Resol FlowCon B User manual

FlowConB
www.resol.de
Manual
B
RESOL FlowConB
Mounting
Installation
Operation
Commissioning
Thank you for buying this RESOL product. Please read this manual carefully, to get the best
performance from this unit.
48001070
*48001070*

FlowConB
© RESOL 08239 Flowcon_B.monen.indd
|2
Subject to technical changes. Errors excepted.
Safety advice
Please pay attention to the following safety advice in order
to avoid danger and damage to people and property.
This product is to be used in accordance with its intended
use only (see page 3).
Please pay attention to the valid local regulations!
Instructions
Attention should be paid to
- the statutory provisions for prevention of industrial acci-
dents,
- the statutory provisions for environmental protection,
- the Health and Safety at Work Act 1974
- Part P of the Building Regulations 2005
- BS7671 Requirements for electrical installations and rele-
vant safety regulations of DIN, EN, DVGW,TRGI,TRF and
VDE.
These instructions are exclusively addressed to authorised
skilled personnel.
- Only qualified electricians should carry out electrical
works.
- Initial installation must be effected by qualified personnel
named by the manufacturer
Declaration of conformity
We, RESOL Elektronische Regelungen GmbH, D-45527
Hattingen, declare under our sole responsibility that our
product FlowConB complies with the following standards:
EN 55 014-1
EN 60 730-1
According to the regulations of the above directives, the
product is labelled with :
89/336/EWG
73/ 23/EWG
Hattingen, 18.06.2007
RESOL Elektronische Regelungen GmbH,
ppa. Gerald Neuse
Contents:
Safety advice...................................................................... 2
Technical data and operation........................................... 3
1. Installation.............................................................. 4
1.1 Wall mounting ....................................................... 4
1.2 Optional compression ring connection............... 5
1.3 Mounting the expansion vessel (optional) .......... 5
1.4 Electrical connection............................................. 6
1.5 Integration of the controller
DeltaSol
®BS /BS Plus....................................... 6
2. Commissioning ...................................................... 7
2.1 Filling and flushing the system ............................. 7
2.2 Emptying the system............................................. 7
2.3 Non-return valves.................................................. 8
2.4 Safety assembly...................................................... 8
2.5 Air-Stopp ................................................................ 9
3. Accessory ............................................................... 9
Imprint ............................................................................. 12

FlowConB
© RESOL 08239 Flowcon_B.monen.indd
3 |
315
520
•Prepared for integration of the
DeltaSol
®BS /BS Plus controller
•Dial thermometer for flow and return
•Outstanding design
•Return line with ball valve and openable non-
return valve
•Integrated flowmeter
•Safety assembly with relief valve and pressure
gauge
•Fill/drain valve for filling and flushing the system
•Wall mounting bracket with screws and dowels
•Insulated casing
Technical data
Height (with insulation): 520 mm
Width (with insulation): 315 mm
Distance axis / wall: 63 mm
Pipe connections: ¾“ IT, with
cutting ring connections (optional)
Connection for expansion vessel: ET pipe 3/4“, flat sealing
Outlet safety valve: ET pipe 3/4“
Max. admissible pressure: 8 bar
Max. admissible temperature: 120°C continuous and 160°C intermittent
Safety valve: 1/2“ x 3/4“ - 3 bar, 6 bar, 10 bar
Pressure gauge: 0 - 6 bar, up to 130°C
Non-return valve: 2 x 200 mm water column, openable
in flow and return ball valve,
PPS - max. 180 °C
Dial thermometer: 0 – 120 °C,
Flowmeter (depending on the version): 0,5-5 l/min, 1-13 l/min, 8-30 l/min
Flat sealings: Klingerit - max. 200 °C
O-Ring sealings: VITON / EPDM - max. 180°C
Insulation: EPP, l= 0,041 W/(m*K)
max. 120 °C continuous and 180 °C intermittent

