PAW FC4.13 User manual

Thank you for buying this product.
Please read this manual carefully to get the best performance from this unit.
Please keep this manual carefully.
Manual
en
Mounting
Connection
Operation
Troubleshooting
Application examples
Manual for the
specialised craftsman
*11208752*
11208752
FC4.13 as heat transfer controller

en
2
©20160725_11210368_11208752_PAW_FWR_FC4_13_SUS.monen.indd
Safety advice
Please pay attention to the following safety advice in order to avoid danger and
damage to people and property.
Instructions
Attention must be paid to the valid local standards, regulations and directives!
Information about the product
Proper usage
The controller is designed for use in the Friwa DHW exchange module in compli-
ance with the technical data specied in this manual.
Improper use excludes all liability claims.
CE-Declaration of conformity
The product complies with the relevant directives and is therefore la-
belled with the CE mark.
Note:
Strong electromagnetic elds can impair the function of the controller.
ÎMake sure the controller as well as the system are not exposed to
strong electromagnetic elds.
Subject to technical change. Errors excepted.
Target group
These instructions are exclusively addressed to authorised skilled personnel.
Only qualied electricians should carry out electrical works.
Initial installation must be effected by the system owner or qualied personnel
named by the system owner.
Description of symbols
WARNING! Warnings are indicated with a warning triangle!
ÎThey contain information on how to avoid the danger
described.
Signal words describe the danger that may occur, when it is not avoided.
• WARNING means that injury, possibly ltife-threatening injury, can occur.
• ATTENTION means that damage to the appliance can occur.
Note:
Notes are indicated with an information symbol.
ÎArrows indicate instruction steps that should be carried out.
Disposal
• Dispose of the packaging in an environmentally sound manner.
• Dispose of old appliances in an environmentally sound manner. Upon request we
will take back your old appliances bought from us and guarantee an environmen-
tally sound disposal of the devices.

en
3
Contents
1 Heat transfer controller installation ...................................................5
1.1 Mounting .................................................................................................................5
1.2 Electrical connection ............................................................................................5
2 Heat transfer controller commissioning.............................................6
2.1 Factory menu .........................................................................................................6
2.2 Running the commissioning menu.....................................................................6
2.3 Operation and function .................................................................................... 10
2.4 Commissioning menu........................................................................................ 14
3 Heat transfer controller adjustments ...............................................15
3.1 Main menu ........................................................................................................... 15
3.2 Status menu ......................................................................................................... 15
3.3 Store loading ....................................................................................................... 18
3.4 Circulation ........................................................................................................... 21
3.5 Stratied return.................................................................................................. 24
3.6 Basic settings ....................................................................................................... 25
3.7 SD card................................................................................................................. 25
3.8 Manual mode....................................................................................................... 26
3.9 User code ............................................................................................................ 27
3.10 Inputs .................................................................................................................... 27
3.11 Parallel relay......................................................................................................... 27
4 Heat transfer controller data communication .................................28
4.1 Data communication / Bus ................................................................................ 28
4.2 SD memory card slot........................................................................................ 28
5 Troubleshooting ...................................................................................29
6 Index .....................................................................................................33

4
en
Overview
170
198
43
Note:
The SD card is not included with the controller.
Technical data
Inputs: 10 inputs for Pt1000 temperature sensors, 1 V40 impulse input, input for 1
analogue Grundfos Direct Sensor™ or 1 FlowSonic ultrasonic sensor (depending
on the controller version), 1 input for a CS10 irradiation sensor, 1 FlowRotor input
Outputs:
3 semiconductor relays, 1 potential-free relay,4 PWM outputs (switchable to 0-10V)
Switching capacity:
1 (1) A 240 V~ (semiconductor relay)
4 (1) A 24 V⎓/ 240 V~ (potential-free relay)
Total switching capacity: 4 A 240 V~
Power supply: 100 … 240 V~ (50 … 60 Hz)
Supply connection: type Y attachment
Power consumption: < 1 W (Standby)
Mode of operation: type 1.B.C.Y
Rated impulse voltage: 2.5 kV
Data interfaces: VBus®, SD card slot
VBus®current supply: 60 mA
Functions: sliding set value adjustment, circulation, thermal disinfection, comfort
function, heat exchanger, stratied return, error relay, blocking protection.
Mounting: wall mounting, also suitable for mounting into patch panels
Display: full graphic display, control lamp (directional pad) and background
illumination
Operation: 7 push buttons at the front of the housing
Protection type: IP 20 / EN 60529
Protection class: I
Ambient temperature: 0 … 40 °C
Degree of pollution: 2
Dimensions: 198 x 170 x 43 mm

