Savch SC-3000 Series User manual

SC-3000 Series Control Panel
For round knitting machine
User Manual
User Manual

SC-3000 Series Control Panel
For round knitting machine
User Manual
File No. 520010143000
Vision No. V1.0
Filing time 2017-11-09
SAVCH electric provide a full range of technical support for our customers.
All users could contact with the nearest SAVCH office or service center,
also could contact with our headquarters directly.
SAVCH Electric reserves the copyrights and all rights,
Subject to change without further notice.

Contents
PREFACE ..................................................................................................................................................................1
1. Safety instructions .................................................................................................................................................1
1.1 Safety precautions and notes ......................................................................................................................1
1.2 Installation and wiring...................................................................................................................................1
1.3 Troubleshooting............................................................................................................................................2
1.4 Maintenance.................................................................................................................................................2
2. Product characteristics ..........................................................................................................................................2
3. Panel functions annotation ....................................................................................................................................3
4. The rear cover terminal and wiring diagram..........................................................................................................5
4.1 Functions of the rear cover terminal ............................................................................................................5
4.2 External wiring..............................................................................................................................................5
5. Example explanations of operation and display....................................................................................................6
5.1 Startup..........................................................................................................................................................6
5.2 Adjustment and display of the normal rotating speed and jog speed..........................................................6
5.3 Parameter setting.........................................................................................................................................6
5.4 Disable / Enable of setting and speed regulation operation........................................................................8
5.5 Startup and operation...................................................................................................................................8
5.6 View production and browse the set values ................................................................................................9
5.7 Abnormal situation display ...........................................................................................................................9
5.8 Application of STOP, JOG and FORCE button ..........................................................................................10
5.9 Shutdown ...................................................................................................................................................11

1
PREFACE
Welcome to use SC-3000M microcomputer controller produced by SANCH. For the safety running and effective
operation of SC-3000M microcomputer controller, this instruction manual shall be read thoroughly prior to use,
which shall also be preserved for later use.
1. Safety instructions
For safety running of the machine and prevention of casualties, please read this instruction and always comply
with the following safety precautions and notes:
1.1 Safety precautions and notes
(1) Make sure it is protected from the following: Dust, lampblack, conductive dust, corrosive gas, flammable gas,
high temperature, condensation, wind and rain, vibration, impact, etc.
(2) Only authorized personnel is allowed to repair and test the electric parts to avoid causing bigger fault and
injury or property loss.
(3) Please do not open the cover plate when the equipment is running, to avoid accident since some parts inside
the product is with high voltage.
(4) It easily causes fire and severe damage if using spare parts that is not provided by our company.
(5) Please do not touch any running parts when the machine is running, otherwise, it is probably to cause injury.
(6) Please do not carry out any production when the running parts is without shields.
(7) Please do not make any insulation test to the input/output circuit of the product, otherwise it will directly cause
equipment damage.
1.2 Installation and wiring
(1) During the processing of installation and wiring, please make sure all the power supply has been cut off in
order to prevent people from electric shock and to prevent the product from damage.
(2) After the finishing of the installation and wiring, never fail to install the incidental terminal cover when
connecting the power supply and running the machine to prevent electric shock.
(3) Please seriously check the power supply wiring, to avoid damaging controller.
(4) The ports no. is unified, which are the same to the no in wiring terminal board that is equipped in equipment
control box.
(5) Upper/Middle broken yarn, pin drive/oil drive, when there are drive out, do not make short circuit between
input port and grounding (L0V), otherwise, it will cause product damage.

2
1.3 Troubleshooting
(1) No display when power on:
Power on and check if button OFF red light is flashing, if no flash, please check if the external cable is wrongly
connected or locked, or if the voltage is fused; If the OFF light is flashing but can not power on, please check if
AC12V(port 5,6) voltage is normal, if the voltage is lower than 11V or below, it will cause unstable power on.
(2) Panel displaying P**Error fault: Please check history alarm and contact with us.
1.4 Maintenance
(1) Never touch the terminals while power on to prevent electric shock and incorrect manipulation.
(2) To clean and tighten the terminal only when power off to prevent electric shock.
(3) Please ensure that it is safe before force start oil pump and fan. Operation mistakes can result in damages of
the machine and occurrence of accidences.
(4) When abandoned, the product shall be treated as industrial waste.
2. Product characteristics
(1) Full digital control system with the high-performance DSP CPU as its core processing;
(2) There are three working models as well as their value setting for the pump operation mode: continuous,
interval by the second and interval by the cycle;
(3) Available to set the jog rate, which could be lightly adjusted during running;
(4) The frequency regulation of the 64 inverter;
(5) Available to disable/enable the operation of setting and adjustment;
(6) Make sure that the power supply method of the inverter complies with the principle of make-before-break,
ensuring that the non-loaded operation of the contactor and the reliable operation of the inverter;
(7) Under the shutdown state, the fan and pump can conduct the forced operation function;
(8) The on-site data storage function at power-down.
(9) Protection and display of multiple anomalies; Force jogging and supper force function of some part anomalies.
(10) The cloth lap counting in working phase, output statistics of the three shifts of A/B/C and the gross statistics
(11) Available to set if output signal light drive of break pin and lack oil.
(12) To avoid machine stop due to break yarn and magnify the break pin accident.
(13) RS485 communication monitor.
(14) Scutcher, gas supply, headlight, One choice from three.

