SIGMA SYSTEMS C4 Owner's manual

Artisan Technology Group is your source for quality
new and certied-used/pre-owned equipment
• FAST SHIPPING AND
DELIVERY
• TENS OF THOUSANDS OF
IN-STOCK ITEMS
• EQUIPMENT DEMOS
• HUNDREDS OF
MANUFACTURERS
SUPPORTED
• LEASING/MONTHLY
RENTALS
• ITAR CERTIFIED
SECURE ASSET SOLUTIONS
SERVICE CENTER REPAIRS
Experienced engineers and technicians on staff
at our full-service, in-house repair center
WE BUY USED EQUIPMENT
Sell your excess, underutilized, and idle used equipment
We also offer credit for buy-backs and trade-ins
www.artisantg.com/WeBuyEquipment
REMOTE INSPECTION
Remotely inspect equipment before purchasing with
our interactive website at www.instraview.com
LOOKING FOR MORE INFORMATION?
Visit us on the web at www.artisantg.com for more
information on price quotations, drivers, technical
specications, manuals, and documentation
Contact us: (888) 88-SOURCE | sales@artisantg.com | www.artisantg.com
SM
View
Instra

C4 Manual Rev 7.5.2
SIGMA SYSTEMS
MODELS C4 & CC-3.5
PROGRAMMABLE TEMPERATURE CONTROLLER / INTERFACE
OPERATING & PROGRAMMING MANUAL
Firmware Version 7.5.2
Manual Revision 4
June 3, 1999
SIGMA SYSTEMS CORPORATION
1817 John Towers
San Diego, California 92116 USA
TEL: (619) 258-3700 WWW.SigmaSystems.Com FAX: (619/258-3712)
Artisan Technology Group - Quality Instrumentation ... Guaranteed | (888) 88-SOURCE | www.artisantg.com

C4 Manual Rev 7.5.2
Copyright 1997, 1998
Sigma Systems Corporation
1817 John Towers
El Cajon, California 92020 USA
All rights reserved
The manual may be reproduced, in whole, or in part, solely for the purposes of use
and training for the use, of Sigma Systems equipment, or as required to assist in the
sale of new Sigma Systems equipment. No modification of the content is permitted.
Artisan Technology Group - Quality Instrumentation ... Guaranteed | (888) 88-SOURCE | www.artisantg.com

3
C4 Manual Rev 7.5.2
TABLE OF CONTENTS
1. INTRODUCTION ................................................. 9
1.1 Models C4 & CC-3.5 Explained ................................. 9
1.2 General Description ........................................ 10
1.3 Custom Features / Interchangeability WARNING .................. 11
1.4 Release7.5.2Firmware ..................................... 11
1.5 C4 vs.CC-3Differences(What’sNew)......................... 12
1.5.1 Hardware & Stability Improvements ..................... 12
1.5.2 Hardware Change (EEPROM replaces BBSRAM) .......... 12
1.5.3 Firmware Uploads ................................... 13
1.5.4 ForcedStartfromPROMFirmware ..................... 13
1.5.5 Front Panel Information Display at Startup ................ 13
1.5.6 Temperature Out of Range Shutdown ................... 13
1.5.7 Internal Error Shutdown Conditions ..................... 14
1.5.8 Fahrenheit Temperature Scale Supported ................ 14
1.5.9 Temperature Probe Correction (Calibration) ............... 14
1.5.10 “Bumpless”TemperatureControl ...................... 14
1.5.11 Intelligent 2 Probe Control (Probe Averaging) ............ 15
1.5.12 DefaultSetupParametersRestore..................... 16
1.5.13 Program Mode Step Insert & Delete .................... 16
1.5.14 Program Mode Any Step Points to Step 100 ............. 16
1.5.15 Program Mode Safer Program Clear ................... 16
1.5.16 Program Mode Run Time Program Pre-check ............ 16
1.5.17 Remote Mode EIA-232 Baud Rate Improvement .......... 16
1.5.18 Remote Mode EIA-232 Port Initialization ................ 17
1.5.19 Remote Mode Fault Tolerant Parser .............. 17
1.5.20 Remote Mode System Information Queries .............. 17
1.5.21 Remote Mode Operation Information Queries ............ 17
1.5.22 Remote Mode Setup Parameter Commands ............. 18
1.5.23 Remote Mode IEEE-488 (GPIB) Monitoring .............. 18
1.5.24 Setup Mode Easier Parameter Access .................. 18
2. PHYSICALDESCRIPTION......................................... 19
2.1 Front Panel ............................................... 19
2.1.1 DigitalLEDDisplay.................................. 19
2.1.2 LEDIndicators ..................................... 19
2.1.3 Mode Switch ....................................... 20
2.1.4 Keyboard ......................................... 21
2.2 Rear Panel Connections .................................... 22
3. GENERALOPERATION&ERRORCONDITIONS ...................... 23
3.1StartupDisplays ........................................... 23
3.1.1 Model Number and Firmware Version Number Display ...... 23
3.1.2 Temperature Range Display ........................... 23
3.1.3SerialNumberDisplay................................ 24
Artisan Technology Group - Quality Instrumentation ... Guaranteed | (888) 88-SOURCE | www.artisantg.com

