PQ Plus UMD 705 User manual

1
Operating Manual for
UMD 705E / CBM

2
Contents
1
General Description 1
1.1 improvements and advanced functions..............................................................................................1
2
Operating the Meter 2
2.1 Safety requirements when using UMD 705 ................................................................................... 2
2.2
Installation of the instrument.................................................................................................... 2
2.2.1 Supply voltage..................................................................................................................... 3
2.2.2 Measured voltage................................................................................................................ 3
2.2.3 Measured currents....................................................................................................................3
2.2.4 Communication peripherals ................................................................................................ 4
2.2.5
Outputs and inputs.............................................................................................................6
2.3
Downloading data to PC.......................................................................................................... 6
2.4 Energy meter readings ........................................................................................................................7
3
Technical Specifications 7
3.1
Basic Parameters..........................................................................................................................7
3.2 Measured Quantities............................................................................................................................9
3.3
Inputs and Outputs .....................................................................................................................12
4
Maintenance, Service, Warranty 13

3
1
General Description
The UMD 705 is specially designed for monitoring of energy and power quality in advanced
power systems and
smart grids. It is intended to be used mostly for DIN rail mounting. This
display-less design with multiple
communication options is suitable for a wide spectrum of
automation tasks in modern buildings, distributed power generation, remote supervision of
the infrastructure and also remote load management. Two different
user interfaces are offered
- UMD 705 D with a small embedded color display on the front panel for simple local
value
reading and an unobtrusive UMD 705 without display with limited ability for hostile user
interaction.
To protect the actual setup and collected data each instrument can be locked by
a custom pin. It uses standard
RS-485 serial line for communication with remote control
systems. Optionally it can be equipped with other
communication peripherals such as
Ethernet, USB.
It is equipped with three voltage inputs and three current inputs.
1.1
Improvements and advanced functions
new front panel display and control.
new power supply option U with 85-510 VAC aux voltage and two universal DIO ports
improved MIN/AVG/MAX measurement and evaluation
precise four quadrant active and reactive energy measurement with optional 10 ms
evaluation period - to
record fluctuations and fast changes of power flow direction
optional push-data function in modbus master - to feed the remote server automatically
Extended set of conditions and control actions in the IO programming section
optional Windows and Linux (ARM, x866) library for custom control software development

4
2
Operating the Meter
2.1
SafetyrequirementswhenusingUMD 705
Warning !
When working with the instrument it is necessary to perform all necessary measures
for the protection of persons and property against injury and electric shock.
The device must be operated by a person with all required qualifications for such
work and this person must know in detail the operation principles of the
equipment listed in this description!
When the device is being connected to the parts which are under dangerous voltage
it is necessary to comply with all the necessary measures to protect users and
equipment against injury with electrical shock.
Person, performing the installation or maintenance of the instrument must be
equipped with and must use
personal protective clothing and tools.
If the analyzer is used in a manner not specified by the manufacturer, the
protection provided by the
analyzer may be impaired.
If the analyzer or its accessories appear to be impaired or not functioning properly,
do not use it and send
it in for repair.
2.2
Installation of the instrument
Natural air circulation should be provided inside the distribution board cabinet, and in the
instrument’s neigh-
borhood. Especially underneath the instrument, no other
instrumentation that is source of heat should be
installed or the temperature value
measured may be influenced. A connection wire’s maximum cross section
area is 2.5mm
2
in case of all screw terminals.
The UMD 705 is primarily intended for DIN-rail mounting. Dimensions of the instrument are on figure
2.
There are also positions marked with dash dot lines of holes for wall-mounting with three screws.

5
58
21.5 10
60.6
30.3
106
UMD
705
Figure 2: Dimensions of the UMD 705 analyzer.
2.2.1
Supply voltage
The power supply terminal is labeled as X1 and X2. The two terminals are complemented
with a symbol (U, L or S), indicating the respective auxiliary voltage option (details in ch.
3). Proper supply voltage must be
connected to the terminals X1 and X2 via a circuit breaking
device (power switch –see installation diagram on figure 3). It has to be located left to the
instrument and easily reachable by the operator. The circuit breaking device must be identified
as the equipment power disconnection switch. A circuit breaker of the nominal value
1A is a
convenient circuit breaking device. Its function and position has to be clearly identified
(symbols ‘0’
and ‘I’ acc. to IEC EN 61010-1). Internal power supply is galvanically isolated
from internal circuits.
2.2.2
Measured voltage
The measured voltages are connected to the terminals L1, L2 and L3. Connect the neutral wire to the
terminal
N. With delta or Aaron connections terminal N remains unused. Voltage measurement inputs
are connected with internal circuits over high impedance.
It is suitable to protect the measured voltage lines for example with 1A fuses of the required
rating. Measured
voltages can also be connected via instrument voltage transformers. A
connection cable maximum cross section area is 2.5mm
2
for voltage terminals.
2.2.3
Measured currents
The instruments are designed for indirect current measurement via external CT only. Proper
current signal
polarity (S1 or S2 terminals, k or l in the older notation) must be observed.
You can check the polarity by the
sign of phase active powers on the instrument display, its
web pages or in the ENVIS.Daq application.
03
2014

