MIR 500 User manual

User Guide (en)
Date: 12/2020
Revision: v.2.1

MiR500Pallet Lift User Guide (en) 12/2020 - v.2.1 ©Copyright 2018-2020: Mobile Industrial Robots A/S. 2
Copyright and disclaimer
All rights reserved. No parts of this document may be reproduced in any form without the
express written permission of Mobile Industrial Robots A/S (MiR). MiR makes no warranties,
expressed or implied, in respect of this document or its contents. In addition, the contents of
the document are subject to change without prior notice. Every precaution has been taken in
the preparation of this document. Nevertheless, MiR assumes no responsibility for errors or
omissions or any damages resulting from the use of the information contained.
Copyright © 2018-2020 by Mobile Industrial Robots A/S.
Contact the manufacturer:
Mobile Industrial Robots A/S
Emil Neckelmanns Vej 15F
DK-5220 Odense SØ
www.mobile-industrial-robots.com
Phone: +45 20 377 577
Email: support@mir-robots.com
CVR: 35251235

MiR500Pallet Lift User Guide (en) 12/2020 - v.2.1 ©Copyright 2018-2020: Mobile Industrial Robots A/S. 3
Table of contents
1. About this document 8
1.1 Where to find more information 8
1.2 Version history 9
2. Product presentation 12
2.1 Main features of MiR500Pallet Lift 13
2.2 External parts 15
2.3 Internal parts 21
2.4 Manual brake release switch 29
2.5 How MiR Pallet Lift 500 works 29
2.6 MiR Pallet Rack 31
3. Warranty 33
4. Accessing the internal parts 34
4.1 Front compartment 34
4.2 Rear compartment 36
4.3 Side compartments 36
4.4 Top compartments 37
4.5 MiR Pallet Lift 500 38
5. Safety 39
5.1 Safety message types 39
5.2 General safety precautions 40
5.3 Intended use 45
5.4 Users 45
5.5 Foreseeable misuse 46

MiR500Pallet Lift User Guide (en) 12/2020 - v.2.1 ©Copyright 2018-2020: Mobile Industrial Robots A/S. 4
5.6 Residual risks 47
6. Getting started 48
6.1 In the box 48
6.2 Unpacking MiR500Pallet Lift 49
6.3 Connecting the battery 52
6.4 Powering up the robot 53
6.5 Connecting to the robot interface 55
6.6 Driving the robot in Manual mode 56
6.7 Checking the hardware status 59
6.8 Mounting the nameplate 59
6.9 Enable the MiR500Pallet Lift feature 61
6.10 Testing the top module 63
6.11 Shutting down the robot 65
7. Battery and charging 67
7.1 Charging the robot 67
7.2 Disconnecting the battery 68
7.3 Battery storage 68
7.4 Battery disposal 69
8. IT security 70
8.1 Managing users and passwords 70
8.2 Software security patches 70
9. Navigation and control system 72
9.1 System overview 72
9.2 User input 74

MiR500Pallet Lift User Guide (en) 12/2020 - v.2.1 ©Copyright 2018-2020: Mobile Industrial Robots A/S. 5
9.3 Global planner 74
9.4 Local planner 76
9.5 Obstacle detection 77
9.6 Localization 83
9.7 Motor controller and motors 86
9.8 Brakes 86
10. Safety system 88
10.1 System overview 88
10.2 Personnel detection 93
10.3 Overspeed avoidance 98
10.4 Stability 98
10.5 Emergency stop buttons 99
10.6 MiR Pallet Lift 500 safety functions 100
10.7 Safety stop 101
10.8 Light indicators and speakers 102
11. Commissioning 106
11.1 Analysis of the work environment 106
11.2 Risk assessment 108
11.3 Lift modifications 110
11.4 Creating and configuring maps 112
11.5 Markers 123
11.6 Positions 127
11.7 Creating missions 128
11.8 Creating a footprint 132

