Moore Inductries STA User manual

STA
STA
Programmable Current/Voltage
Safety Trip Alarm
Programmable Current/Voltage
Safety Trip Alarm
April 2009
225-748-01A1
HLPRG
All product names are registered trademarks of their respective companies.

STA (HLPRG) Quick Start Guide
Use the front pushbuttons to quickly and easily set-up
the STA for your application. After programming your
alarm using the diagram below, install the unit into
your application using the connection diagrams and
terminal designation table located in this manual.
Front Panel
Pushbuttons
Use the UP and DOWN pushbuttons
to scroll through menus and sub-menus.
Use the SELECT pushbutton to access
menus and/or make a choice.
WARNING:
This menu is intended to aid
in the configuration of your instrument.
However, proper use of the STA at
its intended safety level cannot be
acheived without thorough review of the
STA in Safety Instrumented Systems Section of this manual.
Trim Analog Output:
Connect the STA into a calibration
set-up as shown in the manual and
trim the analog output.
(Requires -AO Option)
Password:
View or change password.
Configure Options:
Display mode, decimal places,
50/60Hz filter, display test and factory reset.
CONFG
OPTNS
TRIM
AOUT
Reset Fault:
Reset fault option,
select “Yes” or “No”.
CONFG
PASS
Exit Configuration Menu:
Return to process display.
CONFG
EXIT
D
D
U
CONFG
ALARM
Configure Alarm:
Set trip point, dead band,
high/low trip and
latching/non-latching.
D
SCALE
AOUT
Scale Analog Output:
Set the values for output at
zero and full input
(Requires -AO Option)
D
U
RESET
FAULT
D
D
U
CONFG
AOUT
Configure Analog Output:
Select volt or current output.
Choose damping value
and fail mode.
(Requires -AO Option)
TRIM
INPUT
Trim Input:
Match the actual reading of your
STA to a calibrated or known
value. D
U
U
U
D
U
U
U
D
U
ENTER
PASS
SYS
LOCK
Enter the password
code to enable
settings changes.
(Default = 1)
(
If the incorrect password is entered,
access to the configuration menus is denied.)
Configure Input:
Choose input type.
Security Jumper
installed in Full
Acess position.
Security Jumper
installed in No
Acess position.
Security Jumper
installed in Password
Required position.
CONFG
INPUT
SELECT
DOWN
UP
SCALE
INPUT
D
D
Scale Input:
Set the values to be displayed
at zero and full scale without
calibration equipment.

Table of Contents
Introduction............................................................................................................................................. 6
About This Manual ...........................................................................................................6
Model and Serial Numbers...............................................................................................6
STA Description................................................................................................................6
Inputs ...............................................................................................................................6
Alarms..............................................................................................................................6
Options.............................................................................................................................6
Configuration....................................................................................................................6
STA Application Examples ............................................................................ 7
AlarmTerminology ......................................................................................... 8
STA Diagnostics & Fault Alarms...................................................................9
Specifications............................................................................................... 10
Dimensions ....................................................................................................................11
Security Settings.......................................................................................... 13
Password Setting ...........................................................................................................13
STA Configuration........................................................................................ 14
View Menu .....................................................................................................................14
Main Configuration Menu...............................................................................................15
Configuring the Input......................................................................................................17
Scaling the Input ............................................................................................................18
Input Trimming................................................................................................................19
Configuring the Alarm(s)................................................................................................21
Configuring the Analog Output (-AO Option) .................................................................23

Scaling the Analog Output (-AO Option)........................................................................24
Trimming the Analog Output (-AO Option).....................................................................24
Configuring the Options .................................................................................................26
Password Configuration .................................................................................................27
Reset Fault.....................................................................................................................27
Configuration Exit...........................................................................................................28
STA Diagnostic Messages........................................................................... 28
STATransfer Utility Software....................................................................... 30
Installing the Transfer Utility Software ............................................................................30
Connecting the STA to the PC .......................................................................................30
Transfer Utility Software Summary............................................................. 31
Menu and Tool Bar Legend............................................................................................32
File Management ...........................................................................................................32
Save a File ....................................................................................................................32
Load a File ....................................................................................................................32
Installation..................................................................................................... 33
Mounting ........................................................................................................................33
Making the Electrical Connections.................................................................................33
Recommended Ground Wiring Practices.......................................................................33
CE Conformity................................................................................................................33
Operation....................................................................................................... 33
Maintenance...................................................................................................................33

Customer Support........................................................................................ 33
STA in Safety Instrumented Systems......................................................... 34
Functional Safety Description ........................................................................................34
Failure Rate Data...........................................................................................................34
Product Life....................................................................................................................34
Installation......................................................................................................................34
Configuration..................................................................................................................34
Process Safety Time ......................................................................................................34
Analog Output - Non-Safety...........................................................................................34
Sensor Types..................................................................................................................35
Broken Wire Detection ...................................................................................................35
Sensor Trimming Enable/Disable...................................................................................35
Latching Mode Enable/Disable ......................................................................................35
Remote Manual Reset ...................................................................................................35
Operation and Maintenance...........................................................................................35
Proof Test Steps.............................................................................................................36
Declaration of Conformity............................................................................ 37
Return Procedures and Warranty Information........................................... 38

