S2Tech 699Plus Use and care manual

699Plus – New Functions – FIRMWARE UPDATE
Troubleshooting function
s
S2Tech srl Via Imperia, 28 Milano – ITALY
Tel: +39 02 8910142 Fax: + 39 02 89124848
e-mail: [email protected]
www.s2tech.it
Versione : UK 1r1 dated 13/04/21
Page: 1/2
Notice: The information in this manual is subject to change without notice.S2Tech shall not be liable for technical or editorial errors or omissions contained herein, nor for incidental or consequential damages resulting from the furnishing, performance, or use of this material. This manual contains information protected by
copyright. No part of this manual may be photocopied, or reproduced in any form, or translated without prior written consent from S2Tech. Z:\Manuali\699Plus 2k17\699Plus Troubleshooting Functions Fw 1.41 UK 130421.docx
During system’s calibration it can happen that the lift
installer has unsatisfying calibration due to errors in
performing the calibration procedure or due to the
way lift has been installed or for wrong installation of
the measurement system (wrong placement of the
sensor with poor sensitivity to load variations, etc).
The above conditions can be detected as
measurements with poor repeatability or larger than
expected measurement errors, or errors indicated on
699Plus display.
Messages can be:
a) indications to the installer, that something is
not as ideal for the correct working of the
measurement system, without blocking the lift
b) error messages indicating that performed calibration cannot grant a conversion of the internal
measurement into trustable weight indication, blocking the measurement system
c) error messages indicating a calibration where the internal AD converter is not working, for the
expected measuring range on its working area
A) Calibration concepts:
• To calibrate 699, MANU procedure needs to acquire the coordinates of two points, to define the
conversion function between the measured signals (expressed in internal AD points) and the
reference load.
• TARE: empty cabin.
• HI: cabin loaded with a load as near as possible to the lift’s maximum capacity.
• After a calibration, at the reboot, calibration parameters are verified to check the correctness of
the conversion in the selected engineering units, signaling (with Error codes Er.XX) the
measurement conditions that may lead to non-consistent conversions.
• If 699 Plus indicates an Er condition, Tare and HI parameters can be substituted with a new set of
coordinates with a new calibration.
Some common calibration mistakes:
942 Strain Link is installed on the neutral axis of a bending beam, having not enough signal
variation (as percentage) corresponding to load changes
Structure is too stiff, or Strain link is not correctly fixed on the structure surface (screws not
tightened, paint / rust as interface on the mounting surface, elastic washers used instead of supplied
plain washers, etc.)
MRL Multirope sensor is installed on the counterweight rope side and measurement is not in
position to represent - with enough percentage change - the changes of the applied load
MRL Multirope sensor has been installed with screws not correctly touching the inside of the
deflection bar (see instruction manual)
Electrical connections are not properly done, since no percentage changes are shown when load
changes.
Car floor is installed on TSP sensors but touches other structures
Excessive friction between the guides and the sliding guide shoes is indicated by a suddenly
increase of the value when car starts to move, that then stabilize at lower values.
Problems of guide geometry can be associated to sudden changes in the displayed value, when car
is moving on the shaft
Etc
In the event of an excessive load, which saturates the input of the instrument, Er.28 will appear on the
display.
B) To understand the situation, the following error messages indicates:
ER.01
Negative measurement. ER01 indication is displayed alternatively to the measured weight
(polarity is indicated only with 3 digits values, i.e. -999) – verify zeroing with C key,
electrical connection and system calibration.
Available from firmware version 1.37
ER.22
High load sensitivity. Verify that calibrated [C] screws correspond to rope’s diameter
and that no ropes overlap
HI(AD)-Tare(AD)/ HI(Kg)-TARE(Kg) > 500 bit/kg
Conversion slope not correct: Verify that HI value is entered with the right resolution (use
weight at least 80% FSCA).
ER.23 HI value is too low (in engineering units).
HI
-
Tare must be > 10
ER.24 Known load for calibration is too low. Increase load.
HI(AD)
-
Tare(AD) <100
ER.28 Overflow state detected for ADC (positive or negative) during normal measurement.
