Miyachi STA-100A Manual

USER’S MANUAL NO. 990-350
REVISION E: January 2002
OPERATION, MAINTENANCE
AND SERVICE MANUAL
FOR THE
STA-100A
AC CONTROL
Version 2.11 Software

STA-100A AC CONTROL
ii 990-350
Copyright © 2000, 2002, Unitek Miyachi Corporation
The engineering designs, drawings and data contained herein are the proprietary work of UNITEK
MIYACHI CORPORATION and may not be reproduced, copied, exhibited or otherwise used without the
written authorization of UNITEK MIYACHI CORPORATION.
Printed in the United States of America
Revision Record
Revision
EO
Date
Basis of Revision
A
18147
3/00
Pre-production release
B
18533
11/00
Production Release
C
18677
1/01
Version 1.3 Release
D
19039
8/01
Version 2.0 Release
E
19181
1/02
Version 2.11 Release

STA-100A AC CONTROL
990-350 iii
FOREWORD
Thank you for purchasing a Miyachi STA-100A AC Control. This unit is a component of a larger resistance
welding system.
Upon receipt of your equipment, please thoroughly inspect it for shipping damage prior to its installation.
Should there be any damage, please immediately contact the shipping company to file a claim, and notify us
at:
Miyachi
245 E. El Norte St.
P.O. Box 5039
Monrovia, CA 91017
Telephone: (626) 256-4128
FAX: (626) 303-5396
e-mail: info@miyachi1.com
The purpose of this manual is to supply operating and maintenance personnel with the information needed
to properly and safely operate and maintain Miyachi's STA-100A AC Control.
The Control consists of a cabinet which contains the AC Main Timer Board, A1; SCR Driver Board, A2;
Control Panel Assembly, A3; Valve Expansion Board, A4 (optional); valve and power transformers; SCR
assembly and snubber; surge resistors, and either primary current sensor or input connector for secondary
current sensor (optional). Except for the 300A SCR model, the Control is capable of being mounted either
on its left side or rear (from the perspective of the control panel). The 300A SCR model can only be
mounted on its left side. The Control provides the user with all of the controls for establishing all weld
modes and timing.
We have made every effort to ensure that the information in this manual is accurate and adequate.
Should questions arise, or if you have suggestions for improvement of this manual, please contact us at the
above location/numbers.
Unitek Miyachi Corporation is not responsible for any loss due to improper use of this product.

STA-100A AC CONTROL
iv 990-350
SAFETY NOTES
This instruction manual describes how to operate, maintain and service the STA-100A AC Timer, and
provides instructions relating to its SAFE use.
For SAFETY, and to effectively take advantage of the full capabilities of the workstation, please read these
instructions before attempting to use the workstation.
Procedures other than those described in this manual or not performed as prescribed in it, may expose
personnel to electrical hazards.
After reading this manual, retain it for future reference when any questions arise regarding the proper and
SAFE operation of the unit.
Please note the following conventions used in this manual:
WARNING: Comments marked this way warn the reader of actions which, if not followed, might result in
immediate death or serious injury.
CAUTION: Comments marked this way warn the reader of actions which, if not followed, might result in
either damage to the equipment, or injury to the individual if subject to long-term exposure to the indicated
hazard.
WARNINGS
HIGH VOLTAGE is used in the operation of this equipment
DEATH ON CONTACT may result if personnel fail to observe the safety precautions
labeled on the equipment and noted in this manual
WHEN WELDING always wear safety glasses

STA-100A AC CONTROL
990-350 v
CONTENTS
CHAPTER 1: Description.................................................................................................................... 1-1
Section I: Features....................................................................................................................... 1-1
Section II: Major Components.................................................................................................... 1-1
Major Components........................................................................................................... 1-1
Controls and Indicators.................................................................................................... 1-3
Internal Access................................................................................................................. 1-5
Mounting Holes ............................................................................................................... 1-5
Electrical Connections..................................................................................................... 1-5
Water Connections........................................................................................................... 1-5
CHAPTER 2: Getting Started............................................................................................................. 2-1
Section I: Planning for Installation............................................................................................. 2-1
Environmental Factors..................................................................................................... 2-1
Space and Mounting Requirements................................................................................. 2-1
Power Requirements........................................................................................................ 2-1
Cooling Water Requirements (600 and 1200 Amp Controls Only) ................................ 2-1
Section II: Control Set-up........................................................................................................... 2-2
Unpacking........................................................................................................................ 2-2
Installation........................................................................................................................ 2-2
Mounting the Control........................................................................................... 2-2
Electrical Connections......................................................................................... 2-3
Secondary Current Sensor.................................................................................... 2-4
Cooling Water Hose Connections........................................................................ 2-4
Input/Output Signal Connections......................................................................... 2-4
Input/Output Signal Descriptions ........................................................................ 2-6
CHAPTER 3: Operating Instructions ................................................................................................ 3-1
Section I: Operating Precautions .............................................................................................. 3-1
General Operator Safety .................................................................................................. 3-1
Section II: Preparing for Operation............................................................................................ 3-1
Turning the Equipment On .............................................................................................. 3-1
Pre-Operational Setup...................................................................................................... 3-2
Schedule Screen................................................................................................... 3-2
System Wide Values Screen................................................................................ 3-7
Extended System Wide Values Screen................................................................ 3-8
System Valve Status Screen................................................................................. 3-10
Valve Screen........................................................................................................ 3-10
Mode Screen ........................................................................................................ 3-11
Linked Schedules Screen..................................................................................... 3-14
Monitor Screen..................................................................................................... 3-15
Stepper Screen ..................................................................................................... 3-16

