Rinstrum C530 User manual

C500 Series
Digital Indicator Reference Manual

Copyright
All Rights Reserved. No part of this document may be copied, reproduced, republished, uploaded, posted,
transmitted, distributed, stored in or introduced into a retrieval system in any form, or by any means (electronic,
mechanical, photocopying, recording or otherwise) whatsoever without prior written permission of Rinstrum
Pty Ltd.
Disclaimer
Rinstrum Pty Ltd reserves the right to make changes to the products contained in this manual in order to
improve design, performance or reliability. The information in this manual is believed to be accurate in all
respects at the time of publication, but is subject to change without notice. Rinstrum Pty Ltd assumes no
responsibility for any errors or omissions and disclaims responsibility for any consequences resulting from the
use of the information provided herein.
Warning
This is a class A product. In a domestic environment this product may cause radio interference in which case
the user may be required to take adequate measures.
i C500-600-2.0.3

Contents
1 Introduction 1
2 Installation 2
2.1 Introduction............................................... 2
2.2 EnvironmentalConditions....................................... 2
2.3 Mounting ................................................ 2
2.4 PowerConnection ........................................... 4
2.5 LoadcellConnection .......................................... 5
2.6 EX-ILoadcellConnection ....................................... 6
2.7 OpticalCommunications........................................ 7
2.8 DB9 Serial Port 1 Connection (C520 Only) . . . . . . . . . . . . . . . . . . . . . . . . . . . . . 8
2.9 DB9 Serial Port 2 Connection (C520 Only) . . . . . . . . . . . . . . . . . . . . . . . . . . . . . 9
2.10OptionalModuleConnections..................................... 9
2.11EthernetConnection.......................................... 9
2.12 USB Host and Device Connections . . . . . . . . . . . . . . . . . . . . . . . . . . . . . . . . . . 9
3 User Interface 11
3.1 General ................................................. 11
3.2 DisplayFunctions............................................ 11
3.3 Keys................................................... 12
4 Licensing 14
4.1 UnlicensedPackages .......................................... 14
4.2 Licence Code Entry from Keypad . . . . . . . . . . . . . . . . . . . . . . . . . . . . . . . . . . . 14
4.3 Licence Code Entry from Web Interface . . . . . . . . . . . . . . . . . . . . . . . . . . . . . . . 14
5 Setup 15
5.1 GeneralInformation .......................................... 15
5.2 BUILD:ScaleBuildMenu....................................... 18
5.3 OPTION:ScaleOptionsMenu .................................... 20
5.4 CAL:ScaleCalibrationMenu..................................... 22
5.5 SERIAL: Serial Communications Menu . . . . . . . . . . . . . . . . . . . . . . . . . . . . . . . . 23
5.6 ETH.NET:EthernetMenu ...................................... 27
5.7 SPEC:SpecialSettingsMenu..................................... 28
5.8 TEST:TestMenu ........................................... 30
5.9 SET.PTS:SetpointsMenu....................................... 31
5.10ANALOG:AnalogOutputMenu ................................... 33
5.11CLOCK:ClockMenu ......................................... 34
5.12FILE:FileMenu ............................................ 35
5.13 DSD: Digital Storage Device Menu . . . . . . . . . . . . . . . . . . . . . . . . . . . . . . . . . . 36
5.14CHG.LOG:ChangelogMenu ..................................... 37
5.15FACTRY:Factorymenu........................................ 38
6 Operator Menus 39
7 Calibration and Trade 41
7.1 IntroductionandWarnings ...................................... 41
7.2 GeneralInformation .......................................... 41
7.3 CAL:ZERO Zero Calibration Routine . . . . . . . . . . . . . . . . . . . . . . . . . . . . . . . . 44
7.4 CAL:SPAN Span Calibration Routine . . . . . . . . . . . . . . . . . . . . . . . . . . . . . . . . 44
7.5 Linearisation .............................................. 45
7.6 DirectmV/VCalibration ....................................... 45
7.7 CAL:FAC.CAL Factory Calibration . . . . . . . . . . . . . . . . . . . . . . . . . . . . . . . . . 46
8 Automatic Weight Output 47
8.1 Introduction............................................... 47
ii C500-600-2.0.3

