Siemens-Allis LBS Series User manual

TABLE
OF
CONTENTS
Page
Page
ELECTRICAL
Conduit
Cable
Connections
Secondary
Connections
FINAL
INSPECTION
AND
TESTING
4
INTRODUCTION
GENERAL
INFORMATION
.
WARRANTY
GENERAL
DESCRIPTION
.
.
INTERLOCKING
FEATURES
APPLICATION
RECEIVING
Unloading
Shipment
Inspection
Uncrating
Storing
4
1
4
1
4
1
4
2
3
OPERATION
SEQUENCE
OF
OPERATION
—
OPERATOR
SEQUENCE
OF
OPERATION
—
SWITCH
CONTACTS
3
3
5
3
3
5
3
INSTALLATION
DRAWINGS
.
MECHANICAL
Foundation
Erection
.
.
.
MAINTENANCE
PERIODIC
INSPECTION
SWITCH
OPERATION
AND
ADJUSTMENT
.
.
.
7
TOUCH
-
UP
PAINT
.
.
..
REPLACEMENT
PARTS
7
4
4
8
4
8
4
i
The
information
contained
within
is
intended
to
assist
operating
per
-
sonnel
by
providing
information
on
the
general
characteristics
of
equipment
of
this
type
.
It
does
not
relieve
the
user
of
responsibility
to
use
sound
Practices
and
Safety
Procedures
in
the
installation
,
application
,
operation
and
maintenance
of
the
particular
equipment
purchased
.
If
drawings
or
other
supplementary
instructions
for
specific
applica
-
tions
are
forwarded
with
this
manual
or
separately
,
they
take
prece
-
dence
over
any
conflicting
or
incomplete
information
in
this
manual
.
Courtesy of NationalSwitchgear.com

INTRODUCTION
PHASE
BARRIERS
ARC
CHUTES
MAIN
STATIONARY
CONTACTS
^
MAIN
MOVING
CONTACTS
PYRO
-
SHIELD
INSULATORS
QUICK
-
BREAK
BLADE
233115
-
13
Fig
.
1
—
Type
LBS
Load
-
Break
Switch
.
baseplate
.
These
glass
polyester
insulators
are
flame
re
-
tardant
,
track
resistant
and
have
high
impact
strength
.
They
are
securely
bolted
to
the
mounting
plate
and
termi
-
nals
to
prevent
live
parts
from
rotating
.
Phase
separators
are
also
made
of
Pyro
-
Shield
insulation
.
Main
Stationary
Contacts
are
high
-
pressure
,
silver
-
to
-
copper
line
contacts
.
A
large
copper
mass
immediately
adj
-
acent
to
the
contacts
serves
to
conduct
heat
generated
by
momentary
overcurrents
away
from
the
contact
surfaces
.
Main
contacts
are
of
the
knife
-
blade
type
.
In
closing
,
the
blade
engages
with
the
stationary
contacts
ahead
of
the
contacts
inside
the
interrupter
.
This
enables
the
switch
to
close
against
fault
currents
.
Main
Moving
Contacts
are
of
high
conductivity
,
hard
drawn
copper
bars
with
rounded
edges
.
Quick
-
Break
Blades
are
made
of
silver
-
plated
phosphor
bronze
with
silver
tungsten
on
the
interrupter
tip
and
on
the
restraining
contacts
.
Silver
is
used
for
its
high
conduc
-
tivity
and
tungsten
because
of
its
high
melting
point
.
The
quick
-
break
blades
are
pivot
mounted
to
one
side
of
the
main
blades
with
a
stainless
steel
spring
mounted
parallel
to
the
main
blades
.
Arc
Chutes
are
formed
from
material
especially
selected
for
its
arc
extinguishing
properties
.
The
chute
contains
a
pair
of
silver
tungsten
tipped
restraining
contacts
which
engage
the
quick
-
break
blade
when
in
the
closed
position
.
The
necessary
spring
pressure
is
supplied
by
a
pair
of
phosphor
bronze
compression
springs
inside
the
arc
chute
.
GENERAL
INFORMATION
This
instruction
book
is
to
acquaint
the
purchaser
/
user
with
the
Siemens
-
All
is
Type
LBS
Load
-
Break
Switch
.
In
-
stallation
and
maintenance
instructions
are
provided
in
the
appropriate
sections
.
A
spare
parts
list
at
the
end
of
the
book
provides
a
list
of
the
serviceable
parts
.
WARRANTY
For
warranty
coverage
,
see
the
sales
contract
.
The
equip
-
ment
described
has
been
supplied
to
operate
in
a
system
having
a
circuit
capacity
as
specified
by
the
customer
.
If
for
any
reason
the
equipment
should
be
used
in
a
different
system
,
or
if
the
short
circuit
capacity
of
the
system
should
be
increased
,
the
momentary
rating
of
the
switch
,
the
in
-
terrupting
capacity
of
the
fuses
,
and
the
bus
capacity
should
be
checked
.
Failure
on
the
part
of
the
user
to
receive
approval
of
intended
changes
from
the
supplier
may
be
cause
of
voiding
the
warranty
.
GENERAL
DESCRIPTION
—
See
Fig
.
1
.
