PCB Piezotronics M261M09 User manual

Model M261M09
Triax force link, ICP®, 25 lb (Fz), 10 lb (Fx,y), 100 mV/lb (z), 500 mV/lb (x,y), ground isolated
Installation and Operating Manual
For assistance with the operation of this product,
contact the PCB Piezotronics, Inc.
Toll-free: 716-684-0001
24-hour SensorLine: 716-684-0001
Fax: 716-684-0987
E-mail: [email protected]
Web: www.pcb.com

Manual 21354 Rev E
ECN 50523
Repair and Maintenance
PCB guarantees Total Customer Satisfaction through its
“Lifetime Warranty Plus” on all Platinum Stock Products
sold by PCB and through its limited warranties on all other
PCB Stock, Standard and Special products. Due to the
sophisticated nature of our sensors and associated
instrumentation, field servicing and repair is not
recommended and, if attempted, will void the factory
warranty.
Beyond routine calibration and battery replacements
where applicable, our products require no user
maintenance. Clean electrical connectors, housings, and
mounting surfaces with solutions and techniques that will
not harm the material of construction. Observe caution
when using liquids near devices that are not hermetically
sealed. Such devices should only be wiped with a
dampened cloth—never saturated or submerged.
In the event that equipment becomes damaged or ceases
to operate, our Application Engineers are here to support
your troubleshooting efforts 24 hours a day, 7 days a
week. Call or email with model and serial number as well
as a brief description of the problem.
Calibration
Routine calibration of sensors and associated
instrumentation is necessary to maintain measurement
accuracy. We recommend calibrating on an annual basis,
after exposure to any extreme environmental influence,
or prior to any critical test.
PCB Piezotronics is an ISO-9001 certified company whose
calibration services are accredited by A2LA to ISO/IEC
17025, with full traceability to SI through N.I.S.T. In
addition to our standard calibration services, we also offer
specialized tests, including: sensitivity at elevated or
cryogenic temperatures, phase response, extended high
or low frequency response, extended range, leak testing,
hydrostatic pressure testing, and others. For more
information, contact your local PCB Piezotronics
distributor, sales representative, or factory customer
service representative.
Returning Equipment
If factory repair is required, our representatives will
provide you with a Return Material Authorization (RMA)
number, which we use to reference any information you
have already provided and expedite the repair process.
This number should be clearly marked on the outside of
all returned package(s) and on any packing list(s)
accompanying the shipment.
Contact Information
PCB Piezotronics, Inc.
3425 Walden Ave.
Depew, NY14043 USA
Toll-free: (800) 828-8840
24-hour SensorLine: (716) 684-0001
Repair inquiries: rma@pcb.com
For a complete list of distributors, global offices and sales
representatives, visit our website, www.pcb.com.
Safety Considerations
This product is intended for use by qualified personnel
who recognize shock hazards and are familiar with the
precautions required to avoid injury. While our equipment
is designed with user safety in mind, the protection
provided by the equipment may be impaired if equipment
is used in a manner not specified by this manual.
Discontinue use and contact our 24-Hour Sensorline if:
Assistance is needed to safely operate equipment
Damage is visible or suspected
Equipment fails or malfunctions
For complete equipment ratings, refer to the enclosed
specification sheet for your product.
Definition of Terms and Symbols
The following symbols may be used in this manual:
DANGER
Indicates an immediate hazardous
situation, which, if not avoided, may
result in death or serious injury.

Manual 21354 Rev E
ECN 50523
CAUTION
Refers to hazards that could damage
the instrument.
NOTE
Indicates tips, recommendations and
important information. The notes
simplify processes and contain
additional information on particular
operating steps.
The following symbols may be found on the equipment
described in this manual:
This symbol on the unit indicates that
high voltage may be present. Use
standard safety precautions to avoid
personal contact with this voltage.
This symbol on the unit indicates that
the user should refer to the operating
instructions located in the manual.
This symbol indicates safety, earth
ground.