STA-100A AC CONTROL
vi 990-350
Section III: Setup Messages...................................................................................................... 3-18
Section IV: Operation................................................................................................................ 3-21
Section V: Programming Examples......................................................................................... 3-22
Spot Welds....................................................................................................................... 3-22
Continuous Seam Weld.................................................................................................... 3-23
Section VI: Operational Messages............................................................................................. 3-24
Major Run-Time Error Messages .................................................................................... 3-24
Minor Run-Time Error Messages.................................................................................... 3-27
Section VII: Shutdown................................................................................................................ 3-29
Emergency Shutdown...................................................................................................... 3-29
Normal Shutdown............................................................................................................ 3-29
CHAPTER 4: User Maintenance ........................................................................................................ 4-1
Section I: Maintenance Precautions............................................................................................ 4-1
Precautions....................................................................................................................... 4-1
Section II: Maintenance Procedures ........................................................................................... 4-1
Cooling Maintenance....................................................................................................... 4-1
Heat Sink Cleaning (300 Amp SCR Unit Only).................................................. 4-1
Water Draining (600 and 1200 Amp SCR Units Only)....................................... 4-1
Fuse Replacement............................................................................................................ 4-1
CHAPTER 5: Service........................................................................................................................... 5-1
Section I: Service Precautions .................................................................................................... 5-1
Precautions....................................................................................................................... 5-1
Section II: Service Procedures.................................................................................................... 5-1
Principles of Operation.................................................................................................... 5-1
Fuse Replacement............................................................................................................ 5-2
Components Replacement ............................................................................................... 5-2
General Repair Instructions ................................................................................. 5-2
AC Timer Main Board, A1.................................................................................. 5-2
SCR Driver Board, A2......................................................................................... 5-4
Control Panel Assembly, A3................................................................................ 5-5
Valve Expansion Board, A4 (Optional)............................................................... 5-6
Valve Transformer, T3......................................................................................... 5-6
Power Transformer, T2........................................................................................ 5-7
Power Transformer, T1........................................................................................ 5-7
Surge Resistors .................................................................................................... 5-8
Snubber ............................................................................................................... 5-8
L2 Terminal Block (Optional)............................................................................. 5-8
Ground Terminal Block....................................................................................... 5-8
Primary Current Sensor (Optional)...................................................................... 5-9
Secondary Current Sensor Connector (Optional)................................................ 5-9
Key Lock (Optional)............................................................................................ 5-9
SCR Assembly, 300 Amp, Air Cooled (Optional) .............................................. 5-10
SCR Assembly, 600 and 1200 Amp, Water Cooled (Optional).......................... 5-10
Spare Parts Kit ................................................................................................................. 5-13
Section III: Repair Service.......................................................................................................... 5-13

