Pneumercator TMS1000D User manual

SINGLE
DEF TANK
MONITORING
SYSTEM
PNEUMERCATOR
Liquid Level Control Systems
INSTALLATION MANUAL
MODEL TMS1000D
© COPYRIGHT 2018 PNEUMERCATOR CO., INC.
1785 EXPRESSWAY DRIVE NORTH
HAUPPAUGE, NY 11788
TEL: (631) 293-8450
FAX: (631) 293-8533
http://www.pneumercator.com
TMS1000D Installation.docx June 27, 2018
DRAWING NO. 20156 REV. N/C
PeterSinkiwskij
DigitallysignedbyPeter
Sinkiwskij
DN:cn=PeterSinkiwskij,
o=PneumercatorCo.,Inc.,
ou=Headquarters,
email=peter@pneumerca
tor.com,c=US
Date:2018.06.2720:30:03
-04'00'


INSTRUCTION MANUAL TMS1000D
Note: A separate OPERATING MANUAL is available, but NOT required for TMS1000D installation.
Page
SAFETY INFORMATION.......................................................................................... 4
Section 1 PRODUCT DESCRIPTION
1.1 General System Overview ........................................................................................ 5
1.2 Control Console........................................................................................................ 6
1.3 Liquid Level Probes .................................................................................................. 8
1.4 Liquid Leak Sensors ................................................................................................. 9
Section 2 INSTALLATION DETAILS
2.1 Installation Checklist............................................................................................... 11
2.2 Control Console Installation .................................................................................... 12
2.3 Level Probe Installation........................................................................................... 16
2.4 Leak Sensor Installation –Steel Tanks................................................................... 18
2.5 Leak Sensor Installation –Piping Sumps and Dispenser Pans, Vaulted Tank......... 19
2.6 Leak Sensor Installation –Fiberglass Underground Tanks ..................................... 20
2.7 Leak Sensor Installation –Fiberglass Underground Tank Reservoirs ..................... 21
Section 3 WIRING INSTALLATION AND DIAGRAMS
3.1 System Probe/Sensor Wiring.................................................................................. 23
3.2 Power Wiring .......................................................................................................... 27
3.3 Probe/Sensor Wiring & Splices............................................................................... 28
3.4 Programmable Relay Outputs/Contact Closure Inputs............................................ 30
3.5 Data Communications Wiring.................................................................................. 31
3.6 Probe Map/System Setup....................................................................................... 32
TABLE OF CONTENTS

INSTRUCTION MANUAL TMS1000D
TMS1000D Installation.docx June 27, 2018
PAGE 4
IMPORTANT SAFETY INFORMATION
This manual contains instructions for installing electrical hardware in hazard
areas.
The following warnings must be considered to be in compliance with accepted
codes.
Any inquiries about this manual, or to return defective equipment should be
directed to:
PNEUMERCATOR COMPANY
1785 EXPRESSWAY DRIVE NORTH
HAUPPAUGE, NY 11788
Attention: Technical Services
TEL: (631) 293-8450
FAX: (631) 293-8533
TOLL FREE: (800) 209-7858
www.pneumercator.com
WARNING
Installation must be in strict accordance with this manual as adopted from the
following codes:
- NFPA 70, "National Electric Code."
- NFPA 30A, "Automotive and Marine Service Station Code."
FAILURE TO COMPLY MAY RESULT IN PERSONAL INJURY, PROPERTY LOSS
AND EQUIPMENT DAMAGE.
WARNING
Alteration, modification or replacement with non-factory components could
impair the operation of this equipment, and void the warranty.
FAILURE TO COMPLY MAY RESULT IN PERSONAL INJURY, PROPERTY LOSS
AND EQUIPMENT DAMAGE.

INSTRUCTION MANUAL TMS1000D
TMS1000D Installation.docx June 27, 2018
PAGE 5
SECTION 1 –PRODUCT DESCRIPTIONS
1.1 GENERAL SYSTEM OVERVIEW
The TMS1000D is a fully integrated tank monitor system that combines level measurement with leak
detection using external sensors for secondarycontainment. Figure 1-1 shows a typical block diagram
of how a system should be configured for installation. This diagram is not a detailed wiring diagram,
which is found in Section 3 of this manual. Figure 1-1 is to guide the installer in planning the actual
installation, and give a general overview of the TANK, LEVEL PROBE, EXTERNAL SENSORS, and
OPTIONAL equipment that may be required for a typical installation. Figure 1-1 shows one (1) tank
with two (2) sensors. Refer to the specific design drawing for the customer's actual site for complete
site-specific details on how many sensors are specified.
Figure 1-1 –Typical System Block Diagram
DRAWING NO. 20195 REV. N/C
115/230 VAC
(50/60 Hz)
POWER
TMS1000D
CONSOLE
FIELD WIRING
SEE
MANUAL
SECTION 3
LEVEL
PROBE
LIQUID STORAGE TANK
RELAY CONTACTS
SEE MANUAL
SECTIONS
2.3 - 2.8
REMOTE
MOUNTED
ALARMS
SEE MANUAL SECTION 2.2
DATA DISPLAY /
GATHERING &
CONTROL
EQUIPMENT
SEE MANUAL
SECTION 3.5
CONSOLE
OUTPUTS
SEE MANUAL
SECTION 3.4
IN
°F
%GAL
ULL
GAL
PNEUMERCATOR
LiquidLevelControlS ystems
GROUP ID
MODE TEST
STEP RESET
GROUP EDITREVIEW
EDIT
MODEM / RS-232 / RELAY CONTACTS
OTHER
SENSOR
LEAK
SENSOR
LEAK
H. HIGH
TEMP
DEF TANK MANAGEMENT SYSTEM
TMS 1000D
HIGH
LOW
DIESEL EMISSIONS FLUID

