Omicron CMC 156 User manual

27
CMC 156
Reference Manual

Test Set CMC 156
2
Article Number VESD1002 - Version CMC156.AE.9
© OMICRON electronics. All rights reserved.
This manual is a publication of OMICRON electronics GmbH.
All rights including translation reserved. Reproduction of any kind, e.g., photocopying, microfilming,
optical character recognition and/or storage in electronic data processing systems, requires the explicit
consent of OMICRON electronics. Reprinting, wholly or in part, is not permitted.
The product information, specifications, and technical data embodied in this manual represent the
technical status at the time of writing and are subject to change without prior notice.
We have done our best to ensure that the information given in this manual is useful, accurate and
entirely reliable. However, OMICRON electronics does not assume responsibility for any inaccuracies
which may be present.
The user is responsible for every application that makes use of an OMICRON product.
OMICRON electronics translates this manual from the source language English into a number of other
languages. Any translation of this manual is done for local requirements, and in the event of a dispute
between the English and a non-English version, the English version of this manual shall govern.

Safety Instructions
3
Safety Instructions
ATTENTION: Before starting up the CMC 156, carefully read the following
safety instructions.
The system must not be put into operation without full knowledge of this
information!
The CMC 156 may only be operated by trained personnel on the
company premises!

Test Set CMC 156
4
For your safety
The generator outputs supply voltages up to 125 Vrms therefore:
• Operate the CMC 156 only with mains suppy with protective grounding!
• Connecting of one of the front-sided connectors to protective ground is not
permissible as this may cause dangerous contact voltages at all front panel
connectors. Grounding of a voltage output causes that also the sockets of
the analog inputs as well as the current outputs and N-connectors have
phase voltage.
• Use only measuring cables with 4 mm banana plugs and plastic jacketing
for connection to banana sockets; always insert plugs up to the stops.
Recommendation: use 4 mm safety banana plugs.
• Do not leave test leads exposed; always disconnect test leads at the
CMC 156 first!
• When connecting and disconnecting the test object make sure that all
generator outputs have been turned "OFF". Never disconnect the test
object when in a manual program section a switch in the software is "ON"
or a sweep is still under way (e.g. V, I, ϕ).
• All front panel sockets are to be considered as dangerous voltage contacts
with working voltages of up to 250Vrms. Therefore only cables certified to
the corresponding national standards institute may be used.
• If the generator section lamp lights, there is a dangerous contact voltage
(> 42 Vpk) at least at one of the three voltage outputs!
• Never insert conductive parts (screwdriver, etc.) into the sockets!
• Do not operate in a wet or humid environment (condensation).
• Do not operate if an explosive environment.
• External devices may only be connected to the SELV interfaces of the
CMC 156 (host-interface, Gen. out 7-12, ext. Interface) if they comply to the
SELV requirements according to EN60950.
Do not open the CMC 156 or remove any of its housing components
Voltages of up to 400 V will occur inside the unit! If the unit is opened,
warranty claims will become void.
If the mains fuse must be replaced (rear panel of the test set)
First disconnect the mains plug of the CMC test set!
Unscrew the plastic tile and change the fuse (T6.3AH 250V).

Table of Contents
5
Table of Contents
Safety Instructions...................................................................................................3
Table of Contents.....................................................................................................5
1Introduction .......................................................................................................7
2Start-Up..............................................................................................................9
2.1 System components ............................................................................................................9
2.2 System Start.........................................................................................................................9
3Design and Operation.....................................................................................11
3.1 Modules..............................................................................................................................12
3.1.1 Host Interface .......................................................................................................13
3.1.2 Processor..............................................................................................................13
3.1.3 D/A Converter + Reconstruction Filter .................................................................13
3.1.4 Measuring Module ................................................................................................14
3.1.5 Internal Current and Voltage Amplifiers ...............................................................15
3.1.6 Power Supply........................................................................................................16
3.2 Signal Generation ..............................................................................................................17
3.3 Accuracy ............................................................................................................................19
4Connectors and Interfaces .............................................................................20
4.1 Connectors on the Front Panel..........................................................................................20
4.1.1 Generator Combination Socket for VOLTAGE OUTPUT, CURRENT OUTPUT .22
4.1.2 Measurement Combination Socket for BINARY INPUT and ANALOG INPUT ...24
4.2 Connections on the Back Panel.........................................................................................27
4.2.1 Gen. out 7-12........................................................................................................27
4.2.2 ext. Interface .........................................................................................................29
5Technical Data.................................................................................................31
5.1 Mains Supply .....................................................................................................................31
5.2 Outputs...............................................................................................................................32
5.2.1 Current Outputs CURRENT OUTPUT 1-3 ...........................................................33
5.2.2 Voltage Outputs VOLTAGE OUTPUT 1-3............................................................35
5.2.3 Interface for an External Amplifier ‘Gen. out 7-12’ ...............................................36
5.2.4 Binary Outputs Relays..........................................................................................37
5.2.5 Binary Outputs Transistor.....................................................................................38

