Midland A-718C Series Instruction manual

Document Number: A-718C, Revision # 1
Issue Date: March 9, 2017
Page 1 of 36
7733 Gross Point Road • Skokie, IL 60077 • (847) 677-0333 • Fax (847) 677-0138 • www.midlandmfg.com
1" Angle Valves
A-718C Series
Installation, Operation & Maintenance Manual

Doc. #: A-718C, Rev. 1
Page 2 of 36
Table of Contents
1.0 Introduction ................................................................................................................................... 3
1.1 Technical Specifications ............................................................................................................ 3
1.2 Torque Values for Bolts ............................................................................................................. 4
1.3 Valve Perspectives.................................................................................................................... 5
1.4 Pre-Installation Regulations / Requirements.............................................................................. 7
2.0 Valve Installation ........................................................................................................................... 9
2.1 Preliminary Considerations ....................................................................................................... 9
2.2 Installation Procedure ............................................................................................................... 9
3.0 Operating Instructions ................................................................................................................. 12
3.1 Valve Operation Notes and Precautions .................................................................................. 12
4.0 Maintenance Instructions ............................................................................................................ 13
4.1 Prior to Maintenance Tasks Performed ................................................................................... 13
5.0 Valve Disassembly ...................................................................................................................... 14
6.0 Valve Inspection & Replacement of Parts ................................................................................... 20
6.1 Inspection & Replacement Procedure ..................................................................................... 20
6.2 Special Inspection Considerations .......................................................................................... 23
7.0 Cleaning...................................................................................................................................... 24
8.0 Valve Reassembly ...................................................................................................................... 25
9.0 Valve Testing Procedure ............................................................................................................. 35
9.1 Testing Procedure ................................................................................................................... 35
9.2 Post-Test Procedures ............................................................................................................. 35
10.0 Warranty ................................................................................................................................... 36

Doc. #: A-718C, Rev. 1
Page 3 of 36
1.0 Introduction
The A-718C Series 1" angle valves are top loading transfer valves with a unique seat design that permits self-
draining and ease of maintenance and repair. The energized and adjustable stem packing and soft, self-centering
valve seat eliminates potential leak paths and further increasing the long life and reliability in Chlorine transportation.
Successfully used in Chlorine-transfer applications
Self-centering valve seat permits positive shut-off with lower operating torque
Utilized in the top-loading of pressure cars
1.1 Technical Specifications
Figure 1-1 Valve Specifications

Doc. #: A-718C, Rev. 1
Page 4 of 36
1.2 Torque Values for Bolts
Item #
Description
Material
Torque Value
6
Cap Screws
1/2-13 UNC 2B
Monel
48 ft-lb
CS
38 ft-lb
13
Top Nut
1/2-13 UNC 2B
SS
20 ft-lb
16
Hex Nut
3/8-16 UNC 2A
Monel
22 ft-lb
CS
20 ft-lb
19
Slotted Nut
7/18-20 UNF 2B
Inconel
38 ft-lb
SS
32 ft-lb
Table 1-1 Torque Values for Bolts

Doc. #: A-718C, Rev. 1
Page 5 of 36
1.3 Valve Perspectives
Figure 1-2 Isometric View
Item
Qty.
Part Name
1
1
Hand Wheel
2
1
Stem
3
1
Seal Retainer
4
1
Body
5
1
1" Bonnet
6
3
Cap Screw
7
1
Packing Screw w/Insert
8
1
Packing Insert
9
1
Seat Seal-VV
10
1
Packing Ring Assembly
11
2
O-Ring-Stem
12
2
O-Ring-Flange
13
1
Lock Nut
14
4
Stud
15
4
3/8" Split Lock Washer
16
4
Hex Nut
17
1
O-Ring
18
1
Retaining Pin
19
1
Slotted Nut
20
1
Male Packing Adapter
21
3
1/2" Split Lock Washer
22
1
Outlet Flange Gasket
23
1
Instruction Plate
24
1
Wiper
25
1
Washer
26
1
Name Plate
27
1
Retaining Seal Washer
28
1
Packing Spring
29
1
1" Pipe Plug Assembly
30
1
Outlet Flange
31
1
Seat Insert
32
1
Lower Gasket
33
2
O-Ring-Seat Insert
34
2
Drive Screw
35
1
Placard (Not Shown)

Doc. #: A-718C, Rev. 1
Page 6 of 36
Figure 1-3 Side View and Cross-Sectional View with Callouts

