MOGAS ISOLATOR 2.0 User manual

Installation, Operation
and Maintenance Manual
PREPARE THE VALVE FOR
INSTALLATION
INSTALL THE VALVE
PROPERLY
MAINTAIN THE VALVE FOR
OPTIMAL OPERATION
AND PERFORMANCE
for the
MOGAS ISOLATOR 2.0 Floating Ball Valve
6, 8, 10 and 12 inch

ESI-6152 © Copyright 01/25/2023 MOGAS Industries, Inc. www.mogas.com
2
THIS PAGE INTENTIONALLY LEFT BLANK

ESI-6152 © Copyright 01/25/2023 MOGAS Industries, Inc. www.mogas.com 3
Contents
VALVE ITEM REFERENCE NUMBER
6 - 12 INCH ......................................................... 4
READ BEFORE INSTALLING VALVE...................................6
TRANSPORT AND STORAGE ........................................7
CORRECT VALVE ORIENTATION .....................................8
PRE-INSTALLATION ...............................................9
INSTALLATION ..................................................10
OPERATION.....................................................12
MAINTENANCE ..................................................13
REPLACE STEM PACKING .........................................14
DISASSEMBLY...................................................18
EVALUATION AND REWORK .......................................23
ASSEMBLY......................................................24
LOCATE VALVE INFORMATION .....................................32
RETURN MERCHANDISE AUTHORIZATIONS (RMA) ....................33
SERVICE CONTACT ..............................................33
APPENDIX - GLAND STUD TORQUES................................34
APPENDIX - BODY STUD TORQUES.................................35

ESI-6152 © Copyright 01/25/2023 MOGAS Industries, Inc. www.mogas.com
4
61
04 62
05
64
08
09A 09B
07C
12
15
07
02
01C 01B
01B
01A
10 03
11
Valve Item Reference Number
Size 6, 8, 10 and 12 inch

ESI-6152 © Copyright 01/25/2023 MOGAS Industries, Inc. www.mogas.com 5
VERIFY SPARE PARTS
Contact MOGAS or a MOGAS Authorized Repair
Center to determine the spare parts and quantities
required for your specific serial number.
Valve Item Reference Number
Size 6, 8, 10 and 12 inch
Valve Part Reference Number
Item Description Titanium, F53 All Other
Material
Recommended
Spare Parts
01A Ball • • •
01B Seat • • •
01C Spring Disc • • •
02 Body • • —
03 End Connect • • —
04 Gasket, Spiral Wound •••
05 Stem • • —
07 Gland Flange • • —
07C Spring Discs (Live Loaded) • • —
08 Inner Stem Seal • • •
09A Ring, Stem Packing • • •
09B Ring, Anti-Extrusion •••
10 Stud, Body • • —
11 Nut, Body • • —
12 Stud, Gland • • —
15 Nut, Gland • • —
61 Ring, Seat-locking • • •
62 Seat-locking Screws • • •
64 Anti-Static Device — • —

ESI-6152 © Copyright 01/25/2023 MOGAS Industries, Inc. www.mogas.com
6
All MOGAS valves operate counter-clockwise to open, clockwise to close.
MOGAS valves are supplied in a variety of operator configurations based
upon customer requirements, and may be operated by
• pneumatic actuation • worm gear actuation (handwheel)
• hydraulic actuation
Each of these operator configurations may be installed and tested prior to
shipping, or shipped separately, depending on customer requirements.
Valves can be supplied bare stem or with adaption to accommodate a
variety of gears or actuators.
Please note the configuration of each individual valve and proceed with any
necessary operator adaption procedures prior to installing the valve. CLOSE
OPEN
Sequential procedure
required to perform operation.
Bold numbers correspond
with items shown in the Valve
Item Reference Number
sections.
Warning statement
to prevent unwanted
consequence.
Note(s) to support
procedure.
All information within this manual is relevant to the safe and proper
care of your MOGAS ball valve. Please understand the following
examples of instructional information:
General information or
an alternate / variation
procedure.
How to Read this Manual
Read Before Installing Valve
Note:
The normal direction of flow is from the higher pressure end
(upstream) to lower pressure end when the valve is closed.
CAUTION!
Ensure key length provides and maintains full
engagement.
THIS WILL AFFECT THE VALVE WARRANTY.
!
PRE-INSTALLATION STORAGE
Valves shall remain stored in their shipping crates
with the lids secured.
INSTALL STEM ADAPTOR
Align stem adaptor 13 so the keyways on stem
adaptor correspond with the keys 06 on stem 05.
5

