Ormazabal ekor.rci Instruction manual

LIB
ekor.rci
Integrated control unit
General instructions
IG-158-EN, version 09, 15/11/2016

In view of the constant evolution in standards and design, the characteristics of the elements contained in this manual are subject
to change without prior notice. These characteristics, as well as the availability of components, are subject to confirmation by
Ormazabal.
CAUTION!
When medium-voltage equipment is operating, certain components are live, other parts may be in movement and some may
reach high temperatures. Therefore, the use of this equipment poses electrical, mechanical and thermal risks.
In order to ensure an acceptable level of protection for people and property, and in compliance with applicable environmental
recommendations, Ormazabal designs and manufactures its products according to the principle of integrated safety, based on
the following criteria:
• Elimination of hazards wherever possible.
• Where elimination of hazards is neither technically nor economically feasible, appropriate protection functions are
incorporated in the equipment.
• Communication about remaining risks to facilitate the design of operating procedures which prevent such risks,
training for the personnel in charge of the equipment, and the use of suitable personal protective equipment.
• Use of recyclable materials and establishment of procedures for the disposal of equipment and components so
that once the end of their service lives is reached, they are duly processed in accordance, as far as possible, with the
environmental restrictions established by the competent authorities.
Consequently, the equipment to which the present manual refers complies with the requirements of section 11.2 of Standard
IEC 62271-1. It must therefore only be operated by appropriately qualified and supervised personnel, in accordance with the
requirements of standard EN 50110-1 on the safety of electrical installations and standard EN 50110-2 on activities in or near
electrical installations. Personnel must be fully familiar with the instructions and warnings contained in this manual and in other
recommendations of a more general nature which are applicable to the situation according to current legislation[1].
The above must be carefully observed, as the correct and safe operation of this equipment depends not only on its design but also
on general circumstances which are in general beyond the control and responsibility of the manufacturer. More specifically:
• The equipment must be handled and transported appropriately from the factory to the place of installation.
• All intermediate storage should occur in conditions which do not alter or damage the characteristics of the equipment
or its essential components.
• Service conditions must be compatible with the equipment rating.
• The equipment must be operated strictly in accordance with the instructions given in the manual, and the applicable
operating and safety principles must be clearly understood.
• Maintenance should be performed properly, taking into account the actual service and environmental conditions in
the place of installation.
The manufacturer declines all liability for any significant indirect damages resulting from violation of the guarantee, under any
jurisdiction, including loss of income, stoppages and costs resulting from repair or replacement of parts.
Warranty
The manufacturer guarantees this product against any defect in materials and operation during the contractual period. In the
event that defects are detected, the manufacturer may opt either to repair or replace the equipment. Improper handling of this
equipment and its repair by the user shall constitute a violation of the guarantee.
Registered Trademarks and Copyrights
All registered trademarks cited in this document are the property of their respective owners. The intellectual property of this manual
belongs to Ormazabal.
[1] For example, in Spain the “Regulation on technical conditions and guarantees for safety in high-voltage electrical installations” – Royal Decree
337/2014 is obligatory.

IG-158-EN version 09; 15/11/2016 3
General instructions
ekor.rci
Index
Index
1. General description ...................................................4
1.1. General functional characteristics ............5
1.2. Parts of the ekor.rci unit......................6
1.2.1. Electronic relay ..............................6
1.2.2. Current sensors ..............................7
1.3. Communications and programming
software .....................................8
2. Applications ...............................................................9
2.1. Remote controlled transformer substation....9
2.2. Automatic sectionaliser .....................10
2.3. Automatic transfer . . . . . . . . . . . . . . . . . . . . . . . . . .10
2.4. Detection of a phase with earthing ..........11
2.5. Detection of cable breaks ...................11
2.6. Earthing prevention interlocks ..............11
3. Detection, automation and control functions.......12
3.1. Overcurrent.................................12
3.2. Earth ultrasensitive device...................14
3.3. Presence/absence of voltage ................15
3.4. Fault detection..............................15
3.4.1. Non-directional earth fault indication........16
3.4.2. Directional earth fault indication ............18
3.5. Zero-sequence voltage metering ............19
3.6. Automatic sectionalizer .....................20
3.7. MV monitoring .............................20
3.8. Switch control ..............................21
3.9. Remotecontrol..............................22
4. Metering functions ..................................................23
4.1. Current (I)...................................23
4.2. Voltage (V) .................................23
4.3. Active power (P) ............................23
4.4. Reactive power (Q)..........................23
5. Sensors......................................................................24
5.1. Functional characteristics ...................24
5.2. Vector sum/zero-sequence wiring (current) ...25
5.3. Voltage .....................................26
6. Remote terminal unit (RTU) function.
Medium-voltage monitoring ..................................27
6.1. Medium-voltage monitoring functions ......27
6.2. Hardware characteristics ....................27
6.3. Communication with the dispatching centre.
IEC 60870-5-104 protocol ...................28
6.4. Web server. checking and configuring
parameters .................................28
6.4.1. Access to the web server ....................28
6.4.2. Checking and modifying parameters ........29
6.5. Input and output configuration
of the ekor.rci with remote terminal
unit (RTU) function..........................31
7. Technical characteristics..........................................32
7.1. Rated values ................................32
7.2. Mechanical design ..........................32
7.3. Insulation tests..............................32
7.4. Compatibilidad electromagnética ...........32
7.5. Climatic tests ...............................33
7.6. Mechanical tests ............................33
7.7. Power tests .................................33
7.8. CE conformity . . . . . . . . . . . . . . . . . . . . . . . . . . . . . .33
8. ekor.rci integrated control unit...............................34
8.1. Configurator ................................35
8.2. Functional description ......................36
8.3. Definition of Inputs/outputs.................37
8.4. Cubicle installation..........................40
8.5. Electrical diagram...........................42
8.6. Installation of toroidal-core current
transformers ................................43
8.6.1. Phase toroidal transformers .................43
8.6.2. Zero-sequence toroidal-core current
transformer.................................44
8.7. Checking and maintenance .................44
8.8. Busbar connection applications .............45
9. Setting and handling menus...................................46
9.1. Keypad and alphanumeric display ...........46
9.2. Display .....................................47
9.3. Parameter setting ...........................49
9.4. Fault recognition............................52
9.5. Menu map (quick access)....................53
10. Communications ......................................................55
10.1. Physical medium: RS485 and optical fibre....55
10.2. MODBUS protocol ..........................55
10.2.1. Read/write functions........................56
10.2.2. Password-protected registrer write ..........57
10.2.3. CRC generation . . . . . . . . . . . . . . . . . . . . . . . . . . . . .57
10.2.4. Register map ...............................58
10.3. PROCOME protocol .........................62
10.3.1. Link level ...................................62
10.3.2. Application level ............................64