6 The Interface Solution Experts
STA
Programmable Current/Voltage
Safety Trip Alarm
Introduction
This is the user’s manual for Moore Industries’ STA
(HLPRG): Programmable Current/Voltage Safety Trip
Alarm.
The Moore Industries’ Safety Trip Alarm (STA) is
designed and manufactured to provide a high level of
availability for safety critical applications and for use
as a component part of a safety instrumented system.
This manual contains all of the information needed to
configure, install, operate and maintain this product.
When the STA is used in a SIL rated safety application
(as defined by IEC 61508), the Safety Instrumented
Systems section of this manual must be read and
followed in order for the STA to meet it’s IEC 61508
certification requirements.
About this Manual
Wherever you see a “Note”, “Caution” or “WARNING”
pay particular attention.
WARNING - Hazardous procedure or condition that
could injure the operator.
Caution - Hazardous procedure or condition that
could damage or destroy the unit.
Note - Information that is helpful for a procedure,
condition, or operation of the unit.
Model and Serial Numbers
Moore Industries uses a system of model and serial
numbers to keep track of all of the information on
every unit it sells and services. If a problem occurs
with your STA, check for a tag affixed to the unit
listing these numbers. Supply the Customer Support
representative with this information when calling.
STA Description
Moore Industries’ STA (HLPRG) is a programmable
current/voltage safety trip alarm.
The STA monitors a process variable and provides
two fully user-configurable contact closure outputs
that can be individually programmed to trip whenever
the input falls outside a user-set, high or low trip point.
It also has one fault alarm output which is triggered by
a self-diagnosed failure of the input or the STA itself.
The STA is typically used to activate a warning light,
bell or buzzer; or to initiate a system shutdown. Thus,
the instrument acts as a simple, but highly reliable and
effective means of monitoring and safe-guarding a
process.
The STA is configured using front panel push
buttons and a configuration can also be saved and
downloaded using the PC transfer utility. A large
5-digit display shows menu prompts during push
button configuration and process variable and status
messages during normal operation.
Inputs
The STA (HLPRG) supports either current inputs from
0-50mA (1mA minimum span) or voltage inputs from
0-10V (250mV minimum span). These inputs can be
trimmed and scaled, refer to the Configuring Inputs
section of this manual for additional information.
TX Power
A transmitter excitation power supply (24Vdc
±10%@24mA) is standard on the STA (HLPRG). You
may access this externally at the terminals shown in
Figure 5.
Alarms
The STA has three (-3PRG) contact closure alarms.
One relay is factory configured as a Fault alarm and
the remaining two relays are user-configurable Trip
alarms. A dual color LED (Red/Green) is provided
with each alarm to indicate its condition.
The fault alarm trips on a self-diagnosed failure
within the STA or on any of its inputs. This alarm is
latching and has to be reset by the user. Only user
configuration faults will clear automatically once the
configuration is valid. Input faults can be cleared by
the “RESET FAULT” menu, and self-diagnosed faults
can only be cleared by power cycling the unit. For
more information refer to the Diagnostics and Fault
Alarm section.
The Trip alarms are configurable for high or low trip
with an adjustable dead band. These alarms can be
latching or non-latching. Latched alarms are reset
through the Manual Reset (MR) terminals.

The Interface Solution Experts 7
STA
Programmable Current/Voltage
Safety Trip Alarm
This configuration (Figure 2) offers higher system
availability. The Fault alarm is wired separately to
inform the safety system that there is a fault alarm
and that this component’s ability to carry out its
portion of Safety Instrumented Function cannot
be performed. This configuration can be used in
applications where it is safe to keep the process
running for a short time while a defective instrument
is repaired. The output process trip relays are
connected 1oo2 to trip providing security against a
single relay failure, however this configuration will
NOT trip if an STA fault is diagnosed.
This type of configuration must be used with care in a
safety system. The end user must determine how long
the process is allowed to continue after a STA fault is
detected and ensure that the unit can be repaired or
replaced within this time.
STA Application Examples
The following are examples of typical STA
configurations.
NC1
CM1
NO1
NC2
CM2
NO2
NC3
CM3
NO3
Final Element
READY INPUT TRIP 1 TRIP 2 FAULT
SELECT
DOWN
UP
COM
STA
SAFETY
TRIP
ALARM
TAG
126.39
DEG C
Process
Trip 1
Process
Trip 2
Fault
Alarm
NC1
CM1
NO1
NC2
CM2
NO2
NC3
CM3
NO3
SELECT
DOWN
UP
COM
READY INPUT TRIP 1 TRIP 2 FAULT
17.29
MA
STA
SAFETY
TRIP
ALARM
TAG
Process
Trip 1
Process
Trip 2
Fault
Alarm Logic Solver/
SIF Alarm
Final Element
The relay outputs have a 3A@250Vac or 3A@30Vdc,
50/60Hz non-inductive contact rating. The contact
arrangement is SPDT. All outputs are fail safe and
will de-energize to trip (DET) with NO & NC relay
contacts.
Refer to the Alarm Terminology and Configuring
the Alarms sections of this manual for additional
information.
Options
Analog Output (-AO)
The Analog Output can be configured to provide a
voltage (0-10V) or current (0-20mA) output. The
current output can be sink or source. Refer to the
Configuring the Analog Output section of this manual
for additional information.
Note:
The Analog Output is not part of the safety path in
the STA.
Configuration
The STA can be configured from either the front panel
keyboard or by downloading a proven configuration
using the PC Transfer Utility.
This configuration (Figure 1) offers the highest trip
integrity. Since all three relays are wired in series,
any trip alarm or STA fault will trip the final element
or logic solver. This provides security against one
process relay failure and any unit failures. However
this configuration is vulnerable to spurious trips as
STA safe failures will also trip the final element.
Figure 1. High Integrity example
Figure 2. High Availability example