Manual 21354 Rev E
ECN 50523
PCB工业监视和测量设备 - 中国RoHS2公布表
PCB Industrial Monitoring and Measuring Equipment - China RoHS 2 Disclosure Table
部件名称
有害物质
铅(Pb)
汞
(Hg)
镉
(Cd)
六价铬(Cr(VI))
多溴联苯 (PBB)
多溴二苯醚(PBDE)
住房
O
O
O
O
O
O
PCB板
X
O
O
O
O
O
电气连接器
O
O
O
O
O
O
压电晶体
X
O
O
O
O
O
环氧
O
O
O
O
O
O
铁氟龙
O
O
O
O
O
O
电子
O
O
O
O
O
O
厚膜基板
O
O
X
O
O
O
电线
O
O
O
O
O
O
电缆
X
O
O
O
O
O
塑料
O
O
O
O
O
O
焊接
X
O
O
O
O
O
铜合金/黄铜
X
O
O
O
O
O
本表格依据 SJ/T 11364 的规定编制。
O:表示该有害物质在该部件所有均质材料中的含量均在 GB/T 26572 规定的限量要求以下。
X:表示该有害物质至少在该部件的某一均质材料中的含量超出 GB/T 26572 规定的限量要求。
铅是欧洲RoHS指令2011/65/ EU附件三和附件四目前由于允许的豁免。
CHINA RoHS COMPLIANCE

Manual 21354 Rev E
ECN 50523
Component Name
Hazardous Substances
Lead (Pb)
Mercury (Hg)
Cadmium (Cd)
Chromium VI
Compounds
(Cr(VI))
Polybrominated
Biphenyls (PBB)
Polybrominated
Diphenyl Ethers
(PBDE)
Housing
O
O
O
O
O
O
PCB Board
X
O
O
O
O
O
Electrical Connectors
O
O
O
O
O
O
Piezoelectric Crystals
X
O
O
O
O
O
Epoxy
O
O
O
O
O
O
Teflon
O
O
O
O
O
O
Electronics
O
O
O
O
O
O
Thick Film Substrate
O
O
X
O
O
O
Wires
O
O
O
O
O
O
Cables
X
O
O
O
O
O
Plastic
O
O
O
O
O
O
Solder
X
O
O
O
O
O
Copper Alloy/Brass
X
O
O
O
O
O
This table is prepared in accordance with the provisions of SJ/T 11364.
O: Indicates that said hazardous substance contained in all of the homogeneous materials for this part is below the limit
requirement of GB/T 26572.
X: Indicates that said hazardous substance contained in at least one of the homogeneous materials for this part is above the limit
requirement of GB/T 26572.
Lead is present due to allowed exemption in Annex III or Annex IV of the European RoHS Directive 2011/65/EU.

1
ICP
3-COMPONENT FORCE LINK OPERATION MANUAL
Table of Contents
Section Page
1.0 Introduction 2
2.0 Description 2
3.0 Installation 2
4.0 Operation 3
5.0 Polarity 3
6.0 Low Frequency Monitoring 3
7.0 Discharge Time Constant 4
8.0 Calibration 4
9.0 Troubleshooting 5
10.0 Maintenance 5
Figure Page
1 3-Component Force Link Axis Definition 2
2 ICP® 3-Component Force Link 2
3 Cable Strain Relief 3
4 Characteristic Discharge Time Constant Curve 4
5 Step Function Response 4
MANUAL NUMBER: 29015
MANUAL REVISION: A
ECO NUMBER: 52446

2
ICP
3-COMPONENT FORCE LINK OPERATION MANUAL
1.0 INTRODUCTION
PCB Piezotronics 3-component force link sensors are
designed to simultaneously measure dynamic and quasi-
static force measurements in three orthogonal directions;
Fx, Fv, and F2. (Figure 1) The sensors utilize an array
of precision aligned, quartz sensing crystals stacked in a
preloaded arrangement.
2.0 DESCRIPTION
A link consists of a standard PCB 3-component force
sensor, preloaded between two precision ground plates.
(Figure 2) The plates are internally threaded to facilitate
fixturing for both tensile and compressive force
measurements. External preloads are not required with
these sensors, as they are internally preloaded during
manufacture.
I
C
P
®
f
o
Caution: Loosening or tightening of the hex nuts will
change the internal preload of the sensor. At this
point, the sensitivity provided on the calibration
certificate will 110 longer represent that of the sensor.
If this should occur, refer to the service and repair
document for proper information.
Measurements along the z-axis are proportional to
applied compression, tension, and impact forces.
Measurements along the x- and y-axis are proportional
to shear forces imposed upon the sensor.
ICP® force link sensors contain built-in, microelectronic
signal conditioning circuitry to provide clean, low-
impedance output signals that can be transmitted over
low cost cables and in adverse, industrial environments.
Multi-pin connectors facilitate a single point hookup
with common, multi-conductor cable.
Power to operate ICP® sensors is generally in the form
of a low cost, 24-27 VDC, 2-20 mA constant current
supply. PCB offers a number of AC or battery-powered,
single or multi-channel power/signal conditioners, with
or without gain capabilities for use with force sensors.
In addition, many data acquisition systems now
incorporate constant current power for directly powering
ICP® sensors. Because static calibration or quasi-static
short-term response lasting up to a few seconds is often
required, PCB manufactures signal conditioners that
provide DC coupling.
If questions arise regarding the operation or
characteristics of the force sensor products as outlined in
this manual, feel free to contact an experienced
applications engineer from the Force/Torque Division of
PCB toll-free 888-684-0004.
3.0 INSTALLATION
Refer to the installation/outline drawing supplied with
this manual for specific outline dimensions and
installation details for your particular model. The
specification is also included to provide details of the
sensor's characteristic properties.