INSTRUCTION MANUAL TMS1000D
TMS1000D Installation.docx June 27, 2018
PAGE 6
1.2 CONTROL CONSOLE DESCRIPTION
All standard configurations are equipped with 1 mag. probe/2 leak sensor inputs, 1 RS-232 serial
port, 4 Fully programmable Relay outputs/2 Dry contact inputs, NEMA 4X enclosure.
WARNING
Installation MUST be done by qualified personnel familiar with local wiring codes
and electrical safety practices. FAILURE TO COMPLY MAY RESULT IN
PERSONAL INJURY, PROPERTY LOSS AND EQUIPMENT DAMAGE.
See Figure 1-2 below for overview.
Figure 1-2 –TMS1000D Console Outline
WARNING
The console is designed for Ordinary Location, Non-Hazardous installation only,
as defined by the National Electrical Code (NEC). DO NOT install where
flammable vapors may be present. FAILURE TO COMPLY MAY RESULT IN
PERSONAL INJURY, PROPERTY LOSS AND EQUIPMENT DAMAGE.
DRAWING NO. 20174 REV. A
OPERATING MEMBRANE BUTTONS
ANNUNCIATOR
INDICATOR LIGHTS
DIGITAL DISPLAY

INSTRUCTION MANUAL TMS1000D
TMS1000D Installation.docx June 27, 2018
PAGE 7
The console should be located in an area that is easily accessible to the personnel responsible for
operation and maintenance of the system. Metal conduiting is recommended and may be required by
local codes. All outdoor conduits must be watertight.
All conduit entries are provided on the bottom of the enclosure. If a conduit entry is not being used, it
must be sealed with an appropriate plug.
WARNING
Do not drill or modify enclosure. Use only conduit entries provided. FAILURE TO
COMPLY WILL VOID WARRANTY AND MAY PRESENT A SAFETY HAZARD
RESULTING IN PERSONAL INJURY, PROPERTY LOSS AND EQUIPMENT
DAMAGE.
WARNING
Conduit entries must only be used for their designated purpose in order to
assure safe operation and to maintain safety certification. FAILURE TO COMPLY
WILL VOID WARRANTY AND MAY PRESENT A SAFETY HAZARD RESULTING IN
PERSONAL INJURY, PROPERTY LOSS AND EQUIPMENT DAMAGE.
Figure 1-3 –TMS1000D Designated Conduit Locations
1/2" NPT OR EQUIVALENT CONDUIT SIZE
A1 = PROBE INPUT / (2) SENSOR INPUTS
A2 = COMMUNICATIONS CABLES
A3 = RELAY INPUTS / OUTPUTS
A4 = POWER
A1 - A4
DENOTES CONDUIT
HOLES
A1 A2 A3 A4
DRAWING NO. 20176 REV. A

INSTRUCTION MANUAL TMS1000D
TMS1000D Installation.docx June 27, 2018
PAGE 8
1.3 LIQUID LEVEL PROBE DESCRIPTION
TMS1000D should be ordered with the MP550S magnetostrictive level probe. This probe will
provide inventory management on tanks up to 15’.
Figure 1-4 shows the standard MP550S probe with dimensions and specifications. Note the standard
probe requires a 2-inchfemale NPT tank fitting, and is supplied with a 6-foot cable; it does not include
the MOUNTING HARDWARE, which must be ordered separately. Before installing, verify the model
number matches the tank size intended, and that any accessories are available on site.
Figure 1-4 –Liquid Level Probe Outline
OPTIONAL 316 STAINLESS STEEL
FLOAT FOR 4" OPENINGS
MAX. DIA. 3.85"
PRODUCT
FLOAT
2.00"
BOTTOM
DEADBAND
8.00"
TOP
DEADBAND
OVERALL
LENGTH
316 STAINLESS
STEEL PRODUCT
FLOAT
MAX. Ø2.05"
7/8-16 UNS-2A
EXT. THREAD
Ø1.00"
PROBE CABLE
Ø.63 STAINLESS
STEEL FLOAT
GUIDE/SHAFT
EFFECTIVE
LENGTH
316 STAINLESS
STEEL LOCKING
COLLAR
316 STAINLESS STEEL
COMPRESSION FITTING
w/ TEFLON RINGS
(SEE NOTE 1)
316 STAINLESS STEEL,
POLYPROPYLENE OR
EQUIVALENT BUSHING
(SEE NOTE 1) NOTE:
1. STAINLESS STEEL COMPRESSION
FITTING AND BUSHING PURCHASED
SEPARATELY. POLYPROPYLENE BUSHING
SUPPLIED BY CUSTOMER.
.50"
DRAWING NO. 20168 REV. N/C

