ROLLAND ROLLTWIN Operation instructions

Original instruction : French NT0002 V –h –
03/2012
1
Dear Customer,
You have just purchased a ROLLAND Spreader.
We appreciate the trust you place in us.
The Spreaders by ROLLAND were designed to make the most of
spreading techniques. They result from our technology and our
experience in this field.
This manual should be considered as part of your Rolltwin or
Rollmax Spreader.
For proper use, and to exploit all the capabilities of your Spreader,
we recommend that you carefully read and follow all instructions in
this manual.
The proper function and longevity of your spreader depends on
it as well as your safety and that of others.
Keep this instruction manual so that you can consult it in due
course. It must always accompany the spreader, even in case of
resale.
Non-compliance with the said instructions indemnifies the
manufacturer and the dealer of all liability.
We reserve the right to make any changes to our products at
any time we deem useful without obligation to modify products
previously delivered or on order. We also reserve the right to change
without notice models that are defined in our catalogues, brochures
or on our website.
Yours faithfully.
Z.A des Landes
29800 TREFLEVENEZ - FRANCE
Tél. : 00 33 (0)2 98 85 13 40
Fax : 00 33 (0)2 98 21 38 15
www.remorquerolland.com

Original instruction : French NT0002 V –h –
03/2012
2
Summary
1-Safety instructions 3
2-Conditions of warranty 4
3-Presentation of the vehicle 5
-Areas of use
-Vehicle identification
-Technology and options
4-Commissioning (PDI) 16
5-Normal use and instructions 25
-parking
-loading
-transport
-spreading
6-Settings 28
-Drawbar
7-Care and maintenance 29
-Braking systems
-undercarriage
-Cleaning/lubrication
-Adjusting the bed tension
-Adjusting the steering axle
-Maintenance of controller and hydraulic unit
- Wearing parts
-Maintenance of the beater frames
-Wheels and tyres
-Lighting
8-Assembly 42
-Revolving light flashing beacons
-Equipment
9-Annexes 48
-Hydraulic drawbar
-Passive suspension
-Hydropneumatic suspension (active suspension)
10-Maintenance logbook 58
11-Declaration of Conformity 60
12-Certificate of warranty –Declaration of commissioning61

Original instruction : French NT0002 V –h –
03/2012
3
1-Safety instructions
Before commissioning, study the instructions and follow the safety guidelines!
In this user guide we have marked with this symbol all hazards or
risks that operators are subject or exposed to.
Signs and security stickers attached to the spreader show you that it is
safe to use the machine: Respecting the instructions = safety
A. Normal use
The spreader is designed and manufactured for normal use as described in this
manual.
Four situations are thereby defined as: parking, loading, transporting and spreading
(Chapter 5).
All uses other than specified are considered non-compliant. However, a number of
predictable non-conform situations are discussed and specifically prohibited. The
manufacturer is not liable for resulting damages.
We must respect the rules of accident prevention and other legal safety
regulations, occupational medicine and the Highway Code.
The manufacturer accepts no liability for damage resulting from an unauthorised
modification of the machine.
B. General safety regulations and accident prevention.
a. Vehicle shutdown: Before
working on the machine, stop the
engine, release the hydraulic
pressure engage the brakes
(tractor and trailer) and remove the
ignition key.
b. Before starting the tractor
engine, ensure that the PTO is not
engaged, that all safety devices
are fitted and in good condition.
c. Never deregulate or
override safety devices. For
settings, care and maintenance,
follow the procedures described in
the manual (especially chapter 6/7)
d. It is strictly forbidden to go
under the vehicle when in
operation.
e. The use of the machine
remains the sole responsibility of
the driver. He must ensure the
absence of third parties in the
proximity during any manoeuvre.
f. Given the residual risk of
shock or damage to the spreading
device (AND its projection area)
and that it is technically impossible
to protect (at least in the work
phase), it is the responsibility of
the driver of the machine to ensure
the absence of a third party in this
area when the machine is in
motion.
g. The driver must be in
possession of all necessary means
to use the machine under optimum
conditions.

Original instruction : French NT0002 V –h –
03/2012
4
h.
2- Conditions of warranty
To take full advantage of the manufacturer's warranty, ensure compliance with
maintenance and usage advice given in this manual. In case of problems users
should contact their dealer.
Conditions of warranty :
Spreaders lifts are covered against defects in parts and workmanship for one
year from the date of commissioning.
In no event can ROLLAND SA be held responsible for an incident due to a
failure to comply with instructions for use, safety or maintenance.
The warranty covers only the provision of defective parts.
The guarantee is withdrawn and we disclaim any liability :
-When the machine has been transformed by elements built outside of our
workshops or those of our distributors without our permission.
-When the serial number of origin has been falsified
-If the ROLLAND factory fitted parts have been replaced by parts of another
origin.
-If the damage is due to any negligence, improper use, overloading, even
temporarily, to the inexperience of the user, to the penetration of a foreign
body in an element of the machine during operation or from non-lubrication.
Repair, modification or replacement of parts during the warranty period cannot
have the effect of extending the warranty period of equipment.
Upon receipt of your trailer, make sure it is fully compliant with the technical
specifications and that it has suffered no damage.
To actuate the warranty process
"CERTIFICATE OF WARRANTY - DECLARATION OF COMMISSIONING"
accompanying this data sheet must be completed and returned within one month of
delivery.