STA-100A AC CONTROL
990-350 vii
Section IV: Storage and Shipment.............................................................................................. 5-13
Preparation for Storage or Shipment................................................................................ 5-13
Packaging for Storage or Shipment ................................................................................. 5-13
APPENDIX A: Technical Specifications ............................................................................................ A-1
APPENDIX B: System Timing............................................................................................................ B-1
APPENDIX C: SCR, Wire Size, and Circuit Breaker Selection...................................................... C-1
APPENDIX D: Circuit Modification for External Transformer Thermostat................................ D-1
APPENDIX E: Default Initializations................................................................................................. E-1
INDEX.................................................................................................................................................. Index-1
ILLUSTRATIONS
Figure Title Page
1-1 STA-100A AC Control, Major Components............................................................................... 1-2
1-2 Controls and Indicators................................................................................................................ 1-3
2-1 Installing Mounting Tabs onto Cabinet ....................................................................................... 2-2
2-2 Power Connection Points............................................................................................................. 2-3
2-3 Placement of Secondary Current Sensor Toroidal Coil............................................................... 2-4
2-4 Wiring Connections to Valve (Input Power) Transformer .......................................................... 2-4
2-5 Input/Output Control Signals....................................................................................................... 2-5
2-6 Valve Expansion Board, A4, Input/Output Signals..................................................................... 2-7
3-1 Control Panel with Introductory Screen and Indicators............................................................... 3-1
3-2 Typical Initial Schedule Screen ................................................................................................... 3-2
3-3 Typical Second Schedule Screen................................................................................................. 3-3
3-4 Typical Third Schedule Screen.................................................................................................... 3-3
3-5 Schedule Screen with Percent Heat and Percent Heat Secondary............................................... 3-5
3-6 Schedule Screen Primary Constant Current Mode ...................................................................... 3-5
3-7 Schedule Screen Secondary Constant Current Mode .................................................................. 3-5
3-8 System Wide Values Screen........................................................................................................ 3-7
3-9 Extended System wide Values Screen......................................................................................... 3-8
3-10 System Valve Status Screen......................................................................................................... 3-9
3-11 Valve Screen .............................................................................................................................. 3-10
3-12 Mode Screen .............................................................................................................................. 3-11
3-13 Linked Schedules Screen............................................................................................................. 3-14
3-14 Monitor Screen............................................................................................................................. 3-15
3-15 Stepper Screen ............................................................................................................................. 3-17
3-16 Example of Stepper Function....................................................................................................... 3-17
5-1 Control, Simplified Block Diagram............................................................................................. 5-1
5-2 AC Timer Main Board, A1, Connector Locations....................................................................... 5-3
5-3 SCR Driver Board, A2, Connector Locations ............................................................................. 5-4
5-4 Control Panel Assembly, A3, Connector Locations.................................................................... 5-5
5-5 Valve Expansion Board, A4, (Optional) Connector Locations ................................................... 5-6
5-6 Control, Wiring Diagram............................................................................................................. 5-12

STA-100A AC CONTROL
viii 990-350
TABLES
Table Title Page
4-1 Valve Transformer Fuse Selection............................................................................................... 4-1
5-1 Spare Parts Kit, 4-35732-01......................................................................................................... 5-13

STA-100A AC CONTROL
990-350 1-1
CHAPTER 1
DESCRIPTION
Section I: Features
The STA-100A AC Control, herein called the “Control,” is a device for controlling single-phase AC
welding. It has the following features:
•Multiple pulse capability
•Controlled current ramps
•300, 600, or 1200 amp SCRs with constant current control
•Air (300 amp) or water (600, 1200 amp) cooling of the SCR assembly
•Programming features with LCD display
•Programmable for spot, repeat, successive, or chaining modes
•Continuous seam weld and roll spot seam welding capabilities (optional)
•Programmable for 64 welding schedules and four pressure valve signals
•Valve drivers for up to four valves are included in the basic unit. A Valve Driver Expansion card is
an optional add-on to increase valve-driver capability to 12 valves.
Section II: Major Components
Major Components
The Control is contained in a 18” x 10” x 10” enclosure. Specific dimensions, weight, and locations of
mounting are shown in Chapter 2, Getting Started, and Appendix A, Specifications. Access to the
internal components is gained by opening the hinged side panel, which is secured with two quarter-turn
screw fasteners. The access panel can be locked closed by a key. When open, the panel can be lifted
from the hinges to facilitate installation and maintenance. The major components of the 300A and
600A/1200A units are indicated in the several views comprising figure 1-1.

CHAPTER 1: DESCRIPTION
STA-100A AC CONTROL
1-2 990-350
Components of Control with 300A (Air Cooled) SCR and Primary Current Sensor
Components of Control with 300A (Air
Cooled) SCR and Connector for
Secondary Current Sensor Input
Components of Control with
600A/1200A (Water Cooled) SCR and
Primary Current Sensor
Chassis
Ground
T3
Valve
Trans-
former
A2
SCR
Drive
Board
Key
Switch
A3
Control
Panel
Assy
300 Amp
SCR
Air
Cooling
Fins
Primary
Current
Sensor
SOL
SR1
SR2
1
21
2
H2-1
Valve
Expander
Board, A4
(Optional)
AC Timer
Main Board, A1
Surge
Resistors
Push
Solenoid
Power
Transformers
CT1
Primary
Current
Sensor
300 Amp
(Air Cooled)
SCR
T3
Valve
Transformer
T2
T1
L2
Chassis
Ground
T3
Valve
Transformer CT1
Secondary
Current Sensor
Input Connector
SN1
Snubber SCR1
300 Amp
SCR
H1-1
L1
Chassis
Ground
T3
Valve
Trans-
former
CT1
Primary
Current Sensor
SN1
Snubber
SCR1
600/1200
Amp SCR
H1-1
L1
Figure 1-1. STA-100A AC Control, Major Components
Figure 1-1. STA-100A AC Control, Major Components
Access Panel Side

