mycom IMS20-210 User manual

No.QT33-04005F
Driver for 2 phase stepping motor
IMS20-210(L)
【User’s manual】
MYCOM, INC.

No.QT33-04005F
DANGER
WARNING
CAUTION
DANGER
Attention on safety
Please read this user’s manual carefully before using and use rightly.
The purpose of this attention is to protect users or others from the injure, damage or loss of
property in advance and use this product rightly and safely.
This danger shows the possibility that the user may die or get serious
injures by fire or electrical shock and the contents which are high
emergency of caution when danger is occurred if this warning is neglected
and operated.
This warning shows the possibility that the user may die or get serious
injures, fire or electrical shock if this warning is neglected and operated.
This caution shows the possibility that the user may be injured by electrical
shock or the contents which expect to issue physical damage if this caution
is neglected and operated.
● Do not use the unit broken or disassembled.It may become the cause of fire or
electric shock.
● Do not repair or reconstruct by no means because repair and reconstruction may issue a
danger which causes serious accident.
●Do not use the unit near by corrosive gas, inflammable gas, explosive atmosphere,
watery or oily place or inflammables. It may cause fire, electric shock or injury.
●Only person who has special knowledge is requested to work for setting, wiring,
operation, inspection, maintenance and so on. There is a reason of electric shock
and injury.
●Keep rated input power voltage range surely. There is a reason of fire or damage.
●Make sure the wiring according to wiring example.There is areason of fire or
damage.
●Do not touch the terminal base during power on by no means because some
terminals have high voltage. There is a reason of electric shock.
●Do not put finger or objects on the board. There is a reason of fire or electric shock.
●Do not bent, expand or put into the power cable and motor cable by force. There is
a reason of fire and electric shock.
●There is apossibility of fire if motor output terminal and earth or power is
connected by mistake.
●Observe the installation method described in user’smanual and do not install to
prevent radiation. There is a reason of fire.
●If HEAT(Overheat) is effective during operation, stop the operation soon. There is a
reason of fire or damage.

No.QT33-04005F
WARNING
CAUTION
●Do not operate to move, wire, maintain and test etc. during power on. After power-off and
ten seconds pass, please start to operate. It may cause electric shock and injury.
●Do not touch the unit with wet hand by no means during power on. There is a reason of
electric shock.
●Connect the protective earth (PE) with the earth terminal (3rd type earth) by no means. It
may cause electric shock.
●Install and use the driver in the control box. It may cause electric shock and injure.
●Install terminal cover for terminal during power on. It may cause electric shock and
injure.
●Fix the driver tightly when installing. It may cause injury.
●Do not touch the terminal base during power on by no means because some terminals have
high voltage. There is a reason of fire and electric shock.
●Do not touch the driver during operation and for the time being after stop. Because the
surface of driver is hot depending of operating condition, it may cause injury.
If necessary, we would ask the trading company or distributor to translate this manual into the
importer’s mother language.
●Do not use or store the unit near by corrosive gas. It may cause damage.
●Do not give a large shock. It may cause malfunctions.
●Do not use or store this unit in a place of high or low temperature, extreme high or low
humidity. It may cause a short circuit or malfunctions.
●Avoid dews to form. It may cause a short circuit or malfunctions.
●MYCOM is, in no way, responsible for any damages or malfunctions that are caused by
user’s repair or modifications on this driver. If the user performed these initiations and the
driver does not work satisfactory, a warranty will not be provided.
●When giving up the use of the driver, dispose it according to an appropriate regulation on
the industrial waste.
●Please do not remove the name plate.

