Pneucon Globe User manual

06/19 1 of 23
Document No. : PVIM/110/01
Revision No. : 00
Date. : 01.0
6
.2019
INSTALLATION, MAINTENANCE AND OPERATION
MANUAL OF GLOBE 2 WAY CONTROL VALVES
AND DIAPHRAGM ACTUATOR.

06/19 2 of 23
Document No. : PVIM/110/01
Revision No. : 00
Date. : 01.0
6
.2019
Contents
Sect on
Descr pt on Page.
1 Genera 3
2 Warnings 4
3 Storage and Hand ing 5
4 Pre-Insta ation 6
5 Insta ation 7-8
6 Contro Va ve Maintenance 9-18
7 Actuator Maintenance 19-20
8 Actuator to Va ve Assemb y 21
9
Mounting Accessories / Schematic Line Diagram of Accessories
22
10 Troub eshooting 23

06/19 3 of 23
Document No. : PVIM/110/01
Revision No. : 00
Date. : 01.0
6
.2019
1. GENERAL
The G obe 2 way contro va ve range is a inear rising stem design
which is suitab e for a wide range of process contro app ications.
This proven design is manufactured in accordance with internationa
contro va ve standards and can be supp ied with a wide range of
trim design options ranging from ow capacity types, standard
designs through to mu ti stage severe service options. The G obe 2
way contro va ve is supp ied with the diaphrsgm actuator spring
opposed pneumatic diaphragm actuator a ong with the various
options avai ab e.
In additiona , the G obe 2 way contro va ve cou d be fitted with other
actuator types inc uding pneumatic piston, e ectric, hydrau ic and
e ectro hydrau ic types. For these types of actuator p ease refer to the
specific product OIM documents, which wou d be supp ied as part of
the project documentation package.
This manua provides the guide ines for G obe 2 way contro va ve
and Diaphragm Actuator covering the standard sizes and ratings
manufactured. The manua covers the hand ing, storage, insta ation,
operation and maintenance requirements for these products.
If anci iary equipment is mounted on the va ve and actuator eg.
Positioner, Airset, So enoid Va ve, Air ock, Vo ume Booster, I/P
Converter, Position Transmitter or Limit Switch a copy of the
respective OIM wi be provided within the documentation package.
Instructions not detai ed in this document sha be performed in
accordance with standard and safe acceptab e practices as may be
required by oca codes, specifications and or regu ations.
The instructions contained within this manua must be read before
undertaking any work on the equipment supp ied and if there are
any questions p ease contacts Pneucon va ves.
When ordering any spares p ease specify the unique va ve seria
number detai ed on the equipment namep ate.

06/19 4 of 23
Document No. : PVIM/110/01
Revision No. : 00
Date. : 01.0
6
.2019
2. WARNINGS
a) In order to avoid possib e injury to personne or damage to any equipment any
‘WARNING and CAUTION’ notes must be strict y adhered to.
b) Modification of this product, substitution of non-approved components and use
of maintenance procedures other than those detai ed within this document cou d
drastica y affect the performance, nu ify any warranty and be hazardous to
personne and equipment.
c) Persona injury, equipment damage, eakage due to escaping gas or fai ure of
pressure containing component may resu t if the va ve or anci aries are over
pressured or insta ed where service condition exceed the imits detai ed in the
manufacturer’s specification or on the va ve namep ate. To avoid such injury or
damage a re ief va ve for over pressure protection shou d be provide as required
by industry and sound engineering practices or app icab e safety codes.
d) Due to the possibi ity of both e evated and ow temperatures occurring on
exposed surfaces of the va ve assemb y during operation, adequate safety
precautions must be taken. This may invo ve insu ating the va ve assemb y or
the provision of safety c othing and equipment to avoid persona injury.
e) It is a requirement of PER 1999 that both the maximum working pressure and
temperature of the va ve are detai ed on the namep ate. The stated va ues must
be adhered to separate y and in iso ation. Attention must be paid to the
combined pressure and temperature characteristics of the appropriate va ve
pressure containment materia group as stated in ASME / ANSI B 16.34.
f) When purchased each va ve / trim configuration and construction materia s are
specifica y se ected to satisfy the particu ar app ication, conditions of f ow,
temperature, pressure drop and contro ed f uid conditions for corrosion and
erosion. Inc uded within the Pneucon Va ve se ection process is the
consideration of the amount of power conversion a owed to reduce vibration
eve s within the va ve and a so the materia s of construction are specifica y
se ected for each app ication. The va ve must not be used on any other
app ication, without a review by Pneucon Va ve.
g) The va ve is not suitab e for fire safe service and is not certified for this
app ication or duty. Un ess otherwise detai ed in the quotation and order
documentation the va ve wi not have been designed to dea with excessive
seismic activity or bending moments resu ting from misa igned pipe work.
h) It is not intended that externa y app ied ever arms wi be used on the va ve and
actuator assemb y.
)
For cage guided va ve, use of strainer is recommended to remove ine debris to
protect any damage to va ve interna so as to have smooth movement of p ug in
cage.

06/19 5 of 23
Document No. : PVIM/110/01
Revision No. : 00
Date. : 01.0
6
.2019
3. STORAGE AND HANDLING
3.1 Storage
a. Fo owing receipt of the equipment, it shou d be inspected for any transit
damage. Any damage found shou d be photographed and a copy of the
photograph, together with notification of the damage found sent to Pneucon
Va ve.
b. Any f ange or va ve protectors shou d be eft fitted unti immediate y prior to
insta ation in the pipework.
c. If the va ve is going to be stored prior to insta ation (typica y up to 2 months)
it shou d be in a c ean, dry and heated environment in the crate (or on the
pa et) on which it was de ivered.
d. If the va ve is going to be stored prior to insta ation for onger than the above
2 months p ease contact Pneucon Va ve for recommendations based on the
p anned ength of time to be stored.
3.2 HANDLING
1. The weight of the contro va ve assemb y can cause serious injury if it is not
hand ed correct y,
inc udes using the appropriate ifting equipment and
persona protective c othing.
2. The appropriate ifting equipment must be used and proper y attached. Where
ifting eyes are provided with the equipment these shou d be used to enab e
safe hand ing of the va ve, actuator or assemb y. A ifting equipment shou d
be used within its defined imitations, app icab e codes and safe industria
practices.
3. The recognised safe industria practices inc ude the fo owing.
•S ings to be free of kinks
•Lifting hooks to be positioned direct y over the oad to avoid any severe
movement when ifted
•The operator sha ensure that the oad is safe and we secured
•When ifting the equipment ensure that any s ings or hoists are positioned to
avoid any damage to the accessories or tubing mounted on the va ve assemb y

