ROLLAND ROLLFORCE User manual

Notice originale : Français NT0002 V –p –03/2014
1
Dear Client,
You have just purchased a ROLLAND spreader.
We would like to thank you for the trust you have placed in us.
ROLLAND spreaders have been studied so that their spreading
technique can be maximised. They are the product of our technology and
experience in this field.
This manual must be considered as forming an integral part of your
spreader.
For proper usage, and to be able to take advantage of all of your
spreader’s capability, we recommend that you read this manual carefully,
and adhere strictly to all of the instructions contained herein.
The correct functioning and durability of your spreader will depend
on this, as will your safety and that of others.
Keep this document in its entirety should you need to consult it in due
course. This must always be kept in the spreader, even in the event that it is
resold.
Failure to adhere to the instructions contained herein release both the
manufacturer and seller from all liability.
We reserve the right to add at any time those modifications that we
deem useful for our products etc, without the obligation to previously
delivered products or those under construction. We also reserve the right to
modify without forewarning the models defined in our catalogues, leaflets
or appearing on our web site.
Please accept our best wishes and most sincere thanks.
Z.A des Landes
29800 TREFLEVENEZ - FRANCE
Tél. : 00 33 (0)2 98 85 13 40
Fax : 00 33 (0)2 98 21 38 15
www.remorquerolland.com

Notice originale : Français NT0002 V –p –03/2014
2
Contents
1-Safety Instructions……………………………….………………….3
2-Warranty Conditions…………………………………………………4
3-Vehicle Presentation……………………………………………….5
-Usage Scope
-Vehicle Identification
-Technology and Options
4-Implementation…………………………………………………...20
5-Standard Usage and Counter-Indications……………………….….29
-Parking
-Loading
-Transport
-Spreading
6-Adjustments……………………………………………………….32
-Jib
7-Servicing and Maintenance……………………………………….34
-Braking Systems
-Ro-Ro Transport
-Cleaning / Lubrication
-Regulation of Belt Tension
-Tracker Adjustments
- Maintenance Regulator and Hydraulic Power Stations
-Consumable parts
-Maintenance of Electrical Boxes
-Wheels and Tyres
-Lighting
8-Assembly………………………………………………………….48
-Rotating Warning Lights
-Equipment
9-Annexes………….………………………………………...…………..54
-Hydraulic Jib
-Passive Suspension
10-Maintenance Log……………………………………….……………59
11- Declaration of Conformity.……………………………………....... 61
12-Warranty Certificate –Service implementation declaration …….62

Notice originale : Français NT0002 V –p –03/2014
3
1 –Safety Instructions
Before putting into service, please study the operating instructions and respect safety
guidelines!
In these user instructions all hazards and risks to which
operators or other exposed persons are subject to have been
highlighted by this symbol.
Glued onto the spreaders, safety signs indicate
how to use the machine without danger:
Respect for the notices = safety
Standard Usage
The spreader has been designed and
manufactured for the standard usages
described in this manual
Four situations are defined herein: Parking,
loading, transport and spreading (chapter 5)
Nonetheless, a certain number of foreseeable
non-conformity scenarios are questionable
and specifically forbidden. The manufacture
will not be for damages resulting from these
actions.
It is of the utmost importance to respect the
contingency regulations against accidents as
well as the other applicable legislation in
force in terms of safety, health provision in
the workplace and the Highway Code.
The manufacturer waives all liability with
respect to damages caused as a result of an
unauthorised modification of the machine.
General Safety Regulations and
Contingency Plan against Accidents.
1. Definition of the vehicle’s consignment:
before undertaking any actions on the
machine, switch off the engine, release the
hydraulic pressure, apply the parking
brakes (tractor AND trailer) and remove
the keys from the ignition.
2. Prior to starting the tractor's engine, take
care to ensure that the power take-off is
not engaged and that all safety devices
have been equipped and are in perfect
working order.
3. Never disengage or deactivate safety
device. For adjustments, servicing and
maintenance, the procedures described in
the manual must be strictly adhered to
(above all chapters 6/7.
4. It is wholly forbidden to pass under the
vehicle when operational.
5. The machine’s usage is done so entirely at
the responsibility of the driver. The
absence of third parties in the vicinity of
all manoeuvres must be guaranteed.
6. Given the residual risks from collisions or
damage at the spreader apparatus (AND in
its projection area) and that it is
technically impossible to protect it (at the
very least during the working phase=, it
falls under the responsibility of the driver
to ensure that no third parties are present
in the environs when the machine is in
movement.
7. The driver must be fully empowered to
use the machine in the most appropriate
conditions.

