Omron V600-HAM42-DRT User manual

V600 RFID System
V600-HAM42-DRT Intelligent Flag III
(DeviceNet-compatible)
Operation Manual
Produced February 1999

iv

!
!
!
v
Notice:
OMRON products are manufactured for use according to proper procedures by a qualified operator
and only for the purposes described in this manual.
The following conventions are used to indicate and classify precautions in this manual. Always heed
the information provided with them. Failure to heed precautions can result in injury to people or dam-
age to property.
DANGER Indicates an imminently hazardous situation which, if not avoided, will result in death or
serious injury.
WARNING Indicates a potentially hazardous situation which, if not avoided, could result in death or
serious injury.
Caution Indicates a potentially hazardous situation which, if not avoided, may result in minor or
moderate injury, or property damage.
OMRON Product References
All OMRON products are capitalized in this manual. The word “Unit” is also capitalized when it refers
to an OMRON product, regardless of whether or not it appears in the proper name of the product.
The abbreviation “Ch,” which appears in some displays and on some OMRON products, often means
“word” and is abbreviated “Wd” in documentation in this sense.
The abbreviation “PC” means Programmable Controller and is not used as an abbreviation for any-
thing else.
Visual Aids
The following headings appear in the left column of the manual to help you locate different types of
information.
Note Indicates information of particular interest for efficient and convenient operation
of the product.
1, 2, 3...
1. Indicates lists of one sort or another, such as procedures, checklists, etc.
OMRON, 1999
All rights reserved. No part of this publication may be reproduced, stored in a retrieval system, or transmitted, in any
form, or by any means, mechanical, electronic, photocopying, recording, or otherwise, without the prior written permis-
sion of OMRON.
No patent liability is assumed with respect to the use of the information contained herein. Moreover, because OMRON is
constantly striving to improve its high-quality products, the information contained in this manual is subject to change
without notice. Every precaution has been taken in the preparation of this manual. Nevertheless, OMRON assumes no
responsibility for errors or omissions. Neither is any liability assumed for damages resulting from the use of the informa-
tion contained in this publication.

vi

TABLE OF CONTENTS
vii
SECTION 1
Introduction 1. . . . . . . . . . . . . . . . . . . . . . . . . . . . . . . . . . . .
1-1 Features 2. . . . . . . . . . . . . . . . . . . . . . . . . . . . . . . . . . . . . . . . . . . . . . . . . . . . . . . . . . . . . . .
1-2 Models 3. . . . . . . . . . . . . . . . . . . . . . . . . . . . . . . . . . . . . . . . . . . . . . . . . . . . . . . . . . . . . . . .
1-3 System Configuration 3. . . . . . . . . . . . . . . . . . . . . . . . . . . . . . . . . . . . . . . . . . . . . . . . . . . . .
1-4 Overview of System Operation 5. . . . . . . . . . . . . . . . . . . . . . . . . . . . . . . . . . . . . . . . . . . . .
SECTION 2
Specifications and Performance 7. . . . . . . . . . . . . . . . . . . .
2-1 Amplifiers 8. . . . . . . . . . . . . . . . . . . . . . . . . . . . . . . . . . . . . . . . . . . . . . . . . . . . . . . . . . . . . .
2-2 Sensors 18. . . . . . . . . . . . . . . . . . . . . . . . . . . . . . . . . . . . . . . . . . . . . . . . . . . . . . . . . . . . . . . .
2-3 Data Carriers (EEPROM, Without Battery) 21. . . . . . . . . . . . . . . . . . . . . . . . . . . . . . . . . . .
2-4 Data Carriers (SRAM, With Built-in Battery) 26. . . . . . . . . . . . . . . . . . . . . . . . . . . . . . . . . .
SECTION 3
Transmission Specifications 33. . . . . . . . . . . . . . . . . . . . . . .
3-1 Transmission Distance 34. . . . . . . . . . . . . . . . . . . . . . . . . . . . . . . . . . . . . . . . . . . . . . . . . . . .
3-2 Transmission Time 37. . . . . . . . . . . . . . . . . . . . . . . . . . . . . . . . . . . . . . . . . . . . . . . . . . . . . . .
SECTION 4
Installation 39. . . . . . . . . . . . . . . . . . . . . . . . . . . . . . . . . . . . .
4-1 Installing Amplifiers 40. . . . . . . . . . . . . . . . . . . . . . . . . . . . . . . . . . . . . . . . . . . . . . . . . . . . .
4-2 Installing Sensors 44. . . . . . . . . . . . . . . . . . . . . . . . . . . . . . . . . . . . . . . . . . . . . . . . . . . . . . . .
4-3 Installing Data Carriers 52. . . . . . . . . . . . . . . . . . . . . . . . . . . . . . . . . . . . . . . . . . . . . . . . . . .
SECTION 5
Communicating With Host Devices 61. . . . . . . . . . . . . . . . .
5-1 Read Operation in AUTO Mode 62. . . . . . . . . . . . . . . . . . . . . . . . . . . . . . . . . . . . . . . . . . . .
5-2 Read Operation in SYNC Mode 64. . . . . . . . . . . . . . . . . . . . . . . . . . . . . . . . . . . . . . . . . . . .
5-3 Write Operation in AUTO Mode 66. . . . . . . . . . . . . . . . . . . . . . . . . . . . . . . . . . . . . . . . . . . .
5-4 Write Operation in SYNC Mode 68. . . . . . . . . . . . . . . . . . . . . . . . . . . . . . . . . . . . . . . . . . . .
5-5 Sample Program for Host 70. . . . . . . . . . . . . . . . . . . . . . . . . . . . . . . . . . . . . . . . . . . . . . . . . .
5-6 Error Processing 71. . . . . . . . . . . . . . . . . . . . . . . . . . . . . . . . . . . . . . . . . . . . . . . . . . . . . . . . .
SECTION 6
Chemical Resistance 73. . . . . . . . . . . . . . . . . . . . . . . . . . . . .
6-1 V600-HS51, V600-HS61, V600-HS-63, and V600-HS67 Sensors 74. . . . . . . . . . . . . . . . . .
6-2 Data Carriers 75. . . . . . . . . . . . . . . . . . . . . . . . . . . . . . . . . . . . . . . . . . . . . . . . . . . . . . . . . . .
Appendices
A Accessories (Sold Separately) 79. . . . . . . . . . . . . . . . . . . . . . . . . . . . . . . . . . . . . . . . . . . . . . . . .
B I/O Allocation 81. . . . . . . . . . . . . . . . . . . . . . . . . . . . . . . . . . . . . . . . . . . . . . . . . . . . . . . . . . . . .
C Multi-vendor Applications 83. . . . . . . . . . . . . . . . . . . . . . . . . . . . . . . . . . . . . . . . . . . . . . . . . . . .
D Conformity to Standards 87. . . . . . . . . . . . . . . . . . . . . . . . . . . . . . . . . . . . . . . . . . . . . . . . . . . . .
Revision History 89. . . . . . . . . . . . . . . . . . . . . . . . . . . . . . . . .

ix
About this Manual:
This manual describes the installation and operation of the V600 RFID System Intelligent Flag III for the
DeviceNet and includes the sections described below.
Please read this manual carefully and be sure you understand the information provided before attempting
to install and operate the V600 RFID System Intelligent Flag III. Keep this manual in a convenient location
where it can continue to be used for reference and guidance.
Section 1
provides a general introduction to the V600 RFID System Intelligent Flag III, including the fea-
tures and system configuration.
Section 2
provides specifications and performance details for Amplifiers, Sensors, and Data Carriers.
Section 3
provides transmission specifications, including distances, ranges, and times.
Section 4
explains how to install Intelligent Flag III Amplifiers, Sensors, and Data Carriers.
Section 5
presents the timing charts and operation outlines for Intelligent Flag Amplifiers when communi-
cating with a host device. Write a communications program for the host according to the timing charts
shown in this section.
Section 6
provides information on the chemical resistance of Sensors and Data Carriers.
The Appendices provide information on accessories, I/O allocation, and multi-vendor applications.
WARNING Failure to read and understand the information provided in this manual may result in
personal injury or death, damage to the product, or product failure. Please read each
section in its entirety and be sure you understand the information provided in the section
and related sections before attempting any of the procedures or operations given.
!

