PCS TCM2800 User manual

Ph: 1.804.227.3023 | www.powertraincontrolsolutions.com
PCS TCM2800 QUICK START GUIDE

Table of Contents
Section 1: Installation Instruction Contents ......................................................................................................................................................... 1 - 5
Section 1.1 Introduction ................................................................................................................................................................................... 1
Section 1.2 Check TCM and Harness ............................................................................................................................................................. 1
Section 1.3 TCM and Harness Guidelines ...................................................................................................................................................... 1
Section 1.4 Connections ................................................................................................................................................................................. 2
Section 1.4.1 Inputs .................................................................................................................................................................. 2 - 5
Section 1.4.2 Outputs .......................................................................................................................................................................5
Section 2. Installation Instruction Contents ........................................................................................................................................................ 6 - 7
Section 2.1 System Overview ......................................................................................................................................................................... 6
Section 2.2 System Requirements .................................................................................................................................................................. 6
Section 2.3 Congurable Tuning Software Installation .................................................................................................................................... 6
Section 2.4 Connecting the Communication Cable ................................................................................................................................... 6 - 7
Section 3. Save Calibration File ................................................................................................................................................................................... 8
Section 4. Initial Setup .................................................................................................................................................................................................. 9
Section 4.1 Tire Size and Axle Ration Setup ................................................................................................................................................... 9
Section 4.2 Throttle Position Setup ................................................................................................................................................................ 10
Section 5. Verify Operation of Initial Setup ............................................................................................................................................................... 10
Section 6. Calibrating the Transmission ............................................................................................................................................................ 11 - 14
Section 6.1 Shifting into Gear Pressure ........................................................................................................................................................ 11
Section 6.2 Steady State Pressure ................................................................................................................................................................ 11
Section 6.3 Manual Range Pressure .............................................................................................................................................................. 12
Section 6.4 Upshift/Downshift Tables ............................................................................................................................................................. 13
Section 6.5 Wide Open Throttle (WOT) Upshift RPM A ................................................................................................................................. 13
Section 6.6 Wide Open Throttle (WOT) Downshift Speeds A ........................................................................................................................ 14
Section 6.7 TCC Lockup Settings .................................................................................................................................................................. 14
Section 7. Datalogging ........................................................................................................................................................................................ 15 - 16
Section 7.1 Datalogging Menu ...................................................................................................................................................................... 15
Section 7.2 View Datalogs ............................................................................................................................................................................. 16
03-04-2020 - REV 2.1: Instuctions on how to enter “Basic + Setup” mode added to Section 4.
Revision History

Page 1 Ph: 804.227.3023
10511 Old Ridge Rd. Ashland, VA 23005
v 2.1
Powertrain Control Solutions
PCS TCM2800 Quick Start Guide
1 Installation Instruction Components
1.1 Introduction
Please check your new transmission control system contents. These transmissions are fully electronic and will not
shift automatically without a transmission control system connected to it. Powertrain Control Solution’s TCM, computer
software and wiring harness. The programmable TCM has many features such as; fully tunable part throttle and WOT
shift points, shift rmness for various throttle/torque level, Sport/Tow Haul calibration tables. The torque converter lock-up
vehicle speeds are fully adjustable as well as the lock up on rate. All of the wiring harness connectors are clearly labeled.
You should have received the following items:
• TCM-2800 Transmission Control Unit (TCM)
• Complete wiring harness with labeled connectors
• USB Drive with Software
• 5ft communications cable for TCM to laptop
1.2 Check TCM and Harness
Your TCM should come preloaded with a starting calibration le. Check the sticker on the bottom of the controller to
see what calibration le has been preloaded. If the sticker has “Cal to be loaded by OEM/Dealer” contact the dealer
the controller was purchased from to see if a calibration has been loaded or to acquire the initial calibration. If using the
controller on an unsupported transmission, a more in depth setup is required and is beyond the scope of this document.
Verify the connectors on the harness match the ones on your transmission and sensors. The Wiring harness schematics
have views of all the connectors and should be matched to your applications prior to any installation.
1.3 TCM and Harness Guidelines
The TCM itself is weatherproof, but there are some basic rules to follow when you are deciding a location to mount it
Mounting it in the engine compartment is acceptable or under the vehicle is acceptable. Also verify the wiring harness
has ample length to reach the other connections before permanently mounting it. The TCM requires an 12v power,12V
Switched, ground connection, Throttle Position input to operate correctly. The power connection to the TCM is prewired
to an unterminated wire.
Function Wire Color
12V Power Red
12V Switched Yellow
Ground Black
TPS Yellow/Black
TPS Ground Black/White
Engine RPM Orange/Black
Engine RPM Ground Black/White

