Miller ICE-12C User manual

OWNER’S MANUAL
©2007 MILLER Electric Mfg. Co.
OM-1593 176 877T
Use above FORM number when ordering extra manuals.
2007−08
ICE-12C, ICE-25C, ICE-25CX, ICE-27C, ICE-27T
ICE-40C, ICE-50C, ICE-50CM, ICE-55C, ICE-55CM, ICE-80C, ICE-80CM,
ICE-80CX, ICE-80CXM, ICE-80T, ICE-80TM, ICE-100T, And ICE-100TM Torches
1. Specifications
Air-cooledtorches for plasma arc cutting (PAC)
12 A model: 12 A at 35% duty cycle;
25 A model: 25 A at 35% duty cycle;
27 A model: 27 A at 35% duty cycle;
40 A model: 40 A at 50% duty cycle;
50 A models: 50 A at 60% duty cycle;
55 A model: 55 A at 60% duty cycle;
80 A model: 80 A at 50% duty cycle
100 A model: 100 A at 80% duty cycle
12 A model equipped with 20 ft (6.1 m) cable
25 A model equipped with 15 ft (4.6 m) cable; available with optional 25 ft (7.6 m) cable
27 A model equipped with 20 ft (6.1 m) cable;
40 A model equipped with 25 ft (7.6m) cable; available with optional 50 ft (15.2 m) cable
50 A model equipped with 25 ft (7.6 m) cable; available with optional 50 ft (15.2 m) cable
55 A model equipped with 25 ft (7.6 m) cable; available with optional 50 ft (15.2 m) cable
80 A model equipped with 25 ft (7.6 m) cable; available with optional 50 ft (15.2 m) cable
100 A model equipped with 25 ft (7.6 m) cable; available with optional 50 ft (15.2 m) cable
Use air or nitrogen plasma gas:
12 A model: 1 CFM (28.3 L/min) at 40 PSI (276 kPa);
25 A model: 4.5 CFM (129 L/min) at 60 PSI (414 kPa);
27 A model : 4.5 CFM (129 L/min) at 60 PSI (414 kPa);
40 A model: 6 CFM (170 L/min) at 75 PSI (517 kPa);
50 A model: 5.3 CFM (152 L/min) at 70 PSI (482 kPa);
55 A model: 6 CFM (172 L/min) at 70 PSI (482 kPa);
80 A (C, CM, CX, and CXM) model: 7.2 CFM (207 L/min) at 80 PSI (551 kPa)
80 A (T and TM) model: 7.8 CFM (221 L/min) at 70 PSI (482 kPa)
100 A model: 9.2 CFM (260 L/min) at 75 PSI (517 kPa)
Safety interlock devices shut down power source
12 A, 27 A, 40 A, 50 A, 55 A, 80 A and 100 A models have safety trigger guard
Gear rack pitch for 50 A, 55 A, 80 A and 100A machine-held models: 32
Cutting capacity for mild steel:
12 A model − up to 3/16 in (5 mm) at 12 A;
25 A model − up to 3/8 in (10 mm) at 25 A;
27 A model − up to 3/8 in (10 mm) at 27 A;
40 A model − up to 1/2 in (12.7 mm) at 40 A;
50 A model − up to 7/8 in (22 mm) at 50 A;
55 A model - up to 1 in (25.4 mm) at 55 A;
80 A model − up to 1-1/4 in (32 mm) at 80 A
100 A model − up to 1-1/2 in (38 mm) at 100 A

OM-1593 Page 2
2. Safety Symbol Definitions
DANGER! − Indicates a hazardous situation which, if not
avoided, will result in death or serious injury. The possible
hazards are shown in the adjoining symbols or explained
in the text.
Wear safety glasses with side shields.
Indicates a hazardous situation which, if not avoided,
could result in death or serious injury. The possible ha-
zards are shown in the adjoining symbols or explained in
the text.
Cutting processes cause flying pieces of metal and
sparks. Wear a face shield.
NOTICE Indicates statements not related to personal injury.
Indicates special instructions.
Static electricity can damage parts on circuit boards. Put
on grounded wrist strap before touching circuit board.
Beware of electric shock from the cutting torch or wiring.
Touching the cutting torch while in contact with the work
or ground can cause electric shock. Always wear dry
gloves. Keep all panels and covers closed.
Have only trained and qualified persons install, operate,
or service this unit. Call your distributor if you do not un-
derstand the directions. For CUTTING SAFETY and EMF
information, read power source Manual.
Cutting sparks can cause fire or explosion. Move flam-
mables away. Do not cut on closed tanks or barrels −
they can explode. Clean tanks or barrels properly.
Beware of moving parts. Keep guards and panels in
place, covers closed, and hands away from moving parts.
Arc rays can burn eyes and skin − wear face protection
(helmet or face shield) with correct shade of filter, and
cover exposed skin with nonflammable clothing.
Breathing cutting fumes and gases can harm your health.
Cutting requires good ventilation. If ventilation is impossi-
ble, such as when cutting in a confined space, use an
air-supplied respirator.
Hot parts can cause burns. Cutting makes parts very hot
− let them cool before touching. The plasma arc can cause injury. The intense heat of the
arc or pilot arc can cause serious burns. Keep away from
the torch tip when the trigger is pressed. Do not grip ma-
terial near the cutting path.
Allow cooling period. Reduce current or reduce duty cycle
before starting to cut again. Follow rated duty cycle. Prolonged noise from some cutting applications can dam-
age hearing. Use approved ear plugs or ear muffs if noise
level is high.
3. Duty Cycle And Overheating
rduty1* 5/95
Duty Cycle is percentage of 10
minutes that unit can cut at rated
loadwithout overheating.
NOTICE − Exceeding duty cycle
can damage power source and
torch and void warranty.
6 Minutes Cutting 4 Minutes Resting
12 Ampere Torch: 35% Duty Cycle At 12 Amperes
25 Ampere Torch: 35% Duty Cycle At 25 Amperes
27 Ampere Torch: 35% Duty Cycle At 27 Amperes
3-1/2 Minutes Cutting 6-1/2 Minutes Resting
50 Ampere Torch: 60% Duty Cycle At 50 Amperes
55 Ampere Torch: 60% Duty Cycle At 55 Amperes
5 Minutes Cutting 5 Minutes Resting
80 Ampere Torch: 50% Duty Cycle At 80 Amperes
40 Ampere Torch: 50% Duty Cycle At 40 Amperes 100 Ampere Torch: 80% Duty Cycle At 100 Amperes
8 Minutes Welding 2 Minutes Resting

