Piranha B Series Guide

B-Series & C-Series Plasma Cutting System
Safety, Operation, and Maintenance Manual
With Microstep Gen 2
Original Instruction: English Version 2.7.1

Piranha Plasma Table 2
Revision and Validity
Revised 11/9/2020
Starfire Software version 3.1-2.8.4-FAT and newer
Valid for Machines with Microstep Generation 2 as seen below
Copyright
This manual, including addendums, supplements, and other additions, is protected by
copyright. All rights reserved. No part of this publication can be reproduced, transmitted,
translated, or transferred, without the written consent of Piranha, subsidiary of
MegaFab.
© MegaFab 2019

INTRODUCTION 3
Table of Contents
Table of Contents....................................................................................................................... 3
Chapter 1: INTRODUCTION...................................................................................................... 7
1.1. About Piranha.................................................................................................................. 7
1.2. Contact Information ......................................................................................................... 7
Chapter 2: SAFETY ................................................................................................................... 8
2.1. Introduction...................................................................................................................... 8
2.2. Safety Symbols Used in the Manual................................................................................ 8
2.3. All Users.......................................................................................................................... 9
2.3.1. Supervisors............................................................................................................... 9
2.3.2. Maintenance Personnel............................................................................................10
2.3.3. Operator...................................................................................................................11
2.4. Personal Protection........................................................................................................12
2.4.1. Eye Protection..........................................................................................................12
2.4.2. Noise........................................................................................................................13
2.5. Safety Devices................................................................................................................14
2.6. Risk of Electric Shock.....................................................................................................15
2.6.1. Input Connections....................................................................................................15
2.6.2. Grounding................................................................................................................16
2.7. Fumes and Air Contamination ........................................................................................17
2.7.1. Toxic Fumes ............................................................................................................17
2.7.2. Air Contamination.....................................................................................................17
2.7.3. Metal Fumes............................................................................................................18
2.7.4. Metal Dust................................................................................................................18
2.7.5. Internal Ventilation System.......................................................................................19
2.8. Fire, Explosion, and Burn Prevention..............................................................................20
2.8.1. Hot Surfaces............................................................................................................20
2.8.2. Heat.........................................................................................................................21
2.8.3. Sparks......................................................................................................................21
2.8.4. Burn Prevention .......................................................................................................22
2.8.5. Cutting Aluminum on a Water Table.........................................................................22
2.9. Light and Radiant Energy...............................................................................................23
2.10. Compressed Gas Equipment........................................................................................24
2.10.1. Cylinders................................................................................................................24

Piranha Plasma Table 4
2.10.2. Pressure Regulators...............................................................................................24
2.10.3. Hoses.....................................................................................................................25
2.11. Additional Safety Information........................................................................................26
Chapter 3: SPECIFICATIONS...................................................................................................28
3.1. Machine View.................................................................................................................29
Chapter 4: INSTALLATION.......................................................................................................31
4.1. Introduction and Checklist ..............................................................................................31
4.2. Prior To Receiving..........................................................................................................33
4.2.1. Floor Condition.........................................................................................................33
4.2.2. Space/Location/Weights...........................................................................................33
4.3. Electrical Services..........................................................................................................35
4.3.1. CNC Control.............................................................................................................35
4.3.2. Plasma System........................................................................................................35
4.3.3. Earth Ground ...........................................................................................................35
4.4. Compressed Air & Gas...................................................................................................36
4.4.1. Air Connection Requirements...................................................................................36
4.4.2. Gas Supply Requirements .......................................................................................36
4.4.3. Option A: Air Dryer Unit............................................................................................36
4.4.4. Option B: Three-Stage Filter System........................................................................36
4.5. Fumes & Smoke Extraction Plan....................................................................................37
4.5.1. Exhaust Fan.............................................................................................................37
4.5.2. Water Table .............................................................................................................37
4.6. Required Equipment/Tools .............................................................................................38
4.7. After Receiving...............................................................................................................40
4.8. Unloading.......................................................................................................................40
4.8.1. Lifting with Crane (Recommended)..........................................................................41
4.8.2. Lifting with a Forklift .................................................................................................43
4.9. Unpacking ......................................................................................................................46
4.10. Installing Covers (5’ X 10’ Only)....................................................................................47
4.11. Leveling........................................................................................................................48
4.12. Machine and CNC Connections....................................................................................50
4.12.1. Air to Machine........................................................................................................50
4.12.2. Electrical Connection CNC Control.........................................................................50
4.13. Plasma Power Supply Connections..............................................................................53
4.13.1. For Hypertherm Powermax plasma system furnished by Piranha:..........................53