INSTRUCTION MANUAL TMS1000D
TMS1000D Installation.docx June 27, 2018
PAGE 9
1.4 LIQUID LEAK SENSOR DESCRIPTION
TMS1000D can be integrated with a variety of liquid sensors used for monitoring secondary
containment areas around tanks and pipes. The maximum is 2 sensors depending on the overall job
configuration; check the specific job design drawings for the actual number and type specified.
Figures 1-5 through 1-8 show four (4) typical sensor types provided by Pneumercator with their most
typical applications. Other non-Pneumercator models may be used; however, their use with
TMS1000D should have been approved before attempting to wire them into the system.
Figure 1-5 –LS600 LD Series
Figure 1-6 –ES825-300FL
DRAWING NO. 20006 REV. D
4.00"
[102]
Ø1.50"
[38] Ø1.75"
[45]
1/2" [13] LIQUID
TRIP POINT
304 STAINLESS
STEEL
BUNA N
FLOAT
NYLON
25' (7.5M) LONG
22AWG [.762 DIA.]
2-CONDUCTOR
CABLE
TEFLON
304 STAINLESS
STEEL
316 STAINLESS
STEEL FLOAT
LS600LDBN-1 LS600LDSS
4.00"
[102]
1/2" [13] LIQUID
TRIP POINT
DIMENSIONS: INCHES [MM]
DIMENSIONS: FEET (M)
CABLE GRIP CABLE GRIP
25' (7.5M) LONG
22AWG [.762 DIA.]
2-CONDUCTOR
CABLE
PULL RING
REMOVED
PASS-THRU OPENING SIZE
3/4" NPT MINIMUM
3 CONDUCTOR
CABLE
SHRINK TUBE
("C" & "X" VERSIONS ONLY)
CONVOLUTIONS ACCEPTS 1/2" ENT
REMOVABLE
PULL RING
20' OR 25'
22 AWG CABLE
.62"
(HEX FLAT) 3.00"
DRAWING NO. 20173 REV. N/C

INSTRUCTION MANUAL TMS1000D
TMS1000D Installation.docx June 27, 2018
PAGE 10
Figure 1-7 –LS610
Figure 1-8 –RSU800
DRAWING NO. 20008 REV. A
.236 [6] REF.
.40" [10]
3.02" [77]
1.50" [38]
Ø.130" [3.3]
PULL HOLE
1/2" [13] LIQUID
TRIP POINT
CABLE GRIP
25' (7.5M) LONG
CABLE
DIMENSIONS: INCHES [MM]
DIMENSIONS: FEET (M)
DRAWING NO. 20009 REV. N/C
16' LONG
22 AWGCABLE16' LONG
22 AWGCABLE
18.25"15.00"
CABLE GRIP
PVC HOUSING
11.00"
Ø2.88" Ø2.88"
2.25" 2.25"
HIGH
ALARM
LOW
ALARM
FLOAT
FLOAT
CABLE GRIP
15.00"
18.25"

INSTRUCTION MANUAL TMS1000D
TMS1000D Installation.docx June 27, 2018
PAGE 11
SECTION 2 –INSTALLATION DETAILS
2.1 INSTALLATION CHECKLIST
WARNING
Do NOT apply power to the TMS1000D until its installation has been checked and
found to be in accordance with these instructions; National Electric Code;
Federal, State and Local codes; and other applicable safety codes. FAILURE TO
COMPLY MAY RESULT IN PERSONAL INJURY, PROPERTY LOSS AND
EQUIPMENT DAMAGE.
The following points should be reviewed in preparation for installation, and again when installation is
complete.
1. Review Figure 3-3 to ensure that all of the safety/wiring requirements have been met.
2. Check that all equipment at job site matches the DESIGN DRAWING SPECIFICATIONS for the
tank sizes and control features required.
3. The console should never be mounted inside a hazardous area.
4. POWER to the console should be properly wired to a DEDICATED 120/240 VAC CIRCUIT
BREAKER. No other equipment can be powered from the same circuit breaker as the TMS.
5. System cannot be connected to equipment that uses or generates more than 250 volts with
respect to earth.
6. All TMS grounds must be terminated at the GND BUSS BAR in the same service panel as TMS
power. A grounding rod, coldwater pipe or other connection should not be used. Refer to Figure
3-2 for illustrated details.
7. The magnetostrictive probe input and the sensor inputs are two different circuits and must be
installed in separate cables or in one cable which has suitable insulation. Refer to NEC Article
504-30 (b) or CEC Appendix F6.3 for additional information.
8. Do not drill or modify enclosure. Use only conduit entries provided. Failure to comply will void
warranty and may present a safety hazard.
9. Probe/sensor cabling should be factory approved or electrical equivalents. Color-coding or
numbering is highly recommended.
10. WATERPROOFING FIELD WIRE SPLICES using factory supplied splice kits is required for
proper system operation.