6
RUNCHG ALM
U
U
X/5A current input option
The current signals from 5A or 1A instrument current transformers
must be
connected to the terminal pairs I11, I12, I21, I22, I31, I32 with a cable of maximum
cross section area 2.5mm
2
.
Option S:
10 ÷ 36VDC
Option L: 20
÷ 75VDC
Figure 3: An example of typical installation of UMD 705 instrument in a low voltage network —
options L or S
for various LVDC power supplies. Typical connection options for voltage
measurements: star, delta and single
phase feeders. Option E for Ethernet port remote
communication, option U for local USB communication port
(all instruments provide RS485
serial line).
2.2.4
Communication peripherals
All peripherals stated below are galvanically isolated from the rest of the instrument and from each other:
Ethernet interface (variant “E”)
100 Mbit Ethernet interface with RJ-45 connector (100Base-TX) labeled as
ETH is situated on a top
panel of the device. Ethernet interface can be used as substitution for the primary
RS-485 for
connection of the device to LAN and for easy connection of remote control PC.
USB (variant “CBM”)
Communication port for USB slave is located on the front panel. This communication port is
intended for
easy local configuration and fast download of archived data to the local PC. For correct operation it
needs a driver installed
in your operating system (see the ENVIS user guide for more info).
USB

7
RS-485 serial line
Serves usually as a remote communication for reading of actual data, archive downloading and device
configuration. Serial RS-485 line uses terminals A+, B- with shielding at terminal G of COM1 block (fig.
4). The end point of the communication line must be properly terminated with ˜120n resistor.
Figure 4: Typical wiring of the RS-485 communication line terminals in UMD 705

8
2.2.5
Outputs and inputs
Instrument provides two separate universal I/O ports with terminals C1,D1 and C2,D2. Each
DI/O port can
be used individually as an input or an output function. For a correct operation
of the I/O it is necessary to use
an external power supply with nominal voltage 12 to 24 VDC.
Appropriate polarity of supply voltage for input
resp. output function must be kept.
Warning !
Digital I/Os are unipolar. Right polarity must be kept for a proper operation of
the terminal.
Incorrectly connected external powersupply can damage the instrument.
DI/O as a digital input DI
is connected to the selected I/O terminal (D1 or D2) and a common
terminal
(C1 or C2) with external power supply in the following way: the current flows from
positive terminal of the
supply through the external input contact to a DI terminal (D1 or D2)
and than from the common terminal (C1 or C2) back to the negative terminal of the external
power supply.
DI/O as a digital output DO
is connected to the selected I/O terminal (D1 or D2) and a common
terminal
(C1 or C2) with external power supply in the following way: the current flows from
positive terminal of the
supply to the C1 or C2 terminal and from a DI terminal (D1 or D2)
through the controlled load to the negative
terminal of the supply. If an I/O port is used as
an output (its behavior is controlled by an internal logic
function) the instrument also indicates
its activation with the respective input register.
Figure 5: An example of output and input of UMD 705.
digital output
digital input

9
2.3
Downloading data to PC
Connect the instrument to the PC and run ENVIS.Daq application. Select the appropriate
communication option and connect to the instrument. In the next screen press Refresh All. This
will load and display the actual
status of each supported archive.
Device Information section contains editable description and name under which the actual record is
stored.
Time Frame for Other Archives tab allows you to limit the date ranges of all archives by the time
interval of the
main archive. In the Destination section the actual storage can be selected - either to
the SQL database or to
the file. The check boxes in Archives to Download determines which specific
archive(s) you want to download.
The actual download will start by pressing the Download All button. progress is displayed on screen.
When finished the archive can be viewed in the ENVIS application. User can open the downloaded file
directly from ENVIS.Daq.
2.4
Energy meter readings
UMD 705 has an embedded three phase, four-quadrant energy meter with automatic meter reading
functions and multiple programmable tariffs (Time-of-Use, TOU). The instrument registers active
energy (EP, EP+, EP-) and reactive energy (EQL, EQC or EQC+, EQC-, EQL+, EQL-). According to
the configuration of meter readings
are shuffled to the respective tariffs. It automatically provides
summaries per phase. For star connections and single phase measurements it can also register
energy for each phase separately.
Meter data readings can be downloaded and analyzed in ENVIS or via the standard ModBus protocol
in any other system.
3
Technical Specifications
3.1
Basic Parameters
Auxiliary Voltage
model „230V“
model „24V"
aux. voltage range
85 ÷ 510 VAC
85 ÷ 350 VDC
20 ÷ 75 VDC
power supply
7 VA / 3 W
3,5 VA / 3,5 W
overvoltage category
III (300V)
II (100V)
pollution degree
2
connection
isolated, polarity free