3
ICP
3-COMPONENT FORCE LINK OPERATION MANUAL
The condition of the mating surfaces can adversely
affect the sensitivity of the sensor. It is essential that all
surfaces be clean, rigid and perfectly flat to avoid
erroneous data. A good mating surface may be obtained
by lapping, turning, spot-facing, or surface grinding.
Surface flatness should be held to within 0.001 (TIR)
over the entire mating surface. The protective cap
should remain on the connector during installation to
prevent contamination or damage.
A light coating of silicon grease (DC-4 or equivalent) on
the mating surface enhances the coupling between the
mounting base and mounting surface and provides the
best high-frequency response.
Connect one end of the interconnect cable to the sensor
connector and the other end to the XDCR jack on the
signal conditioner. Make sure to tighten the cable
connector to the sensor. DO NOT spin the sensor onto
the cable, as this fatigues the cable pins, resulting in a
shorted signal and a damaged cable.
For installation in dirty, humid, or rugged environments,
it is suggested that the connection be shielded against
dust or moisture with shrink tubing or other protective
material. Strain relieving the cable/sensor connection
can also prolong cable life. Mounting cables to a test
structure with tape, clamps, or adhesives minimizes
cable whip. See Figure 3.
4.0 OPERATION
ICP® force link sensors require a constant-current
excitation voltage for operation. The enclosed
specification sheet provides specific power
requirements. Required supply voltage is normally 20 to
30 VDC, while the constant current required ranges
from 2 to 20 mA.
PCB standard battery-powered signal conditioners are
factory set at 2 mA and may be used to adequately drive
a signal for 100 feet. PCB line signal supplies are
factory set at 4 mA (and adjustable from 2 to 20 mA),
enabling signals to be transmitted over hundreds of feet.
It is necessary to supply the sensor with a 2 to 20 mA
constant current at +20 to +30 VDC through a current-
regulating diode or equivalent circuit, contained in all
PCB signal conditioners. See Guide G-000IE for
powering and signal conditioning information pertaining
to all ICP® instrumentation.
Most of the signal conditioners manufactured by PCB
have an adjustable current feature allowing a choice of
input currents from 2 to 20 mA. In general, for lowest
noise (best resolution), choose the lower current ranges.
When driving long cables (to several thousand feet), use
The higher current, up to 20 mA maximum. Consult the
factory to determine if higher current settings are
required.
Operation requires the connection of the force sensor
first to a signal conditioner, then to a readout device
(oscilloscope, meter, recorder, or A-to-D board) or to a
readout device with built-in ICP® sensor excitation.
Tighten the cable to the sensor by hand to ensure good
electrical contact.
5.0 POLARITY
Compressive forces upon an ICP® 3-component force
link produce a positive-going voltage output. Tensile
forces produce a negative-going voltage output. Sensors
with reversed polarity are available upon request.
6.0 LOW-FREQUENCY MONITORING
Force link sensors used for applications in short term,
steady state monitoring, such as sensor calibration, or
short term, quasistatic testing should be powered by
signal conditioners that operate in DC-coupled mode.
PCB Series 484 Signal Conditioner operates in either
AC or DC-coupled mode and may be supplied with gain

4
ICP
3-COMPONENT FORCE LINK OPERATION MANUAL
features or a zero "clamped" output often necessary in
repetitive, positive polarity pulse train applications.
If you wish to learn more about ICP® sensors, consult
PCB's General Signal Conditioning Guide (G-000lE), a
brochure outlining the technical specifics associated
with piezoelectric sensors. This brochure is available
from PCB by request, free of charge.
7.0 DISCHARGE TIME CONSTANT
The discharge time constant (DTC) of the entire
transduction system from sensor to readout must be
considered when attempting to calibrate an ICP® force
sensor by static methods. In order to take full advantage
of the long DTC built into the force sensor, it is best to
DC couple from the sensor to the readout device.
Several dual-mode PCB signal conditioners (e.g., Series
484) use direct coupling techniques to decouple the
output signal from the sensor bias voltage. With the
output of the signal conditioner coupled to a DC
readout, such as a digital voltmeter (DVM) or
oscilloscope, the time constant of the sensor is not
compromised by AC coupling elsewhere in the system.
When DC coupling to a system, it is important to DC
couple the entire system and not just from the sensor to
the signal conditioner. The system time constant is
determined by the shortest t ime constant in the system.
For this reason, the signal conditioner, as well as the
readout device, must be DC coupled.
The discharge time constant represents the decay rate of
an input signal. One DTC represents the amount of time
taken for the signal to decay to 37% of the initial peak
value. As illustrated in Figure 4, this is an exponential
decay. Approximately five DTC intervals are needed
for a peak signal to naturally decay back to zero.
The rule of thumb for signal discharge, as outlined in
Figure 4, is this: for the first 10% of the DTC, the signal
lost is approximately proportional to the time elapsed.
