FAAC DAAB EP105 User manual

INSTRUCTION MANUAL
DAAB AUTOMATIC CONTROL UNIT EP105

INSTRUCTION MANUAL DAAB AUTOMATIC CONTROL UNIT EP105
2Revision 3
Contents
EC Declaration of Conformity (original version).............................................................................................4
Declaration of performance............................................................................................................................4
Safety ...............................................................................................................................................................5
Safety classification........................................................................................................................................5
Operation..........................................................................................................................................................6
General ...........................................................................................................................................................6
Service and maintenance................................................................................................................................6
Resetting/replacing tripped fuses...................................................................................................................6
Connection.......................................................................................................................................................7
Safety..............................................................................................................................................................7
Installation .....................................................................................................................................................7
High current....................................................................................................................................................7
Motors.............................................................................................................................................................7
Description of the EP105.................................................................................................................................9
General ...........................................................................................................................................................9
Intended use ...................................................................................................................................................9
Identification...................................................................................................................................................9
Reference documentation ...............................................................................................................................9
Disposal of electronic equipment....................................................................................................................9
Instruction manual .........................................................................................................................................9
Installing the EP105 PCB.................................................................................................................................11
Authorisation ..................................................................................................................................................11
Enclosure ........................................................................................................................................................11
Installing the PCB...........................................................................................................................................11
Connecting a safety edge................................................................................................................................12
Connecting safety edges and photocells.........................................................................................................12
Connecting an encoder (electronic limit switch) .............................................................................................13
Connecting a mechanical limit switch (microswitch) .....................................................................................13
Connecting timer control limit switches..........................................................................................................13
Conguring the EP105 .....................................................................................................................................14
General ...........................................................................................................................................................14
Readout of parameters in the EP105 ..............................................................................................................14
Setting parameters in the EP105 ....................................................................................................................14
Locked settings...............................................................................................................................................15
Configuration channels C700 - C712..............................................................................................................15
Message channel C904...................................................................................................................................15
Display channel C999 .....................................................................................................................................15
Signal list .......................................................................................................................................................16
Low current .....................................................................................................................................................16
Indications......................................................................................................................................................17
Applications......................................................................................................................................................18
Folding doors ..................................................................................................................................................18
Sliding doors/sliding gates .............................................................................................................................18
Up-and-over doors ..........................................................................................................................................18
Swing gates ....................................................................................................................................................18
Barriers...........................................................................................................................................................18
Quick guide to commissioning of swing gate..................................................................................................19
Conditions.......................................................................................................................................................19
Commissioning of drive unit 1 ........................................................................................................................19
Commissioning of drive unit 2 ........................................................................................................................20

INSTRUCTION MANUAL DAAB AUTOMATIC CONTROL UNIT EP105
3
Revision 3
Commissioning.................................................................................................................................................21
Safety..............................................................................................................................................................21
Stop circuit .....................................................................................................................................................21
Frequency converter ........................................................................................................................................21
Limit switches.................................................................................................................................................22
Direction of rotation of motors ........................................................................................................................23
Setting of motor protection .............................................................................................................................23
Type of power supply .......................................................................................................................................23
External protection units.................................................................................................................................24
Load guard......................................................................................................................................................25
Safety edges ...................................................................................................................................................26
Input for photocell...........................................................................................................................................28
Limited running time ......................................................................................................................................28
Checking LED indications ...............................................................................................................................28
Pulse mode and hold-to-run mode..................................................................................................................29
Checking safety functions...............................................................................................................................29
Setting electric motor braking.........................................................................................................................29
Programmable inputs, P channels ..................................................................................................................30
Automatic closing ..........................................................................................................................................30
Run-on time with mechanical limit switches..................................................................................................31
Run-on with encoder.......................................................................................................................................32
Reverse ...........................................................................................................................................................32
Functions using add-in cards..........................................................................................................................32
Channel list ......................................................................................................................................................33
General, C-channels .......................................................................................................................................33
Limit switch, L-channels.................................................................................................................................44
Programmable inputs, P channels ..................................................................................................................46
Error messages in display and in the error code list in channel C903 ..........................................................53
Messages in display and in the error code list in channel C903....................................................................56
Troubleshooting ...............................................................................................................................................56
Resetting/replacing tripped fuses...................................................................................................................57
Notes: ...............................................................................................................................................................58
Notes: ...............................................................................................................................................................59

INSTRUCTION MANUAL DAAB AUTOMATIC CONTROL UNIT EP105
4Revision 3
EC Declaration of Conformity (original version)
Manufacturer
FAAC Nordic AB
Box 125, 284 22 Perstorp, Sweden
Person authorised to compile the technical documentation
Ulf Ivarsson, FAAC Nordic AB, Box 125, 284 22 Perstorp, Sweden
General description and type designation
Automatic control unit for doors, gates or barriers: EP105-1, EP105-2
We hereby declare that the EP105 automatic control unit meets the relevant requirements of Machinery Directive
2006/42/EC, EMC Directive 2014/30/EU, Low Voltage Directive 2014/35/EU, RoHS Directive 2011/65/EU
including (EU)2015/863 and Construction Products Regulation EU 305/2011.
The automatic control unit EP105-1, EP105-2 is, where applicable, compliant with the following harmonised standards:
• SS-EN 13241+A2:2016 Industrial, commercial, garage doors and gates. Product standard, performance characteristics
• SS-EN 13849-1:2016 Safety of machinery. Safety-related parts of control systems – Part 1: General principles for
design.
• SS-EN 60335-1 Household and similar electrical appliances - Safety - Part 1: General requirements.
• SS-EN 60335-2-103 Household and similar electrical appliances - Safety - Part 2-103: Particular requirements for
drives for barriers, doors and windows.
• SS-EN 61000-6-2 Electromagnetic compatibility (EMC) - Part 6-2: Generic standards - Immunity for industrial
environments.
• SS-EN 61000-6-3 Electromagnetic compatibility (EMC) - Part 6-3: Generic standards - Emission standard for
residential, commercial and light-industrial environments.
This declaration relates to automatic control unit EP105-1, EP105-2 specied in the condition in which it is placed on
the market, and does not cover components added and/or modications made thereafter. Nor does it relate to third-party
supplied equipment or to interfaces between third-party equipment and the equipment specied below and supplied by
FAAC Nordic AB. The instruction manual/installation manual for automatic control unit EP105-1, EP105-2 must be
followed and attention must be paid to risks in the installation of a door, gate or barrier.
We declare that the EP105 does not contain, in concentrations above 0.1%, any substances specied in the REACH
(1907/2006/EC) Candidate List of Substances of Very High Concern or banned substances in RoHS, 2011/65/EC.
Declaration of performance
Intended use of the construction product
Automatic control unit intended for installation in doors, gates or barriers for use in industry, commercial areas and
residential areas that are open to the public, and intended to provide secure access for people, goods and vehicles.
System for the assessment and continuous verification of the performance of the construction product
System 3
Performance
Property Performance Harmonised standard
Force exerted SS-EN 13241 + A2:2016
• Safety edge Performance level c SS-EN 13849-1:2016
• Load guard Performance level d SS-EN 13849-1:2016
Perstorp, 06/12/2021
Ola Hansson, CEO

