Newall E Series User manual

E-Series Digital Readout System
NEWALL MEASUREMENT SYSTEMS LTD
CONTENTS
2 INTRODUCTION
2 TECHNICAL SPECIFICATIONS
3 INSTALLATION
3 Mounting
5 Power Supply
6 Encoder Connection
6 Switching On
7 USER INSTRUCTIONS
7 Options
7 Using the Keypad
9 SET-UP
9 Set-Up Introduction
10 Set-Up Defaults
11 Set-Up Menu
17 STANDARD FUNCTIONS
17 Absolute / Incremental
19 Centre Find
19 Digifind
21 Sub Datums (SDM)
27 Inch / Millimetres
27 Datahold (Display Off)
27 Zero Approach
27 MILL FUNCTIONS
27 PCD / Bolt Hole Circle
29 Arc Contouring
30 Line Hole Function
31 Polar Co-ordinates
33 LATHE FUNCTIONS
33 Tool Offsets
35 Taper Function
36 Summing
36 Vectoring
38 AUXILIARY OUTPUT OPTION
38 Position Pulse Output
41 Remote Zero & Enter Inputs
42 TROUBLESHOOTING
42 CLEANING
N

Notes
Newall Measurement Systems
1
ONTENTS

Introduction
Newall Measurement Systems 2
1.0 INTRODUCTION
The E-Series Digital Readout conforms to the relevant European standards for electromagnetic compatibility and low
voltage directive as detailed below.
BS EN 50081-2: Electromagnetic compatibility.
Generic Emission Standard - Industrial Environment
BS EN 50082-2: Electromagnetic compatibility.
Generic Immunity Standard - Industrial Environment.
BS EN 61010-1: Safety requirements for electrical equipment for
measurement, control and laboratory use.
Construction: Two part system - display/keyboard separate from DSU/Inputs
Dimension Display/Keyboard DSU
Height: 170mm (6.7in) 130mm (5.1in)
Width: 295mm (11.6in) 185mm (7.3in)
Depth: 30mm (1.2in) 60mm (2.4in)
Weight: 2.1kg (4.6lbs) 1.7kg (3.7lbs)
Operating Voltage: 115 or 230V (switch selection)
Supply Voltage Fluctuation: Not to exceed +/-15% of the operating voltage
Supply Frequency: 50 to 60 Hz
Maximum Power Consumption: 26VA
Operating Temperature: 0 to 45°C (32°F to 113°F)
Storage Temperature: -20 to 60°C (-4°F to 140°F)
Inputs: Dependant on model, two or three Spherosyn/Microsyn encoders
Resolution:
Spherosyn/Microsyn 10 5µm (0.0002in) / 10µm (0.0005in) / 20µm (0.001in) / 50µm (0.002in)
Microsyn 5 1µm (0.00005in) / 2µm(0.0001in) / 5µm (0.0002in) / 10µm (0.0005in)
Environmental Conditions:Indoor Use, IP20 (IEC 529)
Relative humidity - maximum 80% for temperatures up to 31°C (87.8°F),
decreasing linearly to 33% at 45°C (113°F).
Transient overvoltage according to INSTALLATION CATEGORY II of IEC664
POLLUTION DEGREE 2 in accordance with IEC664
NEWALL MEASUREMENT SYSTEMS LIMITED RESERVES THE RIGHT TO CHANGE SPECIFICATION
WITHOUT NOTICE
Certificate No FM36096
1.1 EMC and Low Voltage Compliance
1.2 Technical Specifications

Installation
Newall Measurement Systems
3
2.0 INSTALLATION
Select the location of the E-Series with due regard of safety and ease of operation. Keep it clear of moving parts and
coolant spray. Ensure that the natural ventilation around the Digital Sending Unit (DSU) is not restricted.
To ensure correct operation of the E-Series , it is recommended that the Digital Sending Unit (DSU) is grounded to
the machine from the equipotential terminal. A ground strap is provided in the fitting kit. The strap should be cut to a
suitable length once the DSU had been fixed to the machine. A terminal is provided for crimping to the ground strap.
This operation should be conducted by a suitably qualified engineer. The machine must also be grounded to a good
earth point.
The DP8 can be mounted in two basic ways as shown in Figure 2.1
view)
Figure 2.1 - Mounting Procedures
2.1.1 Display and Digital Sending Unit (DSU) mounted separately (Figure 2.1a)
The keypad/display unit incorporates an M10 tapped hole at the rear of the unit. The M10 hole can be used to mount
the display in any of the standard methods as shown in Figure 2.2. The M10 stud mount is provided as standard. The
swivel mount assembly (Part No. 600-80290), the E-Series mounting arm (Part No 294-40055) and the DSU mounting
assembly (Part No 600-65595) are all optional items as detailed on the price list.
(a) Mounting DSU separately (b) Mounting DSU with display
2.1 Mounting

