S2Tech PCS III User manual

Doc. # 310715-001; specifications are subject to change without notice
M:\PCS III CANopen UK\PCS III Technical Description CANopen 1r1 UK 310715.docx
S2Tech-DigiTran
PCS III Displacement
Transducer
PRELIMINARY MANUAL
Technical Description
User's Guide
Configuration and CANopen
Interface
Analog
Output
&
CANopen
S2Tech S.R.L.
Via Imperia 28
20142 Milano - Italy
Phone +39 028910142
Fax +39 0289124848
http://www.s2tech.it

Doc. # 310715-001; specifications are subject to change without notice
M:\PCS III CANopen UK\PCS III Technical Description CANopen 1r1 UK 310715.docx
Contents
1. Document history.........................................................................................................................4
2. CE Declaration of Conformity.....................................................................................................5
3. Characteristics..............................................................................................................................6
4. INSTALLATION HINTS.............................................................................................................7
4.1. POWER SUPPLY .................................................................................................................7
4.2. ABSORBED CURRENT......................................................................................................7
4.3. POWER-ON TIME...............................................................................................................7
4.1. ELECTRICAL CONNECTIONS .........................................................................................8
4.2. ANALOG OUTPUTS...........................................................................................................9
4.3. SUMMARY for FAST CANopen MEASUREMENT.........................................................10
4.4. WORKING PRINCIPLE ....................................................................................................10
4.5. NOT MEASURING DEAD LENGTH...............................................................................11
4.6. MANUFACTURING MATERIALS...................................................................................11
4.6.1. TRANSDUCER MANUFACTURING MATERIALS................................................11
4.6.2. MANUFACTURING MATERIALS FOR PARTS NEAR TO THE TRANSDUCER.
11
4.6.3. INSTALLATION IN CYLINDERS.............................................................................12
4.7. EXTERNAL INSTALLATION...........................................................................................13
5. MAGNETIC CURSORS ...........................................................................................................13
5.1. DIFFERENT CURSOR MODELS.....................................................................................13
5.2. POLARITY OF MAGNETIC FIELD.................................................................................13
6. MAGNETIC CURSORS SUPPLIED BY S2Tech ....................................................................14
6.1. WITH RADIAL MAGNETIC FIELD................................................................................14
6.2. WITH AXIAL MAGNETIC FIELD...................................................................................14
6.3. FREE FLOATING CURSOR..............................................................................................14
6.4. MAGNETS CHOSEN BY THE USER ..............................................................................15
7. FLOATS.....................................................................................................................................16
7.1. INSTALLATION ADVICES...............................................................................................16
7.2. BALLAST...........................................................................................................................16
8. TRANSDUCER INSTALLATION............................................................................................16
8.1. PCS Transducer (S = Standard)...........................................................................................16
8.2. PCP Transducer (P = flanged well ) ....................................................................................17
8.3. PCR Transducer (with slide) ...............................................................................................17
8.4. PRESSURE ACTION ON THE MEASURING PROBE...................................................17
8.5. NUMBER OF CURSORS ..................................................................................................17
9. LIN module setting ....................................................................................................................19

Doc. # 310715-001; specifications are subject to change without notice
M:\PCS III CANopen UK\PCS III Technical Description CANopen 1r1 UK 310715.docx
10. FILTER module setting...........................................................................................................21
11. Analog output module.............................................................................................................21
12. Diagnostic ...............................................................................................................................23
13. CANopen ................................................................................................................................24
13.1. Internal Data Structure.....................................................................................................24
13.2. Definitions .......................................................................................................................24
13.2.1. SYSTEM module (0x10).........................................................................................26
13.3. Node Identification..........................................................................................................28
13.4. Operating Parameters.......................................................................................................28
13.5. System Start.....................................................................................................................29
13.5.1. Initialization state .....................................................................................................29
13.5.2. Pre-Operational state................................................................................................29
13.5.3. Operational state.......................................................................................................29
13.6. Power-On messages.........................................................................................................29
13.7. Estimating transmission time...........................................................................................30
14. Transducer data in the TxPDOs..............................................................................................30
14.1. Error messages.................................................................................................................31
15. Parameterization of the CANopen interface with SDO Services ...........................................31
15.1. Assigning baud rate .........................................................................................................31
15.2. Assigning NodeID ...........................................................................................................32
15.3. Saving the settings...........................................................................................................32
16. Node configuration .................................................................................................................32
16.1. Node identification ..........................................................................................................32
16.2. Mode (type of message transmission) .............................................................................32
16.3. Setting data transmission/update rate ..............................................................................33
16.4. Saving the new settings ...................................................................................................33
17. Object Directory......................................................................................................................34
17.1. Communication Profile....................................................................................................34
17.1.1. CANopen Setup........................................................................................................34
17.2. CANopen Interface Module (0x22)...............................................................................35
17.2.1. PDO Communication...............................................................................................36
17.3. Communication Profile (Tables)......................................................................................37
17.4. Application Module (0x30)............................................................................................43
17.5. NewMag Module (0x33).................................................................................................45
17.6. A/D Converter CS5532 (0x02) ..............................Errore. Il segnalibro non è definito.
18. Parameterization of the Measuring system with SDO Services ....Errore. Il segnalibro non è
definito.
18.1. Measure Update Rate setup.....................................Errore. Il segnalibro non è definito.