No.QT33-04005F
Index
1. Specification of driver・・・・・・・・・・・・・・・・・・・・・・・・・・・・・・・・・・・・・・・・・・・・・・・・・・・・・・・・・・・・・・・・1
2. Model number and Factory default・・・・・・・・・・・・・・・・・・・・・・・・・・・・・・・・・・・・・・・・・・・・・・・・・・・・2
2-1. Model number of set ・・・・・・・・・・・・・・・・・・・・・・・・・・・・・・・・・・・・・・・・・・・・・・・・・・・・・・・・・・・・・2
2-2. Model number of driver ・・・・・・・・・・・・・・・・・・・・・・・・・・・・・・・・・・・・・・・・・・・・・・・・・・・・・・・・・・2
2-3. Factory default・・・・・・・・・・・・・・・・・・・・・・・・・・・・・・・・・・・・・・・・・・・・・・・・・・・・・・・・・・・・・・・・・・2
3. Pulse wave ・・・・・・・・・・・・・・・・・・・・・・・・・・・・・・・・・・・・・・・・・・・・・・・・・・・・・・・・・・・・・・・・・・・・・・・・・3
3-1. Input pulse type・・・・・・・・・・・・・・・・・・・・・・・・・・・・・・・・・・・・・・・・・・・・・・・・・・・・・・・・・・・・・・・・・3
3-2. Pulse waveform ・・・・・・・・・・・・・・・・・・・・・・・・・・・・・・・・・・・・・・・・・・・・・・・・・・・・・・・・・・・・・・・・・4
4. Each part name and functions ・・・・・・・・・・・・・・・・・・・・・・・・・・・・・・・・・・・・・・・・・・・・・・・・・・・・・・・・5
4-1. Each part name ・・・・・・・・・・・・・・・・・・・・・・・・・・・・・・・・・・・・・・・・・・・・・・・・・・・・・・・・・・・・・・・・・5
4-2. Description of function ・・・・・・・・・・・・・・・・・・・・・・・・・・・・・・・・・・・・・・・・・・・・・・・・・・・・・・・・・・・6
4-2-1. Power indicator LED (POWER)・・・・・・・・・・・・・・・・・・・・・・・・・・・・・・・・・・・・・・・・・・・・・・・6
4-2-2. Overheat indicator LED (HEAT)・・・・・・・・・・・・・・・・・・・・・・・・・・・・・・・・・・・・・・・・・・・・・・6
4-2-3. Excitation timing ZERO output terminal (MONI) ・・・・・・・・・・・・・・・・・・・・・・・・・・・・・・6
4-2-4. Motor current shutoff signal (CO) ・・・・・・・・・・・・・・・・・・・・・・・・・・・・・・・・・・・・・・・・・・・・・6
4-2-5. Automatic current-off function (A.CO) ・・・・・・・・・・・・・・・・・・・・・・・・・・・・・・・・・・・・・・・・・6
4-2-6. (Automatic current reduction function (A.CD) ・・・・・・・・・・・・・・・・・・・・・・・・・・・・・・・・・・6
4-2-7. Signal I/O connector (CN) ・・・・・・・・・・・・・・・・・・・・・・・・・・・・・・・・・・・・・・・・・・・・・・・・・・・・7
4-2-8. Motor connector terminals (MOTOR)・・・・・・・・・・・・・・・・・・・・・・・・・・・・・・・・・・・・・・・・・・7
4-2-9. Power source connector terminal (AC) ・・・・・・・・・・・・・・・・・・・・・・・・・・・・・・・・・・・・・・・・・7
4-2-10. Protective earth terminal (PE)・・・・・・・・・・・・・・・・・・・・・・・・・・・・・・・・・・・・・・・・・・・・・・・7
5. Example of wiring ・・・・・・・・・・・・・・・・・・・・・・・・・・・・・・・・・・・・・・・・・・・・・・・・・・・・・・・・・・・・・・・・・・・8
6. Wiring and Install condition・・・・・・・・・・・・・・・・・・・・・・・・・・・・・・・・・・・・・・・・・・・・・・・・・・・・・・・・・・8
6-1. Wiring for motor lines and power lines ・・・・・・・・・・・・・・・・・・・・・・・・・・・・・・・・・・・・・・・・・・・・8
6-2. Wiring of motor line ・・・・・・・・・・・・・・・・・・・・・・・・・・・・・・・・・・・・・・・・・・・・・・・・・・・・・・・・・・・・・8
6-3. Applicable clamping terminal・・・・・・・・・・・・・・・・・・・・・・・・・・・・・・・・・・・・・・・・・・・・・・・・・・・・・8
6-4. Tightening torque for terminal block ・・・・・・・・・・・・・・・・・・・・・・・・・・・・・・・・・・・・・・・・・・・・・・9
6-5. Install condition・・・・・・・・・・・・・・・・・・・・・・・・・・・・・・・・・・・・・・・・・・・・・・・・・・・・・・・・・・・・・・・・・9
7. Dimension・・・・・・・・・・・・・・・・・・・・・・・・・・・・・・・・・・・・・・・・・・・・・・・・・・・・・・・・・・・・・・・・・・・・・・・・10
7-1. Dimension ・・・・・・・・・・・・・・・・・・・・・・・・・・・・・・・・・・・・・・・・・・・・・・・・・・・・・・・・・・・・・・・・・・・・10
7-2. Dimension of metal bracket(Option)・・・・・・・・・・・・・・・・・・・・・・・・・・・・・・・・・・・・・・・・・・・・・11
8. Option ・・・・・・・・・・・・・・・・・・・・・・・・・・・・・・・・・・・・・・・・・・・・・・・・・・・・・・・・・・・・・・・・・・・・・・・・・・・12