Test Set CMC 156
6
5.3 Inputs ................................................................................................................................ 39
5.3.1 Binary Inputs........................................................................................................ 39
5.3.2 Counter Inputs 100 kHz....................................................................................... 41
5.3.3 Measuring Inputs ................................................................................................. 42
5.4 Computer Interface ........................................................................................................... 43
5.5 Ambient Conditions........................................................................................................... 43
5.5.1 Climate................................................................................................................. 43
5.5.2 Shock and Vibration ............................................................................................ 44
5.5.3 Electromagnetic Compatibility (EMC).................................................................. 44
5.6 Safety ................................................................................................................................ 45
5.7 Mechanical Data ............................................................................................................... 45
6Technical Data EP Option .............................................................................. 47
6.1 Outputs (EP option) .......................................................................................................... 48
6.1.1 Current Outputs CURRENT OUTPUT 1-3 .......................................................... 49
6.1.2 Voltage Outputs VOLTAGE OUTPUT 1-3........................................................... 53
6.1.3 Output Power with EP option............................................................................... 55
7Appendix ......................................................................................................... 57
7.1 Optional Devices............................................................................................................... 57
7.1.1 Current Amplifier CMA 56.................................................................................... 57
7.1.2 Current Amplifier CMA 156.................................................................................. 58
7.1.3 Voltage and Current Amplifier CMS 156 ............................................................. 60
7.1.4 CMLIB B - Optional connection for meter testing ................................................ 62
7.2 Ordering Notes.................................................................................................................. 64
8Contact Information / Technical Support...................................................... 69
Index ....................................................................................................................... 71

Introduction
7
1 Introduction
The CMC 156 test system consists of the components CMC 156 test set, a
computer and the CMC user software. External amplifiers and optional devices
can also be controlled optionally.
Due to its wide range of optional settings, the CMC 156 test set completely
eliminates the need for operating elements on the front panel - every function
is controlled by the software on the COMPUTER. This means the module-
structured application software as well as the configuration of the test system.
The CMC software is described in the CMC software user's manual.
This description exclusively refers to the hardware of the CMC 156 test set.

Test Set CMC 156
8

Start-Up
9
2 Start-Up
2.1 System components
Before start-up, please verify that all system components are present:
• CMC 156 test set
• Mains cable
• Connection cable CMC 156 ↔computer (25-pole)
• Connection cable CMC 156 ↔test object:
These are provided by the user.
• Standard computer with a parallel interface
2.2 System Start
The instructions below can be followed if the computer is set up completely
and the software is installed properly.1
A description of the installation of the CMC software is found in your CMC
software manual, chapter 1 "Installation".
The following procedure is recommended to connect the system components:
Figure 1 Connection CMC 156 and computer
1These instructions refer to a system including a computer and basic device CMC 156, i.e. without
additional amplifiers. If the system is to be operated with external amplifiers, please refer to the
instructions in your CMC SW user's manual, section "Configuring an external amplifier".

Test Set CMC 156
10
Generally: Make sure that the ventilation slots at the rear panel of the
CMC 156 are free and clear!
1. Connect the CMC 156 test set to the computer:
•If the computer is equipped with a parallel printer port, use the 25-pole
cable (VEHK0002) 1that was supplied with the test set to connect the
CMC 156 to the computer.
•If the computer is equipped with a USB port, use an OMICRON
CMUSB-P converter (ordering number VEHZ2007) instead of the
VEHK0002 to connect the CMC 156 to the computer.
2. Connect the CMC 156 and the computer to the power supply. (Power
supply cable is supplied.)
3. Power both units up. CMC 156: ON/OFF switch on the front panel.
4. For further actions, see the Installation in the appropiate software manual.
5. Start the software.
An extensive hardware test is carried out when the software is starting up. If
there is a hardware fault, the software will put out an appropriate message
after starting).
1Only original centronics cable may be used due to the electromagnetic compatibility (EMC)
requirement for the connecting cable.