4C4 Manual Rev 7.5.2
3.2 Updating Firmware .........................................24
3.2.1 UpgradingFirmwarebyPROMReplacement ..............25
3.2.2 Upgrading Firmware by Uploading through C4 Serial Port ....25
Making the physical connection for upload ................26
Running the upload software on the PC ..................26
Starting the upload on the C4 ..........................27
3.3 RestoringSetupParameterstoDefaultValues....................27
3.4 Fahrenheit Operation .......................................28
3.5 System Operating (Temperature) Range ........................29
3.6 Probe Out of Range Shutdown ................................29
3.6.1 Effect of Probe Correction on Out of Range Shutdown .......30
3.6.2 Probe Out of Range Shutdown Reported in Error/Status String
.................................................30
3.6.3 Clearing a Probe Out of Range Shutdown ................30
3.7 Internal Error Shutdown Conditions ............................31
3.7.1 Watchdog Timer ....................................31
3.7.2 Memory signature checking ...........................31
3.7.3 Setupparameterintegritychecking......................32
3.8 Software Probe Correction (Calibration) .........................32
3.9 Status and Error Reporting ...................................33
3.10 Fail-safeSystem ..........................................34
4. INTELLIGENT2PROBECONTROL..................................35
4.1 How Intelligent 2 Probe Control functions ........................36
4.2 Preparing for Intelligent 2 Probe Control ........................37
4.3 Using Intelligent 2 Probe Control ..............................38
5. LOCALMODE (BasicOperation) ...................................39
5.1 DisplayingTemperature .....................................39
5.2 Displaying and Changing the Setpoint ..........................40
5.3 ControllingtoaSetpoint .....................................41
5.4 CompressorControl ........................................42
6. PROGRAMMODE ...............................................43
6.1 DescriptionofaProgramStep ................................43
6.1.1 FormatofaProgramStep.............................44
6.1.2 Maximizing Ramp Speed & Other Ramp Considerations .....45
6.2 ClearingProgramMemory(Reinitializingprogramsteps)............46
6.3 DisplayingProgramSteps....................................46
6.4 Entering or Changing a Program Step ..........................47
6.5 InsertProgramStep ........................................47
6.6 DeleteProgramstep........................................48
6.7 Running (Executing) a Program ...............................48
6.7.1 ProgramRunTimeInformation/Considerations ............49
6.7.2 Run Time Pre-read Errors .............................49
No Probe 2 Error ...................................50
Artisan Technology Group - Quality Instrumentation ... Guaranteed | (888) 88-SOURCE | www.artisantg.com