MiR500Pallet Lift User Guide (en) 12/2020 - v.2.1 ©Copyright 2018-2020: Mobile Industrial Robots A/S. 6
11.9 Using operating hazard zones 136
11.10 Making a brake test 141
11.11 Creating user groups and users 142
11.12 Creating dashboards 145
11.13 Updating MiR500Pallet Lift software 147
11.14 Creating backups 148
11.15 System settings 148
12. Usage 157
12.1 Creating markers 157
12.2 Creating positions 162
12.3 Creating the mission Prompt user 164
12.4 Creating the mission Try/Catch 169
12.5 Creating the mission Variable docking 175
12.6 Creating the mission Pick up and place pallet 183
12.7 Testing a mission 186
13. Unmounting the top module 188
14. Maintenance 194
14.1 Regular weekly checks and maintenance tasks 194
14.2 Regular checks and replacements 196
14.3 Battery maintenance 198
15. Packing for transportation 199
15.1 Original packaging 199
15.2 Packing the robot for transportation 200
15.3 Battery 200

MiR500Pallet Lift User Guide (en) 12/2020 - v.2.1 ©Copyright 2018-2020: Mobile Industrial Robots A/S. 7
16. Payload distribution 201
17. Disposal of robot 202
18. Interface specifications 203
18.1 General purpose interfaces 203
18.2 Safety interfaces 207
19. Error handling 213
19.1 Software errors 213
19.2 Hardware errors 214

1. About this document
MiR500Pallet Lift User Guide (en) 12/2020 - v.2.1 ©Copyright 2018-2020: Mobile Industrial Robots A/S. 8
1. About this document
This user guide explains how to set up and start operating your MiR500Pallet Lift robot and
provides examples of simple missions you can expand to your purposes. This guide also
contains information regarding the external and internal components of MiR500Pallet Lift
along with instructions for proper maintenance of the robot. You will also find information
regarding safety and specifications needed to commission a safe MiR500Pallet Lift robot
application.
NOTICE
Save this manual. It contains important safety and operating instructions.
1.1 Where to find more information
At the MiR website, you can find the following resources under the Manuals tab on each
product page:
•Quick starts describe how you start operating MiR robots quickly. It comes in print in the
box with the robots. Quick starts are available in multiple languages.
•User guides provide all the information you need to operate and maintain MiR robots and
how to set up and use top modules and accessories, such as charging stations, hooks, shelf
lifts, and pallet lifts. User guides are available in multiple languages.
•Commissioning guides describe how to commission your robot safely and prepare it to
operate in the workplace.
•Operating guides describe how to set up and use MiR accessories or supported functions
that are mainly hardware-based, such as charging stations and shelf functions.
•Getting started guides describe how to set up MiR accessories that are mainly software-
based, such as MiR Fleet.
•Reference guides contain descriptions of all the elements of the robot interface and MiR
Fleet interface. Reference guides are available in multiple languages.
•Best practice guides specify how much space MiR robots need to execute common
maneuvers.
•REST API references for MiR robots, MiR hooks, and MiR Fleet. HTTP requests can be
used to control robots, hooks, and MiR Fleet.
•MiR network and WiFi guide specifies the performance requirements of your network
and how you must configure it for MiR robots and MiR Fleet to operate successfully.

1. About this document
MiR500Pallet Lift User Guide (en) 12/2020 - v.2.1 ©Copyright 2018-2020: Mobile Industrial Robots A/S. 9
1.2 Version history
This table shows current and previous versions of this document.
MiR500Pallet Lift
Revision Release date Description HW
MiR500
HW MiR
Pallet
Lift 500
2.0 2020-12-01 New manual structure.
New sections: Warning label, Mounting
the nameplate, Accessing the internal
parts, Battery and charging, IT security,
Navigation and control system, Safety
system, Usage, Disposal of robot, Error
handling, and Glossary.
The MiR500 User Guide has been
merged with the MiR Pallet Lift 500
Operating Guide to provide a complete
application manual.
As a result, the version histories have
been aligned, and the revision number
has changed to version 2.0.
1.1 1.0
2.1 2020-12-04 General improvements throughout the
document.
1.1 1.0

