Phymetrix ExMa User manual



Please visit our website at www.phymetrix.com for other products that may be applicable to your
needs.
Every effort has been made to ensure accuracy in the contents of this manual. Should there be
any doubts to the accuracy of the content please contact the manufacturer.
The contents of this manual are subject to change without notice.
The instructions, procedures, drawings, specifications and concepts contained in this manual are
the property of Phymetrix Inc., and shall not be used as the basis for the manufacture or sale of
apparatus or services, or reproduced or copied or transmitted in any form or by any means
without written permission.
Read this manual before using the analyzer. For personal and system safety, and for
optimum product performance, make sure you thoroughly understand the contents
before installing, using, or maintaining this analyzer.

Warranty
This instrument is warranted, to the original end-user purchaser, against defects in materials and
workmanship. Liability under this warranty is limited to restoring the instrument to normal
operation or replacing the analyzer, at the sole discretion of the manufacturer. Batteries are
specifically excluded from any liability. This warranty is effective from the date of delivery to
the original purchaser. If Phymetrix determines that the equipment was defective, the warranty
period is:
• one year from delivery for electronic or mechanical failures
• one year from delivery for sensor shelf life
If Phymetrix determines that the equipment was damaged by misuse, improper installation, the
use of unauthorized replacement parts, or operating conditions outside the guidelines specified,
the repairs are not covered under this warranty.
Normal wear and tear, parts damaged by abuse, misuse, negligence or accidents are specifically
excluded from the warranty.
Purchaser acknowledges that in accepting and using this analyzer, notwithstanding any contrary
term or provision in the purchaser's purchase order or otherwise, the only warranty extended by
Phymetrix is the express warranty contained herein. Purchaser further acknowledges that there
are no other warranties expressed or implied, including without limitation, the warranty of
merchantability or fitness for a particular purpose; that there are no warranties which extend
beyond the description of the face hereof; that no oral warranties, representations, or guarantees
of any kind have been made by Phymetrix, its distributors or the agents of either of them, that in
any way alter the terms of this warranty; that Phymetrix and its distributors shall in no event be
liable for any consequential or incidental damages, including but not limited to injury to the
person or property of the purchaser or others, and from other losses or expenses incurred by the
purchaser arising from the use, operation, storage or maintenance of the product covered by the
warranty; that Phymetrix’s liability under this warranty is restricted to repair or replacement of
defective parts at Phymetrix sole option; and that Phymetrix neither assumes nor authorizes any
other person to assume for it any other warranty. The warranty shall be void if serial numbers
affixed to the products are removed, obliterated or defaced.

Return Policy / Procedures
If equipment malfunction is suspected or it is determined that the analyzer needs recalibration,
please contact Phymetrix.
Communicate the instrument model number, serial number, application including dewpoint
range being measured, and the details of the problem.
If the analyzer needs factory service you will be issued a RMA and shipping instructions.
The factory will diagnose the equipment and upon determining the problem will notify you
whether the terms of the warranty cover the required repair. If the costs are not covered you will
need to approve the estimated cost in order to proceed with the repair.

This page intentionally left blank

Table Of Contents
1Introduction............................................................................................................................. 1
2Important Principles of Operation .......................................................................................... 2
2.1 Sensor Operating Principle............................................................................................... 2
2.2 Sampling Mechanism Operating Principle ...................................................................... 2
3Precautions ................................................................................................................ 2
4Moisture System Considerations ............................................................................................ 3
4.1 Integrity of the Materials of the User’s System............................................................... 3
4.2 Moisture Back Diffusion (backflow) Along the Walls of the Exhaust Tubing ............... 3
4.3 Temperature Dependant Equilibrium............................................................................... 4
5Sampling Techniques.............................................................................................................. 4
5.1 Choosing a Measurement Site.......................................................................................... 4
5.2 Sample Conditioning........................................................................................................ 5
5.3 Tubing and Fittings .......................................................................................................... 5
5.4 Sample Pressure ............................................................................................................... 5
5.5 Pressure Considerations ................................................................................................... 6
6Installation............................................................................................................................... 8
6.1 Mechanical Installation.................................................................................................... 8
6.2 Electrical Connections: Power, 4/20mA Analog Output, Serial I/O................................ 8
6.2.1 Powering the ExMa................................................................................................... 8
6.2.2 Analog Output 4/20mA............................................................................................. 8
6.2.3 ExMa HART interface.............................................................................................. 8
6.2.4 Serial I/O RS485/RS-422........................................................................................ 10
7User Interface Overview....................................................................................................... 11
8Operating the Analyzer......................................................................................................... 12
8.1 The Display Mode.......................................................................................................... 12
8.2 Units to Display the Measurement................................................................................. 12
8.3 Pressure Correction........................................................................................................ 13
8.4 Navigating Through the Menus...................................................................................... 15
8.5 The Functions Available in the Menus .......................................................................... 15
9Data Logging ........................................................................................................................ 17
9.1 Retrieving the Data / Clearing the Memory................................................................... 18
9.2 Logging Data Directly into a Personal Computer.......................................................... 18
10 Single Point Calibration........................................................................................................ 18
11 Using the ExMa for temperature control.............................................................................. 19
12 Troubleshooting and Maintenance........................................................................................ 20
12.1 Cleaning...................................................................................................................... 20
12.2 Self Diagnostics.......................................................................................................... 20
12.3 Suspected Erroneous Measurements.......................................................................... 21
13 Specifications for Model ExMa............................................................................................ 23
Appendix A ExMa Installation Drawing................................................................................. 24
Appendix B ExMa Electrical Connections.............................................................................. 25
Appendix C Notes on ExMa use in low power applications e.g. solar power.............................. 28
Revision #3 2016

