SGS electronic TVC-B10 User manual

TVC-B10
1
© SGS electronic 2006-2023
TVC-B10
10A dual speed controller RC tracked vehicles
The controller contains all components for controlling two DC motors in a
tracked vehicle.
The behavior of the integrated mixer can be set for different vehicle types.
The controller can thus be set for full tracks, half tracks and wheeled ve-
hicles with differential drive. In addition, there are variants for historical
tracked vehicles without tableturn as well as the possibility of inertia simu-
lation.
The controller is equipped with BEC and has an EMK brake, which is released
in the middle position of the throttle and steering stick. The braking effect
can be set either via an RC channel, or fixed.

TVC-B10
2© SGS electronic 2006-2023
1 Note
Installation of the module requires intermediate to advanced modeling
skills. Soldering skills are required to connect the wiring. Inexperienced
modelers and persons aged under 16 years old should seek the assistance
of an experienced modeler. Always switch off power when working on
the wiring. Especial take care when connecting more than one receiver
energy source. Prevent the device from getting wet. Check loads before
connecting them to the modul at a current limited, or fuse protected
source.

TVC-B10
3
© SGS electronic 2006-2023
Contents
1 Note 2
2 Introduction 5
2.1 Technology................................. 5
2.2 Scopeofdelivery............................. 6
2.3 options ................................... 6
3 Functional description 7
3.1 Manualcontrol .............................. 7
3.1.1 Channel 1 - proportional forward/back . . . . . . . . . . 7
3.1.2 channel 2 - proportional left/right . . . . . . . . . . . . . 7
4 Einbau 8
4.1 Batteryconnection............................ 8
4.2 Connecting the motors . . . . . . . . . . . . . . . . . . . . . . . . . 8
4.3 Connecting the servo cables . . . . . . . . . . . . . . . . . . . . . 8
4.4 BECjumpers................................ 9
4.5 Scalebus operation (optional) . . . . . . . . . . . . . . . . . . . . . 10
5 Commissioning 12
5.1 Startup ................................... 12
5.2 Correct driving direction . . . . . . . . . . . . . . . . . . . . . . . . 12
5.3 EMFbrake ................................. 13
5.4 Errorstates ................................ 13
5.5 Changing the mixing function . . . . . . . . . . . . . . . . . . . . 14
5.5.1 How to change mixer function . . . . . . . . . . . . . . . . 14
6 Glossary of terms 16
7 Technical data 18
8 Important 19
8.1 Warning .................................. 19
8.2 Environmental protection . . . . . . . . . . . . . . . . . . . . . . . 19
8.3 Address................................... 20
8.4 Contact ................................... 20

TVC-B10
4© SGS electronic 2006-2023
8.5 Documentdate.............................. 20
8.6 Documentation.............................. 20
List of Figures
1 Assignment of the connector for power supply . . . . . . . . . 8
2 pinoutservocable............................ 9
3 servocableposition........................... 9
4 do not forward BEC voltage to receiver . . . . . . . . . . . . . . 10
5 forward BEC voltage to receiver . . . . . . . . . . . . . . . . . . . 10
List of Tables
1 servo cable assignment . . . . . . . . . . . . . . . . . . . . . . . . 9
2 Errorcodes ................................ 13
3 list of optional mixing functions available . . . . . . . . . . . . . 15
4 Abbrevation for the manipulators in the transmitter housing 17

TVC-B10
5
© SGS electronic 2006-2023
2 Introduction
The controller is designed for an input voltage range from 6.5V to 24V.
This means that the controller works with the 6 cell NC packs commonly
used in the RC car sector, but also with lead batteries up to 24V. Two stan-
dard automotive fuses protect the model and the battery from excessive
currents.
The controller has a built-in BEC circuit to power the receiver from the drive
battery.
Please note that the removable BEC current decreases as the supply voltage
increases.
To disconnect the internal BEC regulator from the receiver supply, a jumper
must be removed.
As a failsafe function, an extensive plausibility check of the transmitter
signals is integrated in the software.
In addition, the controller has a temperature monitoring of the output
stage.
It switches off at 75°C and can be switched on again at 65°C and above.
To do this, the transmitter sticks must be set to the neutral position to
prevent a sudden start after the controller has cooled down.
2.1 Technology
The controller is microprocessor controlled. The processor works with
16MHz clock frequency.
The output stage is constructed from N-channel MOSFETs, which have an
inrush resistance of only 0.008 ohms and a continuous current capability of
60A. To make effective use of the low internal resistance, the output stage
transistors are driven by sophisticated MOSFET push-pull output stages
with integrated charge pump.
Under normal ambient conditions, a continuous current of 10A is achieved.
The controller operates with a PWM frequency of 16kHz.
reicht. Der Regler arbeitet mit einer PWM-Frequenz von 16kHz.

