RS S81 User manual

Refrigerating Specialties Division 1
ISO 9001-2000 CERTIFIED
S81,S82 Solenoid Valve March 2006
Port 9mm (3/8”) to 66mm (2-5/8”)
FEATURES
•Pilot Operated
•Interchangeable Capacity Cartridges
•Low Pressure Drop
•Manual Opening Stem
•All Service From The Top
•Sweat-in-place Without Disassembly
•Maximum Opening Pressure Difference (MOPD):20.7
bar (300 psig)
•Design Pressure (MRP): 31.0 bar (450 psig)
•Molded Class “H” Coil Construction
•Pilot Light and QD Coil Assemblies available
S81, S82
iron-bodied solenoid valve with brazed copper couplings
is suitable for most common refrigerants, certain oils
and other fluids approved for use in refrigeration. This
valve may be opened by means of a manual opening
stem in case of electrical power failure or for servicing.
ORDERING GUIDE
Like the R/S line of A8 pressure regulators, the
new S8 solenoids are available in a number of port and
connection size combinations. When ordering, please
indicate both the port and connection size required
along with the coil voltage.
PRINCIPLES OF OPERATION
The Type S81 is a pilot operated solenoid. In
Figure 1, the valve is shown in its closed position with
the solenoid coil de-energized and the plunger and
piston plug in the seated position. When the solenoid
coil is energized, it forms a magnetic field that pulls up
the plunger, lifting it off its seat. Upward motion of the
plunger permits entrance of the fluid from the valve inlet
through the adapter and down through the pilot port to
the top of the piston. This forces the piston downward
and pushes the main port plug open, thereby permitting
flow of the refrigerant through the valve. The closing
spring meanwhile is held in a compressed position. De-
energizing the solenoid coil permits the spring-assisted
plunger to reseat, stopping the flow through the pilot
port. Bleed-off, through the bleed hole in the piston,
decreases the pressure above the piston and allows
the closing spring to force the main port plug upward
into a closed position to stop the flow. The pressure
difference across the valve, acting up on the area of the
valve seat, plus the force of the closing spring, holds the
mainport plug in a tightly closed position.
Fig 1
DESCRIPTION
The new S8 series of commercial solenoids
were developed by the Refrigerating Specialties Divi-
sion of Parker Hannifin as a versatile, all purpose valve
in a wide range of port and connection sizes. With car-
tridge (port) sizes available up to 66mm (2-5/8”), S8 so-
lenoids are capable of handling greater flow rates than
competitive valves with similar non-flanged body styles.
In addition, this unique design incorporates the same
concept of cartridge interchangeability as found inthe
A8 series of regulators. This innovative design actually
utilizes the same capacity cartridges (and valve bodies)
as those used in the A8 regulator series, as well as the
same solenoid actuator, coil, and coil housing. Capac-
ity cartridges can be changed by simply unscrewing the
valve’s four adapter bolts to facilitate the removal of the
adapter and cartridge assemblies. With this flexible line
of commercial solenoids now supplementing the exist-
ing line of A8 regulators, a wide variety of control valves
designed for commercial applications are now available
from a single reliable source. This ductile
050415
32-00A

Refrigerating Specialties Division 2
MANUAL OPENING STEM
The manual opening stem on the Type S81 is for the
purpose of opening the valve without energizing the
solenoid coil. Refer to the exploded view and the parts
list for location of the stem and other related parts. For
access to the stem, the seal cap must be removed.
This must be done with caution as refrigerant may be
trapped inside the seal cap. Manual opening is ac-
complished by turning the stem counter clockwise until
stopped. To reset for automatic operation, turn the stem
clockwise until seated.
INSTALLATION
The solenoid valve can be mounted in a hori-
zontal or vertical line with the flow in the direction of the
arrow on the valve body. Protect the inside of the sole-
noid valve from moisture, dirt and chips during installa-
tion. These valves may be soldered into the line without
disassembly. A wet cloth should be wrapped around the
valve and the soldering flame should be directed away
from the valve body. The S81 solenoid valve must be
installed with the arrow on the valve body in the direc-
tion of flow through the valve. If the valve is backwards,
the flow will not be stopped when the valve is electrically
de-energized. Like all Solenoid Valves, the S81can stop
flow only in the direction from normal inlet to normal
outlet (as shown by the arrow on the body). If reversal
of pressure occurs in the system so the outlet pressure
exceeds the inlet pressure the plug will be blown away
from its seat and reverse flow will occur. If a system has
this type of pressure reversal, a Refrigerating Special-
ties Division Type CK4A check valve, in series with the
solenoid valve, will prevent reverse flow. (The CK4A
must be installed downstream of the solenoid to avoid
trapping liquid.)
