Seametrics PT12 User manual

Precision Environmental Sensors
An ON
I
CON Brand
PROUDLY
MADE
IN THE
USA
C
e
r
t
i
f
i
e
d
C
o
m
p
a
n
y
ISO
9001:2008
PT12
Pressure/Temperature Sensor
Instructions
For PSIG
sensors, refer
to page 16
regarding
desiccant
use!
For Sales & Service Contact
2650 E. 40th Ave. • Denver, CO 80205
Phone 303-320-4764 • Fax 303-322-7242
1-800-833-7958
www.geotechenv.com

PT12 INSTRUCTIONS
Seametrics • 253.872.0284 Page 2 seametrics.com
General Information
General Information ...................................................................................................................................................Page 3
Dimensions ....................................................................................................................................................................Page 3
Specications ................................................................................................................................................................Page 4
How Pressure Sensors Work....................................................................................................................................Page 5
Initial Inspection and Handling..............................................................................................................................Page 6
Do’s and Don’ts............................................................................................................................................................Page 6
Installation
Cable Wiring..................................................................................................................................................................Page 7
Installing the Sensor...................................................................................................................................................Page 7
Desiccant Use................................................................................................................................................................Page 7
Grounding Issues.........................................................................................................................................................Page 8
Sensor/Data Logger Conguration ......................................................................................................................Page 8
Operation/Modbus RTU
Power Consideration ..................................................................................................................................................Page 9
Communication Settings ..........................................................................................................................................Page 9
Modbus Functions.......................................................................................................................................................Page 9
Register Denitions.....................................................................................................................................................Page 9
Sensor Conguration/Control ................................................................................................................................Page 10
Readings and the Auto-Enable Setting...............................................................................................................Page 10
Calibration and Conversion Constants................................................................................................................Page 10
Operation/SDI-12
Reading via SDI-12......................................................................................................................................................Page 11
Calibration Register Denitions .............................................................................................................................Page 15
Maintenance
Removing Debris from End Cone..........................................................................................................................Page 16
Desiccant Tubes ...........................................................................................................................................................Page 16
Sensor/Cable/End Connections .............................................................................................................................Page 17
Troubleshooting
Problems/Probable Causes/Things to Try..........................................................................................................Page 18
TABLE OF CONTENTS

PT12 INSTRUCTIONS
Seametrics • 253.872.0284 Page 3 inwusa.com
GENERAL INFORMATION
The Seametrics PT12 Pressure/Temperature Sensor
has been designed to provide trouble-free submersible
operation in liquid environments. This sensor communicates
via SDI-12 (v1.3) or Modbus®RTU (RS485)protocol.
Pressure/level is measured with an extremely rugged and
stable piezo-electric, media isolated pressure element
and compensated for temperature using Seametrics’
proprietary calibration methodology. Temperature is
measured using an on-board digital chip.
Seametrics also carries a special version of the PT12
designed to measure barometric pressure in reference
to absolute pressure. If you are using an absolute PT12,
contact your representative for details on how our PT12-BV
can facilitate obtaining barometrically compensated
pressure/level.
Dimensions
8.44” (21.4 cm)
0.28” (0.7 cm) Water inlets
Diameter
0.75” (1.9cm)

PT12 INSTRUCTIONS
Seametrics • 253.872.0284 Page 4 seametrics.com
Specications*
GENERAL INFORMATION
Housing & Cable Weight 0.8 lb. (0.4 kg)
Body Material 316 stainless or titanium
Wire Seal
Material Fluoropolymer and PTFE
Cable Submersible: polyurethane, polyethylene, or ETFE; 4 lb./100 ft., 1.8 kg/30 m; 2000 ft max for Modbus®
Desiccant 1-3 mm indicating silica gel
Field Connector Available as an option
Temperature Operating Range Recommended: -15˚ to 55˚C (5˚ to 131˚F) Requires freeze protection kit if using pressure option in water
below freezing.
Storage Range -40˚ to 80˚C (-40˚ to 176˚F)
Power Voltage 9-16Vdc, 24Vdc over voltage protection, electromagnetic & transient protection IEC-61000 - 4-3, 4-4,
4-5, 4-6
Supply Current Active 3mA average/ 10mA peak; sleep 150 µA
Communication Modbus® RS485 Modbus® RTU, output=32bit IEEE oating point
SDI-12 SDI-12 (ver. 1.3) - ASCII
Output Channels Temperature Depth/Level¹
Element Digital IC on board Silicon strain gauge transducer, 316 stainless or Hastelloy
Accuracy ±0.5°C — 0° to 55°C (32˚ to 131˚F)
±2.0°C — below 0°C (32˚F)
±0.05% FSO (typical, static)
±0.1% FSO (maximum, static)
(B.F.S.L. 20˚C)
Resolution 0.06˚C 0.0034% FS (typical)
Range -15˚ to 55˚C (5˚ to 131˚F) Gauge
Absolute3
PSI: 12, 5, 7, 15, 30, 50, 100, 300
FtH₂O: 2.32, 12, 35, 69, 115, 231, 692
mH₂O: 0.72, 3.5, 5, 10.5, 21, 35, 70, 210
PSI: 30, 50, 100, 300
FtH₂O: 35, 81, 196, 658
mH₂O: 10, 24, 59, 200
Compensated --- 0˚ to 40˚C (32˚ to 104˚F)
Max operating pressure 1.1 x full scale
Over pressure protection 3x full scale up to 300psi - for > 300psi (650 ft or 200 m) contact factory
Burst pressure 1000 psi (approx. 2000 ft or 600 m)
Environmental IP68, NEMA 6P
*Specications subject to change. Please consult out web site for the most current data (seametrics.com). Modbus is a registered trademark of Schneider Electric.
1 Higher pressure ranges available upon request
2 ±0.25% accuracy FSO (max) at this range
3 Depth range for absolute sensors has 14.7 PSI subtracted to give actual depth allowed.