1. About this document
MiR500Pallet Lift User Guide (en) 12/2020 - v.2.1 ©Copyright 2018-2020: Mobile Industrial Robots A/S. 10
MiR500
Revision Release date Description HW
1.0 2018-10-29 First edition. 1.0
1.1 2019-01-31 New section: Maintenance.
Updated styles.
1.0
1.2 2019-07-11 New sections: Create mission, Mission editor,
Lift modifications.
Updated section: Status lights.
1.0
1.3 2019-10-08 New section: Updating MiR500 software. 1.1
1.4 2020-06- 11 New section: IT security.
Added new information about payload.
1.1
MiR Pallet Lift 500
Revision Release date Description HW
1.0 2019-01-25 First edition. 1.0
1.1 2019-03-19 General improvements throughout the
document.
1.0
1.2 2019-09-04 Added section: Connecting the cables
General improvements throughout the
document.
New layout.
1.0
1.3 2019-10-30 Updated section: How the top module works.
General improvements throughout the
1.0

1. About this document
MiR500Pallet Lift User Guide (en) 12/2020 - v.2.1 ©Copyright 2018-2020: Mobile Industrial Robots A/S. 11
MiR Pallet Lift 500
Revision Release date Description HW
document.
1.4 2020-06-18 Added new information about payload.
General improvements throughout the
document.
1.0

2. Product presentation
MiR500Pallet Lift User Guide (en) 12/2020 - v.2.1 ©Copyright 2018-2020: Mobile Industrial Robots A/S. 12
2. Product presentation
MiR500Pallet Lift is an autonomous mobile robot with a top module mounted to it. It is
designed to transport pallets indoors within production facilities, warehouses, and other
industrial locations where access to the public is restricted.
Users operate MiR500Pallet Lift via a web-based user interface, which is accessed through a
browser on a PC, smartphone, or tablet. Each robot has its own network—see Connecting to
the robot interface on page 55. The robot can be set up to run a fixed route, be called on
demand, or perform more complex missions.
The robot interface of MiR500Pallet Lift can be accessed via Google Chrome, Google
Chromium, Apple Safari, Mozilla Firefox, and Microsoft Edge browsers.
The robot uses a map of its work area to navigate and can move to any position on the
map—see Navigation and control system on page 72. The map can be created or imported
the first time the robot is used. While operating, the robot avoids obstacles that are not
mapped, like people and furniture.
MiR500Pallet Lift transports pallets or loads with any dimensions that do not exceed the
footprint of the robot. The total payload capacity is 500 kg, which includes the weight of MiR
Pallet Lift 500 and its load. The robot uses MiR Pallet Rack as a load transfer station where it
can pick up or place loads autonomously.
Specifications for MiR500Pallet Lift are available on the MiR website.

2. Product presentation
MiR500Pallet Lift User Guide (en) 12/2020 - v.2.1 ©Copyright 2018-2020: Mobile Industrial Robots A/S. 13
2.1 Main features of MiR500Pallet Lift
The main features of MiR500Pallet Lift are:
•Driving in a populated workspace
The robot is designed to operate among people and maneuvers safely and efficiently in
highly dynamic environments.
•Overall route planning and local adjustments
The robot navigates autonomously to find the most efficient paths to its destinations. The
robot adjusts the path when it encounters obstacles that are not on the map, like
personnel and vehicles.
•Efficient transportation of pallets
The robot is designed to automate transportation of loaded pallets. The total payload of
the robot may not exceed 500 kg, including the weight of the MiR Pallet Lift 500 top
module and its load.
•Sound and light signals
The robot continuously signals with light and sounds, indicating where it will drive and its
current status, for example, waiting for a mission, driving to a destination, or destination
reached.
•User-friendly and flexible
The web-based user interface, accessed from a PC, tablet, or smartphone, gives easy
access to operation and monitoring of the robot and can be programmed without any
prior experience. Different user group levels and tailored dashboards can be set up to suit
different users.
•Alert for 'lost'
If the robot enters a situation where it is unable to find a path to its destination, it stops,
turns on the yellow-purple running error light, and a custom defined Try/Catch action
may be used to alert personnel or take other actions—see Creating the mission Try/Catch
on page 169.
•Automatic deceleration for objects
The built-in sensors ensure that the robot is slowed down when obstacles are detected in
front of it.

