Seetru Quicktester User manual

Quicktester Installation, Operating and Maintenance Instructions Issue: 3 03/08/04 G43INS Page 1 of 3
QUICKTESTER
General Description
The unit has been designed to enable the user to check the set pressure of any elastomer seal safety relief valve and incorporates the
following features: -
• 1/4" BSP parallel male thread Conex supply port (Inlet Port 1 on Picture A)
• 3/8" BSP parallel female safety relief valve test port (Port 2)
• 3/8" BSP parallel pressure gauge port (Port 3)
• Restricted inlet control valve (Control Valve 1)
• Outlet control valve (Control Valve 2)
1. Competent Person
The unit must only be operated by a competent person familiar with the hazards associated with pressurised systems and testing of
safety relief valves. It must only be operated in accordance with these instructions.
2. Setup Procedure
Follow entire set up procedure (2.1 to 2.4) prior to testing a safety relief valve or applying inlet pressure to Quicktester.
2.1 Seals
All joints made by the user must provide an airtight seal when subjected to the regulated inlet pressure. A leaking joint will result
in an inaccurate dial gauge reading.
The maintenance section of these instructions provides details for checking the integrity of the internal pipe work.
2.2 Air/Inert Gas Supply
For best performance, the supply air/inert gas must be regulated, commercially clean and free of moisture.
The regulated supply pressure must be in excess of the expected set pressure of the safety relief valve (Set pressure +10% is
recommended), and importantly not greater than the full scale deflection of the dial gauge being used.
The maximum operating pressure of the unit is clearly marked on the panel and should never be exceeded unless otherwise
indicated by these instructions (refer to section 5 and 6).
Standard Connection - 1/4" BSP Parallel Male - Conex
2.3 Dial Gauge
Note the set pressure of the safety relief valve to be tested; this should be permanently marked on or attached to the valve with a tag.
Optimum accuracy will be obtained if the dial gauge being used is Test Gauge standard and has the required set pressure of the
safety relief valve within the mid third of its range.
The dial gauge should be calibrated using a system that is traceable to a national standard.
Standard Connection - 3/8" BSP Parallel Female rotatable pressure gauge connector.
2.4 Safety Relief Valve Adaptor
A range of stainless steel valve adaptors is included to suit a variety of safety relief valve inlet thread connection type and size. It
is imperative that the correct adaptor is used. Once the correct adaptor has been selected, mount it to the relief valve test port, then
fit the safety relief valve.
Connection - Adaptor to mounting block - 3/8" BSP Parallel Female.
Connection - Adaptor to safety relief valve - to suit safety relief valve inlet connection.
3. Sequence of Operation - See Picture A
3.1 Ensure inlet control valve 1 is fully closed (clockwise)
3.2 Ensure outlet control valve 2 is fully closed (clockwise)
3.3 Apply inlet pressure to unit.
3.4 Slowly open inlet control valve 1 by turning anti-clockwise to pressurise the system.
3.5 When the indicated gauge pressure is equal to the safety relief valve set pressure, the pressure in the system will stabilise and the
dial gauge reading will continually indicate the set pressure.
3.6 Close inlet control valve 1 by turning clockwise. The pressure will reduce to the pressure at which the safety relief valve under test
re-seals. This re-seal pressure is indicated on the pressure gauge.
3.7 If required the safety relief valves ability to re-seal at lower pressures can be established by gradually opening and then closing
outlet control valve 2.
3.8 Vent pressure by fully opening outlet control valve 2 (anti-clockwise).
3.9 When dial gauge reading is zero, remove safety relief valve.
3.10 Repeat set up procedure for next safety relief valve.

Quicktester Installation, Operating and Maintenance Instructions Issue: 3 03/08/04 G43INS Page 2 of 3
Picture A - Quicktester
4. Interpretation of Results
4.1 Correct Set Pressure Reading - If the reading on the dial gauge at test stage 3.5 falls within the allowed tolerance range of the set
pressure of the safety relief valve then this is confirmation that it’s set pressure is correct.