5
C4 Manual Rev 7.5.2
Invalid Loop Count Error ............................. 50
Setpoint Out of Range Error .......................... 50
6.8 Special Commands ........................................ 50
6.8.1 Controlled Program Looping ........................... 51
6.8.2 ExternalCompressorOn ............................. 52
6.8.3 ExternalCompressorOff ............................. 52
6.8.4 Optional Aux/Power Control Port On .................... 52
6.8.5 Optional Aux/Power Control Port Off .................... 52
6.9 CommonProgrammingIssues................................ 53
6.9.1 StepNumbering .................................... 53
6.9.2 Changing Substep Values ............................ 53
6.9.3 ControlPorts....................................... 53
7. REMOTEMODE................................................. 55
7.1 EIA-232 Interface .......................................... 55
7.2 IEEE-488 Interface ......................................... 55
7.3 Command Summary (by functional group) ....................... 56
7.4 SystemInformationQueries.................................. 57
7.4.1 QVQueryFirmwareVersion........................... 57
7.4.2 QNQueryControllerSerialNumber..................... 57
7.4.3 QR Query Controller Temperature Range ................ 58
7.4.4 QS Query Setpoint & Control Probe Number .............. 58
7.4.5 QF,QFA QuerySetupParameterValue ................ 59
7.5 Operation Information Queries & Commands .................... 61
7.5.1 RS, RSA Request Status Byte ......................... 61
7.5.2 RE, REA Request Error Byte .......................... 61
7.5.3 QE,QEA QueryError/StatusString..................... 62
7.5.4 QC QueryLastCommand............................ 64
7.5.5 ES Enable SRQ (Status Request Mode) ................. 64
7.5.6 DS DisabletheSRQ ................................ 64
7.5.7 PT Read Temperature ............................... 65
7.6 Setup Parameter Commands ................................. 66
7.6.1 SC Set Probe Correction ............................. 66
7.6.2 WP SetPIDConstants .............................. 67
7.6.3 BF & BO Blower Off & Blower On Commands ............ 68
7.6.4 SL SetUUTTemperatureLimits ....................... 69
7.6.5 SD SetUUTTemperatureDifferentialLimits.............. 69
7.6.6 UP WriteCurrentParameterstoNVMemory ............. 69
7.7 System Operation Commands ................................ 70
7.7.1 SI SelectImmediateMode............................ 70
7.7.2 SP SelectProgramMode ............................ 70
7.7.3 PN SelectActive(control)Probe ....................... 70
7.7.4 GT,GTF GoToTemperature ......................... 71
7.7.5 RA,RAF RamptoTemperature ....................... 71
7.7.6 DLDelay(DwellInterval) ............................. 72
7.7.7 CO&CF TurntheRefrigerationPortOn................. 72
Artisan Technology Group - Quality Instrumentation ... Guaranteed | (888) 88-SOURCE | www.artisantg.com

6C4 Manual Rev 7.5.2
7.7.8 TO&TF TurnAux/PowerControlPortOn................72
7.7.9 QU Quit Controlling .................................73
7.8 Error and Status Reporting - Overview ..........................74
7.8.1 StatusByte ........................................74
7.8.2 ErrorByte .........................................75
7.8.3 Error/StatusString...................................75
Error/StatusStringBitDefinitions.......................77
8. SETUPMODE...................................................79
8.1 DisplayingtheFieldValues...................................81
8.2 Changing the Value of a Setup Field ............................82
8.3 Two Probe Mode ...........................................82
8.4 Auto-startMode ...........................................82
8.5 BlowerShut-offMode .......................................83
8.6 TemperatureControlTerms(PID)(Setupfields0,10,11,12) ........83
8.7 Software Probe Correction (Calibration) .........................83
Entering probe correction setup data ....................84
9. APPENDIX ......................................................87
9.1 ProgrammingExamples&Notes ..............................87
9.1.1 SimpleLocalProgramExample ........................87
9.1.2 Usingshortcutstoshortenprogramentrytime .............89
9.1.3 Local Program Example Using the Special Commands ......91
9.2 Keeping More than One Program in Memory .....................93
9.3 Sigma Systems C4 Programming Worksheet .....................95
9.4 Sample Command Structure for IEEE-488 GPIB Operation ..........96
9.5 Installation and Use of TTL Outputs and Input ....................98
9.6 Field Calibration of Model C4 Controller .........................99
9.7 Troubleshooting ..........................................101
9.7.1 ServicingConsiderations-ServiceWARNINGS...........101
9.7.2 Beforeyougoanyfurther..............................101
9.7.3 Diagnosing and Solving Hardware Problems .............101
9.7.4 NoiseImmunity ....................................102
9.7.5 Diagnosing and Solving Local Mode Problems ............102
ControllerstartsimmediatelyinLocalMode..............102
9.7.6 Diagnosing and Solving Program Mode Problems .........102
Hard Loops .......................................102
ExplicitProgramEnd ...............................103
Blowers Misbehaving ...............................103
Program hangs on Ramp as Quickly as Possible step ......103
9.7.7 Diagnosing and Solving Remote Mode Problems ..........103
EIA-232 Problems .................................104
GPIB IEEE-488 Problems ...........................104
9.7.8 Firmware Upload Problems ...........................104
StartingtheC4fromPROMbasedfirmware .............105
COMportissues...................................105
Artisan Technology Group - Quality Instrumentation ... Guaranteed | (888) 88-SOURCE | www.artisantg.com