5
en
1 Heat transfer controller installation
1.1 Mounting
WARNING! Electric shock!
ÎAlways disconnect the device from power supply
before opening the housing!
Upon opening the housing, live parts are exposed!
The FC4.13 DHW controller is integrated into the SUS Midi or Maxi heat transfer
module respectively. If the controller is to be installed outside of the heat transfer
module, please mind the following instructions. The device must only be located
in dry interior rooms.The controller must additionally be supplied from a double
pole switch with contact gap of at least 3mm.
Please pay attention to separate routing of sensor cables and mains cables.
In order to mount the device to the wall, carry out the following steps:
ÎUnscrew the cross-head screw from the cover and remove it along with the
cover from the housing
ÎMark the upper fastening point on the wall. Drill and fasten the enclosed wall
plug and screw leaving the head protruding.
ÎHang the housing from the upper fastening point and mark the lower fastening
points (centres 150 mm).
ÎInsert lower wall plugs.
ÎFasten the housing to the wall with the lower fastening screw and tighten.
ÎCarry out the electrical wiring in accordance with the terminal allocation, see
chap. 1.2.
ÎPut the cover on the housing.
ÎAttach with the fastening screw.
cover
screw
lower fastening point
upper fastening point
Note:
Strong electromagnetic elds can impair the function of the controller.
ÎMake sure the controller as well as the system are not exposed to
strong electromagnetic elds.
1.2 Electrical connection
WARNING! Electric shock!
ÎAlways disconnect the device from power supply be-
fore opening the housing!
L' is a fused contact permanently carrying voltage.
ATTENTION! ESD damage!
Electrostatic discharge can lead to damage to electronic
components!
ÎTake care to discharge properly before touching
the inside of the device!To do so, touch a grounded
surface such as a
radiator or tap.
The controller is equipped with 4 relays in total to which loads such as pumps,
valves, etc. can be connected:
Relays 1 … 3 are semiconductor relays, designed for pump speed control.
Relay 4 is a potential-free electromechanical relay.
Conductor R1 … R4
Neutral conductor N (common terminal block)
Protective earth conductor ⏚(common terminal block)
Note:
Connecting the device to the power supply must always be the last step
of the installation!
Note:
In the heat transfer module with this controller, only high-efciency
pumps with a PWM control signal can be used.
Note:
The minimum pump speed must be set to 100% when non-speed-con-
trolled devices such as valves are connected.

6
en
Note:
The cables of the controller are pre-connected. chap. 1.2 is for informa-
tion purposes only. Make sure the hydraulic system is properly grounded!
Note:
For more details about the initial commissioning procedure see chap. 2.2.
Mains and sensor cables are already connected to the device.
Additional temperature sensors (S3 to S10) can be connected to the terminals
S3 … S10 and GND (either polarity).
The controller is supplied with power via a mains cable.The power supply of the
device must be 100…240 V~ (50 … 60 Hz).
The mains connection is at the terminals:
Neutral conductor N
Conductor L
Conductor L' (L' is not connected with the mains cable. L' is a fused contact per-
manently carrying voltage).
Protective earth conductor ⏚(common terminal block)
L'
R4
R1-R3 1 (1) A (100 ... 240) V~
4 (1) A 240 V~
4 (1) A 24V
R4
+VBus-
S1
12345678910111213141516
S2 S3 S4 S5 S6 S7 S8
Temp. Sensor
FlowRotor
N
Isolate mains before removing cover!
Vor Öffnen Gerät spannungslos schalten!
Use neutral conductor common terminal block
Neutralleiter-Sammelklemme benutzen!
Use PE Common terminal block
Schutzleiter-Sammelklemme benutzen
VFS/US
S9 S10
V40
PWM1
0-10V PWM2
0-10V PWM3
0-10V PWM4
0-10V
17 18 19 20 22 24 26 28 30 31 32
R2
R3
R4
R1
Connection for analogue
Grundfos Direct Sensor™ or
FlowSonic ultrasonic sensor
respectively
PWM /
0-10 V terminal
Potential-free
relay
Terminals
Protective conductor
common terminal
block (PE)
Neutral conductor
common terminal
block
VBus®
Opening
latch
Terminals
2 Heat transfer controller commissioning
2.1 Factory menu
In the factory menu, the controller can be adjusted to the heat transfer module in
which it is integrated (SUS Midi, Maxi). In order to do this, the parameter Hydraulic
variant must be adjusted.
WARNING! Scald danger! System damage!
Adjusting a wrong hydraulic variant can lead to inadmissibly high
water temperatures.
ÎThe hydraulic variant must be adjusted by authorised
personnel only
!
The hydraulic variant determines the range of available functions and parameters
of the controller according to the equipment of the heat transfer module.
2.2 Running the commissioning menu
The commissioning menu is run after the rst connection and after every reset. It
will request the following basic adjustments:
• Menu language
• Time
• Date
• System variant
• Hot water set temperature
• Maximum speed of the primary pump
• Maximum speed of the secondary pump
When the last item Save at the end of the commissioning menu is selected,a safety
enquiry appears. If the safety enquiry is conrmed, the adjustments are saved.
For further information about the commissioning menu see page 14.