FlowConB
© RESOL 08239 Flowcon_B.monen.indd
|4
16
1
2
8
14
10
9
13
7
315
4
6
11
5
1. Installation
12
1.1Wall mounting
1. Determine where to mount the pump station;consider
the space for the (optional) expansion vessel!
2. Take the complete station out of the packing.
3. Remove the front half of the insulation by pulling it.The
thermometers loosen from the ball valves.
Do not unsrew the pump station from the back
part of the insulation!
4. Mark the fastening holes (centres 70 mm) and drill holes
(diameter 8 mm); insert the enclosed dowels (S 8).
5. Fasten the complete pump station with the wall
mounting bracket to the wall (depending on the pump
version, upper or lower holes in the insulated casing)
and tighten the screws.For this purpose,use a positive
cross-recessed screwdriver!
6. Connect the connection line between the pump
station and the store and the collectors repectively.
Optionally, compression ring connections can be used
for mounting copper pipes. In order to connect the
pipes with the compression ring connections,
pay attention to the following instructions!
1 Wall mounting bracket of the pump station
2 Insulation - rear
3 Controller
4 Insulation - front cover
5 Flowmeter
6 Drain valve
7 pump
8 ball valve in flow IT-IT, with integrated thermometer
9 ball valve in return IT-IT, with integrated thermometer
10 Safety head-piece, with fill valve
11 Pressure gauge
12 Safety valve 6 bar
13 Optional: expansion vessel set
14 Optional: AirStopp
15 Optional: Compression ring connection for
copper pipe

FlowConB
© RESOL 08239 Flowcon_B.monen.indd
5 |
All connections are pre-assembled by the manufacturer but
have to be tightened by the installer. Check for leaks when
commissioning the station (pressure test).
Screws S6 x 60
- First push the union nut (2),then the brass compression
ring (3) onto the copper pipe (1). In order to ensure
secure load transmission and sealing, the pipe must
extend at leat 3 mm out of the compression ring.
- Insert the support sleeve (4) into the copper pipe (1).
- Push the copper pipe (1) with the attached parts
(2; 3; 4) as far as possible into the body of the
compression ring connection (2).
- First screw on the union nut by hand.Then tighten it
by at least one full rotation with a suitable open-ended
spanner.
Please note: In order to absorb the strain of the pipes, corresponding fittings (strain neutralizers) or expansion bends
(consisting of at least two 90° - bends) are required. For expansion bends, the distance between the bends must be
larger than twice the pipe diameter in cm.
[Example: pipe diameter = 18 mm Þ distance between the bends more than 36 cm].
1.2Optional compression ring connection
1.3Mounting the expansion vessel (optional)
-Attach the wall mounting bracket of the expansion
vessel in a suitable position to the wall. Pay attention
to the corrugated stainless steel hose (optional
accessory).
- Connect the optional hose flatly sealing using the
enclosed sealings (optional) to the quick connector
(optional) of the expansion vessel and to the expansion
vessel connection at the safety head piece of the pump
station.
5
3
2
1
> 3 mm
4

FlowConB
© RESOL 08239 Flowcon_B.monen.indd
|6
1.5Integrating the DeltaSol
®B /BS controller
1.4 Electrical connection
The unit must only be located in dry interior locations. It
is not suitable for installation in hazardous locations and
should not be placed close to any electromagnetic fields.The
controller must additionally be supplied from a double pole
switch with contact gap of at least 3 mm. Please pay atten-
tion to separate routing of sensor cables and mains cables.
Push the cover in front of the controller downwards in order
to access the controller.Open the housing of the controller at
the front.Follow the steps described in the controller manual.
- Pull the cover at the front of the insulated casing down-
wards and remove it.
- Put the controller into the provided space in the insula-
tion and attacht it with the fastening screws 3 x 30 and
large washers.
- Electrical connections (plug, sensor and relay connections)
must be carried out according to the steps described in
the manual.
- The cables - especially those of the pump - must be long
enough so that the front part of the insulation can be
removed without damaging the controller. Please ensure
that the cables do not come into contact with hot water
pipes!
- Attach the front part of the insulation to the pump station.
Do not yet insert the thermometers (red in flow, on the
left / blue in return, on the right), because the insulation
has to be opened once again for commissioning.
For further information on the connection of the con-
troller, see DeltaSol
®BS / BS Plus manual.
Front insluation
front view
Front insluation
rear view