Design and Operation
11
3 Design and Operation
Our computer-controlled design concept allows the following segregation of
functions:
Computer
• Application software
• Control and display
• Measuring data processing
• Reporting and archiving
CMC 156 test set
• Signal generation
• Voltage and current amplifier
• Input signal measurement
• Time-critical processes

Test Set CMC 156
12
3.1 Modules
... Power GND potential
2
4
2
3
3
6
6
4
Mains
Low level
outputs
Gen. out 7-12
Supply Reinforced isolation
to mains
Isolation
for SELV
Isolation for
working voltage (relays)
Signal generator
and measuring units
Current amplifier
Voltage amplifier
±10VInput
± 20mA Input
Binaryoutputs
1-4
Binaryinputs
5-10
Binary inputs
1-4
Idc
Udc
Counter inputs
ext. Interface
Binary outputs
(transistor)
ext. Interface
PC connection
Host Interface
PC
Figure 2 Basic block diagram of the CMC 156

Design and Operation
13
3.1.1 Host Interface
The CMC 156 communicates with the computer via the Host Interface (parallel
printer interface) at its rear side.
If the computer is equipped with a parallel printer port, too, use the 25-pole
cable (VEHK0002) that was supplied with the test set to connect the CMC 156
to the computer.
If the computer is equipped with a USB port, use an OMICRON CMUSB-P
converter (ordering number VEHZ2007) instead of the VEHK0002 to connect
the CMC 156 to the computer.
3.1.2 Processor
A signal processor is the core of the test set hardware. It has the following
tasks:
• Communications with the host computer
• Signal generation
• Control of the test set hardware
• Input signal measurement and filtering
Its Harvard architecture and the built-in arithmetic unit make the signal
processor ideally suited for digital signal processing tasks.
For example, the signal processor needs for multiplication + adding + parallel
data transfer only two machine cycles (30ns). The CMC 156 uses this
advantage of the signal processor for signal generation and digital filtering.
3.1.3 D/A Converter + Reconstruction Filter
For D/A converters 16-bit PCM converters are used. Their high resolution
allows coverage of the entire amplitude range without range switching.
This is important in particular for fault simulation for protective devices,
because range switching in the test set via relays may cause erroneous
tripping when switching from a load to a fault condition.
The reconstruction low pass filter forms the desired output signal from the
stair-step output signals of the D/A converters and suppresses the high
frequency component, which is periodically repeated with the sampling
frequency. The 3dB bandwidth is at 3.1kHz.

Test Set CMC 156
14
3.1.4 Measuring Module
The measuring module for analog signals primarily consists of a laser trimmed
high-precision voltage reference, a 16-bit A/D converter with series-connected
multiplexer and the appropriate input circuits (precision voltage divider, filter).
The input signals Vdc and Idc, the output voltages, amplifier temperatures, etc.
are measured here. Behind the Idc input a PTC thermistor is located as
reversible fuse.
The binary inputs are read via opto-isolators having a time resolution of 100 μs
and are divided in two isolated groups (group 1: binary inputs 1..4; group 2:
binary inputs 5..10). The binary inputs can be configured by means of the
CMC software. You can specify if floating or potential-carrying contacts are to
be connected. For potential-carrying contacts, the expected rated voltage may
be specified (individually for each binary input) and the operating threshold of
the binary inputs may be set.
The operating threshold is set in % of the nominal voltage.1
To isolate single binary inputs against each, other additional opto-Isolators
may be connected in series to the binary inputs.
For ordering notes see section 7.2, „Ordering Notes“.
The configuration of the binary inputs in the CMC software is described in your
CMC software user's manual, section "Configuring the binary inputs".
The binary inputs 1..10 can also be used as counter inputs for input
frequencies of up to 3kHz.
Additionally, for meter testing with higher frequencies
(e.g. with reference meters), two counter inputs for input frequencies of up to
100kHz are available at the ‘ext. Interf.’ interface.
1Range: 10 to 71%; valid for binary inputs 1-10.