Original instruction : French NT0002 V –h –03/2012
5
3 –Presentation of the vehicle
This manual is common to all spreaders in the ROLLAND range. It was designed to
give you all necessary information about the vehicle you have just purchased and to
allow you to get the get the most out of it.
DESCRIPTION :
The spreaders are equipped with either a single axle, rocker, tandem or tri axle.
They can also be equipped with the "ROLLFAST" hydraulic suspension.
They are mounted on a chassis with a drawbar, sprung or hydraulically adjustable.
Identification :
For full features of your trailer, refer to the conformity plate attached to the front right
of your vehicle. In addition, a tare plate sticker specifies the permissible gross
weight (GVWR) and unladen weight (UW). A stamped (serial number) is carried on
the vehicle chassis
This serial number is required for any exchange warranty with your dealership or the
factory
Tare sticker
Conformity plate
PTAC _ _ _ _ kg
PV _ _ _ _ kg

Original instruction : French NT0002 V –h –03/2012
6
Drawn agricultural vehicles fall under two distinct regulations :
The highway code
The labour code
Rolland vehicles come with a sheet crossed out with a red bar and a notice
containing a statement of compliance. These two documents show that the two
regulations have been met.
In addition to these instructions, depending on options chosen, additional
instructions (DASP, hydraulic weighing or on gauges 1.2 or 3 axles, Rollcontrol ...),
will be given to you at the start by your dealer.

Original instruction : French NT0002 V –h –03/2012
7
Side view
ROLLTWIN ROLLMAX
ROLLMAX
Front and rear view
1
Body
7
Running gear
2
Front panel
8
Beaters
3
Protection cover
9
Slurry door
4
Hose arrier
10
Spreader frame (2100Kg maxi)
5
Drawbar
11
Spreader table
6
Drawbar adjustment
ROLLTWIN
ROLLMAX

Original instruction : French NT0002 V –h –03/2012
8
Technology and options available :
Rings :
Welded flat ring
Removable ring
Drawbars with 8 holes interface allowing several types of ring to be fitted (flat,
rotating, spoon, DIN)
Hydraulic drawbar only on "ROLLMAX"
Welded rotating ring

Original instruction : French NT0002 V –h –03/2012
9
Running gear :
Single axle
Bogey
Rocker with
offset shaft
Tandem with
tie rods
Tridem
Rollfast
Driving direction

Original instruction : French NT0002 V –h –03/2012
10
Bed control: There are several types of floor controls, in each, several functions can be
managed from the electrical control box in the cabin in addition to the tractor control valve that is
always available. Here in this table are the various available combinations: Wiring diagram for
tractor troubleshooting (independent hydraulics).
Procedure for carrying out a tractor repair: 1-
Disconnect push-pull 1 + 2 and push-pull 3 + 4
1- Connect push-pull 2 + 4 together with connection kit K1
2- Connect push-pull 1 pressure side of tractor distributor
3- Connecte push-pull 3 to reflux side of tractor distributor
Floor control
Function
Command
n° feed
1) Directly from the tractor:
operates through
hoses connected to the
tractor
1) Basic:
Bed only
manual control
110
no display
111
with display
112
with display + DPA
113
2) 2 functions :
Bed + slurry door
no display
121
with display
122
with display + DPA
123
3) 3 functions :
Bed + slurry door +
hood
no display
131
with display
132
with display + DPA
133
2) Pump:
The pump is operated
mechanically from the PTO and
the gearbox located upstream
(during maintenance or repair,
the hoses can be connected to
the tractor as in the diagram
here below)
1) Basic:
Bed only
no display
211
with display
212
with display + DPA
213
2) 2 functions :
Bed + slurry door
no display
221
with display
222
with display + DPA
223
3) 3 functions :
Bed + slurry door + hood
no display
231
with display
232
with display + DPA
233
to tractor
Do not forget to
plug in this
connector set K1
N.B : To reverse the direction, P and T1 must be inverted, i.e. the push-pull 1 and 3 on the tractor.
1
3
2
4