7
en
Relay / sensor allocation
Connection terminal Description Indication
PWM1 Primary pump Primary pump
PWM2 Secondary pump Secondary pump
PWM3 Circulation pump Circulation pump
S1 Store ow sensor T-FL
S2 Hot water ow sensor T-HW
S3 Temperature sensor source, top T-Source t.
S4 Cold water sensor T-CW
S5 Temperature sensor source, bottom T-Source b.
S6 Temperature sensor sink, bottom T-Sink b.
S7 Temperature sensor sink, centre T-Sink c.
S8 Circulation return sensor T-circ RET
S9 Temperature sensor sink, afterheating T-Sink AH
VFS/US Flow rate sensor Flow rate
R2 Stratied return relay Stratied return
R3 Circulation pump relay Circulation pump
R_pot.frei Afterheating relay Afterheating
Not shown in the system graphics
R1 Parallel relay store loading Parallel relay
2.2.1 Overview of relay and sensor allocation
Heat transfer controller in heat transfer module with preheating
(SUS Sys 1 variant)
L'
R4
R1-R3 1 (1) A (100 ... 240) V~
4 (1) A 240 V~
4 (1) A 24V
R4
+VBus-
S1
12345678910111213141516
S2 S3 S4 S5 S6 S7 S8
Temp. Sensor
FlowRotor
N
Isolate mains before removing cover!
Vor Öffnen Gerät spannungslos schalten!
Use neutral conductor common terminal block
Neutralleiter-Sammelklemme benutzen!
Use PE Common terminal block
Schutzleiter-Sammelklemme benutzen
VFS/US
S9 S10
V40
PWM1
0-10VPWM2
0-10VPWM3
0-10VPWM4
0-10V
17 18 19 20 22 24 26 28 30 31 32
R2
R3
R4
R1
S9
dV
Circulation
PWM3
R3
PWM2
PWM1
S8
S6
S2
R2
S3
S5
S4
S1
S7
R_pot.
free
Primary circuit Secondary circuit

8
en
Relay / sensor allocation
Connection terminal Description Indication
PWM1 Primary pump Primary pump
PWM2 Secondary pump Secondary pump
PWM3 Circulation pump Circulation pump
S1 Store ow sensor T-FL
S2 Hot water ow sensor T-HW
S3 Temperature sensor source, top T-Source t.
S4 Cold water sensor T-CW
S5 Temperature sensor source, bottom T-Source b.
S6 Temperature sensor sink, bottom T-Sink b.
S7 Temperature sensor sink, centre T-Sink c.
S8 Circulation return sensor T-circ RET
S9 Temperature sensor sink, afterheating T-Sink AH
VFS/US Flow rate sensor Flow rate
R2 Stratied return relay Stratied return
R3 Circulation pump relay Circulation pump
R_pot.free Afterheating relay Afterheating
Not shown in the system graphics
R1 Parallel relay store loading Parallel relay
L'
R4
R1-R3 1 (1) A (100 ... 240) V~
4 (1) A 240 V~
4 (1) A 24V
R4
+VBus-
S1
12345678910 11 12 13 14 15 16
S2 S3 S4 S5 S6 S7 S8
Temp. Sensor
FlowRotor
N
Isolate mains before removing cover!
Vor Öffnen Gerät spannungslos schalten!
Use neutral conductor common terminal block
Neutralleiter-Sammelklemme benutzen!
Use PE Common terminal block
Schutzleiter-Sammelklemme benutzen
VFS/US
S9 S10
V40
PWM1
0-10VPWM2
0-10VPWM3
0-10VPWM4
0-10V
17 18 19 20 22 24 26 28 30 31 32
R2
R3
R4
R1
dV
Circulation
PWM3
R3
PWM2
PWM1
S8
S6
S2
R2
S3
S5
S4
S1
S7
S9
R_pot.
free
Heat transfer controller in heat transfer module with buffer store
(SUS Sys 2 variant)
Primary circuit Secondary circuit