CHAPTER 1: DESCRIPTION
STA-100A AC CONTROL
990-350 1-3
Controls and Indicators
All controls and indicators are located on the control panel, shown in figure 1-2, and described in the
following paragraphs.
LCD Display – White on blue 40 X 8 LCD display provides information for programming and
monitoring the unit.
READY indicator – Red LED indicator lights when the Control is ready to weld.
ERROR indicator – Red LED indicator lights when a control error or weld error has occurred.
WELD indicator – Green LED indicator lights when weld is occurring.
START indicator – Red LED indicator lights to indicate receipt of a start signal.
PROGRAM/SAVE pushbutton switch – Pressing this pushbutton switch toggles the Control between
Program Mode and Run Mode. (In the Run Mode, entered data is saved; hence the name on the switch.)
When in the Program Mode, the green LED on the pushbutton switch lights and the operator may enter
program information using the DATA and CURSOR pushbutton switches. When in this mode, the
Control will not accept a Start signal.
At the completion of making Schedule Program changes, pressing the PROGRAM/SAVE switch again,
saves all program changes and places the Control into Run mode. During Run Mode, the DATA
ON/OFF pushbutton switch will be disabled, preventing the operator from modifying programs.
Figure 1-2. Controls and Indicators

CHAPTER 1: DESCRIPTION
STA-100A AC CONTROL
1-4 990-350
WELD ON/OFF pushbutton switch – When the WELD ON/OFF entry (in the Extended System Values
screen) is set to LOCAL, pressing this pushbutton switch will enable or disable the flow of weld current.
The green LED lights when current is enabled. When current is disabled, the Control can still sequence
through its program, but current will not flow.
DATA Two-position pushbutton switch – When the Control is in the Program Mode, pressing this
pushbutton switch will allow the operator to change the program settings. Holding the switch down (in
either position) will scroll the values in the selected direction.
When the Control is in the Run mode, the WELD ON/OFF switch is set to OFF, and the cursor is at the
schedule number position, the operator can use this key to scroll through the schedules.
CURSOR Four-position, momentary-action pushbutton switch – Pressing this pushbutton switch will
allow the operator to move the cursor around the display.
Cursor Movement
Left and Right Arrows – In general, the right arrow will move the cursor from left to right , then
to the left-hand field of the next line down, across that line, and so on. Upon reaching the
bottom, right-hand field, the cursor will “roll over” to the top, left-hand field. The left arrow
works in the reverse direction.
Whichever arrow is pressed, when the cursor enters a field, it will automatically position itself at
the rightmost position of a numeric field or the leftmost position of an ON/OFF or alphabetic
field.
When in a numeric field, successively pressing the left arrow will move the cursor successively
to the next higher order digit or, when the highest order number for that field is reached, to the
previous field.
Up and Down Arrows – These arrows will move the cursor to the field above or below the
current field whose rightmost digit is closest to the current position of the cursor.
Holding any cursor pushbutton down will cause the cursor to rapidly move in the appropriate
direction, eventually rolling over from the last field to the first, or vice-versa.
While in Program Mode, when the cursor is in any position of a digit field, pressing the + or –
key of the DATA pushbutton will cause the digit in that position to increment or decrement by
one digit.
SCHEDULE pushbutton switch – When the WELD ON/OFF switch is set to OFF, pressing this
pushbutton switch will cause the current Schedule number’s screen to be displayed. The cursor shall be
at the unit digit of the Schedule #. If the Schedule # is changed, that specific schedule will be displayed.
See Chapter 3 for details of this screen.
VALVES pushbutton switch – When the WELD ON/OFF switch is set to OFF, pressing this pushbutton
switch will cause the Valve screen to appear on the display. See Chapter 3 for details of this screen.
MODES pushbutton switch – When the WELD ON/OFF switch is set to OFF, pressing this pushbutton
switch will cause the Mode screen to appear on the display. See Chapter 3 for details of this screen.
RESET pushbutton switch – Pressing this pushbutton switch will reset Control after a major error signal
is received. (Major errors are Emergency Stop, Over-temperature, No Current, Mode Change Error, End