IG-158-EN version 09; 15/11/2016
4
General description General instructions
ekor.rci
1. General description
The automation needs of power distribution networks,
resulting from more stringent supply quality requirements,
have made the use of equipment which can monitor
medium-voltage and control switches in secondary
distributioncubiclesincreasinglynecessaryandwidespread.
The ekor.rci integrated control unit includes MV
monitoring functions:
• Detection:
- Fault detection (directional and non-directional)
- Voltage presence or absence
- Anomalies
• Metering:
- Current (I)
- Voltage (V)
- Active and reactive power (P and Q)
• Alarms, etc.
• The ekor.rci unit is equipped with outputs which allow
the switch of the cubicle where the unit is installed to be
opened and closed both locally and remotely, as well as
with inputs which detect the status of this switch.
The applications that can be implemented with the
ekor.rci integrated control unit include, among others:
automatic disconnection of fault lines, local control,
remote controlled operations, automations, interlocks,
etc., related to present and future automation needs of
transformer and switching substations.
Figure 1.1. Integrated control units: ekor.sys family
It can be used in feeder functions of Ormazabal’s
cgmcosmos and cgm.3 systems.
This ekor.rci integrated control unit has been designed
to meet the requirements of the following standards and
guidelines:
IEC 60255, IEC 61000, IEC 62271-200, IEC 60068, IEC 60044,
IEC 61958
Designed to be integrated in a cubicle, the ekor.rci
integrated control unit also provides the following
advantages over conventional systems:
1. Compact remote terminal unit (RTU) integrated into
cubicle, minimising the need to install control boxes on
the cubicles.
2. Reduction in handling of interconnections when
installing the cubicle. The only connection required is
limited to MV cables.
3. V, P and Q metering without the need for Voltage
Transformers.
4. Voltage and current sensors are installed in the cubicle
cable bushing.
5. Avoidanceofwiringandinstallationerrors;minimisation
of commissioning time.
6. The entire unit is factory installed, adjusted and
checked; each piece of equipment (cubicle + control +
sensors) also undergoes a comprehensive check before
being installed. The nal unit tests are carried out once
the unit is incorporated in the cubicle before delivery.
7. Display of a broad range of overcurrents with the same
model (5 A to 1200 A for phases; 0.5 A to 480 A for
earth). Directional fault detection from values of 0.5 A
upwards.

IG-158-EN version 09; 15/11/2016 5
General instructions
ekor.rci
General description
1.1. General functional characteristics
All relays of the ekor.rci integrated control unit include
a microprocessor for processing the signals from the
metering sensors. They process the current and voltage
measurements without requiring auxiliary converters, thus
eliminating the inuence of transient phenomena. They
also calculate the necessary magnitudes for the detection
functions, such as overcurrent, presence and absence of
voltage, directional or non-directional fault, etc. In addition,
theecient currentvalues,which providetheinstantaneous
value of these installation parameters, are determined.
Theyareequipped with ascreenandkeypadforlocal display,
setup and operation of the unit, as well as communication
ports to handle these functions from a computer, whether
locally or remotely. A user-friendly design has been
employed, so that the use of the various menus is intuitive.
The current is measured by means of several current sensors
with a high transformation ratio, making it possible for the
same equipment to detect a wide range of current levels.
Voltage is detected by capturing the signal via a capacitor
divider built into the cubicle bushing.
The unit is equipped with an event log which stores the
last two faults detected by ekor.rci. In addition, the total
number of detected faults is saved, as well as the various
setting parameters.
The local interface uses menus to provide the instantaneous
values of the current metering for each phase and zero-
sequence current, as well as the setting parameters of
the fault detection functions, the unit that detected the
fault, voltage detection parameters, etc. These can also be
accessed through the communication ports.
From a maintenance perspective, the unit has a series of
features that reduce the time and the possibility of errors
in the test and service restoration tasks. Among the main
characteristics, the most prominent are the toroidal-core
current transformers installed in the cubicle bushing, their
built-in test contacts for checking purposes and a terminal
block for physically checking the relay inputs and outputs.
Therefore, the unit allows local testing means in addition to
the communication ports.
Figure 1.2. ekor.rci integrated control unit frontal view

IG-158-EN version 09; 15/11/2016
6
General description General instructions
ekor.rci
1.2. Parts of the ekor.rci unit
The ekor.rci integrated control unit contains the following
parts: electronic relay, voltage and current sensors, terminal
block and wiring.
1Terminal block
3ekor.rci electronic relay
4Voltage and current sensors
5Connection cables
Figure 1.3. Example of installation of an ekor.rci unit in cgmcosmos-l
2Terminal block (inner)
3ekor.rci electronic relay
4Voltage and current sensors
5Connection cables
Figure 1.4. Example of installation of an ekor.rci unit in cgm.3-l
1.2.1. Electronic relay
The electronic relay has keys and a display to set and view
the detection, measurement and control parameters.
Depending on the model, it also allows the switch to
be opened and closed from the front keypad. The relay
includes a seal on the <<SET>> key to ensure that once the
settings have been made they cannot be changed unless
the seal is broken.
Detected faults are registered on the display with the
following parameters: value of the fault, fault direction,
duration of fault or detection time according to parameter
T1, voltage checking time and time and date of the event.
Depending on the model. Consult Ormazabal.
The ‘On’ LED is activated when the equipment receives
power from an external source. In this situation, the unit is
operational to perform the detection, metering and control
functions.
The voltage and current input signals are conditioned
internally by small transformers that isolate the electronic
circuits from the rest of the installation.