9
en
Relay / sensor allocation
Connection terminal Description Indication
PWM1 Primary pump Primary pump
PWM2 Secondary pump Secondary pump
PWM3 Circulation pump Circulation pump
S1 Store ow sensor T-FL
S2 Hot water ow sensor T-HW
S3 Temperature sensor source, top T-Source t.
S4 Cold water sensor T-CW
S6 Temperature sensor sink, bottom T-Sink b.
S7 Temperature sensor sink, centre T-Sink c.
S8 Circulation return sensor T-circ RET
S9 Temperature sensor sink, afterheating T-Sink AH
VFS/US Flow rate sensor Flow rate
R3 Circulation pump relay Circulation pump
R_pot.free Afterheating relay Afterheating
Not shown in the system graphics
R1 Parallel relay store loading Parallel relay
L'
R4
R1-R3 1 (1) A (100 ... 240)V~
4 (1) A 240 V~
4 (1) A 24V
R4
+VBus-
S1
12345678910 11 12 13 14 15 16
S2 S3 S4 S5 S6 S7 S8
Temp. Sensor
FlowRotor
N
Isolate mains before removing cover!
Vor Öffnen Gerät spannungslos schalten!
Use neutral conductor common terminal block
Neutralleiter-Sammelklemme benutzen!
Use PE Common terminal block
Schutzleiter-Sammelklemme benutzen
VFS/US
S9 S10
V40
PWM1
0-10VPWM2
0-10VPWM3
0-10VPWM4
0-10V
17 18 19 20 22 24 26 28 30 31 32
R2
R3
R4
R1
dV
Circulation
PWM3
R3
PWM2
PWM1
S8
S6
S2
S3 S4
S1
S7
S9
Heat transfer controller in heat transfer module without buffer store
(SUS Sys 3 variant)
Primary circuit Secondary circuit

10
en
2.3 Operation and function
2.3.1 Buttons
The controller is operated via the 7 buttons next to the display. They have the
following functions:
button ❶- scrolling upwards
button ❸- scrolling downwards
button ❷- increasing adjustment values
button ❹- reducing adjustment values
button ➄ - con rming
button ➅-
switching to the status menu
button ➆- escape button for changing into the previous menu
1
2
4
63
5
7
2.3.2 Selecting menu points and adjusting values
During normal operation of the controller, the display is in the main menu. If no
button is pressed for a few seconds, the display illumination goes out.
Press any key to reactivate the display illumination.
ÎIn order to scroll though a menu or to adjust a value, press either buttons ❶
and ❸or buttons ❷and ❹.
ÎTo open a sub-menu or to con rm a value, press button ➄.
ÎTo enter the status menu, press button ➅ – uncon rmed adjustments will
not be saved.
ÎTo enter the previous menu, press button ➆ – uncon rmed adjustments will
not be saved.
If no button has been pressed within a couple of minutes, the adjustment is can-
celled and the previous value is retained.
If the symbol »is shown behind a menu item, pressing button ➄will open a new
sub-menu.
If the symbol ➕is shown in front of a menu item, pressing button ➄will open a
new sub-menu. If it is already opened, a ein ➖is shown instead of the ➕.