Doc. #: A-718C, Rev. 1
Page 7 of 36
1.4 Pre-Installation Regulations / Requirements
1.4.1 Regulations
Midland Top Transfer, Angle Valves are used in contact with a variety of products, many of which are
hazardous materials. The acceptance and transportation of products are regulated by the DOT and AAR in
the U.S.A., and in Canada by CTC and Transport Canada. Regulations of other governmental bodies must
be complied with for stationary and mobile applications. All personnel should be familiar with and follow these
regulations. Nothing in these instructions is intended to conflict with or supersede these regulations. The
information in this document was gathered from knowledgeable sources, but Midland Manufacturing
Corporation makes no representations or guarantees about its accuracy or completeness and assumes no
liability for this information.
Specifications are subject to engineering updates and may change without notice.
1.4.2 Safety Precautions
Midland valves are used in connection with a variety of products, many of which are hazardous materials and
could cause serious injury or damage.
CAUTION: Toxic Hazard. Always use extreme caution and proper equipment when involved with
hazardous materials. To avoid exposure to toxic or hazardous materials, make sure the tank car is
empty and clean, and that the work area is free of hazardous chemicals before removing or
installing any valve.
1.4.3 Precautions for Mounted-Valve Repair
When performing maintenance on an angle valve that is mounted on a railcar, observe the following
precautions.
oWear protective clothing and equipment suitable for withstanding the materials to which you may
be exposed
oPosition yourself on the upwind side of the valve when possible
oWork with a partner who can help you in the event of an emergency
oFollow approved safety precautions for hazardous or toxic materials

Doc. #: A-718C, Rev. 1
Page 8 of 36
1.4.4 Required Tools
Before arriving at the installation site obtain the required tools and supplies prior to performing the procedures
indicated in this guide.
Recommended Wrenches
SAE
Component
Material
Torque [ft-lb (N·m)]
Item #
1/2” Socket/Wrench
Cap Screws
Monel
48 ft-lb (65 N·m)
6
CS
38 ft-lb (52 N·m)
1/2” Socket/Wrench
Top Nut
SS
20 ft-lb (27 N·m)
13
3/8” Socket/Wrench
Hex Nut
Monel
22 ft-lb (30 N·m)
16
CS
20 ft-lb (27 N·m)
7/16” Socket/Wrench
Slotted Nut
Inconel
38 ft-lb (52 N·m)
19
SS
32 ft-lb (43 N·m)
1-1/16” Crow Feet/Wrench
Packing Nut
Inconel
65 ft-lb (88 N·m)
8
Table 1-2 Required Tools
Other Tools and Supplies
Screwdrivers
Pipe Wrench
Loctite® (or equivalent adhesive)
Lint-free Cloth
Silicone Grease (or equivalent lubrication)
Emery Paper (400 grit, cut in 1" strips)
Torque Wrench
Wire Brush
Table 1-3 Additional Recommended Tools & Supplies

Doc. #: A-718C, Rev. 1
Page 9 of 36
2.0 Valve Installation
2.1 Preliminary Considerations
2.1.1 New valves are tested, adjusted and sealed at Midland. If a new valve has been left in its original packaging,
is undamaged and is not more than six (6) months old, it may be installed on a tank car without retesting or
recalibration. However, if the valve’s shelf life exceeds six (6) months, retesting or recalibration is
recommended.
2.1.2 Prior to installation, ensure that the valve remains clean and that the gasket-sealing surfaces are not
damaged.
2.2 Installation Procedure
2.2.1 Remove the old valve and then insert a soft rubber plug into the tank opening to prevent debris from entering
the tank during cleaning of the valve-mounting groove and studs on the man-way cover plate.
2.2.2 Wire-brush the 3/4” stud threads of the cover plate until clean.
2.2.3 Remove the gasket in the groove of the cover plate. Avoid scratching the metal in the bottom of the groove.
Discard the used gasket.
2.2.4 Examine the sides of the groove to verify that there are no dents or burrs. Since the valve fits tightly in the
groove, any peening of the groove edges may make it difficult to properly fit the valve’s tongue into the
groove. Install a new 1/8"-thick gasket.
2.2.5 Up to this point, the new valve should have been kept in its original shipping container. Cradle the valve in
your arm and unwind the hand wheel (in the “clockwise” direction) to be in the closed position when it is
bolted onto the cover plate. The valve is in the closed position when the stem is all the way up.
2.2.6 Inspect the tongue by running your finger around the edge of the tongue to be sure it is free of nicks, dents
and burrs. The tolerance on the tongue is plus or minus 0.003", so any irregularity on this surface will make
it difficult to fit the tongue cover plate groove. Similarly, the flat surface of the tongue should be free of
imperfections that could cause a gasket leak when the valve is positioned on the cover plate.

Doc. #: A-718C, Rev. 1
Page 10 of 36
2.2.7 Take out the rubber plug from the cover plate opening.
2.2.8 The valve should be “closed” with the stem all the way up. Under no circumstances should a “cheater” or
handle extension be used to close this valve, as over-tightening will damage the valve’s Teflon® seat. The
hand wheel has been purposely weakened to break if excessive force is used.
NOTE: To operate of the valve closed, turn the handle clockwise, the stem will travel all the way
up.
2.2.9 Holding the valve by the bonnet (item 5) lower it slowly onto the studs. Start all four (4) nuts on the studs
while the valve is still held off the cover plate. It may be necessary to lift the valve to make room to insert
nuts adjacent to the outlet flange to allow room to start nuts while the valve is held up. Insert the remaining
nuts and gently move the valve back and forth until the tongue goes down into the groove on the cover
plate. Hand-tighten all four (4) nuts.
2.2.10 Wrench-tighten the nuts a little bit at a time, going alternately from 1 to 3, then 2 to 4. Do not tighten down
too much on one side because this will shift the valve at an angle and may make it impossible to get a tight
gasket seal.
2.2.11 Torque the nuts according to the torque specifications from the gasket manufacture’s recommendations
and to not exceed the torques specified in Section 1.2.
2.2.12 Inspect the valve for leaks according to your company’s procedures for this testing. The primary areas to
check are in the side-port area, the packing gland area, the flange connection between the cover plate, and
the valve and seat. In order to check the seat for leaks on an
installed valve on the tank car, pressure may be applied to the
outlet flange with the valve in the “closed” position. Look for any
pressure decay. Keep in mind that some compensation would
need to be made for pressure changes as temperature changes.
This is recommended in the event that there is no procedure in
place from your company to test the valve’s seat when installed
on a tank car. When closing the valve, hand-tighten. If it does not
seal, remove the valve for repair per Maintenance Instructions in
Section 4.0.
Figure 2-1 Maintenance Checkpoints
Packing
Gland
Area
Seat
Insert
Side-Port
Area