Page 2 Ph: 804.227.3023
10511 Old Ridge Rd. Ashland, VA 23005
v 2.1
Powertrain Control Solutions
1.4 Connections
1.4.1 Inputs
Transmission Control Module (TCM) Connector
The main transmission connector varies depending on the transmission model you are working with. Verify the
connector and wiring diagram match your transmission prior to beginning the installation. PCS harnesses connect
all of the internal transmission solenoids, sensor switches that the TCM requires to control the transmission.
Simply plug it into the connector of the transmission. Reference Figure 1.
Laptop Calibration Connector
This connector allows the TCM to interface with your laptop. The laptop calibration connector plugs into the
supplied communication cable. Reference Figure 2.
Throttle Position Sensor (TPS)
Throttle position is required for all transmissions to function properly.. There is a three wire connector used for
the throttle position sensor. Typically, the mating connector has 2 wires, Yellow and Black for the TPS reference
signal and black and white for the analog sensor ground. This is typically the AD1 input under the Digital Input
setup. Reference Figure 3.
Figure 3: Throttle Position Sensor (TPS)
Figure 2: Laptop Calibration Connector
Figure 1: TCM Connector

PCS TCM2800 Quick Start Guide
Page 3
Ph: 804.227.3023
10511 Old Ridge Rd. Ashland, VA 23005 v 2.1
RPM Wires (unterminated)
There are 2 wires in the harness that are used for the RPM input. There Orange and Black for the RPM signal and the
Black and White for RPM Ground. This signal will need to be congured. This wire is not required for operation of your
TCM-2800 unit but it is recommended to offer comprehensive diagnostic capabilities. To utilize the full diagnostic function
of your TCM-2800, connect this wire to the tachometer output wire of your ignition system. The TACHOMETER GROUND
wire must also be connected in the Hardware Setup, there are 4 windows that are used to congure this input. The Speed
Input Selection is precongured for Speed 1, since this is what the standard harness utilizes. Reference Figure 4.
The “Speed input Trigger Value” for speed 1, needs to be set to the signal input value from your engine management
system. Reference Figure 5.
The settings for “Speed Input 1 Pulses Per Revolution”, need to be congured. The value for this will depend on what type
of input you are using to monitor Engine RPM. Reference Figure 6.
Figure 6: Speed Input Pulses
Figure 5: Speed Input Trigger Levels
Figure 4: Speed Input Selection

Page 4 Ph: 804.227.3023
10511 Old Ridge Rd. Ashland, VA 23005
v 2.1
Powertrain Control Solutions
CAL A/B Wire
This single wire is one of the unterminated digital inputs that can be used to enable a secondary calibration, Such
as Sport mode. This gives you the ability to create a completely separate shift map and pressure tables for use as a
sport or tow mode. This lead can be attached to a switch that will enable it when pulled low (Grounded) to change to a
completely different calibration. When it is not activated the default position (off) will be the Cal A setting. When switched
on (grounded), the TCM will change to operate from the Cal B calibration.
Cancel Overdrive
When enabled this cancels gear ratios over a 1:1 ratio (overdrive). In automatic transmissions this is almost always the
highest gear.
4WD Low
When enabled, this acts as an output speed divisor. This is for 4WD applications where the transfer case and the speed
output are connected to the output of the transmission. Without any correction, this would cause the speedometer to
read abnormally high. The correction factor enabled by this digital input must be programmed in the gear ratio tables. This
input should be wired to the 4WD low button or (if lever activated) to the 4WD low sensor in the transfer case or shift lever.
Dyno Mode
When enabled, this mode will allow you lockup the torque converter and choose a gear for dynamometer use. Locking
up the torque converter will lower transmission loss and may increase power numbers on the dyno. Typically you will
want to choose a gear that is 1:1 to use for the dyno as this gear ratio usually has the smallest amount of loss in the
transmission. Both parameters are congurable. All upshifts/downshifts will occur at the value specied by 0% TPS in the
upshift/downshift tables. Upshifts will occur until reaching the desired gear specied in the dyno mode form. TCC lockup
will occur based on the speed set in the dyno mode form.
Manual Mode
When enabled, this setting allows the user to upshift or downshift with the press of a button. An analog multiplexed
steering wheel input or two digital inputs may be used for the upshift and downshift commands.
Upshift
This digital input will issue an upshift command to the TCM. This command is only effective when in manual mode.
Downshift
This digital input will issue a downshift command to the TCM. This command is only effective when in manual mode.
The “Speed Input Filter Values” settings lters will assist in receiving a stable signal. Reference Figure 7.
Figure 7: Speed Input Filter Values