The
Type
LBS
Load
-
Break
Switch
is
a
manually
-
operated
,
single
-
throw
,
gang
-
operated
disconnect
with
quick
-
break
blades
and
arc
chute
interrupters
.
The
switch
employs
a
quick
-
break
and
make
mechanism
and
a
spring
-
operated
over
-
center
linkage
which
assures
positive
closing
force
and
fast
uniform
interruption
speed
.
Construction
features
of
the
basic
switch
parts
are
:
Pyro
-
Shield
Insulators
provide
switch
clearance
from
the
1
Courtesy of NationalSwitchgear.com

The
manual
,
front
-
mounted
,
operator
smoothly
and
posi
-
tively
provides
interruption
of
load
and
transformer
mag
-
netizing
currents
.
A
mechanical
interlock
prevents
the
switch
door
from
being
opened
when
switch
is
in
closed
position
.
A
safety
glass
window
allows
inspection
of
switch
blade
position
.
When
fuses
are
provided
with
a
600
amp
load
-
break
switch
in
a
single
45
inch
high
compartment
,
the
fuses
are
connected
on
the
load
side
of
the
switch
.
This
enables
per
-
sonnel
to
change
fuses
without
using
a
hot
stick
.
No
fuse
discharge
gases
are
produced
that
could
contaminate
the
switch
or
arc
chutes
.
See
Fig
.
2
.
The
600
amp
load
-
break
switch
is
mounted
in
a
compartment
32
inches
deep
,
36
inches
wide
and
45
inches
high
.
The
1200
amp
load
-
break
switch
occupies
a
com
-
partment
32
inches
deep
,
36
inches
wide
and
90
inches
high
.
Both
the
600
and
1200
amp
load
-
break
switches
are
com
-
patible
with
theSpaceMakerII
high
voltage
controller
with
or
without
bus
.
When
fuses
are
provided
on
the
bottom
of
the
switch
com
-
partment
,
this
feature
restricts
access
to
them
until
the
switch
has
been
opened
to
remove
power
from
them
.
When
Type
LBS
switches
,
mounted
in
upper
compartment
are
used
to
isolate
high
voltage
circuits
in
the
corresponding
lower
compartments
,
mechanical
interlocking
is
provided
so
the
lower
compartment
doors
cannot
be
opened
until
the
switches
in
the
upper
compartments
are
in
the
open
posi
-
tion
.
Key
interlock
systems
are
also
available
for
safety
se
-
quence
interlocking
of
compartment
doors
,
feeder
circuit
breakers
,
isolating
switches
,
other
load
-
break
switches
,
etc
.
Two
key
interlock
units
can
be
mounted
and
used
simultaneously
to
provide
increased
system
flexibility
.
A
key
interlock
mounted
in
the
top
location
on
the
operator
mechanism
permits
the
switch
to
be
locked
in
the
open
position
only
.
A
key
interlock
mounted
in
the
bottom
loca
-
tion
permits
the
switch
to
be
locked
in
either
the
open
or
closed
position
.
CAUTION
INTERLOCKING
FEATURES
Only
one
key
per
interlock
sequence
is
to
be
available
to
operating
personnel
.
The
Type
LBS
load
-
break
switch
operators
are
also
sup
-
plied
with
padlocking
provisions
.
The
load
-
break
switch
compartment
doors
are
mechani
-
cally
interlocked
so
they
cannot
be
opened
until
the
switch
is
in
the
open
position
.
Vd
*
>
»
k
.
4
-
HOl
.
lS
*
0
*
KM
C
W
OR
BOCTS
VfrOtk
.
4
-
MOLCS
FO
*
KHCHOR
BOLTS
COM
D U
I T
SPfcCCIM
TOP
O P
CUSlClt
COM
DU
IT
SPKCl
It
)
TOf
OF
CVJSICCC
32
32
-
7
^
*
4
‘
4
34
4
’
'
i
T
-
33
vS
.
Jr
-
m
-
PRIMW
1
COMDUIT
FPKC
1
L
,
/
i
*
i
»
W
«
MT
COWDu
>
T
IPKC
1
B
N
JiLJL
>
4
COUDlMY
SPKC
«
TOP
VIEW
?
tin
FLOOR
PL
KM
.
.
r
*
a
TOP
N
/
UEMi
/
FLOOR
PLkKl
I
H
IVJS
DUCT
'
MHC
.
M
*
—
r
~
"
F
‘
i
1
M
)
.
‘
li
*
»
i
r
•
r
»
4
-
a
.
$
2
-
CURR
.
TfckWSF
.
IF
SPECIFIC
©
»
4
V
Ml
HI
,
Ml
,
m
WHIN
ruses
Kut
MOT
MC
a
.
-
m
-
1
3
-
1
M
4
.
L
VM
.
-
VT
w
sptcmoDi
rir
'
I
14
KM
.
fl
.
SWITCH
*
r
SPSClFtCD
&
t
t
n
«
c
*
t
"
2
-
POT
.
TRKMSF
.
I F
sreciricb
37
S
1
DC
VII
W
5
4
32
37
-
J
SI
PC
\
/
lCW
FRONT
V
\
EW
600
AMP
1200
AMP
Fig
.
2
—
Type
LBS
Load
-
Break
Switch
Dimensions
.