INSTRUCTION MANUAL DAAB AUTOMATIC CONTROL UNIT EP105
5
Revision 3
Safety
CAUTION: Important safety instructions Following these instructions is important for
personal safety Retain these instructions
!
Carefully read through this instruction manual in its entirety – it contains important
information about safety, installation, commissioning and use. Particularly important safety
information is identied with the symbol
!
in the left margin.
If you fail to follow the safety instructions in this instruction manual, there is a risk of serious
damage to property or injury to animals or people. You should keep this instruction manual in
a safe place for future use.
EP105 or unit controlled by EP105 can be used by children from the age of 8 years and by
people with physical, sensory or mental disabilities or inadequate experience and knowledge
if it takes place under supervision, or if they have been given instructions on how to use an
EP105 or a unit controlled by an EP105 and understand the dangers that may arise.
Children must not play with the installation or the controlled units. Cleaning and maintenance
must not be performed by children.
The EP105 control unit or the accessories recommended by FAAC Nordic AB must not be
modied without the express consent of FAAC Nordic AB.
Only qualied persons working in their own elds may perform installation, adjustment,
commissioning, repair and other work.
Electrical connections may only be made by qualied electricians, who accept responsibility for
the connections.
Follow the safety instructions of the equipment to be controlled by the control unit.
• Safety classification
FAAC Nordic AB has validated the safety circuits in the EP105 to performance level PL = c
and Category 2 as dened in SS-EN ISO 13849-2:2008.
The EP105 is designed with safety edge inputs and an integrated load guard for use in personal
safety applications. These features are designed to meet the requirements of Machinery
Directive 2006/42/EC.
The validation process assumed a technical service life of 10 years or 1 million operating cycles
for components in safety circuits.
FAAC Nordic is unable to guarantee this validation when the motor contactors and safety
edges exceed this technical service life. For this reason, these components should be replaced
before the end of their service life.

INSTRUCTION MANUAL DAAB AUTOMATIC CONTROL UNIT EP105
6Revision 3
Operation
• General
!
Anyone installing or modifying the EP105 must have documented familiarity with, and
understanding of its functions, as well as experience of setting up the control system for
the application in which it will be used.
Take care when operating internal buttons to avoid touching live components.
The unit may only be connected by a qualied electrician, who accepts responsibility for
ensuring that the electric connections have been carried out in accordance with the applicable
standards and this instruction manual.
Anyone commissioning the EP105 must have documented familiarity with, and understanding
of its functions, as well as experience of commissioning control systems for the application to
be used.
• Service and maintenance
!
Regular inspection is required of the external safety features of the EP105, such as
safety edges, stop buttons, photocells, load guards and safety loops. The condition of the
enclosure, cables and installation must also be checked. This inspection must be carried out at
least twice a year.
CAUTION: EP105 must be disconnected from its power supply during cleaning, maintenance
and in replacement of parts or repairs.
• Resetting/replacing tripped fuses
If the fuse protecting the power supply to the automatic control unit trips, FAAC Nordic AB
recommends following these steps to reset/replace it.
• Switch off the main switch to the automatic control unit.
• Decouple the drive unit.
• Reset or replace the fuse.
• Switch on the main switch to the automatic control unit.
• Check that none of the drive units start before receiving the control signal.
• Check that the drive units can be started and stopped from the control buttons.
• If the drive unit cannot be stopped, contact FAAC Nordic AB.

INSTRUCTION MANUAL DAAB AUTOMATIC CONTROL UNIT EP105
7
Revision 3
Connection
CAUTION: Important safety instructions Follow all instructions,, as incorrect installation can
cause serious injury.
• Safety
!
The electrical connections may only be made by a qualied electrician, who accepts
responsibility for ensuring that the electric connections have been carried out in accordance
with the applicable standards and this instruction manual.
Always disconnect the power supply when connecting the control box.
Mechanical installation of the control unit must be carried out by persons with the necessary
knowledge for the task.
• Installation
The location of the control unit must be selected with regard to the protection class of the
enclosure, at least IP54. A heating and/or cooling element should be included if necessary to
maintain the operating temperature stated in the technical specication.
The control unit must be securely xed to a wall or a bracket intended for this purpose, using
screw joints. The xing holes are on the rear or underside of the enclosure. Cables into and out
of the enclosure must have cable entry seals that are approved for use with the particular cable.
Cables outside the enclosure must be securely xed to the surrounding structure. They must
not hang loose and there must be no possibility of them catching on passing objects.
• High current
The power supply must be connected via a lockable main switch, and have a T10A protection.
Connect the incoming earth to the earth bar.
Check that the power supply and motor voltage are compatible.
• Motors
The largest motor that can be connected is 1.5 kW (3-phase 3x400 V).
See "Commissioning" for details of how to check the direction of rotation.
Connecting motors to EP105
Supply 3x400V with neutral
NT1 N L1 L2 L3 U1 V1 W1 U2 V2 W2
Outlet 230V
3x400V + N
Fuse max T10A
U1
V1
W1
W2
U2
V2
U1
V1
W1
W2
U2
V2
Supply to control unit Supply to motors
Control unit
In/Out Power Motor 1 Motor 2
Switch V1 and W1 and/
or V2 and W2 if the motor
runs in the wrong direction.
3-phase motor
Y-connected
3-phase motor
Y-connected
Supply 3x230V without neutral
Outlet 230V
3x230V
Fuse max T10A
U1
V1
W1
W2
U2
V2
U1
V1
W1
W2
U2
V2
NT1 N L1 L2 L3 U1 V1 W1 U2 V2 W2
Control unit
In/Out Power Motor 1 Motor 2
Supply to control unit Supply to motors
3-phase motor
D-connected
3-phase motor
D-connected
Change of phase
sequence if the load
guard value shows fault.
Switch V1 and W1 and/
or V2 and W2 if the motor
runs in the wrong direction.