8 The Interface Solution Experts
STA
Programmable Current/Voltage
Safety Trip Alarm
Alarm Terminology
Before setting up the STA, or incorporating the unit
in your application, Moore Industries suggests that
all users take a few moments to become familiar with
some of the terms associated with the use of process
instrumentation alarms. Figure 3 illustrates the way
the STA alarms operate.
The Trip Point is the process input level at which the
user wants an alarm relay to change state, typically
going into an alarm condition, or “tripping”. In the
STA, the user sets the trip point for each installed
relay.
High/Low Alarms; High Alarms trip when the
process input goes above the trip point. Low Alarms
trip when the process input drops below the trip point.
Each of the STA relay outputs can be set by the user
to function independently as either high or low alarms.
Latching and Non-latching Alarms; once tripped,
a latching alarm remains in an alarm state until the
input returns to a non-alarm level AND is manually
reset. Non-latching alarms return to a non-alarm
state whenever the process input returns to the Reset
Point. The STA relays can be set by the user to
function as either latching or non-latching.
The Reset Point is the process input level at which
the user wants an alarm relay to change state,
typically going from alarm to non-alarm. The reset
point is not necessarily the same as the trip point,
because most applications call for a buffer zone or
dead band around the trip point to allow for minute
fluctuations in the process input. In the STA, the
reset point is determined by the dead band setting.
Latching STA alarms will not “clear” unless the reset
point has been reached or passed AND the manual
reset contacts have been shorted.
The Dead band is the range in which an alarm
remains tripped even after the process input has
returned to or passed the trip point. Dead band is not
required. When it is not incorporated into an alarm
application, the trip point and reset point are the
same. The dead band of the STA is set by the user.
Failsafe Alarms are de-energized when tripped,
energized when the process input is at a non-alarm
level. Non-failsafe alarms are energized whenever
tripped, de-energized when the process input is at
a non-alarm level. The relays in the STA are failsafe
only.
Normal is the term used to describe the “shelf-state”
of relay contacts. The contacts of a Normally Open
relay are open (infinite resistance) when the relay is
not energized. The contacts of a Normally Closed
relay are open when the relay is energized (closed
when not energized).
Note:
Sometimes a non-alarm input level is
referred to as being in a “normal” condition.
This practice is intentionally avoided in this
manual. Do not confuse the term “normal”,
as in Normally Open or Normally Closed, with
a non-alarm input condition. In this manual,
“normal” is an exclusive reference to the shelf
state or quiescent state of an alarm’s relay
contacts, whether open or closed.
Figure 3. How Alarms Work with the Process Input
HIGH ALARM
TRIP POINT
LOW ALARM
TRIP POINT
DEADBAND
RESET
DEADBAND
RESET
IN ALARM
IN NON-ALARM
TIME

The Interface Solution Experts 9
STA
Programmable Current/Voltage
Safety Trip Alarm
STA Diagnostics & Fault Alarms
The STA has a high level of diagnostic capability to
continually monitor itself and its input. This section
outlines these diagnostics and functionality of the
alarms. For a full list of diagnostic messages and
corrective actions please refer to Table 7.
Internal diagnostics
On power up the unit runs through a thorough
diagnostic test (RAM and ROM TEST messages are
displayed) and an initialization process (SYS INIT
is displayed) before the fault alarm is cleared. If
any failure is found during power up, the fault alarm
will not be cleared and an error message will be
displayed. Once in operation, the unit continues
diagnostic tests in the background and will set the
fault alarm on any failure.
All internal diagnostic faults are latched on the fault
alarm relay. The fault alarm must be cleared by power
cycling the unit. If a fault is still present on power
up then please contact Customer Service for further
assistance.
Note:
The trip alarms are independent from the
fault alarms and will be unaffected by the fault
alarms (however they may be affected by the
specific failure in the unit).
Configuration diagnostics
On power up the stored configuration is validated. If
it is invalid then the fault alarm will be set. To clear
the alarm, use the menu system, to reset to the
factory configuration (FCTRY CONFG selection in the
options menu), then configure as appropriate for the
application.
Before saving a new configuration to the unit, it will be
checked for validity. If it is invalid, the fault alarm will
be set. Once the configuration is corrected, the fault
alarm will be cleared.
Input diagnostics
The STA has extensive hardware diagnostics of the
input to detect broken wire and saturation. It also
detects out of range and linearization errors.
Broken wire is automatically set on the STA and
enables the system to distinguish between a low
trip condition (which sets the trip alarm) and a failed
transmitter or open input (which sets the fault alarm).
See Configuring the Input for more information.
WARNING:
For high level inputs, if Lower Range value is set to
0(V/mA) then broken wire detection is disabled and
the safety function is invalidated.
All input faults are latched on the fault alarm relay.
The fault alarm can be cleared by first clearing the
input failure and then using the configuration menus
to reset faults. If there is degradation of sensor wires,
false readings could occur before the wire breaks
and the trip alarm could be activated before the fault
alarm. (Slow degradation is characterized by events
that occur over a span of a second or so).
Note:
The trip alarms are independent from the
fault alarm and will be unaffected by the fault
alarm. Therefore if the trip alarm has already
been activated it will remain so but will
NOT be activated by a broken wire or input
saturation error. For broken wire detection,
this only applies if the input is immediately
broken. If there is degradation present such
that on the way to being broken, the input
(current or voltage) enters the region between
the low alarm trip point and the broken wire
level, the low trip alarm WILL be tripped.
(Slow degradation is characterized by events
that occur over a span of a second or so)