Original instruction : French NT0002 V –h –03/2012
11
This table explains the function of the components that make up the 18 existing
types of feeds. In the column "relevant system" there are numbers that use the line
advances (for example a two section distributor is used in the feeds 121, 122, 123,
221, 222, 223).
Element
Function
Relevant system
Reservoir
Contains about 80litres of oil
to power the pump (1 oil
change / year or every 200
hours)
Viscosity index: 46
211, 212, 213, 221,
222, 223, 231, 232, 233
Gear box
Allows the PTO running
at 1000 rpm to drive the
pump at 3000 rpm (1 oil
change / year or every
200 hours)
Qty: 0.3 litres max
Viscosity index: 400
211, 212, 213, 221,
222, 223, 231, 232, 233
Pump
Pumps the oil from the
reservoir for distribution
at a rate of 50 l / min at
1000 rpm (PTO)
211, 212, 213, 221,
222, 223, 231, 232, 233
Connector set K1
This set allows
connection and
disconnection of the
pump controller. It is
imperative for its
protection
211, 212, 213, 221,
222,
223, 231, 232, 233
Terminal
Connects all the various
sensors wires into one
harness
112, 113, 122, 123,
132, 133, 212, 213,
222, 223, 232, 233
Réducteur 1/40
Reduces the motor
speed so that the belt
runs at feed rate.
All models

Original instruction : French NT0002 V –h –03/2012
12
Element
Function
Relevant system
Hydraulic motor
Supplied with oil, it
drives the gear which
drives the bed. One
motor 160 cm ³ for the
single drives and two
motors 130 cm³
connected in parallel for
the double drives.
All models
Proportional controller
Ensures the distribution
of oil in the circuit in
proportion to a given
electrical transfer.
Pressure filter to be
changed yearly. This
block is equipped with
two pressure relief
valves for secure
drainage and cleansing.
All electrically controlled
models
Distributor dual function
Allows the oil supply for
the belt and for the hatch
functions
121, 122, 123, 221, 222,
223
Distributor tri-function
Allows the oil supply for
the belt, hatch and hood
functions
131, 132, 133, 231, 232,
233
Wheel inductive sensor
Gives the distance
travelled by the spreader
112, 113, 122, 123, 132,
133, 212, 213, 222, 223,
232, 233
Gearbox inductive
sensor
Indicates the distance
traveled by the bed and
the speed of the bed
112, 113, 122, 123, 132,
133, 212, 213, 222, 223,
232, 233
Pressure sensor
Informs the user of the
oil pressure in the circuit.
112, 113, 122, 123, 132,
133, 212, 213, 222, 223,
232, 233
Manual control
Ensures the distribution
of oil in the circuit. The
adjustment is made with
the rotary selector.
110

Original instruction : French NT0002 V –h –03/2012
13
The various control boxes
Element
Function
Relevant feed
Controls the bed and regulates
its speed, two setting ranges
(hare / tortoise) for optimum
accuracy. The driving is done
via the tractor control valve
111, 211
Controls the bed and regulates
its speed, two setting ranges
(hare / turtle) for optimum
accuracy. The screen displays
bed speed, hydraulic pressure,
and the distance traveled by
the bed. The clearing is done
via the tractor control valve
112, 212
In addition to basic functions, it
can reverse the direction of the
bed, control the opening of the
hatch (2 functions) and the
operation of the TCE hood (3
functions).
121, 131, 221, 231
In addition to basic functions, it
can reverse the direction of the
bed, control the opening of the
hatch (2 functions) and the
operation of the TCE hood (3
functions). The screen displays
belt speed, hydraulic pressure,
and the distance traveled by
the bed.
122, 132, 222, 232
3 function control unit and DPA
(Output proportional to the
progress). The screen displays
bed speed, hydraulic pressure,
the distance travelled by the
bed.
113, 123, 133,
213, 223, 233

Original instruction : French NT0002 V –h –03/2012
14
Steering axle :
The steering axle follows the vehicle and works from the movement caused by
the curves, it must be locked on the highway (at medium or high speed) and in
reverse.
The self-steering axle is a follower controlled by a cylinder located on the
drawbar of the vehicle, it is a closed hydraulic circuit with accumulators to
maintain pressure. It requires the installation of a clevis on the tractor. Note that
the self-steering Rolland axle can become a follower axle when a tractor is
without a clevis because locking cylinders of the follower axle have been
retained. The advantage of this system is that the driver does not need to
intervene when driving, neither forward nor in reverse.
The running gear with 1 self-steering axle are composed mainly of the following
element :
Component
Quantity
Illustration
Hydraulic block 1 axle
1
The running gear with 2 self-steering axles are composed mainly of the following
element :
Component
Quantity
Illustration
Hydraulic block 1
2
Do not connect the follower axle's locking hose during a self-steering
operation.