OM-1593 Page 3
4. Installing 12 Ampere Torch And Work Cable, And Using Trigger Safety Lock
If torch or work cable needs to be
removed or replaced, proceed as
follows:
!Turn power Off, and
disconnectinput power plug
from receptacle.
Remove wrapper from unit.
Torch Connections
Remove existing torch cable from
unit.
1 StrainRelief
2 Torch Cable
Insert cable through strain relief.
Slide strain relief nut onto torch
cable,but do not tighten.
3 Air Line Connector
Install air line connector onto
compressorfitting.
4 Plug PLG4/Receptacle RC4
Connect PLG4 to receptacle RC4
on circuit board PC1.
5 Female And Male Friction
Terminal RC11/ELECT
WHITE
Connectfemale friction terminal on
end of white leads to RC11/ELECT
WHITE.
6 Female And Male Friction
Terminal RC7/PILOT RED
Connect female friction terminal on
end red leads to RC7/PILOT RED.
Tighten strain relief nut.
Tighten strain relief around cable.
Work Cable Connections
Remove existing work cable from
unit.
7 StrainRelief
.Be sure to allow some work
cable slack inside the unit.
Insert work clamp lead through
strain relief, and install strain relief
into front panel.
8 Work Lead Male Friction
Terminal
Connect work clamp lead to male
friction terminal labeled WORK
LEAD on circuit board PC1. Route
lead along torch lead bundle.
9 Trigger
Tools Needed:
801 423 / Ref. 801 300-B
5/8 in
1
3
78
46
2
4
5
586
Ref. 801 300-B / Ref. 802 464 / 199 088 / 801 545-A
3
2
4
56
9
Trigger Locked Trigger Unlocked

OM-1593 Page 4
5. Installing 25 Ampere Torch And Work Cable
801 423 / Ref. 801 300-B
!Turn Off power source, and
disconnectinput power plug
from receptacle before
installing torch and work
cable.
Remove top and screws holding
frontpanel in place. Without discon-
necting any plugs, move front panel
to allow access.
Torch Connections
1 Strain Relief Clamp
2 Torch Cable
Insert cable through strain relief
clamp.
3 Gas Connector
4 Gas Valve
Install gas connector onto gas
valve.
5 Plug PLG18
6 Safety Control Board PC2
7 Receptacle RC18
Connect PLG18 to RC18. Route
leads along existing lead bundle.
8 Female Friction Terminals
9 Male Friction Terminal
10 Power Control Board PC1
11 Receptacle RC4
Connect female terminals to leads
23 and 24 from RC4 (connect to
eitherlead). Connect male terminal
to lead 25 from RC4. Route leads
as shown.
Work Cable Connections
12 Strain Relief Clamp
Insert work clamp lead through
strain relief clamp.
13 Receptacle RC6
Connectwork clamp lead to lead20
from RC6 (leads not shown). Route
leads along existing lead bundle.
5/8 in
Tools Needed:
1
412
1113
6
710
3
2
5
9
88

OM-1593 Page 5
6. Installing 27 Ampere (ICE-27C) Torch And Work Cable, And Using
Trigger Safety Lock
If torch or work cable needs to be
removed or replaced, proceed as
follows:
!Turn power Off, and
disconnectinput power plug
from receptacle.
Remove wrapper from unit.
Torch Connections
Remove existing torch cable from
unit.
1 StrainRelief
2 Torch Cable
Insert cable through strain relief.
Slide strain relief nut onto torch
cable,but do not tighten.
3 Air Line Connector
Insert air line connector into
solenoidfitting.
4 Plug PLG1/Receptacle RC1
Connect PLG1 from torch to
receptacle RC1 on end of wiring
harness connected to circuit board
PC1.
5 Ring Terminal And Terminal
PILOT
Connectring terminal on end of red
leads to PILOT terminal.
6 Ring Terminal And Terminal
L2−RED
Connect ring terminal on end of
white leads to L2−RED terminal.
Tighten strain relief nut.
Tighten strain relief around cable.
Work Cable Connections
Remove existing work cable from
unit.
7 StrainRelief
.Be sure to allow some work
cable slack inside the unit.
Insert work clamp lead through
strain relief, and install strain relief
into front panel.
8 Work Lead Ring Terminal
Connect ring terminal on end of
work clamp lead to terminal labeled
WORK on circuit board PC1. Route
leadalong torch lead bundle.
9 Trigger
Tools Needed:
Ref. 802 854 / Ref. 802 860 / 200 173-A / 802 877
4
86
3
4
1
2
7
586
5
3
2
4
6
5
1/4 in
Trigger Locked Trigger Unlocked
9

OM-1593 Page 6
7. Installing 27 Ampere (ICE-27T) Torch And Work Cable, And Using
Trigger Safety Lock
Tools Needed:
Ref. 804 506-A / Ref. 802 860 / 802 877
1/4 in
Trigger Locked Trigger Unlocked
9
1
2
78
645
3
3
2
4
6
5
!Check DC bus voltage
according to Owner’s Manual,
and be sure voltage is near
zero before touching any
parts.
If torch or work cable needs to be
removed or replaced, proceed as
follows:
Turn power Off, and disconnect
input power plug from receptacle.
Remove wrapper from unit (see
Owner’s Manual).
Torch Connections
Remove existing torch cable from
unit.
1 StrainRelief
Loosen strain relief screw.
2 Torch Cable
Insert cable through strain relief,
but do not tighten.
3 Air Line Connector
Insert air line connector into
solenoidfitting. Pull slightly on torch
to set fitting.
4 Plug PLG1/Receptacle RC1
Connect PLG1 from torch to
receptacle RC1 on end of wiring
harness connected to circuit board
PC1.
5 Ring Terminal And TORCH
WHITE Terminal
Connect ring terminal on end of
white leads to TORCH WHITE
terminal.
6 Ring Terminal And TORCH
RED Terminal
Connectring terminal on end of red
leads to TORCH RED terminal.
Tighten strain relief screw.
Work Cable Connections
Remove existing work cable from
unit.
7 StrainRelief
Loosen strain relief screw.
.Be sure to allow some work
cable slack inside the unit.
Insert work clamp lead through
strain relief, but do not tighten.
8 Work Lead Ring Terminal And
WORK BLACK Terminal
Connect ring terminal on end of
work clamp lead to terminal labeled
WORK BLACK terminal. Route
leadalong torch lead bundle.
Tighten strain relief screw.
Reinstall wrapper.
9 Trigger
Torx 25

