Rockwell Automation Allen-Bradley Guardmaster 442G MABH Series User manual

Multifunctional Access Box
with CIP Safety over
EtherNet/IP
Catalog Numbers 442G-MABH-x, 442G-MABxB-Ux-x,
442G-MABE1
User Manual Original Instructions

2Rockwell Automation Publication 442G-UM002B-EN-P - August 2021
Multifunctional Access Box with CIP Safety over EtherNet/IP User Manual
Important User Information
Read this document and the documents listed in the additional resources section about installation, configuration, and
operation of this equipment before you install, configure, operate, or maintain this product. Users are required to familiarize
themselves with installation and wiring instructions in addition to requirements of all applicable codes, laws, and standards.
Activities including installation, adjustments, putting into service, use, assembly, disassembly, and maintenance are required to
be carried out by suitably trained personnel in accordance with applicable code of practice.
If this equipment is used in a manner not specified by the manufacturer, the protection provided by the equipment may be
impaired.
In no event will Rockwell Automation, Inc. be responsible or liable for indirect or consequential damages resulting from the use
or application of this equipment.
The examples and diagrams in this manual are included solely for illustrative purposes. Because of the many variables and
requirements associated with any particular installation, Rockwell Automation, Inc. cannot assume responsibility or liability for
actual use based on the examples and diagrams.
No patent liability is assumed by Rockwell Automation, Inc. with respect to use of information, circuits, equipment, or software
described in this manual.
Reproduction of the contents of this manual, in whole or in part, without written permission of Rockwell Automation, Inc., is
prohibited.
Throughout this manual, when necessary, we use notes to make you aware of safety considerations.
Labels may also be on or inside the equipment to provide specific precautions.
WARNING: Identifies information about practices or circumstances that can cause an explosion in a hazardous environment,
which may lead to personal injury or death, property damage, or economic loss.
ATTENTION: Identifies information about practices or circumstances that can lead to personal injury or death, property
damage, or economic loss. Attentions help you identify a hazard, avoid a hazard, and recognize the consequence.
IMPORTANT Identifies information that is critical for successful application and understanding of the product.
SHOCK HAZARD: Labels may be on or inside the equipment, for example, a drive or motor, to alert people that dangerous
voltage may be present.
BURN HAZARD: Labels may be on or inside the equipment, for example, a drive or motor, to alert people that surfaces may
reach dangerous temperatures.
ARC FLASH HAZARD: Labels may be on or inside the equipment, for example, a motor control center, to alert people to
potential Arc Flash. Arc Flash will cause severe injury or death. Wear proper Personal Protective Equipment (PPE). Follow ALL
Regulatory requirements for safe work practices and for Personal Protective Equipment (PPE).

Rockwell Automation Publication 442G-UM002B-EN-P - August 2021 3
Table of Contents
Preface
About This Publication . . . . . . . . . . . . . . . . . . . . . . . . . . . . . . . . . . . . . . . . . . . 5
Download Firmware, AOP, EDS, and Other Files . . . . . . . . . . . . . . . . . . . . 5
Summary of Changes. . . . . . . . . . . . . . . . . . . . . . . . . . . . . . . . . . . . . . . . . . . . . 5
Additional Resources . . . . . . . . . . . . . . . . . . . . . . . . . . . . . . . . . . . . . . . . . . . . . 6
Chapter 1
Product Overview Multifunctional Access Box with CIP Safety
over EtherNet/IP Overview . . . . . . . . . . . . . . . . . . . . . . . . . . . . . . . . . . . . . . . 7
Power to Release . . . . . . . . . . . . . . . . . . . . . . . . . . . . . . . . . . . . . . . . . . . . . . . . . 8
Power to Lock. . . . . . . . . . . . . . . . . . . . . . . . . . . . . . . . . . . . . . . . . . . . . . . . . . . . 8
Assembly Overview. . . . . . . . . . . . . . . . . . . . . . . . . . . . . . . . . . . . . . . . . . . . . . . 9
Catalog Number Explanation . . . . . . . . . . . . . . . . . . . . . . . . . . . . . . . . . . . . 11
Auxiliary/Manual Release . . . . . . . . . . . . . . . . . . . . . . . . . . . . . . . . . . . . . . . . 11
Bolt Locking Mechanism. . . . . . . . . . . . . . . . . . . . . . . . . . . . . . . . . . . . . . . . . 12
Mounting Plates. . . . . . . . . . . . . . . . . . . . . . . . . . . . . . . . . . . . . . . . . . . . . 13
Mounting Hardware Reference . . . . . . . . . . . . . . . . . . . . . . . . . . . . . . . 13
Typical Ethernet Configurations . . . . . . . . . . . . . . . . . . . . . . . . . . . . . . . . . 14
Star Topology . . . . . . . . . . . . . . . . . . . . . . . . . . . . . . . . . . . . . . . . . . . . . . . 14
Linear Topology . . . . . . . . . . . . . . . . . . . . . . . . . . . . . . . . . . . . . . . . . . . . . 15
Device Level Ring (DLR) Topology. . . . . . . . . . . . . . . . . . . . . . . . . . . . . 16
Chapter 2
Safety Concept Standards . . . . . . . . . . . . . . . . . . . . . . . . . . . . . . . . . . . . . . . . . . . . . . . . . . . . . . 17
Safety Certification . . . . . . . . . . . . . . . . . . . . . . . . . . . . . . . . . . . . . . . . . . . . . 17
Control of Guard Locking . . . . . . . . . . . . . . . . . . . . . . . . . . . . . . . . . . . . 17
Safety Requirements for Integrated Safety Applications . . . . . . . . . . . . 19
Chapter 3
Use the Multifunctional Access
Box in an Integrated Safety
Controller-based System
Set the Network IP Address . . . . . . . . . . . . . . . . . . . . . . . . . . . . . . . . . . . . . . 21
Set the IP Address with a BOOTP/DHCP Server . . . . . . . . . . . . . . . . . . . . 22
Restore the Access Box to DHCP Mode . . . . . . . . . . . . . . . . . . . . . . . . . . . . 24
When the IP Address of the Access Box Is Known . . . . . . . . . . . . . . . 24
When the IP Address of the Access Box Is Unknown . . . . . . . . . . . . 25
Duplicate IP Address Detection and Resolution . . . . . . . . . . . . . . . . . . . . 25
Add and Configure Access Box in the Logix Designer Application. . . . 25
Add Access Box to the I/O Configuration Tree . . . . . . . . . . . . . . . . . . . . . 26
Configure the Access Box . . . . . . . . . . . . . . . . . . . . . . . . . . . . . . . . . . . . . . . . 26
Change the Access Box Definition . . . . . . . . . . . . . . . . . . . . . . . . . . . . . . . . 28
Configure the Safety Connection . . . . . . . . . . . . . . . . . . . . . . . . . . . . . . . . . 29
Configuration Signature. . . . . . . . . . . . . . . . . . . . . . . . . . . . . . . . . . . . . . . . . 30
Save and Download the Access Box Configuration . . . . . . . . . . . . . . . . . 30
Configuration Ownership — Reset Ownership. . . . . . . . . . . . . . . . . . . . . 30
Reset Access Box to Factory Settings . . . . . . . . . . . . . . . . . . . . . . . . . . . . . . 33
ControlFLASH Application Compatibility . . . . . . . . . . . . . . . . . . . . . . . . . 33