IG-158-EN version 09; 15/11/2016 7
General instructions
ekor.rci
General description
The communication ports on the electronic equipment are
RS232 on the front for local conguration and RS485 on
the rear for remote control. The standard communication
protocols for all models are MODBUS and PROCOME.
1‘On’LED indicator
2Display of measurements and settings
3SET key
4Scroll keys
5RS232 front communication port
6Scroll keys and keys to open/close the switch
Figure 1.5. ekor.rci relay elements
1.2.2. Current sensors
The current sensors are toroidal-core transformers with a
high transformation ratio. Their range of action is the same
as the switchgear where they are installed. They are always
factory-installed in the cubicle bushings, which signicantly
simplies the on-site assembly and connection. In this
way, once the MV cables are connected to the cubicle, the
detection unit is operational.There are no sensor installation
errors, due to earthing grids, polarities, etc. since they are
directly factory installed and tested. See section 8.6
The current sensors have an integrated protection
against the opening of secondary circuits, which prevents
overvoltage.
1Current sensors
2Pasatapas
Figure 1.6. Location of the current sensors

IG-158-EN version 09; 15/11/2016
8
General description General instructions
ekor.rci
1.3. Communications and programming software
The ekor.rci integrated control unit has two serial
communication ports.The standard RS232 front port is used
to set the parameters with the ekor.soft program[2]. At the
rear, there is an RS485 port which is used for remote control.
This remote control connection can use braided wiring and
optical bre, if desired
The standard communication protocols implemented in
all equipment are MODBUS in RTU remote terminal unit
transmission mode (binary) and PROCOME, although other
specic protocols can be implemented depending on the
application.
1ekor.ccp
2ekor.bus
3ekor.rci
4ekor.rci
5ekor.rpt
6ekor.rpg
Figure 1.7. Intercommunicated units of the ekor.sys family
The ekor.soft setup program has four main operating
modes:
1. Display: indicates the unit status, including electrical
measurements, current settings, date and time.
2. User settings: allows to change the earth fault indicator
and the sectionaliser parameters.
3. Event log: display the parameters of the last and
penultimate detected fault, as well as the total number
of faults detected by the corresponding integrated
control unit.
4. Test mode: allows to generate information on the unit
inputs/outputs, without direct electrical interaction
with the switchgear adjoining terminal block, so that it
can be sent to the dispatching centre without cutting
o the power.
Minimum system requirements for installing and using the
ekor.soft software:
1. Processor: Pentium II
2. RAM: 32 Mb
3. Operating System: MS WINDOWS
4. CD-ROM/DVD
5. RS232 serial port
Figure 1.8. ekor.soft screens
[2] For more information about the ekor.soft program, consult Ormazabal’s IG-155 document.

IG-158-EN version 09; 15/11/2016 9
General instructions
ekor.rci
Applications
2. Applications
2.1. Remote controlled transformer substation
The ekor.rci integrated control unit makes it possible to
handle remote control applications of the transformer
and switching substations, by implementing the control
and monitoring of each switch through the ekor.rci units
associated with each function
1Power supply
2Communications
3Remote control cabinet + ekor.ccp
Figure 2.1. Remote controlled switching substation
The use of integrated control units and a remote control
terminal allows the user to display and operate each
functional unit remotely.
Figure 2.2. Viewing the stations remotely

IG-158-EN version 09; 15/11/2016
10
Applications General instructions
ekor.rci
2.2. Automatic sectionaliser
The automatic sectionaliser makes it possible to disconnect
the fault section of a line. The operation of the sectionaliser
is similar to that of the fault detector, supplemented by
automatic opening of the switch once the main circuit
breaker has cleared the fault.
This opening can be done in any of the reclosings that the
main recloser can perform. Therefore, a line fault implies the
tripping of the protection of the transformer or switching
substation and then the rst reclosure attempt. If this is
not successful, the main switch will be tripped again. The
sectionaliser detects this and checks that there is no voltage
by opening the line for the section where it is installed. The
second reclosing manages to feed the line again without
the section where the fault is located.
This operation can be scheduled to be performed after the
second reclosing. Therefore, the second reclosing will not
be successful and the main switch will trip again. When this
occurs, the automatic opening of the corresponding switch
will be ordered.
Figure 2.3. Automatic sectionaliser
2.3. Automatic transfer
The automatic transfer of lines minimises power outages in
loads fed by transformer or switching substations with more
than one incoming line, thereby improving the continuity
of service.
Under normal conditions with voltage present on two
possible incoming lines, the switch selected as preferred
will remain closed and the reserve one will be opened. A
voltage drop in the preferred line will cause the switch of
this line to open and the reserve switch to close afterwards.
Once normality has been re-established in the preferred
line, the inverse cycle is performed, returning the system to
its initial status.
Figure 2.4. Automatic transfer

