Micatrone MF-PFA-PU User manual

MF-PFA-PU
ver 3.x
Micaflex PFA-PU ver 3.
Pressure- and Flow transmitter with alarm
and purging function for flow sensor
Installation- & Operation manual
[Dok. id: mi-312gb_180528]
[© AB Micatrone, mi-312gb_180528] Page 1 of 8
NOTE !
Read through the entire manual before you begin
installation and programming.
APPLICATION
MF-PFA-PU is a microprocessor controlled transmitter/
controller for measurement of differential pressure or
flow. With the four keys on the front panel it is possible
to access all functions, make settings and scale the
output signal. The double row, 2x16 character, LCD
with backlight displays functions and values.
MOUNTING
MF-PFA-PU is designed for wall mounting but can
be fitted with an optional frame kit, MFM-PANEL, for
recessed mounting on wall or through a cabinet door.
MF-PFA-PU is screwed to the wall using four screws,
max ø 4mm. Location of screw holes are shown on the
reverse of the enclosure.
Unscrew the lid and use the bottom screws to
temporarily fix the lid on the upper edge of the
enclosure during installation. See figure.
OUTPUT SIGNAL
MF-PFA-PU has two analogue output signals which
can be used for pressure, flow or control signal. Each
output has three terminals, one for Volt DC, one for mA
DC and one common zero. The outputs allow both the
Volt and mA signals to be used simultaneously.
With activated purging function, the purging unit PU3
is connected to output 1 (Volt or mA). If the unit is fitted
with built-in automatic zero-setting module MFM-ZP, it
is connected to output 2 (Volt or mA). It is still possible
to use the free output signal on both outputs for the
selected source.
ALARM
MF-PFA-PU has two alarms, each independent of the
other. Each alarm has it´s own voltage-free changing
relay output, acoustic beeper and LED indication for
pressure or flow, high or low alarm level and manual or
automatic reset.
START MENU
When the transmitter is connected to supply voltage, a
start menu is displayed.
Using the arrow-keys it is possible to scroll through the
different available start menus. To have the unit always
displaying the same start menu, it can be selected and
programmed in parameter group SYSTEMSETTINGS.
By pressing the ESC-key when other menus are
displayed the selected start menu is displayed.
PROGRAMMING
Push the PGM-key until “PROGRAM-MENU” is
displayed. Release the PGM-key and the first parameter
group is displayed according to the parameter list on
page 2.
Using the arrow-keys it is possible to scroll through the
different available parameter groups. Note, if code
lock is activated, see page 6, the programmed 4-digit
access code must be entered to access the menu.
1. Internals
2. System settings
3. Output 1
4. Output 2
5. Pressure
6. Flow
7. Alarm 1
8. Alarm 2
9. PI Controller
10. Purging unit
11. AutoZero
12. Communication
When the desired parameter group is displayed, press
the PGM-key to select the group for programming. The
available parameters in the selected parameter group
are displayed on the bottom row.
Use the arrow-keys to select which parameter to
program and press the PGM-key.
AA

Page 2 of 8 [© AB Micatrone, mi-312gb_180528]
Nr Lead text Min Max Default
Internals
P00 SW: I/O
P01 SW: OPI
System settings
P03 Display dP
FLOW
dP+FLOW
SRC+CTRL
dP
P04 Damping [s] 0,0 9,9 1,0
P05 Access code 0000 9999 0000
P06 Number of OPI 1 3 1
Output 1
P08 Source dP
FLOW
CTRL
dP
P09 Signal V 0..10
2..10
0..10
P10 Signal mA
0..20
4..20
4..20
Output 2
P11 Source dP
FLOW
CTRL
CTRL
P12 Signal V 0..10
2..10
0..10
P13 Signal mA 0..20
4..20
4..20
Pressure
P15 MinCal [Pa]
P16 MaxCal [Pa]
P17 Unit dP Pa / mbar / iwc Pa
P18 Decimals 0 4 0
P19 Min range MinCal
P20 Max range MaxCal
P21 Min out MinRange MaxRange MinCal
P22 Max out MinRange MaxRange MaxCal
P23 Sign dP POS / NEG POS
Flow
P24 Unit flow l/s
m3/s
m3/h
m/s
cfm
l/s
P25 Decimals 0 4 0
P26 Max flow 0 32767 0
P27 Scale flw 0 32767 0
P28 Set flow 0 32767 0
Alarm 1
P33 Mode OFF
HIGH
LOW
OFF
P34 Source dP
FLOW
dP
P35 Limit MinRange MaxRange 0
P36 Delay [s] 0 3600 0
P37 Reset MANUAL
AUTO
AUTO
P38 Beeper OFF
ON
OFF
P77 Mute BEEP
BEEP&RELAY
BEEP
P39 Mute time 0 3600 0
Alarm 2
P40 Mode OFF
HIGH
LOW
OFF
P41 Source dP
FLOW
dP
P42 Limit MinRange MaxRange 0
Nr Lead text Min Max Default
P43 Delay [s] 0 3600 0
P44 Reset MANUAL
AUTO
AUTO
P45 Beeper OFF
ON
OFF
P78 Mute BEEP
BEEP&RELAY
BEEP
P46 Mute time 0 3600 0
PI Controller
P47 Mode OFF
ON
OFF
P48 Source dP
FLOW
dP
P49 Set point MinRange MaxRange 0
P58 NZ [%] 1 50 2
P59 P-band [%] 0 9999 0
P60 I-time [s] 0 999 10
P61 BZ [%] 0 100 0
P62 I-time BZ [s] 0 999 0
P63 Output DIRECT
REVERSE
REVERSE
P64 Min output 0 100 0
P65 Max output 0 100 100
Purging unit
P69 Mode OFF
ON
TEST
OFF
P70 On Time [s] 0 60 10
P71 Pause [s] 30 3600 600
P84 Output Volt 1
mA 1
mA 1
AutoZero
P81 Interval [h] 0,0 60,0 0,0
P85 Output Volt 2
mA 2
mA 2
Communication
P73 Address 1 247 21
P74 Baud OFF / 600 128000 38400
P75 Parity NONE
ODD
EVEN
NONE
P76 Protect NO
YES
NO
Programming of a numeric value
Each digit in a numeric value is programmed separately.