10
OtherSpecifications
operationaltemperature
- 20 to 60°C
storagetemperature
- 40 to 80°C
operational and storage humidity
< 95 % - non-condensable environment
EMC –immunity
EN 61000 –4 - 2 (6 kV / 8 kV)
EN 61000 –4 - 3 (10 V/m up to 3 GHz)
EN 61000 –4 - 4 (4 kV)
EN 61000 –4 - 5 (2 kV
LL
/ 4 kV
LG
)
EN 61000 –4 - 6 (10 V)
EN 61000 - 4 - 8 (100 A / 1000 A)
EN 61000 –4 - 11 (250 periods)
EMC –emissions
EN 55011, class A
EN 55022, class A (not for home use )
communicationports
RS-485 (2400 ÷ 921600 Bd), optional USB, Ethernet
10Base-T
communication protocols
KMB, Modbus RTU and TCP, web server, DHCP
accuracy of RTC
± 2 seconds per day
capacity of RTC backup battery
> 5 years (without supply voltage applied)
protection
class front
panel whole
instrument
IP 40
IP 20
dimensions front
panel
wholeinstrument
106 x 45 mm
106 x 90 x 58 mm
weight
max. 0.25 kg

11
3.2
Measured Quantities
MeasuredQuantities –Voltage
Frequency
f
NOM
–nominalfrequency
50 / 60 Hz
measuringrange
40 ÷ 70 Hz
uncertainty
± 10 mHz
Voltage
voltage input option
standard variant („230 V“)
U
NOM
(U
DIN
)–rated voltage
180 ÷ 280 V
AC
measuringrangeline-to-
neutral
4 ÷ 420 V
AC
measuringrangeline-to-line
7 ÷ 720 V
AC
intrinsicuncertainty
(t
A
=23±2ºC)
+/- 0.05 % of rdg ± +/- 0.05 % of rng
temperaturedrift
+/- 0.03 % of rdg ± +/- 0.01 % of rng / 10 ºC
measurement category
300V CAT III
permanentoverload
1820 V
AC
( UL–N )
peak overload, 1 second
2730 V
AC
( UL–N )
burden power ( impedance)
< 0.05 VA ( Ri = 3.78 MΩ )
VoltrageUnbalance
measuringrange
0 ÷ 10 %
measuring uncertainty
± 0.3% of rdg or ± 0.3
THDU
measuringrange
0 ÷ 20 %
measuring uncertainty
± 0.5
Harmonics (up to 50
th
order )
referenceconditions
other harmonics up to 200 % of class 3 acc. to IEC 61000–2-4
ed.2
measuringrange
10 ÷ 100 % of class 3 acc. to IEC 61000–2-4 ed.2
measuring uncertainty
twice the levels of class II acc. to IEC 61000–4-7 ed.2

12
MeasuredQuantities–Current, Temperature
Current
current input option
„X/100mA“
„X/5A“
I
NOM
(I
B
) –rated (basic)
current
0.1A
AC
5A
AC
measuringrange
0.00025 ÷ 0.15 A
AC
0.0125 ÷ 7.5 A
AC
intrinsic uncertainty (t
A
=23
±2 ºC)
+/- 0.05 % of rdg ± +/- 0.05 % of rng
temperaturedrift
+/- 0.03 % of rdg ± +/- 0.01 % of rng / 10 ºC
measurement category
600V CAT III
600V CAT III
permanentoverload
1 A
AC
10 A
AC
peakoverload
1second,maximum
repetition frequency > 5
minutes
10 A
AC
90 A
AC
burden power ( impedance)
< 0.001 VA (Ri< 0.1
Ω)
< 0.5 VA (Ri<10mΩ)
CurrentUnbalance
measuringrange
0 ÷ 100 %
measuring uncertainty
± 1 % of rdg or ± 0.5
Harmonics & Interharmonics (up to 50
th
order )
referenceconditions
other harmonics up to 1000 % of class 3 acc. to IEC 61000–2-4
ed.2
measuringrange
500 % of class 3 acc. to IEC 61000–2-4 ed.2
measuring uncertainty
Ih <= 10 % I
NOM
: ± 1 % I
NOM
Ih > 10 % I
NOM
: ± 1 % of rdg
THDI
measuringrange
0 ÷ 200 %
measuring uncertainty
THDI <= 100 % : ± 0.6
THDI > 100 % : ± 0.6 % of rdg
Temperature (internal sensor, measured value affected by the instrument power dissipation)
measuringrange
- 40 ÷ 80°C
measuring uncertainty
± 2 ºC