ESI-6152 © Copyright 01/25/2023 MOGAS Industries, Inc. www.mogas.com 7
These procedures outline the general requirements for storage of MOGAS valves.
TRANSPORT
Valves will be shipped and packaged per customer’s requirements.
Upon arrival at the site, inspect the general condition of the valve (and actuator, if supplied)
for any potential shipping damage.
PRE-INSTALLATION STORAGE
Valves shall remain stored in their shipping crates, or on their pallets, with the lids secured.
For long-term storage, the internal parts of carbon and alloy steel valves should be sprayed
with a rust preventative.
All protective covers and plastic liners should remain in place.
REMOVING VALVE FROM SERVICE
Before the valve is removed from the line, it should be placed in the open position to prevent
further internal damage to valve components unless for flanged valves.
Flange protectors need to be secured to each end of the valve to prevent any foreign debris
from entering the valve. Unless the valve is used, it is recommended to place desiccant
dryer bags inside the valve before storage.
The valve should be stored in the vertical position inside until repairs can be made.
Any valve returned for service should be accompanied by safety data sheets for process
media.
Transport and Storage

ESI-6152 © Copyright 01/25/2023 MOGAS Industries, Inc. www.mogas.com
8
100 PSI 75 PSI
PRESSURE END
Preferred Sealing Seat is located
opposite the pressure end (downstream).
Pressure End is indicated on flange in this location.
When valve is in closed position,
higher pressure should be on this side.
Correct Valve Orientation
Identify Preferred Sealing Seat
2-PIECE BODY
Viewed from TOP
For correct installation, you must verify:
Flow Direction – The preferred direction of flow is from the higher pressure end (upstream)
to lower pressure end, when the valve is closed. In certain conditions, proper operation may
require the sealing seat be positioned opposed to the flow direction.
Pressure End – Always marked on the valve prior to leaving the factory.
Preferred Sealing Seat – Located opposite the marked pressure end, in the downstream
position.
The valve must be installed with the marked pressure end positioned toward the higher
pressure when in the closed position.

ESI-6152 © Copyright 01/25/2023 MOGAS Industries, Inc. www.mogas.com 9
REMOVE VALVE
Remove the valve (and operator, if supplied) carefully
from the shipping crate or pallet using lifting lugs or
nylon straps around the valve body. Do not lift by the
operator.
INSPECT VALVE
Inspect the general condition of the valve (and
actuator, if supplied) for any potential shipping
damage.
Review the valve manual, assembly drawing with the
bill of materials, and the operator manual (if supplied)
shipped with the valve.
REMOVE PROTECTIVE COVERS
Remove protective covers from the valve ends.
Inspect internally for shipping debris or damage.
VERIFY OPERATOR
If the valve was ordered with a gear or actuator from
MOGAS, it should arrive pre-assembled and tested
from the factory. If already assembled, continue with
the valve installation.
If the valve does not have a gear or actuator installed,
you must install the appropriate adaptor and operator
to the travel stops prior to valve installation.
CAUTION!
Do not install valve for pressures or temperatures
higher than rated.
THIS WILL AFFECT THE VALVE WARRANTY
AND SAFE OPERATION.
Pre-Installation
1
2
3
4
!