10 The Interface Solution Experts
STA
Programmable Current/Voltage
Safety Trip Alarm
Specifications
Input Range: Current Input
0-50mA (1mA minimum
span); Voltage Input 0-11V
(250mV minimum)
Input Accuracy and Alarm
Trip Repeatability:
Current inputs, 2microamps
(0.01% of 20mA span);
Voltage inputs, 1mV (0.01%
of maximum span)
Overall Accuracy:
The overall accuracy of the
unit is the combined input
and output accuracies. It
includes the combined
effects of linearity, hysteresis,
repeatability and adjustment
resolution. It does not include
ambient temperature effect.
Stability: Refer to
Table 1
Dead Band: 11V or 50mA,
maximum in Linear Mode;
equivalent of maximum input
range in user-set engineering
units in Scaling/Custom Mode
Input to OutputTrip
ResponseTime:
256msec maximum from step
change on input to alarm
state change when alarm is
set to trip at mid-point of step
AlarmTrip Delay:
Programmable from 0-120
seconds
Isolation: 500Vrms between
case, input, output, and
power
Dielectric Strength: 1966Vdc
for 2 seconds, between case,
input, output, and power
Power Supply:
24DC range, 18-30Vdc; UAC
range, 90-260Vac
Power Consumption:
3.5W maximum for DC
supply; 4W maximum for UAC
supply
Power Supply Effect:
±0.002% of span per 1% line
voltage change
Input Over-Range
Protection: Current,
±100mA, maximum; Voltage,
±30Vdc, maximum
Input Impedance: Current,
20 ohms; Voltage, 1Mohm
Ambient
Conditions
(continued)
Adjustments
Weight
TX Power Supply: 24Vdc,
±10% @ 24mA (regulated)
Output Relays
Dual Process Relays and One
Fault Relay (Relays are
single-pole/double-throw SPDT,
1 form C, rated 3A@250Vac or
3A@30Vdc, 50/60Hz,
non-inductive)
Non-Safety-Critical Analog
Output Option
Output Accuracy: Current,
±0.01% of maximum span
(±2 microamps); Voltage,
±0.01% of max. span (±1mV)
Input to Analog Output
ResponseTime:
256msec for the output to
change 10% to 90% of its scale
for an input step change of 0 to
100%
Analog Output Step
ResponseTime:
100msec maximum
Analog Output Ripple (up to
120Hz): 50mV peak-to-peak
maximum on voltage output;
10mV peak-to-peak measured
across a 250 ohm load resistor
for current output
Analog Output Current
Limiting:
Current outputs,
Voltage output, -0.50 -11.0V
Load Capability: Source mode
(internal power supply),
0-1 kohms for current output;
2 kohms for voltage output; Sink
Mode (External Power Supply),
42Vdc Max.
Load Effect (current outputs):
±0.01% of span from 0 to
maximum load resistance on
current output
Operating Range:
-40°C to +85°C
(-40°F to +185°F)
Relay Range:
-40°C to +85°C
(-40°F to +185°F)
Storage Range:
-40°C to +85°C
(-40°F to +185°F)
AmbientTemperature Effect:
Current, 2 microamps/°C;
Voltage, 1mV/°C; Output,
±0.009% of max. span/°C
Relative Humidity:
0-95%, non-condensing
RFI/EMI Protection:
20V/m@80-1000MHz, 1kHz
AM, when tested to IEC61326
with 0.5% of span or less error
Noise Rejection: Common
Mode, 100dB@50/60Hz
Normal Mode, Current Input,
70dB typical @ 50mAp-p@
50/60Hz; Voltage Input, 70dB
typical@1Vp-p@ 50/60Hz
Front panel push-buttons for
parameter configurations;
Internal jumper and menu
password protect parameter
settings
LCD: 2x5 14-segment
characters, backlit,
alphanumeric readout
accurate to the nearest digit.
Range: -99999 to 99999;
Decimal point can be user-set
LEDType:
INPUT LED:
Dual color LED
indicates input failure
READY LED: Green LED
indicates unit is operating
properly
ALARM 1 and 2 LED: Dual
color LED per relay indicates
alarm status
FAULT LED: Green LED
indicates unit is operating
properly; Red LED indicates
unit has fault or is latched.
Display Accuracy:
±1 digit; when scaling the
display (or in custom mode),
high input-to-display span
ratios decrease display
accuracy
513 g to 564 g
(18.1 oz to 19.9 oz)
Ambient
Conditions
Indicators
Performance
of Analog
Output
(-AO Option)
Performance
(continued)
Specifications and information subject to change without notice.
0-20mA 0, 23.6mA
4-20mA 3.6, 23.6mA
X-20mA
(0<X<4)
Output Failure Limits
(90% of X), 23.6mA
Performance
Input to Non-Safety Critical Analog Output (Years) Input to Relay (Years)
Stability
(% of maximum span)
Current Inputs
Voltage Inputs
1yr
0.081
0.093
3yrs
0.14
0.16
5yrs
0.18
0.21
1yr
0.047
0.066
3yrs
0.81
0.114
5yrs
0.105
0.147
Table 1. Long-Term Stability

The Interface Solution Experts 11
STA
Programmable Current/Voltage
Safety Trip Alarm
Figure 4. STA (HLPRG) Dimensions
C
L
100mm
(3.9 in)
52mm
(2.06 in)
47mm
REF.
REF.
(1.87 in)
118mm
(4.6 in)
131mm
(5.17 in)
136mm
(5.35 in)
123mm
(4.8 in)
READY INPUT TRIP 1 TRIP 2 FAULT
SELECT
DOWN
UP
COM
55mm
(2.1 in)
STA
SAFETY
TRIP
ALARM
TAG
REF.
REF.
Table 2. STA (HLPRG) Terminal Designations
InputType
Current
Voltage
TopTerminals (Left to Right)
KEY:
AC or DC = Power Input
ACC or DCC = Power Input
CM = Relay Common
GND = Ground
NOTES:
1. Terminal blocks can accommodate 14-22 AWG solid
wiring.
2. ±Io/±Vo labeling is present only when the unit is equipped
with the Analog Output (-AO) option.
3. Your input power requirement (AC or DC / ACC or DCC)
will depend upon your unit’s power need.
MR MR -Io Source
+Io Sink +Vo -Vo
-Io Sink
OutputType
Fault Alarm
(SPDT Relays)
MiddleTerminals
(Left to Right)
Io = Current Output
MR = Manual Reset
NO = Normally Open
NC = Normally Closed
Sink = Current Sink
Source = Current Source
SPDT = Single-Pole/Double-Throw
Vo = Voltage Output
+Io Source
Output/PowerType
3PRG
(SPDT Relays)
BottomTerminals (Left to Right)
Not
Used GND
NO CM1 NC1 NO2 CM2 NC2
AC
or
DC
ACC
or
DCC
NO3 CM3 NC3
TX +I COM Not
Used
TX Not
Used COM +V MR MR -Io Source
+Io Sink
+Io Source +Vo -Vo
-Io Sink
T1 T2 T3 T4 T5 T6 T7 T8 T9 T10
11 12 13
B1 B2 B3 B4 B5 B6 B7 B8 B9 B10