8.2 Formats ................................................. 47
8.3 CustomFormatTokens ........................................ 49
9 Printing 52
9.1 Overview ................................................ 52
9.2 CustomTicketHeaders ........................................ 52
9.3 CustomTicketFormat......................................... 53
9.4 CustomFormatTokens ........................................ 53
9.5 ASCIIcodes............................................... 54
10 USB Interface 55
10.1DeviceInterface............................................. 55
10.2HostInterface.............................................. 55
11 Change Log 57
11.1Introduction............................................... 57
11.2FormatandCapacity.......................................... 57
11.3ChangelogSecurity........................................... 57
12 Digital Storage Device (DSD) 58
12.1Introduction............................................... 58
12.2FormatandCapacity.......................................... 58
12.3ChangelogSecurity........................................... 58
12.4ConfiguringtheDSD.......................................... 58
12.5WritingRecords ............................................ 58
12.6ReadingRecords ............................................ 58
13 Alibi Application 60
13.1Introduction............................................... 60
13.2ChangingModes ............................................ 60
13.3WeighingandCountingModes .................................... 60
13.4 DSD and Change log Viewer Modes . . . . . . . . . . . . . . . . . . . . . . . . . . . . . . . . . 61
14 Ethernet Interface 62
14.1Overview ................................................ 62
15 Accessory Modules 64
15.1Introduction............................................... 64
15.2Installation ............................................... 64
15.3Mapping................................................. 64
15.4Configuration.............................................. 64
15.5Details.................................................. 64
16 Setpoints 65
16.1Introduction............................................... 65
16.2Connection ............................................... 65
16.3GeneralSettings ............................................ 65
16.4CommonSettings............................................ 65
16.5 Over, Under, Weigh in and Weigh Out Setpoints . . . . . . . . . . . . . . . . . . . . . . . . . . 67
16.6StatusBasedSetpointTypes ..................................... 68
16.7Example1(fillingabag)........................................ 68
16.8 Example 2 (loss in weight system) . . . . . . . . . . . . . . . . . . . . . . . . . . . . . . . . . . 68
17 Remote Input Functions 69
17.1Introduction............................................... 69
17.2Functions ................................................ 69
17.3RemoteAccess ............................................. 69
17.4Blanking................................................. 69
iii C500-600-2.0.3

17.5Locking ................................................. 70
17.6Totalising ................................................ 70
17.7SingleSerialTransmission....................................... 70
17.8 Thumbwheel IO selection of printer text line . . . . . . . . . . . . . . . . . . . . . . . . . . . . 71
17.9Unitswitch ............................................... 71
17.10Setpointresetinputs.......................................... 71
18 Network Communications 72
18.1Introduction............................................... 72
18.2NetworkrinCMD............................................ 72
18.3rinCMDExamples ........................................... 75
18.4rinCMDRegisters ........................................... 78
19 Modbus 95
19.1RegisterSizes.............................................. 95
19.2ModbusHoldingRegisters....................................... 95
19.3ModbusInputRegisters ........................................ 101
20 Ethernet/IP Optional Software 102
20.1Overview ................................................ 102
20.2Terminology............................................... 102
20.3ObjectModel.............................................. 103
21 Network Commands 119
21.1BasicCommandSet .......................................... 119
21.2 Extended Command Set: Overview . . . . . . . . . . . . . . . . . . . . . . . . . . . . . . . . . . 119
21.3 Extended Command Set: Details . . . . . . . . . . . . . . . . . . . . . . . . . . . . . . . . . . . 121
22 5000 Legacy Modbus ASCII Networking 161
22.1 Connection of the C500 Network . . . . . . . . . . . . . . . . . . . . . . . . . . . . . . . . . . . 161
22.2 Modbus Register Definitions for the 5000 . . . . . . . . . . . . . . . . . . . . . . . . . . . . . . 161
23 Securing the Device 163
23.1 Setting a Safe and Full Passcode . . . . . . . . . . . . . . . . . . . . . . . . . . . . . . . . . . . 163
23.2 Changing the Web Interface Passcode . . . . . . . . . . . . . . . . . . . . . . . . . . . . . . . . 163
23.3 Securing Against Threats via Network . . . . . . . . . . . . . . . . . . . . . . . . . . . . . . . . 163
23.4EnablingExternalAccess ....................................... 164
24 Error Messages 165
24.1WeighingErrors ............................................ 165
24.2SetupErrors .............................................. 165
24.3CalibrationErrors ........................................... 166
24.4SystemErrors.............................................. 166
25 Troubleshooting 168
26 Upgrading Firmware 169
26.1PackagesfortheC500 ......................................... 169
26.2 Upgrading Firmware via the Web Interface . . . . . . . . . . . . . . . . . . . . . . . . . . . . . 170
26.3 Licensing Firmware via the Web Interface . . . . . . . . . . . . . . . . . . . . . . . . . . . . . . 174
26.4 Upgrading firmware via the USB host interface . . . . . . . . . . . . . . . . . . . . . . . . . . . 176
iv C500-600-2.0.3