06/19 6 of 23
Document No. : PVIM/110/01
Revision No. : 00
Date. : 01.0
6
.2019
4
.
PRE
–
INSTALLATION
1. In preparation for the insta ation sufficient c earance above and around the
va ve and actuator shou d idea y be provided for access and maintenance
purposes.
2. Prior to insta ation, the space in the pipework in which the contro va ve is to
be insta ed shou d be checked to be in accordance with the GA drawing
supp ied with the va ve or to the recognised internationa standard for face to
face dimensions.
3. For contro va ves using a pneumatic air supp y as the power source and fitted
with instruments an air supp y fi ter/regu ator shou d be provided to protect
the pneumatic actuator from over pressurisation and be within the operating
range of the pneumatic actuator to be used.
4. For contro va ves fitted with a ‘smart’ e ectro pneumatic positioner the
fi ter/regu ator shou d be suitab e for being fi tered to ISO 8573-1 c ass 2 or
better.
5. If the pipework in which the contro va ve is going to be insta ed is going to be
f ushed prior to operation of the va ve, consideration of removing the interna
trim parts prior to the f ushing process shou d be made, to prevent any
subsequent damage or b ockage within the trim. For this requirement p ease
contact Pneucon Va ve for a more detai ed procedure and detai s of f ushing kit
to be supp ied.
6. Simi ar y for contro va ves supp ied with butt we d end connections and fitted
with PTFE based interna parts eg pressure ba ance sea the trim parts shou d
be removed to enab e the body to be we ded into the pipework.
7. The assemb y shou d be inspected on receipt to ensure that it has not been
damaged during transit. This inspection shou d be undertaken in a safe and
contro ed manner as va ve equipment can be heavy and have sharp edges. Any
damage found shou d be photographed and immediate y reported to Pneucon
Va ve.
8. The end caps or other protection devices shou d not be removed from the
equipment unti the time of insta ation, in order to he p avoid any damage to
the f anges and a so prevent the ingress of dirt or foreign partic es.
9. The adjacent pipework must be free of dirt, pipe sca e, we ding s ag and a
other foreign objects. Safe operation of the va ve cou d be impaired by the
ingress of ine debris or foreign matter.

06/19 7 of 23
Document No. : PVIM/110/01
Revision No. : 00
Date. : 01.0
6
.2019
5. INSTALLATION
•The va ve is supp ied with a f ow direction arrow either cast on to the body,
detai ed on a separate arrow p ate or detai ed on the namep ate. It is very
important that the va ve is insta ed into the pipework with the correct f ow
direction.
•Insta the va ve using accepted piping practises and preferab y with suitab e
engths of straight pipework both upstream and downstream.
•The preferred orientation is for the actuator to be vertica y upright. If a va ve is
required to be insta ed in any other orientation the va ve and actuator must be
adequate y supported. The fo owing is a diagram showing the preferred options
for the insta ation of contro va ves fitted with a pneumatic diaphragm.
•If a norma ising bonnet is provided for a high or ow temperature app ication
and the pipework is therma y agged the agging must be terminated at the
bonnet to body f ange bo ting.
•
If the contro va ve is provided with f anged connections the fasteners shou d be
tightened even y using the ‘cross rotation’ method i ustrated on page no 8 of
23.

06/19 8 of 23
Document No. : PVIM/110/01
Revision No. : 00
Date. : 01.0
6
.2019
•
For contro va ves supp ied with butt we d end connections we ding into the
pipework sha be undertaken by qua ified we ders and approved we d
procedures. Any subsequent oca post we d heat treatment shou d be carried
out in accordance with the approved procedure. It is recommended that the
va ves are in the c osed position during the we ding process.
•If the trim has been removed for we ding the va ve into the ine or for f ushing
purposes it shou d be rep aced with new gaskets.
•Fo owing insta ation of a va ve and actuator fitted with an handwhee
mechanism the actuator mechanism shou d be checked to ensure that it is in
the ‘neutra ’ position. An input signa shou d then be app ied to the va ve
actuator in order to check and confirm correct ca ibration of the assemb y.
•A pneumatic air connections shou d be checked for eaks. During functiona
testing of a spring return diaphragm actuator, the assemb y wou d have been
subject to a pressure test at 3.4 barg.
•
The g and nuts are factory adjusted and fo owing commissioning further
adjustment cou d be required to stop any stem eakage. It shou d be pointed
out that excessive tightening of the g and studs cou d resu t in packing wear or
excessive friction.

06/19 9 of 23
Document No. : PVIM/110/01
Revision No. : 00
Date. : 01.0
6
.2019
6. MAINTENANCE
6.1 General
The maintenance recommendations for a contro va ve and actuator assemb y are a function
of the critica ity of the va ve as part of the overa contro system and a so consideration of
the severity of the duty. These factors need to be considered in determining when and how
frequent y a contro va ve shou d be inspected and maintained. For further recommendations
for specific app ications p ease contact Pneucon Va ve.
With regards to the soft parts used within the construction of a contro va ve and pneumatic
diaphragm actuator assemb y the fo owing are some genera guide ines for periods when
these various parts shou d be rep aced.
•Va ve body, bonnet and seat gaskets (where app icab e) – These shou d be rep aced
every time the va ve is dis-assemb ed and re-assemb ed p us every 3 years between
insta ation or rep acement.
•Va ve g and packing - These again shou d be rep aced every time the va ve is dis-
assemb ed and re-assemb ed p us every 3 years between insta ation or rep acement.
•Va ve pressure ba ance sea (where app icab e) – On y needs to be rep aced if found to
be damaged or worn p us every 4 years between insta ation or rep acement.
•Va ve seat soft face (where app icab e) – On y needs to be rep aced if found to be
damaged or worn p us every 4 years between insta ation or rep acement.
•Actuator diaphragm – On y needs to be rep aced if found to be damaged or worn p us
every 4 years between insta ation or rep acement.
•Actuator O-rings (where app icab e) – On y need to be rep aced if found to be damaged
or worn p us every 4 years between insta ation or rep acement.
6.2 Removal of Actuator from Valve
•Idea y this work shou d be undertaken in a workshop or if not, ensure that the va ve
is correct y iso ated and the pipework de-pressurised.
•If sti insta ed in the pipework remove the instrument signa to the positioner and air
supp y to the airset. If practica attach a temporary regu ated air supp y to the airset.
•Disconnect and remove any instrument inkages connected to the va ve and actuator
interface.
•Lift the va ve p ug off the seat ring using the temporary airsetand remove the stem
coup ing.
•Unscrew and remove the ocking ring from the bonnet threads.
•Check that the handwhee (if fitted) is in the ‘neutra ’ position.
•Remove the actuator from the va ve.