This page intentionally left blank
Revision #3 2016

1Introduction
Thank you for purchasing the state-of-the-art Phymetrix Explosion proof Moisture Analyzer
model ExMa.This User’s Manual describes the functions of this analyzer as well as the
operating methods and handling precautions. There are also some sections that review general
knowledge and concepts of water vapor science. Read this manual thoroughly before using the
analyzer. There is a Quick Setup Manual describing the main functions and basic procedures for
performing measuring operations. Check our website “www.phymetrix.com” for latest versions
of documentation regarding these analyzers.
After reading this manual, keep it easily accessible for future reference. It may come in handy
when there are some challenging measurements to be performed.
Conventions used in this manual:
•When using the word “system” in this manual we are referring to the user’s system in which
the moisture content is being measured. This could be a simple configuration of a pressurized
gas bottle with a pressure regulator, or a complex system of dryers, filters, regulators, long
tubing, valves etc.
•When referring to text that is displayed on the analyzer screen, it is presented in this manual
using a font that makes it stand out.
The analyzer part number is displayed upon power-up and in the About screen, the dash numbers
following the main part number signify options as follows:
-I for Explosion Proof certification, -P for internal pressure sensor,
-A for analog output 4/20mA, -R for Alarm Relays.
Check to see that your analyzer has arrived intact with all accessories that were ordered.
Model: ExMa shown with optional filter pressure regulator and exhaust flow meter
Save the packing materials until you have verified that there is no concealed damage, it may also
be useful for future transportation.
1

2Important Principles of Operation
2.1 Sensor Operating Principle
The nanopore sensor utilized in this analyzer measures the amount of water vapor molecules that
have entered its pores. This amount is directly proportional to the partial water vapor pressure in
the gas surrounding the sensor, and the partial water vapor pressure is dependant on the water
vapor content of the gas and the total pressure of the gas. Thus to compute the water vapor
content of the gas under measurement the analyzer has to “know” the total pressure of the gas. If
the analyzer was purchased with the pressure sensor option then the total pressure is measured
and utilized by the analyzer, if there is no built-in pressure sensor then the user should enter the
total pressure into the analyzer, this can be easily done by entering atmospheric pressure (the
analyzer default setting) and measuring at atmospheric pressure by allowing the outlet (exhaust)
port to vent without restrictions.
2.2 Sampling Mechanism Operating Principle
The analyzer is equipped with a built-in sampling system which has the required tight seals to
measure low moisture content; it consists of a stainless steel 100 micron filter and a flow control
orifice, which may be placed at either the inlet(factory default) or outlet of the sampling cell or
removed. The gas under measurement is exposed only to the stainless steel walls of the sampling
system.
3Precautions
•Observe the appropriate electrical safety codes and regulations. Consult with National
Electrical Code, and/or other nationally or locally recognized procedures relevant to your
location.
•When measuring flammable, explosive or toxic gasses; vent the sample outlet to a safe
and appropriate location.
•When measuring high pressure samples (do not exceed 5000 psia); be sure that the
system is depressurized before connecting or disconnecting the sample tubing.
•Corrosives such as Ammonia, HCl and Chlorine should be avoided; H2S and SO2can be
present if the moisture content is below 10 PPMv.
•Avoid extreme temperatures, pressures and mechanical vibration, refer to specifications.
•Do not disassemble the analyzer.
•Do not use with contaminants and liquids, refer to section 5.2 for sample conditioning.
•Avoid exposing the sensor to ambient air as it may slowdown your next measurement.
•The ExMa is weatherproof as long as the cover is tightly closed, and the conduit ports are
appropriately sealed.
•Designs with circuitry activated by relay contacts should consider noise from contact
bounce, an option for debouncing is placing an appropriately rated capacitor across the
relay contacts.
2