2. Product presentation
MiR500Pallet Lift User Guide (en) 12/2020 - v.2.1 ©Copyright 2018-2020: Mobile Industrial Robots A/S. 14
•Internal map
The robot can either use a floor plan from a CAD drawing, or a map can be created by
manually driving the robot around the entire site in which the robot is going to operate.
When the robot is mapping, the robot’s sensors detect walls, doors, furniture, and other
obstacles, and the robot then creates a map based on these input. After you've finished
mapping, you can add positions and other features in the map editor—see Creating and
configuring maps on page 112.

2. Product presentation
MiR500Pallet Lift User Guide (en) 12/2020 - v.2.1 ©Copyright 2018-2020: Mobile Industrial Robots A/S. 15
2.2 External parts
This section presents the parts of MiR500Pallet Lift that are visible on the outside.
Figure 2.1. MiR500Pallet Lift external parts.
Pos. Description Pos. Description
1 Lift plate 2 Lift frame
3 Emergency stop button: four
buttons, two on each side—
see Emergency stop buttons
on page 99
4 Status light: on all four sides
of the robot—see Obstacle
detection on page 77
5 Left side maintenance hatch:
opens to the left side
compartment—see Internal
6 Front safety laser scanner—
see Obstacle detection on
page 77
Table 2.1.
Identification of the external parts in Figure 2.1

2. Product presentation
MiR500Pallet Lift User Guide (en) 12/2020 - v.2.1 ©Copyright 2018-2020: Mobile Industrial Robots A/S. 16
Pos. Description Pos. Description
parts on page 21
7 Front maintenance hatch:
opens to the front
compartment—see Internal
parts on page 21
8 3D depth cameras: two pcs,
detect objects in front of the
robot— see Obstacle
detection on page 77
9 Proximity sensors: eight pcs.,
two in each corner behind
the corner covers—see
Obstacle detection on page
77.
10 Right side maintenance
hatch: opens to the right side
compartment—see Internal
parts on page 21
11 Rear safety laser scanner—
see Obstacle detection on
page 77
12 Rear maintenance hatch:
opens to the rear
compartment—see Internal
parts on page 21
13 Signal light: eight pcs., two
on each corner—see Light
indicators and speakers on
page 102
Identification label
MiR500Pallet Lift is delivered with identification labels mounted to each product. The
identification labels identify the product, the product serial number, and the hardware
version of the product.
The identification label of MiR500 is located on the rear-right side of the chassis.

2. Product presentation
MiR500Pallet Lift User Guide (en) 12/2020 - v.2.1 ©Copyright 2018-2020: Mobile Industrial Robots A/S. 17
Figure 2.2. Placement of the MiR500 identification label.
The identification label of MiR Pallet Lift 500 is located on rear of the lift and can only be
accessed when the lift is raised.
Figure 2.3. Placement of the MiR Pallet Lift 500 identification label.
Figure 2.4. Example of a MiR Pallet Lift 500 identification label.

2. Product presentation
MiR500Pallet Lift User Guide (en) 12/2020 - v.2.1 ©Copyright 2018-2020: Mobile Industrial Robots A/S. 18
Nameplate
Every MiR application is delivered with a nameplate that must be mounted to the robot. The
nameplate of MiR500Pallet Lift identifies the application model and serial number and
includes the CE mark, the technical specifications, and the address of Mobile Industrial
Robots. The nameplate identifies the complete MiR application, for example, a robot with a
top module.
It is the responsibility of the commissioner to mount the nameplate on the application—see
Mounting the nameplate on page 59.
Figure 2.5. Example of a MiR500Pallet Lift nameplate.
Control panel
MiR500Pallet Lift has a control panel in the rear-left corner of the robot.