IG-158-EN version 09; 15/11/2016 11
General instructions
ekor.rci
Applications
2.4. Detection of a phase with earthing
In networks with either a solid or impedant neutral earth
connection, programmed logic is used to detect this type of
fault. This logic analyses the presence of both voltage and
current in the installation. It therefore avoids faults being
indicated on lines which have not lost voltage (main circuit
breaker trip).
In networks with isolated or resonant earth neutral, the
fault currents are low. In the event of a fault in a system of
this type, the fault current may not reach the set threshold
for overcurrent protection, and therefore this fault may
not be detected. In this type of network, directional
fault indication is used to detect phases with earthing.
Directional fault indication uses both current and voltage
to indicate the fault, thus allow the fault current values to
be set to low values (close to the capacitive return current
values), ensuring the correct type of fault indication for
fault lines, as opposed to undamaged adjacent lines with
capacitive input.
In the case of faults with very high impedance (faults in
rocky or desert areas, etc.), the fault currents have very low
values and may even be below the sensitivity range of the
fault indication overcurrent units. To detect the phase with
earthing in this type of case, zero-sequence overvoltage
detection is used.
Figure 2.5. Detection of a phase with earthing
2.5. Detection of cable breaks
Where cable breaks occur without either earth or
phase-to-phase contact, the unbalance which may be
generated is very small (the overcurrent generated is zero).
In these conditions, zero-sequence overvoltage detection is
used to detect the broken cable state.
2.6. Earthing prevention interlocks
The earthing prevention interlock impedes earthing of the
cubicle switch when voltage is detected on the line.
Figure 2.6. Earthing prevention interlocks

IG-158-EN version 09; 15/11/2016
12
Detection, automation and control functions General instructions
ekor.rci
3. Detection, automation and control functions
3.1. Overcurrent
The relay has an overcurrent unit for each phase and
another for earth. The overcurrent functions performed by
the relay are the following:
1. Phase-to-phase fault detection
2. Non-directional phase-to-earth fault detection
3. Directional phase-to-earth fault detection
The detection curves implemented are dened time for
phase-to-phase fault detection, referred to as DT in the relay
settings. Phase-to-earth fault detection is performed via
dened time, extremely inverse, very inverse and normally
inverse curves (DT, EI, VI and NI, respectively) for the ekor.rci
models with earthing protection.
The parameters of the dened time curve for setting the
phase units have the following meanings:
t(s) ≡Theoretical detection time for a phase-to-phase
fault that evolves with a constant current value I
I≡ Actual current flowing through the phase with the
largest amplitude
In≡Rated setting current. From 5 A to 1200 A, in steps
of 1 A
T> ≡Phase timing. From 0.05 s to 0.1 s, in steps of 0.01s;
and from 0.1 s to 2.5 s, in steps of 0.1 s
• Pick-up current value of DT curve = 1.0 x In
In the case of earth curve settings, the parameters are similar
to the phase settings. Each of them is described below.
to(s) ≡Theoretical detection time for a phase-to-earth
fault that evolves with a constant current value Io
Io ≡Actual current owing to earth
Io> ≡Setting earth current. From 0.5 A to 480 A, in steps
of 0.1A
To> ≡Earth timing. From 0.05 s to 0.1 s, in 0.01 s steps
and from 0.1 s to 2.5 s, in 0.1 s steps
• Pick-up current value of DT curve = 1.0 x lo> (1.1 x lo> for
EI, VI, NI curves)
In addition, depending on the model, ekor.rci can detect
directional phase-to-earth faults, for which it combines
operation of the overcurrent function, timing the curve
congured earlier, with the polarization amplitude available
to determine the fault direction

IG-158-EN version 09; 15/11/2016 13
General instructions
ekor.rci
Detection, automation and control functions
Phase time delay:
Earth time delay:
Figure 3.1. Denite time curve
Earth time delay:
Figure 3.2. Normally inverse curve

IG-158-EN version 09; 15/11/2016
14
Detection, automation and control functions General instructions
ekor.rci
Earth time delay:
Figure 3.3. Very inverse curve
Earth time delay:
Figure 3.4. Extremely inverse curve
3.2. Earth ultrasensitive device
This functionality is available in both directional and non-
directional ekor.rci and corresponds to a particular case
of overcurrent detection for phase-to-earth faults. It is
primarily used in networks with isolated neutral, resonant
earthed neutral or on highly resistive soils, where the phase-
to-earth fault current has a very small value.
The current owing to earth is detected using a toroidal-
core current transformer which covers the three phases.
In this way, the metering is independent from the phase
current, thus avoiding errors in the phase metering sensors.
In general, this type of detection must be used when the
phase-to-earth fault current is less than 10 % of the rated
phase current (e.g. for a rated phase current of 400 A with
earth faults below 40 A).
1Voltage and current sensors
20-sequence toroidal transformer
Figure 3.5. Sensors

IG-158-EN version 09; 15/11/2016 15
General instructions
ekor.rci
Detection, automation and control functions
3.3. Presence/absence of voltage
This function allows the detection of voltage presence or
absence in those lines where the ekor.rci is installed. The
metering is carried out by using the capacitive coupling
of the cubicle bushings. Thus, conventional voltage
transformer systems are not required. Furthermore, it has
the advantage of detecting voltage in the line itself without
using LV from auxiliary services, which could cause an error
in the display
The ekor.rci integrated control unit individually checks
for the presence or absence of voltage in each of the line
phases. For this purpose, there are three input signals, one
per phase.
The ekor.rci integrated control unit detects the presence of
voltage in each of the phases, when the voltage metered
exceeds 70 % of the voltage dened as the‘line voltage (Ur)’
for longer than the ‘voltage time delay (Tu)’. Likewise, the
unit detects the absence of voltage when the voltage drops
below 70 % of the line voltage for more than Tu seconds.
The ‘line voltage’ parameter is the rated phase-to-phase
operating voltage of the MV line.
Ur≡Line Voltage. From 3 kV to 36 kV, in steps of 0.1 kV
TU≡Voltage time delay. From 0,05 s to 0.1 s, in steps of
0.01 s. From 0.1 s to 2.5 s, in steps of 0.1 s
Figure 3.6. Voltage presence detection
3.4. Fault detection
In distribution lines, there are frequently phase-to-phase
and phase-to-earth faults which are cleared by the main
circuit breaker in the substation. When this occurs, the fault
section must be delimited as quickly as possible in order to
restore service to the rest of the customers. The purpose of
the fault detection function performed by the ekor.rci unit
is to identify the fault section.
Devices that include fault detection have two very obvious
eects on network operation. The rst is to immediately
identify the fault section, so that service can be restored to
the‘undamaged’sections as soon as possible. The second is
the reduction of the number of operations on the network
components since it is not necessary to disconnect sections
in order to locate the fault. This decrease in the number
of operations results in a reduction of the equipment
maintenance and an extension of its service life.
The ekor.rci integrated control unit includes detection of
non-directional phase-to-phase faults and may include,
depending on the model, detection of directional
phase-to-earth faults, recommended in isolated or
compensated neutral network topologies, or even
detection of non-directional phase-to-earth faults (use of
this function is aimed at solid and impedant earth neutral
networks).

