siat SM44 HS Guide

SM44 HS
NASTRATRICE AUTOMATICA
AUTOMATIC CASE SEALING MACHINE
MACHINE ENRUBANNEUSE AUTOMATIQUE
AUTOMATISCHE KARTONVERSCHLIESSMASCHINE
PRECINTADORAAUTOMATICA
MANUALE DI ISTRUZIONI E PARTI DI
RICAMBIO
INSTRUCTIONS MANUAL AND SPARE PARTS LIST
MANUAL D’INSTRUCTIONS ET PIECES DETACHEES
BEDIENUNGSANLEITUNG UND ERSTAZTEILLISTE
MANUAL DE INSTRUCCIONES YRECAMBIOS
Cod. pubbl.: SMB00087K.1

SIAT
S.p.A.
- Via Puecher, 22 - 22078 TURATE (CO) ITALY - P.O. BOX 1
Tel.02-964951 - Telefax 02-9689727
Instruction manual for the use, maintenance, safety, shipment, storage, unpacking, set-up, repairing, trouble shoo-
ting, spare parts and disposal concerning the case sealing machine model SM44 HS.
This publication is property of SIATS.P.A.
Via Puecher, 22 - 22078 TURATE (CO) -ITALY
Tel.02-964951 - Fax. 02-9689727
Edition: February 2016
The reproduction of this manual is strictly forbidden.
All rights reserved ©Siat S.p.A. 2016
The manufacturer reserves the right to modify the product at any time withoutnotice.
Publication n. SMB00087K.1
Version 1
SM44 HS
AUTOMATIC CASE SEALING MACHINE WITH DRIVE SIDE BELTS
- Maximum box size:
- Minimum box size:
h. 500 mm x w. 500 mm x l 600 mm
h. 140 mm x w. 160 mm x l 200 mm
- Adhesive tape: w. 50/70 mm
- Belt speed: 30 m/min.
- Production: 13-15 boxes/min
- Average air consumption: 180 Nl/minapproximately
2
February 2016
ENGLISH

ABBREVIATIONSANDACRONYMS
INDEX
LISTOFABBREVIATIONS,ACRONYMSAND UNUSUAL
TERMS TO BE FOUND IN THISMANUAL
Section
Manufacturing specifications
Manual, how to use the
Safety
Serial Number
After-sale service
Warranty
Operators' skill levels
Technical specifications
Dimensions
Transportation
Unpacking
Installation
Controls
Operation
Safety devices
Set-up and adjustments
Machine use
Tapereplacement
Cleaning
Trouble shooting
Maintenance
Lubrication
Blade replacement
Belt replacement
Adjustment of belt tension
Additional Instructions
Enclosures
1.1
1.2
3
2.1
2.2
2.3
3.6
4.2
4.6
5
6
7
8
9
10
11
12
12.3
12.4
12.7
13
13.5
13.9
13.10
13.11
14
15
Dwg.
Encl.
Ex.
Fig.
Max.
Min.
Mod.
N.
N/A
OFF
ON
OPP
Pict.
PLC
PP
PTFE
PVC
Ref.
SIAT SPA
=
=
=
=
=
=
=
=
=
=
=
=
=
=
=
=
=
=
=
drawing
enclosure
example
figure showing spare parts
maximum
minimum
machine model
number
not applicable
machine stopped
machine running
oriented polypropylene adhesive tape
picture
Programmable Logic Control
polypropylene
Polytetrafluorethylene
Polyvinylchloride
reference mark
Società Internazionale Applicazioni
Tecniche (Società per Azioni)
Illustration
Tav.
=
w
h
l
ol
cbh
=
=
=
=
=
width
height
length
overall length
conveyor bed height
Spare parts
last section
February 2016
3
ENGLISH