FlowConB
© RESOL 08239 Flowcon_B.monen.indd
7 |
2.1Filling, flushing and commissioning the pump station
2. Commissioning
· Connect the pressure hose to the fill valve at the safety
head-piece below the pressure gauge (11) and open the
fill and drain valve.
· Connect the flushing hose to the fill and drain valve at
the flowmeter and open the fill and drain valve.
· The slot of the adjustment screw at the flowmeter has
to be in a horizontal position.Thus the integrated ball
valve is closed (see flowmeter manual). Open the non-
return valve above the pump;for this purpose turn the
ball valve by means of an open-ended spanner (wrench
size 14) to a 45° position (half opened, half closed).
· Fill sufficient solar fluid into the tank of a flushing and
filling station (not supplied) and fill the solar thermal
system.
· Flush the solar thermal system using the flushing and
filling station for at least 15 minutes.To remove all air
from the system, open the adjustment screw at the
flowmeter several times.
· The system may be flushed with water before
commissioning but the final installation must con-
tain antifreeze to protect against frost damage.
· Close the drain valve while the pump is running and
increase the system pressure to approx. 6 bar. The
system pressure is indicated at the pressure gauge.
· Close the fill valve and switch-off the pump of the
flushing and filling station; open the adjustment screw
at the flowmeter (vertical position).
· Bleed the system above the collector until the dis-
charged fluid is free of bubbles. Increase the pressure
to approx. 6 bar and check the system for leaks. In the
case of a significant decrease in pressure, there may be
leakage in the system
Adjust the system to the manufacturer‘s recommended
pressure (to approx. 1,8 to 2,3bar with a collector
height of approx. 5 to 10 m).
· Put the circulation pump into operation at maximum
speed (see pump manual) and let it circulate for at least
15 minutes.
· Afterwards, adjust the desired pump speed.
· Adjust the flow rate at the flowmeter according to the
specifications of the collector manufacturer.
· Remove the hoses of the flushing and filling station
and screw the caps onto the valves of the flushing and
filling valves.
· Check the system for leaks. Open both ball valves
· Die vordere Isolierschale der Solarstation anbringen,
die Thermometer einstecken.
2.2Emptying the system
· Open the non-return valve in the ball valve (see
following advice).
· Open the air vent at the highest point of the system
(above the collector).
· Open the fill and drain valve at the lowest point of the
system, if possible close to the store connection (not
supplied) or at the drain valve and the pump.

FlowConB
© RESOL 08239 Flowcon_B.monen.indd
|8
2.3 Non-return valves
- The non-return valves of the pump station are
integrated into the ball valves above the circulation
pump and into the flow and have an opening pressure
of 200 mm head each.
- In order to empty the system completely, the
nonreturn valve has to be opened. For this purpose,
the knob of the ball valve has to be put in a 45°
position. The ball in the ball valve then opens the
non-return valve.
- For normal system operation, the ball valve has to
be completely opened.
2.4 Safety assembly
- The pump station is equipped with a diaphragm safety
valve which corresponds to the relavant directives and
regulations. For installation and operation, please pay
attention to the following advice:
- The safety valve has to be easily accessible.The efficien-
cy of the valve must not be influenced or disabled by
barriers!
- The strainer or other restriction devices must not be
mounted between collector (-field) and safety valve!
- The diameter of the discharge pipe must correspond to
the diameter of the valve outlet; the maximum length
must not exceed 2 m;more than 2 bends are inadmiss-
able. When these values are exceeded (2 bends, 2 m
pipe length), you have to install a discharge pipe with
larger dimensions. Do not use more than 3 bends and
pipes longer than 4 m!
- If the discharge pipe leads into a drain pipe with a hop-
per, the diameter of the drain pipe has to be at least
twice as large as the valve inlet. The opening of the
discharge pipe should be inclined downwards. It should
be routed so that the opening can be seen but does
not present any risk to a person standing or passing
by
- It is useful to place a container under the discharge pipe.If
the safety valve opens,the fluid will be collected and can be
refilled in to the system when the pressure is too low.