12 The Interface Solution Experts
STA
Programmable Current/Voltage
Safety Trip Alarm
Figure 5. STA (HLPRG) Hook-Up Diagram
VOLTAGE
SOURCE
_
+
CURRENT
SOURCE
_
+
2-WIRE
TRANSMITTER
_
+
AC OR DC
POWER
SUPPLY
GND - +
SELECT
DOWN
UP
COM
READY INPUT TRIP 1 TRIP 2 FAULT
STA
SAFETY
TRIP
ALARM
TAG

The Interface Solution Experts 13
STA
Programmable Current/Voltage
Safety Trip Alarm
Security Settings
The password security function of the STA is
controlled by a single jumper inside the top of the
unit housing. You will need to remove the top cover
in order to access the jumper. The password jumper
setting will default to Password Required (Pins 1
and 2).
The default security password is 1. This is valid until
the password is changed to another value.
REMOVE PANEL
BY UNSCREWING
TOP FOUR SCREWS
SET PASSWORD SECURITY
PASSWORD SECURITY
IS OFF. NO PASSWORD
REQUIRED.
PASSWORD SECURITY
IS ON. PASSWORD
REQUIRED.
NO ACESS.
BACK
STA (HLPRG) TOPSIDE
FRONT
Password Setting
The STA can operate in one of three password modes.
Full Access (Security Jumper set to Pins
2 and 3)– Complete access to the STA configuration
menu is permitted with no password required for any
read or write operations.
Figure 6. Setting the Internal Jumper for Password Security ON or OFF
Password Required (Security Jumper set to
Pins 1 and 2)– A one to four-digit access code is
required to gain access to the STA configuration
menu. If the correct code is entered, full read and
write operation is permitted. If an incorrect code is
entered, “WRONG PASWD” will appear for 3 seconds,
and return user to View menu, with read-only access
to the View menu (see Figure 7).
No Access (Security Jumper removed)– The user
is limited to read-only access to the View menu.
“SYS LOCK” will appear if user attempts to enter Main
menu by entering “SEL”. Enter “SEL” a second time to
return to View Menu.
Note:
These security settings are only applicable to
access via the front panel pushbuttons. Security
can be bypassed using the Transfer Utility Software.
See Transfer Utility Software section for more
information.

14 The Interface Solution Experts
STA
Programmable Current/Voltage
Safety Trip Alarm
STA Configuration
The STA (HLPRG) operating parameters are set using
the pushbuttons found on the instrument’s front panel.
This section describes the steps in order to configure
your STA.
There are three pushbuttons on the unit’s front panel;
UP,DOWN and SELECT. Together with the prompts
displayed on the LCD, these are used to access
menus, and to view and change the settings.
Use SELECT as your “Enter” button, to make your
selections.
Use the UP and DOWN buttons to navigate within the
menus.
View Menu
Figure 7 gives an overview of the View menu.
Upon power-up, the STA displays a ‘SYS INIT’
message until the power up self test is complete.
In normal operation the View menu will display the
variable as configured. This can be the process
variable, the analog output variable, or both being
toggled (Refer to Configuring the Options Menu for
more details).
1. From the display, press DOWN.
2. If the -AO option is present, and the unit is
NOT configured to toggle, the other variable
will be displayed. Continue pressing DOWN
to view the Analog output zero, Analog output
full, trip point (AL1), trip point (AL2) and finally
returning to display measured value.
3. Enter Main Menu at any point by pressing
SELECT.
TOP LEVEL
MENU
(Display of Variable)
MAIN Menu
MAIN Menu
MAIN Menu
MAIN Menu
MAIN Menu
MAIN Menu
D
D
D
D
U
If toggling vars
If toggling vars
If no Analog Output
If no Analog Output
D
U
U
SEL
U
U
U
U
Display of
other var
XXXXX
ZERO
XXXXX
FULL
XXXXX
AL1 X*
XXXXX
AL2 X*
D
SEL
SEL
SEL
SEL
SEL
Figure 7. View Menu
Note:
If the Security jumper is removed (see Figure 7.)
entering SELECT will cause “SYS LOCK” to appear
if user attempts to enter Main menu.
Under fault conditions, the STA will display the error
message describing the fault (see Table 7 for list of
messages) which can be cleared from the Reset Fault
menu or by power cycling the unit.

The Interface Solution Experts 15
STA
Programmable Current/Voltage
Safety Trip Alarm
Main Configuration Menu
Figure 9 gives an overview of the Main Configuration
menu.
Upon power-up, the STA displays the variable(s) as
configured via the Configure Options menu. Pressing
the SEL button accesses a series of displays that
show, in succession, the settings currently stored in
unit memory.
Depending upon whether or not the Security Jumper
has been installed (Figure 6), pressing SELECT will
access either the first screen in the main configuration
menu, “CONFG INPUT”, the password code query
screen, “ENTER PASS” or the “SYS LOCK” screen.
Once the Main Menu has been accessed, the DOWN
button is used to move through all of the sub-menus
in a loop. Pressing the SELECT button accesses the
first screen of the sub-menu shown on the LCD.
Note:
STA is programmed to time out from the
configuration menu after 5 minutes of inactivity.
When trimming the unit, 30 minutes of inactivity are
allowed before the time out. If the unit times out, the
previous settings will be reapplied.
Password
This menu is bypassed if the Password Security is
OFF (if the jumper is not installed then no access is
allowed). To access the security jumpers, you must
remove the top cover (refer to Figure 6). Refer to the
Password Configuration section of this manual for a
more detailed description of the password feature.
1. If the Password Security is ON, pressing
SELECT from the display of the process
variable input will bring up the “ENTER PASS”
screen.
2. Press SELECT again to enter the “PASS”
screen. Use the UP and DOWN buttons
to select correct password (default value is
“1”). When the password is displayed, press
SELECT.
Note:
If the correct password is not known, the
password can be determined by either setting
password security to OFF and entering the
menu system, or using the PC Transfer Utility
to download a configuration with a known
password.
3. If you have entered the correct password, the
sensor configuration menu, “CONFG INPUT”,
will be accessed. If not, the display will show a
“WRONG PASS” message.
4. From “WRONG PASS”, wait three seconds to
go back to the View menu. Use the UP and
DOWN buttons to view the settings in the View
menu.
Note:
The menu to set or change the password stored
in STA memory is detailed in the Password
Configuration section of the manual.

