Motortech VariSCR User manual

VariSCR –
NOXEmission Controller
Operating Manual
P/N 01.50.025 – EN | Rev. 06/2020

Original instructions
© Copyright 2020 MOTORTECH GmbH. All rights reserved.
MOTORTECH products and the MOTORTECH logo are registered and/or common law trademarks
of the MOTORTECH GmbH. All further trademarks and logos displayed or used in this publication
are the property of the respective entitled person and are used for reference purposes only.
Information contained in this publication may be changed without prior notice.

Rev. 06/2020 3
1 General Information .................................................................................................... 6
1.1 What Is the Purpose of this Operating Manual? .........................................................6
1.2 Who Is this Operating Manual Targeted to?...............................................................6
1.3 Which Symbols Are Used in the Operating Manual?...................................................6
1.4 Which Abbreviations/Acronyms Are Used in the Operating Manual?...........................7
2 Safety Instructions ..................................................................................................... 9
2.1 General Safety Instructions .....................................................................................9
2.2 Electrostatic Discharge Hazards ............................................................................ 10
2.3 Information on Electric Isolation............................................................................ 10
2.4 Special Safety Instructions for the Device .............................................................. 12
2.5 Proper Disposal.................................................................................................... 14
3 Intended Use ............................................................................................................. 15
3.1 Functional Description .......................................................................................... 15
3.2 Applications......................................................................................................... 15
4 Product Description ................................................................................................... 17
4.1 Technical Data ...................................................................................................... 17
4.1.1 Certifications ..................................................................................................... 17
4.1.2 Mechanical Data ................................................................................................ 17
4.1.3 Warning Notices on the Device............................................................................ 17
4.1.4 Product Identification – Labeling on the Device.................................................... 18
4.1.5 Electrical Data.................................................................................................... 18
4.1.6 Interfaces.......................................................................................................... 21
4.1.7 Overview Drawings.............................................................................................22
5 Installation Instructions.............................................................................................25
5.1 Installation Instructions ........................................................................................ 25
6 Wiring ...................................................................................................................... 26
6.1 Wiring – Power Supply ..........................................................................................28
6.2 Wiring – Sensors on the SCR Catalytic Converter ....................................................30
6.3 Wiring – Pump Module.......................................................................................... 32
6.4 Wiring – Dosing Unit.............................................................................................33
6.5 Wiring – MAT and MAP Sensor...............................................................................34
6.6 Wiring – Binary Inputs ..........................................................................................36
6.7 Wiring – Binary Outputs........................................................................................ 37
6.8 Wiring – Analog Inputs and Outputs ......................................................................39
6.9 Wiring – CAN Bus .................................................................................................40
Table of Contents

Table of Contents
4 Rev. 06/2020
6.10 Wiring – Modbus (RS485)....................................................................................42
7 Functions...................................................................................................................44
7.1 NOx Emission Control............................................................................................ 44
7.2 Pump Self Test .....................................................................................................44
7.3 Control of the Pressure of the Pump.......................................................................44
7.4 Cooling of the Dosing Valve................................................................................... 45
7.5 Protection against Freezing of the Dosing Valve...................................................... 45
7.6 Manual and Automatic Operation .......................................................................... 45
7.7 Access Control......................................................................................................46
8 Settings via the MICT................................................................................................ 48
8.1 MICT System Requirements...................................................................................48
8.2 MICT Installation..................................................................................................48
8.3 Access Levels in the MICT ..................................................................................... 49
8.4 Configuration Pages (Overview) ............................................................................ 50
8.5 Menu Bar and Toolbar............................................................................................51
8.6 Manual Valve Adjustment ..................................................................................... 54
8.7 Manual Pump Adjustment ..................................................................................... 54
8.8 Online Update Settings ........................................................................................ 56
8.9 Access Control for the VariSCR Emission Controller ................................................ 57
8.9.1 Enable/Disable Access Control ........................................................................... 57
8.9.2 Login/Logout .................................................................................................... 57
8.9.3 Changing the PIN .............................................................................................. 58
8.9.4 Reset all PINs.................................................................................................... 58
8.10 Working with Configurations ............................................................................... 59
8.10.1 Create, Open, Save...........................................................................................60
8.10.2 Upload, Download ........................................................................................... 61
8.10.3 Compatibility Information................................................................................. 61
8.11 Configuration...................................................................................................... 62
8.11.1 Inputs/Outputs – Control Setup......................................................................... 63
8.11.2 Exhaust Control – Parameter.............................................................................64
8.11.3 Exhaust Control – SCR – Pump Setup.................................................................66
8.11.4 Exhaust Control – SCR – Pump Self Test............................................................. 67
8.11.5 Exhaust Control – SCR – Dosing Valve ...............................................................69
8.11.6 Exhaust Control – SCR – Feed Forward Control ................................................... 70
8.11.7 Exhaust Control – Check ....................................................................................71
8.11.8 Miscellaneous – Communication....................................................................... 73
8.11.9 Miscellaneous – Service Contact....................................................................... 75

