Rego A8890S-50 Series User manual

A8890S-50 Series Rebuild Kit
for A8890S and A8890W Series
Railcar Pressure Relief Valves
WARNING: Installation, dis-
assembly, repair and main-
tenance MUST be performed
only by qualied personnel. All
gas MUST be evacuated from the system before starting repairs.
Installation, usage and maintenance of this product must be in
compliance with all RegO®instructions as well as requirements
and provisions of NFPA #54, NFPA #58, DOT, ANSI, all applicable
federal, state, provincial and local standards, codes, regulations
and laws.
Inspection and maintenance on a periodic basis is essential.
Be sure all instructions are read and understood before installation,
operation and maintenance. These instructions must be passed
along to the end user of the product.
RegO Rail Tank Car equipment is AAR approved. If repaired, the
continued validity of the AAR approval is contingent upon proper
inspection to determine what needs to be repaired; proper repair
using RegO OEM parts and procedures, proper testing for leakage
and performance following repairs and installation.
ECI EXPRESSLY DISCLAIMS ANY AND ALL LIABILITY – UNDER
ANY THEORY, WHETHER CONTRACT, WARRANTY, TORT OR
OTHERWISE – RELATING IN ANY MANNER TO ANY RAIL TANK
CAR EQUIPMENT REPAIRED USING ANY PRODUCTS NOT MANU-
FACTURED BY ECI.
USE OFANY PRODUCTS NOT MANUFACTURED BY ECI TO REPAIR
ANY RAILTANK CAR EQUIPMENT WILL INVALIDATEANYANDALL
WARRANTIES OF THE RAIL TANK CAR EQUIPMENT, WHETHER
EXPRESS OR IMPLIED.
CAUTION: Contact or inhalation of liquid propane, ammonia and
their vapors can cause serious injury or death! NH3and LP-Gas
must be released outdoors in air currents that will insure disper-
sion to prevent exposure to people and livestock. LP-Gas must be
kept far enough from any open ame or other source of ignition to
prevent re or explosion! LP-Gas is heavier than air and may not
disperse or evaporate rapidly if released in still air.
10
REGO
YEAR
WARRANTY

Disassembly and Rebuild Procedure
CAUTION: READ THROUGH ALL OF THESE INSTRUCTIONS,
INCLUDING THE NOTICEAND WARNINGS ON THE BACK OF THIS
SHEET, BEFORE BEGINNING ANY DISASSEMBLY OR REPAIR.
NOTE: Repairs must be performed in a clean area. Hands, clothing,
tools and work area must be completely free of oil, grease and foreign
matter to prevent contamination of component parts and valves. Take
care to prevent damage to the epoxy coating on the springs.
Normal Service
Evacuate LP-Gas from tank prior to disassembling.
Disassembly - See Figure 1 & 2
1. Remove valve from railcar and place on a stable work surface.
2. Remove and discard cable and tie assembly from the 5/16”
hex head cap screw.
3. Remove and retain the two 5/16” hex head cap screws and
stem guide.
4. Using a 1-1/8” wrench and turning counterclockwise, remove
and retain the 3/4” hex nut and washer that secures the upper
poppet to the stem assembly.
5. Remove the upper poppet and retain.
6. Remove and discard the stem and poppet o-rings.
7. Clean threads below 1” jam nut with wire brush.
8. Using a 1-1/2” wrench and turning counterclockwise, remove
and retain the 1” hex jam nut from the valve stem.
9. Place valve in a press. Compress against spring retainer to
compress springs.
10. Remove and discard cable and tie assembly from the 1” hex
adjusting nut and slowly back o.
11. Slowly remove pressure from spring retainer and springs and
remove from press.
12. Remove springs and spring retainer, retain.
CAUTION: Handle springs with care to prevent damage to epoxy
coating.
13. Slowly remove lower poppet and stem assembly from body.
14. Remove the 5/16” cap screws from the seat clamp ring. (For
A8890W series valves only).
15. Remove the seat clamp ring and seat. (For A8890W series
valves only).
Inspection
Note: Inspect all retained parts for signs of wear and
deterioration. Pay special attention to the surface nish of the
valve seat** and stem** as well as the condition of the springs**,
stem guide** and bushing**. Replace parts as necessary.
1. Check stem straightness. Total indicated runout between lower
poppet and 1” threads to be no greater than 0.125”. Replace
if non-conforming.
2. Inspect weld at stem and lower poppet. Using dye penetrant
testing, verify the integrity of the weld. If any cracks are
observed, replace.
3. For A8890W series valves, inspect seat weld. Using dye
penetrant testing, verify the integrity of the weld. If any cracks
are observed, replace.
4. Inspect the following for signs of pitting, nicks and/or corrosion:
a. Seat face.
b. Upper and lower poppet O-ring grooves.
Damage in these areas can cause improper sealing of the
valve. During testing, if set pressure cannot be obtained,
replace ALL damaged components listed above.
5. Inspect the springs for signs of corrosion or damage to the
epoxy coating, If detected, the springs must be replaced.
6. Inspect the bore of the stem guide and bushing. If the inner
diameter of the stem guide is greater than .688”, replace. If the
inner diameter of the bushing is greater than 1.018”, replace.
Reassembly-See Figures 1 & 2.
Note: Where lubrication is noted use Parker Super-O-Lube® or
compatible silicon based grease.
1. (For A8890W Series valves only)
Apply lubricant liberally to underside of seat clamp ring. Apply
a thin strip of Loctite 242®thread locking compound to threads
Rain Cap and Cable
& Tie Assembly*
(Not Shown)
Figure 1 - A8890S Series Valve
* These items form the A8890S-50 Series Kits, recommended for rebuilds.
** Must be ordered separately from RegO®.
Spring
Retainer
Spring
1” Adjusting Nut
1” Jam Nut
Cable & Tie
Assembly*
Mark here for
reassembly &
testing
5/16” Hex
Head Cap
Screw (2)
Stem Guide
Stem
Tightening Squence
Bushing
Upper Poppet
Spring Height

