mm] 400 400 400 400 400 400 400 400
Weight [kg] 395 685 720 955 1100 1330 1575 2150
Electric motor 30 T 60 T 80 T 100 T 100 T 100 T W 160 T 200 T
Power [kW] 1,5 1,5 2,2 2,2 2,2 2,2 3 3
Voltage [V]
400 /
3~
400 /
3~
400 /
3~
400 /
3~ 400 / 3~ 400 / 3~ 400 /
3~
400 /
3~
Voltage
*
[V]
230 /
3~
230 /
3~
230 /
3~
230 /
3~ 230 / 3~ 230 / 3~ 230 /
3~
230 /
3~
Frequency [Hz] 50 / 60 50 / 60 50 / 60 50 / 60 50 / 60 50 / 60 50 / 60 50 / 60
Rated speed [RPM] 3000 3000 3000 3000 3000 3000 3000 3000
Insulation Protection [IP] 54 54 54 54 54 54 54 54
Insulation Class I I I I I I I I
Hydraulic system 30 T 60 T 80 T 100 T 100 T 100 T W 160 T 200 T
Delivery flow (working /
approaching)
[Lt /
min]
3,3 /
13,5
3,3 /
13,5
6,1 /
18,4
5,8 /
19,6 5,8 / 19,6 5,8 / 19,6 7,3 /
28,4
7,3 /
28,4
Oil tank capacity [dm
3
] 30 30 30 30 30 30 30 30
System capacity [dm
3
] 6,5 8 10 12 12 12 17 23
Oil type HL 46 HL 46 HL 46 HL 46 HL 46 HL 46 HL 46 HL 46
Operating conditions 30 T 60 T 80 T 100 T 100 T 100 T W 160 T 200 T
Working speed [mm/s] 2,6 2,2 3,2 2,7 2,7 2,7 2,3 1,8
Approaching speed [mm/s] 9,9 9,2 9,7 9,2 9,2 9,2 8,9 7,2
Return speed [mm/s] 12,1 12,7 13 12,3 12,3 12,3 12 9,2
copyrighted document - all rights reserved by FBC

v1.0 22052012 5
GB
1.3 Dimensions
Fig. Afmetingen
Afmetingen 30 T 60 T 80 T 100 T 100 T - 1200 100 T - 1500 160 T 200 T
A [mm] 2050 2040 2080 2110 2110 2110 2212 2500
B [mm] 1030 1150 1150 1320 1600 1900 1600 1800
C [mm] 750 900 900 900 900 900 1100 1300
D [mm] 700 750 750 920 1200 1500 1100 1200
E [mm] 250 250 250 300 300 300 350 400
F [mm] 1385 1490 1490 1660 1935 2240 1905 2100
G [mm] 150 150 150 150 150 150 150 150
H [mm] 185 191 275 174 174 174 203 194
I [mm] 900 750 600 750 750 750 750 944
J [mm] 280 300 300 360 360 360 410 460
K [mm] 175 210 230 254 254 254 324 356
Dimensions
copyrighted document - all rights reserved by FBC

v1.0 22052012 6
GB
2 General safety advice
2.1 User’s responsibility
Safe use of the hydraulic press can be achieved in daily work when all the necessary precautions are taken. It
is the responsibility of the user to ensure that:
• The machine is used as directed;
• The machine is used in perfect working condition and the safety installations are checked regularly;
• None of the safety and warning instructions are removed from the machine and these remain legible;
• All regular maintenance operations are conducted as prescribed;
• Only original spare parts are used;
• The direction valve seal is not removed.
2.2 Basic safety advice
Before starting work, inspect the machine carefully. Replace all worn or defective parts immediately. Keep all
parts in good condition and secured in place. Tighten nuts, bolts and screws to keep the equipment in safe
working condition.
When the machine is in operation, do not put your hands into the working area while the
piston rod is moving downwards or upwards. If an operator accidentally puts his hand or
any other part of the body into this danger zone, it could get smashed by the piston rod.
The operator and third parties should ensure that they never reach into dangerous parts of the machine with
their hands (or any other part of the body).
Never turn off the machine when pressing force is being applied to the workpiece; always release the force
from the object, move the piston, and then safely turn off the machine.
Do not use the machine in explosion hazard zones.
The machine cannot be used outdoors during any type of precipitation.
The operator should be equipped with personal safety gear such as: Safety goggles, body-fitting clothing.
Disconnect the machine from the power supply when not in use, before servicing and changing the oil.
copyrighted document - all rights reserved by FBC