Doc. # 310715-001; specifications are subject to change without notice
M:\PCS III CANopen UK\PCS III Technical Description CANopen 1r1 UK 310715.docx
18.2. Output value measurement units .....................................................................................48
18.3. Saving the settings...........................................................................................................48
19. Peak value monitoring ....................................................Errore. Il segnalibro non è definito.
20. Zero Reset operation.......................................................Errore. Il segnalibro non è definito.
21. APPENDIX.............................................................................................................................49
21.1. DigiTran compatibility for non CANopen networks.......................................................49
21.2. Accessing the Object Database using Expedited SDO Protocol.....................................50
22. Operating the CANopen device..............................................................................................52
23. Operation example..................................................................................................................54
24. TERMS OF SALE..................................................................................................................57
24.1. LIMITED WARRANTY .................................................................................................57
24.2. LIABILITY FOR DAMAGES........................................................................................57

Doc. # 310715-001; specifications are subject to change without notice
M:\PCS III CANopen UK\PCS III Technical Description CANopen 1r1 UK 310715.docx
1. Document history
Rev.
Date
Description
FW
HW
Writer
Check
0
23/03/15
First issue
1.0
1.0
SP
FM
1
31/07/15
Single cursor transducer, with analog and digital outputs
2.0
1.0
SP
FM
NOTE:
This manual describes the basic product’s functions referable to the 2.0 firmware version.
Other measurement functions may be available, as option, using specific firmware
versions, as indicated in this document or in the latest revision available on the web site
at www.s2tech.it

Doc. # 310715-001; specifications are subject to change without notice
M:\PCS III CANopen UK\PCS III Technical Description CANopen 1r1 UK 310715.docx
2. CE Declaration of Conformity
Applied Council’s directives: 89/336/CEE modified by directives 92/31/CEE, 93/68/CEE
Conformity to Standards: EMC:
EN 61326-1 (2013)
EN 55011 (2009) + A1 (2010)
EN 61000-4-2 (2009)
EN 61000-4-3 (2006) + A1 (2008) + A2 (2010)
EN 61000-4-4 (2004) + A1 (2010)
EN 61000-4-5 (2006)
EN 61000-4-6 (2009)
EN 61000-4-8 (2010)
EN 61000-4-11 (2004)
EN 61326-2-3 (2013)
Test report reference: 290401-1TRFEMC
Manufacturer: S2Tech srl
Address: via Imperia, 28 Milan (Italy)
Equipment type: Magnetostrictive transducer for position and level
measurement
Model: Magnetostrictive transducer for position and level
measurement
Year of registered mark: 2015
The equipment has been tested in the typical installation configuration, as described by the
instruction manual of the Product.
S2Tech srl certify that the above defined equipment meets the requirements of above mentioned
directives.
Milan, July 16th, 2015
S2Tech srl
Technical Dept.

DIGITAL TRANSDUCER
Configuration and Modbus Interface
PRELIMINARY
PCS III Technical Description CANopen 1r1 UK 310715.docx
09/02/2021
S2Tech srl
6/58
Notice: The information in this manual is subject to change without notice.
S2Tech shall not be liable for technical or editorial errors or omissions contained herein, nor for
incidental or consequential damages resulting from the furnishing, performance, or use of this
material. This manual contains information protected by copyright. No part of this manual
may be photocopied, or reproduced in any form, or translated without prior written consent from
S2Tech s.r.l.
Critical products (1) used in critical devices or systems (2) must be expressly authorized
for such purpose!
S2Tech products may only be used in critical devices or systems with the express written approval of
S2Tech s.r.l.
(1) A critical product is a product used in a device or system whose failure can reasonably be
expected to cause the failure of that device or system, or to affect the safety or effectiveness of
that device or system.
(2) A critical device or system is any system whose failure can be reasonably assumed to endanger
the life or the health of human persons.
3. Characteristics
PCS III transducers allows the following measurements:
A) Cursors position in the internal raw units.
B) Linear displacement of one cursor/floater.
C) Linear displacement of two or more cursor/floater (*).
D) Measurement of the interface between two different cursors (*).
E) Temperature on the measurement’s rod end and on electronics’ head (*).
F) User defined Measurement, obtained using a Linearization Module and an additional Filter
Module, processing the A, B or D measurements, to obtain, in example, a volume
measurement of a tank with a non-regular geometry (using a characterization table with up to
32 - or more - characterization points), or defining a customized measuring range (smaller
than the measuring rod) or calibrating the transducer in order to get the measurement in an
engineering unit different from the one of the Final Test procedure (mm) (*).
G) Measurements (A, B, C, D and F) can be used to drive the analog output.
NOTE:
1) Measurements B, C and D are expressed in 1/100 mm resolution.
2) Measurement A, B and C can be used to drive the analog output.
3) E measurement is expressed in 1/10 °C
4) All Measurements (from A to F), can be obtained through a Modbus connection.
5) The basic position measurements can be used with a Linearization Module, so that User can
define an application specific calibration of the transducer, if needed.
(*) optional function, available on specific product version
The PCS III unit is to be configured using a CANopen connection, using specific software, that is used
to access the parameters (constant) that customize the way the transducer measure, or the
measurements (variables, through SDO or PDO):
For Communication Profile parameterization see Application and Reference part of this manual.
Parameterization distinguishes between transducer-specific and Modbus-specific parameters.
NOTE: analog output type is Factory set –Current or Voltage –and cannot be changed by the
Customer on the field.
Customer cannot modify Factory calibration that provides measurements A, B and C.

