REXROTH RD 500 RD42 User manual

R911200190
Edition 03
Rexroth RD 500 RD42
Power Supply
Operating Guide
Industrial
Hydraulics
Electric Drives
and Controls
Linear Motion and
Assembly Technologies Pneumatics
Service
Automation
Mobile
Hydraulics

About this Documentation RD 500 RD42
DOK-RD500*-RD42*******-IB03-EN-P
RD 500 RD42
Power Supply
Operating Guide
DOK-RD500*-RD42*******-IB03-EN-P
120-1950-B314-03/EN
This documentation describes the power supply of the produkt family
RD 500 RD42
•for planning the mechanical control cabinet construction.
•for planning the electrical control cabinet construction.
•for start-up.
•for fault messages and notes to couse and remedy.
Description Release
Date
Notes
DOK-RD500*-RD42*******-IB01-EN-P 12.2000 First edition
DOK-RD500*-RD42*******-IB02-EN-P 01.2003 Warning added
DOK-RD500*-RD42*******-IB03-EN-P 11.2003 Error correction
¤
2003 Indramat Refu GmbH
Copying this document, giving it to others and the use or communication
of the contents thereof without express authority, are forbidden. Offenders
are liable for the payment of damages. All rights are reserved in the event
of the grant of a patent or the registration of a utility model or design
(DIN 34-1).
The specified data is for product description purposes only and may not
be deemed to be guaranteed unless expressly confirmed in the contract.
All rights are reserved with respect to the content of this documentation
and the availability of the product.
Indramat Refu GmbH
Uracher Strasse 91•D-72555 Metzingen
Telephone +49 (0)71 23/9 69-0 •Fax +49 (0)71 23/9 69-2 60
http://www.boschrexroth.de/
Dept. Development ENG (jr)
This document has been printed on chlorine-free bleached paper.
Title
Type of Documentation
Document Typecode
Internal File Reference
Purpose of Documentation
Record of Revisions
Copyright
Validity
Published by
Note

RD 500 RD42 I
DOK-RD500*-RD42*******-IB03-EN-P
Table of content
1 Description 1-1
1.1 General information....................................................................................................................... 1-1
Operating mode, standby:........................................................................................................ 1-1
Operating mode, run: ............................................................................................................... 1-1
1.2 Dimensioning information ............................................................................................................. 1-1
Dimensioning the power sections ............................................................................................ 1-1
Dimensioning for dynamic regenerative feedback operations................................................. 1-2
1.3 Technical data............................................................................................................................... 1-2
1.4 Block circuit diagram ..................................................................................................................... 1-3
1.5 Type code ..................................................................................................................................... 1-4
2 Mechanical mounting and installation 2-1
2.1 Storage and mounting location ..................................................................................................... 2-1
Storage..................................................................................................................................... 2-1
Minimum requirements at the mounting location..................................................................... 2-1
Installation altitudes above 1000 meters sea level: ................................................................. 2-2
2.2 Mounting the supply modules ....................................................................................................... 2-2
2.3 Dimension drawings...................................................................................................................... 2-3
3 Electrical installation 3-1
3.1 EMC-correct design of drives........................................................................................................ 3-1
3.2 Warnings and information ............................................................................................................. 3-3
3.3 Cable cross-sections..................................................................................................................... 3-4
Alternative fuse types............................................................................................................... 3-4
3.4 Power terminals RD42 .................................................................................................................. 3-5
3.5 Line filter connection ..................................................................................................................... 3-5
3.6 Supply module connection............................................................................................................ 3-6
Power terminal X1.................................................................................................................... 3-6
Power terminal X2.................................................................................................................... 3-6
Power terminal X3.................................................................................................................... 3-6
3.7 Control terminals ........................................................................................................................... 3-7
Terminal diagram ..................................................................................................................... 3-7
Control terminal strip X11 on SN11027 ................................................................................... 3-9
Control terminal strip X52 on NR16236................................................................................. 3-10
3.8 Serial interface ............................................................................................................................ 3-10
Data transfer protocol ............................................................................................................3-10
Connector assignment X16.................................................................................................... 3-11