7
C4 Manual Rev 7.5.2
9.8 TemperatureControl (PID)Tuning&Problems.................. 105
Adjusting for changing needs ......................... 106
The Proportional Term .............................. 107
TheIntegralTerm ................................. 107
TheDifferentialTerm............................... 108
9.9 Displayed Messages and Errors Table ......................... 109
9.10 Technical Support, Repairs & Returns ........................ 110
INDEX .......................................................... 111
Artisan Technology Group - Quality Instrumentation ... Guaranteed | (888) 88-SOURCE | www.artisantg.com

8C4 Manual Rev 7.5.2
Artisan Technology Group - Quality Instrumentation ... Guaranteed | (888) 88-SOURCE | www.artisantg.com

9
C4 Manual Rev 7.5.2
1. INTRODUCTION
This manual describes the operating procedures for the Sigma Systems Models C4
& CC-3.5 Controllers, microprocessor based controllers and control communications
interfaces for the family of Sigma Systems temperature chambers and thermal
platforms.
1.1 Models C4 & CC-3.5 Explained
The models C4 & CC-3.5 controllers are successors to the model CC-3.
The model C4 is a completely redesigned controller that uses a
completely different and more modern set of internal components with
a new processor and completely new firmware. Model C4 controllers
are only available as new products from Sigma Systems.
The model CC-3.5 is a hybrid upgrade controller that uses only the
digital circuitry of the model C4. It is made by substituting the C4
digital p.c. board (known within Sigma Systems as the “CPU board”, or
the “A” board) for the CC-3's “A” board. The upgrade from CC-3 to
CC-3.5 also includes a few small modifications to other internal
components. The power supply, power switching, analog, and front
panel components of the CC-3 remain. Model CC-3.5 controllers are only
available as the product of upgrading a CC-3 controller.
From a functional perspective, models C4 & CC-3.5 are identical because all of the
functionality of the controllers is defined by the processor, bus interface components,
and firmware... all of which are integral with the C4 “A” board. The C4 analog and
front panel components that remain unique to the C4 (not included in the CC-3.5
upgrade from CC-3) provide slightly better accuracy and substantially better noise
and static immunity.
For the balance of this manual, the term C4 will mean to
include both the model C4 controller and the model CC-3.5
controller. In the event that there is a difference between
the two models, that difference will be explicitly detailed.
Artisan Technology Group - Quality Instrumentation ... Guaranteed | (888) 88-SOURCE | www.artisantg.com

10 C4 Manual Rev 7.5.2
1.2 General Description
Using the model C4, temperature control is available manually from the front
panel, by use of user entered programs, or via remote control via either a EIA-232
or IEEE-488 GPIB. The controller has a precision temperature reading capability
with a digital read-out. Two temperature probes can be connected to the
controller allowing either probe or both probes to be the control probe(s) while
either probe can be used to take measurements.
Two additional controlled device ports are available. They are intended for on/off
control of a refrigeration compressor and an external load such as a device under
test, or a main chamber or platform power relay. These ports normally are
supplied as TTL level (low voltage) ports but are optionally available with solid
state relays to control line voltage as in the case of units with mechanical
refrigeration. The compressor control port may be toggled from the front panel at
any time in the manual (LOCAL) mode. The compressor is designed to not cycle
on and off with the temperature control function.
The controller operates in each of four modes:
Local
Mode
Single Setpoint control from the front panel. Simple
Start/Stop functionality.
Program
Mode
Programmed control using programs entered, stored, and
run from the front panel. 100 Temperature/Duration
Program steps available. Multiple programs may be stored
and called as needed.
Remote
Mode
Control via EIA-232 or IEEE-488 GPIB. The IEEE-488
interface implementation is a TALKER/LISTENER with
serial poll. Extended addressing and parallel poll
capabilities are not supported. The EIA-232 interface is
fully configurable for baud rate, data bits, stop bits and
parity.
Setup
Mode
Used to define and store operation and environment
variables that control how the C-4 behaves.
Artisan Technology Group - Quality Instrumentation ... Guaranteed | (888) 88-SOURCE | www.artisantg.com