INSTRUCTION MANUAL DAAB AUTOMATIC CONTROL UNIT EP105
8Revision 3
For information about connecting to the frequency inverter, see the instructions for add-in card
DB409.
Supply 1x230V with neutral
(symmetrical)
Outlet 230V
Switch V1 and W1 and/
or V2 and W2 if the motor
runs in the wrong direction.
1x230V + N
Fuse max T10A
common
common
NT1 N L1 L2 L3 U1 V1 W1 U2 V2 W2
Control unit
In/Out Power Motor 1 Motor 2
Supply to control unit Supply to motors
Single-phase
motor
Single-phase
motor
If a symmetrical single-phase motor is
used (as shown on the left) make the
following changes.
EP105-1: Swap the cable at X12: L1-1
with X12: L1-C1.
EP105-2: Remove the cable between
X11: L2-1 and X4: L2-2.
Swap the cable at X12: L1-1 with X12:
L1-C1. Swap the cable at X7: L1-2 with
X7:L1-C2. See the diagram below for the
terminal locations.
Transformer
Contactor
Supply 1x230V with neutral
(asymmetrical)
Outlet 230V
1x230V + N
Fuse max T10A
U1
Z1
Z2
U2
U1
Z1
Z2
U2
NT1 N L1 L2 L3 U1 V1 W1 U2 V2 W2
Control unit
In/Out Power Motor 1 Motor 2
Switch V1 and W1 and/
or V2 and W2 if the motor
runs in the wrong direction.
Single-phase
motor
Single-phase
motor
Supply to control unit Supply to motors

INSTRUCTION MANUAL DAAB AUTOMATIC CONTROL UNIT EP105
9
Revision 3
Description of the EP105
• General
The EP105 is an automatic control unit for doors, gates, up-and-over doors and barriers, including all the components
necessary to control electric motors – contactors, motor protection, load guards, safety edges, alarm indications, buttons on
the PCB for operation and display, and a programming keypad.
The control unit can be supplied with accessories such as a vehicle loop, wireless functionality, signal lights and magnetic locks.
• Intended use
The purpose of the automatic control unit is to open and close doors, gates, up-and-over doors and barriers, using controllers
connected to the unit.
No other use is permitted without the written agreement of FAAC Nordic AB.
• Identification
• Reference documentation
Instruction manual for drive unit
Instruction manual for the door, gate or barrier
• Disposal of electronic equipment
!
The EP105 is an electronic product, and as such is classied as hazardous waste. All used electronic equipment must
be sent for recycling by a company authorised under environmental legislation to handle hazardous waste including
electronic equipment. FAAC Nordic AB will not charge to process used electronic products supplied by us, provided they
are returned to us.
• Instruction manual
This instruction manual, or an instruction manual that fully complies with the requirements of the applicable Machinery
Directive and Low Voltage Directive and related relevant harmonised standards, must be provided with the nished control
unit to the installer and the end user.
Connector for software
upgrade.
Display
Data entry and
readout buttons
Indications
Control buttons
Terminal block
for low current
Indications
Motor contactors
Terminal block
for high current

INSTRUCTION MANUAL DAAB AUTOMATIC CONTROL UNIT EP105
10 Revision 3
Technical specication
Dimensions (WxHxD) 190x224x60 mm.
Power supply 3-phase or single-phase.
Power supply 3x400 V+N+PE, 3x230 V+PE, 1x230 V+N+PE, 3x400 V+PE (requires an external
transformer)
Permitted voltage variation ±10%
Frequency 50 Hz.
Motor in 3-phase operation
3x400 V
3-phase asynchronous motor 0.18-1.5 kW.
Motor in 3-phase operation
3x230 V
3-phase asynchronous motor 0.18-0.75 kW.
Motor in single-phase
operation
Single-phase motor with capacitor 0.18-0.37 kW.
Fuses External fuse max. T10A.
Power consumption Automatic control unit 22 VA + electric motors.
Operating mode Intermittent operation 50% / maximum period of operation 2 minutes
Temperature range 0 to 45 °C.
Safety edge 2 closing inputs SE.C1 and SE.C2 for a safety edge while closing.
2 opening inputs SE.O1 and SE.O2 for a safety edge while opening.
Variable impedance range 1.0-9.9 kΩ, power capability at least 0.5 W.
Safety circuit Maximum resistance 3 Ω total in the whole safety circuit.
Cable length at 0.75 mm2max 60 m. Cable lengthat at 1.5 mm2max 120 m.
Internal motor protection Setting range 0.5-6 A.
Load guard Setting range 0.05-1.99 kW.
Programmable inputs 6x
Low level 0-8 VDC, high level 12-30 VDC
Input current 6 mA at 24 VDC.
Cable length maximum at cable cross-sectional area 0.75 mm2 ( 1 mm)
Limit switch/Encoder 2+2 inputs
Input current 2 mA at encoder and 22 mA at limit switch
Cable length mechanical limit switches maximum 200 metres at cable cross-sectional
area 0.75 mm2( 1 mm)
Cable length DB405 maximum 50 metres at cross-sectional area 0.75 mm2 ( 1 mm)
Photocell 1 input
Low level 0-8 VDC, high level 12-30 VDC
Input current 6 mA at 24 VDC.
Cable length maximum at cable cross-sectional area 0.75 mm2 ( 1 mm)
Supply voltage VDC max 50 mA.
External supply Unregulated 24 VDC, 18- 28 VDC, max 300mA
Degree of protection The PCB is designed for an enclosure rating of at least IP54.

