Metso LCP9H Series Operating and maintenance manual

Local Control Panels for VG9000H
LCP9H Series
Installation, Maintenance and
Operating Instructions
7 LCP9H 70 en • 9/2011

27 LCP9H 70 en
READ THESE INSTRUCTIONS FIRST!
These instructions provide information about safe handling and operation of the device.
If you require additional assistance, please contact the manufacturer or manufacturer's representative.
Addresses and phone numbers are printed on the back cover.
SAVE THESE INSTRUCTIONS!
Subject to change without notice.
All trademarks are property of their respective owners.
Table of Contents
1 LCP9H Local Control Panels for VG9000H .. 3
1.1 General .................................................. 3
1.2 Technical description............................. 3
1.3 System architecture ............................... 3
1.4 Markings ................................................ 4
1.5 Technical specifications ........................ 4
1.6 Recycling and disposal ......................... 5
1.7 Safety precautions ................................. 5
2 TRANSPORTATION, RECEPTION AND
STORAGE........................................................ 5
3 MOUNTING...................................................... 5
3.1 Buttons ................................................... 5
3.2 Electrical connections............................ 6
4 LCP9H LAYOUT AND FUNCTIONALITY ....... 6
4.1 Functionality ........................................... 7
5 MAINTENANCE............................................... 8
5.1 LED test.................................................. 8
6 TROUBLE SHOOTING 8...................................
7 TOOLS ............................................................. 8
8 TYPE CODING................................................. 8
9 SPARE PARTS................................................ 8
10 DIMENSIONS................................................... 9
11 EC DECLARATION OF CONFORMITY ........ 11

7 LCP9H 70 en 3
1 LCP9H Local Control Panels for
VG9000H
1.1 General
The Local Control Panels LCP9H-series are designed to
be used together with the VG9000H safety valve con-
troller. Later on in this manual LCP9H name is used
when all versions (LCP9H, LCP9HW, LCP9HE and
LCP9HEW) are in question.
Different versions of LCP9H are following:
LCP9H
❑Standard version of Local Control Panel LCP9H
with ATEX and IECEx Ex ia / nL / ic approvals
❑Full functionality
LCP9HE
❑Explosion proof version of LCP9H with ATEX and
Ex d and tb approvals
❑Full functionality
LCP9HW
❑Same approvals than LCP9H
❑Close(/open) functionality is removed
LCP9HEW
❑Same approvals than LCP9HE
❑Close(/open) functionality is removed
This manual only describes the Local Control Panel
LCP9H wiring, configurations and functions. See the
VG9000H manual (7VG92H70en) for detailed informa-
tion, functionality and wiring connections and options
for the VG9000H.
1.2 Technical description
LCP9H and LCP9HE permit the emergency isolation
valve to be closed (or opened) locally (close/open func-
tionality, see 4.1.1 for details). This functionality is
removed from LCP9HW and LCP9HEW. LCP9H permits
the valve to be returned to the normal operating posi-
tion when the trip initiators are normal (manual reset
functionality, see 4.1.2 for details). There is also the
option for functional testing (PST) of the emergency iso-
lation valve (test functionality, see 4.1.3 for details).
LCP9H-series devices also have indicators (LEDs) for
the valve position (open/close), ready to reset, testing
and alarm status (see 4.1.4-7 for LED details).
All the buttons are lockable with e.g. padlock (max.
shackle dia. 5 mm).
1.3 System architecture
The Local Control Panel LCP9H is connected to the
VG9000H with a dual pair twisted cable. Communica-
tion between the devices is handled by a current loop.
The LCP9H also needs a 24 V DC power supply. Refer
to the general wiring of the LCP9H in Fig. 1. See
detailed wiring information in Section 3.2.
If the LCP9H is used in intrinsically safe installations, an
isolator will be needed for the 24 V DC power supply,
see 1.5 for compatible isolators.
Fig. 1 General wiring of LCP9H / VG9000H
Air supply
1. ValvGuard VG9000H
2. Pneumatic actuator
3. Local Control Panel LCP9H
AO (mA)
from safety system (or from RCI9H)
24 V DC supply
(via isolator if required)
Serial
communication