INTRODUCTION 5
4.13.2. For Hypertherm Powermax power supply not purchased from Piranha..................55
4.14. First Time Power On.....................................................................................................59
Chapter 5: OPERATIONS.........................................................................................................60
5.1. Operator’s Panel.............................................................................................................60
5.2. CNC Control Navigation .................................................................................................61
5.3. Using the Torch Height Control.......................................................................................63
5.4. Operating Start Guide.....................................................................................................64
5.4.1. Powering the Machine On and Sending to Machine Home.......................................66
5.4.2. Prepare the Plasma Power Supply and Torch..........................................................69
5.4.3. Setting the Torch Height Controller ..........................................................................71
5.4.4. Setting Pierce Delay Time........................................................................................73
5.4.5. Adjusting Speeds.....................................................................................................74
5.4.6. Methods of Loading Programs .................................................................................76
5.4.7. Editing and Saving Files...........................................................................................82
5.4.8. Verify Program with View.........................................................................................84
5.4.9. Set Program Zero.....................................................................................................86
5.4.10. Verify Program Size on Material with Outline .........................................................87
5.4.11. Setting Kerf Offset (Optional) .................................................................................88
5.4.12. Automatic Operation...............................................................................................89
5.4.13. Stopping the Machine.............................................................................................90
5.5. Active Functions.............................................................................................................91
5.6. Restarting a Cut..............................................................................................................92
5.6.1. Background Information on Restarting.....................................................................92
5.6.2. Cycle Stop................................................................................................................93
5.6.3. Using Section to Restart...........................................................................................94
5.6.4. Break Point Resume ................................................................................................96
5.7. Trim Cuts........................................................................................................................98
5.8. Finding Correct Arc Voltage when Cutting Copper........................................................100
5.9. Test Mode (Dry Run)....................................................................................................102
5.10. Other Functions..........................................................................................................103
5.10.1. Rotate ..................................................................................................................103
5.11. Nesting.......................................................................................................................104
5.12. Database....................................................................................................................107
Chapter 6: PROGRAMMING...................................................................................................108
6.1. Programming Codes.....................................................................................................110

Piranha Plasma Table 6
6.1.1. G Codes.................................................................................................................110
6.1.2. M Codes ................................................................................................................111
Chapter 7: MAINTENANCE ....................................................................................................112
7.1. Error Code List .............................................................................................................113
7.2. Machine Setup Parameters ..........................................................................................116
7.3. Initial Settings –Microstep Torch Height Control ..........................................................118
7.4. Inputs and Outputs.......................................................................................................119
7.5. Procedure - Setting Machine Zero................................................................................120
7.6. Updating Control Software Procedure ..........................................................................123
7.7. Squaring the Machine Procedure..................................................................................124
7.7.1. Determine How Much Out of Square the Machine is:.............................................124
7.7.2. Adjust the Squareness...........................................................................................124
7.8. Troubleshooting Guide .................................................................................................129
Chapter 8: PARTS MANUAL...................................................................................................132
8.1. Automatic Height Control Assembly..............................................................................132
8.2. Y-Axis Drive Assembly .................................................................................................134
8.3. Air and Water Inlet........................................................................................................135
8.4. X-Axis Drive Assembly .................................................................................................136
8.5. Electrical Cabinet..........................................................................................................137
8.6. Electrical Cabinet..........................................................................................................138
8.7. Miscellaneous Parts .....................................................................................................139
Chapter 9: ELECTRICAL DIAGRAM.......................................................................................141
9.1. Machines without Pipe Cutter.......................................................................................141
9.2. Machines with Pipe Cutter............................................................................................142
Chapter 10: PIPE CUTTING ATTACHMENT (Optional)..........................................................143
10.1. Components:..............................................................................................................144
10.2. After Receiving...........................................................................................................146
10.3. Unloading...................................................................................................................146
10.3.1. Lifting with Crane (Recommended)......................................................................147
10.4. Operation and Programming.......................................................................................153
10.4.1. Switching from Plate-Cutting to Pipe-Cutting........................................................153
10.4.2. Programming the Pipe Cutter...............................................................................156
10.4.3. Switching from Pipe-Cutting to Plate-Cutting........................................................157
Chapter 11: APPENDIX A - REVISIONS TO THE MANUAL...................................................160