ESI-6152 © Copyright 01/25/2023 MOGAS Industries, Inc. www.mogas.com
10
While looking in the bore, open and close the valve.
Note:
Larger valves may require the operator to be in place to rotate the ball.
CAUTION!
The operator must not be re-oriented without
removal from the valve. Contact MOGAS service.
(Seat leakage may occur when the ball and seat
surfaces are not matched per the engineered
design.)
THIS WILL AFFECT THE VALVE WARRANTY.
The fully open position is the most important position
to set. It is preferred that the open stop be set while
the valve is not installed in the pipeline. This allows
for the bore to be properly aligned, ensuring that no
edges are exposed to the flow.
Note:
The MOGAS valve operates counter-clockwise to open, clockwise to
close.
VERIFY OPERATING POSITION
Verify that the ball open / closed position matches the
gear or actuator open / closed position indicators.
Verify that the scribed lines on the stem 05 align with
the scribed lines on the gland flange 07. These lines
are approximate indications. For best results, make
sure the lines never under travel — a minimum travel
of 97° is required.
Note:
Misalignment can result in valve under- or over-stroke, creating a
potential leak path and affecting warranty.
These procedures are for flanged end connections.
When securing other end types, please contact
MOGAS Service for proper procedures.
Notes:
Valve item numbers shown in bold correspond with items shown in the
Valve Item Reference Number section (pages 4–5) of this document.
MOGAS ships valves in the open position unless operator is fail closed.
Fully OPEN position.
Fully CLOSED position.
Installation
1
!

ESI-6152 © Copyright 01/25/2023 MOGAS Industries, Inc. www.mogas.com 11
POSITION VALVE IN PIPING
Verify that the valve and actuator / handlever
orientation is correct.
Verify that the valve is in the open position to prevent
any damage to the ball surface from debris. This is not
necessary for flanged valves.
Position the valve in line with corresponding flanges.
Note:
Support or lift as required, using lifting lugs or nylon straps around the
valve body. Do not lift or support by the actuator alone.
CAUTION!
All welding / grinding debris must be thoroughly
flushed from all associated piping before valve is
installed. Valve should always remain in the open
position.
THIS WILL AFFECT THE VALVE WARRANTY.
IDENTIFY PRESSURE END DIRECTION
Identify the preferred sealing direction of the valve,
indicated by Pressure End indicated on the valve
body 02.
Note:
The normal direction of flow is from the higher pressure end (upstream)
to lower pressure end when the valve is closed.
In certain conditions, proper operation may require the indicated flow be
opposed to the line flow. Make sure that the Pressure End is positioned
toward the highest pressure against the valve in the closed position.
SECURE VALVE IN PLACE
Install flange gaskets and bolting per industry
requirements. Always tighten in star pattern to prevent
leaks. Torque as required.
Note:
MOGAS valve flanges are supplied in the customary “straddle centerline”
hole orientation, unless otherwise specified.
VERIFY OPERATION
After installation, open and close several times to
ensure smooth operation.
Straddle centerline hole orientation
02
Installation
2
3
!
4
5

ESI-6152 © Copyright 01/25/2023 MOGAS Industries, Inc. www.mogas.com
12
All MOGAS ball valves are designed for on / off
services only.
To operate, turn counter-clockwise to open and
clockwise to close.
Note:
When cycling the valve open or close, make sure that the valve is fully
opened and fully closed. This wipes debris from the ball and ensures
optimal performance and long valve life.
OPEN / CLOSE
CAUTION!
Throttling with MOGAS isolation ball valves is
NOT recommended. Exposure of a portion of
the ball/seat to flow can compromise the sealing
integrity of the valve.
THIS WILL AFFECT THE VALVE WARRANTY.
Fully CLOSED position.
Fully OPEN position.
Partially OPEN position
(not recommended).
CLOSEOPEN
Operation
!

ESI-6152 © Copyright 01/25/2023 MOGAS Industries, Inc. www.mogas.com 13
CAUTION!
It is extremely important to follow these steps to
ensure maximum valve performance.
THIS WILL AFFECT THE VALVE WARRANTY.
!
VERIFY BOLTING TORQUE
After the first exposure to elevated temperature and
the valve has completely cooled-down, verify bolting
torque at these locations:
1Packing gland flange
2Body to end connection
3Actuator to valve mounting (if present)
Check the bolting at these same locations periodically.
CAUTION!
If bolting torque is lower than specified values on
the test certificate provided for each individual
valve serial number, re-torque bolting as necessary.
THIS WILL AFFECT THE VALVE WARRANTY.
!
OPEN / CLOSE VALVE REGULARLY
Valves remaining open or closed for a long period of
time should be cycled open / closed at least once a
year.
Valves should always be cycled full open/closed
to wipe away any media accumulation on the
sealing surfaces.
ACTUATOR LUBRICATION
Keep hydraulic and worm gear actuators fully
lubricated according to actuator manufacturer’s
specifications. See actuator manufacturer’s
specification or product manual.
2
3
1
Maintenance