Doc. #: A-718C, Rev. 1
Page 11 of 36
2.2.13 Attached to the bonnet is a tag that indicates operating instructions on one side of the tag and on the reverse
side are blanks to be filled in. The record of the valve’s service experience will be valuable information in
evaluating the valve’s performance. Fill in the appropriate information on this tag.
2.2.14 A placard with an adhesive backing has been provided with each car set of valves. This gives important
operating instructions. The placard should be placed on the underside of the hinged protective housing
cover for the guidance of the personnel using these angle valves.
Figure 2-2 Valve Information Tag
Figure 2-3 Important Operating Instructions

Doc. #: A-718C, Rev. 1
Page 12 of 36
3.0 Operating Instructions
3.1 Valve Operation Notes and Precautions
NOTE: Operation of the valve must conform with all applicable CTC, AAR, DOT specifications
(Parts 173.31, 174.67, etc.), other governmental bodies, and the operating instructions of your
company.
3.1.1 Bear in mind with the Midland angle valve that it will seal completely with much less torque than a metal-
to-metal seated valve. It should close with the same approximate torqueing as with a faucet on a wash
basin. Turn the hand wheel clockwise to close the valve; turn the hand wheel counterclockwise to open the
valve.
CAUTION: Do not apply a “cheater” or handle extension to the hand wheel. Excessive force
will shear through the valve’s Teflon® seal, making it difficult or impossible to close off. If the valve
is leaking at the seat inside the valve and you cannot stop it by a firm closing (by hand) of the hand
wheel, inform your supervisor that the valve is defective and must be removed for reworking.
3.1.2 Examine the pipe plug. Be sure its threads are clean, free from corrosion and not worn or crossed. Also,
examine the threads on the side port to see that they are in good operating condition.
3.1.3 This valve has an adjustable packing gland. Use a 1-1/16" wrench to tighten the packing screw (item 8). In
the event of a packing leak, ensure the packing screw is torqued to a minimum of 30 ft-lb. Tighten the
packing screw in 1/4-turn increments until the leak stops, then turn an additional 1/4 turn.
Unnecessary overtightening of the packing screw will cause excessive frictional drag on the valve stem.
Figure 3-1 Pipe Plug
Figure 3-2 Tighten Packing Screw

Doc. #: A-718C, Rev. 1
Page 13 of 36
4.0 Maintenance Instructions
NOTE: It is important that a periodic retest and preventative maintenance program be
established. The DOT and AAR have set forth a retesting interval that should be considered the
maximum length of time between tests. To assist in scheduling valves for retest, a tag showing
the installation date is attached to the valve. However, there are two measurements that will
indicate if the valve should be repaired sooner, regardless of the scheduled retest date:
1. If there is more than 7/8" between the bottom of the hand wheel and the top of the bonnet in the
closed position, the Teflon® seat has been deformed and needs immediate replacement;
Figure 4-1 Hand Wheel and Bonnet
2. If the top of the packing screw (item 7) is within 3/8" of being flush with the yoke surface, the valve
must be repacked since no adjustment is remaining.
Figure 4-2 Packing Screw
If either condition exists, the valve must be removed and repaired. When the valve is removed from
the cover plate, ensure the valve and stem is protected from damage.
NOTE: It is an AAR requirement (refer to D4.04) that new O-rings be installed when a valve is
retested.
4.1 Prior to Maintenance Tasks Performed
4.1.1 Retesting of Valves in Storage
Midland valves are factory set and sealed. If they have been left in their original shipping containers, are
undamaged, and are no more than six (6) months old; they may be installed without being retested.