Original instruction : French NT0002 V –h –03/2012
15
Hydraulic headland kits:
Hydraulic headland kits are available as options on the frames C8, C11, C12, C22,
C13, C23 for the ROLLTWIN spreaders and C10 for the ROLLMAX spreaders.
These headland kits allow spreading at the edge of the plot. It is possible to have
headland kits on the left or on the right or one on each side.
Weighing :
It is possible to equip the ROLLTWIN and ROLLMAX spreaders with a weighing
system. Weight information is detected by sensors on the drawbar and the axle. The
data is then memorised in the weight conrol box per client or plot. In addition to the
weighing system the user can have a data processing software for managing
customers or plots (storage up to 65,000 weighings). Also optionally available is a
compact printer equipped with a battery rechargeable at the mains that can publish
tickets with weight totals, per customer or plot.
Weight control box
Weight sensor
Data processing software
Compact printer

Original instruction : French NT0002 V –h –03/2012
16
4 –Commissioning (PDI)
Vehicle coupling system :
The coupling may not exceed the speed of 32 km/h or 20 mph road speed. The
connection is provided by a standard ring (all types of couplings can be used with
hook, ring bolt or spoon coupling).
PROCEDURE
. Make sure that the tractor used can carry the nominal load of
the trailer.
. After coupling the trailer to the tractor, make sure the skid is
raised properly and in the resting position, securely locked.
.Check all lubrication points before the first use (see chapter
Maintenance)
Adjustable tractor coupling(automatic hook or pick-up coupling):
• Approach slowly in reverse, lower hitch to coincide with the ring.
• Once in place, raise the hitch (the ring will position itself).
• Lock the device.
• Raise the hydraulic or mechanical skid.
Fixed tractor coupling (ring bolt, autohitch, drawbar) :
Place the prop in position (ring above the ring bolt coupling or drawbar).
Approach to adjust coupling devices (tractor and machine): :
the ring bolt and lower the ring (it will position itself).
Pick up hitch
The drawbar
Manoeuver the tractor if necessary
Lock and raise the skid.
Connect all hydraulic hoses (pneumatic optional).
Connect the lights.
Tyres :
On commissioning the vehicle, it is imperative that the tyre pressures be
determined and adjusted according to the load on the tyres and the actual
conditions of use.
OR
OR

Original instruction : French NT0002 V –h –03/2012
17
Connecting the pressure outlets :
. The connections must be made with the engine shutdown,
hydraulic pressure released and ignition key removed
Hose marking
Function
Hose marking
Function
Brakes
Bed pressure
(DE)
Bed reverse
(DE)
Close hood
(DE)
Open hood
(DE)
Load transfer
(SE)
Lock steering
(SE)
Lock steering
(DE)
Slurry door open
(DE)
Close slurry door
(DE)
Extend hydraulic
drawbar cylinder
(DE)
Retract hydraulic
drawbar cylinder
(DE)
Pressure
hydropneumatic
suspension
(DE or SE)
Return
hydropneumatic
suspension
(DE or reflux)
Pressure passive
suspension (SE)
Passive
suspension drain
(Reflux)
*SE : single acting valve (pressure /
float)
*DE : dual acting valve

Original instruction : French NT0002 V –h –03/2012
18
Brake system :
The spreaders are equipped with three brake systems, each one assuring a specific
function.
When parking, use the mechanical hand brake. During the transport it is the
hydraulic brake that is used. The third system is a safety device for in case the
coupling breaks (a cord between the hand brake and a fixed point on the tractor).
Connect the safety cord in case of breakage of the coupling that operates the
parking brake. Check at the start of every season, the tension of the cable
connecting to the brake rods.
PROCEDURE
. Any trailer with a GVWR more than 1.5 tons is obligatorily
equipped with the braking device. It must be coupled to the
tractor braking system.
Hydraulic braking system :
Install the red hose (4) on the pressure outlet "BRAKES" on the tractor.
Ensure the proper functioning of control and check connections for leaks. Brake
pressure: 100 to 130 bar.
Reference
Element
Function
1
Brake drum
Ensures braking
2
Brake cylinders
Actuates the brake rods during transport
3
Brake cables
Is the link between the hand brake and
the brake rods
4
Hose (connected to the tractor)
Supplies the brake cylinders with oil
5
Parking brake
Hand brake
6
Coupling failure cord (attached to a
fixed point on the tractor)
Engages the handbrake should the
coupling break