INSTRUCTION MANUAL DAAB AUTOMATIC CONTROL UNIT EP105
11
Revision 3
Installing the EP105 PCB
If you are installing the PCB in a dedicated enclosure, you must follow the instructions below. Otherwise, the requirements
of the applicable EU directive will not be met, FAAC Nordic's declaration of conformity will not be valid and the product
will not be authorised for use. If the PCB is installed elsewhere, the installer is responsible for obtaining CE approval for
the control system in its entirety. The installer must check that the installation of the PCB fulls the requirement for the
temperature range of the PCB.
• Authorisation
!
Persons installing the PCB in an enclosure must be trained and authorised for the particular task.
• Enclosure
The PCB must be installed in an enclosure designed for the surrounding environment, and must protect the electronics from
moisture, dust and contact.
!
The enclosure must provide protection to class IP54 or better and must be designed for screw xing to a wall or bracket.
For outdoor use, or if there is a risk of condensation in the enclosure, a heating element must be used.
• Installing the PCB
The PCB must be secured to a metal plate. The PCB dimensions are shown below.
Use the screws, spacers and washers provided to x the PCB as illustrated.
!
If the xing plate is painted, scrape off the paint around the holes to ensure good contact between the earth bar, spacers
and the plate.
Fit the earth bar to the xing plate, for connecting the external earth.
12.7
188
223.5
30.4
12.7
189.2
163.8
Metal screw M4
Control Unit
Metal spacer, minimum 10mm
Metal washer
Mounting plate in metal
twith M4 thread
Earth bar
Ø 4.5 (4x)

INSTRUCTION MANUAL DAAB AUTOMATIC CONTROL UNIT EP105
12 Revision 3
• Connecting a safety edge
The safety edge resistor must be installed in the safety edge so that an open-circuit in the resistor or the cable is interpreted as
actuation of the device. See the wiring diagram below. SE.C1 and SE.01 must be used for a safety edge connected to the half
to which motor 1 is connected, and SE.C2 and SE.O2 to the half to which motor 2 is connected.
The impedance can be between 1.0-9.9 kΩ with a 1% tolerance and a power capability of at least 0.5 W. FAAC Nordic AB
recommends an impedance of 8.2 kΩ. A safety edge can only be connected in series.
When connecting in series, only one resistor is used in the outermost safety edge, as shown in the wiring diagram below. The
maximum number of safety edges connected in series with an impedance of 8.2 kΩ is six per input.
Note that the impedance used for a safety edge must be checked and entered into the EP105 on commissioning, see
Commissioning below.
!
Other types of impedance safety edge must not be connected directly to the safety edge inputs – they require an external
control unit.
See the instruction manual for these safety edges.
Use only safety edges approved by FAAC Nordic AB.
• Connecting safety edges and photocells
The diagram below illustrates how to connect an external safety edge unit.
1
2
3
5
4
FC-output 28
FC-input 29
Test output 32
Control unit
Photocell
External unit for
personal protection
Test input
Safety edge SE.C1
Safety edge SE.C2
Safety edge SE.O1
Safety edge
Test input
8,2k
8,2k
8,2k
8,2k
Photocell
Test input
INP6-output 25
INP6-input 27
8,2k
6
Safety edge SE.O2
Safety edge Safety edge
Safety edge Safety edge
Safety edge Safety edge
Safety edge

INSTRUCTION MANUAL DAAB AUTOMATIC CONTROL UNIT EP105
13
Revision 3
• Connecting an encoder (electronic limit switch)
The EP105 supports DB405 type encoders. The encoder uses the same terminals as a conventional mechanical limit switch.
The two diagrams below illustrate how to connect the encoder, and also show which is the left and right motor from the point
of view of the automatic control unit. Make sure the cable to the encoder does not share the same buried pipe as the motor
power supply.
DB405
Motor 1
Left position
DB405
Motor 2
Right position
Control unit
14 17 1 2 3 1 2 334
L.O1 L.O2 GND +24V +24V
GND GND
L.OUT L.OUT+24V
13
+24V
16
Motor 1 Left position Motor 2 Right position
• Connecting a mechanical limit switch (microswitch)
Limit switch
Motor 1
Left position
Control unit
14 17 1 2 318
L.O1 L.O2+24V
13 15 16 4
Limit switch
Motor 2
Right position
1 2 3 4
L.C1 L.C2+24V
• Connecting timer control limit switches
Limit switches can still be used with timer control – they are connected as shown above (mechanical limit switch) but only
for the open position. If there is no limit switch, make the connections as shown below. A mechanical stop in the open
position must be tted.
Control unit
14 17 18
L.O1 L.O2+24V
13 15 16
L.C1 L.C2+24V