06/19 10 of 23
Document No. : PVIM/110/01
Revision No. : 00
Date. : 01.0
6
.2019
6.3 D sassembly Of Globe 2 Way Control Valve w th Contoured, M crospl ne & Mult step
Tr m (Metal To Metal)
1. Remove the g and Stud Nut (Part No - 15),
G and Pusher (Part No - 13) & G and (Part
No - 12).
2. Remove the Body Bonnet Stud Nut (Part
No - 8) and ift the Bonnet (Part No - 2)
from the va ve body, whi e ho ding the p ug
stem assemb y (Part No - 4 & 9).
3. Remove the p ug stem assemb y.
4. Remove Gasket from the body to bonnet
(Part No - 3).
5. Remove the packing set (Part No - 11) and
Spacer (Part No - 10) from the Bonnet.
6. Remova of the Seat Ring (Part No - 5) is
on y necessary for rep acement or
machining.
Where necessary the seat ring is screwed
out of the body and a athe or boring mi
can be used for seat ring that are difficu t
to remove.
For extreme y tight seat rings the va ve
body shou d be heated to assist remova .
7. For Top Guided Va ves, the P ug Guide
Bush (Part No - 6) is pressed into the
bonnet and does not norma y require
remova . When remova of the guide is
essentia it shou d be machine. P ug Guide
Bush (Part No - 6) is not app icab e in
Microsp ine trim Design.
8. A the parts shou d be c eaned and
examined for damage.
MICRO
SPLINE TRIM
MULTISTEP TRIM

06/19 11 of 23
Document No. : PVIM/110/01
Revision No. : 00
Date. : 01.0
6
.2019
6.4 D sassembly Of Globe 2 Way Control Valve w th Cage Gu de Tr m
1. Remove the g and stud nut (Part No -
20), G and Pusher (Part No - 18) &
G and (Part No - 17).
2. Remove the Body Bonnet Stud Nut
(Part No - 14) and ift the Bonnet (Part
No - 02) from the va ve body, Whi e
Ho ding the p ug stem assemb y (Part
No - 05,06,07,08 & 09)
3. Remove the packing set (Part No - 16)
and Spacer (Part No - 15) from Bonnet.
4. Remove the p ug stem assemb y.
5. Remove Gasket from the bonnet Joint
Gasket (Part No - 11).
6. Remove Inner Cage (Part No -12)
7. Remove Gasket from Body Joint Gasket
(Part No - 10).
8. Remova of the Seat Ring (Part No - 04)
is on y necessary for rep acement or
machining.
9. Above a step are a so use in LN2, LN3,
& LN4.
10.A the parts shou d be c eaned and
examined for damage

06/19 12 of 23
Document No. : PVIM/110/01
Revision No. : 00
Date. : 01.0
6
.2019
6.5 Replac ng Pressure Balanced Seal
6.5.1 PTFE Seals n Tr m S zes up to 6”
1.
Remove the Grub Screw (Part No - 09)for the
Retainer nut.
2.
Remove the Retainer Nut (Part No - 07) from
the P ug Stem Assemb y.
3.
Remove the o d Ba ancing Ring (Part No -
06) and Rep ace the new one Ba ancing
Ring.
4.
In the Ba ancing Ring there are Various type
of Ba ancing Ring (Part No - 06).
a) PTFE = -100°C to 180°C.
b) GFT = -50°C To 210°C.
c) Carbon Fi ed PTFE = 0°C to 220°C.
d) Carbon Ring = 200°C to 550°C for High
Temperature.
6.5.2 PTFE Seals n Tr m S zes above 6”
•Unscrew cap heads and remove sea
retainer p ate
•Remove upper anti extrusion ring (6A)
•Remove main pressure ba ance sea (6)
•Remove ower anti extrusion ring (6B)
•Rep ace with new pressure ba ance sea
ensuring orientation is correct (spring
upwards for ‘f ow under’ and spring
downwards for ‘f ow over’
•
Refit anti extrusion rings, sea retainer
p ate and
fit caphead screws

06/19 13 of 23
Document No. : PVIM/110/01
Revision No. : 00
Date. : 01.0
6
.2019
6.5.3
D sassembly Of Globe 2 Way Control Valve w th Cage Gu ded Tr m (Grafo l
Des gn)
1. Remove the g and stud nut (Part No -
19), G and Pusher (Part No - 17) &
G and (Part No - 16).
2. Remove the Body Bonnet Stud Nut
(Part No - 13) and ift the Bonnet (Part
No - 02) from the va ve body, Whi e
Ho ding the p ug stem assemb y (Part
No - 08,09,10 & 11)
3. Remove the packing set (Part No - 14)
and Spacer (Part No - 15) from Bonnet.
4. Remove the p ug stem assemb y.
5. Remove Gasket from the bonnet Joint
Gasket (Part No - 07).
6. Remove Inner Cage (Part No -06)
7. Remove Gasket from Body Joint Gasket
(Part No - 05).
8. Remova of the Seat Ring (Part No - 04)
is on y necessary for rep acement or
machining.
9. A the parts shou d be c eaned and
examined for damage
6.6 Replac ng Soft Seat
6.6.1 Replac ng Contoured Tr m Soft Seat
•Remove p ug assemb y from contro
va ve as per section 6.3
•Unscrew sea retaining ring (Part No -
04).
•Remove soft seat insert (Part No - 03)
•Rep ace soft seat insert
•Screw sea retaining ring on to p ug