16 The Interface Solution Experts
STA
Programmable Current/Voltage
Safety Trip Alarm
PROCESS VALUE
DISPLAY
SEL (Full access)
SEL (No Access)
SEL LOCK MODE
SEL (PW required)
CONFG
INPUT
SCALE
INPUT
SEL
SEL
CONFG INPUT
menu
SCALE INPUT
menu
D
D
U
U
U
TRIM
INPUT
SEL TRIM INPUT
menu
CONFG
AOUT
SCALE
AOUT
D
U
CONFG
EXIT SEL
CONFG
ALARM
SEL CONFG ALARM
menu
CONFG EXIT
menu
D
CONFG
OPTNS
SEL CONFG OPTNS
menu
D
U
CONFG
PASWD
SEL CONFG PASWD
menu
RESET FAULT
D
U
RESET
FAULT
SEL
D
U
U
If no
-AO option
D
U
SEL CONFG AOUT
menu
SEL SCALE AOUT
menu
TRIM
AOUT
D
U
SEL TRIM AOUT
menu
If no
-AO option
D
D
U
ENTER
PASS
SYS
LOCK
WRONG
PASS
SEL
PASS
XXXX
U = Inc. count
D = Dec. count
SEL (if correct PW)
SEL (if incorrect PW)
U = UP Key
D = DOWN Key
SEL = SELECT Key
U = No action
D = No action
PW = Password
UP
VIEW
menu
DOWN
VIEW
menu
Figure 8. Main Menu

The Interface Solution Experts 17
STA
Programmable Current/Voltage
Safety Trip Alarm
Configuring the Input
Figure 9 gives an overview of the Configuration Input
menu. This allows you to select type of signal input
used with the STA unit.
If the Password Security is OFF, the password
sub-menu is bypassed, and the “CONFG INPUT”
menu is accessed by pressing SELECT from the View
menu.
1. From the “CONFG INPUT” display, press
SELECT.
2. At “INPUT TYPE” press SELECT. Use the UP
or DOWN arrow buttons to scroll and select
from “CURNT” or “VOLTS”, for input type. The
default display for this menu is always the
current configuration.
3. When the display shows the type of input that
you choose to use, press SELECT.
4. Next, the “INPUT ZERO” appears. Press
SELECT and use the UP or DOWN buttons to
define the input range. Press SELECT when
correct value has been displayed.
WARNING
For HIGH LEVEL INPUT, the Lower Range Value
(LRV) must be set higher than zero. If set to zero,
Broken Wire Detection will be disabled and the
safety function is invalidated.
5. Next, the “INPUT FULL” appears. Press
SELECT and use the UP or DOWN buttons to
define the input range. Press SELECT when
correct value has been displayed.
Note:
If the input variable goes 1% out of the range
defined by INPUT ZERO and INPUT FULL, the fault
relay will latch in an error state, and the ERROR
OOR (Out of Range) status message will be
displayed.
6. Next, the “BWIRE” appears. Press SELECT
and use the UP or DOWN buttons to define
the point at which broken wire error will be
activated. Press SELECT when correct value
has been displayed.
Note:
Broken Wire Detection “BWIRE” can only be set if
the Lower Range Value (LRV) is set higher than zero
(refer to the “INPUT ZERO” step 4).
Figure 9. CONFG INPUT Menu
CONFG
INPUT
D
U
D
U
INPUT
TYPE
INPUT
ZERO
INPUT
FULL
SEL
D
U
U
Selection:
CURNT
VOLTS
SEL
SEL
SCALE INPUT menu
SEL
SEL
Value Change:
XX.XX
Sensor EGU
SEL
SEL
SEL
SEL
D
U
EXIT
INPUT
BWIRE
LEVEL
Value Change:
XX.XX
Sensor EGU
Value Change:
XX.XX
Sensor EGU
D
U
7. “EXIT INPUT” appears. If all values in this
parameter have been set, press SELECT. If
not, return to the menu and set your values.
8. The next display is the “SCALE INPUT” menu.
To skip the rest of the configuration menus and
return to the process variable display, press
the DOWN until you reach “CONFG EXIT”,
and press SELECT. Refer to “CONFG EXIT”
section of this manual for more information.

18 The Interface Solution Experts
STA
Programmable Current/Voltage
Safety Trip Alarm
Figure 10. SCALE INPUT Menu
Scaling the Input
Figure 10 gives an overview of the Input Scaling
menu.
Scaling allows you to take your PV (Process Variable)
reading and transform it to a custom engineering units
range. PV is the unit read after selecting your input
type. For example, choosing a Current input would
then produce a PV displayed in mA.
Also known as “Smart Ranging”, scaling of the STA
(TPRG) allows you to set the zero and full scale
values of the input from the intended application,
without having to connect the unit to any calibration
equipment.
1. At the “SCALE INPUT” display, press SELECT.
2. “SCALE MODE” appears; press SELECT.
Choose whether or not to enable scaling. This
will be configured in the next menu. Select
“SCALE OFF” or “SCALE ON” and press
SELECT.
Scale Mode– This allows you to customize
your display for your application. For example,
if your process is sending a 6mA-17mA
reading to the STA and you wish to view
the input as 0-100% then this can be
accomplished with the Scale Mode feature.
3. The “SCALE EGU” prompt is brought up.
Press SELECT and choose the desired five
character string to be displayed. While editing
the string, the current position being edited
will be alternated with a “^” character. Use the
UP and DOWN button to select the correct
character. Pressing SELECT will move to the
next position.
If you selected “SCALE OFF” in the “SCALE
MODE” menu, the menu skips to Step 6. If you
selected “SCALE ON”, proceed to Step 4.
4. Next, “SCALE ZERO” is displayed. Use the UP
and DOWN buttons to adjust your scaled zero
value. This is the value that will be displayed
when you are at the zero end of the input
range. Press SELECT.
D
D
D
D
D
U
U
U
U
U
SCALE
MODE
SCALE
EGU
SCALE
ZERO
SCALE
FULL
EXIT
SCALE
SCALE
INPUT
SEL
D
SEL TRIM INPUT menu
U
Selection:
SCALE ON
SCALE OFF
SEL
SEL ON
SEL OFF
SEL
SEL
SEL
SEL
Set Chars:
X----
SEL
Value Change:
XX.XX
SCALED EGU
SEL
Value Change:
XX.XX
SCALED EGU
5. “SCALE FULL” appears. Press SELECT to
enter the menu. Enter the value you wish as
your full scaled range. This value will appear
when you are at the full end of your range.
Press SELECT.
6. “EXIT SCALE” appears. If all scaling
parameters have been set, press SELECT.
The next menu selection to appear is “TRIM
INPUT”.