INSTRUCTION MANUAL DAAB AUTOMATIC CONTROL UNIT EP105
14 Revision 3
Conguring the EP105
This section provides general instructions on how to change settings in the EP105.
Remember to discharge any static charge in your body by always touching an earthed connection before starting installation.
• General
All values are stored according to a list of channels (in the channel reference), with each channel corresponding to a particular
control parameter or value in the EP105.
The display can show a value up to four digits long, or a channel number with the prex C, d, F, L, o, P or r, followed by three
digits.
The display can be used to show values as well as change settings – the value ashes while the setting is being changed.
If E appears followed by a number, this is an error message – see "Error messages". Note that the startup values
"EP-1" and "EP-2" are not error messages. When the power is connected, EP-1 appears when the unit controls one motor,
and EP-2 when the unit controls two motors.
The <┘ button switches between the value and the channel number and, in conguration mode, it saves the value.
The + button scrolls up the channel list in channel mode. In conguration mode, the button increases the value.
The - button scrolls down the channel list in channel mode. In conguration mode, the button reduces the value.
If no button is pressed in 90 seconds, the display switches to economy mode with reduced brightness. Press any button to
return to normal mode.
Display Description
C
nnn Channel number for the EP105
d
nnn Channel number for the vehicle
detector
F
nnn Channel number for the frequency
converter
L
nnn Channel number for the limit switch
o
nnn Channel number for the output card
P
nnn Channel number for programmable
inputs
r
nnn Channel number for the wireless card
E
nnn Error message (not EP-1 and EP-2)
n
nnn Message
nnnn (ashing) The channel value is changed but not
saved
Button Description
+ Button to increase the channel or value
- Button to decrease the channel or
value
<┘Switch between channel number and
value
<┘Save/conrm the changed value
Switch between different channel
groups
• Readout of parameters in the EP105
Press the <┘button so the display shows the channel number – a letter followed by digits.
Press the button to quickly change between letters (channel groups).
Press the + or - button to step to the channel number you want.
Press the <┘to show the value on the display.
Press the <┘button again to exit and return to the channel number. Leave the unit in this mode – you cannot exit any further.
• Setting parameters in the EP105
Select the channel number according to the readout above.
Press the + or – button. The value starts ashing and is ready to be changed. Return to the original value by pressing the
button.
Press the + or - button to step to the value you want.
Press the <┘button to save the value.
Press the <┘button again to exit and return to the channel number. Leave the unit in this mode – you cannot exit any further.

INSTRUCTION MANUAL DAAB AUTOMATIC CONTROL UNIT EP105
15
Revision 3
• Locked settings
Settings in the different channels can be locked by service personnel so that they cannot be changed. Contact an authorised
service engineer, who will have the instructions needed to release the unit for conguration.
• Configuration channels C700 - C712
It is indicated in channel C700 in which application the control will work. There are three main alternatives, gate, door and
road barrier. The subsidiary options are swing, folding or sliding gate or door
It is indicated in channels C701 to C712 which add-in cards are installed. The settings here control to some extent which
channels will be displayed.. If, for example, C707, DB407 output card, is set to 0, none of the o-channels will be shown. The
settings in C700 do not affect the channel display.
• Message channel C904
To facilitate troubleshooting, it is possible choose via channel C904 to display and save in the error code list various events
beyond the error messages. If, for example, safety edge SE.C1 is activated so that reversing takes place, a message, n042, will
be displayed and saved. The message disappears automatically from the display after about a second, but is saved in the error
code list in C903.
• Display channel C999
By entering different values in the display channel, EP105 will switch between different sets of channels. After power on, C700
is displayed as the rst channel when C999 is set to 0 or 1. When C999 is set to 2, 3 or 4, C999 is displayed as the rst channel.
With C999=0, all channels will be displayed.
With C999=1, channels that are changed in comparison with the factory setting are displayed.
With C999=2, channels for power supply, motor protection and limit switches are displayed. This display mode is used to set
open and closed position.
With C999=3, channels are displayed for pulse/hold-to-run, safe edge, load guard, motor protection, ratio for frequency
inverter, limit switches and application with add-in card. This display mode is used to set the load guard.
With C999=4, Displays channels for selection of application and add-on card. These channels are used to hide or show
additional card channels.
• Käyttöönotto C999-näyttökanavalla
When a new EP105 is switched on for the rst time, the C999 is set to 2. Now you can only step around among these
channels using the plus and minus buttons:
C999, which is the rst channel shown
L001, where the limit position for motor 1 is selected
L002, where the limit position for motor 2 is selected
C202, here you select the type of supply voltage
When the C999 is set to 2, you can easily select the supply voltage, set the motor protection and adjust the open and closed
position. When you have selected the limit mode, channels for the selected limit mode type and for the motor protection are
displayed.
When this is done, change the C999 to 3 and proceed with setting the impulse / holder, clamp protection, photocell and load
monitor.
Finish by setting C999 to 4 and select in the channels C700 to C712 application and the additional cards you have connected
to the controller.
Finally, you set the C999 to 0 and you now have access to all channels and can continue with the commissioning of any
additional cards and ne-tune the function of the automatic control. In channel display mode, you can step fast using the left
button.
See the sections "Quick guide for commissioning the swing gate" and "Commissioning" for more information.

INSTRUCTION MANUAL DAAB AUTOMATIC CONTROL UNIT EP105
16 Revision 3
• Signal list
• Low current
!
The safety circuit, safety edge or limit switch must not be connected to, or used for, any other function. If signals from
the EP105 are needed, a separate output card must be used.
The connection instructions are the same for all types of application, but not all signals may be needed.
If stop signals are unused, the associated input signals must be jumpered on the terminal block, see "Signal reference".
!
Note that the 24 V for the stop circuit must not be combined with other 24 V circuits.
UT
+
-
+
-
24VDC
1
2
3
4
5
6
7
8
9
10
11
12
13
14
15
16
17
18
19
20
21
22
23
24
25
26
27
28
29
30
31
32
33
34
35
36
37
38
24VDC
300mA
Connection point
Signal encoder or limit switch open motor 1
Safety edge 1, closing movement (SE.C1)
Safety edge 2, closing movement (SE.C2)
Safety edge 1, opening movement (SE.O1)
Safety edge 2, opening movement (SE.O2)
Stop input 1
Stop input 2
Stop input 3
Power supply encoder or
common limit switch motor 1
Limit switch closed motor 1
Power supplyencoder or
common limit switch 2
Signal encoder or limit switch open motor 2
Limit switch closed motor 2
Shared programmable input 1 & 2
Prog. input 1, Open, Pulse, P160
Prog. input 2, Close, Pulse, P260
Shared programmable input 3 & 4
Prog. input 3, Open, Constantly, P360
Prog. input 4, Close, Constantly, P460
Shared programmable input 5 & 6
Programmable input 5, P560
Programmable input 6, P660
Input for photocell or external loop detector
Output for magnetic lock
Output for self test
Unregulated 24VDC, 18-28VDC
max 300mA
Connection point
Connection point
Connection point