11
en
Values and adjustments can be changed in different ways:
current value savedminimum value maximum value
adjusted value
(not yet con rmed)
adjustment channel
Numeric values can be adjusted by means of a slide bar. The minimum value is
indicated to the left, the maximum value to the right.The large number above the
slide bar indicates the current adjustment. By pressing buttons ❷or ❹the upper
slide bar can be moved to the left or to the right.
Only after the adjustment has been con rmed by pressing button ➄will the num-
ber below the slide bar indicate the new value. The new value will be saved if it
is con rmed by pressing button ➄again, the controller switches to the previous
menu.
inactive area
minimum
value
active area
maximum
value
inactive area
When 2 values are locked against each other, they will display a reduced adjustment
range depending on the adjustment of the respective other value.
In this case, the active area of the slide bar is shortened, the inactive area is indicat-
ed as a dotted line.The indication of the minimum and maximum values will adapt
to the reduction.
If only one item of several can be selected, they will be indicated with "radio but-
tons". When one item has been selected, the radio button in front of it is lled. If
button ➄ is pressed, the selection is con rmed and the controller switches to the
previous menu.
Some selection possibilities are displayed with checkboxes.When an item has been
selected, an x appears inside the checkbox.

12
en
Adjusting the timer
When the Timer option is activated, a timer is in-
dicated in which time frames for the function can be
adjusted.
First of all, an overview of the current adjustments is
displayed. For each day of the week there is an over-
view display.The display can be switched back and forth
between the different days by pressing buttons ❷and
❹.
In order to adjust the timer, press button ➄.
First the individual days of the week or all days of the
week can be selected.
The last menu item after the list of days is Continue. If
Continue is selected, the Edit timer menu opens, in
which the time frames can be adjusted.
Adding a time frame:
The time frames can be adjusted in steps of 15 min.
In order to add an active time frame, proceed as fol-
lows:
ÎMove the cursor to the desired starting point of
the time frame by pressing buttons ❷and ❹.
Conrm the starting point of the time frame by
pressing button ❶.
ÎMove the cursor to the desired ending point of
the time frame by pressing buttons ❷and ❹.
ÎThe end of a time frame can be determined by
pressing button ➄.
ÎIn order to add another time frame, repeat the
last three steps.
ÎPress button ➄again to get back to the overview
of current adjustments.
Removing a time frame:
In order to remove an active time frame, proceed as
follows:
ÎDetermine the point from which on the time
frame is to be removed by pressing button ❸.
ÎMove the cursor to the desired ending point of
the time frame by pressing buttons ❷and ❹.
ÎIn order to conclude removing the time frame,
press button ➄upon reaching the desired ending
point.
ÎPress button ➄again to get back to the overview
of current adjustments.

13
en
2.3.3 Menu structure
Main menu
Status
Store loading
Afterheating
Circulation
Strat. return
Basic settings
SD card
Manual mode
User code
In-/Outputs
Afterheating
AH sensor
∆T on
∆T off
AH mode
Store loading
Emergency operation
T-HW set
Set min
Set max
Prim. max. speed
Sec. max. speed
∆Tmin
∆T store
T-HW set sliding
Blocking protection
Circulation / Disinfection
Manual start-up /Abort
T-disinf set
Disinf. duration
Disinf. day
Disinf. time
Strat. return
Type
T On
Hysteresis
∆T on
∆T off
Circulation
Type
Circ. sensor
Circ. ow rate
T-circ on
∆T-circ. off
Timer
Disinfection
The menu items and adjustment values selectable are variable depending on adjust-
ments already made. The gure only shows an exemplary excerpt of the complete
menu in order to visualise the menu structure.
Basic settings
Language
Auto DST
Date
Time
Factory setting
Display standby
Status
Meas./ Balance values
Store loading
Afterheating
Circulation
Disinfection
Stratied return
Parallel relay
Messages
Service
In- / Outputs
Inputs
Parallel relay