Notice originale : Français NT0002 V –p –03/2014
4
2 –Warranty Conditions
In order to benefit fully from the manufacturer’s warranty, please make sure
you follow the maintenance operations and utilisation advice provided in this
manual. Should any problems arise, the user must contact the dealership.
Warranty Conditions:
Our spreaders are guaranteed for parts and labour for one year, counting
from the date the machine is into service.
Under no circumstances can ROLLAND S.A. be held responsible for an
incident arising from the failure to respect these instructions for handling,
servicing or maintenance of the machinery.
The guarantee is valid only for the supply and replacement of defective
parts.
The warranty is invalid and we waive all responsibility in the following
instances:
1°) where the machine has been modified using elements constructed outside
of our workshops or those not manufactured by our distributers without our prior
authorisation.
2°) where the original serial number has been falsified.
3°) where the factory assembled pieces produced by ROLLAND have been
disassembled and replaced by parts of a different origin.
4°) where breakdowns and malfunctions are the result of negligence, misuse,
overloading, including even passengers, the lack of operational knowledge on
the part of the user, or due to the introduction of a foreign body into the machine
during operations or failing to lubricate it properly.
Repairs, modifications or replacement of pieces during the warranty
period cannot extend the duration of the warranty for the materials.
Following the receipt of your vehicle, make sure that this is in all points,
compliant with the technical specifications and that this has not suffered any
damages.
In order to speed up the guarantee implementation process
“THE GUARANTEE IMPLEMENTATION DECLARATION” accompanying
this technical notice must be completed and returned in the month
following delivery.

Notice originale : Français NT0002 V –p –03/2014
5
3 - Presentation of the vehicle
This manual is standard for all ROLLFORCE and ROLLMAX spreaders from the ROLLAND
range. It has been designed with the aim of giving you all the necessary information on the
vehicle that you have just purchased and to get the best from it.
DESCRIPTION :
The spreaders are all fitted with either a “ROLLAND” sturdy suspension beam , or they may
also be fitted with a "ROLLFAST” hydraulic suspension rod.
These are mounted onto a chassis fitted with an adjustable, spring, or hydraulic jib.
Identification :
To know the features of your trailer, please refer to the sticker board attached below the right
front side of your vehicle. A plate with a self-adhesive sticker will also state the total
authorised load weight (TALW) and the empty weight (EW).
A cold stamping (serial number) is fitted under the vehicle's chassis.
This serial number is necessary all warranty exchanges with your dealership or the factory
MAX WEIGHT STICKER
DISCPLATE
PTAC _ _ _ _ kg
PV _ _ _ _ kg

Notice originale : Français NT0002 V –p –03/2014
6
Towed agricultural vehicles are governed by two different regulations:
The Labour Code
The Highway Code
Rolland’s vehicles come supplied with their official documentation and a label containing the
EC conformity stamp. These two documents verify that the two sets of regulations have been
adhered to.
In addition to this label and depending on the options selected, complementary markings
(TALW, hydraulic weighing or on rod gauges, 1,2 or 3 axles, roll-control…).

Notice originale : Français NT0002 V –p –03/2014
7
Sideways View
ROLLFORCE ROLLMAX
Front and rear view
1
Chassis
7
Ro-Ro Transport
2
Front Deck
8
Spiked roller
3
Protective Hood
9
Hatch
4
Front Nose
10
Spreader Frame (2100Kg maxi)
5
Jib
11
Spreader Deck
6
Jib regulator
ROLLFORCE
ROLLMAX

Notice originale : Français NT0002 V –p –03/2014
8
Technology and options available:
Demount Ring
Jibs with 8 hole interfaces allowing for the mounting of several types of rings: flat, swivel,
spoon, DIN).
Rollforce
Jib
Rollmax
Jibs
Swivel ring
(std)
Flat ring
DIN Ring
K80 Spoon Ring

Notice originale : Français NT0002 V –p –03/2014
9
Haulage :
Simple axle
(ROLLFORCE)
Undercarriage
(option on
ROLLMAX
5420, 6325
and7130)
Offset pin bogie
beam (standard
on ROLLMAX
5420, 6325
and7130)
Semi - Tandem
(option on
ROLLFORCE)
Rod Tandem
(option sur
ROLLMAX)
Triple Axle
(standard on
ROLLMAX
8735)
Rollfast
(option on
ROLLMAX)
Direction of Travel

