Nakanishi E3000C User manual

CAUTIONS FOR HANDLING AND OPERATION
...P.3
FEATURES ..............................................P.5
SPECIFICATIONS ....................................P.5
MILLING AND DRILLING CAPACITY REFERENCE
....P.9
TORQUE CHARACTERISTICS ...............P.10
NOMENCLATURE .................................P.11
CHANGING FUSES................................P.13
BRACKET INSTALLATION .....................P.13
POWER CORD CONNECTION ...............P.16
MOTOR CORD CONNECTION ...............P.16
AIR HOSE CONNECTION.......................P.17
CHANGING CUTTING TOOLS ................P.18
REPLACING THE COLLET .....................P.19
FIXTURING THE MOTOR/SPINDLE........P.19
OPERATION PROCEDURES ..................P.21
EXTERNAL INPUT/OUTPUT CONTROL SIGNAL SPECIFICATIONS
...P.23
PROTECT FUNCTION............................P.30
BREAK-IN PROCEDURE .......................P.32
CUTTING TOOL CAUTIONS...................P.33
TROUBLE SHOOTING ...........................P.34
SYSTEM CHART ...................................P.35
SETTING OF OPERATING PARAMETERS
.....P.36
CONTENTS
5
4
3
2
1
6
7
8
9
10
11
12
13
14
15
16
17
18
19
20
21
22
'08.01.003 A
E3000C
OM-K0446E Rev.B
E3000CK0446Ee08010808.1.86:34PMページ1

1 2
WARNING !
When using electric tools, basic safety precautions should always be followed to reduce the risk of fire, electrical
shock and personal injury, including the following.
Read all these instructions before operating this product and save these instructions.
A. GROUNDING INSTRUCTIONS
1. In the event of a malfunction or breakdown, grounding provides a path of least resistance for electric current
to reduce the risk of electric shock. This tool is equipped with an electric cord with a grounding conductor
and a grounding plug. The plug must be plugged into a matching outlet that is properly installed and
grounded in accordance with all local codes and ordinances.
2. Do not modify the plug provided - if it will not fit the outlet, have the proper outlet installed by a qualified
electrician.
3. Improper connection of the grounding conductor can result in electric shock. The conductor with insulation
having an outer surface that is green with or without yellow stripes is the grounding conductor. If repair or
replacement of the electric cord or plug is necessary, do not connect the grounding conductor to a live
terminal.
4. Check with a qualified electrician or service person if the grounding instructions are not completely
understood, or if in doubt as to whether the tool is properly grounded.
5. Use only 3-wire extension cords that have 3-prong grounding plugs and 3-pole receptacles that accept the
tool's plug.
6. Repair or replace damaged or worn cord immediately.
7. This tool must be used on a circuit that has an outlet that looks like the one illustrated in Sketch A in Figure
(
below
)(
115V
)
. The tool has a grounding plug that looks like the plug illustrated in Sketch A in Figure
(
below
)
.
8. FOR Installation in Machine Electrical Cabinet or when wiring
directly to machine internal power terminal strip:
1) Please refer to the pin diagram below for the proper wiring
configuration. The plug shown is the female plug that attaches
to the NE211 main power inlet.
2) Make sure you test each individual wire to verify proper circuit
prior to attaching any wire to the terminal block. Do not assume
wire colors are the same for all power cords.
9. Install an over current protective device of maximum 10 Amp on
the NE211 main power circuit.
10. USE PROPER EXTENSION CORD. Make sure your extension cord
is in good condition. When using an extension cord, be sure to use
one heavy enough to carry the current your product will draw.
An undersized cord will cause a drop the line voltage resulting in
loss of power and overheating.
Table
(
below
)
shows the correct size to use depending on cord
length and nameplate ampere rating.
If in doubt, use the next heavier gage. The smaller the gage
number, the heavier the cord.
Minimum gage for cord
Ampere Rating Volts Total length of cord
120V
240V
More
Than
Not
More
Than
Only the applicable parts of the Table need to be included. For instance,
a 120-volt product need include the 240-volt heading.
IMPORTANT INSTRUCTIONS AND WARNING - Electric Devices
0
6
10
12
6
10
12
16
18
18
16
14
16
16
16
12
16
14
14
14
12
12
Not Recommended
7.5m (25ft.)15m (50ft.)30m (100ft.)45m (150ft.)
15m (50ft.)30m (100ft.)60m (200ft.)90m (300ft.)
B. OTHER WARNING INSTRUCTIONS
1. For your own safety read instruction manual before operating tool.
2. Wear eye protection.
3. Replace cracked wheel immediately.
4. Always use guards and eye shields.
5. Do not overtighten wheel nut.
6. Use only flanges furnished with the grinder.
7. REMOVE ADJUSTING KEYS AND WRENCHES. Get in the habit of checking to see that keys and adjusting
wrenches are removed from tool before turning it on.
8. KEEP WORK AREA CLEAN. Cluttered areas and benches invite accidents.
9. DON'T USE IN DANGEROUS ENVIRONMENT. Don't use power tools in damp or wet locations, or expose
them to rain. Keep work area well lighted.
10. Risk of injury due accidental starting. Do not use in an area where children may be present.
11. DON'T FORCE TOOL. It will do the job better and safer at the rate for which it was designed.
12. USE RIGHT TOOL. Don't force tool or attachment to do a job for which it was not designed.
13. WEAR PROPER APPAREL. Do not wear loose clothing, gloves, neckties, rings, bracelets, or other jewelry
that might get caught in moving parts. Nonslip footwear is recommended. Wear protective hair covering to
contain long hair.
14. ALWAYS USE SAFETY GLASSES. Everyday eyeglasses only have impact resistant lenses, they are NOT
safety glasses. Also use face or dust mask if cutting operation is dusty.
15. SECURE WORK. Use clamps or a vise to hold work when practical. It's safer than using your hand and it
frees both hands to operate tool.
16. MAINTAIN TOOLS WITH CARE. Keep tools sharp and clean for best performance and to reduce the risk of
injury to persons. Follow instructions for lubricating and changing accessories.
17. DISCONNECT TOOLS before servicing; when changing accessories, such as blades, bits, cutters, and like.
18. REDUCE THE RISK OR UNINTENTIONAL STARTING. Make sure switch is in off position before plugging in.
19. USE RECOMMENDED ACCESSORIES. Consult the owner's manual for recommended accessories. The use
of improper accessories may cause risk of injury to persons.
20. NEVER LEAVE TOOL RUNNING UNATTENDED. TURN POWER OFF. Don't leave tool until it comes to a
complete stop.
21. For recommended operating speed for various applications, please follow the instructions of bur
manufacturers.
GROUNDING
PIN (A)
COVER OF GROUND
OUTLET BOX
Grounding Method
L : Line
N : Neutral
E : Earth
LEN
Power cord connector
E3000CK0446Ee08010808.1.86:34PMページ1

3 4
Thank you for purchasing the Ultra-Precision, High-Speed spindle system, E3000.
The E3000 was designed for use on CNC lathes, robots, NC lathes and special purpose
machines. The motor, spindle and control unit are designed to work as an integrated system
capable of 60,000 min-1. This system utilizes air to cool the motor and protect the spindle,
please use an air line kit to ensure clean, dry, properly regulated air is supplied to the motor
and spindle.
The E3000 system is capable of being used with coolants and cutting lubricants.
Please read this Operation Manual carefully prior to use.
Read these cautions carefully and only use in the manner intended.
Safety instructions are intended to avoid potential hazards that could result in
personal injury or damage to the device. Safety instructions are classified as
follows in accordance with the seriousness of the risk.
CAUTIONS FOR HANDLING AND OPERATION
Class
WARNING A hazard that could result in bodily injury or damage to the device if the safety
instructions are not followed.
CAUTION A hazard that could result in light or moderate bodily injury or damage to the
device if the safety instructions are not followed.
Degree of Risk
WARNING
1. The E3000 is not a hand tool. It is designed to be used on a NC lathe or special
purpose machine.
2. In the event of a malfunction or breakdown, grounding provides a path of least
resistance for electric current, reducing the risk of electric shock. This system is
equipped with an electric cord with a grounding conductor and a grounding plug.
The plug must be plugged into a matching outlet that is properly installed and
grounded in accordance with all local codes and ordnances.
3. Don't use in dangerous environments. Protect the control unit from moisture and
other contaminants. Failure to protect the control unit can result in damage to
internal components and injury to the operator.
4. Always wear safety glasses. Everyday eyeglasses only have impact resistant
lenses, they are not safety glasses. Also use a dust or face mask whenever the
motor is running.
5. Never touch the motor, spindle or cutting tools when the spindle is rotating.
6. Reduce the risk of unintentional starting. Make sure the power switch is in the
Off position before connecting the control unit or plugging the system in.
7. Do not apply excessive force. This may cause tool slippage or tool damage.
8. Do not exceed the maximum allowable tool speed. For your safety, use tools
below the maximum allowable speed.
9. Do not use bent, broken, chipped, out of round or sub-standard tools. They can
shatter or explode, and may cause injury.
CAUTION
1. Motor cooling and Spindle purge air is required to operate the system.
Air hose must be connected to the Air in joint on the front of the control unit.
Between 0.25MPa-0.3MPa air must be supplied.
2. Do not disassemble, modify or attempt to repair the unit or motor as it will
damage internal components and there are no user serviceable parts.
3. When errors occur and error lamp flashes, check and correct the cause of the
malfunction before continuing use. Failure to correct the problem will result in
damage to the unit and motor.
4. When the Warning Lamp on the control unit lights conditions exist that could
result in dangerous operation. Check operating conditions and continue use
only after correcting the problem.
5. Do not hit, drop or subject motor, spindle or control unit to shock as this will
cause damage to internal components and result in malfunctions.
6. Check the tool shank and collet prior to use to ensure they are clean and free of
burs. The introduction of foreign particles or metal chips into the collet or
spindle can cause damage and loss of precision.
7. Make sure that the collet chuck is firmly tightened prior to rotating the spindle.
If the collet chuck and chuck nut are not firmly tightened the tool may be
ejected during rotation resulting in injury.
8. The electric motor and spindle require air for cooling and protection : ensure
that this supply is clean, dry air. Introduction of dust, moisture or other
contaminants into the motor and spindle will cause damage to internal
components.
9. Do not place anything on top of the control unit or block cooling vents.
10. Do not install system next to RF noise sources as malfunctions can occur. If
smoke, noise or strange odors emanate from the unit or motors immediately
turn off the power switch, disconnect and take to a NAKANISHI dealer for
evaluation.
11. Use only tools with shank diameter tolerance similar to the chuck I.D. tolerance.
12. Check if tools, chucks or chuck nuts are damaged before working.
13. When using NE211 continuously, refer to Continuous Area on Torque
Characteristics or check LOAD meter maximum (3 Green Lamps).
14. Attach the provided connector cover when not using Input/Output Connector
A/B or Selector Communication Connector.
15. Stop working immediately when abnormal rotations or unusual vibration are
observed.
16. Do not over tighten the chuck. This may cause spindle damage.
17. Select suitable products or tools for the applications. Do not exceed the
capabilities of the spindles or cutting tools.
1
E3000CK0446Ee08010808.1.86:34PMページ3

