Pulsar dBi 3 User manual

dBi PA series
Intelligent Transducer
INSTALLATION MANUAL
Full manual available @ www.pulsarmeasurement.com
M-DBiPA—000-001-4P
Declaration No. 001004
This declaration of conformity is issued under the sole responsibility of the
manufacturer.
We, the undersigned:
Name of manufacturer/
authorised representative: Pulsar Measurement
Address: Cardinal Building
Enigma Commercial Centre
Sandys Road
Malvern
Worcestershire
WR14 1JJ
Country: UK
Declare under our sole responsibility that the following apparatus:
Apparatus:
description:
Ultrasonic Transducers,
dBi Profibus PA series
Model or Type
No.:
dBi 3, dBi 6, dBi 10 & dBi 15 Ex ia & FISCO
Field device versions
Brand name:
dBi Profibus PA series
Are in conformity with the following relevant EU legislation:
Directives Standards
Electricity Safety (LVD) 2014/35/EU EN61010-1: 2010
EMC: 2014/30/EU EN61326-1: 2013
ATEX general 2014/34/EU EN60079-0: 2012+A11 2013
ATEX (IS) EN60079-11: 2013
RoHS directive 2011/65/EU
I declare that the apparatus named above has been tested and
complies with the relevant sections of the above referenced
standards & directives
The following Notified Body has been involved in the conformity
assessment process:
Notified body: Element Materials Technology Rotterdam B.V.
Notified body No.: 2812
Role: Issue of ATEX EU Type Examination certificate.
Certificate No.: EMT18ATEX0014X
IEC EMT18.005X.
ATEX coding: II 1 G Ex ia IIC T4 Ga & II 1 D Ex ia IIIC T130°C Da
Tamb -40°C to +80°C & FISCO Field Device.
Name and position of person binding the manufacturer or authorised
representative:
Signed:
Name: Tim Brown
Function: Electronics Engineer
Location: Pulsar Process Measurement Ltd.
WR14 1JJ, UK.
Issue date: 23rd November 2020.
UK Office
Cardinal Building
Enigma Commercial Centre
Sandy’s Road Tel: +44 (0)1684 891371
Malvern Fax: +44 (0)1684 575985
WR14 1JJ
United Kingdom
Website www.pulsarmeasurement.com
Canada Office
16456 Sixsmith Drive
Long Sault
ON Tel: 613-938-8956
K0C 1PO Toll Free: 855-300-9151
Canada
Website www.pulsarmeasurement.com
USA Office
11451 Belcher Road South
Largo Tel: 315-788+9500
FL 33773 Toll Free: 888-473-9546
USA
Website www.pulsarmeasurement.com
PULSAR MEASUREMENT CONTACT DETAILS
Check the cable & enclosure are intact; splits or cracks
render the equipment unsafe; remove it from service.
There are no user-serviceable parts.
Remove power before installation or decommissioning.
Dispose of transducer and cable in accordance with
regional environmental regulations for electronic equipment
e.g. WEEE regulations apply within the EU Directive
2012/19/EU
MAINTENANCE & DISPOSAL
EU DECLARATION OF CONFORMITY

The installation is now complete; refer to the PULSARultra user
manual for instructions on how set up the PULSARultra instrument.
dBi FLANGE DIMENSIONS
EN1092 (BS 4504) All dimensions in mm
Size
A
B
C
No. holes
50
165
19
125
4 -18mm
80
200
19
160
8 -18mm
100
220
19
180
8 -18mm
150
286
19
240
8 -23mm
200
337
19
295
12 -23mm
ANSI Class 150 All dimensions in mm
Size
A
B
C
No. holes
2
165
19
121
4 -18mm
3
200
19
152
4 -18mm
4
220
19
190
8 -18mm
6
286
19
241
8 -22mm
8
343
19
298
8 -22mm
Wire the transducer into the relevant PULSARultra instrument as
shown in figure 6. Terminal numbers will depend on the unit.
DESCRIPTION
The dBi Profibus PA transducer range has been specified and
designed to meet the demanding requirements of today’s process
level measurement applications for liquids and solids.
All dBi Profibus PA transducers are 2 wire and draw approx. 20mA
from the bus. The dBi Profibus PA transducers are set up using either
a Profibus PA network or Pulsar PA modem and PA PC software
package.
The dBi Profibus PA transducer is based on a PZT ceramic element.
The nominal beam angle is 10 0 @ -3 dB (depending on unit). When
coupled with the DATEM®signal processing they provide unmatched
performance in industrial process level measurement.