Original instruction : French NT0002 V –h –03/2012
19
Pneumatic braking system
Element
Function
Illustration
Emergency relay valve
(VRU)
Ensuring the service brake and
the automatic braking of the
trailer in case of coupling
breakage or pressure drop in the
supply line
Static corrector
(optional)
Adjusts the brake pressure, that
is the brake force, depending on
the load condition of the vehicle.
Relay valve (optional)
Allows the control circuit to
control the permanent circuit.
Shunt valve
Allows the release of the service
brake of the trailer after initiation
of automatic brake caused by the
disconnection of the hoses.
Reservoir + purge
Compressed air tank. The purge
allows the moisture in the circuit
to be evacuated.
Coupling control
controler
(yellow)
Permits the braking between
tractor and trailer
Coupling Feed
(red)
Ensuring the continuous supply
between the tractor and trailer.
Brake chamber
Ensuring the service brake
system with its front part and the
parking brake with its rear part for
the dual spring cylinder.
Pressure outlet
Used to control the pressure in
the system
N.B : The brake can also be mixed (hybrid pneumatic/ hydraulic fitting)
(mounting for 40 kmh prohibited)
Or
Or

Original instruction : French NT0002 V –h –03/2012
20
Example of air braking system on 2 axles (40 kmh)
Installation of the drive shaft :
PROCEDURE
. All drive shafts must be equipped with safety guards in good
condition.
. Deteriorated guards must be replaced immediately
. Do not forget to install guards and to restrain them with
chains.
. Never operate a PTO without the foreseen guards.
. Wearing loose clothing may be the cause of accidents.
.During the first use, it may be necessary to adjust the length of the drive
shaft. To do this :
Ensure the correct length of the drive shaft tubes.
Tube can be damaged if the turning circle is too severe
Interlock the tubes a minimum of 4500 mm.
On transmissions there are several types of security, safety shear bolt or torque
clutches cams. In case of a shear bolt, it should be replaced by a bolt of the same
type and same quality as the original. Replacement by a stronger bolt will damage
the vehicle.
N.B : for commissioning, operation and maintenance of the transmission
(primary and secondary), refer to the manufacturer's specific instruction
manuals provided with the machine.
T
R
A
C
T
O
R
Or
Or
1 Emergency relay
2 Fixed correcteur
3 Relay valve
4 Brake valve
5 Reservoir
6 Feed
7 Control
8 Pressure
9 Brake cylinders
This manual suits for next models
1
Table of contents
Other ROLLAND Spreader manuals
Popular Spreader manuals by other brands
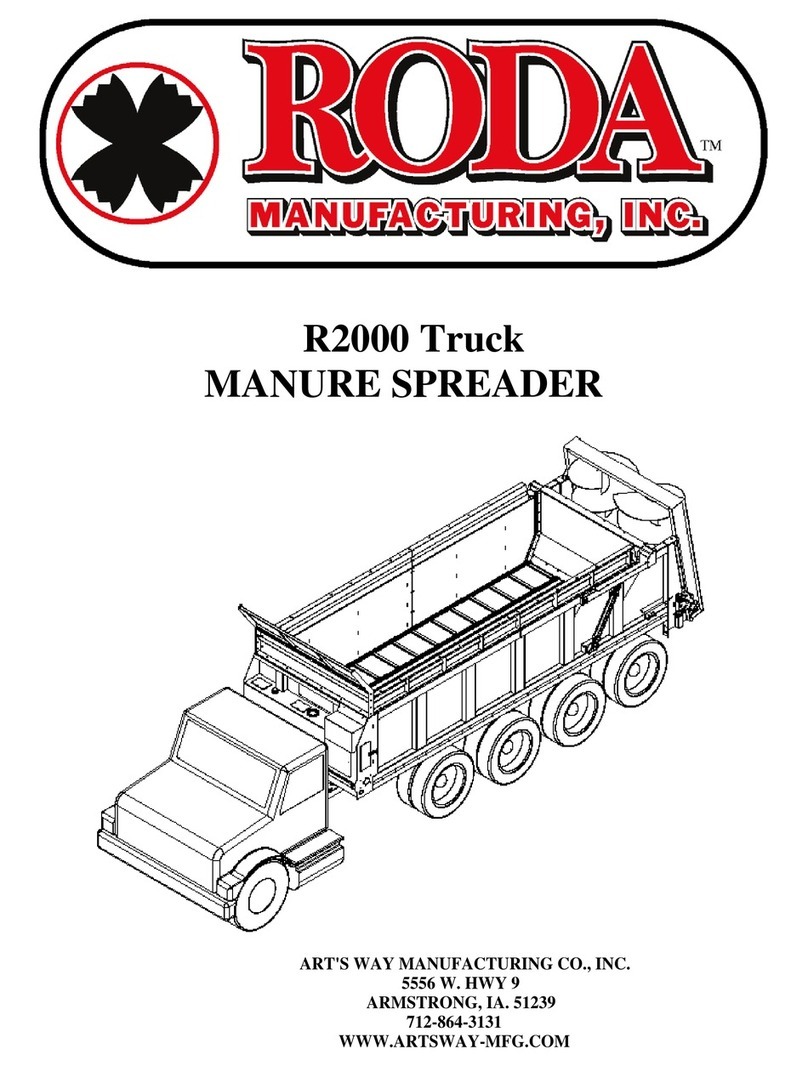
Roda
Roda R2000 Truck manual