DIGITAL TRANSDUCER
Configuration and Modbus Interface
PRELIMINARY
PCS III Technical Description CANopen 1r1 UK 310715.docx
09/02/2021
S2Tech srl
7/58
Programmable Displacement parameters:
–Setting working parameters for conversion of measurement from internal AD raw point, into the
desired engineering units (1/100 mm resolution). These parameters are Factory set, with the Final
Test procedure prior delivery of the units. These parameters cannot be modified.
–Setting working parameters for conversion of measurement from displacement measurement
(1/100 mm resolution) into the desired Customized engineering units, through the optional use of
the Linearization Module.
- Setting working parameters of the optional Filter Module, if filtering is needed like when waves in
the liquid can disturb the measurement representation.
–Setting of zeroing of the measured position, through the Tare value (VTara parameter)
–Setting analog output working parameters, if hardware installed as for Customer’s order.
Modbus communications parameters:
–Setting Baud rate
–Setting Node ID
4. INSTALLATION HINTS
4.1. POWER SUPPLY
Series PC electronics is equipped with built-in voltage regulators that allow transducers to re-
ceive a power supply of 24 VDC, ±15%.
To guarantee correct operation, the supply voltage must be stabilized and filtered.
Calibration and testing are done in the Factory at 24 VDC.
Interconnecting cables must be of size that can support currents at least of 0,4 A.
To reduce external electrical interference, the power supply must satisfy EC standards and
thence be contained within a metal casing with also shielded and grounded supply cables.
4.2. ABSORBED CURRENT
Power consumption is to be expected between 50 and 100 mA @ 24 Vdc, depending from
transducer’s working condition.
Maximum peak inrush current around 200 mA
4.3. POWER-ON TIME
When unit is powered it is needed around 2 seconds from the power on (for auto-diagnostic and
loading of the working parameters), to have the full functionality of the product, being in position
to provide a valid measurement on the digital and analog output. Until the unit is fully operative,
analog output is to be considered non valid and generally will assume a 0V or 0 mA state.

DIGITAL TRANSDUCER
Configuration and Modbus Interface
PRELIMINARY
PCS III Technical Description CANopen 1r1 UK 310715.docx
09/02/2021
S2Tech srl
8/58
4.1. ELECTRICAL CONNECTIONS
Warning:
Avoid soldering activities nearby the transducer or a network of such transducers.
NOTE: the transducers can be connected to other type of fieldbuses, using specific gateways that can
be provided and configured by S2Tech, allowing a wider use of such products.
It is also possible to use units with wireless connection, using WiFi / Bluetooth or other proprietary
means of wireless transmission.
Please refer to the specific product’s drawing for overall dimensions.
Cable Color
(DIN47100)
Cable Pairs
M12 connector
Meaning
Blu
Pair 1
2
Power Supply GND
Red
1
Power Supply + 24 Vdc
Gray
Pair 2
7
CAN_L
Pink
6
CAN_H
Brown
8
CAN GND
Yellow
Pair 3
5
Analog Output GND
Green
3
Analog Output Signal
Note 1: inside the transducer, CAN_GND and Analog GND are in common.
Note 2: We suggest that the digital connection to the instrument should performed using twisted
pairs shielded cables that are specifically designed for data transmission applications.
Note 3: inside the transducer no line termination resistor is installed, so an external line terminator
has to be installed at both ends of the communication line, between the Master and the Slave, in
order to avoid errors.
Pinning installed M12 male connector 8 poles, front view / male
side view (Coding A)
Cable Shield is connected internally to the transducer’s housing
and is to be connected to a good earth reference at the free end.
In case of Plug option, please verify that cable shield is connected
to the housing of the transducer.
Reference = CiA DR-303-1
In order to have good performances it is strongly suggested to:
•Follow connection recommendations from official Technical CAN guidelines
•Terminate transmission line with 120 Ohm terminators
•Use appropriate shielded cables with twisted pairs used:
One twisted couple for CAN_L and CAN_H
One twisted couple for Power Supply + and Power Supply GND
Can GND can stand alone, using and additional twisted couple
•Remember that communication cable must avoid bifurcations and long stubs.
•Allowed connection topology is linear connection between all devices