Doc. #: A-718C, Rev. 1
Page 14 of 36
5.0 Valve Disassembly
5.1.1 Before valve disassembly, open and close the hand wheel to run the stem (item 2) up and down to ensure
that the stem is neither bent nor binding in the threaded part of the bonnet (item 5). Bent stems must be
straightened to proceed with the disassembly.
5.1.2 Remove the three (3) side-port bolts and lock washers (items 6 and 21, respectively).
Figure 5-1 Test Hand Wheel
and Stem
Figure 5-2 Remove Bolts
Figure 5-3 Remove Bolts and Washers

Doc. #: A-718C, Rev. 1
Page 15 of 36
5.1.3 Remove the outlet flange (item 30). If it is difficult to dislodge, screw a 1" threaded nipple about 10" long
into the port. Move it back and forth gently to loosen the flange and work it off the valve body (item 4).
Figure 5-4 Remove Outlet Flange
5.1.4 Loosen the packing screw (item 7). Take care that any trapped chlorine fumes do not release on the person
disassembling the valve.
5.1.5 Using the hand wheel (item 1), lower the stem (item 2) so that the seal retainer (item 3) is below the sealing
area of body (seat).
Figure 5-7 Seal Retainer Below Body (Seat)
Figure 5-5 Loosen Packing Screw
Figure 5-6 Lower Stem

Doc. #: A-718C, Rev. 1
Page 16 of 36
5.1.6 Rest the end portion of the stem on wood block leveled with body. Make sure there is only 3" between the
body and the wood block. Drift out retaining pin using a standard 1/8" diameter drift. Then unscrew the
retainer slotted nut, remove the retainer assembly, retainer O-ring and retainer seal washer. Cut the Teflon®
seat seal out. Do so with care, as so the metallic retainer surface beneath is not damaged.
5.1.7 Take off the four (4) bonnet nuts and lock washers (items 15 and 16, respectively). The body should then
be able to be disengaged from the bonnet.
Figure 5-8 Remove Retaining Pin
Figure 5-9 Unscrew Slotted Nut
Figure 5-10 Remove Retainer
Figure 5-11 Remove Nuts and Washers
Figure 5-12 Lift Bonnet from Body

Doc. #: A-718C, Rev. 1
Page 17 of 36
5.1.7.1 At this point, remove the seat insert (item 31) from the body
(item 4). The seat insert will be held in place by pressure exerted
by the two (2) O-rings (item 33). One possible option to assist
in the removal of the seat insert is by placing a circular piece of
hardwood or plastic on top of the seat insert on the inside of the
body through the outlet hole. Once this block of wood or plastic
is in place, insert a 3/4" diameter plastic or aluminum rod
through the top of the body until it contact the block of
wood/plastic sitting inside the body, resting against the seat
insert. Once contact is made, using a hammer or mallet, lightly
tap the top portion of the rod until the insert is pushed out of the
body. Handle the insert with care, as this is where the crowned
seat is located.
ATTENTION: Do not use a steel block to assist in the
removal of the seat insert as it might nick or damage the top surface of the insert. Additionally,
ensure that the body assembly is supported by the body flange outer edges, as so when the insert
is being pushed out it can come out easily with its path being obstructed.
ATTENTION: The seat insert is not threaded into the body; it is held in place only by the
compressive force of two (2) O-rings. Do not place the bottom of the insert in a vise to assist in
removing it as it may deform the tongue and gasket surfaces, which are machined to a close
tolerance to fit into the groove in the cover plate.
5.1.8 Use a 1-1/16" open-end wrench to unscrew the packing screw (see Figure 5-5). Then remove the hand
wheel nut and washer (items 13 and 25, respectively). Using the hand wheel, screw the stem down through
the bonnet as far as it can go. It should be possible, gripping by hand on the retainer end of the stem, to
screw it all the way out of the bonnet. If it binds on the last threads, put the retainer end of the stem into the
vise, gripping it lightly and proceed to back the bonnet off from the stem.
Figure 5-14 Remove Nut and Washer
Figure 5-15 Lower the Stem
Figure 5-13 Remove Seat Insert

Doc. #: A-718C, Rev. 1
Page 18 of 36
If the packing (item 10) remains in the body, a hook-shaped tool will dislodge it, as well as the male adapter
(item 20) , wave spring (item 28) and the two (2) stem O-rings in the body (item 11). The hook-shaped tool
can be obtained from Midland (P/N: 712-27-CS). This tool should also be used to remove the stem O-rings
(item 11), the outlet O-rings (item 12) and insert O-rings (item 33).
5.1.9 The seat surface of the insert is
very critical and must be examined carefully. The crown of the seat has a full radius
Figure 5-18 Remove Bonnet/
Stem from Body
Figure 5-16 Dislodge Packing, Male Adapter,
Spring and O-rings
Figure 5-17 Packing, Male
Adapter, Spring and O-rings
Table 5-19 Exploded
View
Item 10
Item 20
Item 18
Item 28
Item(s) 11

Doc. #: A-718C, Rev. 1
Page 19 of 36
(approximately 1/16"). Run your fingernail around the crown to be sure it is free of any nicks, scratches or
pits. Also, any chatter or tool marks on the seat crown should removed. The overall height of the crown
should not be less than 7/32". If the tongue needs to be re-dressed, the tongue’s dimensions are 4.745 ±
0.005” ID by 4.005 ± 0.003” OD. If tolerances are exceeded or the condition is questionable, do not take a
chance on it; replace with a new part.
5.1.10 Inspect the retainer assembly [retaining pin (item 18), retaining nut (item 19), seal retainer assembly and
retaining washer (item 27)] that was removed in Step 5.1.7. Inspect O-ring and seal seat for any sign of
degradation; replace with new parts.
Figure 5-20 Inspect Seat Surface
Figure 5-22 Inspect Seat Seal
Figure 5-23 Retainer, Seal, Washer, Pin and Nut
Figure 5-24 Exploded View
Figure 5-21 Exploded View
Inspect
Thoroughly
Item 19
Item 17
Item 27
Item 9
Item 3
Item 18