TVC-B10
6© SGS electronic 2006-2023
2.2 Scope of delivery
The controller is supplied with the connectors for the motor connection
and the battery connection.
2.3 options
•
10 controllable light outputs for brake light, reverse light, turn signal,
warning light, RKL, low beam and high beam.
• Lipo single cell monitoring
• RC channel adjustable standstill brake

TVC-B10
7
© SGS electronic 2006-2023
3 Functional description
3.1 Manual control
A radio remote control with at least one proportional channel is required
to control the module. To use all functions, four RC channels are required.
3.1.1 Channel 1 - proportional forward/back
Direction of rotation for the motor. From the throttle channel is also derived
reverse light on/off, brake light).
3.1.2 channel 2 - proportional left/right
The control of the turn signals is derived from this channel. It is usually
connected to the steering channel with a V-cable, parallel to the steering
servo. If the channel is not connected, the turn signals only function as
warning turn signals.

TVC-B10
8© SGS electronic 2006-2023
4 Einbau
4.1 Battery connection
Fahrakku plus (+)
Fahrakku minus (-)
Figure 1: Assignment of the connector for power supply
Power is supplied via the green, plug-in screw terminal. Please pay atten-
tion to the correct polarity of the supply voltage! (see figure 1).
It makes sense to include a switch in the positive supply line to the battery
to switch the model on/off. Never switch the minus in RC model building,
because the minus also the reference potential of the servo signals.
There are two automotive fuses for the motor output stages on the circuit
board. They are pluggable and can be easily replaced if necessary.
If one of the power stage fuses has blown, the BEC still works and the LED
indicates the function. However, the corresponding motor output stage
no longer supplies power. In addition, the BEC circuit also has a fuse. This
is soldered onto the circuit board. If this fuse has blown, the BEC no longer
supplies voltage and the controller no longer shows any function.
4.2 Connecting the motors
Black, plug-in screw terminals are provided for the drive motors. One
motor is connected to each screw terminal. The motors must be radio
interference suppressed, as is usual in model building.
4.3 Connecting the servo cables
The controller is equipped with JR servo cables. The pinout is shown in
figure 2.

TVC-B10
9
© SGS electronic 2006-2023
Figure 2: pinout servo cable
Figure 3: servo cable position
chan-
nel
connector optional Function
1 X50 no throttle
2 X51 yes steering
Table 1: servo cable assignment
4.4 BEC jumpers
The controller contains a BEC circuit that generates a regulated voltage of
5V from the voltage of the drive battery to supply the receiver and servos.
Since in function models often several controllers with BEC are installed,
but the parallel operation is problematic under certain circumstances, the
connection of the installed BEC to the receiver can be disconnected. Two
green jumpers are used for this purpose.
If the jumpers are inserted vertically, the internal BEC voltage is passed on
to the receiver and from there to the servos.
If the jumpers are inserted horizontally (or are not inserted), the voltage is
not passed on. In this case, another module must supply the receiver with
power.

TVC-B10
10 © SGS electronic 2006-2023
Figure 4: do not forward BEC voltage
to receiver
Figure 5: forward BEC voltage to re-
ceiver
4.5 Scalebus operation (optional)
As an alternative to control via the receiver and the servo cables, the
controller can also be controlled via the scale bus. To do this, the controller
is connected to the other modules with the scale bus cable (white, four-pin
connector).
For example, the FO module TVC-MF-10 can control the controller. The
controller switches to scale bus mode if no servo signal is present at the
two servo cables when it is switched on. Accordingly, the servo cables must
not be plugged into the receiver during scale bus operation.
In scale bus mode, the controlling module specifies the mixing function.
Therefore, a controller for a half-track vehicle can also be operated with an
FO module for a battle tank.
The controller then works as a full track mixer.
Not only the information for controlling the drive motors, but also the
information for the auxiliary drives is sent via the scale bus.
If no jumper is plugged in, the information of the drives is output.
If coding bridges are plugged into servo cables 1 or 2, the motor outputs

TVC-B10
11
© SGS electronic 2006-2023
are controlled as specified in the description of the FO module.
Example tracked vehicle:
1. No coding jumper plugged
→Controller works as drive controller (drive chains)
2. coding jumper plugged into servo cable 1
→
Controller works as tower control (barrel elevation and tower rota-
tion)
It is of course possible to connect several controllers to the scale bus. It is
also possible for two controllers to output the same information.

