Sase PDG 8000P User manual





Table of Contents
Cover 1
Letter From Owner 3
Table of Contents 5
Introduction 6
Operation 7
Changing Diamonds 8
Personal Safety 9
Diamond Tooling Quick Reference 10
Motor On Drum 12-13
Frame Complete 14-15
Handle Stem 16-17
Operator Controls 18-19
Belt Reduction Unit 20-21
Complete Drum 22-23
Bottom Drum Assembly Level I 24-25
Bottom Drum Assembly Level II 26-27
Bottom Drum Assembly Level III 28-29
Top Plate Assembly 30-31
Drum Sheave Assembly 32-33
Intermediate Sheave Assembly 34-35
PTO Tensioner Assembly 36-37
Top Belt Idler Assembly 38-39
Top Tensioner Assembly 40-41
Belt Tightener 42-43
Main Belt Idler 44-45
Main Belt Spindle 46-47
Planetary Assembly 48-49
PTO Assembly 50-51
Flex Head 52-53
Tooling 54-55
Belt Paths 56
Troubleshooting 57
Warranty 58-60
Propane Safety Checklist 61-63

Introduction
The SASE PDG 8000 planetary diamond grinders are designed for wet or
dry grinding of marble, terrazzo, granite and concrete. Their applications
range from rough grinding through to a polished finish.
It is extremely important all users be familiar with the contents of this
manual before commencing operation of either machine. Failure to do so
may result in damage to machinery or expose operator to unnecessary
dangers.
IMPORTANT
Only staff that has received the necessary training, both practically and
theoretically concerning their usage should operate the machinery.
Hazards
While, this machine is easy to use and has been used safely for many years, there
are risks involved in operating any large propane machinery.
Toxic Emission Exposure
Fire Relate Incidents
Mechanical action of moving and hot machine parts
Toxic Emission Exposure
The major toxic gasses created when spent propane is exhausted are:
Carbon monoxide (CO) - Over exposure to carbon monoxide results in
brain damage, or death.
Oxides of nitrogen (NOx) –Can damage lung tissue, aggravates
respiratory diseases.
Hydrocarbons (HC) –Can damage lungs.
We have included a sensor to test the air around the machine to limit exposure
to toxic levels of emissions. Without proper ventilation, this sensor will shut
down the machine after 30 seconds of use.
Fire Relate Incidents
The fire related incidents are few, because of strict fire safety prevention laws,
regulations, devices, and practices. Some common causes of fire related hazards.
Over fill –If the tank is too full, and the pressure is vented indoors,
that gas can start a fire, or be trapped dangerously in a room.
Improper storage –The storage location must be safe from extreme
temperature, but also safe from theft, and tampering.
Uneducated users –The end user that does not understand the
danger of improper use can cause unthinkable damage.
Mechanical Action of Moving and Hot Machine Parts
Several parts of this machine are understood to be dangerous.
The front of the machine has a grill indicating it is “HOT”, this is an
understatement. The muffler can reach nearly 1000F Degrees after use, and air
venting from the motor side, can reach 800F to 1000F degrees as well.
The Grind Head has a rotation and a counter rotation, keep body parts clear of
the moving grinder head.
The handle is heavy. Failure to lock the handle in place can result in operator
injury.
During operation, The entire machine has a force of it’s own. If you lose control
of the machine, it will walk away without you. The operator has to maintain
control of the machine while it is on the ground. The machine moving freely can
damage finished floor sections, or wall sections. Not to mention anyone caught
by the grind head would be injured.
Preventative Maintenance
Preventing the hazard is the best case scenario. Preventative Maintenance (PM)
is the responsibility of the operator.
Check and clean air filter regularly
Check Oil and adjust level as needed
Keep a Log Book for all service done.
Check fuel cylinder for overfill before taking them into a building
Be SURE that adequate ventilation is in use.
Properly store propane fuel cylinders and machines.
Be aware of changes in operation, smell, noise, etc. while operating
Report to management ANY safety concerns.
Follow manufacturer recommendations for all motor maintenance.
Propane Cylinder
The cylinder used is classified as a DOT 4E240 cylinder. The service pressure the
cylinder is designed for is at 20 PSI. The cylinder has a pressure relief if it reaches
an excess of 300 PSI. If the tank is overfilled, this pressure relief will become
active once the tank comes up to room temperature.
Pressure relief is highly flammable!
Never store the propane tank on the machine.
Follow local and national regulation when using, storing and filling
propane.
In the case of pressure relief catching fire, it is necessary to cool the cylinder. Use
non-flammable cooling liquid, or a fire extinguisher, to lower the temperature of
the cylinder. The flow of gas should stop, when the cylinder is cooled. Shutting
off the flow of gas should extinguish the fire the gas was fueling.
Propane cylinders are above the capacity for storage in a place frequented by the
public. So, storage on site at a grocery store would be against national fire safety
code. NFPA 58 chapters 5 and 8
Storage
The machine should always be stored in a cool, dry place when not in use.
Do not store the machine with propane attached.
The propane cylinder has to be stored in accordance with local and national
regulation. Do not overlook the danger of propane fire or explosion!