of the 5/16” cap screws. Install seat clamp and secure with the
5/16” cap screws, turning clockwise, torque 150-160 in-lbs.
2. Coat the o-ring seat area on stem with lubricant (do not get
on threads) and install stem o-ring onto stem.
3. Apply lubricant to outside of stem o-ring.
4. Stretch poppet o-ring to ensure snug t inside upper poppet.
5. Apply a liberal amount of lubricant to the poppet o-ring and
install in the upper poppet.
6. Install upper poppet with o-ring onto stem assembly. Apply
Loctite 242®thread locking compound to stem threads and
secure upper poppet to lower poppet with 3/4” hex nut and
washer. Torque to 50-60 ft-lbs.
7. Paying special attention not to contact the seat, slowly reinstall
the stem assembly through the bushing until the poppet o-ring
contacts the seat.
8. Apply non-detergent grease to stem threads.
9. Reinstall the springs and spring retainer. Align spring ends
so they start 180° apart.
10. Install the valve in a press (recommended), compress spring
retainer to compress the springs to a height of 9.63”. See
gure 1.
11. Using ONLY the 1” adjusting nut, engage until nut contacts
spring retainer.
DO NOT INSTALL 1” HEX JAM NUT UNTIL AFTER TESTING
IS COMPLETE.
12. Reinstall spring guide using two 5/16” hex head cap screws.
Torque to 150-160 in-lbs.
13. Tighten the bolt studs & nuts gradually in an alternate and
opposite sequence around the ange. Follow the sequence
shown in Figure 1 Tightening Sequence.
Testing
NOTE: Valve should be tested no sooner than 24 hours after as-
sembly to allow for proper seat compression.
1. Attach valve to test xture.
Figure 2 - Poppet & Stem Assembly
2. Fill spring guide with water and observe pressure gauge as
pressure is raised. After pressure is raised to within 25 psi
of the set pressure marked on the valve, begin to increase
pressure at a rate no greater than 2 psi per second, until the
rst bubbles through the water seal are observed. If bubbles
do not appear at proper start-to-discharge pressure, tighten or
loosen the adjusting nut until bubbles indicate proper setting.
3. After correct start-to-discharge pressure is reached, shut o
inlet pressure, observe and note at what pressure valve seals
o. Valve must reseal by 80% of start-to-discharge setting.
4. Exhaust air pressure and remove valve from xture.
5. Now that the valve is set, measure the spring height.
• For valves with set pressures of 225, 247.5 & 280.5 psi:
the spring height must not be less than 7 3/8”.
• For valves with a set pressure of 300 psi:
the spring height must not be less than 8 3/4”.
NOTE: If the spring height is less than these, the valve must be
disassembled and both springs must be replaced.
6. Install and tighten 1” hex jam nut, being careful not to turn the
adjusting nut.
7. Install a new cable and tie assembly onto one of the 5/16” hex
head cap screw and around the adjacent arm on the stem
guide. Install new cable and tie assembly onto the 1” adjust-
ing nut, looping the free end of cable through the hole in the
spring retainer, around coil of inner spring, back through hole
in spring retainer, and then back through the tie. Proper cable
and ties assembly installation is shown in gure 1.
Emergency Field Repair
NOTE: “Emergency Field Repair” is considered repair and/or re-
placement of any resilient components while the valve is installed
on a pressurized tank car. This procedure should be performed
only when ABSOLUTELY NECESSARY and when evacuating
the tank car is impractical. Take caution during this repair and
avoid open ames, as it is possible that some product vapor will
escape. The venting of SOME product during the repair procedure
is normal.
Seat Clamp Ring
Lower
Poppet
Upper Poppet
Poppet O-Ring*
Stem O-Ring*
Stem
Body
3/4” Hex Nut
Washer
5/16” Button Head
Cap Screw (2)
Upper Poppet
Poppet O-Ring*
Stem O-Ring*
Stem
Body
3/4” Hex Nut
Washer
A8890W Series A8890S Series
Seat
Seat Weld
Lower
Poppet