CHAPTER 1: DESCRIPTION
STA-100A AC CONTROL
990-350 1-5
of Stepper Function, Weld1 or Weld2 Conduction High, Weld1 or Weld2 Current High, Full Wave
Conduction, Illegal Schedule Number, or SCR shorted.)
MONITOR pushbutton switch – When the WELD ON/OFF switch is set to OFF, pressing this
pushbutton switch will cause the Monitor screen to appear on the display. See Chapter 3 for details of
this screen.
STEPPER pushbutton switch – When the WELD ON/OFF switch is set to OFF, pressing this
pushbutton switch will cause the Stepper screen to appear on the display. See Chapter 3 for details of
this screen.
This screen allows information to be programmed to compensate for gradual deformation of the weld
electrodes by adjusting power to compensate for that deformation.
PROGRAMMING lock –This optional key lock, when locked, prevents any change in the program.
Internal Access
Access to the internal components is gained by opening the hinged side panel, which is secured with two
quarter-turn screw fasteners. For safety, a key locks the panel closed. When open, the panel can be lifted
from the hinges to facilitate installation or maintenance. There are no operator or installation adjustments
inside of the unit, so the cover should not need to be removed except for initial installation (electrical
connections) and for repair of components.
Mounting Holes
Four mounting tabs are provided with the Ship Kit. Eight pairs of mounting holes (four each on the rear
and the left-hand side) are pre-drilled and tapped for convenience of mounting the mounting brackets to
the Control. See figure 2-1 for location of those holes.
Electrical Connections
The user must provide access holes for electrical connections (power and control). If (optional)
secondary current sensing has been ordered, an input connector (CT1) is already mounted in the bottom
of the Control cabinet (figure 1-1).
Water Connections
The 600A and 1200A SCRs require cooling water, which enters the Control through fittings on the
bottom of the Control.


STA-100A AC CONTROL
990-350 2-1
CHAPTER 2
GETTING STARTED
Section I: Planning for Installation
Environmental Factors
We recommend that you install the Control in a well ventilated area that is free from excessive dust,
weld expulsion, acids, corrosive gasses, salt and moisture. Allow adequate space around the unit for
power and signal cabling runs, and additional space in front for the operator. Water-cooled units will
require space below the Control for hose connections. Air-cooled units require space in the back for the
cooling fins. Electrical and signal connections may be made from either the top or bottom of the
Control.
The Control is designed to work in the following ambient conditions:
Temperature: 32-104°F (0-40°C)
Humidity: 20% to 95%, non-condensing
Space and Mounting Requirements
An outline drawing of the unit, including dimensions for the mounting holes, is included in Appendix A.
The approximate dimensions are:
Width: 10 in. (254 mm)
Depth: 10 in. (254 mm)
Height: 18 in. (457 mm)
Weight: 35 to 50 lb. (15.9 to 22.7 kg) depending on options included in unit
Power Requirements
Power requirements are: 230 or 460 VAC (nominal), ±10single phase, 60 Hz. For exact ranges, see
Appendix A, Technical Specifications.
NOTE: The Control is a component of a larger resistance welding system. Please review the complete
system requirements in order to install this component in compliance with all applicable codes and
requirements. An external power control (ON/OFF switch or contactor) must be provided at the junction
box that feeds power to the Control.
Cooling Water Requirements (600 and 1200 Amp Controls Only)
See Appendix A, Technical Specifications, for SCR cooling water requirements. The connections to the
SCR are made with ¼-18 NPT fittings through the bottom of the Control cabinet. It is recommended
that filtered water be used to prevent sediment build-up in the hoses and SCR.