3
(15) Double aerodyne protection to avoid break pin: hardware protection and software protection.
(16) The speed of weaving and cleaning is set separately, which makes the operation more flexible.
3. Panel functions annotation
Figure 1. Schematic diagram of SC-3000M general control panel functions

4
Part of annotation for each function of panel:
No.
Function
No.
Function
(1)
Upper broken yarn indicator
(23)
Setup button
(2)
Middle broken yarn indicator
(24/25)
Increase/decrease vaule setting button
(3)
Probe abnormal indicator
(26)
Enter button
(4)
Broken cloth indicator
(27)
Select button
(5)
Oil starvation indicator
(28)
Present shift count display button
(6)
Deficient air pressure indicator
(29)
Total display button
(7)
Inverter fault indicator
(30)
Running value cleaning button
(8)
Exit open indicator
(31)
Forced control button
(9)
External load Short circuit indicator
(32)
Cleaning/knitting switch button
(10)
Stand-by input indicator
(33)
fan control button
(11)
Tachometer
(34)
Fabric illuminator control button
(12/13)
R.P.M
(35)
Headlight control button
(14)
Count meter running/setting
(36)
Inverter power supply control button
(15)
A/B/C- select indicator
(37)
Jogging control button
(16)
Knitting working indicator
(38)
Stop control button
(17)
Cleaning working indicator
(39)
Start control button
(18)
Oil pump working indicator
(40)
Oil pump continuous working mode indicator
(19)
Speed limit indicator
(41)
Intermittently fuel injection by second of oil pump
(20)
Jogging and low speed indicator
(42)
Intermittently fuel injection by cycle of oil pump
(21)
Allowed broken needle probe signal
drive voltage
(43)
Selection button of oil pump working mode
(22)
Allowed oil pump body iil starvation
indicator drive voltage
(44)
Power switch button
Panel measurement:
The panel model of circular knitting machine
Outside measurement (mm)
Installation measurement (mm)
SC-3000M
270*210
256*196

5
4. The rear cover terminal and wiring diagram
4.1 Functions of the rear cover terminal
SC-3000M controller adopts 555X model 2*1 pin、2*3(2*2) pin、2*7 pin and 2*8 pin socket connector, whose
number has the same meaning with the number of terminal circuit board, Those with the same number belong to
the same circuit, see figure 2 of appendix.
4.2 External wiring
Figure 3 is the reference diagram of controller external wiring.
Descriptions:
(1) Allowable wave range of the power-line voltage connected with the machine: 176V~240V for single phase,
305V~415V for three phases; voltage exceeding this rage will affect the controller's performance, even damage
the controller.
(2) Wiring plan for controller and inverter:
[Plan 1] The controller controls the rotating speed of the machine: controller terminal 42 and 43 output adjustable
constant voltage source and adjust the inverter frequency to change the rotating speed of the machine; Terminal
45, 46 are respectively connected to inverter FWD (Positive rotation), COM to control the rotate/stop of the
controller(no need to use terminal 44);Terminal 27 and 30 are connected with normally open contact of inverter
abnormal relay, in order to stop and cut off the power supply to the inverter when the inverter become abnormal.
[Plan 2] The inverter directly control the rotating speed of the machine: the controller port 44,45 and 46 are
respectively connected with inverter control terminals, jogging, positive rotation and COM of the inverter
operational control end. If the inverter needs to stop and be protected when there is an abnormal situation, it may
connect with terminal 27 and 30. In this plan, the speed regulation and jog speed setting provided by the
controller don't work.
Attention:
Solution 2 is simple, the rotating speed of the machine is offered by inverter directly (including normal speed,
jogging speed and last ring low speed), So the rotating speed adjustment, jogging speed setting and adjustment
of the controller are disabled. Therefore, we suggest use solution 1.
(3) The default power supply for yarn feeder, 3-color lamp, pin drive and oil drive is AC 12V supply (the internal
jumper could be 24V according to the costumer's demand); the default power supply for pumps is AC 220V
supply (the internal jumper could be 24V according to the costumer's demand).
(4) Counter and exit input signal are NPN type.
(5) Output terminal 11 can be selected from either of the three options: Scutcher, gas supply, headlight by
parameter setting.