2
Courtesy of NationalSwitchgear.com

Certain
applications
of
the
Type
LBS
load
-
break
switches
may
result
in
the
main
moving
contacts
as
well
as
the
main
stationary
contacts
being
energized
although
the
switch
is
in
the
open
position
.
This
condition
occurs
when
the
switches
are
used
for
bus
tie
,
multiple
incoming
line
feed
,
reversing
,
and
similar
applications
.
In
such
situations
,
complete
interlocking
protection
is
not
always
possible
;
for
often
the
existing
power
system
must
be
in
-
volved
.
Warning
signs
are
provided
on
compartment
doors
to
indicate
that
main
moving
contacts
or
both
sides
of
the
switch
may
be
energized
when
the
switch
is
in
the
open
position
.
When
such
conditions
occur
,
the
user
is
to
supply
proper
sequence
interlocking
with
existing
isolating
cir
-
cuit
breakers
or
switches
.
RECEIVING
Unloading
Lifting
angles
are
mounted
on
both
the
right
and
the
left
sides
for
safe
easy
handling
.
These
may
be
removed
after
installation
is
complete
.
Shipment
Inspection
As
soon
as
the
load
-
break
switch
is
received
,
carefully
inspect
for
damage
or
shortage
.
Examine
all
shipping
crates
before
uncrating
is
attempted
.
Do
this
to
determine
if
damage
has
occurred
in
transit
.
If
damage
to
the
crating
is
detected
,
make
a
thorough
inspec
-
tion
of
the
contents
.
Check
the
entire
shipment
against
the
packing
list
,
espe
-
cially
when
accessories
are
specified
,
to
be
sure
that
no
items
were
lost
or
omitted
.
NOTE
:
If
any
damage
or
shortage
has
occurred
,
deter
-
mine
the
extent
and
notify
the
carrier
and
your
Siemens
-
Allis
sales
office
immediately
!
Proper
notation
should
be
made
on
the
freight
bill
to
pre
-
vent
any
controversy
when
claim
is
made
.
This
notation
also
facilitates
adjustments
.
Table
1
shows
the
ratings
of
the
Type
LBS
Load
-
Break
Switch
which
are
in
accordance
with
NEMA
,
ASA
and
IEEE
standard
.
SWITCH
TYPE
VOLTAGE
FUSED
UNFUSED
2500
/
2500
/
2300
5000
5000
4160
4800
1200
Continuous
Ampere
Rating
Ampere
Interrupting
Capacity
of
Switch
Fault
Close
Amps
(
Asym
)
Momentary
Current
Amps
Max
.
Transformer
3
Phase
kva
load
KV
BIL
rating
450
450
450
600
600
600
600
1200
600
80.000
80.000
80.000
80.000
80.000
80.000
60
,
000
60
,
000
40.000
40
,
000
1500
2500
3000
60
60 60
60
60
TABLE
1
—
Type
LBS
Load
-
Break
Switch
Ratings
Uncrating
Exercise
care
in
uncrating
equipment
.
Check
all
packing
material
to
insure
that
small
parts
are
not
accidentally
thrown
away
.
Do
not
remove
any
temporary
identification
tags
or
labels
until
the
installation
is
complete
.
APPLICATION
The
manually
-
operated
Type
LBS
Load
-
Break
Switch
in
-
corporates
the
functions
of
a
disconnecting
isolator
switch
and
a
circuit
load
interrupter
.
It
is
available
with
or
with
-
out
fuses
.
When
supplied
with
fuses
,
the
current
limiting
fuses
provide
high
interrupting
capacity
,
short
circuit
pro
-
tection
and
overload
protection
in
case
of
transformer
fuses
.
Storing
If
the
load
-
break
switch
is
not
to
be
erected
immediately
,
it
should
be
stored
in
a
clean
,
dry
location
.
Before
placing
in
storage
,
inspect
and
grease
steel
surfaces
of
gears
,
drive
screws
,
etc
.
,
to
prevent
rusting
.
Protect
mechanism
,
contacts
,
etc
.
,
from
dust
and
grit
with
suitable
covers
.
Space
heaters
should
be
used
to
prevent
damage
from
condensation
.
NOTE
:
Indoor
cubicles
are
neither
weatherproof
nor
dripproof
;
they
should
be
stored
indoors
.
If
indoor
units
must
be
stored
outdoors
,
adequate
covering
must
be
pro
-
vided
.
In
addition
,
a
heat
source
of
approximately
250
watts
output
should
be
placed
inside
each
45
inch
high
compartment
to
prevent
condensation
.
Fused
load
-
break
switch
applications
are
limited
by
the
rating
of
the
fuse
.
Since
the
maximum
continuous
current
rating
of
available
fuses
is
approximately
450
amperes
,
only
the
600
amp
load
-
break
switch
is
fused
.
Typical
applications
are
:
1
.
Incoming
line
isolator
and
interrupter
.
2
.
Bus
tie
.
3
.
Emergency
transfer
.
4
.
Transformer
feeder
.
5
.
Branch
feeder
.
3
Courtesy of NationalSwitchgear.com

INSTALLATION
DRAWINGS
2
.
2
-
500
MCM
per
phase
for
one
600
amp
load
-
break
switch
mounted
in
one
90
inch
high
cubicle
(
either
in
upper
or
lower
compartment
,
the
remaining
compartment
being
blank
)
.