4Rockwell Automation Publication 442G-UM002B-EN-P - August 2021
Chapter 4
Status and Troubleshooting Clear Faults. . . . . . . . . . . . . . . . . . . . . . . . . . . . . . . . . . . . . . . . . . . . . . . . . . . . . 39
Multiple Faults . . . . . . . . . . . . . . . . . . . . . . . . . . . . . . . . . . . . . . . . . . . . . . 39
Appendix A
Specifications Safety Ratings . . . . . . . . . . . . . . . . . . . . . . . . . . . . . . . . . . . . . . . . . . . . . . . . . . 41
Operating Characteristics. . . . . . . . . . . . . . . . . . . . . . . . . . . . . . . . . . . . . . . . 41
Environmental . . . . . . . . . . . . . . . . . . . . . . . . . . . . . . . . . . . . . . . . . . . . . . . . . 42
Physical Characteristics . . . . . . . . . . . . . . . . . . . . . . . . . . . . . . . . . . . . . . . . . 42
Appendix B
EtherNet/IP I/O Assemblies Input Assemblies. . . . . . . . . . . . . . . . . . . . . . . . . . . . . . . . . . . . . . . . . . . . . . . . 43
Output Assemblies . . . . . . . . . . . . . . . . . . . . . . . . . . . . . . . . . . . . . . . . . . . . . . 43
Tag Definitions . . . . . . . . . . . . . . . . . . . . . . . . . . . . . . . . . . . . . . . . . . . . . . . . . 44
Appendix C
Change Actuation Direction of
Handle Assembly
Procedure . . . . . . . . . . . . . . . . . . . . . . . . . . . . . . . . . . . . . . . . . . . . . . . . . . . . . . 47
Index . . . . . . . . . . . . . . . . . . . . . . . . . . . . . . . . . . . . . . . . . . . . . . . . . . . . . . . .49

Rockwell Automation Publication 442G-UM002B-EN-P - August 2021 5
Preface
About This Publication Use this manual if you are responsible for the design, installation,
programming, or troubleshooting of systems that use the Guardmaster® 442G
Multifunctional Access Box with CIP Safety™ over EtherNet/IP™ protocol.
You must have a basic understanding of electrical circuitry and familiarity
with safety-related systems. If you do not, obtain the proper training before
using this product.
This manual is a reference guide for the 442G access box. It describes the
procedures to use to install, wire, and troubleshoot the access box. This manual
does the following:
• Explains how to install and wire your access box
• Provides an overview of the access box
Read and understand this manual before using the described products.
Consult your Allen-Bradley distributor or Rockwell Automation sales office if
you have any questions or comments.
Download Firmware, AOP,
EDS, and Other Files
Download firmware, associated files (such as AOP, EDS, and DTM), and access
product release notes from the Product Compatibility and Download Center at
rok.auto/pcdc.
Summary of Changes This publication contains the following new or updated information. This list
includes substantive updates only and is not intended to reflect all changes.
Topic Page
Updated Additional Resources table. 6
Updated Figure 5.10
Updated Catalog Number Explanation section. 11
Added Reset Access Box to Factory Settings section. 33