II Table of content RD 500 RD42
DOK-RD500*-RD42*******-IB03-EN-P
4 Commissioning 4-1
4.1 Connection .................................................................................................................................... 4-1
4.2 Setting the unit configuration ........................................................................................................ 4-1
Setting the display language.................................................................................................... 4-1
Setting the interface address ................................................................................................... 4-1
Powering-up / down the supply module................................................................................... 4-1
4.3 Powering-up .................................................................................................................................. 4-3
4.4 Changing-over the operating mode .............................................................................................. 4-3
4.5 Ready signal ................................................................................................................................. 4-4
4.6 Operating display .......................................................................................................................... 4-4
5 Fault display and fault diagnostics 5-1
5.1 General information....................................................................................................................... 5-1
5.2 Fault signal.................................................................................................................................... 5-1
5.3 Fault acknowledgement ................................................................................................................ 5-1
5.4 Fault display.................................................................................................................................. 5-1
5.5 Fault messages – cause and remedy........................................................................................... 5-2
5.6 Fault display on the regenerative feedback control NR16236...................................................... 5-3
6 Index 6-1
7 Kundenbetreuungsstellen - Sales & Service Facilities 7-1
Indramat Refu .......................................................................................................................... 7-1

RD 500 RD42 Description 1-1
DOK-RD500*-RD42*******-IB03-EN-P
1 Description
1.1 General information
The RD42 supply modules, which are capable of regenerative feedback,
are designed to be connected to inverters with DC connection from the
REFUdrive 500 series. They are suitable for regenerating into the line
supply, for example, when drives are braked.
The three-phase supply is fed-in via a line filter and an uncontrolled three-
phase bridge rectifier. The DC link capacitors are pre-charged via series
resistors and an auxiliary contactor. If faults develop in the power section,
or e.g. if the drive converter is powered-up with a ground fault at the DC
link output, pre-charging is automatically and safely interrupted. When the
system runs-up correctly, the charged capacitors are connected to the
line supply through a diode rectifier using a power contactor, and then the
inverter is enabled.
The supply modules have two operating modes:
Operating mode, standby:
(terminals X52.5 and .6 open-circuit)
The regenerative feedback into the line supply is active. The quiescent
current (if there is no regenerative feedback) is almost zero. The
regenerative power is limited to 50 % of the specified values; refer to the
technical data.
Operating mode, run:
(Terminals X52.5 and .6 closed or there is a significant level of
regenerative feedback)
The regenerative feedback into the line supply is active. The quiescent
current (if there is no regenerative feedback) is approx. 30 % of the rated
current. The regenerative feedback power corresponds to the specified
values, refer to the technical data. The changeover into the run operating
mode can be externally initiated (X52), or is automatically set as a
function of the regenerative feedback power.
1.2 Dimensioning information
Dimensioning the power sections
Two criteria are taken into account when dimensioning the power
sections:
Power consumption
This is the sum of the power drawn from the DC link, taking into account
losses and a coincidence factor. The power which may be drawn from the
DC link is specified under 1.3 Technical data.
Total number of units which can be connected
Capacitors are used in the inverters which are used to smooth the DC link
voltage. When the drive converter is powered-up, these must be charged
using a pre-charging device. If too many inverter modules are connected
to the DC link, then there is a danger that the pre-charging device will be
overloaded.
Every inverter has a power code, which can be taken from the type code
(e.g. RD52.1-7N-022... => power code 22). In order that the pre-charging