TVC-B10
12 © SGS electronic 2006-2023
5 Commissioning
5.1 Startup
1.
Connectconnect the drive battery on the transmitter the throttle and
control levers to the center position (the corresponding trim as well).
on the receiver. The green LED lights up for approx. 1s.
2.
The green LED on the board flashes until the controller has detected
the center position of the channels. If zero point detection is not
possible, the LED does not light up. The zero point is not determined
again until the receiver is switched on/off.
3. If the green LED is continuously on, the vehicle is ready to drive.
This automatic calibration is done in this way at
every
switch-on. I.e., the
position detected at power-up is stored as the neutral position. This applies
to both steering and speed.
5.2 Correct driving direction
The direction of travel depends on the mechanical arrangement of the
engines in the vehicle. Usually, the motors are mounted so that the motor
shafts are in opposite directions. As a result, the motors must be connected
with different polarity in order to drive in one direction.
Of course the correction of the driving direction can be done directly on
transmitters with the servo reverse setting. If the transmitter does not
have this possibility, you can proceed as follows:
1.
model moves forward when steered backward and vice versa: Change
connections on both motors (reverse polarity).
2.
Model moves left when steered to the right and vice versa: Change con-
nections from both motors, reversing polarity. (connecting line from
motor 1 to motor 2 and vice versa).
3.
The directional control is set to neutral, but the model does not drive
straight ahead: Correct with steering trim

TVC-B10
13
© SGS electronic 2006-2023
5.3 EMF brake
The controller has an adjustable EMF brake. It is activated by moving the
throttle and steering sticks to the center position.
The braking effect with which the brake is applied is indicated by the yellow
LED. The longer the yellow LED is on, the stronger the braking effect.
• LED Off corresponds to 0% braking effect.
• LED On corresponds to 100% braking action.
If you want to change the braking effect, you must press the button. The
button is located between the light connector and the jumpers for the BEC.
Use a thin stick made of plastic or wood to press the button. The push
button has a clearly noticeable pressure point.
If you move the throttle in one direction the on phase of the yellow LED
gets longer and longer, in the other direction shorter and shorter until it is
completely off. The stronger the lever deflection, the faster the adjustment.
The green LED lights up continuously as soon as you take the lever out of
the neutral position to indicate that the controller is making a change. If
you press the button again, the brake setting is saved and is retained even
after switching off and on again.
5.4 Error states
Normally, the green LED is permanently on. If the controller detects an
error, it indicates this by briefly flashing the green LED n times. In addition,
the red LED lights up. All error conditions lead to the motor being switched
off.
blink
code
fault Acknowledgement / Troubleshooting
2 times
no signal from re-
ceiver
Check receiver and connections / elimi-
nate radio interference
3 times
overtemperature allow controller to cool down
Table 2: Error codes

TVC-B10
14 © SGS electronic 2006-2023
5.5 Changing the mixing function
Different vehicles and transmission types need different mixers. In the
past, we offered different versions of the controller (”OG”, ”CM”, ”HT”, etc.).
With this controller, you can now define the mixer function yourself. An
overview of the available mixers is shown in table 3 on page 15.
Notes
Note that the maximum current consumption of mixers with table-
turn is not significantly higher because the drives work against each other
in tableturn.
Be careful when operating with inertia simulation. The vehicle then natu-
rally reacts with a delay to the commands of the radio remote control.
5.5.1 How to change mixer function
1.
Connect everything as described under commissioning and switch
on the transmitter.
2.
press the button when switching on the controller. The setting mode
is indicated by the red and yellow LEDs lighting up.
3.
With the throttle and steering channel you can now select nine posi-
tions by setting the sticks in left/right stop or leave neutral position.
The position number is indicated by the red LED flashing while the
green LED is lit. If the green LED goes out, the cycle starts again.
4.
For example, if the red LED flashes three times, mixer number three
of the table is selected. save this, hold the sticks in position and press
the button again.
5. Then release the stick. Now the mixer is selected and saved.