IG-158-EN version 09; 15/11/2016
16
Detection, automation and control functions General instructions
ekor.rci
3.4.1. Non-directional earth fault indication
The non-directional earth fault detection function is used
for detecting phase-to-phase faults, as well as detection of
phase-to-earth faults in solid and impedant earth neutral
networks.
This function identies permanent faults by combining
the overcurrent functions with a voltage detection logic.
Therefore, once the overcurrent fault has occurred, the
unit only indicates that it has detected a fault if there is
a loss of voltage in the line and fault current, by tripping
the main circuit breaker. Thanks to this function, which
is implemented using a programmed logic, the wrong
indications resulting from the eects of capacitive currents
are eliminated.
The fault detection is signalled locally through the ekor.rci
display, or remotely through the communications or
through one of the available outputs, by sending this signal
to a remote control terminal.
The operating sequence shares the same parameters as
in the case of directional earth fault detection (explained
later in this section). The sequence starts with the fault
detection, and the verication of voltage absence in the
line after T1 seconds (if T1 is dierent to 0.0). If the lack of
voltage persists, a fault is reportedT2 seconds after the fault
is detected. If the line voltage is restored, the fault display
disappears T3 seconds later. This display also disappears
T4seconds after the fault display, or by detecting the reset
of the fault display either locally or remotely.
If the T1 parameter is set with value 0.0, the fault is displayed
when the adjusted curve time is completed. Therefore, the
fault is displayed without waiting for the disappearance
of the overcurrent by tripping the main circuit breaker.
The automatic sectionaliser does not operate under these
conditions.
ALine current
BLine voltage
CFault indication
1Fault
2Main circuit breaker trip Fault detection
3Verication of absence of voltage
4Earth fault indication
5Voltage reset
6Fault indication reset
Figure 3.7. Non-directional earth fault detection operating sequence
Range of settings
T1
0–The relay times the time curve and displays the fault
(it does not monitor voltage)–the sectionaliser does not
operate under these conditions
0.1 s to 999.9 s, steps of 0.1 s–voltage checking time
T2 0–Without indication delay
1 s to 9999 s steps of 1 s–delay in the indication
T3 0–Without voltage–dependent reset
1 s to 9999 s steps of 1 s–wait for reset by voltage restoration
T4* 0–Display without memory (0.1 s)
1 s to 9999 s steps of 1 s–output contact memory
* The display is permanent, and all the data related to the fault is stored in
the equipment memory.
Table 3.1. Non-directional earth fault range of settings

IG-158-EN version 09; 15/11/2016 17
General instructions
ekor.rci
Detection, automation and control functions
This capability may be implemented as shown in the
following gure. The main circuit breaker protection will
trip for a single-phase-to-earth fault in the rst line. In
addition, the ekor.rci fault detection functions installed in
the dierent transformer or switching substations of this
line will generate a fault display, thus determining that the
fault is in this line.
For the same fault, the capacitive return current in parallel
lines can be higher than the rated magnitude set in ekor.rci,
although there is not really any fault in its line. In order to
avoid that, due to overcurrent detection, ekor.rci provides
an incorrect fault detection, the presence of voltage is
veried once the fault current has been detected. Given that
the main circuit breaker protection of the undamaged line
has not tripped, the voltage is not zero and, therefore, the
ekor.rci control unit for this fault-free line will not generate
a fault display.
Figure 3.8. Single-phase-to-earth fault in one line
Moreover, in the case of networks with high capacitive
currents and branches originating from the same substation
line, a curve must be used for the earth unit similar to that of
the substation. This is due to the fact that a fault in a branch
trips the main circuit breaker and all the branches in the line
lose voltage. Thus, the capacitive currents cause the fault
indicators to operate incorrectly even when verifying the
voltage.
Figure 3.9. Fault in a branch
The fault display can be reset in three dierent ways:
1. Reset due to voltage restoration: the fault display is
reset T3 seconds after the voltage restoration.
2. Reset due to time: the fault display is reset T4 seconds
after the fault display.
3. By pressing the ESC-L/T key, depending on the model,
o SET on the front of the relay.
In addition to the above mentioned and as an option, the
reset can be done by:
4. External reset: The equipment has one input to
connect a potential-free contact and to reset the fault
display.
The reset occurs when the volt-free contact changes
to the closed position for at least 20 ms. The main use of
this function is for resetting the fault display remotely.
Alternatively, the fault display can be reset through
communications or locally.

