Sanwa MT-R RX-493i User manual

Sw1
Sw3
Sw2
Trm2
Trm1
Trm3

1
Safe Handling and Precautions
2
When turning the power switch of R/C System on,
please turn on in order of 1.Transmitter → 2.Receiver.
And when turning the power switch off,
please do so in order of 1.Receiver→2.Transmitter.
If you reverse the order of the switches, it causes
sudden high rotation of the engine and the motor
and it’s extremely dangerous.
Please use electrical noise countermeasure on
the body of your car.
If metals rub against each other, it causes electrical
noise which may lead to abnormal performance.
Please be sure that all screws and nuts are not loose.
Nitro or gas engine and electric motor can cause
noise also. Please use a noise countermeasure
such as a plug with resistor or noise killer condenser.
Please make sure to run a performance check
(signalreception test) of R/C System before
operation. When it moves abnormally or it doesn’t
move, please don’t operate. Even if the test result
on a desk is normal,please be cautious when
operating for the first time especially, since the
radio wave arrival distance varies depending on the
installation method of the receiver, how the antenna
is set, the direction of the transmitter antenna is
facing and geography.
Never operate on a rainy day.
To use your purchased R/C System properly and safely, please read this instruction carefully
and make sure to follow the precautions. Improper use of the product or negligence of
following safety precautions can cause trouble to others or harm to the user.
■ For safety, please make sure to follow each of the precautions below.
The interior of the transmitter is built with
sensitive electronic parts. If water runs on
the surface of the case and enters inside,
it can cause abnormal performance or malfunction
and it can be dangerous.
If the receiver or a servo
sinks in the water,
immediately collect it
and dry the interior.
When the interior is dry,
please submit it to
the Sanwa Service
for inspection even if it
performs normally.
The receiver is a precise instrument. Please do not add
a strong impact or vibration.
Use a thick sponge to prevent vibrations.
Install the receiver as far as possible from the speed
controller, motor and the battery.
When installing the receiver on a metallic chassis or
a carbon chassis, use three layers of double adhesive
tape pieces to keep the receiver from touching the chassis.
When there is a radio disturbance, change the
installation location of the receiver or change from a
vertical placement to a horizontal placement or vice
versa.
Don't place a motor cord or a battery cord close
to the receiver since it can cause abnormal
performance.
Keep the antenna of the receiver out as much as possible.
And keep it straight and stretched. Don't cut the extra
length of the line or bend it.
It’s dangerous when the antenna is short since the
range of travelling becomes narrow.
Never cut the antenna.
Don't place the antenna close to a motor cord or a
battery cord.
Using a conductive piano wire on a metallic chassis
or carbon chassis can cause abnormal performance
from electrical noise. Don’t place a piano wire close
to the chassis.
When operating an RC car, please make sure to follow
the following notes and avoid giving trouble to others.
Maintain the body of the car (boat) in a perfect condition
and check the safety.
Do not operate an RC car in a crowd or on a public road.
Make sure to disconnect the connector of the power battery
and remove the power battery from the car after operation.
When operating simultaneously with other RC users,
make sure to have a control staff and follow the
instruction of the control staff.
Try not to interfere with other people’s operation.
Be sure to apply for a radio control insurance.
For application to apply a radio control insurance, inquire
a radio control operator registration agency.
Be sure to install a “muffler (sound absorber)” with a
silencing effect on an engine car.
Don't start engine early in the morning.
Please make sure to clean the location used for
operation before you leave.
Do not use this RC system for other than model use.
Since this product is manufactured for models based on
the Radio Law in each country, it cannot be used in
countries other than your original place of purchase.
When the exhaust of the engine or fuel is on the
radio, wipe it with a soft, dry cloth. When it gets
dirty, please wipe it with a tightly squeezed clean
soft cloth impregnated with water or neutral
detergent. Thinner, benzene, alcohol, motor
cleaner, brake cleaner, etc. may cause surface
finish to deteriorate or degenerate, so please do
not use.
Please do not hit, drop or cause strong shocks.
In addition, if you touch the transmitter, receiver, servo,
FET speed controller, etc. with hands applied with tire
traction agent, it will cause breakdown or case deformation.
Caution
Caution
Caution
Caution
Warning Precautions for Installation and Operation
About Usage
Daily Care
Careful When Driving Handling Transmitter
About Storage
Warning
Meaning of the mark
Warning
Caution Things you are expected to do to
prevent accidents and injuries.
Things that you should follow in
order to prevent break down.
Do not store in following places.
Extremely hot place or extremely cold place.
A place that is exposed to direct sunlight for
a long time. Especially if you leave it in a place
where direct sunlight hits like in a closed car
window, the interior temperature becomes
80 0 C or more depending on the season, so
please be careful as it may cause deformation
or breakdown.
A place with high humidity, poor ventilation.
A place with considerable vibrations.
Places with high dust places subjected to
steam or hot air.
A place that gets exhaust gas from an engine
or a place near the fuel tank.

3 4
Safe Handling and Precautions INDEX
■How To Use Each Feature・・・・・・・・・・・・・・・・・・・・・・・・・・・11,12,17-52
■Structure and the Standard of the Set・・・・・・・・・・・・・・・・・・・・・・・5
●Structure of The Set (5)
●Set Specication (5)
■Before Using・・・・・・・・・・・・・・・・・・・・・・・・・・・・・・・・・・6-7
●Adjusting Tension of The Steering and Throttle (6)
●Adjusting The Adjustable Trigger (7)
●About The Power Source, Bind (7)
■Names of Each Part of The Transmitter・・・・・・・・・・・・・・・・・・・・・・8
■Connections and Installation of Receiver ・・・・・・・・・・・・・・・・・・・・・9,10
●About Receiver, And How to Handling The Antenna (9)
●About Connection Setup (10)
■Before Driving A RC Car・・・・・・・・・・・・・・・・・・・・・・・・・・・・・13-16
●How To Place Servo Horn (13)
●How To Set Reverse [REV] (13)
●How To Set Sub Trim [SUB-T] (14)
●Sub Trim and Trim Dierences (14)
●How To Set End Point Adjustment [EPA] (15)
●How To Set Dual Rate [D/R] (16)
● 2.4 GHz frequency band is not only used for radio control. This frequency band
is shared with ISM (Industry, Science and Medical) band. It can be affected by
microwave ovens, wireless LAN, digital cordless telephones, audio equipment,
Bluetooth of game machines or cell phones and short-range communication such
as VICS. Also, be cautious about being affected by amateur radio and premises
radio stations for moving body identification since this frequency band is used for
them as well. When a harmful radio frequency interference is done to an existing
radio station, stop the transmission of the radio frequency immediately and take a
measure to avoid the interference.
● For RC circuit, minimize the use of equipment that can affect 2.4 GHz systems and
make sure to check the safety beforehand. Also, follow the instruction of the facility
manager.
● When operating the models behind a building or a steel tower, blocking the direction
of radio wave transmission can cause reduction of operation response or loss of
control. Always operate within the range you can visually check.
● Don't grab the transmitter antenna. Doing so can be dangerous since it can weaken
the radio signal output and narrow the range of operation.
● Don't attach any metal parts around the antenna of the transmitter.
● If you have the transmitter’s antenna extremely close to a servo or speed controller
other than the receiver, it can cause malfunction but it is an influence of a strong high
frequency output and it is not abnormal.
● The receiver is a precise instrument. Don’t subject it to strong impact or vibrations.
Use a thick sponge to prevent vibrations.
● Keep the antenna wire of the receiver out as much as possible. And keep it straight
and stretched. Don't cut the extra length of the antenna line or bend it.
● Keep the antenna wire of the receiver out as much as possible. And keep it straight
and stretched. Don't cut the extra length of the antenna line or bend it.
● Don't place the antenna wire of the receiver close to a electrical noise source like a
motor wire or a battery wire.
● When installing the receiver on a metallic chassis or a carbon chassis, use layers of
double adhesive tape pieces to keep the receiver from touching the chassis as much
as possible.
Warning Note Precautions for Safe Use
●About Key Operation (11)
●About the Display Panel (12)
●About the Menu Structure (17)
●Setting [SETTING] (18-34)
・Dual Rates (D/R] (18)
・Speed [SPEED](19)
・Curve [CURVE] (20)
・Fail Safe [F/S] (21)
・Base [BASE] (22-24)
・Reverse [REV] (22)
・Sub Trim [SUB-T] (22)
・End Point Adjustment [EPA] (23-24)
・Function [FUNC] (25-28)
・Trim [TRIM] (25)
・Anti-Lock Brake [ALB] (26)
・Oset [OFFSET] (27)
・Throttle Type [TH TYPE] (28)
●AUX [AUX] (29-34)
・Step AUX [STEP AUX] (29)
・Point AUX [POINT AUX](30)
・4 Wheel Steering [4WS] (31)
・Motor On Axle [MOA] (32)
・AUX Mixing [AUX-MIX] (33)
・Code AUX [CODE AUX] (34)
●Model [MODEL] (35-38)
・Model Select [MODEL SELECT] (35)
・Model Name [MODEL NAME](36)
・Model Copy [MODEL COPY] (37)
・Model Clear [MODEL CLEAR] (38)
●Timer [TIMER] (39-40)
・Lap Timer [LAP TIMER] (39)
・Interval Timer [INT TIMER](40)
・Down Timer [DOWN TIMER] (40)
●Telemetry [TELEMETRY] (41-42)
・Logger[LOGGER] (41)
・Alert Setting [ALERT SETTING] (42)
・Telemetry Setting [TELEMETRY SETTING](42)
●System [SYSTEM] (43-48)
・Bind [BIND] (43-44)
・Key Assign Switch [KEY ASSIGN SW](45)
・Key Assign Trim [KEY ASSIGN TRIM] (46)
・Buzzer [BUZZER] (47)
・Battery [BATTERY] (47)
・LCD [LCD] (48)
・Calibration [CALIBRATION] (48)
●Setup Wizard (49-50)
●About Quick Setup Wizard (51-52)
■Assign Function List
・・・・・・・・・・・・・・・・・・・・・・・・・・ 53
■Transmitter LED Indication List
・・・・・・・・・・・・・・・・・・・・・ 54
■Index・・・・・・・・・・・・・・・・・・・・・・・・・・・・・・・・・55
■When this happens...
・・・・・・・・・・・・・・・・・・・・・・・・・・56
■Service and Support
・・・・・・・・・・・・・・・・・・・・・・・・・・57
■FCC Compliance Statement・・・・・・・・・・・・・・・・・・・・・・・58