Table of Contents
Rev. 06/2020 5
8.12 Runtime Data...................................................................................................... 76
8.12.1 Runtime Data – Overview ..................................................................................78
8.12.2 Runtime Data – Sensors ................................................................................... 81
8.12.3 Runtime Data – Dosing Unit ..............................................................................83
8.12.4 Runtime Data – Trends .....................................................................................85
8.12.5 Runtime Data – Message Log ............................................................................87
8.12.5.1 Information ...................................................................................................88
8.12.5.2 Warnings......................................................................................................88
8.12.5.3 Errors ...........................................................................................................89
8.12.6 Runtime Data – Diagnostics..............................................................................90
8.12.7 Runtime Data – Information ..............................................................................92
8.13 Runtime Adjustments..........................................................................................93
8.13.1 Runtime Adjustments – Pump ...........................................................................93
8.13.2 Runtime Adjustments – Dosing Valve ................................................................94
8.13.3 Runtime Adjustments – Gas Mixer..................................................................... 95
8.14 Log .................................................................................................................... 95
9 Operation ..................................................................................................................97
9.1 Start-up ............................................................................................................... 97
9.1.1 Determine Values for Feed Forward Control ..........................................................98
9.2 Firmware Update ................................................................................................ 102
10 Errors ..................................................................................................................... 106
10.1 Troubleshooting................................................................................................ 106
10.2 Possible Faults ................................................................................................. 106
10.3 Acknowledging Faults ....................................................................................... 107
10.4 Customer Service Information............................................................................ 107
10.5 Returning Equipment for Repair/Inspection ........................................................ 108
10.6 Instructions for Packaging the Equipment .......................................................... 108
11 Maintenance........................................................................................................... 109
11.1 Spare Parts and Accessories............................................................................... 109
12 Index ..................................................................................................................... 110

6 Rev. 06/2020
Read through this operating manual carefully before use and become familiar with the product.
Installation and start-up should not be carried out before reading and understanding this
document. Keep this manual readily available so that you can reference it as needed.
1.1 What Is the Purpose of this Operating Manual?
This manual serves as an aid for the installation and operation of the product and supports the
technical staff with all operating and maintenance tasks to be performed. Furthermore, this
manual is aimed at preventing dangers to life and health of the user and third parties.
1.2 Who Is this Operating Manual Targeted to?
The operating manual provides a code of conduct for personnel tasked with the setup,
operation, maintenance, and repair of gas engines. A certain level of technical knowledge with
respect to the operation of gas engines and basic knowledge of electronic ignition systems are
necessary. Persons who are only authorized to operate the gas engine shall be trained by the
operating company and shall be expressly instructed concerning potential hazards.
1.3 Which Symbols Are Used in the Operating Manual?
The following symbols are used in this manual and must be observed:
Example
This symbol indicates examples, which point out necessary handling steps
and techniques. In addition, you receive additional information from the
examples, which will increase your knowledge.
Notice
This symbol indicates important notices for the user. Follow these. In
addition, this symbol is used for overviews that give you a summary of the
necessary work steps.
Warning
This symbol indicates warnings for possible risks of property damage or
risks to health. Read these warning notices carefully and take the
mentioned precautionary measures.
1 General Information

1 General Information
Rev. 06/2020 7
Danger
This symbol indicates warnings for danger to life, especially due to high
voltage. Read these warning notices carefully and take the mentioned
precautionary measures.
1.4 Which Abbreviations/Acronyms Are Used in the Operating Manual?
In the operating manual or the user interface, the following abbreviations/acronyms are used.
Abb. Term Description Explanation
CAN bus Controller Area Network
bus
Bus for control
devices/ networks
Asynchronous serial
connection system for
linking control units
CE Conformité Européenne Conformity with EU
directives
Mark based on EU legislation
for certain products in
conjunction with product
safety
CPU Central Processing Unit
CSV Comma-separated
Values
Text file for storage or
exchange of structured data
DC Direct Current
EMC Electromagnetic
Compatibility
Compatibility of electrical or
electronic equipment items
with their surroundings
ESD Electrostatic Discharge
LED Light Emitting Diode Light emitting electronic
semiconductor
MAP Manifold Absolute
Pressure
MAT Manifold Air
Temperature
MICT MOTORTECH Integrated
Configuration Tool
Configuration software for
MOTORTECH control units