1 Introduction
The C520 is a precision digital indicator. The C530 is a precision digital weight transmitter. Both use a
sigma-delta analog-to-digital (A/D) converter to ensure extremely fast and accurate weight readings. This
advanced technology allows the C520 and C530 to be configured for up to 100,000 divisions with up to 100
A/D conversions per second. The units have extended sensitivity adjustment which can handle scales with
outputs 0.2-5.0mV/V for full range. The design is optimized to deliver precision performance on scale bases
delivering above 0.5mV/V at display resolutions of up to 10000 divisions in single range mode, or 5000 divisions
in dual range mode.
Throughout this document the two devices will be referred to as the C500 series.
The C520 digital weight indicator has a green six digit 14 segment LED display with additional indication of
weighing status. Each digit is 14mm high. The instrument has 8 setpoints with status display on the front
panel. The C530 digital weight transmitter has no display, but can be accessed by the C500 series viewer PC
software.
The C500 series can either operate from mains AC supply (86-260VAC 48-62Hz) or from stable DC supplies
(12-24VDC).
The setup and calibration are digital, with a non-volatile security store for all setup parameters. The built-in
clock can be used to date-stamp printouts. There is an NVRAM store to ensure day to day operating settings
(zero, tare, date/time, etc) are retained when power is removed.
The C520 and C530 have the following interfaces as standard:
Infrared communications port for easy configuration.
USB slave
USB host
Ethernet
RS232 and RS485 (C520 only)
Two optional accessory modules can be fitted to the indicator. These provide additional hardware interface
features such as:
AC power input
Additional serial ports for RS232 and RS485
Inputs and outputs
Analog outputs
1 C500-600-2.0.3

2 Installation
2.1 Introduction
The C520 can be used as either a desk-top or panel-mount instrument. The C530 is intended for installation in
electronics cabinets. The C500 series contains precision electronics and must not be subject to shock, excessive
vibration, or extremes of temperature, either before or after installation. The operating environment must fall
within the allowed temperature range and humidity.
The inputs of the C500 series are protected against electrical interference, but excessive levels of electromagnetic
radiation and RFI may affect the accuracy and stability of the instrument. The C500 series should be installed
away from any sources of electrical noise. The loadcell cable is particularly sensitive to electrical noise, and
should be located well away from any power or switching circuits. Termination of the loadcell shield at
the indicator end (with a sound connection to the indicator case via the DB9 plug or screw terminal shield
connection) is important for EMC immunity.
The C500 series must be installed in a manner and location that is protected from impacts.
Warning!
If the equipment is not installed and used as specified by the manufacturer, the
protection provided by the equipment may be impaired.
2.2 Environmental Conditions
The C500 series is designed for use in the following environmental conditions:
C520: Indoor use only. Although the front of the device can be washed down (as per IP65), the rear of
the device, along with cable attachments and optional accessories, must be protected from liquids and
small objects (as per IP30).
C530: Indoor use only. The device cannot be washed down. The device, along with cable attachments
and optional accessories, must be protected from liquids and small objects (as per IP30).
Altitude: up to 2000m
Operating temperature range: -10
°
C to 40
°
C
Storage temperature range: -20
°
C to 50
°
C
Humidity: Maximum relative humidity of 80% for temperatures up to 31
°
C decreasing linearly to 50%
at 40
°
C
Mains supply voltage fluctuations: up to ±10%.
Pollution degree: 2
2.3 Mounting
2.3.1 C520 Panel Mounting
The C520 fits a DIN 43 700 standard 138(-0/+1)mm x 67(-0/+1)mm panel cut-out. Panel mounting is included
standard. To panel mount:
1. Insert the 4 supplied M4 screws in the mounting tabs in the corners.
2. Insert the indicator into the panel and rotate the 4 tabs out from the indicator.
3. Tighten the screws to clamp the indicator into the panel. Do not over tighten.
2 C500-600-2.0.3

2.3.2 C530 Surface Mount
The C530 can be attached to a surface using the four mounting holes.
1. Use four M4 bolts, or four #6 screws to attach the C530 to the mounting surface as shown below.
2.3.3 C530 DIN Rail Mounting
The C530 can be attached to a DIN rail using the optional DIN rail mounting kit:
1. Attach the two DIN rail mounts to the C530 using the four supplied screws
2. Clip the C530 to the DIN rail
3 C500-600-2.0.3

2.4 Power Connection
The C500 series can be powered from DC or AC supplies.
2.4.1 DC Power
The C500 series requires a 12-24VDC power supply. The supply need not be regulated, provided that it is free
of excessive electrical noise and sudden transients. The C500 series can operate from good quality plug-packs
of sufficient capacity to drive both the indicator and the loadcells.
The case ground connection is available via the earth stake on the rear of the unit. The resistance measured
between the case of the indicator and the nearest earth point should be less than 2 ohms.
2.4.2 AC Power Module
There is an optional AC supply module which requires an AC input of 100-240VAC, 50-60Hz, ≈0.6A. Maximum
supply voltage variations should not exceed ±10% of the voltage range specified.
The AC supply module also provides a 12DC 0.5A(max) output. Attachment of the AC module is shown
below.
4 C500-600-2.0.3