PCS TCM2800 Quick Start Guide
Page 5
Ph: 804.227.3023
10511 Old Ridge Rd. Ashland, VA 23005 v 2.1
Brake Light Wire
Although not necessary, the wire labeled “brake light” should be run to a factory brake pedal switch (NC) so the TCC will
unlock when you apply the brakes
1.4.2 Outputs
Overdrive Cancel Indicator
This output is driven when Overdrive Cancel is selected. It can be used to activate an LED to indicate that Overdrive
Cancel is in use.
Spare Output (unterminated)
This output can be congured for other indicators such as TCC Status, Dyno Mode etc…
Speedometer Drive
Some speedometers may not be driven correctly by the normal speedometer output of the TCU. In such cases, a digital
output may be programmed to output the same speed signal. The default is 2000 PPM. This value can be modied in the
Tuning Software if needed. Under the Hardware Setup/Speedo Output Settings Window. Reference Figure 8.
Figure 8: Speedo Output Settings

Page 6 Ph: 804.227.3023
10511 Old Ridge Rd. Ashland, VA 23005
v 2.1
Powertrain Control Solutions
2 Install Software
2.1 System Overview
Use the supplied USB drive or download link to install the PC tuning software. The PC software installation also includes
drivers for any supplied communication cables. Leave the cable unplugged from the PC until this process has completed.
Once software installation is complete, you can plug in the communication cable.
2.2 System Requirements
PC: 80386 or higher CPU
Operating System: Microsoft® Windows XP /Vista/Windows 7, Windows 8, Windows 10
Graphics: VGA
RAM: 2MB minimum
Hard Disk: 1 MB minimum
RS-232: A free COM port (#1, 2, 3 or 4 without conicting interrupts) is required. Use of a USB to RS-232 adapter is
required in the event your PC is only equipped with a USB port.
2.3 Congurable Tuning Software Installation
Option 1: Installation from Download Link
Visit the link below and download “TCM2800_Tuning-Install.exe” to your computer.
https://www.powertraincontrolsolutions.com/download/Released/Public/TCM2800_Tuning-Install.exe
1. Double click the downloaded le to begin the installation.
2. Follow the instructions that appear on the screen to complete the installation.
Option 2: Installation from USB Drive
1. Insert the supplied software on the USB into your computer’s USB port.
2. Open the contents of your USB drive.
3. Double click “TCM2800_Tuning-Install.exe”
4. Follow the instructions that appear on the screen to complete the installation
2.4 Connecting the Communication Cable
Executing the Software
To execute the program once it’s installed, click on the desktop shortcut open the software. The software is also installed
in the Start Menu Programs folder.
Special Notes
If the TCM is not connected and powered (key off) when the software is executed for the rst time, the software will be in
an ‘Ofine’ mode. Reference Figure 9. If the software is executed after the TCM is powered up (key on) and connected (by
the communication cable), communication will be attempted. You can also press the CTRL G keys to cause the software
to attempt communication with the TCM. Once controller installation has been completed, power on the controller from its
switched 12V source. With the communication cable connected, start the PC software. If everything has been installed
correctly, the software will automatically nd the controller and connect. This is indicated by the software background
turning blue and by a green icon on the Tool Bar. Reference Figure 10.