INSTRUCTION MANUAL TMS1000D
TMS1000D Installation.docx June 27, 2018
PAGE 12
2.2 CONTROL CONSOLE INSTALLATION
The TMS1000D is designed for both indoor and outdoor installation. If the unit is to be installed outdoors, the
installer must pay attention to local code requirements for outdoor conduit runs containing AC line voltage.
2.2.1 MOUNTING
The TMS1000D is designed for wall mounting using the four mounting holes as shown in Figure 2-1. Mounting
hole placement is made easy using supplied 1:1 scale mounting template in Figure 2-2. Note that these
mounting holes are outside of the gasketed interior of the enclosure and therefore do not affect weatherproof
performance.
Figure 2-1 –Mounting Dimensions
DIMENSIONS: INCHES [MM]
97
16 [240]
4 [100]
OVERALL HEIGHT
65
16
[160]
213
16
[71]
17
16
[36]
101
4[260]
45
16
[110]
(4) Ø7
8[Ø22] HOLES FOR 1/2" NPT
OR EQUIVALENT CONDUIT FITTINGS
81
8[206]
13
16 [20]
(4)
MOUNTING
HOLES
21
8[54] 41
8[105] 61
8[156]
13
16 [20]
COVER
SHOWN
FOR REF.
3
8[10]
1 [25]
PROBE AND SENSORS
CONDUIT OPENING
COMMUNICATIONS
CONDUIT OPENING
AC POWER
CONDUIT OPENING
RELAY INPUTS/OUTPUTS
CONDUIT OPENING
USE (4) #10 [5] X 2" [50] LENGTH
MOUNTING SCREWS
(3/8" [10] MAX. SCREW HEAD DIA.)
SCREW
ANCHOR
DRAWING NO. 20167 REV. N/C
WARNING! This device is designed for Ordinary Location, Non-Hazardous
installation only, as defined by Underwriters Laboratories (UL) and the National
Electrical Code (NEC). DO NOT install where flammable vapors may be present.

DRAWING NO. 20166 REV. N/C
USE (4) #10 [5] X 2" [50] LENGTH
MOUNTING SCREWS
(3/8" [10] MAX. SCREW HEAD DIA.)
45
16 [110.0]
DIMENSIONS: INCHES [MM]
SCALE 1:1
97
16 [240.0]
NOTE: TEMPLATE MUST BE PRINTED WITHOUT SCALING (1:1) ON STANDARD
8 1/2" X 11" CLEAR LAMINATE OR COPY PAPER SHEET AS REQUIRED.
13
4[44.0]
33
4[94.8]
53
4[145.6]
73
4[196.4]
(4) CONDUIT
CENTERLINE
LOCATIONS
TMS1000 MOUNTING AND CONDUIT LOCATION TEMPLATE
3
8[10.0]
1 [25.0]
Figure 2-2
Mounting Template


INSTRUCTION MANUAL TMS1000D
TMS1000D Installation.docx June 27, 2018
PAGE 14
2.2.2 CONSOLE INTERIOR
Note that the console is divided into two electrical areas:
LEFT SIDE RIGHT SIDE
for Probe/Sensor signals for Power and Control
Figure 2-3 shows the console interior, again indicating the power and signal separation. THIS
SEPARATION MUST BE MAINTAINED when conduits are connected. Refer to Section 3 for
electrical conduit and wiring.
Figure 2-3 –Control Console Interior
DISPLAY CABLE
CONNECTOR
RS-232
CONNECTION
(2) LEDS
FUSE HOLDER
LINE VOLTAGE
SWITCH
115V
S1
TB1
OFF
250 VAC FAST ACTING
ON
S2
F1
1/2 AMP
AC
IN
HOT
NEUTRAL
GND
ISGND
+V
TB6 TB5
S1
GND
+V
S2
GND
+V
GND
SHD
IN
OUT
S
E
N
S
O
R
S
P
R
O
B
E
S3
J3 RS232
1 432
OPEN
DISPLAY
BOARD
J1 +5V +3.3V
D2 D3
J4
CC
CONTACT
CLOSURE INPUTS
NO
RELAY OUTPUTS
CC
NO
NO
NO
1
2
3
4
1
2
TB4
TB2
TB3
ON/OFF SWITCH
COMMUNICATIONS PORT
CONNECTOR
DIP
SWITCH
SENSOR PLUG-IN
TERMINAL BLOCK
PROBE PLUG-IN
TERMINAL BLOCK
RELAY I/O
STANDARD TERMINAL BLOCKS
AC POWER
STANDARD TERMINAL BLOCK
DRAWING NO. 20169 REV. N/C