FlowConB
© RESOL 08239 Flowcon_B.monen.indd
9 |
2.5AirStopp, manual bleed valve (optional)
Mounting
The AirStopp is for bleeding the solar fluid in the solar ther-
mal system.The air precipitated from the solar fluid gathers in
the upper area of the manual bleed valve and can, if required,
be discharged at the bleeding valve.
In order to make sure that the AirStopp operates fault-
lessly, it is to be mounted vertically and with the bleed valve
upwards!
Operation
The air precipitated from the solar fluid gathers in the up-
per area of the manual bleed valve (see figure).At first you
should bleed the solar thermal system daily and then weekly
or monthly, depending on the volume of discharged air. Bleed
the solar thermal system half-yearly with the manual bleed
valve to achieve optimal efficiency.
Plese note: Check the system pressure after bleeding and if necessary increase it to the specified operating pressure!
3.Accessory
Overvoltage protection
In order to avoid overvoltage damage at collector sensors
(e.g. caused by local lightning storms), we recommend in-
stalling the overvoltage protection RESOL SP1 .
Sensors
Our product range includes high temperature sensors, flat-
screw sensors, outdoor temperature sensors, indoor tem-
perature sensors, cylindrical clip-on sensors and irradiation
sensors, also as complete sensors with immersion sleeves.
Flowmeter
If you wish to carry out a heat quantity measurement,
you need a flowmeter for measuring the flow rate in your
system.

FlowConB
© RESOL 08239 Flowcon_B.monen.indd
|10
Notes

FlowConB
© RESOL 08239 Flowcon_B.monen.indd
11 |
Notes

FlowConB
© RESOL 08239 Flowcon_B.monen.indd
|12
Distributed by:
RESOL - Elektronische Regelungen GmbH
Heiskampstraße 10
45527 Hattingen / Germany
Tel.: +49 (0) 23 24 / 96 48 - 0
Fax: +49 (0) 23 24 / 96 48 - 755
www.resol.de
info@resol.de
Important notice
We took a lot of care with the text and drawings of this
manualand to the best of our knowledge and consent. As
faults can never be excluded, please note:
Your own calculations and plans,under consideration of the
current standards and directives should only be basis for your
projects.We do not offer a guarantee for the completeness
of the drawings and texts of this manual - they only represent
some examples They can only be used at your own risk.
No liability is assumed for incorrect, incomplete or false
information and / or the resulting damages.
Please note
The design and the specifications are to be changed without
prior notice
The illustrations may differ from the original product.
Imprint
This mounting- and operation manual including all parts is
copyrighted.Another use outside the copyright requires the
approval of RESOL - Elektronische Regelungen GmbH.This
especially applies for copies, translations,micro films and the
storage into electronic systems.
Editor: RESOL - Elektronische Regelungen GmbH
Table of contents
Other Resol Measuring Instrument manuals
Popular Measuring Instrument manuals by other brands

Würth
Würth FLL13 Translation of the original operating instructions
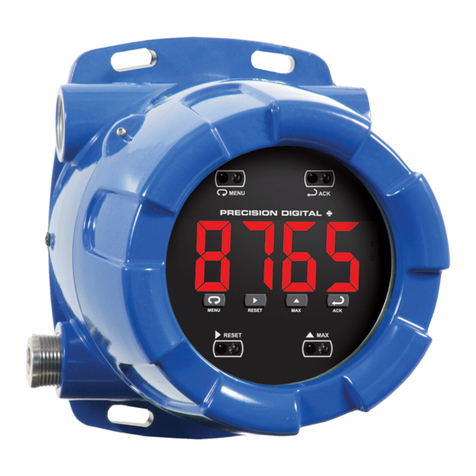
Precision Digital Corporation
Precision Digital Corporation ProtEx Max Series instruction manual
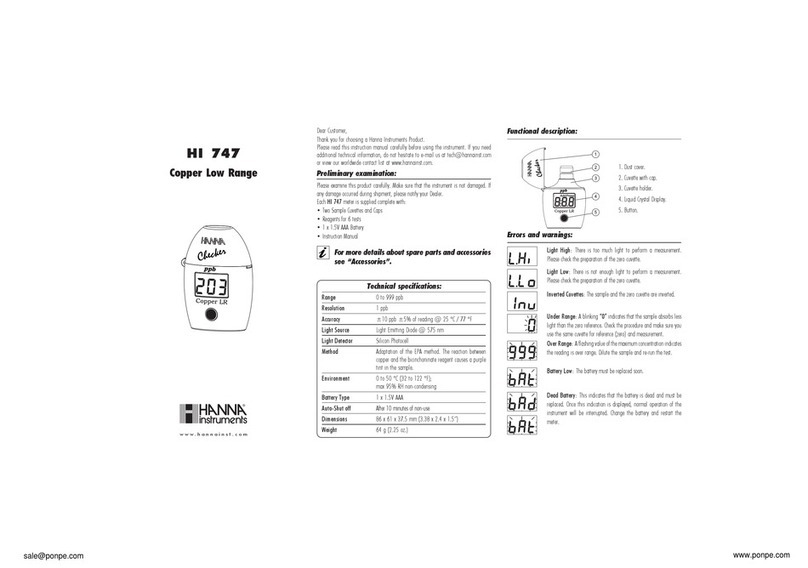
Hanna Instruments
Hanna Instruments HI 747 manual
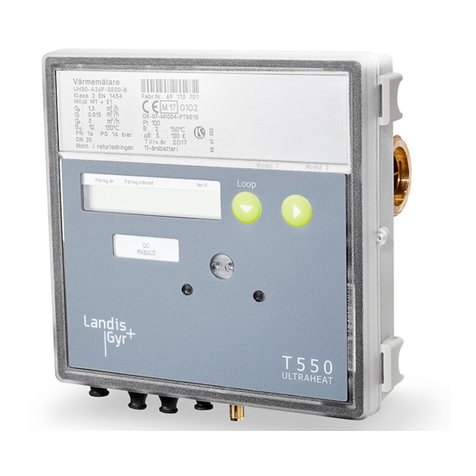
Landis+Gyr
Landis+Gyr UH50 Series installation instructions