Western
Western ICE BREAKER Hopper Spreader installation instructions

Cub Cadet
Cub Cadet 125 lb Spreader & 10 Gallon Sprayer Operator's manual
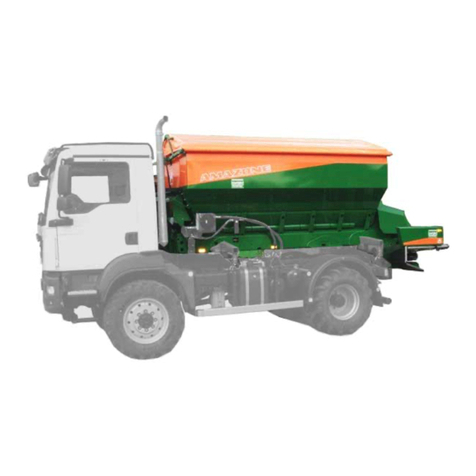
Amazone
Amazone ZG-B 8200 Truck operating manual
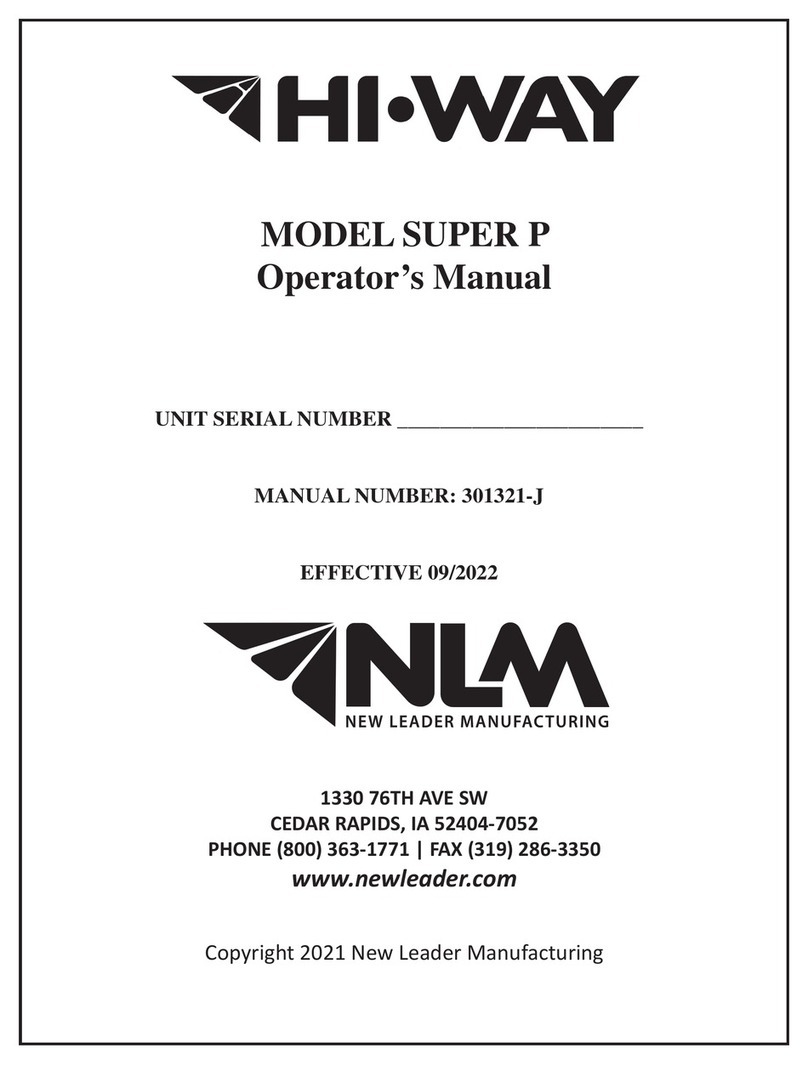
Hi-Way
Hi-Way SUPER P Operator's manual