ESI-6152 © Copyright 01/25/2023 MOGAS Industries, Inc. www.mogas.com
14
REMOVE OPERATOR
If operator is present, remove per instructions
provided by manufacturer, or consult MOGAS for
assistance.
CAUTION!
It is extremely important to follow these steps to
ensure maximum valve performance.
THIS WILL AFFECT THE VALVE WARRANTY.
!
Note:
Mark any matching components with a marker, tape, etc., prior to
disassembly, for ease of reassembly.
REMOVE GLAND NUTS
Remove the packing gland nuts 15 and spring discs
(live loading) 07C.
REMOVE GLAND FLANGE
Lift upward to remove the packing gland flange 07.
15
07C
07
Replace Stem Packing
1
2
3

ESI-6152 © Copyright 01/25/2023 MOGAS Industries, Inc. www.mogas.com 15
PREPARE PACKING RING SET
The fugitive emission packing ring set will contain
four rings total, (two anti-extrusion rings 09B and two
packing rings 09A).
Note:
The rings must be installed in the order shown. Refer to Bill of Materials
supplied with each individual valve serial number for specific quantity.
CAUTION!
If you have rings that contain skive cuts (see
illustration), the location of each skive cut must be
staggered or alternated during installation. This is
done to prevent formation of a possible leak path.
THIS WILL AFFECT THE VALVE WARRANTY.
Correct staggered or alternating skive
cut positioning.
!
09B
09B
09A
09B 09A
REMOVE STEM PACKING
Using a small pick or scribe, carefully remove the
fugitive emission packing material 09A and 09B.
Make sure that all of the packing is removed.
CAUTION!
Do not scratch the stem or the packing bore in the
body. Scratches could cause a leak.
THIS WILL AFFECT THE VALVE WARRANTY.
CLEAN PACKING BOX
Before installing the new packing, make sure the
packing box is clean.
If needed, use an air hose to clean debris from
packing box before installing new packing rings.
Note:
Always wear a face shield or goggles to protect eyes from flying debris.
!
Replace Stem Packing
4
5

ESI-6152 © Copyright 01/25/2023 MOGAS Industries, Inc. www.mogas.com
16
INSTALL PACKING RING SET
Note:
Applying a spray lubricant to packing ring surfaces may ease the
installation process.
Install the rings one at a time (one anti-extrusion ring
09B first, then two stem packing rings 09A, then the
final anti-extrusion ring 09B) using the gland flange
07 as a packing tool to stuff each packing ring all the
way down against the previous ring.
CHECK POCKET DEPTH
Before installing the final anti-extrusion ring 09B,
ensure there is enough depth for the anti-extrusion
ring to fit flush in the pocket.
INSTALL FINAL ANTI-EXTRUSION RING
If there is enough depth for the final anti-extrusion ring
to fit flush in the pocket, install the anti-extrusion ring
09B.
If there is not enough depth for the final anti-extrusion
ring to fit flush in the pocket, the packing rings must
be compressed.
To compress packing rings, temporarily install the
gland flange 07 over stem 05 and gland nuts 15
over gland studs 12. Install gland studs, using anti-
seize compound. Tighten all nuts evenly until there is
enough depth for the final anti-extrusion ring 09B to
fit flush into the pocket.
Once this is accomplished, remove the gland nuts 15
and gland flange 07.
Install the final anti-extrusion ring 09B.
6
7
09B
09B
12
05
07
07C
15
09A
Replace Stem Packing