Notice originale : Français NT0002 V –p –03/2014
10
Advancing : There are several types of forward movement, and in each case several of these can be
managed from the junction box in the cabin as well as from the tractor control unit which is always on
standby. See the table below for the current existing combinations : Troubleshooting tractor repairs
(Insulation pump ).
Procedure for carrying out traction repair: 1- Disconnect the push-pull 1 and 2 and push-pull 3 and 4.
2- Connect push-pull 2 and 4 between them with the help
of connector kit K1.
3- Connect push-pull 1 with one with one of the two
troubleshooting connectors on the pressure side of the
tractor distributor.
.
4- Connect the push-pull 3 with one of the two
troubleshooting connectors on the return side of the
tractor distributor.
Power Source
Function
Command
n° d'avance
1) Open tractor :
operates due to the tractor’s
coupling connectors
1) Base:
Forward drive belt solely
Manual adjustment
110
Without display
111
With display
112
With display+DPA
113
2) 2 functions :
With display
Without display
121
With display
122
With display+DPA
123
3) 3 functions :
forward drive belt + hatch
+fume hood
Without display
131
With display
132
With display+DPA
133
2) Pump:
The pump is mechanically
activated using the power take-off
and multiplier located upwind
(during repairs, troubleshooting or
servicing, the coupling elements
may be connected to the traction,
as per the basic diagramme below).
1) Base:
solely with forward drive
belt
Without display
211
With display
212
With display+DPA
213
2) 2 functions :
forward drive belt + hatch
Without display
221
With display
222
With display+DPA
223
3) 3 functions :
forward drive belt + hatch
+fume hood
Without display
231
With display
232
With display+DPA
233
N.B : To carry out this operation in reverse it is necessary to invert P and T1 either push-pulls 1 and 3 on
the tractor.
Flexible repair
kit
Towards tractor
Do not forget to
connect the coupling
kit

Notice originale : Français NT0002 V –p –03/2014
11
Procedure for carrying out traction repair (please refer to traction repair on page 10)
Repair of the distributor in forced mode
Use a screwdriver to force open manually a section of the distributor
(Opening or closing the hood trap, as in the photo)
N.B : A collar is fitted as standard to prevent shifting to LS involuntarily (causing risk
of pump deterioration !!)
Rest on the knurled nut to
perform AR manual
operation
Use an allen key and tighten
the hc screw to empty the
machine manually (manual
repair).
For utilisation in LS mode, connect
the flexible to the opening with the
LS markings, then support and screw
the left knurled nut

Notice originale : Français NT0002 V –p –03/2014
12
This table explains the functions of the elements that comprise the 18 types of forward
motions in use. In the column « forward motions in question>> we have the numbers of the
forward advances used by the item in that line (for example in 122, two forward motions are
used in 121, 122, 123, 221, 222, 223).
Element
Function
Forward motion in
question
Fuel tank
Contains around 80 litres
of oil to power the pump
(1 emptying per year or
every 200 hours’ usage)
Viscosity Index: 46
211, 212, 213, 221, 222,
223, 231, 232, 233
Multiplicator
Provides the impetus to
turn at1000r/min to spin
the pump 3000 tr/min (1
emptying per year or after
every 200 hours’ usage)
Amount : 0.32 litres max
Viscosity Index : 400
211, 212, 213, 221, 222,
223, 231, 232, 233
Pump
Oil fuel pump from the
tank to the distributor with
output rate of 50 l/min to
1000 tr/min (power take-
off)
211, 212, 213, 221, 222,
223, 231, 232, 233
Connector kit K1
This coupling kit allows
for the disconnection from
the regulator and the
pump. This is essential for
its protection.
211, 212, 213, 221, 222,
223, 231, 232, 233
Terminal block
Attaches all the different
sensor threads to a harness
112, 113, 122, 123, 132,
133, 212, 213, 222, 223,
232, 233
Reductor 1/40
Reduces engine speed so
that the belt operates at
working speed.
All models

Notice originale : Français NT0002 V –p –03/2014
13
Element
Function
Stage in question
Hydraulic Engine
Powered by oil, this
maintains the reductor that
supplies the belt. A 160
cm³ engine for simple
drills and two motors of
130 cm³ mounted side by
side for double drills.
All models
Proportional Regulator
Ensures even oil
distribution throughout the
circuit, in proportion to any
given electrical data.
Pressure filter to be
changed annually. This unit
is fitted with two pressure
caps to safeguard emptying
and clearance operations.
111, 112, 113, 211, 212,
213
2 –way distributor
Allows for oil feed for
shock absorbers and hatch
functions.
121, 122, 123, 221, 222,
223
3-way distributor
Allows for oil feed for
tappet and hatch and
tractor funnel functions.
131, 132, 133, 231, 232,
233
Inductive wheel sensor
Gives the distance run with
the spreader in tow.
112, 113, 122, 123, 132,
133, 212, 213, 222, 223,
232, 233
Inductive sensor on the
reductor
Indicate the distance
covered by the shock
absorber and their
condition.
112, 113, 122, 123, 132,
133, 212, 213, 222, 223,
232, 233
Pressure gauge
Inform the user of the oil
pressure within the circuit.
112, 113, 122, 123, 132,
133, 212, 213, 222, 223,
232, 233
Manual regulator
Ensure even distribution
of oil throughout the
circuit. This is adjusted by
a rotary selector.
110