6
Before Using
Before Using
5
Structure and the Standard of the Set
Structure
&
the Standard of the Set
65
MT-R (TX-4101)
MT-R RX-493i PC (Primary Component)
<A>
<B>
<C>
<D>
RX-493i
●Please check items before use
Brake Trigger +1/+2 x each 1
Receiver Dust Cover x1
Bind Plug x1
Antenna Pipe x1
User Manual x1
Transmitter
Receiver
Servo
Accesories
MT-R (TX-4101)
366 g
2.4 GHz Spread Spectrum System
Digital display (Power Source Voltage Display)
AA BATT x4 (Corresponding VOLT: DC4.8 - 7.4 V)
Output Display
Product No.
Power Source
Weight
Modulation 26.0x23.2x14.0mmSize
RX-493i
DC3.7~7.4V
6.2 g
Product No.
Power Source
Weight
2.4GHz Spread Spectrum SystemModulation
*Be careful with the input voltage.
If voltage above allowable voltage is inputted, the transmitter will be damaged.
<A>
Transmitter
<B>
Receiver
Adjusting screw for
the trigger postion
Fixing screw of the trigger
Fixing screw of the trigger
Trigger position gauge
Adjustable range: approx. 7mm
STRUCTURE OF THE SET
SET SPECIFICATION
ADJUSTING THE STEERING AND THROTTLE TENSION
ADJUSTING THE ADJUSTABLE TRIGGER
By inserting a hex wrench driver (1.5mm) to the place where the
arrow is pointing at in the illustration on the right and turning, you
can adjust the tension of the steering spring.
*The spring tension is the softest at the time when the product is
shipped out from the factory. As you tighten with a hexagon wrench
driver (1.5mm), the spring tension will be hardened.
Adujsting the Steering Tension
Adjusting the Throttle Trigger Tension
MT-R can adjust the tension of the steering/throttle trigger to match operation of the steering/throttle to the user’s preference.
By inserting a hex wrench driver (1.5mm) to the place where the
arrow is pointing at in the illustration on the right and turning, you
can adjust the tension of the throttle spring.
*Please do CALIBRATION when changing steering and throtte
tention. (p.48)
Loosen the fixing screws of the trigger on
the back of the transmitter. Then, adjust the
adjusting screw of the trigger position on the
back of the transmitter to set the trigger at
the position of your preference. When you
turn the adjusting screw of the trigger position
clockwise, the trigger position gauge moves to
the direction A. By turning it counter clockwise,
the trigger position gauge moves to the
direction B.
*The range of the trigger movement is 7mm.
If you turn the screw forcefully beyond the
range, it can cause malfunction. Once you set
the trigger position, tighten the fixing screw
and adjusting the trigger is done.
*Be careful with the direction of turning the
screw because the trigger position is set at the
furthest point of the A side at the factory.
MT-R can adjust the throttle trigger position ting to the user’s hand size.
Adjusting the trigger position
*Setting Advice
Please t trigger position to your nger naturally.
It would be smoother to operate braking.

7
Before Using
Before Using
Before Using
8
Name of Each Part of Transmitter
Name of Each
Part of Transmitter
7
( +1 )
( +2 )
Brake trigger fixing screw
Brake trigger
Sw1
Sw3
Sw2
Trm2
Trm1
Trm3
▲
▼
Trm1
Trm2
Display Panel LED
Internal Antenna
Power Switch
Trim 1
Trim 2
(
TRM 2
)
(
TRM 1
)
Trim 3
Switch 2
(
SW 2
)
(
TRM 3
)
Steering Wheel
Switch 3
(
SW 3
)
Switch 1
(
SW 1
)
Throttle Trigger
Trigger Position
Adjusting Screw
Strap Hole
ADJUSTING THE ADJUSTABLE TRIGGER
ABOUT THE POWER SOURCE
ABOUT BIND
You can adjust brake trigger position accroding
to your fingers by replaceing the included brake
trigger.
Standard Size, +1 Size, +2 Size is included.
1) Remove the brake trigger fixing screw.
2) Select Brake Trigger according to your fingers.
3) Fix the brake trigger by the screw.
Adjusting the brake trigger
*Setting Advice
If you feel much gaps between a nger with trigger, please change brake trigger to +1 or +2.
After changing the brake trigger size, please check the dierences while driving.
Combination of trigger position and brake trigger adjustment would give optimic operation by fiting to
personal hand.
HOW TO PLACE THE TRANSMITTER BATTERIES
<1>Open the battery
compartment cover by sliding
the cover to the direction of
the arrow while pressing it
lightly.
<2>Place 4 size AA
batteries. Make sure to
observe correct polarities.
<3>Align the convex part of
the battery compartment cover
and the groove of the battery
compartment, slide the cover to
the direction of the arrow and
close tightly.
● About Bind
Each MT-R transmitter has own ID number for transmition. Receiver memorizes the ID number to bind.
After binding, the transmitter can work with the receicer.eceiver and the antenna are installed.
● BINDING is not done at the factory. Please make sure to complete BINDING before use.
● When the receiver is new, make sure to complete BINDING for the transmitter and the new receiver.
● Make sure to use the set of the transmitter and the receiver that completed BINDING.
*About details of bind, please refer p.43-44 in this manual.