PCS TCM2800 Quick Start Guide
Page 7
Ph: 804.227.3023
10511 Old Ridge Rd. Ashland, VA 23005 v 2.1
Figure 9: Software Ofine
Figure 10: Software Online

Page 8 Ph: 804.227.3023
10511 Old Ridge Rd. Ashland, VA 23005
v 2.1
Powertrain Control Solutions
3 Save Calibration File
When the software is connected with the controller, click the “Read Cal” tool bar button. Reference Figure 11. You will
be prompted, with a window, to select where to save the calibration le and what to name it. It is recommended that you
save a copy of the calibration le, that your controller came with, before you start making changes. After clicking “save,”
the calibration will be retrieved from the controller and saved in the selected location. After this process completes, the
software will automatically open the retrieved calibration. When a calibration le is open in the software, you will have the
calibration tree view on the left hand side of the software. Reference Figure 12.
Figure 12: Tree View
Figure 11: Read Calibration Button

Page 9 Ph: 804.227.3023
10511 Old Ridge Rd. Ashland, VA 23005
v 2.1
Powertrain Control Solutions
4 Initial Setup
4.1 Tire Size and Axle Ratio Setup
The two most important settings that must be done before going any further are the Vehicle Speed and the Throttle
Position calibrations. In order to calibrate the vehicle speed that is used by the controller, the tire size and nal drive ratio
need to be entered into the calibration. Tire size is entered in inches. If this is not known, you can use the calculator in the
software to enter the side wall information and get the size. The nal drive ratio will be the ratio of the rear end on a rear
wheel drive vehicle. In the calibration tree view select “Setup Info/Gear Ratio and Tire Size”. Enter your vehicles axle ratio
and tire size only. The transmission ratios typically do not need
to be changed. Reference Figure 14.
NOTE: In order to access the parameters required for initial setup you must be in Basic + Setup mode. To do this,
click Software Setup > Tuning Mode > Basic + Setup. Reference Figure 13.
Figure 14: Gear Ratios and Tire Size
Figure 13: Basic + Setup Mode

Page 10 Ph: 804.227.3023
10511 Old Ridge Rd. Ashland, VA 23005
v 2.1
Powertrain Control Solutions
5 Verify Operation of Initial Setup
When connected to the TCM, open the monitor screen by selecting the “Monitor” icon on the tool bar. Instructions for
verifying TPS and VSS operation. Reference Figure 17.
Figure 17: Monitor Button
4.2 Throttle Position Setup
Throttle position calibration may or may not need to be done, depending on installation. The most common installations
consist of wiring into an existing TPS or supplying the TCM with a dedicated TPS. If set up in this way, the minimum and
maximum voltages of the throttle range must be entered into the calibration. The analog input pin from the TCM will be
wired to the signal output pin of the TPS. The TCM wiring harness provides a +5v reference voltage signal (red wire with
white stripe) and a ground reference signal (black with white stripe). The TPS output pin should increase in voltage as you
open the throttle. A typical closed throttle voltage value is .45v. A typical wide open throttle (WOT) value is 4.5v. After you
connect the wires you can verify the voltage readings on the TCM Monitor window. Click on the monitor icon or use CTRL
M. when you are online with the ignition on and the engine off you will be able to monitor and record the min voltages at
0 Throttle and Max throttle voltage when you depress the pedal to the oor. Reference Figures 15 and Figure 16.
* If you are using an existing TPS sensor you do not need to connect the 5v reference wire.
*Other types of TPS installations are covered in section (ENTER Section here) of the full manual. At this time, it is recommended to save the calibration
le with a different le name than the original le. You can do this by clicking “File,” then “Save Calibration as…”
Figure 16: TPS Calibration
Figure 15: Monitor Screen, TPS Voltage Range

