RTA X-PLUS C Series User manual

R.T.A. s.r.l. – XPCSME03 – 12/20
MOTION CONTROL SYSTEMS
X-PLUS C – X-PLUS S
SERIES
STEPPING MOTOR DRIVES
INSTRUCTION MANUAL
R.T.A. s.r.l.
Via E. Mattei – Frazione DIVISA
27020 MARCIGNAGO (PV)
Tel. +39.0382.929.855 - Fax +39.0382.929.150
R.T.A.
DEUTSCHLAND GmbH
Bublitzer Straße, 34
40599 DÜSSELDORF (Germany)
Tel. +49.211.749.668.60-Fax +49.211.749.668.66
Internet: http://www.rta-deutschland.de
e-mail: info@rta-deutschland.de
R.T.A. IBERICA
MOTION CONTROL SYSTEMS S.L.
C/Generalitat 22, 1° 3°
08850 GAVA – BARCELONA (Spain)
Tel. +34.936.388.805-Fax +34.936.334.595
Internet: http://www.rta-iberica.es
e-mail: [email protected]

R.T.A. s.r.l. – XPCSME03 – 12/20
2/29
INDEX
1 -
NOTICES, MANUAL STRUCTURE AND TERMINOLOGY ......................................3
2 -
HAZARDS AND PRECAUTIONS..............................................................................4
3 -
GENERAL CHARACTERISTICS AND IDENTIFICATION ........................................6
4 -
INPUT AND OUTPUT LOGIC SIGNALS ..................................................................7
5 -
POWER INPUTS AND OUTPUTS............................................................................9
6 -
SETTING AND SIGNALLING..................................................................................11
7 -
DRIVE EXTERNAL CONNECTIONS......................................................................15
8 -
INSTALLATION AND ENVIRONMENT...................................................................17
9-
MAINTENANCE......................................................................................................17
10 -
LOGIC INTERFACING EXAMPLES .......................................................................18
11 -
APPLICATION NOTES...........................................................................................20
12-
STO FUNCTION (X-PLUS S2 / S4 and X-PLUS S2.1 / S4.1).................................24
WARNING
: it is user RESPONSIBILITY to check that this manual refers
to product model and version that will be used
SYMBOL MEANING
WARNING!
The section marked with this symbol contains warnings regarding
safety problems.
If the directions indicated in these sections are not
fulfilled, it could arise hazardous situations for human life.
CAUTION! The section marked
with this symbol contains information
regarding operations which are strictly forbidden.
INFORMATION
The section marked with this symbol contains important information
s to avoid not compliant installations.
[...] UL
Some parts of the text between square brac
kets are the original
definition of UL standard rules.
These requirements
are mandatory for the models of this manual
that are UL compliant. These models can be identified by UL mark
in the identification label on the specific model.
In any case, we advise to comply with these requirements even for
non-UL certified models.

R.T.A. s.r.l. – XPCSME03 – 12/20
3/29
1 - NOTICES, MANUAL STRUCTURE AND TERMINOLOGY
1.1 - This manual covers the following items:
•X-PLUS C and X-PLUS S series stepping motor drives in all their standard versions.
•Standard characteristics of special versions of X-PLUS C and X-PLUS S series stepping motor
drives (see chapter 1.2).
•For models and versions identification see also chapter 3.
1.2 - For the purposes of this manual the terms used assume the meaning below described (see Fig. 1).
Control system
(PLC, CNC or others)
Stepping
motor drive
Electrical
supply
Movement
mechanical
system
External commands
and/or sensors
Stepping
motor
Fig. 1
•Drive: electronic part of an electromechanical motion system, which receives some digital or
analog input signals from an external control system and gives to the stepping motor the
suitable phase excitation sequences, in order to obtain the mechanical movements required by
the control system. The drive can also communicate its status to the control system through
some logic signals. Concerning UL standard, the drive is classified as an [Open Type Motor
Drive] and it is suitable to control stepping motors with 4 terminals.
•Control system: part of the machine which decides and controls all machine functions and gives
to the drive all execution commands. It could be a numerical or programmable control, a
personal computer or a specific control card. In the simplest machines it could also be a group
of sensors and electromechanical switches.
•Electrical supply: all machine parts suitable to supply the drive in a correct way; anti-interference
filter, switches, protection systems and in some cases transformer.
•Standard drives are all models (see chapter 3 for identification) whose characteristics comply
completely with those described in this manual. Special versions are all models in which some
characteristics differ from the description given in this manual. For these models, some part of
the manual does not apply and, in these cases, you must have the specific "variation sheet"
which becomes an integral part of the manual itself.
1.3 - Products described in this manual (see identification code in chapter 3) complies with Low Voltage
(2014/35/CE) and Electromagnetic Compatibility (2014/30/CE).
Product standards:
1) UL 61800-5-1 1st Edition – Power Conversion Equipment
2) CSA C22.2 No.274 - Industrial control equipment.
1.4 - Remember that, as stated in all regulations, compliance exists only when a product is installed and
used in accordance with its destination and following manufacturer prescriptions. Thereby, all
relevant indications about use, cautions, installation and limitations here described must be followed
by user in order to stay within safety and compliance limits: from this point of view, chapter 2, 8 and
10 are particularly important, but the entire content of this manual has to be carefully read and
considered in order to obtain the information necessary for a correct use of the product.