PT12 INSTRUCTIONS
Seametrics • 253.872.0284 Page 5 inwusa.com
GENERAL INFORMATION
How Pressure Sensors Work
Liquids and gasses do not retain a xed shape. Both
have the ability to ow and are often referred to as
uids. One fundamental law for a uid is that the uid
exerts an equal pressure in all directions at a given level.
Further, this pressure increases with an increasing depth of
“submergence”. If the density of a uid remains constant
(noncompressible...a generally good assumption for water
at “normal” pressures and temperatures), this pressure
increases linearly with the depth of “submergence”.
We are all “submerged” in the atmosphere. As we increase
our elevation, the pressure exerted on our bodies decreases
as there is less of this uid above us. It should be noted
that atmospheric pressure at a given level does vary
with changes in the weather. One standard atmosphere
(pressure at sea level at 20º C) is dened to be 14.7 PSI
(pounds per square inch).
There are several methods to reference a pressure
measurement. Absolute pressure is measured with respect
to an ideal vacuum (no pressure). Gauge pressure is the
most common way we express pressure in every day life
and is the pressure exerted over and above atmospheric
pressure. With this in mind, gauge pressure (Pg) can be
expressed as the dierence between the absolute pressure
(Pa) and atmospheric pressure (Patm):
Pg = Pa - Patm.
To measure gauge pressure, atmospheric pressure is
subjected to one side of the system and the pressure to be
measured is subjected to the other. The result is that the
dierential (gauge pressure) is measured. A tire pressure
gauge is a common example of this type of device.
Recall that as the level of submergence increases (in a
noncompressible uid), the pressure increases linearly.
Also, recall that changes in weather cause the absolute
atmospheric pressure to change. In water, the absolute
pressure (Pa) at some level of depth (d) is given as follows:
Pa = Patm + kd
where k is simply a constant
(i.e.: 2.307 feet of water = 1 PSI)
Seametrics’ standard gauge submersible pressure
devices utilize a vent tube in the cable to allow the
device to reference atmospheric pressure. The resulting
gauge pressure measurement reects only the depth of
submergence. That is, the net pressure on the diaphragm
is due entirely to the depth of submergence.
Pressure Diagram: See Detail A.
Absolute pressure is given as Pa = Patm + kd
(where k is 2.307 feet of water)
d
Water Line
Patm
A
P = Patm + kd
“A”

PT12 INSTRUCTIONS
Seametrics • 253.872.0284 Page 6 seametrics.com
GENERAL INFORMATION
Initial Inspection and Handling
Upon receipt of your sensor, inspect the shipping package for damage. If any damage is apparent, note the signs of
damage on the appropriate shipping form. After opening the carton, look for concealed damage, such as a cut cable. If
concealed damage is found, immediately le a claim with the carrier.
Check the etched label on the sensor to be sure that the proper range and type were provided. Also check the label
attached to the cable at the connector end for the proper cable length.
Do’s and Don’ts
Don’t drop into well
Lower gently to prevent
damage
Don’t scrape cable
over edge of well
May nick or fray the
cable
Don’t bend cable sharply
May close o vent tube
and/or weaken internal
wires
Don’t support sensor
with the connector
Use a strain relief device
Do handle sensor with
care
Do store sensor in a
dry, inside area when
not in use
Do install a desiccant
tube if using a gauge
sensor
Do not disassemble—
will void warranty!

PT12 INSTRUCTIONS
Seametrics • 253.872.0284 Page 7 inwusa.com
INSTALLATION
Cable Wiring
For SDI-12
White
Purple
Yellow
Brown
Blue
Shield
12 VDC+ (Vaux)
Modbus D- (Not used)
Modbus D+ (Not used)
SDI-12 Signal
12 VDC- (GND)
Earth ground
For Modbus®
— with optional 5-pin connector
White
Purple
Yellow
Brown
Blue
Shield
12 VDC+ (Vaux)
Modbus D-
Modbus D+
SDI-12 (Not used)
12 VDC- (GND)
1
2
3
4
5
5-Pin
Connector
For Modbus®
White
Purple
Yellow
Brown
Blue
Shield
12 VDC+ (Vaux)
Modbus D-
Modbus D+
SDI-12 Signal (Not used)
12 VDC- (Gnd)
Earth ground
For SDI-12
— with optional 5-pin connector
White
Purple
Yellow
Brown
Blue
Shield
12 VDC+ (Vaux)
Modbus D- (Not used)
Modbus D+ (Not used)
SDI-12 Signal
12 VDC- (GND)
1
2
3
4
5
5-Pin
Connector
Installing the Sensor
ThePT12 measures pressure. Themost common application
is measuring liquid levels in wells and tanks. In order to do
this, the sensor must be installed below the water level at a
xed depth. The installation depth depends on the range
of the sensor. One (1) PSI is equal to approximately 2.31
feet of water. If you have a 5 PSI sensor, the range is 11.55
feet of water and the sensor should not be installed at a
depth below 11.55 feet. If the sensor is installed below its
maximum range, damage may result to the sensor and the
output reading will not be correct.
• Lower the sensor to the desired depth.
• Fasten the cable to the well head using a weather
proof strain-relief system. When securing a vented
cable, make sure not to pinch the cable too tightly
or the vent tube inside the cable jacket may be
sealed o.
• Take a measurement to insure the sensor is not
installed below its maximum range.
For vented sensors, install the sensor so that the desiccant
tube will not ood or lie in water.
The sensor can be installed in any position; however, when
it leaves the factory it is tested in the vertical position.
Strapping the sensor body with tie wraps or tape will not
hurt it. Seametrics can provide an optional 1/4” NPT input
adapter which is interchangeable with the standard end
cone for those applications where it is necessary to directly
attach the sensor to a pipe, tank, or other pipe port. If the
sensor is being installed in a uid environment other than
water, be sure to check the compatibility of the uid with
the wetted parts of the sensor.
Desiccant Use
On vented sensors a desiccant tube prevents moisture in
the air from being sucked into the vent tube, which can
cause erratic readings and sensor damage.
The desiccant tube is lled with blue silica gel beads. A
locking barb and a hydrophobic water lter are attached to
the end of the desiccant tube. This lter prolongs the life of
the desiccant as much as three times over a desiccant tube
without the lter.
Install the sensor so that the desiccant tube and cable
connector will not ood or lie in water.
The desiccant is a bright blue color when active and dry. See
Maintenance section for care and changing of desiccant.