Design and Operation
15
3.1.5 Internal Current and Voltage Amplifiers
The output amplifiers are designed as linear amplifiers and direct voltage
coupling with MOSFET output stages.
Using this technology, excellent harmonic distortion and frequency response
specifications can be realized in a very compact design.
The direct voltage coupling allows accurate representation of any transient
function.
Protection of the current and voltage outputs
If a current output is feed externally from one of the voltage outputs, it will not
self-destruct. However, if power is supplied from an external source, the
current output may be destroyed.
The voltage outputs are also protected against overload and sustained short
circuit by means of a fast electronic current limiter and temperature sensors.
Protection against transient overvoltage is effected by means of transient
absorbers.
If two voltage outputs are shorted against each other, the output elements are
brought close to their capacity limits, but they will not be destroyed.
For heat sink temperatures > 167°F (75°C), all outputs are thermally
disconnected (including the outputs on the rear panel of the test set).
Overload displays in the software
At the event of an overload at one of the current or voltage outputs a
corresponding display will be shown in the CMC software.1
1This display depends on the software version; for how your software will display these states,
please refer to chapter 3 of the CMC software manual.

Test Set CMC 156
16
What to do in case of a switching OFF due to
overtemperature?
If a thermal switching OFF occurs due to a low ohmic burden in connection
with a high ON period, one of the following messages is displayed on screen:
Overtemperature at voltage output! All V and I outputs
switched off!
Overtemperature at current output! All V and I outputs
switched off!
The most important status messages can be found in chapter 13 of the CMC
software manual.
To avoid switching OFF, the power supply voltage of the current amplifier can
be reduced. For more information, please refer to the CMC software manual,
chapter ‘System configuration’.
3.1.6 Power Supply
The following power supplies are used in the CMC 156:
a. The mains-sided power supply with power factor correction creates an
intermediate circuit voltage for the supply of the connected isolated power
supplies.
b. Auxiliary supply for the supply of the processor and of all analog circuits of
the power amplifiers.
c. Supply for the voltage amplifiers
d. Supply for the current amplifiers
e. Supplies for the two isolated binary input groups
f. Supply for the parallel SELV1 interface to the computer
g. Supply for the analog SELV interfaces for controlling additional amplifiers
1Safety extra-low voltage.

Design and Operation
17
3.2 Signal Generation
To achieve the specified quality of the output signals, the generation of sine
signals of high quality is necessary. The requirement for 6 fixed-phase
coupled signals suggests a digital implementation.
In the CMC 156 the quality of the signals is achieved due to the use of a
modern and powerful signal processor.
The implemented algorithm linearly interpolates between the basic values of
any signal table according to the following equation:
S[i+x]=S[i]+x*{S[i+1]-S[i]}
S[i]..........basic table value i
x .............fractional component of the table pointer
The table may be processed with any real step width. The output of sine
signals uses the internal sine table which has 256 basic entries. The
frequency resolution is 2.33 μHz, and the phase resolution is < 50 μdegrees.
16k words are available per channel in the signal table for transient signals. By
means of interpolation, the signals are always output at 10k-samples/s, even if
the basic value table contains less samples/s, as is common in fault
recordings.

Test Set CMC 156
18
Generator
triple
1
Generator
triple
2
Generator
triples
3 and 4
3
3
6
0 ... 5 V
rms
Gen. out 7-12
0 ... 125 V
rms
VOLTAGE
OUTPUT 1-3
0 ... 12,5 A
rms
CURRENT
OUTPUT 1-3
I
V
Figure 3 Block diagram of the generator outputs of the CMC 156
The CMC 156 test system supplies four generator triples of three signals each.
The generator triples 1 and 2 are output via the internal amplifiers to the
outputs of the front panel.
• The generator triple 1 is output via the internal voltage amplifier to the
outputs VOLTAGE OUTPUT 1-3 on the front panel.
• The generator triple 2 is output via the internal current amplifier to the
outputs CURRENT OUTPUT 1-3 on the front panel.
The completely independent generator triples 3 and 4 are output on the
interface Gen. out 7-12 at the back panel, which is intended for controlling
external amplifiers (0 to 5Vrms).
The generator triples 3 (Gen. out 7-9) and 4 (Gen. out 10-12) can be
• put out via external amplifiers, which can be connected via the isolated
interfaces at the back panel of the unit
or
• used directly.
The selection of the amplifiers takes place in the software.
The configuration of amplifiers in the CMC software is described in chapter 3
your CMC software user's manual.