47 LCP9H 70 en
1.4 Markings
The Local Control Panel is equipped with an identifica-
tion plate (Fig. 2 or 3).
1.5 Technical specifications
VG9000H compatibility
Compatible with VG9_H_L2_ versions.
See the VG9000H type coding for further details of
different VG9000H versions.
Temperature range
LCP 9H,
LCP9HW -20° to +65 °C
LCP 9HE ,
LCP9HEW -20° to +55 °C
Electronics
Electrical connection:
max. 2.5 mm2
LCP 9H
LCP9HW 2 pcs. conduit entry, dia. 21 mm, cable glands
for cable with with ext. dia. 8-12 mm included
LCP 9HE
LCP9HEW 2 pcs. conduit entry, M20x1.5
Power consumption:
400 mW
Power supply:11–24 V DC, 50 mA
Output is short circuit protected
Maximum distance for power supply:
1200 m
Ex ia IIC T4/T5/T6 Gb
Input values for the power supply:
Ui ≤25.2 V
Ii ≤150 mA
Pi ≤650 mW
Ci ≤30 nF
Li ≤252 µH
Output values for the communication interface:
Uo ≤9.8 V
Io ≤47 mA
Po ≤120 mW
Co ≤3.3 µF
Lo ≤15 mH
Ex ic IIC T4/T5/T6, Ex nL IIC T4/T5/T6 Gc
Input values for the power supply:
Ui ≤25.2 V
Ii ≤150 mA
Pi ≤650 mW
Ci ≤25 nF
Li ≤201 µH
Output values for the communication interface:
Uo ≤8.8 V
Io ≤42 mA
Po ≤93 mW
Co ≤45 µF
Lo ≤45 mH
Ex d IIB+H2 T6 Gb
Ex tb IIIC T85°C Db IP65
Input values for the power supply:
Ui ≤25.2 V DC
Ii ≤50 mA
Pi ≤1.26 W
Output values for the communication interface:
Uo ≤8.8 V DC
Io ≤42 mA
Po ≤0.37 W
ATEX and IECEx approvals are valid under these conditions.
Compatible isolators for power supply
MTL 5021
P&F KFD0-SD2-Ex1.1045
STAHL 9176/.0-14-0
ABB V17132-520
Communication cable
The communication cable between LCP9H and
VG9000H must be a shielded, twisted pair, 4-wire
cable. The shield must be connected to housings in
both ends. The maximum distance between VG9000H
and LCP9H is 60 m.
Cable requirements:
Signals and corresponding ground wires twisted
Wire thickness min. 0.8 mm
Shield coverage > 85 %
Test voltage > 1500 V (Ex requirement)
Resistance < 50 Ω/km
Capacitance < 50 pF/m
Fig. 2 Example of identification plate,
LCP9H and LCP9HW
Fig. 3 Example of identification plate,
LCP9HE and LCP9HEW
Metso Automation Oy, Vanha Porvoontie 229, 01380 Vantaa Finland
II 2GD
LOCAL CONTROL PANEL
Type LCP9HE Rev 1.0
0575
SIRA 11 ATEX 1170
IECEx SIR 11.0078
Ex d IIB+H2 T6 Gb
Ex tb IIIC T85°C Db IP65
Ta -20 - +55°C
Supply: 11-24 VDC, 50 mA, Ui = 25 VDC
Cable entry -M20

7 LCP9H 70 en 5
Material and weight
LCP 9H,
LCP9HW 316L stainless steel, 2.8 kg
LCP 9HE ,
LCP9HEW Copper-free aluminium alloy with
epoxy coating, 14.6 kg
Dimensions
LCP9H and LCP9HW
Without buttons and cable glands:
250 mm x 200 mm x 114 mm (h x w x d)
With buttons and cable glands (approx.):
270 mm x 200 mm x 137 mm (h x w x d)
LCP9HE and LCP9HEW
Without buttons:
364 mm x 317 mm x 220 mm (h x w x d)
With buttons:
364 mm x 317 mm x 252 mm (h x w x d)
APPROVALS
Intrinsically safe and non incendive
IECEx Ex ia IIC T4/T5/T6 Gb
Ex ic IIC T4/T5/T6 Gc
IEC 60079-0: 2004, 2007
IEC 60079-11: 2006
Ex nL IIC T4/T5/T6 Gc
IEC 60079-0: 2004, 2007
IEC 60079-15: 2005
ATEX II 2G Ex ia IIC T4/T5/T6 Gb
II 3G Ex ic IIC T4/T5/T6 Gc
EN 60079-0: 2009, EN 60079-11: 2007
II 3G Ex nL IIC T4/T5/T6 Gc
EN 60079-0: 2009, EN 60079-15: 2005
Flameproof and explosion proof
IECEx Ex d IIB+H2 T6 Gb
Ex tb IIIC T85°C Db IP66
IEC 60079-0: 2007, IEC 60079-1: 2007,
IEC 60079-31: 2008
ATEX Ex d IIB+H2 T6 Gb
Ex tb IIIC T85°C Db IP65
EN 60079-0: 2007, EN 60079-1: 2007,
EN 60079-31: 2008
Electromagnetic protection
Electromagnetic compatibility
Emission acc. to EN 61000-6-4: 2007
Immunity acc. to EN 61000-6-2: 2005
1.6 Recycling and disposal
Most local control panel parts can be recycled if sorted
according to material. Most parts have material mark-
ing. In addition, separate recycling and disposal
instructions are available from the manufacturer.
The Local Control Panel may also be returned to the
manufacturer for recycling and disposal. There will be a
charge for this.
1.7 Safety precautions
2 TRANSPORTATION, RECEPTION
AND STORAGE
The Local Control Panel is a sophisticated instrument,
handle it with care.
❑Check the Local Control Panel for any damage
that may have occurred during transportation.
❑Store the Local Control Panel preferably indoors
and keep it away from rain and dust.
3 MOUNTING
3.1 Buttons
The open / close button face is user selectable (open/
close). Both face plates are included in the delivery.
This applies to LCP9H only.
CAUTION:
Do not exceed the permitted values!
Exceeding the permitted values may cause dam-
age to the local control panel and to equipment
attached to the panel.
Damage to the equipment and personal injury may
result.
CAUTION:
During maintenance or commissioning when the
device cover is open, ensure that water does not
go inside the enclosure.
CAUTION:
Do not operate the device with the cover open or
removed!
Electromagnetic immunity is reduced.
Ex d WARNING:
Do not open the cover when an explosive atmos-
phere may be present!
Ex d and Ex tb WARNING:
Use a cable gland with suitable Ex d IIC and Ex tb IIIC
certification. Use cable gland suitable for at least
-20 °C to 70 °C.
Ex d NOTE:
Only persons familiar with Ex d explosion protection
are allowed to work with the device. Special attention
has to be paid to careful handling and closing of the
cover.
NOTE:
Avoid earthing a welding machine in close proximity
to the LCP9H.
Damage to the equipment may result.
NOTE:
The enclosure of the LCP9H meets the IP66 protection
class according to EN 60529 in any position when the
cable entries are plugged according to IP66.
Based on good mounting practice, the recommended
mounting position is with electrical connections placed
downwards. If these requirements are not met, and the
cable glands are leaking and the leakage is damaging
the LCP9H electronics, our warranty is not valid.