4Moisture System Considerations
This section is offered as background information. There are several considerations in keeping
your system at a stable and pure moisture level, free of contamination from ambient air moisture:
•The integrity of the materials isolating the pure gas from the external air, including leaks
from poorly secured fittings.
•The back diffusion of moisture through the exhaust outlet, the exhausts of both the
analyzer and the user system under measurement should be considered.
•The effects of temperature on the equilibrium of moisture and the surrounding materials,
often observed as diurnal cycles in the measurement.
4.1 Integrity of the Materials of the User’s System
Before considering the materials of a system where a specified dewpoint level must be
maintained, one should review two concepts.
•Compared to the structure of solids the water molecule is much smaller. This is true
compared to even the crystalline structure of metals but especially important in the
polymer structure of plastics.
•Water vapor pressure in gasses obeys Dalton’s law of partial pressures, which states that
the overall pressure of a gas is the sum of its constituent gases. And each gas seeks to
equilibrate its pressure across gradients of only its own gas pressure.
Let’s consider air in a pipe at a total pressure of 100 psia, which has been dried down to -40°C
dewpoint. The partial water vapor pressure in the pipe is 0.13mB. If the ambient temperature is
22°C with relative humidity of 30%, then the partial water vapor pressure in the surrounding
atmosphere is 7.9mB or approximately 60 times greater than the partial water vapor pressure in
the pipe. Thus even though the total pressure in the pipe is much greater that the pressure outside,
the reverse is true for the water vapor pressure, and as we discussed earlier the water vapor seeks
to equilibrate its pressure thus it “wants” to flow from the outside to the inside and will do so
through the cracks in the joints (such as poorly tightened fittings, or NPT threads even if they are
properly taped), as well as through the walls of pipes tubes and other vessels. The integrity of the
system is extremely important in maintaining a stable low dewpoint; for dewpoints below -60°C
always use stainless steel or PTFE, while for higher dewpoints you can use copper or galvanized
steel; but never use rubber, Tygon, Nylon or other plastic tubing. Pressure regulators often use
rubber diaphragms, check and if necessary replace with a stainless steel diaphragm regulator.
Filter bowls should be stainless steel or glass, plastic bowls should be avoided. If a flow meter is
placed at the inlet of the analyzer it should have a glass tube and be rated for the expected
pressure levels, however in general it is best to place flow meters at the analyzer exhaust.
Another material consideration relates to materials sealed in the system such as paper filters;
these may not contribute to leaks but will greatly slow down the measurement because they will
adsorb and desorb water molecules as the system dewpoint is changing.
4.2 Moisture Back Diffusion (backflow) Along the Walls of the Exhaust Tubing
The linear velocity of gas flowing in a tube is close to zero immediately along the wall of the
tube. This coupled with the previously discussed “need” for the moisture to flow from the higher
water vapor pressure to the lower one, allows for water molecules to flow against the total flow
through the exhaust outlet into the sampling chamber of the analyzer. The fact that water
3

molecules are highly polar further enhances their ability to migrate against the gas flow at the
sampling chamber outlet. To prevent this backflow of moisture from influencing the
measurement, the analyzer should have at least 12” in length of 1/8” dia. stainless steel tubing at
its exhaust port, and a minimum flow of 2 SCFH (1 SLPM) should be maintained; higher flows
will produce faster equilibrium time and thus are desirable for quick measuring. A small pigtail
(coiled 1/8” dia. ss. tubing 12” long) can be connected to the exhaust port of the analyzer. The
short tube with attached flow meter also provides protection from back diffusion of moisture.
4.3 Temperature Dependant Equilibrium
The effect of ambient temperature on the gas partial water vapor pressure of a system can change
the moisture content of the gas. This is not the temperature sensitivity of the measuring analyzer,
rather the actual change of partial water vapor pressure in the user’s system due to increase in
ambient temperature and thus the increase of energy of the water molecules on and in the walls
of the system (tubing, vessels etc…). A typical example would be the observation of a daily
cycling of the measurement in a system with tubing or other components exposed to direct
sunlight. During the day as the sun transfers energy into the system, the dewpoint will appear to
increase, while at night the dewpoint will appear to decrease. There may be other reasons for this
daily dewpoint cycling such as the effect of sun/temperature on the efficiency of gas dryers etc.
It is possible to minimize this effect using sun shields and tubing insulators. Alternatively one
may study the response of the particular system to ambient temperature, by logging data over
several days during different seasons, and compensating the measurements for this effect. The
temperature effect will vary greatly depending on the size and materials of the system, for
example stainless steel walls will have a much smaller effect than brass or copper walls.
5Sampling Techniques
The amount of moisture measured will be influenced by the system moisture content as well as
leaks in the system and transient effects of adsorption / desorption from materials in the system
(as described in the previous sections).
5.1 Choosing a Measurement Site
The ExMa has been designed to perform extractive measurements. It is important to choose an
appropriate sampling location that is representative of the moisture content of the system of
interest.
4

5.2 Sample Conditioning
Particulate and liquid contaminants can effect the measurement, especially the response time.
Sample conditioning may be necessary to remove contaminants and improve the measurement
and the longevity of the sensor. Make sure that sample conditioning components are made of
suitable materials. Avoid paper or other fiber filter elements, use stainless steel instead. For
expected dewpoints below -50°Cdp (39 PPMv), avoid plastic filter bowls, use stainless steel or
glass instead. Drain trapped liquids from filter bowls.
If the application is suspect of possible presence of liquids for example:
• Compressed air with possible oil and/or water,
• Gas Insulated Switchgear or Transformer, SF6or N2blanket with suspected oil carryover,
• Natural Gas with possible Triethylene Glycol carryover,
Consult with Phymetrix for specialized sampling systems.
5.3 Tubing and Fittings
Make sure all tubing is constructed of materials suitable for low dewpoint measurement, i.e.
stainless steel or Teflon, do not use rubber or plastic tubing (refer to section 4.1 for more details).
Check for leaks after connecting.
Flow meters can be a source of moisture ingress especially if they have a plastic flow tube;
ensure flow meters are connected at the analyzer exhaust, not at inlet. However metering valves
should be at the inlet in order to maintain constant atmospheric pressure in the sampling chamber.
5.4 Sample Pressure
Pressure variations will effect the measurement. Higher pressure is more likely to produce
condensation and thus erroneous readings or even damage the sensor. If the sample pressure
needs to be reduced use a suitable pressure dropping device such as a stainless steel needle valve
or pressure regulator with a stainless steel diaphragm or a flow control orifice. Make sure Joule-
Thomson effects do not cool the gas below hydrocarbon and water dewpoints.
5