3
.
1
-
500
MCM
per
phase
for
two
high
arrangements
,
in
-
cluding
one
load
-
break
switch
in
a
45
inch
compartment
and
either
a
motor
starter
,
transformer
,
or
second
load
-
break
switch
in
the
other
compartment
.
Should
any
of
these
particular
limitations
be
exceeded
,
a
cable
entry
compartment
will
be
required
.
Refer
to
outline
and
wiring
drawings
for
location
of
termi
-
nals
,
cable
sizes
,
and
connections
.
Before
making
cable
connections
,
consider
phase
rotation
.
When
the
switch
is
feeding
a
transformer
,
phasing
is
traced
from
the
transformer
throat
.
Refer
to
cable
manufacturer
’
s
recommendations
for
detailed
information
.
Outline
drawings
and
wiring
diagrams
are
furnished
in
advance
to
the
customer
.
The
drawings
and
wiring
dia
-
grams
furnished
will
include
any
changes
originated
by
the
customer
during
manufacture
,
and
any
changes
or
correc
-
tions
by
the
supplier
necessary
to
insure
proper
installa
-
tion
and
operation
of
the
equipment
.
When
erecting
and
connecting
this
equipment
,
use
only
the
latest
certified
drawings
and
wiring
diagrams
supplied
.
Preliminary
drawings
may
be
changed
,
and
should
not
be
used
.
MECHANICAL
Foundation
The
load
-
break
switch
cubicles
can
be
mounted
on
a
con
-
crete
pad
or
any
type
of
floor
.
The
use
of
floor
sills
or
grouting
wrork
is
not
necessary
,
however
,
they
must
be
mounted
perfectly
level
and
continuously
supported
.
An
-
chor
bolts
must
be
installed
.
Refer
to
the
outline
drawing
.
Secondary
Connections
Secondary
wiring
,
wrhen
required
,
is
carefully
installed
and
tested
at
the
factory
.
If
special
customer
connections
are
required
,
such
as
spaceheater
connections
to
an
internal
power
source
,
wire
terminal
blocks
are
provided
as
shown
on
the
wiring
diagram
.
Erection
The
load
-
break
switch
cubicle
must
be
mounted
in
a
level
position
.
Install
shims
,
as
required
.
When
only
a
single
unit
is
being
installed
,
it
should
be
securely
anchored
when
properly
set
in
place
.
When
multi
-
ple
units
are
being
installed
,
align
the
front
of
each
unit
with
the
first
and
bolt
the
units
together
before
securely
anchoring
.
If
the
cubicle
is
not
properly
mounted
,
difficulty
may
be
encountered
with
door
swing
.
FINAL
INSPECTION
AND
TESTING
Before
the
equipment
is
placed
in
service
,
a
thorough
in
-
spection
and
test
must
be
made
.
Any
defects
that
are
found
should
be
corrected
immediately
.
The
Type
LBS
Load
-
Break
Switch
is
completely
adjusted
,
tested
,
and
inspected
at
the
factory
before
shipment
.
No
additional
adjustment
should
be
necessary
.
However
,
a
careful
inspection
should
be
made
to
be
certain
that
ship
-
ment
,
unloading
,
uncrating
,
storage
,
or
installation
have
not
resulted
in
damage
or
change
of
adjustment
.
ELECTRICAL
WARNING
Conduit
Incoming
and
outgoing
power
cables
(
and
control
,
if
any
)
may
enter
and
exit
the
load
-
break
switch
cubicles
at
the
top
or
bottom
in
any
combination
required
.
When
cable
entry
is
through
the
bottom
,
conduit
should
be
located
in
the
prescribed
area
as
shown
on
the
floor
plan
of
the
outline
drawing
.
When
cable
entry
is
through
the
top
,
conduit
should
be
located
in
the
prescribed
area
as
shown
on
the
top
view
of
the
outline
drawing
.
From
this
point
to
initial
operation
ensure
that
cir
-
cuits
are
not
energized
.
After
the
switch
is
installed
properly
in
position
and
sec
-
urely
anchored
,
proceed
as
follows
:
1
.
Remove
blocking
and
other
temporary
supports
.
2
.
Check
that
high
voltage
connections
are
properly
tightened
and
insulated
(
if
required
)
.
3
.
Check
incoming
and
outgoing
connections
for
proper
electrical
connections
,
shorts
,
and
undesired
grounds
.
4
.
Check
that
interphase
harriers
are
in
position
.
5
.
Check
that
interlocks
are
functioning
properly
.
Cable
Connections
The
cable
size
limitations
are
as
follows
:
1
.
6
-
500
MCM
per
phase
for
a
1200
amp
load
-
break
switch
.
4
Courtesy of NationalSwitchgear.com

6
.
If
fuses
arc
provided
,
see
that
they
are
properly
positioned
in
the
fuse
clips
with
the
target
facing
the
front
.
Also
check
for
correct
fuse
size
.
7
.
Inspect
complete
load
-
break
switch
assembly
for
loose
nuts
and
bolts
.
8
.
Close
the
switch
to
check
for
proper
operation
and
lubrication
.