The Interface Solution Experts 19
STA
Programmable Current/Voltage
Safety Trip Alarm
InputTrimming
Figure 11 gives an overview of the Input Trimming
menu.
Sensor trimming increases the measurement
accuracy of your instrument by matching the reading
of its actual input to its scaling. The STA offers the
use of a factory-configured trimming feature (“FCTRY
TRIM”) or user-set, one-point or two-point (“USER 1
PNT” OR “USER 2 PNT”) trimming.
Unit default is “FCTRY TRIM”. If another trimming
selection had been made and you wish to return to
the “FCTRY TRIM” feature follow the instructions
below.
1. Press SELECT at the “TRIM INPUT” screen.
Once “TRIM MODE” appears, press SELECT.
2. Use the UP and DOWN buttons to reach
the “FCTRY TRIM” display, and then press
SELECT. This takes you to the “EXIT TRIM”
screen.
3. To exit, press SELECT. Proceed to the
“ALARM CONFG” menu
To input user-specific trim values, perform the
following steps: Refer to Table 6 for necessary
equipment.
1. At the “TRIM INPUT” display, press SELECT.
When “TRIM MODE” appears, press SELECT
again. Use the UP and DOWN buttons to
reach the user-set trimming menus. Press
SELECT once the desired parameter is
displayed– “USER 1 PNT” or “USER 2 PNT”.
2. “RESET TRIM ” appears, press SELECT. Use
the UP and DOWN buttons to the desired
parameter, “RESET NO?” or “RESET YES?”.
Select “RESET YES?” to clear previous
trimming adjustment values, or “RESET NO?”
to keep them.
Resetting will keep trimming enabled, however
no adjustment will be made to the input value.
If the input is about to be trimmed, then this
step is unnecessary
3. “TRIM ZERO” appears. To program, press
SELECT. Your present zero-scale trimming
value is shown, use the UP and DOWN
buttons to change value, to “APPLY” your
value; press SELECT. Once your value is
present and flashing, press SELECT again.If
you selected “USER 1 PNT” trimming, “EXIT
TRIM” appears. Press SELECT to reach the
“CONFG ALARM” menu. Proceed to Step 4
for “USER 2 PNT” trimming.
4. If you selected “USER 2 PNT” trimming, repeat
the instructions in Step 2 for the “TRIM FULL”
setting. Press SELECT when “EXIT TRIM”
is displayed to reach the “CONFG ALARM”
menu.
Note:
In the event that captured values for TRIM ZERO
and/or TRIM FULL are incorrect, ERROR TRIM
will be displayed after values are applied. Press
SELECT to exit ERROR TRIM, which will prompt
EXIT TRIM. Use the UP and DOWN buttons to
return to TRIM ZERO and/or TRIM FULL to make
changes needed.

20 The Interface Solution Experts
STA
Programmable Current/Voltage
Safety Trip Alarm
Figure 11. TRIM INPUT Menu
TRIM
MODE
D
U
RESET
TRIM
Selection:
RESET NO
RESET YES
D
U
TRIM
ZERO
D
U
D
U
U
TRIM
FULL
TRIM
INPUT
SEL
SEL
U
SEL
SEL
Change Value:
XX.XX
APPLY
SEL
Capture Value:
XX.XX
(Flashing)
SEL FCTRY TRIM
FCTRY TRIM
FCTRY TRIM
Selection:
FCTRY TRIM
USER 1 PNT
USER 2 PNT
D
EXIT
TRIM
SEL
SEL
Change Value:
XX.XX
APPLY
SEL
Capture Value:
XX.XX
(Flashing)
SEL
USER 1PT
SEL 1PT
SEL 2PT
USER 1PT
1PT
SEL 2PT
ERROR
TRIM
SEL
ERROR
TRIM
SEL
SEL
CONFG ALARM menu
Table 6. Necessary Equipment to Configure Input trimming on the STA (HLPRG)
Device Specifications
Power Supply
Multimeter
24Vdc, ±10% or 117/230Vac, 110Vdc (depending on model)
Accurate to ±0.009% of span; e.g., HP Model 3478A
Current or Voltage, 2-Wire Variable; Accurate to ±0.05% of unit span
Table of contents
Popular Security System manuals by other brands