Inspect all retained parts for signs of wear and deterioration. Re-
place parts as necessary.
1. Remove and discard cable and tie assembly from the 5/16”
hex head cap screw.
2. Remove and retain the two 5/16” hex head cap screws and
stem guide.
3. Using a 1-1/8” wrench and turning counterclockwise, SLOWLY
remove the 3/4” hex nut and washer that secures the upper
poppet. Remove upper poppet.
NOTE: Before completely removing the nut & washer, note the
amount of product vapor escaping (if any) from the seat. If the
amount is excessive or progressively getting worse, retighten the
nut and perform a normal service after the tank is evacuated.
4. Remove & discard the stem o-ring and poppet o-ring.
5. Coat the o-ring seat area on stem with lubricant (do not get
on threads) and install stem o-ring onto stem.
6. Apply lubricant to outside of stem o-ring.
7. Stretch poppet o-ring to ensure snug t inside upper poppet.
Apply a liberal amount of lubricant to the poppet o-ring and
install in the upper poppet.
8. Install upper poppet and o-ring onto stem and lower poppet
assembly and secure with the 3/4” hex nut and washer. Torque
to 50-60 ft-lbs.
9. Reinstall spring guide with two 5/16” hex head cap screws.
Torque to 150-160 in-lbs.
10. Install new cable and tie assembly onto 5/16” hex head cap
screw and around the adjacent arm on the stem guide. See
gure 1.
Printed in the USA REV D 04-1219-0613
Instruction Sheet A8890S-301
Other Rego Control Unit manuals
Popular Control Unit manuals by other brands
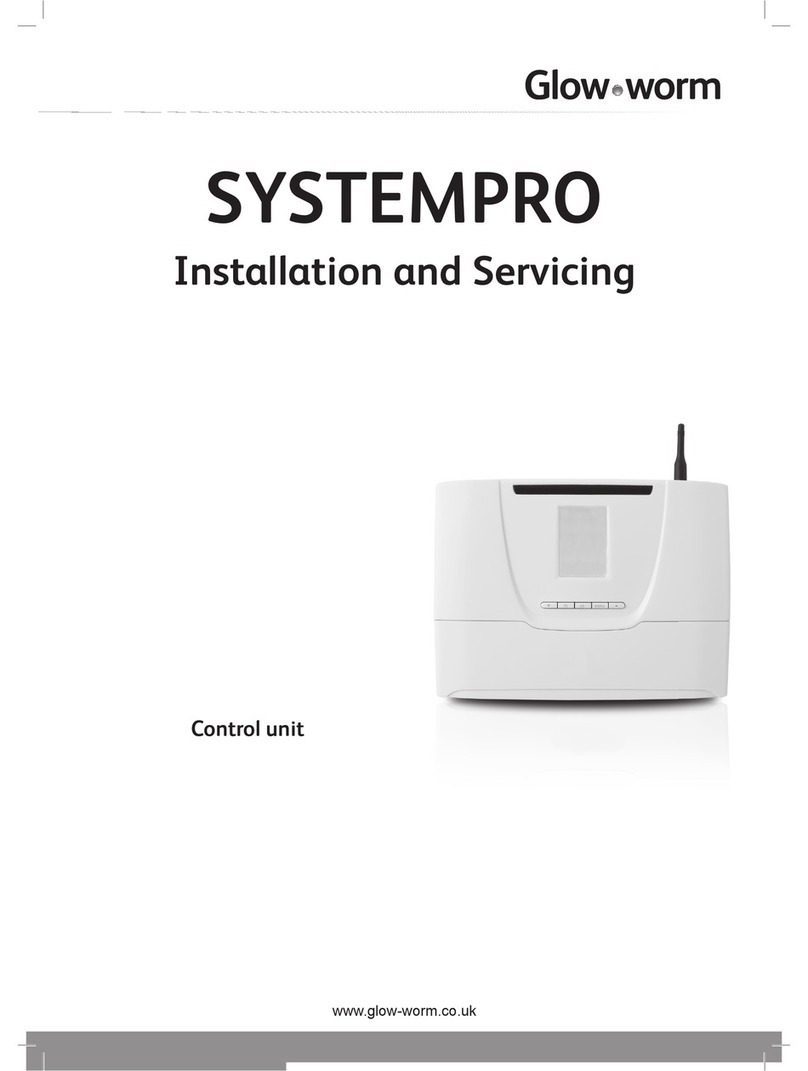
Glowworm
Glowworm SYSTEMPRO Installation and servicing