5.5 Pressure Considerations
When sampling gases from sources above 50 psia the user needs to exercise some caution.
The model ExMa has a built-in orifice. This orifice can be used to regulate the flow from various
pressures.
• The sample cell has a built-in filter and flow control orifice at the inlet.
• On Request the orifice can be moved to the outlet to perform measurements at pressure.
The inlet orifice eliminates the need for any pressure regulators while maintaining sufficient but
not excessive flows throughout the pressure rating of the analyzer.
6

For example 0.004” to 0.016” dia. orifices, produces flows described in the following table.
The grayed boxes are preferred operating points. Other orifices can be provided to accommodate
different pressures and flows. Consult PhyMetrix support for its proper sizing.
Measuring with the ExMa, Near Atmospheric Pressure
It is recommended for most applications to perform the measurement at near atmospheric
pressure. Placing the flow control orifice at the inlet and allowing the outlet to be unrestricted
(other than the exhaust pigtail and flow meter), assures that the analyzer has sufficient but not
excessive flow and the pressure inside the sampling chamber is near atmospheric. This approach
guarantees safe conditions and eliminates the need for the optional pressure sensor. If there is no
pressure sensor the analyzer can be set with atmospheric pressure 14.7psia for the Mea. at
setting of the pressure correction (refer to section 8.3), the orifice and unrestricted outlet will
guarantee repeatable conditions for all pressures within the rating of the orifice.
Measuring with the ExMa, at Pressure of Sample
If it is desired to perform the measurement at the same pressure as the sample, up to the rating of
the analyzer (5000 psia standard), then place the orifice at the outlet.
The analyzer is now setup with the orifice at the outlet, thus the measuring chamber will be
pressurized to the same pressure as your sample. To perform accurate measurements, you must
know the pressure and enter it into the analyzer, or order the optional built-in pressure sensor
which will perform the measurement and correction automatically.
source pressure
psia - (Bar)
flow
SLPM
0.016” orifice
flow
SLPM
0.012” orifice)
flow
SLPM
0.008” orifice
flow
SLPM
0.006” orifice
flow
SLPM
0.004” orifice
15 - (1.03)
0.7
0.4
0.17
0.08
0.04
25 - (1.72)
2
1.3
0.6
0.3
0.1
35 - (2.4)
3
1.9
0.8
0.5
0.2
55 - (3.8)
4.8
3.0
1.4
0.7
0.3
75 - (5.2)
6.6
4.1
1.9
1.0
0.4
100 - (6.9)
8.9
5.5
2.6
1.4
0.6
150 - (10.3)
13.4
8.3
3.8
2.1
0.9
200 - (13.8)
17.9
11.0
5.1
2.7
1.1
300 - (20.7)
26.8
16.6
7.7
4.1
1.7
400 - (27.6)
35.7
22.1
10.3
5.5
2.3
500 - (34.5)
44.7
27.6
12.8
6.9
2.9
600 - (41.4)
53.6
33.1
15.4
8.2
3.4
700 - (48.3)
62.5
38.7
18.0
9.6
4.0
800 - (55.1)
71.5
44.2
20.5
11.0
4.6
900 - (62)
80.4
49.7
23.1
12.4
5.1
1000 - (68.9)
89.3
55.2
25.7
13.7
5.7
1500 - (103.4)
134.0
82.8
38.5
20.6
8.6
2000 - (137.9)
178.7
110.5
51.3
27.5
11.4
7

6Installation
6.1 Mechanical Installation
The ExMa can be mounted directly on the pipe or can be mounted on a panel surface and
connected with tubing. Refer to Appendix A ExMa Installation Drawing.
Connections for inlet and outlet of the gas being measured are made through a variety of
available options e.g. ⅛” or ¼” Swagelok® tubing compression fittings.
Refer to Mechanical Installation Drawing Appendix A.
6.2 Electrical Connections: Power, 4/20mA Analog Output, Serial I/O
6.2.1 Powering the ExMa
The ExMa has two (2) standard modes of being powered.
1) AC powered from 90-260 VAC 47-440 Hz
2) DC powered from a 12 – 24 VDC 10VA power supply
Optionally the ExMa can be ordered to also operate in 4/20mA Loop Powered mode.
Refer to the ExMa Electrical Connection diagram in Appendix B for the various power modes
and the specific wiring for each mode.
6.2.2 Analog Output 4/20mA
The ExMa has an isolated 4/20mA output, which may be connected as a sink in configurations
where the power is provided externally, or if the ExMa is actively powered (modes 1&2) the
4/20mA can be configured to source the current.
Refer to the ExMa Electrical Connection diagram in Appendix B for the 4/20mA
configurations and specific wiring for each.
The ExMa status bar will have an Analog Output Loop Open message if the 4/20mA output is
not connected. The user menus allow the user to force the 4/20mA output to known values for
purposes of testing and calibrating the 4/20mA interface, refer to section 8.5.
6.2.3 ExMa HART interface
The ExMa is equipped with a HART interface which overlays digital signals on the 4-20mA
loop current. Thus the ExMa can be used in any 4-20mA loop and can simultaneously
communicate digitally on the same two wires.
The ExMa responds to all of the HART Universal (Common Practice) Commands as well as
some important setup and configuration commands.
When wiring the ExMa for use with HART make sure that there is sufficient resistance between
the power supply and the ExMa 4/20 interface. Usually there is a 250 Ohm resistor used for
sensing the current this is adequate to provide the proper impedance isolation for HART modems
to operate properly.
8