INSTRUCTION MANUAL DAAB AUTOMATIC CONTROL UNIT EP105
17
Revision 3
• Indications
To simplify commissioning and troubleshooting, LEDs are provided to indicate faults and the status of input signals, as shown
in the table below.
Colour Indication Active when
Yellow START
A constant LED when control signal received, ashing LED when counting down for
automatic closing.
Slowly ashing when counting down channel C520.
Red
M1 A constant LED means that the load guard setting has been exceeded, and a ashing
LED means that the load guard has been triggered for motor 1.
M2 A constant LED means that the load guard setting has been exceeded, and a ashing
LED means that the load guard has been triggered for motor 2.
SE.C1 A constant LED means that the safety edge has been activated, and a ashing LED
means that the safety edge has been reset.
SE.C2 A constant LED means that the safety edge has been activated, and a ashing LED
means that the safety edge has been reset.
SE.O1 A constant LED means that the safety edge has been activated, and a ashing LED
means that the safety edge has been reset.
SE.O2 A constant LED means that the safety edge has been activated, and a ashing LED
means that the safety edge has been reset.
Yellow
LOOP2 Vehicle loop 2 activated
LOOP1 Vehicle loop 1 activated
L.C2 Motor 2 not nished closing, extinguished in closed position, ashing means the input
is not programmed, quick ashing means hold-to-run without limit switch
L.O2 Motor 2 not nished opening, extinguished in closed position, ashing means the
input is not programmed, quick ashing means hold-to-run without limit switch
L.C1 Motor 1 not nished closing, extinguished in closed position, ashing means the input
is not programmed, quick ashing means hold-to-run without limit switch
L.O1 Motor 1 not nished opening, extinguished in closed position, ashing means the
input is not programmed, quick ashing means hold-to-run without limit switch
Green PHOTO Photocell not activated, circuit closed
Yellow
OPEN Signal from internal button – open
CLOSE Signal from internal button – close
INP6 Signal on programmable input 6, closed circuit between terminals 25 & 27
INP5 Signal on programmable input 5, closed circuit between terminals 25 & 26
INP4 Signal on programmable input 4, closed circuit between terminals 22 & 24
INP3 Signal on programmable input 3, closed circuit between terminals 22 & 23
INP2 Signal on programmable input 2, closed circuit between terminals 19 & 21
INP1 Signal on programmable input 1, closed circuit between terminals 19 & 20
Green STOP Stop not activated, safety circuit closed - OK
SAFE Electronics for the internal safety circuit is active - OK
Green 12 V Voltage 12VDC - OK
24 V Voltage 24VDC - OK
Indications in top right-hand corner
Yellow
CLOSE2 Contactor for closing movement activated – motor 2
OPEN2 Contactor for opening movement activated – motor 2
CLOSE1 Contactor for closing movement activated – motor 1
OPEN1 Contactor for opening movement activated – motor 1

INSTRUCTION MANUAL DAAB AUTOMATIC CONTROL UNIT EP105
18 Revision 3
Applications
This section describes the settings required for various types of application. Type of application should be indicated in
channel C700
• Folding doors
Load guard
When a folding door is commissioned, the load guard must be congured for personal protection. This means that it
provides protection during the opening movement according to the applicable standards (obstacles while opening and
also inside the folds). Personal protection means that a normal power is dened – the power used by the motor cannot
fall below a lower limit or exceed an upper limit, calculated automatically by the system on the basis of the normal power.
As a result, the load guard cannot be set higher than the normal effect, providing optimum protection during the opening
movement.
Safety edge
There are usually two safety edges for a folding door, one for each half. They are connected to SE.C1 and SE.C2 and
adjusted as described in the section on Safety edge. According to the factory settings, the safety edge inputs for opening
movement, SE.O1 and SE.O2, are disabled.
• Sliding doors/sliding gates
Load guard
When a sliding door/gate is installed, the load guard should be congured without personal protection. This means that
the purpose of the load guard is more to protect the motor and other mechanisms from damage. The load guard does not
therefore provide effective protection for the opening movement if the door is opened against an obstacle with a crush risk.
Safety edge
Up to two safety edges are used in a sliding door/gate – one at the front and possibly one at the back. More than one safety
edge is usually tted to sliding gates to provide protection from crushing between the gate buffers and xed objects like
gate posts, drive units, etc. The safety edges tted to the front provide protection for the closing movement, and those tted
to the back provide protection for the opening movement. Safety edges providing protection for the closing movement
are connected to SE.C1 and SE.C2, while SE.O1 and SE.O2 are for the opening movement. Adjust the safety edge as
described in the section on Safety edge. Note that according to the factory settings, the safety edge inputs for opening
movement, SE.O1 and SE.O2, are disabled.
• Up-and-over doors
Load guard
When an up-and-over door is installed, the load guard should be congured without personal protection. This means that
purpose of the load guard is more to protect the motor and other mechanisms from damage.
Safety edges
A safety edge for an up-and-over door must be set to send acknowledgements. This is a setting that is made in the EP105
by setting value 1 in channel C101 (C448 must be set to 0), safety edge acknowledgement. The safety edge is connected to
SE.C1 and adjusted as described in the section on Safety edge. Note that safety edge acknowledgement only works with
input SE.C1.
• Swing gates
Load guard
When a swing gate is installed, the load guard should be congured without personal protection. This means that purpose
of the load guard is more to protect the motor and other mechanisms from damage. The load guard does not therefore
provide effective protection for the opening movement if the gate is opened against an obstacle with a crush risk.
Safety edges
There are usually two safety edges for a hinged gate, one on each side. They are connected to SE.C1 and SE.C2 and
adjusted as described in "Safety edge". If no safety edge is used for the opening movement, SE.O1 and SE.O2 are disabled.
• Barriers
Load guard
Load guards on barriers are only intended to protect the barrier and other mechanical components, so they are congured
without personal protection. This means that the barrier changes direction in the presence of a high load in either direction.
Safety edge
A barrier usually has no safety edge at all – in this case, disable SE.C1, SE.C2, SE.O1 and SE.O2. Otherwise, adjust the
safety edge as described in "Safety edge".