1
SECTION 1
Introduction
This section provides a general introduction to the V600 RFID System Intelligent Flag III, including the features and system
configuration.
1-1 Features 2. . . . . . . . . . . . . . . . . . . . . . . . . . . . . . . . . . . . . . . . . . . . . . . . . . . . . . . . . . . . . . . .
1-2 Models 3. . . . . . . . . . . . . . . . . . . . . . . . . . . . . . . . . . . . . . . . . . . . . . . . . . . . . . . . . . . . . . . . .
1-3 System Configuration 3. . . . . . . . . . . . . . . . . . . . . . . . . . . . . . . . . . . . . . . . . . . . . . . . . . . . . .
1-4 Overview of System Operation 5. . . . . . . . . . . . . . . . . . . . . . . . . . . . . . . . . . . . . . . . . . . . . .

1-1SectionFeatures
2
1-1 Features The Intelligent Flag III provides innovative electronic ID flags which replace con-
ventional mechanical flags and Kanbans and also improve quality control and
production process control systems. The host interface conforms to DeviceNet
(CompoBus/D), one of the global standard buses, and it can be used for
constructing a more widely applicable system.
The Intelligent Flag III is the successor to the Intelligent Flag and Intelligent Flag
II, and retains essential functions such as data reading, data writing, bit setting,
and bit clearing.
Data reading is now enabled for up to 24 bits, which is 1.5 times more than the
existing Intelligent Flag series. Data can now be written in units of either eight or
16 bits. Moreover, access addresses (00Hto FFH) for Data Carriers can now be
set from remote Masters.
A single read/write head is now equivalent to anywhere from eight to 24 sensors.
The space required for flags or Kanbans can be greatly reduced because only
one Data Carrier is required.
With the longer transmission distance of up to 100 mm, precise positioning as
required for older sensors is not necessary. Furthermore, there is no need to be
concerned about mutual interference during installation.
Since the Intelligent Flag III has no mechanical parts, such as the cylinders used
in conventional mechanical flags, there is no need to be concerned with service
life or mechanical failures.
The Intelligent Flag III is compatible with V600 Data Carriers, so it can be used
for expanding an existing line.
Sets with Amplifiers, Sensors, and Data Carriers conform to EN standards (EMC
instructions: EN50081-2, EN50082-2).
Builds on Existing
Intelligent Flag Series
More Flexible
Applications
Space Saving
Workable With
Approximate Positioning
Trouble-free Maintenance
Compatible with Other
OMRON RFID Systems
Conforms to EN
Standards

1-3SectionSystem Configuration
3
1-2 Models The Intelligent Flag models are shown below. Select the one best suited to the
application.
8-bit Intelligent Flag 16-bit Intelligent Flag II
8-bit Amplifier for
Read Data Output:
V600-HAR91
8-bit Amplifier with
Versatile Functions:
V600-HAM91
16-bit Amplifier for
Read Data Output:
V600-HAR92
Amplifier with Versatile
Functions Conforming to
DeviceNet (CompoBus/D)
V600-HAM42-DRT
Intelligent Flag III
(This is the model described
in this manual.)
OMRON’s V600 RFID
System Intelligent Flags
1-3 System Configuration
The Intelligent Flag III conforms to DeviceNet (CompoBus/D), an open network,
and can be connected with special-purpose connectors as a Slave. Usability has
been improved by making the Amplifiers and Sensors also connectible by one-
touch connectors.
All V600 Data Carriers can be used.

1-3SectionSystem Configuration
4
(Master)
Master Unit
Slave
DCA1/DCA2-5C10
Intelligent Flag III
Amplifier
(Slave)
V600-HAM42-DRT
Connection
Sensor Sensor
V600-HS51 V600-HS61 V600-HS63 V600-HS67
Wireless transmission Wireless transmission
Data Carrier (DC)
(All V600 Data Carriers can be accessed.)
V600-
D23P53 V600-
D23P54 V600-
D23P61 V600-
D23P66 V600-
D23P66SP V600-
D23P72 V600-
D23P71 V600-
D8KR12 V600-
D8KR04 V600-
D2KR16
Master Unit
I/O I/O

1-4SectionOverview of System Operation
5
1-4 Overview of System Operation
Host device
(Programmable Controller)
Interface cable
Sensor Transmis-
sion area Data
Carrier
Pallet
Line control
Master Unit
V600-HAM42-DRT
(Amplifier)
1, 2, 3...
1. The host system, such as a Programmable Controller, issues a request to
the Amplifier to read or write data from or to a Data Carrier. At this time it also
specifies the address of the Data Carrier to be accessed.
2. When the Data Carrier mounted on a pallet comes into the transmission
area of the Sensor, data is read from or written to the specified address in the
Data Carrier.
3. When data is read, it is sent from the Amplifier to the host system and output
by DeviceNet. When data is written, the result of the write processing (i.e.,
whether the write was successfully completed or not) is sent to the host.
4. Upon receiving the result, the host system performs tasks such as produc-
tion line control.

7
SECTION 2
Specifications and Performance
This section provides specifications and performance details for Amplifiers, Sensors, and Data Carriers.
2-1 Amplifiers 8. . . . . . . . . . . . . . . . . . . . . . . . . . . . . . . . . . . . . . . . . . . . . . . . . . . . . . . . . . . . . . .
2-1-1 Names and Functions of Components 8. . . . . . . . . . . . . . . . . . . . . . . . . . . . . . . . . .
2-1-2 Specifications 13. . . . . . . . . . . . . . . . . . . . . . . . . . . . . . . . . . . . . . . . . . . . . . . . . . . . .
2-1-3 I/O Specifications 13. . . . . . . . . . . . . . . . . . . . . . . . . . . . . . . . . . . . . . . . . . . . . . . . .
2-1-4 Dimensions 17. . . . . . . . . . . . . . . . . . . . . . . . . . . . . . . . . . . . . . . . . . . . . . . . . . . . . .
2-2 Sensors 18. . . . . . . . . . . . . . . . . . . . . . . . . . . . . . . . . . . . . . . . . . . . . . . . . . . . . . . . . . . . . . . . .
2-2-1 Specifications 18. . . . . . . . . . . . . . . . . . . . . . . . . . . . . . . . . . . . . . . . . . . . . . . . . . . . .
2-2-2 Dimensions 19. . . . . . . . . . . . . . . . . . . . . . . . . . . . . . . . . . . . . . . . . . . . . . . . . . . . . .
2-3 Data Carriers (EEPROM, Without Battery) 21. . . . . . . . . . . . . . . . . . . . . . . . . . . . . . . . . . . . .
2-3-1 Specifications and Dimensions 21. . . . . . . . . . . . . . . . . . . . . . . . . . . . . . . . . . . . . . .
2-3-2 Memory Map 24. . . . . . . . . . . . . . . . . . . . . . . . . . . . . . . . . . . . . . . . . . . . . . . . . . . . .
2-3-3 Write Protect Function 25. . . . . . . . . . . . . . . . . . . . . . . . . . . . . . . . . . . . . . . . . . . . . .
2-4 Data Carriers (SRAM, With Built-in Battery) 26. . . . . . . . . . . . . . . . . . . . . . . . . . . . . . . . . . .
2-4-1 Specifications and Dimensions 26. . . . . . . . . . . . . . . . . . . . . . . . . . . . . . . . . . . . . . .
2-4-2 Memory Map 28. . . . . . . . . . . . . . . . . . . . . . . . . . . . . . . . . . . . . . . . . . . . . . . . . . . . .
2-4-3 Write Protect Function 29. . . . . . . . . . . . . . . . . . . . . . . . . . . . . . . . . . . . . . . . . . . . . .
2-4-4 Battery Service Life 30. . . . . . . . . . . . . . . . . . . . . . . . . . . . . . . . . . . . . . . . . . . . . . . .