In case that AREL parameter (available on SERV menu, default = 0) is set to 1, this error
condition will activate relay
the greatest percentage,
blocking the lift
.
ER.30 Pushbutton detected as continuously pressed at the end of the calibration procedure (reboot)
ER.FF ER.FF can be shown after calibration and reboot of the unit, if the calculated ADC points
corresponding to the greatest LEV percentage (Lev1, Lev2 or Lev3) multiplied by FSCA
value is greater than the working limits for the ADC.
ER.FE or ER.FD can be shown after calibration and reboot of the unit, if the calculated
ADC points corresponding to HI / Tare is greater / lower than the working limit for the
ADC.
In case that AREL parameter (available on SERV menu, default = 0) is set to 1, this error
condition will activate relay
the greatest percentage,
blocking the lift
.

699Plus – New Functions – FIRMWARE UPDATE
Troubleshooting function
s
S2Tech srl Via Imperia, 28 Milano – ITALY
Tel: +39 02 8910142 Fax: + 39 02 89124848
e-mail: [email protected]
www.s2tech.it
Versione : UK 1r1 dated 13/04/21
Page: 2/2
Notice: The information in this manual is subject to change without notice.S2Tech shall not be liable for technical or editorial errors or omissions contained herein, nor for incidental or consequential damages resulting from the furnishing, performance, or use of this material. This manual contains information protected by
copyright. No part of this manual may be photocopied, or reproduced in any form, or translated without prior written consent from S2Tech. Z:\Manuali\699Plus 2k17\699Plus Troubleshooting Functions Fw 1.41 UK 130421.docx
In addition to the error messages, the following troubleshooting functions can be used, depending
from the firmware installed on the unit.
C) DELTA view: Firmware: any
Already on older firmware versions it is possible to display the difference between the HI and TARE
calibration points – expressed as internal AD points:
1) Power-on / Reboot the 699+ keeping pressed the + E pushbuttons, until the display shows :
2) P.xxx
3) Press button to display r.yyy value
4) Take note of both xxx and yyy values, as xxxyyy is the difference between HI and TARE
5) Xxxyyy value gives indications about the sensitivity of the measurement element (sensor or Sensor
+ mechanical media like ropes, car metal frame, underfloor sensor) to the applied load used during
the calibration procedure of the measurement system.
Calibration Sensitivity = Xxxyyy /(HI - TARE).
Typical working calibrations have around 100 points/Kg
The above can be useful to have an idea of the sensitivity to the load of the measuring element (i.e 942
Strain Sensor attached to the metal frame of the car), or to verify the reason of an Er.24 (perhaps because a
MRL Multirope sensor was installed on the counterweight side of the ropes, or because the during
calibration Tare and Hi measurements were acquired with the same load inside the cabin, or the sensor
was not properly electrically connected to the instrument). For MRL installation a value lower than
typical can signal the need to increase the deflection of the ropes (with shorter screws), while a greater
value can indicate the need to decrease deflection (using longer screws), to avoid overloading of the
sensor. Please refer to the instruction manual specific for Your transducer or contact S2Tech, with the
troubleshooting data.
D) PERCENTAGE view: Firmware: ≥1.41
During the Final Quality Test, performed individually on each 699Plus Weight Controller - prior to
delivery - the calibration done is stored permanently inside the unit and is used, as reference, to display
live measurement independently from Installer’s calibration. Measurement is displayed - as percentage -
of the stored Reference Calibration and is used to show the live measurement, when lift is loaded and/or
unloaded.
Reference Calibration is performed at S2Tech with a sample load cell, acquiring the values of TARE and
HI while using a reference weight of 1.000 gram (corresponding of approximately 1.81mV analog signal)
and is stored in the memory of the device, independently from customer’s own calibration.
When 699Plus is set for PERCENTAGE view, measurements are not depending from Customer’s
calibration and are displayed as a percentage of the Reference Calibration.
Displayed value can range ±9999 (no decimals, with negative values indicated as 9999.)