4.2 Incorrect Set Pressure Reading - If the reading on the dial gauge at test stage 3.5 is above or below the allowable tolerance
range of the set pressure of the safety relief valve then this indicates that the safety relief valve is not set correctly. The safety
relief valve should be overhauled or replaced.
4.3 Correct Re-Seal Pressure Reading - If the reading on the pressure gauge at test stage 3.6 is not less than the allowed re-seat
pressure then this is confirmation that the valve has re-sealed correctly.
4.4 Incorrect Re-Seal Pressure Reading - If the reading on the pressure gauge at test stage 3.6 is less than the allowed re-seat
pressure then this indicates that the safety relief valve has not re-sealed correctly. The valve should be overhauled or replaced.
4.5 General - The safety relief valve manufacturer should always be consulted if there is any doubt about the acceptability of the
performance of the safety relief valve.
Note. Seetru Limited offers a safety relief valve refurbishment service.
5. Pressure Gauge Check Rig
The unit may also be used to check the accuracy of pressure gauges against a known standard reference gauge.
Follow the set up procedure 2 but mount the pressure gauge to be checked in the safety relief valve test port 2. It is also
recommended that the regulated gauge pressure is not greater than the full-scale deflection of the gauge to be checked up to
a maximum pressure of 55 Bar.g.
The sequence of operation is similar to that for safety relief valves, however the pressure is applied incrementally at the desired
check pressures. Use outlet control valve 2 to vent the pressure prior to removal of the tested gauge.
6. Integrity Test
The integrity of the internal pipe-work must be checked every 12 months. This is carried out as follows:
6.1 Fit a dial gauge, which has a full-scale deflection of greater than 55 bar to pressure gauge port 3.
6.2 Fit the sealing plug into the safety relief valve test port 2.
6.3 Connect the unit to a regulated supply.
6.4 Adjust the supply regulator to 55 bar.
6.5 Ensure outlet control valve 2 is closed.
6.6 Open inlet control valve 1 and pressurise the unit to 55 bar.
6.7 Watch the dial gauge rise and stop at 55 bar.
6.8 Shut off inlet control valve 1.
6.9 Watch the dial gauge for 1 minute. The pressure must not drop.
6.10 If a pressure drop is observed check each connection for leaks.
6.11 Use outlet control valve 2 to vent the unit pressure to atmosphere.
6.12 Disconnect the supply at inlet port 1 and tighten any leaking joint or replace seals as required (refer to section 8 - Maintenance).
6.13 Repeat the test from stage 6.3.
Valve Test Port 2
(Shown with Safety
Valve & adaptor fitted)
Pressure Gauge
Port 3
(Shown with
Di
g
ital Gau
g
e
Inlet Port 1
Inlet Control
Valve 1
Outlet
Control Valve

Quicktester Installation, Operating and Maintenance Instructions Issue: 3 03/08/04 G43INS Page 3 of 3
7. Test Integral Fitted Safety Valve
The integrity of the safety relief valve, which is set at 61 bar and is supplied with the unit, can readily be checked in a similar
manner to the integrity test. Using this method, the safety relief valve does not have to be removed from its position inside the case
where it is attached to the valve test port block.
7.1 Fit a dial gauge that has a full-scale deflection of 90 bar to pressure gauge port 3.
7.2 Fit a sealing plug into the safety relief valve test port 2.
7.3 Connect the unit to a regulated supply.
7.4 Adjust the supply regulator to 70 bar.
7.5 Follow section 3 ‘Sequence of Operation’.
7.6 On no account apply a pressure in excess of 70 bar.
8. Maintenance
Prior to any maintenance, the supply pressure must be isolated and attached pipe-work
disconnected.
8.1 Access to Internal Components
The unit contains a safety relief valve, which must be included in any maintenance scheme required by the current pressure
systems regulations. To gain access to the internal components open the case by:
8.1.1 Remove the safety relief valve test port adaptor.
8.1.2 Remove the pressure gauge and adaptor.
8.1.3 Remove the control valve operating hand wheels by prising off the plastic cover and unscrewing the retention nut.
8.1.4 Turn the unit over.
8.1.5 Unscrew the four rubber feet.
8.1.6 The top and bottom halves of the case will now separate.
8.1.7 Turn the unit over, exposing all of the internal components.
8.2 Flow Restrictor
Periodically check the restrictor for blockage by holding up to a light source and viewing through the bore. Replacement
restrictor’s are available from Seetru. Please quote part reference number M00000210.