(1) Control Unit
5 6
SPECIFICATIONS
(1) The E3000 system is designed to be mounted in a CNC lathe, robot, NC lathe or special
purpose machine for drilling, milling, slitting, grinding or other similar application.
(2) A high-speed brushless motor is used to achieve a maximum speed of 60,000 min-1 and
eliminate the nuisance of brush maintenance.
(3) Speed control and protection functions utilize a high performance microprocessor.
(4) Automatic control and monitoring of spindle functions are possible.
(5) Wide speed range, 1,000-60,000 min-1 makes high precision machining possible.
(6) Compact control unit design allows easy installation in space restricted machines.
Connectors and control panel are front mounted for easy access.
(7) Control Unit is capable of being connected to AC100V to 240V power sources.
(8) Two types of control units are available. Standard type NE211 and NE211-OP1 which
conforms to European standards for safe, automatic machine operation.
(9) Gear Mode Select Switch installed. Set Gear Mode to display the rotating speed at the
cutting tool when using an angle spindle or speed reducer.
(
10
) The motor/spindle housing is made of Stainless Steel (SUS-416), precision ground to 20,
25 or 30mm making the motor/spindle very versatile and easy to mount on NC or special
purpose machines.
(
11
) Installation and motor replacement for the E3000 system is very simple because the
connector is placed at the rear of the motor.
*Note2 <NE211-OP1 Features>
• The installed Safety Relay is designed to comply with EN standards, ‘a’ contacts switch the Motor Power Line
and ‘b’ contacts switch the external outputs to the machining center’s controller.
• The Safety Relay utilizes Normally Open contacts. The Emergency Stop Signal lines must be supplied with
power to hold the Safety Relay contacts closed and allow the control unit to supply power to the motor. Any
system errors, trouble with the machining center or the connections between the E3000 control unit and the
machining center’s controller will cause the relay contacts to open and the E3000 motor to stop.
• The Emergency Stop Signal Input can be connected to any and all portions of the machine’s safety systems to
stop the E3000 motor any time that stoppage of the spindle and motor is required.
• The ‘b’ contact outputs can be used to detect an open circuit on the motor line and integrated with the
machines safety systems to stop the machine in case of trouble. If the ‘a’ contacts of the Safety Relay are
welded together by an over load or short circuit the ‘b’ contacts’ separation is maintained at more than 0.5mm
spacing by the relay’s spring release mechanism.
3-1 Specifications
*Note1 : Protectively Separated
FEATURES
(2) Motor Spindle
*Note : Collet Chucks are sold separately. Please specify the desired Collet Chuck size when ordering.
CHA-[][] : ø0.5mm-ø4.0mm in 0.1mm increments and ø2.35mm, ø3.175mm
CHK-[][] : ø0.5mm-ø6.0mm in 0.1mm increments and ø2.35mm, ø3.175mm, ø6.35mm
*
Caution!
:Control Limitation of Motor Speed
The fllowing motor is automatically controlled the speed.
So,please check the specification of the Motor Spindle prior to use.
For EM25N-5000,EM25-5000 : 1,000-50,000min-1
For EM-3030J : 1,000-32,000min-1
2
3
Model NE211 NE211-OP1 *Note2
Input AC100V-240V, 50/60Hz, 1PHASE, 1.8A
Output AC33V, 0-1KHz, 3PHASE, 2.4A
Operating Temperature 0-40°C
Ambient Humidity MAX. 85%
Over Voltage Category Ⅱ
Pollution Degree 2
Speed Range 1,000-60,000 min-1
Control Signal
Input
*Note1
Transistor Activation Connections : 6
Analog Connections : 1 Transistor Activation Connections : 9
Analog Connections : 1
Output
*Note1
Transistor Activation Connections : 9
Analog Output Connections : 3
Transistor Activation Connections : 9
Relay Contact Connections : 2
Analog Output Connections : 3
Protection Circuits
Over-Voltage, Over-Current,
Over Load, Sensor Malfunction,
Overheat, Brake Malfunction,
Spindle Lock, Low Air Pressure,
Start-Up Error, Over-Speed
Over-Voltage, Over-Current,
Over Load, Sensor Malfunction,
Overheat, Spindle Lock,
Brake Malfunction, Low Air Pressure,
Start-Up Error, Over-Speed,
Emergency Stop Circuit
Weight 2.8kg
Dimensions W88 x D138 x H238 mm
Model EM20-S6000 EM25-S6000 EM30-S6000
Speed Range 60,000 min-1
Spindle Accuracy Within 1µm
Diameter ø20 mm ø25 mm ø30 mm
Max. Output 250W 350W
Collet Chuck
(Optional) *Note CHA-[][] CHK-[][]
Weight (W/O Motor Cord)
230g 375g 575g
IP Rating IP64 (If not using cooling air rating is IP40)
E3000CK0446Ee08010808.1.86:34PMページ5

-0.01
0
ø20
11.5
(156)
(14.7) 133
(8.3)
58 (75)
ø11.8
ø20
20
-0.02
-0.02
-0.01
-0.01
ø20 -0.02
-0.01
Fig. 3
(2) Motor Spindle (EM20-S6000)
• Chuck Nut (CHN-A) : Provided • Spanner (8 x 5), (9 x 11) : 1pc. each
• Operation Manual
7 8
(162.5)
139.5
(8.3)
64 (75.5)
ø2525 -0.02-0.02
-0.01-0.01
-0.01
0
ø25
11.5
(14.7)
ø11.8
ø25 -0.02
-0.01
(3) Motor Spindle (EM25-S6000)
(175.2)
(17.4) 149.5
12.5 68 (81.5)
(8.3)
ø2525 -0.02-0.02
-0.01-0.01
-0.01
0
ø30
ø16.9
ø30 -0.02
-0.01
Fig. 5
(4) Motor Spindle (EM30-S6000)
Fig. 4
Model Standard Equipment •Accessories
NE211
• Power Cord 2m •Air Hose with filter
•Reducer •Connector Cover (Provided)
•Connector Cap (Provided) •Bracket
•Nylon Tension Relief •Screw
•Rubber Pad •Fuse (T6.3AL) : 2pcs.
•Operation Manual
3-3 Standard Equipment
(1) NE211
Model Standard Equipment •Accessories
EM20-S6000 • Chuck Nut (CHN-A) : Provided • Spanner (8 x 5), (9 x 11) : 1pc. each
• Operation Manual
(2) EM20-S6000 *Sold separately
Model Standard Equipment •Accessories
EM25-S6000
(3) EM25-S6000 *Sold separately
Model Standard Equipment •Accessories
EM30-S6000 • Chuck Nut (K-265) : Provided • Spanner (12 x 14) : 2pcs. each
• Operation Manual
(4) EM30-S6000 *Sold separately
Model Standard Equipment •Accessories
EMCD-3000 • Air Hose • Connector Cap (Provided)
(5) Motor Cord 4M *Sold separately
3-2 Diagrams
168
246
138
88
188
M4x0.7
Stepped Bracket
65
45
86.2
4.5
10
(1) NE211 Control Unit
Fig. 1 Bottom Mounting
236
138
144
271
251
65
91
45
10
4.5
M4x0.7
Stepped Bracket
Fig. 2 Back Mounting
E3000CK0446Ee08010808.1.86:34PMページ7

910
MILLING AND DRILLING CAPACITY REFERENCE TORQUE CHARACTERISTICS
(1) Torque Characteristics of ø20, ø25 mm
(2) Torque Characteristics of ø30 mm
*End Mill Cutting Condition
• Use End Mill 2 flutes with ultra hard coating.
• Used in conjunction with water or oil based
coolants.
*Milling Depth/per
1D : End Mill Size
0.9D
0.2D
Work Material
*Drilling Conditions
• Use Twist Type Drill with ultra hard coating.
• Used in conjunction with water or oil based
coolants.
*Drilling/Step
D : Drilling Size
1D
0.2D
6050403020100
0
450
9
400
8
350
7
300
6
250
5
200
4
150
3
100
2
50
1
Torque (cN.m)
Output (W)
Speed ( x 103min-1 )
Torque
Output
Continuous Duty Area
6050403020100
0
450
9
400
8
350
7
300
6
250
5
200
4
150
3
100
2
50
1
Torque (cN.m)
Output (W)
Speed ( x 103min-1 )
Torque
Output
Continuous Duty Area
•
The following tables express the E3000 milling & drilling capacity with the max usable cutting tool
diameter under our conditions.
•Cutting tool capabilities vary depending on the tools being used or cutting conditions.
ø : Tool Size S : Spindle Motor Speed (min-1) F : Feed Rate (mm/min)
ø : Tool Size S : Spindle Motor Speed (min-1) f : Drilling Step (mm/rev.)
45
S50C
(Carbon Steel)
SUS304
(Stainless Steel)
A2017
(Aluminium)
EM30-S6000
ø2.0 ø2.0 ø2.0
ø1.5
ø1.5
ø1.5
ø1.5
S : 16,000
F:480 S : 12,000
F:250 S : 57,000
F:2,400
S : 20,000
F:1,000 S : 16,000
F:700 S : 60,000
F:5,000
S : 20,000
F:100 S : 16,000
F:100 S : 60,000
F:1,000
ø1.5
ø1.5
EM25-S6000
EM20-S6000
Milling
S50C
(Carbon Steel)
SUS304
(Stainless Steel)
A2017
(Aluminium)
EM30-S6000
ø2.5 ø1.5 ø3.0
ø1.0
ø1.0
ø2.5
ø2.5
S : 18,000
f : 0.06 S : 10,000
f : 0.01 S : 23,000
f : 0.08
S : 20,000
f : 0.05 S : 12,000
f : 0.01 S : 23,000
f : 0.07
S : 20,000
f : 0.05 S : 12,000
f : 0.01 S : 23,000
f : 0.07
ø2.0
ø2.0
EM25-S6000
EM20-S6000
Drilling
E3000CK0446Ee08010808.1.86:34PMページ9