Doc. #: A-718C, Rev. 1
Page 20 of 36
6.0 Valve Inspection & Replacement of Parts
Follow the guidelines in this section for inspecting the condition of valve components after disassembly. In some
instances a component can be properly evaluated for damage or cracks only with the use of specialized techniques,
such as dye-penetration or magnetic-particle testing, according to a qualified procedure by certified trained
personnel. Such testing is indicated within this document where mandatory.
Additionally, specific inspections must be performed during and after reassembly of the valve to ensure proper and
reliable operation.
ATTENTION: The Teflon® seat seal, packing, gaskets and O-rings should be replaced periodically
based upon experience. All replacement parts must be obtained from Midland Manufacturing Corp.
No remachinging of any parts is permitted, excepted where noted herein. By not observing these
prohibitions that purchaser assumes full repsonsibility and liability for the proper functioning of the
valves.
CAUTION: O-Ring Degradation. O-rings develop micro cracks, can swell or shrink, and become
harder or softer with age and chemical exposure. An O-ring that fits loosely in the cap, or can only
be pushed into the O-ring retainer with difficulty, is quite likely not the correct size. Many of
Midland’s O-rings are made on special molds to non-standard sizes and are obtainable only from
Midland.
CAUTION: Defective Parts. If any parts appear defective, it is recommended they be replaced, or
consult with Midland for recommended repair techniques when applicable.
6.1 Inspection & Replacement Procedure
6.1.1 Hand Wheel (item 5). The part is designed to fail when the stem is over-torqued. The metal around the
square fragments. If this metal is cracked in the corners or broken off, the hand wheel must be replace.
Figure 6-1 Hand Wheel
Table of contents
Other Midland Control Unit manuals