2-1SectionAmplifiers
8
2-1 Amplifiers
2-1-1 Names and Functions of Components
Component Names
DeviceNet (CompoBus/D) Connector
For connecting to DeviceNet.
Data Indicators
Green: Read data displayed in bit units.
Red: Flashes to show error classification (bits 0 to 7 only).
CS Indicator
Shows results of communications with Data Carrier.
Green: Normal completion
Red: Error
NS Indicator
Shows DeviceNet communications status.
MS Indicator
Shows operating status.
DIP Switch 1
DeviceNet communications settings
Power supply terminals
Sensor Connector
For connecting the Sensor.
Cover
DIP Switch 2
Operating mode settings

2-1SectionAmplifiers
9
An XW4B-05C1-H1-D COMBICON screw plug is provided for the cable end at
the Unit.
Connector (Plug)
Wire color Signal classification
Red Power supply cable, + side (V+)
White Communications data high side (CAN H)
--- Shield
Blue Communications data low side (CAN L)
Black Power supply cable, – side (V–)
Note For details regarding plugs and cables, refer to the
CompoBus/D (DeviceNet)
Operation Manual (W267)
.
Indicators
Name Function Contents
Data indicator Data 0 to 7 Green lit 16-bit indicators for data 0 to 7.
Error Red flashing Shows error classification.
Data 8 to 15 Green lit 16-bit indicators for data 8 to 15.
CS indicator Communications status Green lit Data Carrier read/write normal completion
Red lit Data Carrier read/write error
NS indicator Network status Green lit Communications connection completed.
Green flashing Communications not connected.
Red lit Fatal communications error
Red flashing Nonfatal communications error
Not lit Power supply OFF.
MS indicator Machine status Green lit Normal
Green flashing Not set
Red lit Fatal malfunction
Red flashing Nonfatal malfunction
Not lit Power supply OFF.
This DIP switch is used to make the DeviceNet (CompoBus/D) communications
settings. To make the settings, first lift the cover.
DIP Switch 1
Node number setting Baud rate setting
All pins are factory
set to 0.
DeviceNet Connector
DIP Switch 1

2-1SectionAmplifiers
10
Node Number Setting
Set the node number with pins 1 to 6. The node number can be set from 00 to 63.
Node
b
DIP switch 1 pins
number 123456
00 OFF OFF OFF OFF OFF OFF
01 ON OFF OFF OFF OFF OFF
02 OFF ON OFF OFF OFF OFF
03 ON ON OFF OFF OFF OFF
04 OFF OFF ON OFF OFF OFF
to : : : : : :
61 ON OFF ON ON ON ON
62 OFF ON ON ON ON ON
63 ON ON ON ON ON ON
Baud Rate Setting
Set the baud rate with pins 7 and 8. Any of the following three rates can be set:
125 Kbps, 250 Kbps, or 500 Kbps.
Baud rate DIP switch 1 pins
7 8
125 Kbps OFF OFF
250 Kbps ON OFF
500 Kbps OFF ON
Cannot be set. ON ON
Note 1. Set the same baud rate for all of the nodes (Masters and Slaves) on the net-
work. If a Slave’s baud rate is different from the Master’s, not only can the
Slave’s communications not be referenced, but communications errors may
occur for communications between correctly set nodes.
2. Be sure to turn OFF the power supply before making DIP switch settings.
This DIP switch is used to set the operating mode. To make the setting, first lift
the cover.
DIP Switch 2
Access mode
setting
Not used. (Must be OFF.)
All pins are factory
set to 0.
Output mode setting
Output Mode Setting
This pin is used to set the time for outputting the results following communica-
tions with the Data Carrier.
Output mode DIP switch 2, pin 1
100 ms OFF
500 ms ON
DIP Switch 2

2-1SectionAmplifiers
11
Access Mode Setting
This pin sets the mode for beginning communications with the Data Carrier. For
beginning communications by receiving synchronized inputs from Sensors, use
the SYNC mode. For beginning communications automatically by waiting for the
Data Carrier to come into range without synchronous inputs, use the AUTO
mode. Select either of these modes according to the application.
Access mode DIP switch 2, pin 2
AUTO mode OFF
SYNC mode ON
Note Be sure to turn OFF the power supply before making DIP switch settings.
The sensor connector is for connecting V600-HS51, V600-HS61, V600-HS63,
or V600-HS67 Sensors.
These terminals are for connecting the power supply and protective conductor
terminal.
No. Name Function
124 VDC + Input terminals for 24-VDC
l
224 VDC – (0 V) power supply
3GR Protective conductor terminal
Note If the environment has a large amount of noise, ground the GR terminal to 100 Ω
or less. Do not use the same ground wire for any other devices. If the ground wire
is shared with another device, there will be a greater chance of incurring adverse
effects.
V600-HAM42-DRT Another device
V600-HAM42-DRT Another device
Ground to 100 Ω. or less.
Ground to 100 Ω. or less.
Correct
Incorrect
The V600-HAM42-DRT Amplifier has both read and write functions.
With the read function, 24 bits in three bytes from the address specified in the
Data Carrier can be read.
There are three write modes: BYTE, BIT SET, and BIT CLEAR. In BYTE mode,
8-bit (1-byte) data is written. In BIT SET mode, particular bits are turned ON (1).
In BIT CLEAR mode, particular bits are turned OFF (0). This write function is the
same as that of mechanical flags.
Either 16 bits (2 bytes) or 8 bits (one byte) can be selected as the write range.
Toggling between read and write is executed by turning ON the bit (WTBYTE
signal) assigned by DeviceNet (CompoBus/D).
Read Function
1, 2, 3...
1. Three bytes of data (24 bits) is read from the Data Carrier, beginning from
the address specified by the address input. The read data is output with the
data output signal.
Sensor Connector
Power Supply Terminals
Functions
Cover