INSTRUCTION MANUAL TMS1000D
TMS1000D Installation.docx June 27, 2018
PAGE 15
2.3 BUSHING OR FLANGE MOUNT METHOD FOR ALL TANKS
This method is recommended for DEF tanks with standard 2, 3 and 4-inch openings. The level probe
will "hang" inside the tank at a fixed position supported by the tank-mounting fitting. This will protect
the purity of the DEF by reducing the number of wetted materials.
Because the probe is fixed to the mounting fitting, it is critical during installation to allow a 1-INCH
BOTTOM CLEARANCE between the probe's FOOT REST and tank bottom or strike plate. This will
prevent the probe touching the tank bottom during tank expansion and contraction. The 1-inch
clearance dimension is standard and has been properly accounted for in the probe's manufacture.
The customer must supply an appropriate mounting fitting to mate with the tank opening, if less than
2 inches, to accommodate the PK2-DM3 Direct Mount Probe Kit. Assembly is as illustrated in Figure
2-5.
Figure 2-4 - Reducer Fitting or Flange Mounting for Aboveground Tanks
Install the level probe per Figure 2-4 as follows:
1. Select the correct probe for the tank. Match the model number with the tank internal dimensions
per Figure 1-4.
2. Remove the probe from its shipping container. Remove all packing material.
3. Slowly lower the probe into tank opening. The probe should be vertical with its electronic housing
totally visible above the tank fitting. When the probe touches the bottom, screw the bushing into
the tank. DO NOT tighten the compression fitting at this time. Mark the shaft and lift the probe up
1 INCH.
PROBE CABLE
LEVEL
PROBE
3/4" NPT
COMPRESSION FITTING
"MOUNTING HEIGHT"
1" BOTTOM
CLEARANCE
NOTE:
1. 2" NPT BUSHING WITH
COMPRESSION FITTING
PURCHASED SEPARATELY.
BUSHING / REDUCING FITTING
OR FLANGE (BY CUSTOMER OR
SEE NOTE 1 )
CABLE GRIP
TO CONSOLE
DRAWING NO. 20170 REV. N/C

INSTRUCTION MANUAL TMS1000D
TMS1000D Installation.docx June 27, 2018
PAGE 16
Figure 2-5 –MP55xS Probe Assembly Instructions - Direct Mount
ASSEMBLY INSTRUCTIONS - MP550S DIRECT MOUNTED MODEL
PNEUMERCATOR
Liquid Level Control Systems
8"
FOR INSTALLATION AND WIRING SEE TMS MANUAL
The top of the probe is an ungageable deadband. Verify that the probe is of sufficient length so that the float's magnet will not travel into
this deadband.
Questions? Contact Technical Support at (800) 209-7858
PROBE HEAD
Page 1 of 1
1
2
COMPRESSION *
FITTING
2" X 3/4" NPT *
BUSHING
S.S. COLLAR
PRODUCT
FLOAT
1/2"
* PURCHASED SEPARATELY FROM PNEUMERCATOR AS MODEL NO. PK2-DMx.
2" DIRECT MOUNTING ASSEMBLY
Diesel Emissions Fluid (DEF)
Bulletin 238 No Change (05/09/14)

INSTRUCTION MANUAL TMS1000D
TMS1000D Installation.docx June 27, 2018
PAGE 17
4. Tighten the cable connector on top of the probe housing to ensure a WATERTIGHT SEAL.
5. Route the probe cable to the junction box and complete the wiring installation in accordance with
Section 3
EXTERNAL LEAK SENSOR INSTALLATION
The interstitial or double-wall space of steel tanks and vaulted tanks as well as many other secondary
containment areas can be fitted with leak sensors. Also, for float type sensors, switch actuation may
be factory set for either NORMALLY OPEN or NORMALLY CLOSED.
2.4 LEAK SENSOR INSTALLATION IN STEEL AND VAULTED TANKS
Check the specific design drawings for the job, or choose the sensor type desired from Figures 1-5
and 1-6. Install sensor per Figure 2-6 as follows:
1. Remove the watertight CORD CONNECTOR supplied by sliding it off the sensor cable.
2. Thread the watertight CONNECTOR into the top of a 2" by 1/2" reducer bushing or monitor pipe
cap pre-tapped for a 1/2" NPT hole. (The use of any standard monitor cap from 2" to 4" pipe size
is recommended. The cap or reducer bushing IS NOT SUPPLIED with the sensor and must be
provided by the installer).
3. Measure the "MOUNTING HEIGHT" from top to bottom of monitoring pipe.
4. Feed the sensor cable through the watertight CONNECTOR from the BOTTOM SIDE of the
REDUCER (or CAP) fitting to a cable length suitable for the MOUNTING HEIGHT; or to allow
sensor to rest on the monitor pipe bottom; or as required by local codes. Cable may be cut or
extended to proper length.
5. Re-tighten the CORD CONNECTOR to fix the sensor cable length.
6. Mate the REDUCER or CAP to the top of the monitor pipe. Tighten the CONNECTOR to ensure
a WATERTIGHT SEAL.
7. Route the sensor cable to the junction box and complete the wiring installation in accordance with
Section 3.
Figure 2-6 –Leak Sensor Installation - Steel Vaulted Tanks
DRAWING NO. 20016 REV. C
DOUBLE WALL TANK
WATERTIGHT JUNCTION BOX
AND CONDUIT SEAL
MONITOR PIPE
CAP OR
REDUCER
MOUNTING HEIGHT
12" MINIMUM MANHOLE
IS REQUIRED FOR
UNDERGROUND TANKS
2" OR LARGER
MONITORING PIPE
LEAK SENSOR