6Rockwell Automation Publication 442G-UM002B-EN-P - August 2021
Additional Resources These documents contain additional information concerning related products
from Rockwell Automation.
You can view or download publications at rok.auto/literature.
Resource Description
Multifunctional Access Box with CIP Safety over EtherNet/IP Installation
Instructions, publication 442G-IN004 Provides information on how to install the access box such as mounting information, wiring,
and specifications.
GuardLogix 5570 and Compact GuardLogix 5370 Controller Systems Safety
Reference Manual, publication 1756-RM099 Provides the safety requirements that are required to reach SIL 3 in a safety system.
GuardLogix 5570 Controllers User Manual, publication 1756-UM022 Provides information on how to install, configure, program, and use GuardLogix® 5570
controllers in Studio 5000 Logix Designer® projects.
ControlFLASH Firmware Upgrade Kit User Manual, publication 1756-UM105 Provides information on how to upgrade your module firmware by using ControlFLASH™
software. (1)
Compact GuardLogix 5370 Controllers User Manual, publication 1769-UM022 Provides information on how to install, configure, program, and use Compact GuardLogix
5370 controllers.
EtherNet/IP Network Devices User Manual, ENET-UM006 Describes how to configure and use EtherNet/IP devices to communicate on the EtherNet/IP
network.
Ethernet Reference Manual, ENET-RM002 Describes basic Ethernet concepts, infrastructure components, and infrastructure features.
System Security Design Guidelines Reference Manual, SECURE-RM001 Provides guidance on how to conduct security assessments, implement Rockwell
Automation products in a secure system, harden the control system, manage user access,
and dispose of equipment.
Industrial Components Preventive Maintenance, Enclosures, and Contact
Ratings Specifications, publication IC-TD002 Provides a quick reference tool for Allen-Bradley industrial automation controls and
assemblies.
Safety Guidelines for the Application, Installation, and Maintenance of Solid-
state Control, publication SGI-1.1
Designed to harmonize with NEMA Standards Publication No. ICS 1.1-1987 and provides
general guidelines for the application, installation, and maintenance of solid-state control in
the form of individual devices or packaged assemblies with solid-state components.
Allen-Bradley™ Industrial Automation Glossary, publication AG-7.1 Glossary of industrial automation terms and abbreviations
Industrial Automation Wiring and Grounding Guidelines, publication 1770-4.1 Provides general guidelines for installing a Rockwell Automation industrial system.
Product Certifications website, rok.auto/certifications. Provides declarations of conformity, certificates, and other certification details.
(1) Devices manufactured with firmware revision 1.002 (check unit label) cannot be upgraded using ControlFLASH. Devices that are manufactured with firmware revision 1.005 and higher can
be upgraded using ControlFlash.

Rockwell Automation Publication 442G-UM002B-EN-P - August 2021 7
Chapter 1
Product Overview
Multifunctional Access Box
with CIP Safety over
EtherNet/IP Overview
The multifunctional access box with CIP Safety™ over EtherNet/IP™ is a
combined interlocking module with guard locking and integrated control
elements. The intended use of the access box is at entry points for full-body
access into automation cells or areas that require restricted or controlled
access.
This access box can be used in an integrated safety system with a GuardLogix®.
safety controller. Safety data is exchanged by using CIP Safety via an
EtherNet/IP network.
In combination with a movable safety guard and the control system, this safety
module can help prevent opening of the safety guard while a dangerous
machine function is performed. The position of the guard locking is monitored
during this process.
• Starting commands that cause a dangerous machine function must
become active only when the safety guard is closed and locked.
• The guard locking module must not be unlocked until the dangerous
machine function has ended.
• Closing and locking a safety guard must not cause automatic starting of
a dangerous machine function. A separate start command must be
issued.
The locking module detects the position of the safety guard and the position of
the bolt actuator. The position of the locking arm is also monitored. The bolt
actuator is moved into and out of the locking module by actuating the door
handle. When the bolt is fully inserted into the locking module, the locking
arm can lock the bolt actuator in this position.
The GuardLocked input signal is turned on only when the locking bolt is
sensed in its extended position in the lock module and the locking arm is in
position (for example, the guard is closed and the bolt is both extended and
locked).

8Rockwell Automation Publication 442G-UM002B-EN-P - August 2021
Chapter 1 Product Overview
Power to Release For Power to Release versions, spring force keeps the locking arm in the locked
position and unlocks by solenoid force when power is applied to the solenoid.
Guard locking is activated when the guard is in the closed position and power
is removed from the solenoid.
Guard locking is deactivated when voltage is applied to the solenoid.
Power to Lock For Power to Lock versions, solenoid force keeps the locking arm in the locked
position when power is applied to the solenoid and unlocked by spring force
when power is removed from the solenoid.
Guard locking is activated when the guard is in the closed position and power
is applied to the solenoid.
Guard locking is deactivated when voltage is removed from the solenoid.
IMPORTANT Safety output signal Unlock is turned off.
IMPORTANT Safety output signal Unlock is turned on.
ATTENTION: If the safety guard is open when power is removed from the
solenoid and the guard is then closed, guard locking is activated. This
activation can lead to persons being locked in unintentionally.
IMPORTANT Safety output signal Unlock is turned off.
IMPORTANT Safety output signal Unlock is turned on.
ATTENTION: An unintended loss of power causes guard locking to be
deactivated. Power to Lock versions should only be used for personal
protection if minimum safe distance is provided in accordance with
EN ISO 13855.