Step Function Response
For example, a sensor with a 500-second DTC loses
approximately 1% of its output level the first five
seconds (I% of 500) after the application of a steady
state force within the measuring range. In this case, the
output reading must be taken within five seconds of the
force application for I% accuracy. If it is impossible to
avoid AC coupling somewhere in the sensing system, try
to keep the coupling DTC at least an order of magnitude
longer than the DTC of the force sensor. This avoids
compromising the sensor DTC.
8.0 CALIBRATION
A NIST (National Institute of Standards and
Technology) traceable calibration graph is supplied with
each force sensor certifying its voltage sensitivity
(m V /lb). Calibration procedures follow accepted
guidelines as recommended by ANSI (American
National Standards Institute), ISA (Instrument Society
of America), and ISO (International Organization for
Standardization). These standards provide the
establishment and management of complete calibration
systems, thus controlling the accuracy of a sensor's
specifications by controlling measuring and test
equipment accuracy. PCB is A2LA accredited for
technical competence in the field of calibration, meeting
the requirements of ISO/IEC 17025-1999 and
ANSI/NCSL 2540-1-1994.

5
ICP
3-COMPONENT FORCE LINK OPERATION MANUAL
9.0 TROUBLESHOOTING
When a PCB signal conditioner with any of the
following indicators are used, tum the power on and
observe the voltmeter ( or LED's) on the front panel.
Output voltage moves from YELLOW to GREEN
slowly until charging is complete. AC coupled signal
conditioners require sufficient time to charge the
internal coupling capacitor. Allow signal conditioner to
charge for approximately 5 discharge time constants for
stable operation.
Note : Most PCB force sensors have an output bias of 8-
14 VDC. Refer to the specification sheet with this
manual for the bias range of the model you are using. If
you are using a low bias sensor, the indicator will be at
the bottom end of the green portion of the dial indicator,
and may even be in the red portion. This is the expected
10.0 MAINTENANCE
The sensor connector must be kept clean, especially if it
is operating in a dusty and/or wet environment. Because
the force sensor is of welded construction, it should be
returned to the factory for servicing in the event of
serious malfunction.
Observe the following precautions in using the sensor:
■ Do not exceed the maximum load levels for the
force sensor (see specification sheet).
■ Do not subject the sensor to temperatures exceeding
that of the specification, normally 250°F (121°C).
■ Do not apply voltage to the sensor without current-
limiting diodes or other current protection.
■ Do not apply more than 20 mA of current to the
force sensor.
■ When mounting the force sensor, observe
installation procedures detailed in Section 3.0 and as
outlined on the specific sensor installation/outline
drawing to avoid overtorquing when mounting.
■Do not apply more than 30 volts to the sensor.
■Avoid metal-to-metal impacts during applications,
which can produce high frequency ringing.
Electrical low-pass filtering or a damping material
can help reduce such effects.
■Do not spin the sensor onto the cable. This may
fatigue the cable pins, causing cable damage.
Always insert the cable pin into the sensor and
tighten the knurled cable nut to the sensor.
ICP® is a registered trademark of PCB Piezotronics, Inc.

Model Number
261M09 3-COMPONENT ICP® FORCE SENSOR Revision: D
ECN #: 52940
Performance EN G LISH SI
Sensitivity(± 20 %)(Z Axis) 100 mV/lb 22.5 mV/N
Sensitivity(± 20 %)(X or Y Axis) 500 mV/lb 112 mV/N
Measurement Range(Z Axis) 25 lb 0.111 kN
Measurement Range(X or Y Axis) 10 lb 0.044 kN
Maximum Force 300 lb 1.334 kN
Maximum Force(X or Y Axis) 60 lb 0.267 kN
Maximum Moment(Z Axis) 14 ft-lb 19.0 Nm
Maximum Moment(X or Y Axis) 13 ft-lb 17.6 Nm
Broadband Resolution(Z Axis) 0.0003 lb-rms 0.0133 N-rms [1]
Broadband Resolution(X or Y Axis) 0.00004 lb-rms 0.0002 N-rms [1]
Low Frequency Response(- 5 %)(Z-Axis) 0.01 Hz 0.01 Hz
Low Frequency Response(- 5 %)(X or Y axis) 0.01 Hz 0.01 Hz
Non-Linearity ≤ 1 % FS ≤ 1 % FS [2]
Cross Talk(between X and Y Axis) ± 3 % ± 3 %
Cross Talk(between (X or Y axis) and Z Axis) ± 5 % ± 5 %
Environmental
Temperature Range -65 to +250 °F -54 to +121 °C
Electrical
Full Scale Output(Z Direction) ± 2.5 VDC ± 2.5 VDC
Full Scale Output(X and Y Direction) ± 5 VDC ± 5 VDC
Discharge Time Constant(Z axis) ≥ 50 sec ≥ 50 sec
Discharge Time Constant(X or Y axis) ≥ 50 sec ≥ 50 sec
Excitation Voltage(all channels) 20 to 30 VDC 20 to 30 VDC
Constant Current Excitation(all channels) 2 to 20 mA 2 to 20 mA
Output Impedance ≤ 100 Ohm ≤ 100 Ohm
Output Bias Voltage 8 to 14 VDC 8 to 14 VDC
Electrical Isolation(Base) ≥ 108≥ 108
Ph ysical
Stiffness(X or Y Axis) 1.9 lb/µin 330 N/µm [1]
Stiffness(Z Axis) 4.9 lb/µin 860 N/µm [1]
Stiffness(RX or RY Axis) 7.5E5 lbf*in/radian 8.5E4 N*m/radian [1][3]
Stiffness(RZ Axis) 3.4E5 lbf*in/radian 3.8E4 N*m/radian [1][3]
Coupled Stiffness(X-RY or Y-RX Axis) 1.0 lbf*in/µin 4.4 N*m/µm [1][3]
Weight 13.60 oz 386 gm
Housing Material Stainless Steel Stainless Steel
Sealing Hermetic Hermetic
Electrical Connector 4-Pin 4-Pin
Electrical Connection Position Side Side
[4]
All specifications are at room temperature unless otherwise specified.