[1]Unit (NE211)
[2]Control Panel
Refer to Control Panel details.
[3]Input/Output Connector A
Connector for automatic control and monitoring of motor/spindle system. When not in use please
install the connector cover to prevent damage or contamination of connector or pins.
[4]Input/Output Connector B
Connector for automatic monitoring of emergency conditions. The pin configurations of this
connector are different on the NE211 and NE211-OP1. Please refer to page 27 for a complete
description of the pin input and output signals. When not in use please install the connector cover
to prevent damage or contamination of connector or pins.
[5]Communication Connector for NE212 Selector Unit
When not in use please install the connector cover to prevent damage or contamination of
connector or pins.
[6]Motor Connector
[7]Air Input Joint
Supply clean, dry, regulated air for motor cooling. Regulate air to between 0.25MPa-0.3MPa.
Air Consumption 30NR/min. Air must be supplied to operate the system.
[8]Air Output Joint
Connect Air Hose to supply clean, dry, regulated air for motor cooling.
[9]Power Switch
[
10
]Main Power Inlet
Insert the Plug for Power Cord (Provided). Fuse (T6.3AL 250V) : 2pcs.
[
11
]Digital Speed Indicator (SPEED)
Preset Speed, Actual Speed, Warning and Error Codes are displayed to 2 digits. When the motor is
stopped the Preset Speed is displayed, when the motor is rotating the actual speed is displayed.
The display also displays the error codes when an error has occurred.
And displays the gear ratio setting when the gear mode is set.
[
12
]Load Monitor LED (LOAD)
The motor/spindle load is displayed by 6 LED’s (3 Green, 2 Yellow and 1 Red). Continuous
operation is possible with up to all 3 green LED’s lit. If one of the yellow LED’s is lit the
motor/spindle can only be run for a short time. Please refer to PROTECT FUNCTION of this
manual for allowable duration of high load operation. When any of the yellow or red LED’s are lit
the warning LED (Warning) [
20
]will flash, if this condition is continued beyond the allowable interval
the error LED (Error) [
19
]will flash and the motor/spindle will be shut down.
[
13
]Motor Speed Adjustment Switch (SPEED)
Steplessly adjustable speed control. Pushing the UP button will increase motor speed. Speed is
adjustable from 1,000-60,000 min-1.
[
14
]Start Switch (START)
Starts and stops motor rotation
[
15
]Rotation Direction Switch (FWD./REV.)
Right hand rotation (FWD.) and left hand rotation (REV.) are as viewed with the cutting tool facing
the operator. With the cutting tool facing the operator right hand rotation (FWD.) will be clockwise
rotation.
[
16
]Controller Switch (AUTO-MANUAL)
This switch selects motor/spindle control from the Control Panel or from an external source.
Manual : Control Panel
Auto : External control through the input/output connector.
[
17
]Gear Mode Select Switch (GEAR)
Set Gear Mode to display the rotating speed at the cutting tool when using an angle spindle or
speed reducer. Select the gear ratio by [
13
] Motor Speed Adjustment Switch. When setting gear
mode, the gear ratio will be displayed in [
11
] Digital Speed Indicator.
[
18
]Error Reset Switch (RESET)
This switch resets and allows restarting of the motor/spindle after an error has been corrected.
Some error codes will not allow the unit to be reset until after the power switch has been turned off.
11 12
NOMENCLATURE 6-2 Control Panel
Fig. 7
[
20
]
[
13
]
[
19
]
[
18
]
[
17
]
[
10
]
[9]
[6]
Fig. 6
[2]
[3]
[4]
[5]
[7]
[8]
[
14
]
[
15
]
[
16
]
[
11
]
[
21
]
[1]
6
17
[
12
]
E3000CK0446Ee08010808.1.86:34PMページ11

13
WARNING
•Before removing fuse make sure that the main power switch is in the off position
and the power cord is disconnected from the power supply.
•Make sure and use only the properly rated and type of fuse.
•Failure to use the proper type and rated fuse will result in fire, injury, electric
shock and/or product damage.
CHANGING FUSES
Fig. 8
BRACKET INSTALLATION
CAUTION
8-1 Bottom Mounting
8-2 Back Mounting
Fig. 9
Fig. 10
Attach the 2 brackets using the 4 hole on the bottom of the unit using the provided screws.
Attach the 2 brackets using the 4 holes on the back of the unit using the provided screws.
Bracket
Bracket
Cap
Bracket
Bracket
14
[
19
]Error LED (ERROR)
When a serious problem with the system is detected this LED blinks, the motor/spindle is
shut down and the Digital Speed Indicator [
11
]displays the error code.
[
20
]Warning LED (WARNING)
The operating and working conditions of the system are constantly monitored and the
warning LED blinks when a hazardous condition has been detected. When a hazardous
condition is detected the warning LED blinks and the Digital Speed Indicator [
11
]alternates
between the warning code and the actual or preset speed, depending on whether or not the
motor/spindle is rotating.
[
21
]Rotating LED (RUN)
When the motor is rotating this LED will flash.
(1)
Push on the clips on the top and bottom of the fuse holder and remove the fuse holder and
fuses.
(2) Remove the bad fuse or fuses and replace with the proper type and rating of fuse as listed
below and determined by the input voltage being used.
Fuse : T6.3AL (250V)
(3) Replace the fuse holder containing the fuses into the fuse inlet box and make sure it
snaps in place.
Never install the unit in such a manner as to block the air vents on the side of the
control unit. This manner of installation will cause heat buildup and damage to the
internal components of the control unit.
7
8
(1) Two mounting brackets are provided with the system.
(2) The brackets can be installed on the bottom or on the back of the control unit.
(3)
After installing the brackets you can use the screw cutouts to mount the control unit.
E3000CK0446Ee08010808.1.86:34PMページ13

15 16
POWER CORD CONNECTION
WARNING
Only use grounded power sources. Failure to properly ground the unit may result
in electric shock, injury, fire and/or damage to the system components.
(1) Insert the female plug into the main power inlet box [
10
] on the front of the unit.
(2) A screw hole is provided on the lower, right side of the control unit for attaching the
tension relief. Use the provided Nylon Tension Relief to attach the power cord to the side
of the control unit.
Fig. 15
MOTOR CORD CONNECTION
(1) Align the guide pin A on the motor plug with the key way B on the motor socket on the
front of the control unit.
(2) Screw in the coupling nut C of the motor plug to the motor socket D on the front of the
control unit.
Fig. 17Fig. 16
AB
D
C
8-3 Rubber Pad Installation
When placing the control unit horizontally, the Rubber Pad (Provided) is installed at the side
of the air vents. Install the control unit so the air vents are underneath the control unit.
When installing horizontally, remove the 4 screws on the Control Panel and remount the
panel at a 90° Angle.
Before removing the control panel be sure the Power Switch is OFF and remove the Power
Inlet Cord.
8-4 Proper Clearance
When installing 2 or more control units in the machine cabinet make sure to check that each
single control unit has the proper clearance on all sides.
Fig. 11 Fig. 12
Fig. 13
Vertical mounting
Horizontal mounting
min.30mm min.20mm
min.30mm min.30mm
Rubber Pad
Control Panel
Screw
CAUTION
Never install the air vents upward when installing the control unit horizontally.
This may cause damage to control unit.
[
10
]
CAUTION
Before connecting the motor cord, make sure the power source is switched off.
Nylon Tension Relief
9
10
Fig. 14
min.30mm min.20mm
min.30mm min.30mm
E3000CK0446Ee08010808.1.86:34PMページ15

CHANGING CUTTING TOOLS
17 18
(1) Set the provided 12mm wrench for EM30-S6000/8mm wrench for EM20-S6000 & EM25-
S6000 on the spindle.
(2) Place the provided 14mm wrench for EM30-S6000/11mm wrench for EM25-S6000 &
EM20-S6000 on the chuck nut and turn it counterclockwise to loosen the collet and
remove the cutting tool. (The first turn will loosen the chuck nut, but the tool will not
release and turning will become stiff. Keep turning through the stiffness and the collet will
open.)
(3) Insert the new tool and tighten the collet by turning clockwise.
14
14
12
12
Loosen
Tighten
Spindle
Tool
Chuck Nut
Fig. 19
CAUTION
Never install a collet into the spindle quill without first assembling it in the chuck
nut. Do not tighten the collet without mounting a cutting tool or dummy bur as this
will result in damage to the collet, spindle and chuck nut and make it impossible to
remove the collet.
AIR HOSE CONNECTION
(1) Insert the provided ø6mm filtered air hose from the AL-0201 air line kit into the inlet joint
[7]on the front of the control unit. (If you are not using the AL-0201 air line kit make sure
that the incoming air supply is dry, clean air.)
(2) Insert one end of the provided ø3.2mm cooling air hose into the back of the motor.
(3) Insert the other end of the ø4mm cooling air hose into the air output joint [8]on the front
of the control unit using the provided ø6mm to ø4mm adaptor.
(4) Regulate air pressure between 0.25-0.3MPa.
The system can be set to operate without cooling air. Please see parameter setting
to set this option. Maximum speed is 30,000min-1 when not using cooling air.
Note : It is not recommended to use the system in this manner for general machining.
This setting is only for light cutting and not for use with coolants.
Fig. 18
CAUTION
1. Regulate the air supply between 0.25-0.3MPa. If the air pressure is too low the
control unit will not operate.
2. The cooling air provides two functions, to cool the electric motor and to protect
the spindle from contaminants. If air supply is shut off do not subject the spindle
to direct coolant spray or use in dusty areas.
3. Do not bend the air hose in any sharp bends or pull on the hose this can cause
the hose to break, cut off the air supply or weaken the hose over time resulting in
deterioration of the motor and spindle.
4. Attach the connector cover (provided) for safety, when not using Input/Output
Connector A/B and communication connector.
Reducer
(ø6–ø4
Adaptor)
[8]
[7]
Air Hose with filter
Air Joint
[9]
11 12
E3000CK0446Ee08010808.1.86:34PMページ17