No.QT33-04005F
- 1-
1. Specification of driver
Model number IMS20-210(L)
Power source Single phase AC100-120V±10%, 50/60Hz
Power consumption 240 VA or less
Driving type Bi-polar type
Driving current Max. 2.0A (Total output current)
Correspondence
motor current
Uni-polar type :Max. 2.0A/phase
Bi-polar type :Max. 1.0A/phase
Step angle Basic step (FULL) Half step (HALF)
Function Auto-current-down, Auto-current-off, Driving current-off input
Timing output, Overheat output
Signal input
1 clk (PLUSE, CW/CCW), 2 clkCW, CCW), CO
Photo coupler input : input resistance 390ohm
Input signal voltage : L ; 0 to 0.5V, H ; +4 to +5V
Signal output MONI, HEAT (Photo coupler, Open collector output)
External usage condition : DC24V or less, 10mA or less.
Applicable standard EN60950
Dielectric
Strength
No abnormality detected after the application of 2.0kV(60Hz)
between the below terminals for one second.
Power input/Motor output terminal –PE terminal
Power input/Motor output terminal –Signal I/O terminal
Insulation
Resistance
100Mohm or higher with DC500V mega applied to the below
terminals in normal temperature and humidity.
Power input/Motor output terminal –PE terminal
Power input/Motor output terminal –Signal I/O terminal
Operating environment
temperature 0 to +40 degree, NO freezing
Operating environment
humidity 80% or less, No condensation
Storing environmental
temperature -10 to +60 degree, No condensation
Storing humidity 80% or less, No condensation
Operating height Less than 1,000m from sea level
Atmosphere In the room without corrosive gas, inflammable gas and dust.
Without splashing water and oil
Weight 650 g(IMS20-210L:500 g)
Accessories User’s manual(This book)

No.QT33-04005F
- 2-
2. Model number and Factory default
2-1. Model number of set
IMS20−210−264B
Series name Extension of set
List of motor and driver combination
Series name IMS20
Extension of set Motor model
(Uni-polar type)
Output
currrent
CE
marking Driver model
243A(B) PF243-A(B) 0.9A/phase
244A(B) PF244-A(B)
245A(B) PF245-A(B) 1.2A/phase
264A(B) PF264-A(B)
265A(B) PF265-A(B)
268A(B) PF268-A(B)
2.0A/phase
Not
approved
IMS20-210
IMS20-210L
・Please use our CE marked motor.
・Please use the motor in safety condition after careful confirmation of
using condition, heating and ground setting if another motor than CE
marked motor is used.
2-2. Model number of driver
IMS20−2 10L
Cover L: With no cover
Power supply voltage 1: AC100V
Driving current 2: Max 2.0 A
(Total output current)
2-3. Factory default
Driver model number IMS20-210
Driving current MAX 2.0 A (Total output current)
Auto-current-off function Auto-current-off function : release
Auto-current-down function Auto-current-down function : effective
Input pulse type 2 clk type
Step angle Half step
Please specify if other setting than standard setting is required when ordering.
If not specified, setting is standard and delivered.
Attention

No.QT33-04005F
- 3-
3. Pulse wave
3-1. Input pulse type
・2 pulses type
Timing chart
Motor starts to rotate by rising edge(↑) of CCW or CW signal.
・1 pulse type
Timing chart
Motor starts to rotate by rising edge(↑) of Pulse signal.
CCW−
CCW+
CW−
CW+
MOTOR
Pulse signal
Pulse signal
CW CCW
CW/CCW−
CW/CCW+
PULSE−
PULSE+
MOTOR
Pulse signal
Direction signal
CW CCW