Installation
Newall Measurement Systems 4
INSTALLATION
The DSU is normally mounted on a vertical face on the rear of the machine. The DSU facilitates the fixing in 2, 3 or 4
point location. For metric applications drill and tap an M6 hole and locate the DSU by inserting one of the M6 bolts
provided. Ensure the DSU is level, mark the next location and drill and tap the second hole. Repeat this process for
the required number of fixing locations. For those customers requiring imperial (Inch) fittings, repeat the above
process substituting 1/4 inch UNC tapped hole and bolts.
Note: The fitting kit includes both the metric and imperial fittings. The metric fittings are zinc
coated whereas the imperial fittings are black
The DSU is connected to the keypad/display via a 3.5 metre 9 pin “D” type cable. The cable can only be connected in
one direction. Once connected, secure the cable at both ends using the slotted locking screws.
Please note, as shown in Figure 2.1, the encoder and mains leads should be positioned underneath the DSU to avoid
any ingress of coolant.
2.1.2 Display and Digital Sending Unit (DSU) mounted together (Figure 2.1b)
An optional bracket (Part No 600-65595) is available to facilitate the mounting of the DSU directly to the display using
four M6 bolts. These bolts are provided with the bracket kit which includes a 300mm 9 pin “D” type cable. This cable
is to be used to connect the DSU to the keypad/display and the 3.5 metre cable is not needed in this configuration
and can only be connected in one direction.
Figure 2.2 - M10, Swivel Mount and Arm .

Installation
Newall Measurement Systems
5
INSTALLATION
BEFORE CONNECTING THE ELECTRICAL SUPPLY TO THE DIGITAL SENDING UNIT (DSU),
CHECK THAT THE VOLTAGE SELECTOR SWITCH IS CORRECTLY SET. Figure 2.3 shows the
position of this switch.
The mains supply is connected through a detachable supply cord. The Digital Readout is supplied with a cord with a
right-angle connector. If another supply cord is used, it must have fitted a IEC320, 10A, EARTHED mains connector
with a cord rated for at least 10A.
The PROTECTIVE EARTH CIRCUIT of the mains supply MUST BE CONNECTED to the protective earth terminal of
the DSU through the supply cord.
The supply cord should be secured with cable ties to ensure that it cannot drop into a hazardous position, ie. the
floor or coolant tray, when disconnected from the DSU.
The supply cord must be routed away from moving parts, swarf, coolant or sources of heat.
If a mains plug is not already fitted to the supply cord or is of the wrong type, then a suitable EARTHED plug should
be used which complies with the relevant specifications for plugs and socket-outlets.
The mains supply fuse is a 20x5mm, type T0.5A, 250V. It is not to be replaced by the operator. If the fuse blows it is a
possible indication of some significant problem with the power source. Check the supply and wiring carefully. If the
fuse is replaced, the DSU must first be disconnected from the supply by the removal of the IEC socket from the inlet.
This connector is the primary disconnect device for the equipment and must be accessible at all times. Do not
position the equipment so that it is difficult to operate the disconnect device.
NOTE: If the equipment is used in a manner not specified by the manufacturer, the protection
provided by the equipment may be impaired.
Figure 2.3 - Connection diagram for the Digital Sending Unit (DSU)
2.2 Power Supply
Equipotential terminal for grounding the DSU to the machine. Refer to section 2.1.
Caution. Refer to section 2.2 before connection to the mains supply.

Installation
Newall Measurement Systems 6
The mains supply switch for the E-Series is mounted on the side of the DSU as shown in Figure 2.3.
When you switch on the E-Series, the unit will automatically go through a brief self diagnostic routine.
During this routine, the name E70 will be shown, then the software version number will be displayed and all segments
of the displays will be lit.
After this routine, the unit will display measurements and is ready for use.
The E-Series can be switched off via the mains switch on the DSU. Alternatively, the keypad/display can be
switched off by pressing the key. Please note that the DSU remains under power when the key
is pressed.
Figure 2.3 shows the connection sockets on the DSU. The E-Series is designed for use with Newall Spherosyn and
Microsyn encoders only. The encoders are connected to the DSU with 9-pin D Type connectors.
Switch off the E-Series before connecting or disconnecting the encoders. To fit the connectors into the appropriate
socket on the back of the E-Series , first align the connector and then push firmly in place.and secure with the locking
bolts. To remove the connector, disengage the locking mechanism and pull the connector clear.
The encoders and the display/keyboard are connected to the DSU at a separated extra low voltage (SELV) level. Any
additional interconnections must also be at SELV level.
CONVENTIONS USED IN THIS MANUAL
The direction of travel of an axis refers to the travel of the tool relative to the workpiece.
Keys on the keypad are signified in bold print, such as for the enter key.
2.3 Encoder Connection
2.4 Switching On
ent
SPHEROSYN & MICROSYN ARE REGISTERED TRADEMARKS OF NEWALL MEASUREMENT SYSTEMS

User Instructions
Newall Measurement Systems
7
Standard Keys Function Purpose
CS
3.0 USER INSTRUCTIONS
The E-Series is available in two models, the E-Series Mill and E-Series Lathe. Each E-Series model is available with an
optional auxiliary port.The auxiliary port is used for (i) a remote zero pendant (part number 600-17690) and (ii) for
positional output data
The keys are used as follows
Models 2 Axes 3 Axes Additional Features
E-Series Mill 3 3 Bolt Hole Circle (PCD) and Bolt Hole Arc mode,
Line Hole (max 999 holes),Arc contouring, Polar co-ordinates, Sub-
Datums
E-Series Lathe 3 3 Tool Offsets,99 ,Taper calculations, Internal summing,Vectoring, Sub-
Datums
On/Off (Display only, not DSU)
Select axis to enter dimension (preset)
Set the current position for the axis to zero
(reset)
Clear entry values in preset mode
Enter key to confirm data entry
Switches between absolute & incremental
readings
Centre find function
Select the Digifind function
Switches between inch and millimetre display
(LED indicates choice of mode)
Numeric keypad for data entry
Selecting the required Sub-Datum number
Setting the selected Sub-Datum to zero
Insert / Delete
Scroll Previous / Scroll Next
XZ Z
abs
inc
ce
12
ent
ref
in
mm
1 2 3 45
6 7 89 0
.
+
_
sdm
sdm
zero
del.
ins.
3.2 Using the keypad
3.1 Options
ON / OFF
[CE] KEY
[ENT] Key
[ABS / INC] Key
[IN / MM] Key
[SDM] Key
[SDM ZERO] Key
[INS] / [DEL] Key
XZ0Z0