109
Connections and Installation of Receiver
Connection
&
Installation of Receiver
Connection
&
Installation of Receiver
109
接続について
*Indicate receiver working condition by LED light. Indication of Receiver Working Condition by LED light
Connected
Blue light On
*When binding with 2 transmitter,
blue light flush at 2 sec intervals.
In BIND Setting Blue light flushing
Blue light blinking
Blue and red light on
NOT Connected
Battery Fail Safe Working
Red light on
Receiver is not connected
in Battery Fail Safe working
CH4: 4ch
SSL/BAT: BIND/SSL Port
* Please do not connect devices except SANWA SSL
Compatible devices.
CH3: 3ch
CH2: Throttle (ESC / FET Speed Controller)
CH1: Steering
BIND Plug
LED
Antenna
Antenna pipe amount
Please use SANWA antenna pipe.
Antenna Pipe
Antenna
■Case of connecting PGS servo to 2 SSL ports
■Case of connecting PGS servo and SUPER VORTEX Gen2/PRO/SUPER VORTEX Stock to SSL port
●
Connection example in case of using in EP car
Please refer the below picture for receiver and servo connection
Switch harness
Connect the receiver battery
Connection with BATT
Connection with
CH2
Connection with CH1
Power battery
Motor
ESC / FET speed controller
Steering servo
Throttle servo
Connection with CH1
Connection with CH2
Steering servo
CH2
BATT
CH1
CH2
BATT
CH1
SUPER VORTEX Gen2/PRO
/SUPER VORTEX Stock
●Set AUX TYPE of the transmitter for both AUX1, AUX2 to CODE 10.
AUX1 CODE10: Setting of SUPER VORTEX Gen2 / PRO /SUPER VORTEX Stock can be from the transmitter.
AUX2 CODE10: Setting of each of the parameters of PGSⅡ servo can be from transmitter.
Note) In SUPER VORTEX Gen2 / PRO, do not assign function to CODE 10 of AUX2 by code
assign of PROGRAM BOX Gen2. It interferes with CODE 10 of AUX2 of PGS servo and suitable
setting cannot be done.
Note) Set SSL-CH of PGS servo to [1].
(Factory setting of PGS servo is [1].)
Note) CODE of AUX2 is used for SUPER VORTEX ZERO / SUPER VORTEX TYPE-D /
SUPER VORTEX SPORT. It interferes with CODE 10 of AUX2 of PGS servo and
suitable setting cannot be done. Therefore, it cannot be used along with SSL of PGS servo.
Note)When Connecting PGS servo with SGS-02 cannot change setting at the same time.
When using SGS-02, Gain connector connect to SSL port.
*Please DO NOT connect another devices except SANWA SSL compatible products.
About setting and connection, please refer manuals of SSL compatible product.
Short Y harness
Steering servo
PGS servo:SSL - CH1 setting
SSL Port
Connect the receiver battery
●Set AUX TYPE of AUX2 of the transmitter to CODE 10.
AUX2 CODE10: Setting of each of the parameters of PGS servo can be done from the transmitter.
Note) Set SSL-CH of PGS servo used in steering servo to [1].
Set SSL-CH of PGS servo used in throttle servo to [2].
(Factory setting of PGS servo is [1].)
Note) In case of setting each parameter by the function of CODE10 of AUX2, setting of PGS
servo of SSL-port set by CODE1 of AUX2 can be directly changed from the transmitter.
PGS servo not specified by CODE1 of AUX2 works on the parameters saved inside.
PGS servo: SSL - CH1 setting
Steering servo
Throttle servo
Switch harness
Short Y harness
PGS servo: SSL 2 CH2 setting
SSL Port
Other Empty Port
*Please, refer on our Website about any other examples. http://www.sanwa-denshi.co.jp
*When using PGS Servo with SGS-02,
PGS servo cannot set by CODE10 at the same time.
Only SGS-02 can be set when connect with PGS servo.
ABOUT THE RECEIVER
ABOUT HANDLING THE ANTENNA
ABOUT CONNECTION SETUP
● RX-493i
RX-493i can evaluate received signal strength and packet delivery ratio from transmitter.
*MT-R cannot check received signal strength and packet delivery ratio.
RX-493i can store 2 transmitter ID Number. It is able to combine using individual transmitter which is
different setting in endurance race .
If you bind with 2 different transmitter, the receiver store the different transmitter and can operate by
transmitters without re-bind.
*CANNOT operate by the 2 different transmitter at the same time. 2 ID store system is only compatible
with M17, MT-5, or MT-R.
Throttle neutral position or operation quantities might be different each transmitter. Please adjust each
transmitter setting to fit chassis linkage.
When setting SSL compatible devices by MT-R CODE AUX function, please connect SSL compatible
device to SSL port.
MUST set fail-safe setting on each transmitter.
Please set same RF mode and response mode as 1st transmitter when you bind 2nd transmitter. If it was
different mode, cannot bind with 2 transmitters.
*If 2nd transmitter was different RF node and response mode from 1st transmitter, 1st transmitter ID No. is
deleted and only write 2nd transmitter.
*If you bound 3rd transmitter, 1st transmitter ID No. will be deleted.
*When using first time, please bind with receiver. (p.43)
● Reception distance may vary depending on the location
where the receiver and the antenna are installed.
● To protect the reception part (3 cm from the top) of the
antenna, make sure to place the antenna in the antenna
pipe as shown in the right illustration so that the top of the
antenna is not exposed outside of the antenna pipe.
● Don’t bend the antenna reception part or the antenna
coaxial cable because breaking can occur inside.
● Don’t pull the coaxial cable forcefully. It may damage the
receiver interior.
● Install the antenna on an RC car so that the antenna
reception part is in as high place as possible.
● Don’t cut or bind the antenna reception part or the antenna
coaxial cable since the receiver sensitivity might decrease.
● Keep the receiver antenna away from the motor and the
ESC / FET Speed Controller (including cables) and raise it
straight.
Note
• If the connector is disconnected due to a vibration during operation, it can cause runaway. Connect the connector
of the receiver, servos and switches securely.
• Because the receiver is susceptible to vibration, impact and water, make sure to take measures for vibration-proof
and waterproof. Negligence of taking these measures can cause runaway.
• When installing the receiver, keep the receiver away from a carbon chassis and metallic chassis.
• If metal parts installed on an RC car touch each other, it can cause noise that affects reception performance and it
can cause runaway.
• Make sure to install a noise killer condenser on the brush motor for electric RC cars. Without a noise killer
condenser, it can cause noise and runaway.
• For R/C System parts such as the transmitter, receiver, servos, ESC (FET Speed Controller) and transmitter
battery, use genuine SANWA products.
*When combining products other than genuine SANWA products, modifying, adjusting or exchanging parts is
done at a place other than SANWA, we do not take any responsibility.

1211
How to Use Each Feature
How to Use Each Feature
How to Use Each Feature
▲
▼
▲
▼
Push
▲
▼
▲
▼
▲
▼
Display Panel
Up Key
Down Key
Enter Key
Back and Cancel Key
Key Operation Names Performance
Enter
Up
Down
Back / Cancel
●Moves to the setup screen from the top
screen.
●Selects a feature and item to set.
*By long pressing the Enter, the setting
goes back to default.
●The cursor moves upward.
●The set value increases.
●Moves the cursor downward.
●The set value decreases.
●Goes back to one step before.
●Cancels the setting.
↑
↓
↑
↓
▲
▼
Push
Top Menu
Telemetry Menu
Menu Window
*Push enter operation
to switch from Top menu
When using RX-491/492/493/493i and
SUPER VORTEX Series/PGS Servo Series/SGS-02,
Turn telemetry function on, then display telemetry
data from receiver.
ENTER
BACK
ENTER
BACK
Push up and down key, display
switches top display to telemetry display
Antenna mark will be shown
while using telemetry
*Push down key on the
telemetry display.
Telemetry data will be
shown max values.
When holding down key,
max values will be reset.
ABOUT KEY OPERATION ABOUT DISPLAY PANEL
● The user can set up and make a calling easily with each key. ● Each feature of MT-R can be selected directly by each key.
● You can set up each channel feature separately.
● As you turn the power switch on, the top screen launches after the boost screen is displayed(when the
boot setting is on). When changing each setting, select the menu by enter operation.

1413
Before Driving A Car
Before Driving A Car
Before Driving A Car
1413
1. Taking off an arm from servo
2. Turn on transmitter & receiver
3. Powered the servo to be
neutral position
4. Please place servo arm on 90 degree
as the picture. Please use SUB TRIM for
slight arrangement.
5. Place the servo on the RC Car.
*Servo arm angle depends on
EC Car. Please check and
follow RC Car manual.
Taking on servo arm before servo
does not make neutral position.
Servo arm will be neutral position
after turning on the servo.
This would be incorrect servo arm position
and it is caused to servo and car broken.
OK NG
No Operation
Right Operation
Left Operation
REV Setting Requirement
Tire direction is right Tire direction is left
No Operation
Right OperationLeft Operation
Tire direction is right
Tire direction is left
Wanted to place servo arm in
car manual but cannot place
slightly different.
Arrange neutral position by
SUB TRIM setting.
Example of SUB TRIM Arrangement
Before Trim Adjustment After Trim Adjustment
Go straight
Automatically turning right or left
Steering
No Operation
HOW TO PLACE SERVO ARM
HOW TO SET REVERSE [REV]
HOW TO SET SUB TRIM [SUB-T]
SUB TRIM AND TRIM DIFFERENCES
●
Power the servo will be returned neutral position.
●
Turn on binded receiver and transmitter before taking on servo horn.
●
Be sure about transmitter Trim and Sub Trim are no setting (value is 0).
In case Trim and Sub Trim did not set 0, please set 0 for these setting.
●
Please place servo arm on center postion such as the below picture.
*Servo horn angle may not be 90 degree due to RC car type.
Please place servo horn to follow instruction manual of RC car.
● Please check
steering operation and tire direction are same after tacking on servo arm.
●
Please set REVERSE in case steering operation and tire direction are direrent. About REVERSE
setting please reer p.22 in this manual.
● In case servo cannot place correctly as 90 degree or RC Car manual instruction, please arrange neutral
position by SUB TRIM setting. About SUB TRIM setting, please refer p.22 on this manual.
● SUB TRIM is for neutral position and mainly used on the pit as taking on servo horn.
TRIM is for driving arrangement and mainly used while driving such as below picture. Please refer p.22 in
this manual.
*RC car did not go straight as accident.
TRIM is used for direction arrangement.

1615
Before Driving A Car
Before Driving A Car
Before Driving A Car
Example of Driving
In case of maximum angles differences for both right and left,
car turns around different for both sides.
Steering Angle
About Steering Angle
Tire
Weird Sound
Servo will be locked
Possible to damage
Fully Right OperationFully Left Operation
Right And Left Maximum Steering Angles Are Different
After EPA
Adjustment
Before EPA
Adjustment
To Be Same for Both Right And Left Maximum Steering Angles
Less right maximum angle
Example
No Operation
Fully Right OperationFully Left Operation
No Operation
Full Right AngleFull Left Angle
Full Right Angle
D/R
100%
(Default)
D/R
20%
100% 100%
20% 20%
Full Left Angle
HOW TO SET END POINT ADJUSTMENT [EPA] HOW TO SET DUAL RATE [D/R]
● Adjust right and left maximum steering angle are same after setting SUB TRIM
.
*In case of not setting EPA, right and left cornering are dierent as the below picture.
This may be caused to servo broken. Please refer p.23 in this manual.
*Please arrange EPA setting as the below picture and make sure same maximum steering angles for
both right and left.
● About Steering Operation
In case RC car is too much cornering and difficult to drive, DUAL RATE(D/R) adjust maximum steering angle.
EPA adjust each left and right maximum steering angle.
D/R adjust both left and right maximum steering angle at the same time and same ratio.
Please refer p.18 on this manual.