Operation
Break-Down
The machine can be divided into two main parts.
1. Chassis/Frame section –This comprises the handle bars, body
panels, Propane tank, Steel frame and wheels.
2. Head –this comprises the motor, cover, grinding/satellite/
planetary heads and internal components
The machine has been manufactured to allow movement between the chassis
and head via the connection point. This movement is important during the
grinding process as it creates a “floating” effect for the head. The floating gives
the head a self leveling effect, negating the need to adjust the height of the
head as the machine passes over floor areas with different slopes or
undulations.
Set-Up
Position the grinder in the working area. Make sure there are diamonds
underneath the machine, and that the head locks are tight.
IMPORTANT
Planetary head and grinding heads are set to turn in opposite directions of each
other.(as shown in this depiction)
When using the machine, each grinding head must always have the
same diamond type and number of diamonds as the other heads.
Each diamond must also be the same height as the next.
The Rubber skirt must be adjusted so that a good seal is established,
between the floor and the drum.
When setting the height of the handle, the operator is the guide. The comfort of
the operator during grinding is key. The handlebar should rest right at the
operator’s hip bone. When the machine is running, there will be a grinding force
to one side that can be felt through the handlebars. Use the hip to resist this
force instead of the arms.
Transportation
When transporting, it is important to ensure the machinery is properly
secured at all times to eliminate “bouncing”. Ensure the chassis or frame section
of the machine is secured down at all times when in transit. The machine should
always be transported under cover limiting the exposed to natural elements –in
particular rain and snow. The machine should not be lifted by handle, motor,
chassis or other parts. Transportation of the machine is best done on a
pallet/skid to which the machine must be firmly secured. Do not attempt to slide
the tines/forks from a fork lift under grinding heads unless on a pallet/skid.
Failure to do so can cause extreme damage to grinding heads of machine and
internal parts.
Control Panel
The operator controls consist of a number of toggles and switches, giving 4
separate controls.
Ignition Turn to “START”until motor starts, leave in “ON”until
finished. Turn to “OFF”, for motor stop.
Speed Control The motor is connected to a throttle cable for speed
control. Twist to lock/Unlock, Pull for fast, push for slow.
Clutch Engage/disengage the drum rotation
NEVER ENGAGE/DISENGAGE CLUTCH ABOVE 2000 RPM!
Machine Power-Up
Connect battery harness & propane tank.
Turn Key to “START” position for a moment
Turn Key to “ON” position
Drum Rotation
The green switch controls the electric clutch.
Do not engage the clutch above 2000 RPM’s
In case of emergency stop, disengaging the clutch above 2000 RPM’s could be
harmful to the motor. As some situations are more important than the service
life of your machine, we recommend you use your discretion.
Speed / Throttle
The grinding speed should start low and increase as the operator becomes more
comfortable with the application. Be sure that the RPM’s do not exceed 2000
when starting and stopping the drum rotation. The machine should be running
and the drum rotating before speed selection is fine tuned.
IMPORTANT
It is recommended that machinery be transported with a set of diamonds
attached at all times to ensure protection of locking mechanism for diamond
plates.

Determining Diamond Selection
Diamond Background
Diamond abrasives usually consist of 2 components:
Diamond powder (also known as diamond crystals or grit). By
changing the size of the diamond powder or grit, we can change how
coarse or fine the scratches will be that are left behind from the
grinding process.
A binding agent (metal or resin). Diamond powder is mixed and
suspended in either a metal or resin binding agent. When suspended
in a metal bond matrix, the finished product is referred to as a Metal
Bond or Sintered diamond segment. When suspended in a resin bond
matrix, the finished product is referred to as a Resin Bond diamond
segment or pad.
General Diamond Principles
Diamond Grit Size:
Changing the size of the diamond grit to a smaller particle/ grit size will affect the
performance of the diamond tool in the following ways:
Create a finer scratch pattern.
Increase the life of the diamond tool.
The opposite will occur when changing to a larger particle/grit size.
The Binding Agent/Metal Bond or Resin Bond:
Increasing hardness of bond will
Increase life of diamond tool.
Decrease production rate.
Cause diamond tool to leave finer scratches in dry –grinding
applications (when compared to a softer bond diamond tool with the
same diamond grit size).
A hard bond matrix should be used on a soft floor and a soft bond
matrix should be used on a hard floor.
Grinding disc set-up:
The set-up of diamond segments on the grinding heads of the machine will
influence the performance of the machine, the productivity levels and also the
finished floor quality.
There are basically two types of diamond configurations that can be used when
grinding:
1. Half set of diamonds –when there are diamonds placed at three alternating
positions on the diamond holder discs. ( See pictures on upper right).
2. Full set of diamonds –when there are diamonds placed at each of the six
positions on the diamond holder discs. (See pictures on middle right).
Changing of Diamonds
Different applications often require different selections of diamond tooling.
There will be many occasions when the grinding discs need to be changed.
Following is a guide for this procedure.
Preparation
Turn off the clutch, and then turn the key to the off position..
As an extra precaution, unplug battery from motor, to avoid unintentional
starting of the machine while changing disc, which could result in serious injury.
WARNING
It is highly recommended to have a set of gloves ready, as diamonds can get very
hot, especially during dry grinding applications.
Changing
1. Set handle in upright position.
2. Pull back on handle to lift grinding head off the ground (Illustrated
middle right).
3. Lay machine back on the ground
4. Put on gloves.
5. Remove grinding disc from flex plate.
6. Check to ensure that all discs are secure.
7. Once new diamonds have been attached, reverse procedure to lower
machine to ground.
8. As new diamonds may be a different height than the set being
previously used, re-adjust skirt to ensure good seal is established with
the floor.
HALF-SET OF
DIAMONDS
When the diamonds are
set-up as a half-set, they
tend to follow the surface
of the floor. The half-set
diamond configuration
should only be used when
an extremely flat floor
finish is not required.
FULL-SET OF
DIAMONDS
Diamonds that are set-up
as a full-set tend to not
follow the surface of the
floor. If the floor is wavy
the machine will grind the
high areas yet miss the low
spots. The full-set
diamond configuration should be used when a very flat floor finish is desired.