1 General Information
8 Rev. 06/2020
Abb. Term Description Explanation
SCR Selective Catalytic
Reduction
Technology for the reduction
of nitrogen oxides in exhaust
gases
USB Universal Serial Bus Serial connection system to
link a computer to external
devices

Rev. 06/2020 9
2.1 General Safety Instructions
MOTORTECH equipment is manufactured as state of the art and therefore safe and reliable to
operate. Nevertheless the equipment can cause risks or damage can occur, if the following
instructions are not complied with:
–The gas engine must only be operated by trained and authorized personnel.
–Observe all safety instructions of the system and all safety instructions of the system
operator.
–Operate the equipment only within the parameters specified in the technical data.
–Use the equipment correctly and for its intended use only.
–Never apply force.
–For all work such as installation, conversion, adaptation, maintenance, and repair, all
equipment must be disconnected from the mains and secured against unintentional
reactivation.
–Perform only such maintenance and repair work as is described in this operating manual,
and follow the instructions given while working.
–Only use spare parts supplied by MOTORTECH for the maintenance of the device.
–Further work must only be performed by personnel authorized by MOTORTECH. Non-
compliance with the instructions will void any warranties for the proper function of the
equipment as well as the responsibility for the validity of the certifications.
–Safety devices must not be dismounted or disabled.
–Avoid all activities that can impair the function of the equipment.
–Operate the equipment only while it is in proper condition.
–Investigate all changes that occur during operation of the gas engine or electronic engine
control.
–Ensure compliance with all laws, directives, and regulations applicable to the operation of
your system, including such not expressly stated herein.
–If the system is not entirely tight and sealed, gas may escape and result in explosion hazard.
The inhalation of gas can also lead to death or severe health damages. Therefore, upon
completion of all assembly works, always check the system's tightness.
–Always ensure adequate ventilation of the engine compartment.
–Ensure a safe position at the gas engine.
–There is a risk of burning on hot surfaces. Allow the engine to cool down before starting any
work.
–Personal protective equipment (PPE), e.g. safety shoes and gloves, must be worn during all
work on the engine.
2 Safety Instructions

2 Safety Instructions
10 Rev. 06/2020
–Noise from the system can cause permanent or temporary damage to your hearing. Wear
suitable hearing protection at the system.
–Your behavior can reduce possible residual risks to a minimum. Observe responsible
handling of the gas engine and the gas-carrying system.
2.2 Electrostatic Discharge Hazards
Electronic equipment is sensitive to static electricity. To protect these components from damage
caused by static electricity, special precautions must be taken to minimize or prevent
electrostatic discharge.
Observe these safety precautions while you work with the equipment or in its vicinity.
–Before performing maintenance or repair work, ensure that the static electricity inherent to
your body is discharged.
–Do not wear clothing made from synthetic materials to prevent static electricity from
building up. Your clothing should therefore be made of cotton or cotton mix materials.
–Keep plastics such as vinyl and Styrofoam materials as far away from the equipment as
possible.
–Do not remove the circuit boards from the housing of the device.
2.3 Information on Electric Isolation
If ground and earth potential are not properly isolated, the following problems as well as others
can occur:
–Electromagnetic interferences (e.g. ground loops)
–Signal corruption (e.g. of the analog voltage signal)
–Unwanted leakage currents
Therefore, earth potential and the negative pole of the power supply of all devices in the electric
assembly that provide the option, should be connected separately. If possible, the negative pole
of the power supply should only be connected to earth potential at one point in the entire
system.

2 Safety Instructions
Rev. 06/2020 11
Wiring Example
Device with
shielded wires
Device featuring
protection class II
Occurrence of ground loops
The devices shown in the following image do not feature the possibility to
connect the earth potential and the negative pole of the power supply
separated from each other. How ground loops are created.
A ground loop is a ground connection of an electric wiring assembly that is
closed as a loop. Due to impedance (resistance R > ) of the loop, low-
frequency interference currents can lead to an unwanted voltage drop in the
signal path.
Device 1 Device 2
Ground loop

2 Safety Instructions
12 Rev. 06/2020
2.4 Special Safety Instructions for the Device
Explosion hazard!
Do not disconnect any connectors while the system is live. If the system is
located in a hazardous area, there is a risk of explosion.
Explosion hazard!
Only use the NOXsensor for measurement in non-explosive gas mixtures, as
explosive gas mixtures can ignite on the hot sensing element. Especially in
the case of engine malfunction, make sure that no unburned gas mixture
enters the exhaust pipe.
Operational safety!
All screws of the connectors must be adequately tightened.
Operational safety!
The proper functioning of the device is only guaranteed if the device is
operated within the permissible supply voltage range. Therefore, use a
power supply in accordance with the specifications in the operating
manual.