ESI-6152 © Copyright 01/25/2023 MOGAS Industries, Inc. www.mogas.com 17
INSTALL GLAND FLANGE
Make sure gland studs 12 are in place. If necessary,
install gland studs 12, using anti-seize compound.
Install gland flange 07 over stem and gland studs.
Install spring discs (live loading) 07C over gland studs.
Note: Spring discs must be installed in opposing pairs. Number of spring
discs may vary depending upon size of valve.
Apply anti-seize compound onto gland studs 12 and
gland nuts 15.
Install gland nuts 15, and torque all nuts evenly per
the specifications included with the test certificate
for each individual valve serial number.
CAUTION!
The gland flange must be pulled down evenly to
prevent “cocking” or side loading, as this could
cause damage to the packing and prevent the
valve from operating properly. Watch the gland
flange to ensure that it remains perpendicular to
the stem, and the gap around the stem remains
concentric during the tightening process.
Do not over-tighten nuts. Torque all nuts evenly
per the specifications included with the test
certificate for each individual valve serial number.
THIS WILL AFFECT THE VALVE WARRANTY.
12
07C
8
!
CHECK FOR OPERATOR
If valve requires actuator, install per instructions
provided by manufacturer or consult MOGAS for
assistance.
If valve uses handlever operator, install stop plate first.
Replace Stem Packing
10
9INSTALLATION PROCEDURE
FOR STEM PACKING
After installing the packing ring set 09A and 09B
apply a gasket stress of 60 MPa. Stand by for five
minutes. Actuate the stem 05 five times. Reduce the
gasket stress until 0 MPa. Repeat this process three
times. Apply a final gasket stress per test certificate.

ESI-6152 © Copyright 01/25/2023 MOGAS Industries, Inc. www.mogas.com
18
Disassembly
!
Note:
Larger valves may require that the actuator remain installed to rotate
the ball position prior to disassembly. Secure tightly if stroking after
removing from pipe.
Larger valve / actuator combinations with limited clearance may
require removal of the valve and the actuator from piping as separate
components.
Smaller valve / actuator combinations with adequate clearance may
typically be removed from piping as one assembly.
CAUTION!
Verify that the ball is in the fully closed position
prior to actuator removal and valve disassembly.
REMOVE OPERATOR
If operator is present, remove per instructions
provided by manufacturer.
REMOVE MOUNTING FLANGE ADAPTOR
If mounting flange adaptor is present, it must be
removed.
Note:
Mark any matching components with a marker, tape, etc., prior to
disassembly, for ease of reassembly.
1
2
Before beginning any work, identify the valve model
by checking the number on the side of the valve body.
To locate the model number, see page 32, Locate
Valve Information.
Apply match marks on all mating components with
a marker, tape, etc., prior to disassembly, for ease of
reassembly.
!CAUTION!
If you disassemble, rework and re-assemble this
ball valve, YOU WILL VOID YOUR WARRANTY.
REMOVE VALVE
Remove valve from piping.
Note:
Support or lift as required.
Let valve rest on body end with bore vertical.
3

ESI-6152 © Copyright 01/25/2023 MOGAS Industries, Inc. www.mogas.com 19
Disassembly
REMOVE END CONNECTION
Remove end connection 03 from body 02 .
CAUTION!
Do not damage sealing surface inside body gasket
counter bore.
!
REMOVE BODY NUTS
Remove body nuts 11.
Place end connection on a flat surface in the vertical
position with flanged-end down.
5
4
CAUTION!
Do not damage seat pocket when removing
seat ring.
REMOVE SEAT RING
Remove seat-locking ring 61 and seat locking
screws 62 located in end connection. These must be
removed before removing seat ring 01B.
Seat locking screws are tac-welded during original
assembly. The tac should break when using the allen
wrench to remove the screws.
!
6
11
03
02
03
01B
62
61

