Re ICENI/AI-04 User manual

Instruction Manual
ICENI/AI-04
4 Channel RTD Input Module
Pub_3645 - Issue 1

ICENI/AI-04
© Regulateurs Europa Ltd 2014
The contents of this document are the exclusive
Property of Regulateurs Europa Ltd
They must not be copied or reproduced without the
written authorisation of the Company
Pub_3645 Page 2 of 25

ICENI/AI-04
INDEX
1FOREWORD............................................................................................................5
2GENERAL USE.......................................................................................................6
2.1 General........................................................................................................6
2.2 Product Condition......................................................................................6
2.3 Signal Connection......................................................................................6
2.4 Module Damage / Repair............................................................................6
3PRODUCT OVERVIEW...........................................................................................7
3.1 Iceni Node...................................................................................................7
3.2 ICENIbus Interface .....................................................................................8
3.3 Field Wiring Interface.................................................................................9
4ICENI/AI-04 KEY FEATURES...............................................................................10
5PRODUCT SPECIFICATION ................................................................................11
5.1 Electrical Properties.................................................................................11
5.1.1 Power Supply Input ......................................................................11
5.1.2 Signal Channels ...........................................................................11
5.1.3 Fault Status Indication..................................................................11
5.1.4 Signal Isolation.............................................................................11
5.1.5 Field Wiring Termination...............................................................12
5.2 Mechanical Properties .............................................................................13
5.2.1 Temperature Range .....................................................................13
5.2.2 Material.........................................................................................13
5.2.3 Weight ..........................................................................................13
5.2.4 Ingress Protection.........................................................................13
5.2.5 Dimensions...................................................................................13
6UNPACKING & INITIAL PREPARATION FOR USE............................................14
6.1 Unpacking.................................................................................................14
6.2 Node Assembly ........................................................................................14
6.3 Node Disassembly ...................................................................................14
6.4 Module Positioning Within a Node .........................................................15
7FIELD WIRING TERMINATION ............................................................................16
7.1 Terminal & Connector Layout.................................................................16
7.2 Wiring Schematic .....................................................................................16
7.3 Earthing / Grounding ...............................................................................17
Pub_3645 Page 3 of 25

ICENI/AI-04
8MODULE USER INTERFACE ...............................................................................18
8.1 Indicators..................................................................................................18
8.2 Pushbutton ...............................................................................................18
9MODULE OPERATION..........................................................................................19
9.1 Module Configuration ..............................................................................19
9.2 Signal Configuration................................................................................19
9.3 Signal Measurements ..............................................................................19
9.4 Module & Signal Failure Detection .........................................................20
10 DATA COMMUNICATIONS TO MASTER MODULE .............................................22
11 SOFTWARE VERSION..........................................................................................23
12 CONTACT..............................................................................................................24
13 REVISION HISTORY..............................................................................................25
Pub_3645 Page 4 of 25

ICENI/AI-04
1 FOREWORD
These instructions have been compiled to assist personnel responsible for the
operation and maintenance of equipment manufactured by Regulateurs Europa
Ltd.
Care has been taken to ensure that the equipment has been accurately
represented, but it should be appreciated that, with the continued progress of
design and the diversity of application, certain items may differ in detail.
It should be noted that these instructions are issued for general information and do
not constitute a specification of the equipment.
Whilst reserving the right to make any alteration in design which they may
consider advisable the manufacturers absolve themselves from making any such
alteration retrospective.
In addition to the information given herein, practical advice and assistance is
always available from the Customer Support Department at Regulateurs Europa
Ltd.
Pub_3645 Page 5 of 25