During
the
closing
operation
,
observe
that
the
main
moving
contacts
and
quick
-
break
blade
move
freely
and
are
in
line
with
the
mai
n
slat
ionary
contacts
and
arc
chute
respectively
.
Open
and
close
switch
ten
times
to
be
sure
that
switch
is
properly
aligned
(
does
not
bind
)
.
9
.
Megger
test
the
high
voltage
circuit
to
l
>
e
sure
that
all
connections
made
in
the
field
are
properly
insulated
.
10
.
Make
dielectric
test
,
if
possible
,
on
the
high
voltage
circuit
for
one
minute
at
a
voltage
equal
to
2000
volts
plus
2
l
<
t
times
the
rated
voltage
.
CAUTION
Disconnect
all
lightning
arrestors
,
surge
capacitors
,
potential
transformers
,
and
any
other
equipment
that
may
be
damaged
by
the
test
voltage
during
this
test
.
WARNING
Keep
face
and
hands
clear
of
quick
-
acting
blade
.
OPERATION
NOTE
:
initial
position
it
cannot
be
returned
to
that
position
until
the
opening
or
closing
stroke
has
been
completed
.
The
Type
LBS
Load
-
Break
Switch
is
operated
by
the
operator
shown
in
Fig
.
3
.
To
close
or
open
load
-
break
switch
,
proceed
as
follows
:
Once
the
operating
handle
is
moved
from
its
1
.
Remove
any
padlocks
or
unlock
any
key
interlocks
used
.
SEQUENCE
OF
OPERATION
—
OPERATOR
2
.
Grasp
operating
handle
with
left
hand
.
The
operator
is
a
combination
of
a
chain
-
d
ri
ve
operator
and
a
spring
loaded
mechanism
as
shown
in
Fig
.
4
.
3
.
Grasp
knob
with
right
hand
.
To
close
switch
,
puli
knob
and
move
handle
to
a
straight
up
position
.
As
the
handle
is
moved
the
main
moving
contacts
start
to
move
and
crank
compresses
spring
in
operator
assembly
.
When
crank
is
over
center
,
spring
takes
over
and
closes
switch
independent
of
the
speed
of
the
handle
.
Re
-
verse
motion
of
handle
to
open
switch
.
4
.
Pull
knob
and
move
operating
handle
through
complete
stroke
in
one
continuous
motion
.
-
KEY
INTERLOCK
POSITION
PADLOCK
HOLE
SEQUENCE
OF
OPERATION
—
SWITCH
CON
-
TACTS
As
switch
is
closed
,
main
current
carrying
contacts
engage
prior
to
the
quick
-
break
blade
contacts
inside
arc
chute
.
This
reduces
the
possibility
of
damage
or
welding
of
the
quick
-
break
blades
if
switch
is
closed
on
rated
or
fault
currents
.
As
switch
closes
fully
,
the
quick
-
break
blade
passes
between
,
and
is
restrained
by
the
stationary
arcing
contacts
within
the
arc
chute
.
As
closing
is
completed
,
the
current
is
shunted
through
the
main
contacts
with
very
little
passing
through
the
quick
-
break
blade
.
Fig
.
5
shows
the
working
components
of
the
switch
.
See
Fig
.
6
.
As
switch
is
opened
,
main
moving
contact
opens
first
and
quick
-
break
blade
is
held
back
by
the
restraining
contacts
.
When
main
moving
contact
is
at
a
set
distance
from
the
main
stationary
contact
,
the
quick
-
break
blade
is
stopped
from
further
angular
movement
at
the
pivot
point
,
causing
it
to
snap
rapidly
out
through
the
arc
chute
.
The
resulting
arc
is
elongated
and
extinguished
within
the
arc
chute
.
Both
the
main
moving
contact
and
the
quick
-
break
blade
then
move
to
full
open
position
,
easily
visible
through
inspection
window
.
KNOB
KEY
INTERLOCK
POSITION
PADLOCK
HOLE
OPERATING
HANDLE
233143
-
3
Fig
.
3
—
Typical
Operator
.
5
Courtesy of NationalSwitchgear.com

MAINTENANCE
WARNING
In
the
opening
operation
of
the
load
-
break
switch
(
14
,
Fig
.
7
)
,
the
quick
-
break
blades
(
13
)
should
remain
locked
with
stationary
arcing
contacts
(
18
)
in
position
until
stop
pin
(
15
)
of
main
movable
contact
(
16
)
acts
on
quick
-
break
blade
spring
housing
(
17
)
.
Continued
opening
movement
of
the
main
movable
contacts
will
draw
the
quick
-
break
blades
(
13
)
through
their
stationary
arcing
contacts
(
18
)
to
com
-
plete
a
quick
opening
of
the
circuit
due
to
the
spring
(
19
)
action
on
the
quick
-
break
blades
(
13
)
.
The
main
movable
contacts
should
be
opened
approximately
one
inch
before
the
quick
-
break
blades
disengage
.
If
any
of
the
quick
-
break
blades
(
13
)
should
start
to
move
with
the
initial
movement
of
the
main
movable
contact
(
16
)
,
or
if
they
should
start
to
withdraw
from
the
stationary
contacts
(
18
)
before
stop
pin
(
15
)
starts
to
act
on
spring
housing
(
17
)
this
means
that
the
quick
-
break
blades
(
13
)
have
not
penetrated
sufficiently
into
the
stationary
arcing
contacts
(
18
)
.