PT12 INSTRUCTIONS
Seametrics • 253.872.0284 Page 8 seametrics.com
INSTALLATION
Grounding Issues
It is commonly known that when using electronic
equipment, both personnel and equipment need to be
protected from high power spikes that may be caused by
lightning, power line surges, or faulty equipment. Without
a proper grounding system, a power spike will nd the path
of least resistance to earth ground—whether that path
is through sensitive electronic equipment or the person
operating the equipment. In order to ensure safety and
prevent equipment damage, a grounding system must be
used to provide a low resistance path to ground.
When using several pieces of interconnected equipment,
each of which may have its own ground, problems with
noise, signal interference, and erroneous readings may be
noted. This is caused by a condition known as a Ground
Loop. Because of natural resistance in the earth between
the grounding points, current can ow between the points,
creating an unexpected voltage dierence and resulting
erroneous readings.
The single most important step in minimizing a ground
loop is to tie all equipment (sensors, data loggers,
external power sources, and any other associated
equipment) to a single common grounding point.
Seametrics recommends the following:
• The sensor cable shield (the wrapped shield inside
the cable) be attached to the power ground on the
data logger
• The grounding lug be connected via a 12 AWG
or larger wire, to a grounding rod driven into the
earth.
• If you are using an external power supply to power
the data logger that it be tied to the same earth
ground.
Sensor/Data Logger Conguration
The PT12 submersible pressure/temperature transducer is
designed for use with SDI-12 or Modbus®data loggers.
Every sensor is individually calibrated at the factory, using
an environmental test chamber and dead-weight tester.
Sensor specic calibration values are stored in the sensor.
When taking measurements, the internal microprocessor
uses these calibration values to thermally compensate the
pressure readings.
In addition to the factory set calibration values, the user can
enter a eld calibration slope and oset for the pressure
and temperature channels. Pressure readings default to
psi and temperature readings to degrees Celsius. The user
can enter a units conversion slope and oset to change
units, if desired. See the operation sections for details on
changing these values. The power supply voltage channel
always returns values in volts.

PT12 INSTRUCTIONS
Seametrics • 253.872.0284 Page 9 inwusa.com
OPERATION/MODBUS RTU
This section explains how to read your PT12 via Modbus®
RTU. (If you want to read via SDI-12, see the next section
beginning on page 11.)
Power Consideration
If your sensor is not powered continuously by an auxiliary
power supply, then you must turn power on to the sensor
at least two seconds before a reading is to be taken to
allow the sensor to warm up.
Communication Settings
The PT12 is congured to communicate with 8 data bits,
one stop bit, and no parity. Default baud rate is 19200.
Modbus®Functions
All readings are obtained using Modbus®function 03-Read
Holding Registers. Readings are located in two registers
each. The data is returned as a 32-bit IEEE oating-point
value, high word rst, also referred to as big-endian, oat
inverse, or Float AB CD.
Channel Registers Using High Addressing—to match Seametrics Smart Sensors
(Available with rmware 0.13 and higher)
Zero-Based One-Based +40,001
Pressure 62592 62593 462593
Temperature 62594 62595 462595
Power Supply Voltage 62596 62597 462597
Averaged Pressure 62598 62599 462599
Maximum Pressure 62600 62601 462601
Minimum Pressure 62602 62603 462603
Averaged Temperature 62604 62605 462605
Channel Registers Using Standard Addressing
Zero-Based One-Based +40,001 +400,001
Pressure 0 1 40001 400001
Temperature 2 3 40003 400003
Power Supply Voltage 4 5 40005 400005
Averaged Pressure 6 7 40007 400007
Maximum Pressure 8 9 40009 400009
Minimum Pressure 10 11 40011 400011
Averaged Temperature 12 13 40013 400013
Register Denitions
The physical register addresses on the PT12 start numbering
from zero – the rst address is 0, the second is 1, etc. On the
other hand, Modbus® protocol considers the rst logical
address to be 1, the second logical address to be 2, etc. For
example, to take a pressure reading you have to read the
physical address 0.
Some programs and equipment when asked to read
address 0 will read that physical address. Others however
will read that logical address, which is actually the physical
address -1 (which does not exist). With these programs and
equipment you must add a one to the address – thus in this
example you would request a read at address 1.
Still other programs and equipment require the addition
of 40,000 or 400,000 to the address to indicate reading
holding registers. These usually also require the addition of
one to the physical address. Check with your program and/
or equipment documentation to determine what style of
register addressing is required.
Like many common Modbus®devices the PT12 returns
readings starting at register address 0 (or 1 if using one-
based addressing). In addition, for compatibility with other
Seametrics Smart Sensor equipment, the PT12 also returns
these same readings starting at a register address 62592 (or
62593 if using one-based addressing).

PT12 INSTRUCTIONS
Seametrics • 253.872.0284 Page 10 seametrics.com
OPERATION/MODBUS RTU
Calibration and Conversion Constants
The data is returned as a 32-bit IEEE oating-point value,
high word rst, also referred to as big-endian, oat inverse,
or Float AB CD.
Field calibration values and units conversion values can be
set by the user. If set, these values will be applied to the
readings before values are returned.
Zero-
Based
One-
Based
+40,001 Description
200-01 201-02 40201-02 Factory Calibration* - Pressure Scale
202-03 203-04 40203-04 Factory Calibration* - Pressure Linearization 1
204-05 205-06 40205-06 Factory Calibration* - Pressure Linearization 2
206-07 207-08 40207-08 Factory Calibration* - Pressure Slope 0
208-09 209-10 40209-10 Factory Calibration* - Pressure Slope 1
210-11 211-12 40211-12 Factory Calibration* - Pressure Slope 2
212-13 213-14 40213-14 Factory Calibration* - Pressure Oset 0
214-15 215-16 40215-16 Factory Calibration* - Pressure Oset 1
216-17 217-18 40217-18 Factory Calibration* - Pressure Oset 2
218-19 219-20 40219-20 Field Calibration - Pressure Slope
220-21 221-22 40221-22 Field Calibration - Pressure Oset
222-23 223-24 40223-24 Field Calibration - Temperature Slope
224-25 225-26 40225-26 Field Calibration - Temperature Oset
226-27 227-28 40227-28 Factory Calibration* - Temperature Alpha
228-29 229-30 40229-30 Factory Calibration* - Temperature Oset
230-31 231-32 40231-32 Factory Calibration* - Tempearture Slope
232-33 233-34 40233-34 Pressure Units - Conversion Slope
234-35 235-36 40235-36 Pressure Units - Conversion Oset
236-37 237-38 40237-38 Temperature Units - Conversion Slope
238-39 239-40 40239-40 Temperature Units - Conversion Oset
* Factory calibration values are set at the factory.
Writing to Factory Calibration
registers will void calibration!
Zero-
Based
One-
Based
+40,001 Description
300=n 301=n 40301=n Set averaging: This enables sensor for n
seconds. Each second, the statistical data
registers will be updated to contain new
averages, max and min. At the completion of n
seconds, the nal statistical values will be left in
the registers, and the sensor will be put to sleep.
n = 0..10,800. If n = 0, the sensor is put to sleep,
and the statistical data values are not updated.
400=a 401=a 40401=a Set sensor address = a (Write Only)
500=b 501=b 40501=b Set baud rate = b (Write only)
0=38400, 1=19200 (default), 2=9600, 3=4800,
4=2400, 5=1200
600=w 601=w 40601=w Set auto-enable. Causes sensor to be enabled
automatically for w seconds after a read of any
parameter data register. W=0 disables auto-
enable. (This is normally set to 10 seconds at the
factory.) For lowest power usage, set this to zero.
For fastest readings while still retaining as much
power savings as possible, set slightly longer
than your read frequency. See section below
for information on how this setting aects your
readings.
700=L 701=L 40701=L Set serial number. L= unsigned longword value
0x0000000 .. 0xFFFFFFF (0 .. 4,294,967,295)
800 801 40801 Read sensor rmware revision. Word MSB =
Major revision, LSB = minor revision.
E.g., 0013 = revision 0.13
Sensor Conguration/Control
Readings and the Auto-Enable Setting
When a reading is requested, four things happen:
• The sensor wakes up.
• The current value in the register is returned.
• The sensor turns on the analog portion, begins
sampling, and begins putting the new values in the
registers.
• If auto-enable is set to a positive value w, the sensor
stays awake for w seconds, sampling and moving
values into the registers all the while, and then goes
to sleep.
• If auto-enable is set to zero, the sensor immediately
goes to sleep after putting the reading in the
register.
If your read frequency is less than the auto-enable value,
the sensor will stay on continuously, and your readings will
always be fresh, with the exception of the very rst reading.
If your read frequency is greater than the auto-enable
value, the following reading sequence is recommended:
1. Request a reading. This begins the wakeup process
on the sensor and returns the value currently in the
register, which will be old data. Throw this value
away.
2. Wait one second, then take another reading. This
reading will have fresh data. Record this reading.