Design and Operation
19
3.3 Accuracy
The data sheet values for the CMC 156 are not typical values but guaranteed
values over one year from the time of factory calibration at 23 °C ±5 %
(73 °F ± 10 °F).
Some factors had to be taken into account during development in order to
achieve the desired accuracy. For example, let's look at the signal path from
the signal generator to the output jack:
Si g n al
generation
DSP
D/A conver t er Rec. f il t er
A
mplifier Output
signal
Figure 4 Output signal path
When the signal is generated in the DSP, an adequate bit width is ensured.
Naturally, the drift and the temperature coefficients are unimportant.
Therefore, the amplitude and offset correction is preferably carried out in the
DSP. There are no conventional trim pots (with poor temperature coefficients)
at all.
The amplification and offset errors of the D/A converters are corrected by the
DSP. For component selection the linearity as well as temperature and long-
term drift were taken into account above all.
In the case of the voltage amplifier it is important that there is a gain-fixing
negative feedback across the entire amplifier, which is built via precision
resistors with corresponding temperature coefficient.
To ensure precision production appropriate measuring devices are necessary.
The measuring devices used by OMICRON are calibrated at regular intervals.
This ensures traceability to national and international standards.

Test Set CMC 156
20
4 Connectors and Interfaces
4.1 Connectors on the Front Panel
+
_
I
0
BINARY OUTPUT
4 internal floating binary outputs
routed out individually.
8-pole combination jack for outputs
and
.
(for assignment see the following)
VOLTAGE OUTPUT 1-3
CURRENT OUTPUT 1-3
VOLTAGE OUTPUT
VOLTAGE OUTPUT 1-3
Signals brought out via
internal amplifiers.
.
Combination jack for ,
20-pole combination jack for the
following connections:
- current measuring input
- voltage measuring input
- 10 binary inputs
(for assignment see the following)
BINARY INPUT
ANALOG INPUT
ANALOG INPUT
0..±20mA: DC current input
routed out individually.
0..±10V: DC voltage input
routed out individually.
BINARY INPUT
Binary inputs 1 .. 10 routed out
individually.
POWER
Mains switch.
CURRENT OUTPUT
CURRENT OUTPUT 1-3
Signals brought out via
internal amplifiers.
.
Warn display
:
At least one phase has
more than 42 V.
Figure 5 Front panel
Table of contents
Other Omicron Measuring Instrument manuals
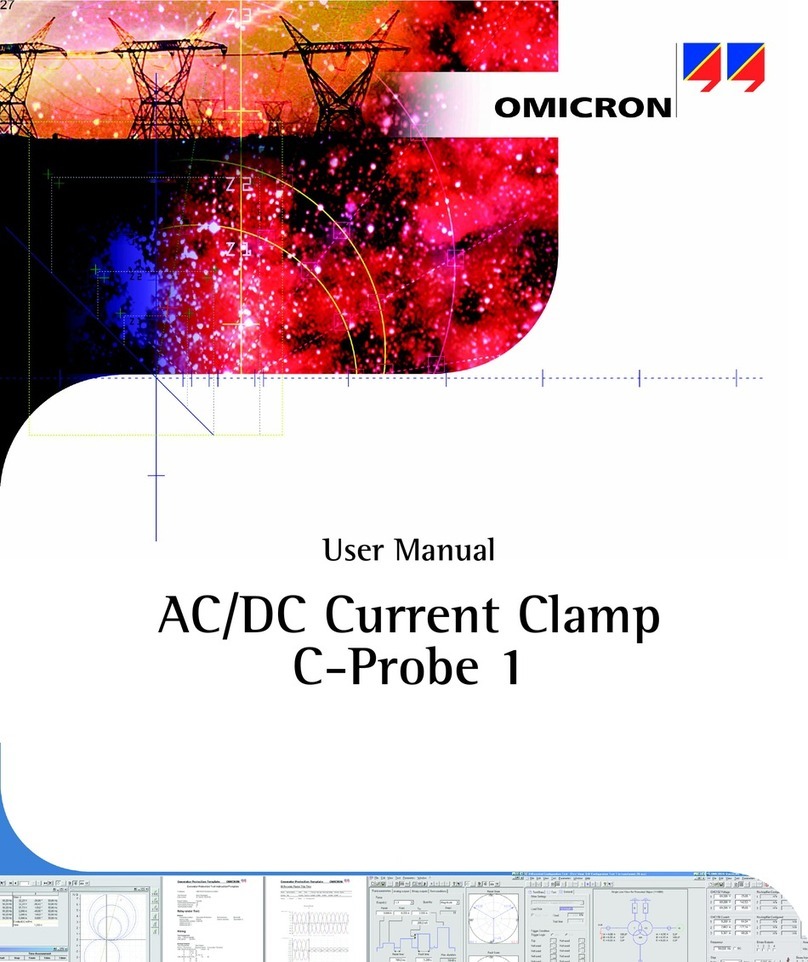
Omicron
Omicron C-Probe 1 User manual
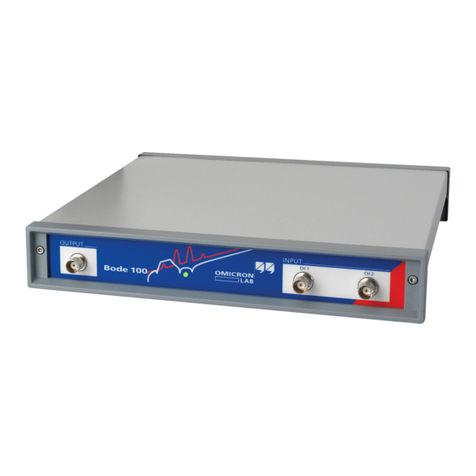
Omicron
Omicron Bode 100 User manual