Rockwell Automation Publication 442G-UM002B-EN-P - August 2021 9
Chapter 1 Product Overview
Assembly Overview Figure 1 - Components at a Glance
Figure 2 - Bus Module
Figure 3 - Locking Module with Control Cover
Bus Module
Escape Release
(optional)
Lock Module
Mounting Plates
Handle Assembly
Power Connectors
Status Indicators
Ethernet Connectors
Connector for
Attaching an Enabling
Switch (select models)
Status/Diagnostic
Status Indicators
1 x Torx T8
Marking for Maximum
Mounting Distance
Locking Arm
Manual Release Cover

10 Rockwell Automation Publication 442G-UM002B-EN-P - August 2021
Chapter 1 Product Overview
Figure 4 - Handle Assembly
Figure 5 - Escape Release (optional)
IMPORTANT The length of the actuation shaft (115 mm [4.53 in.]) is optimized for
mounting on a 45 mm (1.77 in.) profile. An extended shaft is available
(Cat. No. 442G-MABASHFT). See publication 442G-IN004 for instructions
regarding mounting on smaller or larger profiles.
3 mm
(0.12 in.)
Locking Pin for Handle
Adjustment
Bolt Tongue
Guard Door Handle
Roll-out Bolt
Locking Mechanism Automatically
Extended Bolt
Lock Mechanism
2 x Torx T10
Protective
Sleeve
Setscrew
Handle
Cover
Actuation Shaft
8 x 8 mm (0.31 x 0.31 in.)

Rockwell Automation Publication 442G-UM002B-EN-P - August 2021 11
Chapter 1 Product Overview
Catalog Number
Explanation
See Figure 21 on page 45 and Figure 22 on page 45.
Auxiliary/Manual Release The manual release lets you unlock the guard door when unforeseen or
uncommon circumstances occur.
The system enters into a latching fault (fault code 2744) when the manual
release is actuated.
To clear the fault, open the guard and cycle the LockSequenceFaultUnlatch
input signal (see Clear Faults on page 39).
IMPORTANT The following information is for reference purposes only. Not all
combinations produce a valid catalog number.
442G-MAB R B-U R E0 J P4679 N4
abcdef
ab c
Lock Type Hinge Side E-stop
Code Description Code Description Code Description
R Power to Release R Guard door hinged on the right EO Illuminated E-stop in position S0
L Power to Lock L Guard door hinged on the left Blank No E-stop
def
Enabling Switch Connector Push Button Position Connector
Code Description Code Description Code Description
J Enabling switch connector P49 Push buttons in positions 4 and 9 Blank M12 micro
Blank No connector for enabling switch P4679 Push buttons in positions 4, 6, 7, 9 N4 7/8 in. mini
IMPORTANT The manual release is not a safety function. The machine manufacturer
must select and use a suitable release according to the risk
assessment. The correct function must be checked at regular intervals.
IMPORTANT The system might not enter into a latching fault if the manual release is
actuated slowly.
ATTENTION: The locking screw must be screwed back in and sealed after
assembly and after use of the manual release. Tightening torque is 0.5 N•m
(4.42 lb•in).

12 Rockwell Automation Publication 442G-UM002B-EN-P - August 2021
Chapter 1 Product Overview
To unlock the guard door with the manual release:
1. Undo locking screw.
2. Use a screwdriver to lift the locking arm actuate the guard door handle.
Figure 6 - Auxiliary/Manual Release
Bolt Locking Mechanism The access box has two mechanisms for locking the bolt actuator to help
prevent locking the guard and restarting the machine while an operator is
inside the safeguarded area.
One of the bolt locking mechanisms extends automatically when the handle is
in the OPEN position. The other mechanism is manually extended (see
Figure 6). To pivot out, press the grooved part (only possible with the handle in
the OPEN position and the bolt retracted).
Figure 7 - Bolt Locking Mechanism
Torx (T8)
IMPORTANT With the manual bolt locking mechanism rolled out, the bolt cannot be
extended.
Automatically
Extending Mechanism
Roll-out
Mechanism
The minimum padlock diameter is
2 mm (0.08 in.) and the maximum
diameter is 10 mm (0.39 in.) You can
fit a maximum of three locks in an
8 mm (0.31 in.) diameter.

Rockwell Automation Publication 442G-UM002B-EN-P - August 2021 13
Chapter 1 Product Overview
Mounting Plates
Figure 8 - Handle Assembly Mounting Plate [mm (in.)]
Figure 9 - Escape Release Mounting Plate [mm (in.)]
Mounting Hardware Reference
Handle Assembly Mounting Plate is supplied with the following hardware:
• 4X DIN 7984-M6X12 ZN (screw)
• 4X DIN 433-6 NI (washer)
• 4X DIN 6797-JZ-D6,4 (lock washer)
Escape Release Mounting Plate is supplied with the following hardware:
•4XDIN7984-M6X8(screw)
• 4X DIN 433-6 NI (washer)
• 4X DIN 6797-JZ-D6,4 (lock washer)
IMPORTANT The use of the handle assembly mounting plate is required with the
Ethernet version of the access box. The use of the escape release
mounting plate is optional.
16
(0.63)
10
(0.39)
32 (1.26)
15
(0.59)
6.5 (0.25)
12 (0.47)
17.5 (0.69)
17.5
89.4
(3.54)
135
(5.31)
130.5 (5.14)
12.5
(0.49)
4 (0.16)
170
(6.69)
25
(0.98)
30 (1.18)
110
(4.33)
17.5
M6 (4x)
10
(0.39)
32 (1.26)3
(0.12)
6.5
(0.25)
12 (0.47)
17.5
(0.69)
17.5
135
(5.31)
113.5 (4.47)
4 (0.16)
170
(6.69)
20
(0.79)
89.4
(3.54)
M6 (4x)
20
(0.79)
68
(2.68)
43.5
(1.71)
83
(3.27)
7.5
(0.29)
86.5 (3.40)
19.5
(0.77)