19 20
(2) The installation shown in Fig. 23 is the recommended fixturing method. If this is not
possible, install as shown in Fig. 24. Do not use set screws directly in contact with the
motor or spindle body as shown in Fig. 25, this will result in damage to the housing and
internal components. When mounting the spindle take care not to fixture over the bearings
as this will result in bearing damage.
Fastening Bolt
Slit
Bushing with Slit
Fastening Bolt
Slit of Bushing
Fastening Bolt
Fig. 23 Fig. 24 Fig. 25
CAUTION
•Caution about tightening the bolt
Do not over tighten the bolt. This may cause damage to the spindle’s precision.
Tighten the bolt until the spindle body can not be turned by hand within the Fixture.
Apply working force and check that the spindle is tight before use.
•Caution about split type Holder
Insert a shim into the holder bore, and tighten the bolt with the specified torque.
Manufacture the holder with roundness and cylindrical tolerance of less than 5µm.
Insert a thin shim into the split in the holder and reduce the shim size in 5µm
increments until the spindle is held firmly.
Tighten the clamping bolt to the torque specified for that size and type of bolt.
The final responsibility for ensuring a product’s suitability for use in a given
application is left to the designer of the equipment in which NAKANISHI’s spindle is
installed. NAKANISHI offers spindles with a wide variety of capabilities and
specifications. Please carefully check the product’s specifications against the
requirements of your application and verify suitability and safety prior to initial use.
WARNING
When installing a motor/spindle to a fixed base, make sure the fixed base is
grounded in order to avoid the risk of an electric shock.
REPLACING THE COLLET
(1) Remove the cutting tool according to the “ CHANGING CUTTING TOOLS” procedure
above and remove chuck nut assembly. (Fig. 20)
(2) The collet and chuck nut are held together by a groove in the collet and a flange in the
chuck nut. To remove the collet hold the chuck nut in one hand and push diagonally down
on the collet. The collet should pop out. (Fig. 20)
(3) Install the new collet in the chuck nut by positioning the collet in the chuck nut and
pressing down on a flat surface. (Fig. 21)
14
12
Loosen
Spindle
Chuck Nut
Fig. 20 Fig. 21
Spanner Seat
Collet Chuck
Push
Chuck Nut
FIXTURING THE MOTOR/SPINDLE
(1) When mounting the motor/spindle, refer to the recommended clamping area. (Fig. 22)
If the motor/spindle is mounted incorrectly, this will cause and damage to the spindle.
(The following drawings are the recommended clamping areas for EM30-S6000. As for
EM20-S6000/EM25-S6000, please refer to the respective operation manuals)
Fig. 22
13
14
20 36
Recommended
Clamping Area
( )
12
E3000CK0446Ee08010808.1.86:34PMページ19

21
(4) Motor Start/Stop
Push Start Switch [
14
]and START LED will illuminate.
(5) Setting Motor Speed
Set the speed by pushing the Motor Speed Adjustment Switch [
13
].
•Motor Speed Range is 1,000-60,000 min-1.
If the air pressure is too low the control unit will not operate.
•The motor speed is displayed in 1,000 min-1. 60 equals 60,000 min-1.
•During Gear Mode operation the speed change rate of the Motor Speed Adjustment
Switch will change.
Fig. 27
2-2 Setting Auto Mode
(1) Set motor rotating direction
Input the motor rotating direction signal to Pin No. 2 : DIR_IN
Right hand rotation is OFF ‘Open’ (“FWD.” LED will light)
Left hand rotation is ON ‘Closed’ (“REV.” LED will light)
(2) Set 500 min-1 rotation
Input the centering rotation signal to Pin No. 16 : 500 min-1
500 min-1 LED will light
Never use 500 min-1 centering rotation for cutting
(3) Setting Gear Ratio
Push Gear Ratio Switch [
17
]. Check the spindle/reducer gear ratio, select the gear ratio by
pushing the Motor Speed Adjustment Switch [
13
].
Display Indicator [
11
]will display the gear ratio as follows 1.0, 1.5, 2.7, 4.0, 16.
If you are not using the straight type speed reducer or an angle type spindle, you do not need
to set Gear Ratio Mode. (Use Gear Ratio 1.0)
All the functions of the system can be controlled by input control signals to Input/Output
Connector A [3] (Except setting gear ratio)
[
13
]
[
14
]
[
17
][
15
]
OPERATION PROCEDURES
1. Select Control Mode (Manual/Auto)
Fig. 26
2. Setting motor rotating direction, gear ratio (GEAR), Motor Start/Stop, Motor Speed
2-1 Setting Manual Mode
(1) Set motor rotating direction
Push the motor rotating direction switch [
15
].
Select FWD. Right hand rotation
Select REV. Left hand rotation
(2) Set 500 min-1 centering rotation
To select 0.5 (500 min-1), stop the motor and push Motor Speed Adjustment Switch [
13
]to
lower the motor speed. The Display Indicator will show 5 then 0.5. Never attempt to cut
while rotating in the centering mode.
(3) Setting Gear Ratio
Push Gear Mode Switch [
17
]. Check the spindle or gear reducer gear ratio, select the
correct gear ratio by pushing Motor Speed Adjustment Switch [
13
].
Display Indicator [
11
]will show the selected gear ratio. 5 possible gear ratios can be
selected as the follows 1.0, 1.5, 2.7, 4.0, 16.
If you are not using the straight type speed reducer or an angle type spindle, you do not
need to set Gear Ratio Mode. (Use Gear Ratio 1.0)
When Gear Mode is active the dot after the second digit on the Display Indicator will
flash.
(1) Using the control switch [
16
] you can select between Manual (Front Panel Control) or Auto
(External Signal Source) modes. External Signal Source can be used to control Motor
Start/Stop, Rotational Direction, Motor Speed, and etc.
(2) Manual Mode-Front Panel Operation.
Auto Mode-Control by External Signal Source.
[
16
]
22
[
15
]
[
13
]
[
17
]
[
11
]
15
[
11
]
E3000CK0446Ee08010808.1.86:34PMページ21

23 24
Pin No.
Pin Name Description
Input/Output
Signal Function
11
12
13
16
17
18
19
22
14
15
20
21
23
24
25
VCC
MOTOR_1
GND
500 min-1
SEL0
COM (-)
PULSE
—
START
UD-IN
WARNING
COIN
VR
LOAD
SPEED_V
Power Source for
Analog Signal
Motor Current
Monitor
Power Source GND
Rotates Motor at
‘Centering’ Speed
Motor Selection
Signal 0
External Power Source GND
Rotating Pulse
Not Used
Rotate Command
Signal
UP/DOWN Signal for
Motor Speed Signal
Warning Signal
Speed Achievement
Signal
Motor Speed Control
Signal
Torque Load Monitor
Rotating Speed
Monitor Voltage
Output
Output
Output
Input
Input
Output
Output
—
Input
Input
Output
Output
Input
Output
Output
+10VDC
0-10VDC
0V : 0A
10V : 20A
Internal GND
ON (Closed) : 500 min-1
OFF(Open) : Normal
Operation
OFF (Open)
ON (Closed)
External Ground
1 pulse/rotation
—
ON (Closed) : Rotation
OFF (Open) : Stop
ON (
Closed
) : Speed Up
OFF (
Open
) : Speed Down
OFF (Open) : Normal
Operation
ON (Closed) : Warning
ON (Closed) : Ordered
Speed Achieved
OFF (Open) : Ordered
Speed Not Achieved
0-10VDC
0V : 1,000 min-1
9V+: 60,000 min-1
0-10VDC
0V : 0%
10V : 200%
0-10VDC
1V : 10,000 min-1
6V : 60,000 min-1
Power Source for VR
Output +10VDC
Voltage Output shows the motor current consumption.
Output voltage is proportional to the motor current
consumption.
Internal Ground (*2)
Maintains constant 500
min-1
motor speed for centering.
Select Motor (Refer to Table 1)
Input when using Selector Unit NE212.
Connect to GND of external Power Source.
1 revolution of the motor generates one pulse. Duty 50%
(*3)
Starts and Stops motor rotation.
When Cut-IN Signal is in, 1,000 min-1 speed up.
This output shows a Warning has occurred. The
Warning Code is shown on the Digital Speed Indicator.
Voltage output shows that the motor has achieved
more than 90% of the set speed.
Sets rotating speed of Motor.
Voltage output shows the torque being applied to the
motor. Load monitor voltage x 20 equals the torque
load %. 20V=Load%
Voltage Output is proportional to the motor speed.
EXTERNAL INPUT/OUTPUT CONTROL SIGNAL SPECIFICATIONS
1. Connector A
(1) Input/Output Connector A
•Error Output Signal.
•Front Panel or External Signal Speed Control during Auto Mode Operation.
•Fix the Motor Rotation Speed.
•Set the maximum motor speed.
•Auto Control Mode Speed Adjustment Method.
•Motor Start Command Signal Method.
•Air Input monitoring override.
•Confirmation of Parameter Settings.
If an error occurs an error signal is output to the Input/Output Connectors. The default setting
is ON (‘Closed’) and OFF (‘Open’), this setting can be reversed if desired. Please refer to the
Setting of Parameters section of this manual for details on reversing these signals.
3. Setting other Motor Speed Parameters
The following Motor Speed Parameters can also be preset.
Pin No.
Pin Name Description
Input/Output
Signal Function
1
2
3
4
5
6
7
8
9
10
COM
DIR_IN
CNT_IN
RESET
SEL1
RUN
DIR_OUT
ERR
—
GND
24VDC Power
Source for External
Control Inputs
Rotating Direction
Signal
Count Pulse Signal
for setting Motor
Speed
Error Release Signal
Motor Select Signal 1
Rotating Signal
Rotating Direction
Signal
Error Signal
Not Used
Power Source GND
Input
Input
Input
Input
Input
Output
Output
Output
—
Output
+24V or 0V DC
OFF (Open) : FWD.
ON (Closed) : REV.
OFF (Open) ON (Closed)
ON (Closed) OFF (Open)
OFF (Open)
ON (Closed)
ON (Closed) : Motor Rotating
OFF (Open) : Motor Stopped
OFF (Open) : FWD.
ON (Closed) : REV.
ON (Closed) : Normal
OFF (Open) : Error
—
Internal GND
Power Source to be used for External Inputs.
+24V or 0V DC (*2)
Controls the direction of rotation of the motor.
Count Pulse for setting Motor Speed.
(Need to set parameter)
Error code can be released and the system restarted
by switching this signal OFF and ON.
Select Motor (Refer to Table 1)
Input Signal when using Selector Unit NE212.
Voltage output shows that the motor is rotating.
Voltage output shows the direction the motor is
rotating.
Error has occurred. (*1)
Error Code is displayed on the Digital Speed Display.
(*3)
Internal Ground (*2)
CAUTION
•If you input 0V, DO NOT connect PIN1 to PIN10 or 13 (Internal Ground).
•DO NOT connect PIN10 or 13 (Internal Ground) to PIN18 (External Power Source
Ground).
CAUTION
Never use the pins marked NOT USED.
*3
*1The error signal output can be reversed. Please refer to the setting of parameters section
of this manual.
*2
16
(4) Motor Start/Stop
Input the motor start signal to Pin No. 14 : START
Motor rotating is ON ‘Closed’ (START LED will light)
Motor stopped is OFF ‘Open’ (START LED is Off)
(5) Setting Motor Speed
Input the motor speed signal to Pin No. 23 : VR
•Motor Speed Range is 1,000-60,000 min-1
If the air pressure is too low the control unit will not operate.
•The motor speed is displayed in 1,000 min-1. 60 equals 60,000 min-1
E3000CK0446Ee08010808.1.86:34PMページ23