06/19 14 of 23
Document No. : PVIM/110/01
Revision No. : 00
Date. : 01.0
6
.2019
6.7 Valve Assembly
6.7.1 General
•New p ugs are norma y supp ied with stems which are integra or fitted into the p ug
head. If the parts are separate the stem shou d be screwed into the p ug head and
tightened. The p ug shank and stem shou d be dri ed and countersunk. The pin is
then fitted and pin peened over, before being fina y machined f ush to the p ug shank.
•A the parts of the assemb y shou d be c eaned and free from any debris.
6.7.2 Assembly w th Contoured, Spl ne M cro or Mult step Tr ms
•App y sea ing compound to the seat
(5) and screw into body (1). The seat
ring shou d be tightened using a seat
too (contact Pneucon Va ve for
further detai s)
•Insta the p ug (4) and stem (9)
assemb y
•P ace body joint (3) in body recess
•Carefu y ower the bonnet (2) over the
p ug stem and a so over the body
studs (7). The bonnet shou d be
centred to ensure that the p ug and
stem assemb y move free y
•Fit the body nuts (8) and tighten
even y using the ‘star ogic’ sequence.
The va ve shou d be moved in a inear
direction on y, to ensure free
movement of the stem
•Refer to 6.8 for assemb y of g and
packing options

06/19 15 of 23
Document No. : PVIM/110/01
Revision No. : 00
Date. : 01.0
6
.2019
6.7.3 Assembly w th Cage Gu ded Tr m
•P ace seat gasket (3) in body and
insta seat (4)
•P ace cage gasket (10) in body(1) and
p ace cage (12) in body
•Insta the p ug and stem assemb y
•P ace body joint (11) in body recess
•Carefu y ower the bonnet (2) over
the p ug stem and a so over the body
studs. The bonnet shou d be centred
to ensure that the p ug and stem
assemb y move free y
•Fit the body nuts (14) and tighten
even y using the ‘star ogic’ sequence.
The va ve shou d be moved in a
inear direction on y, to ensure free
movement of the stem
•Refer to 6.8 for assemb y of g and
packing

06/19 16 of 23
Document No. : PVIM/110/01
Revision No. : 00
Date. : 01.0
6
.2019
6.7.4
Assembly w th Cage Gu ded Tr m and Graph te Pressure Balance Seal
•P ace seat gasket (5) in body and fit seat (4)
•P ace cage gasket (10) in body (1) and p ace cage (6) in body
•Insta graphite sea (8)
•Insta sea retainer (9)
•Insta the p ug and stem assemb y (10 + 11)
•P ace body joint (7) in body recess
•Carefu y ower the bonnet (2) over the p ug stem and a so over the body studs.
The bonnet shou d be centred to ensure that the p ug and stem assemb y move
free y
•Fit the body nuts (13) and tighten even y using the ‘star ogic’ sequence. The
va ve shou d be moved in a inear direction on y, to ensure free movement of
the stem
•Refer to 6.8 for assemb y of g and packing

06/19 17 of 23
Document No. : PVIM/110/01
Revision No. : 00
Date. : 01.0
6
.2019
6.8
Gland Pack ng Assembly
6.8.1 PTFE Gland Pack ng Assembly
1. A the parts shou d be c eaned and examined
for damage before the packing box assemb y.
2. Insert first Packing Spacer (Part No - 08).
3. Insert G and Packing PTFE (Part No - 05,06 &
07) Tota set of ring shou d be fu y insta ed.
4. Insert G and (Part No - 04).
5.
Insert G and Pusher (Part No - 02)and tight
with G and Stud & G and Stud Nut (Part No -
03 & 09)
6.8.2 Graph te Gland Pack ng Assembly
1. A the parts shou d be c eaned and examined
for damage before the packing box assemb y.
2. Insert first two Nos of G and Packing Grafoi
one by one and ensure the each ring shou d be
fu y insta ed (Part No - 14).
3. Insert Packing Spacer (Part No - 15).
4. Insert G and Packing Grafoi (Part No - 14) one
by one and ensure the each ring shou d be
fu y insta ed.
5. Insert G and (Part No - 16).
6.
Insert G and Pusher (Part No - 17)and tight
with G and Stud & G and Stud Nut (Part No -
18 & 19)

06/19 18 of 23
Document No. : PVIM/110/01
Revision No. : 00
Date. : 01.0
6
.2019
6.9
SEAT AND
PLUG LAPPING PROCESS.
•Lapping of the p ug to the seat (if required) is norma y carried out during the contro
va ve assemb y and without the actuator fitted
•The va ve bonnet shou d be fitted with the g and parts and the stem insta ed with a
ight oi app ied to assist the apping process
•App y a apping compound to either the seat or p ug seating face (not both) and fit the
bonnet assemb y on to the body and oose y tighten a number of the bonnet nuts
ensuring the bonnet is centra ised
•Lap the p ug and seat using short osci ating movements, raising the p ug occasiona y
and owering it to another position to ensure apping of the entire p ug and seat
seating faces
•The p ug and seat shou d show evidence of the apping continuous y around the
seating faces
•Prior to fina assemb y of the bonnet to the body both the p ug and seat parts shou d
be c eaned
BEFORE LAPPING
AFTER LAPPING

06/19 19 of 23
Document No. : PVIM/110/01
Revision No. : 00
Date. : 01.0
6
.2019
7Actuator Ma ntenance
7.1 PDC Actuator D sassembly and Assembly
1. Open the Window Cover (Part No - 22).
2. Using the Spring Adjuster (Part No - 12) to re ease the Spring Compression (Part No -
08).
3. Remove the Casing Bo t and Nut (Part No - 23 & 14).
4. Remove the Top Casing (Part No - 01).
5. Remove the Hex Bo t from coup ing (Part No - 32) and separate the coup ing (Part No -
17).
6. Remove the Indicator ock nut (Part No - 16) and Trave indicator (Part No - 15) from
stem.
7. Unscrew the stem Lock Nut (Part No - 26) and remove the Spring Washer (Part No - 27)
and remove Spring Guide (Part No - 19) and remove the Area P ate (Part No - 05).
8. Remove the Diaphragm from the actuator (Part No - 06).
9. C ean a the interna parts and examine for any damage. Any significant y damaged
parts shou d be rep aced.
10.For PDC actuator the two 'O' Ring (Part No - 28) in Sea Box (Part No - 04) shou d be
rep aced.
11.After rep acing the diaphragm Re-assemb e the actuator.
12.Using the spring adjuster (Part No - 12) to compress the spring (Part No - 08) unti the
actuator start to operate at the bench set figure detai ed on the namep ate.