INSTRUCTION MANUAL TMS1000D
TMS1000D Installation.docx June 27, 2018
PAGE 18
2.5 LEAK SENSOR INSTALLATION IN PIPING SUMPS AND DISPENSER PANS
Check the specific design drawings for the job, or choose the sensor type desired from Figures 1-5
and 1-6. Install sensor per Figure 2-7 as follows:
1. Measure the "MOUNTING HEIGHT" from conduit or junction box to the bottom of the SUMP (or
MANHOLE, VAULT or DISPENSER PAN).
2. Feed the sensor cable through the watertight CONNECTOR to length suitable for the MOUNTING
HEIGHT; or to allow sensor to rest on the containment bottom; or as required by local codes.
Feed an additional 12 inches past the CONNECTOR for splicing inside the junction box; cable
may be cut to proper length.
3. Thread the CONNECTOR into the WATERTIGHT JUNCTION BOX and tighten the
CONNECTOR cord grip over the cable to insure a WATERTIGHT SEAL. The sensor should rest
on the containment floor or as required by local codes.
4. Complete the wiring installation in accordance with Section 3.
Figure 2-7 –Leak Sensor Installation in Piping Sumps, Manholes, and Dispenser Pans
MOUNTING HEIGHT
SENSOR FLEXIBLE CABLE
LIQUID TIGHT
CABLE GRIP
WATERTIGHT JUNCTION BOX
AND CONDUIT SEAL
LEAK SENSOR
MANHOLE
PIPING SUMP OR
DISPENSER PAN
DRAWING NO. 20017 REV. D

INSTRUCTION MANUAL TMS1000D
TMS1000D Installation.docx June 27, 2018
PAGE 19
2.6 LEAK SENSOR INSTALLATION IN FIBERGLASS TANK ANNULUS
The annular space of fiberglass tanks can be fitted with either a "DRY ANNULUS" type sensor,
models ES825 (Figure 1-6) and LS610 (Figure 1-7), or a "WET RESERVOIR" sensor model RSU800
(Figure 1-8). The wet reservoir is also referred to as the HYDROSTATIC METHOD. Check the
specific design drawings for the job, or choose the type sensor desired from Figures 1-6 through 1-
8. Install sensor per Figures 2-8 or 2-9.
Instructions per Figure 2-8, DRY ANNULUS SENSOR:
1. Calculate the sensor cable's MOUNTING LENGTH from tank size data so the sensor rests at tank
bottom; or use the following method.
Determine the cable's MOUNTING LENGTH by
adding the cable measurement M from the table at
the right to the RISER HEIGHT. Mark the cable at
that length. DO NOT CUT THE CABLE.
2. Remove the watertight CORD CONNECTOR
supplied by sliding it off the cable.
3. Thread the CONNECTOR into the top of a 2" by
1/2" reducer bushing or riser pipe cap pre-tapped
for a 1/2" NPT hole. (The use of any standard
monitor capfrom 2" to 4" pipe size is recommended.
The cap orreducer bushing ISNOT SUPPLIED with
the sensor and must be provided by the installer).
4. At riser top, attach the annular space PULL CORD
(this is part of the tank supplier's pre-installed
accessories) to the sensor's PULL HOLE.
5. Pull the free end of the PULL CORD out of the riser while feeding the sensor into the riser and
through the annular space until the sensor is at the bottom centerline of the tank. The MOUNTING
LENGTH MARK should be about 5INCHES above the open riser. Adjust its position asnecessary
and, without disconnecting the PULL CORD, coil its excess inside the riser pipe.
6. Feed the sensor cable through the BOTTOM of the riser cap (or bushing), and through the CORD
CONNECTOR while positioning cap over the riser pipe. Mate riser and cap.
7. Tighten CONNECTOR over the cable to ensure a WATERTIGHT SEAL.
8. Complete the wiring installation in accordance with Section 3.
CABLE MEASUREMENT
FROM END OF SENSOR
Tank Dia. Cable M
4 Feet 81 in.
6 Feet 118 in.
8 Feet 150 in.
10 Feet 194 in.
12 Feet 222 in.
Table of contents
Popular Control Unit manuals by other brands