1-INTRODUCTION
1.2
1.2.1
HOW TO READ AND USE THE INSTRUCTIONMANUAL
IMPORTANCE OF THEMANUAL
The manual is an important part of the machine; all information contained herein is intended toenable the equip-
ment to be maintained in perfect condition and operated safely. Ensure that the manual is available to all ope-
rators of this equipment and is kept up to date with all subsequent amendments. Should the equipment be sold
or disposed of, please ensure that the manual is passed on. Electrical and pneumatic diagrams are included in
themanual.EquipmentusingPLCcontrolsand/orelectroniccomponentswillincluderelevantschematicsorpro-
grammes in the enclosure, and in addition the relevant documentation will be delivered separately.
1.2.2
MANUAL MAINTENANCE
Keep the manual in a clean and dry place near the machine. Do not remove, tear or rewrite parts of the manual
for any reason.
Use the manual without damagingit.
Incasethe manual has been lost or damaged, ask your after sale servicefor a new copy,quoting thecode num-
ber of the document.
CONSULTING THEMANUAL
The manual is composed of:
1.2.3
-
-
-
-
pages which identify the document and the machine;
index of the subjects:
instructions and notes on the machine: sections2÷14
enclosures, drawings and diagrams:
sections 15÷16
spare parts: last section.
-
All pages and diagrams are numbered. The spare parts lists are identified by the figure identification number.
All the notes on safety measures or possible dangers are identified by thesymbol:
All the important warning notes related to the operation of the machine are identified by the symbol:
The parts typed in bold refer to technical data or technical notes on a specificsubject.
1.2.4
HOWTOUPDATETHEMANUALINCASEOF MODIFICATIONSTOTHEMACHINE
Modifications to the machine are subject to manufacturer’s internal procedures.
The user receives a complete and up-to-date copy of the manual together with themachine.
Afterwards the user may receive pages or parts of the manual which contain amendments or improvements
made after its firstpublication.
The user must use them update this manual.
4
February 2016
ENGLISH

2-GENERALINFORMATION
2.1
SERIAL NUMBER OF THE MACHINE AND NAME OF THE MANUFACTURER
Part Number
SIATs.p.a.Via G.PuecherN°22
Turate (CO) ITALY
Watt
Year
Ampere
Model
Serial Number
Hertz
Type
Volt
Phase
2.2
FOR AFTER-SALE SERVICE AND SPARE PARTS PLEASE APPLYTO:
February 2016
5
ENGLISH
AGENT/DISTRIBUTOR OR LOCAL
AFTER SALE SERVICE:

WARRANTY
Withinthelimitsofwhatissetforthbelow,SelleragreestorepairorreplacewithoutcosttoBuyeranydefectivegoodswhensuchde-
fectoccurswithinaperiodoftwelve(12)monthsfromthedateinwhichSeller'sgoodshavebeenputintouse,butinnoeventbeyond
thirteen(13)monthsfromthedateofshipment.
Expresslyexcludedfromthiswarrantyarethosepartssubjecttonormalwearandtear(bywayofillustration,butnotlimitation,such
partsasbelts,rubberrollers,gaskets,brushes,etc.)andelectricalparts.
BuyermustimmediatelynotifySellerofanydefect,specifyingtheserialnumberofthemachine.
BuyershallsendtoSellerthedefectiveitemforrepairorreplacement.Sellerwillperformtherepairsorprovideareplacementwithina
reasonableperiodoftime.
Uponeffecting such repair or replacement,Sellershall have fulfilleditswarranty obligations.In theevent the repairsor replacement
mustbe effectedat theplacewherethemachineis installed,allexpensesforlabor,traveland lodging of Seller'spersonnelshallbe
sustainedbytheBuyer.Buyerwillbe invoicedinconformitywithSeller'sstandardchargesfortheservicesrendered.
Sellerisnotresponsiblefordefectsresultingfrom:
-
-
-
Improperuseofthemachine
Lackofpropermaintenance
TamperingwiththemachineorrepairseffectedbytheBuyer.
Sellerwillnotbe liableforany injuryto personsorthingsor forthefailureofproduction.Withrespectto thematerialsnot manufactu-
redbySeller,suchasmotorsandelectricalequipment,SellerwillgranttoBuyerthesamewarrantySellerreceivesfromitssupplierof
suchmaterials.Sellerdoesnotwarrantthecomplianceofitsmachineswiththelawsofnon-EECcountriesinwhichthemachinesmay
beinstalled,nordoesitwarrantcompliancewithlawsorstandardsrelatingtothepreventionofaccidentsorpollution.
AdaptationofSeller'smachinestotheaforesaidlawsorstandardsshallbetheresponsibilityofBuyerwhoassumesallliabilitythere-
fore.
BuyershallindemnifyandholdSellerharmlessagainstanyclaimbythirdpartiesresultingfromfailuretocomplywiththeaforesaidlaws
andstandards.
SIAT S.p.A.
Via Puecher, 22 - 22078 TURATE (CO) ITALY - Tel.02964951 - Fax 029689727 - http://www.siat.com - Email:[email protected]