2-1SectionAmplifiers
12
2. The NORMAL output signal is turned ON after the data is output.
3. When data in the Data Carrier fails to be read normally, the ERROR output
turns ON at the same time as the error classification is output with the data
output signal.
The write function has the following three modes:
1. BYTE Mode
1, 2, 3...
1. Data entered with the data input signal (16/8 bits) is written to the Data Carri-
er in the area specified by the address input,16/8 bit switch input, and write
area input.
2. After write processing is complete, the normal termination output signal
NORMAL is turned ON.
3. When data fails to be written normally to the Data Carrier, the ERROR output
turns ON at the same time as the error classification is output with the data
output signal.
2. BIT SET Mode
1, 2, 3...
1. Only the bits that are turned ON by the data input signal (16/8 bits) are set in
the area specified by the address input,16/8 bit switch input, and write area
input.
2. After write processing is complete, the normal termination output signal
NORMAL is turned ON.
3. When data fails to be written normally to the Data Carrier, the ERROR output
turns ON at the same time as the error classification is output with the data
output signal.
3. BIT CLEAR Mode
1, 2, 3...
1. Only the bits that are turned ON by the data input signal (16/8 bits) are
cleared to 0 in the area specified by the address input,16/8 bit switch input,
and write area input.
2. After write processing is complete, the normal termination output signal
NORMAL is turned ON.
3. When data fails to be written normally to the Data Carrier, the ERROR output
turns ON at the same time as the error classification is output with the data
output signal.
Write Function

2-1SectionAmplifiers
13
2-1-2 Specifications
General Specifications
Item Specifications
Number of Master words Input: 2; output: 2 (total: 4 words)
Number of Sensor
connections 1 channel
Communications power
supply voltage 11 to 25 VDC (provided from communications
connector)
Internal circuit power supply
voltage 18 to 26.4 VDC
Internal current consumption Communications power supply: 40 mA max.
Internal circuit power supply: 150 mA max.
Noise immunity Internal circuit power supply normal ±600 V
Internal circuit power supply common: ±1,500 V
Dielectric strength 50/60 Hz at 500 VAC for 1 minute; leakage current
10 mA max.
Vibration resistance 10 to 55 Hz, 1.5-mm amplitude, with 4 sweeps of 8
min each in 3 directions
Shock resistance 294 m/s2(approx. 30G), 6 times each in 3 directions
Ambient temperature Operating:0°C to 55°C (with no icing)
Storage: –25°C to 65°C
Ambient humidity Operating: 35% to 85% (with no condensation)
Degree of protection IEC60529 IP20 (built-in structure)
Mounting method DIN track or direct mounting using accessory fittings
(M4 screws)
External dimensions 656560 (mm)
Weight Approx. 150 g
Applicable Sensors
Model
V600-HS51
V600-HS61
V600-HS63
V600-HS67
Applicable Standards
Standards
EN50081-2
EN50082-2
Note These standards apply to the EMC regulations in the EC Directives when the
V600-HS63 Sensor (2m) is used.
2-1-3 I/O Specifications
The V600-HAM42-DRT occupies 32 input bits (2 words) and 32 output bits (2
words) of the Programmable Controller. The particular words occupied (word X
and word Y) vary according to the Master (model and operating mode) and the
node number set by the V600-HAM42-DRT DIP switch.

2-1SectionAmplifiers
14
Allocated I/O Words
Point Input (IN)
Word X Word (X+1)
0 ID0 ADDR0
1 ID1 ADDR1
2 ID2 ADDR2
3 ID3 ADDR3
4 ID4 ADDR4
5 ID5 ADDR5
6 ID6 ADDR6
7 ID7 ADDR7
8 ID8 WT_MODE1
9 ID9 WT_MODE2
10 ID10 WT_BYTE
11 ID11 WT_AREA
12 ID12 Reserved. (See note 1.)
13 ID13 Reserved. (See note 1.)
14 ID14 READ/WRITE
15 ID15 INHIBIT/TRG
Point Output (OUT)
Word Y Word (Y+1)
0 OD0 EXT OD16
1 OD1 EXT OD17
2 OD2 EXT OD18
3 OD3 EXT OD19
4 OD4 EXT OD20
5 OD5 EXT OD21
6 OD6 EXT OD22
7 OD7 EXT OD23
8 OD8 Not used.
9 OD9 Not used.
10 OD10 Not used.
11 OD11 Not used.
12 OD12 Not used.
13 OD13 ERROR
14 OD14 NORMAL
15 OD15 HS
Note 1. Reserved inputs must be used as 0.
2. Refer to
Appendix B I/O Allocations
for examples of I/O allocations. For de-
tails, refer to the
CompoBus/D (DeviceNet) Operation Manual (W267)
.