2.5 Loadcell Connection
2.5.1 Overview
The C500 series can drive any number of full bridge strain gauge loadcells up to the equivalent of 16 x 350
ohm cells (21 ohm load).
The span range of the loadcell outputs (the change of signal from the loadcells between zero load and full gross
load) must be within the range of 0.2 to 5.0 mV/V. Very low output scale bases can be used with the C500
series, but may induce some instability in the weight readings when used with higher resolutions. Generally
speaking, the higher the output, or the lower the number of divisions, the greater the display stability and
accuracy.
When shunting loadcells, use only good quality metal film resisters with high temperature stability ratings.
Typical values for zero adjustment would fall within the range of 500k ohms (small effect) to 50k ohms (larger
effect).
The C500 series has a mV/V meter test mode which can be used to check scale base signal output levels. Refer
to Section 5.8.
Warning!
Sense lines must be connected. Failure to do this will result in the C500 series
displaying an error message (E00040, E00080 or E000C0).
The C500 series offers two loadcell connection options. For replacement of 5000 indicators, the DB9 connection
can be used, as shown below:
For new installations, the loadcell adaptor can be attached to the rear of the indicator. This permits easier
connection of the loadcell using screw terminals.
5 C500-600-2.0.3

2.5.2 Cable
When wiring loadcells use only high quality shielded multi-core cable. The cable should be run as far away
from any other cabling as possible (minimum separation distance 150mm). Do not bundle loadcell cables with
power or control switching cables as interference can trigger display instability, and cause unreliable operation.
The loadcell shield must be installed so as to connect electrically with the metal shell of the DB9 plug or screw
terminal shield connection in order for the C500 series to provide its full EMC resistance. Any noise absorbed
by the cable shield must be conducted as quickly as possible to the indicator case via the DB9 plug shell,
then direct to a solid earthing point via the earth terminal in the power input socket (or earthing lug on DC
models).
2.5.3 Six Wire Connection
The connection is made using a standard DB9 male plug. The loadcell socket is wired for six wire systems as
follows:
DB9 Pin Screw Terminal Pin Function
1 1 Positive excitation
2 5 Positive sense
3 2 Negative excitation
4 6 Negative sense
9 3 Positive signal
8 4 Negative signal
Shell 7 Cable shield
2.5.4 Four Wire Connection
When a four wire loadcell system is connected some solder or wire bridges are used to ensure that the excitation
voltages are fed into the sense inputs. For DB9 connections, short the following:
EX pin Short to
1 2
3 4
For screw terminal connections, short the following:
EX pin Short to
1 5
2 6
2.6 EX-I Loadcell Connection
The C500 series can be installed with barriers for EX-i applications. Six-wire connection is necessary in this
case to achieve an acceptable performance. The C500 series is not intrinsic safe and must be installed outside
the hazardous area. Connections for an EX-I application are:
6 C500-600-2.0.3

SD01
EX-Area
(Zone 1,2)
Non-EX-
Area
UN = 6,3 eff. V
Ri = 317 Ohm
UN = 6,3 eff. V
Ri = 3017 Ohm
UN = 1 eff. V
Ri = 310 Ohm
Excitation +
Excitation +
Sense +
Sense +
Signal -
Signal -
Signal +
Signal +
Sense -
Sense -
Excitation -
Excitation -
C520 or C530
Scale
If errors E00040, E00080 or E000C0 occur in an EX-I application the check of the voltage drop over the sense
lines can be turned off with the OPTION:SENS.CH setting. Thus the C500 series will accept a higher voltage
drop over the sense lines, but will no longer detect problems with the sense connections.
2.6.1 Non-trade Limits
C520/C530 with zener barrier SD01 (Input signal ≥0,2 µV/e, divisions 3000d, loadcells 2mV/V)
No of loadcells Minimum yield of the loadcells 350 Ω Minimum yield of the loadcells 700 Ω
1 7 % 6 %
2 11 % 7 %
3 14 % 9 %
4 17 % 11 %
6 24 % 14 %
8 31 % 18 %
2.6.2 Trade Limits
C520/C530 with zener barrier SD01 (Input signal ≥1,0 µV/e, divisions 3000d, loadcells 2mV/V)
No of loadcells Minimum yield of the loadcells 350 Ω Minimum yield of the loadcells 700 Ω
1 36 % 28 %
2 53 % 36 %
3 70 % 45 %
4 87 % 53 %
6 - 70 %
8 - 87 %
The minimum yield of the loadcells is proportional to the divisions. E.g. at 2000d and 4 loadcells 350 ohm the
minimum yield is 58%. These calculations are valid for an overall maximum cable resistance of 3.5 ohm per
lead. Larger cable resistances increase the minimum yield.
2.7 Optical Communications
A temporary infrared communications link can be established between the instrument and a PC using an
optional cable. This connection can be used to transfer setup and calibration information from a PC.
7 C500-600-2.0.3