3-SAFETY
3.1
GENERAL SAFETYINFORMATION
Read all the instructions carefully before starting the work with the machine; please pay particular attention to
sections marked by the symbol
The machine is provided with a complete safety protection
and with a two LOCKABLE EMERGENCY STOP BUTTON
placed on the same protection and on the control panel;
when one button is pressed, it stops the machine atany point
in the working cycle.
Disconnect the machine from the mains before any maintenanceoperation.
.
Keep this manual in a handy place near the machine: its information will help you to maintain the machine in
good and safe working condition.
3.2
DEFINITION OF THE OPERATORS' QUALIFICATIONS
- Machine operator
- Maintenance technician
- Electrician
- Manufacturer’s technician
Only persons who have the skills described in the following page should be allowed to work on the machine.
It is the responsibility of the user to appoint the operators having the appropriate skill level and the appropriate
training for each category of job.
SKILL 1
MACHINE OPERATOR
This operator is trained to use the machine with the machine controls, to feed cases into the machine, make
adjustments for different case sizes, to change the tape and to start, stop and restart production.
N.B.: the factory manager must ensure that the operator has been properly trained on all the machinefunctions
before starting work.
February 2016
7
ENGLISH

3-SAFETY
SKILL 2
MECHANICAL MAINTENANCE TECHNICIAN
This operator is trained to use the machine as the MACHINE OPERATOR and in addition is able to work with
the safety protection disconnected, to check and adjust mechanical parts, to carry out maintenance operations
and repair the machine.
He is not allowed to work on live electricalcomponents.
SKILL 2a
ELECTRICAL MAINTENANCE TECHNICIAN
This operator is trained to use the machine as the MACHINE OPERATOR and in addition is able to work with
the safety protection disconnected, to make adjustments, to carry out maintenance operations and repair the
electrical components of the machine.
He is allowed to work on live electrical panels, connector blocks, control equipment etc.
SKILL 3
SPECIALIST FROM THE MANUFACTURER
Skilled operator sent bythe manufacturer or its agent to perform complex repairs or modifications, when agreed
with thecustomer.
3.3
INSTRUCTIONS FOR A SAFE USE OF THEMACHINE
Only persons who have the skills described on the following paragraph 3.6 are allowed to work on the ma-
chine.
It is responsibility of the user to appoint the operators having the appropriate skill level and the appropriate
training for each category of job.
3.4
STATE OF THE MACHINE
List of the modes which are possible with thismachine:
-
-
-
-
-
-
automatic running;
running with safety protections removed or disabled;
stopped by using the main switch;
stopped by using the lockable emergency stop button;
electric powerdisconnected;
compressed air disconnected.
8
February 2016
ENGLISH

3-SAFETY
3.5
NUMBER OF THE OPERATORS
The operations described hereinafter have been analized bythe manufacturer; the number of operators
shown for each operation is suitable to perform it in the best way.
Asmaller or larger number of operators could be unsafe.
3.6
OPERATORS’ SKILLLEVELS
The table below shows the minimum operator's skill for each operation with themachine.
February 2016
9
ENGLISH
OPERATION
MACHINE MODE
OPERATOR’S
SKILL
NUMBER OF
OPERATORS
Installation and set up of the machine
Running with safety protectionsdisabled.
2 e 2a
2
Tape replacement
Stopped by pressing the EMERGENCY
STOP button.
1
1
Replacement of blades
Electric powerdisconnected.
2
1
Replacement of drivebelts
Electric powerdisconnected.
2
1
Ordinary maintenance
Electric powerdisconnected.
2
1
Extraordinary maintenance (mecha-
nical)
Running with safety protectionsdisabled.
3
1
Extraordinary maintenance (electri-
cal)
Running with safety protectionsdisabled.
2a
1
Extraordinarymaintenance(pneuma-
tic)
Stopped by pressing the EMERGENCY
STOP button.
3
1