67 LCP9H 70 en
3.2 Electrical connections
There are two terminal blocks located in the circuit
board inside the LCP9H (see Fig. 4). LOOP terminals
are for connection to the VG9000H and PWR terminals
are for the 24 V DC power supply.
See the VG9000H manual 7VG9H70EN for detailed
electrical connections in the VG9000H.
4 LCP9H LAYOUT AND
FUNCTIONALITY
The LCP9H front panel layouts with push buttons and
LEDs can be seen in Fig. 5–8.
The push buttons (described in the Section 4.1) are as
follows:
❑Reset
❑Tes t
❑Close / Open
The LEDs (described in the Section 4.1) are as follows:
❑Ready-To-Reset (amber)
❑Tes t ( a m ber)
❑Open (green)
❑Closed (red)
❑Alarm (red)
Fig. 4 LCP9H electrical connections
NOTE:
When installing the LCP9H, standard IEC 60079-14/
12.2.4 should be considered. The circuits of the appa-
ratus are assumed to be earthed.
Fig. 5 LCP9H front panel
VG9000HLCP9H
LOOP_CHGND
LOOP_B-
LOOP_B+
LOOP_A-
LOOP_A+
PWR_IN_CHGND
PWR_IN-
PWR_IN+
24 V DC
supply
ground
ground
Fig. 6 LCP9HW front panel
Fig. 7 LCP9HE front panel
Fig. 8 LCP9HEW front panel

7 LCP9H 70 en 7
4.1 Functionality
The functionality of the LCP9H push buttons and pur-
pose of the LEDs are described below in 4.1.1-7.
Functionality of the LCP9H is lost in the following cases:
❑If the 24 V DC supply power is disconnected
❑If there is no communication between the LCP9H
and the VG9000H, e.g. the cable is broken or
disconnected
❑If the polarity of wires is incorrect
❑If the Loop A (7, 8) and Loop B (9, 10) wires are
mixed in the VG9000H
These above-mentioned cases do not affect the valve
position. Alarm LED is blinking in those cases.
The buttons need to be pushed (0.2–10 seconds) and
released to perform the desired function.
4.1.1 Close / Open button
❑This functionality is only available in LCP9H.
LCP9HW and LCP9HEW do not have the valve
close/open functionality.
❑The purpose of the Close / Open button is to
manually close or open the valve depending on
the assembly and configuration of the valve. It
means that this will drive the valve to safety posi-
tion.
❑The button face is user selectable (open/close).
This applies to LCP9H only and there are two
faceplates in the delivery of the LCP9H box.
4.1.2 Reset button
❑The purpose of the Reset push button is to return
the valve to the normal operating position after
the emergency trip.
❑The Reset button is operational only when the
mA signal from the safety system (or RCI9H) to
VG9000H is in the normal state, i.e. above
16.0 mA.
❑The Ready-to-Reset LED is lit when mA signal
from the safety system (or RCI9H) to VG9000H is
above 16.0 mA, i.e. in the normal state. The
Reset button is then operational.
❑Push and release the Reset button to return the
valve to the normal operating position.
4.1.3 Test button
❑The purpose of the Test button is to start the par-
tial stroke test (PST) manually or to cancel the
manual partial stroke test of the emergency isola-
tion valve.
❑The stroke size of the test can be set via HART
(DTM, EDD) or from the LUI (Local User Inter-
face) of the VG9000H. See VG9000H manual
7VG970en for details.
❑The manual test via LCP9H uses the same stroke
size than manual PST programmed into
VG9000H itself.
❑To start the PST test, press and release the Test
button and the Test LED will be illuminated.
❑To stop the ongoing manual PST test, press and
release the Test button and the manual PST test
will be cancelled. The valve will return to its nor-
mal operating position.
❑It is also possible to cancel the manual PST test
with this Test button even if the test is started via
HART or LUI.
4.1.4 Ready-To-Reset LED
❑The Ready-To-Reset LED is turned on when mA
signal from the safety system (or RCI9H) to the
VG9000H is in the normal state (above 16.0 mA)
and the Reset button has not yet been pushed. It
indicates that the Reset button can be used.
4.1.5 Open and Closed LEDs
❑Open and Closed LEDs indicate the valve posi-
tion and whether the emergency isolation valve is
open or closed.
❑If the valve is in the intermediate state both LEDs
are turned off.
❑The position information is taken from the posi-
tion information of the VG9000H safety valve con-
troller and the triggering limits are user
selectable.
4.1.6 Test LED
❑The function of the Test LED is to indicate when
the Test button is pushed and the PST test with
VG9000H has started. See Section 4.1.3. for the
Test button functionality.
❑The Test LED will be turned on when the Test but-
ton is pushed and released. It will be on also dur-
ing the Test Warning Time. The Test Warning
Time is the VG9000H parameter and can only be
seen and changed via HART (DTM, EDD).
❑The Test LED will also be turned on during other
tests: pneumatics test, automatic or manual PST
and ETT. See the VG9000H manual for other test
details.
❑The LED will blink few times if the test starting
fails.
NOTE:
When the button is pushed and released, the valve will
be driven to the safety position; i.e. it will close the
valve if it is the emergency shutdown valve and it will
open the valve when it is the emergency blowdown
(venting) valve.
NOTE:
When the button is pushed and released, the valve will
be driven to the normal operating position; i.e. it will
open the valve if it is the emergency shutdown valve
and it will close the valve when it is the emergency
blowdown (venting) valve
NOTE:
Make sure to push the Reset button only when it is safe
to return the valve to the normal operating position.
NOTE:
Make sure to push the Reset button only when it is safe
to return the valve to the normal operating position.