25 26
Fig. 30
Motor Speed Control Signal
Refer to Fig. 31 for connections.
Monitoring Signals
There are 3 kinds of monitoring signals : Motor Current, Torque Load Monitor and Rotating
Speed Monitor. Please refer to Fig. 32 for connections.
• Motor Current Monitor
• Torque Load Monitor
• Rotating Speed Monitor Voltage
Fig. 31
Fig. 32
V
V
V
13
25
24
12 1K
1K
1K
0V
The side of unit
Motor Current Monitor
Torque Load Monitor
Rotating Speed
Monitor Voltage
Output Signal
There are 6 kinds of output signals : rotating, rotating direction, rotating pulse, rotating
speed achieved, warning, and error. These signals are pulsed transistor activation signals.
Voltage and Current Specifications
• Applied Voltage (V max) 30VDC
• Working Current (Ip) 100mA (Rotational Pulse 50mA)
Use an external power source for output circuits. It is recommended to use the same
24VDC power source used for input signals. Please refer to Fig. 30 for connections.
(2) Input/Output Signal
Fig. 29
Fig. 28
Table 1 Motor Selection Signal
*Table 1 Motor Selection Signal is effective when using Selector Unit NE212.
Pin1 (COM) connected to +24V DC Pin1 (COM) connected to 0V DC
Input Signal
There are 8 kinds of input signals : rotation command, rotation direction, error release,
speed up-down signal, speed command pulse signal, motor selection signal 0, motor
selection signal 1, 500 min-1 speed command. These signals are +24VDC signals from an
external signal source.
Please use a separate power source that is capable of supplying 24VDC±10 %, 40mA
(5mA/circuit). Refer to Figures below for connections.
*When using NE212, input signal : Motor Selection Signal 0, Motor Selection Signal 1.
*By setting parameter, Motor Speed change is possible by pulse signal.
If input “Speed up-down signal” “Speed Command pulse signal”.
1
Select Motor SEL1 (Pin No. 5) SEL0 (Pin No. 17)
Motor 1 OFF (Open) OFF (Open)
Motor 2 OFF (Open) ON (Closed)
Motor 3 ON (Closed) OFF (Open)
Motor 4 ON (Closed) ON (Closed)
2
3
4
+24V
-
COM : 0V
18
The side of unit
R
R
0V
COM : +24V The side of unit
1
+24V
COM : 0V
1
The side of unit
10
23
11
The side of unit
10VDC Power Source for
External Control Inputs
Motor Speed Control
Potentiometer
5K 0V
E3000CK0446Ee08010808.1.86:34PMページ25

27 28
Output Signal
PIN No. 2-10, 5-13, 6-14
There are 3 kinds of output signals : “Motor Connection Monitoring”, “AUTO MODE” and
“Unit Power Source Monitoring”.
These signals are pulsed transistor activation signals.
Voltage and Current Specifications
• Applied Voltage (V max) 30VDC
• Working Current (Ip) 100mA (Rotational Pulse 50mA)
Use an external power source for output circuits. It is recommended to use a separate
power from the one used for Input/Output Connector A. Please refer to Fig. 33 for
connections.
(2) Input/Output Signals
Emergency Stop Signal Input
PIN No. 1-9
This signal is a switched 24V DC output.
Please use a separate power source that is capable of supplying 24VDC±10%,
25mA (5mA/circuit). Refer to Fig. 34 below for connections.
Normal Operation circuit is ON (Closed) Emergency Stop circuit is OFF (Open).
If the Emergency Stop Signal is OFF (Open) the Safety Relay is OFF and the power supply
to the motor is interrupted and the motor stops.
Fig. 34
Fig. 33
0V
14
6
0V
13
5
0V
10
2
+24V
The side of unit
R
R
R
The side of unit
1
9
+24V
(or 0V)
0V
(or 24V)
The side of unit
1
9
+24V
(or 0V)
0V
(or 24V)
OR
Pin No. Pin Name
Description
Input/Output
Signal Function
1
2
3
4
5
6
7
8
9
10
11
12
13
14
15
EMG-IN+
MT-CNA
SAFE-1A
SAFE-2A
AUTO+
PWON+
–—
–—
EMG-IN-
MT-CNB
SAFE-1B
SAFE-2B
AUTO-
PWON-
–—
Emergency Stop
Signal
Motor Signal
Connect Contact A
Safety Relay
Contact 1A
Safety Relay
Contact 2A
AUTO Mode
Signal (+)
Unit Power Source
Monitor (+)
Not Used
Not Used
Emergency Stop
Signal (-)
Motor Signal
Connect Contact B
Safety Relay
Contact 1B
Safety Relay
Contact 2B
AUTO Mode
Signal (-)
Unit Power Source
Monitor (-)
Not Used
Input
Output
Output
Output
Output
Output
–—
–—
Input
Output
Output
Output
Output
Output
–—
External Power Source
input for Emergency Stop
Signal or Emergency
Stop Signal OFF (Open)
Continuity, OFF (Open),
between PIN2 and PIN10
the motor is connected.
PIN3 and PIN11
continuity ON (Closed)
Safety Relay is OFF
PIN4 and PIN12
continuity ON (Closed)
Safety Relay is OFF
ON (Closed) : Main Power
Supply is connected
OFF (Open) : Main Power
Supply is disconnected
External Power Source
input for Emergency Stop
Signal or Emergency
Stop Signal OFF (Open)
Continuity, OFF (Open),
between PIN2 and
PIN10 the motor is
connected.
PIN3 and PIN11
continuity ON (Closed)
Safety Relay is OFF
PIN4 and PIN12
continuity ON (Closed)
Safety Relay is OFF
Auto Mode Operation
ON (Closed)
ON (Closed) : Main Power
Supply is connected
OFF (Open) : Main Power
Supply is disconnected
–—
–—
–—
Auto Mode Operation
PIN5 and PIN13
ON (Closed)
External Power Source input for Emergency Stop
Signal or Emergency Stop Signal. Normal Operation
ON (Closed), Emergency OFF (Open).
When there is continuity, OFF, between PIN2 and
PIN10 the selected motor is connected, if no
continuity the motor is disconnected or the motor
cord is broken.
When there is continuity between PIN3 and PIN11 ON
(Closed) Safety Relay is OFF (System Stopped), no
continuity Safety Relay is OFF (Open) Normal Operation.
When there is continuity between PIN4 and PIN12 ON
(Closed) Safety Relay is OFF (System Stopped), no
continuity Safety Relay is OFF (Open) Normal Operation.
When AUTO Mode is being used this Pin5 & PIN13
is ON (Closed).
If the main power supply to the unit is connected
this output is ON (Closed).
External Power Source input for Emergency Stop
Signal or Emergency Stop Signal. Normal Operation
ON (Closed), Emergency OFF (Open).
When there is continuity, OFF, between PIN2 and
PIN10 the selected motor is connected, if no
continuity the motor is disconnected or the motor
cord is broken.
When there is continuity between PIN3 and PIN11 ON
(Closed) Safety Relay is OFF (System Stopped), no
continuity Safety Relay is OFF (Open) Normal Operation.
When there is continuity between PIN4 and PIN12 ON
(Closed) Safety Relay is OFF (System Stopped), no
continuity Safety Relay is OFF (Open) Normal Operation.
When AUTO Mode is being used this Pin is ON
(Closed).
If the main power supply to the unit is connected
this output is ON (Closed).
–—
–—
–—
2. Connector B
If you use NE211-OP1 connected to a machine tool, connect the signal line of SAFE-1A,
SAFE-1B, SAFE-2A, SAFE-2B to the safety circuit at the side of the machinery in order to build
a safety shutdown system with higher reliability.
(1) Input/Output Connector B
CAUTION
When using 0V DO NOT connect to PIN10 or 13 (Internal Ground) of Input/Output
Connector A.
CAUTION
NE211 does not use PIN No. 1, 3, 4, 9, 11, 12.
NE211-OP1 use PIN No. 1, 3, 4, 9, 11, 12.
1
2
E3000CK0446Ee08010808.1.86:34PMページ27