Personal Safety
Please read the operator’s manual carefully and make sure you
understand the instructions before using the machine.
WARNING! Dust forms when grinding which can cause injuries if
inhaled. Use an approved breathing mask. Always provide for good
ventilation while machine is in use.
Always wear approved:
Protective helmet Hearing protection
Dust Mask Protective goggles
Non-slip boots with steel toe Protective gloves
WARNING
Under no circumstances may the machine be started without observing the
safety instructions.
At no time should lifting of machinery be attempted without
mechanical means such as a hoist or a forklift.
Should the user fail to comply with these, SASE Company Inc or its
representatives are free from all liability both directly and indirectly.
Read through these operating instructions and make sure that you understand
the contents before starting to use the machine.
Should you, after reading these safety instructions, still feel uncertain about the
safety risks involved you must not use the machine, please contact your SASE
representative for more information.
Reminder
Always check oil level before starting.
Only qualified personnel should be allowed to operate machinery.
Never use a machine that is faulty. Carry out the checks, maintenance
and service instructions described in this manual. All repairs not
covered in this manual must be performed by a repairer nominated by
either the manufacturer or distributor.
Always wear personal safety equipment such as sturdy non-slip boots,
ear protection, dust mask and approved eye protection.
The machine should not be used in areas where potential for fire or
explosions exist.
Machinery should only be started when grinding heads are resting on
the ground.
The machine should not be started without the rubber dust skirt
attached. It is essential a good seal between floor and machine be
established for safety, especially when operating in dry grinding
applications.
When changing the grinding discs ensure the unit is OFF by turning
the Key “OFF”, and set the clutch to “OFF”.Disconnecting the battery
would add another layer of protection.
The machine should not be lifted by handles, motor, chassis or other
parts. Transportation of the machine is best done on a pallet / skid to
which the machine must be firmly secured.
Extreme caution must be used when moving machinery by hand on an
inclined plane. Even the slightest slope can cause forces/ momentum
making the machinery impossible to brake manually.
Never use the machine if you are tired, if you have consumed any
alcohol, or if you are taking medication that could affect your vision,
your judgment or your coordination.
Never use a machine that has been modified in any way from its
original specification.
Be on your guard for electrical shocks. Avoid having body contact with
lightning conductors/metal in the ground.
Do not disconnect the static strap, this should discharge a great deal
of static that is generated during grinding concrete..
Follow Propane gas safety regulations at all times.



19
25
11
14
8
7
910
1
28
2
4
23
18
6
5
202122
26/
27
3
15
16
17
24
Battery and Battery Box not displayed,
should be on clutch wiring side(right)
- Box gets foam insert
- Top of Battery, should be above,
Top of Box
'Adel Clamp' Not displayed.
Drill ~6.2mm to mount clamp
with 6mm bolt/nut
12
13
34
33
32
30
29
31
Motor On Drum
SHEET 1 OF 1
SCALE: 1:50
WEIGHT:
5
4
3
2
1
PDG 8000 PROPANE

Item No. Part No. Description Quantity
1 PDG.80210.01 DRUM COMPLETE 1
2 SEE PAGE 58 Tooling Plate Complete W/ Mag. 3
3 NB.13.216 SCREW, FLAT HEAD SOCKET CAP M8-1.25 X 16 ZINC 9
4 PDG.80066.00 SHROUD, MOLDED VACUUM 1
5 PDG.20249.00 RUBBER, EPDM GASKET 8FT
6 NB.11.108 SCREW, FLANGED HEX HEAD CAP M6 -1.0 X 16 NON-SERRATED ZINCED 8
7 PDG.20267.00 NIPPLE, 1/4" X CLOSE GALV 2
8 PDG.20268.00 ELBOW, BRASS FEMALE 1/4 NPT X 1/4 NPT 2
9 PDG.20247.00 VALVE, 1/4 BALL 2
10 PDG.20246.00 FITTING, PUSH TO CONNECT 3/8 X 1/4 2
11 PDG.20262.00 TUBING, WATER 5 FT
12 PDG.83352.00 BUMPER, RUBBER 1-1/2" 2
13 NB.30.112 WASHER, FENDER M8.4 X 35 X 2.5 ZINC 2
14 SEE PAGE 24 Belt Reduction Unit W/ Motor 1
15 NB.52.201 CLAMP, ADEL 3/8" 1
16 NB.11.109 SCREW, FLANGED HEX HEAD CAP M6-1.0 X 12 NON-SERRATED ZINCED 1
17 NB.20.132 NUT, NYLOC M6 1
18 PDG.20246.00 FITTING, PUSH TO CONNECT 3/8 X 1/4 2
19 PDG.80055.01 TANK, WATER 1
23 NB.20.140 NUT, SLOTTED-BODY RIVET M6 4
20 PDG.20274.00 T-HANDLE, FLEXIBLE 2
21 NB.12.118 SCREW, SOCKET HEAD CAP M6-1.0 X 35 12.9 ZINC 6
22 PDG.20270.00 TRIM, FLEXIBLE 3/16" X 5/8" 3ft
24 PDG.80081.00 DECAL SET, PDG 8000 1
25 SEE PAGE 18 PROPANE, FRAME COMPLETE 1
26 PDG.83205.00 BOX, BATTERY WITH BRACKET 1
26 NB.16.119 SCREW, BUTTON HEAD SOCKET CAP M8-1.25 X 12 2
26 PDG.83204.00 BATTERY, 12 VOLT 1
28 PDG.80067.00 SHIELD, RUBBER DUST 1
29 PDG.80107.00 SPACER, MOTOR FOR COUPLING DESIGN 1
30 NB.13.256 SCREW, FLAT HEAD SOCKET M16 X 90 ZINC 4
31 PDG.80071.30 GASKET, MOTOR 1
32 NB.82.300 STUD, DOUBLE END THREADED M16 -2.00 X 150 4
33 NB.30.113 WASHER, M14 4
34 NB.20.116 NUT, JAM M16 X 0.5 4
Motor On Drum