Omicron
Omicron COMPANO 100 Installation and operating instructions
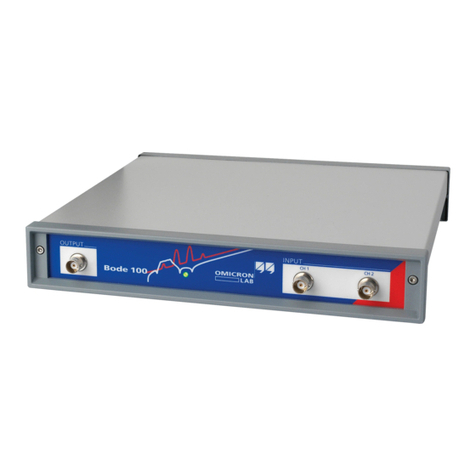
Omicron
Omicron Bode 100 User manual
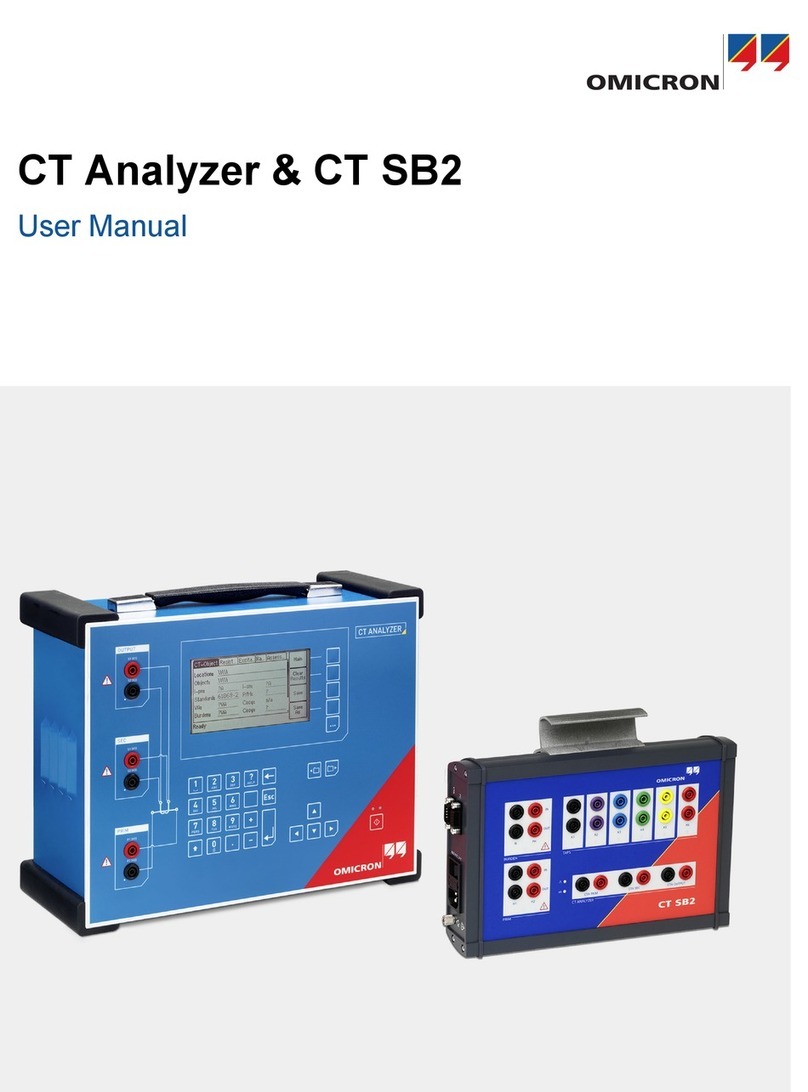
Omicron