3-SAFETY
3.7
RESIDUAL HAZARDS
The case sealer SM44 HS has been designed following the EC direc-
tives, and incorporates various safety protections which should never
be removed or disabled.
Notwithstanding the safety precautions conceived by the designers of
the machine, it is essential that the operator and service personnel be
warned that the following uneliminable residual hazardsexis
WARNING! Tape cutting blades.
Never remove thesafety device which covers the blade on the top and
bottom taping units.
Blades are extremely sharp.Any error may cause serious injuries.:
WARNING!: Side flaps fold device guard knobs
Don’t remove the orange plastic guard knobs on the side flaps fold de-
vice ends.
3.8
RECOMMENDATIONSAND MEASURESTOPREVENT OTHER HAZARDS WHICH CANNOT BEELIMINA-
TED
The operator must stay on the working position shown on paragraph 12.1. He must never touch the running
driving belts or put his hands inside anycavity.
The box must be fed by keeping the hands in the rightposition.
The operator must pay attention to the blades during the tapereplacement.
3.9
PERSONAL SAFETY MEASURES
(Safety glasses, safety gloves, safety helmet, safety shoes, air filters, ear muffs).
None is required, except when recommended by the user.
10
February 2016
ENGLISH

3-SAFETY
3.10
PREDICTABLE ACTIONS THAT ARE INCORRECT AND NOT ALLOWED
-
Never try to stop or hold the box while it is being driven by the belts.
Use only the EMERGENCY STOPBUTTON.
Never work without the safety protections.
Neverremoveordisablethesafetydevices.
-
-
- Only authorised personnel should be allowed to carry out the adjustments, repairs or maintenance which re-
quire operation with reduced safety protections. During such operations, access to the machine must be re-
stricted. When the work is finished, the safety protections must immediately bereactivated.
- The cleaning and maintenance operations must be performed after disconnecting the electric power.
- Clean the machine using only dry cloths or light detergents. Do not use solvents, petrochemicals etc.
- Do not modify the machine or any part of it. The manufacturer will not be responsible for anymodifications.
- We advise to apply directly to Siat formodifications.
- Follow carefully the installation instructions of thismanual.
The manufacturer will notbe responsible for damages caused by improper installation.
3.11
TABLE OF WARNINGS, LABELS, PLATES AND DRAWINGS TO BE FOUND ON THE MACHINE
Beforestartinganymaintenance operations theelec-
trical power must bedisconnected.
a
Label code: 3.0.01097.96A
b
Show the sharp knife on the taping head.
Label code:3.0.01028.96A
Tapethreading path for bottom taping unit and posi-
tion of the sharp knife.
c
Label code:3.0.01024.96A
February 2016
11
ENGLISH
SYMBOLS COLOURS
DANGER AND PARTSIN MOVEMENT YELLOW COLOUR
COMPULSORYACTIONS/PROHIBITION RED COLOUR
CONTROLS AND INFORMATION LIGHT BLUECOLOUR

3-SAFETY
Shows the running direction of thebelts.
d
Label code:3.0.01040.96A
Showthe earth wire connection point on the machine
frame.
e
Label code:3.0.01039.96A
Caution!: High voltage
f
Label code: 3.0.01100.96A
g
Tapethreading path for upper taping unit.
Label code:3.0.01023.96A
Compulsory position to lift the machine
ktrucks or other suitable raisingequipment.
with for-
h
Labelcode:SBC0010337
Identificationdataforthemachinemodel,serialnum-
ber andmanufacturer.
i
Label code:S340277700A
12
February 2016
ENGLISH
SBC0010337