2 Safety Instructions
Rev. 06/2020 13
Risk of injury!
The VariSCR emission controller is designed for operation in circuits with
protected extra-low voltage with safe electrical isolation (PELV). The
voltages in these circuits must not exceed 50 V AC or 75 V DC.
The VariSCR emission controller must not be electrically connected to
circuits which carry dangerously high voltages or which could lead to a
single failure.
Therefore, the following conditions, among others, must be fulfilled:
–The power supply may only be provided from power supply units with
safe electrical isolation or from batteries.
–Relays with safe isolation must be used for coupling to circuits that
carry dangerous voltages or could carry in the event of a failure.
–All currently applicable standards and regulations must be taken into
account.
Risk of burning!
The surfaces of the system may heat up to high temperatures. Ensure good
heat transfer through ventilation when installing in the control cabinet.
Risk of burning!
There is a risk of burns when touching the sensing element of the NOX
sensor because the sensing element becomes hot during operation.
Therefore, note the following points:
–Therefore, install the sensing element on the exhaust pipe at a suitable
location where people at the plant cannot be burned by it, or attach a
protective grid around the sensing element to prevent contact with the
sensing element.
–The sensing element must have cooled down sufficiently at the end of
operation before you can touch the sensing element again.
Danger of damage to health!
If AdBlue®evaporates, harmful gases can be produced. Therefore, avoid
contact of AdBlue®with hot surfaces (e.g. on the catalytic converter).
Furthermore, when working with AdBlue®, observe the applicable safety
regulations.

2 Safety Instructions
14 Rev. 06/2020
Danger of interference with radio reception!
The device is not intended for use in residential areas and cannot ensure
adequate protection of radio reception in such environments.
2.5 Proper Disposal
After the expiration of its service life, MOTORTECH equipment can be disposed of with other
commercial waste, or it may be returned to MOTORTECH. We will ensure its environmentally
friendly disposal.

Rev. 06/2020 15
3.1 Functional Description
The NOXemission controller VariSCR is a component of an exhaust aftertreatment system based
on an SCR catalytic converter. The emission controller evaluates the signals from sensors and
controls the AdBlue®injection into the catalytic converter according to the parameters
determined. The signals from the MAP and MAT sensors and the NOXsensor upstream of the
catalytic converter are used for feed forward control. The signal from the NOXsensor after the
catalytic converter then enables the system to be regulated more precisely.
To ensure the system functions properly, the temperature at the dosing valve is monitored and,
if necessary, it is cooled or heated. In addition, the emission controller offers the following
monitoring functions:
–Monitoring of pressure and speed of the AdBlue®pump
–Monitoring of the exhaust temperature before and after the catalytic converter
–Monitoring of the NOXsensors and temperature sensors function
The emission controller is configured using a connected computer. The software used for this
purpose is also used to display current system data and error messages.
3.2 Applications
The full functionality of the VariSCR emission controller can only be guaranteed if the
components of the MOTORTECH SCR system are used, consisting of:
–SCR catalytic converter
–NOXsensors
–Temperature sensors
–Pump module
–Dosing unit
–MOTORTECH cable harnesses including MAT sensor PT100 and MAP sensor
Other required components (not included):
–Urea tank including level sensor and piping
–Master Generator & CHP Control System
Two SCR systems are generally required for V-engines.
Any use other than the one described in the operating manual shall be considered improper use
and will result in the voiding of all warranties.
3 Intended Use

3 Intended Use
16 Rev. 06/2020
System Overview (Example)
NOXEmission controller VariSCR Engine
Dosing unit (incl. pressure and temperature sensor,
dosing valve and heating)
Master Generator & CHP
Control System
Pump module AdBlue®tank
NOXand temperature sensor before the SCR catalytic
converter
Exhaust tract
SCR catalytic converter MAP and MAT sensor
NOXand temperature sensor after of the SCR catalytic
converter

Rev. 06/2020 17
4.1 Technical Data
4.1.1 Certifications
The emission controller VariSCR is certified according to the following directives:
CE
EMC Directive 2014/30/EU
–EN 61326-1:2013 – Electrical equipment for measurement, control and laboratory use. EMC
requirements. General requirements
–EN 55011:2009 + A1:2010 – Industrial, scientific and medical equipment. Radio-frequency
disturbance characteristics. Limits and methods of measurement
–Group 1, Class A
RoHS Directive 2011/65/EU
The EU Declaration of Conformity can be found as a PDF file on the storage device enclosed with
the device.
4.1.2 Mechanical Data
The VariSCR emission controller has the following mechanical characteristics:
Feature Value
Dimensions 160 mm x 126 mm x 61 mm (6.30" x 4.96" x 2.40")
(length x width x height)
Weight 766 g (1.7 lbs)
Shape of device See chapter Overview Drawings on page 22
Mechanical environmental
conditions
Protection: IP20
Climatic environmental
conditions
–20 °C to +60 °C (–4 °F to +140 °F)
Max. 85 % humidity without condensation
up to 3,000 m (9,842') above sea level
4.1.3 Warning Notices on the Device
Top of Device
WARNING! Read and understand the installation and operating manual prior to installing or
making any adjustments. Do not disconnect equipment unless power has been switched off.
4 Product Description