06/19 20 of 23
Document No. : PVIM/110/01
Revision No. : 00
Date. : 01.0
6
.2019
7.2 PDO Actuator D sassembly and Assembly
1. Open the Window Cover (Part No - 19).
2. Using the Spring Adjuster (Part No - 12) to re ease the Spring Compression (Part No -
08).
3. Remove the Casing Bo t and Nut (Part No - 21 & 22).
4.
Remove the Top Casing (Part No - 01).
5.
Remove the Hex Bo t from coup ing (Part No - 28) and separate the coup ing (Part No -
16).
6. Remove the Indicator ock nut (Part No - 16) and Trave indicator (Part No - 14) from
stem.
7.
Unscrew the Diaphragm Co ar Nut (Part No - 06) and Remove the Spring Guide (Part
No - 07) and Remove the Area P ate (Part No - 03).
8. Remove the Diaphragm from the actuator (Part No - 04).
9. C ean a the interna parts and examine for any damage. Any significant y damaged
parts shou d be rep aced.
10.After rep acing the diaphragm Re-assemb e the actuator.
11.Using the spring adjuster (Part No - 12) to compress the spring (Part No - 08) unti the
actuator start to operate at the bench set figure detai ed on the namep ate.
Table of contents
Other Pneucon Control Unit manuals
Popular Control Unit manuals by other brands