HumanTechnik
HumanTechnik iBell Operation instructions

NAPCO
NAPCO Prima quick start guide
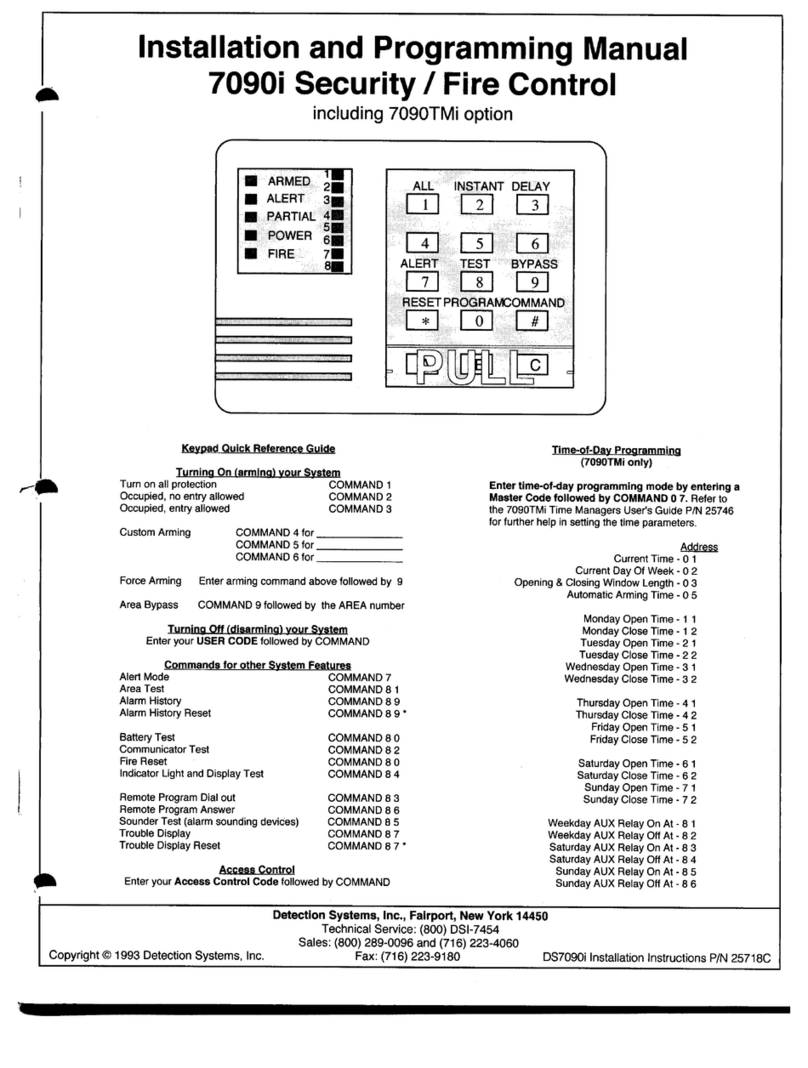
Detection Systems
Detection Systems 7090i Installation and programming guide

Polycom
Polycom Group Series reference guide
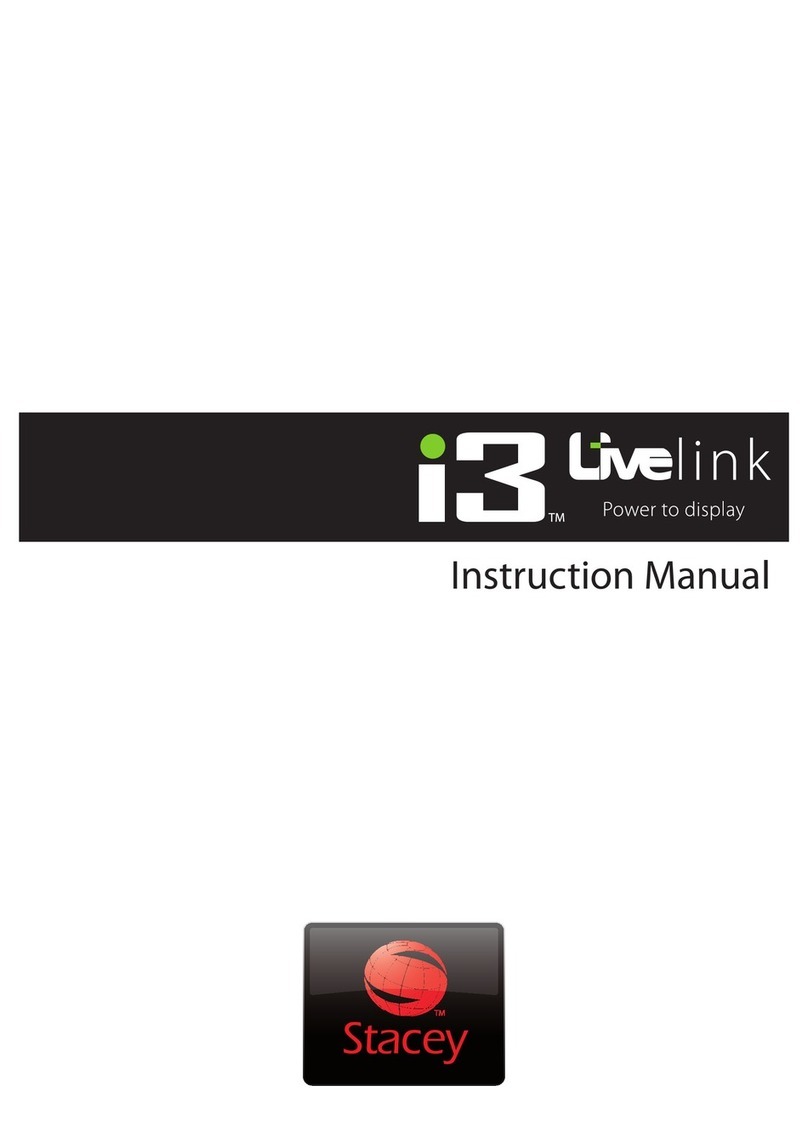
Stacey
Stacey i3 Livelink instruction manual
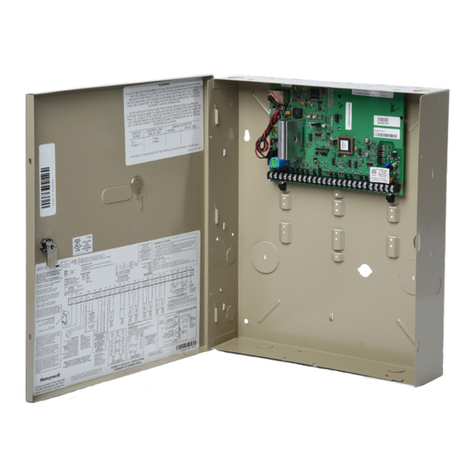
Honeywell Home
Honeywell Home Ademco Vista-21iPLTE Quick guide to user functions