CHAPTER 2: GETTING STARTED
STA-100A AC CONTROL
2-2 990-350
Section II: Control Set-up
Unpacking
Unpack the Control from its shipping box. The box also contains a Ship Kit with the components
itemized on a packing list within the kit.
NOTE: Carefully save and store packing materials for future storage or shipment of the Control.
Installation
Installation consists of mounting the unit, making power and signal connections, and making cooling
water connections (600A and 1200A units only). After determining how the unit will be mounted, and
how electrical and water hose connections will be made, it may be more convenient to move the Control
to another work area prior to punching the mounting and connector holes.
CAUTION: Protect electronic components from metal shards when drilling pilot holes and punching
holes. Be sure all metallic shards are removed from the Control after punching holes.
Mounting the Control.
The ship kit contains four mounting tabs, two with mounting holes, two with mounting slots, as
shown in figure 2-1. Depending on how you intend to mount the unit, the tabs will be attached to the
cabinet on either the left-hand side or the rear, as shown. Each of the four tabs are mounted to the
cabinet with two 8-32 x3/8” flat-head machine screws, also contained in the ship kit. Mount the
tabs with slots on the bottom of the cabinet.
NOTE: Due to the presence of the SCR cooling fins, 300 amp models cannot be mounted on the
rear surface; they must be mounted on the left-hand side. Be sure there is adequate air flow around
the cooling fins for heat dissipation.
As each installation is
different, no mounting
hardware is provided
for the cabinet. The
holes on the mounting
tabs are designed for
1/4” (or M6) screws or
bolts. You will need to
provide the appropriate
screws or bolts, flat and
lock washers, and nuts.
Loosely install the two
lower mounting screws.
Slide the Control
bottom (slotted) tabs
into the two lower
mounting screws. With
Figure 2-1. Installing Mounting Tabs onto Cabinet
Location of threaded
holes for mounting
tabs when mounting
the Control on the
left-hand side.
Location of threaded
holes for mounting tabs
when mounting the
Control on the rear.
NOTE: This cannot be
done on configurations
with 300 amp SCRs.
Typical Mounting
Bracket and Screw
Typical Mounting
Bracket and Screw

CHAPTER 2: GETTING STARTED
STA-100A AC CONTROL
990-350 2-3
one person holding the Control in place, have a second person install the two upper mounting screws
then tighten the two lower mounting screws.
Electrical Connections
WARNING: The installer must make electrical connections in accordance to all applicable codes.
For appropriate circuit breaker rating, see Appendix C. For Emergency Stop connections, see figure
2-5.
NOTES:
•See figure 1-1 for identification of
components, figure 2-2 for power
connection points, and figure 5-6 for a
wiring diagram.
•If you have not ordered the optional
Terminal Block L2, skip steps 1b and
2b and perform step 3.
Power and signal connections are made
through the customer-provided punch-out
holes in the Control. Connect the power
cables as follows:
1Connect the control to the weld
transformer using the appropriate wire
gauge for your requirements. (See
Appendix C.)
aConnect one wire to H1-1 of the
SCR.
bConnect the other wire to H2-1 of
optional Terminal Block L2.
2Connect the Control to the appropriate
power source (230 V or 460 V), using
the appropriate wire gauge for your
requirements. (See Appendix C.)
aConnect one wire to L1 of the SCR. If you have the Primary Current Sensor Option, be sure that
the wire passes through the current sensor as shown in figure 2-2 and the wiring diagram in
figure 5-6
bConnect the other wire to L2 of optional Terminal Block L2.
NOTE: If one of the inputs is neutral, it should be connected to L2.
Perform this step only if you do not have optional Terminal Block L2.
cConnect the second wire from the weld transformer (H2-1) to the line 2 (L2) wire in accordance
with all applicable codes. (See Appendix C for appropriate wire gauge.)
Figure 2-2. Power Connection Points
SR1
SR2
H2-1
AC Timer
Main Board, A1
Surge
Resistors
L2
To Weld
Transformer
To Line L2
CT1
Primary
Current Sensor
SCR1
600/1200
Amp SCR
H1-1
L1
Chassis
Ground
To Weld
Transformer
To Line L1
To Ground

CHAPTER 2: GETTING STARTED
STA-100A AC CONTROL
2-4 990-350
dConnect an 18 gauge wire between the junction of L2 and H2-1 to terminal H4 of the valve
transformer, T3. There will already be a gray wire connected to that terminal from the surge
resistors, SR-1.
Secondary Current Sensor (Optional)
If you have ordered secondary current
sensing, you will receive a toroidal coil,
specified at time of order, with an attached
cable that connects the connector on the
bottom of the Control box. Place the
toroidal coil on the secondary of the weld
transformer.
NOTES (For MB-400K and MB-800K
Coils):
•Make sure that the metal buckle on the
toroidal coil is as far away from the
secondary as possible, as shown in figure
2-3.
•For most accurate measurement, do
not distort the shape of the toroidal
coil.
NOTE: Unless otherwise ordered, units
are shipped with the Valve Transformer
T3 connected for 460V configuration
(figure 2-4). If you re-configure the unit
for 230 V, you must change the jumpers
as shown in that figure. You must also
slightly bend up the tab connector on H4
of the transformer so that the connector of
the gray and orange wires slides all the
way onto the tab. Otherwise, the
connector will “bottom out” against the
jumper, and prevent a good connection.
Cooling Water Hose Connections
Connect the water, specified in Section I, using water hoses and ¼-18 NPT fittings.
Input/Output Signal Connections
Connect the input/output (I/O) signals as shown in the I/O drawing, figure 2-5. If you have a Valve
Expansion Board, also make the output connections to that board, as shown in figure 2-6.
Descriptions of these signals follow their respective figure. With the exception of the valve outputs,
all output signals are isolated contact relays. Valve outputs may be either 115 VAC (standard) or
24 VAC. Input signals are referenced to either an internal or external 24 VDC power supply.
Secondary
Toroidal coil
Secondary
current sensor
conection cable
Metal buckle
Figure 2-3. Placement of Secondary
Current Sensor Toroidal Coil
Figure 2-4. Wiring Connections to Valve
Transformer
H4
H1
XF
X2
YEL
RED
BLK
H2
H3
ORG
H4
H1
XF
X2
YEL
RED
BLK
H2
H3
To SCR
Jumper
To SCR
To Terminal
Block
Jumpers
230V Wiring Configuration 460V Wiring Configuration
GRY
To Surge
Resistors
ORG
To Terminal
Block
GRY
To Surge
Resistors