1817
How to Use Each Feature
How to Use Each Feature
How to Use Each Feature
(P.18)
(P.29-34) (P.39
-
40)
(P.19)
(P.20) (P.37)
(P.21)
(P.22-24)
(P.25-28)
D/R
SETTING
SPEED
CURVE
F/S
BASE
FUNC
AUX
(P.35)
(P.36)
(P.38)
SELECT
MODEL
NAME
COPY
CLEAR
TIMER
(P.41)
(P.42)
(P.42)
LOGGER
TELEMETRY
ALERT SETTING
TELEMETRY SETTING
(P.43
-
44)
(P.45
-
46)
(P.47)
(P.47)
(P.48)
(P.48)
BIND
SYSTEM
KEY ASSIGN
BUZZER
BATTERY
LCD
CALIBRATION
Set up all
items of the
accessory
channels of
3ch/4ch.
Various timer
setups and lap
display menu.
Sw1
Sw3
Sw2
Trm2
Trm1
Trm3
TRIM 3
(TRM 3)
ENTER
⇒
*Make sure that the servos do not
lock to make clicking sound!
Note) The same for throttle.
Note • If the linkage is locked for a long period, it
can cause the servo motor breakage.
• Adjust the end point of the steering/throttle linkage before adjusting dual rates (P. 23, 24).
SUPPLEMENT
Steering Dual Rate Display
Steering Dual Rate Display
ABOUT THE MENU STRUCTURE DUAL RATE [D/R]SETTING
● The user can set up features and do model memory call easily by using each key.
● The Menu consists of Setting, AUX, Model, Timer, Telemetry and System Menu, and related features are
included in each menu.
● You can adjust steering angle when operating the steering wheel and throttle trigger to their peak.
Please adjust the steering angle to fit RC car and surface condition when driving.
*You can adjust steering for both right and left at the same time and throttle separately for high and brake
sides. You can also adjust the brake side more precisely than adjusting with EPA.
● Don't increase the setting rate of dual rates (D/R) from the condition in which the linkage locks by
operating the steering wheel and throttle trigger.
● You can also adjust more precisely by adjusting dual rates of the throttle side.
*A1 and A2 cannot be set even moving to D/R on A1 and A2 page.
1) Select features [ST/TH/BR] to adjust with the up and down key.
2) Determine the feature to adjust with the Enter key. Adjust the valus of DUAL RATE by up and down key.
3) During operation, the steering dual rates can be adjusted with Trim 3. It's possible to assign other features
to Trim 3 with the key assign trim feature (P. 46).
*When cancelling a selected feature, operate the Back key.
*Depending on car types, dual rate is not assigned to TRIM3.
○
Setting Range:
ST/TH: 0%~100%
BR: 0%~120%
○
Default:
ST/TH/BR: 100%

2019
How to Use Each Feature
How to Use Each Feature
How to Use Each Feature
N
FORWARD
RETURN
FORWARD
RETURN
• For driving an RC car, steering operation that suits the movement of the RC car is important and
excessive operation is not recommended. Steering speed can minimize unnecessary operation
and enables smooth cornering.
• When steering speed and steering curve are combined, the effect is doubled.
SUPPLEMENT
N
FORWARD
RETURN
End
H
Neutral
• For driving an RC car, throttle operation that suits the movement of the RC car is important
and excessive operation is not recommended. Throttle SPEED can minimize unnecessary
operation and enables smooth performance.
• When throttle SPEED and throttle CURVE are combined, the effect is doubled.
SUPPLEMENT
Quick Quick
Normal Normal
Mild Mild
Servo Operating Quantity
Servo Operating Quantity
Neutral Position
Steering Wheel L End Operating Quantity
Throttle Trigger H End Operating Quantity
Steering Wheel R End Operating Quantity
Throttle Trigger B End Operating Quantity
Point Setting Position
Point Setting Position
Select H/B by Throttle Trigger
SPEED SETTING
STEERING SPEED
[ST]
THROTTLE SPEED
[TH]
CURVE SETTING
STEERING CURVE
[ST]
THROTTLE CURVE
[TH]
● Features to control the speed of the servos used for steering and throttle. By setting, the RC car is not
affected even when doing a sudden operation. On the steering side, smooth corner work becomes
possible and on the throttle side, stable rising from a corner by throttle work with saved power.
*When setting AUX TYPE to [CODE], adjusting the speed feature of the AUX channel does not affect the
performance.
*When setting the speed of the AUX channel, do so using steering/throttle as a reference.
● A feature to delay the speed of the steering servos against the steering operation. You can set speed for steering
forward and returning individually. For steering operation slower than setting, the speed feature does not work.
1) [ST (Steering)] with up and down key.
2) Setting on the forward side [FORWARD]
Select [FORWARD] with the Enter key and adjust
the setting value by up and down key.
*When cancelling a selected feature, use the Back key.
○Setting Range: 0~-100
○
Default: 0
3) Setting on the Return side [RETURN]
Select [RETURN] with the Enter key and adjust
the setting value with by up and down key.
○
Setting Range: 0~-100
○
Default: 0
*Adjust during actual operation. When not using the features or when a setting value cannot be determined
even after adjustment, set the value to 0% (linear).
● A feature to slow down the performance speed of the throttle servos and delay the response of the speed
controller against throttle operation. You can set speed for entering throttle (Forward) and returning
(Return) individually. The speed feature does not work with throttle operation slower than the setting.
*Setting is only for High side and Brake side cannot be set.
1) Select [TH (Throttle)] with up and down key.
2) Setting on the forward side [FORWARD]
Select [FORWARD] with the Enter key and adjust
the setting value by up and down key.
*When cancelling a selected feature, use the Back key.
○Setting Range: 0~-100
○
Default: 0
3) Setting on the Return side (RETURN)
Select [RETURN] with the Enter key and adjust the setting
value by up and down key.
○Setting Range: 0~-100
○
Default: 0
*Adjust during actual operation. When not using the features or when a setting value cannot be determined
even after adjustment, set the value to 0% (linear).
● Curve changes servo work rate by steering and throttle position. It responds quickly when the set value is
on plus (+) side whereas it responds mildly when the set value is on minus (-) side.
● MT-R has adjustable rate controller (ARC) of linear position.
*If the AUX type is set to [CODE], curve does not work.
*Please adjust curve setting on AUX cannel to refer steering and throttle.
Adjustable rate controller (ARC)
Position at where operation is variable can be changed by adjusting the setting of POINT.
● You can change the steering feature from Mild to Linear and to Quick.
If you nd your RC car oversteering, change the setting to the minus side and if you nd understeering,
change to the plus side. Steering Adjustable Rate Control is a simultaneous setting for L and R.
1) Select ST with up and down key.
2) Setting Rate [RATE]
Select [RATE] and adjust the setting value with up and down key.
*When cancelling a selected feature, use the Back button.
○Setting Range: -100~100% ○Default: 0%
3) Setting Point [POINT]
Select [POINT] and adjust the setting value with up and down key.
○Setting Range: 5~95% ○
Default: 50%
● You can change the throttle feature from Mild to Linear and to Quick.
In general, when operating on a slippery road or if you nd over powering, change the setting to the minus
side. When operating on a high-grip road or if you nd lack of power in the power unit, change to the plus
side. You can set the High side and the brake side separately.
*Selection of the High side and the brake side is done by trigger operation.
1) Select TH with up and down key.
2) Setting Rate [RATE]
Select [RATE] with with up and down key.
Adjust the setting value.
○Setting Range: -100~100% ○
Default: 0%
3) Setting Point [POINT]
Select [POINT] with up and down key.
Adjust the setting value.
○
Setting Range: 5~95% ○
Default: 50%
*When cancelling a selected feature, use the Back button.
1.If you feel slippy while driving drift car, please set High side point 20 to 30% and Rate -15 to - 30%. It can
be more smooth and getting traction easily. *Please arrange ideal point and rate values while driving.
2. In case of using motor of stock class, please set High side point 20 to 30% and Rate 15 to 30%. It would
give quick throttle timing and get more car acceleration.