1-2 Description RD 500 RD42
DOK-RD500*-RD42*******-IB03-EN-P
device is not overloaded, the sum of the power codes of the connected
inverters may not exceed 200% of the power code of the power supply
module used.
Dimensioning for dynamic regenerative feedback operations
Depending on the dynamic behavior, the following dimensioning should
be considered: For applications, where the DC link power must be
provided within 5 and 15 ms, the peak regenerative feedback power ≤the
rated output of the unit. For applications where the DC link power
increases more slowly (rise time > 30 ms), the unit can be dimensioned
with a peak regenerative power ≤peak power of the unit. Independent of
this, it must be guaranteed, that as an average, the rated output of the
unit is not exceeded.
1.3 Technical data
RD42 power code 026 053 084 105
Line supply 3-ph. 380 V AC ...480 V ±10 %, 50 / 60 Hz
3-ph. 500 V AC ± 10 %, 50 / 60 Hz
Fuse, FF [A] 63 125 200 250
Control voltage supply 3-ph. 380 V AC ... 480 V ± 10 %, 50 / 60 Hz
3-ph. 500 V AC ± 10 %, 50 / 60 Hz
DC link voltage 530 ... 640 V DC ± 10 %
660 V DC ± 10 %
DC side
DC rated current [A] 50 100 160 200
Peak current for 60 s [A] 75 150 240 300
Line supply side
For Vline supply = 400 V
Rated output
Peak output
[kW]
[kW]
26
40
53
80
84
127
105
160
For Vline supply = 480 V
Rated output
Peak output for 60 s
[kW]
[kW]
32
48
64
96
102
154
128
192
For Vline supply = 500 V
Rated output
Peak output for 60 s
[kW]
[kW]
33
50
66
100
105
160
132
200
Line supply rated current
at the rated line supply power
[A] 45 90 150 180
Power factor, line supply Approx. 1
Losses at rated output [kW] 0.8 1.15 1.5 2
Ambient conditions, radio interference suppression level, noise immunity
Cooling airflow requirement m³/s 0.08 0.12 0.2 0.3
Environmental Class 3K3 acc. to DIN IEC 721-3-3 (ambient temperature 0-40 °C)
Radio interference suppression level /
noise immunity
A 1 acc. to EN 55011 / EN 61800-3
Mechanical design
Size Class D E F G
Degree of protection IP 20 acc. to EN 60529
Fig. 1-1: Technical data

RD 500 RD42 Description 1-3
DOK-RD500*-RD42*******-IB03-EN-P
Note: The specified values refer to the “Run”operating mode. In the
“Standby”mode, the regenerative feedback only represents 50
% of the specified values.
1.4 Block circuit diagram
+-
X2
CCD
U1 V1 W1
X1
122121
U1 V1 W1
+
U1 V1 W1
U2 V2 W2
K1K2
33
NF
VL
V
C
PE
D
Checkback signal
line contactor
K1
X3
D
PE
Display
4 V
V
3 x 2A
1
2
X11
3
4
5
6
7
8
9
1
11
12
13
14
15
X16
RS485 / 232
WS
PE
X1 D
C
X2 V2 PEW2 PEPE
M 3~
J
U2
PTC / KTY85+
PTC / KTY85-
SR17000
-
U1' V1' W1'
1
2
3
4
5
6
7
8
46 V
5 V
SV
3 V
23 V
X3
K2
X3
X3
X16
T1
K1
X16
SN
NR
X52
X1 D
X2 V2 PEW2 PE
M 3~
J
U2
PTC / KTY85+
PTC / KTY85-
SR17002
Spee encoder
K1
K1 K1
G
C
Output +24V
ON
Acknowledge
External fault
Output +24V
GND
GND
Enable slave
Enable inverter
3 phase power supply
DC - link
Power Supply R 42
Output +24V
ON
Signaling relay
Ready
Changeover
standby / run
Inverter REFUdrive 500 RD52
X1
C1 D1
2 A
Inverter REFUdrive 500 RD51
Dig. input
Function: "Enable operation"
Dig. input
Function: " N"
X1
C1 D1
2 A
Checkback signal slave
It is also possible to use an
external P24V signal from
the PLC = no fault
Output +24V
Dig. input
Function: "Enable operation"
Dig. input
Function: " N"
Output +24V
Fig. 1-2: Block circuit diagram RD42

1-4 Description RD 500 RD42
DOK-RD500*-RD42*******-IB03-EN-P
1.5 Type code
1234 6789
1
05 1234 6789
2
0512346789
3
05 1234 6789
4
05
Example:
Abbrev.
Column
RD42 . 1 - 4R- 026- L
1. Product group
1.1 RD. . . . . . . . . . . . = RD
2. Line
2.1 42. . . . . . . . . . . . . . . . = 42
3. Design
3.1 1 . . . . . . . . . . . . . . . . . . . . . . . = 1
4. Mains connecting voltage
4.1 3 x
AC 380 to 480 V, 10 %
. . . . . . .
= 4
4.2 3 x AC 500 V, 10 % . . . . . . . . . . . = 5
5. Ba e chopper
5.1 without brake chopper, regenerativ. . . = R
6. DC-bus nominal power at 3 x AC 400 V
6.1 26 kW. . . . . . . . . . . . . . . . . . . . . . . . . . . . = 026
6.2 53 kW. . . . . . . . . . . . . . . . . . . . . . . . . . . . = 053
6.3 84 kW. . . . . . . . . . . . . . . . . . . . . . . . . . . . = 084
6.4 105 kW. . . . . . . . . . . . . . . . . . . . . . . . . . . . = 105
7. Cooling mode
7.1 forced air cooling . . . . . . . . . . . . . . . . . . . . . . . . . . . . = L
Illustration example: RD42.1
Fig. 1-3: Type code RD42