11
C4 Manual Rev 7.5.2
1.3 Custom Features / Interchangeability WARNING
Each Sigma Systems C4 Controller has been custom configured for the chamber or
platform with which it was supplied or for which it was specified. Many units
include special wiring for custom control applications, precision fail-safe additions,
non-standard voltages, external unit power control, etc. Units that may appear
to be identical may be internally quite different. Do not interchange
controllers between controlled devices (chambers and/or platforms)
unless you are certain that the controllers have been identically
constructed.
Failure to heed this warning voids your warranty, may cause unpredictable
controlled device behavior that could cause damage to persons or property, pose a
risk of fire, or cause other problems. If you must move controllers between
controlled devices, please contact the Sigma technical support department for
assistance and advice.
1.4 Release 7.5.2 Firmware
This manual is specifically written to cover the features of Release 7.5.2 firmware
for the Sigma Systems Model C4 controller. The features of this release firmware
are largely backward compatible with all CC-3 and earlier CC-3.5 & C4 firmware.
This release fixes a number of bugs found in the CC-3.5 interim release versions
6.8.6, 6.9.0, and 7.0.0. It also adds a number of new features. See Section 1.5.
Note: This release implements probe temperature correction on a per
probe basis. Interim CC-3.5 releases implemented this feature on a global
basis.
Sigma highly recommends that all users update to the latest firmware release.
Contact Sigma Technical Support. See Section 9.10.
Note: This release is not available as an upload file for serial port firmware
updating of your controller. Due to non-backward compatible change in the way
some data is stored internally, this version must be installed using a PROM
obtained from Sigma Systems.
Artisan Technology Group - Quality Instrumentation ... Guaranteed | (888) 88-SOURCE | www.artisantg.com

12 C4 Manual Rev 7.5.2
1.5 C4 vs. CC-3 Differences (What’s New)
1.5.1 Hardware & Stability Improvements
The new C4 introduces a number of new improvements to make the controller
faster and more reliable than its predecessor.
The C4 has a completely new digital processing board. The new board has a much
faster processor, more memory, and a much faster IEEE-488 GPIB controller.
Interrupts have been completely restructured to improve stability. The multilayer
design is far more tolerant of both static and power line interference. There is
now a watchdog timer to detect system lockups in the event that something does
interfere with the system. The battery backed RAM has been replaced by an
EEPROM. The Vactrol type isolation device in the failsafe circuit has been
replaced. The C4 contains no components that have a time based failure mode.
The new firmware also monitors the state and integrity of internal memory.
Critical system information is stored in multiple places so that minor errors due to
uncontrollable transients or other causes can be repaired on the fly with no
disruption in process control. Likewise, both the front panel display and the GPIB
interface are monitored constantly to assure that their operation has not been
compromised by static discharge or line transient. In the event of a problem,
either device can be reset on the fly to allow operations to continue normally.
System integrity is further enhanced by a series of successive shutdown processes
that monitor the integrity of the data coming from the sensor probes. In the event
that any probe reports a temperature more than 20/C beyond the limits set in the
controller, the controller will shut down all heating and cooling and display a
warning message. Likewise, in the event that a sensor probe reports an extreme
temperature, either hot or cold, the system will assume that a probe has become
compromised by an open or shorted circuit and stop applying heat and cooling,
shut down the system and display an appropriate warning message..
1.5.2 Hardware Change (EEPROM replaces BBSRAM)
All C4 controllers and CC-3.5 controllers converted after January 1998 have the
battery backed static RAM (BBSRAM) replaced with an EEPROM. This change
was implemented to reduce the possibility that the controller will require service.
Although changing the BBSRAM when the battery died (about every 5-12 years)
was a fairly simple matter, the necessity for doing so was found to be a nuisance
as was diagnosing the need for the change. The BBSRAM or EEPROM provides
the non volatile memory where the C4 stores both the setup parameter
information and the user programs.
Artisan Technology Group - Quality Instrumentation ... Guaranteed | (888) 88-SOURCE | www.artisantg.com