2221
How to Use Each Feature
How to Use Each Feature
How to Use Each Feature
F/S Setting
F/S Setting
BATT- F/S Setting
F/S Setting Point
• About the Fail Safe Operation
When the Fail Safe feature is on, check the setting of the Fail Safe before operating.
Don't change the setting of the Fail Safe during operation.
IMPORTANT
Sw1
Sw3
Sw2
Trm2
Trm1
Trm3
TRIM 1
(TRM 1)
TRIM 2
(TRM 2)
90°
Adjusting the center position
●About Trim and Sub Trim
Trim is a feature for adjusting the neutral (center) position of the servo. When your model does not run straight after installing the steering servo onto the model,
Trim adjusts the main trim of the steering. Also, the neutral position of the carburetor on RC cars needs neutral adjustment of the throttle servo along with linkage
adjustment after installing the servo. Neutral position adjustment is necessary not only after installing the servo but for changes that happen during running such
as tire wears and chassis twist. MT-R Trim features two types of Trim including Center Trim that adjusts only the neutral position without changing the end of the
operating angle and Parallel Trim that moves the end of the operating angle and the neutral position simultaneously. Sub Trim that adjusts the neutral (center)
position before fixing the servo horn is Parallel Trim and the main trim is Center Trim.
○Center Trim (Main Trim)
Even if you move the neutral position with Trim, the
end of the operation angle does not move.
○Parallel Trim (Sub Trim)
When you move the neutral position with Trim, the end of the
operation angle also moves.When Sub Trim is adjusted after
linkage is completed, readjustment of End Point Adjustment
(EPA) will be necessary.
When installing the servo horn onto your servo, fix the servo horn as
close to the center as possible and center it with Sub Trim.
If Sub Trim and the transmitter main trim are off to one side,
it causes dead band (the range the servo does not move) to the steering
wheel and the throttle trigger.
Note
Setting SUB-T
REV Setting
FAIL SAFE [F/S]SETTING BASE SETTING
REVERSE [REV]
SUB TRIM [SUB-T]
● Fail Safe Operation is a feature to keep the servos in a predetermined position for each channel in the
event that the receiver cannot receive a signal from the transmitter. A feature to keep the servos in a
predetermined position for the servo of the throttle channel (2ch) in the event that the battery voltage on
the receiver side of an engine RC car goes below the set voltage is Battery Fail Safe Operation.
● Battery Fail Safe Operation cannot be set when the throttle channel (2ch) is set to FREE/HOLD (*Battery
Fail Safe Operation works only for the throttle channel).
*Don't use Battery Fail Safe Operation for electric RC cars.
1) Select F/S with up and down key and select a channel to set fail safe operation (ST/TH/A1/A2).
2) Enter the set channel and operate by up and down key.
The fail safe mode setting changes in order of
FREE→FS→HOLD.
○
Setting Range: FREE/FS(-100~100%)/HOLD
○
Default: FREE
FREE (Free Mode)
When thre receiver cannot receive the signal from the transmitter, the signal output to the servo stops and
the servo will be free.
FS (Fail Safe Mode)
When the receiver cannot receive the signal from the transmitter, the servo will be held in the set position.
HOLD(Hold Mode)
The last postion before the signal from the transmitter to the receiver is lost will be held.
*When the receiver can receive the signal from the transmitter again, each mode of FREE/HOLD/FS is
automatically released.
3) Setting the Fail Safe (FS)
Move to the position where the Fail Safe Operation is used. When the position is determined, holding the
Enter key to set the position when the Fail Safe Operation works.
*For safety, we recommend setting the throttle channel on the brake side when setting the Fail Safe.
4) Setting the Battery Fail Safe Operation
After setting the throttle channel position, move the cursor to [B-F/S] to set the voltage.
○Setting Range: OFF, 3.5v ~7.4v
*The Battery Fail Safe Operation is a feature to activate
Fail Safe Operation when the receiver battery voltage belows
to the set voltage on a Nitro car.
Don't use the Battery Fail Safe feature on electric RC cars.
5) Checking the Fail Safe Operation
Turn off the power of the transmitter while
the Fail Safe Operation is set and check
if the servo moves to the position where
the Fail Safe Operation is set.
● Base sets multiple functions all at once such as the Reverse that determines the direction of the servo of
each channel, the speed controller according to a specic RC car, the Sub Trim that adjusts the neutral
position, and the End Point Adjustment [EPA].
● This is used when operation and the movement of the servo are reversed while operating Steering/throttle/
AUX1/AUX2.
1) Select BASE with up and down key
Select a channel to set (ST/TH/A1/A2).
2) Enter with the channel to be set by using up and down key.
The Reverse setting will be changed.
*When cancelling a selected feature, use the back key.
○
Setting Range: NOR/REV
○
Default: NOR
● Using the Sub Trim feature, correct the neutral (center) of Steering/Throttle/A1/A2 so that Trim can be
used from the center position. When installing a servo on to an RC car, center the servo with Sub Trim rst
before adjusting End Point Adjustment.
1) Before using, center (0) each main trim.
2) Select SUB-T with up and down key
Select a channel (ST/TH/A1/A2) to adjust Sub Trim.
3) Set the channel by Enter key.
4) Install the servo horn (servo saver horn) as close to
centered as possible.
*For installation position of the servo horn,
follow a car product instruction.
5) Adjust the center by using up and down key.
○Setting Range:L150~R150(ST)
H150~B150(TH)
H150~L150(AUX1, AUX2)
○Default: 0

2423
How to Use Each Feature
How to Use Each Feature
How to Use Each Feature
Note
• If the linkage is locked for
a long period, it can cause
the servo breakage.
*Make sure the servos do not lock to make clicking sound
Note
• When EPA setting value is
too large on the fully open
side of the carburetor and
the brake side for throttle
linkage, the servo is locked
and it can cause the motor
malfunction and runaway.
*Make sure the servos
do not lock to make
clicking sound
BASE SETTING
END POINT ADJUSTMENT [EPA]
STEERING END POINT ADJUSTMENT
[ST-EPA]
THROTTLE END POINT ADJUSTMENT
[TH-EPA]
AUX1・END POINT ADJUSTMENT
[AUX1-EPA]
AUX2・END POINT ADJUSTMENT
[AUX2-EPA]
● Base sets multiple functions all at once such as the Reverse that determines the direction of the servo of
each channel, the speed controller according to a specic RC car, the Sub Trim that adjusts the neutral
position, and the End Point Adjustment [EPA].
● EPA setting can adjust left and right steering servo range for steering operation, high and brake throttle
working range for throttle trigger operation, and the servo working range for AUX1, AUX2 (3ch, 4ch).
● Due to linkage, suspension balance and the difference of the tire diameter, left and right cornering radius
can be different. In case of this, this feature adjusts the servo working range of left and right so that left and
right cornering radius can be the same.
1) Before adjusting Steering End Point Adjustment (ST-EPA),
make a neutral adjustment of the servo (P.22).
Neutral adjustment is to align the center position with
Sub Trim by turning the power on and installing
the servo horn in the approximate center position.
2) Select either of [EPA-L/EPA-R] with up and down key
Determine with the Enter.
3) Adjust the working range with
up and down key.
*When the cursor is on either of
EPA-L/EPA-R, it is also possible to
move the cursor by steering operation.
○Setting Range:L/R 0%~150%
○Default: L/R 100%
● It adjusts the High Point of FET Speed Controller, Brake Point, carburetor of engine and the brake working
range.
1) For a nitro car, make a neutral adjustment of the servo (P.20) before adjusting
the Throttle End Point Adjustment (TH-EPA).
Neutral adjustment is to align the center position with Sub Trim
by turning the power on and installing the servo horn in
the approximate center position.
2) Select [TH/Throttle] with up and down key.
3) Select either of [EPA-H/EPA-B] with up and down key.
Determine with the Enter.
4) Adjust the operating quantity with up and down key.
When adjusting ESC / FET Speed Controller, normally set
both the high side and the brake side to 100% and set
neutral, high point and brake point on the ESC / FET Speed
Controller side (Setting method is different depending on
the ESC / FET Speed Controller).
*When the cursor is on either of
EPA-H/EPA-B, it is also possible to
move the cursor by trigger operation.
○Setting Range:H/B 0%~150%
○Default: H/B100%
● You can use AUX1 for functions of accessories and adjust the maximum steering angle with EPA. Since
you can set H/L separately, precise adjustment is possible.
*When setting AUX1 to [CODE5/CODE10] in AUX TYPE, the operation will not be refected even by
adjusting EPA.
1) Before adjusting AUX1 End Point Adjustment (A1-EPA), make a neutral adjustment of the servo (P. 22).
Neutral adjustment is to align the center position with SubTrim by turning the power on and installing the
servo horn in the approximate center position.
2) Select [AUX1] with up and down key.
3) Select either of [EPA-H/EPA-L] with up and down key.
Determine with the Enter.
4) Adjust the working range with up and down key.
○Setting Range:H/L 0%~150%
○Default: H/L100%
● You can use AUX2 for functions of accessories and adjust the maximum steering angle with EPA. Since
you can set H/L separately, precise adjustment is possible.
*When setting AUX2 to [CODE5/CODE10] in AUX TYPE, the operation will not be reflected even by
adjusting EPA.
1) Before adjusting AUX2 End Point Adjustment (AUX2-EPA), make a neutral adjustment of the servo (P. 22).
Neutral adjustment is to align the center position with Sub Trim by turning the power on and installing the
servo horn in the approximate center position.
2) Select [AUX2] with up and down key.
4) Select either of [EPA-H/EPA-L] with up and down key.
Determine with the Enter.
3) Adjust the working range with up and down key.
○Setting Range:H/L 0%~150%
○Default: H/L100%