DIGITAL TRANSDUCER
Configuration and Modbus Interface
PRELIMINARY
PCS III Technical Description CANopen 1r1 UK 310715.docx
09/02/2021
S2Tech srl
9/58
4.2. ANALOG OUTPUTS
The analog output –if ordered - is Factory configured, as type (voltage/current) and range:
a) From 0 to + 10 V.
b) From 0 to + 5 V
c) From 4 to 20 mA.
d) From 0 to 20 mA.
Note: custom ranges are configurable to values lying between the above indicated standard val-
ues.
It is possible to match the analog output to one of the measurements available from the
transducer (straight or reversed) configuring the unit through the digital Modbus connection.
For voltage output, a signal of 0.00Vdc is not obtainable as the transducer is supplied with only
positive voltage. The minimum voltage is about 50 mV (typical).
Analog output slope is User configurable as needed by Customer.
Voltage output: in order to have a quality measurement, avoid a flow of current on the Analog GND
(current that may be referable to the power supply or to the CANopen communication line).
Typical output impedance on Voltage output is 22 Ohm (with active compensation from the internal
DAC, up to 1 V, so that through feedback the voltage output available by the User is compensated for
the internal 22 Ohm resistor). Maximum output current is 10 mA.

DIGITAL TRANSDUCER
Configuration and Modbus Interface
PRELIMINARY
PCS III Technical Description CANopen 1r1 UK 310715.docx
09/02/2021
S2Tech srl
10/58
4.3. SUMMARY for FAST CANopen MEASUREMENT
If transducer has been ordered with analog output (voltage or current), it has been Factory set as
Zero and Full Scale signal values.
This chapter indicates, in summary, the location of the measurement data that can be of first interest
for measurement or calibration purposes, using SDO object on CANopen, considering a default
transducer’s configuration:
Ref.
Data of interest
Index
reference
Note
A
Displacement Cursor 1
0x2001 5
1/100 mm resolution, near
measurement rod tip (Net
value = Gross –Tare)
B
Displacement Cursor 2 (if appropriate
Firmware is installed)
0x2001 13
1/100 mm resolution, between
Cursor 1 and electronic head
(Net value = Gross –Tare)
C
Interface (if appropriate Firmware is
installed)
t.b.d
1/100 mm resolution, as
Cursor 2 - Cursor 1
D
Linearized measurement Cursor 1
(if appropriate Firmware is installed)
0x2008.2
Result of interpolation on
Linearization table, using A,B
or C measurement as input
E
Filtered measurement
(if appropriate Firmware is installed)
0x2009.2
Measurement filtered from A,
B, C or D data
F
Tip Temperature(if appropriate Firmware
/ Hardware is installed)
0x2001.1C
1/10 °C, indicative
measurement
Note: the unit can be customized using Modbus connection, in order to obtain different configurations
and measurement combination, than what is indicated in the above table.
4.4. WORKING PRINCIPLE
An electrical pulse is injected into the waveguide contained in the probe. This pulse generates a
corresponding magnetic pulse, which then links onto the magnetic field of the magnets contained
in the cursor and generates a magnetostrictive mechanical torque pulse.
This mechanical pulse is generated along the wave guide at the velocity of sound found in metals
(about 2800 m/sec) until reaching the sensor positioned in the head inside the electronics. The
cursor position is calculated by measuring the time lapse between the electrical pulse and the
return mechanical pulse

DIGITAL TRANSDUCER
Configuration and Modbus Interface
PRELIMINARY
PCS III Technical Description CANopen 1r1 UK 310715.docx
09/02/2021
S2Tech srl
11/58
4.5. NOT MEASURING DEAD LENGTH
The dead length refers to the stretch at the very far end of the measuring probe where there is
either no measurement or the measurement does not satisfy the technical specifications of the
transducer.
Series PC certificates indicate dead length values.
Probe end (A) dead length (see certificate) is generally used for mechanical anchorage of the
probe itself.
Should you require an improvement on standard linearity, you are advised to consider an
adjunctive “dead length”, of about 20 – 25 mm, positioned near the measuring head.
4.6. MANUFACTURING MATERIALS
4.6.1. TRANSDUCER MANUFACTURING MATERIALS
The working principle requires that the manufacturing materials of the probe (cylindrical rod), the
hexagonal part and relative fastening nuts of the head and the floats be made of non-magnetic
materials.(=NM=diamagnetic).
For models bearing the suffix (-S), the probe and the union are made of AISI 316 L stainless
steel. The measuring head casing is made of die-cast aluminum alloy.
For models bearing the suffix (-A), we have aluminum alloy instead of steel.
4.6.2. MANUFACTURING MATERIALS FOR PARTS NEAR TO THE TRANSDUCER.
In order to have transducer to work correctly, the magnetic field of the cursor must close across
the magnetostrictive guide inside the transducer, even in the end areas of the A probe and near
the head.
Permanent external magnetic fields generated by other magnets or residual magnetic fields,
generated from the cursor coming into occasional contact or proximity of magnetisable materials
(paramagnetic materials), can affect the measurement.