TVC-B10
15
© SGS electronic 2006-2023
Code
drive type name
table-
turn
vehicle type description
1 full track
simulation
superposition
gearbox 100%
yes
tracked con-
struction
machines,
modern
tanks, snow
groomers
Simulation of the driving behavior
of a mechanical superimposed trans-
mission without limitation of the
drive power
2 full track
simulation
superposition
gearbox 80% /
60%
yes
tracked con-
struction
machines,
modern
tanks, snow
groomers
Simulation of the driving behavior
of a mechanical superimposed trans-
mission with straight-line driving lim-
ited to 80% and steering limited to
60%. Only when cornering is 100%
given to the drives to account for the
increased friction.
3
half track/
wheeled
classic mixer no
wheeled on-
struction
machines,
halftracks
The chain inside the curve is reduced
from 100% to 50% of the driving
speed at steering angle
4 full track
mechanical
superimposed
gearbox
yes
modern
tanks, snow
groomers
This setting is for mechanical super-
imposed gear units
5 full track
no mixer, sin-
gle chain con-
trol
yes
Operation via
manual mixer
or mixer in ra-
dio
This variant has no mixer, only a
brake that acts when both drives
come to a standstill.
6 full track
classic mixer
with tableturn
yes
tracked con-
struction
machines,
modern
tanks, snow
groomers
Mixing function as used e.g. by
Tamiya
7 full track
classic mixer
without table-
turn
no
historical
construction
machinery and
tanks
Mixing function as used for exam-
ple in Tamiya but when cornering the
chain does not run backwards.
8 full track
simulation
superposition
gearbox 100%
and inertia
simulation
yes
tracked con-
struction
machines,
modern
tanks, snow
groomers
Table 3: list of optional mixing functions available

TVC-B10
16 © SGS electronic 2006-2023
6 Glossary of terms
BEC Battery Eliminator Circuit
This circuit replaces a extra Battery needed for the receiver and con-
nected servos, by generating a fixed voltage from the drive battery.
ESC Electronic Speed Controller
This is a unit to control the speed and direction of a DC motor.
LED Light Emmitting Diode
A light-emitting diode (LED) is a semiconductor device that emits
visible light when an electric current passes through it. Benefits of
LEDs are low power requirement and long life. Disadvantages is the
more complicated wiring, compared to a classic bulb, it has a polarity
and a resistor is needed to limit the current.
Scalebus
The Scalebus is a development of
SGS electronic
to connect con-
trollers and modules to compose solutions for complex RC models.
SBus
The Sbus has been introduced by
Futaba
to simplify the wiring be-
tween RC Receivers and servos / esc.
SBus
The SBus was introduced by the company
Futaba
to simplify the
wiring between receiver and servos/controllers. This is especially
useful for models with many controllers.
IBus
The IBus was introduced by the company
Flysky
to simplify the wiring
between receiver and servos/controllers. This is especially useful for
models with many controllers.
SUMD
The SUMD sum signal has been introduced by the company
Graup-
ner
to simplify the wiring between receiver and servos/controllers.
This is especially useful for models with many controllers.

TVC-B10
17
© SGS electronic 2006-2023
Abbre-
vation
meaning explanation
Stick Stick Stick not self centering
StickS S
tick
Selfcentering
self centering Stick
TSMS T
hree
S
tage
M
omentary
Switch
self centering momentary switch with three
stages
TSS T
hree
S
tage
Switch
switch with three stages
Pot Potentiometer linear- or rotary knob
PotC Pot
entiometer
with Center key
linear- or rotary knob with a center key
Table 4: Abbrevation for the manipulators in the transmitter housing

TVC-B10
18 © SGS electronic 2006-2023
7 Technical data
Rated motor current drive (per mo-
tor)
15 Ampere 1 minute: 20 Ampere
/ 10s: 220 Ampere
Supply voltage (with BEC) 6,5 to 24 V
Allowable BEC current
1000mA short term, 600mA at
12V, 300mA at 24V
PWM frequency 16kHz
Typical maximum power dissipation 5 Watt
Typical voltage drop in the output
stage
0,15 Volt
Dimens 75x47x30mm
software version 1.2