ICENI/AI-04
2 GENERAL USE
Before carrying out any repairs, adjustments or maintenance to any equipment
supplied by Regulateurs Europa Ltd, it is essential the following safety precautions
be observed.
2.1 General
The operator should take care to make themselves thoroughly familiar with the
operating principles, methods of adjustment and the dismantling and assembly
procedures (where applicable) concerning the equipment in use.
2.2 Product Condition
Before power-up ensure that the product is in a good condition and not damaged,
paying particular attention to the ICENIbus connectors on each side of the module
and the field wiring connectors at the top of the module. Ensure that any wires are
fitted securely into terminals.
2.3 Signal Connection
If the module requires configuration then ensure that any critical signals are
disconnected from the module until configuration of the module has been
performed. This will prevent unwanted or unexpected changes in signal polarity
from affecting other circuitry.
2.4 Module Damage / Repair
The Iceni modules are not repairable. Where damage is found that could
compromise the operation of the module, a replacement part should be sourced
from Regulateurs Europa Ltd.
Iceni module should be disposed via an approved disposal scheme suited to
electronic products and in accordance with local legislation.
Pub_3645 Page 6 of 25

ICENI/AI-04
3 PRODUCT OVERVIEW
3.1 Iceni Node
An Iceni node comprises of a master module, between one and sixteen signal
conditioning modules and at least one power supply module.
A typical Iceni node:
master signal conditioning modules power
module (x8 in this example) supply
module
According to the mix of signal conditioning modules, the Iceni node manages the
measurement and generation of electrical signals to/from sensors and field
devices. Information is exchanged with other nodes in a system via a field
communications network connected to the Iceni master module.
Pub_3645 Page 7 of 25

ICENI/AI-04
3.2 ICENIbus Interface
Iceni modules are designed to plug together to form a node. The connection
system used to join one module to another is called ICENIbus and is used to
transfer both data and power supply between modules.
All modules have a 10-way ICENIbus connector on both sides of the lower
housing, although for end modules (master and main power supply) one side
connector will be supplied fitted with a protective cover.
ICENIbus
connectors
ICENIbus ICENIbus
power power
data
field communications network
field devices
& sensors
field devices
& sensors
power
signals
signalssignals
signals
Pub_3645 Page 8 of 25

ICENI/AI-04
3.3 Field Wiring Interface
As standard, Iceni modules are supplied with screw-clamp field wiring connectors,
although cage-clamp variants are available as an option.
For ICENI/AI-04 there are four connectors marked 1-4, 5-8, 9-12 and 13-16 to
match the numbers marked on the Iceni housing. This arrangement identifies the
connector to its location on the module.
When fitted properly, the field wiring connectors are held securely in the module
housing. In order to remove a terminal, a small flat bladed screwdriver should be
inserted between the top of the connector and the module housing to enable the
connector to be carefully levered free. This will release the connector without
damage.
Pub_3645 Page 9 of 25

ICENI/AI-04
4 ICENI/AI-04 KEY FEATURES
The ICENI/AI-04 module is a component of an Iceni node and provides four
isolated input channels for monitoring field temperature sensors (fluids, bearings,
motor windings, etc.)
The ICENI/AI-04 module provides the following key features:
oFour sensor inputs, each configurable to support PT100, PT200, PT500 and
PT1000 type sensors (alpha = 0.00385).
oSignal fault indication via illuminated channel indicator on ICENI/AI-04 module
and on master module display.
oMeasured real world value (i.e. measured temperature) available to field
communications network and master module display.
oSignal health status available to field communications network and master
module display.
Pub_3645 Page 10 of 25

ICENI/AI-04
5 PRODUCT SPECIFICATION
5.1 Electrical Properties
5.1.1 Power Supply Input
Maximum ICENIbus consumption: 200mA
5.1.2 Signal Channels
Number of channels: 4
Input type: RTD
Sensors supported: PT100, PT200, PT500, PT1000
(European curve / alpha = 0.00385)
Sensor characteristic supported: 3-wire
2-wire (for low loop resistance and / or
high resistance sensor types)
Accuracy: +/- 0.5% fsd
Update rates: 10Hz (at master module)
20Hz (internal)
Signal filtering: software and hardware
Input resistance: > 1MOhm
Signal measurement range: -200°C to 850°C (-328°F to 1562°F)
5.1.3 Fault Status Indication
Faults sensed: sensor open circuit
sensor short circuit
sensor resistance too low
sensor resistance too high
5.1.4 Signal Isolation
Signal channel to signal channel: none
Signal channel to external power supply: 1kV
Signal channel to other modules: 1kV
Pub_3645 Page 11 of 25