weintek
weintek MT8121XE Series Installation instruction
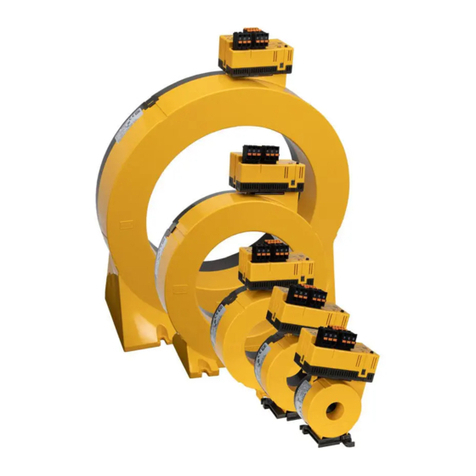
Bender
Bender MRCDB300 Series manual
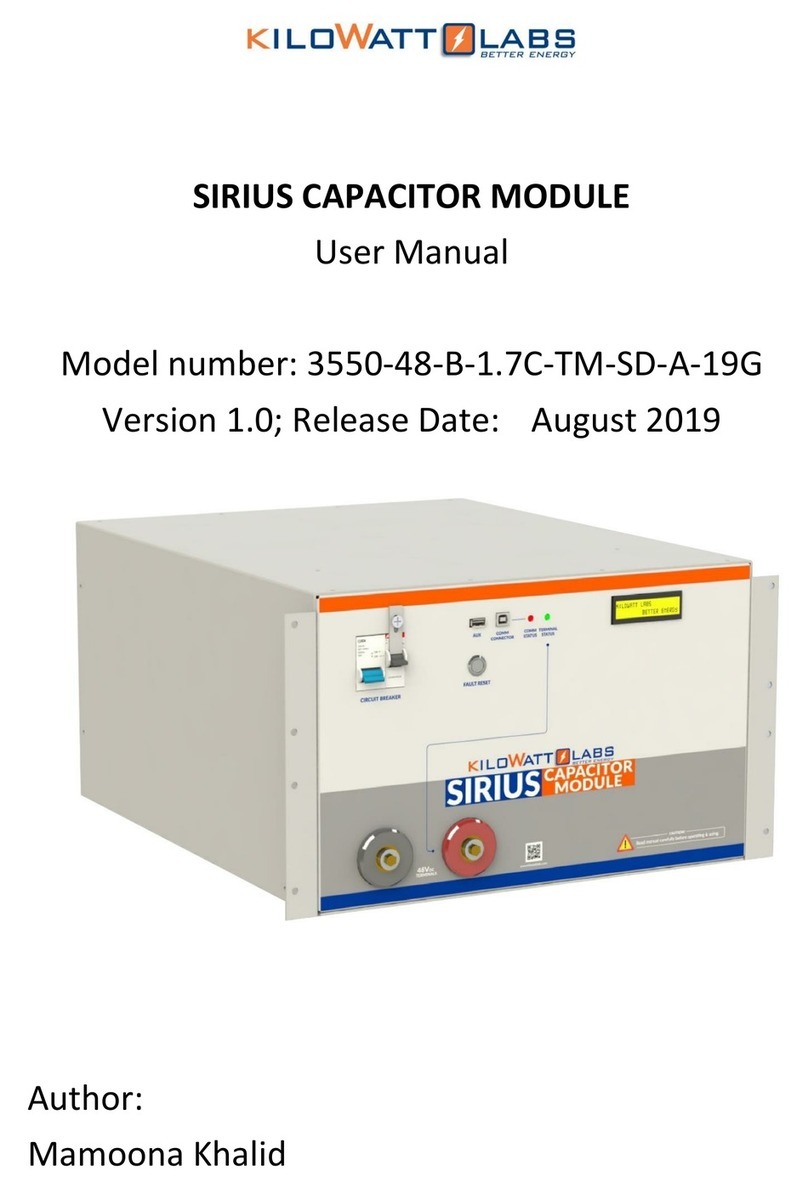
Kilowatt Labs
Kilowatt Labs Sirius 3550-48-B-1.7C-TM-SD-A-19G user manual