v1.0 22052012 7
GB
Maximum pressing force can be exerted for a short time only. We recommend that you avoid using maximum
force when the piston is extended further than ¾ of its length.
Remember that the manometer is filled with glycerine and the correct force level reading takes a few seconds.
The machine cannot be used in horizontal position.
2.3 Special risks
Before starting the machine, the following checks must be performed:
• Check the machine for visible damage. Defects need to be repaired immediately. The machine may be
operated only when everything is in good working order.
• Check electrical connections regularly.
• Secure any loose connectors. Damaged electrical cables must be replaced immediately by an electrician.
• Never clean electrical equipment with water or similar liquid.
• Bare electrical cables must not be used.
• Remember: children like to imitate their parents. Do not allow children to operate the machine.
• Modifications to the machine: For safety reasons, users are not allowed to modify the machine.
• The screen does not protect the operator against impact of the worked element in the case of its cracking
or sliding out from under the piston, however it provides protection from accidental access of the operator
or unauthorized.
Never perform welding operations on the press table.
copyrighted document - all rights reserved by FBC

v1.0 22052012 8
GB
2.4 The press must not be used when :
1. The operator has not read the Operator’s Manual.
2. The work to be done is not in agreement with the recommendations in this
3. Manual.
4. The press is not complete or has been repaired with non-original parts.
5. 4. The specifications of the power supply do not conform to those stated on the motor plate.
6. The operator did not check press state, especially the state of hydraulic conduits, the supply cord, the
control panel and the emergency stop switch.
7. The direction valve seal has been removed or is damaged.
8. The power supply socket is not equipped with a protection circuit.
9. Bystanders are present in the immediate vicinity of the machine.
3 Installation
3.1 Transporting the press
This machine can be transported using a pallet truck. The use of a forklift truck is also permitted for transport,
as long as special care is taken. During transport, the working table must be placed in its lowest position, with
the oil tank mounted on the inside of the machine frame on the supporting brackets.
3.2 Environmental conditions for the installation
• Use the press only in clean, dry and dust-free rooms.
• Surrounding temperature: +5 to +50 °C.
• Humidity: max. 90%: not condensing.
• The press should be fixed to the floor with bolts.
• Ensure that the machine is placed safely.
• Ensure that electrical cables and hydraulic hoses are kept away from the working area.
copyrighted document - all rights reserved by FBC

v1.0 22052012 9
GB
4 Before first use
4.1 Mounting the oil tank
After placing the press in a suitable position, unscrew M10 bolts (a) and dismount the oil tank. Next, unscrew
the M10 bolts (b) from the two supporting brackets and move these brackets from the inner side to the outer
side of the machine frame. Refit the bolts and tighten them. Remove rubber stopper (60 T and 30 T only).
Remember to locate the brackets parallel to each other and perpendicular to the machine frame. Finally, mount
the oil tank on the brackets and tighten the four bolts (a).
Secure hydraulic hoses using two hose clamps on the upper lateral frame side.
4.2 Filling the oil tank
Remove the filler plug on the hydraulic tank cover. Pour in an appropriate volume of HL 46
or similar hydraulic oil that is unused and clean. It is important that the oil level reading
lies between the MIN and MAX marks. The filling operation must be performed when the
piston is in raised position. This corresponds to a proper position of the suction hose when
the piston is in its lowest position. Once the tank has been filled, replace the filler plug. A
drain plug is located at the bottom of the oil tank.
Take care to prevent dirt and water getting inside the oil tank.
copyrighted document - all rights reserved by FBC

v1.0 22052012 10
GB
4.3 Electrical connection
The machine must be connected to an earthed socket!
Electrical connections may be performed only by an electrician. The turning direction of the electric
motor is clockwise (looking from above). A different direction will damage the machine in a short time.
The turning direction can be set from the control panel or on the electric motor. The cable from the
panel is connected to the 400/3~ supply via a plug and socket.
The electric circuit must be protected by a fuse not greater than 16 A!
The electric connection socket must be equipped with a safety contact.
4.4 Direction valve control
When the lever is in the middle position, the hydraulic oil passes directly through the splitter and the piston
stands still. When the lever is pushed down, the piston moves downwards; pulling the lever up moves the
piston upwards (see label).
4.5 Checks before first installation
• Check electrical components for damage.
• Inspect all fixed parts.
• Check the tightness of the hydraulic fittings.
Warning! Tightening and any other maintenance can be performed only
when there is no pressure in the hydraulic circuit.
• Inspect all hydraulic connections.
• Test that the press is standing firmly.
• Test that the motor turns clockwise.
• Check the oil level.
copyrighted document - all rights reserved by FBC