29 30
Fig. 36
Connector A
14
15
16
17
18
19
20
21
22
23
24
25
1
2
3
4
5
6
7
8
9
10
11
12
13
4. Input/Output Connector A, B Pin Configuration
Connector B
9
10
11
12
13
14
15
1
2
3
4
5
6
7
8
1. Warning Function
Always check the control unit, motor, spindle and the condition of the cooling air prior to
use. This will help prevent system errors that will result in undesired operating conditions.
(1) The Warning LED [
20
]will flash.
(2) The Warning Code (listed in Table 2) will be displayed on the Digital Speed Indicator [
11
].
(3) A Warning Signal is output to the Warning Signal (PIN No. 20 : WARNING) of
Input/Output Connector A.
2. Detection of unsafe operating conditions
Always check the control unit, motor, spindle and the condition of the cooling air prior to
use. This will help prevent system errors that will result in undesired operating conditions.
When an Error Occurs the following events happen :
(1) Motor stops
(2) The Error LED [
19
]will flash.
(3) Error Code (listed in Table 3) will be displayed on the Digital Speed Indicator [
11
].
(4) An Error signal is output to the Error Signal (PIN No. 8 : ERR) of Input/Output Connector.
PROTECT FUNCTION
Warning Code Warning Function Trouble
A0
A1
A2
A3
Motor Cord
Low Air Pressure
Control Unit Overheat
Over Load
Internal Temperature of the Control Unit too High
Motor Torque load exceeding safe limits
A4
A5
Emergency Stop
Over Air Pressure
Emergency Stop system activated
Over Air Supply
Motor Cord or Connector is disconnected or misaligned
Low Air Pressure
Table 2
CAUTION
When the Warning LED [
20
]flashes, please check the Warning code.
Safety Relay Signal
PIN No. 3-11, 4-12
• The Safety Relay will be ON or OFF depending on the state of the Emergency Stop Signal
PIN1-9.
• When there is continuity between PIN3 (SAFE-1A) and PIN11 (SAFE-1B) or between PIN4
(SAFE-2A) and PIN12 (SAFE-2B) the motor is off. If there is no continuity between these
pairs of pins then the system is operating normally.
• If the Emergency Stop Signal is OFF (Open) the Safety Relay will be OFF (Open) and the
motor power will be interrupted and the motor will stop.
• If the ‘a’ contacts of the Safety Relay are welded together by an over load or short circuit
the ‘b’ contacts’ separation are maintained with more than 0.5mm spacing by the relay’s
recoil mechanism.
• The voltage/current specifications of PIN3-11 & PIN4-12.
Applied Voltage (V max) 30VDC
Working Current (Ip) 2A
Fig. 35
Input/Output Connector A
Plug Part Number : XM2A-2501 OMRON (or other similar high-quality product)
Cover Part Number : XM2S-2511 OMRON (or other similar high-quality product)
Input/Output Connector B
Plug Part Number : XM2A-1501 OMRON (or other similar high-quality product)
Cover Part Number : XM2S-1511 OMRON (or other similar high-quality product)
• The Plug and Cover are not provided with the system. Please purchase the specified plug
and cover from local suppliers.
• Use only shielded cables to minimize RF interference and noise. Connect the shield to
the plug cover.
• Different makers use different names for the cover.
CAUTION
To minimize RF interference and noise please keep the length of the cables as short as
practical and route separate from power cables.
3 (SAFE-1A)
4 (SAFE-2A)
12 (SAFE-2B)
11 (SAFE-1B)
The side of unit
Safety Relay
Contact
Motor
output part
Motor
output line
3. Input/Output Signal Connector Specifications
17
3
1
2
E3000CK0446Ee08010808.1.86:34PMページ29

31 32
4. Torque Overload
When the Load Monitor LED (Load) [
12
] lights 4 or more LEDs (3 green LEDs and 1 or more
yellow LEDs) an overload condition exists. During overload operation the follow occurs.
(1) Warning LED (Warning) [
20
] flashes
(2) Warning Code A3 is displayed on the Digital Speed Indicator [
11
]
(3) Warning Signal is output to the Warning Signal (Warning) of Input/Output Connector
Overload operation is considered short term operation mode. The allowable operation time
depends on the number of lighted LEDs on the Load Monitor LED (Load).
The allowable time is detailed below.
(1) Load Monitor LED 4 LEDs : 30 Seconds
(2) Load Monitor LED 5 LEDs : 10 Seconds
(3) Load Monitor LED 6 LEDs : 5 Seconds
When the allowable time is exceeded the motor will stop and the following occurs.
(1) Error LED (Error) [
19
] flashes
(2) Error Code E8 is displayed in the Digital Speed Indicator [
11
].
(3) Error Signal is output to the error signal PIN8 (ERR) of Input/Output Connector A.
CAUTION
If you operate the system in short term operation for long periods of time the
control unit will overheat and damage to the motor and spindle is possible.
NAKANISHI recommends only continuous duty operation (Load LED has 3 LEDs lit :
Torque Load Monitor (Load) voltage is less than 5V.
The E3000 is a high-precision, high-speed motor-spindle, the following procedure must be
followed to ensure proper operation and longevity.
During transportation, storage or installation the grease inside the bearings will settle. If the
motor-spindle is suddenly run at high-speed excessive heat will cause bearing damage. After
installation, repair, initial operation, or long periods of non operation please follow the break-
in procedure detailed in Table 4.
12345
60,000
10 Min
min-1
Running Time
Items to Check
15,000
15 Min
No Abnormal
Noises
30,000
10 Min
Spindle Housing
no hotter than
20°C. If hotter
than 20°C stop
for at least 20
minutes, check
installation and
restart Break-In
procedure.
40,000 50,000
10 Min 10 Min
Spindle Housing
no hotter than
20°C. If hotter
than 20°C stop
for at least 20
minutes, check
installation and
restart Break-In
procedure.
Spindle Housing
no hotter than
20°C. If hotter
than 20°C stop
for at least 20
minutes, check
installation and
restart Break-In
procedure.
Spindle Housing
less than 20°C.
BREAK-IN PROCEDURE
Table 4
Steps
3. Resetting System after Error Codes
There are 2 methods of releasing error codes.
(1) Push Error Reset Switch [
18
] RESET on the front panel.
(2) Switch the signal on PIN4 (RESET) of Input/Output Connector A OFF (Open) ON
(Closed) OFF (Open).
When releasing Error using the Motor Start/Stop (Pin No. 14 : START) is ON (Closed),
OFF (Open) Motor Start/Stop before resuming operation.
Error Code Problem Area Trouble
E1
E2
E3
E4
E5
E6
E8
EA
EH
EE
EC
E7
Excess Current
Over voltage
Motor Sensor
Control Unit Overheat
Brake Circuit Trouble
Rotor Lock
Low Air Pressure
Torque Overload
External Control Signal
Error
Over Speed
Emergency Stop Error
Internal Memory Error
Trouble with the sensor signal in the motor
Internal Temperature of the Control Unit too High
Trouble with the motor brake circuit
Motor stalled for more than 3 seconds
Inadequate air supplied for more than 4 seconds during rotation
or inadequate air supply when motor start commanded.
Torque limits exceeded for too long a period of time.
External control sequencing problem
E9 Communication
Interception Intercept communication with Selector Unit (NE212)
(Only if using NE211 connect to NE212)
Rotating speed is beyond the set speed for too long
Safety Relay has been activated and the Emergency Stop
System has stopped the motor
Trouble with memory (EEPROM)
Motor Current beyond safe limits
Motor Voltage beyond safe limits
EL Incompatible Motor Incompatible motor is connected to the system.
Table 3
18
CAUTION
•When using the Input/Output Connector and external monitoring please check
and resolve the source of the trouble anytime a Warning Code is displayed.
•
The following Error Codes cannot be released : E4 (Control Unit Overheat), E5
(Brake Circuit Trouble), E9 (Trouble with Power Source), EC (Internal Memory Error).
Once the source of the error is corrected, turn the system off and the Error Code
will be released when the system is turned on.
E3000CK0446Ee08010808.1.86:34PMページ31

33 34
TROUBLE SHOOTING
(1) The proper surface speed for vitrified grindstones is 600-1800m/min.
(2) Do not exceed 13mm overhang for mounted grindstones. In case overhang must exceed
13mm reduce the motor speed in accordance with Fig. 37 and Table 5.
(3) Do not use tools with bent or broken shanks, cracks or excessive runout.
(4) Dress the grindstone prior to use.
(5) For grinding the maximum depth of cut should not exceed 0.01mm radially or axially.
Reciprocate the tool several times after each in feed step.
(6) Always operate tools within the tool manufacturer’s recommended speed limits. Use of a
tool outside of the manufacturer’s recommended speed limits could cause damage to the
spindle and injury to the operator.
(7) Keep the tool shank and collet clean. If contaminants are left in the collet they can cause
excessive runout and damage the tool and spindle.
(8) Do not drop or hit spindle.
CUTTING TOOL CAUTIONS
3.14 x Diameter (mm) x rotation speed min-1
1,000
Surface Speed (m/min)=
CAUTION
Do not exceed a surface speed of 2,000m/min for grinding.
13
Overhang (mm) Speed (min-1)
20
25 N x 0.3
50 N x 0.1
Table 5. Overhang and Speed
N=Max. operating speed at 13mm overhang.
Fig. 37
N x 0.5
Trouble Cause
Power is not supplied.
Motor Cord or Connector Disconnected.
Controller Switch is set to Manual but
trying to start with an external command
signal through Input/Output Connector A.
Controller Switch is set to Auto but trying
to start with the Start Switch on the
Control Panel.
Motor Cord is connected to the wrong Motor Connector
on NE212. Emergency Stop Signal on Input/Output
Connector B is OFF (Open) NE211-OP1 Only.
Error Code Indicated.
Low Air Pressure
Motor Fixed Speed is set in the or
parameters.
Set Gear Mode except “1.0”.
Foreign Particles stuck in the collet chuck
or spindle.
Collet Nut is not properly positioned.
Ball Bearings Worn.
Foreign Particles in the ball bearings.
Ball Bearings Worn.
Tool out of Balance.
Motor Does Not Run
Motor Speed is not
displayed correctly
High Run-Out
Abnormal Vibration or
Noise during Operation
•Check the Main Power Inlet connection
on the front of the unit.
•Insert the Power Plug correctly.
•Check if the fuse is short.
Connect the Motor Cord to the connector
or check the Motor Cable.
Start with the Start Switch on the Control
Panel, or set the Controller Switch to Auto.
Start with an external command signal or
set the Controller Switch to Manual.
Check the Motor Cord connection and correct if necessary.
Check the source of the Emergency Stop Signal and correct
the problem. After correcting the problem, restart the system.
Check and correct the source of the Error
Code.
Adjust air pressure to between
0.25MPa-0.3MPa.
Check the and parameter
settings and adjust as needed.
Check the gear ratio.
Clean the inside of the collet chuck and
spindle.
Position the collet nut properly.
Send to NAKANISHI for Repair.
Send to NAKANISHI for Repair.
Change the tool.
Inspect/Corrective Action
19 20
E3000CK0446Ee08010808.1.86:34PMページ33