RD 500 RD42 Mechanical mounting and installation 2-1
DOK-RD500*-RD42*******-IB03-EN-P
2 Mechanical mounting and installation
2.1 Storage and mounting location
Storage
The units must be stored in clean, dry rooms. The storage temperature
must lie between -25°C and +70°C. Temperature fluctuations exceeded
20 K per hour are not permissible. (environmental Class 3K3 according to
DIN IEC 721-3-3)
Hinweis: Supply modules accommodate Al Elko DC link capacitors.
They can be stored for 2 years at a storage temperature of
≤ 40 °C.
Minimum requirements at the mounting location
•The operating room/area should be dust-free. Dust-laden air must be
filtered.
•The ambient temperature must lie in the range 0 ... 40°C.
•The relative air humidity may not exceed 90 %; moisture condensation
is not permissible.
•The air drawn-in may not contain any aggressive or electrically
conductive gases which could have a negative impact on the function
of the equipment.
•The fan airflow may not be restricted. The specified minimum
clearances for air intake and air discharge may not be restricted by
additional mounted components.
•The unit has a certain power loss and heats-up its environment. This
means that it is important that there is sufficient clearance to
temperature-sensitive devices and equipment.

2-2 Mechanical mounting and installation RD 500 RD42
DOK-RD500*-RD42*******-IB03-EN-P
Installation altitudes above 1000 meters sea level:
If the unit is mounted above 1000 meters above sea level, the supply
module utilization must be reduced corresponding to the adjacent
diagram.
It is not permissible to install the unit at altitudes above 2000 meters
above sea level!
1 %
9 %
83 %
8 %
7 %
5 1 15 2 25
Installation altitude in m
above sea level
Utilization
Fig.. 2-1: Derating as a function of the installation altitude
2.2 Mounting the supply modules
•The modules must be mounted vertically onto a flat surface.
•A minimum clearance of 100 mm both above and below the units must
be maintained to ensure that the airflow is not restricted.
•When the units are mounted in a cabinet, the cooling air requirement
of the installed units (refer to Section 1: Technical data) must be
calculated and the cabinet cooling/ventilation appropriately
dimensioned.
•For supply modules, size Classes D to G, the line filter is externally
mounted for space reasons. We recommend that the line filter is
mounted below the unit; refer to the dimension drawings.
•Please refer to the dimension drawings for the mounting dimensions
and the location of the retaining points.
•Use M6x10 Z 2 DIN 7985 screws to mount the units.

RD 500 RD42 Mechanical mounting and installation 2-3
DOK-RD500*-RD42*******-IB03-EN-P
360
HighVoltage. Danger of
electrical shock. Donot touch
electricalconnections f or 5
minutes after switching
poweroff.
Readand follow "Safety
Instructions for Electrical
Drives "manual DOK-GENE-
RL-DRIVE******-SVS...
before operating
DANGER
REFU
Display
990
100 100
Min. clearance
for cooling
Dimension in mm
line filter
RD42
Warm discharged air
Cooling air
U1 V1 W1
U 2
U 2
V 2
V 2
W 2
W 2
260
Min. clearance
for cooling
Fig. 2-2: Minimum clearance
2.3 Dimension drawings
360
200 320
240 360
HighVoltage. Danger of
electrical shock. Donottouch
electric alconne cti o nsfor 5
minutes after switching
poweroff.
Readand follow "Safety
Instructions for Electrical
Drives "manual DOK-GENE-
RL-DRIVE******-SVS...
before operating
DANGER
REFU
Display
10
550
530
HighVoltage. Danger of
electrical shock. Donot touch
electricalconnections f or 5
minutes after switching
poweroff.
Readand follow "Safety
Instructions for Electrical
Drives "manual DOK-GENE-
RL-DRIVE******-SVS...
before operating
DANGER
REFU
Display
990
20
7
Dimension in mm
Size DE
line filter
RD42
Warm discharged air
Cooling air
168
269
U2 V2 W2 PEPE
U1 V1 W1 PEPE
7120
253
194
12
110
10
7
11
U1 V1 W1
U 2
U 2
V 2
V 2
W 2
W 2
260
153
122
325
184
225
Fig. 2-3: Dimension drawing, size Classes D and E