All dBi Profibus PA transducers are fitted with internal temperature
compensation.
Optional submersion shield is available to prevent spurious signal if
the transducer becomes submerged.
A range of flange mounting options (ANSI & EN1092) with or
without a PTFE facing to give improved chemical resistance is
available.
An aiming kit is recommended for solids level measurement, to help
focus on the material surface angle of repose.
Standard cable lengths: 5, 10, 20 or 30m.
Process Connection: 1” BSP & M20 adaptor
Operating Temperature: -40 to +80°C
Ingress Protection: IP68
Enclosure Material: Valox 357
GENERAL INSTALLATION
The dBi Profibus PA transducer should be installed directly above
the liquid or solid level with the transducer axis perpendicular to the
surface to be measured.
The transducer can be installed using the 1” BSP thread on the top
of the transducer or with the supplied 1” BSP to M20 thread adapter.
See figure 1 for example.
In some applications, it may not be possible to install the transducer
using either a flange or the 1” BSP thread, in these circumstances it
may be possible to suspend the transducer from its cable. In these
installations, it is recommended that the transducer be secured using
a small chain fitted to one of the chain holes on the top of the
transducer, see figure 2.
When installing the transducer avoid aiming the transducer directly
at fixed obstructions as they may mask the required return echo from
the liquid or solid level being monitored, see figure 3.
Flanged versions of the transducer should be installed using plastic bolts with an insulating
gasket between the transducer flange and the process vessel flange. The bolts should not
be fully tightened as this may cause acoustic resonance that results in increased ring down.
A typical flange application is shown above.
Figure 1
Figure 2
Figure 3
HAZARDOUS AREA INSTALLATION
dBi Profibus PA transducers are ATEX certified for use in hazardous
areas. The product is certified as Ex ia and for FISCO (see label for
more information), they are certified for use in Zone 0,1 & 2 when
used with the correct barriers.
The ‘X’ in the Certification No.’s indicates that certain special
conditions apply. See EU Declaration of Conformity on the flip side
of this document.
Wiring Detail
Colour
Description
Limits
RED
DC Power +ve
Max 28V DC
BLACK
DC 0V
GREEN
Cable Screen
ATEX labelling for the two versions of protection Ex ia & FISCO
X Limitations on use:
1. Electrostatic hazard –The dBi transducers must only be wiped with a
damp or anti-static cloth.
2. Special condition of safe use: The Profibus PA transducer must be
powered by either an ATEX approved barrier or FISCO ATEX approved
power supply that meet the following parameters:
3. The dBi transducers must be routinely inspected to avoid the build-up
of dust layers when installed in Zones 20, 21 & 22.
4. The power supply cable to the transducers shall meet the relevant
installation requirements of clause 9, EN60079-14.
5. The equipment is considered suitable for use in a FISCO system only
when it is installed in accordance with EN60079-25.
The dBi Profibus PA transducer is designed to work in a Profibus
system. The Profibus PA devices are normally connected to a
Profibus DP system via a segment coupler.
A segment coupler translates the DP messages to PA and vice
versa, it also performs a transfer rate change as Profibus PA bus
normally runs at 31.25KBaud, whereas the DP bus can run up to 12
MBaud. The PA devices on the segment coupler are addressed
transparently by the Profibus DP Master.
The number of devices that can be placed on the PA bus is
dependent on the segment coupler used and the power requirements
of the PA devices. The Pulsar dBi Profibus PA transducer draws
20mA in normal operation.
The segment coupler will be designed either Exia or FISCO. The
FISCO standard allows for more current in the PA bus meaning more
PA field devices can be powered from one bus.
The cable length on a PA bus should not exceed 1000m.