ESI-6152 © Copyright 01/25/2023 MOGAS Industries, Inc. www.mogas.com
20
REMOVE BODY STUDS
Remove body studs 10 from body 02.
7
VERIFY CLOSED POSITION
Verify that the ball 01A has been rotated to the fully
closed position.
REMOVE BALL
Remove ball by lifting the end opposite stem 05 and
rolling it out until ball 01A is clear of body 02.
9
10
REMOVE SPRING DISC
Remove spring disc 01C from body 02.
12
REMOVE SEAT RING
Remove seat ring 01B from body 02.
11
Disassembly
CAUTION!
Do not damage sealing surface inside body gasket
counter bore.
!
REMOVE BODY GASKET
Remove body gasket 04 from body 02.
8
10
04
01A
01B
01C
02
05
15
07C
07 12
05
02
REMOVE GLAND NUTS
Remove the packing gland nuts 15 and spring discs
(live loading) 07C.
REMOVE GLAND FLANGE
Lift upward to remove the packing gland flange 07.
REMOVE GLAND STUDS
Remove gland studs 12 from body 02.
13
14
15
Other manuals for ISOLATOR 2.0
1
Table of contents
Other MOGAS Control Unit manuals
Popular Control Unit manuals by other brands
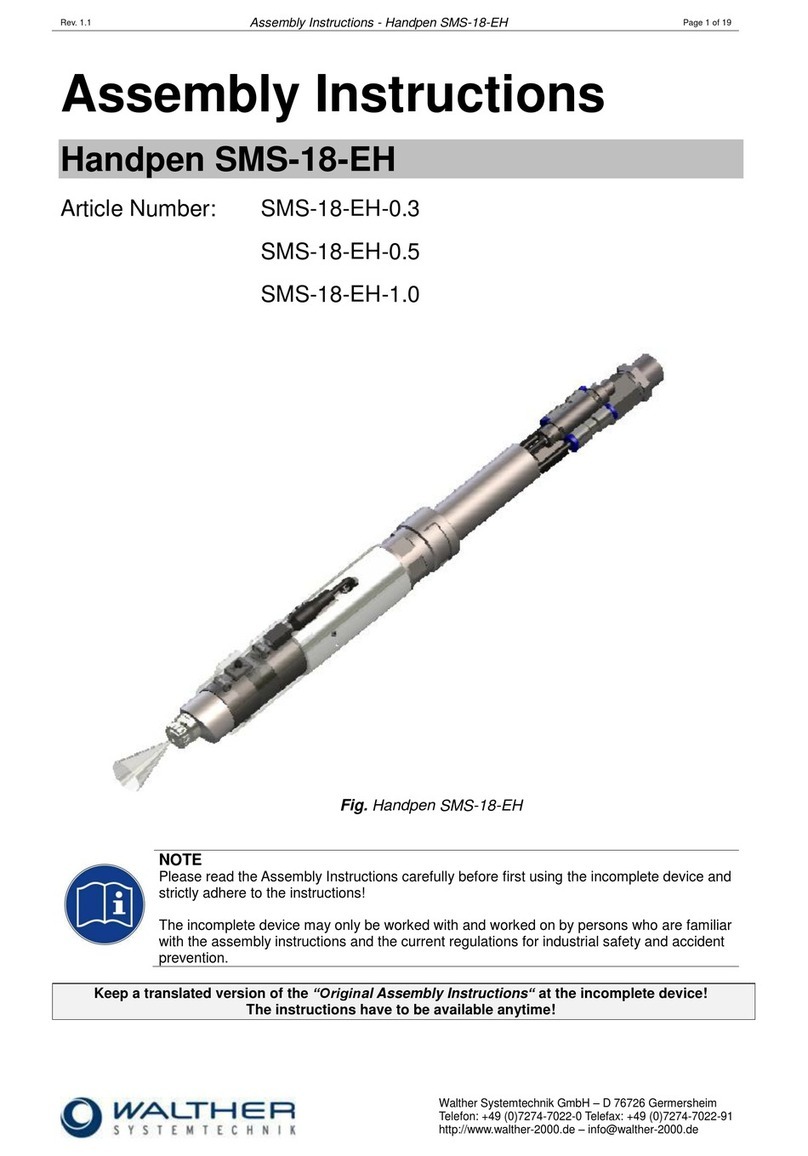
Walther Systemtechnik
Walther Systemtechnik SMS-18-EH Assembly instructions
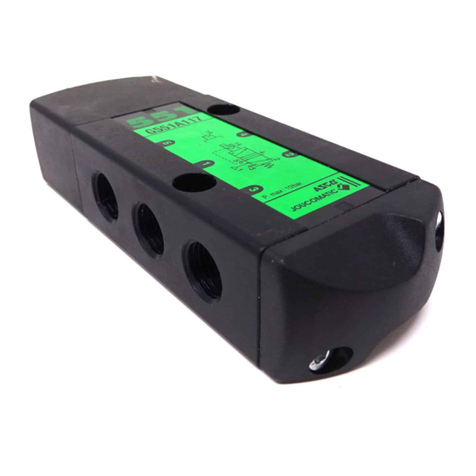
Asco
Asco 551 Series Installation and maintenance instructions