INTRODUCTION 7
Chapter 1: INTRODUCTION
1.1. About Piranha
Piranha is a subsidiary of MegaFab, based in Rockford Illinois. MegaFab is a
manufacturer of metal fabrication machinery, including laser cutting machines, plasma
cutting machines, ironworkers, press brakes, bending rolls, combination punching and
cutting machines, and structural steel punching equipment. Equipment is sold under the
Piranha, Whitney, and Bertsch brands.
1.2. Contact Information
Congratulations on the purchase of a genuine Piranha Plasma Machine. If there are
questions regarding the machine, or if you need help, please use the following:
For technical support:
Via Phone: 815.490.0473
For ordering parts and consumables:
Via Phone: 800.338.5471
Please have the serial number or model ready when calling.
Piranha
650 Race St. • P.O. Box 1206
Rockford IL 61105, USA
www.piranhafab.com

Piranha Plasma Table 8
Chapter 2: SAFETY
2.1. Introduction
Read this chapter on safety and the sections of vendor components manuals on safety
before beginning to operate the Piranha Plasma Cutting Table.
Do not become complacent about safety or completely dependent on safety devices.
2.2. Safety Symbols Used in the Manual
This document uses the following symbols to highlight areas of importance.
Note:
Indicates information easily overlooked, or of special
importance.
Caution
Indicates a hazardous situation with low risk that could
result in minor injury and/or damage to machine.
Danger
Indicates a hazardous situation with high risk that could
result in injury or death.
Please do not underestimate the importance of other text not designated by any symbols.
Warning
Indicates a hazardous situation with medium risk that
could result in moderate injury.

SAFETY 9
2.3. All Users
Read this manual thoroughly before operating the machine.
Read the Torch Height Control Manual before operating the machine.
Read the CNC Control Operator Manual before operating the machine.
2.3.1. Supervisors
It is very important that a safe and appropriate working environment is provided for this
Piranha equipment and in compliance with applicable federal and local industry
standards.
It is imperative that programmers, machine operators and maintenance personnel be
trained adequately in the use and care of the equipment. These employees should
receive the proper instruction in order to have a complete understanding of the operation
of this machine before beginning to program, operate or service it.
Careful programming and debugging of new programs is essential for successful
operation of this machine. Use program Stop Codes to stop machine motion for operator
removal of parts or scrap.
Never allow operators to place any part of their body into the machine while the machine
is active. Ensure that all personnel understand the function and use of EMERGENCY
STOP and CYCLE STOP button.

Piranha Plasma Table 10
2.3.2. Maintenance Personnel
Only qualified personnel should make repairs on this equipment. Use caution and follow
Piranha procedures when working on the machine. Be sure to observe the following
guidelines:
1. Before performing maintenance or repair, turn the power OFF and follow lock
out/tag out (zero energy shutdown) procedures. Also, follow any lock out/tag out
procedures applicable to your specific plant requirements.
2. Wear safety glasses and other personal protective equipment as required by
applicable federal, local industry, and plant safety program standards.
3. Wear proper clothing. Do not wear watches, rings, jewelry, or loose-fitting
clothes.
4. Read and review the manual carefully.
5. Be familiar with the operation of the machine.
6. Practice preventative maintenance. Inspect the equipment regularly and repair or
replace worn components and tooling. Read the vendor components manuals for
any additional preventative maintenance.
7. Always replace safety guards and other safety devices removed for service and
make sure that they are fully functional before operating the equipment.
8. Never remove, jumper out or bypass a safety device to permit machine
production.
9. Never place yourself in a hazardous situation to observe a problem and ask
someone else to operate the machine. This could be a very dangerous and life-
threatening situation.