TVC-B10
19
© SGS electronic 2006-2023
8 Important
This equipment described above has been tested and inspected for quality
and function. And it is intended for installation and use only as described
above. This equipment does not contain any user serviceable parts. The
supplier accepts no responsibility, financially or otherwise, for damages
caused by use or misuse of the equipment described above. The equip-
ment must be protected from exposure to water to prevent short circuit.
Do not open the equipment or attempt to change function, wiring, or doc-
umentation in any way. Do not connect to incorrect voltage or reverse the
battery polarity. Do not use in a careless or abusive fashion around persons
or property. Do not attempt to repair. Any legitimate use, e.g. Installa-
tion in a model makes the user responsible to ensure that the operating
instructions and non-liability agreement are provided to the purchaser of
the module described above.
Do operate the device only in the permissible operating conditions. Do
not make any changes to the controller through. The device shall not be
exposed to splashing water or rain (causing a short circuit).
8.1 Warning
Due to choking hazard caused by small parts that may be swallowed, this
product is not suitable for children under 6 years of age.
8.2 Environmental protection
For defective devices, repair is possible in many cases. Please contact us. If
you do decide to dispose of the device, you will be making a contribution to
environmental protection if you return the device to a municipal collection
point for recycling. Electronic devices do not belong in household waste.

TVC-B10
20 © SGS electronic 2006-2023
8.3 Address
SGS electronic
Zeppelinstraße 36
47638 Straelen
Germany / Europe
8.4 Contact
Web www.sgs-electronic.de
Email [email protected]
Ust-IdNr.: DE 249033623
WEEE-Reg.-Nr.: DE 90290947
8.5 Document date
This document was created on 2023-03-31 01:04:34+02:00
8.6 Documentation
We reserve the right to make updates, changes or additions to the infor-
mation and data provided.
The documentation that accompanies your product applies.
Please note that documents obtained later via download may not corre-
spond to the status of your module.
Table of contents
Other SGS electronic Controllers manuals
Popular Controllers manuals by other brands
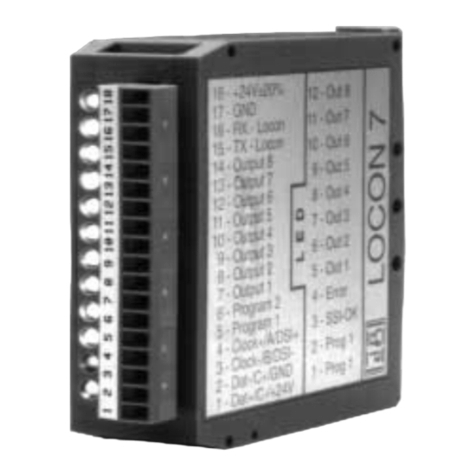
DEUTSCHMANN AUTOMATION
DEUTSCHMANN AUTOMATION LOCON 7 instruction manual
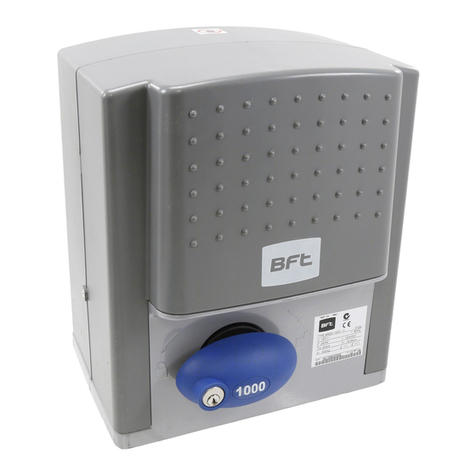
BFT
BFT ARES Installation and user manual