6
If any special requirement that is not in above using conditions, please contact us, we will make special setting for
u before shipping.
5. Example explanations of operation and display
After installing the controller, please make sure all wiring is correct.
5.1 Startup
Closing textile power supply, if the red light on the left right of OFF ( ) button in the control panel is on, it
means machine is connected to the power supply. When the controller is power off, push button ON ( ), the
green light on the left side is on, it means the controller is connected to power supply. Now tube and LED are both
light on, then display the software of the controller, and 3 nixietube displays “00.0”, 5 nixietube displays the
working status at the time when the controller is turned off last time(first display is H0000), STOP light on.
5.2 Adjustment and display of the normal rotating speed and jog speed
The continuous pressing of the ( ) buttons can increase or decrease the normal rotating speed ranging
from 0 to 63 grade that the inverter provide to general supply during operation, when the nixietube displays the
change progression "uXX".
Press and hold the JOG button, then press the ( ) buttons, by doing this the jog speed can be changed
ranging from 00 to 40 grade. Now the nixietube displays the change progression "uXX", when jogging speed is
adjusted, “u” is flashing and the indicator light above the button JOG light up.
2 seconds after stopping the speed regulation, the 3-bit nixietube area automatically switched to display real-time
RPM value.
5.3 Parameter setting
Under set condition, 3 bit nixietube area indicates setting code, while 5 bit nixietube area indicates setting content,
their corresponding relation and default setting value is as the following.
Setting
code
Representing meaning
Setting content and
adjustable range
Default setting
value
Remarks
1
Weaving setting
0001~9999 cycle
2000 cycle
2
Cleaning setting
01~99 cycle
99 cycle
3-1
Delay time for continuous
fuel injection of oil pump
┖0000~9999
5s
Indicate the delay time
for starting fuel injection
after the machine
running

7
Setting
code
Representing meaning
Setting content and
adjustable range
Default setting
value
Remarks
3-1
Continuous fuel injection
of oil pump
┙0000s
0
3-2
Intermittently fuel injection
by second of oil pump
running┖0001~9999s
300s
Intermittently fuel injection
by second of oil pump
stop┙0001~9999s
1s
3-3
Intermittently fuel injection
by cycle of oil pump
running┖0001~9999
cycle
100 cycle
Intermittently fuel injection
by cycle of oil pump
stop┙0001~9999
cycle
1 cycle
4
Over-speed setting
00~999rpm
50rpm
When the parameter is
set to be "0", it will close
this function
5
Jog speed
00~40 grade
20 grade
6
Broken needle signal light
drive
0-1
0
1/0: yes/no output
7
Oil starvation signal light
drive
0-1
0
1/0: yes/no output
8
Gas supply/Scutcher/
Headlight
0-2
0
0: Gas supply
1: Scutcher
2: Headlight
Setting access is available only in the status of machine halt. Setting exit is available only when pushing the
confirmed button and return knitting status. In the status of running, the set parameter can be checked by setting
button and display relative items via indication light. The default setting value is the factory setting of
controller,which can be reinstalled according to the customer's demand, the method and description are as
follows:
(1) Enter setting 1 and 2(knitting setting and clear setting status, if no operation more than 3 minutes, it will save
and exit): Push button ( ) to enter status 1, and once more to enter setting 2, long push parameter setting
button ( ), it can continuously increase/decrease setting lap.

8
(2) Enter setting 3-8: Under setting 1 or 2, push clear+setup ( + ) button, and enter.
(3) Setting 3 include three oil working mode parameter setting 3-1, 3-2, 3-3, working mode is selected by pushing
button ( ),the Signal “L” display on the left side of the 5 digital nixietub indicates running data, signal “┙”
indicates stopping data, unit by S or Loop.
(4) Setting 4 is max rotation speed limited value of the machine.
(5) Setting 5 is jogging speed series number of the machine.
(6) Setting 6 and 7 are only with “0” and “1” conditions, “1” indicates allowed drive voltage when the controller
output broken needle or leak oil signal light.”0” indicates that output is prohibited.
(7) Push button ( ) to confirm after setting, then save and exit setting screen, return to knitting status.
5.4 Disable / Enable of setting and speed regulation operation
When the power of the controller is off, press parameters setting up and down buttons ( ), then press
the power button to startup the power supply. This operation can disable or enable setting and speed regulation
operation. Under disable state, both the setting and speed regulation are not available.
The default state of controller when it leaves the factory is "enable" state. Disable/enable state can be memorized
when shutdown.
5.5 Startup and operation
(1) Function selection
Press ( ) button, select weaving or cleaning (only valid in the state of stop), when the indicator light is off, it
indicates that the machine implements weaving operation, when the fourth nixietube displays "H"; when the
indicator light is on, it indicates that the machine implements cleaning, when the nixietube displays "C".
In oil pump working mode, oil model lock must be released firstly, the way it to long push button ( ) for 8s,
when three-color light is on at the same time, it indicates lock status is switched(on/off). At ON status, push
( )to switch oil pump working mode.
Oil pump working mode can operate when setting the value, which is not affected by oil-model lock limit.
(2) Startup
Firstly press the ( ) button, which is valid when the indicator light light up, then press ( ) button after about
2 seconds, the machine starts running. After 5 seconds of time delay, the fan rotates; the air valve opens and
provide air (open the fan operation switch in advance); the oil pump starts and runs in the selected working mode.