2625
How to Use Each Feature
How to Use Each Feature
How to Use Each Feature
Sw1
Sw3
Sw2
Trm2
Trm1
Trm3
TRIM 1
(TRM 1)
TRIM 2
(TRM 2)
• About Trim
Trim is a feature to adjust the neutral (center) position of the servos. After installing
the steering servo onto a car, you can adjust with Trim when the car does not move straightly. Neutral
position adjustment is necessary not only after installing the servo but for changes that happen
during running such as tire wears and chassis twist.
• It's Sub Trim that adjusts het center position when adjusting linkage (P. 22)
Note
• If Trim and Sub Trim are off to one side, it causes dead band (the range the servo does not
move) to the steering wheel and the throttle trigger. When installing the servo horn, fix the
servo horn as close to the center as possible and center it with Sub Trim.
IMPORTANT
Trigger indicator
Point Position
ALB will be worked when trigger
operation is right side (Brake side)
[ ]
ENTER BACK
Full Brake
Position of the Point
Neutral
*ALB is activated when operating from the point
position to full brake.
Neutral
Point
Lag Cycle
Stroke
Servo action
Duty
(A:B ratio)
Brake operation
Duty A : brake ON
Duty B : brake OFF
•Activate the brake rather strongly not to the extent that the tires of your RC car lose their grips (not to
slip) and adjust so that Anti-Lock Brake is activated just before the tires are locked and slide.
•If you set ALB using a speed controller with a back on an RC car, you may not able to operate back
movement. When using a back movement, turn ALB off.
SUPPLEMENT
FUNCTION [FUNC] SETTING
TRIM
ANTI-LOCK BRAKE [ALB]
● Anti-Lock Brake enables stable braking on a low grip road.
● Because of the stable braking, you can drive ideal cornering lines as intended.
1) Select [ALB] with up and down key.
2) The menu changes to ALB setup menu
with the enter operation.
3) Setting Stroke (STROKE)
Set Stroke of ALB with up and down key.
Stroke is the width of repeated actions
at the time of braking.
○Setting Range:OFF, 0%~100%
○Default:OFF *ALB does not work when it is off.
4) Setting Point (POINT)
Set Point of ALB with up and down key.
Point is the position where ALB starts acting
when operating the brake.
○Setting Range: 5%~100%
○Default: 80%
5) Setting Lag (LAG)
Set Lag of ALB with up and down key.
Lag is a setting of time lag from the time
when operating to the point to the time
when ALB starts acting.
○Setting Range: 0.00s~1.00s
○Default: 0.00s
6) Setting Cycle (CYCLE)
Set a cycle of ALB with up and down key.
Cycle is a frequency setting of
repeated actions for braking.
○Setting Range: 0.01s~1.00s
○Default: 0.03s
*While Anti-Lock Brake working, transmitter LED will be
high-speed flashing.
*LED flashing time and way of flashing are same
in any setting values.
● Function can set trim, ALB (Anti-Lock Brake), OFFSET, and TH TYPE (Throttle Type) on each channel.
● Correct neutral (center) of each channel (ST/TH/A1/A2) with Trim.
● As default, steering is set for Trim 1 (TRM1), and throttle for Trim 2 (TRM2).
1) Select a channel (ST/TH/AUX1/AUX2) for
adjusting Trim with up and down key.
2) Determine with Enter operation and adjust
with up and down key.
○ Setting Range:
ST:L100~R100
TH:H100~B100
AUX1:H100~L100
AUX2:H100~L100
○ Default:
ALL : 0
*Make an adjustment with TRM1 (ST) and TRM2 (TH)
during operation.You can change the Trim lever position
with the Key Assignments Trim feature (P. 46).

2827
How to Use Each Feature
How to Use Each Feature
How to Use Each Feature
ENTER BACK
Servo Operating Quality
OFFSET Position
When setting plus
OFFSET Position
Neutral postion
When setting plus
Trigger Control Input
Neutral position
for Normal
OFFSET Position Neutral
positionwhen setting minus
OFFSET Position
When setting minus
・NO →Cancel to Change Throttle Type
・YES →Confirm to Change Throttle Type
ENTER BACK
FUNCTION [FUNC] SETTING
OFF SET
THROTTLE TYPE [TH TYPE]
● Function can set trim, ALB (Anti-Lock Brake), OFFSET, and TH TYPE (Throttle Type) on each channel.
● By moving the position of the throttle neutral at the time of starting a nitro RC car engine, it improves the
start-up performance of the engine.
● You can x at a position where idling speed is increased so that the engine will not stop during refueling
your nitro RC car.
● By operating the switch that has been set, you can stop the engine of your RC boat.
● You can use various power sources with Offset feature.
● ON/OFF of the Offset can be assigned to the switch.
1) Select [OFFSET] with up and down key.
2) Determine with enter operation.
It will change to OFFSET Setting menu.
3) Setting Offset [OFFSET]
Set ON/OFF of the Offset feature with up and down key.
○ Setting Range: ON/OFF
○ Default: OFF
4) Setting Position [POSI]
Set Position of the Offset with up and down key.
○ Setting Range: H100%~B100%
○ Default: 0%
● You can move the neutrals position of the throttle and set the operating ratio of the forward side and the
brake (backward) side to either 7:3 or 5:5.
*Set the throttle type according to the speed controller to be used.
1) Select [TH TYPE] with up and down key.
2) Determine with enter operation.
It will change to TH TYPE Setting menu.
3) Setting the Throttle Type
Set the Throttle Type with up and down key.
○ Setting Range: F7:B3 / F5:B5
○ Default: F7:B3
*When changing TH TYPE, the screen changes to
the conrmation screen and a message is displayed.
Operate following the message.

3029
How to Use Each Feature
How to Use Each Feature
How to Use Each Feature
Sw1
Sw3
Sw2
Trm2
Trm1
Trm3
Switch 3
(SW3)
STEP Setting
Shortcut for Key Assign
ENTER BACK
Operation Position
AUX1 Setting AUX2 Setting
Switch CH to SET with up and down key.
Select CH with enter.
Sw1
Sw3
Sw2
Trm2
Trm1
Trm3
Switch 3
(SW3)
Shortcut for Key Assign
Switch Type
Trim 3
(TRM 3)
ENTER BACK
Switch CH to SET with up and down key.
Select SET with enter.
AUX AUX
STEP AUX
POINT AUX
● AUX menu sets the performance of AUX1 and AUX2 (3ch, 4ch). You can choose from STEP AUX (STEP),
POINT AUX (POINT), 4WS (4-Wheel Steering: Coordinate Phase, Opposite Phase). MOA (Motor On
Axle), AUX-MIX (AUX Mixing: ST → AUX/TH-AUX) and CODE-AUX.
● Setting Step AUX allows you to set the operating quantity by operating assigned Trim or a switch.
● By factory default, the AUX feature is set to the Step AUX.
1) Select [AUX] with up and down key.
2) Determine with enter operation.
It will change to CH Setting menu.
3) Setting Step AUX (STEP AUX)
Determine [CH] to activate with the enter.
Set the position of the motion with up and down key.
*Operating range also can be set by
EPA (End Point Adjustment, P.24).
○ Setting Range: H100% ~L100%
○ Default: 0%
4) Mode Setting (MODE)
Determine with enter, and set working step values
to the used method.
○ Setting Range: 1/2/5/10/20/25/50/100
○ Default: 5
SET can be AUX TYPE and MODE setting and
shortcut of the key assign function.
*Assign the features to Trim and switch with
Key Assignments according to the used method.
● By setting Point AUX and assigning the movement of AUX1/AUX2 (3ch, 4ch) to the
switch and Trim, you can move the servo to Point1, Point2, and Point3 position.
The Point that moved can be set with EPA (End Point Adjustment). Adjust the Point position according to
the usage.
*Point number is 3 point cannot change.
1) Select [AUX] with up and down key.
2) Change [SET] menu with enter.
*Switch CH to SET with up and down key.
3) Type Setting (POINT)
Select [POINT] on AUX TYPE with up and down key.
4) Point and setting values
Select A1 or A2 you want to set and enter.
Select 1, 2, or 3 you want to set and enter.
Set values with up and down key.
*AUX1 and AUX2 can be set AUX TYPE separately.
*Operating range also can be set by
EPA (End Point Adjustment, P.24).
*Assign on SW3 or trim according to the used method.

3231
How to Use Each Feature
How to Use Each Feature
How to Use Each Feature
Switch Working Mode
F-ST
REV
F-ST F-ST
R-ST
2mode 3mode 4mode
Servo Monitor
NOR
REV
R-ST
F-ST
Shortcut for Key Assign
Switch CH to SET with up and down key.
Select SET with enter.
REV
NOR
REV
NOR
Steering Working Image
L side Neutral R side
L side Neutral R side
L side Neutral R side
L side Neutral R side
Shortcut for Key Assign
Switch Type STEP Setting
Front-Rear Drive Ratio
Servo Monitor
Switch CH to SET with up and down key.
Select SET with enter.
MOA Motion Image
Front Drive
Rear Drive
Front Drive
Rear Drive
Front Driv
e
Rear Drive
*By changing the ratio, you can adjust the gear ratio of front-rear.
AUX AUX
4-WHEEL STEERING [4WS]
FRONT-REAR WHEEL SEPARATE DRIVE [MOA]
● AUX menu sets the performance of AUX1 and AUX2 (3ch, 4ch). You can choose from STEP AUX (STEP),
POINT AUX (POINT), 4WS (4-Wheel Steering: Coordinate Phase, Opposite Phase). MOA (Motor On
Axle), AUX-MIX (AUX Mixing: ST → AUX/TH-AUX) and CODE-AUX.
● With the operation of assigned Trim or Switch, control the motion of the 4 Wheel Steering.
1) Select [AUX] with up and down key.
2) Change [SET] menu with enter.
*Switch CH to SET with up and down key.
2) Type setting (4WS)
Select [4WS] on AUX TYPE setting with up and down key.
4) Mode setting
Set 4WS working mode to used method.
○
Setting Range: 2 mode / 3 mode/ 4 mode
○
Default: 4 mode
*Please refer the above picture for working mode.
5) Working mode setting
Enter working mode setting and change the mode
with up and down key.
*In case of changing mode while driving,
please asign workig mode on trim or switch.
○
Setting range: F-ST / REV / NOR / R-ST
* Switch working mode by mode setting on SET.
* Rear steering servo will work on AUX 1 or AUX channel
by setting 4WS.
*Operating range can be set by
EPA (End Point Adjustment, P.24).
● By setting Motor On Axle (MOA), you can adjust the drive ratio of front and rear wheels of a front-rear dual
motor car.
1) Select [AUX] with up and down key.
2) Change [SET] menu with enter.
3) TYPE setting (MOA)
Select [MOA] on AUX TYPE setting with up and down key.
4) MODE setting
Set MOA drive ratio to the used method.
Setting Range: 1/2/5/10/20/25/50/100
Default: 10
*Connect the speed controller for controlling the rear motor
to the channel (AUX1/AUX2) that is set to MOA.
*When using, assign the features to switch or trim
or operate with up and down key.