13
C4 Manual Rev 7.5.2
1.5.3 Firmware Uploads
When new firmware is available for your C4, you can easily upload it into the
controller using the controller’s serial port. The procedure requires only a diskette
bootable PC and a serial cable and takes only about ten minutes. Firmware
updates, when available, may be obtained on diskette for a fee from Sigma
Systems or for free by download from www.SigmaSystems.Com or
ftp.SigmaSystems.Com. See Section 3.2.2
1.5.4 Forced Start from PROM Firmware
The controller can be started from the original firmware version that is stored in
the PROM. Uploaded versions are stored in flash memory. If a firmware upload
session should go astray somehow, this feature allows the controller to still
operate. See Section 9.7.8.
1.5.5 Front Panel Information Display at Startup
The controller model is displayed at startup - See Section 3.1.1
The firmware version number is displayed at startup - See Section 3.1.1
The operating range may be displayed at startup - See Section 3.1.2
The controller serial number may be displayed - See Section 3.1.3
1.5.6 Temperature Out of Range Shutdown
The controller now stores the operational limits for itself, the controlled device
(Sigma chamber or platform), and the unit under test (UUT). The operating
temperature is checked against these limits, if it is too far outside these limits,.
the system is shutdown with an appropriate error message displayed. See
Section 3.5.
Artisan Technology Group - Quality Instrumentation ... Guaranteed | (888) 88-SOURCE | www.artisantg.com

14 C4 Manual Rev 7.5.2
1.5.7 Internal Error Shutdown Conditions
The C4 monitors system health by keeping track of three additional areas;
they are:
Processor health Tracked by watchdog timer
Memory condition Checked at startup
Setup parameter table Checked continuously as used
Some detected internal errors can be repaired on the fly. If this is possible, the C4
will recover from the error and you will not know the error existed. If, however,
the error is not repairable and the system must be shut down, an error message
will be displayed to help you understand what happened and how to prevent or
cope with it. See Section 3.7.
1.5.8 Fahrenheit Temperature Scale Supported
The controller will now operate in either Celsius /C or Fahrenheit /F mode. See
Section 3.4.
1.5.9 Temperature Probe Correction (Calibration)
The C4 will allow you to enter data via the Setup mode that will correct anomalies
in the temperature readings and control. Such adjustments are sometimes
necessary to optimize accuracy at a particular temperature, or to compensate for
differences between raw probe temperature data and actual temperatures. These
differences can be the result of probe placement, effects of the unit under test on
the temperature data, or other causes. See Section 3.8
1.5.10 “Bumpless” Temperature Control
(Not in this release. Available in next release, without charge. Check the
Sigma Systems FTP or WWW site for downloadable file.)
When the setpoint is changed, the PID control algorithm begins a new “search” for
the right amount of heat and/or cooling to maintain the new setpoint. Normally,
for each new setpoint, the PID routines begin the search anew... behaving as if the
controller was just turned on. The controller will quickly determine that heat or
cooling is called for, and while the chamber or platform advances toward the new
Setpoint, the PID routine adjusts for the response to heat and cool and
methodically settles the chamber or platform in on the new setpoint. For most
setpoint changes, where the new and old setpoints are quite different, this is a
fast, accurate and appropriate method of control.
Artisan Technology Group - Quality Instrumentation ... Guaranteed | (888) 88-SOURCE | www.artisantg.com