No.QT33-04005F
- 4-
Attention
3-2. Pulse waveform
t4t2t3t1t3
・2pulses type
CW signal
CCW signal
・ section shows ON status(turn on of photo coupler) of input circuit photo coupler.
・Motor starts to rotate by rising edge(↑)of CCW or CW signal.
t1:6μsec or longer
t2:10μsec or longer
t3:2μsec or shorter
t4:20μsec or longer
t5t4t2t1 t3t3
・1pulse type
Pulse signal
・ section shows ON status(turn on of photo coupler) of input circuit photo coupler.
・Motor starts to rotate by rising edge(↑)of pulse signal.
・Direction signal input is to rotate CW direction by inputting pulse signal at ON status.
Also if pulse is inputted at OFF status, motor rotates to CCW direction.
・Signal name of product uses pulse signal as CW input and direction signal as CCW input.
Direction
signal
t4,t5:20μsec or longer
t3 :2μsec or shorter
t2 :10μsec or longer
t1 :6μsec or longer
1. If the signal exceeds the voltage of DC5V in use, please insert the series resistor near
Input voltage−5V
2. Current down function is invalid if the photo coupler of pulse input keeps ON
status at stopping.
to output terminal(connector) of using controller so that 10mA current pass.
10mA
Value of resistor to be inserted(Ω)= −Register value of wiring(Ω)

No.QT33-04005F
- 5-
4. Each part name and functions
4-1. Each part name
①Power display LED
This lights up on during power on.
②Overheat display LED
This rights on when the temperature of
internal hea-sink rises and becomes overheat
condition.
③C.ADJ (Motor run current adjustment)
・This VR is pre-adjusted for the applicable
motor. This VR is adjustable if a lower
current level setting is needed to reduce
motor torque and motor/driver heat
generation.
・Please turn the volume within the range of
torque of 0.98〜19.6mN・m(10〜200gf・cm).
④Signal I/O connector
Various I/O signals are connected.
⑤Motor connector terminal
Connect color coded motor leads to these
terminals.
⑥Power connector terminal
Connect AC line power to these terminals.
⑦Protective earth terminal(PE)
Connect to the protective earth terminal of
the machine.
①
④
③
②
⑦
⑥
⑤
CN
MOTOR
B
A
A
B
120V〜
AC
N
L
100‑
C.ADJ
H E A T
POWER
IMS20

No.QT33-04005F
- 6-
Attentio
4-2. Description of function
4-2-1. Power indicator LED (POWER)
This rights on during power on.
4-2-2. Overheat indicator LED (HEAT)
This rights on when the temperature of internal heat-sink rises and becomes overheat
condition. Then a signal is outputted to the HEAT output of CN.
4-2-3. Excitation timing ZERO output terminal (MONI)
Asignal is outputted from MONI terminal of CN when output excitation pattern is
excitation timing origin.
4-2-4. Motor current shutoff signal (CO)
Motor winding current turn-on/off signal. When this input terminal of CN is kept ON,
the motor shaft can be rotated externally.
H level : Motor winding current-off
L level : Motor winding current-on
4-2-5. Automatic current-off function (A.CO)
This function is to cut automatically all current to motor when the temperature in the
driver rises and becomes overheat condition.
4-2-6. (Automatic current reduction function (A.CD)
200ms after the motor stops, the motor winding current is reduced until about 50% of
normal driving to minimize motor heating.
In case of current down status, certain position gap issues without relation
to resolution by affecting motor characteristic to be used.

No.QT33-04005F
- 7-
4-2-7. Signal I/O connector (CN)
This is to be connected with driving pulse, current off signal and various monitor signals.
(Front panel side)
Connector combination 9 pin D-sub connector Socket type
Connector : OMRON, XM2D-0901 equivalent
Hood : OMRON, XM2S-0911 equivalent(M2.6×0.45)
4-2-8. Motor connector terminals (MOTOR)
Connect color coded motor leads to these terminals.
4-2-9. Power source connector terminal (AC)
Connect single phase AC100V-120V, 50/60Hz
18AWG(0.75mm2) leads or larger are recommended.
4-2-10. Protective earth terminal (PE)
Connect with protective earth terminal of the device for safety without fail.
Use bigger leads for protective earth terminal connection than the leads used for power
source connector terminal.
Connector pin assignment
1CW+ 6CO-
2CW−7MONI+
3CCW+ 8HEAT+
4CCW−9COM−
5CO+
6
9
5
1