TRU Components
TRU Components 2256179 operating instructions
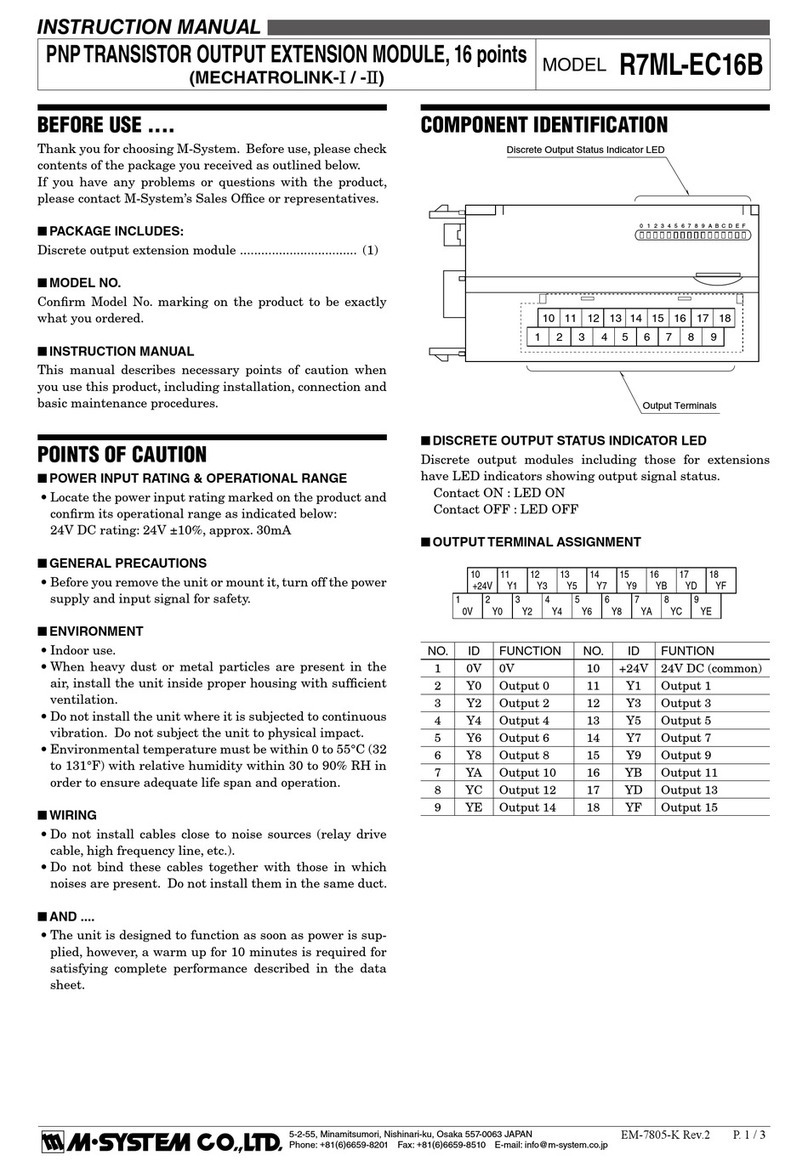
M-system
M-system R7ML-EC16B instruction manual
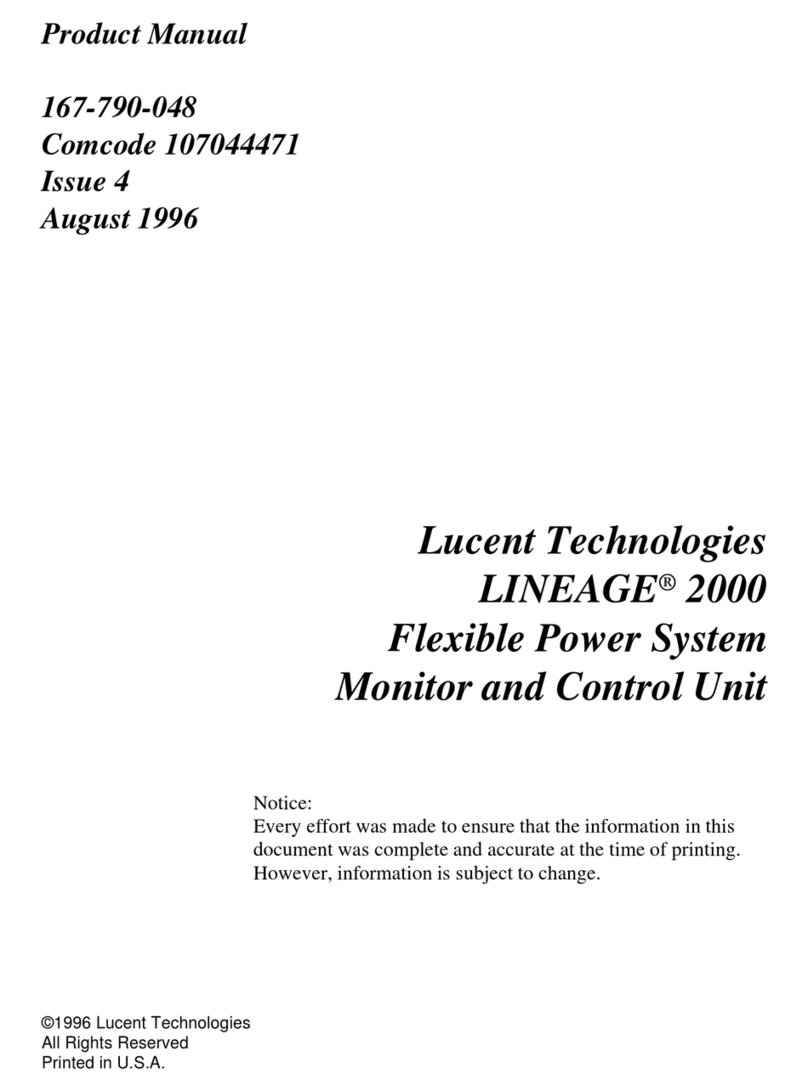
Lucent Technologies
Lucent Technologies LINEAGE 2000 FPS product manual
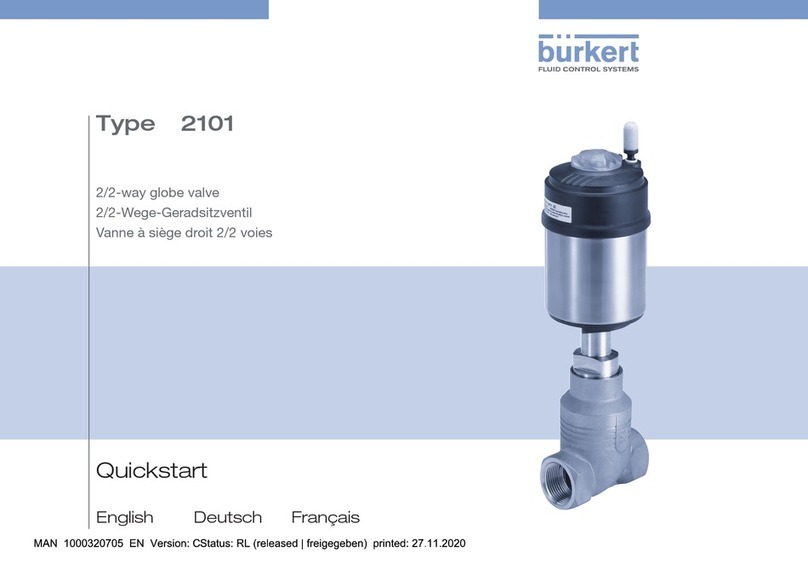
Burkert
Burkert 2101 quick start guide
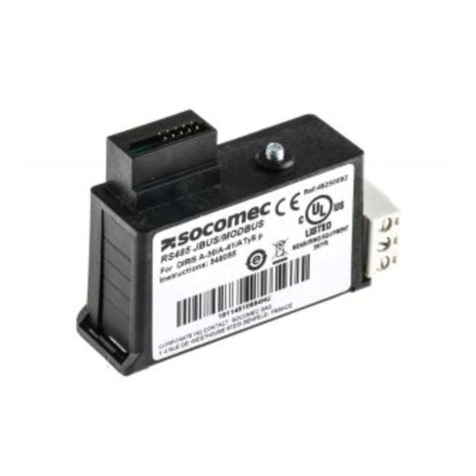
socomec
socomec DIRIS A41 operating instructions