HART Commands Implemented in the ExMa
HART Command
Description
#
Name
0
Read Unique Identifier
Read Device identification such as address, manufacturer, revision
level etc.
1
Read Primary Variable
Read the measurement of the Primary Variable (P.V.)
2
Read Current and % of range
Read the current that is produced by the Primary Variable and the
percent of range it represents. These depend on the command #51
measurement assigned to the P.V., the value of that measurement and
the assignments of command #35.
3
Read Dynamic Variables and
P.V. current
Read the measurements of up to 4 measurement variables as assigned
by command # 51.
6
Write Polling Address
Assign a polling address to a device. An address (1-15) puts the
device in fixed 4mA mode for multidrop connectivity. Address 0 puts
the device in 4/20mA mode.
11
Read Unique Identifier
Associated with Tag
Find device that has the desired textual Tag assigned by
command # 18.
12
Read Message
Read information written by command # 17.
13
Read Tag, Descriptor and Date
Read information written by command # 18.
14
Read P.V. Sensor Information
Information on primary sensor Serial Number, range etc.
15
Read P.V. Output Setup
Analog output range, alarms etc.
16
Read Final Assembly Number
Read number written by command # 19.
17
Write Message
For use by owner/operator to identify the device and its use.
18
Write Tag, Descriptor and Date
For use by owner/operator to identify the device and its use. Can
search for the Tag, with command # 11, on multidrop connections.
19
Write Final Assembly Number
For use by owner/operator to identify the device and its use.
35
Write Primary Variable
Range Values
Setup the measurement units and values that correspond to 4mA and
20mA output of the loop.
40
Analog Out Fixed
Forces the Analog Output DAC to a specified value.
44
Write Primary Variable Units
Select the units of measure for the Primary Variable.
45
Trim DAC Zero
Trims the DAC Zero by difference of Cmnd. #40 and observed value.
46
Trim DAC Gain
Trims the DAC Gain by ratio of Cmnd. #40 and observed value.
50
Read Dynamic Variable
Assignments
Read the assignments of
command # 51.
Measurement Variables and [available units]:
00 – Moisture Measurement
°C & °F dewpoint, ppmV, mB H2O vapor pressure,
grams of H2O / m3and
Lbs H2O /106standard cubic feet in Natural Gas
01 – Temperature of Gas [ °C, °F ]
02 – Temperature of Board [ °C, °F ]
03 – Pressure [ psi, bar, mbar, kg/sqcm, pascal …]
08 – Loop Voltage [ mV ]
09 – Status Bits
51
Write Dynamic Variable
Assignments
Assign Measurement
Variables to each of the four
primary variables reported by
the analyzer by command # 3.
53
Write Transmitter Variable
Units
Select Units of measure for
each of the Variables.
108
Write Burst Command Number
Select command number to burst.
109
Burst Mode Control
Enable/Disable burst (continuous) transmissions.
A free of charge program may be downloaded from our website www.phymetrix.com that
allows communicating with the ExMa HART interface.
9

The ExMa HART interface Address is the Instrument Serial Number which can be seen in the
About menu. The ExMa can be set up to operate in HART polling mode by selecting a polling
address 1-15 in the HART user interface menu, in this mode multiple (up to 15) ExMa's or other
HART devices can communicate on the same loop but each device consumes only 4mA.
6.2.4 Serial I/O RS485/RS-422
The ExMa can optionally provide a RS-485/422 interface in power modes 1 and 2. Refer to the
ExMa Electrical Connection diagram in Appendix B for connections. The default
communication port settings are 19200, E, 7, 2; however they can be modified in the COMsuser
interface menu.
10

7User Interface Overview
The analyzer user interface consists of a backlit graphic LCD display, an audio sounder and four
touch areas on the glass cover of the explosion proof enclosure. These touch areas provide the
button functions which are dependant on the required selection choices, thus appropriate legends
appear on the display immediately above the touch areas. For ease of discussion we will refer to
these touch areas as “buttons” in the rest of the user’s manual. To “press” a button, the user must
touch the appropriate metal colored oval area on the glass with a finger. It may be necessary to
press the finger firmly on the glass to get a wide contact area. When a button is activated a small
light will be illuminated immediately above the touch area.
Note: A personal computer Virtual Analyzer program is available on our website
(www.phymetrix.com) allowing the user to familiarize themselves with the user interface and
train on its operation.
Note that the analyzer distinguishes between long and short presses of the glass touch areas
(buttons). Normally to operate the analyzer one must perform short presses (less than 1
second), the button must be released after the beep.
11