User Instructions
Newall Measurement Systems 8
Mill Option Keys Function Purpose
For using the Pitch Circle Diameter (PCD) function
For using the Line Hole function
For using the ARC function
For selecting between Cartesian (x,y,z) and Polar
(Length+Angle) co-ordinates
Lathe Option Keys Function Purpose
For Taper calculations
For using Tool Off-Sets
Setting Tool Off-Sets
Summing function, vectoring function
R
set
1+1
E-Series Mill 2 Axes E-Series Mill 3 Axes
E-Series Lathe 2 Axes E-Series Lathe 3 Axes
[PCD] Key
[LINE] Key
[ARC] Key
[POLAR] Key
[TAPER] Key
[TOOL USE] Key
[TOOL SET] Key
[SUMMING] Key

4.0 SET-UP
The E-Series digital readout display is equipped with a Set-Up Routine.The routine enables the operator to change
factory settings in order to increase efficiency and productivity. If the factory defaults are suitable, select the NORMAL
option at the end of the Routine to restore the factory defaults.
Generally, the entire Set-Up Routine is performed only one time. Changing some parameters in Set-Up may alter
datums, SDMs, tool compensations and Digifind.
DO NOT RUN SET-UP IF YOU ARE NOT PREPARED TO LOSE THIS DATA.
Set-Up is enabled while the unit is running its initial self-test, just after powering on. Press the [ON/OFF] on the
face of the display as the self-test is running.
The Set-Up procedure makes use of a menu system.The main menu consists of a list of options that can be cus-
tomised for your use (See Table 1). You simply press the [<<]]and [ >>]keys to scroll through this list until you reach
the option you wish to change.To change the option when selected, press [ENT]
To exit the Set-Up routine scroll through to the quit option and press [ENT]
If the keypad/display has been switched off by pressing the [ON/OFF] key rather than switching off at the mains, it is
possible to enter the Set-Up routine by pressing the [ABS/INC] key followed by the [ON/OFF]
Set-Up
Newall Measurement Systems
9
4.1 Set-Up Introduction

Set-Up
Newall Measurement Systems 10
Table 1 - Set-Up Defaults
FUNCTION DESCRIPTION DEFAULT SETTING MENU OPTIONS
LANGUAGE Selects the language to display messages ENGLISH English/French/German/Spanish
Italian/Danish/Czech
KEY BEEP Enables the audible beep when keys are pressed on the keypad ON On/Off
I/P TYPE Selects the type of transducer on each axis SPHEROSYN Spherosyn/Microsyn 5/Microsyn 10
RAD/DIA Selects radius or diameter reading for each axis RAD (DIA - X axis lathe) Rad/Dia
RESOLUTION Selects the resolution to be displayed on each axis 5µm 1 / 2 / 5 / 10 / 20 / 50µm
DIRECTION Changes the direction of count for each axis 1 0 / 1
ERR COMP Selects the type of error compensation for each axis OFF OFF / LINEAR COMP / Seg Error
ERR SET Sets the error compensation NO COMPENSATION Sel Axis (for lin or seg error setting)
SDM Enables the subdatum memory function on the keypad ON On/Off
POS OUT Enables the position pulse output function OFF Off/X Axis/Y Axis/Z Axis/
(Only available when the optional auxiliary port is included) All Axes
POS SET Sets the position that triggers a pulse output ALL ZERO Posit-1 / Posit-2 / Posit-3 /
(Only available when the optional auxiliary port is included) Reset / Pulse MS
ZERO APPROACH Enables zero approach function on the keypad OFF On/Off
ZERO SET Enables approach window to be set 0.000 User definable window
(Selectable only if zero approach is “on”)
NORMAL Sets factory settings - Quit Normal/Default
QUIT Exits the Set-Up routine and saves settings to memory -
MILL OPTIONS
ARC Enables the arc contour function on the keypad ON On/Off
PCD Enables the bolt hole circle function on the keypad ON On/Off
LINE Enables line hole function on keypad ON On/Off
POLAR Enables line polar co-ordinate function on the keypad ON On/Off
LATHE OPTION
TOOL Enables tool offset compensation ON On/Off
SUMMING Enables summing of axes on the keypad OFF Off/ X+Zl/ Z+Zl/ Vectored
TAPER Enables Taper function on the keypad. ON On/Off
4.2 Set-Up Defaults