Notice originale : Français NT0002 V –p –03/2014
14
The different control units
Element
Function
Forward
movement
Controls the fanbelt and regulates
its speed, 2 setting ranges (hare /
tortoise) for optimal operational
capacity.
Clearance is achieved through the
tractor’s distributor command
box.
111, 211
Controls the fanbelt and regulates
its speed, 2 setting ranges (hare /
tortoise) for optimal operational
capacity. The screen displays the
belt speed, the hydraulic pressure,
and the distance travelled by the
belt.Clearance is achieved through
the tractor’s distributor command
box.
112, 212
On top of the basic functions, it
can invert the belt’s direction,
give the order for the hatch (2
functions) to be opened and also
the escape funnel TCE (3
functions).
121, 131, 221, 231
On top of the basic functions, it
can invert the belt’s direction,
give the order for the hatch (2
functions) to be opened and also
the escape funnel TCE (3
functions).The screen postss the
speeds, hydraulic pressure and the
distance covered by the belt.
122, 132, 222, 232
3-Way command box with FP
(Forward Proportional Debit).
The screen posts the speeds,
hydraulic pressure and the
distance covered by the belt.
113, 123, 133, 213,
223, 233
Axle lock:

Notice originale : Français NT0002 V –p –03/2014
15
The axle follows the vehicle and operates by displacement caused by turns, and should be
blocked whilst travelling (at average or high speeds) and in reverse.
The auto-pilot axle is an axle controll cylinder located on the vehicle’s jib, a closed
hydraulic circuit with nitrogen-filled spheres to keep up the pressure. A tread needs to be
placed on the tractor. It is to be noted that Rolland auto-pilots can be turned into axles
when attached to a treadless tractor since the blocking cylinders of the axle lock have been
preserved. The advantage of this system is that heat doesn’t need to enter at the point of
driving motion, whether forwards or in reverse.
Rolling mechanisms with 1 auto-piloted axle mainly comprise of the following element:
Component
Quantity
Illustration
Hydraulic block 1 axle
1
Rolling mechanisms with 2 auto-piloted axles are mainly composed of the following
elements :
Component
Quantity
Illustration
Hydraulic block 1
2
Do not connect the shut-off tube on the axle lock when pipe is in auto-pilot
mode.

Notice originale : Français NT0002 V –p –03/2014
16
Hydraulic flaps:
Hydraulic flaps are available as an option with models V17, V21 and V25 for C10 and
ROLLFORCE spreaders. Thjese flaps facilitate spreading operations on the borders of land
plots. It is possible to have a left or right-sided flap, or even one on both sides.
Weighing:
ROLLFORCE and ROLLMAX spreaders are able to be fitted with weighing
systems.Weighing information is shown on the jib or axle mounted sensors.Weighing
information is then caught on the weighing control box. The data is then recorded in the box
by client or plot of land worked. Over and above the weighing system, the user may instal
data evaluation software which enables client or plot management (data memory up to 65
000 weighings).A compact, on-board battery operated printer which issues a ticket giving
information on load weight, cumulative totals, by client or land plot is also available as an
option.
Weighing box
Weighing sensor
Data analysis software
Compact printer

Notice originale : Français NT0002 V –p –03/2014
17
FPD (Foward Proportional Decrease) :
Please note :
As soon as the box is correctly wired, you may go ahead and use the product as
follows :
-Press the ON/OFF switch (1) to the ON position.
Characteristics :
-Aluminium box
(Dimensions : l = 160mm, L= 110mm, P= 40mm)
- IP 67.
- Protected against reverse polarity. -
Beam base IP68.
- Screen 2*12 characters with blue backlight.
- Printing option.
- Command 6 solenoid valves (3A max)
Printer
(Optional)
Prininting plate
(Optional)

Notice originale : Français NT0002 V –p –03/2014
18
Normal display :
The machine’s speed of travel is given in kilometres per hour and emanates from the sensor attached to
the machine’s wheel.
Fan belt speed is given in metres per hour and originates from the sensor mounted on the belt (on the
reducer).
FPD mode : allows for the setting up of machine tuning guides
This function is activated by pressing on button « » (5).The setting up of parameters is carried out
by touch « » (4) which in turn causes the cursor to move. Cursor position signals the number which will be
modified on touching « + » (3) et « - » (2).
After set-up of first adjustment, press on 1st, press by touch « » (5) to change menu and save the
set-up .
The adjustable set ups are :
Normal Menu
Operation
A page which permits spreader speed
reference configurations in FPD mode.
A page which permits previously returned belt
speed configurations.
A page which indicates the number of
hectares worked since the spreader set off ;
this counter can be reset to zero by pressing
touch (4) .
Page signalling the distance travelled by the
bbelt in metres since the spreader was
brought into service.
A page which indicates the number of hectares
worked since the spreader set off; this counter cannot
be reset to zero.
A page which allows the length of the
spread to ber configured, this set-up is
important in calculating surface areas
worked.