14 Rockwell Automation Publication 442G-UM002B-EN-P - August 2021
Chapter 1 Product Overview
Typical Ethernet
Configurations
The Multifunctional Access Box with CIP Safety can be connected in any of the
following three network topologies: star, linear, or Device Level Ring (DLR).
Star Topology
The star structure consists of a number of modules that are connected to a
central switch. Modules can be added or removed without affecting the rest of
the network.
Figure 10 - Example of Star Topology
ATTENTION: The access box does not currently support time-sensitive
applications that are based on CIP Sync™, including CIP Motion™ applications.
Do not use the access box in DLR topologies where other nodes are using CIP
Sync or CIP Motion. To be used in linear topologies, where other nodes are
using CIP Sync or CIP Motion, the access box must be connected at the end of
the line.
LNK1LNK2 NET OK
EtherNet/IP
1
2

Rockwell Automation Publication 442G-UM002B-EN-P - August 2021 15
Chapter 1 Product Overview
Linear Topology
The linear topology uses the embedded switching capability to form a
daisy-chain style network that has a beginning and an end. Linear topology
simplifies installation and reduces wiring and installation costs, but a break in
the network disconnects all modules downstream from the break. When this
topology is used, both Ethernet connections on the access box may be used. For
the network connection, use Link 1, Link 2, or both.
Figure 11 - Example of Linear Topology
IMPORTANT Modules without dual ports must include the 1783-ETAP module or be
connected at the end of the line.
ATTENTION: The access box does not currently support time-sensitive
applications that are based on CIP Sync, including CIP Motion applications. Do
not use the access box in DLR topologies where other nodes are using CIP
Sync or CIP Motion. To be used in linear topologies, where other nodes are
using CIP Sync or CIP Motion, the access box must be connected at the end of
the line.
LNK1LNK2 NET OK
EtherNet/IP
1
2

16 Rockwell Automation Publication 442G-UM002B-EN-P - August 2021
Chapter 1 Product Overview
Device Level Ring (DLR) Topology
A DLR network is a single-fault-tolerant ring network that is intended for the
interconnection of automation modules without the need for more switches.
The ring topology offers these advantages:
• Media redundancy
• Fast-network fault detection and reconfiguration
• Resiliency of a single-fault-tolerant network
• Easy implementation without more hardware requirements
One DLR network can support as many as 50 nodes. A DLR network supports
copper connections (maximum of 100 m [328 ft]), fiber-optic connections
(maximum of 2 km), or a mix of copper and fiber.
Figure 12 - Example Device Level Ring Topology
IMPORTANT This section summarizes a DLR network. To plan, configure, and
monitor DLR networks, see publication ENET-AP005.
ATTENTION: The access box does not currently support time-sensitive
applications that are based on CIP Sync, including CIP Motion applications. Do
not use the access box in DLR topologies where other nodes are using CIP
Sync or CIP Motion. To be used in linear topologies, where other nodes are
using CIP Sync or CIP Motion, the access box must be connected at the end of
the line.
LNK1LNK2NET OK
EtherNet/IP
1
2

Rockwell Automation Publication 442G-UM002B-EN-P - August 2021 17
Chapter 2
Safety Concept
Standards The access box satisfies applicable requirements in the following standards
that are related to functional and machinery assembly:
• IEC 60947-5-3: 1999/A: 2005
• EN/ISO 13849-1:2008/AC: 2009 (Performance Level e [PLe], Category 4)
• IEC 61508: 2010 (SIL 3)
• IEC 62061: 2005 (SIL CL 3)
• EN/ISO 14119:2013
• UL 508 17th Edition dated 3/19/2013
Safety Certification The Guardmaster® access box is a Type 4 interlocking module with guard
locking and high-coded RFID actuators according to EN ISO 14119.
The access box is certified for use in safety applications up to and including
Performance Level PLe and Category 4 in compliance with EN ISO 13849-1 and
SIL 3 according to IEC 61508 and IEC 62061, for guard position monitoring,
guard lock monitoring, and guard locking control.
Control of Guard Locking
The access box PFHdand the external control (for example, PFHdof the
standstill monitor) determine the safety level of guard locking control. Guard
locking is controlled with the Unlock output signal.
Figure 13 - Control of Guard Locking
Access Box
PFHd
(internal electronics)
PFHd
(For example,
standstill monitor)
Safety Output Signal
(Unlock)

18 Rockwell Automation Publication 442G-UM002B-EN-P - August 2021
Chapter 2 Safety Concept
Figure 14 applies to access boxes with emergency stop.
Figure 14 - Emergency Stop Function
Figure 15 applies to access boxes with a connection for an enabling switch.
Figure 15 - Enabling Switch Function
The access box must be installed in accordance with the applicable regulation
and standards.
While the access box can be used for PLe and Category 4 applications, the
installer must comply with guard requirements (for example, EN/ISO 13854
and EN/ISO 13857) and in some cases also minimum (safe) distance
requirements (for example, EN/ISO 13855).
The installed system, including the safety control system and the means by
which the machine stops, must achieve the needed safety performance. The
access box is one element in the safety system.
Before safety components are used, a risk assessment must be performed on
the machine in accordance with:
• EN ISO 12100, Safety of machinery — Basic concepts - General principles
for design - Risk assessment and risk reduction.
• EN ISO 13849-1, Safety of machinery. Safety-related parts of control
systems. General principles for design, Annex B
• IEC 62061, Safety of Machinery — Functional safety of safety-related
electrical, electronic, and programmable electronic control systems.
Correct use includes compliance with the relevant requirements for
installation and operation, in particular:
• EN ISO 13849-1, Safety of machinery. Safety-related parts of control
systems. General principles for design
• EN ISO 14119, Safety of machinery. Interlocking modules that are
associated with guards. Principles for design and selection
• EN 60204-1, Safety of machinery. Electrical equipment of machines.
General requirements.
Access Box
B10d
(Emergency stop)
PFHd
(internal evaluation of
the emergency stop)
PFHd
(Safety controller)
Input Signal
(E-stop)
Guard Locking Module
B10d
(Enabling switch)
PFHd
(internal evaluation of
the emergency stop)
PFHd
(Safety controller)
Input signal
(Enabling Switch)