Press PGM to begin programming. The selected digit
is flashing. Press the up-arrow key for digits between 1
and 9. When passing digit “9”, negative digits between
-9 and 0 are shown if they are allowed in the parameter
value. Confirm each digit by pressing the PGM-key.
When all digits are programmed, press the PGM-key
to save the new value. The entire row is flashing to
confirm programming. To abort ongoing programming,
press the ESC-key and then begin a new programming
with the PGM-key.
Note! It is always possible to abort or cancel incorrect
programming using the ESC-key unless you have
pressed the PGM-key after programming the last digit.
Programming of alternative units or values
Press the arrow-keys to select the desired alternative
unit or value. Press the PGM-key to save the change.
The entire row is flashing to confirm programming.
Note! It is always possible to abort or cancel incorrect
programming using the ESC-key unless you have
pressed the PGM-key after selected unit/value.
PARAMETER LIST

[© AB Micatrone, mi-312gb_180528] Page 3 of 8
End programming mode
Press the ESC-key to return to parameter group
selection display. Press the ESC-key a second time
to close the programming menu and return to the start
menu.
If no key has been pressed during 5 minutes, the
program menu is closed automatically.
1. INTERNALS
Displays the program versions for the I/O-board
(motherboard) and Operator Interface (display).
No Lead text Min Max Default
P00 SW: I/O
P01 SW: OPI
2. SYSTEM SETTINGS
General settings in MF-PFA-PU
No Lead text Min Max Default
P03 Display dP
FLOW
dP+FLOW
SRC+CTRL
dP
P04 Damping [s] 0,0 9,9 1,0
P05 Access code 0000 9999 0000
P06 No of OPI 1 3 1
• P03 Display, select start menu to display. Select-
ing ‘SRC+CTRL’ show the selected source (SRC)
in the PI-controller + control output signal (CTRL).
• P04 Damping, programme, in seconds, the damp-
ing for the pressure output signal.
• P05 Access code, used for activating or deactivat-
ing the code lock, see page 6.
• P06 Number of OPI, number of operator interfaces
connected. See separate instruction.
3-4. OUTPUT 1 and OUTPUT 2
Settings for the two output signals
No Lead text Min Max Default
P08 Source dP
FLOW
CTRL
dP
P09 Signal V 0..10
2..10
0..10
P10 Signal mA 0..20
4..20
4..20
P11 Source dP
FLOW
CTRL
CTRL
P12 Signal V 0..10
2..10
0..10
P13 Signal mA 0..20
4..20
4..20
MF-PFA-PU has 2 output signals which can be set
to either 0..10 Volt, 2..10 Volt, 0..20 mA or 4..20 mA.
Both Volt and mA are simultaneously available for both
outputs.
• P08/P11 Source, is used to select which measuring
value/signal (source) to direct as output signal. ‘dP’
is the pressure signal, ‘FLOW’ is the flow signal and
‘CTRL’ is the control signal from the PI-controller.
• P09/P12 Signal V is used to switch between 0..10
Volt and 2..10 Volt output signal.
• P10/P13 Signal mA is used to switch between
0..20 mA and 4..20 mA output signal.
With activated purging function, the purging unit PU3 is
connected to output 1 (Volt or mA) and the parameter
(P09 or P10) is hidden in the parameter list. If the unit
is fitted with built-in automatic zero-setting module
MFM-ZP, it is connected to output 2 (Volt or mA) and
the parameter (P12 or P13) is hidden in the parameter
list. It is still possible to use the free output signal on
both outputs for the selected source.
5. PRESSURE
Settings for pressure measurement
No Lead text Min Max Default
P15 MinCal [Pa]
P16 MaxCal [Pa]
P17 Unit dP Pa / mbar / iwc Pa
P18 Decimals 0 4 0
P19 Min range MinCal
P20 Max range MaxCal
P21 Min out MinRange MaxRange MinCal
P22 Max out MinRange MaxRange MaxCal
P23 Sign dP POS / NEG POS
• P15/P16 MinCal[Pa] / MaxCal[Pa],
The MF-PFA-PU is factory calibrated for a specific
range. The range is written on a label located on
the right side of the enclosure. The calibration is
always in Pascal (Pa). Min cal and Max cal is the
calibrated pressure range in Pa. These values are
notes and not possible to change.
• P17 Unit dP, Select in which unit to display the
pressure. The alternatives are Pa, mbar or iwc
(inch water column).
• P18 Decimals, Number of decimals to show for the
pressure value. When using Pa as unit it is recom-
mended not to use decimals.
In case any set value is above 32767 regardless of
where the decimal point is placed the adjustment is
not carried out.