Notice originale : Français NT0002 V –p –03/2014
19
Manual mode:
Manual mode is activated by changeover from the 2nd switch (6) to
« manual », but there is then no speed adjustment. The hydraulic block can be
varied by the intervention potentiometer which will alter the current which
can alter the current from 0 to the highest factory setting.
Ticket Printing (Option) :
Stop mode :
Stop mode is reached by centring the switch (6), which causes a ceasing of adjustment.
A page which allows the configuration of
the system reactivity index, this setting is to
be adjusted in order to avoid belt pumping.
A page indicating work time (belt
deployment time) since it was last reset to at
zero. Resetting to zero can be done by
pressing touch for this counter (4) .
Page indicating working time (total belt
operating time) since being brought into
service. It is not possible to reset this counter
to zero.
Client :
------------------------
Surface : 10.0 Ha
Time : 0010 H 25min
P 20) Press on the pushbutton which is to be found on the upper FPD lid
in order to give ticket print-off order.
The printing settings are as follows:
-The surface area worked since last zero reset of the part-hour
counter.
-Time in service since last reset to zero on the hour gauge
Page which indicates in metres the total belt
travel distances since it was last reset to
zero by pressing on touch(4)
-It isn’t possible to print a ticket if you’re on the main
page.

Notice originale : Français NT0002 V –p –03/2014
20
4- Commissioning
Trailer hitching :
Hitched trailer speeds should not exceed 25 km/h or 40 km/h (according to model). The
attachment is assured via a standardised ring (all hitching types can be secured by using a
bracket, flange and pin).
PROCEDURE
Ensure that the tractor used can tolerate the weight burden
imposed by the trailer.
After hitching the trailer to the tractor, check that the cup plate is
properly positioned and secured in the locked -on position.
Before commissioning, check that all applicable points have been
greased (see the maintenance chapter)
Adjustable tractor hitching (automatic bracket or collector) :
Reverse slowly, with tow bar lowered and ring and tow pole married up.
Once in position, raise the towing apparatus (the ring will automatically find its own level).
Lockt he device in place.
Re-introduce the hydraulic or mechanical stand.
Attelage tracteur fixe (ringbolts, tow plate, hitch bar) :
Place the stand in position (ring above the ringplates or at tow plate level, or at the
hitching bar level).
Adjust hitching devices (tractor and machine) :
the ringbolt and then move down ring (the ring will automatically find
its own level).
Tow plate
Hitch bar
Manoeuvre tractor into position where necessary
Place the stand support in position and lock the stand.
Connect all hydraulic cables (tyres optional).
Wire up the lighting.
Tyres :
At the time of vehicle commission, it is vital to check and adjust pressure in line with the
tyre’s load-bearing capacity and the conditions under which the vehicle is to be used.
OR
OR
This manual suits for next models
1
Table of contents
Other ROLLAND Spreader manuals
Popular Spreader manuals by other brands