87 LCP9H 70 en
4.1.7 Alarm LED
❑The Alarm LED indicates the alarm state in the
VG9000H.
❑If the Alarm LED is turned on, it means that the
Alarm status is activated in the VG9000H.
❑The Alarm LED will blink, if the communication
between the LCP9H and the VG9000H is discon-
nected or not functional, or if the External
Devices parameter in the VG9000H is not
defined as "LCP". That parameter can only be
changed via HART or LUI.
5 MAINTENANCE
Under normal service conditions there is no require-
ment for regular maintenance.
5.1 LED test
Push the Test button for more than 10 seconds. All the
LEDs will then be turned on and off after one another in
the following sequence: open, closed, reset, test,
alarm. After the lamp test, the LEDs which were turned
on prior to this testing will be turned on.
6 TROUBLE SHOOTING
If the LCP9H does not work, check the following:
❑Check the LCP parameter in the VG9000H:
The LCP parameter in the VG9000H needs to be
enabled. Go to the parameters menu in the
VG9000H and check that LCP is enabled. For
details see the VG9000H IMO.
This can also be checked in Assembly Related
view in the VG9000H DTM. Check that LCP is
selected in the External Devices parameter. For
details see the VG9000H DTM manual.
❑Wiring:
Check that the wiring between the LCP9H and
the VG9000H is done according to the instruc-
tions in this manual and/or in the VG9000H IMO.
❑Power supply:
Check that the power supply for the LCP9H is
connected according to the instructions in this
manual and it is turned on.
❑VG9000H:
Check that the VG9000H installation and setup is
done according to the instructions in the
VG9000H IMO.
If starting the test fails:
❑Check that there are no alarms/warnings in the
VG9000H. See the VG9000H and/or DTM manual
for details.
❑The push of the test button may be too short or
too long. You need to push the test button for
0.2–10 seconds and then release.
If the reset function does not work:
❑Check that the mA signal to VG9000H is above
16 mA. See the VG9000H and/or DTM manual for
details.
❑Check that supply pressure to the VG9000H is
turned on and in the correct range.
❑The push of the test button may be too short or
too long. You need to push the test button for
0.2–10 seconds and then release.
7TOOLS
Use the provided key for opening and locking the cover
(LCP9H, LCP9HW). No other special tools are required.
Use 8 mm hex key for the cover screws in the LCP9HE
or LCP9HEW.
8 TYPE CODING
See the Neles ValvGuard VG9000H typecoding for the
LCP9H and VG9000H detailed type coding.
9 SPARE PARTS
The following spare parts are available:
❑printed circuit board
❑push buttons
❑button covers
Contact the local Metso's Automation business line
office for ordering spare parts.
NOTE:
LCP9H maintenance must only be carried out by Metso
certified service personnel.

7 LCP9H 70 en 9
10 DIMENSIONS
LCP9H, LCP9HW
Note: This button is only available in LCP9H.
LCP9HW does not have this button.

10 7 LCP9H 70 en
LCP9HE, LCP9HEW
Note: This button is only available in LCP9HE
LCP9HEW does not have this button.