hyfire
hyfire TAURUS TAU-MO-SB-01 quick start guide
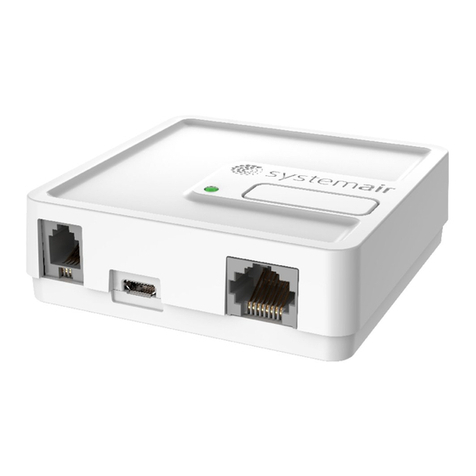
System air
System air IAM user manual
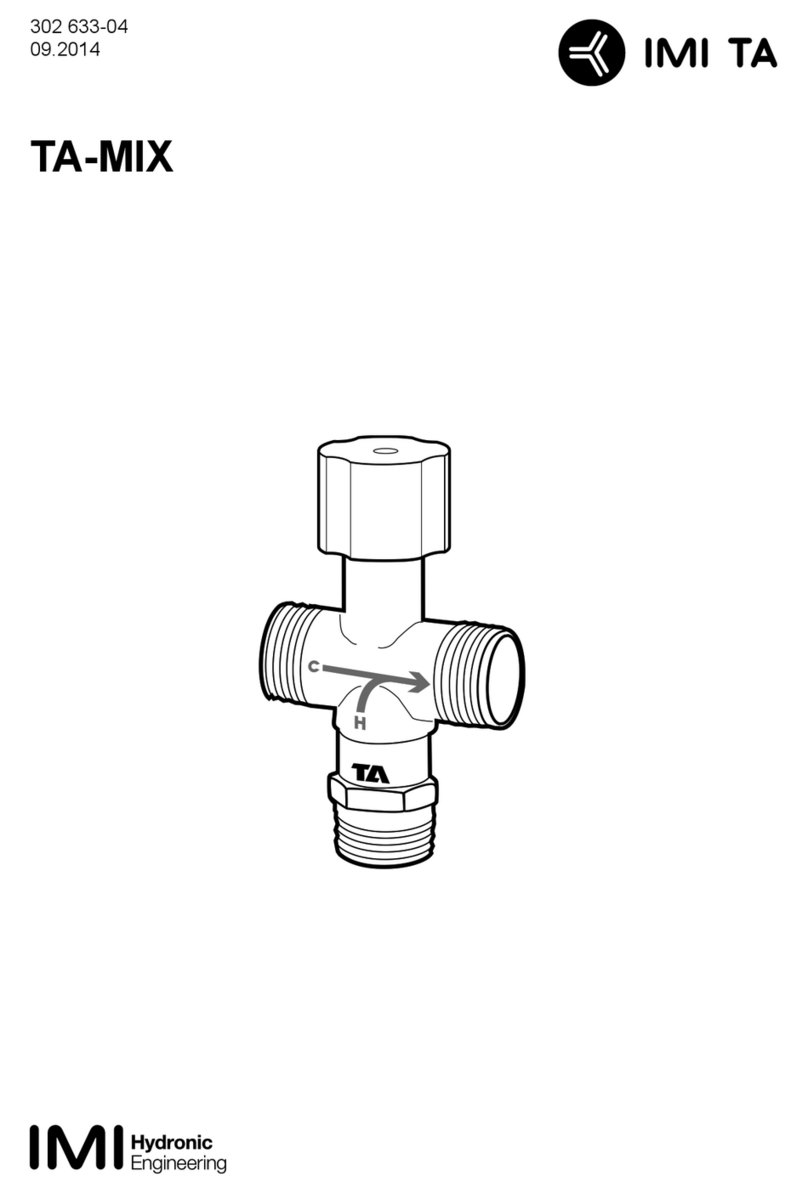
IMI Hydronic
IMI Hydronic IMI TA TA-MIX quick start guide

APARIAN
APARIAN J1939/B Series quick start guide