Rockwell Automation Publication 442G-UM002B-EN-P - August 2021 19
Chapter 2 Safety Concept
Additional guidance on guards, guard locking, and guard interlocking is found
in:
• EN/ISO 12100 Safety of machinery — General principles for design —
Risk assessment and risk reduction
• EN/ISO 13855 Safety of machinery — Positioning of safeguards
concerning the approach speeds of parts of the human body
• EN/ISO 13857 Safety of machinery — Safety distances to prevent hazard
zones from being reached by upper and lower limbs
• EN/ISO 14120 General requirements for the design and construction of
guards
Safety Requirements for
Integrated Safety
Applications
Safety application requirements include evaluating the probability of failure
rates (PFD and PFH), system reaction time settings, and functional
verification tests.
For safety system requirements, including information on the safety network
number (SNN), functional verification test intervals, system reaction time,
and PFD/PFH calculations, see the GuardLogix® safety reference manual for
your controller. You must read, understand, and fulfill the requirements that
are detailed in the safety reference manual before operating a safety system
that uses this access box.

20 Rockwell Automation Publication 442G-UM002B-EN-P - August 2021
Chapter 2 Safety Concept
Notes:
This manual suits for next models
2
Table of contents
Other Rockwell Automation IP Access Controllers manuals
Popular IP Access Controllers manuals by other brands
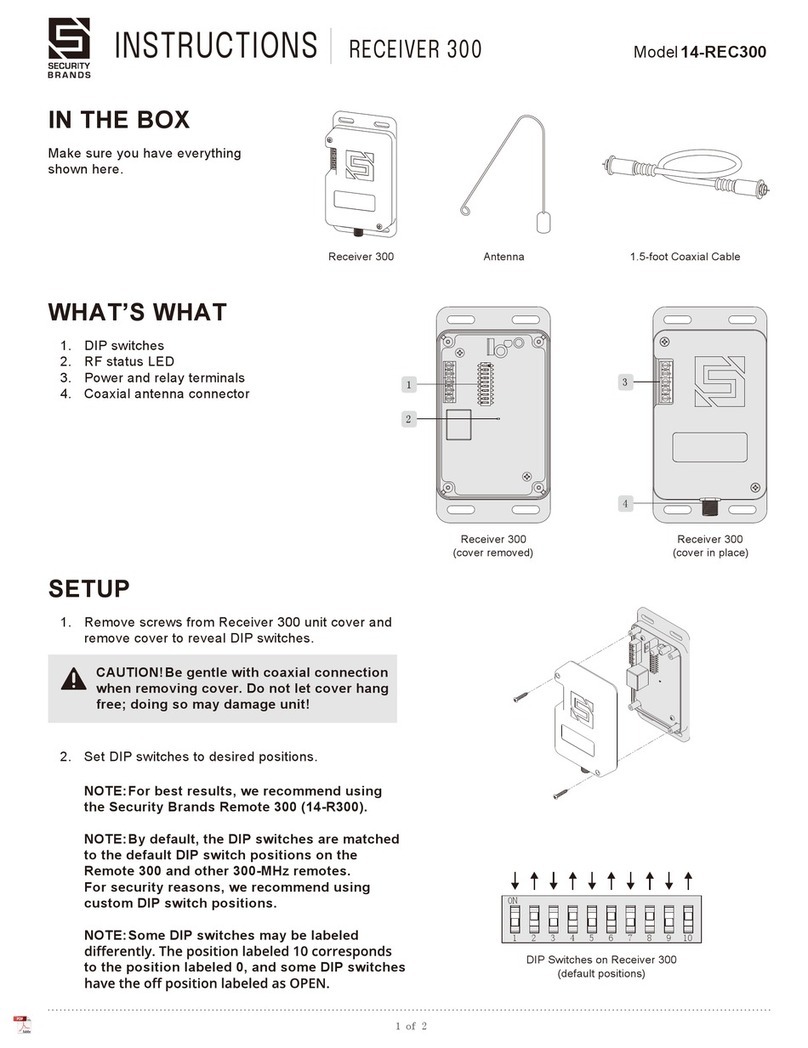
Security Brands
Security Brands RECEIVER 300 instructions
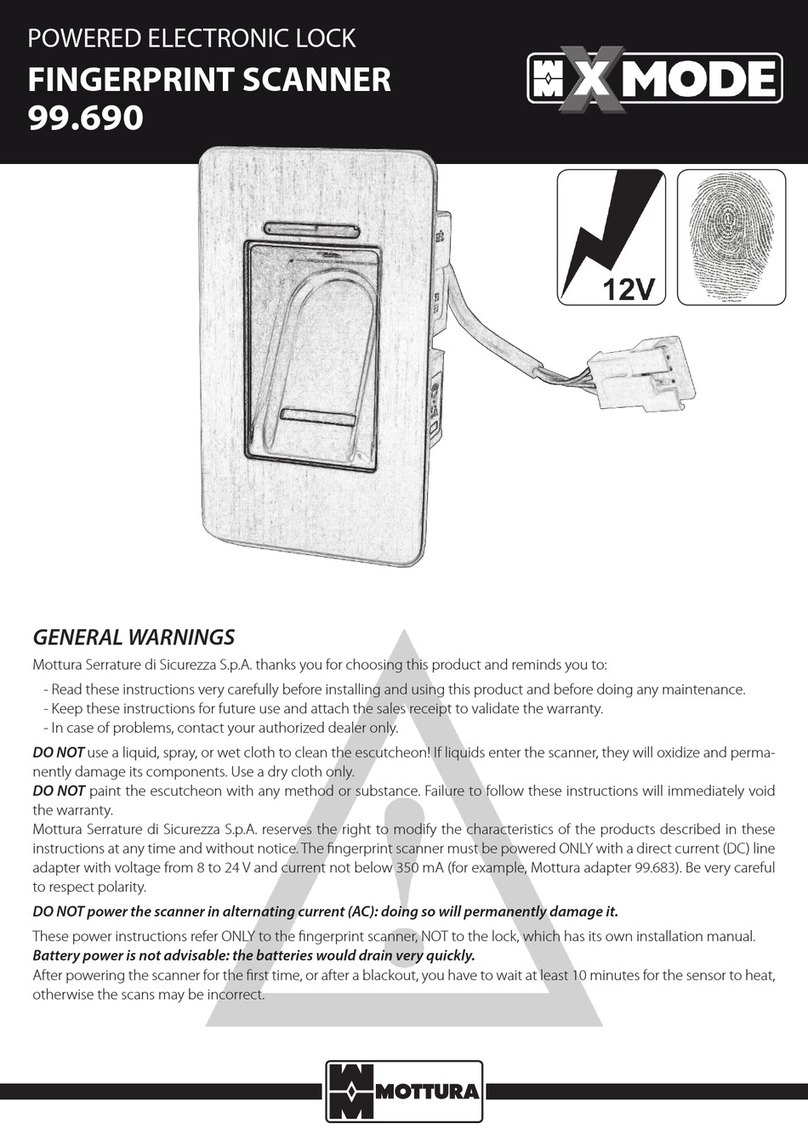
Mottura
Mottura X Mode 99.690 manual