3433
How to Use Each Feature
How to Use Each Feature
How to Use Each Feature
When Mode Setting Is CODE 10
*CODE6~10 is not displayed on top display.
Please check display on the AUX menu.
+100 -100
CODE1 Parameter
CODE2 Parameter
CODE3 Parameter
CODE4 Parameter
CODE5 Parameter
0
Switch Type Mode Setting
Shortcut for Key Assign
Switch CH to SET with up and down key.
Select SET with enter.
AUX TYPE = When setting is CODE AUX, bar display
Servo Monitor
Mixing Rate Setting
Shortcut for Key Assign
Switch CH to SET with up and down key.
Select SET with enter.
AUX AUX
AUX MIXING [AUX MIX]
CODE AUX
● AUX menu sets the performance of AUX1 and AUX2 (3ch, 4ch). You can choose from STEP AUX (STEP),
POINT AUX (POINT), 4WS (4-Wheel Steering: Coordinate Phase, Opposite Phase). MOA (Motor On
Axle), AUX-MIX (AUX Mixing: ST → AUX/TH-AUX) and CODE-AUX.
● Setting AUX Mixing allows you to mix from the steering to AUX and from the throttle to AUX.
1) Select [AUX] with enter.
2) Change [SET] menu with enter.
*Switch CH to SET with up and down key.
3) TYPE setting (AUX-MIX)
Select [AUX-MIX] on AUX TYPE setting with up and down key.
4) MODE Setting
Set mixing mode to the used method.
○Setting Range: ST-mix / TH-mix
○Default: ST-mix
*ST-mix is mixed from the steering to AUX.
TH-mix is mixed from the throttle to AUX.
5) Mixing rate setting
Set mixing rate with up and down key.
○Setting Range: 0%~100%
○Default: 100%
*Assign the features of the Mixing Rate to Trim or the switch
with Key Assignments, or operate with up and down key.
● Code AUX (CODE AUX) is a feature to perform code communication
by assigning a setting value to each code of CODE1-CODE10.
It is an extension feature to change the setting of speed controller (SUPER VORTEX series/ SV-D2), PGS
servo series, and the Gyro System (SGS-01C/SGS01D/SGS-02) that are compatible to CODE AUX.
● You can set 2 types of Code AUX1 and CODE AUX2.
*Please set response mode [SHR] on A1 and A2 when binding with a receiver. (p.43).
*In case of using CODE AUX, please do NOT conect servos on receiver CH3 and CH4 port.
1) Select [AUX] with up and down key.
2) Change [SET] setting menu with enter.
*Switch CH to SET with up and down key.
3) Type Setting (CODE AUX)
Select [CODE] on AUX TYPE setting with up and down key.
*CODE is only compatible with CODE10 products.
*MT-R is not compatible with CODE5 products such as
SV-ZERO, SV-SPORT, SV-TYPE D, SGS-01, and SGS-01D.
4) Mode setting
Display function name for CODE10 products
by setting mode for compatible product.
○Setting Range: CODE/SV-G/D(only AUX1)
CODE/PGS/SGS-02 (only AUX2)
○Default: CODE
5) CODE AUX setting
Select CODE with enter you want.
Set value with up and down key.
*In case of setting CODE on AUX TYPE, CODE AUX
setting condition will display on top screen as below pictures.

3635
How to Use Each Feature
How to Use Each Feature
How to Use Each Feature
ENTER BACK
1. Model Display
Select model you want to use
ENTER BACK
ENTER BACK
MT-R has a feature of Direct Model Select. When turning the power switch of the
transmitter on while
pressing the Back/Cancel button, it starts from the MODEL SELECT screen so that you can easily call a
model to use.
SUPPLEMENT
2. Model Select
3. Confirmation
Confirm model you want to use
No: Back to 2.
Yes: Change Model and Back to 2.
Current Model
Model for Change
Alphabet lower cases
Japanese Katakana Japanese Little Katakana
Number and Symbols
ENTER BACK
ENTER BACK
Cursor for select word
Cursor position for select word
(When moving cursor, the line will be flashed)
MODEL MENU MODEL
MODEL SELECT
MODEL NAME
● You can set the features about Model Select, Model Name, Model Copy and Model Clear.
● Installed with high capacity EEPROM and it can memorize data for 20 models of M01 ~ M20.
● You can call model data of memorized M01 ~ M20 easily.
1) Select [MODEL] with up and down key.
Determine with enter.
2) Setting Model Select (MODEL SELECT)
Select [MODEL SELECT] with up and down key.
Determine with enter.
3) Selecting Model
Select Model to call with up and down key.
○ Setting Range: M01 ~M20
4) When moving the cursor to the model to call
and Enter is being operated, a message
is displayed on the screen.
Follow the display to operate and select a model.
● You can register a model name with up to 10 characters of alphabets, numbers, symbols, and Japanese
Katakana for each model.
1) Select [MODEL] with up and down key.
Determine with the Enter operation.
2) Setting Model Name [MODEL NAME]
Select [MODEL NAME] with up and down key.
Determine with the Enter operation.
3) Setting Model Name
Move the cursor “______” with up and down key
to the position to input texts. Once the position
is determined, press the Enter key to determine
the cursor position.
“______” is flashing when moving,
and is turning on when determied.
4) Select texts to enter with up and down key. Once the
texts to enter are determined, enter with the Enter key.
*When changing texts are already entered or
when moving the cursor of the text input position,
press the Back button to cancel the action.
○ Setting Range: A~Z,a~z,0~9,Symbols, Space,
Japanese Katakana, Little Katakana.
5) Repeat 3) and 4), and enter texts.