The PC end of the cable is a standard USB connector. The instrument end of the cable attaches to the left
side of the indicator display, or the rear of the indicator as shown below.
Warning!
The optical coupling head contains a strong magnet and should not be placed near
any magnetic storage media (eg. credit cards, floppy disks etc.)
2.8 DB9 Serial Port 1 Connection (C520 Only)
2.8.1 Overview
This port has two types of output drivers: RS232 and RS422/RS485. It is generally used for connecting
external computers or PLCs, or as a driver for remote displays. External devices can be connected as either
RS232 or RS422/485 (4 wire). All connections for the port are on the Serial 1 connector. This is a standard
DB9 socket requiring a female DB9 plug. Since both RS232 and RS422/485 are connected in parallel within
the C520, they will both output exactly the same message. The connections for the outputs are shown below.
Pin No Function Description Connect to external device
2 RX1 RS232 receive Transmit (DB9 pin 3)
3 TX1 RS232 transmit Receive (DB9 pin 2)
5 GND1 RS232 ground Ground (DB9 pin 5)
6 RA RS422/RS485 receive A-
If RS232 is used, do not connect pins 6..9. A
null-modem cable is not suitable. These pins
are connected internally to serial port 2.
7 RB RS422/RS485 receive B+
8 TA RS422/RS485 transmit A-
9 TB RS422/RS485 transmit B-
Shield: Connect as directly as possible to the metal DB9 shell.
2.8.2 RS422/RS485 Termination Resistors
The termination resistors required by RS422 or RS485 networks are built into the C520. The resistors are used
to terminate the ends of the network to provide a balanced loading. See Section 5.5.
2.8.3 RS232 Connection To A PC
C520
SERIAL 1
C520
SERIAL 1
2 RXD
3 TXD
5 GND
2 TXD
3 RXD
7 GND
PC
COM 1
DB9
PC
COM 2
DB25
2 RXD
3 TXD
5 GND
2 RXD
3 TXD
5 GND
8 C500-600-2.0.3

2.8.4 RS485/RS422 Bus Connection
Pins 6 to 9 of serial 1 are connected directly to pins 6 to 9 of the Serial 2 connector. This provides for convenient
implementation of multi-drop RS422 or RS485 communications.
RA
RB
TA
TB
RA 6
RB 7
TA 8
TB 9
SERIAL
1
SERIAL
2
TO NEXT UNIT
RA 6
RB 7
TA 8
TB 9
RA 6
RB 7
TA 8
TB 9
RA 6
RB 7
TA 8
TB 9
RS485/RS422
HOST
SERIAL
1
SERIAL
2
UNIT 1
UNIT 2
2.9 DB9 Serial Port 2 Connection (C520 Only)
2.9.1 Overview
This port is generally used to drive serial printers (with DTR handshaking) and remote displays. It can also
be used as a network port. All connections for the port are on the Serial 2 connector. This is a standard DB9
socket requiring a female DB9 plug. The only output available from Serial 2 is RS232. The connections for
this are shown below.
Pin No Function Description Connect to external device
2 RX2 RS232 receive Transmit (DB9 pin 3)
3 TX2 RS232 transmit Receive (DB9 pin 3)
4 DTR RS232 DTR handshake DTR (DB9 pin 4)
5 GND2 RS232 ground Ground (DB9 pin 5)
6 RA Serial 1 RS422/RS485 receive A-
If RS232 is used, do not connect pins 6..9. A
null-modem cable is not suitable. These pins
are connected internally to serial port 1.
7 RB Serial 1 RS422/RS485 receive B+
8 TA Serial 1 RS422/RS485 transmit A-
9 TB Serial 1 RS422/RS485 transmit B-
Shield: Connect as directly as possible to the metal DB9 shell.
2.10 Optional Module Connections
Two optional modules can be connected. These provide a range of external drivers and features. See Section 15
and the module datasheets (for module specific connection details).
2.11 Ethernet Connection
A standard 10/100 Ethernet port is provided. See Section 14.
2.12 USB Host and Device Connections
A USB host and USB device interface are provided. See Section 10.
9 C500-600-2.0.3

Warning!
Do not connect the USB host port to another USB host port.
It is possible to purchase USB A Male to USB A Male cables
as shown in the picture below that permit such a connection.
Making such a connection will damage the indicator and PC,
voiding the warranty on both devices.
10 C500-600-2.0.3