v1.0 22052012 11
GB
5 Using the press
5.1 First use
Before using the press for the first time, the piston needs to be moved up and down a few times. From the mid
position, push the piston down and back up, then move it up to the maximum stroke position and back down
(avoid hitting the piston against the pilot sleeve or head cover). Repeat these movements a few times, which
will remove air from the cylinder and enable effective lubrication.
In presses equipped with a hydraulic actuator with an internal safety valve, after reaching the lower extreme
stamp position – the pressure in the hydraulic system and force on the stamp drops to a value close to zero.
5.2 Regular use
Place the workpiece on the working table so that it is directly under the piston rod. The centre of the piston
must be in alignment with the application axis. Take care when performing operations on elements that are
likely to fly off, break (especially casting elements and hardened elements) or bounce up as a result of the
applied load. In this event, a cover must be installed around the workpiece, or the operator should stand at a
safe distance.
It is not permitted to use the return stroke of the piston for performing operations on a workpiece (e.g.
stretching).
Upward movement of the piston rod can be used only for adjustment of the working
table or returning the piston rod to its start position
After correct placement of the workpiece on the working table, press the start button on the control panel
and push down the direction valve lever (see label next to the lever). If the application point does not lie on
the cylinder’s axis or the contact area is not right, move the piston upwards and adjust the location of the
workpiece.
copyrighted document - all rights reserved by FBC

v1.0 22052012 12
GB
This is important because an eccentric application point may cause damage to the piston rod and the fixing
bolts (especially when working with long strokes). When pressing is finished, pull the control lever back up,
as indicated by the arrows on the label. When the piston rod has returned to a suitable position, remove the
workpiece from the working table and turn off the machine.
5.3 Adjustment of the working table
This machine has pin holes on its frame for proper positioning of the working table. This enables the operator
to place a wide range of workpieces on the working table. The table is connected to the frame by blocking
pins.
When you need to change its position, first pass the chain through the connecting tubes and attach it to the
piston’s hooks. Then slowly move the piston rod upwards until a small gap appears between the blocking pin
and working table pin holes (at both sides of the pin). Remove the safety pins. You can then easily pull out the
blocking pins and by moving the piston rod downwards or upwards, lower or raise the working table to the
required position. After that, replace the blocking pins and safety pins, lower the table until the chain is loose
and remove it from the hooks.
5.4 Emergency stop button
The emergency stop button is located on top of the oil tank. In the event of any danger to the operator or
the machine, the user (or any other person) can shut down the power quickly and easily by pressing this red
button.
The emergency stop button is reset by turning it the direction indicated by the arrows marked on it.
Emergency stop button
copyrighted document - all rights reserved by FBC

v1.0 22052012 13
GB
5.5 Hand pump*
The machine can be purchased with a hand pump.
This device can be used for the manual application of force.
It is also very useful when a precision distance setting or force value is needed.
If you want to operate the machine using the hand pump, you must first set the
direction lever in the up or down position and then start pumping (remember to
not turn off hand pump valve).
Turn off the motor while operating the hand pump.
In mechanical presses equipped with a hand pump, after filling with oil, carry
out about 15 full work cycles using the hand pump lever.
This action is carried out in order to deaereate the hand pump.
Failure to conduct deaeration of the pump can result in uncontrolled (unsafe)
motions of the hand pump lever during the operation of the hydraulic press!!
5.6 Moving cylinder*
This machine is equipped with a moving cylinder that enables the pressing point to be adjusted left – right,
without moving the workpiece. To move this cylinder, first unscrew the four M12 fixing bolts (using hexagonal
socket wrench 10) and move it directly above the pressing point, then retighten the bolts. We recommend
that you secure the cylinder after it has been moved, using four bolts of the type mentioned, to increase the
machine’s lifespan.
5.7 Pressure regulation valve*
Some machines are purchased with additional pressure regulation valve. Using it operator can manually adjust
pressing force applied on workpiece. While turning knob right (clockwise) the pressure will be increased. To
set a proper value of pressing force, first turn off regulation valve till it loose (do not remove knob). Then apply
force on workpiece and increase pressure watching manometer reading. To reduce pressing force operator
has to move up piston from workpiece, loose the valve and start regulation from the beginning. It is important
to adjust pressing force only when speed change lever is in working (low only) position.
(* Depending on version)
copyrighted document - all rights reserved by FBC