R.T.A. s.r.l. – XPCSME03 – 12/20
4/29
1.5 -
INFORMATION
.
This manual is conceived in a way to offer to the personnel involved in project and safety verification
of a machine all information concerning characteristics, working conditions, application limits hazards
and cautions about X-PLUS C and X-PLUS S series stepping motor drives. The knowledge of this
information is essential for a correct project of machines, apparatus and systems in which the drives
are used; it is strongly recommended not to start any operation with the drives before you have
completely read and understood the content of this manual; if you find some part of this manual not
completely understandable or lacking regarding your particular application, do not hesitate to contact
directly R.T.A. that can provide, if necessary, further information in order to make the user able to
design his machine and the related safety systems in the best way. Take into account that an
incorrect use or installation, a wrong dimensioning of external safety elements related with the drive
could bring to economical damages and also to hazards for human life.
1.6 - The terms "user and customer" often used in this manual always indicate a skilled person as defined
in chapter 2.4
1.7 -
INFORMATION
.
This manual is considered valid at the moment of the selling of the product. It cannot be considered
inadequate as a consequence of product or manual changes or improvements after the selling.
R.T.A. reserves the right of products and manual revisions without notice neither obligation of
previous products and manuals revision.
2 - HAZARDS AND PRECAUTIONS
2.1 -
INFORMATION
.
X-PLUS C and X-PLUS S series drives are suitable to drive two phases stepping motors with 4, 6 or
8 terminals. (see also section 10 for more details about motor and application limits). Their use for
different purposes is not allowed.
2.2 -
WARNING!
X-PLUS C and X-PLUS S series drives [UL category: Open Type Motor Drive] are power conversion
equipments with protection degree IP20 (IEC 60529), foreseen for use in pollution degree 2
environment, with a working temperature range between 5°C (41 °F) and 40°C (104 °F). Thereby,
they must be located within a protective enclosure suitable to maintain the above mentioned
conditions. The position inside the enclosure must be chosen in a way to avoid that small tools or
particles of material can drop inside the drive through the ventilation holes. Avoid absolutely to
install in explosive or flammable environments. Avoid also to install near easily flammable
materials and components; we recommend to verify that all the components located in the
enclosure are realized using self-extinguishing materials.
2.3 -
WARNING!
X-PLUS C and X-PLUS S series drives are designed for use in general industrial equipments. Do not
use in installations in which an utilization mistake or a malfunction or a failure of the drive could
cause:
•Injuries or hazards for human life
•Property damages
•Risks of social and public upsets
In these cases, the person responsible of the installation must design and provide specific
equipments or safety techniques, external and independent from the drive, suitable to prevent all
dangerous consequences.

R.T.A. s.r.l. – XPCSME03 – 12/20
5/29
2.4 -
CAUTION!
All products considered in this manual are sub-assemblies without a direct function, foreseen to be
integrated in a more complex machine. Only a professional assembler, expert in the field of motor
drives and in their related problems, can install and put in service this component. It is exclusive
responsibility of the designer of the complete machine or installation in which this component is used
to take care of the safety and reliability of his project. It is forbidden to use this material in application
covered from one or more EEC directives (for instance 2014/30/CE, 2006/42/CE, etc.) before the
conformity to those directives has been declared. Regarding 2014/30/CE directive, see chapter 10.
2.5 -
CAUTION!
Suitable for use on a circuit capable of delivering not more than 5000 A rms symmetrical amperes,
230 Volts maximum; overvoltage category III. Overvoltage category IV is not permitted.
2.6 -
CAUTION!
Remote overload protection is required. Integral solid state short circuit protection does not provide
branch circuit protection. Branch circuit protection must be provided in accordance with National
Electrical Code and any additional local code] (see Fig. 5 or Fig. 6 chapter 7).
[The drive does not provide Motor Overload protection. External or remote Motor Overload protection
shall be provided in the end-use applications]. [The drive does not provide motor over-temperature
sensing. It shall be provided in the end-use applications].
It is exclusive responsibility of the designer of the complete machine or installation in which this
component is used to take care of the safety and reliability of his project.
2.7 -
CAUTION!
The drive and related motor have a protective earth terminal which must be connected to earth, in
order to prevent risk of electric shock.
2.8 -
CAUTION!
With the drive switched on, do not perform any wiring, maintenance, inspection; in particular, do not
perform the setting of the dip-switches. After switching the power off, wait at least 10 minutes before
to fulfill these tasks.
Do not touch the inside of the drive and do not get close to connection terminals while the device is
powered on.
Do not plug or unplug the connectors while the device is powered on. These operations cause some
underhand damages of the contact surface which could bring to a subsequent risk of overheating
and fire.
2.9 -
CAUTION!
Do not try to repair a faulty device. Only R.T.A. personnel is authorized to repair operation.
2.10 -
CAUTION!
During normal working conditions, the heatsink can reach temperatures until 80°C ( 176 °F). Do not
touch this component for some minutes, after switching off, in order to avoid scald hazard.
2.11 - R.T.A. cannot be considered liable for property losses, equipment damages and personnel injuries
arising from use or installation not fully compliant with specifications contained.
2.12 - For STO inputs and Monitor output correct use (X-PLUS S only), please refer to Chapter 12.