OM-1593 Page 7
8. Installing 40 Ampere Torch And Work Cable
If torch or work cable needs to be removed
or replaced, proceed as follows:
!Turn power Off, and disconnect
input power plug from receptacle.
Remove wrapper from unit.
Torch Replacement
1 Strain Relief
2 Torch Cable
Loosen outer strain relief pigtail so that
torch cable can slide freely.
3 Plug PLG1/Receptacle RC1
DisconnectPLG1 from receptacle RC1 on
Controlboard PC1.
4 Plug PLG11/Receptacle RC11
Disconnect PLG11 from receptacle RC11
on Control board PC1.
5 Air Line Connector
Push orange fitting inward toward air
solenoid while pulling connector out of
fitting.
Remove nut, located inside of unit, from
back of strain relief.
Slide torch cable, connector, and plugs
throughnut and out of unit. Retain nut for
use on replacement strain relief.
Insert replacement cable with strain relief
throughopening where old cable and strain
reliefwere removed. Slide strain relief nut
over plugs, connector, and cable. Install nut
ontostrain relief, but do not tighten.
Insert air line connector into solenoid fitting.
Connect PLG1 to RC1 on Control board
PC1.
ConnectPLG11 to RC11 on Control board
PC1.
Tighten strain relief nut.
Tighten strain relief around cable.
Work Cable Replacement
6 Rubber Boot
7 Work Cable Ring Terminal
Slide rubber boot away from ring terminal
connectionon Control board PC1. Remove
hardwaresecuring ring terminal to PC1.
8 Strain Relief
Remove nut, located inside of unit, from
back of strain relief.
Slidework cable through nut and out of unit.
Retain nut for use on replacement strain
relief.
Sliderubber boot over ring terminal and off
of work cable. Retain rubber boot for use on
replacementwork cable.
.Be sure to allow some work cable
slack inside the unit.
Insert replacement cable with strain relief
throughopening where old cable and strain
reliefwere removed. Slide strain relief nut
over ring terminal and cable. Install nut onto
strain relief, but do not tighten.
Routecable along bottom of unit and up to
PC1.
Slide rubber boot over ring terminal and
ontowork clamp lead. Connect work cable
ring terminal to terminal labeled WORK on
circuit board PC1. Torque to 35 in lb
(4 N⋅m). Slide boot over connection.
Tighten strain relief nut.
Tighten strain relief around cable.
Tools Needed:
803 386 / 803 385
5
4
1
2
6
37
5
2
4
3
5/16, 3/8 in
8

OM-1593 Page 8
9. Installing 50 Ampere, 55 Ampere or 80 Ampere Torch And Using Trigger Safety Lock
801 395-A / 801 545-A
!Turn Off power source, and
disconnectinput power plug
from receptacle before
installingtorch.
1 Power Source
2 Torch Connection Receptacle
3 Plug
4 Threaded Collar
5 Keyway
To connect to receptacle, align
keyway, insert plug, and tighten
threadedcollar.
6 Trigger
3
4
5
1
2
NOTICE − Be sure plug is correctly
aligned before tightening collar to
avoid cross-threading.
6
Trigger Locked Trigger Unlocked
.The 50 ampere torch is shown in the illustrations below.
The procedure for the 55 ampere and 80 ampere
torches is identical.
.The 55 ampere torch can be used on a 50 ampere model
powersource. The 50 ampere torch cannot be used on
a 55 ampere model power source. The 55 ampere pow-
er source has a special torch connection receptacle that
preventsthe 50 ampere torch from being connected.

OM-1593 Page 9
10. Installing Either 80 Ampere Or 100 Ampere T/TM Torch
!Turn off power source and
disconnectinput power.
1 Torch Connector
2 Quick Connect Collar
3 Nipple
4 Receptacle
5 Securing Pin
To connect torch:
Push torch connector onto
receptacleand quick connect until
collar secures nipple.
Rotate securing pin to lock
connector to unit.
To disconnect torch:
Rotate securing pin to unlock
connector from unit.
Push quick connect collar back
towards unit to release nipple, and
pulltorch connector away from unit.
804 055-A
2
13
4
5

OM-1593 Page 10
out bottom of cut.
801 400-A
11. Sequence Of Operation For 12 Ampere Torch
After cutting arc starts, slowly
start moving torch across metal.
Adjust torch speed so
sparks go thru metal and Pause briefly at end of
cut before releasing trigger.
EXAMPLE Of Cutting Operation
Raise trigger lock and press
trigger. Pilot arc starts.
Postflow continues for approx. 12 seconds
after releasing trigger; cutting arc can be in-
stantly restarted during postflow by raising
trigger lock and pressing trigger.
!The pilot arc starts immediately when trigger is pressed.
For shielded cutting, place drag shield on edge
of metal. For non-shielded cutting (non-CE
only), use 1/8 in (3.2 mm) standoff distance
(dragging tip will reduce tip life).
.Moisturefrom the compressor will form in the air line and at
the torch. It will be normal to sometimes see moisture come
out the end of the torch.

OM-1593 Page 11
out bottom of cut.
Ref. 802 878
12. Sequence Of Operation For 27 Ampere Torch
After cutting arc starts, slowly
start moving torch across metal.
Adjust torch speed so
sparks go thru metal and Pause briefly at end of
cut before releasing trigger.
EXAMPLE Of Cutting Operation
Raise trigger lock and press
trigger. Pilot arc starts.
Postflow continues for 20 seconds after
releasing trigger; cutting arc can be instantly
restarted during postflow by raising trigger
lock and pressing trigger.
!The pilot arc starts immediately when trigger is pressed.
Place tip on work for drag cutting.
.For maximum cutting speed and tip life,
use a standoff distance of 1/16 in (1.6
mm) to 1/8 in (3.2 mm). Dragging tip will
reducetip life.

OM-1593 Page 12
out bottom of cut.
161 698-A
13. Sequence Of Operation For 25, 40, 50, 55, 80, And 100 Ampere Torches
Put On Personal
Safety
Equipment
After cutting arc starts, slowly
start moving torch across metal.
Adjust torch speed so
sparks go thru metal and Pause briefly at end of
cut before releasing trigger.
Install &
Connect
Equipment
EXAMPLE Of Cutting Operation
Press trigger. Pilot arc starts.
Postflow continues for approx. 20 to
30 seconds after releasing trigger;
cutting arc can be instantly re-
started during postflow by pressing
trigger.
Check Torch Tip,
Electrode, And
Retaining Cup
Check Gas/Air
Pressure Set
Controls
Begin
Cutting
Turn On
Power Source
!The pilot arc starts immediately when trigger is pressed.
For 25 ampere torch, place tip on
edge of metal.
For 40, 50, 80 and 100 ampere
hand-held torches, place drag
shield on edge of metal, or allow
correct standoff distance −
approximately
1/8 in (3.2 mm).
!Inspectshield cup, tip, and electrode for wear be-
fore cutting or whenever cutting speed has been
significantlyreduced (see Section 17). Do not op-
erate torch without a tip or electrode in place.
NOTICE − Do not clean torch by hitting it against a hard
surface. Hitting hard surfaces can damage torch parts
and stop proper operation.
NOTICE − Having pilot arc turn On and Off repeatedly,
such as during the cutting of chain fence, will shorten tip,
electrode and torch life. Put a continuous piece of sheet
metalunder the fence to prevent pilot arc from cycling On
and Off. Avoid constant starting and restarting of arc.