No.QT33-04005F
- 8-
6mm
4.7mm
φ3.2
or more
or less
5. Example of wiring
6. Wiring and Install condition
6-1. Wiring for motor lines and power lines
・When wiring, surely wire the protect earth line at first.
・Install noise filter at power input where noise sources exist near the driver.
・This driver has fuse inside, but use no-fuse-breaker of “3A current capacity”or circuit
protector of the capacity of below table for safety.
6-2. Wiring of motor line
・The radiant noise can be depressed by shield cable equal to or bigger than AWG22(0.5mm2)
in case that redundant radiant noise is trouble.
・In case that the motor wiring is longer, please use the shield cable equal to or bigger than
AWG22(0.5mm2)
6-3. Applicable clamping terminal
Use circle clamping terminal with insulated
cover to connect with terminal block.
V1.25-MS3 (J.S.T)
TGV1.25-3 (NICHIFU) or equivalent
HEAT+
MONI+
CO +
CCW −
CCW +
CW −
CW +
390Ω
+24V
0 V
2.7k
Controller
(SNC series)
Driver output
Twisted pair wire
Photo coupler
COM −
IMS20‑210(L)
2.7k
AC
AC
Power
Earth
390Ω
CO −
390Ω
Noise
filter
No‑fuse breaker
・
Circuit Protector
↓
0 V
+ 5 V
supply
2‑phase motor
A
B
A
B
Sensor input

No.QT33-04005F
- 9-
Attention
6-4. Tightening torque for terminal block
Do not add vertical force against screw when connecting with terminal.
Please tighten the screw within torque of 0.392〜0.686N・m(4〜7Kgf・cm) at stopping.
6-5. Install condition
・Do not use driver outside of control box. This unit is designed for the following condition.
Over voltage category: Category II, Material group III
Pollution degree: Class 2
Protection structure: IP20(IMS20-210), IP00(IMS20-210L)
Protection against electric shock: Class I component
・Fix driver on heat conductive metal plate tightly.
・Put 3cm or more space between each driver and fix the drivers when multiple drivers
are arranged.
・Pay attention not to close the side slits of driver.
・Confirm that the driver environmental temperature is less than 40℃when overheat
lamp lights.
・Use screws of “thickness of installing place plus 3 to 5mm”if the driver is installed
directly by screws not by accessory bracket.
・Because this unit uses high speed photo coupler for the part of input pulse, use the
shield line for signal cable.
・Put this unit vertically because this unit radiates by natural convection. (Refer the
below figure)
There is a possibility that driver chassis temperature exceeds 60℃depending on load
condition or other environmental condition.
Attachment is impossible
C.ADJ
AC
CN
H E A T
POWER
MOTOR
B
B
A
A
120 V〜
100 ‑
N
L
I M S 2 0
C.ADJ
AC
CN
H E A T
P O W E R
MOTOR
B
B
A
A
120V 〜
100‑
N
L
I M S 2 0

No.QT33-04005F
- 10 -
7. Dimension
7-1. Dimension
Unit : mm, The screw head is not included.
B(Reverse)
name plate
A(Bottom)
16 15
31.5 54
16 15
1954
A
40
142
C . A D J
AC
CN
H E A T
P O W E R
MOTOR
B
B
A
A
120V〜
100‑
N
L
IMS20
B
16MAX110

No.QT33-04005F
- 11 -
7-2. Dimension of metal bracket(Option)
Dimension when option is assembled.
Unit : mm
4.5
168
160
37
16 4.54.5
B(Reverse)
26.531.5
14 12
A(Bottom)

No.QT33-04005F
- 12 -
8. Option
It is available to supply the following optional cables which have covering connector at the one
side.
・CN: Pulse cable
Model number :OPC-DS9P15
Connector :9pin D-sub
Cable :More than AWG28 multi-core twisted pairs cable with shield 1.5m
Connect the unused cables with the ground of the upper. Otherwise it may become the
cause of incorrect operation. Please refer 6-3 “Wiring of signal line”for the detail.
・Motor Cable
Model number :OMC-NC5P15
Cable :AWG20 Both-ends end Shield-less multi-core cable 1.5m
1500mm+20
‑10
In case of noise measures required depending on users usage condition, we can supply
special cable. Please consult with our sales department.