Omicron CT SB2 User manual
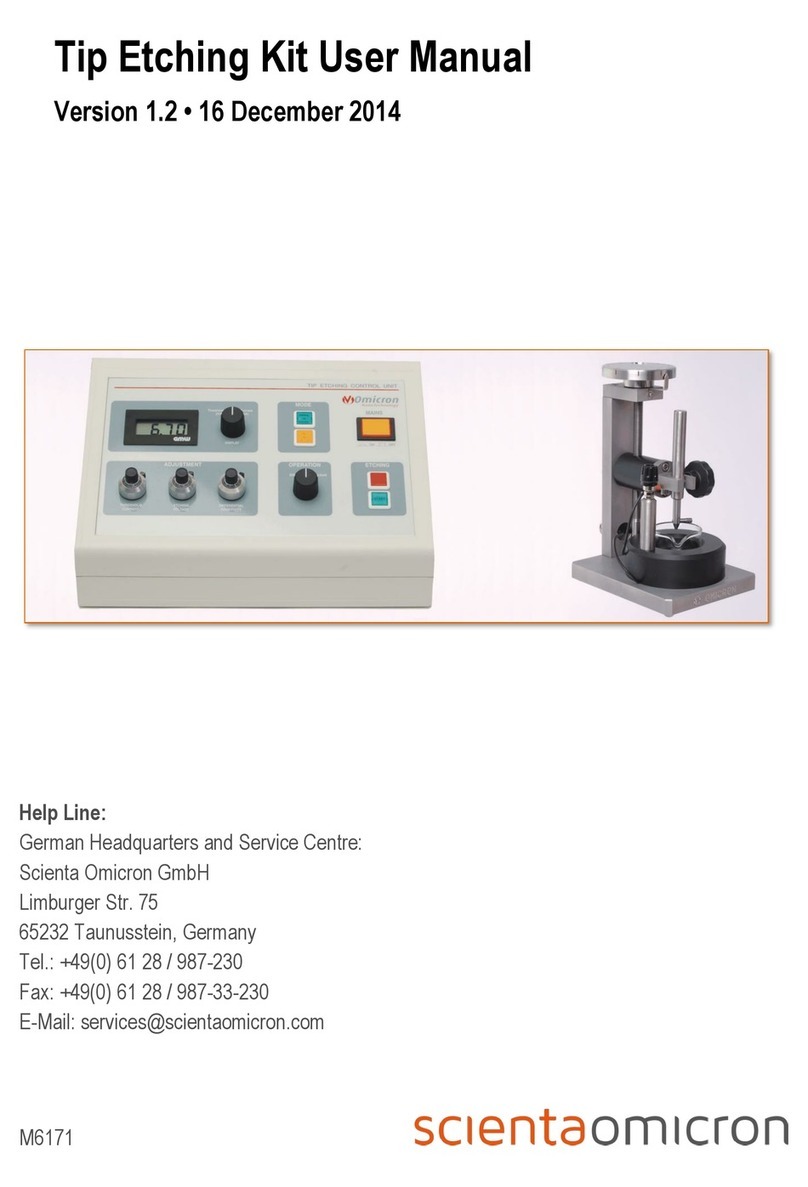
Omicron
Omicron Tip Etching Kit User manual
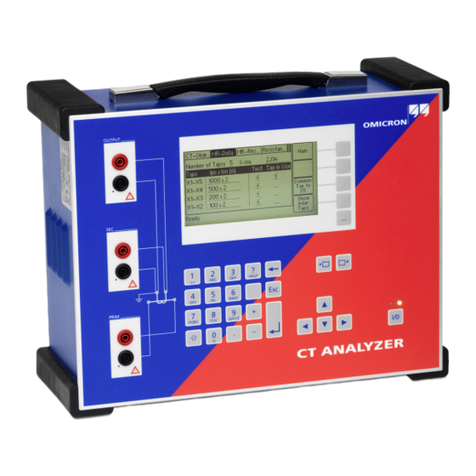
Omicron
Omicron CT Analyzer User manual