PCS TCM2800 Quick Start Guide
Page 11
Ph: 804.227.3023
10511 Old Ridge Rd. Ashland, VA 23005 v 2.1
6 Calibrating the Transmission
This section will walk through the basics of tuning an electronic automatic transmission. First verify that the transmission
setup has been correctly programmed for your transmission. New calibration les provided with your install will give you
a good starting point. It is recommended you work on the calibration “A” tables rst. Then use these as a starting point for
Calibration “B”. The pressure tables are the most critical. It these are command a low pressure during shifting or steady
state, your transmission will fail. For this reason, we recommend getting these settings adjusted rst.
6.1 Shifting into Gear Pressure
Shifting Pressure are controlled by an electronic pressure control solenoid. The greater the amperage (Y-Axis) the lower
the Line pressure (shift pressure in this case). As TPS increases for a commanded shift, the amperage should decrease
to increase the shift pressure Keep in mind too low of pressure will cause long, soft shifts and will cause a durability
problem. Setting these values to low numbers and then gradually increasing them in the individual TPS/Load areas to
achieve the desired shift feel is a safer approach. Due this for each shift event. For the best results the transmission
calibration should be performed in the normal operating region (160-200). Remember to save your calibration le to your
computer. Reference Figure 18.
6.2 Steady State Pressure
Steady state pressure is the amount of pressure required to hold the applied clutch without slipping after the shift has
completed. As TPS/Load increases the amount of holding force needs to increase. This table is the transmission line
pressure that is commanded per gear after the shift is completed. Typically, these values are lower the shifting pressure
since the load transfers are completed at this point. While you may think it is safer to just let the transmission run at High
pressure all the time during this drive condition, you should consider the following. First, high pressure outputs from
the pump cause the transmission to run hotter. Second this also creates addition load which reduce engine power and
decreases fuel economy. Ideally you should set these to a point that has enough pressure to hold the clutch. Similar
to the “Shifting into Gear Pressure Tables”, Shifting Pressure are controlled by an electronic pressure control solenoid.
The greater the amperage (Y-Axis) the lower the Line pressure (shift pressure in this case). Reference Figure 19 on the
following page.
Figure 18: Shifting Into Gear Pressure A

Page 12 Ph: 804.227.3023
10511 Old Ridge Rd. Ashland, VA 23005
v 2.1
Powertrain Control Solutions
Figure 19: Steady State Line Pressure A
Figure 20: Manual Range Pressure A
6.3 Manual Range Pressure
The manual range pressure tables are used to increase the transmissions pressure when you shift the transmission down
in the D3,D2 and D1 Positions. Additional pressure is sometime desired to assist in applying and holding the clutches and
bands. Especially when using the transmission to assist in engine braking on a grade. Reference Figure 20.

PCS TCM2800 Quick Start Guide
Page 13
Ph: 804.227.3023
10511 Old Ridge Rd. Ashland, VA 23005 v 2.1
Figure 23: Manual Range Pressure A
Figure 21: Shift Table A showing shifts from 1st to 2nd Figure 22: Shift Table A showing all shifts
6.4 Upshift/Downshift Tables
Shift points are determined by MPH (miles per hour) and TPS (throttle position sensor) percent. Open the calibration “A”
folder then the shift points Cal A folder. There is a table, gure X, that when rst opened lets you view all the shift points
for each gear. This table controls the part throttle upshift and downshift parameters for each gear. There is a second set
of tables that are identical to this in the Calibration “B” folder. These give you the option of creating two distinct patterns,
such as Normal and Sport mode or Tow Haul mode etc. Keep in mind while editing this table that the WOT settings, if
enabled, contain your full throttle upshift and downshift parameters and should be matched to these tables. Also keep in
mind that your TPS input must be congured to determine what WOT throttle is.
You will notice that next to the shift lines are boxes with check marks. This lets you choose the shift lines that are plotted
in the chart. For explanation purposes, we have selected Low gear to high gear shift (upshift). A good example to walk
through is pictured in Figure X. The shift table below shows a 1st to 2nd gear shift with a purple line. In most congurations
you will want to use load (TPS or MAP) as an indicator of desired shift speed. At low load you will want a low shift speed
to keep the engine from revving too high. Maintaining a low shift speed will also lead to smoother shifting as line and
accumulator pressure are typically programmed for softer operation at low load. At high load you will want a high shift
speed to utilize full engine power before shifting. Your upshift points (purple line) should always be higher than your
downshift points (blue line). In each cell, the transmission will not upshift until reaching the speed value in the box for
each load point. Be careful not to exceed your maximum RPM with any speed value.
Shift points are determined by MPH (miles per hour) and TPS (throttle position sensor) percent. In the example below,
you will see we are in the Shift Table A, with all the boxes checked. This lets you view all the upshift and downshift lines.
Reference Figure 21 and Figure 22.
6.5 Wide Open Throttle (WOT) Upshift RPM A
There are setting for Wide Open Throttle engines RPMs for both Calibration “A” and Calibration “B”. These are used for
the upshifts only. You can set this to the desired engine RPM per gear. Reference Figure 23.