SAFETY 11
2.3.3. Operator
This equipment has been designed with operator safety in mind (when used under normal
operating conditions). The user must always be alert to the possibility of dangerous
situations. Always exercise care and caution. Report any minor problems immediately, so
that they can be corrected before becoming major difficulties. Only qualified personnel
should make repairs on the machine.
1. Be familiar with the machine. Read and review the Piranha and vendor
component manuals carefully.
2. Be alert to the significance of the various warning indicators and be conscious of
the functions of pushbuttons and other controls. Use the controls properly.
Review and understand the operation of the EMERGENCY STOP function and
the CYCLE STOP function.
3. Never operate the equipment unless it is in good working order.
4. Wear safety glasses and other personal protective equipment as required by
applicable federal, local industry and plant safety program standards.
5. Wear proper clothing. Do not wear watches, rings, jewelry or loose-fitting clothes.
6. Avoid all moving parts of the machine or workpiece when setting up or operating
the equipment. Never reach into the machine while it is active. Use the
EMERGENCY STOP or CYCLE STOP function to stop machine motion. Never
use the machine Dwell time code for parts removal or other operator intervention
activities that puts the operator in a hazardous position.
7. Recognize and avoid unsafe operating conditions.
8. Maintain a clean work area. Avoid accidents by keeping work areas clean and
neat.
9. Never leave the machine in an unsafe condition.
10.Never leave a machine running unattended.
11.Never remove or bypass safety devices.
12.Report any unsafe conditions, personal injury or machine problems immediately
to your appropriate supervisor(s) and safety manager(s). In case of personal
injury, notify Piranha Service Department giving a brief description and date
reported injury occurred.
13.Never operate the machine with someone within a hazardous area.

Piranha Plasma Table 12
2.4. Personal Protection
▪Keep the operator’s body and clothing dry.
▪Do not stand, sit, or lie in/on any wet surfaces when using this equipment.
▪Never work in a damp or wet area without proper insulation against electric
shock.
▪Disconnect main power before servicing the torch, power supply or service
connections to the plasma arc system, or any part of the machine bed.
▪Wear adequate personal equipment (overalls, gloves, safety boots etc.) when
operating the machine.
▪Remove or secure articles of clothing, such as ties and loose sleeves, which may
catch or be drawn into moving machinery.
2.4.1. Eye Protection
LENS SHADE
Arc Current
AWS (USA)
ISO 4850
Up to 100A
No. 8
No. 11
100 –200A
No. 10
No. 11 –12
200 –400A
No. 12
No. 13
Above 400A
No. 14
No. 14
Medical treatment facilities and a qualified first aid person should be available for
immediate treatment of flash burns to the eyes and skin.
It is recommended that the cutting area be prepared in such a way as to minimize the
reflection and transmission of ultraviolet radiation. Walls and other surface areas should
be painted in dark colors to reduce reflection. Protective screens or curtains may be
installed to avoid unnecessary ultraviolet transmission.
Warning
The plasma arc cutting process produces rays that can
burn eyes and skin. Always wear eye protection with
appropriate lens shades.

SAFETY 13
2.4.2. Noise
The noise levels generated during plasma arc cutting may be as high as 105 decibels.
This depends on the distance from the machine, arc, plasma torch nozzle design, gas
velocity, material type, and plate thickness. Piranha recommends that each user check
the sound levels in his own shop under normal operating conditions.
Based on those findings, provide adequate ear protection to all personnel who must work
near the machine, in accordance with applicable local, state, and federal industry
standards.
Noise levels that can cause discomfort or damage to hearing will vary greatly from one
individual to another. Piranha recommends that ear protection be furnished to any worker
who requests it, regardless of applicable industrial standards or tested noise levels.
Warning
Exposure to noise from the cutting process can damage
hearing. Wear appropriate ear protection when operating
the machine or when working in the proximity of the
machine.