13
Measured Quantities –Power, Power Factor, Energy
Active / Reactive Power, Power Factor (PF), cos φ(P
NOM
= U
NOM
x I
NOM
)
reference conditions
“A”: ambient
temperature (t
A
) U,
I
for active power, PF,
cos φfor reactive
power
23 ± 2 ºC
U = 80 ÷ 120 % U
NOM
, I = 1 ÷ 120
% I
NOM
PF = 1.00
PF = 0.00
act. / react. power uncertainty
± 0.5 % of rdg ± 0.005 % P
NOM
PF & cos φuncertainty
± 0.005
reference conditions
”B”: ambient
temperature (t
A
) U,
I
for active power, PF,
cos φfor reactive
power
23 ± 2 ºC
U = 80 ÷ 120 % U
NOM
, I = 2 ÷ 120
% I
NOM
PF >= 0.5
PF <= 0.87
act. / react. power uncertainty
± 1 % of rdg ± 0.01 % P
NOM
PF & cos φuncertainty
± 0.005
temperature drift ofpowers
± 0.05 % od rdg ± 0.02 % P
NOM
/ 10 ºC
Energy
measuringrange
corresponds to U & I measuring ranges
4 quadrant energy counters for both
active and reactive energies
active energyuncertainty
class 1 acc. to EN 62053 –21
reactive energyuncertainty
class 2 acc. to EN 62053 –23

14
3.3
Inputs and Outputs
Digital Outputs & Digital Inputs: universal 1+1 DIO (only models with „U“auxiliary voltage)
DigitalOutputs
type
Opto-transistor, unipolar (Cx +, Dx -)
loadrating
35 V
DC
, 30 mA
DC
dynamic parameters (pulse
output):
-
pulseduration
-
gapduration
-
maximumfrequency
S0 -
compatible
50 ms
>= 50 ms
10 Hz
DigitalInputs
type
Opticaly isolated, unipolar (Cx -, Dx +)
maximumvoltage
30 V
DC
voltage for “logical 1“
> 7 V
DC
voltage for “logical 0“
< 3 V
DC
inputcurrent
5 mA @ 12V / 13 mA @ 24V
dynamic par. (pulse counter):
-
pulse/gapduration
-
maximumfrequency
>= 0.5 / 0.5 ms
1 kHz