ICENI/AI-04
5.1.5 Field Wiring Termination
4 x 4-way free part sockets with screw terminals. (Cage-clamp option available)
Wiring cross section / strip length 0.14 to 0.5mm2/ 7mm
Pub_3645 Page 12 of 25

ICENI/AI-04
5.2 Mechanical Properties
5.2.1 Temperature Range
Operating: -20°C to +70°C (-4°F to +158°oF)
Storage: -40°C to +85°C (-40°F to +185°F)
5.2.2 Material
Enclosure: Polyamide
Labels: Polyester
Membrane overlay: Polyester
5.2.3 Weight
Module weight
(including free part screw terminals): 130g (approx.)
5.2.4 Ingress Protection
Assembled node: IP20
5.2.5 Dimensions
(Dimensions shown in mm)
22.5
99
114
Pub_3645 Page 13 of 25

ICENI/AI-04
6 UNPACKING & INITIAL PREPARATION FOR USE
6.1 Unpacking
The module should be removed from the sealed bag inside the protective cardboard
carton. All packaging should be disposed of in an appropriate way.
6.2 Node Assembly
The module is designed to clip and fit onto TS 35 DIN terminal rail (both standard
and deep types) with other Iceni modules to form a node. A metal clip is provided on
the base of each module for this purpose.
DIN rail clip
An Iceni node can be mounted in both vertical and horizontal orientations according
to terminal rail layout. Assembly of the Iceni node can be achieved in one of two
ways:
oThe Iceni node (including the ICENI/AI-04 module) can be assembled on a
bench and then fitted into place on the DIN rail with a slight tilting action. It is
important that the metal DIN rail latch on the underside of each module engages
properly with the rail to retain the modules in place.
oThe ICENI/AI-04 module can be fitted with other modules one at a time on the
DIN rail with a slight tilting action. It is important that the metal DIN rail latch on
the underside of each module engages properly with the rail to retain the module
in place. The modules can then be pressed together tightly to ensure that each
module plugs into its neighbour to form the node.
6.3 Node Disassembly
Disassembly of the Iceni node is essentially the reverse of the procedure above and
can be achieved in one of two ways:
oEach module can be separated from the next on the rail. The metal DIN rail latch
can then be operated with a small screwdriver and the modules removed with a
tilting action, one by one.
oThe metal DIN rail latches for all modules can be released in turn with a small
screwdriver until the Iceni node is free to be removed with a tilting action. The
modules can then be separated from each other.
Pub_3645 Page 14 of 25

ICENI/AI-04
6.4 Module Positioning Within a Node
The ICENI/AI-04 module/s should be fitted in any of the yellow locations shown in
the diagram below according to the total number of signal conditioning modules
assembled in the node.
1 16
Modules should be assembled with population starting at position 1 on the left hand
side, continuing towards position 16 on the right.
Pub_3645 Page 15 of 25

ICENI/AI-04
7 FIELD WIRING TERMINATION
7.1 Terminal & Connector Layout
CHANNEL TERMINAL DESCRIPTION
1 R+
2 R-
3 LOOP
1
4 -
CHANNEL TERMINAL DESCRIPTION
5 R+
6 R-
7 LOOP
2
8 -
CHANNEL TERMINAL DESCRIPTION
9 -
10 LOOP
11 R-
3
12 R+
CHANNEL TERMINAL DESCRIPTION
13 -
14 LOOP
15 R-
4
16 R+
1234
5678
9101112
13 14 15 16
(- : not connected)
7.2 Wiring Schematic
R+
LOOP
RTD
ICENI/AI-04
R-
Notes:
oFor 3-wire operation, wiring for R+, R- and LOOP must be the same length and
cross sectional area (CSA).
oFor 2-wire operation, R- and LOOP should be linked at the ICENI/AI-04
module terminals. Wiring for R+ and R- must be the same length and cross
sectional area (CSA).
Pub_3645 Page 16 of 25