14
en
1. Language:
ÎAdjust the desired menu language.
3. Time:
ÎAdjust the clock time. First of all adjust the
hours, then the minutes.
4. Date:
ÎAdjust the date. First of all adjust the year,
then the month and then the day.
2. Daylight savings time adjustment:
ÎActivate or deactivate the automatic daylight
savings time adjustment.
2.4 Commissioning menu
When the controller is commissioned or when it is reset, it will run a commis-
sioning menu after the initialisation phase.The commissioning menu leads the user
through the most important adjustment channels needed for operating the system.
The commissioning menu consists of the following channels which can be entered
and adjusted line by line.
5. Selecting the variant
ÎSelect the variant of the heat transfer system.
For detailed information see page 7.
6. Hot water set temperature / Set temper-
ature secondary circuit fl ow
ÎAdjust the desired set temperature of for
loading the secondary store.
For detailed information see page 15.
7. Maximum speed of the primary and sec-
ondary pump
ÎAdjust the desired maximum speed of the pri-
mary pump.
Note:
The output of the heat transfer module
can only be limited by adjusting the max-
imum speed of the secondary pump.
Note:
Limiting the maximum speed of the pri-
mary pump will lead to a smooth start of
the pump. Only adjust the default value, if
a boiler with low power is directly con-
nected to the station.
ÎAdjust the desired maximum speed of the
secondary pump.
Note:
The adjustable values of both channels
represent the speed of the correspond-
ing pump.
Maximum speed (100%) is reached at 80
to 90 % of the PWM signal duty cycle.The
minimum value (1.5%) is reached at 10 to
20 % of the PWM signal duty cycle.
The duty cycle of the corresponding
PWM signal is indicated in the status
menu.
Note:
For detailed information see manual of
the heat transfer module!

15
en
8. Completing the commissioning menu:
ÎIn order to save the adjustments, select Save.
The controller is then ready for operation
and normally the factory settings will give
close to optimum operation.
ÎIn order to get back to the commissioning
menu channels, press button ➆.
The adjustments carried out during commission-
ing can be changed anytime in the corresponding
adjustment channel.
3 Heat transfer controller adjustments
3.1 Main menu
In this menu, the different menu areas can be selected.
The following menus are available:
Status
Store loading
Afterheating
Circulation
Strat. return
Basic settings
SD card
Manual mode
User code
In-/Outputs
Note:
If no button is pressed for the adjustable time T-display standby, the dis-
play illumination goes out.After 3 more minutes, the controller switches
to the Status / Store loading. menu.
ÎIn order to get from the Status / Store loading menu into the main
menu, press button ➆twice!
3.2 Status menu
In the Status menu of the controller, the status messages for every menu area can
be found.

16
en
3.2.1 Meas./ Balance values
In the Status / Meas./ Balance values menu, all current measurement values as
well as a range of balance values are displayed. Some of the menu items can be
selected in order to enter a sub-menu.
The status of the store loading, the circulation, the disinfection, the strati ed re-
turn, the allocation of sensors and relays as well as the operating hours counter
are indicated.
If, for example, Store loading is selected, a submenu with the sensors and relays
allocated opens. In the submenu, the current temperatures and the current pump
speed are indicated.
When a line with a measurement value is selected, another sub-menu will open.
In the Meas. /Balance values / Store loading menu, information about the heat
quantity generated in the secondary circuit is indicated, e. g. the total heat quantity,
the heat quantity generated on the current day, the current power and the total
draw-off quantity.
If, for example, VFS is selected, a submenu indicating the minimum and maximum
values will open.
3.2.2 Store loading
In the Status / Store loading menu, the status of the store loading is indicated.
3.2.3 Afterheating
In the Status /Afterheating menu, the status of the afterheating is indicated.

17
en
3.2.4 Circulation
In the Status / Circulation menu, the status of the circulation, the circulation type
selected and, if applicable, remaining runtimes and blocking times are indicated.
3.2.5 Disinfection
In the Status / Disinfection menu, the status and the progress of the thermal dis-
infection, different time counters and the number of previous starts are indicated.
3.2.6 Stratifi ed return
In the Status / Stratifi ed return menu, the status of the function is indicated.
In the corresponding menus, the status values of the function selected are indicated.
3.2.7 Parallel relay
In the Status / Parallel relay menu, the status of the parallel relay (active or
inactive) is indicated.
3.2.8 Messages
In the Status / Messages menu, error and warning messages are indicated.
During normal operation, the message Everything OK is indicated.
A line break or short circuit in a sensor line is indicated as !Sensor fault.A precise
error code can be found in the Status / Meas.- / Balance values menu.
In the case of an error, the LED of the directional pad ashes red in addition.
3.2.9 Service
In the Status / Service menu, each sensor and relay is indicated with the compo-
nent or function it has been allocated to.
Relays and sensor inputs that are not used will not be indicated here.