PROFIBUS SYSTEM
This manual suits for next models
4
Other Pulsar Transducer manuals
Popular Transducer manuals by other brands
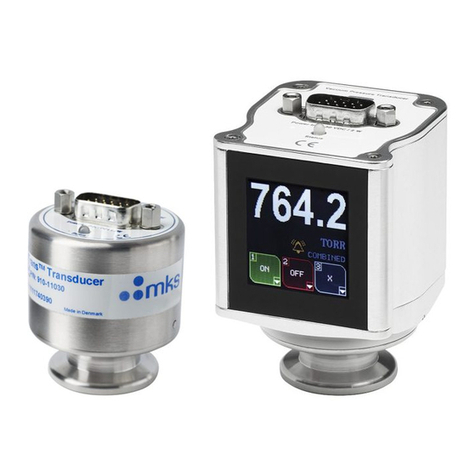
MKS
MKS 910 DualTrans Series Owner's operation and maintenance manual
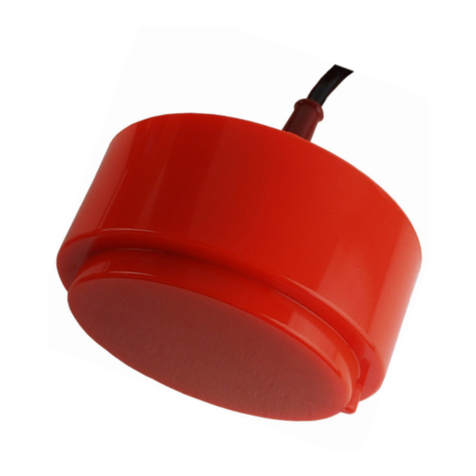
Simrad
Simrad ES70-7C - INSTALLATION REV B installation manual
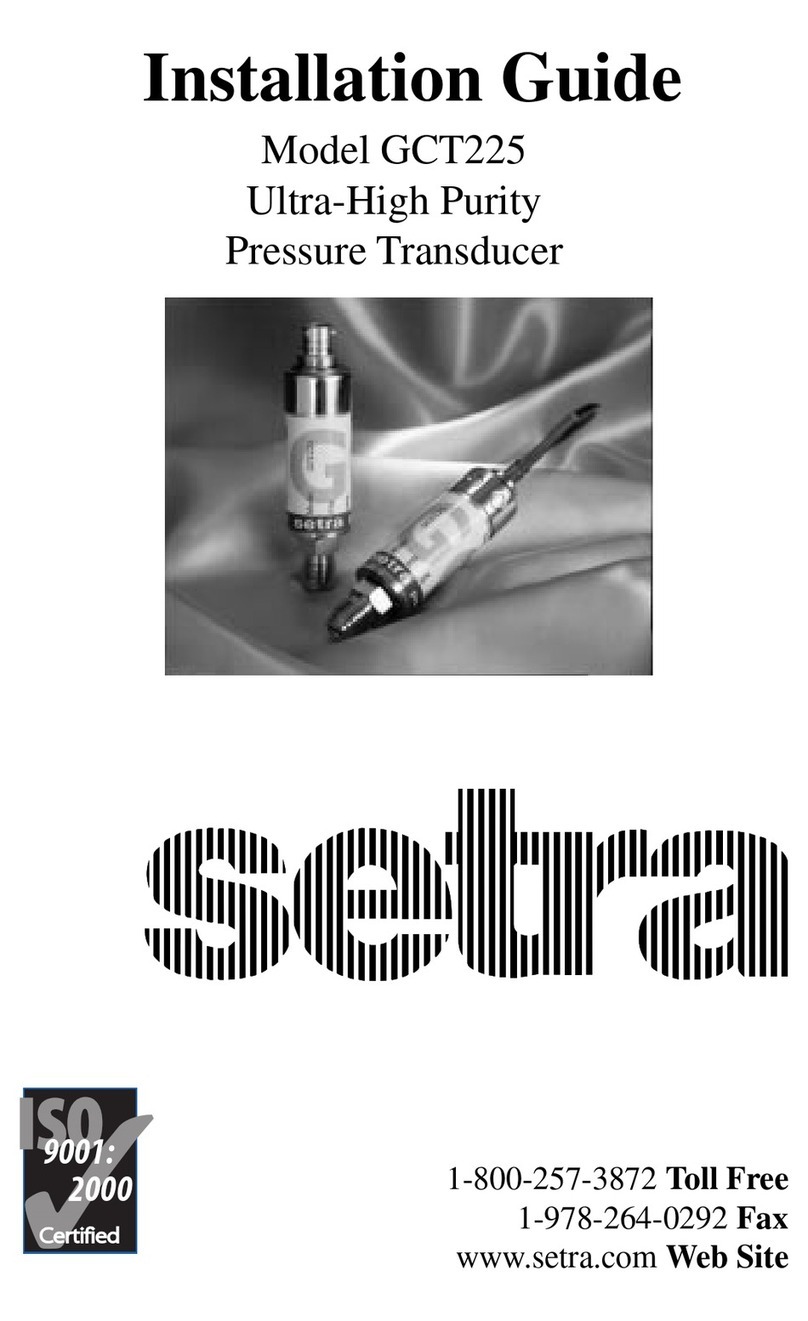