PT12 INSTRUCTIONS
Seametrics • 253.872.0284 Page 11 inwusa.com
Addressing
Default SDI-12 Address: 0
SDI-12 Command Nomenclature
<a> = Sensor address
{crc} = SDI-12 compatible 3-character CRC
<cr> = ASCII carriage return character
<lf> = ASCII line feed character
highlighted values indicate variable data
SDI-12 Commands
Sensor Identication
<a>I! <a>13 INWUSA PT12 0.13ssssssssss<cr><lf> Note: 0.13 will change to reect current
rmware version.
ssssssssss = device serial number
Acknowledge Active, Address Query
<a>! <a><cr><lf>
?! <a><cr><lf>
Change Address
<a>A<b>! <b><cr><lf> Change address to <b>
Request Measurement
<a>M! <a>0023<cr><lf> Request all basic measurements
<a>D0! <a>+7.15863+25.0000+12.0512<cr><lf> Read: pressure, temperature, voltage
<a>M1! <a>0021<cr><lf> Request pressure measurement only
<a>D0! <a>+7.15863<cr><lf> Read pressure
<a>M2! <a>0021<cr><lf> Request temperature measurement only
<a>D0! <a>+25.0000<cr><lf> Read temperature
<a>M3! <a>0021<cr><lf> Request power supply voltage
<a>D0! <a>+12.0512<cr><lf> Read power supply voltage
<a>M4! <a>0ttt4<cr><lf> Request averaged data. ttt depends on
programmed average duration.
<a>D0! <a>+7.15863+7.23215+7.051283+25.0000<cr><lf> Read average pressure, max. pressure, min.
pressure, average temperature
Reading via SDI-12
OPERATION/SDI-12
All SDI-12 requests consist
of a command followed by
a request for values. Some
software or equipment may
combine these, making the
second one unnecessary. Refer
to your software or equipment
documentation for details.
<a>D0! <a>+7.15863<cr><lf>
Request Response
Address
Request for
Address
Returned
value(s)
Carriage Return
Linefeed
values read
<a>M1! <a>0021<cr><lf>
Request Response
Address
Command
Address
Time until
response
Carriage Return
Linefeed
# of values to
be returned
(in seconds)

PT12 INSTRUCTIONS
Seametrics • 253.872.0284 Page 12 seametrics.com
M5!, M6!, and M7! only available on PT12-BV/PT12 combination units!
<a>M5! <a>0023<cr><lf> Request barometrically compensated down-
hole pressure, down-hole temperature, surface
temperature
<a>D0! <a>+2.58613+19.2100+21.05122<cr><lf> Read: barometrically compensated down-hole
pressure, down-hole temperature, surface
temperature
<a>M6! <a>0024<cr><lf> Request non-barometrically compensated
down-hole pressure, down-hole temperature,
surface pressure, surface temperature
<a>D0! <a>+17.31813+19.2100+14.732+21.0512<cr><lf> Read non-barometrically compensated down-
hole pressure, down-hole temperature, surface
pressure, surface temperature
<a>M7! <a>ttt1<cr><lf> Request averaged barometrically compensated
pressure. ttt depends on programmed
average.
<a>D0! <a>+7.12050<cr><lf> Read temperature averaged barometrically
compensated pressure
Request Measurement with CRC
<a>MC! <a>0023<cr><lf> Request all basic measurements
<a>D0! <a>+7.15863+25.0000+12.0512{crc}<cr><lf> Read: pressure, temperature, voltage
<a>MC1! <a>0021<cr><lf> Request pressure measurement only
<a>D0! <a>+7.15863{crc}<cr><lf> Read pressure
<a>MC2! <a>0021<cr><lf> Request temperature measurement only
<a>D0! <a>+25.0000{crc}<cr><lf> Read temperature
<a>MC3! <a>0021<cr><lf> Request power supply voltage
<a>D0! <a>+12.0512{crc}<cr><lf> Read power supply voltage
<a>MC4! <a>0ttt4<cr><lf> Request averaged data. ttt depends on
programmed average duration.
<a>D0! <a>+7.15863+7.23215+7.051283+25.0000{crc}<cr><lf> Read average pressure, max. pressure, min.
pressure, average temperature
MC5!, MC6!, and MC7! only available on PT12-BV/PT12 combination units!
<a>MC5! <a>0023<cr><lf> Request barometrically compensated down-
hole pressure, down-hole temperature, surface
temperature
<a>D0! <a>+2.58613+19.2100+21.05122{crc}<cr><lf> Read: barometrically compensated down-hole
pressure, down-hole temperature, surface
temperature
<a>MC6! <a>0024<cr><lf> Request non-barometrically compensated
down-hole pressure, down-hole temperature,
surface pressure, surface temperature
<a>D0! <a>+17.31813+19.2100+14.732+21.0512{crc}<cr><lf> Read non-barometrically compensated down-
hole pressure, down-hole temperature, surface
pressure, surface temperature
OPERATION/SDI-12