3837
How to Use Each Feature
How to Use Each Feature
How to Use Each Feature
ENTER BACK
ENTER BACK
1. Select Copy Model
2. Confirm to Copy
3. Executed
NO: Back to 1.
YES: Move to 3.
Back to 1. after completed
Copy from this model
Model for copy
ENTER BACK
ENTER BACK
1. Confirmation
2. Clear Completion
NO: Back to Model Display
YES: Move to 2.
After flashing twice,
Back to model display
MODEL MENU MODEL
MODEL COPY
MODEL CLEAR
● You can set the features about Model Select, Model Name, Model Copy and Model Clear.
● Installed with high capacity EEPROM and it can memorize data for 20 models of M01 ~ M20.
● You can copy a selected model data to another model.
1) Select [MODEL] with up and down key
Determine with the Enter operation.
2) Setting Model Copy [MODEL COPY]
Select [MODEL COPY] with up and down key.
Determine with the Enter operation.
3) Selection of a Copy Destination Model
Select a Copy Destination Model with up and down key.
*Model for copy is model date is current using model.
4) When Enter is being operated a message is displayed
on the screen. Follow the display to operate
and complete Model Copy.
● A feature to clear (initialize) the setting data of Models.
1) Select [MODEL] with up and down key.
Determine with the Enter operation.
2) Setting Model Clear [MODEL CLEAR]
Select [MODEL CLEAR] with up and down key.
Determine with the Enter operation.
3) When Enter is being operated, a message is displayed
on the screen. Follow the display to operate
and complete Model Clear.
Table of contents
Other Sanwa Control System manuals
Popular Control System manuals by other brands
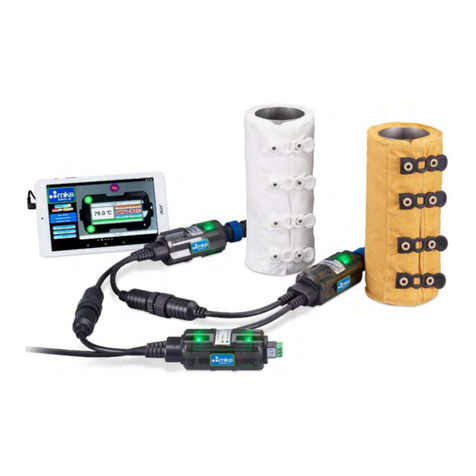
MKS
MKS 49 Series User manual & installation guide
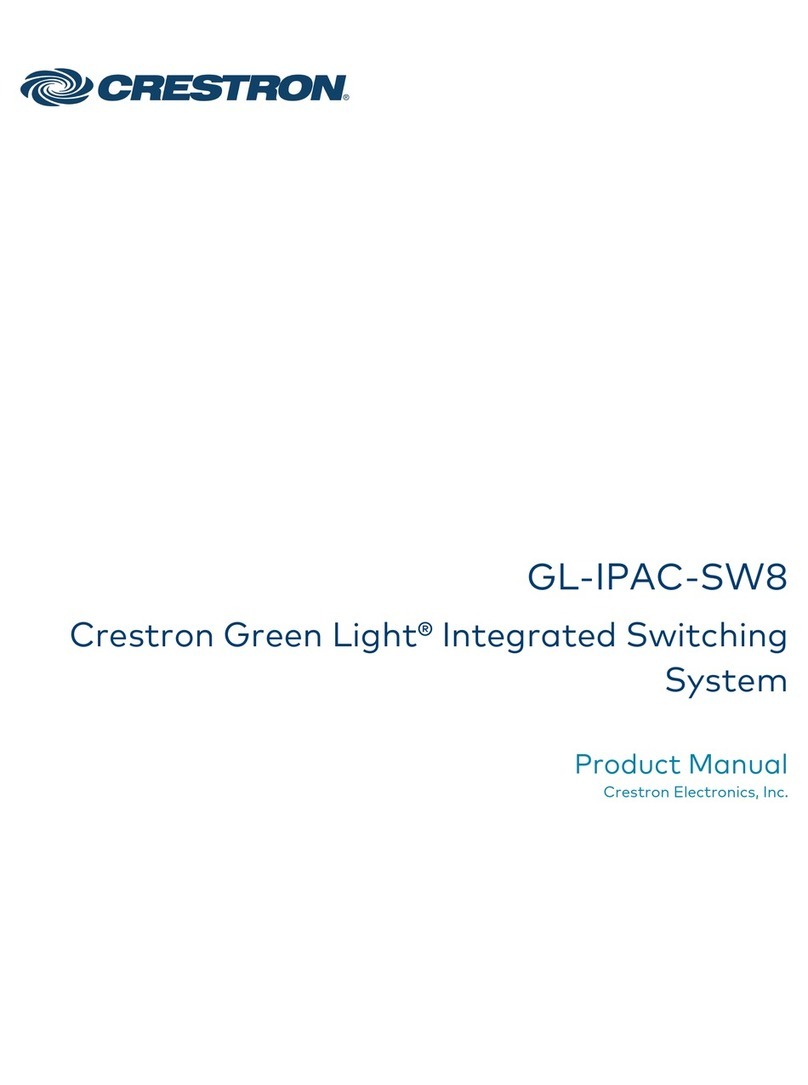
Crestron
Crestron Green Light GL-IPAC-SW8 product manual
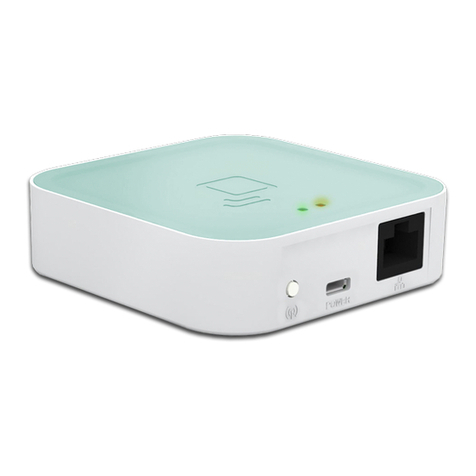
Ducasa
Ducasa Smart Command Tevolve Installation and operating manual
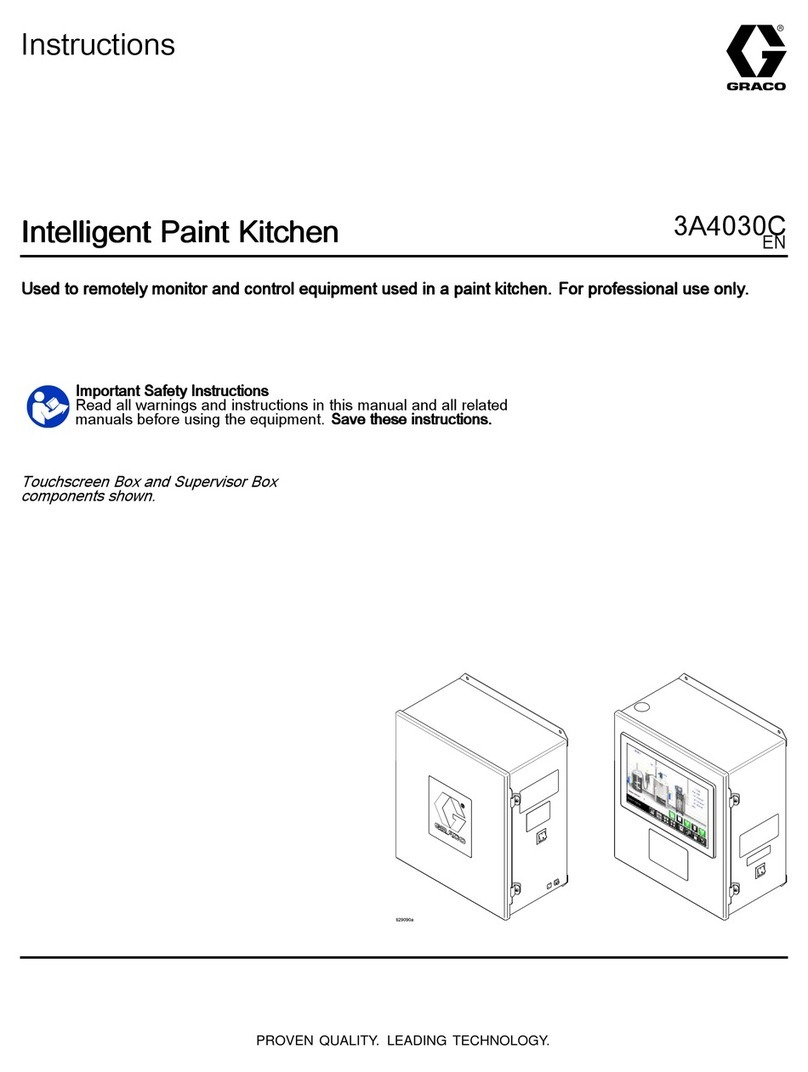
Graco
Graco 25A693 instructions
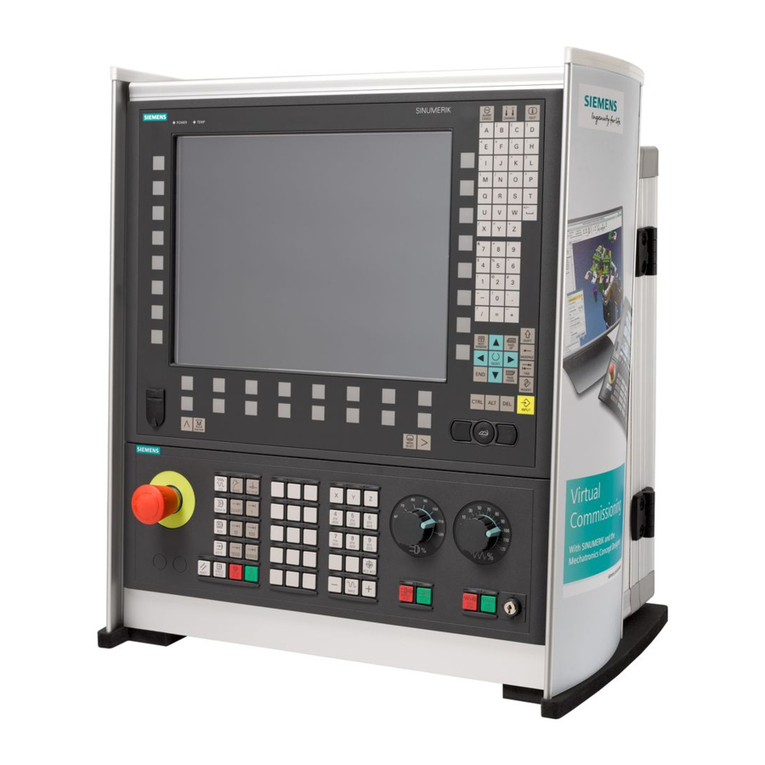
Siemens
Siemens SINUMERIK 840D sl Programming manual
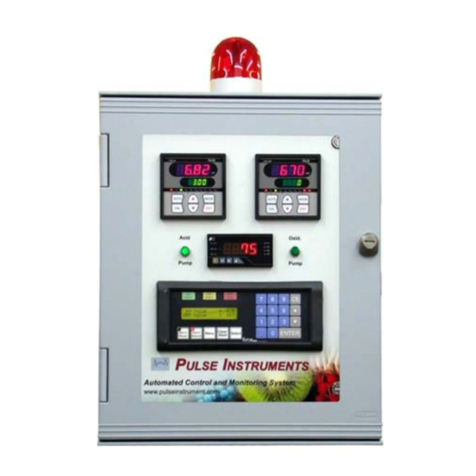
Pulse Instruments
Pulse Instruments System 4 user manual