4 Product Description
18 Rev. 06/2020
4.1.4 Product Identification – Labeling on the Device
You find the numbers required for unique product identification on the label on the side of the
device:
–Part number of the emission controller (P/N)
–Serial number of the emission controller (S/N)
–Arrangement number of the emission controller (A/N)
–Revision number of the emission controller indicating its precise construction status (R/N)
(Exemplary representation)
4.1.5 Electrical Data
The VariSCR emission controller has the following electrical characteristics:
Feature Value
Power consumption Max. 180 W
Power supply Nominal voltage: 24 V DC
Operating voltage: 18 V DC to 32 V DC
Required current Max. 10 A

4 Product Description
Rev. 06/2020 19
Electrical Data for Inputs and Outputs
The inputs and outputs of the emission controller have the following electrical data:
Inputs and outputs Values/characteristics
Binary inputs –Input voltage up to 32 V DC
–Input current at least 5 mA for high level (approx. 12 mA at
24 V DC)
–galvanically isolated
(rated insulation voltage: max. 70 V DC)
When the reset signal is given, the high level must be present
at the relevant input for at least 50 ms before it is possible to
initiate the reset.
Binary outputs – Inactive: output is high-impedance
–Active: output is low-impedance
–Switching voltage: max. 32 V
–Current: max. 100 mA
–Max. voltage drop at 100 mA: 2.5 V
–galvanically isolated
(rated insulation voltage: max. 70 V DC)
Analog voltage input –Permissible voltage: 0 V to 10 V
–Input resistance: 12.4 kΩ
Analog current input – Permissible current: 0 mA to 20 mA
–Max. difference in potential relative to device ground:
+3.5 V
–Input resistance: max. 25 Ω
Analog voltage output –Output voltage: 0 V to 10 V
–Working resistance: min. 500 Ω
Analog current output – Output current: 0 mA to 20 mA
–Working resistance: max. 500 Ω
Electrical Data for Connection of the Pump Module
The connections of the pump module have the following electrical data:
Feature Value
Power supply for the pump 18 V DC to 32 V DC; max. 1.5 A