7 LCP9H 70 en 11
11 EC DECLARATION OF CONFORMITY
EC DECLARATION OF CONFORMITY
Manufacturer:
Metso Automation Oy
01301 Vantaa
Finland
Product:
Local Control Panel LCP9H-series
Approvals:
As the products within our sole responsibility of design and manufacture may be used as parts or components in machinery and are not alone
performing functions as described in Article 6(2) in the Machinery Directive (2006/42/EC), we declare that our product(s) to which this Declaration of
Conformity relates must NOT be put into service until the relevant machinery into which it is to be incorporated has been declared in conformity with
the provisions of the Machinery Directive.
The product above is manufactured in compliance with the applicable European directives and technical specifications/standards.
Protection from e.g. static electricity caused by the process or connected equipment must be considered by the user ( EN 60079-14 §6 ).
The product do not possess any residual risk according to hazard analyses made under the applicable directives providing that the procedures
stated by the Installation, Operation and Maintenance manual are followed and the product is used under conditions mentioned in the technical
specifications.
Vantaa 8th September 2011
Ralf Liljestrand, Quality Manager
A
uthorized person of the manufacturer within the European Community
Applicable directives:
EMC 2004/108/EC Electrical
ATEX 94/9/EC Approved and Ex marked types
ATEX Notified Bodies for EC Type Examination Certificate:
SIRA (Notified body number 0518)
Sira Certification Service
Rake Lane, Eccleston,
Chester, CH4 9JN
England
VTT (Notified body number 0537)
VTT, Expert Services
Otakaari 7B, Espoo
P.O.Box 1000, FI-02044 VTT
Finland
ATEX Notified Body for Quality Assurance:
ISO 9001:2008 Certificate No: 73538-2010-AQ-FIN-FINAS
ATEX 94/9/EC Annex IV Certificate No: DNV-2006-OSL-ATEX-0260Q
Det Norske Veritas AS (Notified body number 0575)
Veritasveien 1
1322 Høvik, Oslo
Norway
Type Approval EC Type examination Certificate
LCP9H
LCP9HW
(EMC 2004/108/EC) EN 61000-6-2 (2005),
EN 61000-6-4 (2007) NEMKO 135608
LCP9HE
LCP9HEW
(EMC 2004/108/EC) EN 61000-6-2 (2005),
EN 61000-6-4 (2007) NEMKO Attestation 164606S
LCP9H
LCP9HW
ATEX II 2G Ex ia IIC T4/T5/T6 Gb
ATEX II 3G Ex ic IIC T4/T5/T6 Gc
ATEX II 3G Ex nL IIC T4/T5/T6 Gc
VTT 09 ATEX 047X
EN 60079-0: 2009, EN 60079-11: 2007
VTT 09 ATEX 048X
EN 60079-0: 2009, EN 60079-11: 2007
VTT 09 ATEX 048X
EN 60079-0: 2009, EN 60079-15: 2005
LCP9HE
LCP9HEW
ATEX 2 IIG Ex d IIB+H2 T6 Gb
ATEX 2 IID Ex tb IIIC T85°C Db IP65
SIRA 11 ATEX 1170
EN 60079-0: 2007, EN 60079-1: 2007,
EN 60079-31: 2008

Metso Automation Inc.
Europe, Vanha Porvoontie 229, P.O. Box 304, FI-01301 Vantaa, Finland. Tel. +358 20 483 150. Fax +358 20 483 151
North America, 44 Bowditch Drive, P.O. Box 8044, Shrewsbury, MA 01545, USA. Tel. +1 508 852 0200. Fax +1 508 852 8172
Asia Pacific, 20 Kallang Avenue, Lobby B, #06-00, PICO Creative Centre, Singapore 339411, Singapore. Tel. +65 6511 1011. Fax +65 6250 0830
China, 19/F, the Exchange Beijing, No. 118, Jianguo Lu Yi, Chaoyang Dist, 100022 Beijing, China. Tel. +86-10-6566-6600. Fax +86-10-6566-2575
Middle East, Roundabout 8, Unit AB-07, P.O. Box 17175, Jebel Ali Freezone, Dubai, United Arab Emirates. Tel. +971 4 883 6974. Fax +971 4 883 6836
www.metso.com/valves
South America, Av. Independéncia, 2500-Iporanga, 18087-101, Sorocaba-São Paulo, Brazil. Tel. +55 15 2102 9700. Fax +55 15 2102 9748
12 7 LCP9H 70 en
Other manuals for LCP9H Series
3
This manual suits for next models
4
Table of contents
Other Metso Control Panel manuals
Popular Control Panel manuals by other brands