In the interest of constant product improvement, we reserve the right to change specifications without notice.
ICP® is a registered trademark of PCB Piezotronics, Inc.
M - Metric Mount
W - Water Resistant Cable
OPTIONA L VERSION S
Optional versions have identical specifications and accessories as listed for the standard model except
where noted below. More than one option may be used.
NOTES:
[1]Typical.
[2]Zero-based, least-squares, straight line method.
[3]See PCB White Paper WPL_88_1121 for details.
[4]See PCB Declaration of Conformance PS023 for details.
Date: 11/23/2022 Date: 11/23/2022 Date: 11/23/2022 Date: 11/23/2022 39306
Entered: ND Engineer: EB Sales: BS Approved: RPF Spec Number:
Phone: 716-684-0001
Fax: 716-684-0987
E-M ail: info@ pcb.com
3425 Walden Avenue, Depew, NY 14043

SECTION A-A
1
1
2
2
3
3
4
4
A A
B B
CODE
IDENT. NO.
52681
DWG. NO.
SCALE: SHEET
DRAWN CHECKED ENGINEER
TITLE
UNLESS OTHERWISE SPECIFIED TOLERANCES ARE:
DIMENSIONS IN MILLIMETERS
[ IN BRACKETS ]
ANGLES 2 DEGREES
3425 WALDEN AVE. DEPEW, NY 14043
DIMENSIONS IN INCHES
ANGLES 2 DEGREES
FILLETS AND RADII
.003 - .005
FILLETS AND RADII
0.07 - 0.13
OUTLINE DRAWING
39307
1 OF 11.65X
MODEL 261M09 & M261M09
TRIAXIAL FORCE SENSOR
DECIMALS XX ±.03
XXX ±.010
DECIMALS X ± 0.8
XX ± 0.25
NJF 11/22/22 JJF 11/22/22 EDB 11/22/22
CABLE TOLERANCES IN ENGLISH CABLE TOLERANCES IN METRIC
1"≤LENGTH < 1' = +1"/ - 0
1'≤LENGTH < 5' = +2"/ - 0
5'≤LENGTH < 100' = +6"/ - 0
100'≤LENGTH = +1'/ - 0
2.54cm ≤LENGTH < 30.5cm = +2.54cm/ - 0
30.5cm ≤LENGTH < 1.5m = +5.1cm/ - 0
1.5m ≤LENGTH < 30.5m = +15.2cm/ - 0
30.5m ≤LENGTH = +30.5cm/ - 0
A
A
PIN OUT
SCALE 4.5X
Y
X
Z
39307
PCB Piezotronics Inc. claims proprietary rights in
the information disclosed hereon. Neither it nor any
reproduction thereof will be disclosed to others
without the written consent of PCB Piezotronics Inc.