5
4
2
3
2
1
9
8
10
6
7
14 12 13 11 18
15
16
17
19
21
20
23
22
24
Frame Complete
SHEET 1 OF 1
SCALE: 1:20
WEIGHT:
5
4
3
2
1
PDG 8000 PROPANE

Item No. Part No. Description Quantity
1 PDG.83320.00 FRAME, ECONO - PROPANE 1
2 VAC.10.095 CLAMP, 3" BLACK PDG VACUUM HOSE 4
3 VAC.HS3.00050 HOSE, BLACK PDG VACUUM 3.0" ID BY THE FOOT 6 FT
4 VAC.10.111 COUPLER, PLASTIC MALE FOR 3" VAC HOSE 1
5 WVAC.10.113 COUPLER, PLASTIC FEMALE FOR 3" VAC HOSE 1
6 PDG.80062.00 BUSHING, METAXENTRIC 2
7 NB.10.132 SCREW, HEX METAXENTRIC ELECTRIC 1"-8 X 5" 2
8 PDG.20412.00 CLAMP, META 2
9 NB.12.219 SCREW, SOCKET HEAD CAP M8-1.25 X 25 12.9 ZINC 6
10 NB.12.253 SCREW, SOCKET HEAD CAP M12-1.75 X 35 2
11 PDG.20411.00 WHEEL, REAR 2
12 PDG.20421.00 CAP, HUB 2
13 PDG.20422.00 RING, QUAD BUNA 2
14 NB.10.219 SCREW, SOCKET LOW HEAD CAP M8-1.25 X 20 ZINC 2
15 WHOL.TC.1502 TANK, PROPANE 1
16 PDG.83345.00 BRACKET, PROPANE 1
17 NB.10.130 SCREW, SOCKET HEAD CAP M10-1.5 X 20 12.9 ZINC 4
18 NB.50.145 PIN, LOCKING M3 X 12 2
19 PDG.83356.00 STRAP, STATIC 1
20 NB.10.126 SCREW, HEX M10 X 16 ZINC 1
21 NB.30.110 WASHER, FLAT M10 ZINC 1
22 PDG.20424.00 EYE, LIFTING 2
23 NB.12.249 SCREW, SOCKET HEAD CAP M12-1.75 X 25 4
24 NB.30.116 WASHER, FLAT M8 X 20 X 4 ZINC 4
Frame Complete

17
18
1
4
5
6
3
2
7
Pivot Assembly
15 14 13 12 11 8 16 10 9
Propane Handle Stem
SHEET 1 OF 1
SCALE: 1:7
WEIGHT: 20.38
5
4
3
2
1
PDG 8000 PROPANE

Item No. Part No. Description Quantity
1 PDG.20395.00 ADAPTER, USB CHARGER 1
2 PDG.83321.00 STEM, HANDLE 1
3 PDG.20410.00 BAR, HANDLE 1
4 NB.10.219 SCREW, SOCKET LOW HEAD CAP M8-1.25 X 20 ZINC 4
5 SEE PAGE 22 OPERATOR PANEL PROPANE 1
6 NB.11.106 SCREW, FLANGED SOCKET HEAD CAP M4-0.70 X 10 ZINCED 4
7 PDG.20423.00 HOLDER, CUP 1
8 PDG.20416.00 PIN, SLOTTED SPRING 1
9 PDG.20418.00 SPRING, COMPRESSION 1
10 PDG.20404.00 HUB, LOCK ACTUATOR 1
11 PDG.20405.00 SCREW, MODIFIED HEX 3/4-16 X 7 1
12 NB.20.154 NUT, JAM 3/4 -16 ZINC 1
13 PDG.20402.00 DISC, STEMLOCK REACTION 1
14 PDG.20401.00 SPLINE, STEM LOCK 1
15 PDG.20403.00 CENTER, STEMLOCK 1
16 PDG.20417.00 KNOB, STEMLOCK 1
17 PDG.83215.00 COVER, STEM 1
18 NB.16.116 SCREW, BUTTON HEAD M5 X 12 ZINC 2
Propane Handle Stem
As of 02/27/2015 we added a USB PORT to the handle stem (PDG.20395.00)

2
4
3
1
5
6
7
Operator Controls
SHEET 1 OF 1
SCALE: 1:5
WEIGHT:
5
4
3
2
1
PDG 8000 PROPANE

Item No. Part No. Description Quantity
1 PDG.83340.00 PLATE, CONTROL 1
2 PDG.83211.00 CABLE, THROTTLE TURN-TO-LOCK 1
3 PDG.83213.00 SWITCH 1
4 PDG.83212.00 HOUR METER 1
5 PDG.83214.00 SWITCH, IGNITION 1
6 PDG.83346.00 WIRING HARNESS (NOT DISPLAYED) 1
7 PDG.83354.00 HOLDER, FUSE 20A (NOT DISPLAYED) 1
Operator Controls