OM-1593 Page 13
14. Routine Maintenance
!Turn Off power source
and disconnect
input power plug
before maintaining.
.25 ampere torch is shown.
Maintenance schedule for
50 and 80 ampere torches is the same.
n= Check Z= Change ~= Clean l= Replace
* To be done by Factory Authorized Service Agent Reference
Each
Use
Use
nCheck Gas/Air Pressure nTorch Tip, Electrode,
And Shield Cup
Every
Week
Week
nShield Cup Shutdown
System
Every
Every
3
lCracked Parts nGas/Air Hose nTorch Body, Cable
3
Months
nTape Torn Outer
Covering
1 Torch Shield Cup
Turn Power On and loosen shield
cup. If shutdown system works
properly, Ready light on power
source goes off and Cup light com-
es on. If not, turn power Off and
check for proper gas/air pressure,
blocked or leaking hose, or loose
shield cup.
If system works properly, retighten
cup and reset power.
15. Shield Cup Shutdown System
Ref. 801 300-A / Ref. 801 300-A
1
.Power source Power switch must be reset whenever cup shutdown
system is activated. Always turn Off power source when changing or
checking consumables.
.Procedureapplies to all torch models.
1

OM-1593 Page 14
16. Checking/Replacing Retaining Cup, Tip, And Electrode For 12 And 27 Ampere Torch
NOTICE − Overtightening will strip threads. Do not overtighten retaining cup
during assembly. Do not cross-thread parts causing stripping. Use care
duringtorch assembly and parts replacement.
!Inspectshield cup, tip, and electrode for wear before cutting or whenever
cuttingspeed has been significantly reduced. Do not operate torch with-
out a tip or electrode in place. Be sure to use genuine replacement parts.
.A good practice is to replace both the tip and electrode at the same time.
802 465
Turn Off power source.
1 Shield Cup
2 O-Ring
Remove shield cup. Check cup for cracks,
and replace if necessary.
Check O-ring for cracks or worn spots, re-
place shield cup if necessary.
3Tip
4 Opening
Remove tip. Check tip, and replace if open-
ing is deformed or 50% oversize. If inside of
tip is not clean and bright, clean with steel
wool.Be sure to remove any pieces of steel
wool afterwards.
5 Electrode
Check electrode. If center has a pit more
thana 1/16 in (2 mm) deep, remove and re-
place electrode.
6 Swirl Ring
7 O-Ring
Remove swirl ring. Check ring, and replace
if side holes are plugged.
Check O-ring for cracks or worn spots,
replaceswirl ring if necessary.
8 O-Ring
Check O-ring for cracks or worn spots, and
replace if necessary.
Carefullyreassemble parts in reverse order.
Makesure this area is clean of
any debris.
Makesure swirl ring is clean of any
debris and no holes are
obstructed.
!Turn Off power source before checking torch
parts.
New
Worn
New
Worn
5
4
3
6
1
2
7
8
*1/32in (1 mm) — 1/16 in (2 mm)
maximum pit depth depending on
acceptable cut quality.
*Pit
Depth

OM-1593 Page 15
17. Checking/Replacing Retaining Cup, Tip, And Electrode For 25, 40, 50, And 55
Ampere Torches
NOTICE− Overtightening will strip threads. Do not overtighten electrode, tip,
andretaining cup during assembly. Do not cross-thread parts causing strip-
ping.Use care during torch assembly and parts replacement.
!Inspectshield cup, tip, and electrode for wear before cutting or whenever
cuttingspeed has been significantly reduced. Do not operate torch without
a tip or electrode in place. Be sure to use genuine replacement parts.
.A good practice is to replace both the tip and electrode at the same time.
Ref. 801 301 / 801 139 / Ref. 801 396-A / 801 405
Turn Off power source.
1 Drag Shield
2 Retaining Cup
Remove retaining cup. Check retaining cup
for cracks, and replace if necessary.
3Tip
4 Opening
Remove tip. Check tip, and replace if open-
ing is deformed or 50% oversize. If inside of
tip is not clean and bright, clean with steel
wool.Be sure to remove any pieces of steel
wool afterwards.
5 Electrode
Check electrode. If center has a pit more
thana 1/16 in (2 mm) deep, remove and re-
place electrode.
6 Swirl Ring
Remove swirl ring. Check ring, and replace
if side holes are plugged.
7 O-Ring
Check O-rings on torch. If needed, coat with
thin film of silicone lubricant (part no.
169 231). Replace if damaged.
8 Plunger Area
Check this area for any debris or foreign ma-
terial.Clean out if necessary.
Carefullyreassemble parts in reverse order.
For the 25 ampere model, swirl ring must be
installedwith word “front” facing away from
torch body.
6
Makesure this area is clean of
any debris.
New
Worn
New
Worn
2
5
4
3
7
8
The word “front” on swirl ring must
face away from torch body.
Makesure swirl ring is clean of any
debris and no holes are
obstructed.
!Turn Off power source before checking torch parts.
New
Worn
New
Worn
5
43
8
7
6
2
1
25 Ampere Model 50 Ampere and 55 Ampere Models
*1/32 in (1 mm) — 1/16 in (2 mm)
maximum pit depth depending on
acceptable cut quality.
*Pit
Depth
*Pit
Depth

OM-1593 Page 16
18. Checking/Replacing Retaining Cup, Tip, And Electrode For 80 Ampere (C/CM) Torch
NOTICE− Overtightening will strip threads. Do not overtighten electrode, tip,
and retaining cup during assembly. Do not cross-thread parts causing strip-
ping.Use care during torch assembly and parts replacement.
!Inspectshield cup, tip, and electrode for wear before cutting or whenever
cutting speed has been significantly reduced. Do not operate torch with-
out a tip or electrode in place. Be sure to use genuine replacement parts.
.A good practice is to replace both the tip and electrode at the same time.
803 612-A
Turn Off power source.
1 Drag Shield
2 Retaining Cup
Remove retaining cup. Check retaining cup
for cracks, and replace if necessary.
3Tip
4 Opening
Remove tip. Check tip, and replace if open-
ing is deformed or 50% oversize. If inside of
tip is not clean and bright, clean with steel
wool.Be sure to remove any pieces of steel
wool afterwards.
5 Electrode
Check electrode. If center has a pit more
thana 1/16 in (2 mm) deep, remove and re-
place electrode.
6 Swirl Ring
Remove swirl ring. Check ring, and replace
if side holes are plugged.
7 O-Ring
Check O-rings on torch. If needed, coat with
thin film of silicone lubricant (part no.
169 231). Replace if damaged.
8 Torch Head
Check this area for any debris or foreign ma-
terial.Clean out if necessary.
Carefullyreassemble parts in reverse order.
6
Makesure this area is clean of
any debris.
New
Worn
New
Worn 2
5
4
3
7
8
Make sure swirl ring is clean of
any debris and no holes are
obstructed.
!Turn Off power source before checking torch parts.
1
80 ampere model requires
electrode wrench 189 086
*1/32 in (1 mm) — 1/16 in (2 mm)
maximum pit depth depending on
acceptable cut quality. *Pit
Depth