R.T.A. s.r.l. – XPCSME03 – 12/20
6/29
3 -GENERAL CHARACTERISTICS AND IDENTIFICATION
3.1 - DIMENSIONS
129.8 (5.11)
46 (1.81)
OFF
DP1
ON
1
5
2
(
5
.
9
8
)
116.8 (4.6)
Ø 4.5 (0.18) Ø 4.5 (0.18)
Ø 4.5 0.18)Ø 4.5 (0.18)
23 (0.90)
94.7 (3.73)
5
.
2
5
(
0
.
2
1
)
HV
C1
SHIELD
B-
B
MOTOR
N
46 (1.81)
OFF
DP1
ON
HV
-
Dir.
-
C. Off
-
-
-
-
X-PLUS
series
C1
SHIELD
B-
B
MOTOR
N
X-PLUS C X-PLUS S
Fig. 2 – Dimensions: all measures in mm.
3.2 - IDENTIFICATION
The models identification of X-PLUS C and X-PLUS S series drives is as follows:
X-PLUS Cz.y, X-PLUS Sz.y
where:
.y
is not present in standard models. If present
y
can be a number or an alphanumeric
character identifying a special version with some variations with respect to standard models.
Z can be equal to 2for 2 A nominal phase current version or 4for 4 A nominal phase current
version.
Each sample is also identified with a serial number.

R.T.A. s.r.l. – XPCSME03 – 12/20
7/29
4 -INPUT AND OUTPUT LOGIC SIGNALS
All input and output logic signals are optically insulated among them and from internal power circuits.
Positive and negative terminals are separately accessible. For all logic signals in the following we indicate
the corresponding numbers of connector C2. An input signal is considered ON when a voltage is applied
(Fig. 3a). For STO inputs and Monitor output correct use and indications in X-PLUS S, please refer to
Chapter 12.
20 and 19 EDM OUTPUT (ERROR DETECTION MONITOR) (X-PLUS S only): this output is ON if
both STO1 and STO2 inputs are OFF. In this case, the drive is in Safe Torque Off
operation mode and the current flowing in each motor winding is inhibited. The output is
OFF if one or both STO1 or STO2 inputs are ON.
EDM OUTPUT not available in X-PLUS C.
18(-) and 17(+) STO2 INPUT (X-PLUS S only): with this signal ON drive is active (with flowing current in
each motor winding) on condition that STO1 input is ON. When STO2 is OFF the drive is
inhibited, thus motor current (and so holding torque) is turned to zero.
STO2 INPUT not available in X-PLUS C.
Note: The current flows in the motor winding 50 ms. later from the OFF-ON transition of
the STO inputs.
Depending on the mechanical load and inertia of the system, it needs to wait additional 50
ms to allow the mechanical settling of the motor. During this time it is not allowed to send
commands to the drive.
16(-)and 15(+) STO1 INPUT (X-PLUS S only): with this signal ON drive is active (with flowing current in
each motor winding) on condition that STO2 input is ON. When STO1 is OFF the drive is
inhibited, thus motor current (and so holding torque) is turned to zero.
Note: The current flows in the motor winding 50 ms. later from the OFF-ON transition of
the STO inputs.
Depending on the mechanical load and inertia of the system, it needs to wait additional 50
ms to allow the mechanical settling of the motor. During this time it is not allowed to send
commands to the drive.
CURRENT OFF INPUT (X-PLUS C only): with this signal ON drive is active. When this
signal is OFF the drive is inhibited, thus motor current (and so holding torque) is turned to
zero.
14(-)and 13(+) DIRECTION INPUT: with this signal ON motor rotation direction is opposite to the one
obtained when this input is OFF. This signal has to be valid at least 100 µsec before STEP
signal and has to stay in this status for at least 100 µsec after last STEP sent to the drive.
12(-)and 11(+) STEP INPUT: active transition is the ON-OFF transition of this signal. Suggested duty-
cycle 50%. Max frequency: 120 kHz (with square signal amplitude = 5 Volt) with square
wave signal supplied from an output able to produce a voltage between 5 and 24 Volt.
10 and 9 FAULT OUTPUT: when this output is ON, drive is normally working; when it is OFF drive is
in no-working state. Drive automatically goes in no-working state when some protection is
active and automatically recovers when this protection resets.

R.T.A. s.r.l. – XPCSME03 – 12/20
8/29
Step & Direction input structure scheme FAULT output structure
DRIVE
R1
In+
5 < Vin < 24 Volt
R1 = 1.0 KOHM
I=5mA
DRIVE
Out
9
NOTE:
Insert a protection diode in parallel with the load
in case of inductive load.
Out
10
Vmax = 45 Volt
Imax = 50 mA
Vsat 0.8 Volt (@ 20 mA)≤
(3a)
(3b)
STO1 /
STO2
and CURRENT OFF
inputs structure scheme MONITOR output structure (X-PLUS S only)
DRIVE
R2
R1 (1W)
In+
Vin = 24 Volt
18 Volt < Vin < 27 Volt
H
0 Volt < Vin < 3 Volt
L
R1 = 1.8 KOHM
R2 = 680 OHM
X-PLUS C:
R1 = 3.3 KOHM
R2 = 390 OHM
X-PLUS S:
DRIVE
Out
19
Vmax = 45 Volt
Imax = 50 mA
Vsat 0.8 Volt (at 20 mA)
≤
Out
20
NOTE:
Insert a protection diode in parallel with the load
in case of inductive load.
(3c)
(3d)
Fig. 3 – Inputs and outputs scheme.