IG-158-EN version 09; 15/11/2016
18
Detection, automation and control functions General instructions
ekor.rci
3.4.2. Directional earth fault indication
This type of earth fault detection is used in topologies where
the fault current is capacitive in origin, in other words, it
comes from undamaged lines electrically interconnected
with the fault line, and as a result these currents have very
low values. On the other hand, the overvoltages which
occur in fault conditions may reach voltage levels between
phase and earth.
For a single-phase earth fault in an isolated neutral network
the fault current is higher the nearer it is to the faulty point,
which may mean that, depending on the setting, the
main circuit breaker protection does not trip. The use of
directional fault indication is therefore essential in this type
of network, as it continuously checks the fault direction.
To determine the direction of a forward fault (identied as
“Co” on the relay) or reverse fault (identied as “Bo”) with
respect to the point where the current is being measured,
the current phase-dierence must be determined with
respect to the selected polarization amplitude, which is
zero-sequence voltage in the case of ekor.rci.
Several main factors are involved in dening the fault
direction, including:
• Operating amplitude: Io.
• Polarization amplitude: Uh. kV.
• Characteristic angle (MTA): this parameter constitutes
the maximum torque angle in which the voltages and
currents are in phase. This is - 90° in the case of Isolated
Neutral networks.
• Operation limit or dead angle zone: this corresponds to
the angle around the transition between the operation
zone (Co, forward fault) and non-operation zone (Bo,
reverse fault), which is ± 15°.
• Threshold Vhminimum: to allow starting of the neutral
directional unit, a minimum threshold Vh must be
exceeded. The fault is signalled whenever the fault is
within the working area delimited by the minimum
zero-sequence current values (I0) and minimum zero-
sequence voltage values (Uh.min). We recommend
keeping minimum setting values of I0of 0.5 A whenever
there is an earth toroidal-core current transformer and
at least 2 A as a vector sum.
Figure 3.10. Directional earth fault detection
To enable the directional function, it must be activated by
setting DIR to “Yes”. Otherwise the selected detection will
correspond to non-directional fault detection, including
when the integrated control unit is directional.
The fault detection is indicated locally on the ekor.rci display
or remotely through the communications or through one
of the available outputs, by sending this signal to a remote
control terminal.

IG-158-EN version 09; 15/11/2016 19
General instructions
ekor.rci
Detection, automation and control functions
The directional earth fault operating sequence is dened
by means of four time parameters also used by the non-
directional earth fault indication:
• T1 [s]: When the detection curve has been timed
according to the programmed setting and a polarization
amplitude higher than Uh.min is present, the programmed
time T1 [s] elapses and then the absence of voltage in
the network is tested. The fault is indicated when there
is no voltage in the network. If voltage is present in any
of the phases, no fault is indicated.
• T2 [s]: For this application it must always equal 0, so that
if the dened fault conditions are met, The fault mode is
indicated immediately.
• T3 [s]: Once the line voltage has been restored this
parameter allows us to select how quickly the fault
indication should be eliminated.
• T4 [s]: The fault indication can also be eliminated after a
dened time by means of this parameter.
The gure below shows directional earth fault indication for
an isolated neutral network. The fault is signalled in each
of the functional units, dierentiating between those which
see the fault in forward (Co) direction and those which see
the fault in reverse (Bo) direction. This signalling system is
used to locate, simply and easily, the area where the fault
occurred.
Figure 3.11. Single-phase earth fault in an isolated neutral network
3.5. Zero-sequence voltage metering
The ekor.rci unit calculates the zero-sequence voltage
value by measuring the single voltages of the network.
Uh[kV]=3V0=VR+VS+VT
This amplitude is used for the directional fault indication to
determine the fault direction.
The settings are:
• Uh [kV]: Zero-sequence voltage detection threshold.
From 1.00 kV to 25.00 kV in steps of 0.1 kV.
• Tu[s]: Voltage presence timing. From 0.05 s to 0.1 s, in
steps of 0.01 s. From 0.1 s to 2.5 s, in steps of 0.1 s.
Figure 3.12. Zero-seguence voltage vectors