DIGITAL TRANSDUCER
Configuration and Modbus Interface
PRELIMINARY
PCS III Technical Description CANopen 1r1 UK 310715.docx
09/02/2021
S2Tech srl
12/58
4.6.3. INSTALLATION IN CYLINDERS
You are advised to install the transducer considering Figure 1. Transducer’s installation as for
Fig. 2, where the surrounding parts are made of magnetic material (= M: soft metal, usually
steel), should be considered very carefully and possibly avoided if all the aforementioned condi-
tions are to be respected.
The recommended distances (= limit) are indicated in Fig. 2 (in mm).
A max. = 1/8 of the diameter (outside ) of the cursor

DIGITAL TRANSDUCER
Configuration and Modbus Interface
PRELIMINARY
PCS III Technical Description CANopen 1r1 UK 310715.docx
09/02/2021
S2Tech srl
13/58
4.7. EXTERNAL INSTALLATION
Installed with brackets, clamps etc.: all the brackets and the hexagonal head fastening nut must
be made of non -magnetic material (=NM = non-magnetic: aluminum, brass, AISI 300 series
stainless steel).
5. MAGNETIC CURSORS
Figures 3, 4 and 5
5.1. DIFFERENT CURSOR MODELS
They include: magnetic rings, floats, slides (if PCR transducer is considered).
All these models include: built-in magnets whose magnetic field may be radial or axial with refer-
ence to the magnetostrictive waveguide axis.
In order to work, it is essential that their magnetic field is sufficiently high and it is entirely coupled
along the waveguide.
5.2. POLARITY OF MAGNETIC FIELD
Magnetic field polarity is established by the Manufacturer of the Transducers. No other polarity
values are permitted as they might jeopardise performance. For this reason, be sure to follow in-
dications in Figures 3-4-5.
IMPORTANT
Cursors, magnets or float, not produced by S2Tech and chosen by the Customer must be sent to S2Tech, in order to be checked. S2Tech, if possible, will custom
calibrate the transducer with them.
Customer must tell to S2Tech the application conditions: used materials , pole position, distance between magnets and probes etc..
For further supplies it is advisable to always have S2Tech keep a sample.

DIGITAL TRANSDUCER
Configuration and Modbus Interface
PRELIMINARY
PCS III Technical Description CANopen 1r1 UK 310715.docx
09/02/2021
S2Tech srl
14/58
6. MAGNETIC CURSORS SUPPLIED BY S2Tech
6.1. WITH RADIAL MAGNETIC FIELD
These are ring models: ARR-1E; ARR-2E; ARR-3E.
They consist of rare earth cylindrical magnets, radial to the probe and contained inside polyamide
plastic or aluminum rings.
Polarities are shown in Fig. 5.
The ring works correctly regardless of which side of the ring is pointed towards the measuring
head.
The cursor can be fixed with glue or non-magnetic screws (AISI 300 series stainless steel, brass,
etc..)
Take care to apply instructions given in figure Fig. 1 –2. The space “C” in Fig. 2 can be filled with
a non-magnetic material. (e.g. aluminum).
6.2. WITH AXIAL MAGNETIC FIELD
Ring toroid (Fig. 3): They are from ARA-5F models to ARA-10E models.
Toroid Cursors with opposing poles on the two base planes.
Important: in order to work correctly it is necessary that the polarity towards the measuring heads
corresponds to the one indicated in Figure 3.
The material (ferrite (= F) or rare earth (=E) ) is hard and delicate. It cannot be drilled and must
be fixed with glue, preferably inside the relative housing or with an adapter made by the User.
6.3. FREE FLOATING CURSOR
Model AFR-1E –(Figure 4A ):
It contains two parallel magnets arranged in radial fashion on a plate made of non-magnetic
material, supplied with central fixing holes.
The distance from the AFR-1E cursor and the measuring probe must be 5mm with a ±1mm
tolerance.
After having clamped the cursor within the above mentioned tolerance, when moving along the
probe, It must nonetheless maintain a 0,2 mm maximum fluctuation from the probe.
These distances must be constant along all the measuring stroke onto the mod. PCR
transducers.
Whenever the distance is bigger than 6 mm, there is not enough magnetic field magnitude to
recognize the magnetic cursor position.