Kelly
Kelly KLS11601-8080N user manual
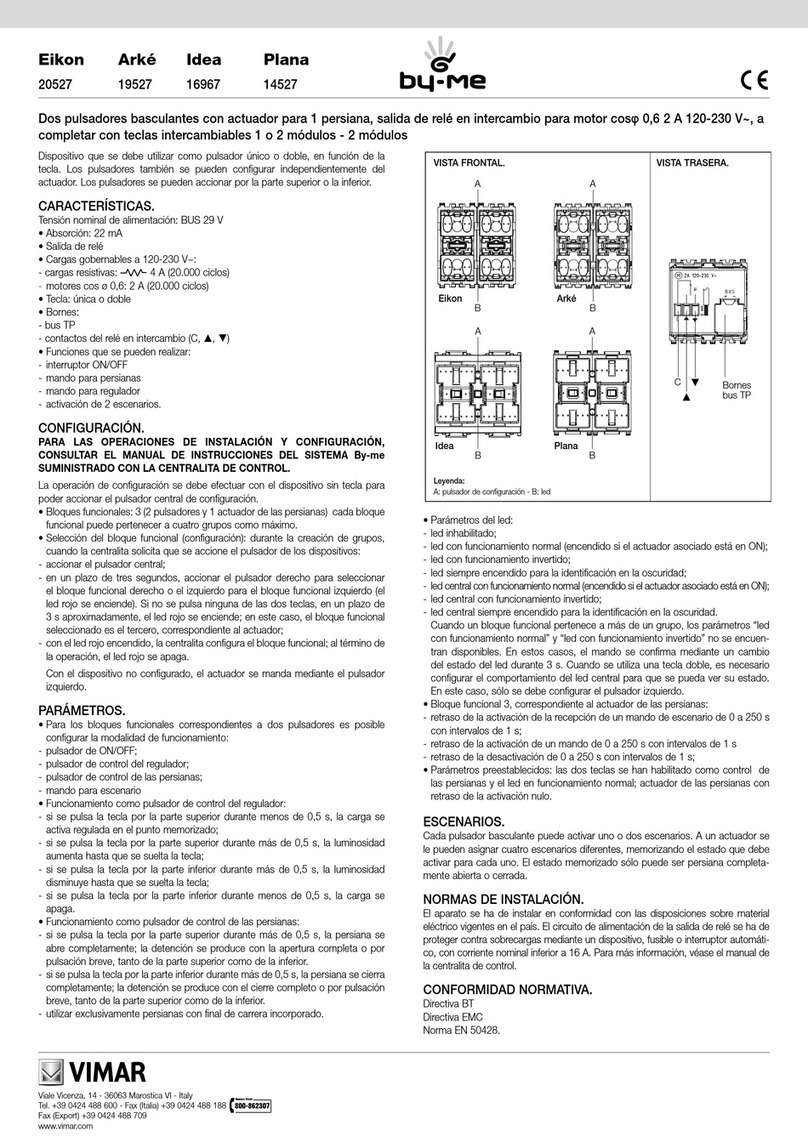
Vimar
Vimar by-me Eikon 20527 quick start guide
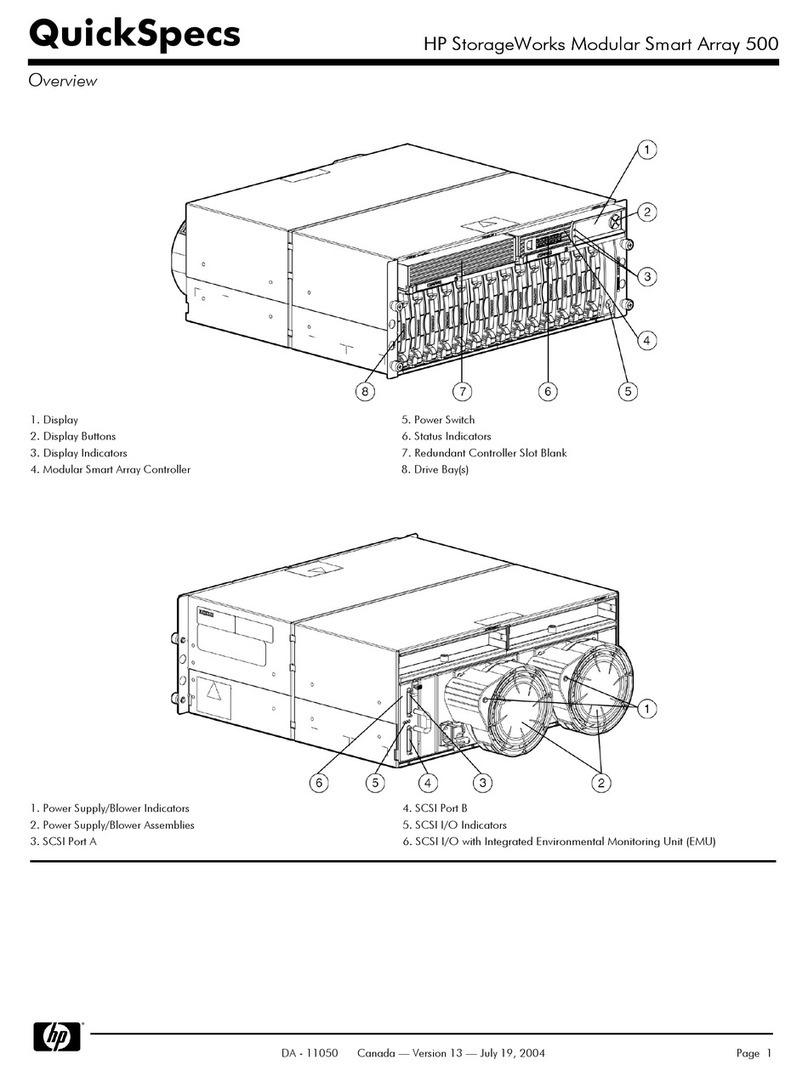