PT12 INSTRUCTIONS
Seametrics • 253.872.0284 Page 13 inwusa.com
<a>MC7! <a>ttt1<cr><lf> Request averaged barometrically compensated
pressure. ttt depends on programmed
average.
<a>D0! <a>+7.12050{crc}<cr><lf> Read temperature averaged barometrically
compensated pressure
Concurrent Measurement
<a>C! <a>0023<cr><lf> Request all basic measurements
<a>D0! <a>+7.15863+25.0000+12.0512<cr><lf> Read: pressure, temperature, voltage
<a>C1! <a>0021<cr><lf> Request pressure measurement only
<a>D0! <a>+7.15863<cr><lf> Read pressure
<a>C2! <a>0021<cr><lf> Request temperature measurement only
<a>D0! <a>+25.0000<cr><lf> Read temperature
<a>C3! <a>0021<cr><lf> Request power supply voltage
<a>D0! <a>+12.0512<cr><lf> Read power supply voltage
<a>C4! <a>0ttt4<cr><lf> Request averaged data. ttt depends on
programmed average duration.
<a>D0! <a>+7.15863+7.23215+7.051283+25.0000<cr><lf> Read average pressure, max. pressure, min.
pressure, average temperature
C5!, C6!, and C7! only available on PT12-BV/PT12 combination units!
<a>C5! <a>0023<cr><lf> Request barometrically compensated down-
hole pressure, down-hole temperature, surface
temperature
<a>D0! <a>+2.58613+19.2100+21.05122<cr><lf> Read: barometrically compensated down-hole
pressure, down-hole temperature, surface
temperature
<a>C6! <a>0024<cr><lf> Request non-barometrically compensated
down-hole pressure, down-hole temperature,
surface pressure, surface temperature
<a>D0! <a>+17.31813+19.2100+14.732+21.0512<cr><lf> Read non-barometrically compensated down-
hole pressure, down-hole temperature, surface
pressure, surface temperature
<a>C7! <a>ttt1<cr><lf> Request averaged barometrically compensated
pressure. ttt depends on programmed
average.
<a>D0! <a>+7.12050<cr><lf> Read temperature averaged barometrically
compensated pressure
OPERATION/SDI-12

PT12 INSTRUCTIONS
Seametrics • 253.872.0284 Page 14 seametrics.com
Concurrent Measurement with CRC
<a>CC! <a>0023<cr><lf> Request all basic measurements
<a>D0! <a>+7.15863+25.0000+12.0512{crc}<cr><lf> Read: pressure, temperature, voltage
<a>CC1! <a>0021<cr><lf> Request pressure measurement only
<a>D0! <a>+7.15863{crc}<cr><lf> Read pressure
<a>CC2! <a>0021<cr><lf> Request temperature measurement only
<a>D0! <a>+25.0000{crc}<cr><lf> Read temperature
<a>CC3! <a>0021<cr><lf> Request power supply voltage
<a>D0! <a>+12.0512{crc}<cr><lf> Read power supply voltage
<a>CC4! <a>0ttt4<cr><lf> Request averaged data. ttt depends on
programmed average duration.
<a>D0! <a>+7.15863+7.23215+7.051283+25.0000{crc}<cr><lf> Read average pressure, max. pressure, min.
pressure, average temperature
CC5!, CC6!, and CC7! only available on PT12-BV/PT12 combination units!
<a>CC5! <a>0023<cr><lf> Request barometrically compensated down-
hole pressure, down-hole temperature, surface
temperature
<a>D0! <a>+2.58613+19.2100+21.05122{crc}<cr><lf> Read: barometrically compensated down-hole
pressure, down-hole temperature, surface
temperature
<a>CC6! <a>0024<cr><lf> Request non-barometrically compensated
down-hole pressure, down-hole temperature,
surface pressure, surface temperature
<a>D0! <a>+17.31813+19.2100+14.732+21.0512{crc}<cr><lf> Read non-barometrically compensated down-
hole pressure, down-hole temperature, surface
pressure, surface temperature
<a>CC7! <a>ttt1<cr><lf> Request averaged barometrically compensated
pressure. ttt depends on programmed
average.
<a>D0! <a>+7.12050{crc}<cr><lf> Read temperature averaged barometrically
compensated pressure
Extended Commands
Set duration for averaging reading
<a>XAttt! <a>ttt<cr><lf> Set duration of averaged data for M4, MC4, C4,
and CC4 commands. ttt = 1–997 seconds
Read/Modify Calibration Values
<a>XCnn{=<value>}! <a><value><cr><lf> Read {modify} calibration value nn
Examples:
<a>XC00! <a>+1.591600e-5<cr><lf> Read the value from calibration register 00
<a>XC00=1.704e-4! <a>+1.704000e-4<cr><lf> Set the value of calibration register 00
Set number of signicant digits
<a>XSt! <a>t<cr><lf> Set number of signicant digits for SDI-12
report data. t= 1–7
OPERATION/SDI-12

PT12 INSTRUCTIONS
Seametrics • 253.872.0284 Page 15 inwusa.com
OPERATION/SDI-12
Calibration Register Denitions
Field calibration values can be set by user. If set, these values will be applied to readings before values are returned. All
calibration registers contain oating point values.
* Factory calibration values are set at the factory.
Writing to Factory Calibration
registers will void calibration!
SDI-12 Reg. ID Mnemonic Description Default value
00 Scale Units scale (counts * Scale = base units, default psi) 1.591600e-5
01 a Factory calibration linearized correction factor 1* 0.000000e+00
02 b Factory calibration linearized correction factor 2* 1.000000e+00
03 m0 Factory calibration slope coeent 0* 1.000000e+00
04 m1 Factory calibration slope coeent 1* 0.000000e+00
05 m2 Factory calibration slope coeent 2* 0.000000e+00
06 b0 Factory calibration oset coeent 0* 0.000000e+00
07 b1 Factory calibration oset coeent 1* 0.000000e+00
08 b2 Factory calibration oset coeent 2* 0.000000e+00
09 mField Field pressure calibration slope 1.000000e+00
10 bField Field pressure calibration oset 0.000000e+00
11 mT Field temperature calibration slope 1.000000e+00
12 bT Field temperature calibration oset 0.000000e+00
13 T_Alpha Factory temperature calibration–Alpha* 0.000000e+00
14 T_Oset Factory temperature calibration–Oset* 0.000000e+00
15 T-ZeroSlope Factory temperature calibration–ZeroSlope* 0.000000e+00
16 P_mUnits Pressure units conversion slope 1.000000e+00
17 P_bUnits Pressure units conversion oset 0.000000e+00
18 T_mUnits Temperature units conversion slope 1.000000e+00
19 T_bUnits Temperature units conversion oset 0.000000e+00