!
2-1SectionAmplifiers
15
Signal Functions
Signal Name Function
ID0 to ID15 Data Input Input write data to the Data Carrier.
OD0 to OD15 Data Output Output read data from the Data Carrier. The data indicator is lit during
output.
EXT OD 16 to 23 Extension Data Output Output read data from the Data Carrier. There is no data indicator for
these outputs.
ADDR0 to ADDR7 Address Input Specify start address for reading or writing.
INHIBIT/TRG INHIBIT Input/Trigger
Input Inputs the INHIBIT signal when in AUTO mode.
INHIBIT signal 0: No communication with the Data Carrier.
INHIBIT signal 1: Communication with the Data Carrier.
Inputs the TRG signal when in SYNC mode.
When the TRG signal is input, communication with the Data Carrier will
start.
READ/WRITE R/W Switching Input Switches between READ and WRITE.
When this bit is OFF (0), data is read from the Data Carrier.
When this bit is ON (1), data is written to the Data Carrier.
WT_MODE1 Write Mode 1 Input Switches between bytes and bits for WRITE operations.
When this bit is OFF (0), data is written in byte units.
When this bit is ON (1), data is written in bit units.
WT_MODE2 Write Mode 2 Input Switches between BIT SET and BIT CLEAR for WRITE operations.
When this bit is OFF (0), BIT SET is performed.
When this bit is ON (1), BIT CLEAR is performed.
WT_BYTE 16/8 Bit Switching Input Switches between 16-bit and 8-bit data for WRITE operations.
When this bit is OFF (0), 16-bit data is written to the Data Carrier.
When this bit is ON (1), 8-bit data is written to the Data Carrier.
WT_AREA Write Area Input Switches between ID0 to ID7 and ID8 to ID15 for 8-bit WRITE BYTE
operations.
When this bit is OFF (0), the data in ID0 to ID7 is written to the Data
Carrier.
When this bit is ON (1), the data in ID8 to ID15 is written to the Data
Carrier.
HS HS Output Controls INHIBIT/TRG input signal handshaking. Becomes “1” when
INHIBIT/TRG input is received, and “0” when cleared. The response