ELECTRICAL
The Refrigerating Specialties Division
molded water resistant Class “H” solenoid coil is
designed for long life and powerful opening force.
The standard coil housing meets NEMA 3R and4
requirements. This sealed construction can with-
stand direct contact with moisture and ice. By
definition, Class “H” coil construction will permit coil
temperatures, as measured by resistance method,
as high as 185°C (366°F). Final coil temperatures
are a function of both liquid and ambient tem-
peratures. The higher fluid temperatures require
lower ambient temperatures so the maximum coil
temperature is not exceeded. Conversely, low flu-
id temperatures permit high ambient temperatures.
A solenoid coil should never be energized except
when mounted on its corresponding solenoid tube.
The molded Class “H” coil is available from stock
with most standard voltages. However, are avail
avail ble for other voltages and frequencies, as
well as direct current. Coils are also available as
transformer type with a 6 volt secondary winding
for use with the Refrigerating Specialties Division
Pilot Light Assembly PLT2. See Bulletin No. 60-20.
The solenoid coil must be connected
to electrical line with volts and Hertz same as
stamped on coil. The supply circuits must be prop-
erly sized to give adequate voltage at the coil leads
when other electrical equipment is operating. The
coil is designed to operate with line voltage from
85% to 110% of rated coil voltage. Operating with
a coil voltage above or below these limits may
result in coil burnout. Also, operating with a coil
voltage below the limit will definitely result in lower-
ing the valve’s maximum opening pressure differ-
ential. Power consumption during normal operation
will be 10.2 watts or less.
SERVICE POINTERS
1. Failure to Open: (a) Coil is of incorrectly high
voltage. See “Electrical”. Check voltage printed on
the coil. (b) Line voltage is abnormally low. See
“Electrical”. Check line voltage at coil leads with a
voltmeter. (c) Failure to electrically energize. Check
control circuit. (d) Pressure difference across valve
is too high. The S81 and S82 will open against a
maximum pressure difference across the valve of
21 bar (300 psig). (e) Solenoid
Coil is burned out. See “Electrical”, and replace
with proper coil. (f) Plunger Assembly is stick-
ing. To disassemble the S81for inspection of
internal parts (after pumping out the system as
required); disconnect power source to Solenoid
Coil, remove(number 36) Solenoid Operator As-
sembly, then Adapter. Remove every trace of dirt
from Adapter and Cartridge Assembly. Thoroughly
clean all parts and reassemble using alight film
of refrigerant oil. 2. Failure to Close: (a) Electrical
control circuit is not opening properly. Check wiring
and controls. (b) There are chips or dirt on the Pilot
Seat or the Piston Plug Seat, preventing proper
seating. Disassemble and clean Valve as outlined
in 1 (f) above.(c) Piston Plug Seat or Pilot Seat
may be worn or damaged and therefore leaking.
Disassemble and clean Valve as outlined in 1 (f)
above. If any of these parts need replacing, it is
advisable to replace using the proper replacement kit.
(d) Manual Opening Stem is turned all or partly out and
permitting flow through the valve. 3. Leakage Through
Valve: See (2) above

Refrigerating Specialties Division 3
S82 S81
S82 S81
Repair Kits for S81 & S82 Solenoid Valves Coil & Hsg Kit for S81 & S82
Item # Description
S81
3/8” thru 1-3/8”
S82
1-5/8” thru 2-5/8”
6Bolt Package 204677 204676 120/60,110/50 202940
13,14,19,20,36,37 Adaptor Assy 204671 204670 240/60,220/50 202941
14,17,17A,18 Cartridge Kit(3/8”) 202712 N/A 480/60,440/50 202943
14,17,17A,18 Cartridge Kit(5/8”) 202711 N/A 24/60 202944
14,17,17A,18 Cartridge Kit(7/8”) 202710 N/A 240/50 202945
14,17,17A,18 Cartridge Kit(1-1/8”) 202709 N/A 208/60 202942
14,17,17A,18 Cartridge Kit(1-3/8”) 202708 N/A 120/6/60 202946
14,17,17A,18,26,30 Cartridge Kit(1-5/8”) N/A 203811 208/6/60 2020947
14,17,17A,18,26,30 Cartridge Kit(2-1/8”) N/A 203812 240/6/60 202948
14,17,17A,18,26,30 Cartridge Kit(2-5/8”) N/A 203813 Q/D 240/60,220/50 203730
14,17A,18,26 Piston/Plug Kit N/A 203823 Q/D 240/50 203734
14,17A,18,26,27,28 Piston Kit N/A 203824
36,37,38
Solenoid Operator
Kit 202700

Parker Hannifin Corporation Refrigerating Specialties Division
2445 South 25th. Avenue Broadview, IL 60155-3891
Telephone: (708) 681-6300 Fax: (708) 681-6306
4
WARRANTY
All Refrigerating Specialties Products are warranted
against defect in workmanship and materials for a
period of one year from date of shipment from the fac-
tory. This warranty is in force only when products are
properly installed, maintained and operated in use and
service as specifically stated in Refrigerating Specialties
Catalogs or Bulletins for normal refrigeration applica-
tions, unless otherwise approved in writing by Refrig-
erating Specialties Division. Defective products, or
parts thereof,returned to the factory with transportation
charges prepaid and found to be defective by factory
inspection will be replaced or repaired at Refrigerating
Specialties’ option, free of charge, F.O.B. factory.
