Openpath OP-SH-24V User manual

OPENPATH
ACCESS CONTROL SYSTEM
INSTALLATION GUIDE
V1.8

Openpath Access Control System Installation Guide
GETTING STARTED
ADDITIONAL RESOURCES
PRIOR TO INSTALLATION
Installation
NETWORK REQUIREMENTS
SELECTING A BACKUP BATTERY
MOUNTING INSTRUCTIONS
INSTALLING CORE SERIES BOARDS IN E1 ENCLOSURE
INSTALLING CORE SERIES BOARDS IN E2 ENCLOSURE
INSTALLING CONTROLLER BOARD WITH 24V LOCKING HARDWARE
INSTALLING CONTROLLER BOARD WITH 12V LOCKING HARDWARE
WIRING OPENPATH READERS
STANDARD CONFIGURATIONS
WIRING THE CORE SERIES 24V SMART HUB - 4ENT-SYS-24V
WIRING THE CORE SERIES 24V SMART HUB - 20ENT-SYS-24V
ELEVATOR BUTTON WIRING
GENERAL PURPOSE INPUTS
WIRING THE CORE SERIES 12/24V SMART HUB - 4ENT-SYS-1224V
WIRING THE CORE SERIES 12/24V SMART HUB - 8ENT-SYS-1224V
WIRING WITH THE 12/24V POWER SUPPLY
WIRING THE REX WITH THE DOOR STRIKE
WIRING THE REX WITH THE ELECTROMAGNETIC LOCK
WIRING FAIL SAFE AND FAIL SECURE LOCKING HARDWARE
WIRING THE OPENPATH ELEVATOR BOARD TO A STANDALONE CONTROLLER BOARD
ADVANCED CONFIGURATIONS
CHANGING I/O TYPES
WIRING TO LEGACY PANELS AND MOBILE GATEWAY
WIRING TO WIEGAND DEVICES ON CORE SERIES SMART HUBS
END-OF-LINE SUPERVISION
Troubleshooting
ACU LEDS
READER LEDS
LEGACY WIRING
RESETTING THE ACU
SOFT RESET
HARD RESET
To hard reset the ACU:
PROVISIONING THE ACU
REQUIREMENTS
CREATE ACU IN CONTROL CENTER
Regulatory
UL 294
CAN/ULC 60839-11-1-16 GRADE 1
FCC
IEC 62368-1
RF Radiation Hazard Warning
Industry Canada Notice and Marking
Warnings
Technical Specifications
Version 1.8
© Openpath 2020
Page 2

Openpath Access Control System Installation Guide
GETTING STARTED
This Installation Guide explains how to install and configure Openpath Smart Hubs
(ACUs) and Openpath Smart Readers as part of an Openpath Access Control
system. This guide includes information about Core Series Smart Hubs and first
generation Smart Hubs. For information on the Single Door Controller, refer to the
Openpath SDC Install Guide.
ADDITIONAL RESOURCES
●Access Control Core Data Sheet
●4-Port Board Data Sheet
●8-Port Board Data Sheet
●16 I/O Elevator Board Data Sheet
●24V 4-Door Controller Data Sheet
●12/24V 4-Door Controller Data Sheet
●12/24V 8-Door Controller Data Sheet
●24V Elevator Controller Data Sheet
●Smart Reader Data Sheet
●First Gen Smart Hub Data Sheet
●Openpath User Guide
●Life Safety Power FPV Installation Guide
●Life Safety Power FPO Installation Guide
●Life Safety Power B100 Installation Guide
●Life Safety Power C4 Installation Guide
PRIOR TO INSTALLATION
Prior to installing Openpath hardware, perform a customer site survey to determine
the following:
●How many entries need to be configured (e.g. doors, gates, and/or elevator
floors)
●Whether you’re using legacy wiring or new wiring
●What kind of electronic entry mechanisms, Request to Exit (REX) mechanisms,
and door contact sensors will be used and their power requirements. If your
locking hardware requires 24V, either use a Smart Hub with an included 24V
power supply (Core Series Smart Hub or OP-4ESH-24V) or use a separate 24V
supply.
○Note: The 12V Smart Hub (OP-4ESH-12V) supports up to 2A for 12V
locking hardware.
●Whether you’re providing backup batteries for the ACUs. See SELECTING A
BACKUP BATTERY.
●Whether you’re supporting a legacy access control panel. See WIRING TO
LEGACY PANELS.
Version 1.8
© Openpath 2020
Page 3