Setra Systems
Setra Systems GCT225 installation guide

Swagelok
Swagelok S user manual

Airmar
Airmar CM599LH Owner's guide and installation instructions
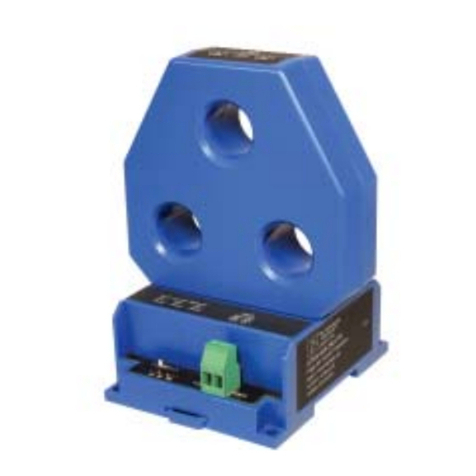
NK TECHNOLOGIES
NK TECHNOLOGIES AT-TH Series instructions

SENSONETICS
SENSONETICS SEN-410 Series installation instructions
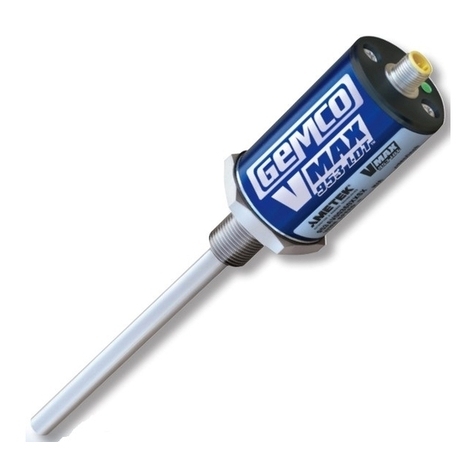
Ametek