Warranty does not cover products which have
been altered or repaired in the field; damaged in
transit,or have suffered accidents, misuse, or abuse.
Products
disabled by dirt, or other foreign substances will not be
considered defective. THE EXPRESS WARRANTY SET
FORTH ABOVE CONSTITUTES THE ONLY WARRANTY
APPLICABLE TO REFRIGERATING SPECIALTIES
PRODUCTS, AND IS IN LIEUOF ALL OTHER WAR-
RANTIES, EXPRESS OR IMPLIED,WRITTEN OR ORAL,
INCLUDING ANY WARRANTY OFMERCHANTABIL-
ITY, OR FITNESS FOR A PARTICULARPURPOSE. No
employee, agent, dealer or other person is authorized to
give any warranties on behalf of Refrigerating Special-
ties, nor to assume, for Refrigerating Specialties, any
other liability in connection with any of its products.
SAFE OPERATION (See Bulletin RS-
BCV)
People doing any work on a refrigeration system must
be qualified and completely familiar with the system
and the valves involved, or all other precautions will be
meaningless. This includes reading and understanding
pertinent product bulletins and the current Bulletin RSB
prior to installation or servicing work.
S81 S82
S81 S82
Bolt Diameter Valve Size Torque
1/4”(6mm) 3/8”-2-5/8” 8 ft lb(1.1mkg)
5/16”(8mm) 1-5/8”-2-5/8” 12 ftlb(1.7mkg)
Jam Nut 1-5/8”-2-5/8” 8 ft lb(1.1mkg)
Solenoid
Operator all 6 ft lb(.8mkg)
Type S81 S82
Connection
Size
7/8” 1-1/8” 1-3/8” 1-5/8” 2-1/8” 1-5/8” 2-1/8” 2-5/8”
22mm 28mm 35mm 42mm 54mm 42mm 54mm 67mm
A 9.6(244) 9.6(244) 9.4(236) 9.9(251) 11.1(282) 11(279) 12(305) 13.5(343)
B 4.8(122) 4.8(122) 4.7(119) 5(127) 5.6(142) 5.9(149) 6.4(162) 7.1(181)
C 0.8(20) 0.9(23) 1(25) 1.1(28) 1.2(30) 1.1(28) 1.4(36) 1.7(44)