PT12 INSTRUCTIONS
Seametrics • 253.872.0284 Page 16 seametrics.com
MAINTENANCE
Removing Debris from End Cone
At times mud, silt, or other debris may foul the water inlets
to the pressure element. The end cone can be removed to
clean out the debris.
Twist Open Housing
1. Gently twist o end cone portion only - do not twist
o pressure element!
2. Remove debris. Do not poke anything into the
sensor. This can damage the sensor element and
void the warranty.
3. Replace and retighten the end cone.
Gently twist o the end cone and carefully remove debris
Set Screw Housing
1. Remove the two set screws at the bottom of the
housing tube, using a 1/16” allen wrench.
2. Gently remove the end cone.
3. Remove debris. Do not poke anything into the
sensor. This can damage the sensor element and
void the warranty.
4. Replace the end cone and secure with set screws.
Remove end cone by removing set screws.
Gently clean out debris.
Pressure element
Water inlet
End cone
Pressure element
Water inlet
End cone
Set screw
Desiccant Tubes
On vented sensors, inspect the desiccant tube at least once
every two months. The desiccant tube prevents moisture
in the air from being sucked into the vent tube, which can
cause erratic readings and sensor damage.
The desiccant tube is lled with blue silica gel beads. A
locking barb and a hydrophobic water lter are attached to
the end of the desiccant tube. This lter prolongs the life of
the desiccant as much as three times over a desiccant tube
without the lter.
Install the sensor so that the desiccant tube and cable
connector will not ood or lie in water.
The desiccant is a bright blue color when active and dry.
As moisture is absorbed the color will begin to fade,
becoming a light pink, which indicates full saturation and
time to replace. Replacement desiccant and hydrophobic
lters can be purchased from Seametrics.
To Change the Desiccant:
• Pulling gently remove the black tube tting from
the clear desiccant tube.
• Using needle-nose pliers, remove the dark gray
foam plug. Do not discard the plug.
• Dump out the old desiccant beads and rell with
new desiccant beads – tapping desiccant tube
frequently during relling to ensure that the beads
are fully seated in tube.
• Push the foam plug back into the tube.
• Reinsert the black tting.

PT12 INSTRUCTIONS
Seametrics • 253.872.0284 Page 17 inwusa.com
MAINTENANCE
Sensor
There are no user-serviceable parts. If problems develop
with sensor stability or accuracy, contact Seametrics. If the
transducers have been exposed to hazardous materials, do
not return them without notication and authorization.
Cable
Cable can be damaged by abrasion, sharp objects, twisting,
crimping, crushing, or pulling. Take care during installation
and use to avoid cable damage. If a section of cable is
damaged, it is recommended that you send your sensor
back to replace the cable harness assembly.
End Connections–if using optional eld connector
The contact areas (pins & sockets) of the connectors will
wear out with extensive use. If your application requires
repeated connections other types of connectors can be
provided. The connectors used by Seametrics are not
submersible, but are designed to be splash-resistant.

PT12 INSTRUCTIONS
Seametrics • 253.872.0284 Page 18 seametrics.com
TROUBLESHOOTING
Problem Probable Causes Things to try…
Erratic readings Poor connection due to moisture between
contacts in connector
Dry thoroughly. Be sure desiccant is fresh (see
Maintenance section).
Loose or broken wires in connector Repair or return for evaluation and repair
Damaged cable, cracked or fraying Replace cable
Moisture in the unit Return for evaluation and repair
Damaged transmitter Return for evaluation and repair
Oscillating readings
over time (usually
0.5 to 1.5 feet of
water)
Plugged vent tube (if using a vented unit) Be sure desiccant tube is installed. Test by
gently applying a small amount of pressure
to the end of the desiccant tube and seeing
if this aect the transmitter reading. If it does
not, then the vent tube is plugged. Return for
evaluation and repair.
Actual water level changes in the aquifer
itself in response to barometric pressure
changes. This eect can occur in tight
formations where the transmitter will
immediately pick up barometric changes
but the the aquifer will not.
You will need to record barometric pressure as
well as the water level pressure and compensate
the data
Zero readings when
pressurized
Poor connection due to moisture between
contacts in connector
Dry thoroughly. Be sure desiccant is fresh (see
Maintenance section).
Loose or broken wires in connector Repair or return for evaluation and repair
Damaged cable, broken, cracked, or fraying Replace cable
No apparent damage upon visual inspection Return for evaluation and repair