Page 14 Ph: 804.227.3023
10511 Old Ridge Rd. Ashland, VA 23005
v 2.1
Powertrain Control Solutions
Figure 24: Wide Open Throttle Downshift Speeds A
6.6 Wide Open Throttle (WOT) Downshift Speeds A
There are setting for Wide Open Throttle Downshift Speed settings for both Calibration “A’ and Calibration “B”. These are
used for the downshifts only. Set these to the point where you want to perform a downshift in each gear at 100% throttle.
The speed usually matches what is in you shift tables downshift point. With the RPM calculator, you can verify that the
speed you enter is lower than you upshift RPM. There should be approximately a 1800-2000 RPM delta between the
upshift and downshift Reference Figure 24.
NOTE: This function is only available if it is enabled and you have an RPM signal.
NOTE: In order to use the “Use Lockup Per Gear” setting must be checked. This gives you the ability to set the
TCC Lockup Points for each gear set. This is for experienced calibrators only. More information on these settings
is available in the full manual.
6.7 TCC Lockup Settings
The torque converter lockup settings need to be congured for each Calibration “A” and “B”, depending on what pattern
are being utilized.
The TCC Lockup Flags have setting to keep the converter applied during upshift, downshifts and during coast mode.
Enabling these settings.
The setting to enable control slip can be enabled to allow the converter to maintain a small amount of slip instead of
fully locking. This Feature can only be used on certain torque converters that were designed to run at a controlled slip.
Enabling this also requires conguring the TCC Settings under Setup info folder (see advanced user guide for further
information on calibrating these).
Use Lockup Per Gear. If this is unchecked the Single Point TC Lockup tables are used. This table has just apply and
release points and are used in conjunction with the TCC Lockup Parameters to set the lowest gear to use the apply and
release lines. Reference Figure 25.
Figure 25: Single TCC Lockup/Unlock A

PCS TCM2800 Quick Start Guide
Page 15
Ph: 804.227.3023
10511 Old Ridge Rd. Ashland, VA 23005 v 2.1
7 Datalogging
7.1 Datalogging Menu
Datalogging is one of the most powerful features offered by the TCM. It allows a user to see transmission behavior and
engine behavior. The extra analog and digital inputs offered by the TCM also allows the TCM to be used as a general
datalogging device for any other vehicle functions you may wish to record.
To begin a datalog, do the following:
1. The TCM power must be on and the TCM must be communicating/online with your computer.
2. Select “Datalog” from the le menu and double click“Start/Stop Datalogging” or double click on the “Start Log” button
on the toolbar. Reference Figure 26 and Figure 27.
3. A window will appear with the option to “Start Logging” and several datalogging rates will be offered. Choose your
datalogging rate and click on the “Start Log” button. When prompted, choose a le name and location for your datalog.
Reference Figure 28. As with calibration les you may want to choose a descriptive name including the time, date, and/
or application of your datalog. Once you have chosen a name and location, click save or press enter.
4. The software and your computer will now begin datalogging. You may view the transmission behavior through the
monitor screen while datalogging. When you have completed your datalog, you may click on the “Stop Logging”
button. This will complete your datalogging session and save your datalog le to the location you specied.
Figure 26: Datalog Dropdown
Figure 28: Choose File Name and Location/Start Logging
Figure 27: Start Log Button