Motorline professional
Motorline professional MLB3 User's and installer's manual
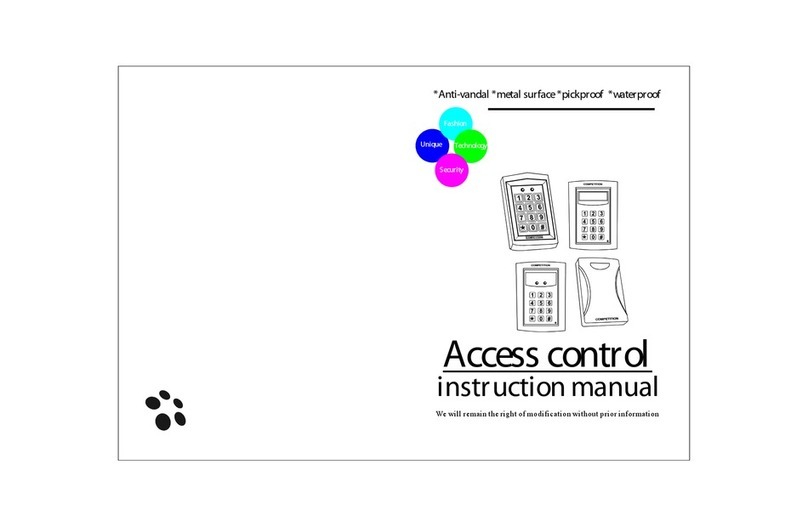
Competition
Competition DH16A-11DT instruction manual