Please understand that we may make modifications to our products without notification in
order to improve the capabilities and external appearance of our products.
MYCOM, INC.
1-29, Goryoohara, Nishikyo-ku, Kyoto 615-8245, Japan
TEL: 81-75-382-1580 FAX : 81-75-382-1570
E-mail [email protected]
Home Page : http//www.mycom-japan.co.jp/
This manual suits for next models
1
Table of contents
Popular Control Unit manuals by other brands
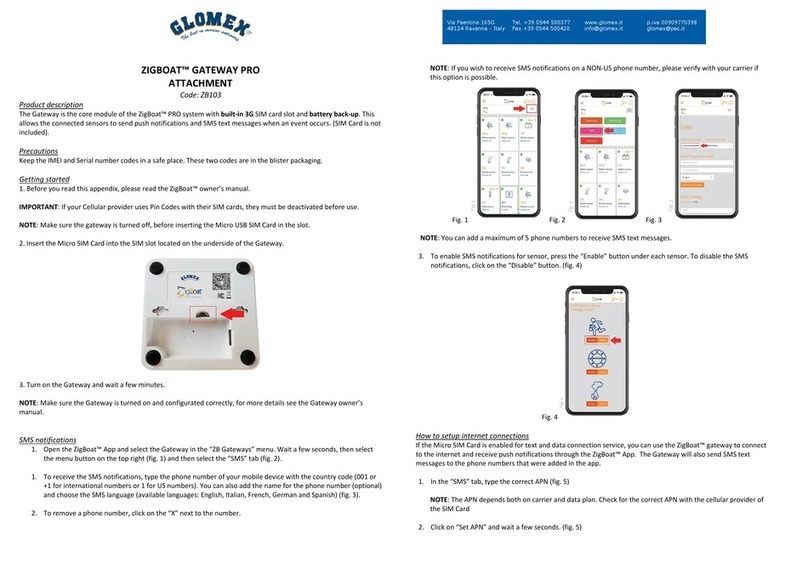
Glomex
Glomex Zigboat Gateway Pro quick start guide
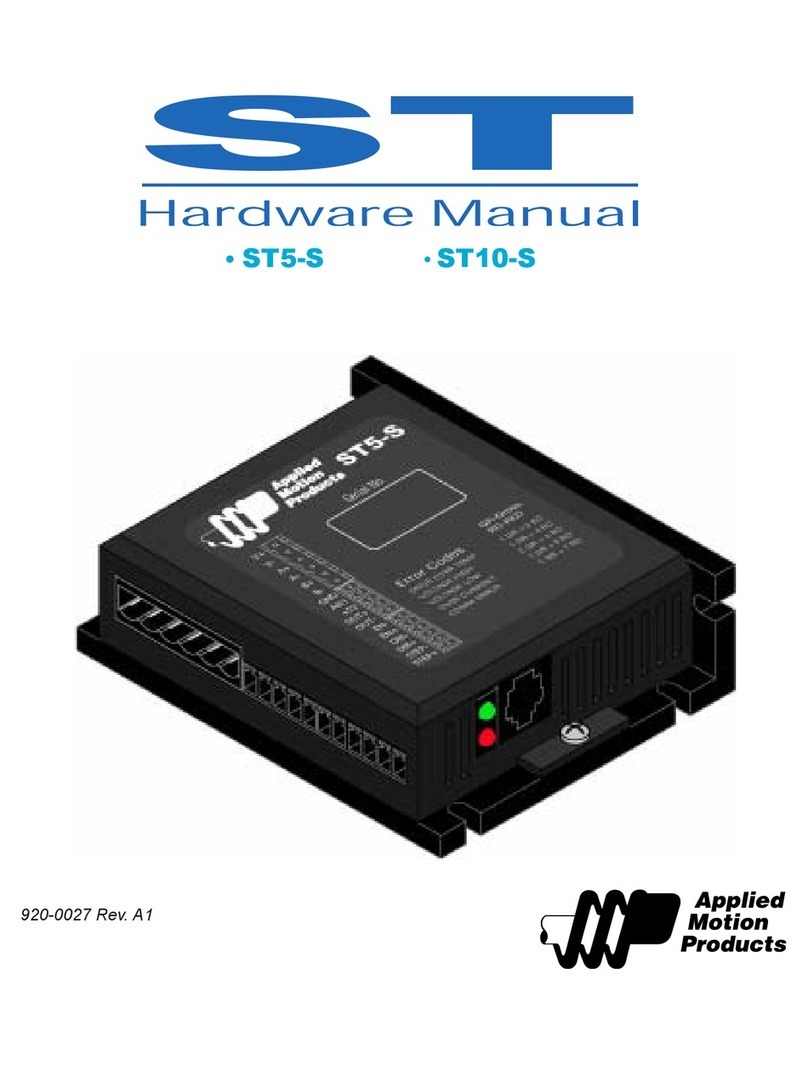
Applied Motion Products
Applied Motion Products ST10-S Hardware manual
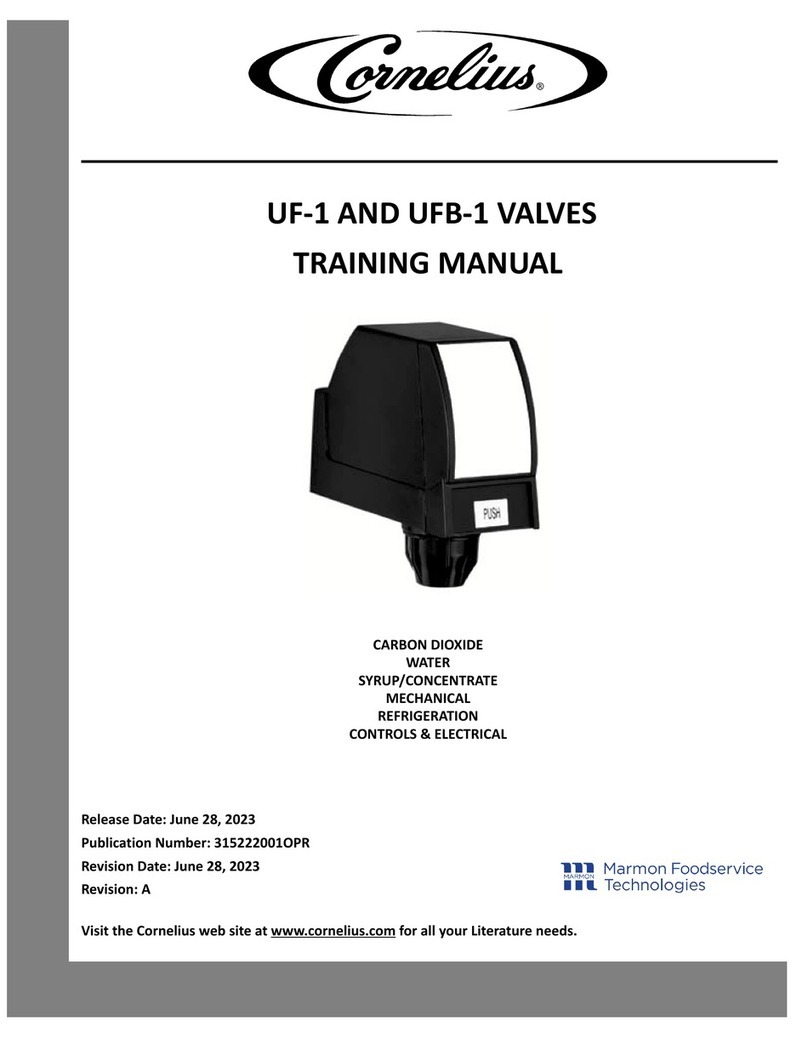