REVISIONS
REV DESCRIPTION DIN
A UPDATED FOR METRIC & REFERENCE DIMENSIONS 52940
NOTCH
GROUND
Y-AXIS
X-AXIS
Z-AXIS
.276 [7.01]8X ( )
.621 [15.77]2X ( )
1.652 .006 41.96 .15
[]
.415 [10.54]16X ( )
.27 [6.9]
8X 1/4-28 UNF - 2B THRU
[M6x1.0 - 6H THRU]
1.260 .001 32.00 .03
[]
2X
1.655 .001 42.04 .03
[]
2X
1/4-28 UNF - 2A
4-PIN ELECTRICAL CONNECTOR
26947-01 WASHER
(SUPPLIED)
5/16-24 UNF - 2B NUT
(SUPPLIED)
081M175 MOUNTING STUD
(SUPPLIED)
083M16 BUSHING
(SUPPLIED)
NON-CONDUCTIVE
CERAMIC COATING
Table of contents
Other PCB Piezotronics Network Hardware manuals
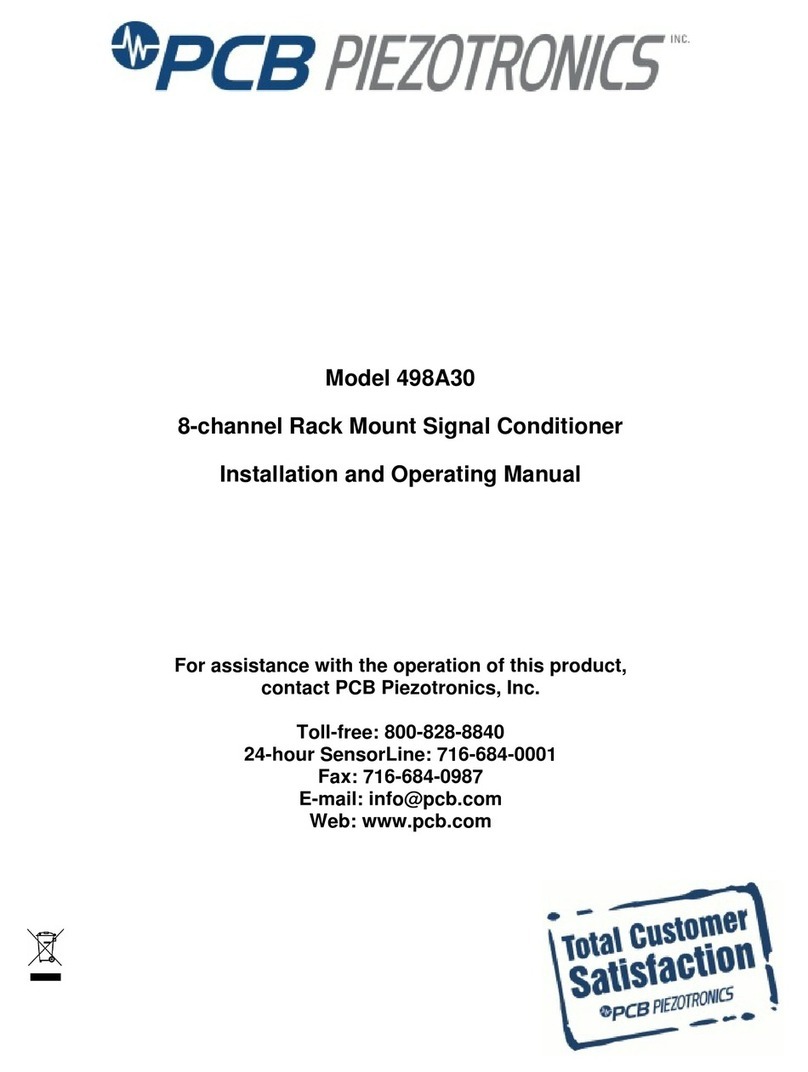
PCB Piezotronics
PCB Piezotronics 498A30 User manual
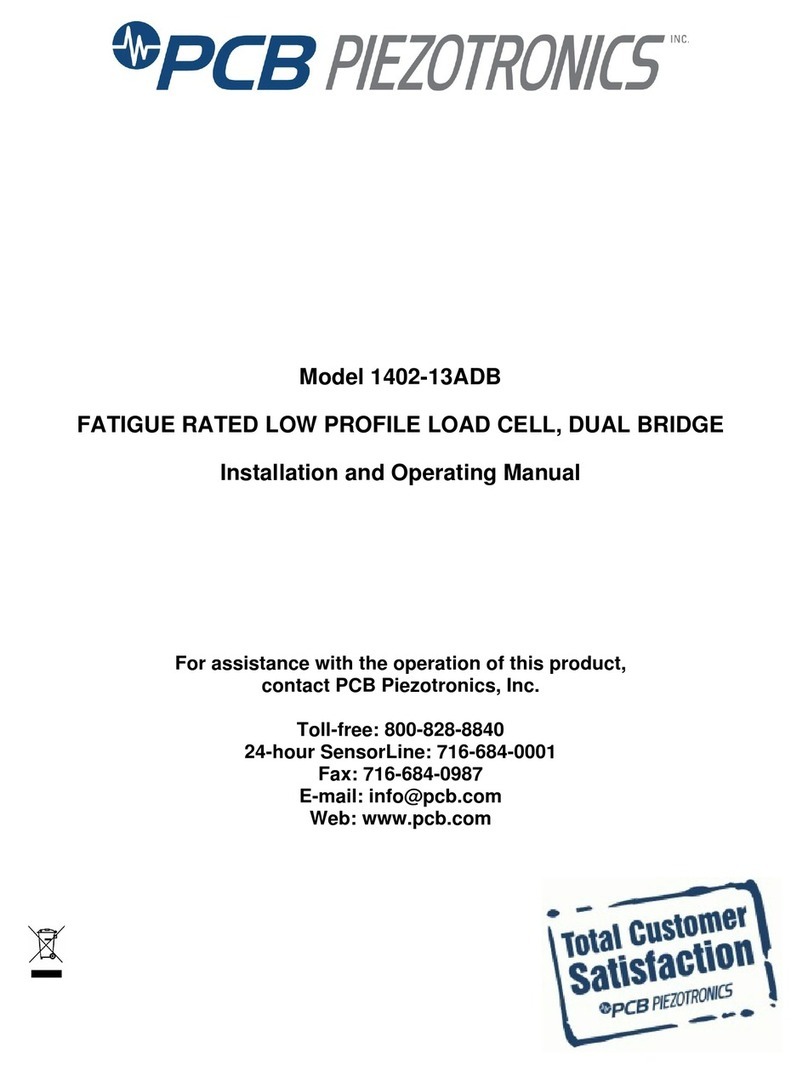
PCB Piezotronics