E.g. If Set Point = 5000 and one decimal is se-
lected, the adjustment will not work since the value
5000,0 is greater than the allowed max value of
3276,7. Of the same reason, 500,0 cannot be
adjusted to 500,00.
• P19/P20 Min range / Max range
When programming a new unit, min and max limits
in the new unit are displayed in parameter Min
range and Max range. These values are notes and
are not changeable.
• P21 Min out, Lower limit for scaling the output
signal is set in pressure units, e.g. 10 Pa will result
at 10 Pa pressure the min output signal of, 0/2 V
resp. 0/4 mA.
• P22 Max out, Higher limit for scaling the output
signal is set in pressure units, e.g. 90 Pa will result
at 90 Pa pressure the max output signal of 10 V
resp. 20 mA.
• P23 Sign dP, If the transmitter is without zero
crossing, the MF-PFA-PU will indicate a negative
pressure similar to positive pressure (i.e. Without
negative sign). When programming Sign dP =
‘NEG’ a negative sign (-) is shown in front of the
current value.
To change the range for the output signal, the Min out
and Max out are programmed. Programmed values

Page 4 of 8 [© AB Micatrone, mi-312gb_180528]
must be in the selected unit (Pa, mbar, iwc). When
scaling, be aware that the accuracy is always in
percent of the factory calibrated pressure range.
To measure and control the flow or velocity it is
necessary to connect the transmitter to flow sensors
with a known formula and k-factor.
6. FLOW
Settings for flow measuring.
No Lead text Min Max Default
P24 Unit flow l/s
m3/s
m3/h
m/s
cfm
l/s
P25 Decimals 0 4 0
P26 Max flow 0 32767 0
P27 Scale flw 0 32767 0
P28 Set flow 0 32767 0
• P24 Unit flow, select a suitable unit for flow display,
l/s, m3/s, m3/h, m/s or cfm (cubic feet / minute).
• P25 Decimals, Number of decimals to show for the
flow value. In case any set value is above 32767
regardless of where the decimal point is placed the
adjustment is not carried out.
E.g. if Max Flow = 5000 and one decimal is se-
lected, the adjustment will not work since the value
5000,0 is greater than the allowed max value of
3276,7. For the same reason, 500,0 cannot be
adjusted to 500,00.
• P26 Max flow, set the flow that corresponds to the
pressure range on the MF-PFA-PU.
• P27 Scale flw, set the flow for max output signal,
10 V resp. 20 mA.
• P28 Set flow, Programme this parameter if adjust-
ing the displayed flow is necessary. Programme
the current flow using a reference flow measure-
ment. Max flow is re-scaled to correspond with the
reference measurement. If the unit is connected to
a computer system or similar, the receiving system
should also be programmed if the Scale flw value
is higher than the new value of Max flow.
NOTE! Programming must be performed at the
same time as when the reference value is meas-
ured (The PGM-key is pressed for the last digit and
the value is stored).
The basic flow calculation used is made with √dP.
To have the display and the output corresponding
to the actual flow or velocity in the selected unit it is
necessary to make some calculations. Different manu
factors of flow measurement devices have different
calculation, but common for all is √dP.
Use the actual formula to calculate the max flow for
the factory calibrated measure range. The calculated
flow or velocity is then programmed under Max
flow in the selected unit. E.g. 5,0 m3/s. It is possible
to scale the flow range under Scale flw. When
scaling the flow, note that the accuracy depends
on the “Max flow” range. Scale flw must always
be set to the same or a lower value than Max flow.
E.g. 3,5 m3/s = 10 VDC.
The output signal is linear to the flow or velocity.
7-8. ALARM 1 and ALARM 2
Settings for two alarm limits.
No Lead text Min Max Default
P33 Mode OFF
HIGH
LOW
OFF
P34 Source dP
FLOW
dP
P35 Limit MinRange MaxRange 0
P36 Delay [s] 0 3600 0
P37 Reset MANUAL
AUTO
AUTO
P38 Beeper OFF
ON
OFF
P77 Mute BEEP
BEEP&RELAY
BEEP
P39 Mute time 0 3600 0
P40 Mode OFF
HIGH
LOW
OFF
P41 Source dP
FLOW
dP
P42 Limit MinRange MaxRange 0
P43 Delay [s] 0 3600 0
P44 Reset MANUAL
AUTO
AUTO
P45 Beeper OFF
ON
OFF
P78 Mute BEEP
BEEP&RELAY
BEEP
P46 Mute time 0 3600 0
MF-PFA-PU has an alarm with two, each independent,
alarm limits. Each alarm has a voltage-free changing
relay output, acoustic (buzzer) and visual indication
with LED (light emitting diode). Normal state is
indicated with green LED and alarm state with red
flashing LED on the lid. The acoustic alarm can be
disabled for each alarm limit. Red LED is activated by
the first alarm state that occurs. At the alarm limit, the
red LED is lit and after set time delay it begins to flash.
The display shows which of the alarm limits triggered
the alarm.
• P33/P40 Mode, select if the alarm should be trig-
gered for high or low level. Programme as ‘OFF’ to
deactivate monitoring.
• P34/P41 Source, Choose which measuring value
is to be monitored. ‘dP’ = pressure, ‘FLOW’ = flow.
• P35/P42 Limit, set at which level the alarm is to be
triggered.
• P36/P43 Delay [s], set time delay before alarm
state occurs.
• P37/P44 Reset, ‘Manual’ if the alarm should be
reset manually by pressing the ESC-key or ‘Auto’
if the alarm state should return automatically to
normal state when the level is back to normal.