Page 16 Ph: 804.227.3023
10511 Old Ridge Rd. Ashland, VA 23005
v 2.1
Powertrain Control Solutions
7.2 View Datalogs
Datalogs may be viewed with the Datalog Viewer software, Microsoft Excel or any other program that can handle tab
delimited values contained in the datalog. The Datalog Viewer software offers a much stronger set of capabilities and
datalogging viewing options; however we understand that many users may wish to use other tools or analysis methods
which do not fall within the scope of the TCM software. The datalog les use the le extension .tlg which is associated
with the Datalog Viewer Software; however this does not prevent users from opening the same le in Microsoft Excel.
To view a datalog, do the following:
1. Select “Datalog” from the le menu and double click “View. Datalogs”
2. A blank screen will appear. Click the “Load” button or go to File->Open and choose the location and name of your
datalog.
3. The datalog initially opens in graph view. o begin viewing the data, click in the boxes next to the data elds you wish
to see near the top of the screen. You may view this data in a tabular view by clicking the “Table View” button.
NOTE: You may also double click the datalog le to open it in the Datalog Viewer software.
ZOOMING
Several zooming options are available by right clicking your mouse button. You may zoom in by clicking on a beginning
time and an ending time for your graph selection. You may also choose to view all the data, zoom to a percentage, or
zoom to a particular time period.
HOTKEYS
Please refer to the hotkeys list for a complete listing of key options for navigating the datalog menu.
You may load another datalog or continue tuning at any time.
use the Communications -> Go Online command or CTRL-G to attempt to connect to the TCM again. If you are still
unable to connect to the TCM, please contact your dealer for support
LIMITED WARRANTY STATEMENT. Powertrain Control Solutions, LLC. Warrants all merchandise against defects in factory
workmanship and materials for a period of 12 months after purchase. This warranty applies to the rst retail purchaser and
covers only those products exposed to normal use or service. Provisions of this warranty shall not apply to Powertrain Control
Solutions, LLC. Product used for a purpose for which it is not designed, or which has been altered in any way that would be
detrimental to the performance or life of the product, or misapplication, misuse, negligence or accident. On any part or product
found to be defective after examination by Powertrain Control Solutions, LLC., Powertrain Control Solutions, LLC. will only repair
or replace the merchandise through the original selling dealer or on a direct basis. Powertrain Control Solutions, LLC. assumes
no responsibility for diagnosis, removal and/or installation labor, loss of vehicle use, loss of time, inconvenience or any other
consequential expenses. The warranties herein are in lieu of any other expressed or implied warranties, including any implied
warranty of merchantability or tness, and any other obligation on the part of Powertrain Control Solutions, LLC., or selling dealer.
This manual suits for next models
1
Table of contents
Other PCS Controllers manuals
Popular Controllers manuals by other brands
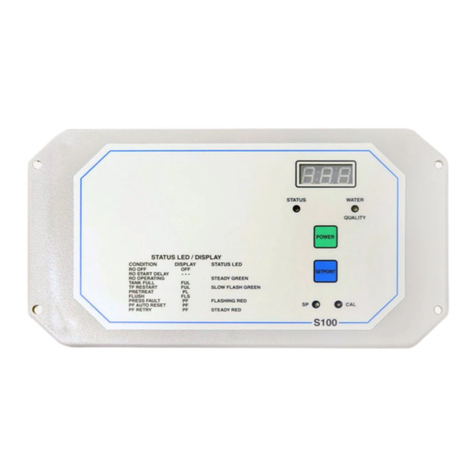
Crystal Quest
Crystal Quest C-100 installation manual