v1.0 22052012 14
GB
5.8 Two speed pump*
Two speed presses are equipped with automatic working speed changing circuit.
Approaching and return piston rod speed is twice higher as in single speed press, but when piston rod contact
to workpiece (or any obstacle) it’s speed is automatically reduced to » 2 mm/s. At the top of oil tank cover it is
located a lever and operator can manually set working speed (low speed only).
5.9 Protective screen controlled by a limit switch*
The machine can be equipped with a screen protecting against accidental access of the operator or
unauthorized personnel. Starting the press is possible after closing the screen. Every time the screen is opened,
it causes cut-off of supply to the electric engine of the hydraulic supply.
5.10 Working time
A standard machine is not designed for constant work, that is, it can work at an intensity of no more than 2
work cycles per minute, and no longer than 10 min of constant work when the speed change lever is in the
“WORKING MOTION” position. If this limit is not observed, it can lead to overheating of the hydraulic oil and
the operator may suffer burns.
6 Maintenance
6.1 Daily maintenance
• Remove all dust and debris from the press that could disturb its operation.
• When press operations are over, remove any dust or debris found on the working table.
• At the end of operations, the press and working table should be cleaned appropriately.
• Check the oil level and temperature.
• Check winch line is in perfect condition, is not twisted and in a right place.
6.2 Six monthly maintenance
• Inspect all hydraulic fittings and tighten any loose connections.
• Every 12 months or 1000 working hours, change the hydraulic oil (used oil should be warm when it is
drained).
• Check the screws connecting the cylinder assembly to the machine frame and tighten them, if necessary.
• In the event of oil leakage in the fittings, detach the fitting and replace the seal. If this does not solve the
problem, replace the whole fitting.
• Check the motor fixing bolts and tighten, if necessary.
(* Dependign on version)
copyrighted document - all rights reserved by FBC

v1.0 22052012 15
GB
7 Circuit diagrams
7.1 Hydraulic diagram
7.1.1 Single speed press
(* Not present in motor-only version)
M
1
2
3
4
5
6
7
8
9
No. Description QTY
1 Hydraulic cylinder 1
2 Manometer 1
3 Oil tank 1
4 Motor 1
5 Oil pump 1
6 Pressure regulator 1
7 Direction valve 1
8 Non-return valve* 1
9 Hand pump* 1
copyrighted document - all rights reserved by FBC

v1.0 22052012 16
GB
7.1.2 Double speed press
(* Not present in motor-only version)
M
1
2
3
4
56
8
7
99
10
11
7
12
13
No. Description QTY
1 Hydraulic cylinder 1
2 Manometer 1
3 Oil tank 1
4 Motor 1
5 Oil pump 1 1
6 Oil pump 2 1
7 Pressure regulator 1
8 Direction valve 1
9 Non-return valve 1
10 Hand pump 1
11 Cut-off valve 1
12 Overflow valve 1
13 Throttle valve (custom)
∗
1
copyrighted document - all rights reserved by FBC

v1.0 22052012 17
GB
7.2 Electrical circuit
Legend:
Q1 – Starter
S1 – Emergency stop button
copyrighted document - all rights reserved by FBC

v1.0 22052012 18
GB
Electric circuit with safety screen controlled by a limit switch*.
(*Depending on version)
copyrighted document - all rights reserved by FBC

v1.0 22052012 19
GB
8 EC Declaration of conformity
The Manufacturer/Retailer Metalworks (Europe) Limited
Unit 5
Flitwick Industrial Estate
Commerce Way
Flitwick - Bedfordshire
MK45 1UF Great Britain
Hereby declares that the following products:
Products:
Motorized presses
Order nr:
Relevant EU directives: 2006/42/EG (Machine directive)
2006/95/EG (Low voltage directive)
Meet the provisions of the aforementioned directives, including, any amendments valid at the time of this
statement.
B. VYNCKIER
VYNCKIER TOOLS SA
PM30V2(757161603)
PM60V1(757161605)
PM60B1(757161606)
PM60B2(757161608)
PM60BD2(757161609)
PM100V1(757161611)
PM100B1(757161612)
PM100B2(757161614)
PM100B2D(757161615)
PM100B2XL(757161616)
PM100B2XLD(757161617)
PM160V1(757161618)
PM160B1(757161619)
PM160B2(757161621)
PM160B2D(757161622)
PM160B2XL(757161623)
PM160B2XLD(757161624)
PM200B2(757161625)
copyrighted document - all rights reserved by FBC
This manual suits for next models
35
Table of contents
Other Metalworks Power Tools manuals
Popular Power Tools manuals by other brands

Kobalt
Kobalt KMT 224B-03 manual
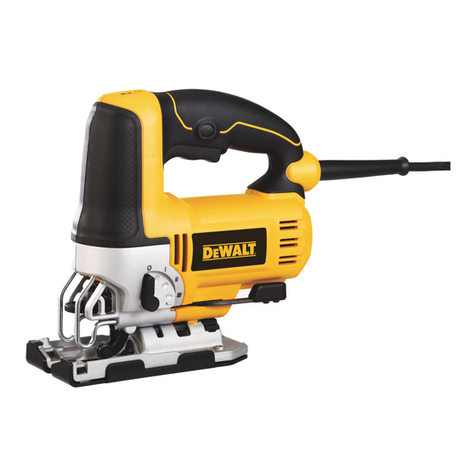
DeWalt
DeWalt DW300 instruction manual

Nation Flooring Equipment
Nation Flooring Equipment 6280 series quick start guide

Black & Decker
Black & Decker 90537965 instruction manual

Matatakitoyo Torque Tools
Matatakitoyo Torque Tools META Operation manual

Weston
Weston 07-0801 instructions