Set-Up
Newall Measurement Systems
11
The I/P (Input) Type function allows the operator to specify the
type of transducer connected to each axis.The E Series reads
Newall's Spherosyn, Microsyn 10 or Microsyn 5 Encoders
SEL AXIS
Options: SPHEroSn
uSn 10
uSn 5
ent
I/P TYPE
ent
Scroll through available options for each axis
using the (AXIS) key, once all axes read the
desired encoder type, select with [ENT]
X
Y
Z
>
IMPORTANT:
The input type selected for each axis must match the trans-
ducer connected to that axis.The E Series will give incorrect
readings if the I/P Type does not match the encoder installed.
(d) I/P Type
The Set-Up procedure can only be entered by pressing the
[ON/OFF] during the power on sequence or by turning the
display off using [ON/OFF] and then pressing [ABS/INC]
before pressing [ON/OFF] again.
When you have entered the Set-Up routine, the letters ‘SET-
UP’ appear in the top axis display.
Press the [ >>] key to move to the next menu option.
SET-UP
abs
inc
>
ENGLISH
Options: ENGLISH FRANCAIS
DEUTSCH ITALIANO
ESPANOL DANSK
CESKY
ent
LANGUAGE
BEEP ON >
Options: BEEP ON
BEEP OFF
ent
KEY BEEP
ent
>
Scroll through the available options using the
arrow keys and select the desired
language mode with [ENT]
Toggle between Beep On and Beep Off using the
arrow keys and select desired mode with [ENT]
>ent
>
(a) Set-Up
(b) Language
(c) Key Beep
4.3 Set-Up Menu
Press the [ >>] key to move to the next menu option.
Press the [ >>] key to move to the next menu option.
Press the [ >>] key to move to the next menu option.

Set-Up
Newall Measurement Systems 12
ET-UP
The Radius/Diameter function allows the operator to
display actual (radius) or twice-actual (diameter) measurements
for each axis.This function is generally used in
turning applications, such as the cross travel on a lathe.
SEL.AXIS
Options: RAD
DIA
RAD/DIA
The Resolution function allows the operator to determine the
resolution for each axis.
SEL.AXIS
Options: 0.001mm (0.00005”)
0.002mm (0.0001”)
0.005mm (0.0002”)
0.010mm (0.0005”)
0.020mm (0.002”)
0.050mm (0.005”)
RESOLUTION
Toggle between Radius and Diameter using the
(AXIS) keys and select desired mode with [ENT]
Scroll through available options for each axis
using the (AXIS) key, once all axes read the
desired resolution, select with [ENT]
ent
ent
X
Y
Z
>
ent
ent
X
Y
Z
>
Direction allows the operator to change the direction of travel
for each axis. Changing the setting will reverse the current direc-
tion.
EXAMPLE:
If the current setting is 0 and the travel is positive from right to
left, changing the setting to 1 will reverse the
direction to measure positive from left to right.
SEL.AXIS
Options: 0
1
ent
DIRECTION
ent
Toggle between 0 and 1 for each axis using the
(AXIS) key. When all axes read the desired direc-
tion, select with [ENT]
X
Y
Z
>
IMPORTANT:
The Resolution available for each axis depends upon the I/P
(Input) Type established for that axis.
(e) Radius / Diameter
(f) Resolution
(g) Direction
Press the [ >>] key to move to the next menu option.
Press the [ >>] key to move to the next menu option.
>
Press the [ >>] key to move to the next menu option.

Set-Up
Newall Measurement Systems
13
Errors can result from a number of sources, including installa-
tion and machine wear.Where the degree of error increases lin-
early along the length of travel of the encoder, Linear Error
Compensation should be applied. However, where the errors
are local to an area of travel, the Segmented Error
Compensation should be applied.
Press the [ >>] key to move to the next menu option.
(h) Error Compensation
ERROR COMP
Options: ERR. OFF
LIN. COMP
SEG. COMP
Scroll through the available options using the
arrow keys and select desired compensation with
[ENT]
ent
X
Y
ZIMPORTANT:
If Error Compensation is applied, it is important that it is
absolutely correct. If it is not correct, errors could be
increased rather than reduced.
ent >
(i) Set Error Compensation - Linear Error Compensation
ERROR SET
SEL.AXIS
Select the axis to be compensated using the axis
keys.
The axis displays will show which axes have been
selected for linear
error compensation.
ent
X
Y
Z
Linear Error Compensation allows the operator to apply a
constant correction factor to all measurements displayed.
Linear error may occur if the axis of the machine is not
running perfectly parallel to the scale (cosine error) or if the
machine is moving in an arc (Abbé errors).The causes may be:
1. Machine wear.
2. Deflection of the machine due to weight acting on an
overhanging section.
3. Misalignment of the scale due to poor installation.
ENT. COMP
The factor may be directly entered.
Load the required factor.
A Linear Error Compensation factor of 1.000000
is equivalent to
no compensation
The further away the scale is mounted from the centre line of
the workpiece, the greater is the potential for linear error.
Linear Error Compensation is expressed as a multiplier,
which is displayed for each axis when ENT. COMP is selected.A
factor of 1.000000 indicates no compensation.
The compensation factor is: True or standard distance moved
Measured distance
A gauge block, standard bar or laser measurement should be
used as the standard against which the displayed movement is
compared.
Press the [ >>] key to select another axis for compensation.
ent
>
ENT. COMP >Alternatively, the factor may be automatically calculated and
entered.When ENT. COMP is displayed press the
[ >>] key to enter the routine
1.00 5