• P38/P45 Beeper, ‘OFF’ disable the acoustic alarm.
‘ON’ if alarm state should sound.
• P77/P78 Mute, Select ‘BEEP’ to reset the acoustic
alarm or ‘BEEP&RELAY’ to reset both acoustic and
relay function.
• P39/P46 Mute time, is used to silence (mute) the
alarm for a set time in seconds when the ESC-key
is pressed.
If the time is set to ‘0’, the alarm is muted until the
alarm is reset and a new alarm state occur.

[© AB Micatrone, mi-312gb_180528] Page 5 of 8
9. PI-CONTROLLER
Settings of PI-controller.
No Lead text Min Max Default
P47 Mode OFF
ON
OFF
P48 Source dP
FLOW
dP
P49 Set point MinRange MaxRange 0
P58 NZ [%] 1 50 2
P59 P-band [%] 0 9999 0
P60 I-time [s] 0 999 10
P61 BZ [%] 0 100 0
P62 I-time BZ [s] 0 999 0
P63 Output DIRECT
REVERSE
REVERSE
P64 Min output 0 100 0
P65 Max output 0 100 100
MF-PFA-PU has a PI-controller specially made for
pressure and flow control.
The controller could be programmed as a standard PI-
controller, but in most of the applications together with
pressure and flow control we recommend to program it
as an integral controller without P-band.
There are two programmable I-times. Outside a
desired limit on both sides of the set point it is possible
to have a shorter I-time and inside the limits a longer
I-time. The PI-control signal is directed to a desired
output in parameter group Output 1 or Output 2.
• P47 Mode, ‘ON’ activates PI-controller, ‘OFF’ dis-
ables the controller.
• P48 Source, select which measuring value to con-
trol. ‘dP’ = pressure, ‘FLOW’ = flow.
• P49 Set point, Set point value in the selected unit.
• P58 NZ [%], select desired neutral zone, normally
1..5%. Half zone above and half below set point
value. Set in percent of the measuring range.
• P59 P-band [%], normally not used for pressure or
flow control, default 0%. If P-band is programmed
to 0 % the P-function is disabled and the I-time is
calculated for a P-band of 100%.
• P60 I-time[s], set suitable I-time, normal 10s.
• P61 BZ [%], Break zone, used when you want to
reduce the control speed when surrounding the set
point.
• P62 I-time BZ, set I-time inside the break zone. En-
ter a longer I-time for a stable control when close
to the neutral zone.
• P63 Output, direction of the control output signal.
Normally ‘REVERSE’ (if the pressure or flow is
above set point, the output signal will decrease).
• P64 Min out, set a lower limit for the control output
signal in %.
• P65 Max out, set a higher limit for the control out-
put signal in %.
I-time
When programming as an I-controller there are two
possibilities.
• The same I-time over the full range. Normally used.
Program BZ = 000 and I-time BZ = 000. The I-time
should normally be longer than the time for the
damper motor etc. to go from min to max.
• Shifting between two I-times. The reason for work-
ing with two I-times is often that outside a set pres-
sure or flow limit you want to have a fast response
and inside a slow response (see figure below).
BZ: limit for switching I-time. BZ is in % of the scaled
pressure or flow range. The set break zone, BZ, is
counted from the neutral zone, NZ, higher and lower
limit. The set value is on each side of the neutral zone
and moves with any changes in the neutral zone. If
the control output is not entering a stable position,
increase the I-time, you could also try to increase the
neutral zone.
Manual operation
Return to the start menu and select the display option
where output signal for PI-controller together with
pressure or flow is indicated. Which one is displayed
is determined by what the PI controller is programmed
for.
“Flow / dP”
“AUTO 50.00 %”
Press PGM, ‘AUTO’ changes to ‘HAND’ and the output
signal can be set in % using the arrow keys.
Return to position ‘AUTO’ by pressing the PGM-key.
To display the programmed start menu, press the
ESC-key.
The display showing the text “PI-” in front of ‘HAND’
or ‘AUTO’ is not possible to use for manual operation.
10. PURGING UNIT
Settings for the purging function with a connected
purging unit, PU3.
No Lead text Min Max Default
P69 Mode OFF
ON
TEST
OFF
P70 On Time [s] 0 60 0
P71 Pause [s] 30 3600 30
P84 Output Volt 1
mA 1
mA 1
• P69 Mode, ’ON’ activates the function and ’TEST’
begin purging.
• P70 On Time, time in seconds for purging.
• P71 Pause, time in seconds between each
purging.
• P84 Output, Select which output the PU3 is
connected to.
DP/Flow
BZ
BZ
Setpoint
NZ
NZ
12
I-time BZ
I-time I-time
sec.

Page 6 of 8 [© AB Micatrone, mi-312gb_180528]
11. AUTOZERO
Automatic zero adjustment. This parameter group is
only visible when solenoid valve MFM-ZP is installed.
No Lead text Min Max Default
P81 Interval [h] 0,0 60,0 0,0
P85 Output Volt 2
mA 2
mA 2
Using the optional built-in solenoid valve, automatic
zero adjustment can be set. During this process, the
displayed values and the output signals are halted.
After the zero adjustment is done in approx. 15
seconds, the transmitter restore to normal operation.
Zero adjustment can also be carried out manually
according to instructions on page 7.
• P81 Interval[h], The time between adjustment can
be set between 0,1 and 60 hours.