2-4 Mechanical mounting and installation RD 500 RD42
DOK-RD500*-RD42*******-IB03-EN-P
13
32
36
46
5
1
65
63
36
1 9
72
Dimension in mm
RD42
Line filter
FG
Warm
discharged
air
1
7
11
U1 V1 W1
U 2
U 2
V 2
V 2
W 2
W 2
26
U1 V1 W1
PE
M8 Bolt
PE
M8 Bolt
U 2
U 2
V 2
V 2
W 2
W 2
325
184
225
167
215
365
26
26
15
9
225
Size
Cooling air
Display
16
DANGER
DANGER
Display
12
153
122
Fig. 2-4: Dimension drawing, size Classes F and G

RD 500 RD42 Electrical installation 3-1
DOK-RD500*-RD42*******-IB03-EN-P
3 Electrical installation
3.1 EMC-correct design of drives
The following 10 rules are the basic guidelines for EMC-correct design of
drive systems. Details are provided in separate instructions.
Rules 1 to 7 are generally valid. Rules 8 to 10 are especially important to
limit noise emission.
Rule 1 All of the metal parts and components of the cabinet must be connected
to one another through the largest possible surface area. (Not paint on
paint!) If necessary, use contact or serrated washers. The cabinet door
should be connected to the cabinet itself through grounding strips which
should be kept as short as possible.
Rule 2 Signal, line supply and motor cables and power cables should be routed
separately from one another (avoid having any mutual coupling lengths of
cable!). Minimum clearance: 20 cm. Provide separating sheet metal
panels between power and signal cables. These panels should be
grounded at several locations along their length.
Rule 3 Contactors, relays, solenoid valves, electromechanical operating hour
counters etc. in the cabinet must be provided with noise suppression
devices. These can include, e.g. RC elements, diodes, varistors. These
devices must be connected directly to the coil.
Rule 4 Non-shielded cables belonging to the same circuit (outgoing and incoming
conductors) should be twisted and the surface area between the outgoing
and incoming conductors should be kept as small as possible. Ground the
cores which are not used at both ends.
Rule 5 Noise which is coupled-in is generally reduced if cables are routed close
to grounded sheet metal panels. This is the reason that wiring shouldn’t
be freely routed in the cabinet, but should be routed close to the cabinet
housing or to mounting panels. This is also true for cables which are
presently not being used.
Rule 6 Tachometers, encoders or resolvers must be connected using a shielded
cable. The shield should be connected to the tachometer, encoder or
resolver and to the AC drive converter through the largest possible
surface area. The shield may not be interrupted, e.g. by using
intermediate terminals. For encoders and resolvers, pre-assembled
cables with multiple shielding should be used.
Rule 7 The shields of signal cables must be connected at both ends to ground
(sender and receiver) through the largest possible surface area. If there is
poor potential bonding between the shield connections, to reduce the
current flowing through the shield, an additional bonding conductor,
minimum 10 mm²cross-section should be routed parallel to the shield.
The shield can be connected at several locations with ground (=cabinet
housing). The shields may also be grounded at several locations outside
the cabinet. Avoid using foil-type shields. Their shielding effect is a
minimum of a factor of 5 less than braided shields.
If the potential bonding is poor, analog signal cables may only be
grounded at one end at the AC converter, in order to eliminate low-
frequency noise (50 Hz) on the shield.
Rule 8 A radio interference suppression filter must always be located close to the
noise source. The filter must be connected flush with the cabinet housing,
mounting panel etc. The most favorable solution is a bare metal mounting
plate (e.g. manufactured out of stainless steel, galvanized steel), as in this
case, the complete mounting surface establishes the electrical contact.
Input and output cables to and from the radio interference suppression
filter must be routed separately from one another.