LinkAYL
LinkAYL LK-CP63 Series quick start guide
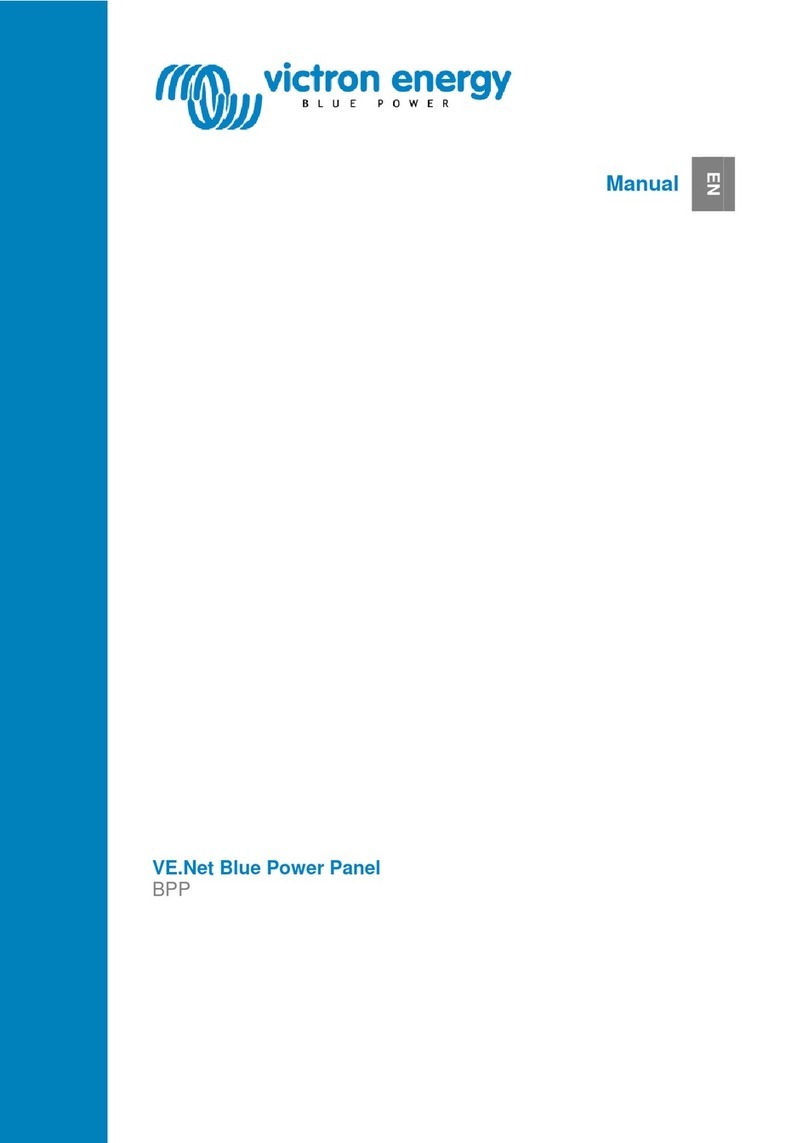
Victron energy
Victron energy VE.Net Blue Power Panel manual
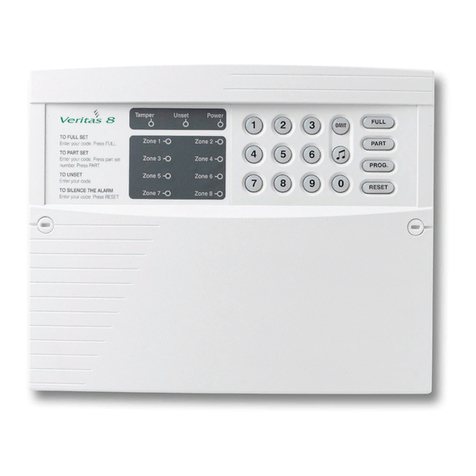
Texecom
Texecom Veritas 8 user guide
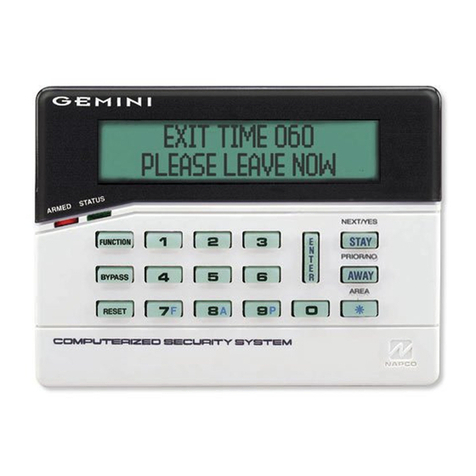
NAPCO
NAPCO Gemini GEM-X255 Programming instructions