Ametek Gemco 953 Series installation manual
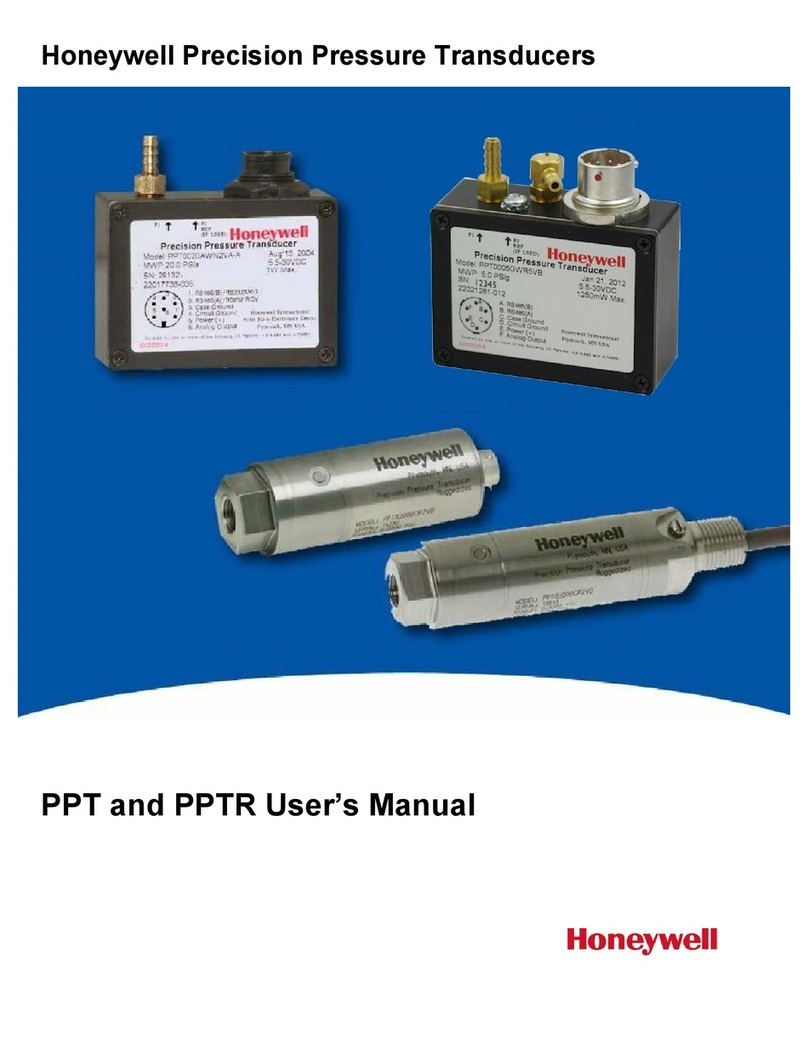
Honeywell
Honeywell PPT user manual
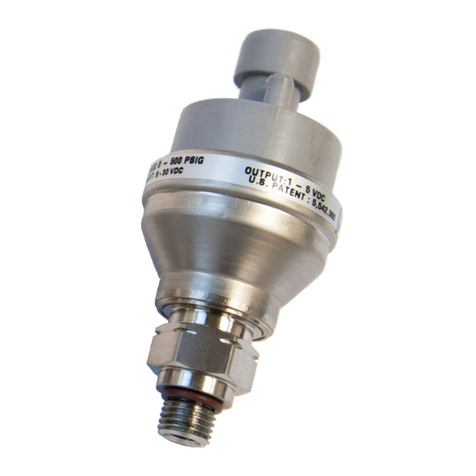
Setra Systems
Setra Systems 209 installation guide
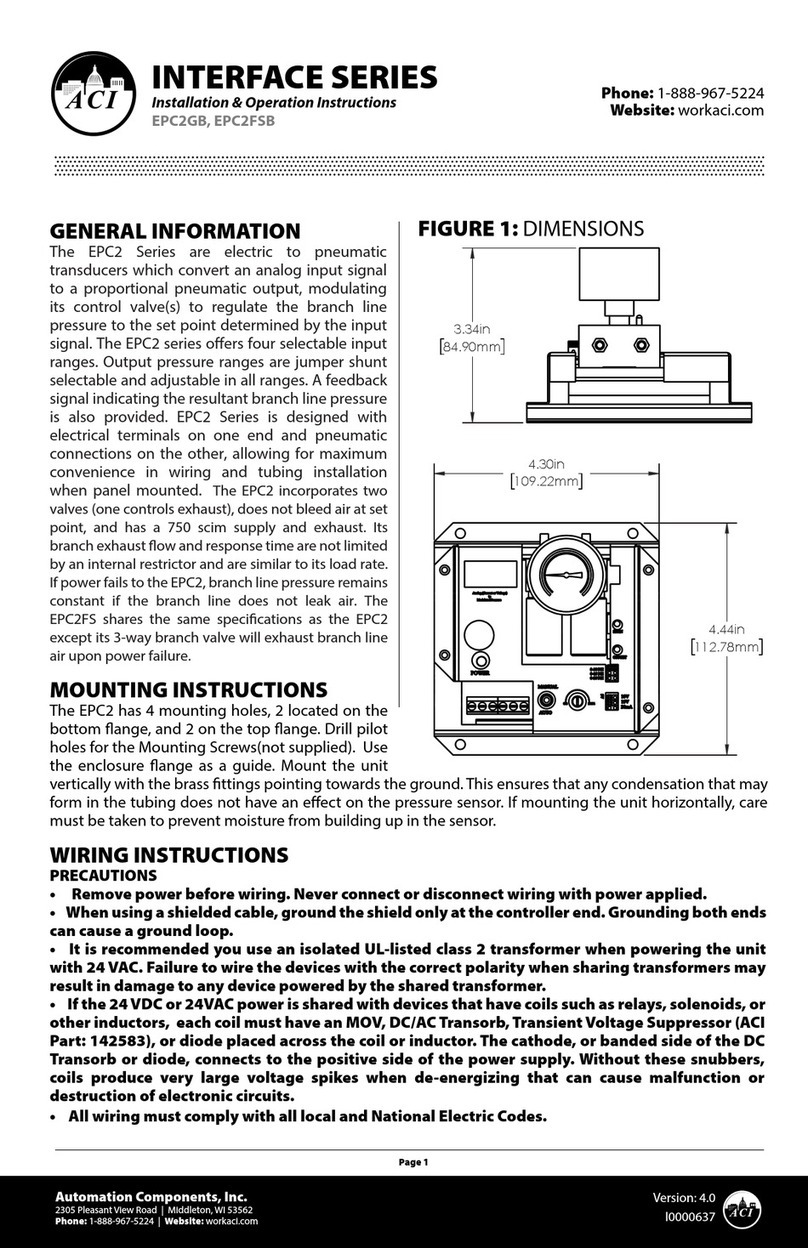
aci
aci ACCESS series Installation & operation instructions

Balluff
Balluff MICROPULSE BTL7-A/E1 0-M Series Condensed guide