PCB Piezotronics 1402-13ADB User manual
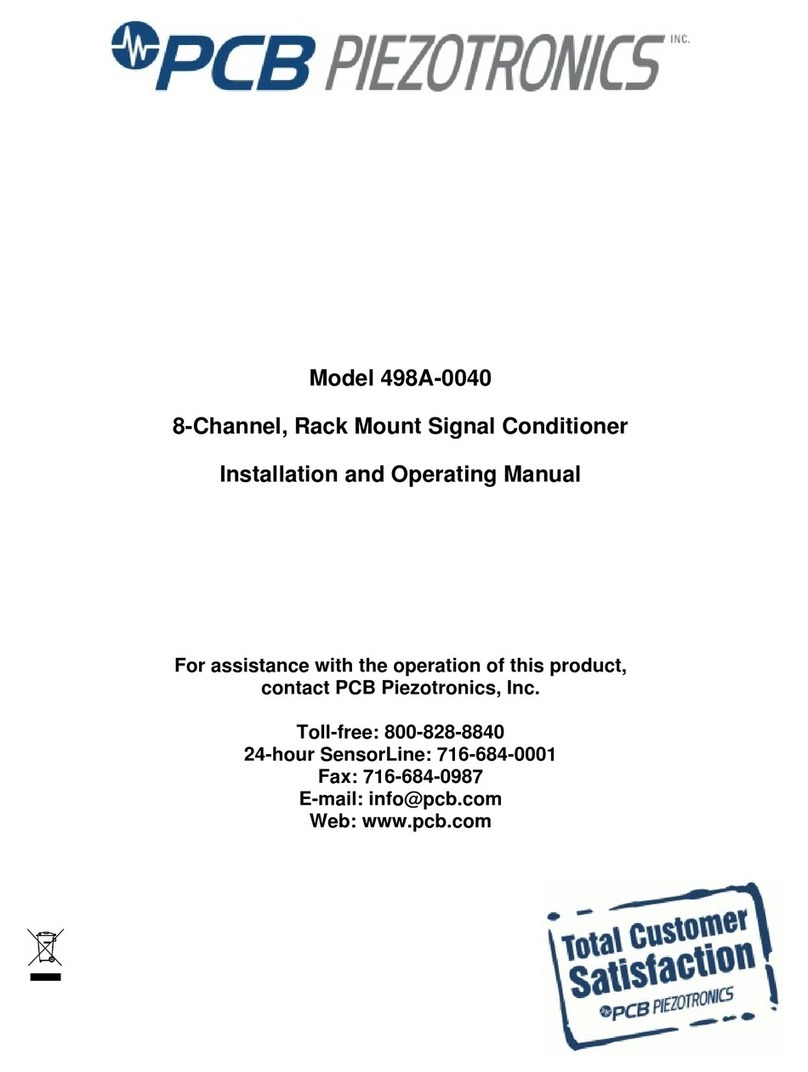
PCB Piezotronics
PCB Piezotronics 498A-0040 User manual
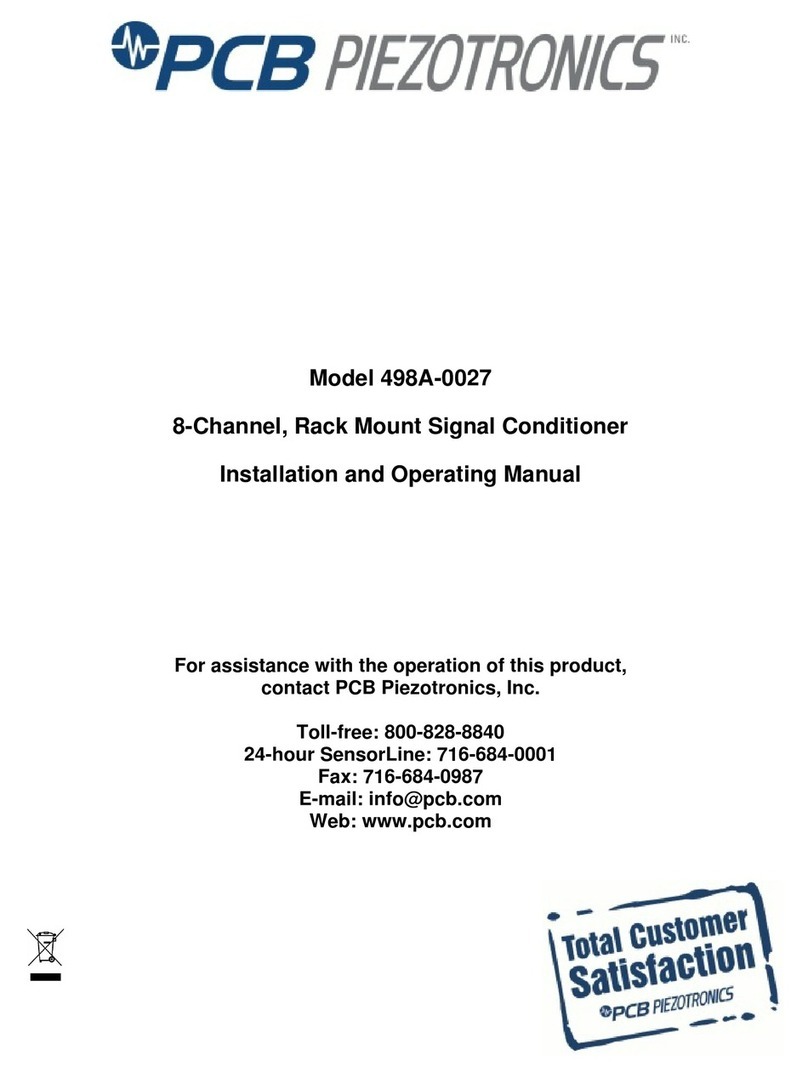
PCB Piezotronics
PCB Piezotronics 498A-0027 User manual
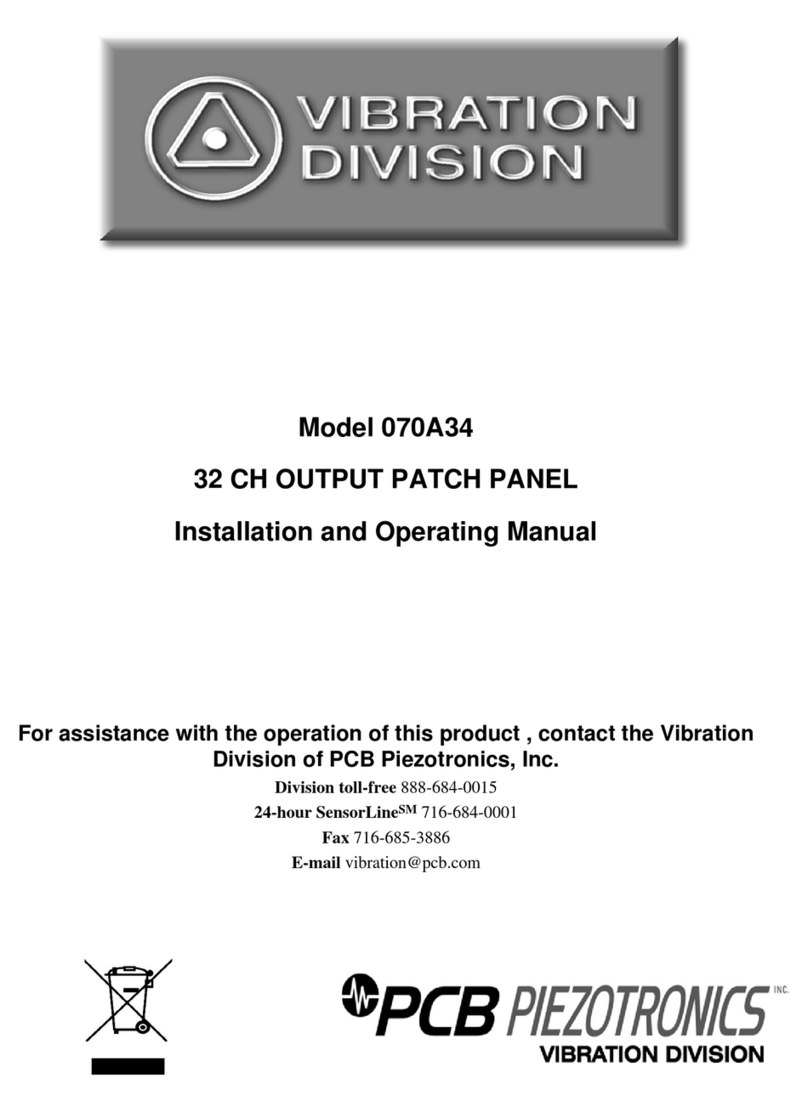
PCB Piezotronics
PCB Piezotronics 070A34 User manual

PCB Piezotronics
PCB Piezotronics JM320C16 User manual