Menvier Security
Menvier Security TS400 operating instructions
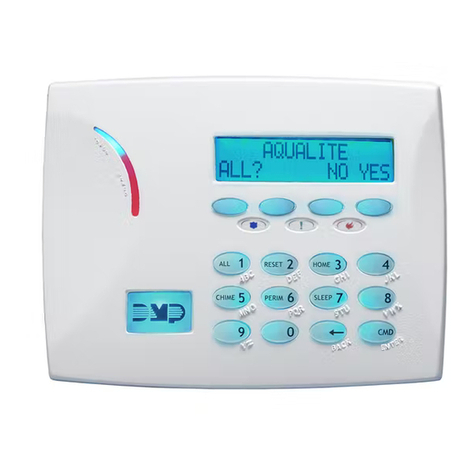
DMP Electronics
DMP Electronics XT50 Series user guide
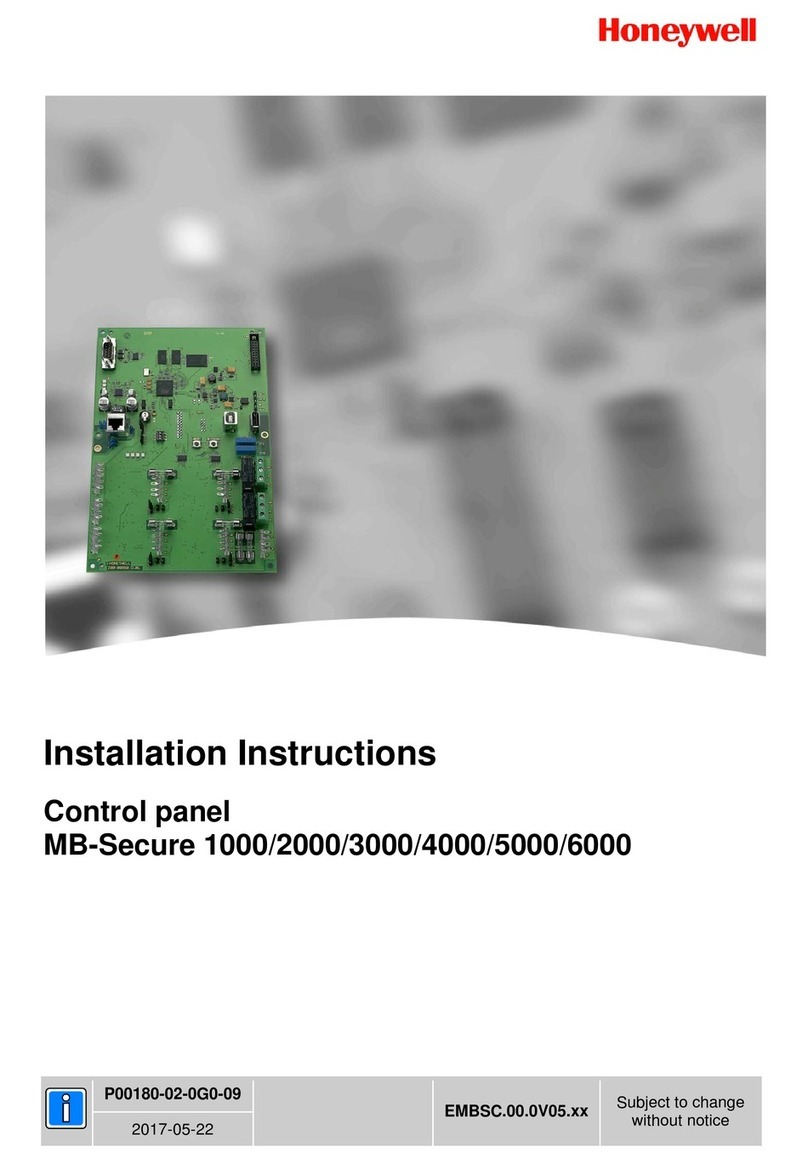
Honeywell
Honeywell MB-Secure 1000 installation instructions
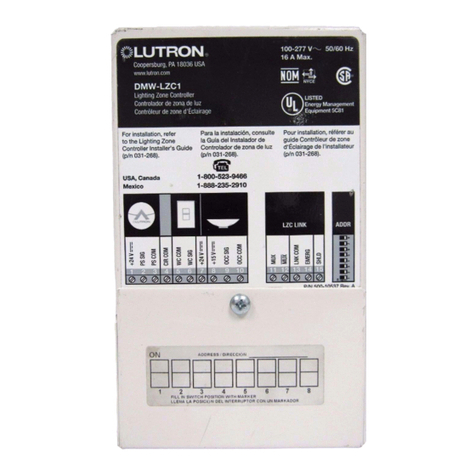
Lutron Electronics