9
(3) Operation
Machine rotates for one cycle, the decimal of 5 nixietube display from first to end for one time, and count value
+1.The count value of both the current shift and the total shifts separately add 1, and the three-bit digital meter
displays real-time RPM value.
When count value on 5 nixietube is 1 smaller than setting value of knitting(clear) ,it means that weaving (or
cleaning) operation is performing the last cycle, at this moment the fan stops running, the air valve shuts, the oil
pump stops working, the JOG indicator light is on, and the machine operates in jogging. If the inverter running
frequency is controlled by the controller, the last cycle jogging implements stepless speed regulating by the
controller control; otherwise, the machine jogging implements step speed droop.
After finishing the last cycle, the machine stops running automatically, the weaving (or cleaning) operation
indicator light and the green light of external tricolored signal light blink. Press RESET ( ) button, the five-bit
digital meter value is cleared, the blink indicator light and signal lights is off, ready to implement weaving (or
cleaning) again.
When terminal 11 is set as scotching function and power supply for slitting machine, those two terminals will
output AC220V voltage as long as the machine rotates (including jog).
5.6 View production and browse the set values
(1) View production: Pressing the ( ) button can switch shifts between A, B and C, and the corresponding
indicator light light up. Press the ( ) button, and the digital meter displays a six-figure production of current
shift, and returns to working status display after 3 seconds. Press the TOTAL ( ) button, and the digital meter
displays a eight figure accumulative total of all three selects, and returns to working status display after 3 seconds.
If press and hold the QUANT ( ) button, then press RESET ( ) button, the display of current shift
production will be cleared.
(2) Total table is reset, when 8 bits count value is full, and can not counting the output, it requires to carry out
cleaning to total table, please turn off the controller and push total and reset button ( + ) at the same time,
then push ON ( ) button to power on the controller, release unitl the controller display with normal knitting
data, at that time, total data is reset.
5.7 Abnormal situation display
(1) Controller self-check at startup
The controller will self-check internal circuit at startup, when inspect any abnormal situation, it will display flashing
Err and alarm code, when the situation is appear, please make a note of the alarm code and contact us.

10
(2) Controller external abnormal situation display.
Either one in below 10 external abnormal situations will cause machine stop.
(a) Upper broken yarn: The ( ) indicator light blinks, red light of external 3-color lamp and corresponding
yarn feeding light blink (super force state inhibits all yarn feeding light from blink).
(b) Middle broken yarn: The ( ) indicator light blinks, yellow light of external 3-color lamp and
corresponding yarn feeding light blink (super force state inhibits all yarn feeder light from blink).
(c) Probe abnormal: The ( ) indicator light blinks, external broken needle signal blinks (when setting 6 is
allowed).
(d) Broken cloth: The ( ) indicator light blinks(Broken cloth detector is required to equip in machine).
(e) Oil starvation: The ( ) indicator light blinks, Oil pump body alarm signal light blinks (when setting 7 is
allowed).
(f) Deficient air pressure: The ( ) indicator light blinks.
(g) Inverter fault: The ( ) indicator light blinks, the ( ) indicator light above button goes out, the power
supply to the inverter is cut off. After check the alarm, push button to recovery the power supply , alarm
indicator go out.
(h) Exit not closed: The ( ) indicator light blinks, fabric illuminator light up.
(i) The short circuit of external low-voltage load: The ( ) indicator light blinks, the power supply to
external low-voltage load (such as yarn feeder, 3-color lamp) is cut off. if recovery the machine operation is
required, please turn off the machine and check fault, then turn on again to start the machine.
(j) Standby input fault: The ( ) indicator light blinks.
(k) Machine over-speed: When machine rotation speed is over the setting limited speed, 3 nixietube will flashing
display the over-speed rpm value.
5.8 Application of STOP, JOG and FORCE button
(1) STOP: Pressing ( ) button in operation status can stop the machine from running, reaching set number of
laps or any abnormal situation will result in machine halt, when the air valve shuts, and the fan as well as the oil
pump will also stop running.
Start and stop button priority from high to low are: STOP, JOG and START.

11
(2) JOG: Pressing the ( ) button when stopping the machine, the machine will slowly run or stop. Implement
JOG operation under normal running state, the machine will turn into micro running, and stop after releasing the
button. If press ( ) and ( ) buttons at the same time, the machine will turn into micro running, then release
( ) button, and the machine automatically turns into running in jog speed. The fan and oil pump don't start
when jog.
(3) Application of FORCE button
a) Forcing function: under the 5 kinds of abnormal situation like upper/middle broken yarn, clout, oil starvation,
deficient air pressure, if you want to make the machine have jog function, you must first press the () button,
which is valid when the indicator light above the FORCE button light up.
b) Super forcing function: press () button for 3 seconds, and the indicator light above the FORCE ()
button turns on. At this time, the machine has forcing function,and the power supply to yarn feeder and three color
lamp is cut off, to prevent over-current accident from large quantity of yarn feeding lights' turning on during yarn
changing or tuning. Press () button to quit super forcing function.
c) Forced start of fan/oil pump: Long push button ( ) and do not release under stop condition, pushing button
( ) again can forced start the fan, now the indicator above the button ( ) blinks,. Push button ( ) or
( ), can exit fan forced condition. Long push button ( ) and do not release, pushing button ( ) can forced
start oil pump, now oil works in continuous mode, pushing button ( ) or ( ) can exit oil pump forced
condition, and return to original oil pump. When inverter alarm/short-circuit/exit open accurs, forced fan/oil pump
start is disabled.
5.9 Shutdown
When need to stop using the machine and shutdown, first press ( ) button to make the machine stop rotating,
turn off the load like headlights, then press the ( ) button now on-site data is stored in controller system. If it
is a long-time stop, the general power supply should be switched off.