Installation
NETWORK REQUIREMENTS
An Ethernet connection with DHCP must be used to connect the ACU to the Local
Area Network (LAN). You also need to configure firewall settings to communicate with
the Openpath system. Openpath uses the following outbound ports:
●TCP port 443
●TCP port 80
●UDP port 123
Note: If using an external DNS server, outbound UDP port 53 must also be open.
To support Wi-Fi unlocking from the mobile app, the ACU’s inbound TCP port 443
must be available from within the LAN. Inbound port forwarding on the router, firewall,
or NAT device is not required.
SELECTING A BACKUP BATTERY
While not required, Openpath recommends having a backup battery in case of
power outages. The size of battery depends on your setup and how long you want to
power the system.
Table 1: Power requirements for legacy Smart Hubs (12V)
Controller board
1A
Smart Reader
0.25A
Locking hardware
(while engaged)
0.25A–0.5A
Assuming a 12V power supply, a Smart Hub configured with four Openpath Readers
and locking hardware uses 4 Amps. To keep the system running for 3 hours with all
entries engaged, you need 4A x 3 hours = 12AH, so a 12V 12AH sealed lead acid (SLA)
or gel cell battery.
Version 1.8
© Openpath 2020
Page 4

Table 2: Power requirements for Core Series Smart Hubs (24V)
Access Control Core
0.4A
4-Port Board
0.3A
Smart Reader
0.14A
Locking hardware
(while engaged)
0.12A–0.25A
Assuming a 24V power supply, a Core Series Smart Hub configured with four
Openpath Readers and locking hardware uses about 2 Amps. To keep the system
running for 3 hours with all entries engaged, you need 2A x 3 hours = 6AH, so two 12V
6AH sealed lead acid (SLA) or gel cell batteries wired in series.
MOUNTING INSTRUCTIONS
Openpath Smart Hubs use LifeSafety Power E1 and E2 enclosures. Core Series Smart
Hubs are shipped with power supplies pre-installed, but Openpath boards must be
installed separately.
To mount the enclosure to the wall:
1. (Optional) Remove the enclosure’s cover
2. Locate the top keyhole mounting holes in the back of the enclosure
3. Mark and pre-drill the locations for the keyholes in the mounting surface
4. Partially install two fasteners appropriate for the surface on which the
enclosure is being installed. Leave the heads of the fasteners approximately ¼"
out from the surface. Minimum fastener size should be #10 or larger.
5. Hang the enclosure on the two fasteners and mark the locations of the
remaining mounting holes
6. Remove the enclosure and pre-drill the locations for the remaining mounting
holes
7. Re-hang the enclosure on the top mounting fasteners, install the remaining
fasteners and tighten all fasteners
8. Reinstall the enclosure’s cover, if removed in step 1
Version 1.8
© Openpath 2020
Page 5

INSTALLING CORE SERIES BOARDS IN E1 ENCLOSURE
1. Mount 4-Port in upper corner of enclosure by snapping board standoffs into
holes in back of enclosure
2. Mount Core Board below 4-Port, perpendicular to back of enclosure, by
hooking tabs into holes in back of enclosure
3. Mount Elevator/IO Board (if included) below the Core Board using 6-32 screws
(insert screws from back of enclosure) with USB port on the left
4. Connect Core Board to 4-Port Board with included USB cable. Connect Core
Board to Elevator/IO Board with additional USB cable.
Figure 1: E1 Board Placement
Version 1.8
© Openpath 2020
Page 6

INSTALLING CORE SERIES BOARDS IN E2 ENCLOSURE
1. Mount 8-Port in upper right corner of enclosure by snapping board standoffs
into holes in back of enclosure
2. Mount Core Board with the USB and Ethernet ports facing up as shown in the
diagram, and hook the tabs on into the holes in the enclosure and slide to the
left to lock in place
3. Connect Core Board to 8-Port with included USB cable
Figure 2: E2 Board Placement
Version 1.8
© Openpath 2020
Page 7

INSTALLING CONTROLLER BOARD WITH 24V LOCKING HARDWARE
For a UL Listed System, the standalone Controller Board must be mounted in a
LifeSafety Power E1 enclosure with an FPO75 power supply.
WARNING: Only connect the Controller Board to 12V. Over voltage can damage the
board.
If you purchased the Controller Board separately and are using 24V locking
hardware, we recommend using the LifeSafety Power E1 enclosure, FPO75 power
supply (or FPV4 power supply), B100 secondary power supply, and C4 power control
module.
1. Follow all LifeSafety Power instructions for installing the FPO75 (or FPV4), B100,
and C4 in the enclosure
2. Mount the Controller Board using the provided back plate
3. Connect the B100 secondary supply to the Controller Board
IMPORTANT: Verify that the jumper on the B100 is set to 12V
4. Mount the enclosure according to mounting instructions above
Figure 3: First gen 12/24V Smart Hub configuration
Version 1.8
© Openpath 2020
Page 8