4 - PRELIMINARYINFORMATION
4.1
GENERAL DESCRIPTION OF THE MACHINE
The SM44 HS case sealer with side drive belts is designed to seal boxes by applying two tape strips on the
top and bottom flaps simultaneously. No operator isrequired.
The machine adjusts itself automatically to the case size and folds the 4 upper flaps. The introduction of the
cases into the machine is performed by the indexing system AS24. All the operations are managed by a PLC
located in the controls board.
4.2 TECHNICALSPECIFICATIONS
- Production = 850 boxes/hour (average)
- Standard power supply = see plate
- Installed power: 1,2 kW
- Taping units K11 or K12, tape width 50/75 mm
- Machine+control board+AS24 weight=430+70+90kg
- Compressed air = 6 BAR; feeding pipe diameter 10mm
- Belts speed = 30 m/min.
- Infeed conveyor speed: 21 m/min.
- Air consumption: 230 Nl/min
TAPE DIMENSIONS
Suitable adhesive tapes:
PVC
OPP
ADHESIVE PAPER
A = 410 mm max
B = 50/75 mm
C = 76 mm
4.3
PURPOSE OF THE MACHINE
The purpose of this machine is the sealing with adhesive tape of boxes having the dimensions (in millimeters)
shown in the table below:
BOXES DIMENSIONS
CASE WEIGHTS
min.: 2 kg
max.: 30 kg
Warning:Themachinesuppliedwiththestandardelectricsystemisnotdesignedforuseinatmospherewithriskof
deflagration.Insuchconditions themachinemustbeequippedwith anti-deflagration componentsand/orairmotors.
February 2016
13
ENGLISH
SM44 HS
w
h
l
min.
160
140
200
max.
500
500
600
h
l
w
A
C
B

4-PRELIMINARYINFORMATION
4.4
MAIN COMPONENTS
The machine is composed of:
The infeed conveyor is composed of:
n. 1
n. 4
n. 1
n. 1
frame
adjustable legs
electric motor
motorized belt
n. 1
n. 4
n. 2
n. 2
n. 1
n. 2
n. 2
n. 1
n. 2
n. 1
frame
adjustable legs
columns
taping units
top head
side drive belts
electric motors
safety guard
emergency stop button
controls board
For the technical features of the electric parts refer to section15-ENCLOSURES
4.5
OPERATIVE FLOW
The boxes, coming from the filling stations, are centred, gated and fed to the machine by the indexing unit
AS24.
The same indexing unit is equipped with a reading head for the identification of the format of the introduced box
and the position of the following upper forming group correctly by appropriate electro-pneumatic interface de-
vices.
The driving belts transport the box during the different phases, from flaps folding to the following sealing, to the
exit of the same box.
4.6
MACHINE NOISE MEASUREMENT
Acoustic pressure at 1 meter distance from the machine with the tape roll inserted: 73 dB. Acoustic pressure
at a height of 1,6 meter above the machine with the tape roll inserted: 73 dB.
The measurement has been performed by a SPYRI-MICROPHONphonometer..
14
February 2016
ENGLISH

4-PRELIMINARYINFORMATION
4.7
OVERALL DIMENSIONS
February 2016
15
ENGLISH

5-SHIPMENT - HANDLING -STORAGE
5.1
MACHINE TRANSPORTATION AND HANDLING
The machine and the infeed conveyor are shipped in 2 separate pac-
kings, fixed on a wooden pallet. They can be lifted with a normal fork
lift. The standard packing is suitable for surface and air transportation.
Oversea packing on request.
Packing dimensions
SM44HS
l= length: 2880 mm
w= width: 1480 mm
h= height: 2050 mm
Weight: 617 kg
AS24
l: length: 1170 mm
w= width: 980 mm
h= height: 980 mm
Weight: 134 kg
5.2
PACKING FOR OVERSEAS SHIPMENT
(OPTIONAL)
Themachinesshippedbyseafreightarecoveredbyanaluminium/po-
lyester (Vacupol) bag which contains dhydrating salts.
Machine packing
-machine 1
-guards 3
-accessories 4.
Indexing unit packaging.
5.3
STORAGE OF THE PACKED OR UNPACKED MACHINE
In case the machine must stay inactive for a long period, please take the following precautions:
-
-
-
store the machine in a dry and clean place;
if the machine is unpacked it is necessary to protect it from the dust;
do not stack anything on top of the machine;
16
February 2016
ENGLISH
11
3
3
4

6-UNPACKING
6.1
Cut the polypropylene straps.
Use a cutter to remove the part of the carton fixed by the staples
along the entire perimeter of the packing. (Otherwise remove the
staples by using a suitable tool)
After having cut the carton or removed the staples, lift the packing up
in order to free the machine. (2persons)
Move the machine and the infeed conveyor to where they will be lo-
cated.
Cut the stretch film and remove the guard panels and the
accessories box.
Sealing machine brackets removal
Caution: the operations must be accomplished on all the four legs
one at a time.
Remove the screws 1;
Unscrew the nut 2 and remove the bracket;.
Replace and tighten the screws 1;
Acting in similar way on the other legs, in sequence.
February 2016
17
ENGLISH
1
2