12
Diagram 2. SC-3000M Rear cover wiring diagram

13
Diagram 3. SC-3000M Controller external wiring diagram

■ Innovate for more | win forever
■ Industry intelligence | Energy saving | Green power
Savch wechat
Service Number
Quanzhou Factory
Address:3# Zixin Road, Jiangnan Hi-Tech Industrial Park,
Quanzhou, Fujian, China
Tel:0595-24678267 Fax:0595-24678203
Service Network
Website:www.savch.net
Qualification
Received ISO9001 and CE recognition
All rights reserved. Subject to change without further notice.
Sales service contact address
Table of contents
Popular Control Panel manuals by other brands
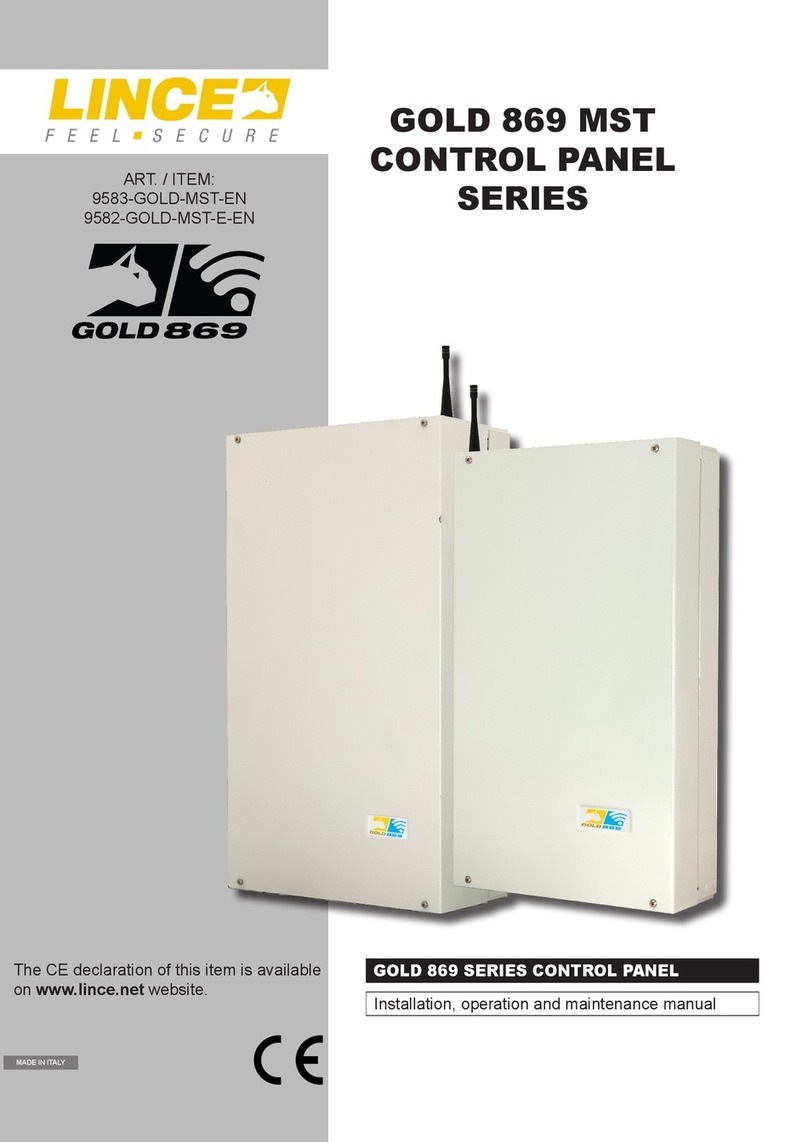
Lince
Lince GOLD 869 MST Series Installation, operation and maintenance manual
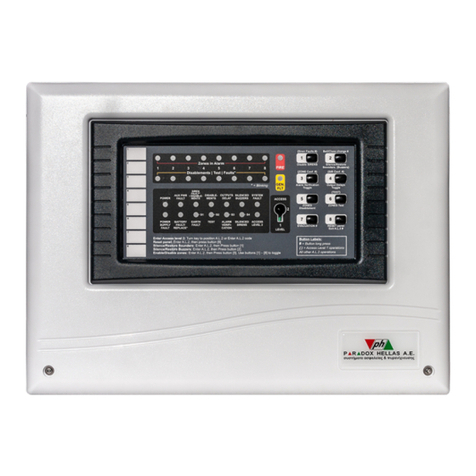
Paradox Hellas S.A.
Paradox Hellas S.A. DEVELOPED Neon 2 Installation and operation manual
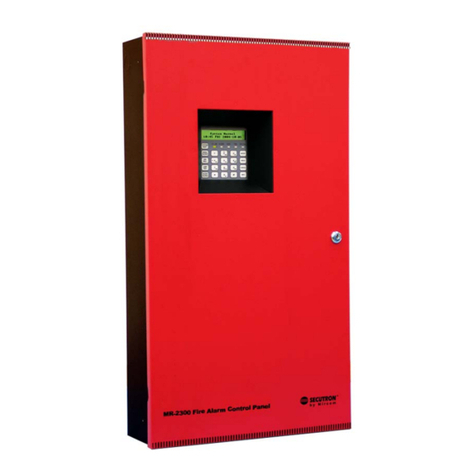
Secutron
Secutron MR-2300 series Installation & operation manual
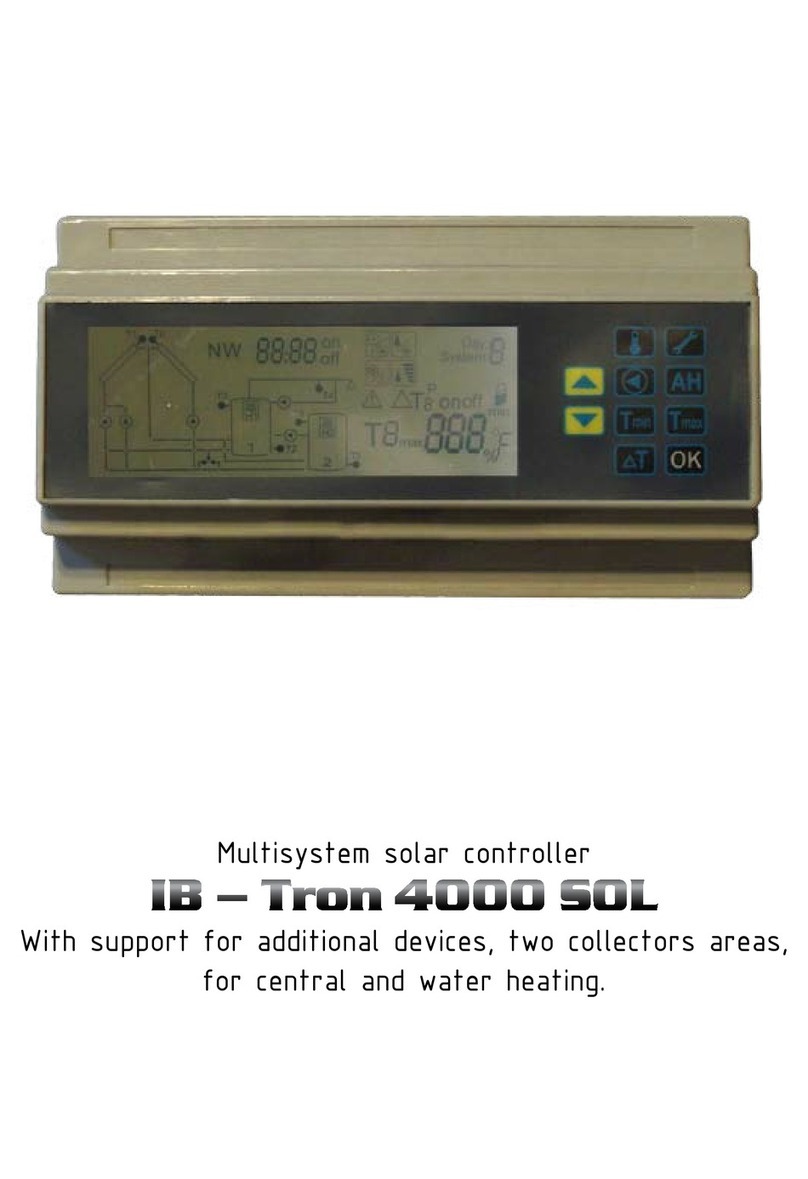
INSBUD
INSBUD IB-TRON 4000 SOL instruction manual
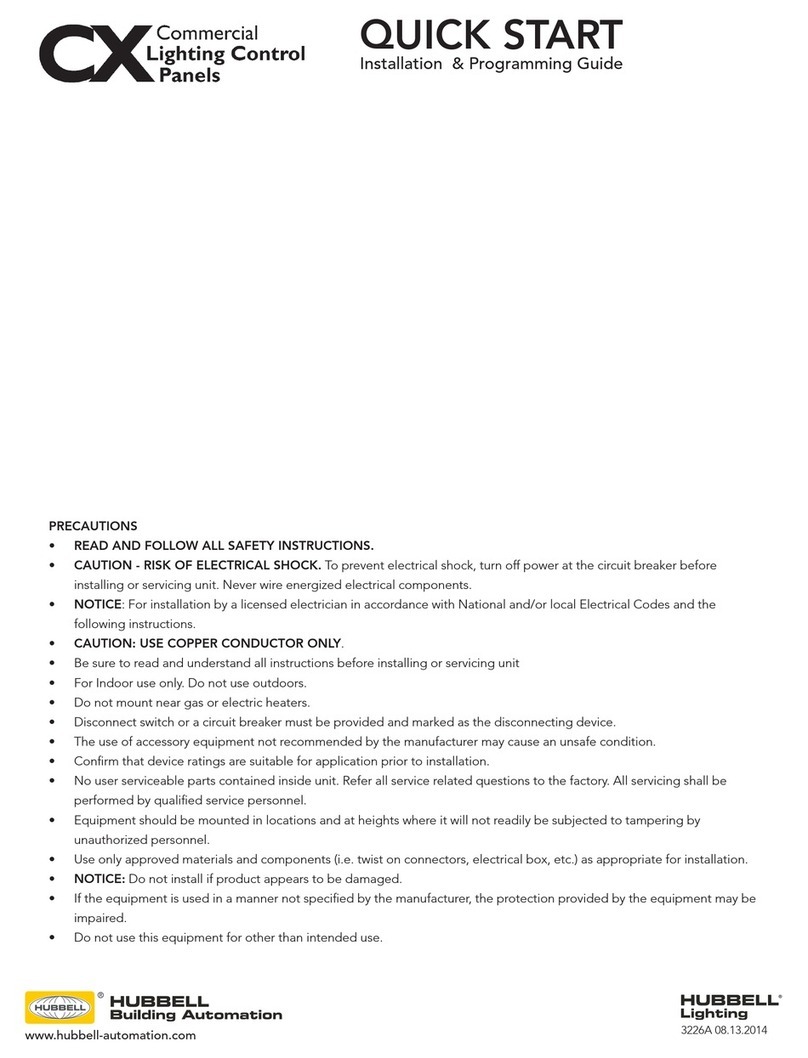
HUBBELL LIGHTING
HUBBELL LIGHTING CX quick start