Set-Up
Newall Measurement Systems 14
ZERO A gauge block, standard bar or laser measurement should be
used as the standard against which the displayed movement is
compared
Move the machine to the zero position of the
standard against which the axis is being com-
pared and zero the axis with the zero key.
Xo
Yo
Zo
STANDARD
Move the machine a known distance as deter-
mined by the
standard and enter that value.
20
ent
Select another axis for compensation or press [ENT] to end.
(j) Set Error Compensation - Segmented Error Compensation
ERROR SET
SEL.AXIS
Select the axis to be compensated using the axis
keys.
The axis displays will show which axes have been
selected for segmented error compensation.
The scale travel is broken down into as many as 99 user-defined
segments, each with their own correction factor, measured
against a high-accuracy standard.The following parameters need
to be identified:
ent
X
Y
Zerror
travel
Starting Point - zero
Correction Points
Reference Point
0
1
2
3
4
5
6
SET ZERO
The start point must be at one end of the section
that is to be error-corrected. Points must progress
in sequence, i.e. there must be no reversals in
direction.
Move the machine to the desired start point,
press [ENT]
ent Each Correction Point is measured with respect to the Starting
Point - zero - which is usually set close to one end of the scale.
The Reference Point can be set anywhere along the scale, and
does not need to coincide with either the absolute datum or
any of the correction points. However, it may be convenient to
make the absolute datum and the reference point the same.
Always approach the Starting Point, Correction Points and
Reference Point from the same direction. If you do not, then
the size of the tool or probe will render the measurement inac-
curate.
GO TO 1
The current position relative to the new zero
point is displayed in the relevant axis. Move to
1st (nth) correction point (against a standard).
Press [ENT] to move on
ent WARNING!
Starting this procedure deletes existing segmented error data
for the axis.

Set-Up
Newall Measurement Systems
13
Setting ARC (Arc Contouring) ON enables the [ARC] key on
the keypad. If ARC OFF is set, the [ARC] function on the key-
pad is disabled.
ARC is explained further in the E-Series Mill Section, see
Section 6.0 of this manual.
Press the [ >>] key to move to the next menu option.
ARC ON
Options: ARC ON
ARC OFF
ARC
Toggle between ARC ON and ARC OFF
using the arrow keys and select desired mode
with [ENT]
ent
>ent
>
(l) Arc Contouring (DP8 MILL VERSION ONLY)
SDM (Sub Datum Memory or Stored Dimension Memory) ON
enables the [SDM] function key on the keypad. If SDM OFF is
set, the function key on the keypad is disabled.
SDM is explained further in the Sub Datums Section, See Section
5.4 of this manual.
Press the [ >>] key to move to the next menu option.
SDM ON
Options: ON
OFF
SDM
Toggle between SDM ON and SDM OFF
using the arrow keys and select desired mode
with [ENT]
ent
>ent
>
(k) SDM (Sub Datum Memory / Stored Dimension Memory)
ENT. STANDARD
Enter the standard measurement.
50ent
CORRECTION 1
The correction factor is displayed for this point.
>Do not worry about the direction of the standard
measurement, eg. 50.0 and -50.0 are treated the same.
Segmented compensation need not be over the entire scale
length. It can be applied just to a length of high importance, or it
can be as small as one segment.
GO TO 2 ent
The procedure is repeated for each point.
To complete the segmented error compensation Set-
Up, press [abs/inc] after the last required point has
been entered. abs
inc
GO TO REFERENCE X
Y
Z
Switching On with Segmented Compensation Set
When power is applied, the display for any axis that is set to use
Segmented Compensation shows " rESEt ".
If the machine has not been moved since the power was turned
off, simply press [ce], and the C80 will restore the last positions
recorded.
Alternatively set each axis close to the Reference Point - to
within:
6.3mm (0.25") for a Spherosyn encoder or
2.5mm (0.1") for a Microsyn encoder,
and press the axis key for the axis.The E-Series will
re-establish alignment with the correction parameters

Set-Up
Newall Measurement Systems 14
Setting PCD (Bolt Hole Circle) ON enables the [PCD] function
key on the keypad. If PCD OFF is set, the [PCD] function on the
keypad is disabled.
PCD is explained further in the E-Series Mill Section See Section
6.0 of this manual.
Press the [ >>] key to move to the next menu option.
PCD ON
Options: PCD ON
PCD OFF
PCD
Toggle between PCD ON and PCD OFF
using the arrow keys and select desired mode
with [ENT]
ent
>ent
>
Setting LINE (Line Hole Tool) ON enables the [LINE] key on
the keypad. If LINE OFF is set, the [LINE] function on the key-
pad is disabled.
Line Hole is explained further in the E-Series Mill Section, See
Section 6.0 of this manual.
Press the [ >>] key to move to the next menu option.
LINE ON
Options: LINE ON
LINE OFF
LINE
Toggle between LINE ON and LINE OFF
using the arrow keys and select desired mode
with [ENT]
ent
>ent
>
Setting POLAR (Polar Co-ordinates) ON enables the
[POLAR] key on the keypad. If POLAR OFF is set, the
[POLAR] function on the keypad is disabled.
Polar Co-ordinates are explained further in the E -Series Mill
Section, See Section 6.0 of this manual.
Press the [ >>] key to move to the next menu option.
POLAR ON
Options: POLAR ON
POLAR OFF
POLAR
Toggle between POLAR ON and POLAR
OFF using the arrow keys and select desired
mode with [ENT].
ent
>ent
>
(m) PCD / Bolt Hole Circle (E-Series MILL VERSION ONLY)
(n) Line Hole Tool (E-Series MILL VERSION ONLY)
(o) Polar Co-ordinates (E-Series MILL VERSION ONLY)
Setting TOOL (Tool Offsets) ON enables the TOOL keys on
the keypad. If TOOL OFF is set, the [TOOL] function on the
keypad is disabled.
Tool Offsets are explained further in the E-Series Lathe Section,
See Section 7.0 of this manual.
Press the [ >>] key to move to the next menu option.
TOOL ON
Options: TOOL ON
TOOL OFF
TOOL
Toggle between TOOL ON and TOOL OFF
using the arrow keys and select desired mode
with [ENT].
ent
>ent
>
(p) Tool Offset Compensation (E-Series LATHE VERSION ONLY)