Midland
Midland A-1477 Series Instruction manual
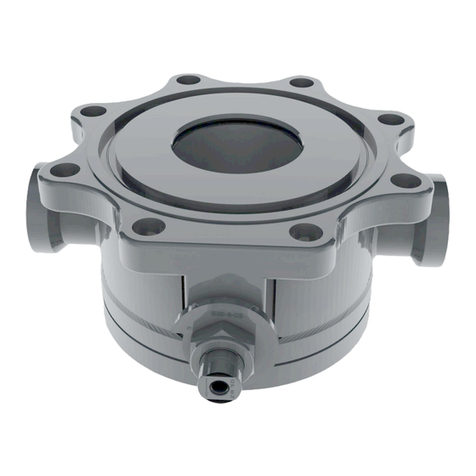
Midland
Midland A-520 Series Instruction manual
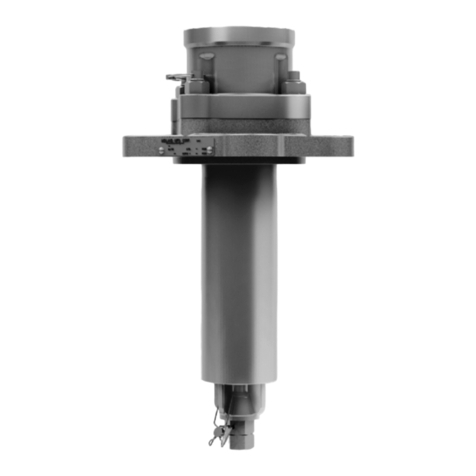
Midland
Midland A-1075 Instruction manual
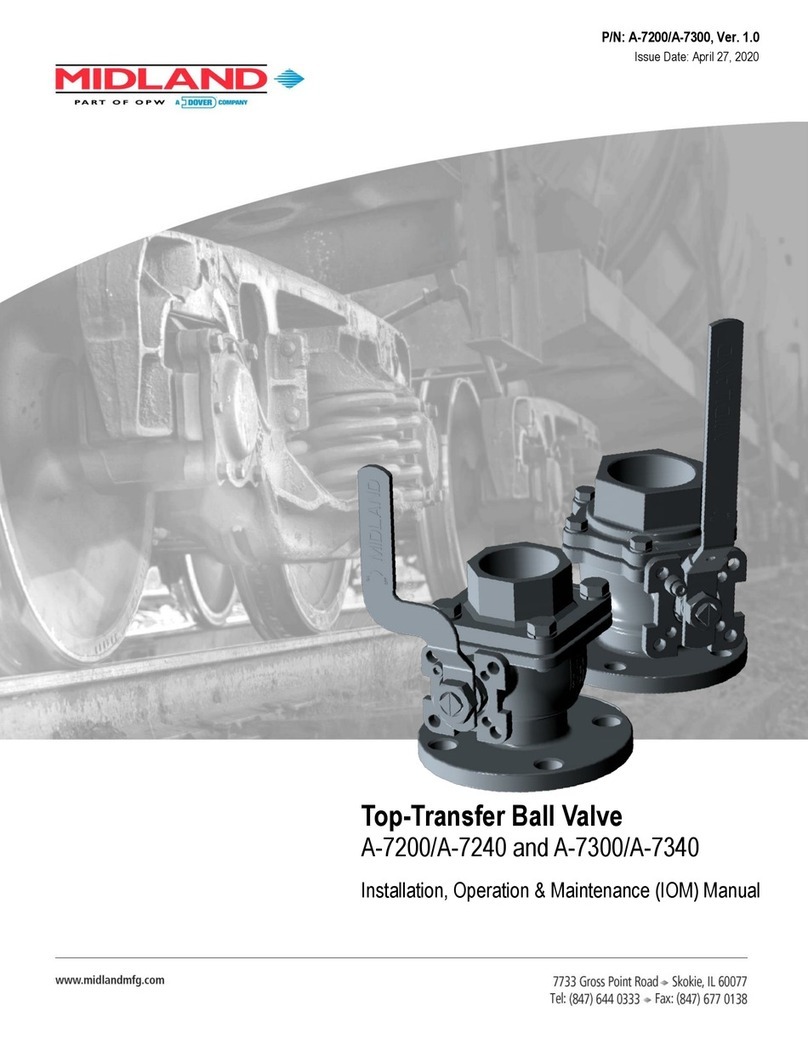