ICENI/AI-04
7.3 Earthing / Grounding
The metal terminal rail to which the Iceni node is attached should be connected to a
‘clean’ earth / ground point. In many applications this would be the chassis of the
product.
It is recommended that screened signal cables are used, with the screen connected
to a ‘clean’ earth / ground point at the Iceni node end only. This might be via the
terminal rail, for example.
Pub_3645 Page 17 of 25

ICENI/AI-04
8 MODULE USER INTERFACE
8.1 Indicators
The top face of the module presents the following status indicators:
module health status
channels 1 to 4
signal status
8.2 Pushbutton
The top face of the module presents a pushbutton for access to channel information
on the master module display:
pushbutton
Pub_3645 Page 18 of 25

ICENI/AI-04
9 MODULE OPERATION
9.1 Module Configuration
Following power up the ICENI/AI-04 module will wait for the master module to
automatically configure the Iceni node.
During the configuration process, the module health status indicator will flash green.
Following a healthy node configuration, the module health status indicator will light
green continuously.
If the ICENI/AI-04 module loses communication with the master module, a self-reset
will take place and the module will await re-configuration. During this period, the
health status indicator on the ICENI/AI-04 module will flash green.
Following a ‘cold’ power up each channel will take up to approximately 15 seconds to
initialise and present a measurement value. However, the value may not be accurate
until the module has reached a stable operating temperature. It is recommended that
the module is left to ‘warm up’ for at least thirty minutes before the values are
considered accurate.
Following a ‘warm’ power up (where the power has been removed for greater than
two minutes) each channel will take up to approximately 15 seconds to initialise and
present a measurement value. However, the value may not be accurate until the
module has reached a stable operating temperature. It is recommended that the
module is left to ‘warm up’ for at least five minutes before the values are considered
accurate.
9.2 Signal Configuration
Each signal input can be configured to accept a PT100, PT200, PT500 or PT1000
type RTD sensor. Configuration is initiated by pressing the pushbutton on the
ICENI/AI-04 module and then following the configuration procedure provided by the
master module display.
9.3 Signal Measurements
The resistance across the sensor, and across the cable loop is measured at each
input channel and combined in a calculation to establish the temperature sensed by
each RTD sensor.
This real world measured temperature value (in °C or °F) is made available to the
field communications network and shown on the master module display.
Scaling for input signals is such that a value of 500 represents a real world measured
temperature of 500°C or 500°F, according to the temperature units selected.
Pub_3645 Page 19 of 25