35 36
(1) The following operating parameters can be preset depending on the application
requirements. The operating parameter presets are retained in non-volatile memory and
will be maintained even if power is disconnected.
SETTING OF OPERATING PARAMETERS
Setting the Error Output Mode
When an operating error occurs, an error signal will be output to Input/Output Connector A.
This output can be set to normally ON (Closed) or normally OFF (Open).
Setting AUTO Mode Motor Speed Control
Control Mode is set to AUTO
• Motor Speed can be controlled by the Motor Speed Adjustment Switch on the Control
Panel.
• When using Selector Unit NE212, Motor Speed can be adjusted on the NE212 control
panel.
Setting Fixed Motor Speed for Motor #1 and #2 and #3 and #4
• Single Motor Speed is desired.
• Machine Operator can not change motor speed.
Setting the Maximum Motor Speed for Motor #1 and #2 and #3 and #4
• Set maximum motor speed to the maximum allowable speed for the cutting tools being
used.
• Set the maximum motor speed to the maximum recommended speed for the spindle
being used.
Selection of external Input/Output Signal Speed
During Auto mode operation, you can select variable voltage DC or pulse signal to control
motor Speed.
Selection of the type of external signal for motor start method
Allows selection of Start signal and Direction Signal or REV. Start and FWD. Start signals.
Air Input monitoring override
The system can be configured to operate without cooling air, maximum speed is
30,000 min-1.
Check operating parameter settings
CAUTION
Once a parameters default setting has been changed the setting will be maintained
even if power is disconnected. Please set the Error Output Mode, AUTO Mode
Motor Speed Control, Fixed Motor Speed, and Maximum Motor Speed.
22
SYSTEM CHART
21
1
2
3
4
5
6
7
Brushless Motor Spindle
EM20-S6000
Motor Cord
EMCD-3000
Motor Cord
EMCD-3000
Motor Cord
EMCD-3000
Spindle
NR-3060S
Spindle
NR-453E •NR-403E
Automatic Tool Replacement Spindle
NR40-5100 ATC
90º Angle Spindle
RAX-271E (1/1.5)
RAX-71E (1/6)
90º Angle Spindle
RA-151E (1/2.67)
90º Angle Spindle
RA-271E (1/1.5)
Brushless Motor Spindle
EM25-S6000
Brushless Motor Spindle
EM30-S6000
Selector Unit
NE212
*
Single motor can only be
operated at the same time.
No simultaneous operation.
*
Cooled-air is supplied.
Control Unit
NE211
100-240V
Compressor
Air Line Kit
AL-0201
90º Angle Spindle
RAS-151E
(1 / 2.67)
Speed Reducer
ARG-021E (1/16)
Speed Reducer
ARG-011E (1/4)
*May be connected between
the motor and the spindle as
the need of torque.
*(1/OO ) indicates reduction
ratio.
Brushless Motor EM-3060
Motor Cord EMCD-3000
High-Speed Milling Spindle
HES510
8
E3000CK0446Ee08010808.1.86:35PMページ35

Setting AUTO Mode Motor Speed Control
•Allows the setting of the manner in which motor speed can be controlled when the
system is being used in AUTO mode (External Command Signal Control).
•This parameter selects between speed control with the Motor Speed Adjustment Switch
or by External Command Signal through Input/Output Connector A.
Procedure
1. Push the Start Switch.
2. is displayed. This indicates that speed control is by External Command Signal
Control and the Motor Speed Adjustment Switch are Disabled.
3. Push the Start Switch.
4. is displayed. This indicates that speed control is by the Motor Speed Adjustment
Switch and the External Command Signal Control for speed is disabled.
5. You can cycle through the choices by pushing the Start Switch.
6. Push the Reset Switch to send the settings to memory will be displayed
depending on the parameter being set.
7. If you desire to set other parameters push the Motor Speed Adjustment Switch to
select the parameter to be set.
8. If you are finished setting parameters, turn the Power Switch off.
Setting Fixed Motor Speed
•Allows the motor speed to be fixed.
•Fixes the motor speed in both MANUAL and AUTO modes.
Procedure
1. Push the Start Switch.
2. is displayed. This indicates that Fixed Motor Speed cannot be set.
3. Push the Start Switch.
4. is displayed. This indicates that Fixed Motor Speed can be set.
5. The Digital Speed Indicator will oscillate between and the selected motor speed.
The motor speed can be set by pushing the Motor Speed Adjustment Switch. The
speed control range is 1,000-60,000 min-1.
6. Push the Reset Switch to send the settings to memory will be displayed
depending on the parameter being set.
7. If you desire to set other parameters push the Motor Speed Adjustment Switch to
select the parameter to be set.
8. If you are finished setting parameters, turn the Power Switch off.
37 38
2
3
(2) Entering Parameter Setting Mode
(3) Setting Procedure
While pushing and holding the Error Reset Switch [
18
]turn the Power Switch [9]On. Hold the
Reset Switch down for 3 seconds, the buzzer will ‘beep’ 3 times, release the Reset button
and Parameter Setting Mode will start. The Start LED flashes to indicate Parameter Setting
Mode is active.
• After entering Parameter Setting Mode the parameters to be set can be selected by
pushing the Motor Speed Adjustment Switch.
~
Error Output Mode
AUTO Mode Motor Speed Control
Fixed Motor Speed
Maximum Motor Speed
External Speed Control Mode
External Motor Start Signal Control Mode
Air Input monitoring override
~Confirm settings of parameters ~
Setting Error Output Mode
•Allows setting of the output signal on PIN No. 8 : ERR of Input/Output Connector A.
•When an error occurs the output can be set to ON (Closed) or OFF (Open).
Procedure
1. Push the Start Switch.
2. is displayed. This indicates that when an error occurs the output will be
OFF (Open).
3. Push the Start Switch.
4. is displayed. This indicates that when an error occurs the output will be
ON (Closed).
5. You can cycle through the choices by pushing the Start Switch.
6. Push the Reset Switch to send the settings to memory will be displayed
depending on the parameter being set.
7. If you desire to set other parameters push the Motor Speed Adjustment Switch to
select the parameter to be set.
8. If you are finished setting parameters, turn the Power Switch off.
If the Error Output Mode has been changed from the default setting, that setting will be
displayed the next you enter Parameter Setting Mode.
1
E3000CK0446Ee08010808.1.86:35PMページ37
Table of contents
Other Nakanishi Controllers manuals
Popular Controllers manuals by other brands
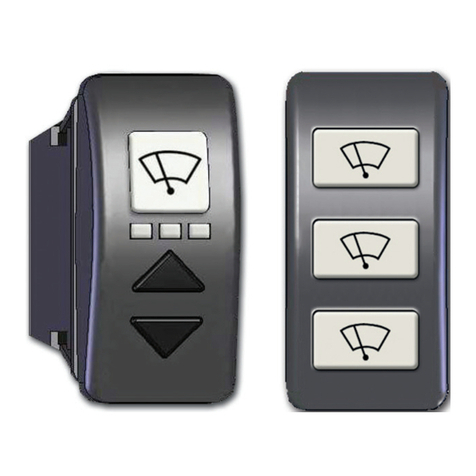
Exalto
Exalto 214303 manual

ZPA Pečky
ZPA Pečky MODACT MOA OC Instructions for assembly operation
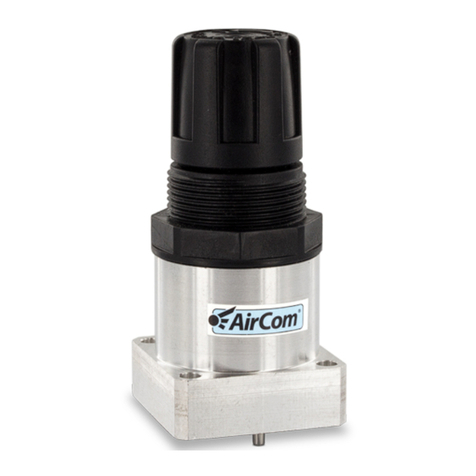
AirCom
AirCom R342 operating manual