To remove the flow restrictor (See Picture B):
8.2.1 Unscrew conex supply port.
8.2.2 Unscrew and discard the flow restrictor.
8.2.3 Assemble a new flow restrictor.
8.2.4 Reassemble is reverse of above. Ensure restrictor is fitted in direction indicated by arrow.
8.2.5 Carry out an integrity test as detailed Para 6.
Picture B – Shown with Cover Removed, not necessary to replace Restrictor
Conex Supply Port
Dowty Seal
Flow RestrictorPressure Gauge
Port 3
Inlet Control
Valve 1
Table of contents
Popular Control Unit manuals by other brands

Johnson Controls
Johnson Controls NIE39 installation instructions
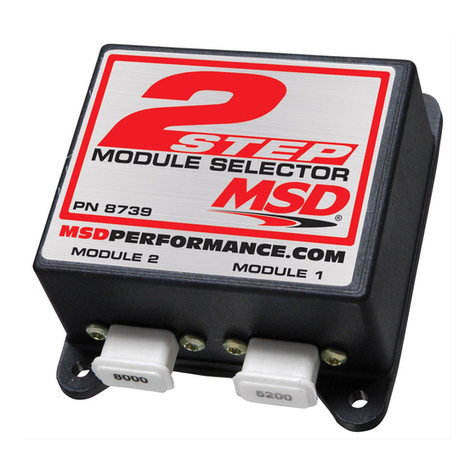