8Operating the Analyzer
Performing measurements with the analyzer is a simple process:
•Connect the sample gas to the analyzer (refer to section 5.2 and section 6.1)
•Connect Power and Signals to the analyzer (refer to section 6.2)
•If possible adjust the flow of the gas to be greater than 1 LPM (2 SCFH)
•Select the graphing display mode
•Observe the reading once the graph is stable
•Change the display mode if desired
8.1 The Display Mode
Once powered, the analyzer will enter one of three display modes (whichever was last used) that
show the measurements performed by the analyzer. Pressing the Disp button will change the
display mode. Use the mode best suited for your application.
•Dewpoint Units and Graph of the measured dewpoint in the last 90 minutes is displayed.
The graph span (Y-axis above shown 40°Fdp) will automatically resize to accommodate
the minimum and maximum measurements in the last 90 minutes. Select between 90 or 3
minute time axis by choosing Continuous or Spot measurement modes in the ModeOf
Use option available in MENU-2.
•Pressure corrected and at pressure measurements, as well as the gas pressure in the
sampling chamber is displayed. The pressure correction selection in this display mode
will be also utilized in the other two display modes. If pressure correction is enabled, then
the status bar will provide an indication in all three display modes, so that the user is
made aware that the displayed measurement is pressure corrected. In the example shown
above, the pressure correction is disabled.
•Dual Dewpoint Units and Temperature of gas under measurement is displayed. Allows
the user to view the measurement in two different units as well as the temperature in the
sampling chamber. In the right most screen in the example above the moisture content is
being viewed in °C and in ppm by volume, while the temperature is displayed to be
21.5°C.
8.2 Units to Display the Measurement
Measuring water vapor content in gasses presents many challenges not the least of which is
understanding the units of measuring. Different industries require different units of measure for
various reasons some technical some historical. The units typically used are in several categories:
12