With this view it is possible to understand if changes in the load correspond to changes in the percentage
value (so electrical connection is ok) or if they are enough wide to grant a correct calibration in the
engineering units chosen for the calibration.
1) How to activate the Troubleshooting function
At any time press for at least 5 seconds the Epushbutton, until 699Plus display shows tbls and a
measurement followed by a blinking comma at the rightmost bottom of the display.
Percentage displaying view is now active and can be recalled:
– during normal measurement
– in case of an error message
With this function it is also possible to show the internal AD points corresponding to the difference of HI
– TARE, as result of Installer’s calibration:
– Press pushbutton, to display n.abc value (as number)
– Press pushbutton to show r.def value
– a,b,c,d,e,f are numbers and their sequence abcdef, represents the range of AD points
resulting from Installer’s calibration. The abcdef value is to be communicated to S2Tech,
in case of technical assistance.
– Press the Cpushbutton to return to the currently set display model.
If measurement is negative, a decimal point on the bottom right side of the display is powered on
continuously (i.e. like when friction is “holding” lift in position, when ropes are released when cabin must
move down on the shaft).
To get back to standard measurement, keep pressed the Epushbutton, until on 699Plus display OPmd
again the measurement obtained, as result of Your calibration procedure.
E) Reset working parameters: Firmware: ≥1.41
In case Installer messed up working configuration parameters and behavior of the unit is unpredictable, it
is possible to reset to default all the parameters using the following procedure:
1) Power-on / Reboot the 699+ keeping pressed the ++ C pushbuttons, until the display shows
EClr
2) Use and to display CLrA