R.T.A. s.r.l. – XPCSME03 – 12/20
9/29
5 - POWER INPUTS AND OUTPUTS
In this chapter drive power input and output and the necessary power supply for drive working are described.
5.1 - Drive power outputs are the four connections to stepping motor. Drive power inputs can be connected
to the main or to an insulation transformer. All connector C1 terminals are listed in the following
Table 1.
TABLE 1
CONNECTOR C1 DESCRIPTION
1 Motor winding terminal B
2 Motor winding terminal B-
3 Motor winding terminal A-
4 Motor winding terminal A
5 SHIELD
6 GROUND
7 AC power supply.
N (Neutral).
8 AC power supply.
L (Line).
5.2 -
CAUTION!
Earth terminal screw – Earth terminal screw is in frontal panel inferior part and has to be electrically
connected to earth (PE terminal of the machine in which the drive is installed). The terminal 6 of C1
connector has to be connected to earth too.
Earth terminal screw and terminal 6 of C1 connector are the points of motor-drive system that have to
be connected to earth (PE terminal). No other point at a different potential power circuit has to be
connected to earth. The terminal 5 of C1 connector (SHIELD) is internally connected to terminal 6 of
C1 connector. Other points at the same potential of GND could be connected to earth using the
cautions suggested by classical techniques to obtain a correct location of multiple earth connections.
Shielded cables of motor outputs must be connected to points at the same potential. See connection
schemes of Fig. 5, 12 and 13.
5.3 - The drive is
Protection Class I
, it is necessary to take into account earth connections to ensure
correct protection levels.

R.T.A. s.r.l. – XPCSME03 – 12/20
10/29
5.4 - Table 2 and Table 3 show power inputs and outputs characteristics:
TABLE 2
AC input X-PLUS C4 / X-PLUS S4 X-PLUS C2 / X-PLUS S2
V
AC
nom
(VOLT)
110 - 230 110 - 230
Tolerance
V
AC
nom
(%)
15 15
Max input current (AMP)
4 2
Max input power (VA)
440 - 920 440 - 920
Dimensions
(mm)
152 × 129 × 46 152 × 129 × 46
TABLE 3
Motor phase outputs X-PLUS C4 / X-PLUS S4 X-PLUS C2 / X-PLUS S2
V
PH
min
(VOLT)
0 0
V
PH
max
(VOLT)
+/- 1.41 x V
AC
+/- 1,41 x V
AC
I
NP
min
(AMP)
2.4 1,2
I
NP
max
(AMP)
4 2
5.5 - Definition of terms used in Table 2 and in Table 3:
V
AC
nom :
indicates nominal alternating voltage for drive operation with not stabilized
power supply.
Max input current :
maximum input current allowed for continuous operations.
Max input power :
maximum input power allowed for continuous operations.
V
PH
min :
minimum value of the voltage at each motor phase output.
V
PH
max :
maximum value of the voltage at each motor phase output.
I
NP
:
indicates nominal phase current, which flows in each motor winding,
measurable with motor turning at
low speed.
The drive is equipped with
automatic current reduction with motor at standstill. Phase current is calibrated
at final test moment and can be set from the customer, choosing among four
different values, by means of DIP-SWITCH. This value is the peak value of the
sinusoidal approximation of the phase current.
I
NP
min and max :
minimum and maximum nominal phase current value which can be set by user
using DIP-SWITCH.

R.T.A. s.r.l. – XPCSME03 – 12/20
11/29
6 - SETTING AND SIGNALLING
6.1-
INFORMATION
.
X-PLUS C and X-PLUS S series drives are general purpose products which can be used to drive many
different motor models in different kind of applications. For this reason they have a six positions DIP-
SWITCH suitable to adapt drive characteristics to the specific motor and/or application.
The setting of
this dip-switch has to be made by customer before putting in service the drive. Do not forget to
do these settings: wrong setting could get application errors and also motor damages and
hazards.
Led signalling drive status are also present.
6.2- Fig. 4 shows the position of DIP-SWITCH DP1, signalling LEDs, connectors and labels in X-PLUS C
and X-PLUS S series drives.
EARTH
(CONNECT TO PE)
FRONTAL LABEL:
MODEL AND SERIAL NUMBER
ON
OFF
C1
C2
DIP SWITCH
DP1
HV
X-PLUS
series
ON OFF
C1
C2
DIP SWITCH
DP1
HV
EARTH
(CONNECT TO PE)
FRONTAL LABEL:
MODEL AND SERIAL NUMBER
X-PLUS C
X-PLUS S
Fig. 4 – Dip-switch DP1, signalling leds and connectors.