4 Product Description
20 Rev. 06/2020
Feature Value
Output for control signal
for pump speed
–Open collector
–Voltage: 18 V DC to 32 V DC
–PWM: 100 Hz
–Current: Max. 30 mA
Input for feedback signal
for pump speed
–NPN with pull-up resistor 12 kΩ
–Input voltage up to 32 V DC
–Frequency: 0 Hz to 500 Hz (square wave signal)
Electrical Data for Connection of the Dosing Unit
The connections of the dosing unit have the following electrical data:
Feature Value
Power supply of the
integrated sensors
5 V DC; max. 30 mA
Analog voltage input for
AdBlue®pressure
–Permissible voltage: 0 V DC to 4.5 V DC
–Measuring range: 0 bar to +19.5 bar abs. (0 psi to
+282.8 psi abs.)
–Measuring tolerance: 2 % of measured value
Analog voltage input for
AdBlue®temperature
–Permissible voltage: 3.3 V DC to 0.5 V DC
–Measuring range: –50 °C to +150 °C (–58 °F to +302 °F)
–Measuring tolerance:
+/–4 °C (in the range 0 °C to +90 °C)
+/–7.2 °F (in the range +32 °F to +194 °F)
Connection for the dosing
valve
PWM: 5 kHz, 18 V to 32 V; max. 1 A
Connection for the heating
resistor
Power supply: 18 V DC to 32 V DC; max. 2 A
Electrical Data of the Connections for the Sensors on the Catalytic Converter
The connections of the sensors have the following electrical data:
Feature Value
Power supply of the
sensors
18 V DC to 32 V DC; max. 1.5 A
Table of contents
Other Motortech Controllers manuals
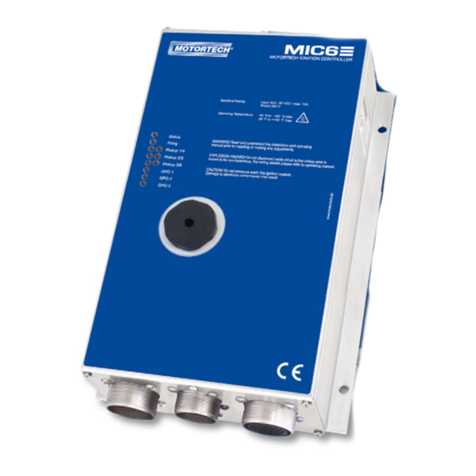
Motortech
Motortech MIC-Marine User manual
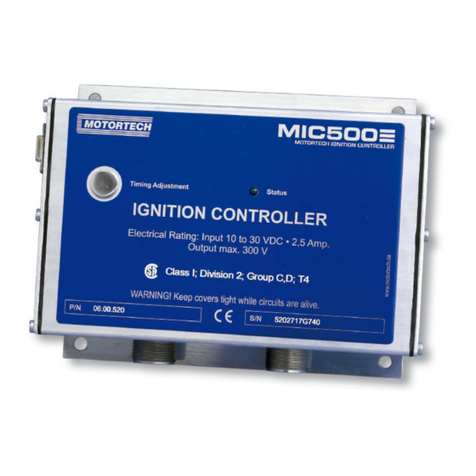
Motortech
Motortech MIC500 User manual
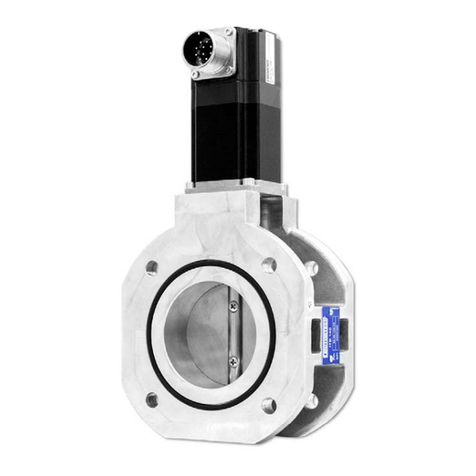
Motortech
Motortech ITB 50 Series User manual
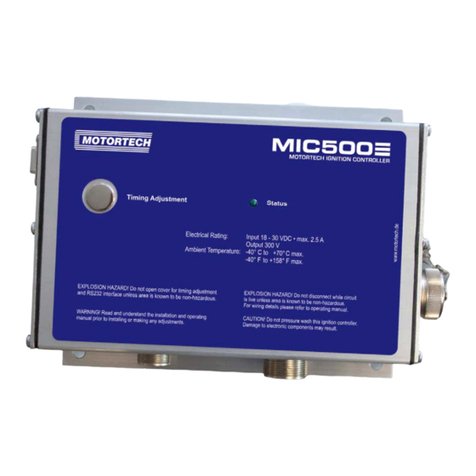
Motortech
Motortech MIC500 User manual
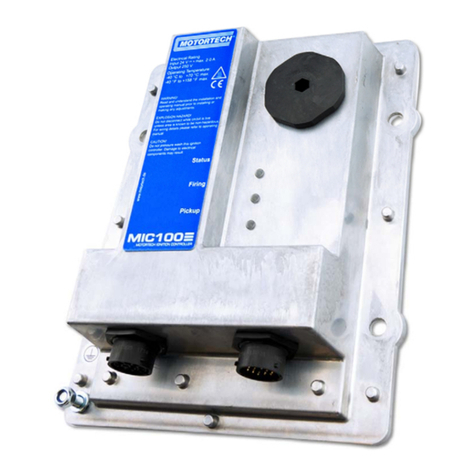
Motortech
Motortech MIC100 User manual