Midland
Midland A-7200 Instruction manual
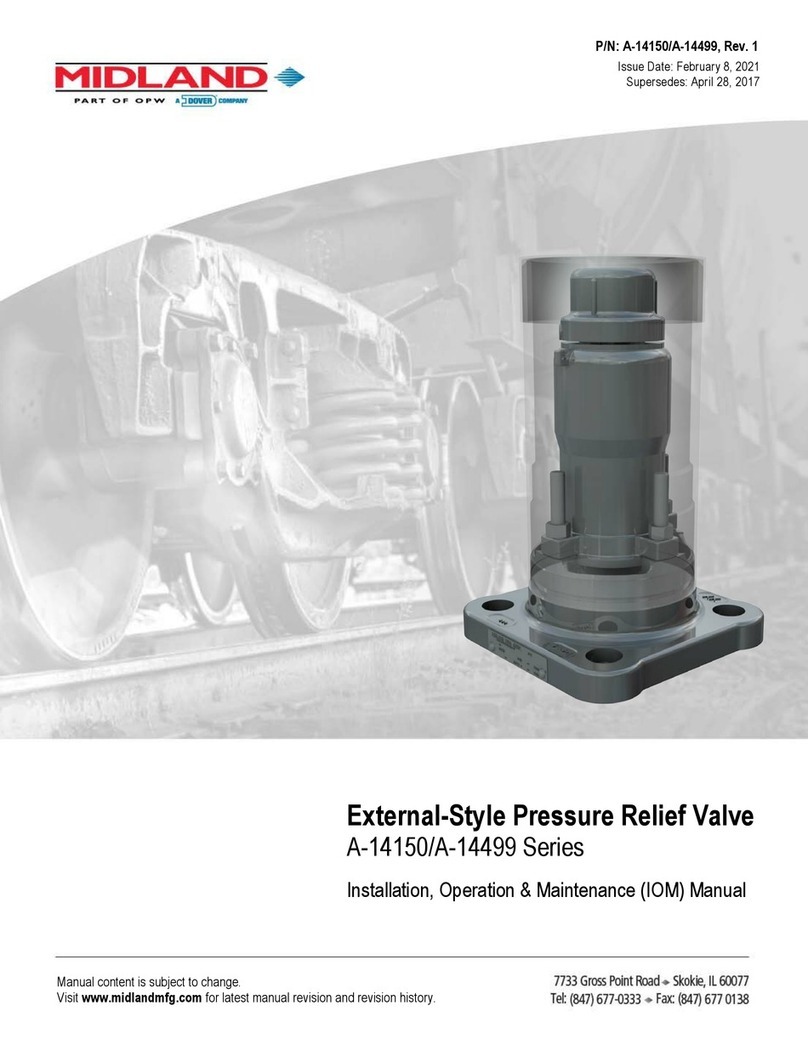
Midland
Midland A-14150 Series Owner's manual
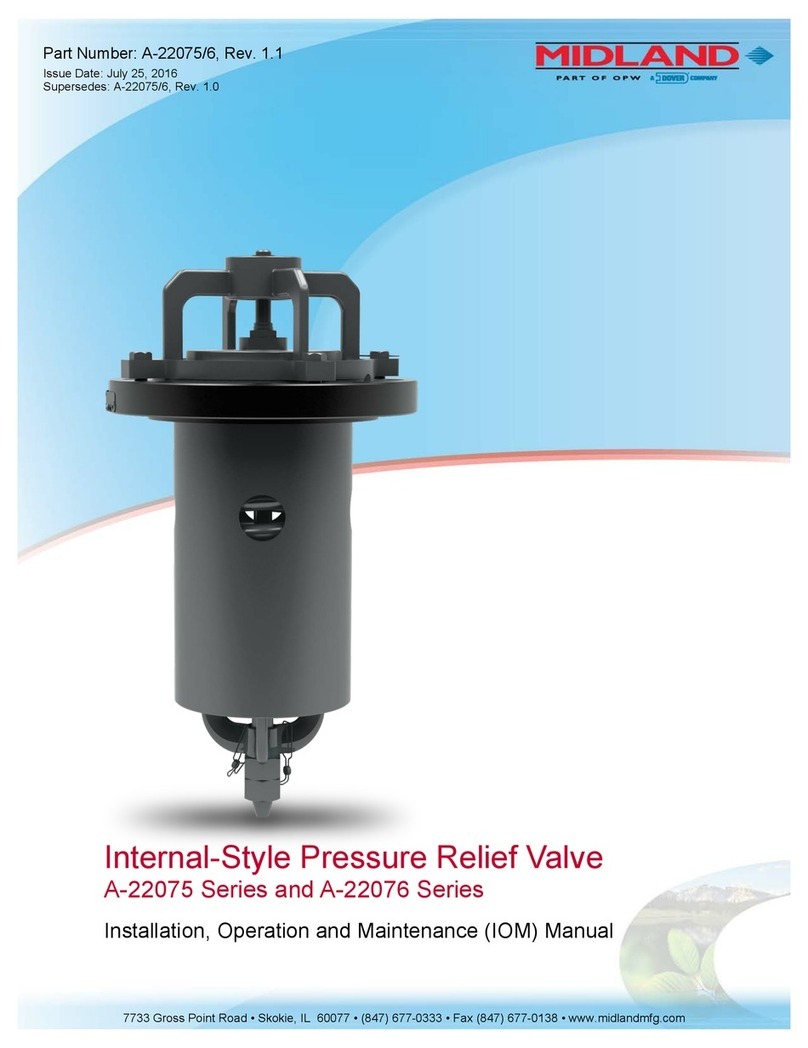
Midland
Midland A-22075 Series User manual