Set-Up
Newall Measurement Systems
15
Zero approach function can be set ON or OFF.
When Zero Approach is ON, the leftmost character of the axis
display flashes when the position is within a defined envelope.
The flash rate increases as zero is approached.
Press the [ >>] key to move to the next menu option.
ZERO ON
Options: ZERO ON
ZERO OFF
ZERO APP
Toggle between ZERO ON and ZERO OFF
using the arrow keys and select desired mode
with [ENT]
ent
>ent
>
Setting a summing option enables the [SUMMING] key
[1+1] on the keypad. If SUMMING OFF is set, the
[SUMMING] function on the keypad is disabled.
The Summing function is explained further in the E-Series Lathe
Section (See Section 7.0) of this manual.
Press the [ >>] key to move to the next menu option.
VECTORED
Options: X + Zi
Z + Zi
VECTORED
OFF
SUMMING
Toggle between the options using the arrow keys
and select desired mode with [ENT].
ent
>ent
>
Setting TAPER ON enables the [TAPER] key on the keypad. If
TAPER OFF is set, the TAPER function on the keypad is disabled.
The Taper function is explained further in the E-Series Lathe
Section (See Section 7.0) of this manual.
Press the [ >>] key to move to the next menu option.
TAPER ON
Options: TAPER ON
TAPER OFF
TAPER
Toggle between TAPER ON and TAPER
OFF using the arrow keys and select desired
mode with [ENT]
ent
>ent
>
(q) Summing (E-Series 3 AXES LATHE VERSION ONLY)
(r) Taper (E-Series LATHE VERSION ONLY)
(s) Zero Approach
If Zero Approach has been selected as ON, then Zero Set
appears as the next “Set-Up” option.
The example refers to a 3 Axis Lathe. For an E-Series Mill the
axis would be [X],[Y],[Z].
The maximum envelope width is 2500mm (99”).
Press the [ >>] key to move to the next menu option.
SEL AXIS
ZERO SET
Enter the Zero Set window by selecting the axis
and entering the required value. Entering “0”
omits the approach warning from that axis
ent
>ent
>
(t) Zero Set
2.000
2.500
0.000
X
Z
Zl
2ent
ent
2
ent
0
. 5

Set-Up
Newall Measurement Systems 16
SET-UP
Normal returns all the Set-Up Options to the original
factory settings (Except language setting).
DEFAULT
Options: DEFAULT
QUIT NORMAL
NORMAL
Toggle between Default and Quit Normal using
the arrow keys and select desired mode with
[ENT]
ent
>ent
>
WARNING!
Selecting DEFAULT will cancel all changes made
during set-up.The E-Series will return to the original
factory settings. Select QUIT NORMAL to leave
the settings unchanged.
Quit exits the Set-Up procedure and returns the E-Series to
operational use.
Returns to normal operating mode.
QUIT
QUIT ent
The Position Set function is only available on DSU’s which have
been fitted with the optional auxiliary output.
The function allows the operator to set parameters for each
axis specified as output during the Position Pulse Output Set-
Up.
Press the [ >>] key to move to the next menu option.
POSIT - 1
Options: POSIT-1 RESET
POSIT-2 PULSE MS
POSIT-3
POS SET
Scroll through available settings using the arrow
key, Load the relevant axes with the required
data.
ent
>ent
>
The Position Pulse Output function is only available on DSU’s
which have been fitted with the optional auxiliary output.
The function provides the operator with a way to control
external devices such as relays or PLCs using the
E-Series.
Setting Position Pulse Output to X AXIS,Y AXIS, Z AXIS or ALL
AXES activates the feature for the selected axis.
NOTE: For the Lathe version,Y AXIS refers to the Z
AXIS and the Z AXIS refers to the Zl AXIS.
Press the [ >>] key to move to the next menu option.
ALL AXES
Options: OFF
X AXIS
Y AXIS
Z AXIS
ALL AXES
POS OUT
Scroll through available options using the arrow
keys and select the desired axis with [ENT].
ent
ent
>
(u) Position Pulse Output (Auxiliary Option only)
(v) Position Set (Auxiliary Option only)
(w) Reset to Original Factory Settings
(x) Quit Set-Up
IMPORTANT!
This is only available with the optional auxiliary version and is
detailed in Section 8.0
IMPORTANT!
This is only available with the optional auxiliary version and is
detailed in Section 8.0