3 User Interface
3.1 General
The front panel of the C520 has a six digit LED display and a 6 key keypad. A cover on the rear allows access
to a hidden key which can be used to enter full digital setup and calibration. The diagram below shows the
main elements of the front panel.
1
2
3
4
5
6
7
8
The C520 user interface includes:
1. 6 digit 14 segment LED display
2. Units indicator
3. Weighing status
4. Setpoint status
5. 6 key keypad
6. Multiple range/interval status
7. Check weigh status
8. Rinlink attachment
9. Full setup key (on the rear of the indicator)
3.2 Display Functions
Display (1): weight readings, errors, information and setup.
Units indicator (2): units for the weight reading (pounds (lb), kilograms (kg), grams (g), ounces (oz),
and tons (t)).
Status indicators (3), (4), (6) and (7): The indicator bank made up of 4 groups of LEDs. The weighing
status (3) shows the status of the displayed reading. The multirange status (6) shows the current
multirange operation. The setpoint status set (4) shows the status of the 8 setpoints (IO).
11 C500-600-2.0.3

Lit when the displayed reading is within ±1
4of a division of true zero.
Lit when the displayed reading is in motion.
Lit when the displayed reading represents net weight.
Lit when the displayed reading is within the zero range.
Lit when the display reading has been held.
Ranges 1 and 2 (multiple range/interval modes only). The three annunciators are flashed
within the setup menus to indicate the current menu level.
Lit to indicate when a setpoint output is active.
Lit to indicate various states during checkweigh.
3.3 Keys
The C520 has 6 front panel keys that control the operation of the instrument. The 7th key (SETUP) is on
the rear of the instrument. The setup key can be sealed to prevent unauthorized tampering of trade critical
settings and calibration. Each of the front panel keys has two separate functions:
A normal function that is available during normal weighing (as printed on the key). These are described
below.
A setup function which is available during setup and calibration (as printed beneath the key). Refer to
Section 5.1.4.
3.3.1 Zero Key
Normal function Zero Zero the scale.
Long press function Cancel zero Cancel all previous zero operations (not available in trade
mode).
The range of the zero setting is limited according to settings OPTION:USE and OPTION:Z.RANGE.
3.3.2 Tare Key
Normal function Tare Tare the scale.
Long press function Preset tare Enter a preset tare value to apply to the scale.
The Tare key can operate over the entire weight range. In trade mode the Tare key will not operate if the
gross weight is negative.
3.3.3 Gross/Net Key
Normal function Gross / Net Toggle between gross and net weight.
Long press function Operator and setup menus Access to the operator and setup menus and
alibi mode.
12 C500-600-2.0.3

4 Licensing
The C500 series uses licence codes to activate software packages installed on the indicator. All packages with
names in the C500-K5xx and L9xx-5xx range will require a license to be entered.
Licence codes are unique for each indicator and can be acquired from the nearest Rinstrum office.
4.1 Unlicensed Packages
If a package requiring a license is installed but not yet licensed, a message like “C500” “K501” “NOT” “LC-
NSED” will be displayed when the indicator has finished startup. In this example the package C500-K501
requires a license. Care must be taken to ensure the license entered matches the package name the indicator
is displaying.
When an unlicensed package is installed, the indicator can not be used until the package is licensed or unin-
stalled.
To allow temporary use of the indicator, license entry can be skipped by pressing the cancel key. The indicator
will allow 5 minutes of normal operation before returning to a license entry prompt. If the license is not
successfully entered at this stage the indicator will restart.
4.2 Licence Code Entry from Keypad
To license a package on the C500 series, first install the required firmware (see the Install Firmware section for
details). After successful startup, the indicator will prompt the user with the text ‘C500”, “K501”, “NOT”,
“LCNSED”. Pressing the OK button will allow the user to enter the licence code.
Once the license code has been entered, press OK. If successful the indicator will prompt “LCNSE” “OK” and
the indicator will continue to normal operation.
Note
The JI keys are used to move to the next letter and the HN keys are used to select
the appropriate letter.
Alternatively, the network communication command LRP can be used to license pacakges (see Section 21.3.32).
4.3 Licence Code Entry from Web Interface
Packages can also be licensed via the web interface. See Section 26.3 for instructions on using this method.
14 C500-600-2.0.3