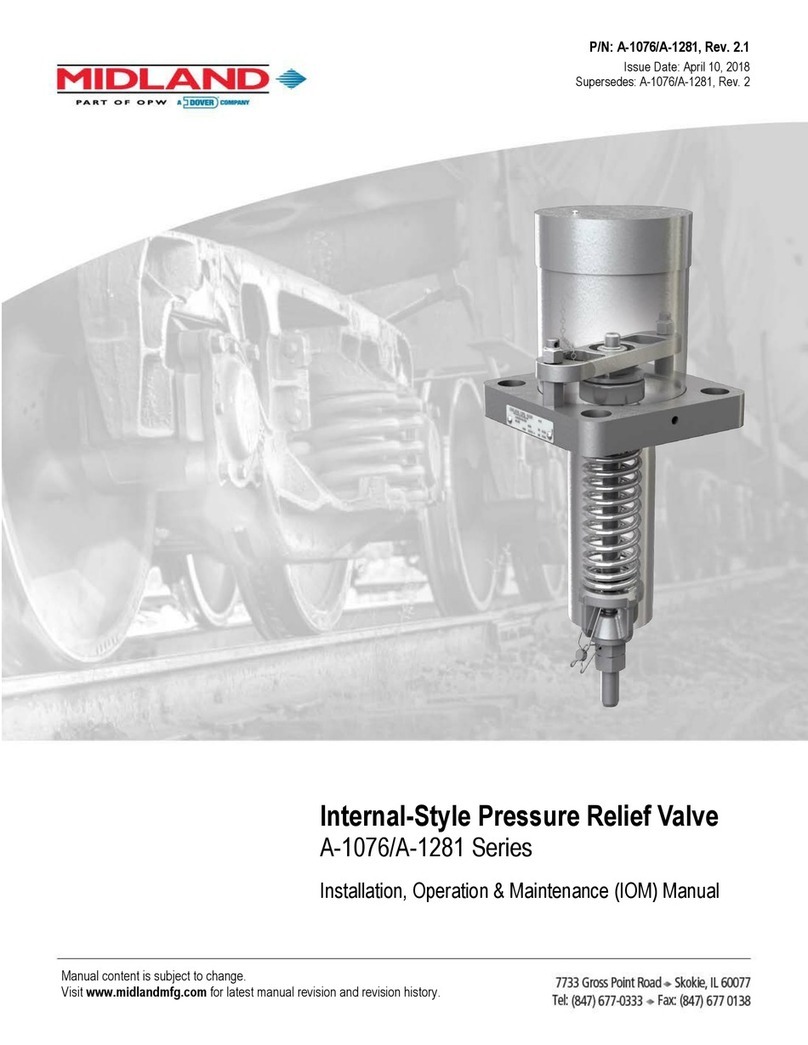
Midland
Midland A-1076 Series Instruction manual
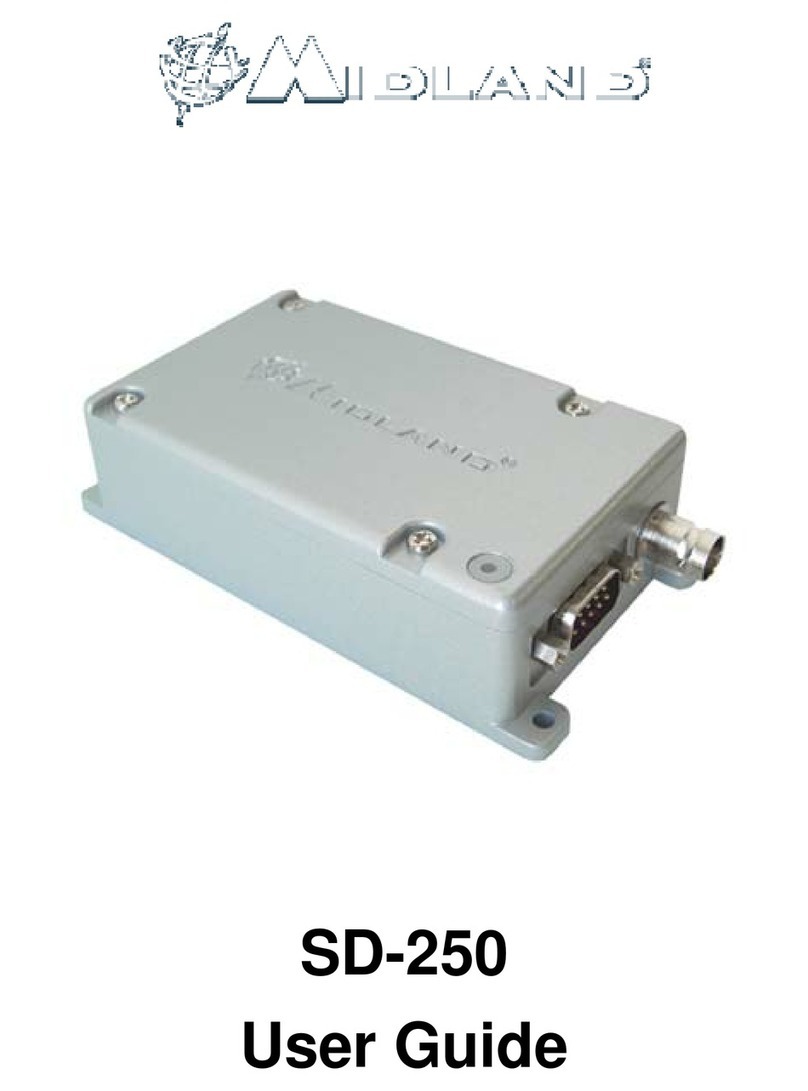
Midland
Midland SD-250 User manual
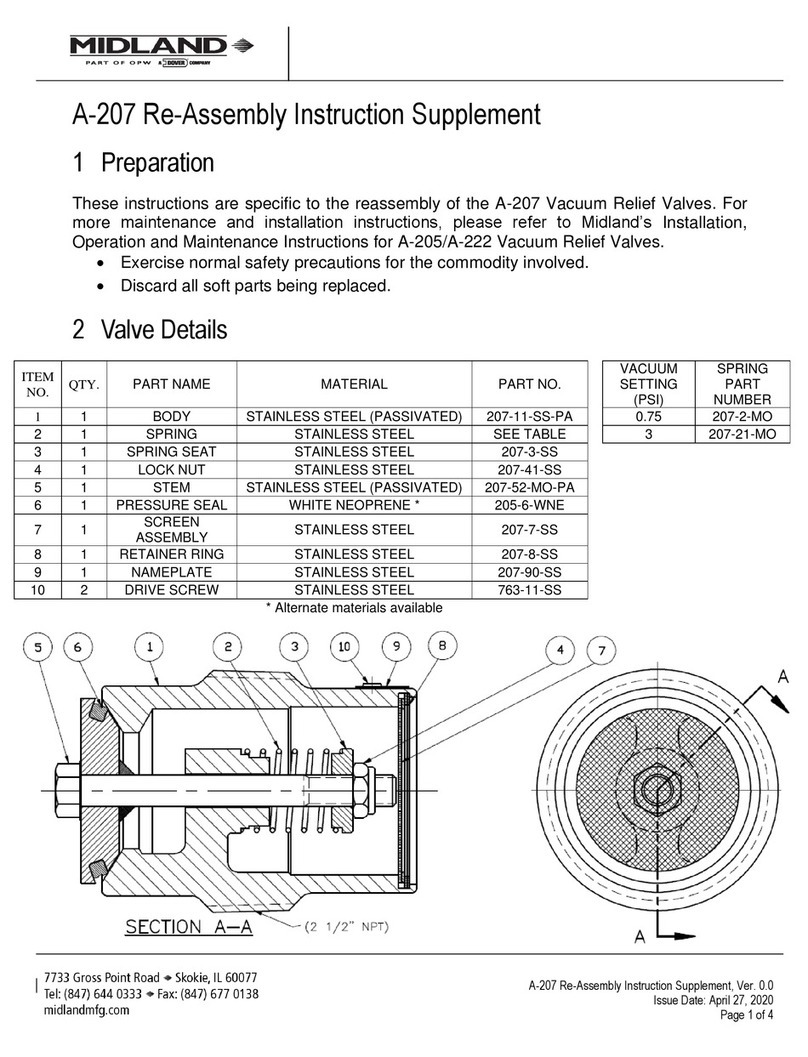
Midland
Midland A-207 Installation instructions