Siemens
Siemens SIRIUS 3SE5000-0A Series Original operating instructions
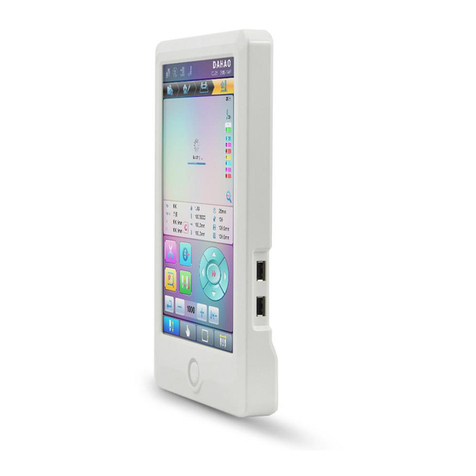
DAHAO
DAHAO BECS-A15 owner's manual
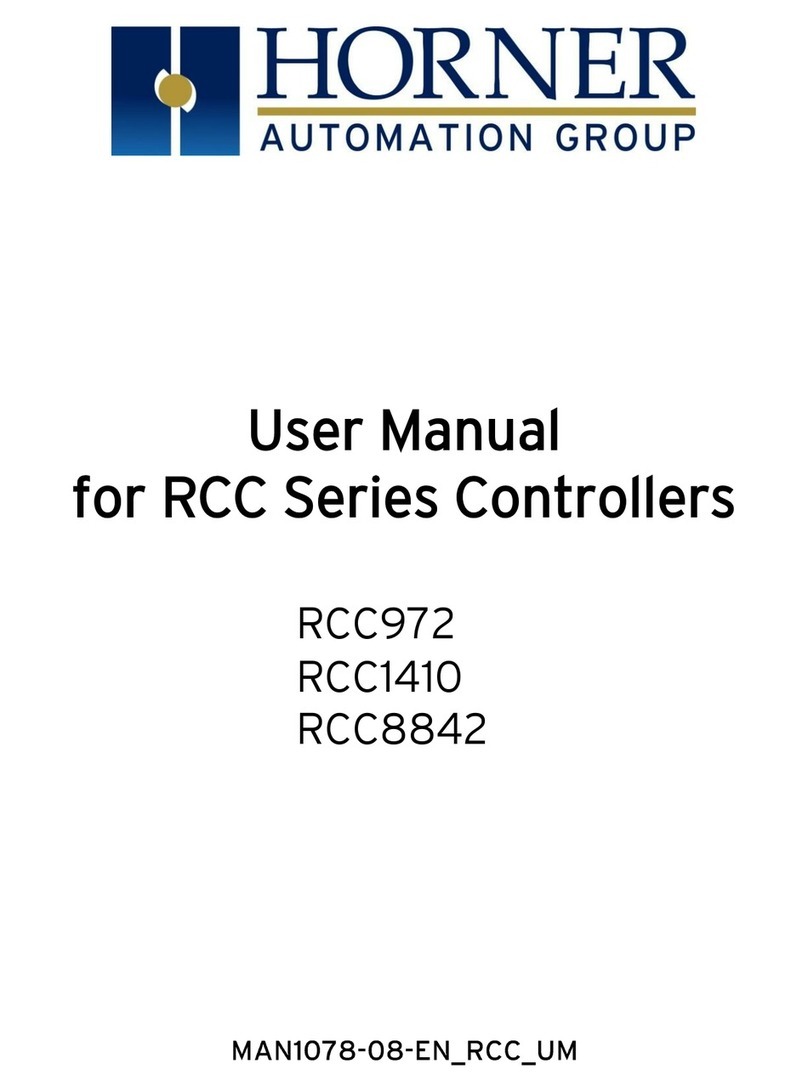
HORNER APG
HORNER APG RCC Series user manual
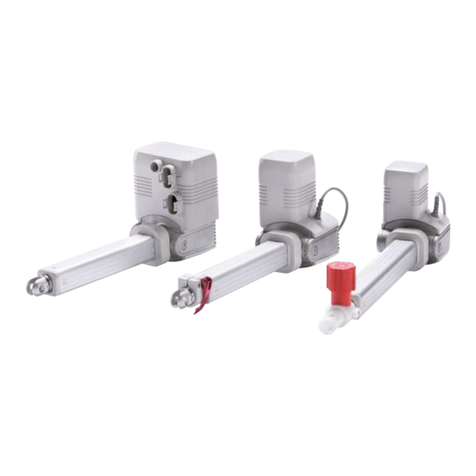
SKF
SKF Matrix Installation, operation and maintenance manual
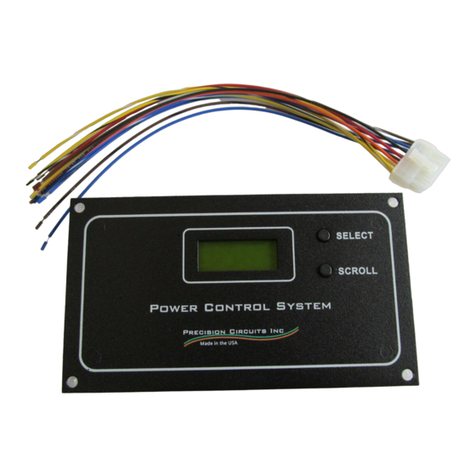
Precision Circuits
Precision Circuits Midi-PCS quick start guide