CHAPTER 2: GETTING STARTED
STA-100A AC CONTROL
990-350 2-5
Figure 2-5. Input/Output Control Signals

CHAPTER 2: GETTING STARTED
STA-100A AC CONTROL
2-6 990-350
Input/Output Signal Descriptions
EMO – Emergency Stop – Pressing the external Emergency Stop switch opens the connection
across these two pins and will cause an immediate termination of the welding operation. Control
power remains on. When the emergency stop switch is released and the reset button is pressed, the
Control will automatically re-boot and then be ready for operation.
VAL1, N & L through VAL4, N & L – Valve Output 1 Neutral and Line through Valve
Output 4 Neutral and Line – Output signals to drive up to four valves. (If more valves are needed,
a Valve Expander Board is required.) Each set of connections provides 115 VAC (standard) or
24 VAC (optional) power to the valve solenoid connected across those connections.
NOTE: The following four outputs are isolated contact relays that are closed when active.
FT1/FTC – Fault Output – An output signal indicating a major error has occurred. The ERROR
OUTPUT setting, set on the Weld Mode screen, determines whether this signal will be sent.
MT1/MTC – Step End Output – Output signal indication stepper is completed. Once this output is
on, the unit can no longer be fired and the error must be cleared. If the front panel RESET button or
external Fault Reset is initiated at the end of the stepper, the fault will clear and the unit may be fired
one more time. After firing one more time, the fault will re-appear. To clear the step counters, use
the Step Reset input. After clearing with Step Reset, the unit will once again start counting at the
first programmed step count.
EH1/EHC – End Signal Output – Output signal indicating completion of the weld schedule
sequence. In Chain Sequence, EH1 occurs after all schedules have fired. EH1 is 40-70 ms in
duration. If the Start signal is held beyond the end of the schedule, EH1 will stay on until either