D 5.5(140) 5.5(140) 5.5(140) 5.5(140) 5.5(140) 7.2(183) 7.2(183) 7.2(183)
E 6.9(175) 6.9(175) 6.9(175) 6.9(175) 6.9(175) 9.4(239) 9.4(239) 9.4(239)
This manual suits for next models
1
Other RS Control Unit manuals
Popular Control Unit manuals by other brands
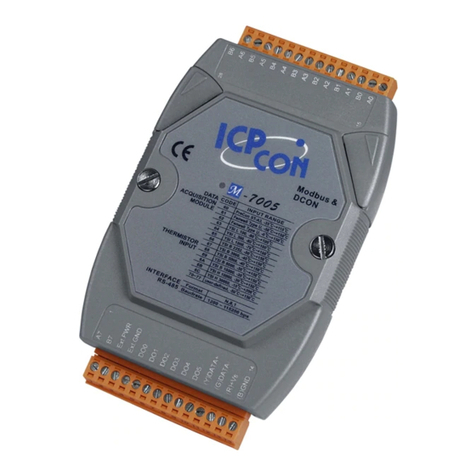
ICP DAS USA
ICP DAS USA M-7002 quick start guide
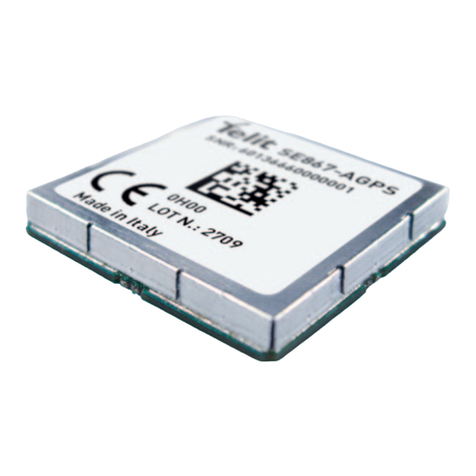
Telit Wireless Solutions
Telit Wireless Solutions SE867-AGPS user guide
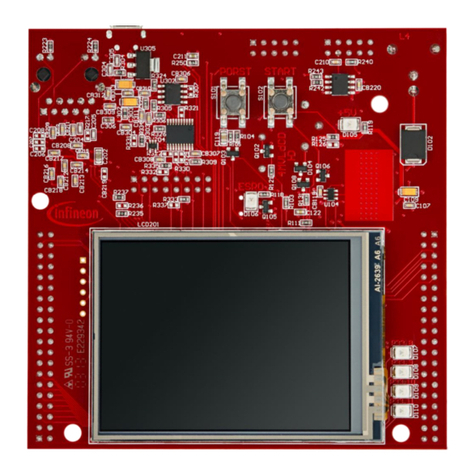
Infineon
Infineon STM Interrupt 1 manual
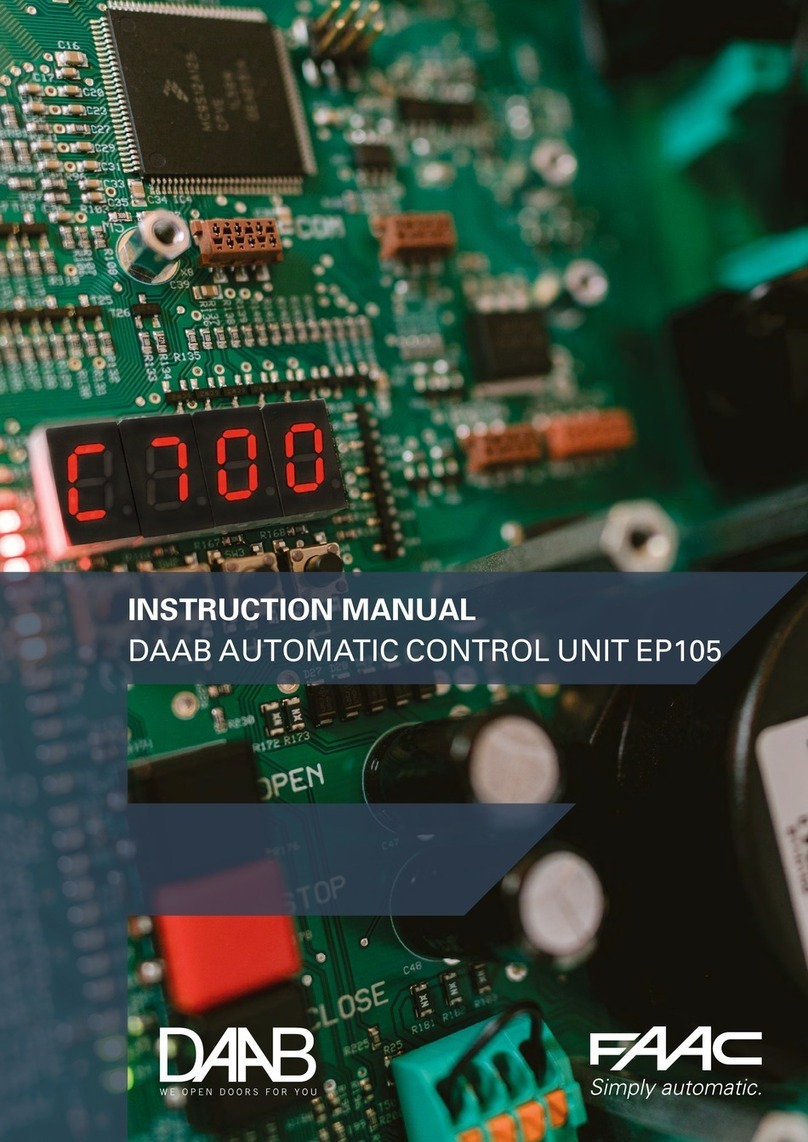
FAAC
FAAC DAAB EP105 instruction manual
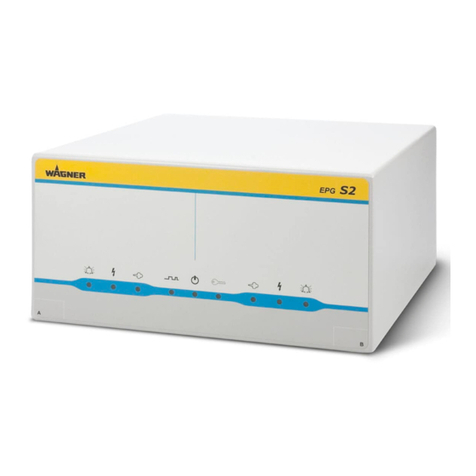
WAGNER
WAGNER EPG S2 Translation of the original operating manual
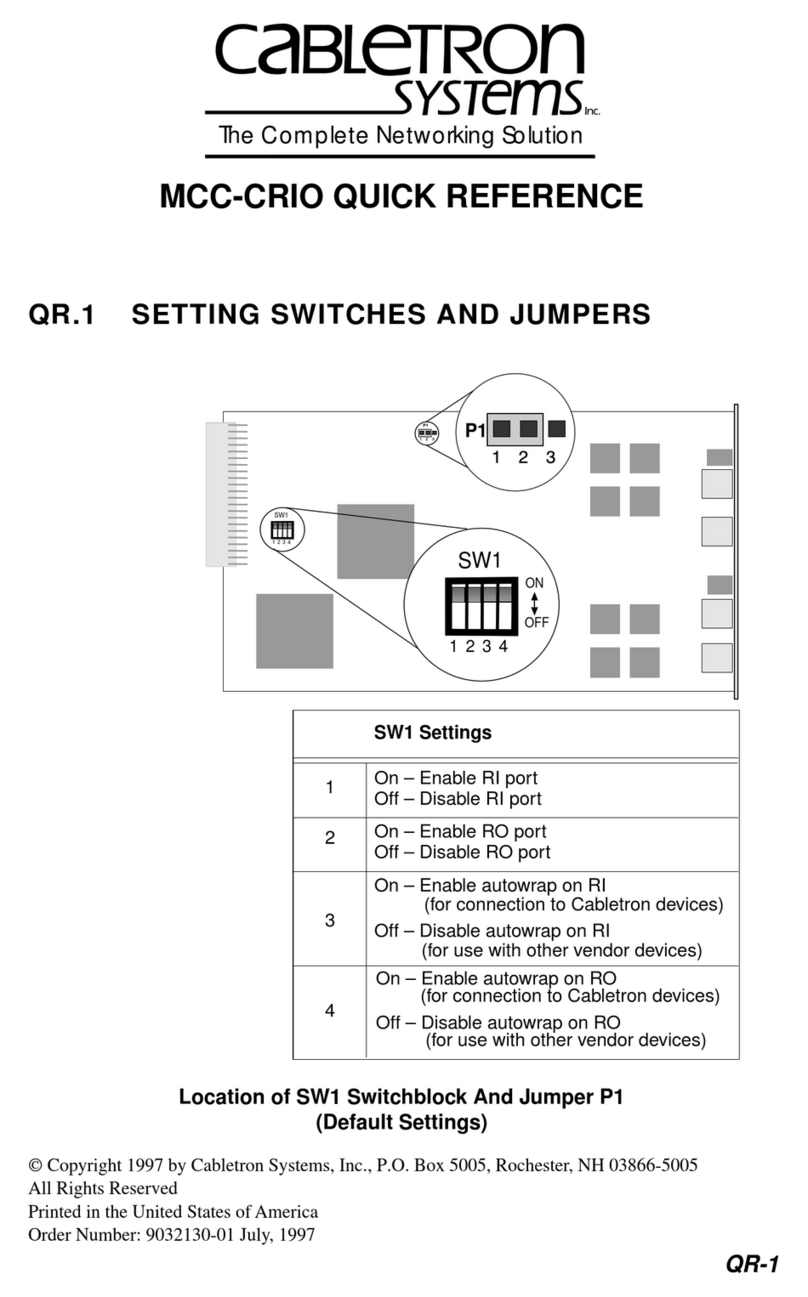
Cabletron Systems
Cabletron Systems MCC-CRIO quick reference