MSD Ignition
MSD Ignition 8739 installation instructions
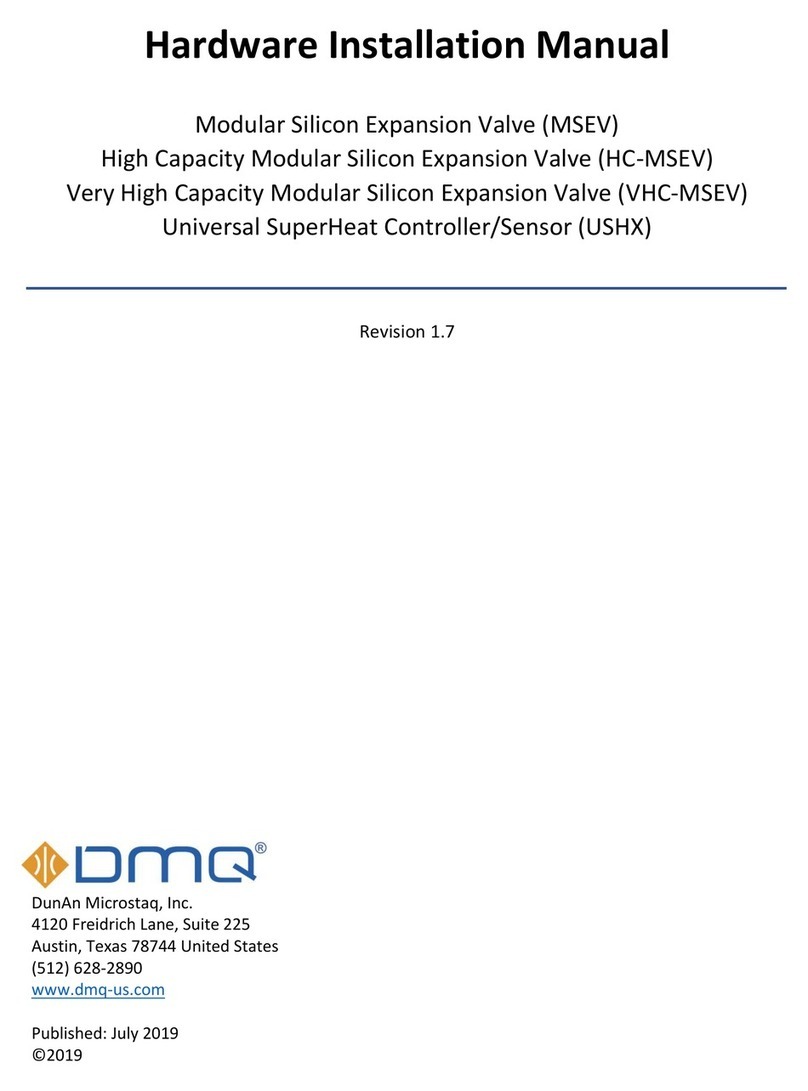
DMQ
DMQ A12V-U112 Hardware installation manual
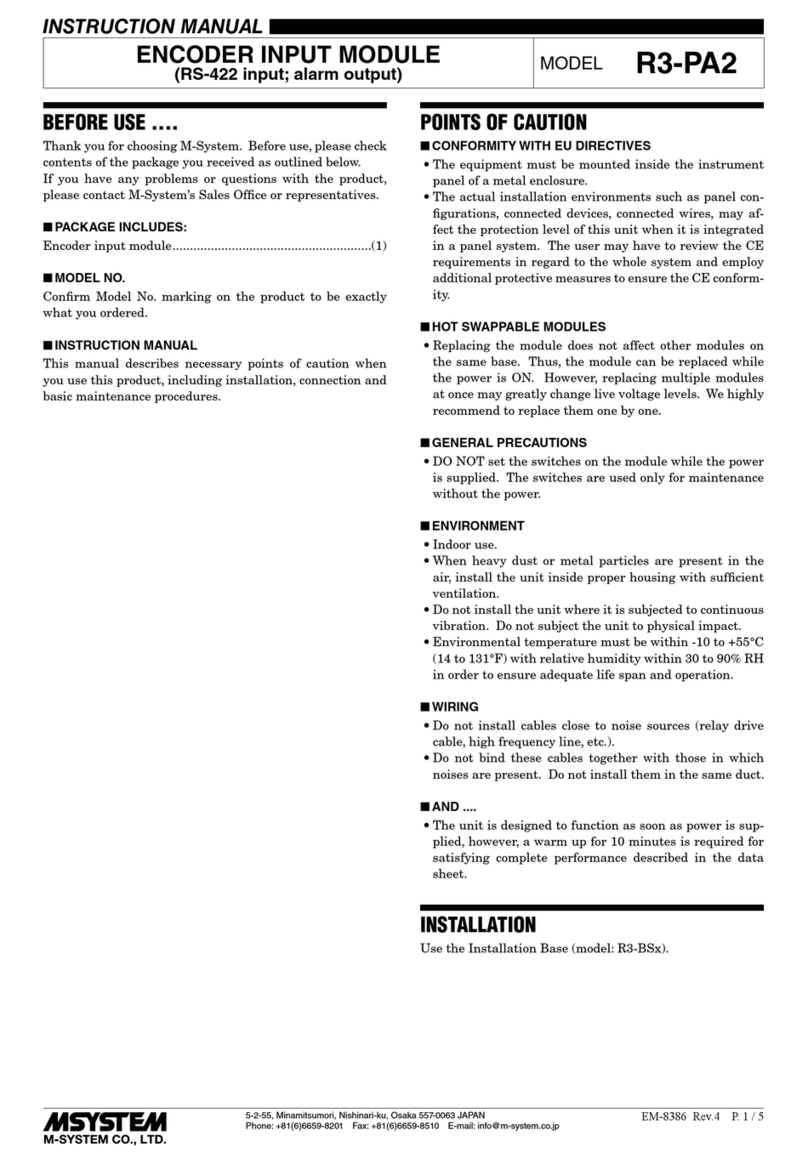
M-system
M-system R3-PA2 instruction manual
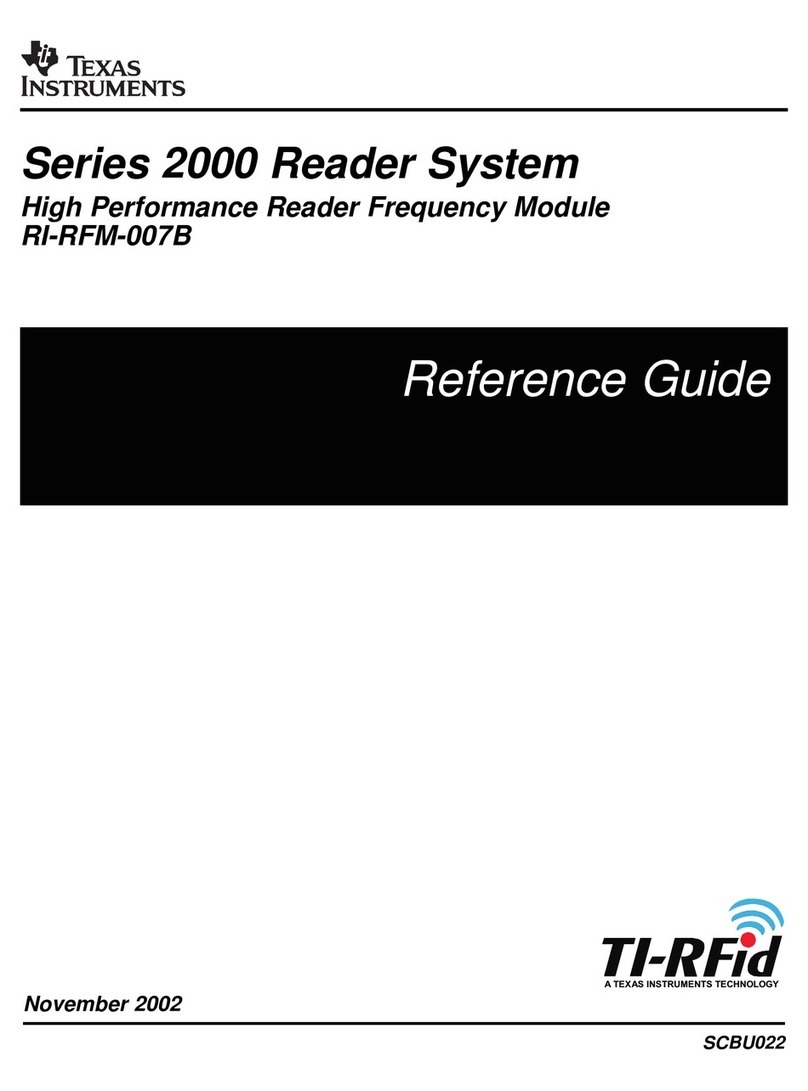
Texas Instruments
Texas Instruments 2000 series reference guide