1
2
5
4
6
3
7
8
9
10
12
13
14
15
17
18
16
23
22
21
20
19
25 2728
26
1129
24
PROPANE BELT
REDUCTION UNIT
SHEET 1 OF 1
SCALE: 1:8
WEIGHT: 49.70
5
4
3
2
1
PDG 8000
Other manuals for PDG 8000P
1
Table of contents
Other Sase Floor Machine manuals
Popular Floor Machine manuals by other brands
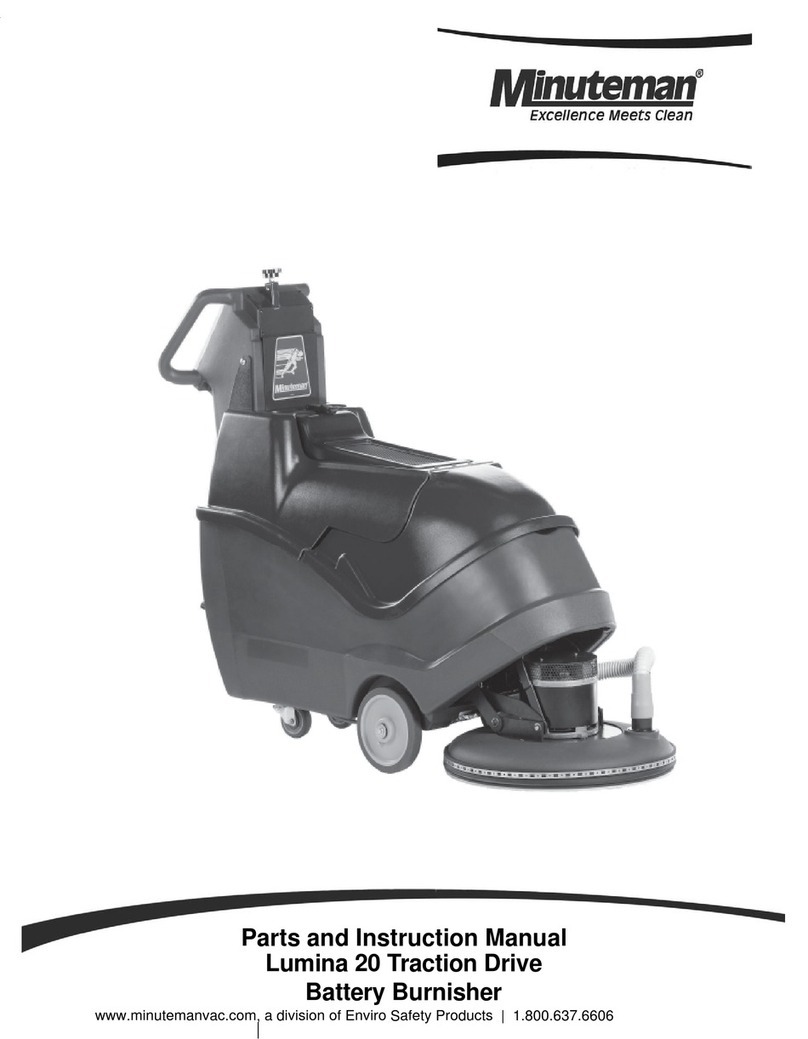
Minuteman
Minuteman Lumina 20 Traction Drive Parts and instruction manual