INSTRUCTION MANUAL DAAB AUTOMATIC CONTROL UNIT EP105
19
Revision 3
Quick guide to commissioning of swing gate
• Conditions
Electrical installation has been carried out and drive units are disconnected. Commission one drive unit at a time only and
start with drive unit 1. The supply voltage in C2020 is set to 0, 3x400V with neutral The limit switch is of the encoder type.
The display channel C999 is set to 2 The indications for safety edge are unlit. The indications for photocell, stop circuit and
24V are lit green.
• Commissioning of drive unit 1
Direction of movement: Start L001 to 4, hold-to-run without limits. Check that the motor arm attachment is running in the
right direction by pressing the OPEN or CLOSE buttons on the automatic control unit. For change of direction of rotation,
see section on Connection in EP105 Instruction Manual.
Open and closed position: Connect the gate half to drive unit 1 and enter the positions for open and closed After this,
L001 is set to 1, encoder
L110=1, Motor 1 Left position L120=2; Motor 2 Right position
L113, Closed position
L112, Open position
L111, Position readout
Motor protection: Read the motor current during operation in C251 and enter this value in C252 for opening and in C253
for closing. E201 means that the entered value is set too low. E206 means that the entered value is set too high.
Load guard: Set C999 to 3. In a hinged gate application personal protection is not normally required, and C230 is set to
0.00. Set C033 to 3, pulse to activate the load guard. After the load guard has tripped, the indication M1 ashes and the
message n071 or n072 is shown on the display and in the error code list in C903. Check that the setting in the load guard
in C232 and C233 is just high enough not to cause material damage, but at the time is so high that it is guaranteed to open
depending on weather conditions and mechanical changes.
Safety edges: Check the safety edges on gate half 1 by pressing on the safety edges during movement. Note that safety
edge function in opening is closed in C131. In activated safety edge during closing, the gate must reverse to the fully open
position, while in opening it must reverse to closed position during the time in C494. Flashing indication for SE.C1 or
SE.O1 means tthat the safety edge has been activated, but is now disabled.

INSTRUCTION MANUAL DAAB AUTOMATIC CONTROL UNIT EP105
20 Revision 3
• Commissioning of drive unit 2
Preparations: C999 is set to 2. Open half 1 and set L001 to 0 to keep drive unit 1 in open position Set C033 to 5, service
position.
Direction of movement: Start L002 to 4, hold-to-run without limits. Check that the motor arm attachment is running in the
right direction by pressing the OPEN or CLOSE buttons on the automatic control unit. For change of direction of rotation,
see section on Connection in EP105 Instruction Manual.
Open and closed position: Connect the gate half to drive unit 2 and enter the positions for open and closed After this,
L002 is set to 1, encoder.
L110=1, Motor 1 Left position L120=2; Motor 2 Right positionL123, Closed position
L122, Open position
L121, Position readout
Motor protection: Read the motor current during operation in C261 and enter this value in C262 for opening and in C263
for closing. E202 means that the entered value is set too low. E207 means that the entered value is set too high.
Load guard: C999 is set to 3. In a hinged gate application personal protection is not normally required, and C240 is set
to 0.00. Set C033 to 3, pulse to activate the load guard. After the load guard has tripped, the indication M2 ashes and the
message n073 or n074 is shown on the display and in the error code list in C903. Check that the setting in the load guard
in C242 and C243 is just high enough not to cause material damage, but at the time is so high that it is guaranteed to open
depending on weather conditions and mechanical changes.
Safety edges: Check the safety edges on gate half 2 by activating the safety edges during movement. Note that safety
edge function in opening is closed in C141. In activated safety edge during closing, the gate must reverse to the fully open
position, while in opening it must reverse to closed position during the time in C494. Flashing indication for SE.C2 or
SE.O2 means that the safety edge has been activated, but is now disabled.
Additional boards: Set C999 to 4. Channels C702 to C712 show or hide channels for additional boards.
If e.g. DB407, Output board, to be used set C707 to 1
Finishing: Set C999 to 0, display of all channels Set L001 to 1, encoder and make nd adjustments to the gate halves in closed
position using L113 and L123. Note all channels in EP105 Instruction Manual and the Log Book.
Other manuals for DAAB EP105
1
Table of contents
Other FAAC Control Unit manuals
Popular Control Unit manuals by other brands
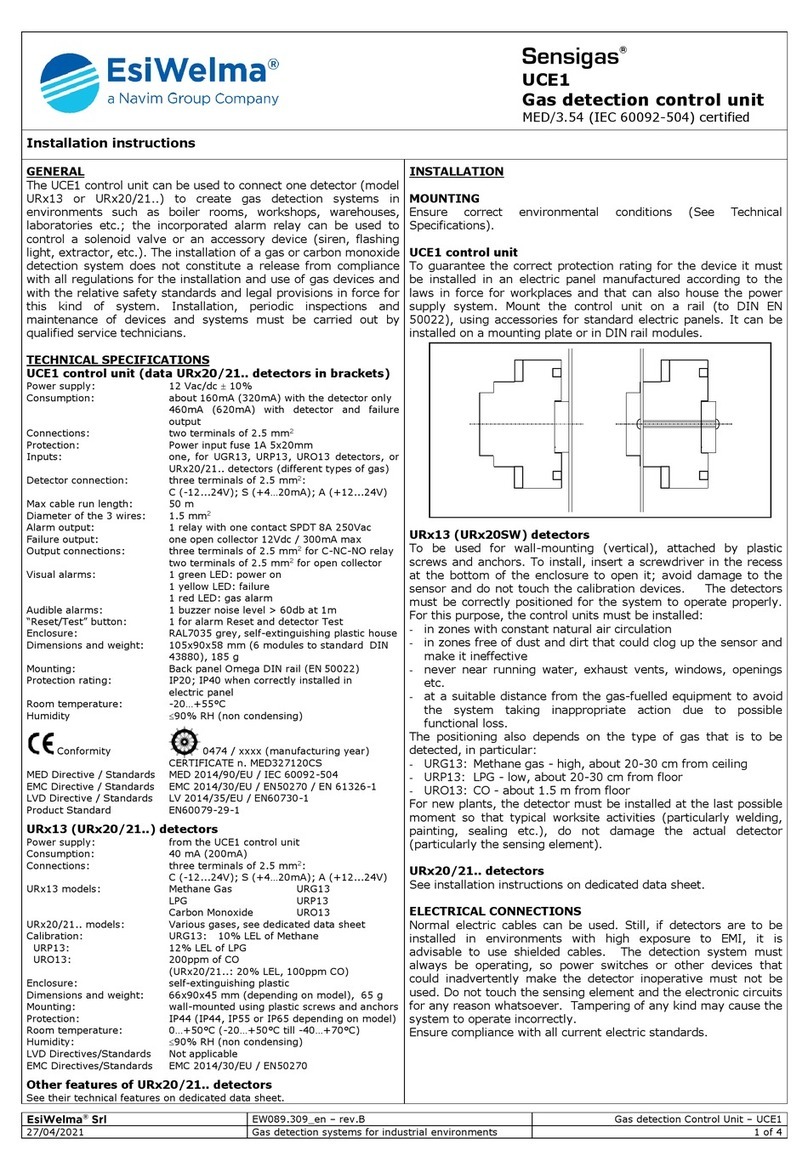
Navim Group Company
Navim Group Company EsiWelma Sensigas UCE1 installation instructions
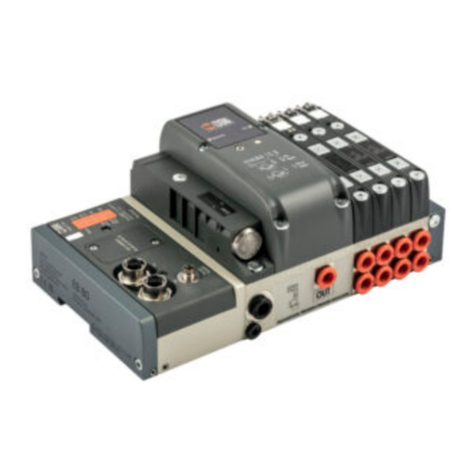
Metal Work
Metal Work EB 80 user manual
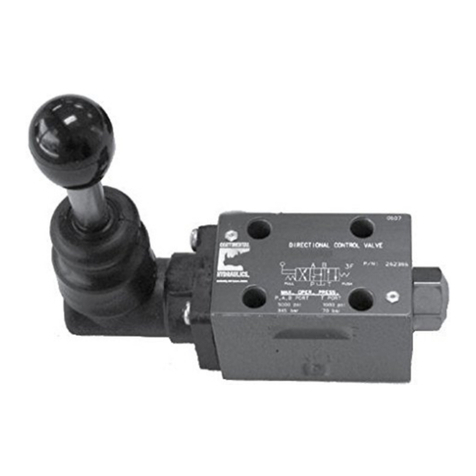
Continental Hydraulics
Continental Hydraulics A Design Series Service manual