time depends on network conditions (baud rate, number of nodes,
Master settings, etc.). Create a program so that the host device waits
for this signal to turn ON before clearing the INHIBIT/TRG input.
NORMAL Normal Output This signal is output when communications with the Data Carrier are
completed normally for READ or WRITE operations. For READ
operations, read the data in OD0 to OD15 and EXT OD16 to EXT
OD23 with the rising edge of this signal.
ERROR Error Output This signal is output when communications with the Data Carrier are
not completed normally for READ or WRITE operations.
Caution Be sure to observe the following precautions.
Note 1. Power Supply Voltage
Do not use an AC (100 VAC) power supply or any voltage exceeding the
rated voltage. Unsuitable power supplies may cause the equipment to ex-
plode or burn.
2. Load Short-circuiting
Do not short-circuit the load or connect it to the power supply. Doing either of
these may cause the equipment to explode or burn.
3. Wiring
Be careful not to make wiring mistakes such as reversing the polarity of the
power supply. Wiring mistakes may cause the equipment to explode or
burn.
Table of contents
Other Omron Amplifier manuals
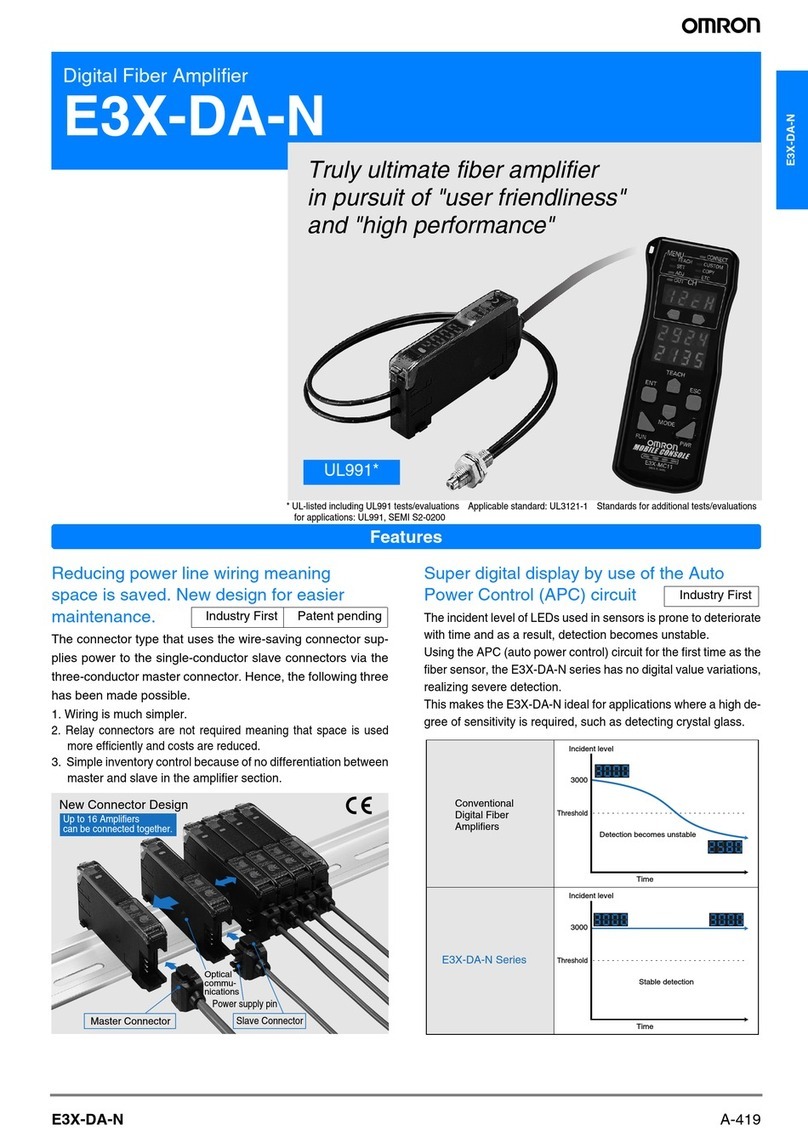
Omron
Omron E3XDAC21S2M User manual
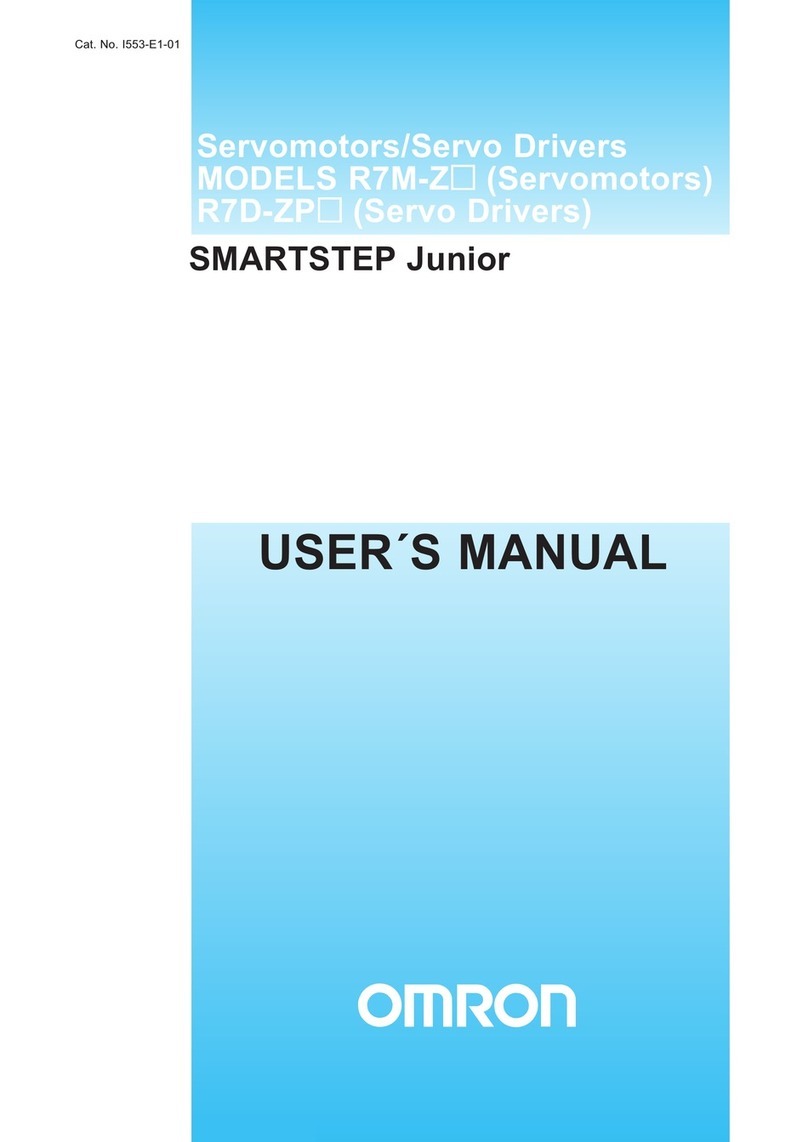
Omron
Omron SMARTSTEP Junior R7D-ZP User manual
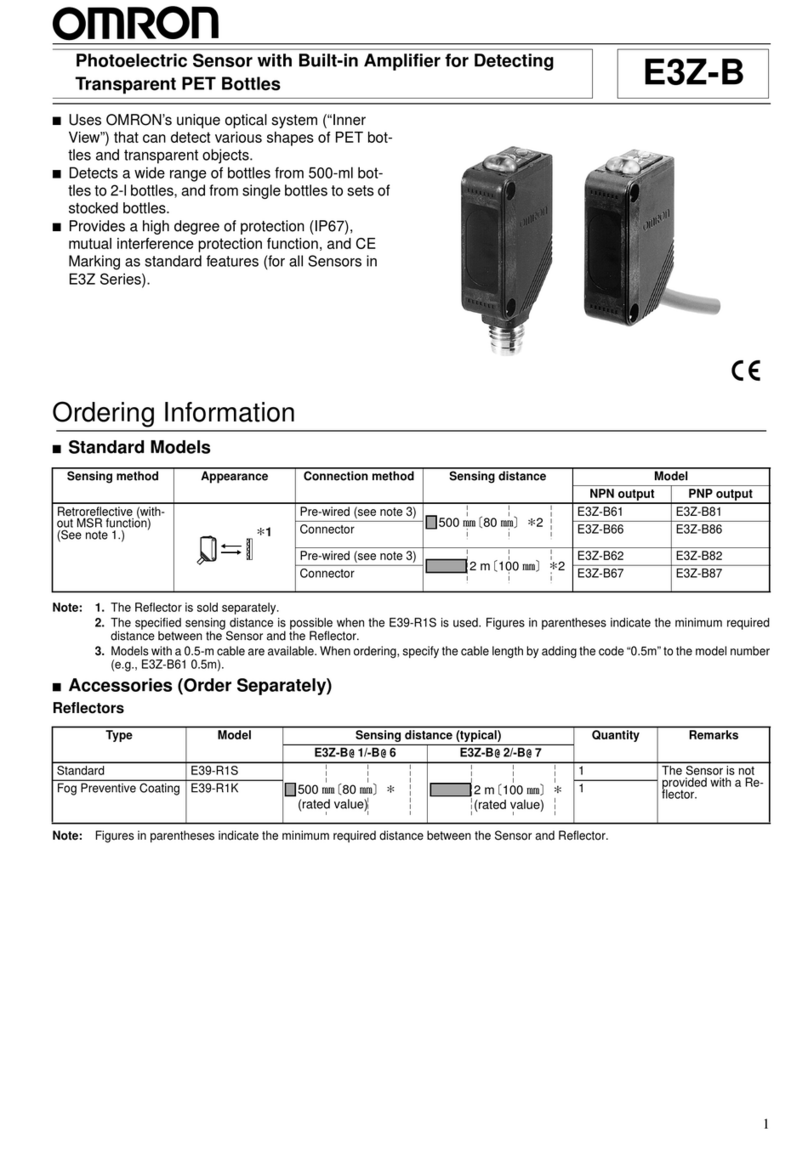
Omron
Omron E3Z-B61 2M User manual
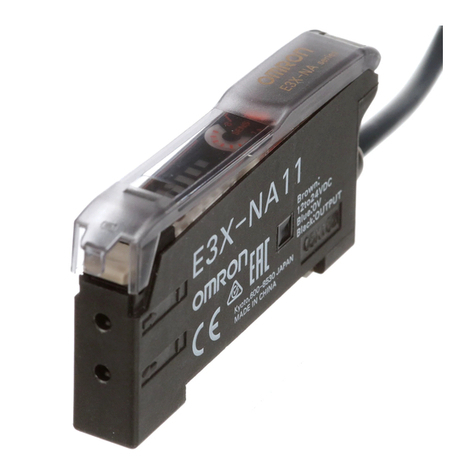
Omron
Omron E3X-NA F Series User manual
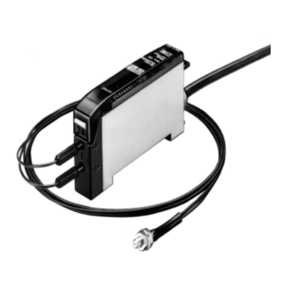
Omron
Omron E3X-NH User manual
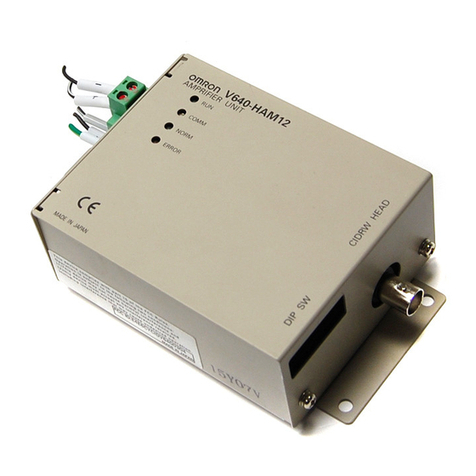
Omron
Omron V640 User manual
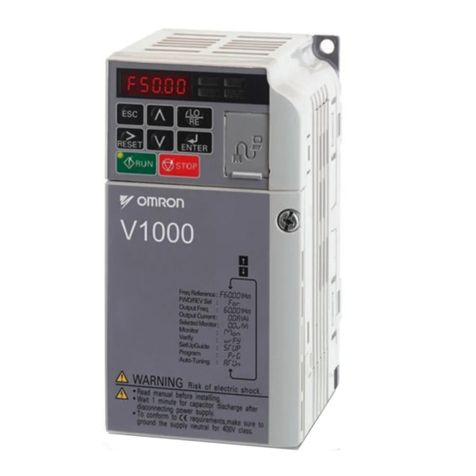
Omron
Omron V1000 User manual
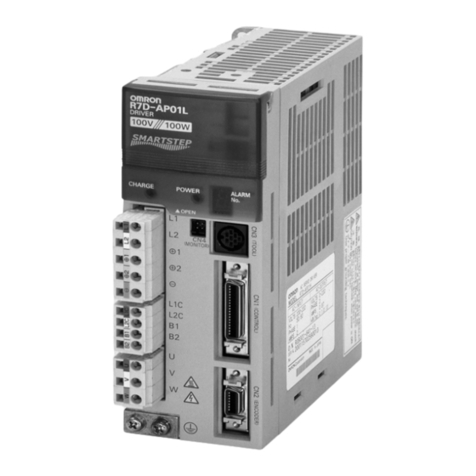
Omron
Omron SMARTSTEP R7D-AP Series User manual
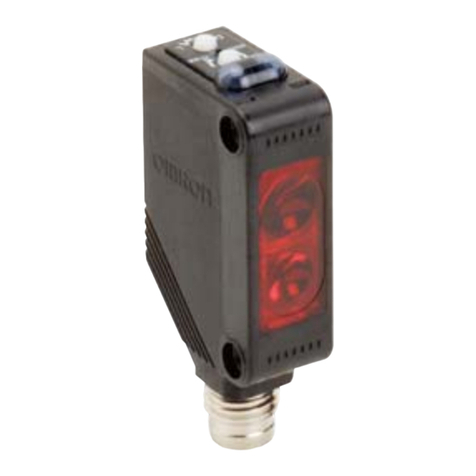
Omron
Omron E3Z-L User manual