Piranha Plasma Table 14
2.5. Safety Devices
Plasma arc units are provided with certain safety interlocks designed to prevent
equipment damage and/or personal injury.
Never short out or in any way attempt to defeat the safety interlock devices.
All exposed electrical connections must be covered with the proper insulation material.
Safety devices must be regularly checked for proper operation and replaced immediately
if found to be inoperative.
Warning
Never attempt to operate the plasma unit with any of the
power supply covers not in place. This is extremely
hazardous to the operator and any other person in the
area. It also prevents the equipment from properly cooling
critical components and could result in equipment
damage.

SAFETY 15
2.6. Risk of Electric Shock
Plasma cutting equipment uses high open circuit voltages to initiate the plasma arc.
Normal load voltages are higher than experienced with other types of welding equipment.
Extreme CAUTION must be exercised when operating or servicing this equipment.
2.6.1. Input Connections
1. A wall mounted line isolating switch, fused as required by local electrical codes,
must be fitted as close as possible to the plasma arc power supply.
2. Three-phase input conductors must be sized to carry the rated current of the
plasma arc power supply.
3. Primary power cable must be provided with a minimum 600v rating.
Danger
Always verify that ALL electrical supplies are isolated
before undertaking any service or maintenance work.The
machine may have more than one electrical supply.
Warning
Plasma arc can cause injury and burns. Verify that no
person is in the proximity of the plasma torch at any time
that the plasma system is switched on. Serious burn and
electrical shock hazards exist, even when the plasma
cutting system is not active.
Warning
Frequently inspect the cable for damage or cracking of the
cover. Bare wiring can kill. Replace damaged cable
immediately.

Piranha Plasma Table 16
2.6.2. Grounding
Input Power
1. Connect the ground lead of the four-conductor / three phase input cable to the
electrical system ground in the disconnect box and the ground stud provided in
the plasma arc supply.
2. Be sure all ground lugs are of adequate size to carry the rated current load.
3. Make all connections tight to avoid resistance heating.
Output
1. Connect all positive output ground leads to the material grid of the worktable.
2. Connect the material grid of the worktable to a good earth ground.

SAFETY 17
2.7. Fumes and Air Contamination
2.7.1. Toxic Fumes
Proper precautions must be exercised to prevent the exposure of others in the vicinity to
toxic fumes that may be generated while plasma cutting.
Certain chlorinated solvents such a perchloroethylene and trichlorethylene will
decompose under ultraviolet radiation to form phosgene and other gasses. Care must be
taken to avoid the use of these solvents on materials being cut with plasma arc cutting
equipment. Containers of these solvents and other degreasing agents should be removed
from the immediate area around the plasma arc.
Metals coated with or containing significant amounts of lead, cadmium, zinc, mercury or
beryllium can produce harmful concentrations of toxic fumes when the plasma arc cuts.
Adequate local exhaust ventilation must be used, or the operator must be supplied with
special equipment to guarantee a supply of fresh air such as a respirator or air supplied
helmet.
Metals coated with materials that emit toxic fumes must not be cut unless:
1. The coating is removed prior to cutting.
2. The area is adequately ventilated.
3. The operator is supplied with fresh air breathing equipment.
2.7.2. Air Contamination
The plasma cutting process generates large quantities of hot metal dust and fumes that
would be hazardous if uncontrolled.
A blower pulls a vacuum through the fume extraction assembly in the bed of the machine.
The blower pulls the dust-laden air through a customer supplied filter before exhausting
the air to the environment.
The gases listed below either are produced normally during plasma arc cutting or can
form under certain conditions.
2.7.2.1. Ozone
Ozone is produced by the reaction of the plasma arc's ultraviolet radiation with oxygen
in the air. Uncontrolled, excessive levels of ozone can constitute a hazard. When there
is proper venting to the outside and the machine's internal ventilation system is
functioning properly, there is adequate control of ozone during torch cutting.
2.7.2.2. Nitrogen Dioxide
Nitrogen dioxide gas is produced when nitrogen and oxygen in the air pass through the
electric arc. A hazard may exist if uncontrolled, excessive levels of nitrogen dioxide are
formed. With proper venting to the outside, the machine's internal ventilation system is
adequate to control nitrogen dioxide during torch cutting, if the system is functioning
normally.