Western
Western Striker 98810 installation instructions

Gardena
Gardena Comfort 500 Assembly instructions
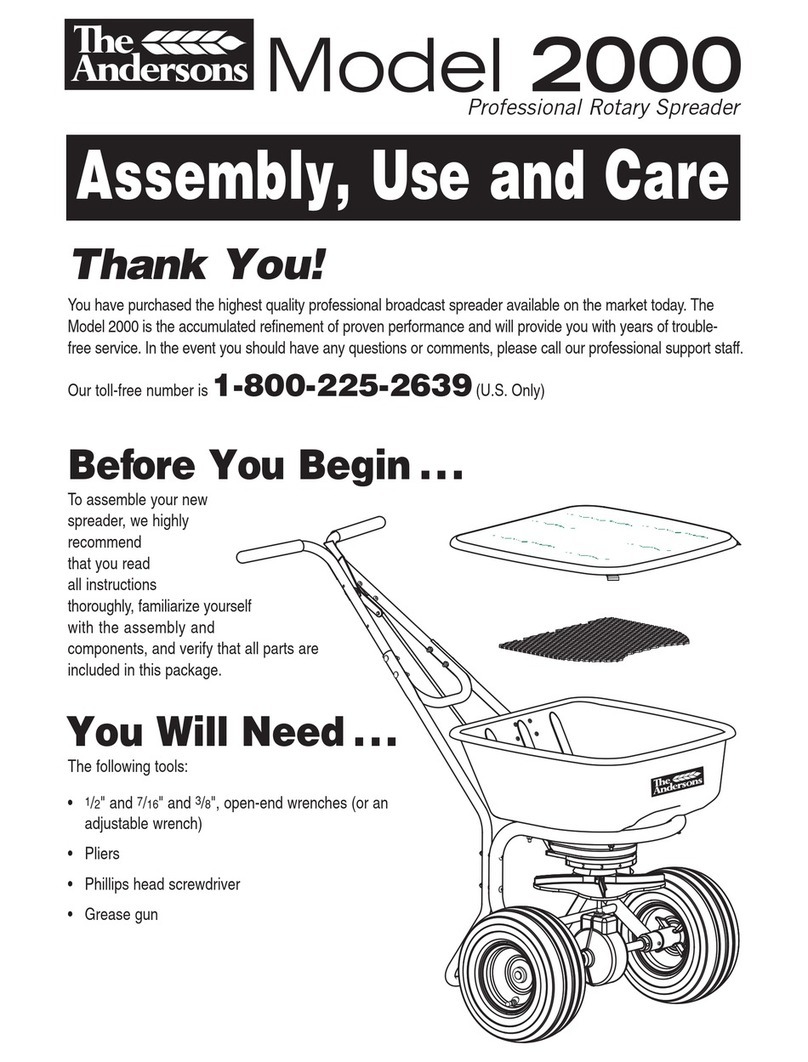
Andersons
Andersons Model2000 manual
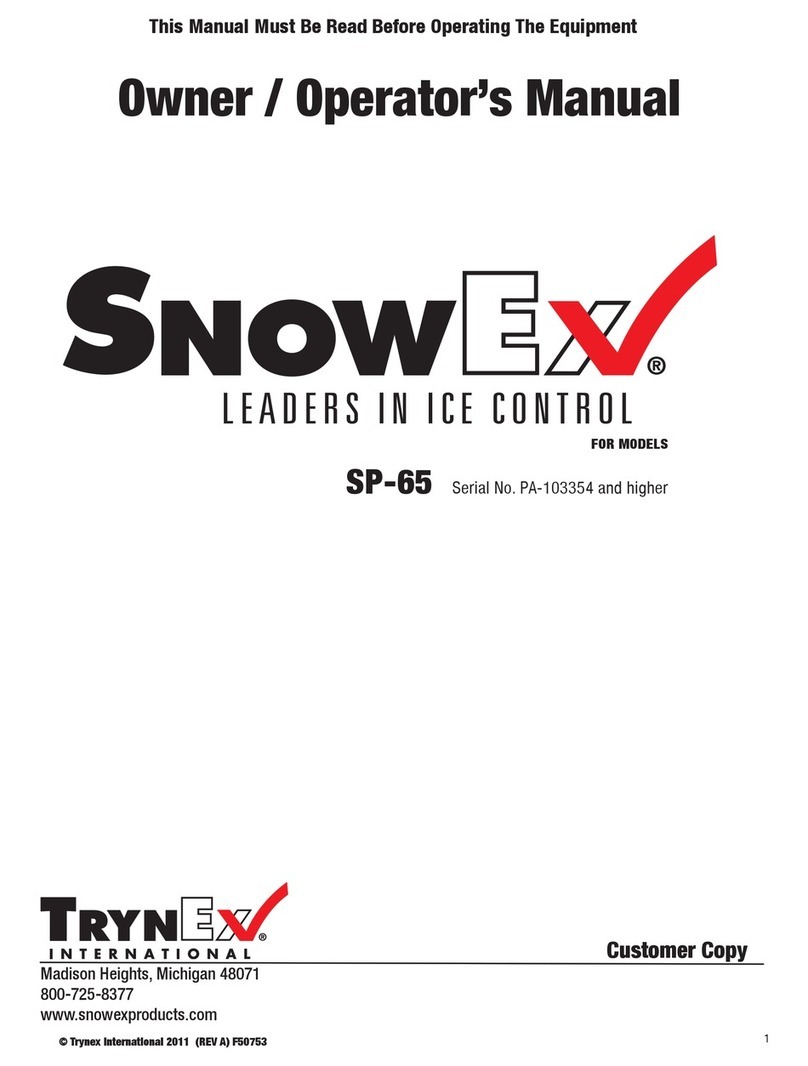
Trynex
Trynex SnowEx SP-65 Owner's/operator's manual
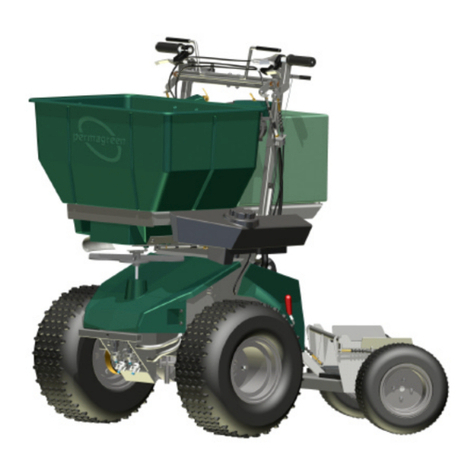
PermaGreen Supreme
PermaGreen Supreme MAGNUM SmartSteer C3C 2009 Operator's manual