18
en
3.3 Store loading
In this menu, all adjustments for the DHW heating and loading of the secondary
store can be made.The following parameters and functions are available:
• Emergency operation
• Hot water set temperature / Set temperature secondary circuit ow
• Minimum hot water set temperature/minimum set temperature secondary
circuit ow
• Maximum hot water set temperature/maximum set temperature secondary
circuit ow
• Sliding set value
• Blocking protection
Emergency operation
Main menu / Store loading / Emergency operation
Adjustment
channel Description Adjustment
range / selection
Factory
setting
Emergency
operation Activation of the function Yes, No No
Em. prim. Emergency speed of the primary pump 1.5 … 100.0 % 30.0 %
Em. sec. Emergency speed of the secondary pump 1.5 … 100.0 % 30.0 %
T-HW Indicates the current ow temperature in the sec-
ondary circuit for aligning the emergency speed. - -
back
The Emergency operation function can be used for ensuring the hot water
supply and loading of the secondary store in the case of a sensor fault. In this case
the pumps will run at the adjustable Em. prim. and Em. sec. For this purpose,
the emergency speed must be aligned with the resulting temperature at the hot
water ow sensor in the secondary circuit. The display channel T-HW allows this
alignment directly in the Store loading menu, as soon as the emergency operation
has been activated.
Note:
If a sensor fault inhibiting DHW heating or store loading has occurred,
activate the emergency operation in the Emergency mode channel.
In order to ensure a quick entry to emergency operation in the case of an emer-
gency, perform the alignment of the emergency speed as early as possible.
Hot water set temperature / Set temperature secondary circuit fl ow
(T-HW set)
Main menu / Store loading /T-HW set
Adjustment
channel Description Adjustment range /
selection
Factory
setting
T-HW set Hot water set temperature/Set temperature
secondary circuit ow (T-HW set) 20 … 75 °C 60 °C
This parameter can be used for adjusting the T-HW set temperature which is to
be reached at the HW ow sensor. This temperature is also used for loading the
secondary store. The controller then determines the pump speed of the primary
pump such that the temperature at the HW ow sensor in the secondary circuit
continuously keeps the required set temperature T-HW set.
Note:
If the SUS Sys 2, 3 variants have been selected and the circulation function
is active, T-HW set cannot be adjusted to a value smaller than (T-circ
on + ∆T-circ off + hysteresis).

19
en
Maximum speed of the primary pump
Main menu /Store loading/ Prim. max. speed
Adjustment channel Description Adjustment range /
selection
Factory
setting
Prim. max. speed Maximum speed of the primary pump 1.5 … 100 % 100 %
With the parameter Prim. max. speed the maximum speed of the primary pump
can be adjusted.
Note:
The adjustable value represents the speed of the corresponding pump.
Maximum speed (100%) is reached at 80 to 90% of the PWM signal duty
cycle. The minimum value (1.5%) is reached at 10 to 20% of the PWM
signal duty cycle.
The power of the PWM signal is indicated in the status menu.
Maximum speed of the secondary pump
Main menu /Store loading/ Sec. max. speed
Adjustment channel Description Adjustment range /
selection
Factory
setting
Sec. max. speed Maximum speed of the secondary pump 1.5 … 100 % 80 %
With the parameter Sec. max. speed the maximum speed of the primary pump
can be adjusted.
Note:
The adjustable values of both channels represent the speed of the cor-
responding pump.
Maximum speed (100%) is reached at 80 to 90% of the PWM signal duty
cycle. The minimum value (1.5%) is reached at 10 to 20% of the PWM
signal duty cycle.
The duty cycle of the corresponding PWM signal is indicated in the status
menu.
Minimum hot water set temperature
Main menu / Store loading / Set min
Adjustment channel Description Adjustment range /
selection
Factory
setting
Set min Minimum hot water set temperature 20 … 75 °C 20 °C
This parameter determines the minimum limitation for the adjustment of the hot
water set temperature T-HW set.