15
4
Maintenance, Service, Warranty
Maintenance:
the UMD 705 power analyzer does not require any additional maintenance during its
operation besides the regular maintenance processes for the whole cabinet. For reliable operation it
is only necessary to
meet the operating conditions specified and not expose the instrument to violent
handling and contact with
water or chemicals which could cause mechanical damage.
The lithium cell built in the instrument can backup a real time circuit for more than 5 years without
power
supply, at average temperature 20
➦
C and load current in the instrument less than 10µA. If the
cell is empty, it
is necessary to ship the instrument to the manufacturer for battery replacement.
The 18350 rechargable Li-ion battery cell for the instrument operation backup is also optionally
installed
inside the UMD 705 option S or L. If the battery malfunctions it is necessary to ship the
instrument to the
manufacturer for battery replacement.
Service:
In the case of failure or a breakdown of the product, you should contact the PQ Plus GmbH:
PQ PLUS GmbH
Hagenauer Str. 6
91094 Langensendelbach
info@pq-plus.de
+49 9133-60640-0
www.pq-plus.de
The product must be in proper packaging to prevent damage during transit. A description of the
problem
or its symptoms must be delivered together with the product.
If a warranty repair is claimed, the warranty certificate must be sent in. In case of an out-of-warranty
repair you have to enclose an order for the repair.
Warranty certificate:
warranty period of24 monthsfrom the date of purchase is provided fortheinstrument,
however, no longer than 30 months from the day of dispatch from the manufacturer. Problems in the
warranty period, provably because of faulty workmanship, design or inconvenient material, will be
repaired free of charge
by the manufacturer or an authorized servicing organization.
The warranty ceases even within the warranty period if the user makes unauthorized modifications or
changes
to the instrument, connects it to out-of-range quantities, if the instrument is damaged
due to ineligible or
improper handling by the user, or when it is operated in contradiction with the
technical specifications presented.
Type of product: UMD 705 ……………. Serial Number: ……………………………………………
Date of dispatch: ……………………….. Final quality: ………………………………………………
Inspection: …………………………….... manufacutrer’s deal: …………………………………….
Date of purchase: ……………………… supplier’s deal: ……………………………………………
Other manuals for UMD 705
1
This manual suits for next models
2
Table of contents
Other PQ Plus Measuring Instrument manuals
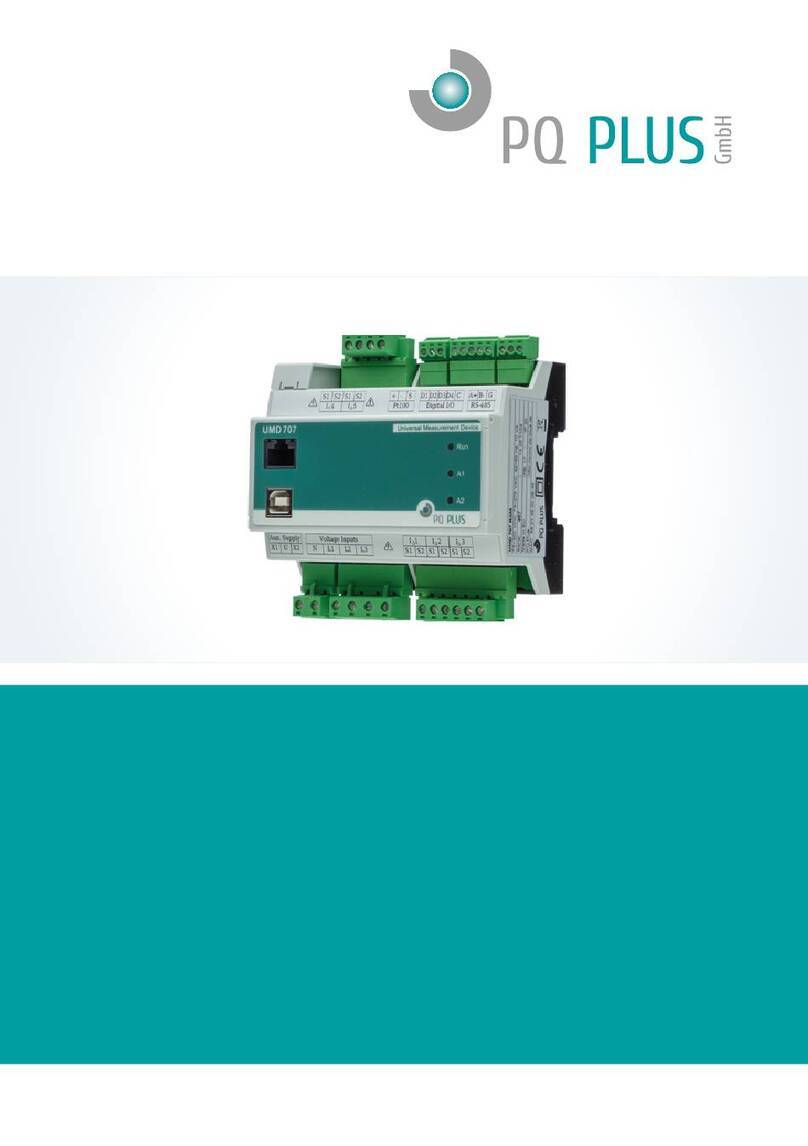
PQ Plus
PQ Plus UMD 707 Instruction manual
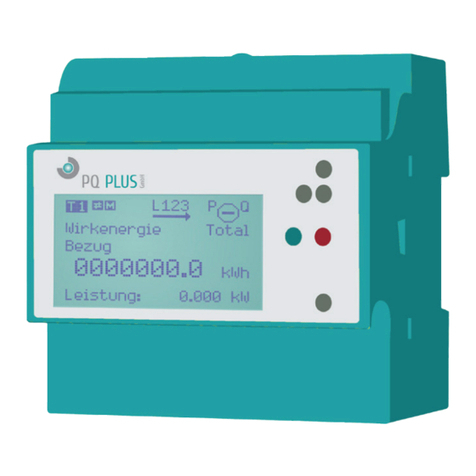
PQ Plus
PQ Plus CMD 68-54 Instruction manual
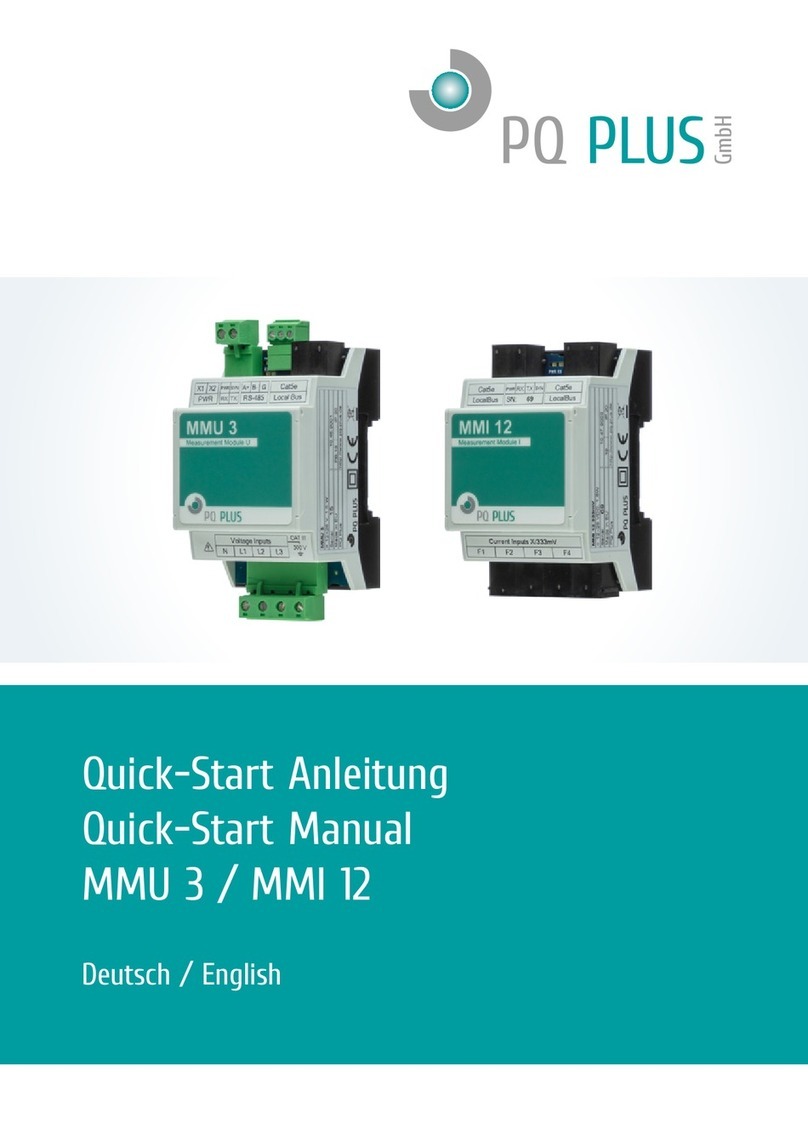
PQ Plus
PQ Plus MMU 3 Instruction manual
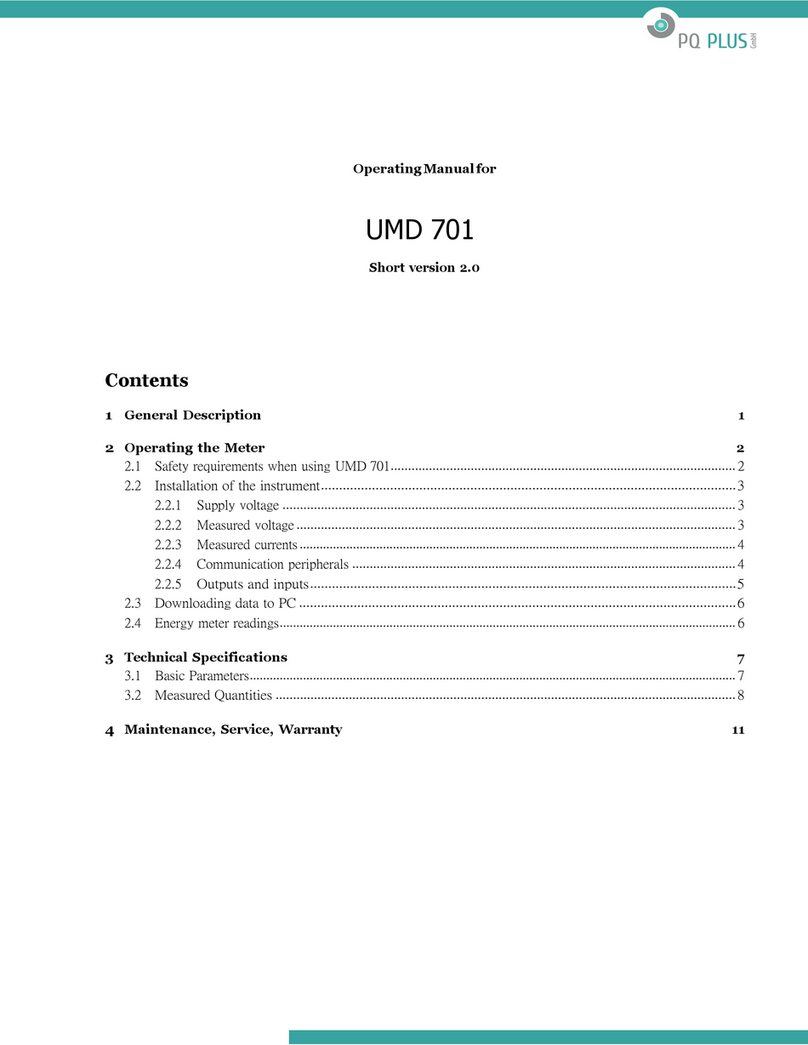
PQ Plus
PQ Plus UMD 701 User manual