Table of contents
Other Phymetrix Measuring Instrument manuals
Popular Measuring Instrument manuals by other brands
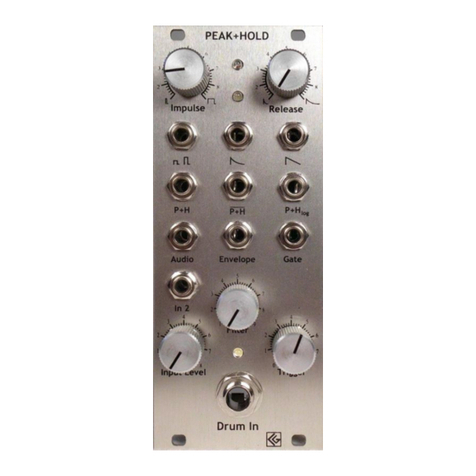
CG Products
CG Products Peak & Hold manual
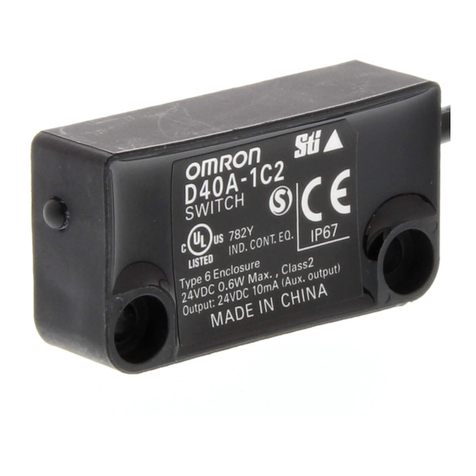
Omron
Omron G9SX Series user manual
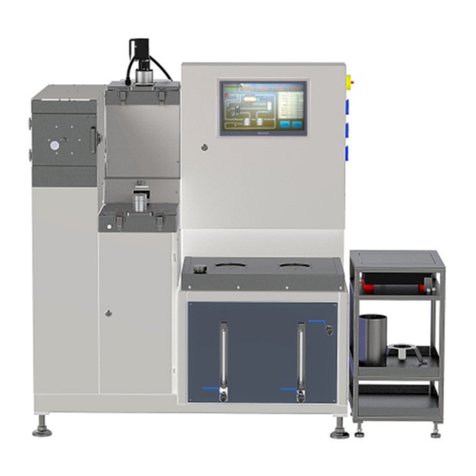
C-Tech
C-Tech HTHY-8159 product manual
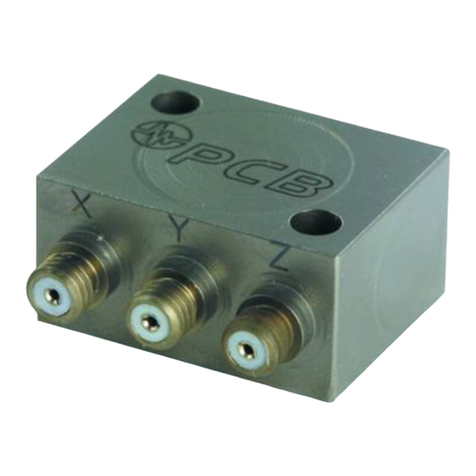
PCB Piezotronics
PCB Piezotronics M356A71 Installation and operating manual
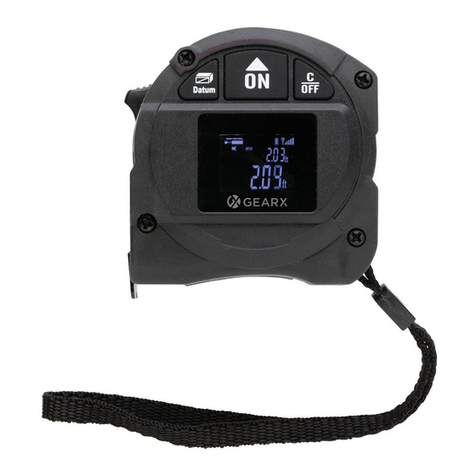
Gearx
Gearx P113.211 manual
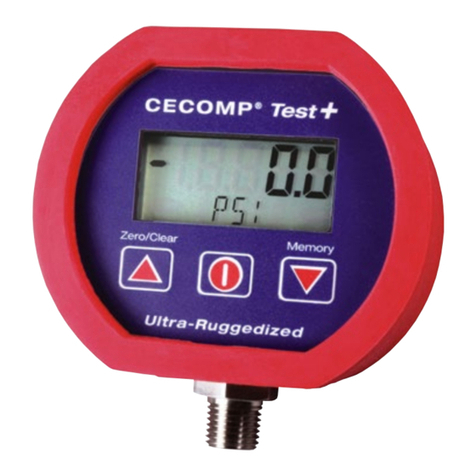
Absolute Process Instruments
Absolute Process Instruments Cecomp Test+ CTP3B instructions
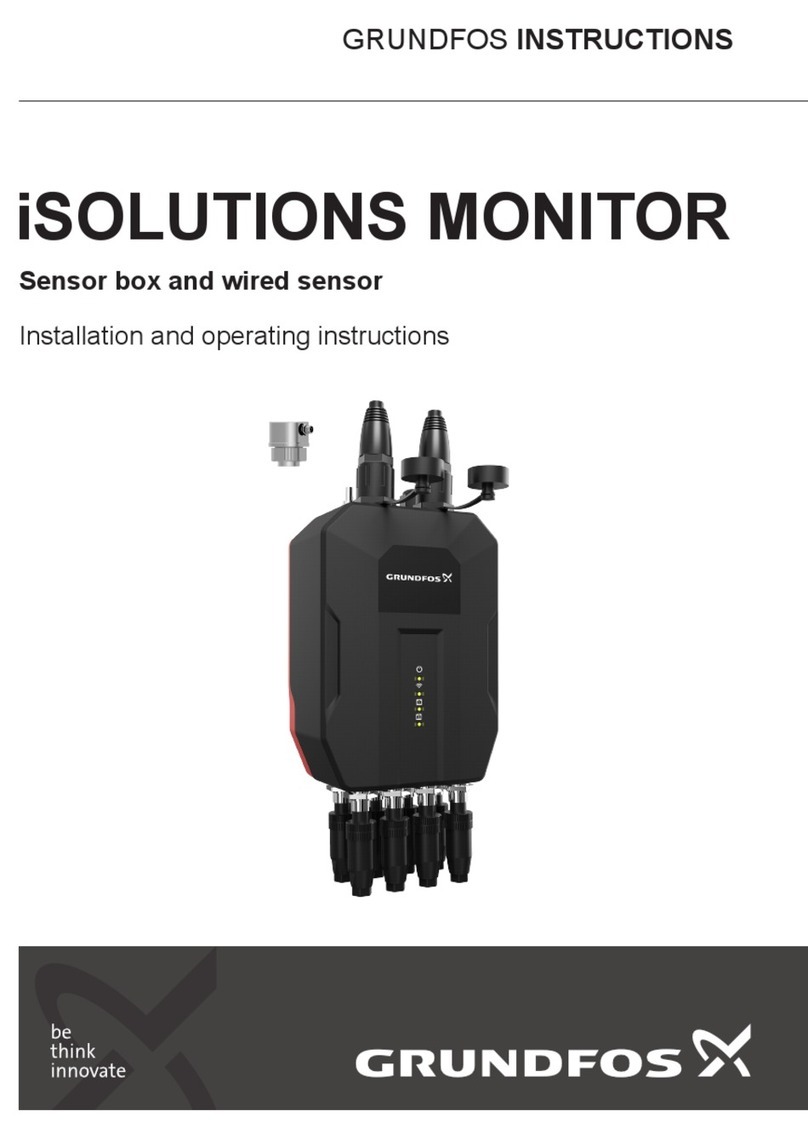
Grundfos
Grundfos iSolutions Monitor Installation and operating instructions
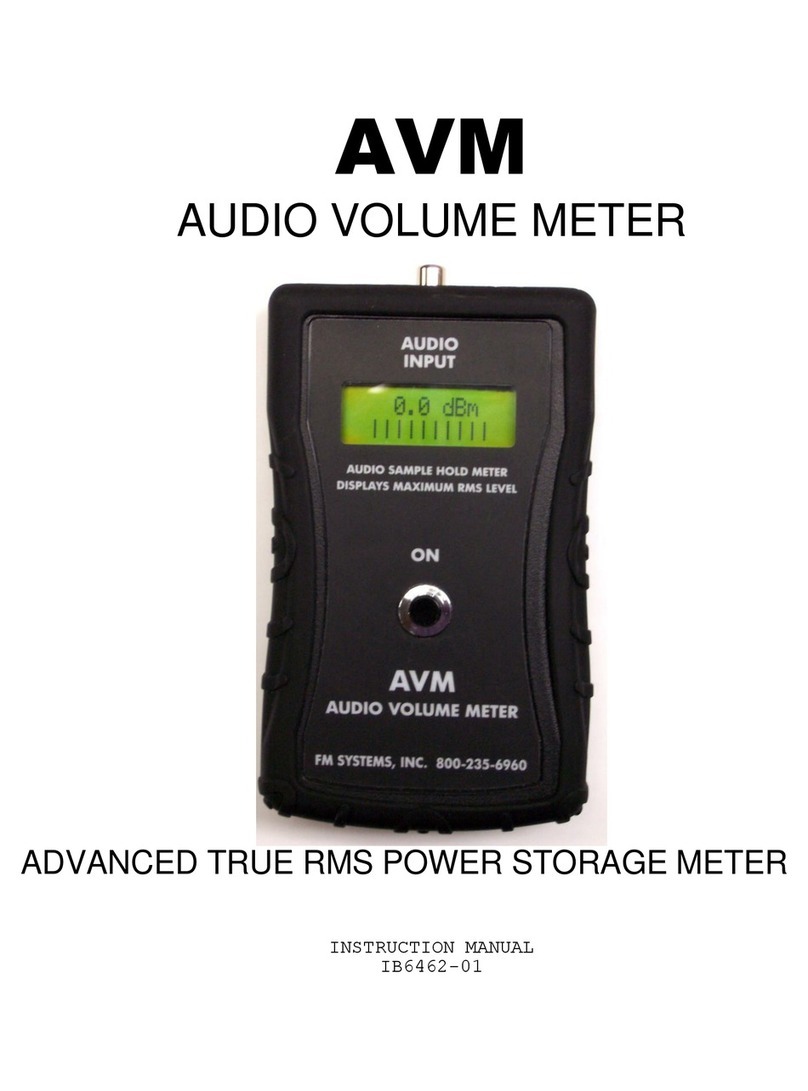
FM Systems
FM Systems AVM manual
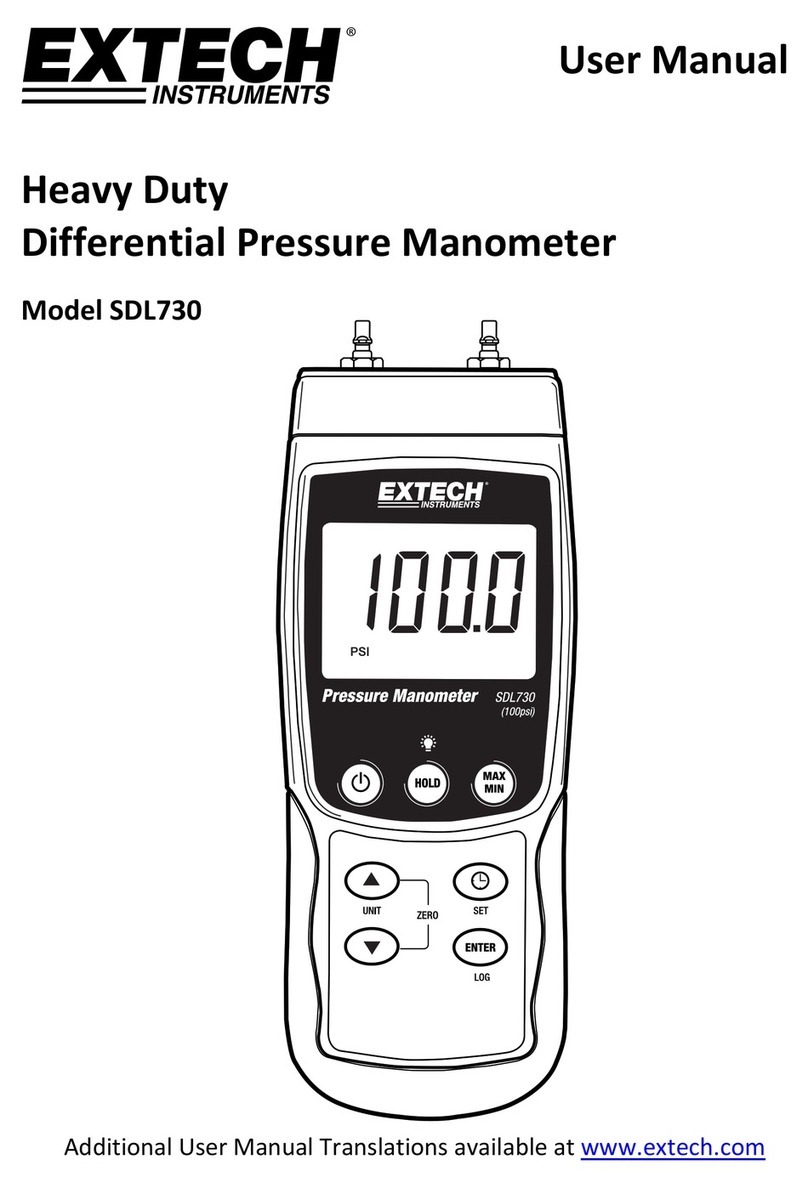
Extech Instruments
Extech Instruments SDL730 user manual

yellow jacket
yellow jacket 69008 Operation manual

DMQ
DMQ QS5 Series user manual

Galaxy Audio
Galaxy Audio Check-Mate CM-140 instruction manual