PT12 INSTRUCTIONS
Seametrics • 253.872.0284 Page 19 inwusa.com
WARRANTY/DISCLAIMER
LIMITED WARRANTY/DISCLAIMER - PT12
SUBMERSIBLE PRESSURE TRANSDUCER
A. Seller warrants that products manufactured by Seller when properly installed, used and maintained with a properly
installed desiccant tube, shall be free from defects in material and workmanship. Seller’s obligation under this warranty
shall be limited to replacing or repairing the part or parts or, at Seller’s option, the products which prove defective in
material or workmanship within TWO (2) year from the date of delivery, provided that Buyer gives Seller prompt notice
of any defect or failure and satisfactory proof thereof. Any defective part or parts must be returned to Seller’s factory
or to an authorized service center for inspection. Buyer will prepay all freight charges to return any products to Seller’s
factory, or any other repair facility designated by Seller. Seller will deliver replacements for defective products to Buyer
(ground freight prepaid) to the destination provided in the original order. Products returned to Seller for which Seller
provides replacement under this warranty shall become the property of Seller.
This limited warranty does not apply to lack of performance caused by abrasive materials, corrosion due to aggressive
uids, mishandling or misapplication. Seller’s obligations under this warranty shall not apply to any product which (a)
is normally consumed in operation, or (b) has a normal life inherently shorter than the warranty period stated herein.
In the event that equipment is altered or repaired by the Buyer without prior written approval by the Seller, all warranties
are void. Equipment and accessories not manufactured by the Seller are warranted only to the extent of and by the
original manufacturer’s warranty.
THE FOREGOING WARRANTIES ARE IN LIEU OF ALL OTHER WARRANTIES, WHETHER ORAL, WRITTEN, EXPRESSED,
IMPLIED OR STATUTORY. IMPLIED WARRANTIES OF FITNESS AND MERCHANTABILITY SHALL NOT APPLY. SELLER’S
WARRANTY OBLIGATIONS AND BUYER’S REMEDIES THEREUNDER (EXCEPT AS TO TITLE) ARE SOLELY AND EXCLUSIVELY
AS STATED HEREIN. IN NO CASE WILL SELLER BE LIABLE FOR CONSEQUENTIAL DAMAGES, LABOR PERFORMED IN
CONNECTION WITH REMOVAL AND REPLACEMENT OF THE SENSOR SYSTEM, LOSS OF PRODUCTION OR ANY OTHER
LOSS INCURRED BECAUSE OF INTERRUPTION OF SERVICE. A NEW WARRANTY PERIOD SHALL NOT BE ESTABLISHED
FOR REPAIRED OR REPLACED MATERIAL, PRODUCTS OR SUPPLIES. SUCH ITEMS SHALL REMAIN UNDER WARRANTY
ONLY FOR THE REMAINDER OF THE WARRANTY PERIOD ON THE ORIGINAL MATERIALS, PRODUCTS OR SUPPLIES.
B. With respect to products purchased by consumers in the United States for personal use, the implied warranties
including but not limited to the warranties of merchantability and tness for a particular purpose, are limited to twenty
four (24) months from the date of delivery.
Some states do not allow limitations on the duration of an implied warranty, so the above limitation may not apply to
you. Similarly, some states do not allow the exclusion or limitation of consequential damages, so the above limitation or
exclusion may not apply to you. This limited warranty gives you specic legal rights; however, you may also have other
rights which may vary from state to state.

Seametrics • 19026 72nd Avenue South • Kent, Washington 98032 • USA
(P) 253.872.0284 • (F) 253.872.0285 • 1.800.975.8153 • seametrics.com LT-14372r18 20180306 3/6/2018
Table of contents
Other Seametrics Temperature Controllers manuals
Popular Temperature Controllers manuals by other brands