Endress+Hauser
Endress+Hauser Proline Promass O 300 technical information

Westover
Westover RHB-18 Operation manual

ATAGO
ATAGO DR-M2 instruction manual

International Biomedical
International Biomedical AeroNOx 2.0 Operator's manual

PeakTech
PeakTech 4135 Operation manual
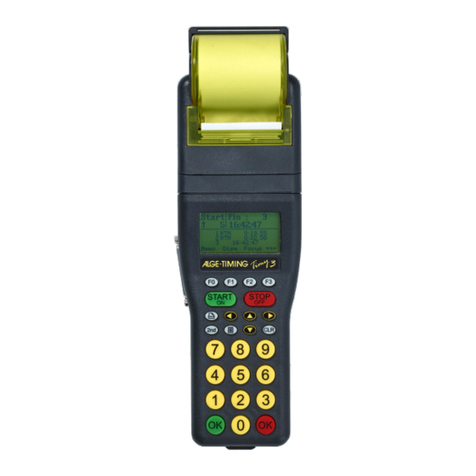
ALGE-Timing
ALGE-Timing Timy SPEED manual
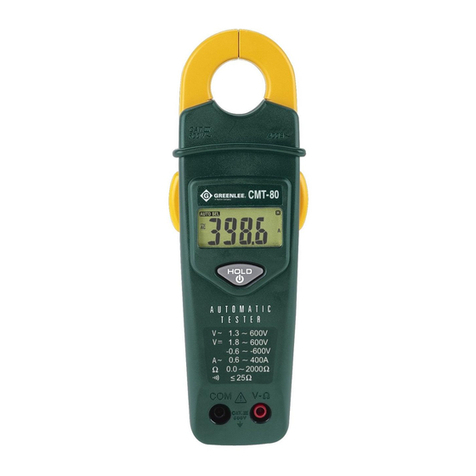
Greenlee
Greenlee CMT-80 instruction manual
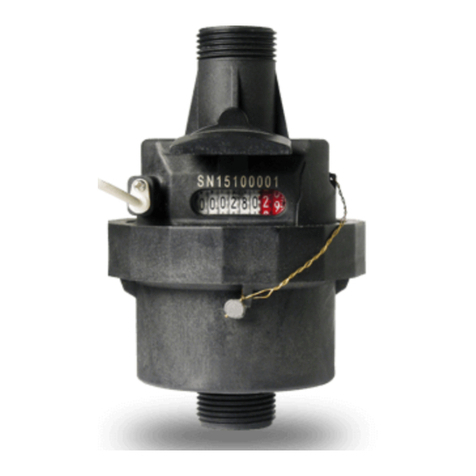
Assured Automation
Assured Automation WM-PD Series Use & care manual