• P85 Output, Select which output the solenoid valve
is connected to.
12. COMMUNICATION MODBUS
Modbus RTU through RS-485 serial connection.
This parameter group is only visible when communi-
cation module is installed.
No Lead text Min Max Default
P73 Address 1 247 21
P74 Baud OFF / 600 128000 38400
P75 Parity NONE
ODD
EVEN
NONE
P76 Protect NO
YES
NO
MF-PFA-PU can be fitted with a built-in expansion
module (Option) for network communication with a
computer.
P73 Address, network address for MF-PFA-PU, factory
default as 21.
P74 Baud, transfer rate, factory default 38400 baud.
P75 Parity, Parity bit in data transfer. Factory default
‘NONE’.
P76 Protect, Protection for parameter programming
through network communication. ‘YES’ = write
protection. This parameter can only be set to ‘NO’
using the MF-PFA-PU keypad.
CODE LOCK PROTECTION
The code lock is used to protect against unauthorised
programming. A four-digit code must be entered to
access the program menu and the functions menu. It
is still possible to read measuring values and operating
state without entering the access code.
At delivery, the code is set to ‘0000’, unless otherwise
agreed on. When the code is set to ‘0000’, the code
lock is inactivated and no protection against an
authorized programming is present.
Activation
To activate the code lock, a 4-digit code must be
programmed in parameter P05 Access code which
is found in parameter group SYSTEM SETTINGS.
The code can not be ‘0000’, since this code is used
to deactivate the function. When a code has been
programmed and saved, the next time it will be
necessary to enter the code to access the program
menu and the functions menu.
Deactivating
The code lock can only by deactivated in the program
menu and therefore the access code must be available
to deactivate the code lock. Set the parameter P05
Access code to ‘0000’. The parameter is found in the
parameter group SYSTEM SETTINGS.
Contact Micatrone if the code has been lost!
Entering the code
To access the program menu or functions menu it is
necessary to enter the access code.
Example:
1. Press the PGM-key to open the program menu.
Press the PGM-key until “PROGRAM- MENU” is
displayed.
2. Release the PGM-key. Following text is displayed
if key code is activated: “ENTER CODE:” and
“0***”.
3. The first digit of the access code can be entered
using the arrow keys. When ready press the PGM-
key to continue with the next digit. Repeat until all
digits are entered.
4. When the 4 digits are entered, press the PGM-key
a final time. The entered code is now compared
with the programmed code in parameter P05
Access code. If the codes match, the program
menu is displayed. The program menu is available
until it has been exited using the ESC-key.
5. If the entered access code is incorrect, the text
“INVALID CODE” is displayed during 2 seconds.
Restart from point 1.
6. By pressing the ESC-key, the entering code
operation is cancelled and the default start menu
is displayed.

[© AB Micatrone, mi-312gb_180528] Page 7 of 8
FUNCTIONS MENU
Functions that are not used frequently are found in
the functions menu. The functions menu is accessed
by pressing simultaneously the PGM and ESC-key
until the text “FUNCTIONS-MENU” is displayed. If
code lock is activated, see page , a valid access code
must be entered to access the menu.
Use the arrow keys to scroll through the different
functions, when displayed, select the desired function
by pressing the PGM-key. Exit the present menu by
pressing the ESC-key.
Functions
• Serial number Display the serial number xxxxx-xxx.
• Date of cal. Display the latest factory calibration
date.
• Reset Defaults Restore all data to the latest
factory calibration.
- List of params All values in the entire parameter
list are restored to default values at factory
delivery.
- Calibrations All calibrations are restored to
original values at factory delivery.
Note: field calibrations will be reset.
• Calibration
- Input, five-point calibration of the pressure
measurement
• Statistics Displays statistics for internal restarts.
- Power on, Number of normal power-on´s.
- Brown out, Number of restarts due to poor supply
voltage.
- Watchdog reset, Number of restarts due to run-
time error.
- SW error reset, Number of restarts due to soft-
ware error.
- Last reset cause, The cause for the latest restart.
- Operating time, Operating time since latest start.
Shown in days, hours and minutes (d:hh:mm).
Zero setting of pressure transmitter
Disconnect the pressure connections or place the
block valve in position calibration.
Press repeatedly on the ESC-key until the start menu
is displayed.
Press simultaneously on both arrow keys, keep
pressed until the display show:
Release the keys when following is shown:
When the zero setting is done, the display show:
Followed with the start menu.
If the transmitter is equipped with built-in auto zero
module, manual zero setting is done using the arrow
keys without the need to detach any tubes or changing
position of a connected mono block valve.
Calibration of MF-PFA-PU
MF-PFA-PU can be re calibrated against a pressure
reference.
1. Keep PGM and ESC pressed until following text
is displayed: “FUNCTIONS-MENU”.
2. Scroll using the arrow keys until “Calibration” is
displayed.
3. Press PGM. ‘Input’ is shown.
4. Press PGM. ‘Cal dP’ is shown.
5. Press PGM. The first calibration point is shown.
Example:
MF-PFA-PU (-50..50 Pa)
Pnt 1(5) = -50
6. Connect shown pressure. In this case, 50 Pa, to
the pressure connection marked negative [-].
7. Press the PGM-key and the MF-PFA-PU will
start to measure the first calibration point (9
measurements).
8. Press the PGM-key to continue with the second
calibration point, ESC aborts the calibration.
9. Proceed with all five calibration points and
be careful to connect to the correct pressure
connection.