INSTALLING CONTROLLER BOARD WITH 12V LOCKING HARDWARE
If you purchased the Controller Board separately and are using 12V locking hardware,
we recommend using the FPV4-E1 power supply/enclosure.
1. Follow all LifeSafety Power instructions for installing the power supply in the
enclosure
2. Mount the Controller Board using the provided back plate
3. Connect the power supply to the Controller Board
IMPORTANT: Verify that the jumper on the FPV4 is set to 12V
4. Mount the enclosure according to mounting instructions above
Figure 4: First gen 12V Smart Hub ACU configuration
Version 1.8
© Openpath 2020
Page 9

WIRING OPENPATH READERS
Openpath Readers and ACUs communicate via RS-485. The following wire types are
compatible, listed in the order of preference which impacts distance.
●Shielded CAT6A (recommended, additional two pairs can be used for sensors)
●Shielded CAT6
●Shielded RS485 w/22-24AWG (lower gauge, thicker wire is better)
●Shielded CAT5
●Unshielded CAT6
●Unshielded CAT5
●Shielded 22/6
●Unshielded 22/6
Ideally, use one twisted pair for GND and VIN (power) and one twisted pair for +B and
-A (data).
Recommended maximum cable length: 300 ft (91 m) with CAT6 or 500 ft (152 m) if
two wire pairs are used for GND and VIN (power).
For shielded wiring: Connect one side of the drain wire (the shield around the wires)
to the GND terminal on the ACU. Both the shield and the GND wire can share the
same GND terminal. Do not connect the other side of the shield to anything.
For standard reader installation: We recommend that you install a 1-Gang 20 CU
box in order to flush-mount the reader. Alternatively, the reader may also be surface
mounted with the included back plate.
Note: For elevators, all relays and readers must be connected to the same ACU. If you
need more than four access controlled floors or readers, add the Openpath Elevator
Expansion Module. See WIRING THE OPENPATH ELEVATOR BOARD.
WARNING: Always remove power from the Smart Hub and locking hardware when
wiring readers and other devices. Failure to do so can damage the ACU.
Version 1.8
© Openpath 2020
Page 10

WIRING THE CORE SERIES 12/24V 4-DOOR SMART HUB
The Core Series 12/24V 4-Door Smart Hub (4ENT-SYS-1224V) uses an FPV4 to power
the Core and 4-Port Board, a B100 secondary power supply, and a C4 Control Module
to power 12-24V locking hardware.
Figure 6: 4ENT-SYS-1224V Wiring Diagram
Version 1.8
© Openpath 2020
Page 12

ELEVATOR BUTTON WIRING
Interrupt one of the signal wires from each button and run through the C and NC
contacts for the corresponding relay on the Elevator Expansion Board.
GENERAL PURPOSE INPUTS
The general purpose inputs respond to voltages between 3V and 24V. The inputs will
not respond directly to a switch or relay connection to ground. To use these inputs
with a switch or relay, connect one side of the switch to the input and the other side
of the switch to a supply voltage between 3V and 24V. If desired, you can add a 1k
ohm resistor in series with the switch.
Figure 8: Elevator Board Wiring Diagram
Version 1.8
© Openpath 2020
Page 14

WIRING THE CORE SERIES 12/24V 8-DOOR SMART HUB
The Core Series 12/24V 8-Door Smart Hub (8ENT-SYS-1224V) uses an FPV6 to power
the Core and 8-Port Board, a B100 secondary power supply, and a C8 Control Module
to power 12-24V locking hardware.
Figure 9: 8ENT-SYS-1224V Wiring Diagram
Version 1.8
© Openpath 2020
Page 15