Standard Functions
Newall Measurement Systems
17
STANDARD FUNCTIONS
5.0 STANDARD FUNCTIONS
5.1.1 Using Incremental
When the E-Series is set to incremental mode, it can be
used to display each new position relative to the last position.
This is also known as point-to-point use.
On setting to incremental you can reset each axis by
pressing [Xo] [Yo] or [Zo].
As an alternative to resetting the axes, you can enter the coordinates relative to the current incremental position. If
done in a negative sense, the operator can move to “0.000” which may save a great deal of machining time.
Each time you switch to incremental mode, the E-Series will display the position relative to the last reset
position while in the incremental mode.
5.1.2 Using Absolute
When the E-Series is set to absolute mode it will display the
position relative to an established datum point.
5.1.3 Establishing the Datum
When you reset the display in absolute mode, you are setting the current position of your machine as your datum
point. All absolute positions will be measured relative to this datum.
To set the datum, position the machine at the point you intend to establish the datum and then reset any or all axes,
while in the absolute mode.
The diagram below is used in the following example to show Absolute and Incremental modes.
A
B
C
50
100
200
30
30
150
300
30 70 40 50
30
100
140
190
5.1 Absolute/Incremental abs
inc
50
(0,0)
Y
X
Table of contents
Other Newall Measuring Instrument manuals
Popular Measuring Instrument manuals by other brands
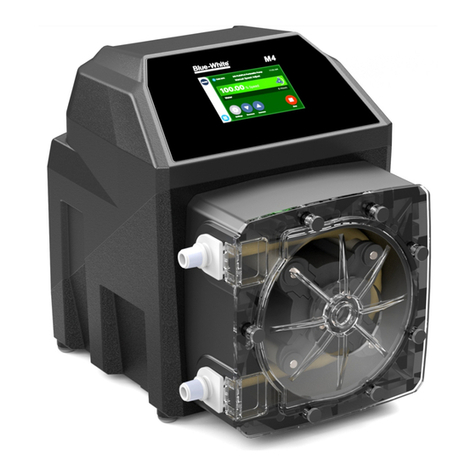
Blue-White
Blue-White FLEXFLO M4 Series operating manual
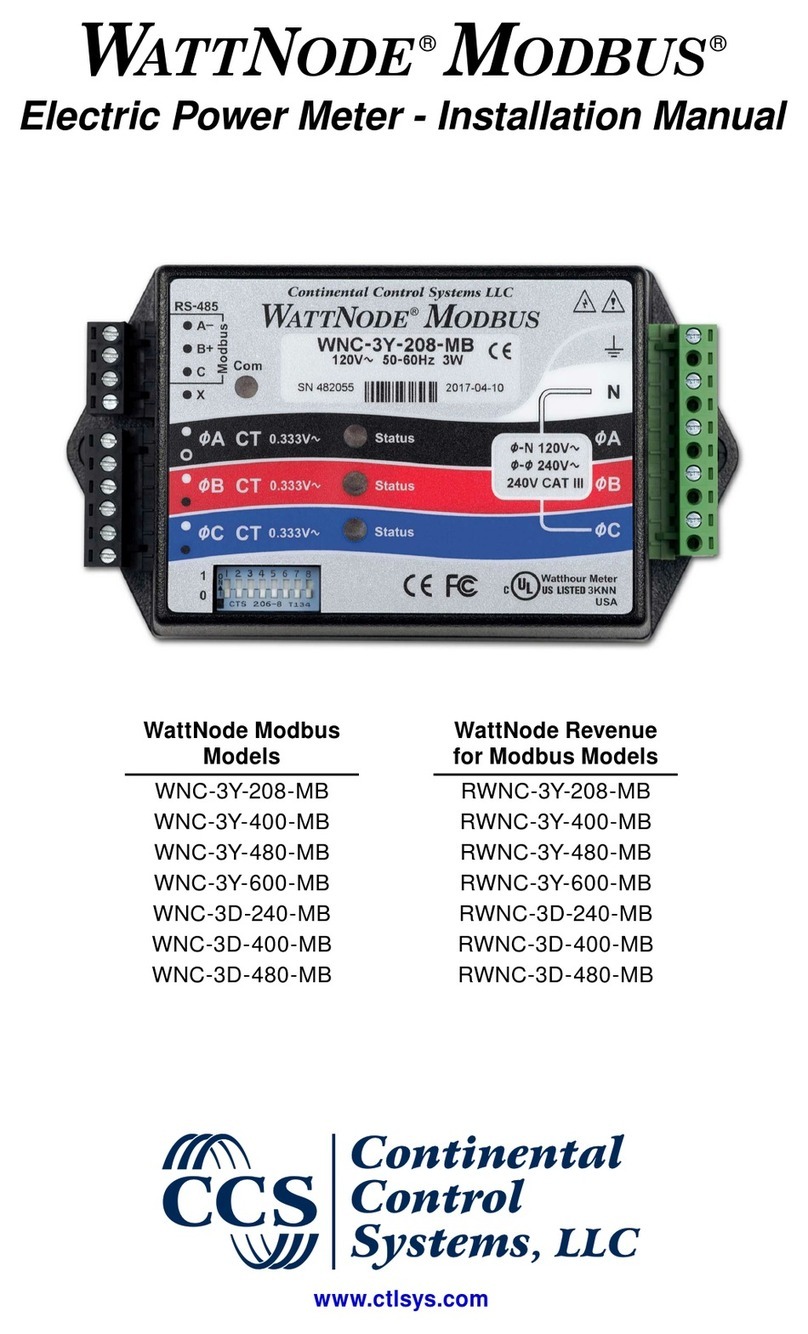
CONTINENTAL CONTROL SYSTEMS
CONTINENTAL CONTROL SYSTEMS WattNode WNC-3Y-208-MB installation manual