Cornelius
Cornelius UF-1 Training manual
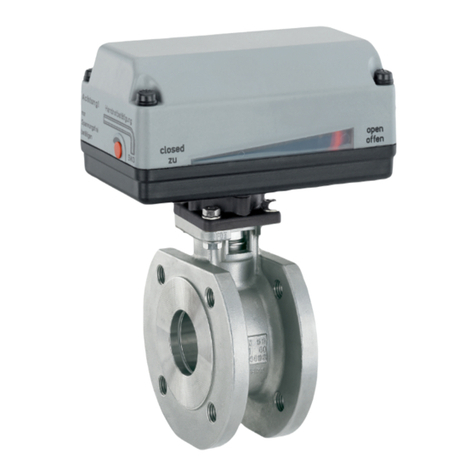
GEM
GEM 768 operating instructions
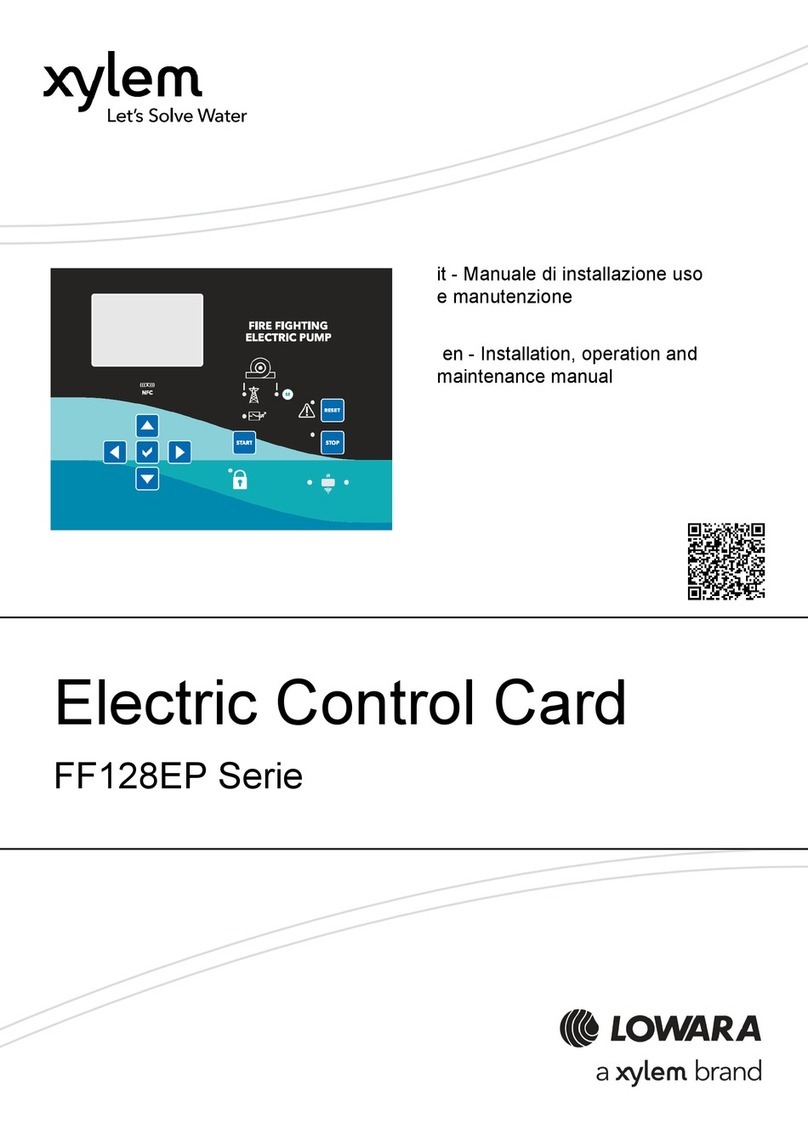
LOVATO ELECTRIC
LOVATO ELECTRIC FF128EP Series Installation, operation and maintenance manual
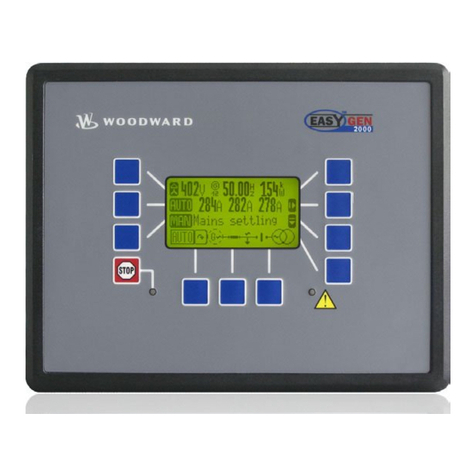
Woodward
Woodward easYgen-2000 Series manual