OM-1593 Page 17
19. Checking/Replacing Retaining Cup, Tip, And Electrode For 80 Ampere (CX/CXM/
T/TM, And 100 T/TM) Torch
NOTICE − Overtightening will strip threads. Do not overtighten electrode,
tip, and retaining cup during assembly. Do not cross-thread parts causing
stripping. Use care during torch assembly and parts replacement.
!Inspectshield cup, tip, and electrode for wear before cutting or whenever
cutting speed has been significantly reduced. Do not operate torch with-
out a tip or electrode in place. Be sure to use genuine replacement parts.
.A good practice is to replace both the tip and electrode at the same time.
804 056-A
Turn Off power source.
1 Drag Shield
Check this area for any debris or foreign
material.Clean out if necessary.
2 Retaining Cup
Remove retaining cup. Check retaining cup
for cracks, and replace if necessary.
3Tip
4 Opening
Remove tip. Check tip, and replace if open-
ing is deformed or 50% oversize. If inside of
tip is not clean and bright, clean with steel
wool.Be sure to remove any pieces of steel
wool afterwards.
5 Electrode
Check electrode. If center has a pit more
than a 1/32 in (1 mm) deep, remove and
replaceelectrode.
6 Swirl Ring
Remove swirl ring. Check ring, and replace
if side holes are plugged.
7 O-Ring
Check O-rings on torch. If needed, coat with
thin film of silicone lubricant (part no.
169 231). Replace if damaged.
8 Plunger Area
Check this area for any debris or foreign
material.Clean out if necessary.
Carefullyreassemble parts in reverse order.
Make sure this area is
clean of any debris.
!Turn Off power source before checking torch parts.
New
Worn
New
Worn
5
4
3
8
7
6
2
1
1/32 in
(1 mm)
Pit
Make sure this area is
clean of any debris.

OM-1593 Page 18
20. Troubleshooting For 12 Ampere Torch
Torch travel speed too slow;
increase travel speed (see
Power Source Owner’s
Manual). Clean or replace
torch consumables as
necessary (see Section16).
Be sure work clamp is
securely attached to
workpiece.
Yes
No
Does arc go
on and off
while cutting?
Does arc go out
while cutting?
No
Yes
Be sure work clamp is
securely attached to work-
piece. Make sure drag
shield contacts metal while
cutting. Clean or replace
torch consumables as
necessary (see Section 16).
Do sparks come
out of top of cut;
or cut is not
clean?
No
Yes
Torch travel speed too fast;
reduce travel speed (see
Power Source Owner’s
Manual). Clean or replace
torch consumables as
necessary (see Section 16).
Be sure work clamp is
securely attached to
workpiece.Unit not capable
of cutting metals thicker
than rating (see Section 1).
Is Trouble light
On; unit has no
cuttingoutput?
Yes Check torch shield cup (see
Section15); reset unit
Power switch. *Check torch
and connections inside unit.
See Power Source Owner’s
Manual.
See Power Source Owner’s
Manual.
See Power Source Owner’s
Manual.
No
See Power Source Owner’s
Manual.
*Servicing procedure to be performed
only by authorized Service Station.

OM-1593 Page 19
21. Troubleshooting For 25, 27, 40, 50, 55, 80, And 100 Ampere Torches
Trouble Remedy
Power source Cup trouble light On; no
cuttingoutput. Tighten cup onto torch and reset Power (see Section 15).
Check torch connections on power source. See power source Owner’s Manual.
Sparks come out top of cut, or cut is not
clean. Torch travel speed too fast; reduce travel speed (see Section 13).
Clean or replace worn consumables as necessary (see Section 17).
Metal being cut is too thick; increase output control setting. See power source Owner’s Manual.
Be sure work clamp is securely attached. See power source Owner’s Manual.
Arc goes out while cutting. Make sure torch tip is contacting metal while cutting.
Be sure work clamp is securely attached. See power source Owner’s Manual.
Clean or replace worn consumables as necessary (see Section 17).
Arc goes on and off while cutting. Torch travel speed is too slow; increase travel speed (see Section 13).
Clean or replace worn consumables as necessary (see Section 17).
Be sure work clamp is securely attached. See power source Owner’s Manual.

OM-1593 Page 20
22. Parts Lists
1 183 427 Handle Assy, left and right
w/screws (1)
2 171 248 Pushbutton Switch (1)
3 196 931 Leads, 20ft (1)
4 196 930 Label, ICE-12C (1)
5 196 932 Main Body (1)
6 185 833 Switch Assy w/Spring (1)
190 220 Spring, trigger assy (1)
169 231 Grease, silicone (1)
196 923 Torch, replacement 20ft (1)
Part
No.
Item
No. Description
1
23
1
5
6
4
See Figure 22-2 for additional
consumable parts.
Figure 22-1. Torch, ICE-12C
206 304
206304
Retaining
Cup
197567 Tip
196926 Electrode
196925
Swirl
Ring
196927 O−Ring
196935
Retaining
Cup
196928
Drag
Shield
196929
1/8”(3mm)
stand−off
recommended
Apply silicone
grease(169231)
beforeinstalling.
Turn off power before
checking torch parts.
Check before each
use and hourly
during operation.
CAUTION
FAILURE TO RE−
PLACE WORN TIP
OR ELECTRODE
WILL RUIN TORCH
AND VOID
WARRANTY.
ICE−12C
CONSUMABLES
S
S
Figure 22-2. Consumable Parts For ICE-12C
This manual suits for next models
17
Table of contents
Other Miller Flashlight manuals
Popular Flashlight manuals by other brands
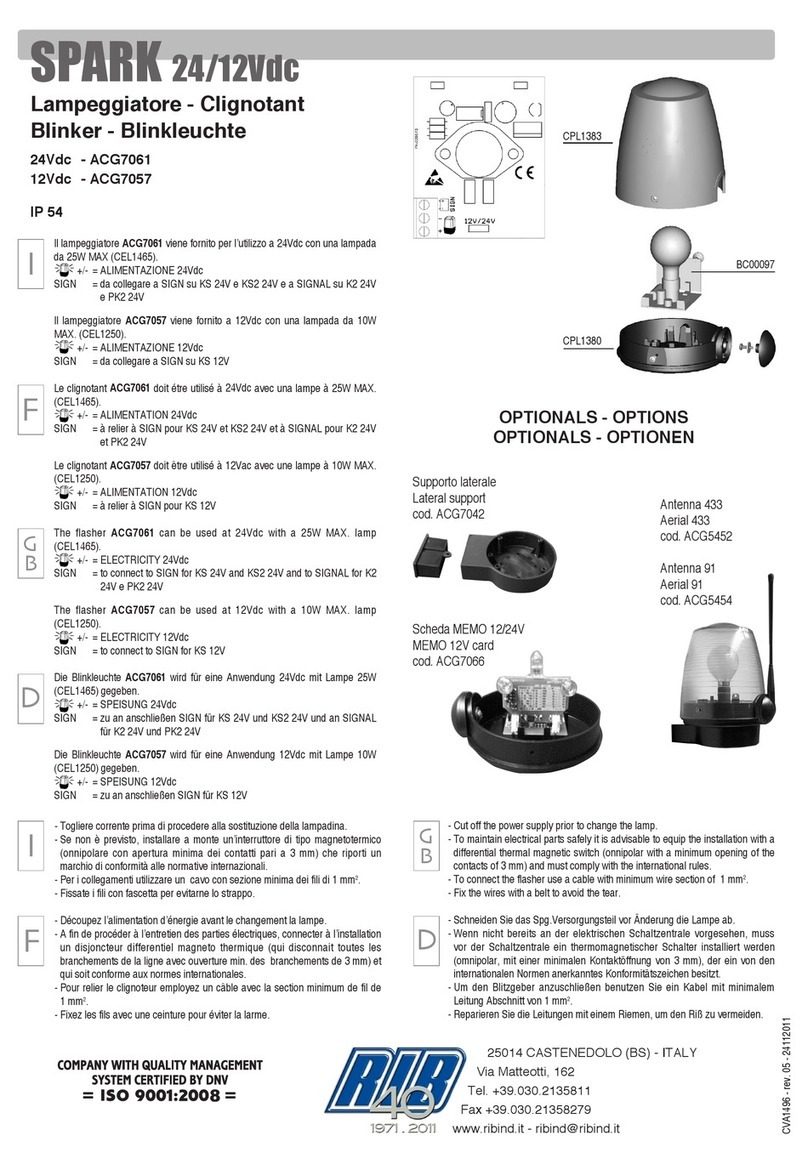
RIB
RIB SPARK ACG7061 quick start guide
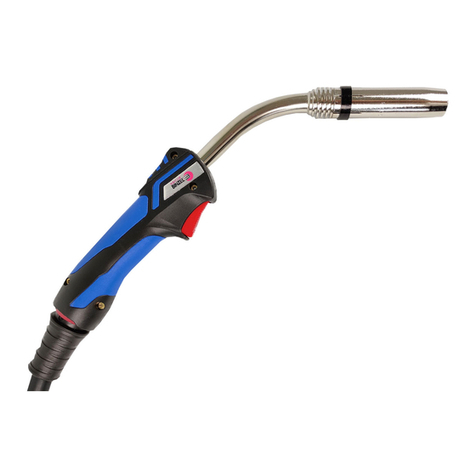
Abicor Binzel
Abicor Binzel MB EVO PRO Series operating instructions