2. Product presentation
MiR500Pallet Lift User Guide (en) 12/2020 - v.2.1 ©Copyright 2018-2020: Mobile Industrial Robots A/S. 19
The control panel buttons
Figure 2.6. The MiR500Pallet Lift control panel.
Pos. Description Pos. Description
1 Manual stop button 2 Resume button
3 Power button 4 Operating mode key
Table 2.1.
Identification of items on the control panel in Figure 2.6
Manual stop
Pressing this button stops the robot. After pressing this button, you must press the Resume
button to let the robot continue operating.
Color indication:
•Red: It is possible to engage the Manual stop.
Resume
Pressing this button:
•Clears the Emergency stop state.
•Lets the robot continue operating after the Manual stop button was pressed or after the

2. Product presentation
MiR500Pallet Lift User Guide (en) 12/2020 - v.2.1 ©Copyright 2018-2020: Mobile Industrial Robots A/S. 20
operating mode changes.
•Lets the robot start operating after powering up.
Color indication:
•Blinking blue: The robot is waiting for a user action (clear the Emergency stop state,
acknowledge the change of operating mode).
Power
Pressing this button for three seconds turns the robot on or shuts it off.
Color indication:
•Blue: The robot is off.
•Blinking green: The robot is starting up.
•Green: Normal operation.
•Blinking red: The battery level is too low to start without additional charging, or the robot
is shutting down.
The Operating mode key
The Operating mode key lets you switch between operating modes.
•Left position: Autonomous mode
Puts the robot in Autonomous mode.
•Middle position: Locked
Locks the robot. The robot blocks the wheels; you cannot start a mission or drive the robot
manually.
•Right position: Manual mode
Puts the robot in Manual mode.
For more information on operating modes, see Operating modes below.
Operating modes
MiR500Pallet Lift has two operating modes: Manual mode and Autonomous mode.
Other manuals for 500
6
This manual suits for next models
5
Table of contents
Other MIR Lifting System manuals
Popular Lifting System manuals by other brands
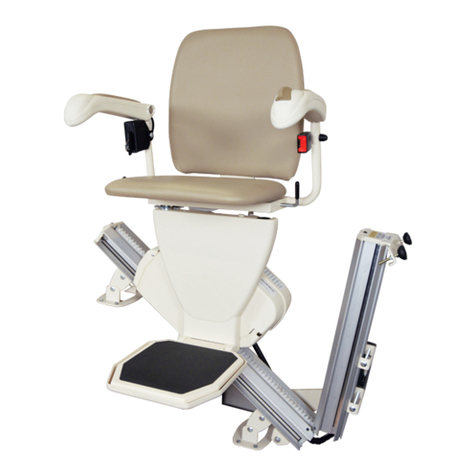
Harmar Mobility
Harmar Mobility Pinnacle SL600 Installation & service manual
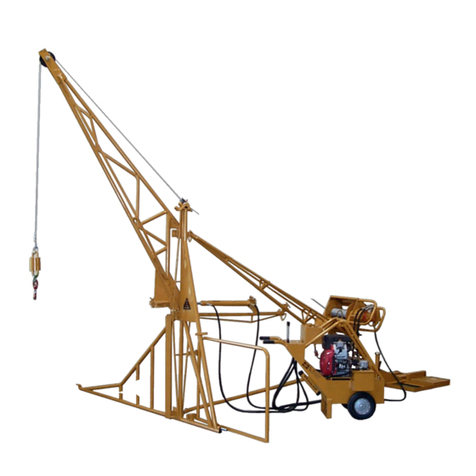
ASE
ASE 2000 owner's manual
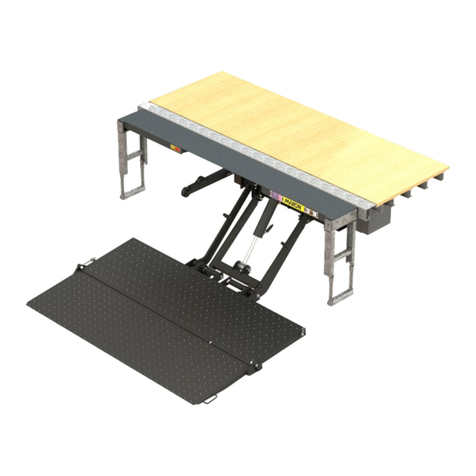
Maxon
Maxon TE-15 Maintenance manual