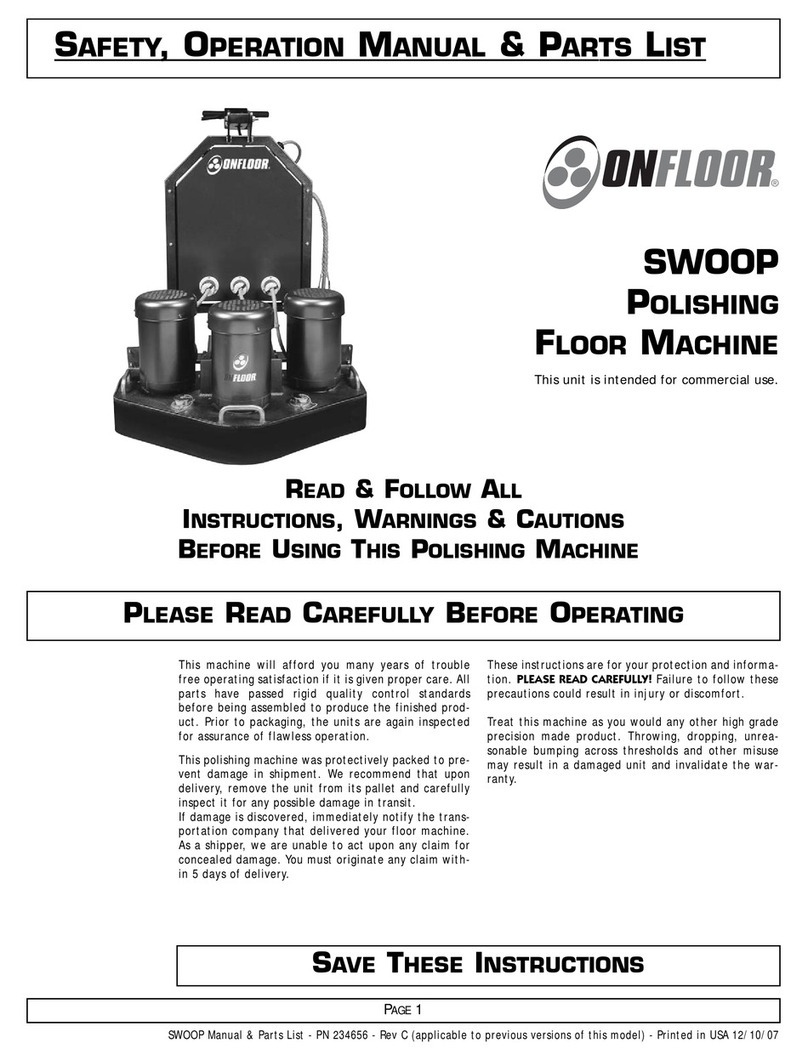
Onfloor
Onfloor SWOOP Safety, operation manual & parts list
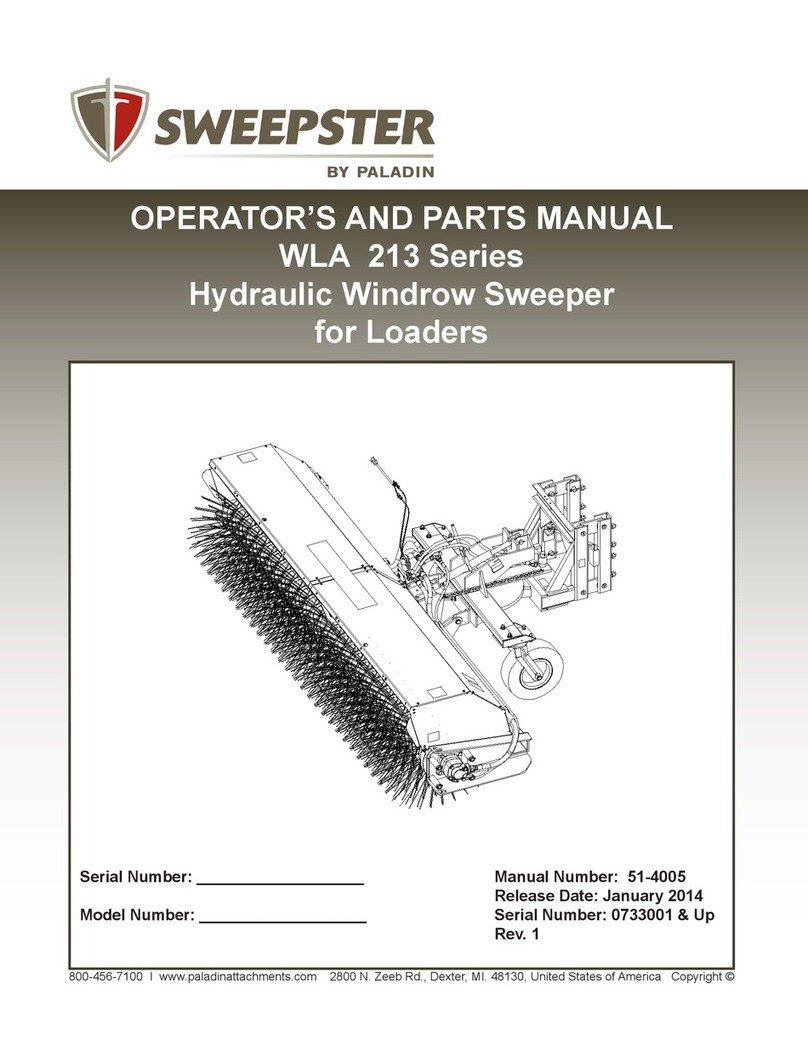
Sweepster
Sweepster WLA 213 Series Operator and parts manual
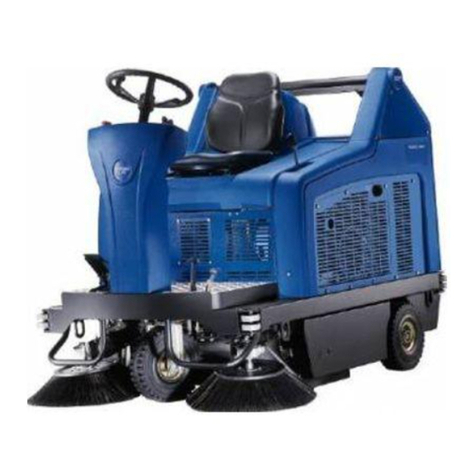
Nilfisk-ALTO
Nilfisk-ALTO FLOORTEC R 580 P user manual
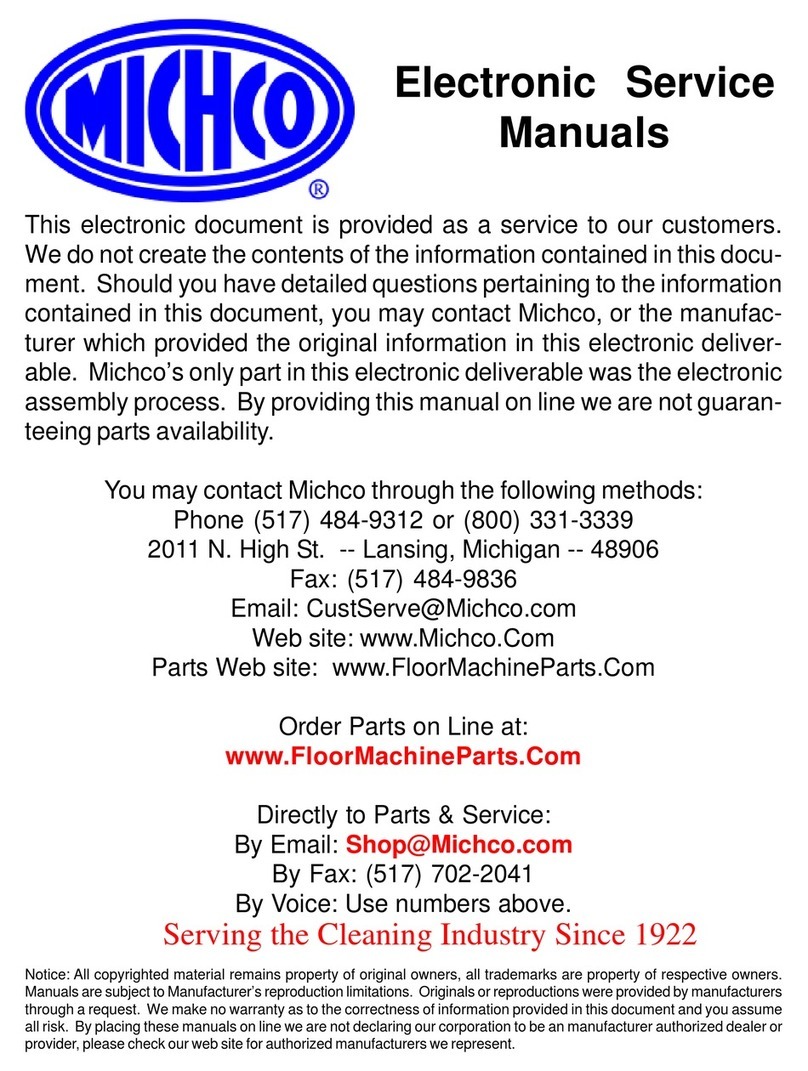
Clarke
Clarke Carpetmaster 577 Operator's manual