WIRING WITH THE 12/24V POWER SUPPLY
The 12/24V Smart Hub ACU (OP-4ESH-24V) uses an FPO75 to power 24V locking
hardware, a B100 secondary power supply to power the ACU Board, and a C4 Control
Module to power 12V locking hardware.
Figure 10: OP-4ESH-24V Wiring Diagram
This example contains:
●An Openpath Reader on READER 1 port (also connected to a Wiegand reader,
optional)
●A door contact sensor on CONTACT 1 port
●A REX on REX 1 port
●A 24V fail secure door strike on RELAY 3
●A 12V fail safe electromagnetic lock on RELAY 1
All of this is configured as one Entry in the Openpath Control Center. We recommend
matching port numbers (READER 1 with CONTACT 1, for example). When setting up
Version 1.8
© Openpath 2020
Page 16

Sites in the Control Center using Quick Start, Entries will default to matching READER 1
with CONTACT 1, RELAY 1, and so on. For more complex Entry setups, you’ll need to
manually add Controls to the Entry. For the example above, you’d need to add an
additional Entry/Exit Hardware Control to the Entry. For more information, refer to the
Openpath User Guide.
WIRING THE REX WITH THE DOOR STRIKE
Except where required by fire or safety codes, for convenience you can wire the REX
in parallel with the Door Strike on the same Relay output. You can wire additional
REXs to the REX inputs on the ACU, as shown in figure 10.
Figure 11: Wiring the REX with the Door Strike
Version 1.8
© Openpath 2020
Page 17

WIRING THE REX WITH THE ELECTROMAGNETIC LOCK
For safety-related applications, you must wire the REX directly to the electromagnetic
lock. You can wire additional REX switches and sensors to the REX inputs on the ACU,
as shown in figure 10.
Figure 12: Wiring the REX with the Mag Lock
Version 1.8
© Openpath 2020
Page 18

WIRING FAIL SAFE AND FAIL SECURE LOCKING HARDWARE
Fail safe and fail secure are ways of configuring locking hardware:
●Fail safe hardware unlocks when power is interrupted
●Fail secure hardware locks when power is interrupted
Figure 13: Wiring Fail Safe and Fail Secure Locking Hardware
Note: Some door strikes can be wired as fail safe and some electromagnetic locks
can be fail secure; always check your third-party locking hardware wiring
instructions and ensure you’re using the right configuration for your requirements.
Version 1.8
© Openpath 2020
Page 19

WIRING THE OPENPATH ELEVATOR BOARD TO A STANDALONE CONTROLLER BOARD
Figure 14: Wiring the Openpath Elevator Board to a Standalone Controller
Version 1.8
© Openpath 2020
Page 20
This manual suits for next models
10
Table of contents
Other Openpath Control System manuals
Popular Control System manuals by other brands
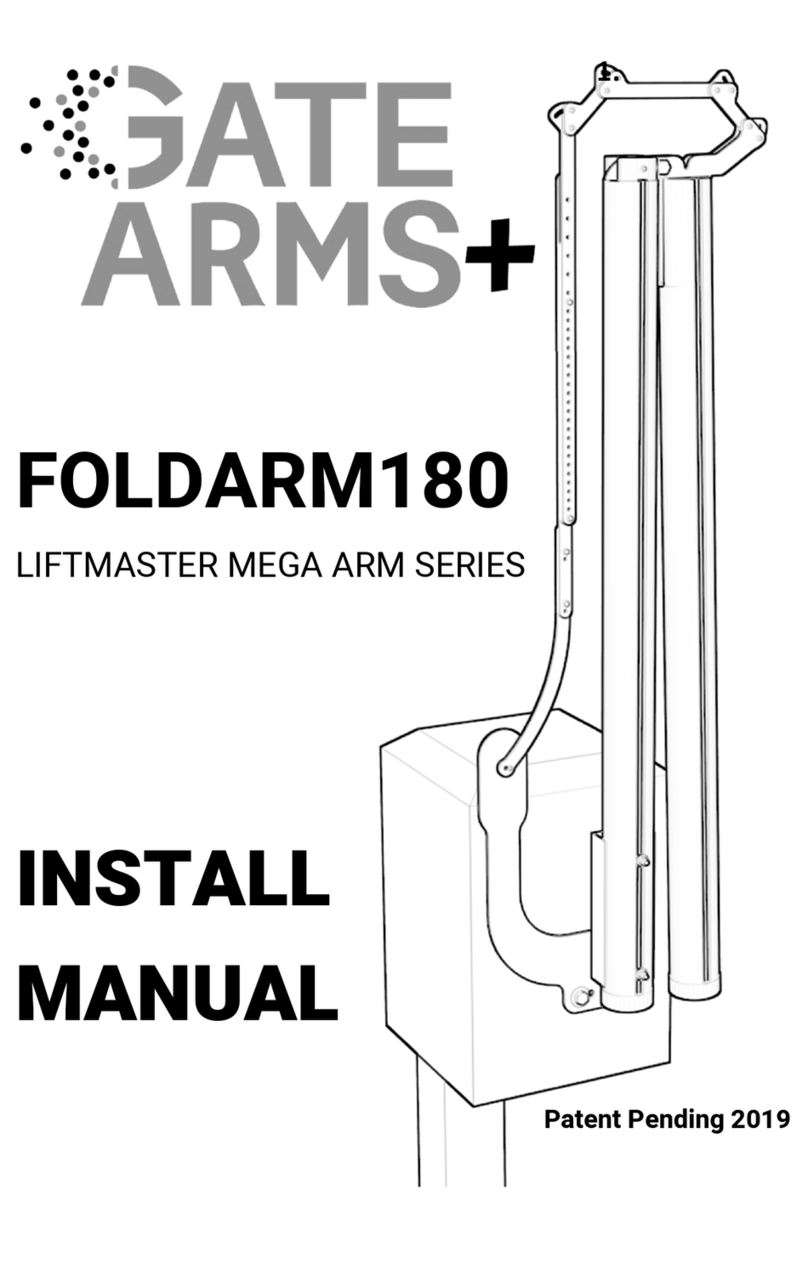
GATE ARMS+
GATE ARMS+ LIFTMASTER MEGA ARM Series installation manual