3-2 Electrical installation RD 500 RD42
DOK-RD500*-RD42*******-IB03-EN-P
Rule 9 All variable-speed motors must be connected-up using shielded cables.
The shields must be connected at both ends to the housings/enclosures
through a low-inductance connection (large surface area). The motor
cables must also be shielded inside the cabinet or at least shielded using
separating sheet metal panels.
Rule 10 Steel-shielded cables are not suitable.
Rule 11 A suitable PG gland with shield contact can be used to connect the shield
at the motor (e.g. “SKINDICHT SHV/SRE/E”, from the Lapp Company,
Stuttgart). It should be ensured that there is a low-impedance connection
between the motor terminal box and motor enclosure. If required, connect
using an additional grounding conductor.
Never use motor terminal boxes manufactured out of plastic!
Rule 12 The shield between the motor and AC drive converter may not be
interrupted, i.e. by mounting components such as output reactors,
sinusoidal filters, motor filters, fuses, contactors. The components should
be mounted on a mounting panel, which simultaneously serves as a
screen connection for the incoming and outgoing motor cable. If required,
separating sheet metal panels should be used to shield the components.

RD 500 RD42 Electrical installation 3-3
DOK-RD500*-RD42*******-IB03-EN-P
3.2 Warnings and information
GEFAHR
Electric shock which can lead to death as a
result of live components at voltage levels more
than 50 V!
The supply modules are operated with high voltages.
All work must be carried-out with the equipment in a
no-voltage condition!
Only qualified, fully-trained personnel may carry out
any work!
Death, severe bodily injury or significant material
damage can result if this warning information is not
observed.
The equipment is still a hazardous voltage level even
after it has been powered-down for up to 5 minutes
due to the DC link capacitors. This means that it is
only permissible to work on the equipment or the DC
link terminals at the earliest after the appropriate
delay time and after having first carefully checked
that the equipment actually is in a no-voltage
condition.
The power and control terminals can still be live
(under voltage) even if the motor is stationary.
If the DC link is supplied centrally, it must be ensured
that the inverter is reliably isolated from the DC link
voltage!
When working on equipment which has been
opened-up, it should be observed that live
components are accessible.
The user is responsible in ensuring that all of the
units have been mounted and connected-up in full
compliance with recognized technical regulations of
the particular country as well as any other regionally
valid regulations and specifications. The correct
cable dimensions, fusing/protection, grounding,
powering-down, isolation and overcurrent protection
must be especially taken into account.
CAUTION
Damaging the units by applying the incorrect
supply voltage!
The equipment supply modules are built for various
line supply voltages! This is the reason that line
supply voltages are not specified in the drawings and
tables for the terminal strips.
When connecting-up, take care to observe the rating
plate and the line supply voltage specified in the
technical data.

3-4 Electrical installation RD 500 RD42
DOK-RD500*-RD42*******-IB03-EN-P
Information on protective grounding:Due to the discharge currents of
the units (>3.5 mA) via the protective conductor (PE), the
cable cross-section of the protective conductor to the cabinet
must be at least 10mm2Cu in accordance with DIN VDE
0160, or a second protective conductor must be routed in
parallel (VDE 0160, Section 6.5.2). The discharge currents of
theunitscanbeupto100mA.
For larger connected powers, the minimum cross-section of
the protective conductor must be in the appropriate ratio to the
cross-section of the phase conductor. Please refer to DIN
57100 Part 540 / VDE 0100 Part 540 Table 2. The line-side
circuit of the drive converter corresponds to circuit type 7 (DIN
VDE 0160-5.5.3.4.2 Fig. 8).
In this case, an e.l.c.b. may not be used as protection.
3.3 Cable cross-sections
Maximum cross-sectionRecommende
d minimum
cross-section
of the feeder
cable
Finely
stranded
conductors
Power
code
Supply / DC
link
Solid wire
Supply / DC
link
Line supply
fusing
FF
026 6/6mm
216 mm210 / 2x10 mm263 A
053 25 / 25mm235 mm225 / 2x25 mm2125 A
084 50 / 50 mm250 mm250 / 2x50 mm2200 A
105 95 / 2x50 mm2120 mm295 / 2x50 mm2250 A
Fig. 3-1: Cable cross-sections
For supply modules with power code 105, 2 cables, each 50 mm2must be
used to connect to the DC link
Alternativefusetypes
J.M. M00 (M1) üf2 / ...A 500 V~ gR 32 A ... 250 A
Sitor 3NE80... 660 V~ gR 35 A ... 63 A
Sitor 3NE8727... 660 V~ aR 125 A ... 250 A
The cross-section of the protective conductor (PE) is, according to VDE
0160 for all equipment classes, minimum 10 mm2.
Note: Control cables and power cables must always be routed
separately with a specific clearance between them.
Shielded cables must be used to connect setpoint inputs and
measured value outputs. The shield is connected, on the
equipment side, to the strain relief element.