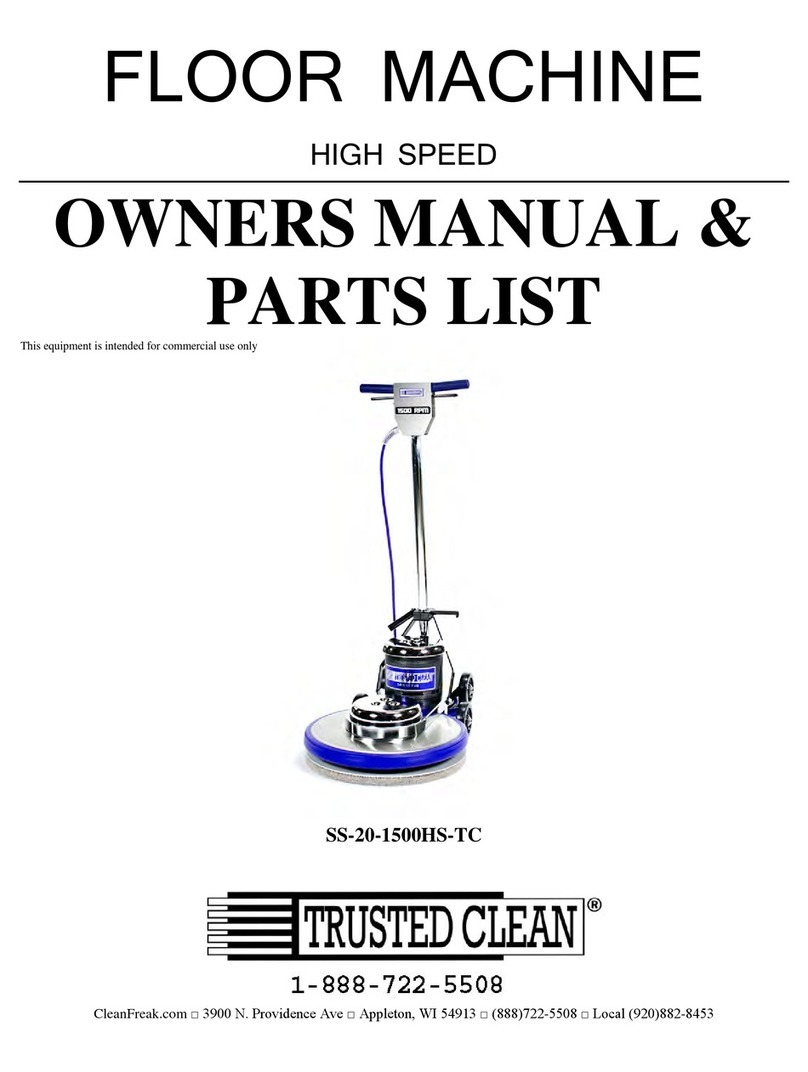
Trusted Clean
Trusted Clean SS-20-1500HS-TC owner's manual
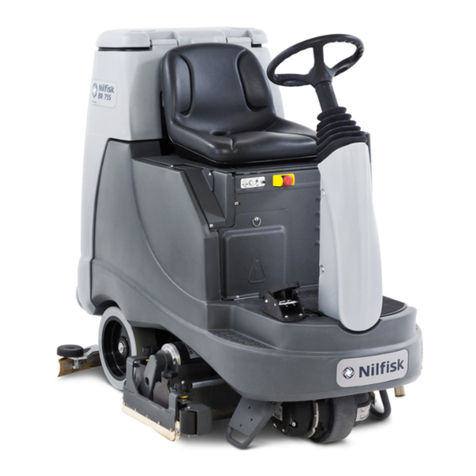
Nilfisk-Advance
Nilfisk-Advance Advenger BR 755 Instructions for use
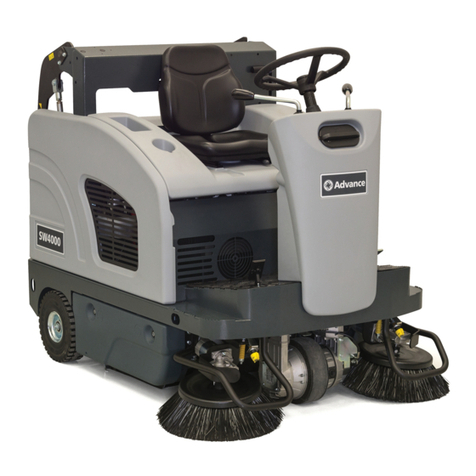
Nilfisk-Advance
Nilfisk-Advance SW4000 Instructions for use
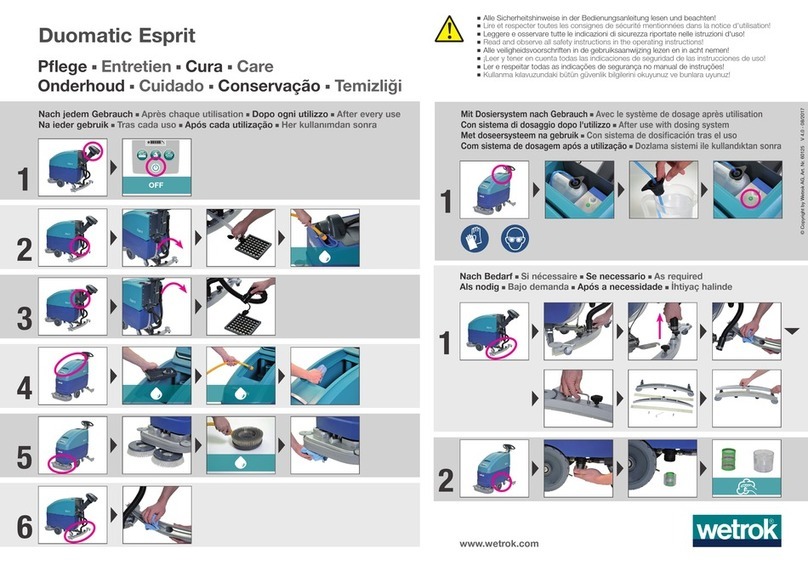
Wetrok
Wetrok Duomatic Esprit manual