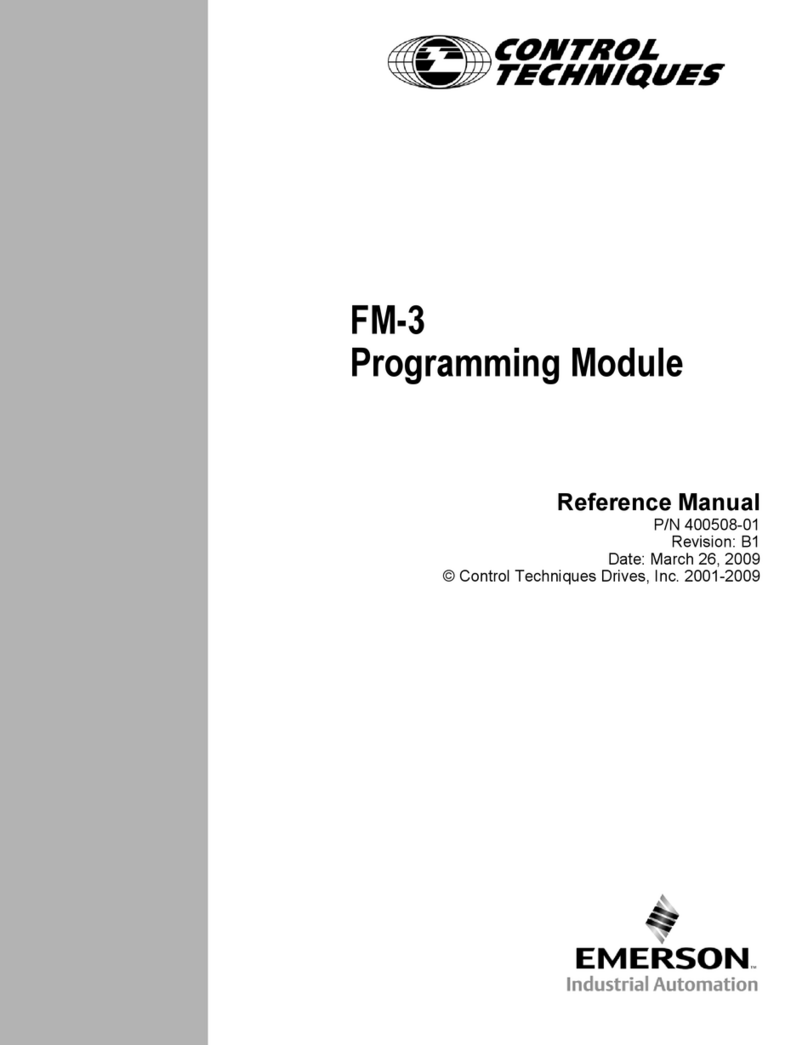
Control Techniques
Control Techniques FM-3 Reference manual
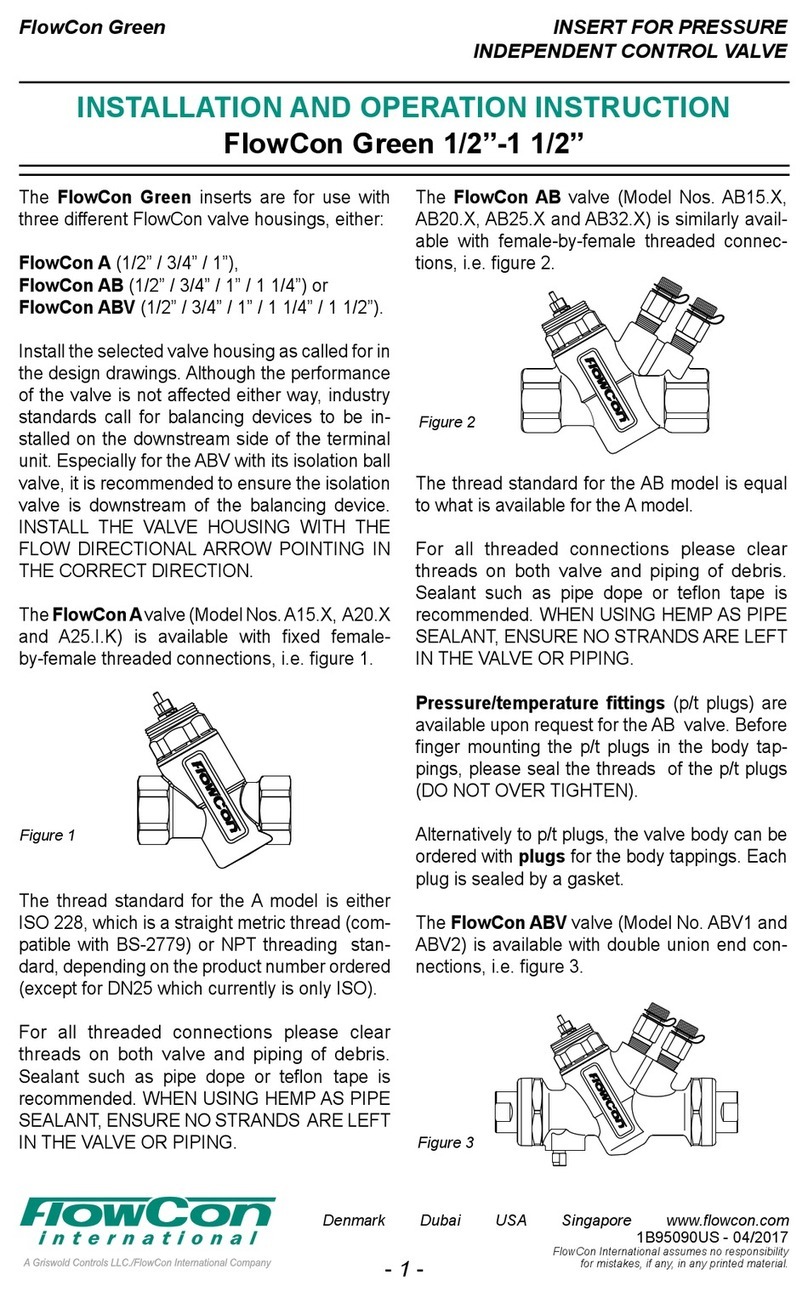
FlowCon
FlowCon FlowCon Green Series Installation and operation instruction
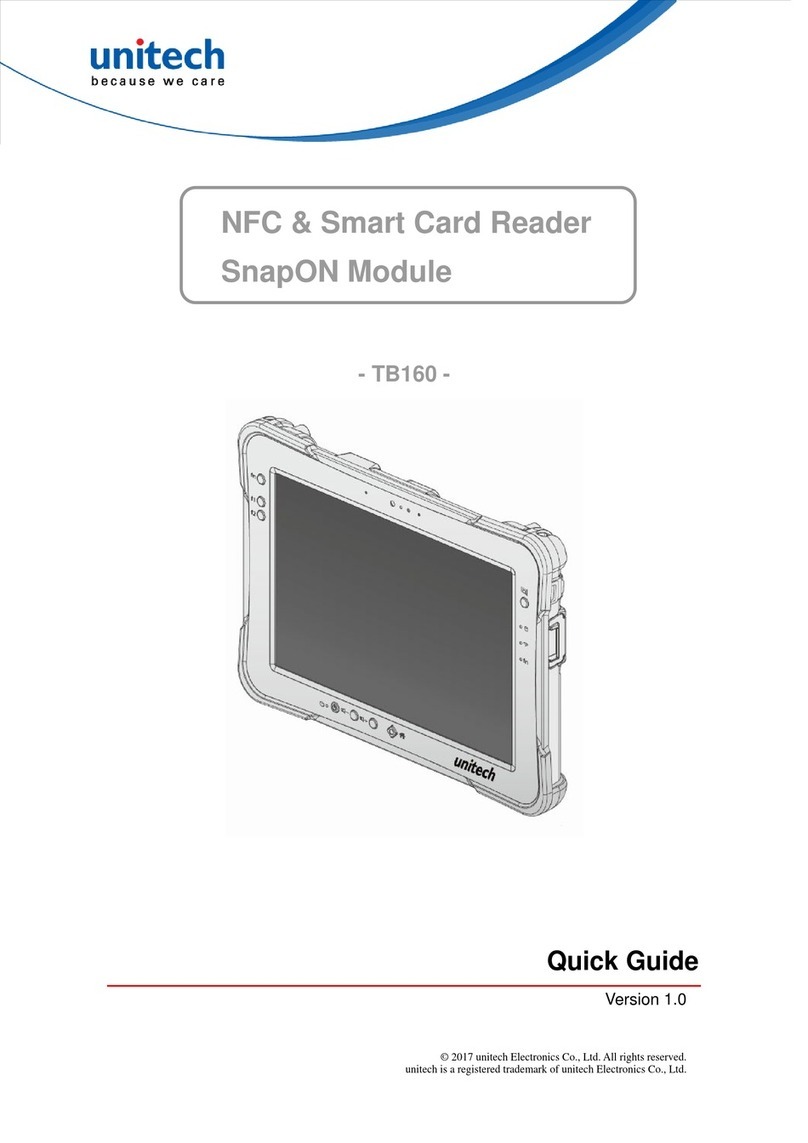
Unitech
Unitech TB160 quick guide
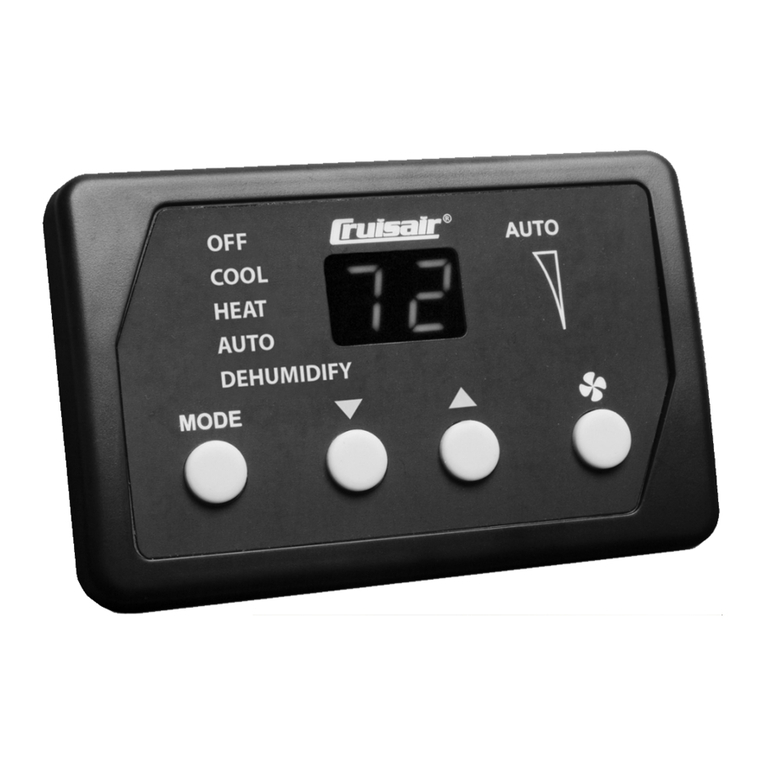
Dometic
Dometic Q3 Operation manual
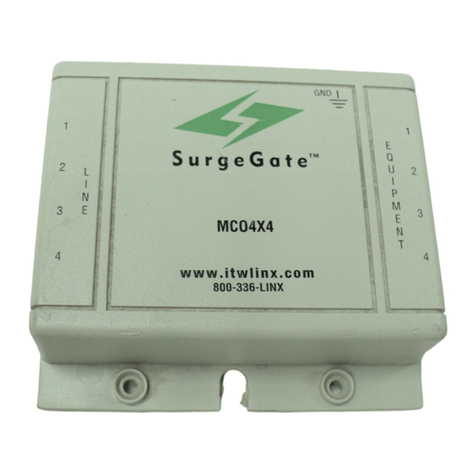
ITW Linx
ITW Linx SurgeGate MCO4 Product instructions