IG-158-EN version 09; 15/11/2016
20
Detection, automation and control functions General instructions
ekor.rci
3.6. Automatic sectionalizer
The sectionaliser allows to disconnect the fault section
of a line automatically. The operation of the sectionaliser
complements that of the the fault detector, ordering the
automatic opening of the switch for a specic number of
detected faults (according to the setting) and once the
main circuit breaker has cleared the fault (with voltage
and current absence). Due to the ratio between the fault
detection and the sectionaliser, the latest does not operate
if the voltage absence is not checked to indicate the fault
(if the fault indicator is set with T1 = 0.0).
This opening can be done in any of the reclosings that the
main recloser can perform. Therefore, a line fault implies the
tripping of the protection in the transformer or switching
substation, as well as the fault display of all the integrated
control units of that line, followed by a rst reclosing. If
this rst reclosing is not successful, the main protection
will trip again and the ekor.rci units will display the fault.
If the sectionaliser is set to open after the second detected
fault, the sectionaliser automation will check that there is
no voltage (while the main circuit breaker times the second
reclosing), by opening the section of the line where it is
installed. The second reclosing manages to feed the line
again without the section where the fault is located.
This operation can be scheduled to be performed after
the second reclosing (during the 3rd reclosing and later).
Therefore, the second reclosing will not be successful
and the main switch will trip again. When this occurs, the
automatic opening of the corresponding switch will be
ordered (with voltage and current absence).
The following settings are dened in the ekor.rci as the
parameters for this function:
Range of settings
SECC Non-directional
units
ON Automatic sectionaliser on
OFF Automatic sectionaliser o
Directional units OFF Automatic sectionaliser o
Cabl Automatic sectionaliser on for
faults in forward direction (C0) or with
no direction
Barr Automatic sectionaliser on for
faults in reverse direction (B0)
NDEF 1 to 9999 – number of faults to count to activate the
automatic sectionalisr
Tb 0.1 to 999.9 – sectionaliser automation blocking time
Table 3.2. Automatic sectionalizer range of settings
3.7. MV monitoring
The ekor.rci unit with remote terminal unit (RTU) function
can monitor medium voltage if tted with the ethernet
module.
These functions are described in detail in section 5.
Table of contents
Popular Control Unit manuals by other brands
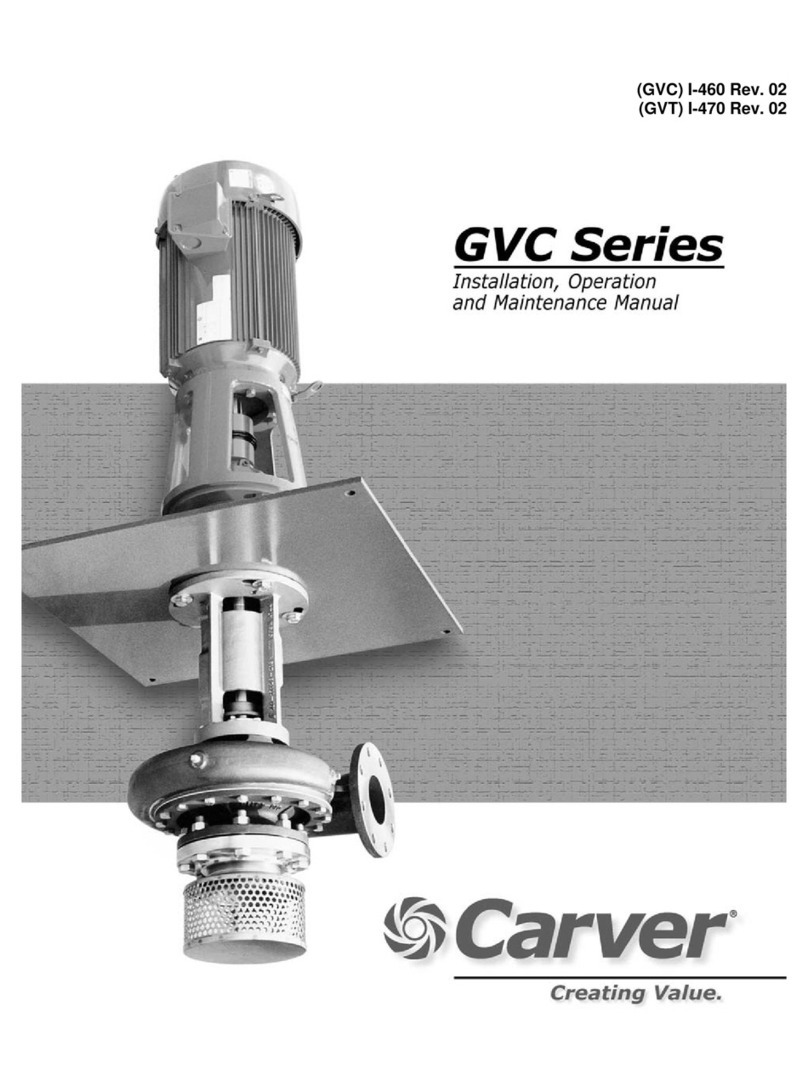
Carver
Carver GVC Series Installation, operation and maintenance manual
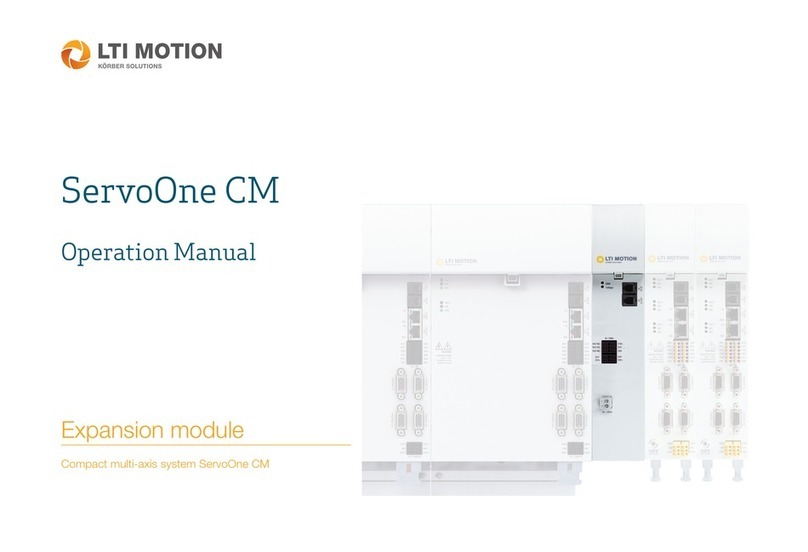
Korber Solutions
Korber Solutions LTI MOTION ServoOne CM Operation manual
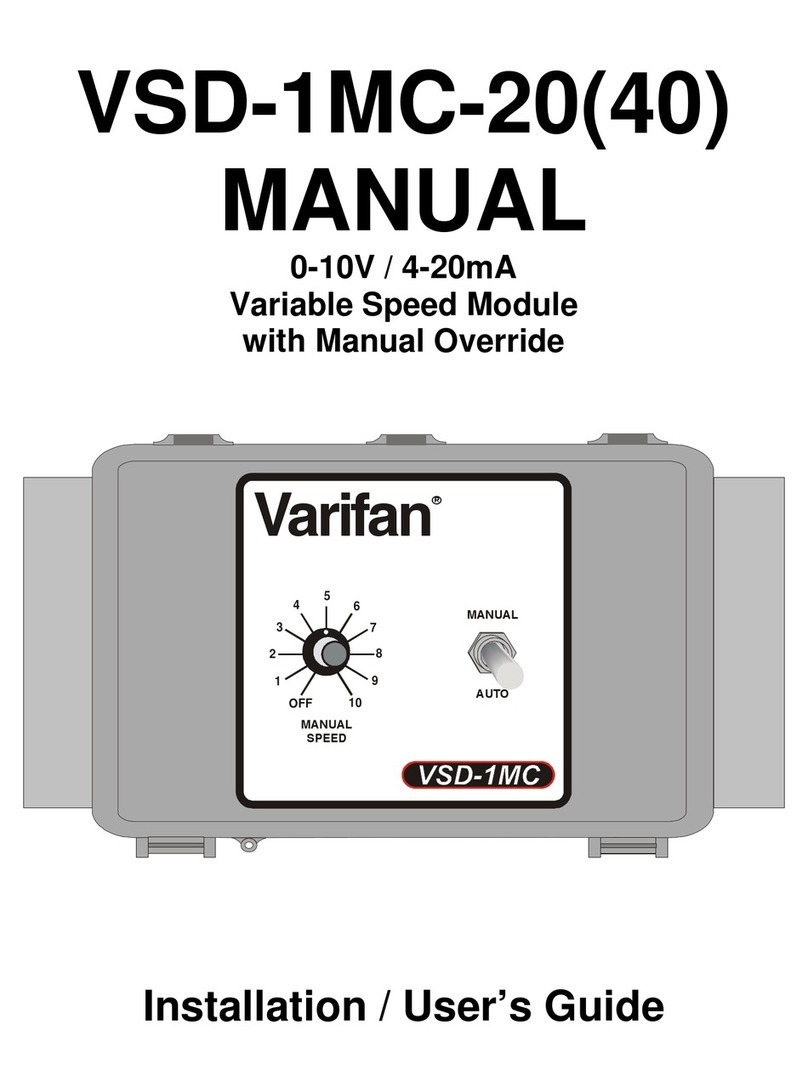
Varifan
Varifan VSD-1MC-20 manual
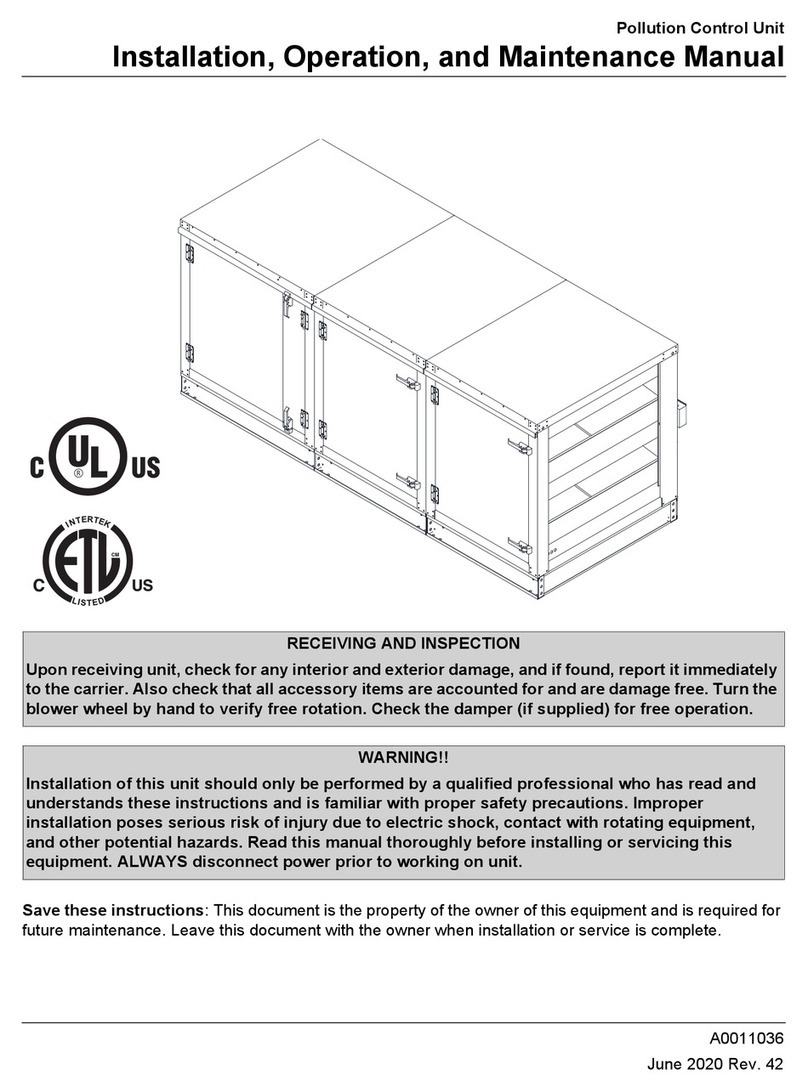
ThermoTek
ThermoTek PCU Installation, operation and maintenance manual
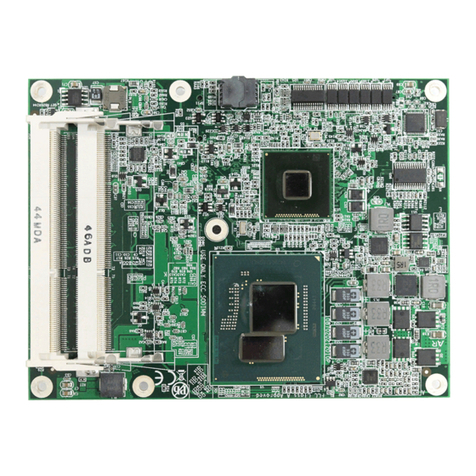
Arbor Technology
Arbor Technology EmETXe-i87M2 user manual
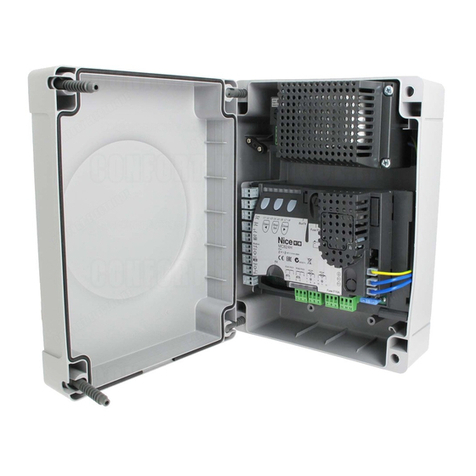
Nice
Nice Moon MC824H instructions