5 Setup
5.1 General Information
5.1.1 Introduction
Setup and calibration is carried out entirely from the front panel using the setup functions on the control keys.
There are 3 types of setup:
Full setup: Allows access to all setup parameters, including calibration.
Safe setup: Allows access to setup parameters which are not critical for trade operation of the scale.
Operator setup: Allows access setpoint targets and inflights. See Section 6.
The setup menus are a menu tree of parameters. All parameters can be edited using the C500 series interface.
They can also be edited using the PC configuration tool.
Note
There are several layers of menu settings. This document uses a colon to show
these layers. For example, BUILD:DP refers to the DP setting (decimal point) in
the BUILD menu.
5.1.2 Setup security
There are 2 types of security for unauthorised setup access:
Passcodes:
–Access to the setup can be passcode protected to prevent unauthorized tampering.
–Safe and full setup have separate passcodes. These are set in SPEC:SAFE.PC and SPEC:FULL.PC
–The full setup passcode can be used to access safe setup.
–The safe passcode cannot be used to access full setup.
–Set these passcodes to 0 to disable passcode protection. This is the default.
Physical seals: It is possible to disable access to the full setup via the gross/net key (using SPEC:R.
ENTRY). The rear key must then be used to access full setup. The rear key can be sealed via physical
seals such as destructible labels, lead seals, etc.
5.1.3 Entry
There are 2 methods of entering the setup program.
Safe/full setup (front keys):
1. Long press the Gross/net key.
2. Press the Gross/net key to choose which level of setup is required.
Note
Full setup will not be available if this has been disabled in the setup
3. Press the OK key.
4. If a passcode has been set: Use the Gross/net and Print keys to enter the passcode. Press the OK
key to confirm the passcode.
Full setup (rear key):
1. Press the key on the rear of the indicator. The security cover may have to be removed.
15 C500-600-2.0.3
This manual suits for next models
3
Table of contents
Other Rinstrum Touch Panel manuals
Popular Touch Panel manuals by other brands
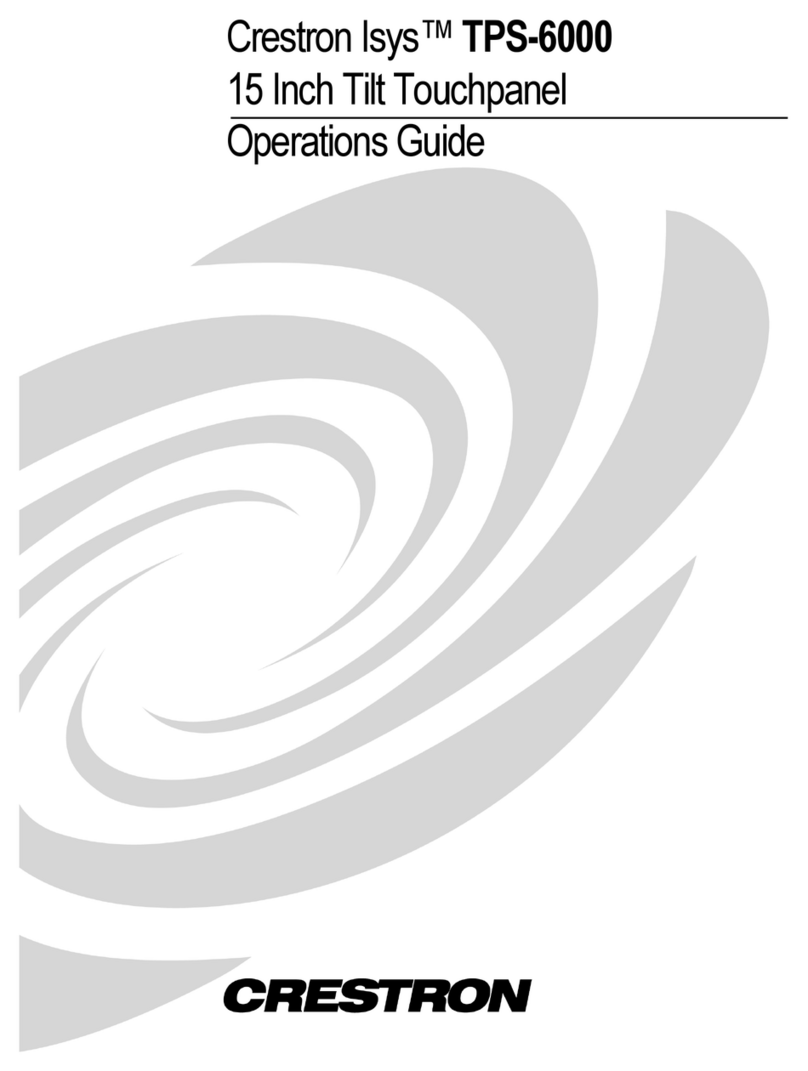
Crestron
Crestron Isys TPS-6000 Operation guide