ICENI/AI-04
9.4 Module & Signal Failure Detection
The ICENI/AI-04 module and its input signals are monitored at regular intervals by
the master module to check their health status.
The following faults are detected locally by the ICENI/AI-04 module:
Field Communications
NetworkFault
Type Fault
Category Master
Display
ICENI/AI-04
Channel
Status
LED Measured
Value Status
Value
sensor resistance
(PT100) < 15 Ohms
(PT200) > 30 Ohms
(PT500) > 75 Ohms
(PT1000) > 150 Ohms
minor
signal fault measured signal :
‘warning: low R’ flashing -200°C
-200°F 1
sensor resistance
(PT100) > 395 Ohms
(PT200) > 790 Ohms
(PT500) > 1975 Ohms
(PT1000) > 3950 Ohms
minor
signal fault measured signal :
‘warning: high R’ flashing 850°C
850°F 2
sensor
short circuit major
signal fault measured signal :
‘fault: s.circuit’ off -9999°C
-9999°F 3
sensor / cable loop
open circuit major
signal fault measured signal :
‘fault: o.circuit’ off 9999°C
9999°F 4
The faults above are non-latching and will self-reset when the failure condition is
removed.
In addition, the following faults are detected by the master module:
Field Communications
Network
Fault
Type Fault
Category Master
Display
Master
Fault
Status
Output Measured
Value Status
Value
field communications
network attempts to
access data for a
signal channel > 4
network
access
fault -- 9999°C
9999°F
7
(channel
unavailable)
ICENI/AI-04 module
stops responding to
master module
module
fault
module status
shown as
flashing red
de-
energises - 8
(module lost)
The faults above are non-latching and will self-reset when the failure condition is
removed.
With the system operating in a healthy state the following will be observed:
Field Communications
Network
Master
Display
ICENI/AI-04
Channel
Status
LED Measured
Value Status
Value
measured value on measured 0
Pub_3645 Page 20 of 25
Table of contents
Popular Control Unit manuals by other brands
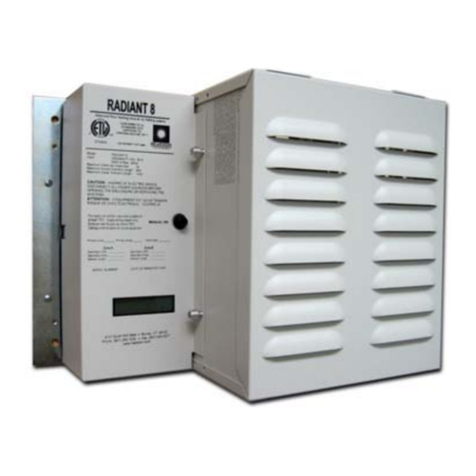
HEATIZON SYSTEMS
HEATIZON SYSTEMS CBX6 manual
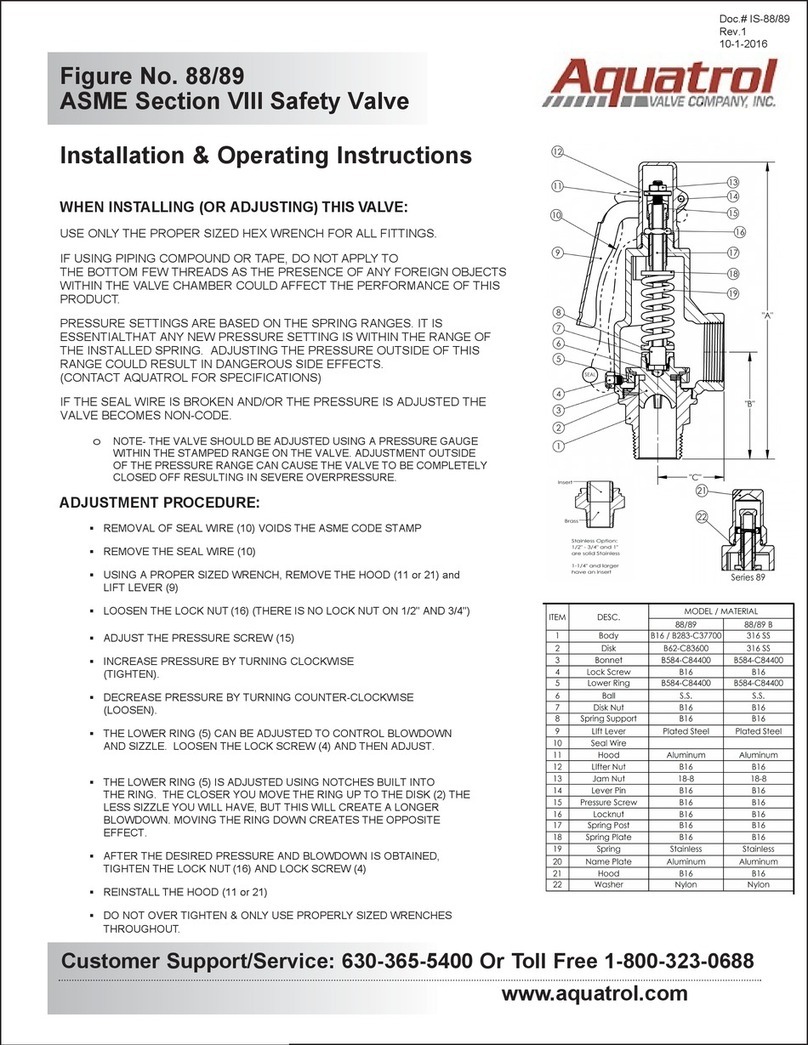
AQUATROL
AQUATROL 88 Installation & operating instructions