Piranha Plasma Table 18
2.7.2.3. Acetyl Chloride
Acetyl chloride gases form in the air surrounding the plasma arc when theairborne vapors
of chlorinated solvents or degreasers decompose upon being exposed to the ultraviolet
radiation of the arc. A hazard may exist if uncontrolled, excessive levels of acetyl chlorides
are formed. A pungent "sweetish" aroma similar to chlorine bleach is the first sign that
these gases are being produced. Shut down the plasma arc cutting system immediately
if you detect the acetyl chloride odor. Do not resume cutting until you locate and control
the source of the vapors.
Various cleaning solvents and vapor degreasers contain chemicals that decompose
rapidly when exposed to ultraviolet radiation.
If the solvents, cleaning solutions, or vapor degreasers used in the shop contain any of
the following chemicals, do not use them near the plasma arc cutting system:
1. trichloroethylene
2. trichloroethane
3. perchloroethylene
4. perchloroethane
5. trifluoro-trichloroethane (fluorocarbon-113)
These chemicals also decompose into small amounts of the toxic gases phosgene and
chlorine. You will notice the acetyl chloride odor long before phosgene or chlorine levels
become harmful.
The vapors can decompose up to several feet away from the arc, do not rely on the
machine's internal ventilation system to control solvent vapors and their products. Do not
use or store chlorinated solvents, cleaning solutions, and vapor degreasers close to the
machine, where the vapors can enter the torch-cutting area.
Note:
It may prove advisable to provide separate ventilation for
the solvent/degreaser storage area.
2.7.3. Metal Fumes
Metal fumes are produced when the plasma arc vaporizes the metal. A hazard may exist
when uncontrolled, excessive levels of metal fumes are produced some vaporized metals
form toxic gases. These metals may be in their pure metallic state, in an alloy, or in a
coating such as paint or plating.
Metals that are known to produce toxic fumes include beryllium, cadmium, lead,
manganese, mercury, and zinc. Beryllium products require particular care, because their
fumes are highly toxic. If there is proper venting to the outside and the machine's internal
ventilation system is functioning normally, there should be adequate control of metal
fumes during torch cutting.
2.7.4. Metal Dust
Metal dust is formed as metal vaporizes during torch cutting. A hazard may exist when
uncontrolled, excessive levels of metal dust are produced. If there is proper venting to the

SAFETY 19
outside and the machine's internal ventilation system is functioning normally, there should
be adequate control ofmetal dust during torch cutting. For proper ventilation, at least 90%
of the worktable should be covered by the workpiece (or other sheet metal covers).
See dust collector vendor installation and operation manual for additional precautions.
2.7.5. Internal Ventilation System
Due to the noxious and toxic nature of many torch cutting by-products, Piranha
recommends venting the machine's internal ventilation system (referred to as the "dust
collector") to the outside atmosphere. This recommendation is especially important when
the shop has one of the following:
1. Low ceilings and/or confined area
2. Large amount of welding and/or torch cutting near the plasma system
3. Poor cross plant ventilation