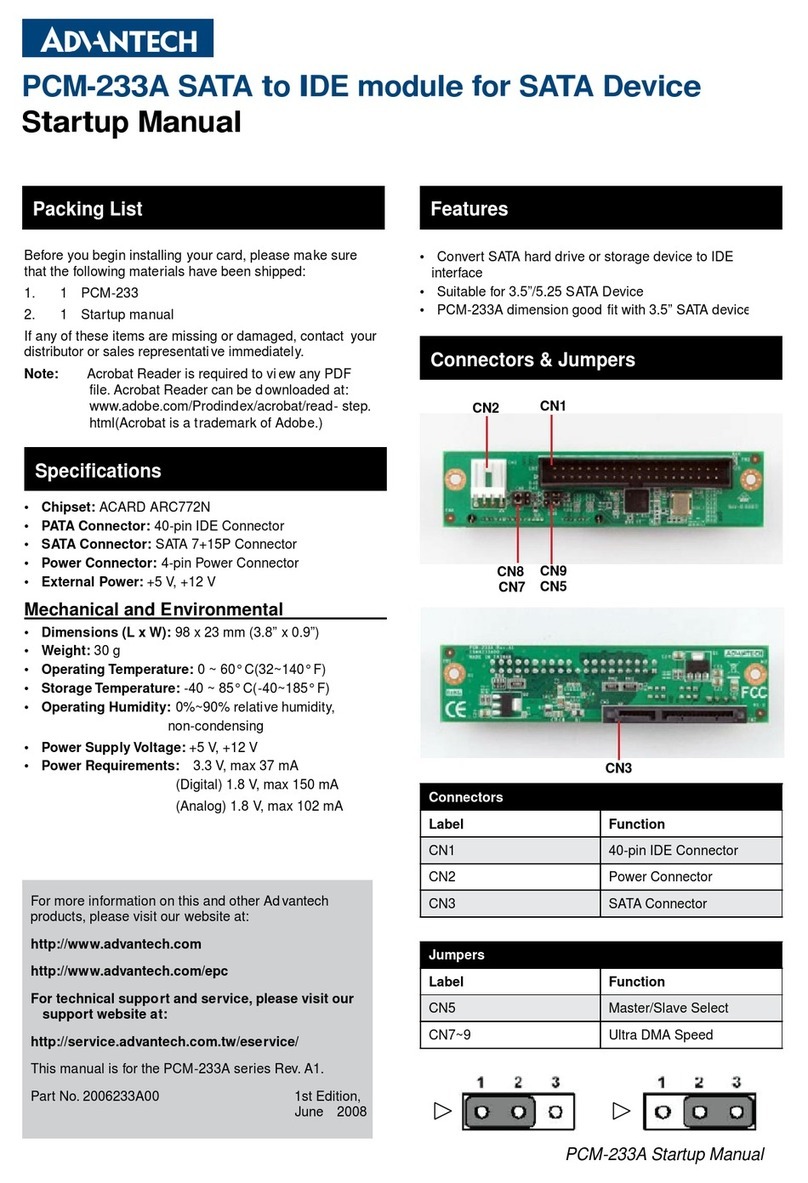
Advantech
Advantech PCM-233A Startup manual
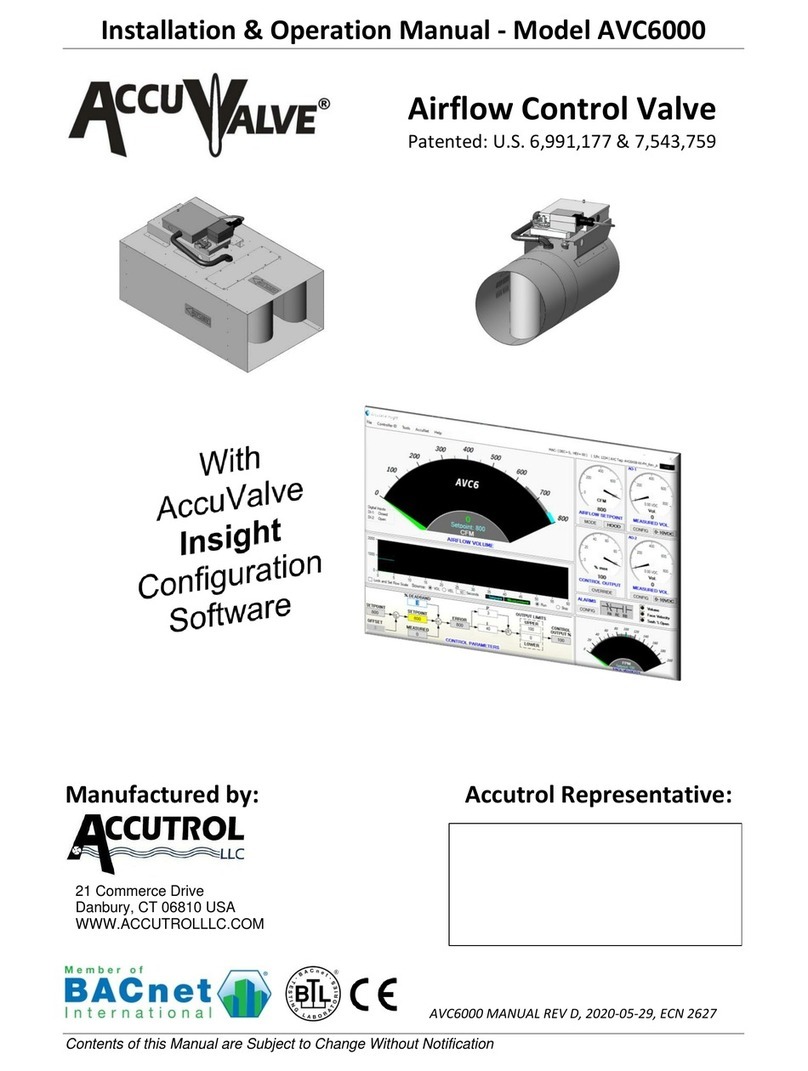
Accutrol
Accutrol ACCUVALVE AVC6000 Installation & operation manual

Eaton
Eaton EASY205-ASI Instruction leaflet