Craftsman
Craftsman 486.243231 owner's manual
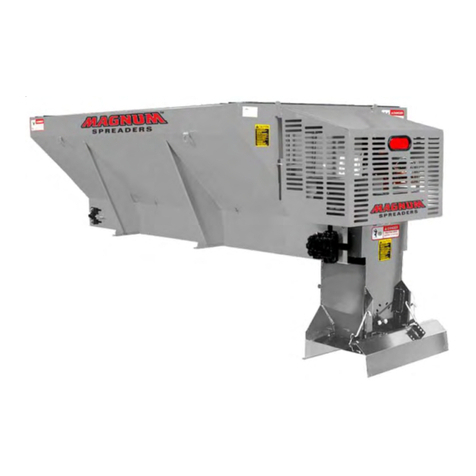
Magnum
Magnum V-BOX PV Series Installation and operating instruction manual
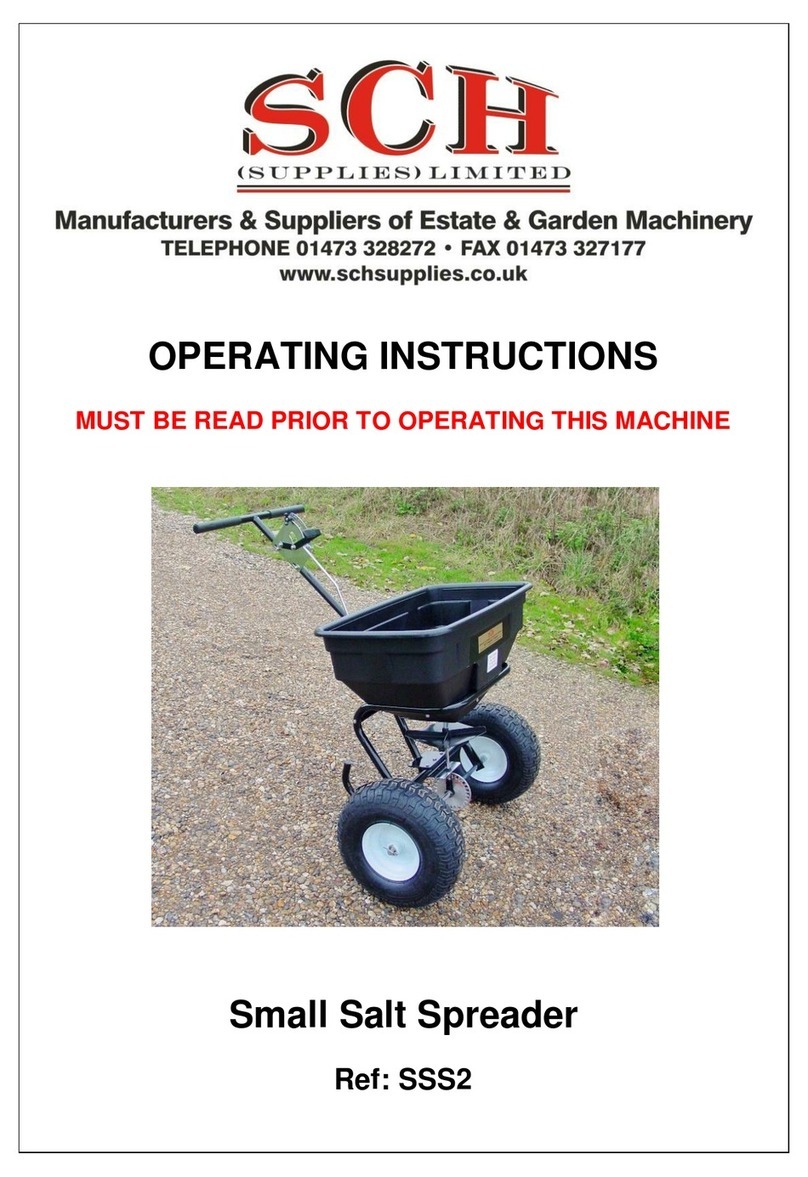
SCH
SCH SSS2 operating instructions
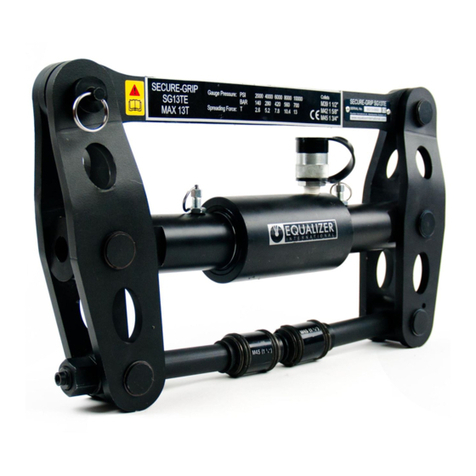
Equalizer International