R.T.A. s.r.l. – XPCSME03 – 12/20
12/29
6.3-
INFORMATION
.
Table 4 shows the position of dips 1 and 2
(DP1)
and the related motor nominal current.
NOMINAL CURRENT SETTING
X-Plus C4 / S4 X-Plus C2 / S2
DIP 1
DIP 2
I
NP
(A) I
NP
(A)
ON ON 2,4 1,2
ON OFF 3 1,5
OFF ON 3,4 1,7
OFF OFF 4 2,4
Table 4
6.4-
INFORMATION
.
Tables 5a and Table 5b show damping mode settings depending on different model:
- FOR X-PLUS C2 / C4 and X-PLUS S2 / S4:
CURRENT PROFILE MANAGEMENT
DIP 3
TYPE
CHARACTERISTIC
►
OFF A ENHANCED MOTOR TORQUE (EXCLUDED DAMPING)
ON C STANDARD (ACTIVE DAMPING)
Table 5a
- FOR X-PLUS C2.1 / C4.1 and X-PLUS S2.1 / S4.1:
CURRENT PROFILE MANAGEMENT
DIP 3
DIP 4
TYPE
CHARACTERISTIC
OFF OFF A ENHANCED MOTOR TORQUE
►OFF ON B MIXED
ON OFF C STANDARD
ON ON D ENHANCED MOTOR SMOOTHNESS
Table 5b
APPLICATION NOTES:
Damping electronic circuit ensures low acoustic noise and reduces the amount of typical stepping motor
mechanical vibrations. In any case, these can be reduced using higher values of steps/revolution in
accordance with the maximum frequency produced by control system and with maximum revolution
speed requested to the motor.
For example, in the case of control system generating a maximum frequency of 10 KHz and if the
desired speed is equal to 600rpm = 10 revolutions/sec, 1000 steps/rev (=10.000/10) is the maximum
resolution that can be used.
•A type current profile performs higher motor torque.
•B type current profile performs higher motor movement smoothness with lower acoustical noise and
vibrations with low speed and enhanced motor torque with high speed.
•C type ia a standard current profile (used in X-PLUS C4 and X-PLUS S4 series).
•D type current profile performs higher motor movement smoothness with lower acoustical noise and
vibrations. Smoothing effect of D type depends on resolution setting: the resolution is lower, the
smoothing is more effective.

R.T.A. s.r.l. – XPCSME03 – 12/20
13/29
6.5-
INFORMATION
.
Table 6a and Table 6b operation mode setting:
- FOR X-PLUS C2 / C4 and X-PLUS S2 / S4:
RESOLUTION
DIP 4 DIP 5 DIP 6
STEP/REV
ON ON ON 4.000
ON ON OFF 2.000
►
ON OFF ON 1.000
ON OFF OFF 500
OFF ON ON 3.200
OFF ON OFF 1.600
OFF OFF ON 800
OFF OFF OFF 400
Table 6a
- FOR X-PLUS C2.1 / C4.1 and X-PLUS S2.1 / S4.1:
RESOLUTION
DIP 5 DIP 6
STEP/REV
ON ON 3.200
ON OFF 1.600
►
OFF ON 800
OFF OFF 400
Table 6b
= default factory setting.

R.T.A. s.r.l. – XPCSME03 – 12/20
14/29
6.6- The following list shows the meaning of the alert LEDs.
LED HV (green)
:
ON = supply voltage is in the correct operating range.
OFF = drive is not supplied or supply voltage is out of the correct range (in the second
case also LED FAU is ON).
LED FAU (red)
:
ON = drive is in no-working state due to one of the following protection:
a-Thermal protection (if LED TER is ON).
b-Max or Min supply voltage (if LED HV is OFF).
c-Short circuit or wrong motor connection (if LED HV is ON and LED TER is OFF).
OFF = drive is in working state if LED HV is ON.
LED TER (yellow)
:
ON = drive is in no-working state by thermal protection (in this case LED FAU is ON).
OFF = heatsink temperature is lower than the limiting value.
BLINKING (not available for X-PLUS C2.1/C4.1 and X-PLUS S2.1/S4.1):
- 1 FLASH = Min/max voltage protection memory
- 2 FLASHES = Thermal protection memory
- 3 FLASHES = Short circuit protection memory
- 4 FLASHES = Motor cable not connected (active with motor in stop state only)
Note:
- X-PLUS C2 / C4:
To reset each protection memory turn off and on the drive
- X-PLUS S2 / S4:
Not connected motor cable alarm is ON when STO function is OFF
only.
Reset of each protection memory starts when the drive is turned on or turned off or
when STO function is OFF. Memory must be reset by removing power supply voltage or
STO function disabling.
All protection circuit and alarm reset itself when the alarm source disappears.