Intermatic
Intermatic MULTIWAVE PE653RC Programming and usage instructions
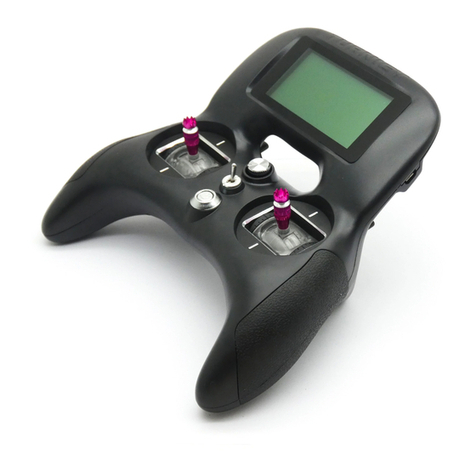
Turnigy
Turnigy Evolution instruction manual
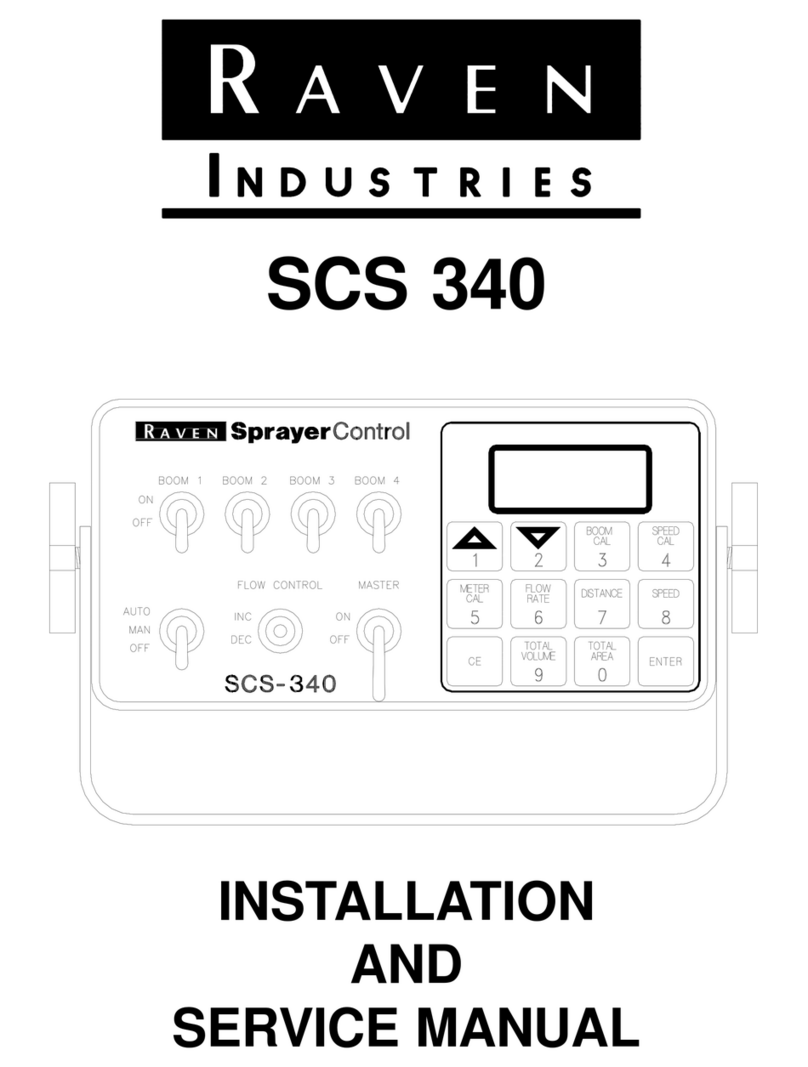
Raven