Velux
Velux INTEGRA KLR 200 user manual
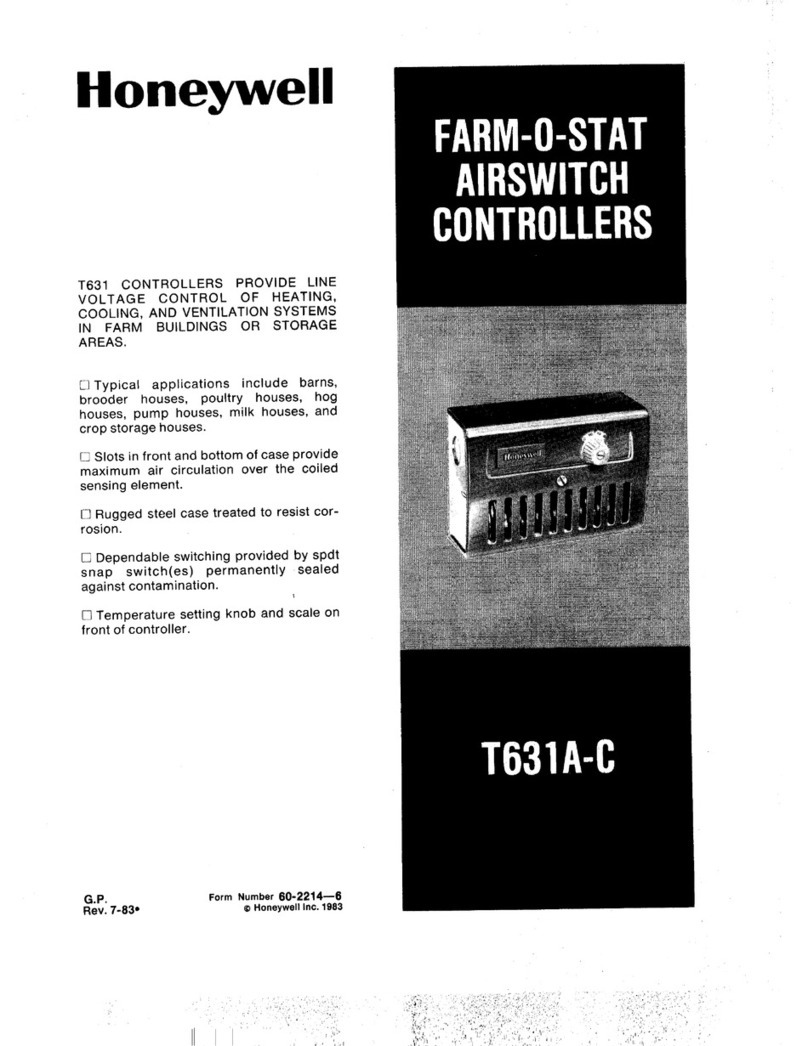
Honeywell
Honeywell T631A-C FARM-O-Stat user guide
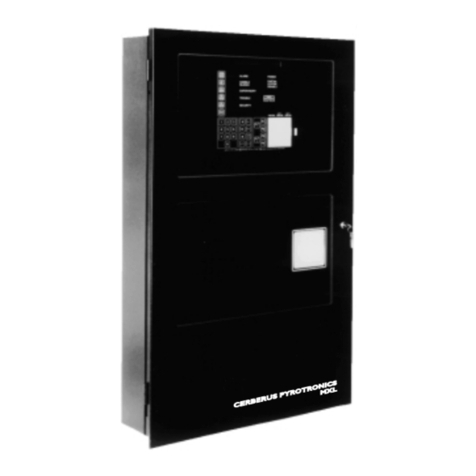
Siemens
Siemens Cerberus PYROTRONICS MXL Operation, installation, and maintenance manual
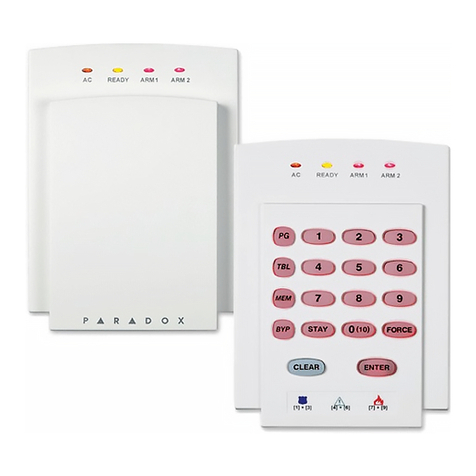
Spectra