RD 500 RD42 Electrical installation 3-5
DOK-RD500*-RD42*******-IB03-EN-P
3.4 Power terminals RD42
A supply module, size Class G is shown in the terminal layout diagram.
The position of the terminals corresponds to the narrower or wider units.
HighVo ltage. Dan ger of
electrical sh ock. Donottouch
electricalc onnectionsfo r 5
minutesafterswitching
poweroff.
Readand f ollow "Safety
Instructionsfor Electrical
Drives"manual DOK-GENE-
RL-DRIVE******-SVS...
beforeoperating
DANGER
drive 500
REFU
Display
U1 V1 W1
U 2
U 2
V 2
V 2
W 2
W 2
Legend
X3 Control voltage
terminal strip from left
U1 / V1 W1 PE 121 122 / / / /
C
X2 DC bus
X2 input power connection
with line filter
U1 V1 W1
D
Fig. 3-2: Terminal diagram RD42
3.5 Line filter connection
Terminal Designation
PE Protective conductor
U1
V1
W1
Line supply connection, 3 phases L1, L2, L3
U2
V2
W2
Connection to the supply module
Fig. 3-3: Line filter connection

3-6 Electrical installation RD 500 RD42
DOK-RD500*-RD42*******-IB03-EN-P
3.6 Supply module connection
Power terminal X1
Terminal
X1
Designation
PE Protective conductor
U1
V1
W1
Supply connection via the external line filter
3 phases L1, L2, L3
Fig. 3-4: Power terminal X1
Power terminal X2
Terminal
X2
Designation
C DC link connection + (double terminal)
D DC link connection –(double terminal)
Fig. 3-5: Power terminal X2
Power terminal X3
Terminal
X3
Designation
121
122 Checkback signal contact (NC contact) from the main contactor
U1
V1
W1
Control supply voltage, 3-ph. 380 V –500 V AC
Fig. 3-6: Power terminal X3
Please observe the following when connecting the control voltage:
Depending on the control voltage, the power supply transformer must be
changed-over. The power supply transformer T1 has 3 connections:
380/400 V, 460 V and 500 V; also refer to Fig. 1-2: Circuit principle RD42.
You can see the position of the power supply transformer from Fig. 3-7:
Terminal diagram for size Classes D to F.
The control voltage must be externally fused using 2A slow-acting fuses.
When connecting the control voltage, the phase rotation and phase
position must be the same as the three-phase system at terminals X1,
power input U1,V1,W1.

RD 500 RD42 Electrical installation 3-7
DOK-RD500*-RD42*******-IB03-EN-P
3.7 Control terminals
Terminal diagram
NR 16236
SN 11027
H1
1
1
8
15
1
S1
S12
32
H2
H3
X52 Control terminals
X11
Jumper
power supply
transformer 5 V
46 V
4 V
V
T3
DISPLAY
X16 RS485 / RS232
LEDs
U1
V1
W1
PE
PE
PE
Fault acknowledgement
red: fault
yellow: on
green: ready
not used
Control terminals
Fig. 3-7: Terminal diagram for size Classes D to F

3-8 Electrical installation RD 500 RD42
DOK-RD500*-RD42*******-IB03-EN-P
X52 Control terminals
X11 Control terminals
NR16236
power supply transformer
5 V
46 V
4 V
V
T3
H1
132
H2
H3
SN11 27
X16 RS485 / RS232
Jumper
Fault acknowledgement
LEDs
not used
red: fault
yellow: on
green: ready
Fig. 3-8: Terminal diagram for size Class G
Table of contents
Popular Power Supply manuals by other brands