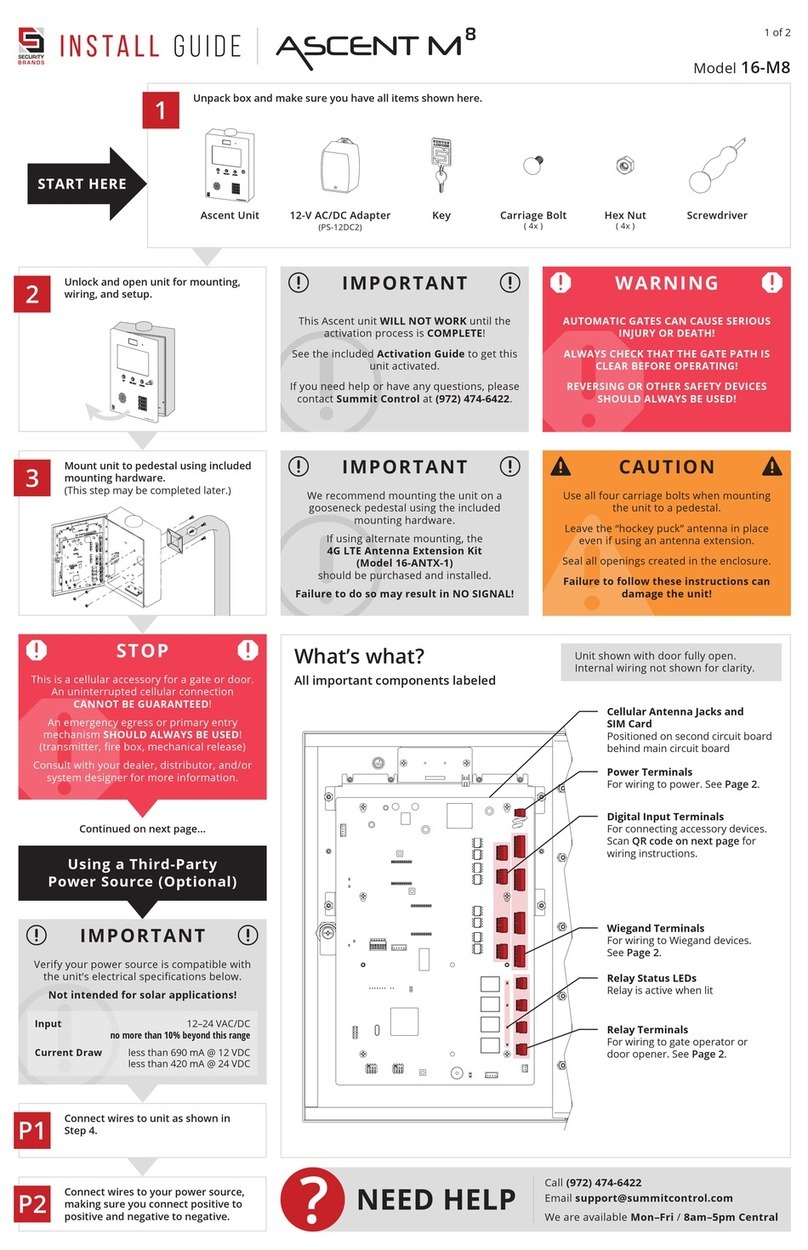
Security Brands
Security Brands ASCENT M8 install guide
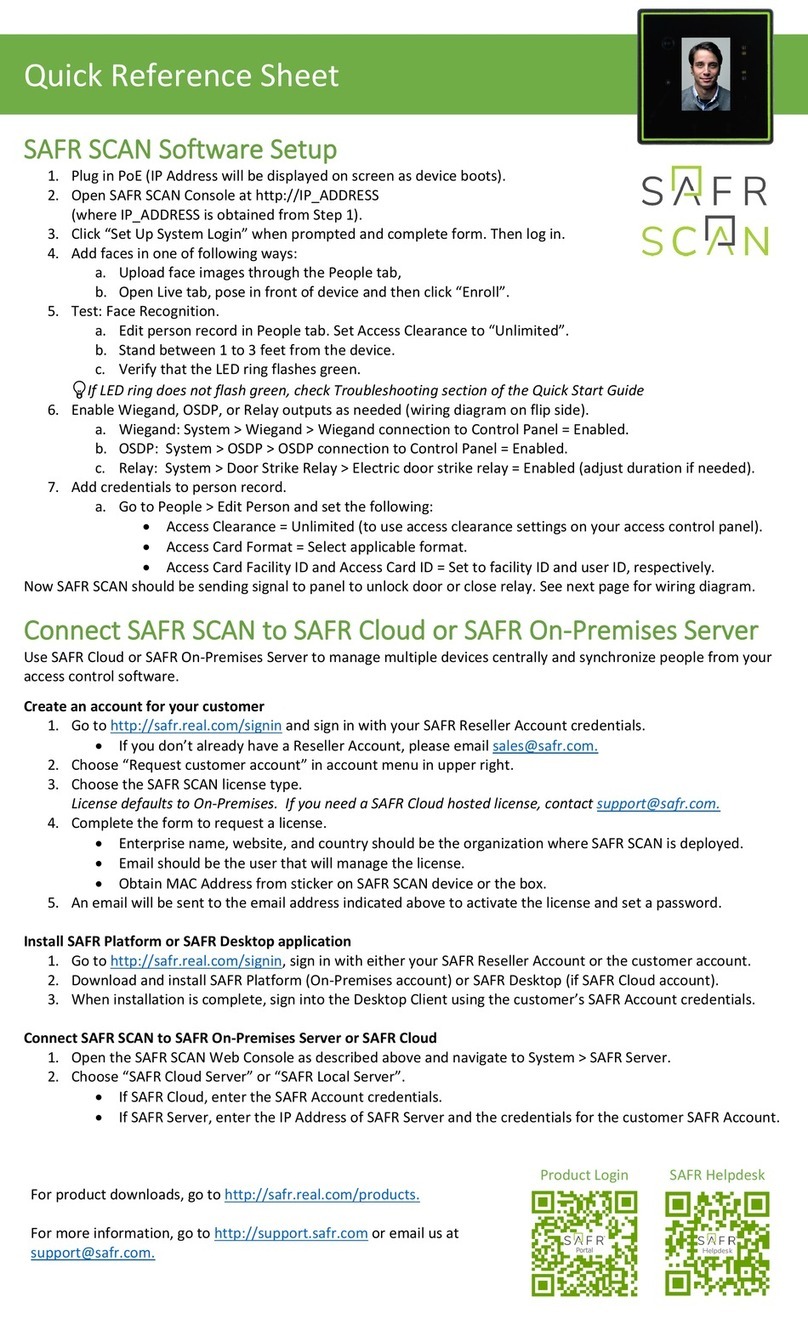
RealNetworks
RealNetworks SAFR SCAN Quick reference sheet