Omron
Omron E3X-CN11 User manual
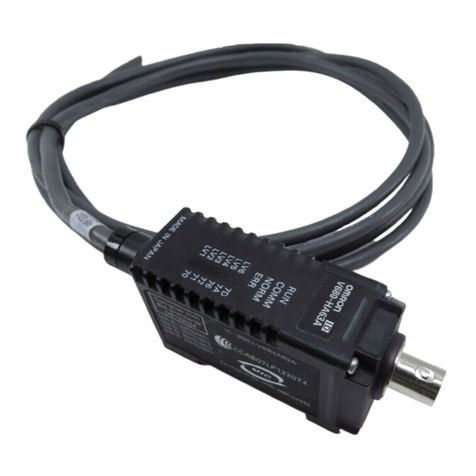
Omron
Omron V680-HA63 User manual

Omron
Omron V600-HA User manual
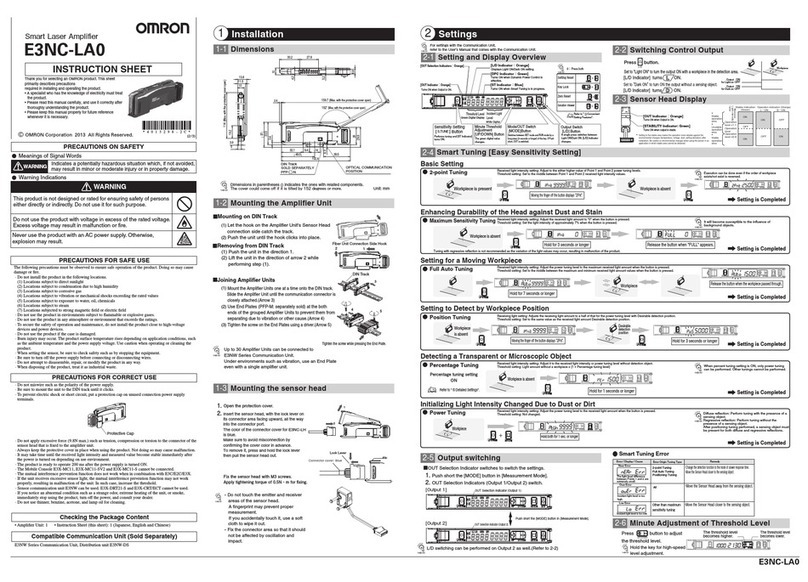
Omron
Omron E3NC-LA0 User manual
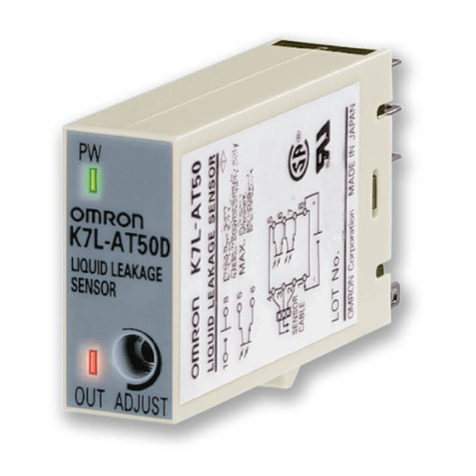
Omron
Omron K7L-AT50 User manual
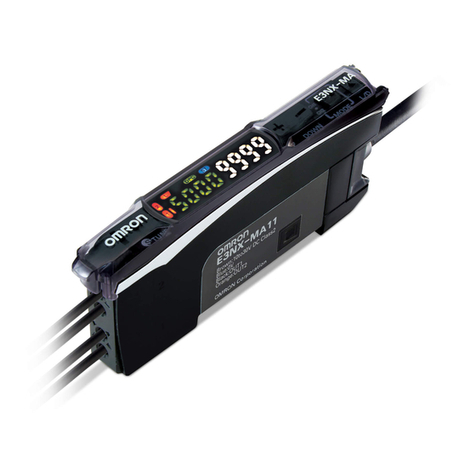
Omron
Omron E3NX-MA Series User manual