This
is
rectified
by
lengthening
connecting
rods
(
20
)
through
adjustment
of
eye
bolts
(
31
)
.
If
the
quick
-
break
blades
(
13
)
continue
to
withdraw
from
their
stationary
arcing
contacts
(
18
)
before
stop
pin
(
15
)
has
acted
upon
spring
housing
(
17
)
,
then
check
for
missing
compression
spring
(
22
)
,
on
stationary
arcing
contacts
(
18
)
.
Quick
-
break
blades
must
make
and
break
at
approximately
the
same
time
.
Disconnect
switch
from
all
external
power
sources
before
performing
any
inspection
or
maintenance
op
-
eration
.
PERIODIC
INSPECTION
Thorough
inspection
at
periodic
intervals
is
important
to
satisfactory
operation
.
Conditions
affecting
maintenance
are
weather
and
atmosphere
,
experience
of
operating
per
-
sonnel
,
and
special
operation
requirements
.
The
frequency
of
inspection
and
maintenance
will
,
therefore
,
depend
on
installation
conditions
and
can
be
determined
only
by
ex
-
perience
and
practice
.
It
is
recommended
,
however
,
that
the
following
inspections
be
performed
at
least
once
a
year
or
after
100
operations
of
a
600
amp
switch
or
20
operations
of
a
1200
amp
switch
.
More
frequent
inspection
may
be
necessary
if
local
conditions
require
.
1
.
Inspect
interior
for
dust
and
dirt
accumulation
.
Remove
dust
from
all
parts
.
2
.
Inspect
bus
bars
and
cable
connections
to
see
that
they
are
in
proper
condition
.
If
they
show
signs
of
having
overheated
,
check
for
poor
or
loose
connections
or
loose
connections
or
for
overloads
.
3
.
Check
condition
1
of
main
contacts
,
quick
-
break
blades
and
arc
chute
.
Replace
any
worn
or
damaged
parts
.
4
.
Check
arc
chutes
for
loose
bolts
and
retighten
if
needed
.
Check
fastening
of
switch
shaft
assembly
.
Apply
grease
to
parts
requiring
lubrication
.
5
.
Apply
high
temperature
lubricant
(
silicon
or
molyb
-
denum
based
)
to
contact
component
surfaces
subject
to
abrasion
.
Hydrocarbon
based
grease
may
be
applied
,
very
sparingly
to
bearings
,
linkages
,
sprockets
and
drive
chains
not
directly
associated
with
current
carry
-
ing
components
.
6
.
Examine
and
test
all
safety
interlocks
.
This
equipment
is
designed
to
give
top
performance
when
installed
in
normal
indoor
locations
(
and
in
normal
outdoor
locations
when
so
specified
)
.
When
abnormal
conditions
—
such
as
corrosive
atmospheres
—
are
encountered
,
special
precautions
must
be
taken
to
minimize
these
effects
.
The
quick
-
break
blade
should
he
centered
in
the
slot
of
the
arc
chute
and
have
Vs
in
.
movement
to
the
bottom
of
the
stationary
contact
.
If
hlade
is
not
centered
,
then
loosen
the
two
screws
(
10
)
holding
jaw
contact
and
arc
chute
assembly
(
11
)
to
insulator
(
12
)
.
Close
switch
slowly
,
while
lining
up
arc
chute
(
11
)
with
quick
-
break
blade
(
13
)
.
When
correct
alignment
has
been
achieved
,
tighten
the
two
screws
(
10
)
.
The
entry
and
travel
of
quick
-
break
blade
into
and
through
arc
chute
should
occur
freely
.
Hinge
contact
and
stationary
contact
must
be
in
line
.
Main
moving
contact
must
make
contact
on
all
four
surfaces
of
the
stationary
contact
.
To
check
contact
pressure
of
main
switch
contact
at
hinge
contact
(
23
)
,
slack
off
nut
(
25
)
until
drag
is
sufficient
to
harely
permit
turning
of
the
clamping
bolt
by
hand
,
then
tighten
nut
(
25
)
,
one
turn
.
(
Must
not
exceed
one
turn
.
)
To
check
pressure
at
jaw
contact
,
slack
off
nut
(
26
)
until
drag
is
sufficient
to
barely
permit
turning
of
the
clamping
bolt
by
hand
,
then
tighten
nut
(
26
)
one
turn
.
(
Must
not
exceed
one
turn
.
)
Main
movable
contact
must
make
contact
on
a
%
i
nch
minimum
of
the
contact
surface
of
the
main
stationary
contacts
.
SWITCH
OPERATION
AND
ADJUSTMENT
The
checking
and
adjustment
of
contact
operation
must
be
undertaken
with
the
over
center
spring
disengaged
and
the
incoming
power
de
-
energized
.
The
spring
action
is
disabled
by
removi
ng
the
cotter
pin
and
pin
which
fastens
the
spri
ng
and
clevis
to
the
crank
(
Fig
.
4
)
.
WARNING
Keep
face
and
hand
clear
of
quick
-
hreak
blades
.
7
Courtesy of NationalSwitchgear.com

Fig
.