10.When all calibration points are done, following
text is shown:
“PGM=OK/ESC=ABORT”
11. The PGM-key will confirm the calibration and
store the new calibration values.
12.The ESC-key will abort and cancel the calibration.
Press repeatedly on the ESC-key to return to the
start menu again.
Note! The pressure reference should comply with the
demand of desired accuracy in the measurement.
ZERO OFFSET
ZERO OFFSET
ADJUSTING
ZERO OFFSET
DONE

AB Micatrone Telephone: +46-8-470 25 00
Aldermansvagen 3
SE-171 48 SOLNA Internet: www.micatrone.com
Page 8 of 8 [© AB Micatrone, mi-312gb_180528]
Technical Data:
Display: Alphanumeric LCD
2 row, 2x16 characters
with backlight
Power supply: 24 ± 15% VAC
20...32 VDC
Pwr consumption: Max 3 VA (24VAC)
Pressure range: see label on enclosure.
Flow range:
(max 4 decimals)
l/s 0...32767
m3/s 0...32767
m3/h 0...32767
m/s 0...32767
cfm 0...32767
Measurement error: < ± 0,5 % of the pressure
range ± 0,5 Pa
Temperature drift: < ± 0,5 % /10 °C
Damping: 0,0...9,9 sec.
Output signal: Two analogue outputs,
0/2...10 VDC, 0/4...20 mA
selectable and scalable.
Both mA and Volt output
can be used simultaneously
Ambient temp: 0...50°C
Alarm: Two separate alarms for
high & low level, voltage-
free changing relay and
alarm indication with red
LED and buzzer (joint)
Max Load Relays: 48 VAC 5A / 48 VDC 1,5A
Degree of protection: IP 65, ABS plastic
El-connection: 1 x 2,5 mm2/ terminal
Cable glands: 4 pcs M16x1.5mm
(glands not included)
Dimensions: WxHxD = 122x120x90 mm
Height excl. standard
pressure connections
(30mm)
Weight: 0,86 kg
Maintenance:
It is recommended to check the zero setting every 6
months.
Accessories:
• Mounting kit for recessed mounting
• External transformer 24, 115, 230 VAC
• Modbus RTU data communication module with
RS-485 interface
• Module for automatic zero setting
• Separate display unit for remote placement up to
30m beyond main unit. Two seperate display units
can be connected to the same main unit
EMC/LVD/RoHS II:
AB Micatrone declare under sole responsibility
that MF-PFA-PU is in conformity with the essential
requirements in the EMC-, the LVD- and the RoHS II
directive. The full text of Manufacturers declaration of
conformity is available on Micatrones website.
Electrical connection: Note!. Contacts in fallen/unpowered state
Table of contents
Other Micatrone Transmitter manuals
Popular Transmitter manuals by other brands
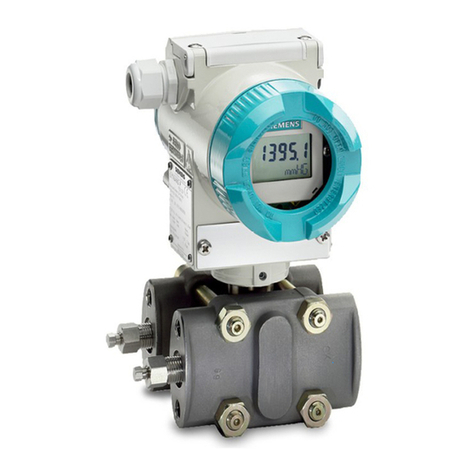
Siemens
Siemens SITRANS Series operating instructions
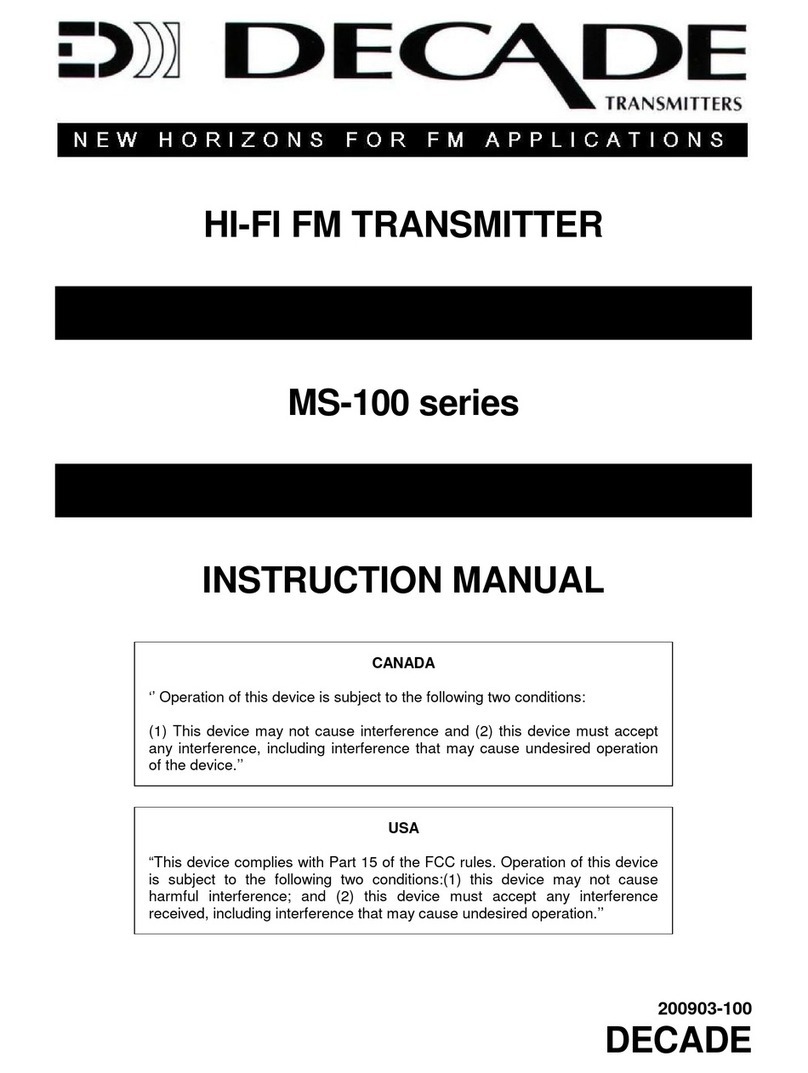
Decade
Decade MS-100 series instruction manual
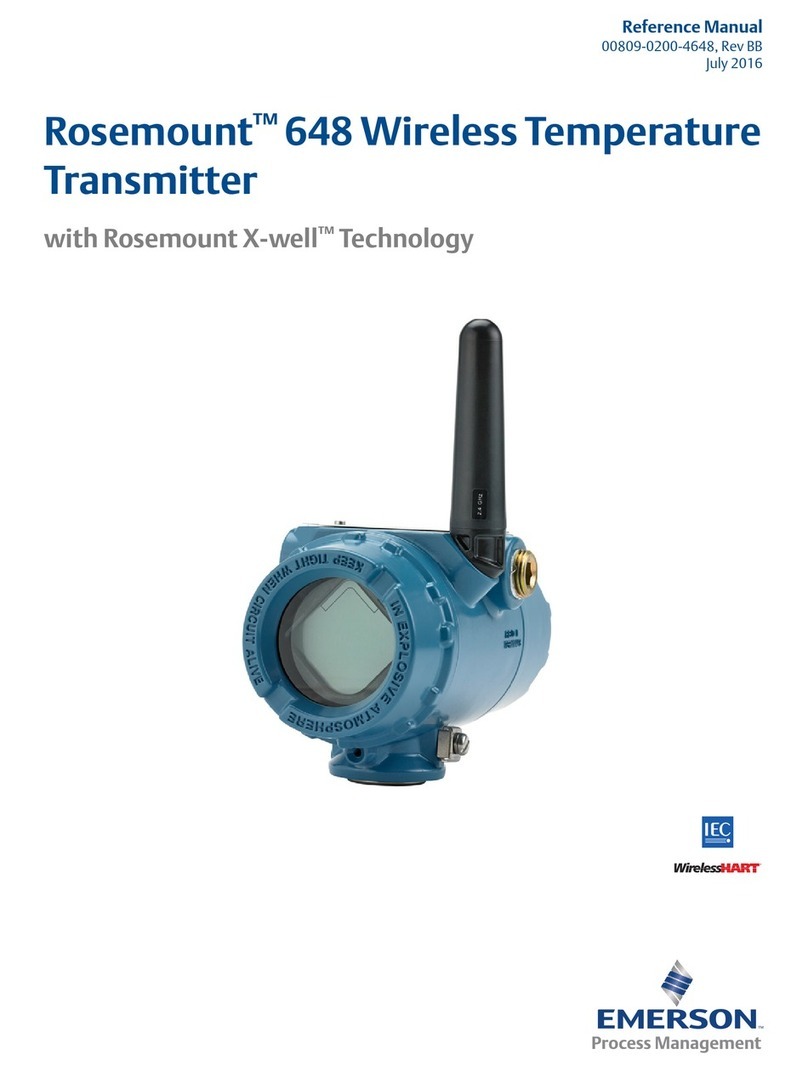
Emerson
Emerson Rosemount X-well 648 Reference manual
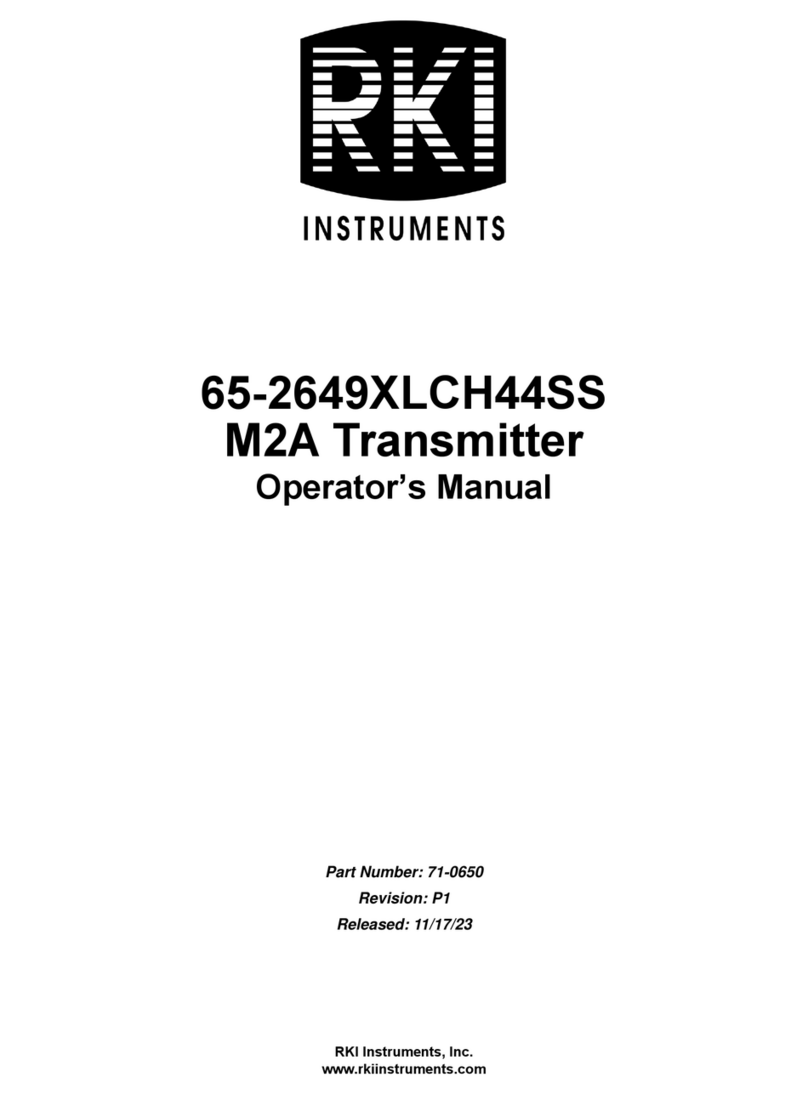
RKI Instruments
RKI Instruments 65-2649XLCH44SS Operator's manual
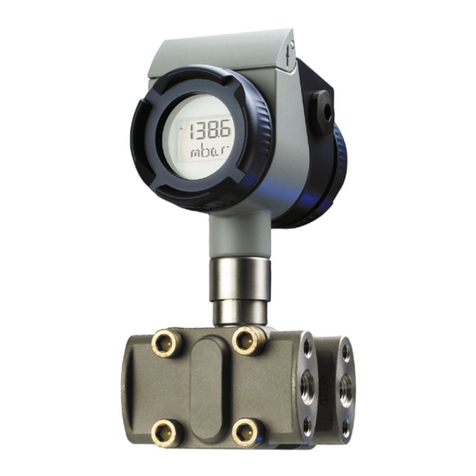
JUMO
JUMO dTRANS p02 DELTA operating instructions
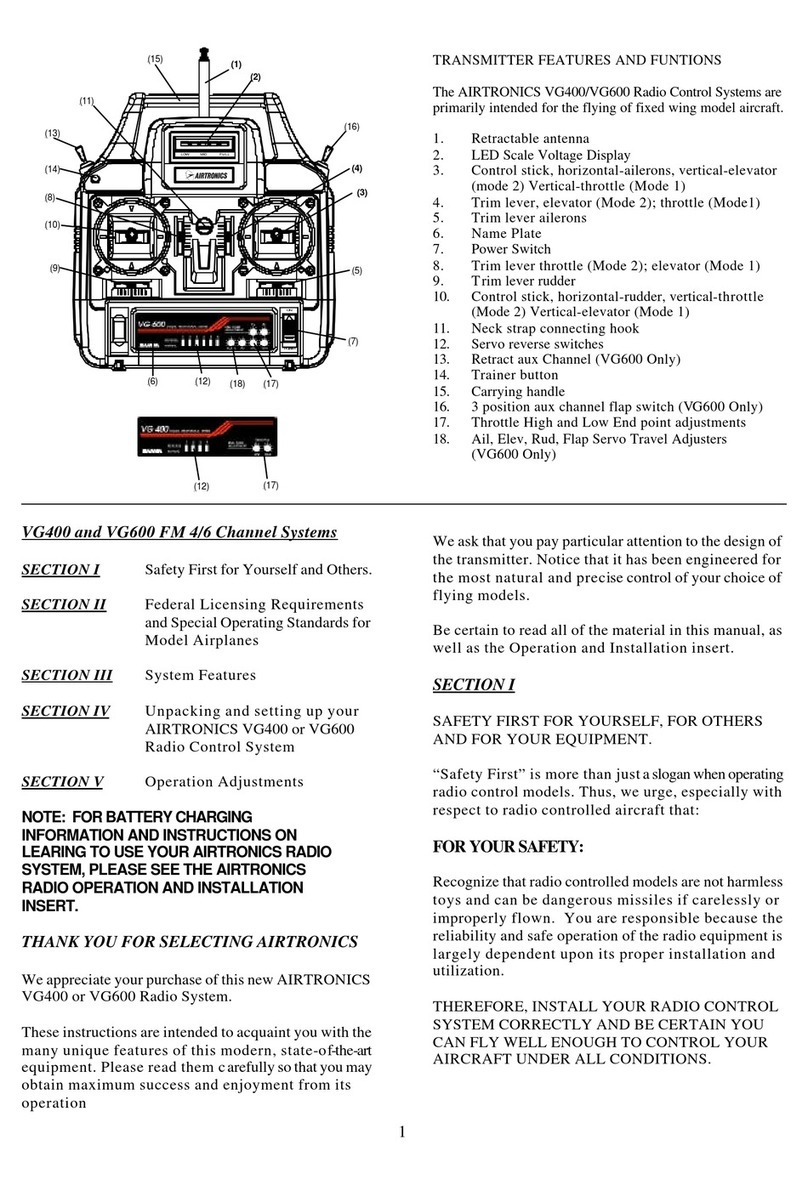
AIRTRONICS
AIRTRONICS VG600 instruction manual