Genebre
Genebre 5985 Installation, operation and maintenance manual
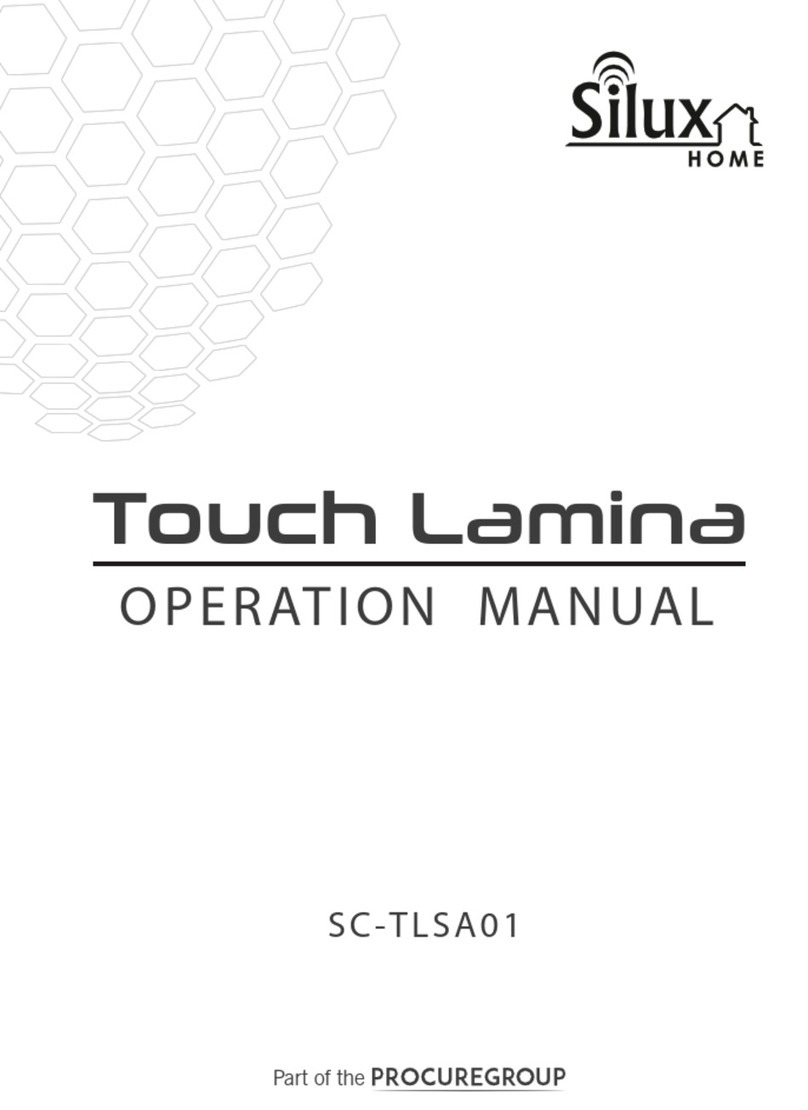
Silux Home
Silux Home Touch Lamina SC-TLSA01 Operation manual