6-UNPACKING
To lift the machine up, position the lift forks where there are the labels
on right hand side or front-back sides and remove thepallet.
Machine weight + control board: 430 + 70 kg.
Conveyor brackets removal
Loosen the nuts 1 and remove thebrackets.
To lift the conveyor, position the lift forks where there are the labels
on front or back side and remove thepallet.
Conveyor weight: 90 kg
6.4
PACKING DISPOSAL
The packing of the machine Mod. SM44 HS
is composed of:
-
-
-
-
-
-
-
-
wooden pallet
carton box
wooden supports
steel fixing brackets
polythene foam protection
plastic straps (PP)
clay dehydrating pouches
aluminum/polyester/polythenebag
(only for seafreight shipments)
For the disposal of these materials please follow the provisions of the law in your country.
18
February 2016
ENGLISH
SBC0010337
SBC0010337
Back sdie
Back sdie
Front sdie
Front sdie
RH side
LH side
1
RH side

7-INSTALLATION
7.0.
SAFETY MEASURES
Read carefully chapter 3.
7.1.
ENVIRONMENTAL CONDITIONSREQUIRED
-Temperature min. = 5 °C; max. 40 °C
-Umidity min 30%; max. 80%
-Dust free environment
7.2.
SPACE REQUIRED FOR MACHINEOPERATION AND
MAINTENANCE
Min. distance from the wall: A = 1500 mm; B = 1000 mm;
Min. height:= 2500 mm
7.3
SPARE PARTS AND THREADING TOOL FOR TAPING HEADS
For a detailed description of the tools kit see section13.1.
7.4
MACHINE POSITIONING
Raise the machine with a fork lift positioning the lift forks under the
points where there are thelabels.
7.4.1
WORK HEIGHT ADJUSTMENT
Lift the machine as shown in picture.
Unlock the screws and take the legs out looking for the desired con-
veyor bed height on the graduatedlabel.
Then lock the screws again.
February 2016
19
ENGLISH
SBC0010337
B
A

7-INSTALLATION
7.5
SAFETY GUARDS: INSIDE AND OUTSIDE MACHINE
EMERGENCY STOP PUSH-BUTTON
Position and assemble the inside (A) and outside (B) guard panels
with the upper and bottom brackets and stiffening frofile plates as
shown in the pictures.
7.5.1. INSIDE SAFETY GUARDS
Support brackets (upper and bottom); 2+2 socket head screws each
bracket.
7.6
CONNECTION BETWEEN THE INDEXING UNIT AS24 AND THE
MACHINE SM44 HS
Lift the indexing unit by placing the forks under the points where the
labels are.
7.6.1
Move the indexing unit to the machine and fix it using the screws pre-
viously removed.
7.6.2
Unlock the screws of the legs, move the legs down to the floor and
lock the screws.
20
February 2016
ENGLISH
SBC0010337
A
B
B
Table of contents
Popular Food Saver manuals by other brands

MELAG
MELAG MELAseal 101 Comfortable operating manual
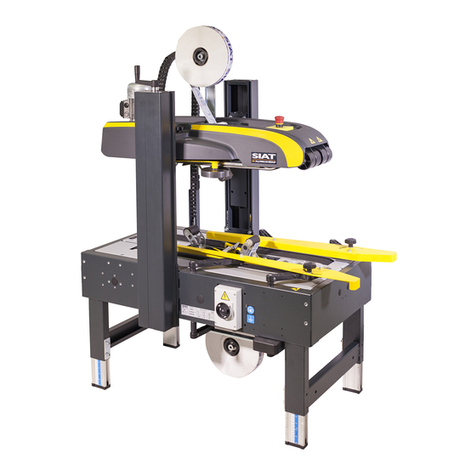
M. J. MAILLIS GROUP
M. J. MAILLIS GROUP SIAT SK20 Operation and maintenance manual

HOFFEN
HOFFEN SU-801 instruction manual

FoodSaver
FoodSaver V2040 series reference guide

FoodSaver
FoodSaver Vac 1050 user manual

miniland
miniland naturRound Series quick start guide