Raven SCS 340 Installation and service manual
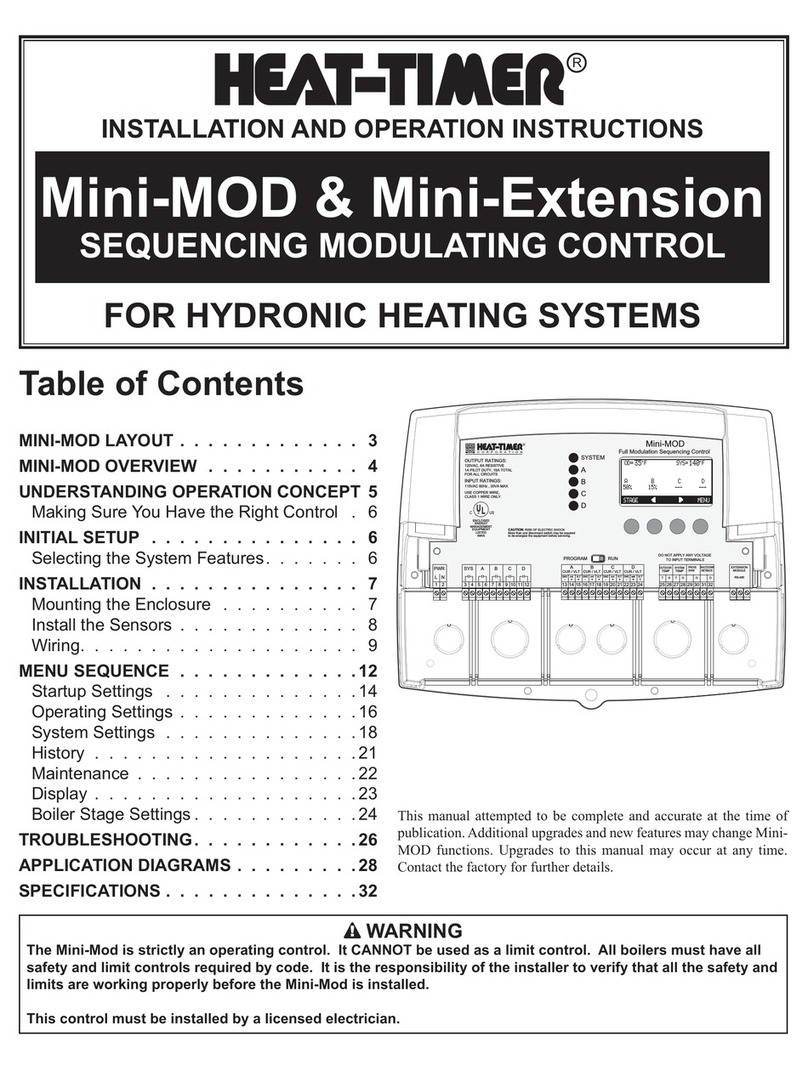
heat-timer
heat-timer Mini-Extension Installation and operations
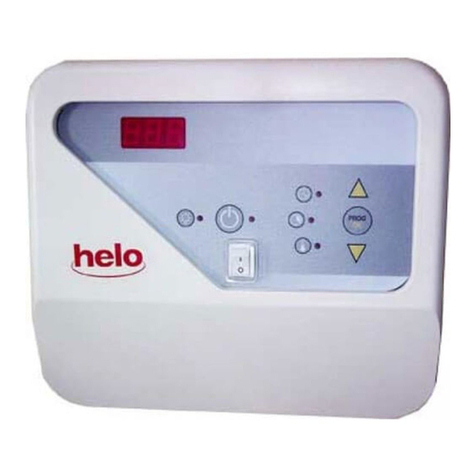
Helo
Helo OT 2 PLE product manual