PQ Plus
PQ Plus UMD 807 E User manual
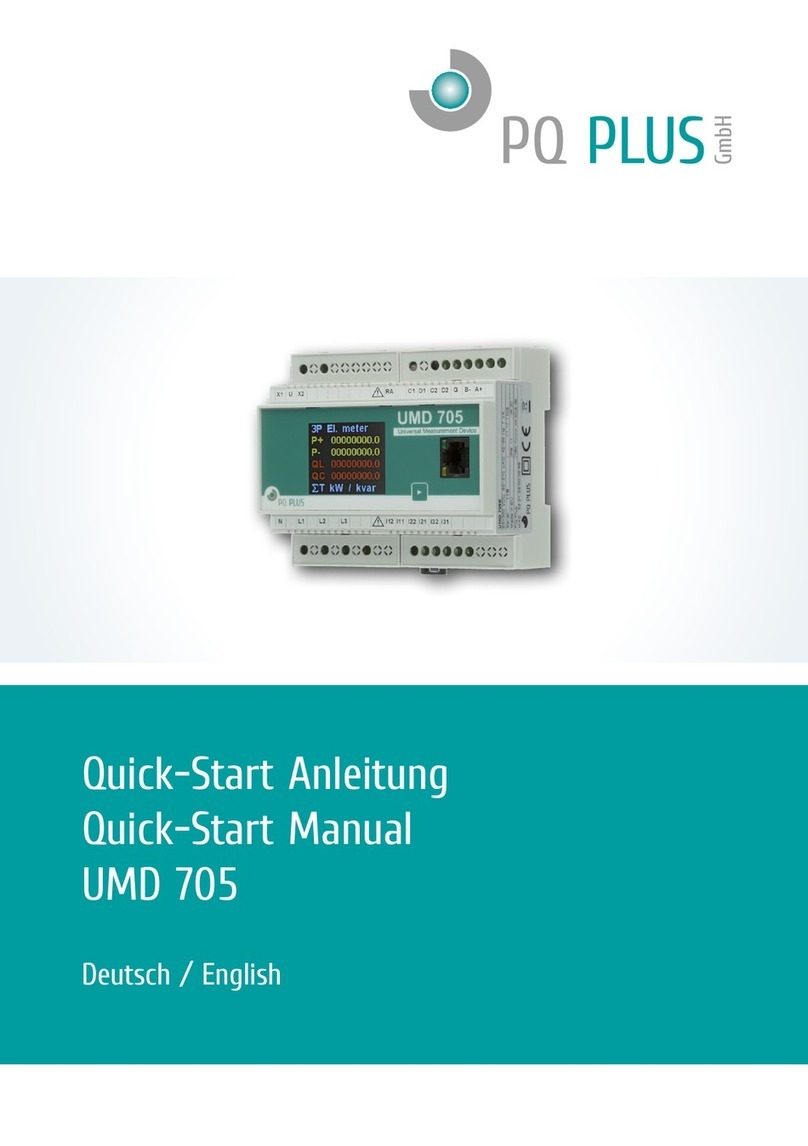
PQ Plus
PQ Plus UMD 705 Instruction manual
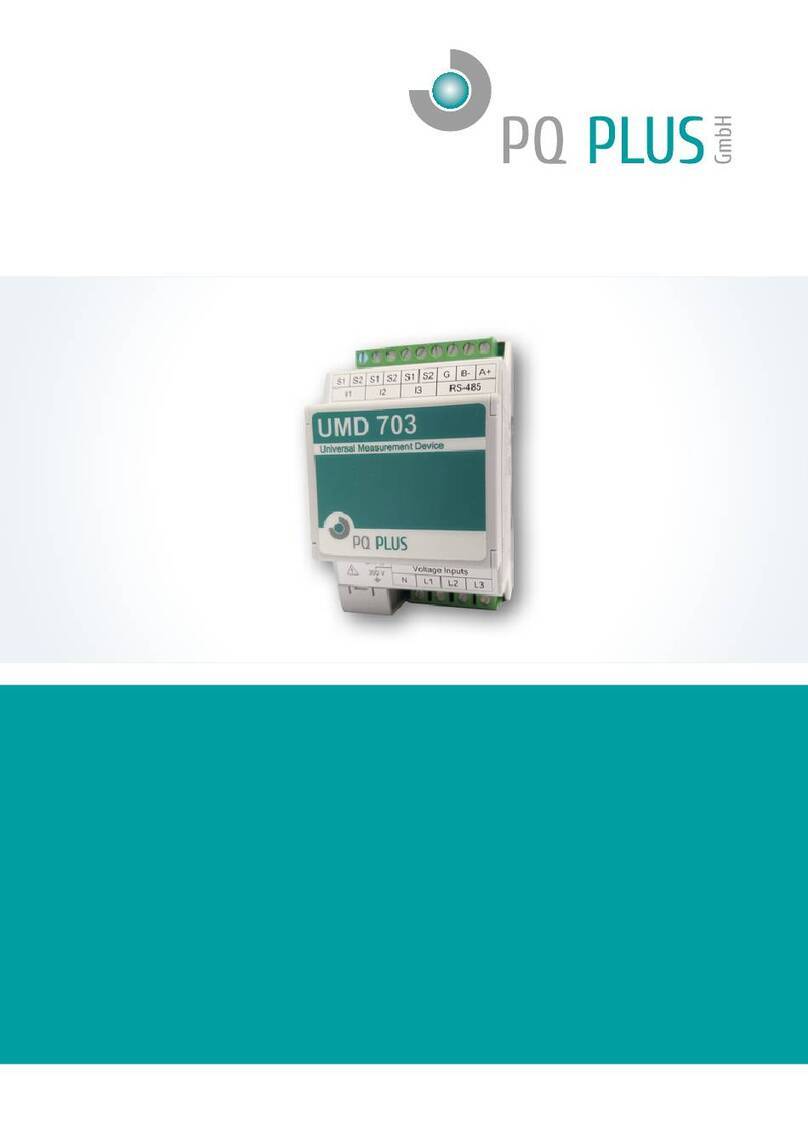
PQ Plus
PQ Plus UMD 703 Instruction manual
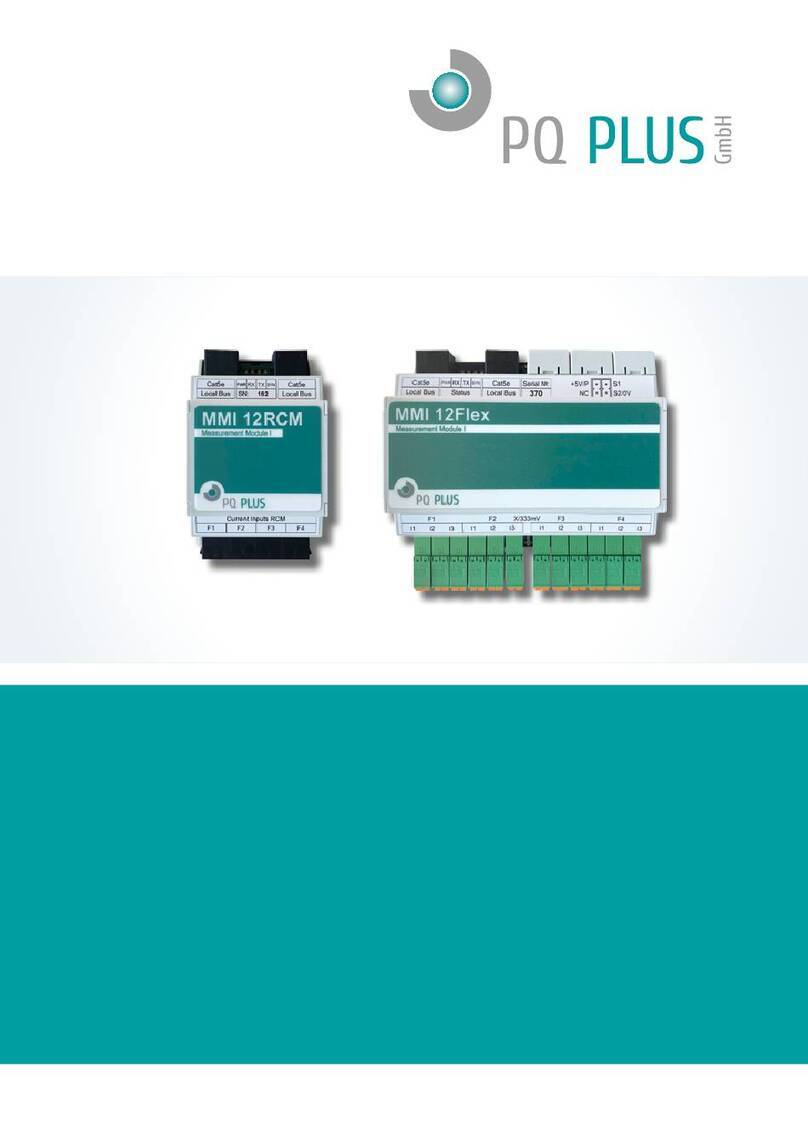