IFM Electronic
IFM Electronic Ecomat 100 CR0302 Mounting and installation instructions
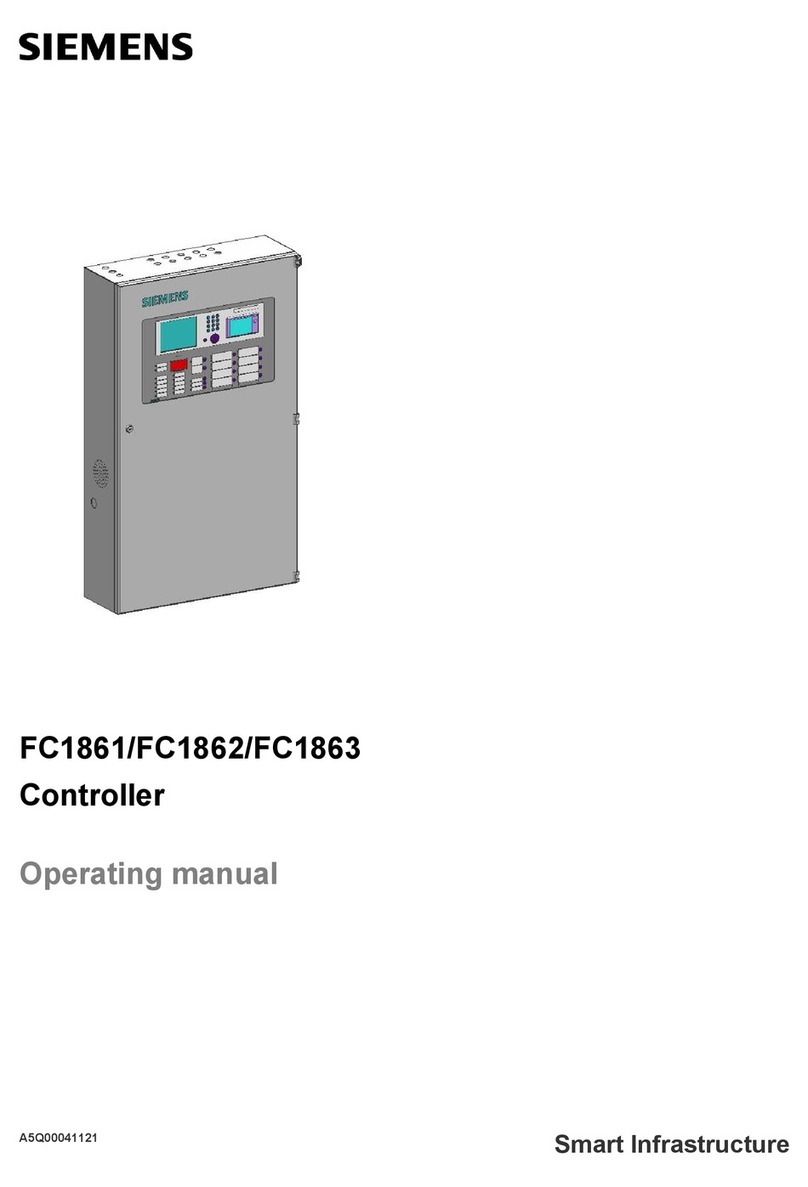
Siemens
Siemens FC18 Series operating manual
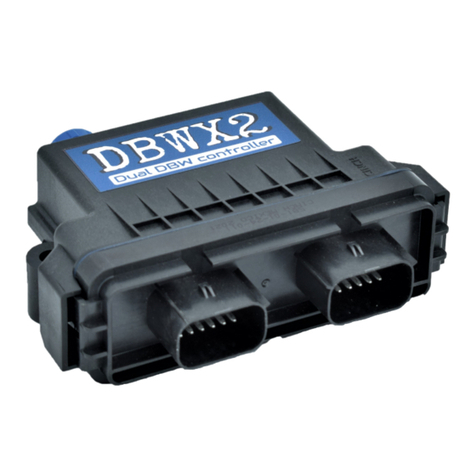
MegaSquirt
MegaSquirt DBWX2 Abridged user manual
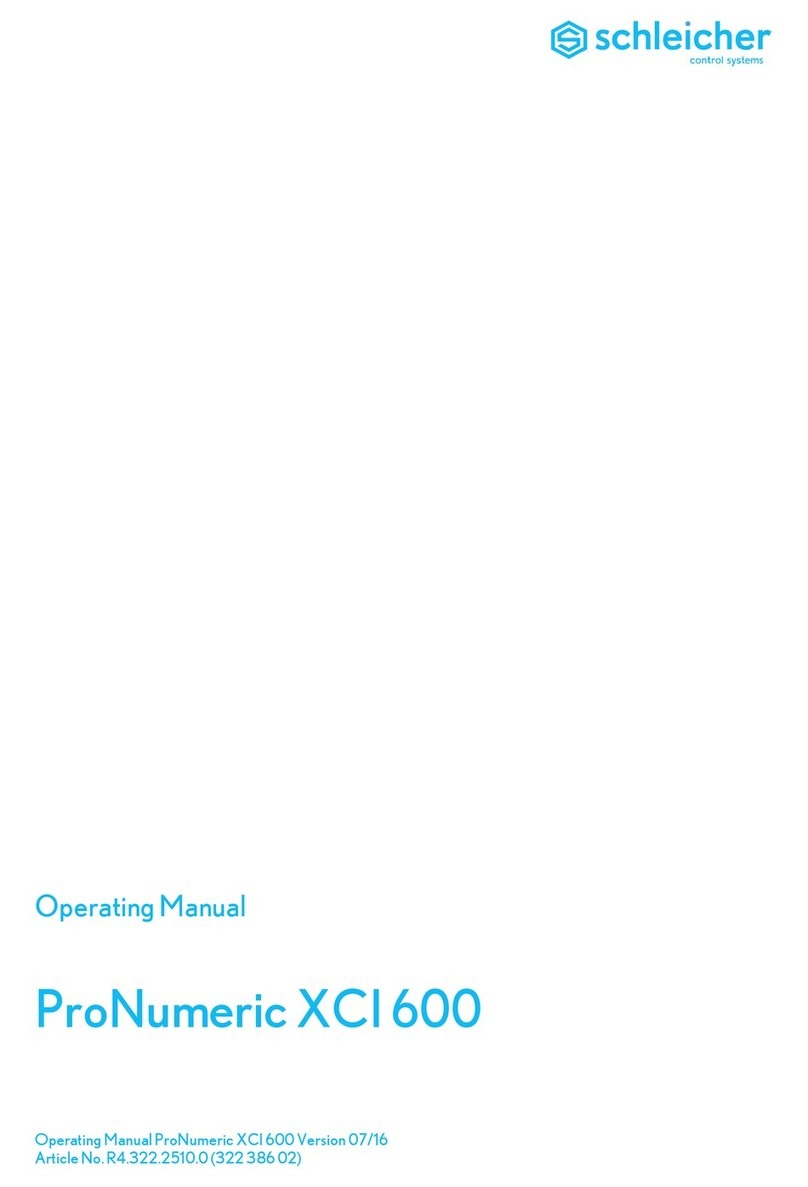
Schleicher
Schleicher ProNumeric XCI 600 operating manual
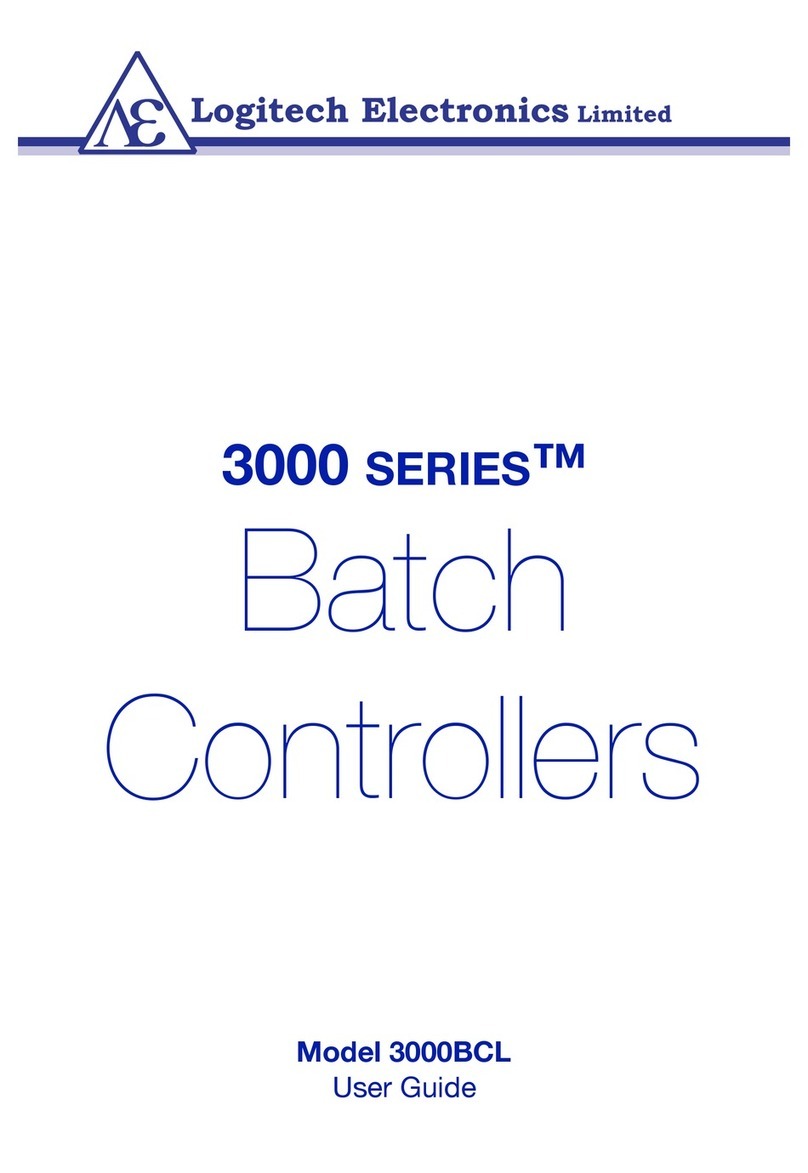
Logitech Electronics
Logitech Electronics 3000 Series user guide
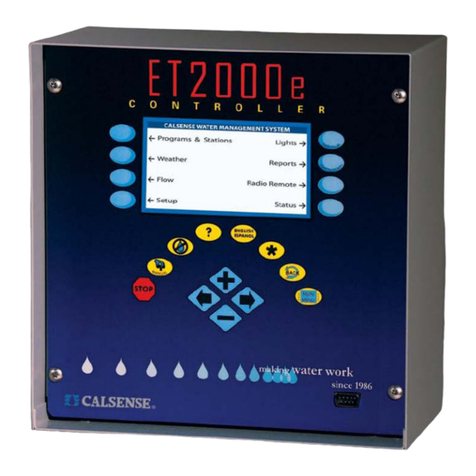
Calsense
Calsense ET2000e Setup guide
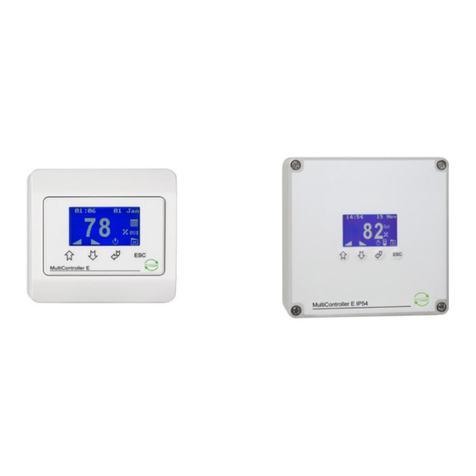
LS Control
LS Control MultiController E manual
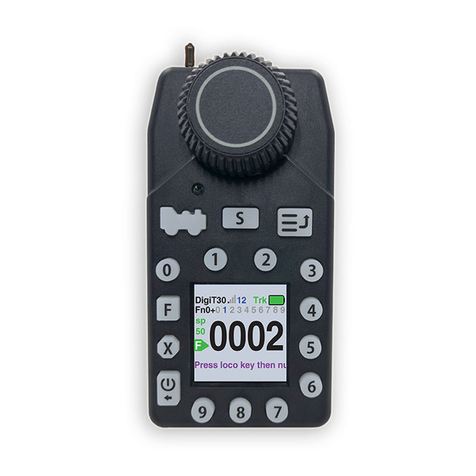
Digitrax
Digitrax UT6 Series manual
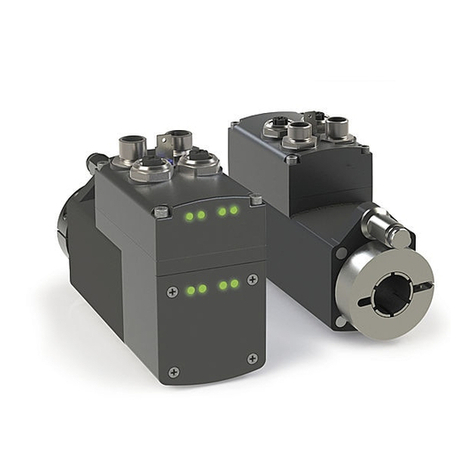
Siko
Siko AG26 Translation of the original installation instructions