DIGITAL TRANSDUCER
Configuration and Modbus Interface
PRELIMINARY
PCS III Technical Description CANopen 1r1 UK 310715.docx
09/02/2021
S2Tech srl
15/58
Figure 4A
The PCR transducer is Factory calibrated with the distances indicated as the above image.
When Mod. PCR is used together with AFR-1E floating cursor, It is calibrated in order to have a
measuring stroke in the middle of two death zones A= 30 mm and C= 25 mm (Figure 4A ).
The AFR-1E can pass over these two “A” and “C” death zones without causing any damage but
analog outputs will assume the value expected by the calibration at the C end of the
measurement range, while the CANopen connection will indicate the cursor lost status, if the
cursor is not detected.
For performance optimization, the Customer must supply S2Tech with all the installation
conditions
6.4. MAGNETS CHOSEN BY THE USER
It must have a high magnetic field, invariable throughout time and with a high maximum working
temperature. The lobe of the magnetic flow must be wide enough to interest the magnetostrictive
waveguide. Polarity must be as indicated in Fig. 4.
Mark the North Pole with a colored dot.
You are advised to use permanent rare earth magnets for temperatures up to 120°C, with
diameters of 5÷8 mm and lengths of 10÷20 mm.
The magnetic field is considered to be sufficient when the measurement, controlled in the
Factory, occurs near the dead length “A” of the probe end and at all the points along the
measuring stroke.
The magnets must be sent to the Factory for performance optimization, indicating how they are
used toward the transducer.

DIGITAL TRANSDUCER
Configuration and Modbus Interface
PRELIMINARY
PCS III Technical Description CANopen 1r1 UK 310715.docx
09/02/2021
S2Tech srl
16/58
7. FLOATS
7.1. INSTALLATION ADVICES
•The magnet inside the float (usually in the middle or on the top) is placed towards the meas-
uring head: in order to reduce or cancel (Fig. 3) the dead length (A) of the probe end.
The top of the float closer to the magnet is marked by a coloured dot, or is marked “ALTO”.
•When the float is used in the liquid, it must remain upright in order to reduce probe contact
friction and avoid possible measuring errors resulting from different positions that may be tak-
en up, with respect to the measuring probe.
7.2. BALLAST
For measurement (Fig. 3) of two liquids with different specific gravities, in a tank with two floats,
be sure that the float has been “sunk”.
Drill a tiny hole (1÷1,2 mm max). Introduce as much lead or heavy liquid that is re-
quired. Then weld the hole close.
8. TRANSDUCER INSTALLATION
NOTE 1): Radial movements of the probe, with respect to the cursor or vice versa, due to
vibration, shocks or not good axial alignment of the probe, do not have a great effect on
measuring.
NOTE 2): The PCS and PCP models are supplied in two versions: in one version the parts which
come into contact with liquid are made of stainless steel and welded to one another (suffix: –S)
and in the other version these parts are made of aluminum and glued to one another (suffix: - A).
In the aluminum version (-A), great attention must be taken to prevent vibration, shocks or
overpressure that could damage the transducer.
8.1. PCS Transducer (S = Standard)
The measuring probe is fitted with a threaded union.
The thread is: M 18 x 1,5. The thread on the fixed side ( on the base of the hydraulic actuator,
on the tank) can have cylindrical or conical sealing.
The sealing must be effected with an O-Ring inserted in the union or in the fixed part.
When the probe is very long (more than one meter), It is advisable to take special constructive
provisions to prevent undesired excessive probe wavering (more than 1-2 mm) or swinging due
to vibration and shocks.
It is to be considered the possibility of using a magnetic cursor with a radial slotting system (Mod.
ARR-2E) through which It can pass the probe anchorage.