either Start switch (FS1 or FS2) is turned off.
SPR1/SPR1C –Weld On/Off Status - This output indicates the NW1 status. (See NW1) When
the output is closed, the unit is ready to weld.
FS1 – Foot Switch Stage 1 Input – The first level of a two-level foot switch or a single level foot
switch is connected to this connector. This signal will switch the valve driver on, causing the
electrode(s) of the weld head to apply force to the work pieces and start the squeeze delay period. In
the case of a single level footswitch, the weld schedule will continue to its completion; no further
input is required. In the case of a two-level footswitch, the schedule will stop at the completion of
the squeeze (SQZ) period and wait for the input of the FS2 signal.
FS2 – Foot Switch Stage 2 Input – In the case of a two-level foot switch, this signal allows the
continuation of the weld schedule beyond the squeeze (SQZ) period.
SR1 – Step Reset Input – Input signal that, with the presence of a step end signal, will set the
stepper back to 0000 and the step number back to 01. This input will also clear the fault output when
step end occurs.
FR1 – Fault Reset Input – Input signal that resets a fault condition and clears the fault output.
After an EMO (Emergency Stop), a fault reset input will re-boot the system.
IN1 – General Purpose Input 1 – Unused
IN2 – General Purpose Input 2 – Unused
Table of contents
Popular Control System manuals by other brands
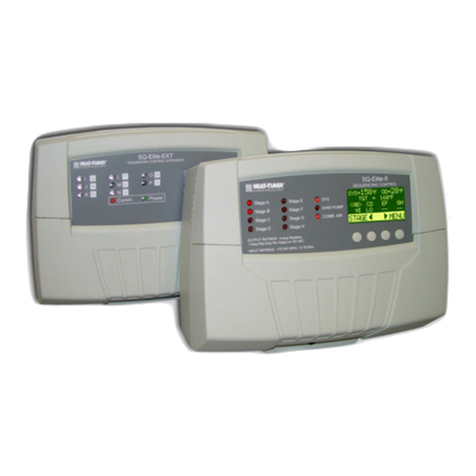
heat-timer
heat-timer SQ-Elite-8S Installation and operation instruction manual
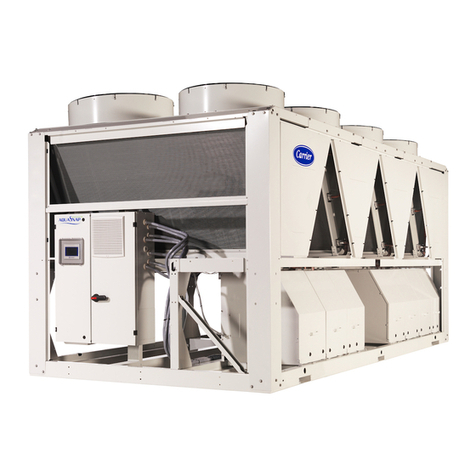
Carrier
Carrier SmartView manual
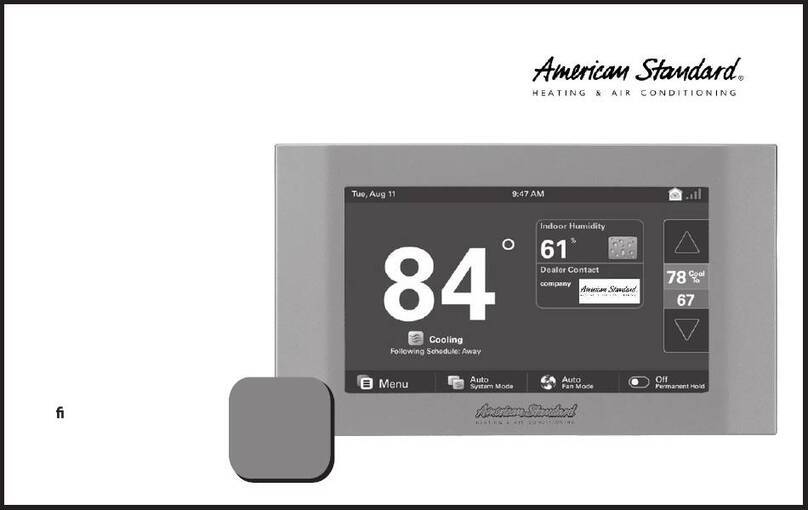
American Standard
American Standard Gold 824 user guide
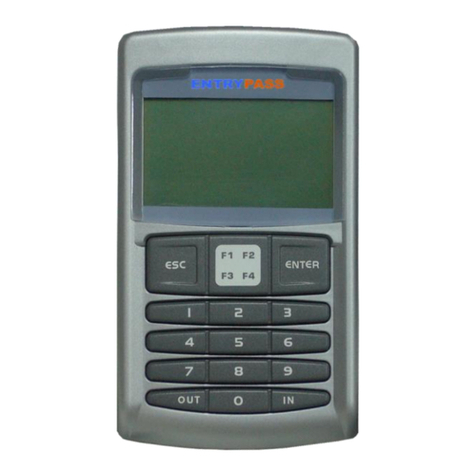
ENTRYPASS
ENTRYPASS EP.MINI Wiring guide

Carrier
Carrier AQUASNAP 30RA/RH Operation & maintenance instructions
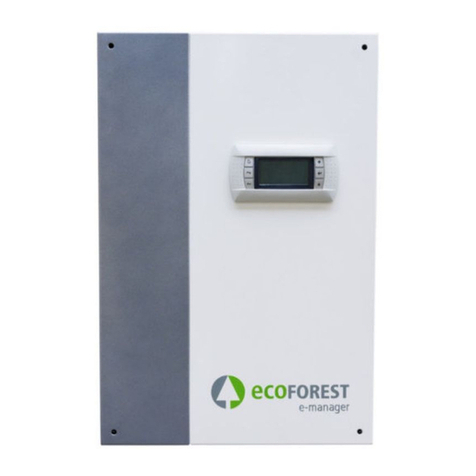
ECOFOREST
ECOFOREST ecoSMART Supervisor USER, INSTALLER AND TECHNICAL SERVICE MANUAL