Omicron
Omicron DANEO 400 User manual
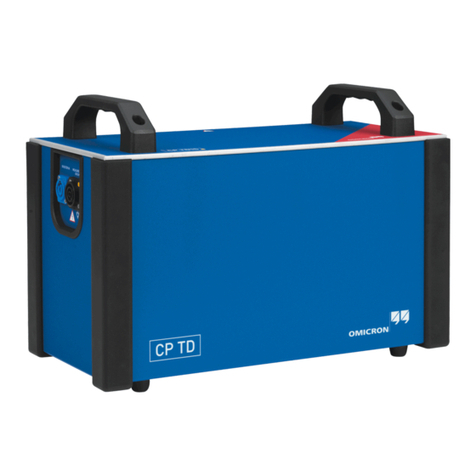
Omicron
Omicron CP TD1 User manual
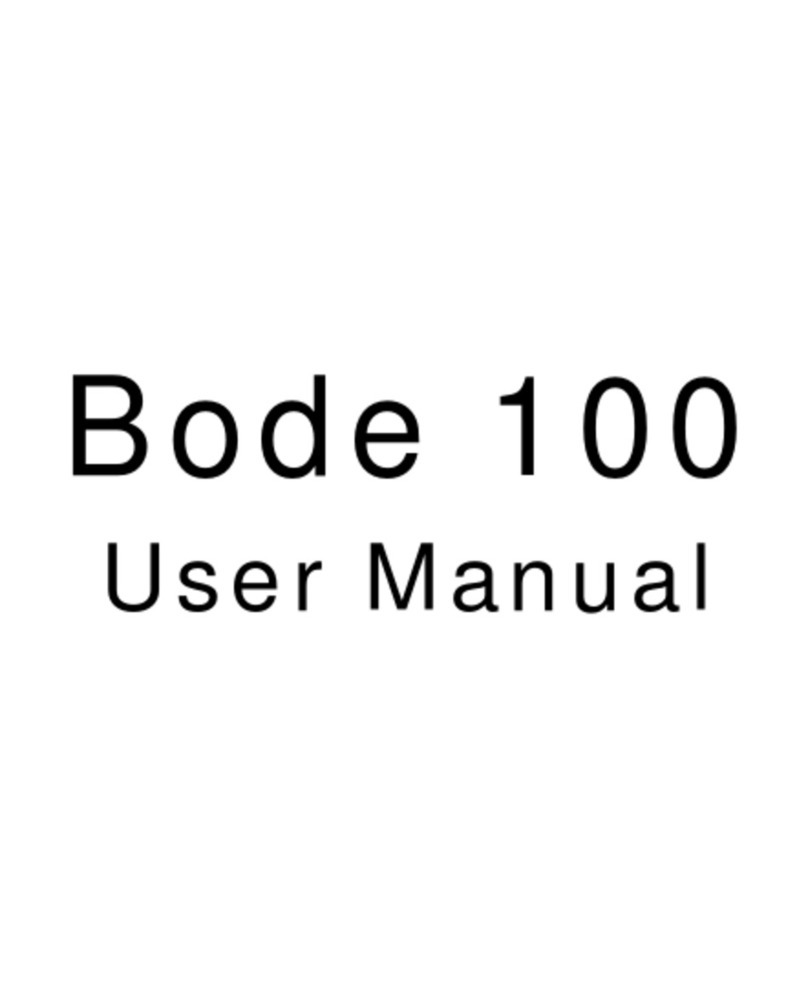
Omicron
Omicron Bode 100 User manual