Motortech
Motortech MIC3+ User manual
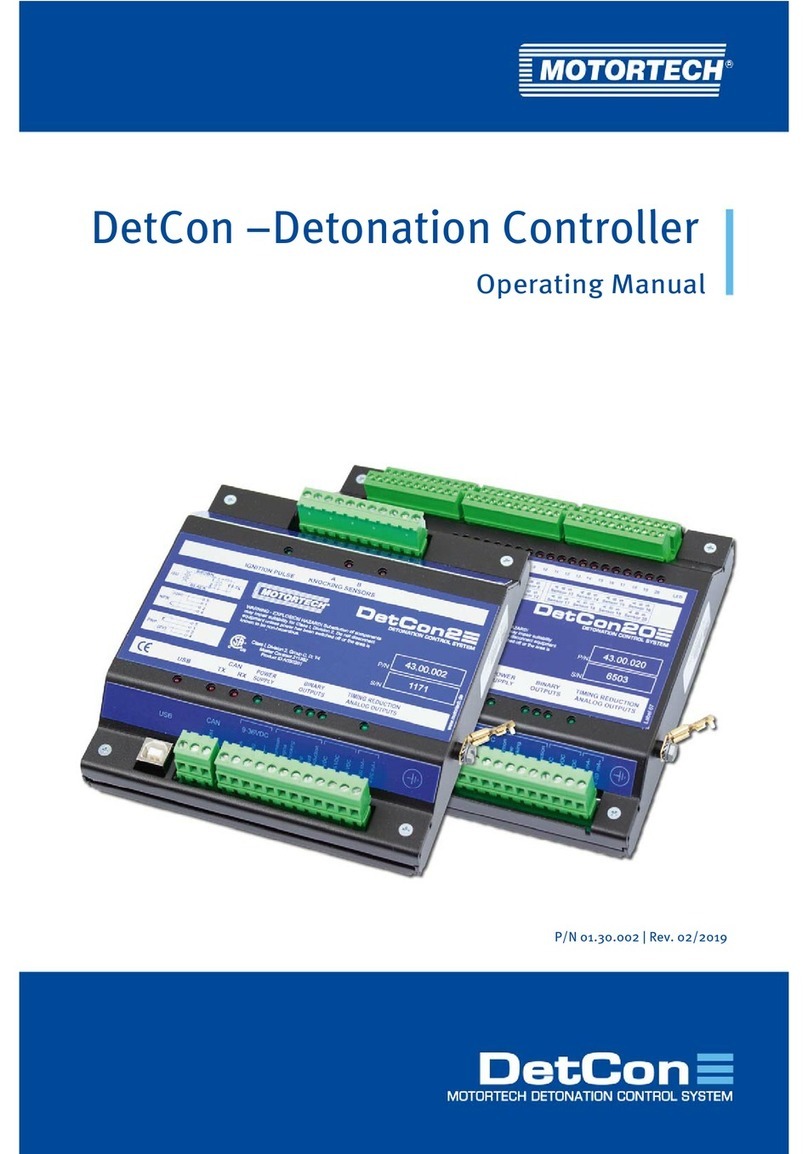
Motortech
Motortech DetCon series User manual
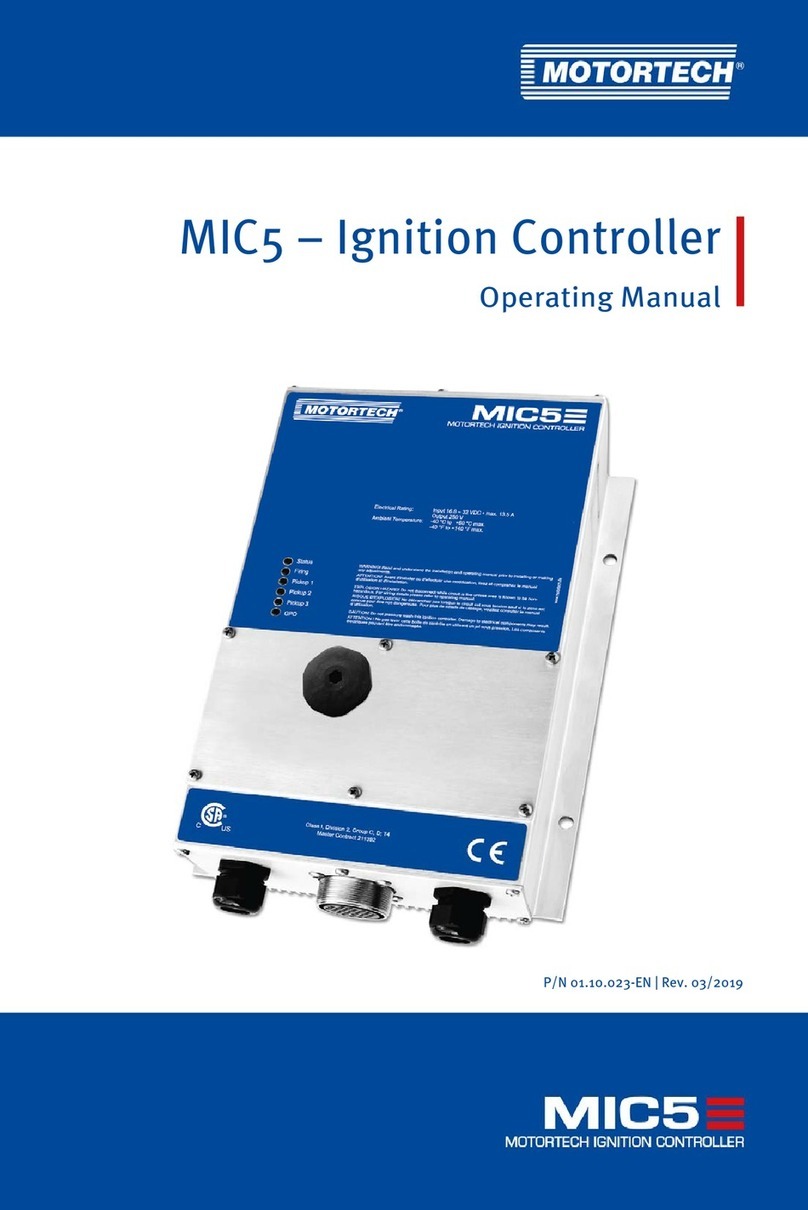
Motortech