resideo
resideo Braukmann BG04MAN installation instructions

Nederman
Nederman TAV 50 user manual
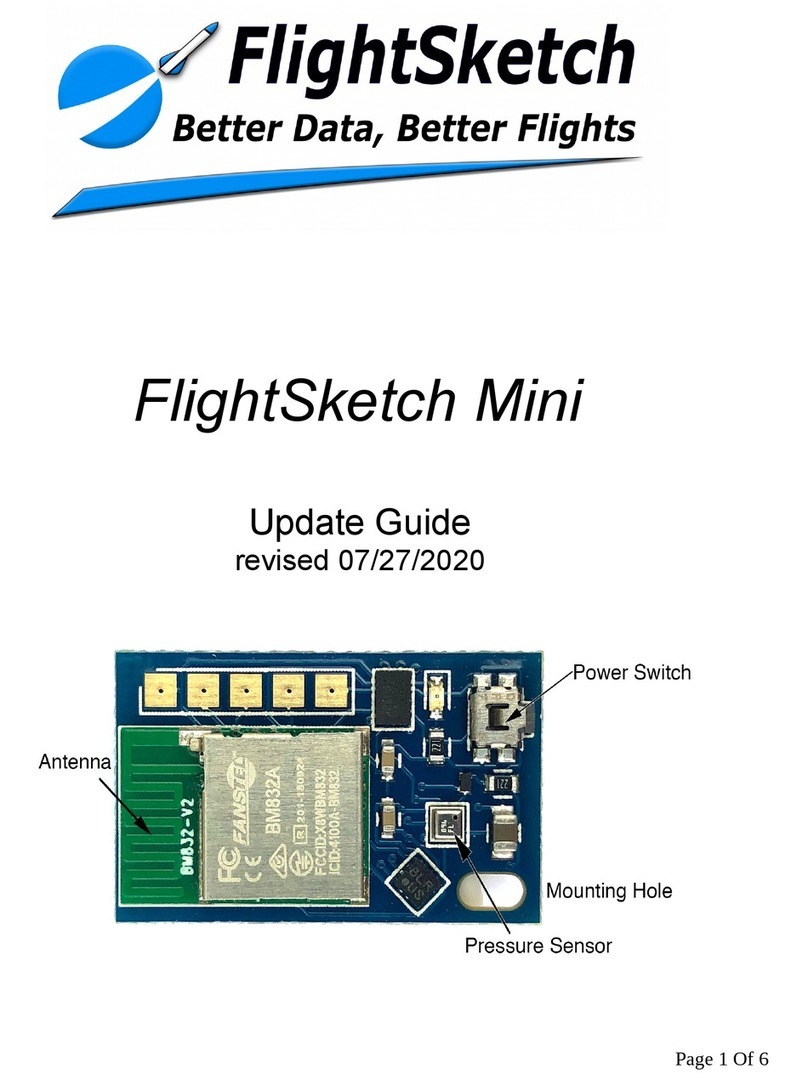
FlightSketch
FlightSketch Mini Update guide