DIGITAL TRANSDUCER
Configuration and Modbus Interface
PRELIMINARY
PCS III Technical Description CANopen 1r1 UK 310715.docx
09/02/2021
S2Tech srl
17/58
8.2. PCP Transducer (P = flanged well )
The probe (well) and the threaded union connected to it are previously installed in the hydraulic
cylinder or in the tank so that there is no need to disassemble them should the transducer need
servicing.
The waveguide (together with the measuring head) is inserted in the well and the head is
clamped to the hexagonal flange of the well union.
Assembly of PCP model is similar to PCS model.
IMPORTANT: the waveguide must be always kept straight and any bending on the axis
exceeding 10 mm per meter will irreversibly damage the wave guide. This kind of damage can be
easily found out by S2Tech and is not covered by the warranty.
NOTE: during installation or removal of a transducer equipped with threaded union (PCS, PCP,
PCM), use only the hexagon for clamping.
NO CLAMPING TORQUE MUST BE APPLIED TO THE CASE CONTAINING THE
ELECTRONICS. USE THE HEXAGON.
8.3. PCR Transducer (with slide)
The transducer is supplied with two fixing bases with plastically insulated suspensions.
Remember to ground measuring head pin.
8.4. PRESSURE ACTION ON THE MEASURING PROBE
The outside pressure has a radial direction on the external wall of the probe itself and axial on
the tip of the probe (A) (fig. 3).
Radial action tends to reduce (= press) the circular walls of the probe but has no significant effect
on the measurement.
The axial action of the pressure on the tip of the measuring probe (A) tends to reduce its length.
This is also generally negligible.
8.5. NUMBER OF CURSORS
The transducers can be configured –with the appropriate firmware - in order to measure the
cursor’s position for up to 4 cursors / floaters on the measuring rod.
In case where, during operating, the configured cursors are not present –or are too near each
other - on the measuring rod, the unit will signal this through:
•analog output: in case no cursors are detected on the measurement’s rod, the output value
goes to the analog output signal (voltage or current) expected on the tip of the transducer.
•serial output: the absence of the expected cursors is signaled by the diagnostic of the unit,
that is not in position to recognize which cursor is lost. This means that if the unit is configured
for 3 cursors (in sequence, starting from the electronics’ head A, B and C) and on the rod, on-
ly two cursors are detected (A and C):
•the diagnostic will indicate a lost cursor condition
•the measurement that will be updated will always be the first and second, meaning that
the C cursor will shift, at the Modbus index, where the B measurement is expected.

DIGITAL TRANSDUCER
Configuration and Modbus Interface
PRELIMINARY
PCS III Technical Description CANopen 1r1 UK 310715.docx
09/02/2021
S2Tech srl
18/58
The minimum distance between the two cursors, in order not to interfere one with the
other is 100 mm (Aluminum cursor) or 120 mm for standard floaters.
Smaller distances can generate interference between magnetic fields and there is even the pos-
sibility to have errors or to lose the detection of one of the cursors or detection of more cursors.