PQ Plus
PQ Plus MMI 12RCM Instruction manual
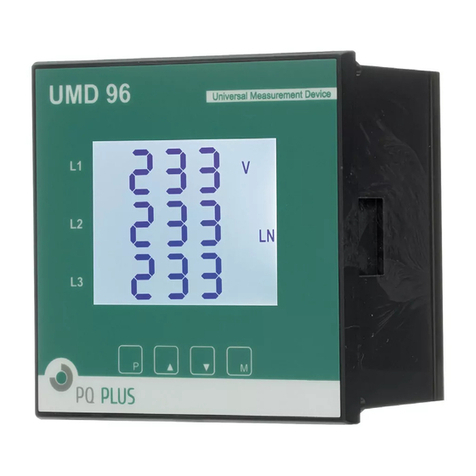
PQ Plus
PQ Plus UMD 98 Instruction manual
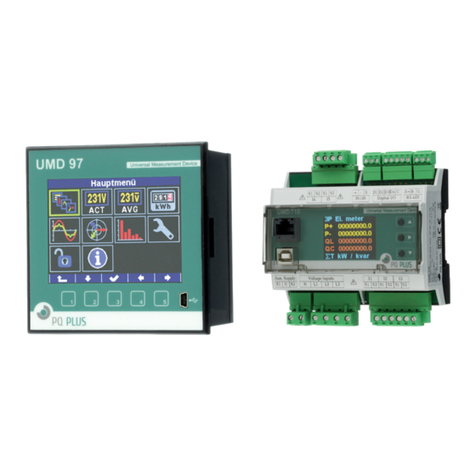
PQ Plus
PQ Plus UMD 97EVU Instruction manual