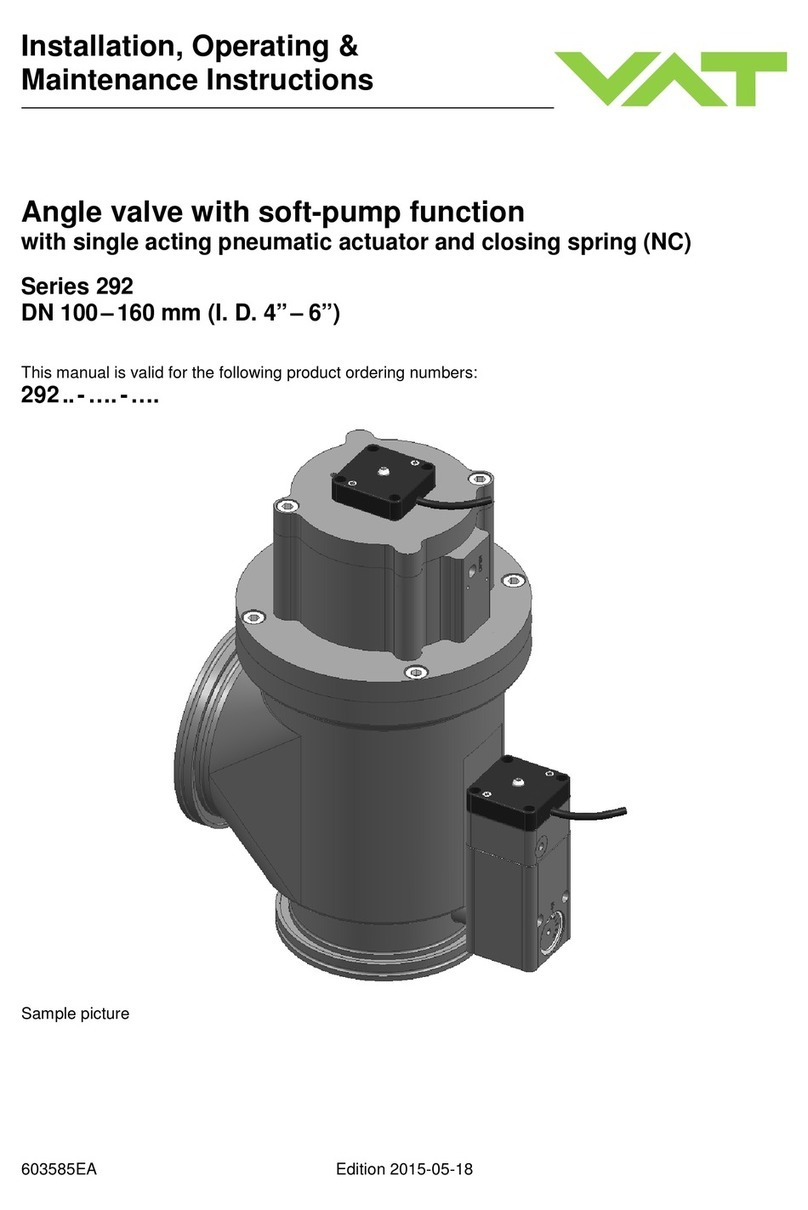
VAT
VAT 292 Series Installation, operating, & maintenance instructions
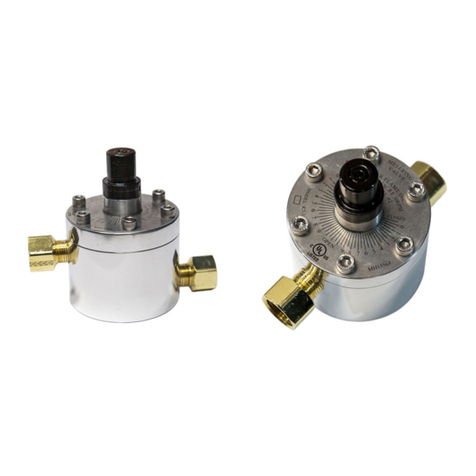
Power Flame
Power Flame K7 Installation and operation manual
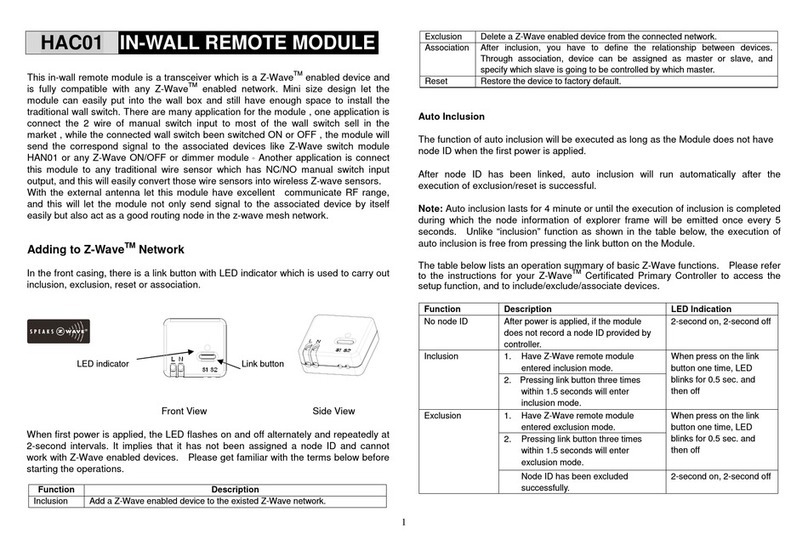
EVERSPRING
EVERSPRING HAC01 user manual

VAT