R.T.A. s.r.l. – XPCSME03 – 12/20
15/29
7 -DRIVE EXTERNAL CONNECTIONS
7.1-
CAUTION!
Dimensioning power for filter, switching and protection system and possible transformer. The basis to
calculate this power is the total power required from drive and motor. It is the sum of the following terms:
- Mechanical power delivered to load: mainly depending on application characteristics like friction,
inertia, efficiency of mechanical transmission etc.
-Motor losses: mainly depending on motor type, drive voltage, speed and duty cycle.
-Drive losses: mainly depending on drive model, current setting and duty cycle; according with these
parameters these losses can approximately vary between 60 and 130 Watt. It is often very hard to
do an exact forecast of drive and motor losses; in these cases a safety over-dimensioning of the
supply elements proportional to the uncertainty of the data is recommended. To get more accurate
information, contact R.T.A. describing all the data of the particular application.
7.2-
WARNING!
Protection systems indicated in Fig. 5 must include:
- SPD (Surge Protection Device) nominal working voltagedi 240 V
AC
, overvoltage category III,
1500 V
P
, 20 kA (Modello VAL-US-240/40/1+0 Phoenix Contact GmbH or equivalent) [Primary
Circuit Overvoltage Protection].
- Residual current protective device with operating residual current of 30 mA.
- Branch circuit protection fuses: UL Type JDDZ, class CC, 600 VAC, 8 Amp (Cooper Bussman
model KTK-R-8 or equivalent) [Branch circuit protection fuses].
7.3-
WARNING!
For external connections copper wire must be used [Use Copper Conductors only] and certified to work
at 60/75 °C [Use 60/75 °C wires only].
The cross-sectional area of conductors used in power supply circuit must be chosen according with
dimensioning power (see 7.1). The cross-sectional area of the four shielded conductors between motor
and drive must be chosen in accordance with nominal current which has been set in the drive.

R.T.A. s.r.l. – XPCSME03 – 12/20
16/29
PE
PE
1
2
3
4
5
6
7
8
A
A -
B
B -
PE
9
10
11
12
13
14
15
16
17
18
19
Dir.
Fault
-
-
-
-
-Step
V
AC in
20 -
MAIN
(230 o 110 V )
AC
V
AC
SPD
Surge Protection
Device
Torque
5-7 lb in
0.6-0.8 N m
⋅⋅
AWG: min 17 - Max 14
Stranded conductor
Torque
13-22 lb in
1.5-2.5 N m
⋅⋅
C1
C. Off
Aux 1
Aux 2
MOTOR
SHIELDED CABLE
STEPPING
MOTOR
Line
Neutral
Drive chassis
earth
Shield
FUSES
EMI FILTER
(section 10.1.1)
see
section 7.2
RESIDUAL
CURRENT
DEVICE
AWG:
min 28
Max 20
Stranded conductor
C2
Fig. 5 – X-PLUS C external connections scheme.
PE
PE
1
2
3
4
5
6
7
8
A
A -
B
B -
PE
9
10
11
12
13
14
15
16
17
18
19
Dir.
Fault
-
-
STO1
-
-
-Step
V
AC in
20 Monitor
-
MAIN
(230 o 110 V )
AC
V
AC
STO2
SPD
Surge Protection
Device
Torque
5-7 lb in
0.6-0.8 N m
⋅⋅
AWG: min 17 - Max 14
Stranded conductor
Torque
13-22 lb in
1.5-2.5 N m
⋅⋅
C1
MOTOR
SHIELDED CABLE
STEPPING
MOTOR
Drive chassis
earth
Shield
FUSES
EMI FILTER
(section 10.1.1)
see
section 7.2
RESIDUAL
CURRENT
DEVICE
Line
Neutral
AWG:
min 28
Max 20
Stranded conductor
C2
Fig. 6 – X-PLUS S external connections scheme.

R.T.A. s.r.l. – XPCSME03 – 12/20
17/29
8 - INSTALLATION AND ENVIRONMENT
All products considered in this manual have the following common characteristics:
8.1 - Protection degree IP20: it is user responsibility to provide an adequate protection enclosure suitable to
meet the standards regarding the specific application in which the products are used.
8.2 -
CAUTION!
Installation and work environment. Installation is allowed in a micro-environment with:
•
Environment conditions class 3K3
(IEC 721-3-3): that implies, among other things, a working
temperature from +5°C to +40°C and relative humidity from 5% to 85% non condensing.
•
Pollution degree 2
: that implies, among other things, that installation in environments in which
explosive and/or flammable and/or chemically aggressive and/or electrically conductive gas, vapor or
dust could be present is strictly forbidden.
•
Mechanical conditions class 3M1
(IEC 721-3-3).
•
Maximum operating altitude:
2000 meters.
If the environment in which the machine is used does not satisfy these conditions, suitable conditioning
systems have to be provided for the enclosure.
8.3 - Storage environment in original enclosure:
•Temperature: from -25°C to +55°C. Relative humidity: from 5% to 95%.
•Environment conditions class 1K3 (IEC 721-3-1). Pollution degree 2.
8.4 - The drives generate some amount of heat (see chap. 7.1). Take care of this in considering the total
amount of heat generated in the enclosure in which the drives are located. In order to make easier air
circulation in the drive, install the drive vertically (not turned upside down) with at least 5 cm of free
space over and under the drive and 1 cm to the left and the right of the drive. Do not obstruct air
gratings.
9- MAINTENANCE
9.1-
INFORMATION
.
ROUTINE MAINTENANCE.
It needs to check periodically status and installation of the drive:
•Screw tightening torque (suggested torque 0.6-0.8 Nm, 5-7 lb) and correct insertion of input
and output power connectors.
•Correct insertion of logic signals connector.
•Tightening of earth connections.
•Cleaning air gratings both on the chassis and on the heatsink of the drive.
9.2-
FAILURE MAINTENANCE.
In case of failure, the faulty drive must be returned to R.T.A.
Do not try to repair a faulty device. Only R.T.A. personnel is authorized to perform repair operations.