Equalizer International SG13TE Operator's instruction manual
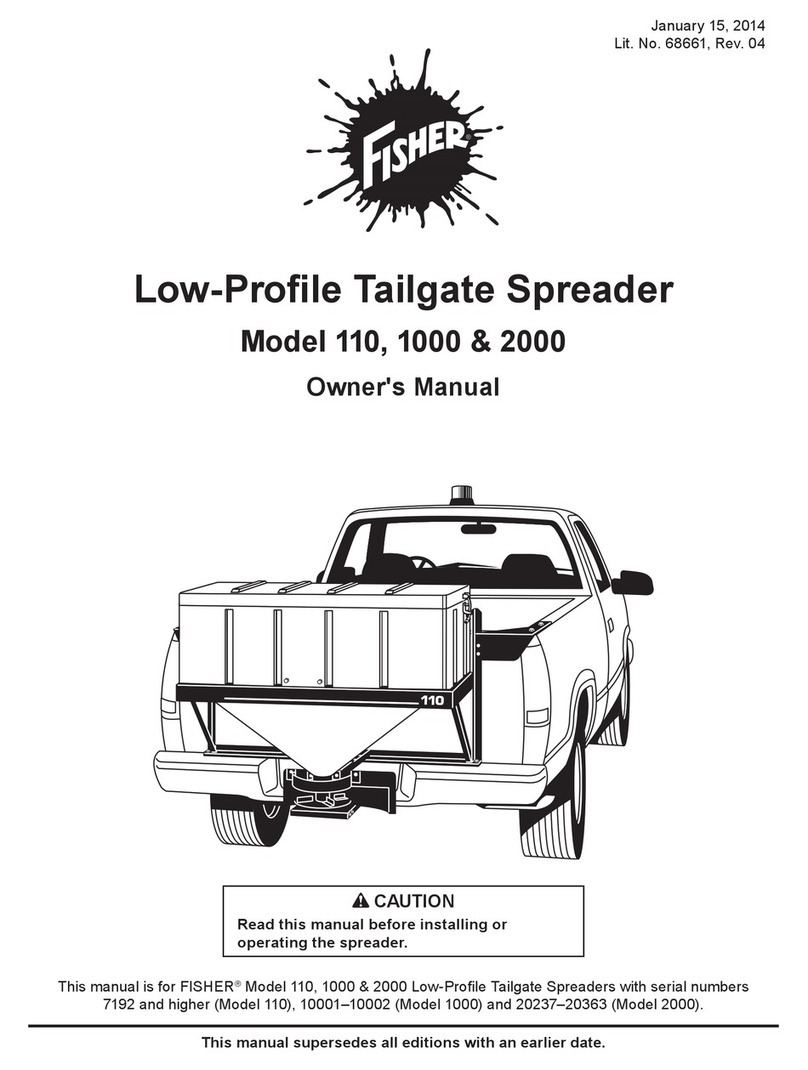
Fisher
Fisher 110 owner's manual
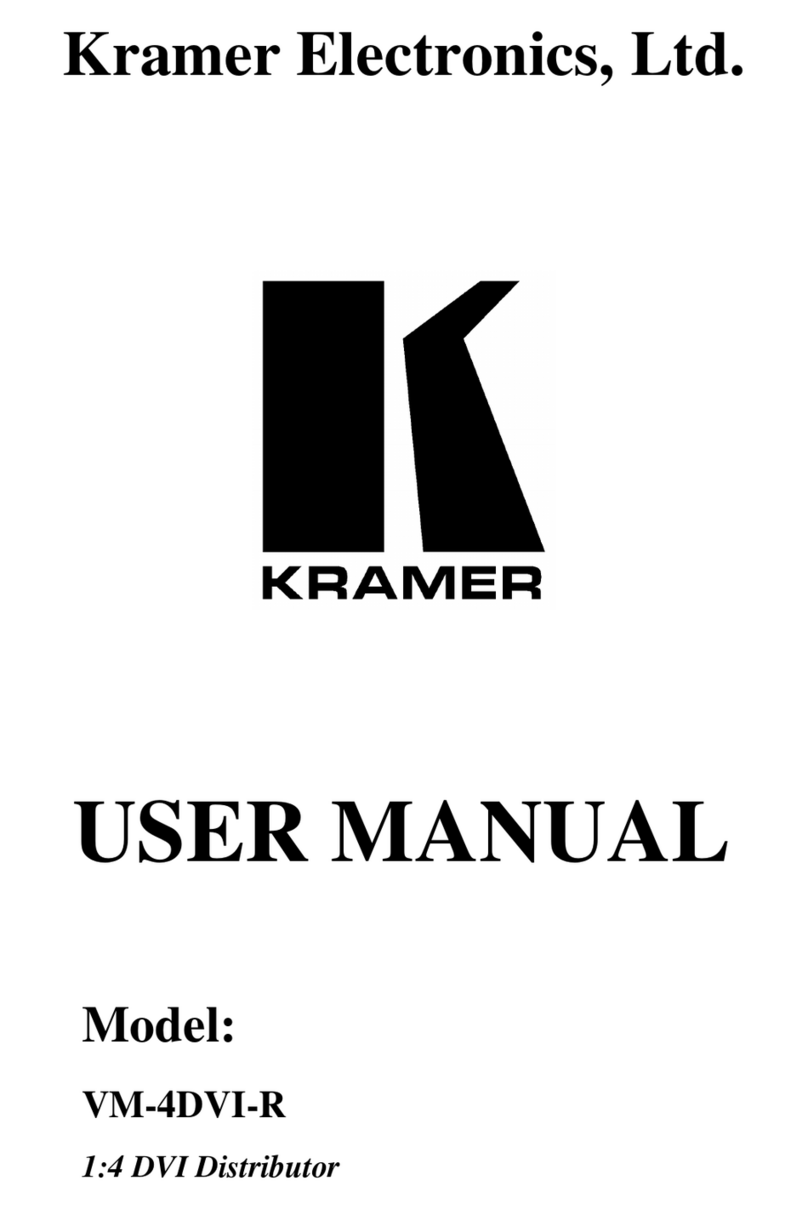
Kramer
Kramer VM-4DVI-R user manual
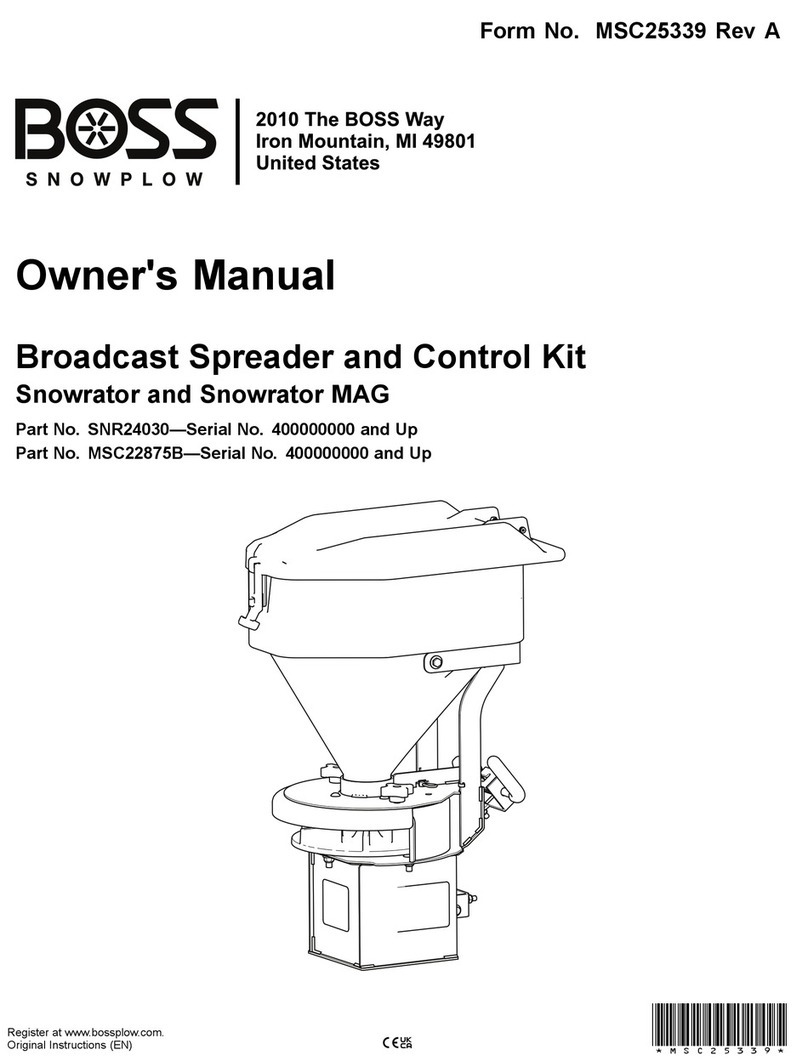
Boss Snowplow
Boss Snowplow MSC22875B owner's manual