Motortech MIC5 User manual
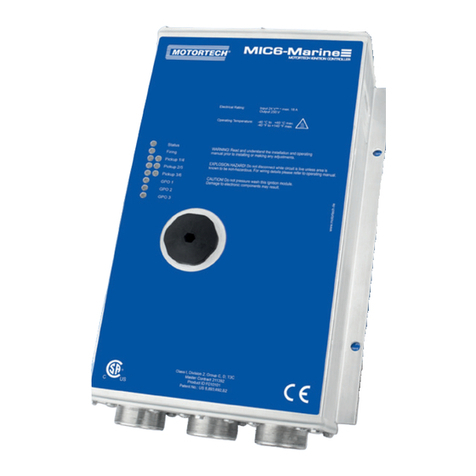
Motortech
Motortech MIC6 User manual
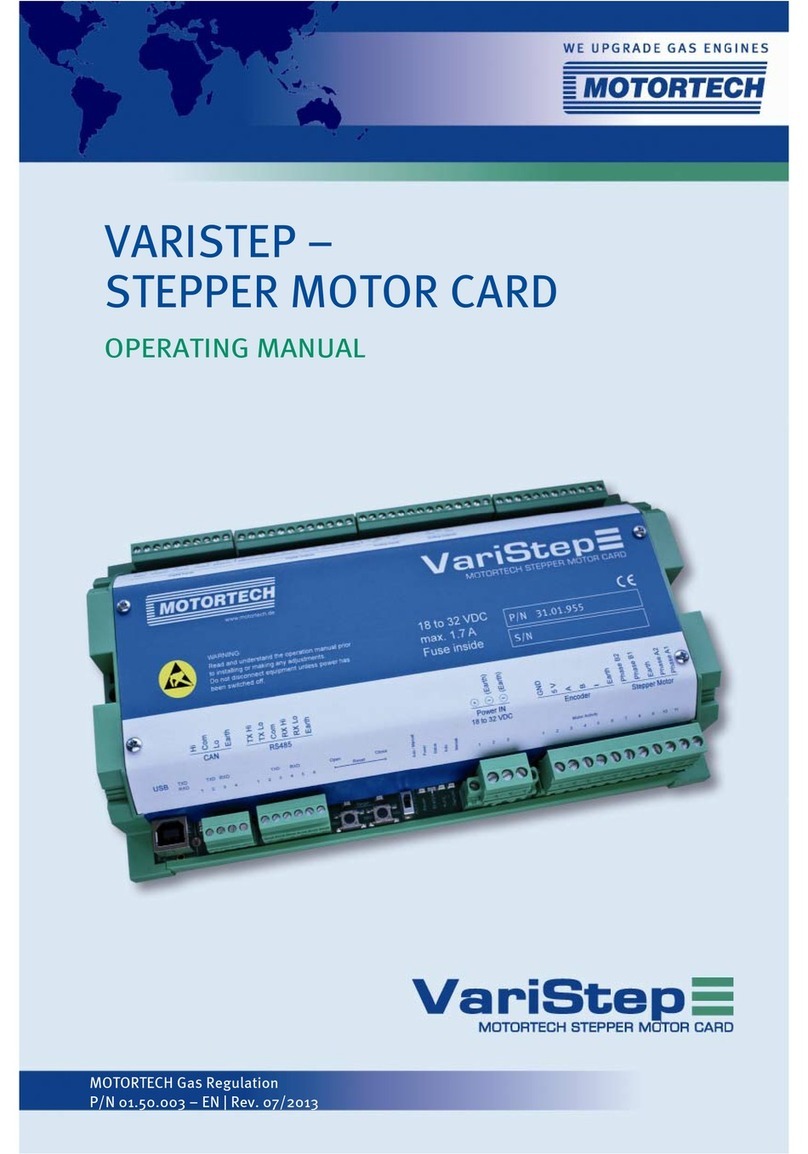
Motortech
Motortech Varistep User manual