Piranha Plasma Table 20
2.8. Fire, Explosion, and Burn Prevention
All combustible materials must be removed from the immediate cutting area to at least 35
feet away. Appropriate fire extinguishing equipment must be available in the immediate
cutting area.
After cutting, be sure to allow the metal to cool sufficiently before handling or before
allowing contact with combustible materials.
Never plasma cut empty containers that have held toxic or potentially explosive materials.
Those containers must be thoroughly cleaned according to national standards prior to
cutting or welding.
Never plasma cut in an atmosphere that contains heavy concentrations of dust,
flammable gas, or combustible liquids (such as petrol).
2.8.1. Hot Surfaces
Assure that the bed is free of obstructions and no person or articles of clothing are in
the proximity of moving parts when the machine is in operation. This safety precaution
also applies when the machine is manually moved and when the plasma system is off.
Warning
Since plasma arc cutting produces hot metal, sparks,
and slag, precautions must be taken to prevent fire or
explosions.
Warning
Components may remain hot for a considerable period
of time. Always wear gloves to remove components and
scrap from the bed.
Warning
During prolonged periods of cutting, parts of the machine
bed may become hot to the touch.
Warning
Moving machinery can be dangerous.
This manual suits for next models
4
Table of contents
Other Piranha Cutter manuals
Popular Cutter manuals by other brands

Han-Bond
Han-Bond HB Series User guideline
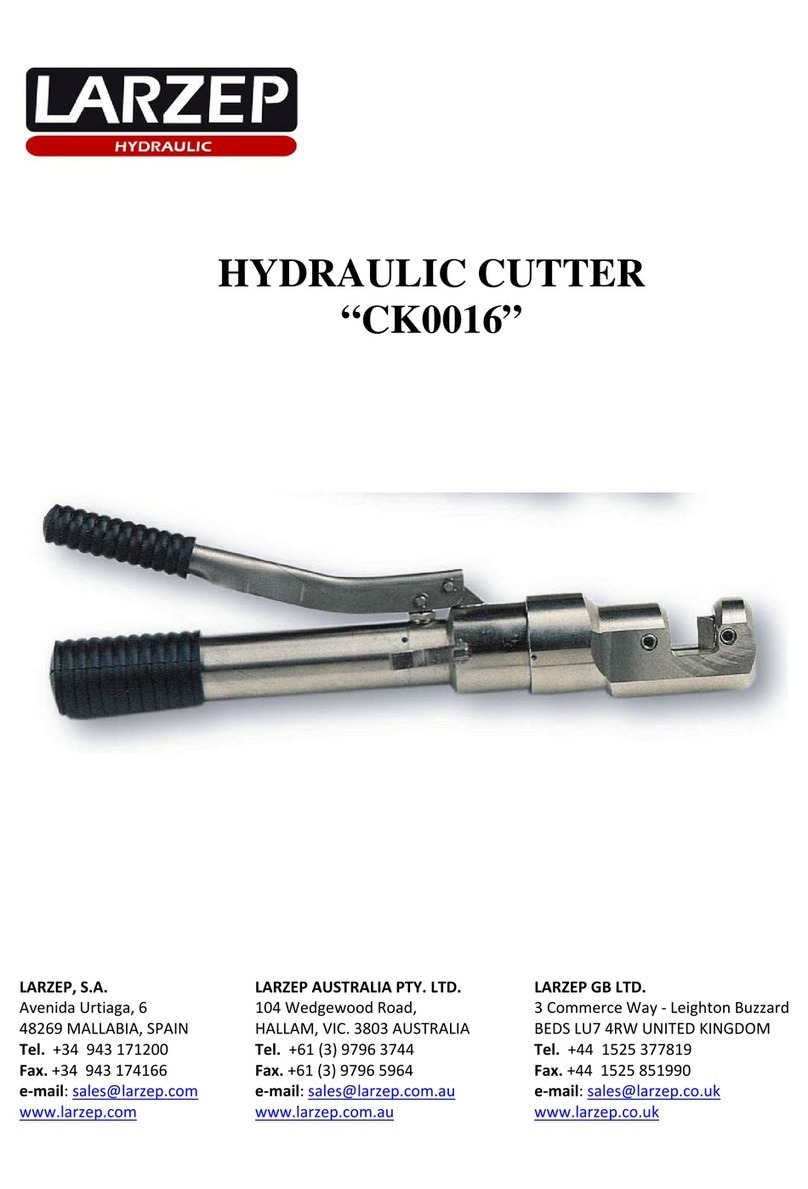
Larzep
Larzep CK0016 instruction manual