VAT 190 Series Installation, operating, & maintenance instructions
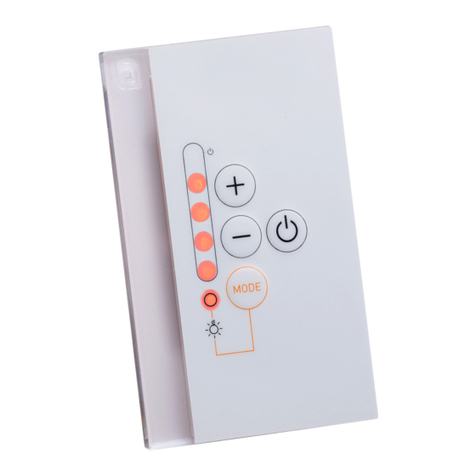
Sentiotec
Sentiotec Infrabox basic S Instructions for installation
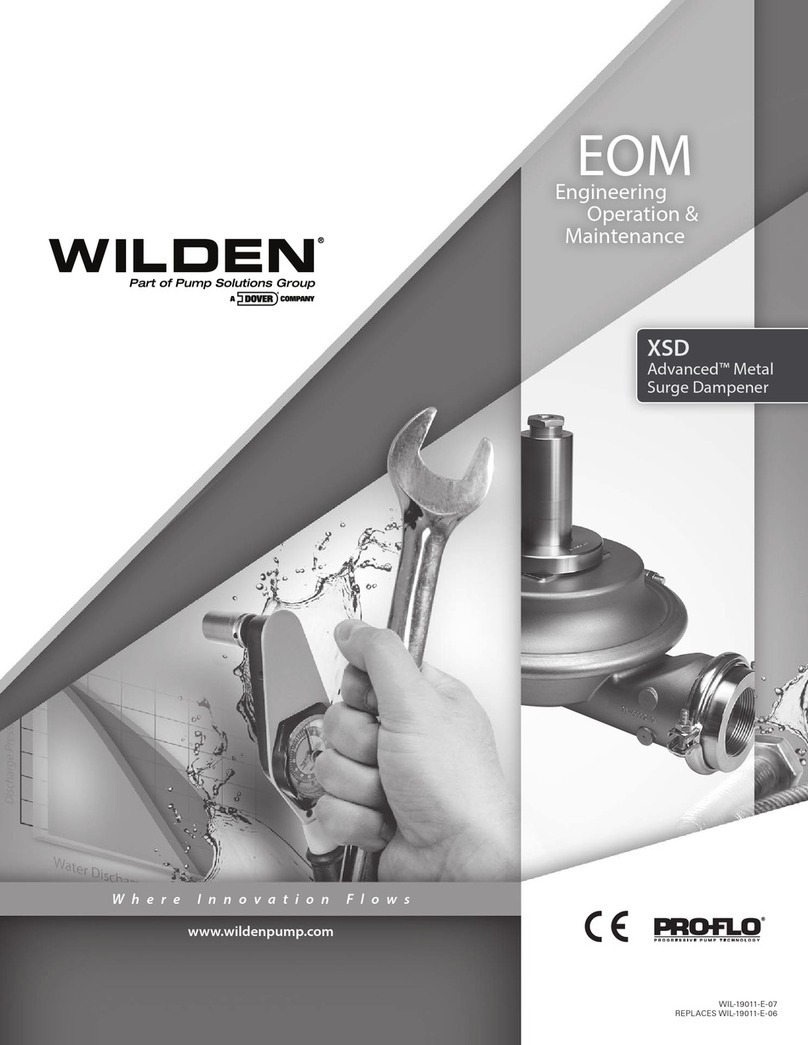
PSG
PSG Wilden XSD Series Engineering, operation & maintenance

RMG
RMG 711 S2 Operation and Maintenance, Spare Parts