7
—
Switch
Operation
and
Adjustment
.
ready
for
use
,
is
supplied
with
each
order
for
touching
up
any
scratches
,
etc
.
made
during
installation
.
Inspect
the
surface
and
retouch
where
necessary
.
Paint
is
furnished
in
spray
-
on
,
one
-
pint
cans
.
Space
heaters
,
when
specified
are
controlled
by
thermos
-
tats
mounted
inside
the
cubicle
.
The
thermostats
are
fac
-
tory
set
to
cut
in
and
out
at
a
definite
temperature
.
When
humid
conditions
exist
,
be
sure
to
provide
power
to
these
heaters
well
in
advance
of
energizing
the
equipment
to
insure
that
the
insulation
is
dry
.
QUANTITY
PER
PART
NUMBER
DESCRIPTION
SWITCH
REPLACEMENT
PARTS
3
Stationary
Contact
(
upper
)
Stationary
Contact
(
lower
)
Arc
Chute
Assembly
Moving
Contact
Assembly
600
A
(
Includes
movable
arcing
Contact
)
Operating
Link
Contact
Lubricant
25
-
205
-
109
-
002
25
-
205
-
109
-
004
18
-
375
-
793
-
501
18
-
376
-
028
-
502
The
following
list
of
parts
represents
the
major
components
of
the