Milwaukee
Milwaukee M18 IL Original instructions
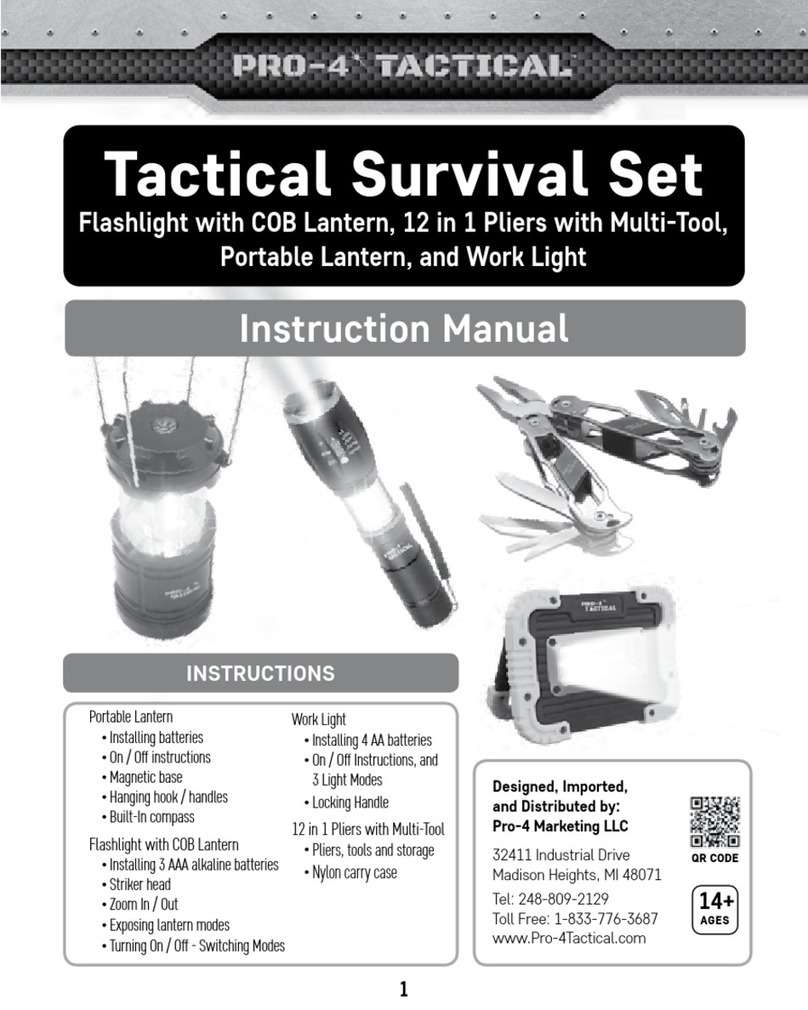
Pro-4 Tactical
Pro-4 Tactical Tactical Survival Set instruction manual
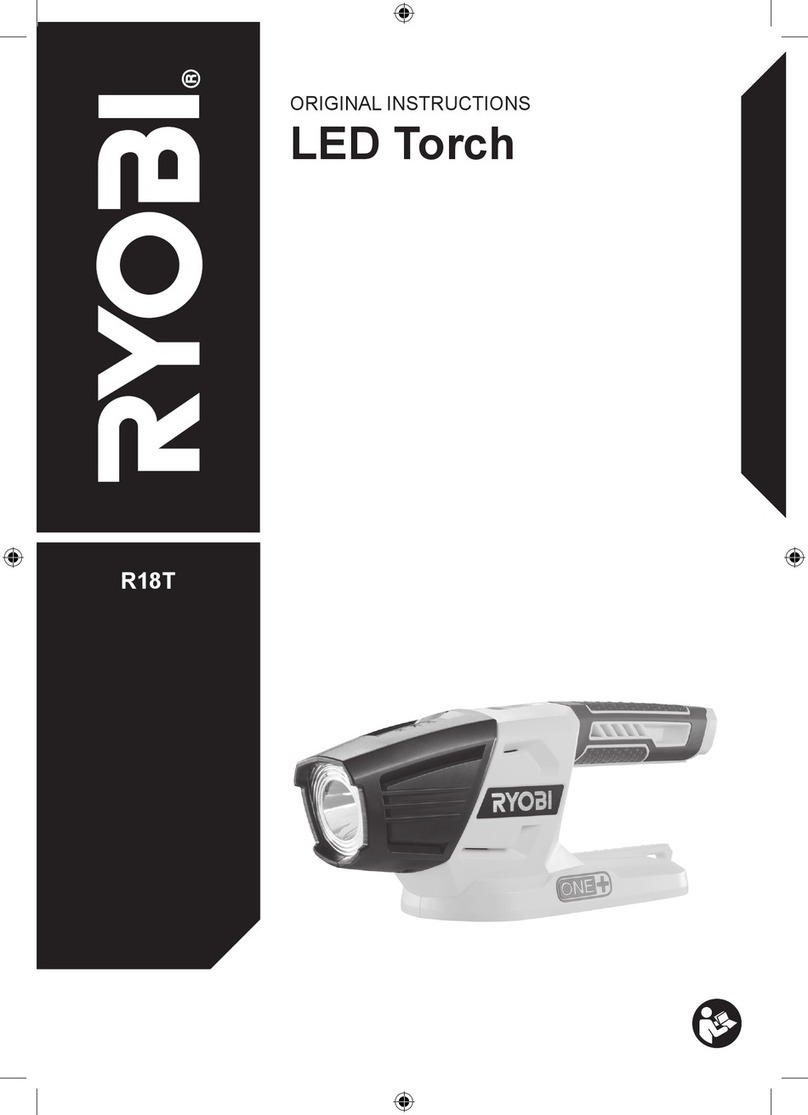
Ryobi
Ryobi R18T Original instructions
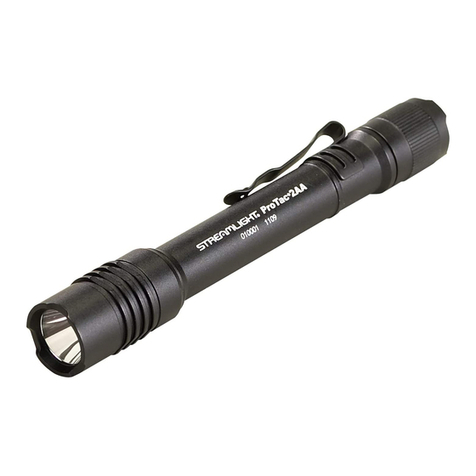