Webb
Webb WEMC26 Operators manual & parts lists
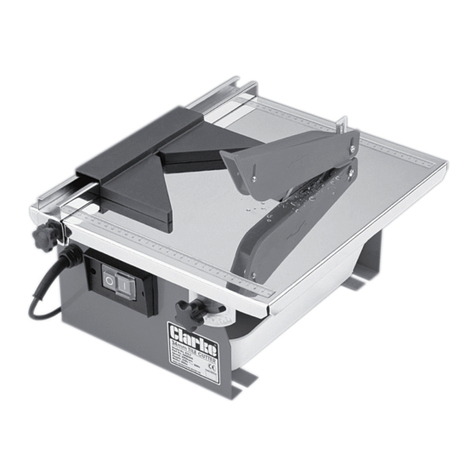
Clarke
Clarke ETC7 Operating & maintenance instructions
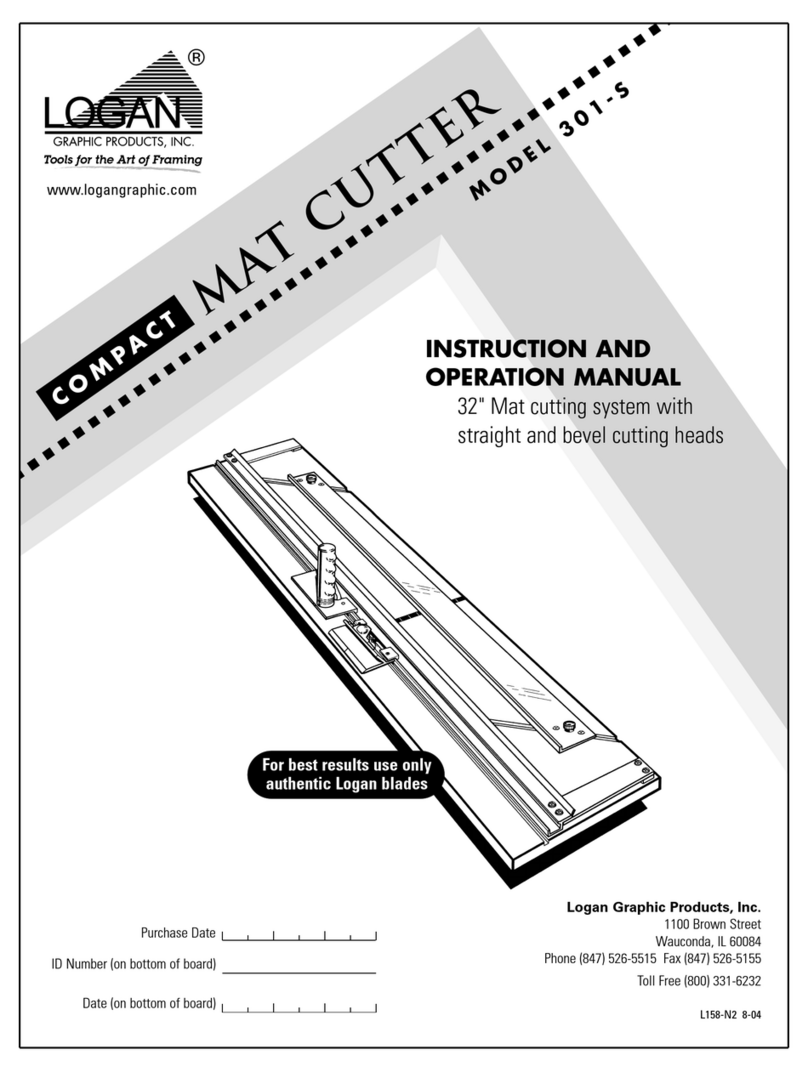
Logan Graphic Products
Logan Graphic Products 301-S Instruction and operation manual

KRUG+PRIESTER
KRUG+PRIESTER IDEAL 5560 operating instructions