HP
HP StorageWorks Modular Smart Array 500 System overview
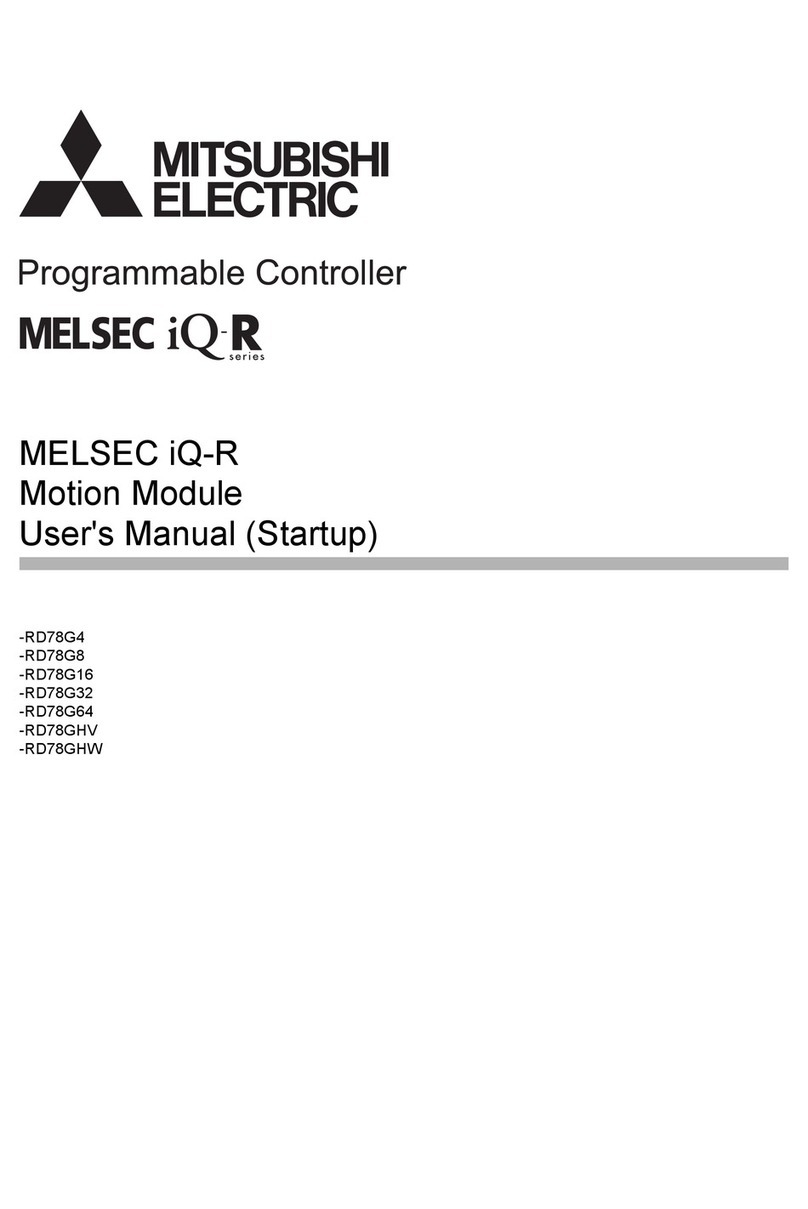
Mitsubishi Electric
Mitsubishi Electric MELSEC iQ-R RD78G4 user manual