StreamLight
StreamLight PROTAC 2AA quick start guide
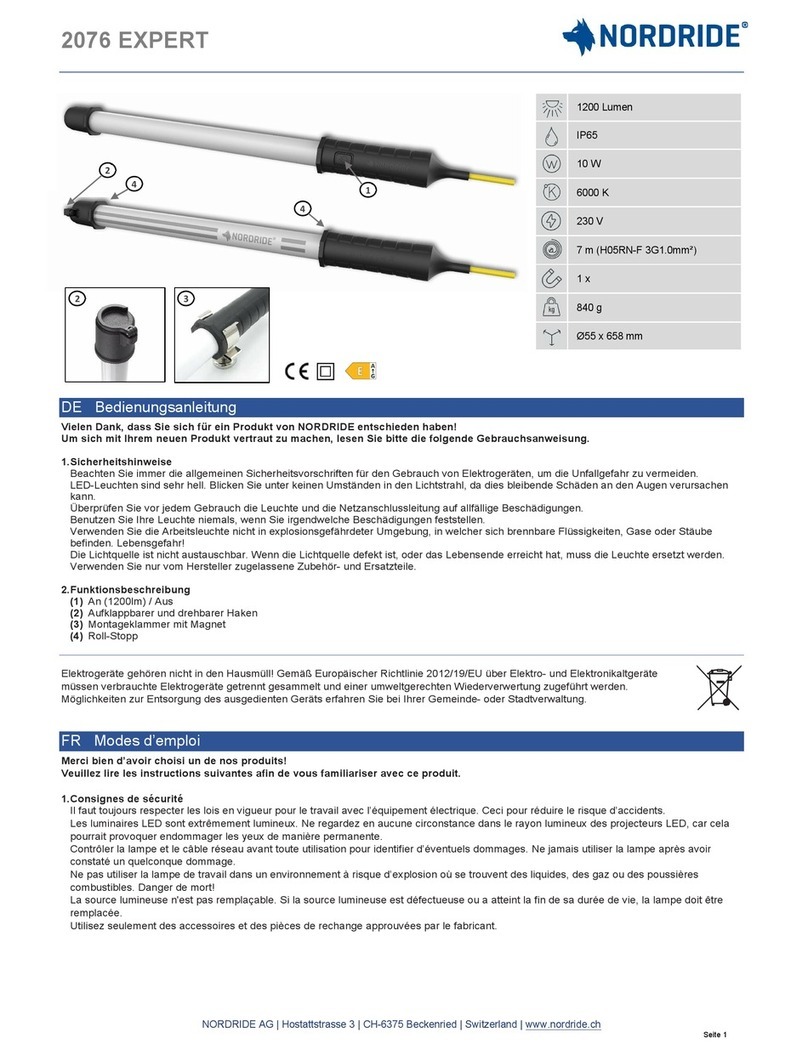
NORDRIDE
NORDRIDE 2076 EXPERT operating instructions
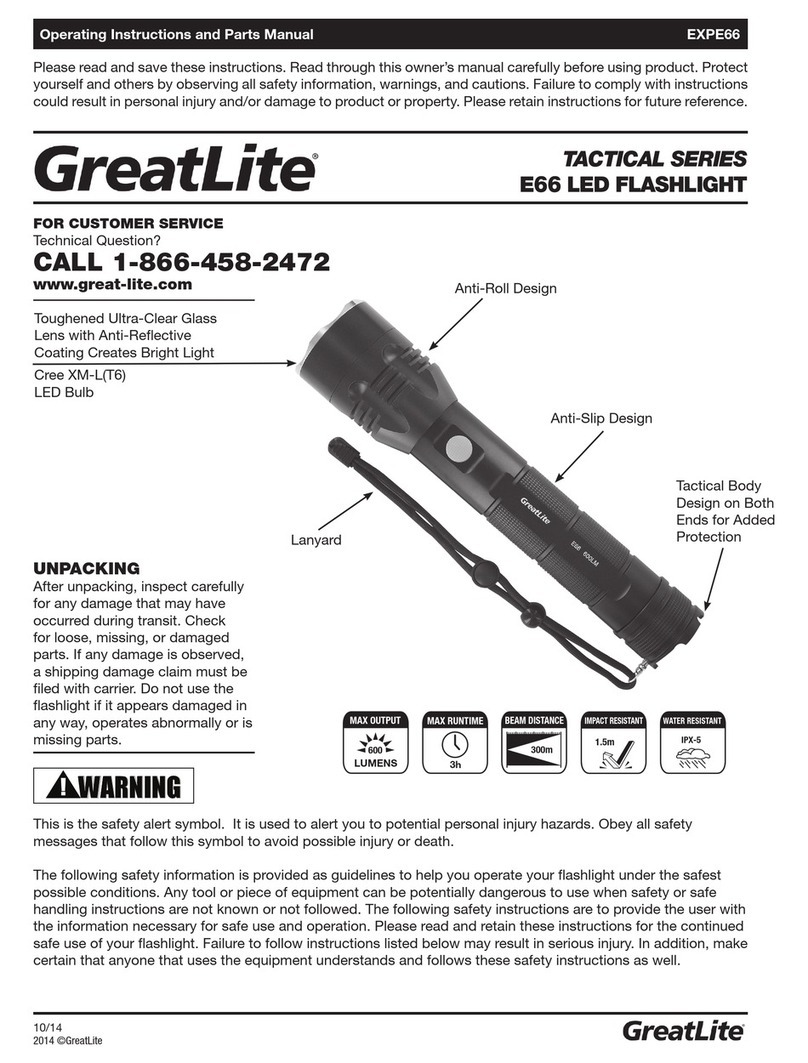
GreatLite
GreatLite Tactical E66 Operating instructions and parts manual