Kohler
Kohler MT80CHP Installation

Newcastle Systems
Newcastle Systems PowerPack Ultra 2.6 series owner's manual

WAGO
WAGO 787-1202 manual

Heritage MedCall
Heritage MedCall HM-535 Installation and service instructions
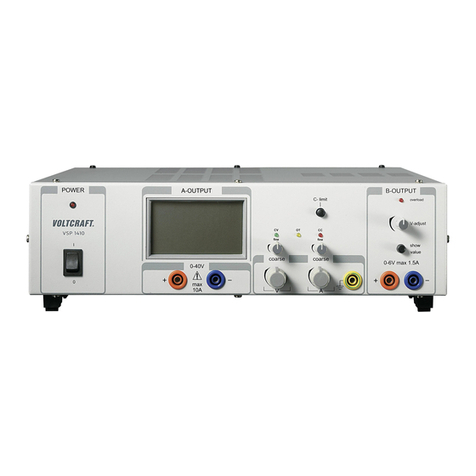
VOLTCRAFT
VOLTCRAFT VSP Series operating instructions
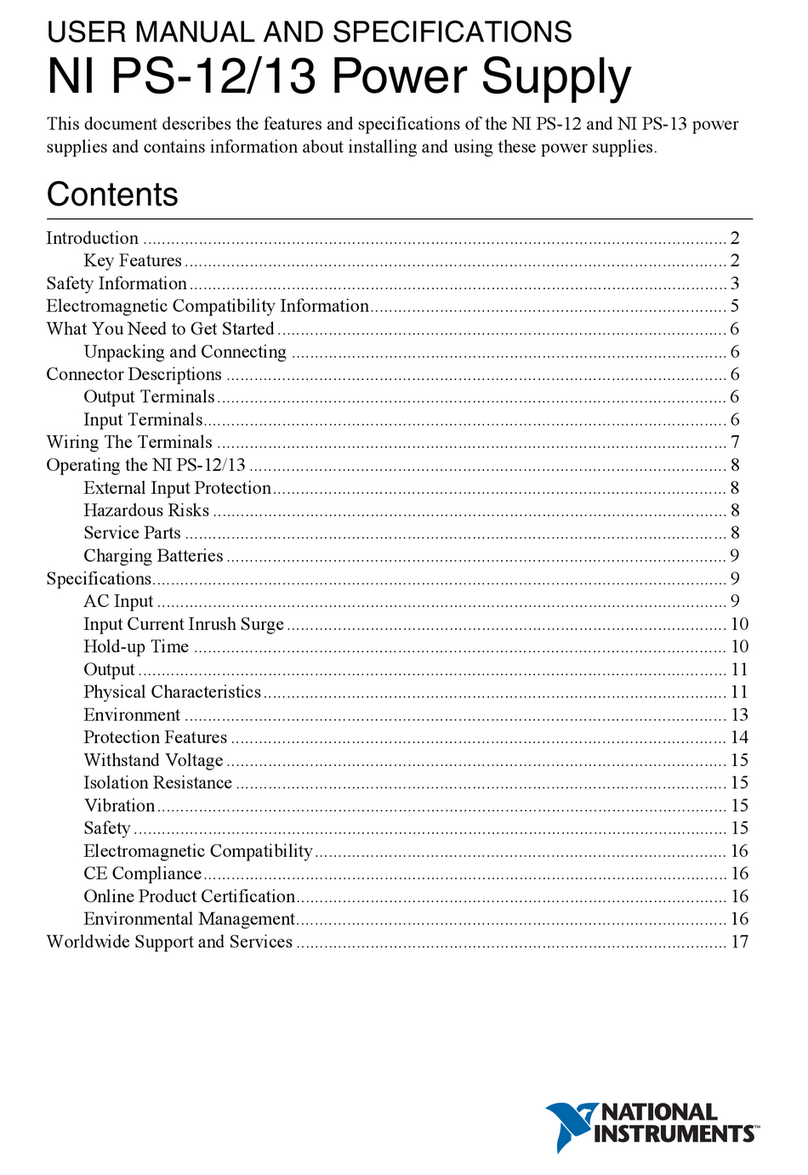
National Instruments
National Instruments NI PS-13 User manual and specifications