Lutron Electronics DMW-LZC1 Installation and maintenance guide
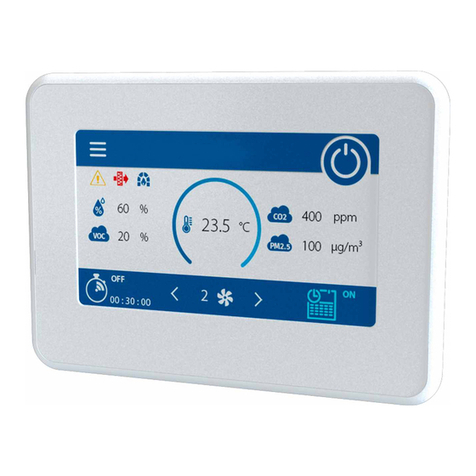
Vents
Vents A25 user manual
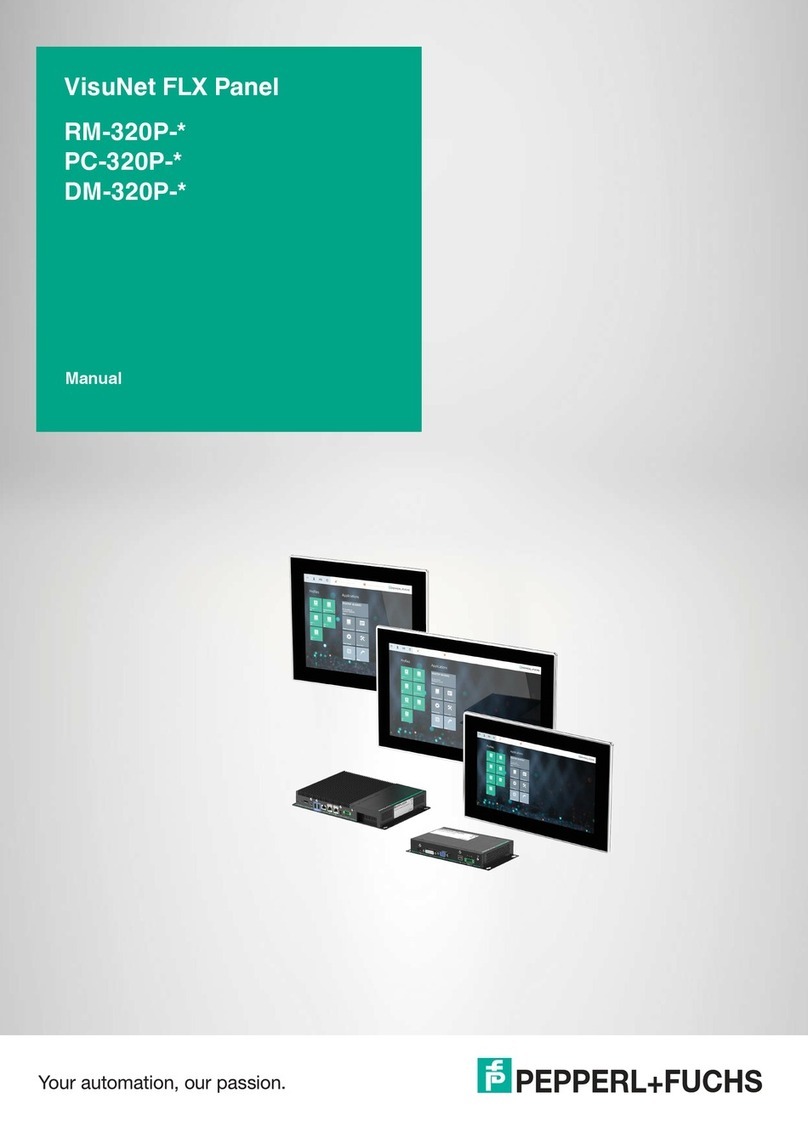
Pepperl+Fuchs
Pepperl+Fuchs VisuNet FLX RM-320P Series manual
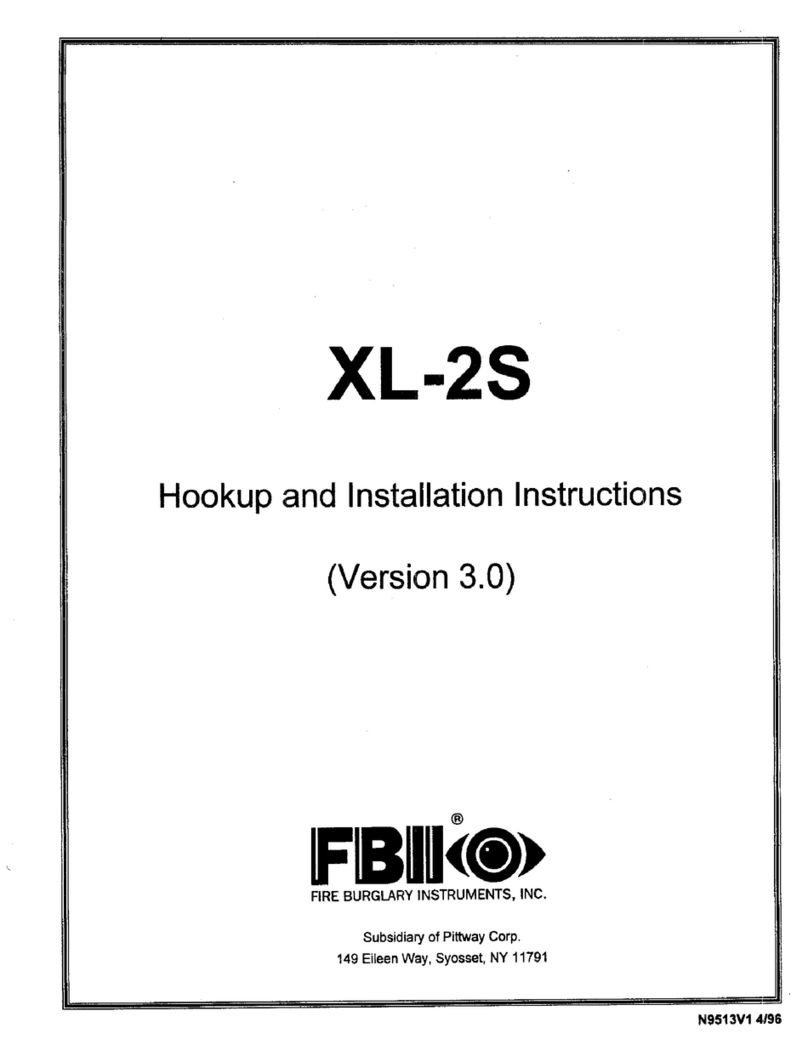
FBII
FBII XL-2S Silver Hookup and installation instructions

Bosch
Bosch Ultima 862 Quick reference guide