load
-
break
switch
subject
to
wear
.
The
number
of
operations
and
the
severity
of
interruption
are
the
factors
to
be
considered
when
determining
the
quantity
of
spare
parts
for
stocking
.
3
3
3
1200
A
Consult
Factory
25
-
105
-
931
-
501
15
-
171
-
370
-
002
3
TOUCH
-
UP
PAINT
3
Matching
paint
,
one
pint
per
three
units
,
thinned
and
AR
8
Courtesy of NationalSwitchgear.com
Other Siemens-Allis Switch manuals
Popular Switch manuals by other brands

Homefibre
Homefibre OMS 126 RR-DL user manual
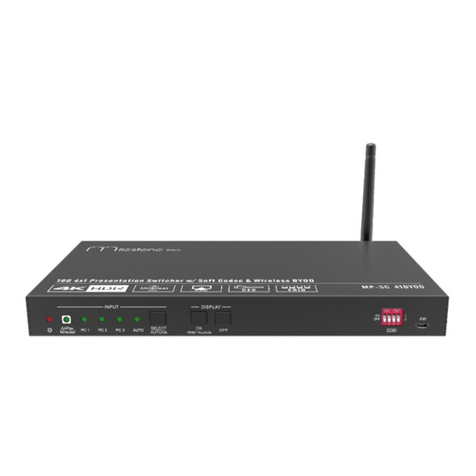
Milestone pro
Milestone pro MP-SC-41BYOD user manual
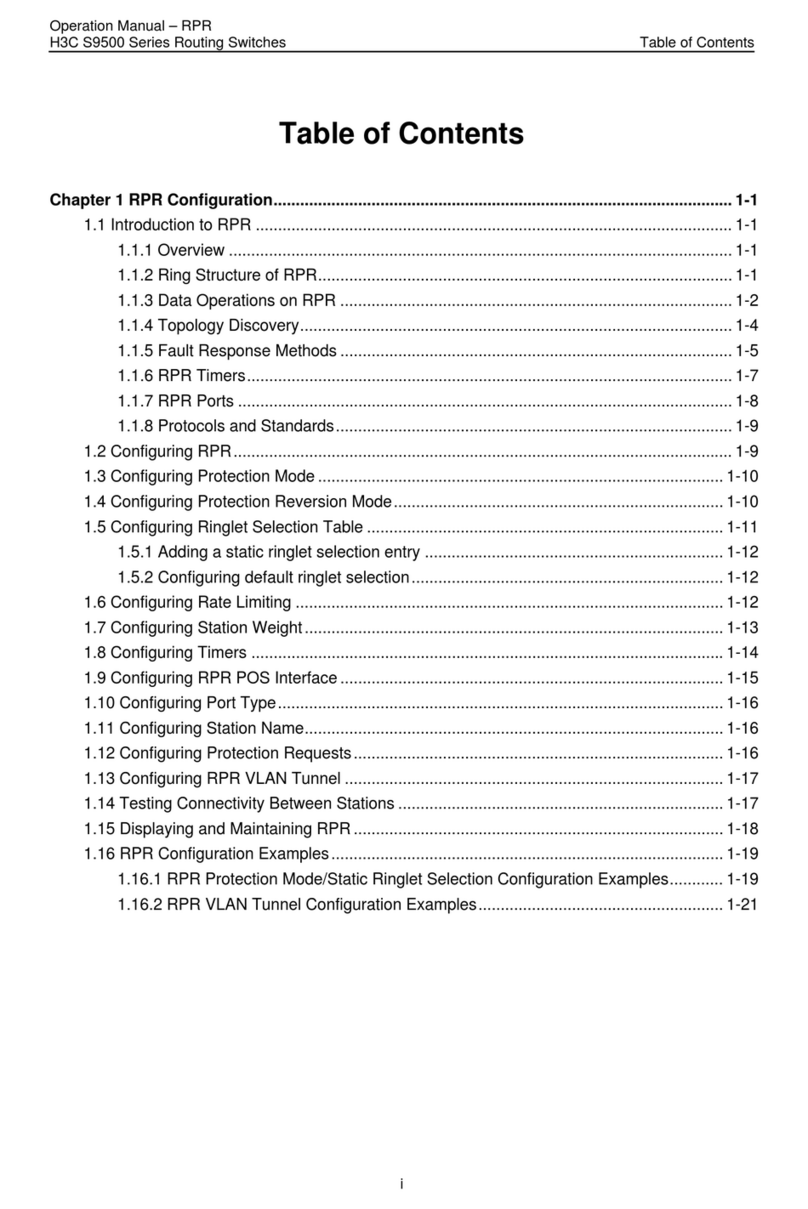
H3C
H3C S9500 Series Operation manual
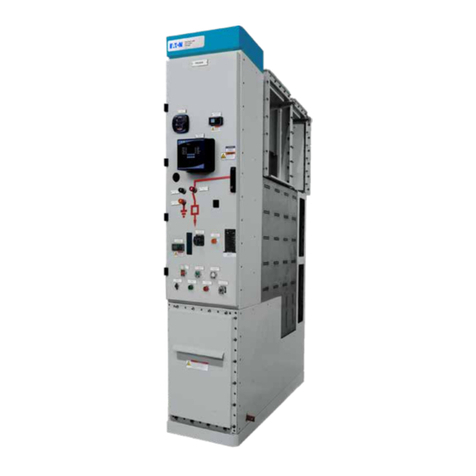
Eaton
Eaton Power Xpert XGIS INSTRUCTIONS FOR THE OPERATION AND MAINTENANCE
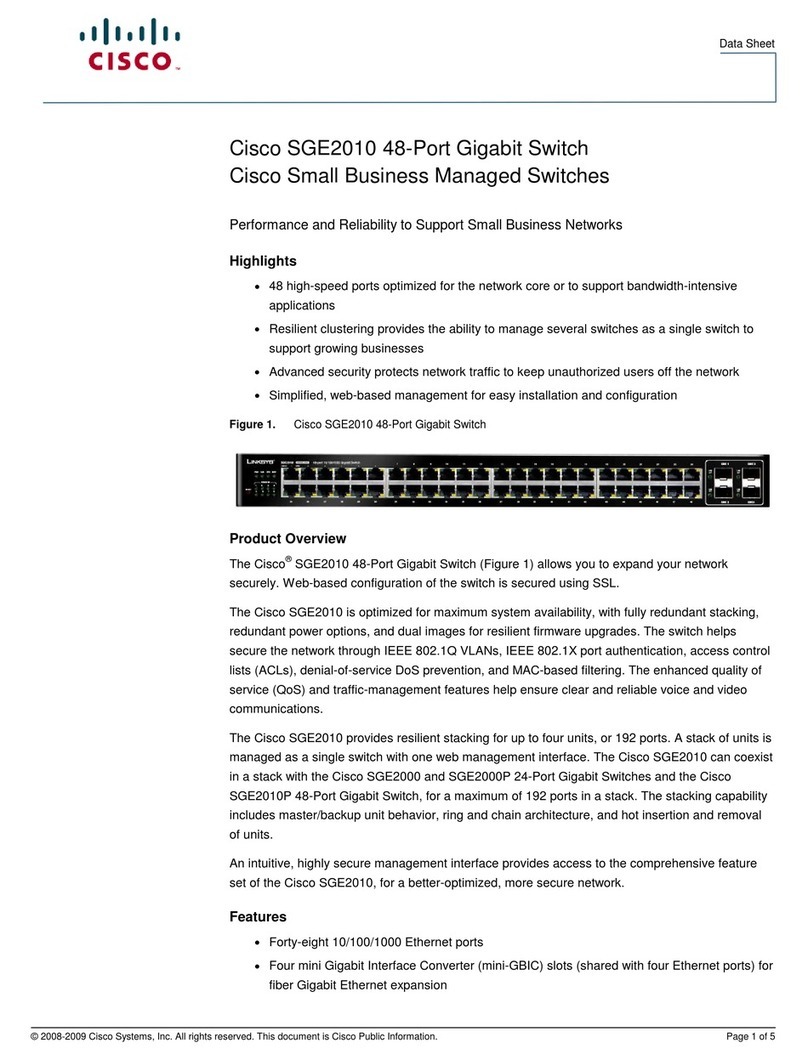
Cisco
Cisco Linksys SGE2010 datasheet
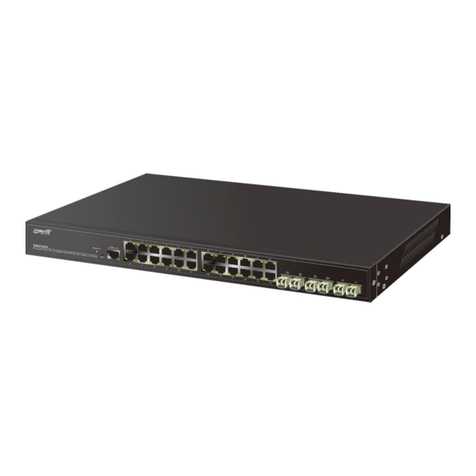
Transition Networks
Transition Networks SM24T6DPA quick start guide