20
en
Maximum hot water set temperature
Main menu / Store loading / Set max
Adjustment channel Description Adjustment range /
selection
Factory
setting
Set max Maximum hot water set temperature 20 … 75 °C 60 °C
This parameter determines the maximum limitation for the adjustment of the hot
water set temperature T-HW set.
∆Tmin
Main menu /Store loading /∆Tmin
Adjustment
channel Description Adjustment range /
selection
Factory
setting
∆Tmin
Set temperature difference between between
source and sink
5 … 30 K 10 K
The parameter ∆Tmin determines the set temperature difference, that has to be
reached between T-Source t. and T-Sink b., in order to activate store loading.
∆T store
Main menu /Store loading /∆T store
Adjustment
channel Description Adjustment range /
selection
Factory
setting
∆T store Set difference between hot water set tempera-
ture and store temperature 1 … 10K 4 K
The parameter ∆T store determines the set temperature difference, that has to
be reached between the temperature at T-Sink c. and the adjusted set tempera-
ture T-HW set, in order to activate store loading.
Sliding set value
Main menu / Store loading / Sliding set value
Adjustment channel Description Adjustment range /
selection
Factory
setting
T-HW set sl. Activation of the function Yes, No Ye s
back
When the T-FL temperature measured at the T-FL sensor is insuf cient for reaching
the T-HW set temperature, T-HW set will be decreased dynamically.
The speed of the primary pump will be controlled such that the dynamic set tem-
perature T-HW set sl. is held at the T-HW sensor .
Table of contents
Other PAW Controllers manuals
Popular Controllers manuals by other brands
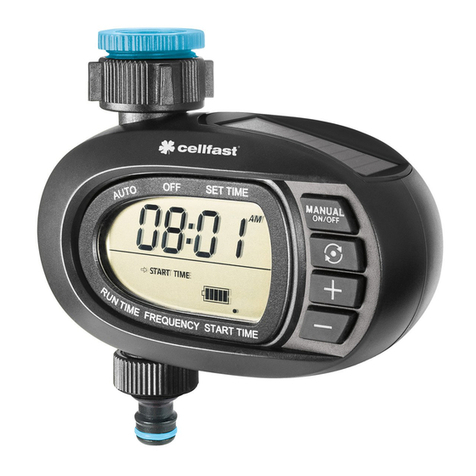
Cellfast
Cellfast ergo 52-590 user manual

Kenwood
Kenwood KCA-R20 instruction manual
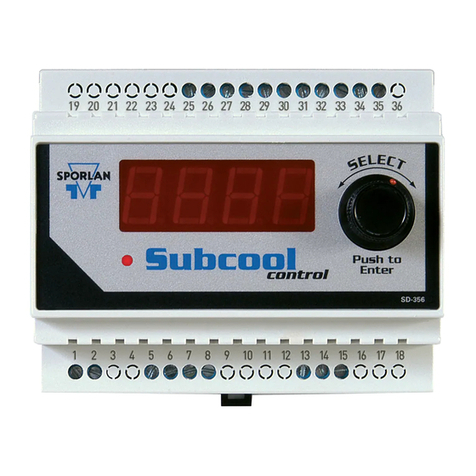
Parker
Parker Sporlan Subcool Control Installation and operation instructions

RS
RS 313-2122 Instruction leaflet
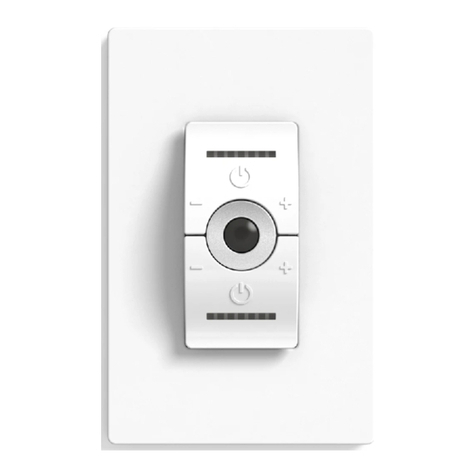
Haiku
Haiku L Wired Wall Control installation manual
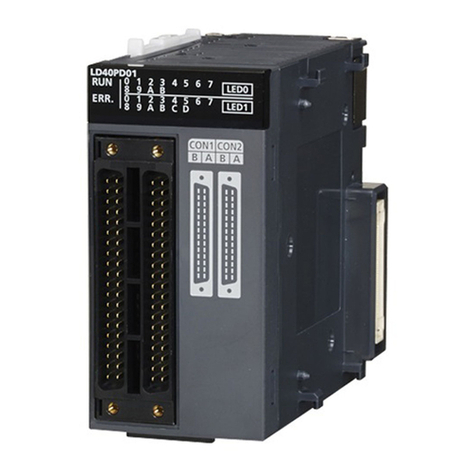
Mitsubishi Electric
Mitsubishi Electric MELSEC-L Series LD40PD01 user manual