Pulse Shower Spas
Pulse Shower Spas 3005-RIVD-BN owner's manual
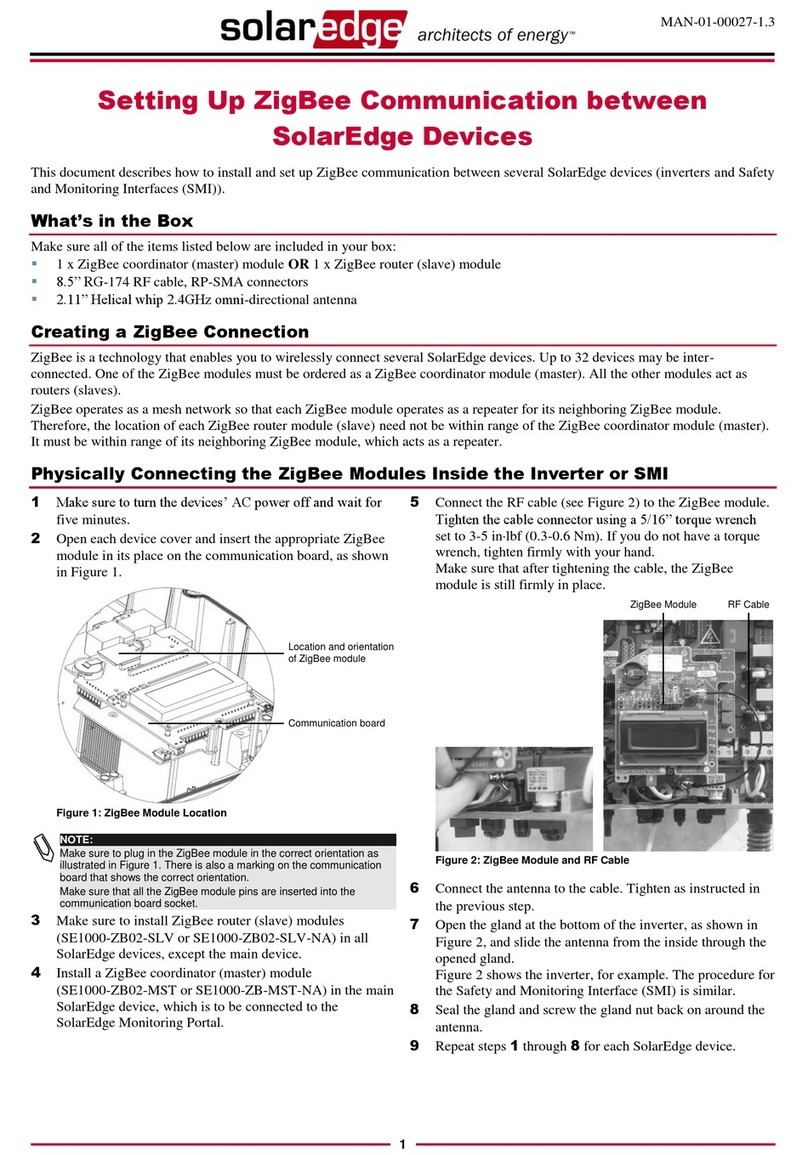
SolarEdge
SolarEdge ZigBee Setting up

RAFTEC
RAFTEC CHROME Series manual
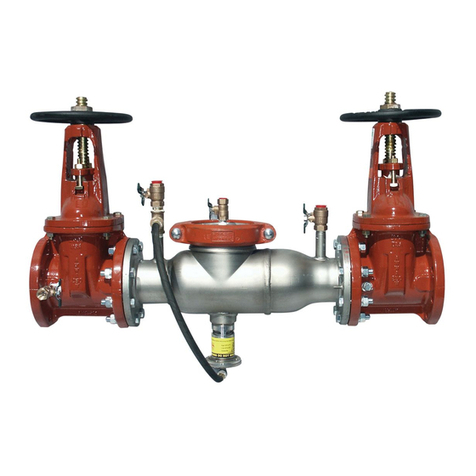
Watts Industries
Watts Industries AMES Silver Bullet 4000SS Series installation instructions