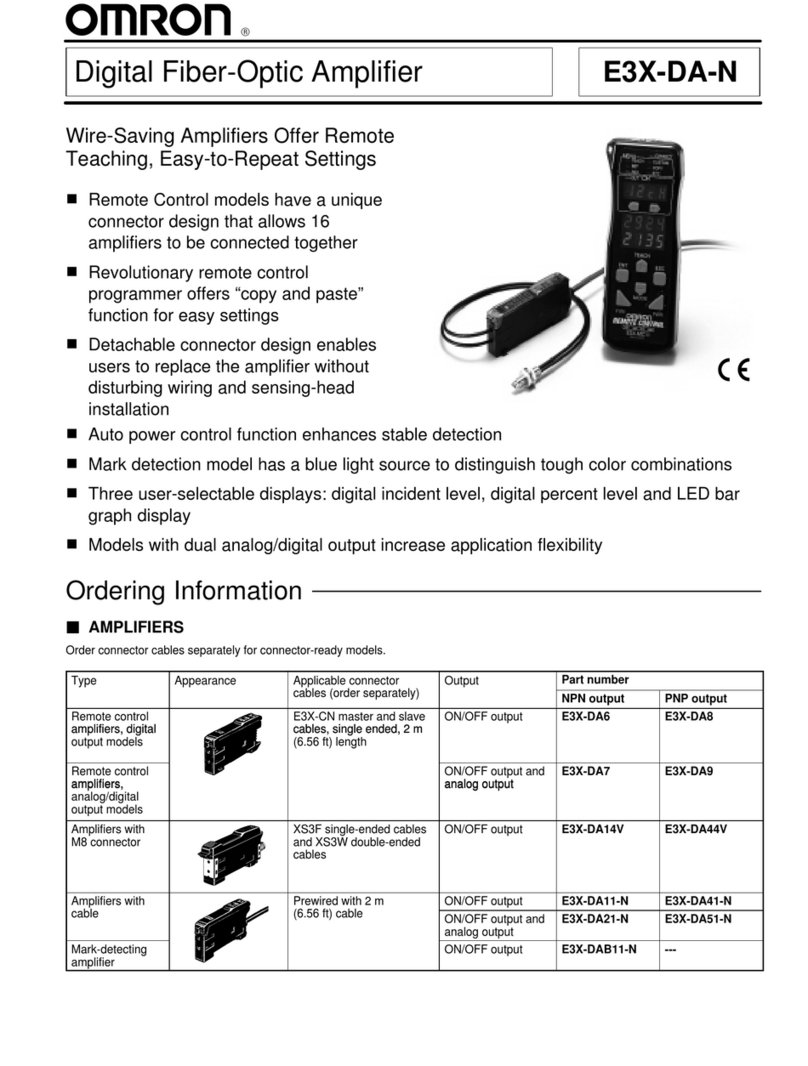
Omron
Omron E3X-DA-N series User manual
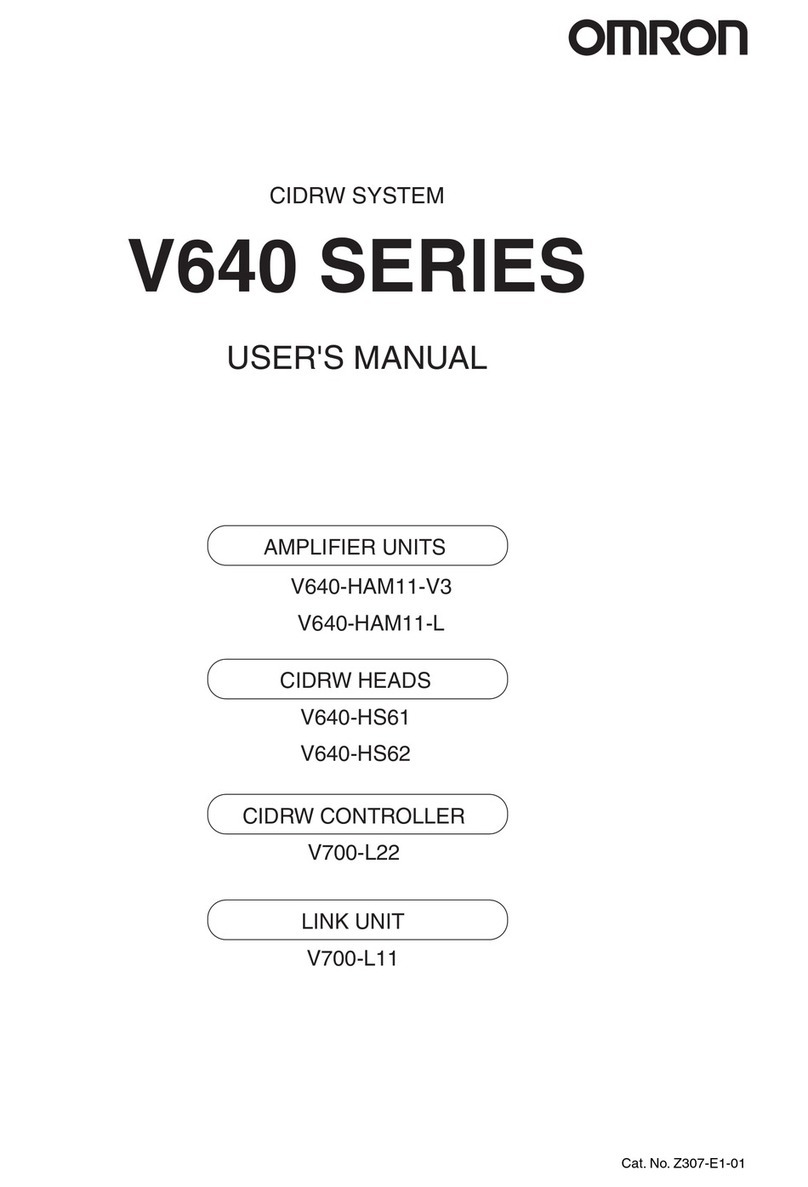
Omron
Omron V640-HAM11-V3 User manual
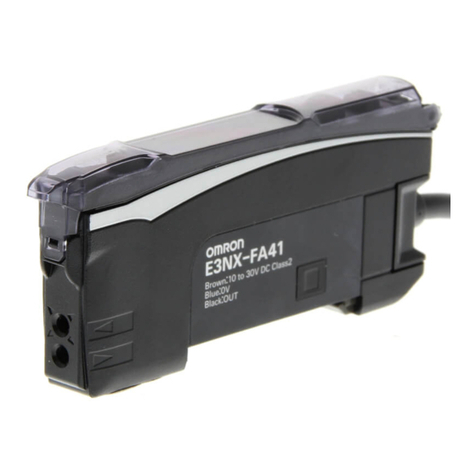
Omron
Omron E3NX-FA11AN User manual
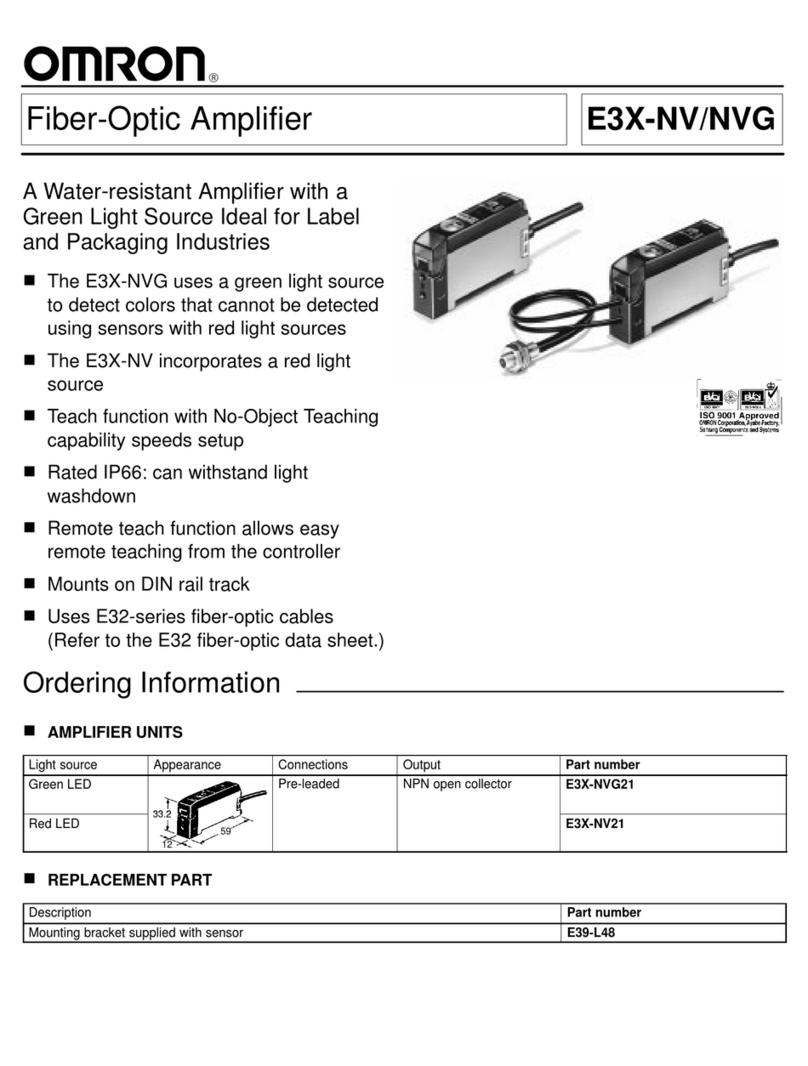
Omron
Omron E3X-NV User manual
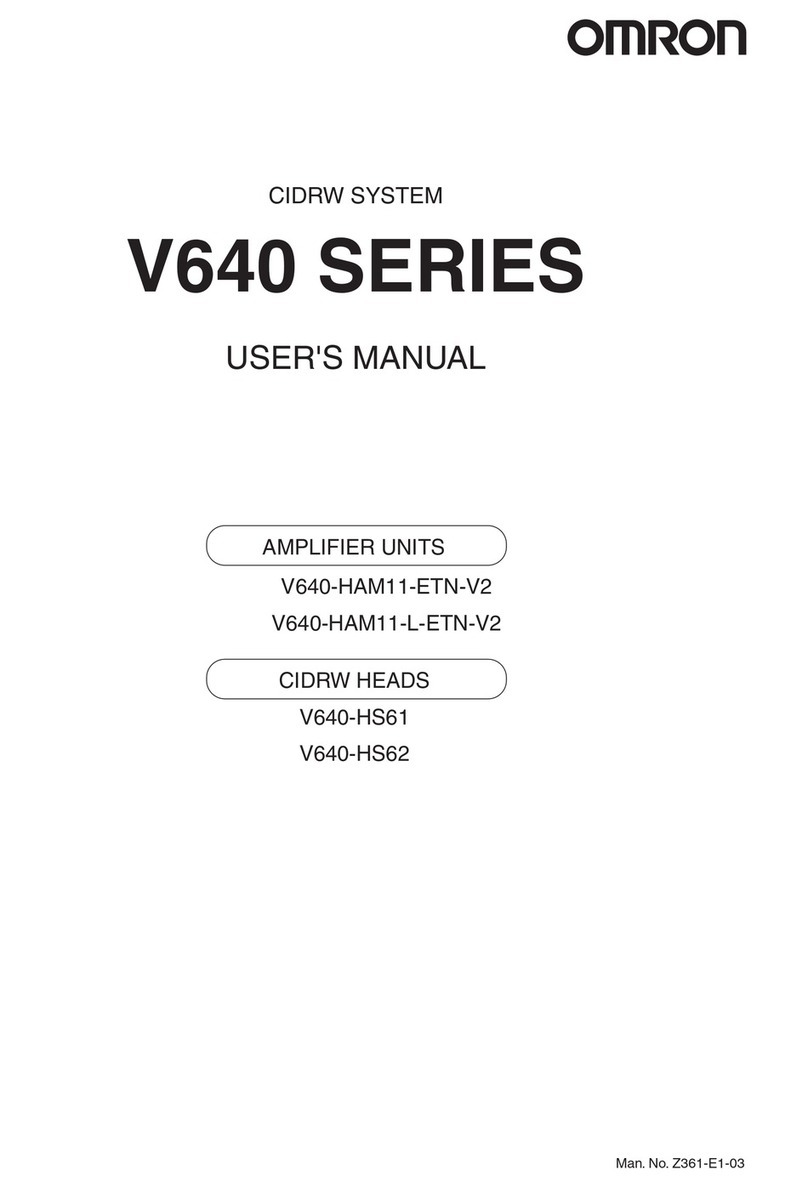
Omron
Omron V640 Series User manual