R.T.A. s.r.l. – XPCSME03 – 12/20
18/29
10 - LOGIC INTERFACING EXAMPLES
In this chapter some interfacing techniques are shown. They have to be considered only as examples. The
best way to interface the drive with the control system can be chosen only with a complete knowledge of
control system and application needs.
NOTE:
The following interfacing examples MUST NOT be used with STO1, STO2 inputs and MONITOR
output.
X-PLUS C
X-PLUS S
SERIES DRIVE
OUTPUT
V+
CONTROL
SYSTEM
PNP INPUT
CONTROL
SYSTEM
NPN INPUT
X-PLUS C
X-PLUS S
SERIES DRIVE
OUTPUT
V+
V+ < 45 Volt
Fig. 7 Interfacing a X-PLUS C and X-PLUS S logic output and an input of a control system operating
at V+ voltage.
X-PLUS C
X-PLUS S
SERIES DRIVE
OUTPUT
V+
V+ < 45 Volt
I < 50 mA
Fig. 8 Driving a micro-relay by means of a X-PLUS C and X-PLUS S logic output.
CONTROL
SYSTEM
NPN OUTPUT
X-PLUS C
X-PLUS S
SERIES DRIVE
INPUT
+
V+
5 V
DC
< V+ < 24 V
DC
Fig. 9 Driving a X-PLUS C and X-PLUS S logic input from a control system with a NPN open collector
output.

R.T.A. s.r.l. – XPCSME03 – 12/20
19/29
CONTROL
SYSTEM
PNP OUTPUT
X-PLUS C
X-PLUS S
SERIES DRIVE
INPUT
V+
+
5 V
DC
< V+ < 24 V
DC
Fig. 10 Driving a X-PLUS C and X-PLUS S logic input from a control system with a PNP output.
CONTROL SYSTEM
5 VOLT OUTPUT
INPUT
GND
OUTPUT +
-
X-PLUS C
X-PLUS S
SERIES DRIVE
Fig. 10
-
Connection example with control system with 5 Volt TOTEM-POLE (PUSH-PULL) output.
INPUT
+
+
-
GND
-
CONTROL SYSTEM
DIFFERENTIAL OUTPUT
X-PLUS C
X-PLUS S
SERIES DRIVE
Fig. 11 - Connection example with control system with DIFFERENTIAL output (or LINE DRIVER or
RS422).

R.T.A. s.r.l. – XPCSME03 – 12/20
20/29
11 - APPLICATION NOTES
11.1-
INFORMATION
.
Electromagnetic compatibility (directive 2014/30/CE). X-PLUS C and X-PLUS S series drives are
BDM (Basic Drive Module), as defined in the EN 61800-3. Only a professional assembler, expert in
the field of motor drives and in their EMC aspects, can install and put in service this component.
R.T.A. has the responsibility to verify the products compatibility in some typical way of use in order to
give correct installation information. In any cases, it is responsibility of the professional assembler,
who installs this product, to verify the compatibility of the complete machine or system.
11.1.1- The set consisting of drive, motor, transformer and all related cablings are source of electromagnetic
interferences. The assembler of installation must consider these problems during the project of the
plant where the drive (or drives) will be installed in order to shield and/or reduce these interferences.
Tests performed by R.T.A. show that the most effective measures able to reduce these interferences
are the following:
•Shielding of cables for the connection between motor and drive. The shield of this cable has to
be directly connected to X-PLUS C or X-PLUS S series drive terminal 5. This shielding can be
avoided only in case of very small and compact machine where motor, drive and related
connections are located in the same enclosure, showing adequate shield performance.
•Connect earth line to motor chassis. To reduce the radio-frequency emissions, the mechanical
connection of motor to machine chassis (by means of mounting flanges and screws), is typically
simple and effective solution. In this case, both screws and chassis must be of conductor
material and the chassis must be connected to earth. See Fig. 12.
•Location of drive in a cabinet shielded from electromagnetic interferences.
•Interpose an EMI filter in AC power input line (see Fig. 5) in order to reduce conducted
electromagnetic interferences. Filter characteristics in a specific installation depend on following
factors:
- Strictness degree of the specific standard regarding the machine on which drive is used.
- Power level of application (voltage and current setting of the drive).
- Presence of other filtering systems in the general electrical machine installation.
In any case, following filter type is recommended:
- CORCOM SK series.
Different models inside these series differ for current rating; thereby choose the specific model
according to power level of your installation.
•Consider that the position of the filter in the system is extremely important: no electromagnetic
coupling must take place between electromagnetic source and circuits (and lines). To this end,
filter and main must be kept as close as possible.
•All earth connections mentioned above have to be realized with the less possible inductance.
11.1.2- To improve the drive logic input signals immunity from external noise the following well known
procedures, to manage the relatively fast signals treatment must be considered:
•Use shielded cables.
•Keep signal cables separate from power cables. In particular keep signal cables separate from
motor output cables.
•Carefully verify logic level compatibility when interfacing drive with control system.
This manual suits for next models
1
Table of contents
Popular Control Unit manuals by other brands