DIGITAL TRANSDUCER
Configuration and Modbus Interface
PRELIMINARY
PCS III Technical Description CANopen 1r1 UK 310715.docx
09/02/2021
S2Tech srl
19/58
9. LIN module setting
PCS III transducer, has the possibility to apply - on the displacement measurements - a conversion into an
Engineering unit (Dependent Measurement ) that is different from the one used when the transducer has
been Factory calibrated (Independent Measurement).
This is obtained using an integrated Linearization module that performs the conversion task using up to
32/64 characterization points, that must be entered by the User to describe the relationship between the
original measurement (independent variable, X) and the derived data that results from the computation
(dependent variable, Y).
To modify the corresponding parameters, the CANopen connection is used.
The characterization points may describe a linear relationship between the X and Y variables or may
describe a non-linear relationship, like when on a level measurement there is the need to convert a linear
displacement measurement (vertically installed transducer) into a volume measurement, considering a
circular shape of a tank (or a tank with a non-regular shape).
The linearization module, in this latter case will consider the circular shape as a sequence of straight lines
that will represent the internal profile of the tank, with an approximation.
The use of a high number of points to characterize the shape will reduce the over mentioned
approximation.
It is also possible to use this module to define a proportional or inverse relationship between the
Independent measurements (X) and the dependent ones (Y), or to shift the measurements, just by defining
a relationship on the endpoints.
Table of contents
Other S2Tech Measuring Instrument manuals
Popular Measuring Instrument manuals by other brands
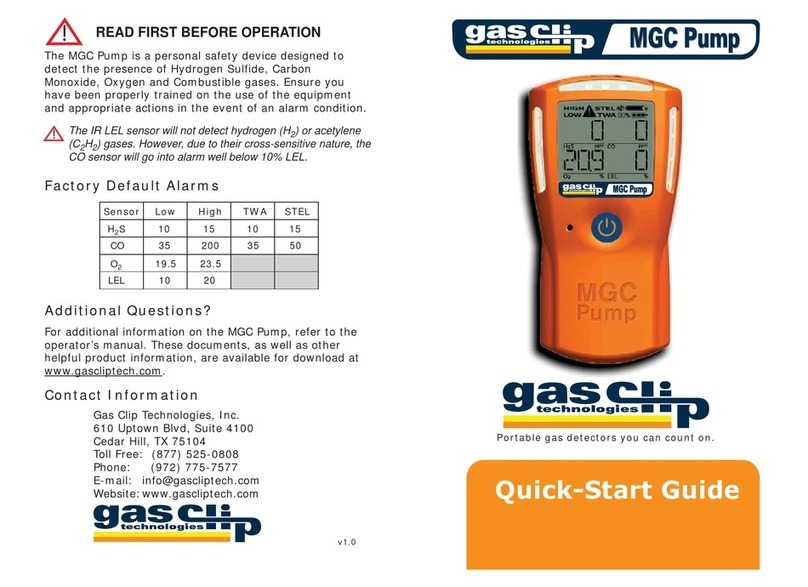
Gas Clip Technologies
Gas Clip Technologies MGC Pump quick start guide
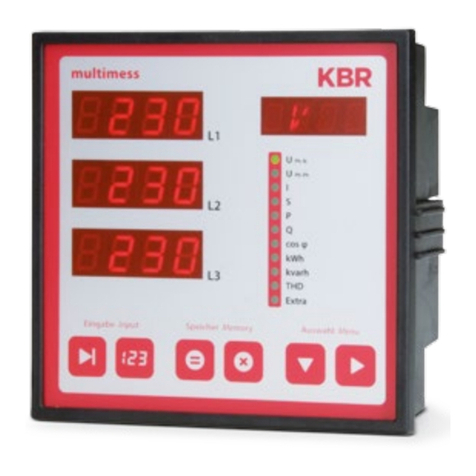
KBR
KBR multimess F144-0-LED 5 Series User Manual Technical Parameters
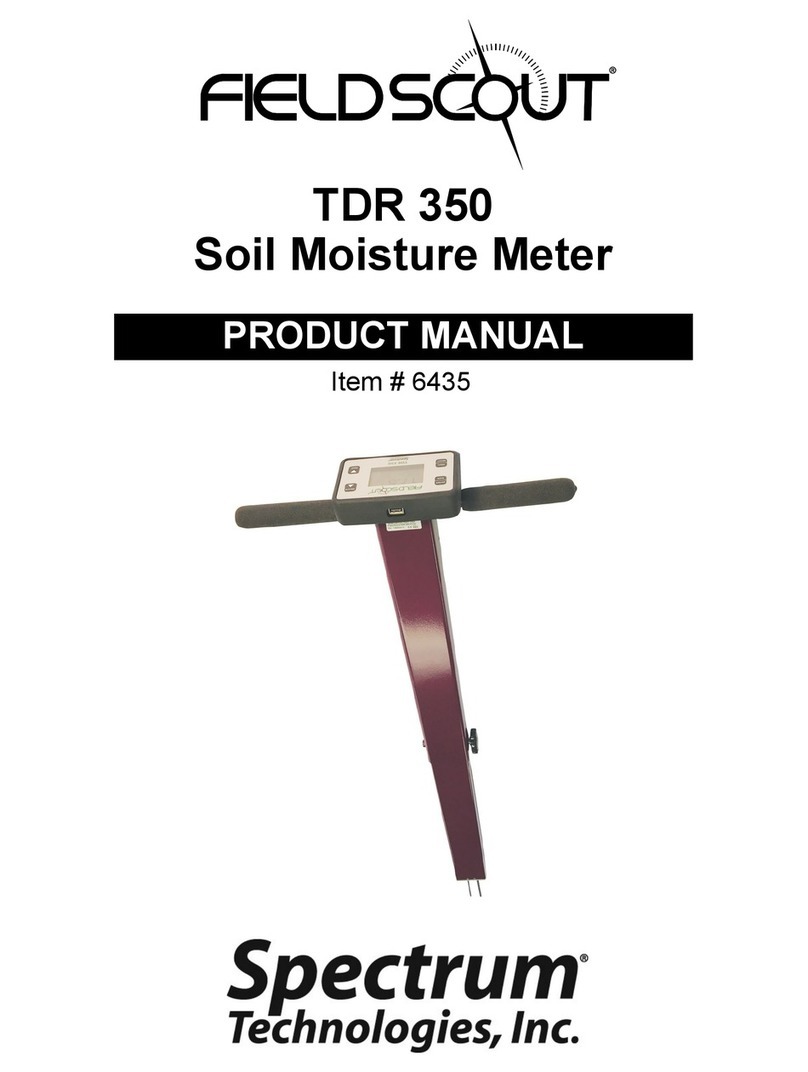
Spectrum Technologies
Spectrum Technologies Field Scout TDR 350 product manual

OptoTest
OptoTest OP740 quick start

Pasco Scientific
Pasco Scientific PS-2235 reference guide
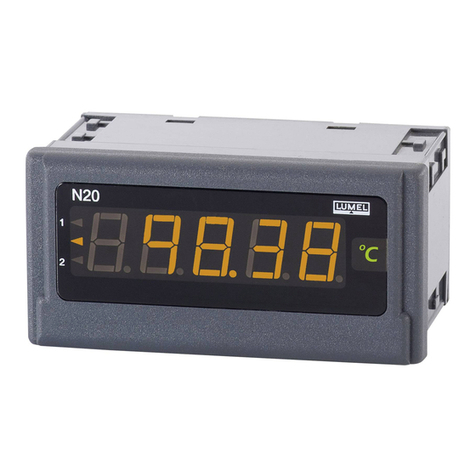
Lumel
Lumel N20 User Manual & Quick Start