Jasco
Jasco V-530 Hardware/Function Manual
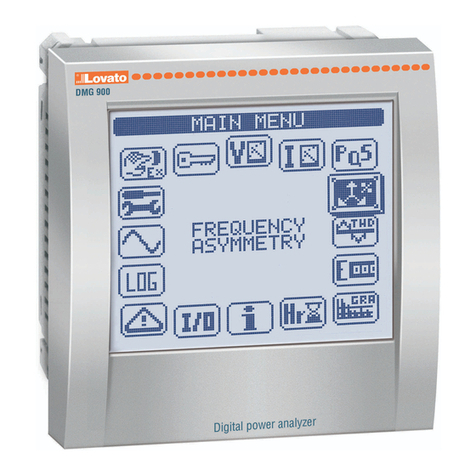
LOVATO ELECTRIC
LOVATO ELECTRIC DMG900T installation manual
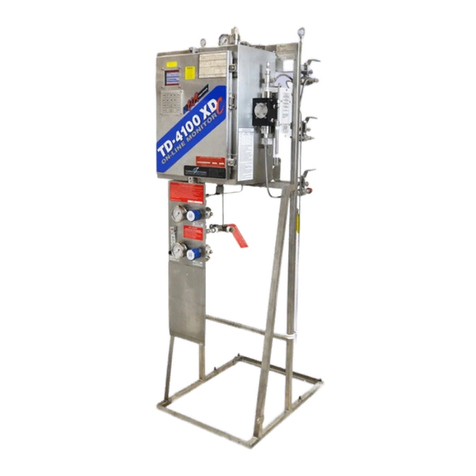
Turner Designs
Turner Designs TD-4100XD E09 Addendum
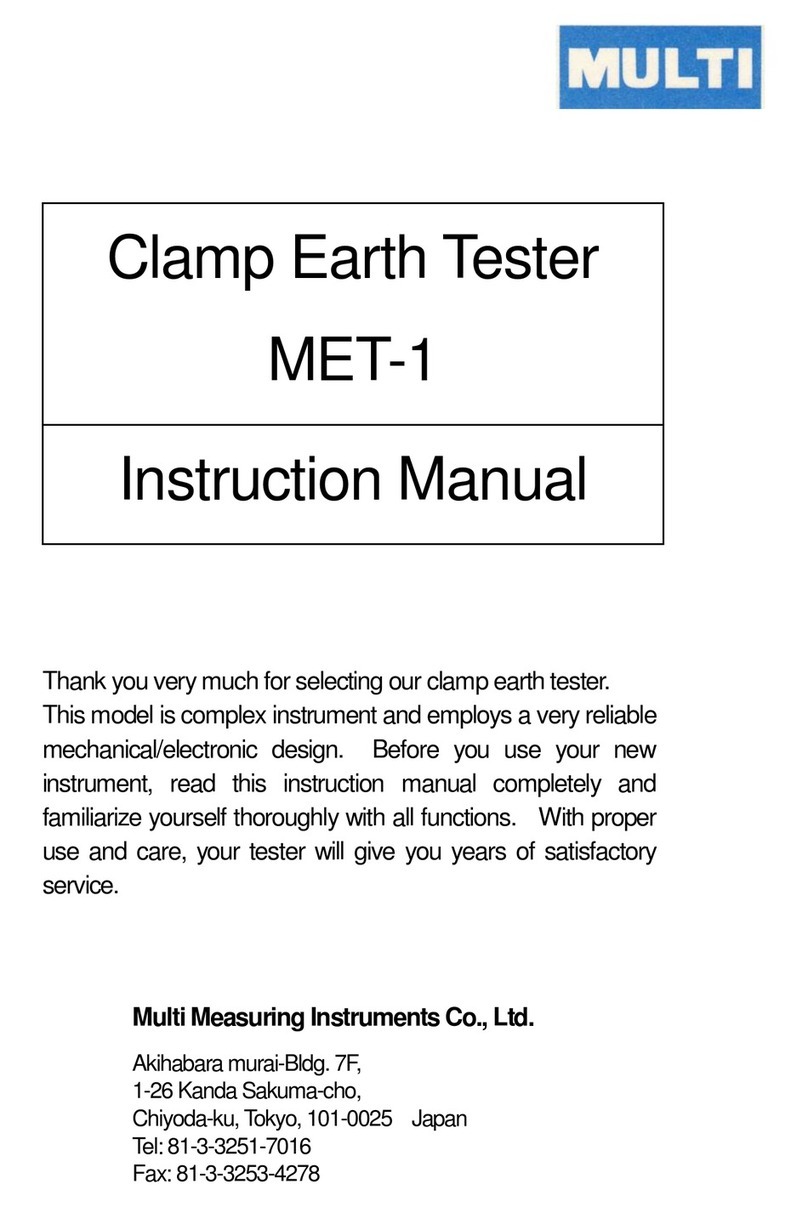
MULTI MEASURING INSTRUMENTS
MULTI MEASURING INSTRUMENTS MET-1 instruction manual