Clas Ohlson
Clas Ohlson 36-3497/18-1080 quick guide

Abicor Binzel
Abicor Binzel ABTIG Little 9 operating instructions
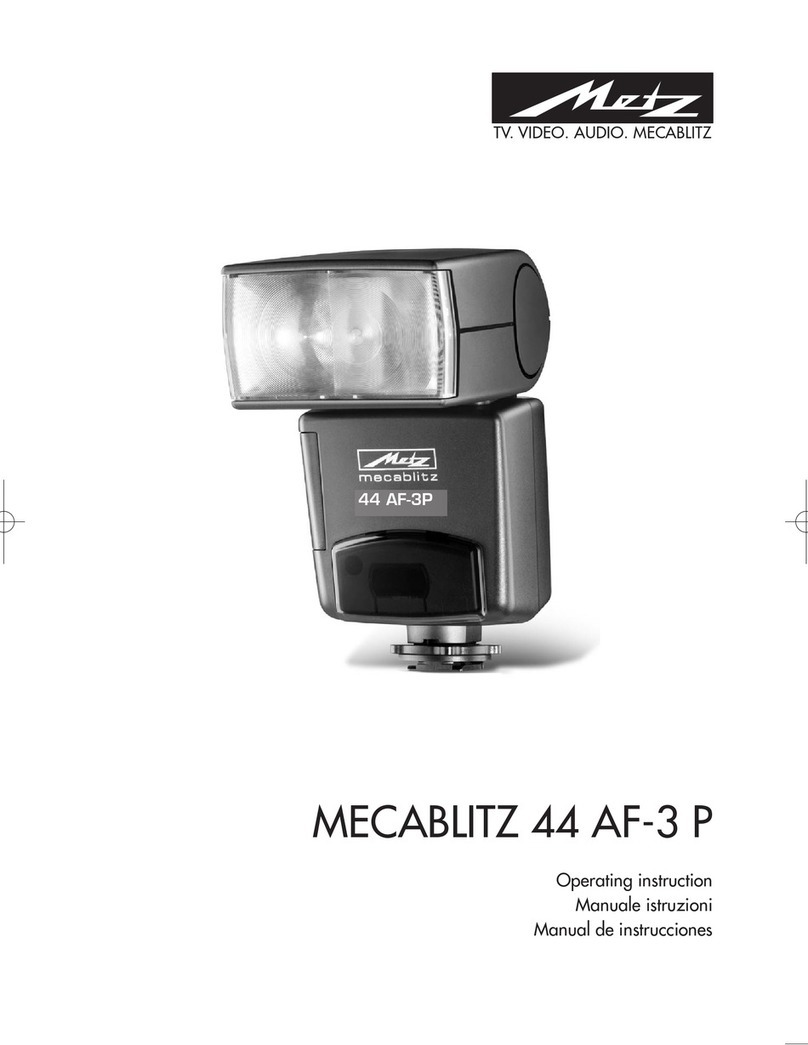
Metz
Metz MECABLITZ 44 AF-3 P Operating instruction
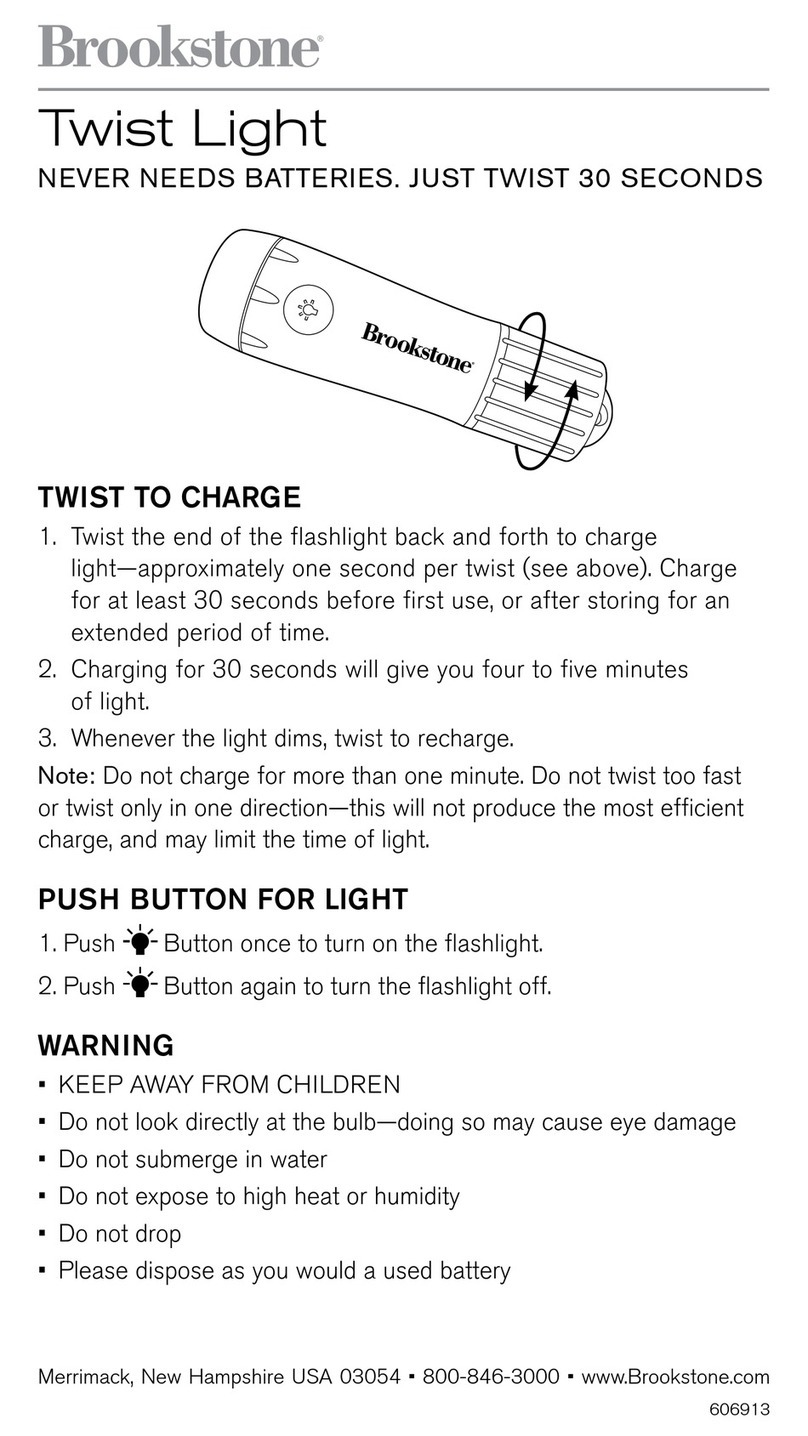
Brookstone
Brookstone Twist Light manual