Clevertouch
Clevertouch clevertouchplus Basic functions guide

Nedlands Group
Nedlands Group FLS-RC-W installation manual
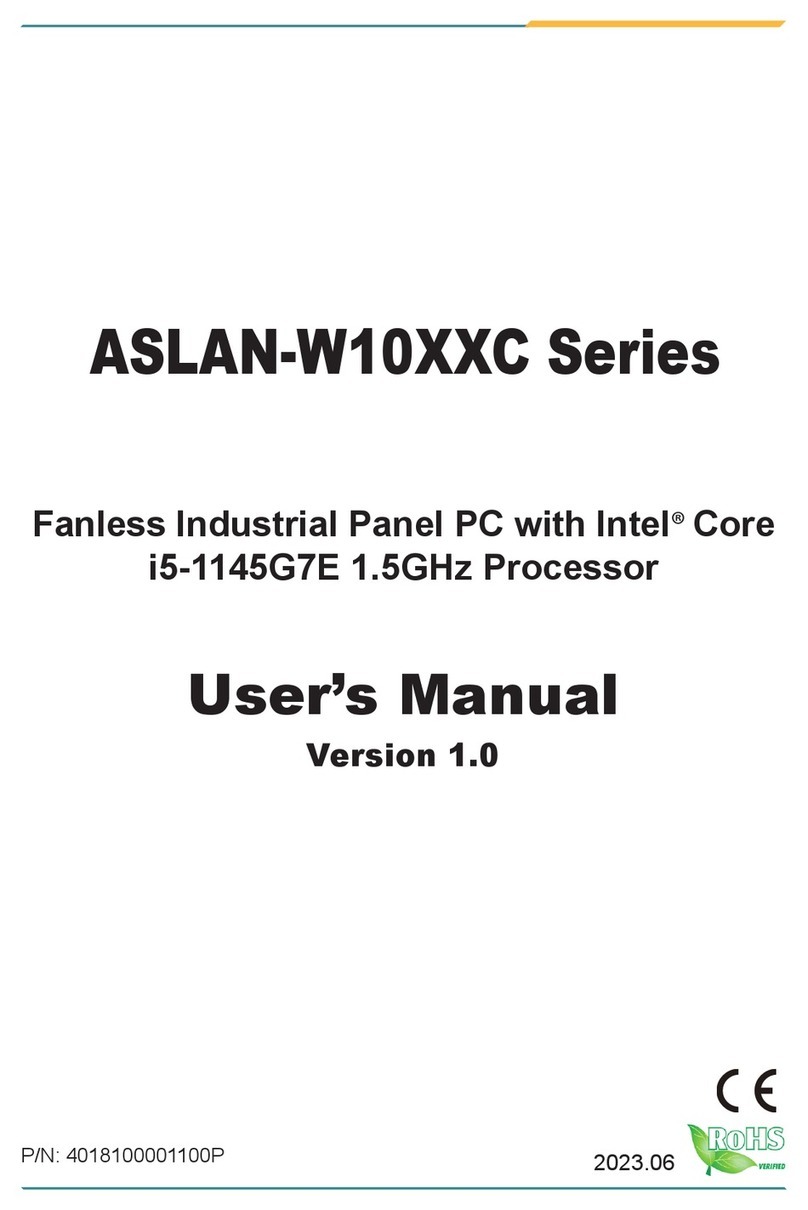
Arbor Technology
Arbor Technology ASLAN-W10 C Series user manual
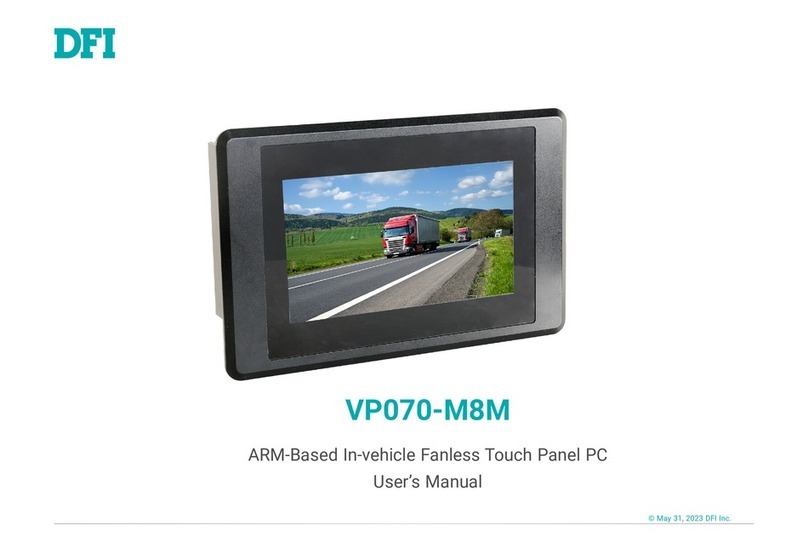
DFI
DFI VP070-M8M user manual
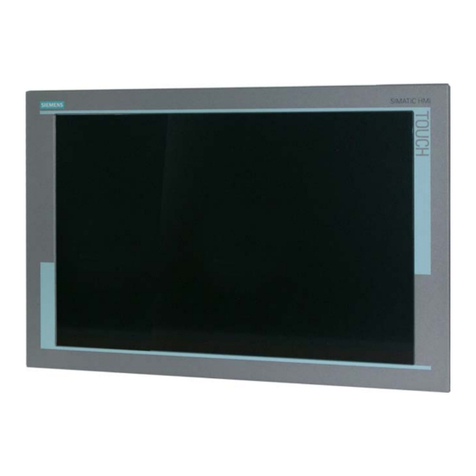
Siemens
Siemens SIMATIC SCD1900 operating instructions