Nibe
Nibe HTS 40 Installer manual
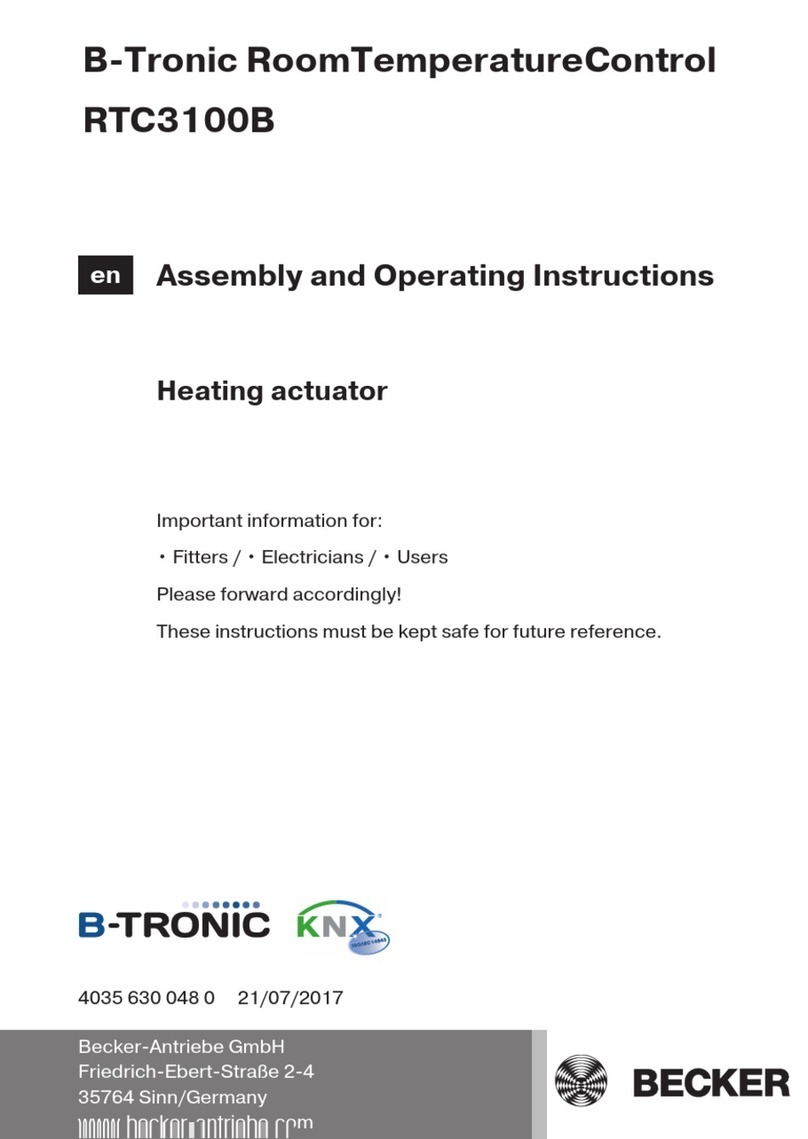
Becker
Becker B-Tronic RTC3100B Assembly and operating instructions
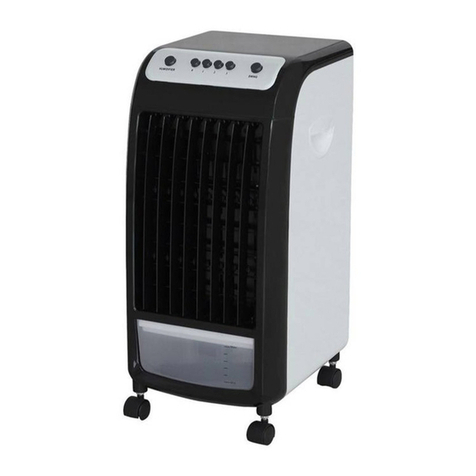
Ravanson
Ravanson KR-1011 user manual
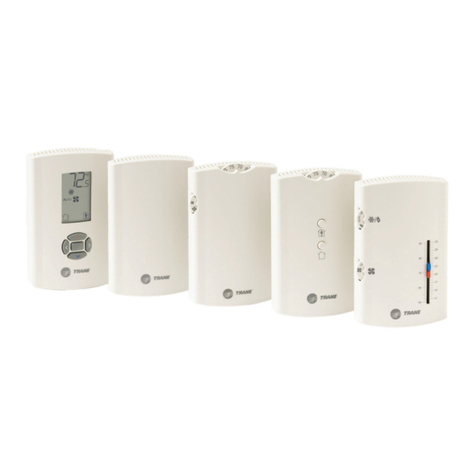
Trane Technologies
Trane Technologies X1351152701 Installation, operation and maintenance
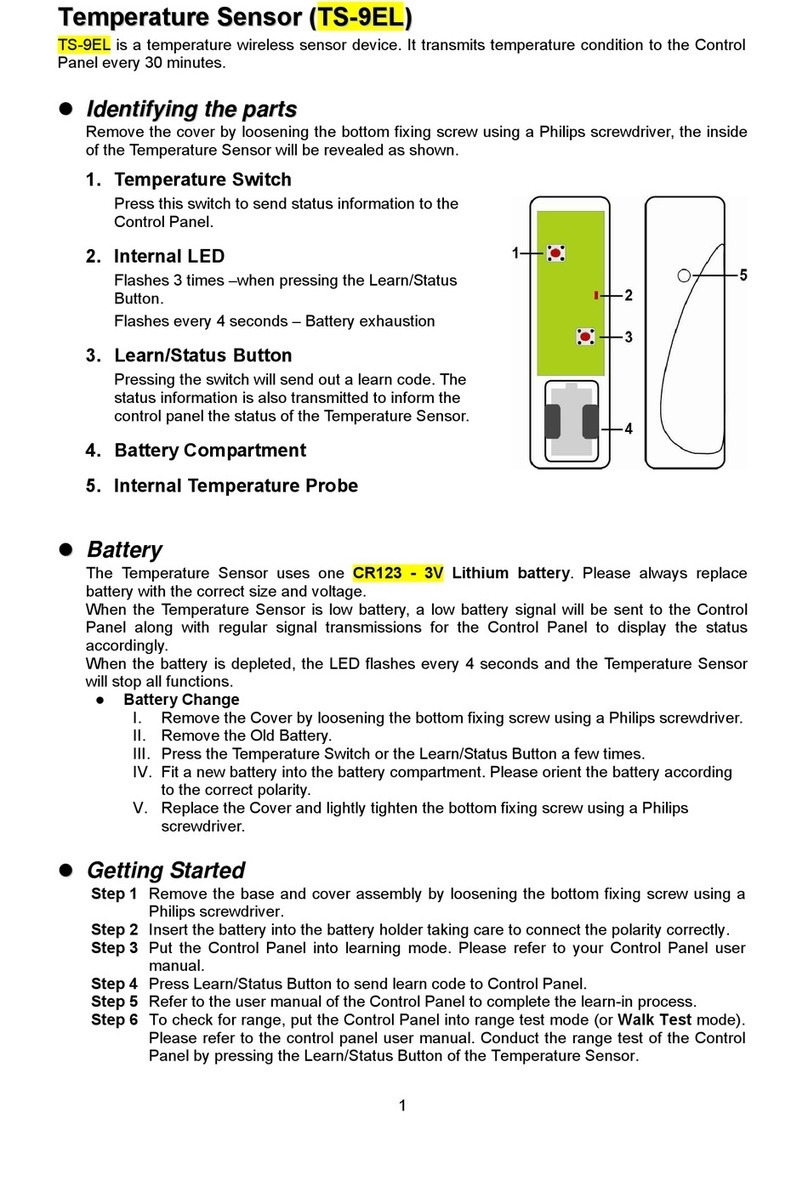
Climax Technology
Climax Technology TS-9EL manual
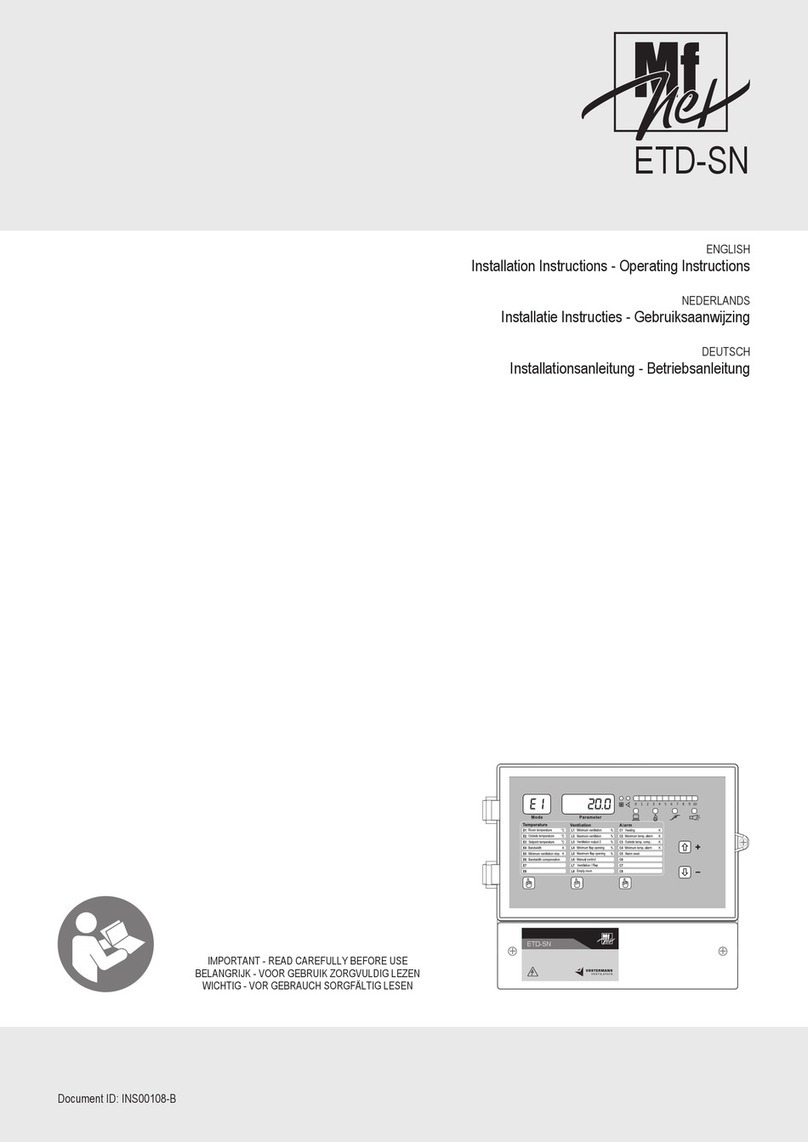
Vostermans Ventilation
Vostermans Ventilation Mf Net ETD-SN Installation and operating instructions