AUTOPSTENHOJ
AUTOPSTENHOJ Masterlift 2.30 installation instructions
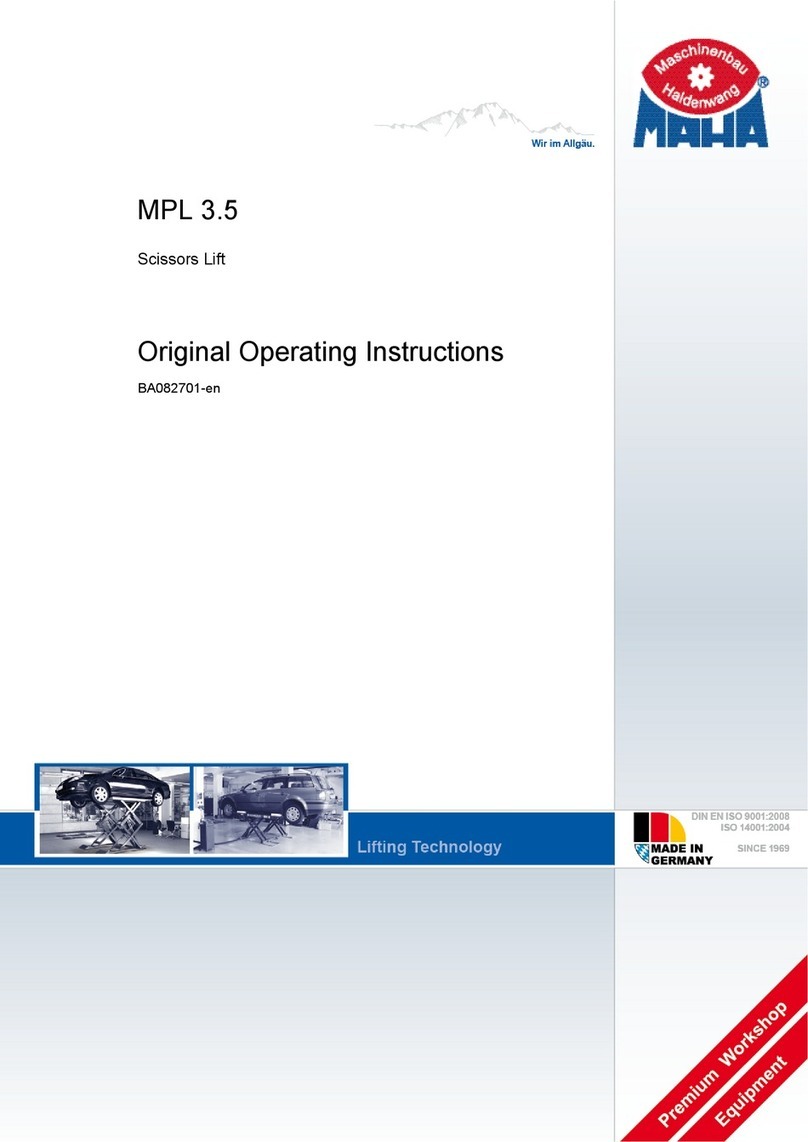
MAHA
MAHA MPL 3.5 operating instructions

PFlow Industries
PFlow Industries B Series Owner's, Installation and Maintenance Manual