Armstrong
Armstrong OB-2000PT Integral Assembly instructions
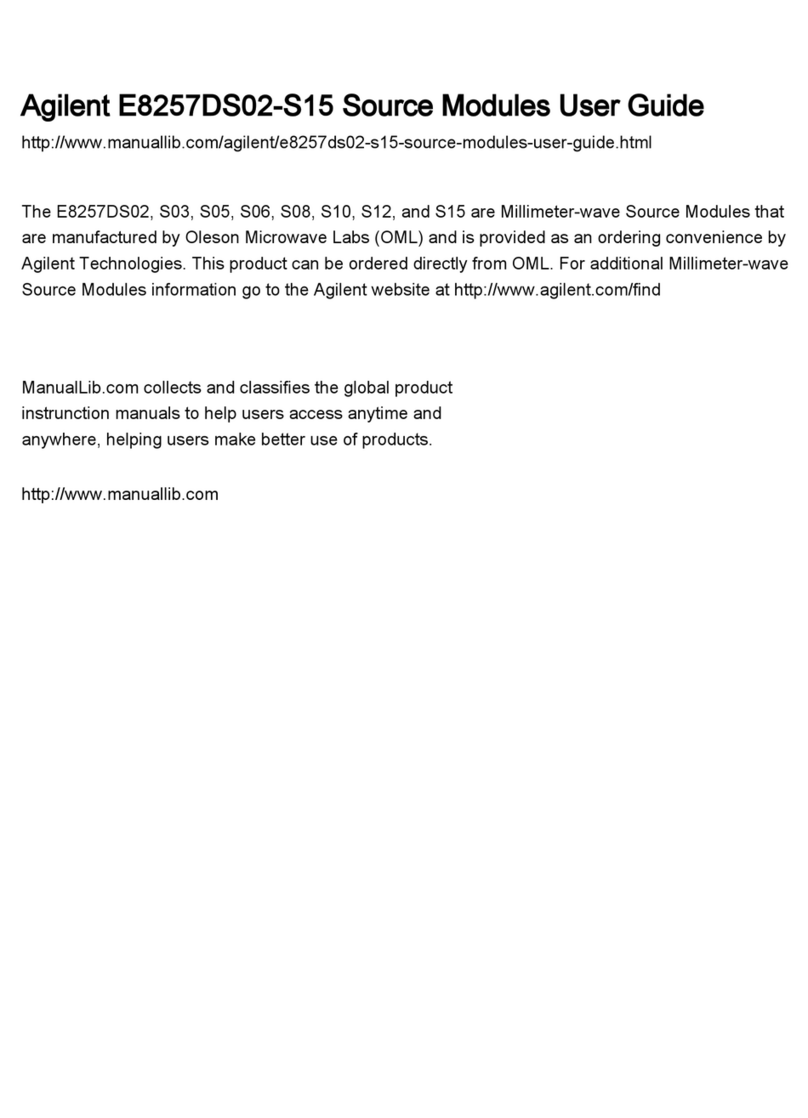
Agilent Technologies
Agilent Technologies E8257DS02 user guide
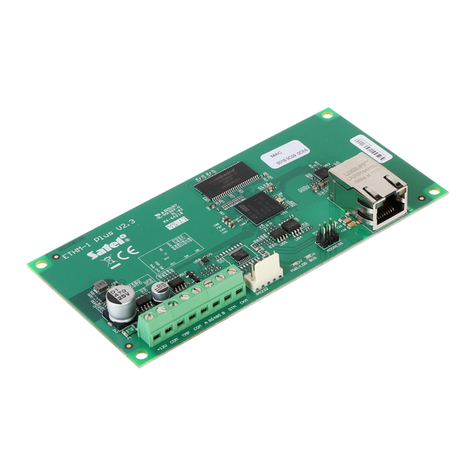
Satel
Satel ETHM-1 Plus manual

Stübbe
Stübbe MV 310 Series operating manual
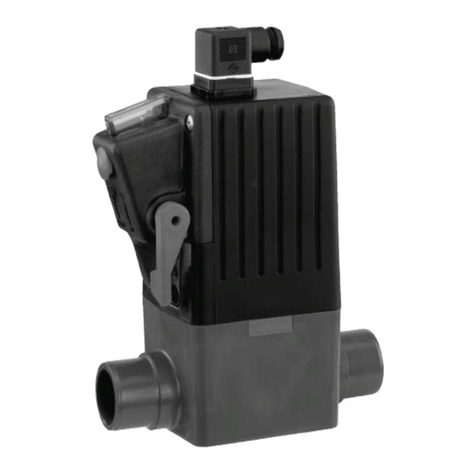
GEM
GEM 225 Installation, operating and maintenance instructions
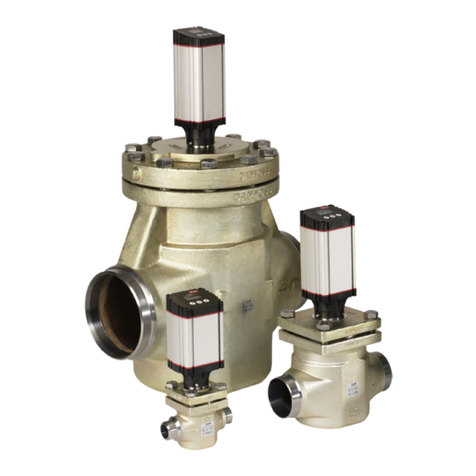
Danfoss
Danfoss ICM 20 Installation, programming, and troubleshooting manual