GEM
GEM ZRSK operating instructions
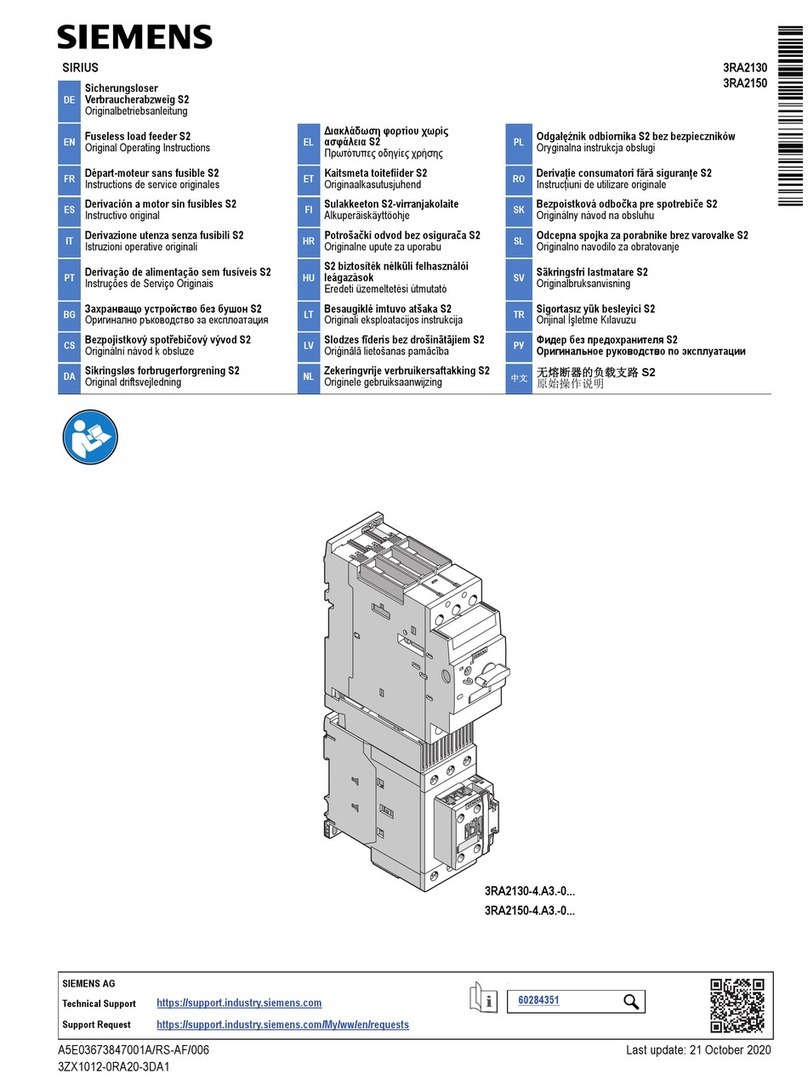
Siemens
Siemens SIRIUS 3RA2130-4 A3 Series Original operating instructions
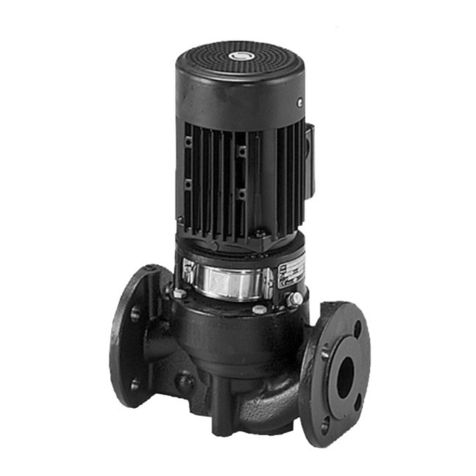
Grundfos
Grundfos TP Installation and operating instructions

Quectel
Quectel RG50-Q Series user guide

Victaulic
Victaulic I-769N Installation, Maintenance, and Testing Manual