Euroclean
Euroclean PS 2000 Operator's manual
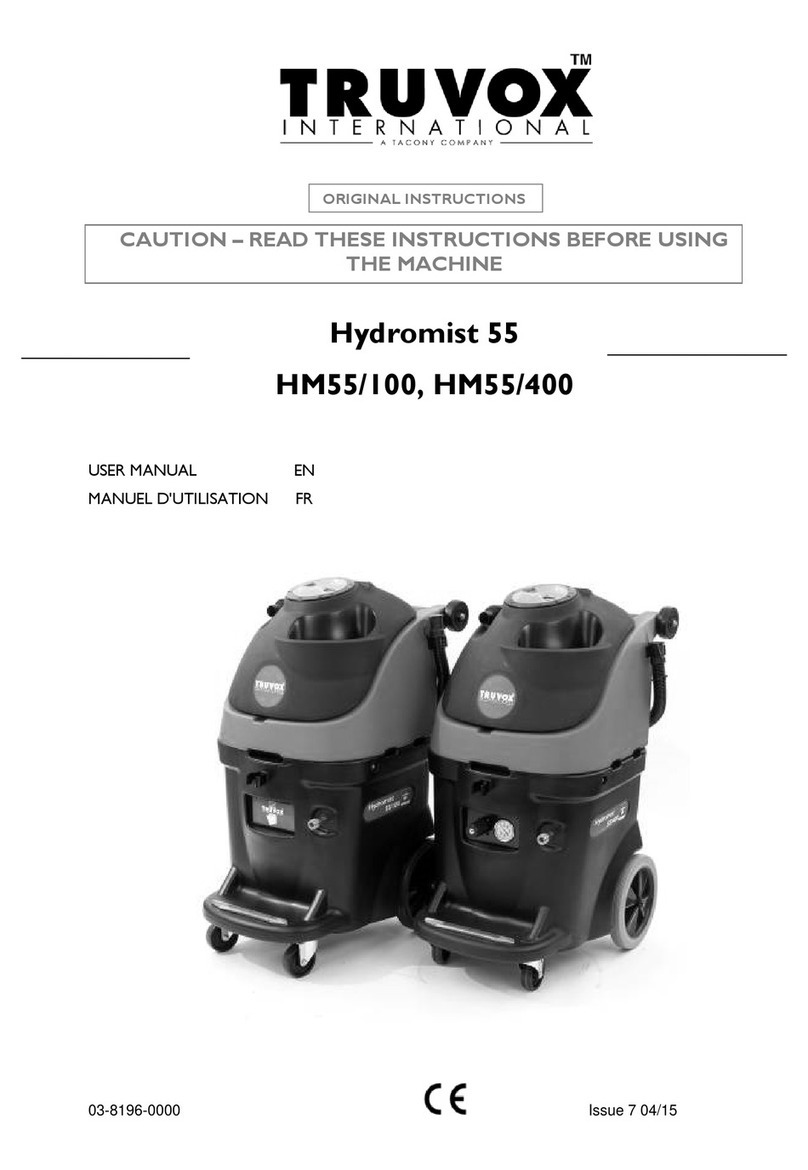
Truvox International
Truvox International Hydromist 55/100 user manual

Eagle power
Eagle power Panther 28 Service manual