3) Press E to enter the password protection, so to be in position to enter the input field to set the
number that will enable the reset procedure
4) When display shows 0, use and pushbuttons to set the password that S2Tech supplied You
for this purpose
5) PASS is shown, to indicate that system accepted the password
6) Use and to display dFLT and press E to display current parameter “0”
7) Set dFLT to 1, using arrows, to confirm the activation of the reset function.
8) Press C to exit and after SAVE is shown and instrument resets, the unit is set to default parameters
After this procedure the percentage view parameters are still available, but any previously change to the
699 configuration is lost.
NOTE: when You recall this function, avoid any power loss to the system and do not press the reset
pushbutton until the procedure ends by itself with a reboot of the unit. Any interference during this
procedure will lead to a not working unit.
F) Instruction manuals download page
Instruction manuals of our products can be downloaded or viewed form the web
using the following link. On the new instruction manuals or on the usual labels
applied on the instruments, You will find a datamatrix code like the one on the
right, that if scanned brings Your mobile device directly to the manuals page.
https://s2tech.it/699plus/
Date Firmware
Hardware Description
Other S2Tech Measuring Instrument manuals
Popular Measuring Instrument manuals by other brands
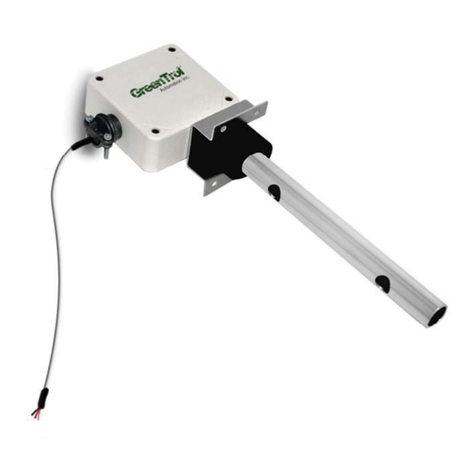
Greentrol Automation
Greentrol Automation GF-A1000-DI Series installation guide
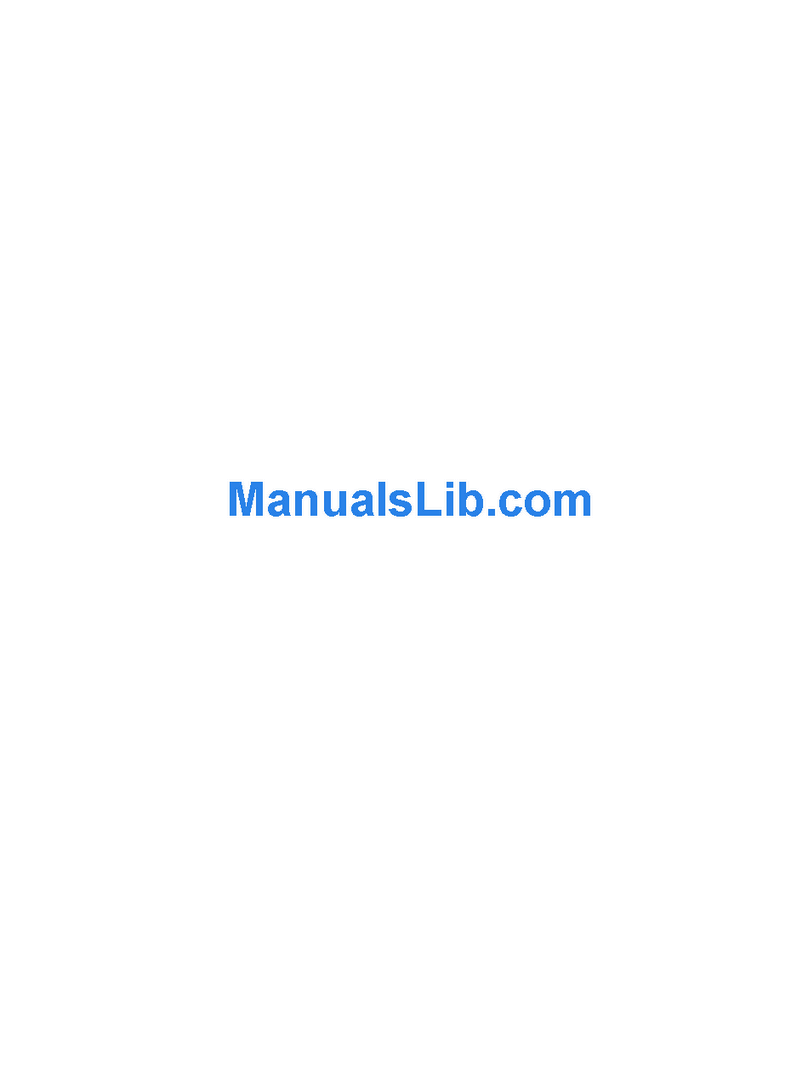
Agilent Technologies
Agilent Technologies 83483A manual
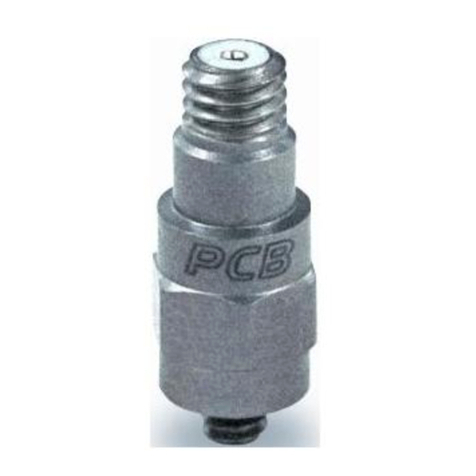
PCB Piezotronics
PCB Piezotronics J353B18 Installation and operating manual
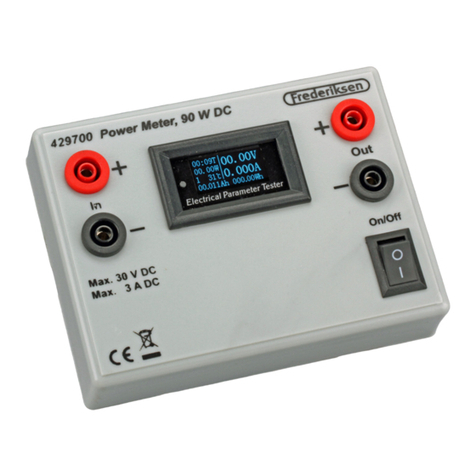
Frederiksen
Frederiksen 429700 product manual

Greenlee
Greenlee 200fp instruction manual

UFM
UFM KATflow 210 operating instructions