Spectra 1728EX System programming
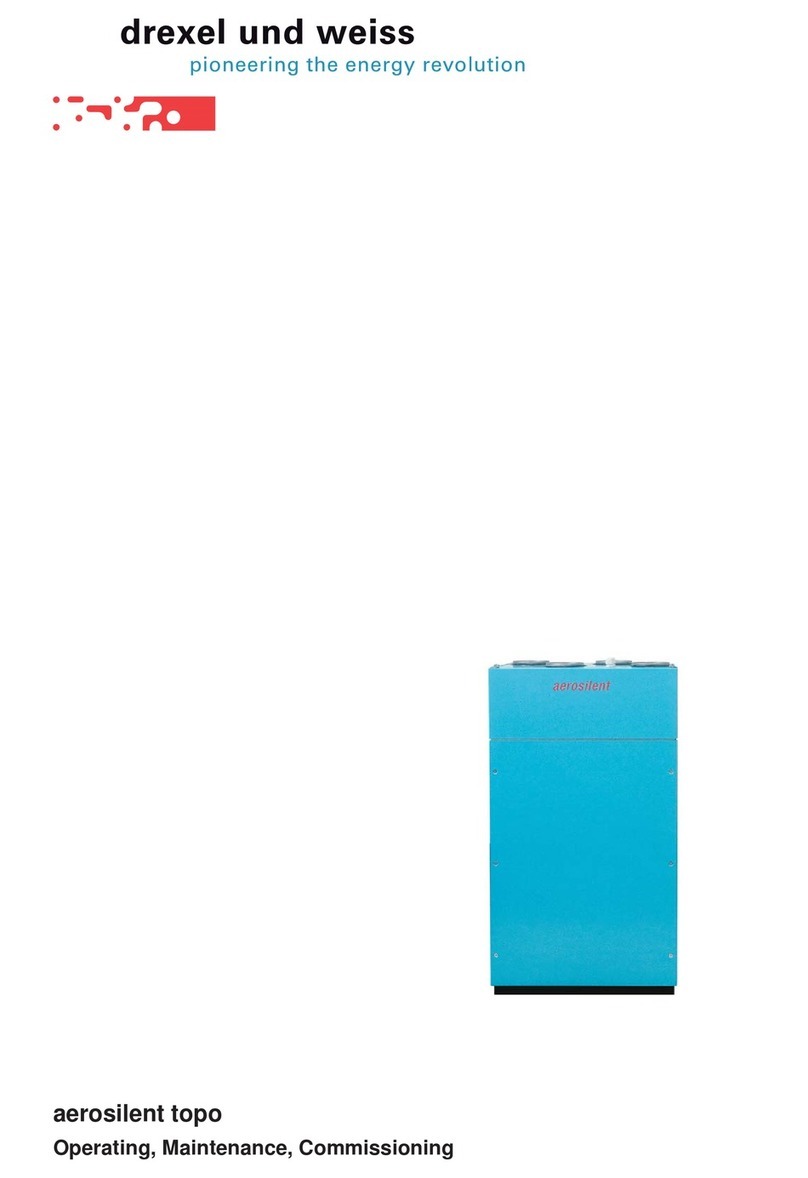
drexel und weiss
drexel und weiss aerosilent topo Operating, Maintenance, Commissioning
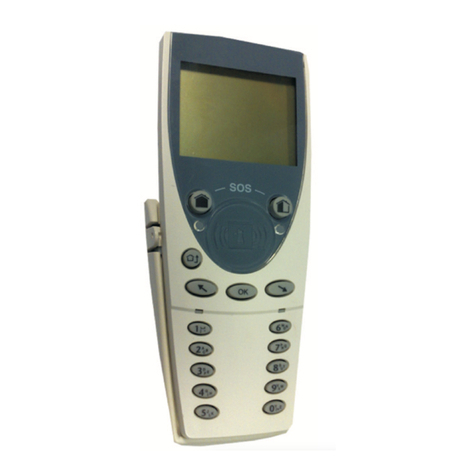
ADT
ADT Honeywell Domonial QUICK CONSUMER REFERENCE GUIDE
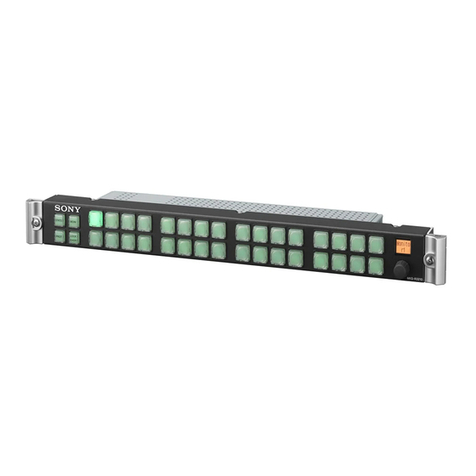
Sony
Sony MKS-R3210 operating instructions