HYDRA-PULL
HYDRA-PULL Pik Rite HP 380 Operation and parts manual
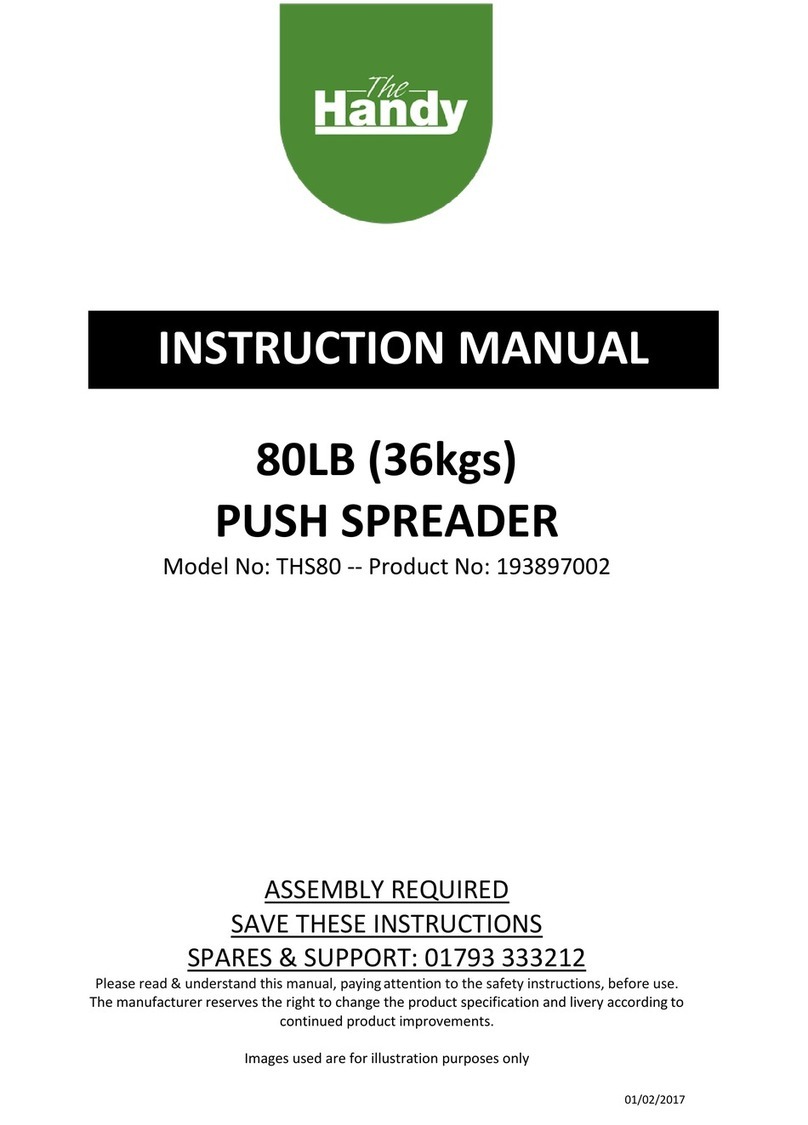
The Handy
The Handy THS80 instruction manual