Pik Rite
Pik Rite Hydra-Pull HP-500 Operation and parts manual

CynkoMet
CynkoMet N-233 Series Instructions for Use and Operation
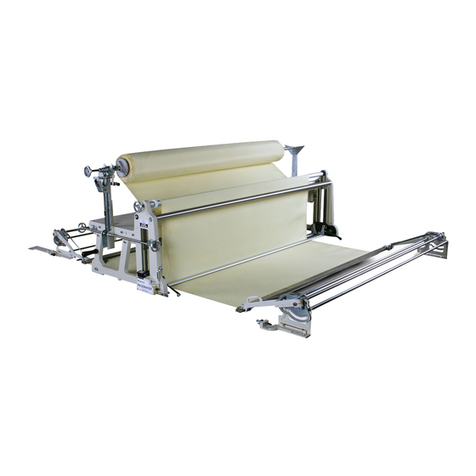
EASTMAN
EASTMAN PACEMAKER Instruction Manual & Illustrated Parts List
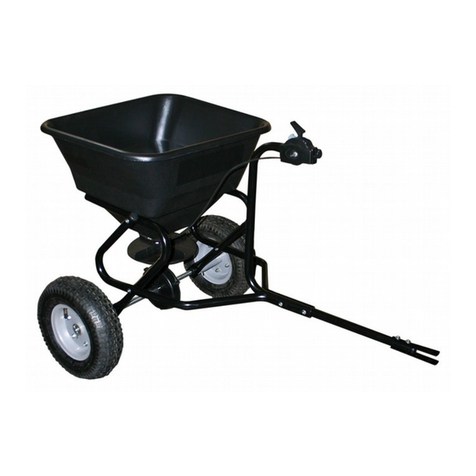
WilTec
WilTec 50144 Operation manual
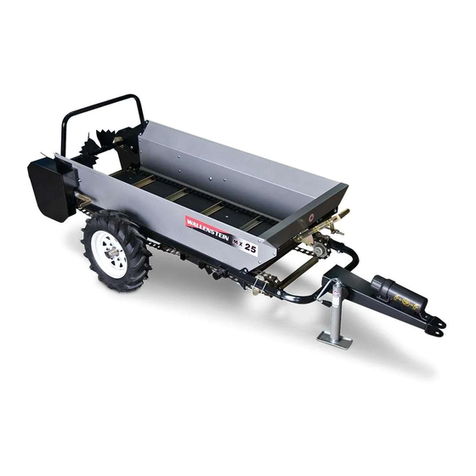
Wallenstein
Wallenstein MX Series Operator's manual