15
C4 Manual Rev 7.5.2
However, when the change in the Setpoint is very small, this “start from the
beginning” search routine can search over such a wide range that it will introduce
a “bump” in the platform or chamber temperature that can exceed the amount of
the Setpoint change. The C4 includes an intelligent PID routine that constrains
the search appropriately for the change in Setpoint and thus eliminates the “PID
bump”.
1.5.11 Intelligent 2 Probe Control (Probe Averaging)
(Not in this release. Available in next release, without charge. Check the
Sigma Systems FTP or WWW site for downloadable file.)
Intelligent 2 Probe Control allows the internal temperature of the unit under test
(UUT) to be used in the temperature control algorithm. Both the primary probe,
located in the chamber airstream or platform, and the secondary probe, typically
located inside the UUT, are used to provide a chamber or platform response that
can accelerate testing while respecting the absolute and relative limits of all the
affected components.
Common single probe control strives to maintain the Setpoint temperature in the
chamber airstream, or at the platform surface. If the UUT is massive, or is a poor
thermal conductor, the internal temperature of the UUT can lag the chamber or
platform temperature considerably. Conversely, using a second probe, buried
inside the UUT, to control the temperature may achieve better UUT interior
temperature control, but it will do so at the risk of extreme temperatures in the
chamber or on the platform. If not carefully monitored, second probe only control
can result substantial damage to the chamber or platform and UUT and risk
operator injury.
Intelligent 2 Probe Control is designed to achieve the Setpoint temperature inside
the UUT (probe 2) either as quickly as possible, or at a controlled ramp rate, while
always respecting the limits of the controller, chamber or platform, and UUT. The
user may specify the absolute limits of the exterior of the UUT as well as limit
themal shock by specifying a dynamically changing “sliding scale” maximum
temperature differential for the UUT skin to core temperature. Intelligent 2
Probe Control will maximize speed in achieving internal UUT Setpoint
temperatures, while, at the same time, controlling the thermal stress on the UUT.
An in depth discussion of this feature can be found in Section 4.
1.5.12 Default Setup Parameters Restore
There is a procedure for erasing the current setup parameter table data and
restoring it basic default values. See Section 3.3
Artisan Technology Group - Quality Instrumentation ... Guaranteed | (888) 88-SOURCE | www.artisantg.com

16 C4 Manual Rev 7.5.2
1.5.13 Program Mode Step Insert & Delete
Program steps may now be deleted from or inserted into programs.
See Sections 6.5 & 6.6.
1.5.14 Program Mode Any Step Points to Step 100
Any program step may now point to step 100 (program end) as the next step to
execute.
1.5.15 Program Mode Safer Program Clear
Some deliberate delays have added to the key sequence to completely clear the
program memory to lessen the likelihood that all of program memory will be
erased by accident.
1.5.16 Program Mode Run Time Program Pre-check
When a program is run in Program Mode, the C4 pre-reads the program to look
for run-time errors that it can report to you before starting. By pre-checking your
program, errors are dealt with immediately rather than after the program has
partially completed. The following items are checked:
Calls for probe 2 when only one probe is defined for the system
Calls for setpoints that are not within the system operating range
Loop counter numbers not within the range of 1 to 999 integer
See Section 6.7.2 for a full explanation.
1.5.17 Remote Mode EIA-232 Baud Rate Improvement
EIA-232 communications are now supported at 19,200 and 38,400 bps.
See Section 8.
Artisan Technology Group - Quality Instrumentation ... Guaranteed | (888) 88-SOURCE | www.artisantg.com

17
C4 Manual Rev 7.5.2
1.5.18 Remote Mode EIA-232 Port Initialization
The CC-3 required that to use the EIA-232 port, the port had to be initialized by
switching the mode switch to SETUP before switching to REMOTE mode. The C4
eliminates this requirement. The EIA-232 port is initialized each time the remote
switch is switched to REMOTE mode.
1.5.19 Remote Mode Fault Tolerant Parser
The C4 uses a very fault tolerant parser. Command strings received over either
the EIA-232 or GPIB ports are converted to upper case, extra spaces and tabs are
removed, commas are converted to spaces and line terminators are corrected if
necessary. For this reason, programs that work properly with the C4 and not with
a CC-3, that use only CC-3 commands, probably have syntax errors that the C4
parser corrects. See Section 9.7.7
1.5.20 Remote Mode System Information Queries
QV QueryFirmwareVersion ..................... SeeSection7.4.1
QN QuerySerialNumber ........................ SeeSection7.4.2
QR QueryTemperatureRange .................... SeeSection7.4.3
QS QuerySetpoint&ControlProbeNumber ........ SeeSection7.4.4
QF QuerySetupParameterData(BinaryQuery)..... SeeSection7.4.5
QFA Query Setup Parameter Data (ASCII Query) ..... SeeSection7.4.5
1.5.21 Remote Mode Operation Information Queries
RSA Request Status Byte (ASCII Query) ............. SeeSection7.5.1
REA Request Error Byte (ASCII Query) ............. SeeSection7.5.2
QE QueryError/StatusString(BinaryQuery) ....... SeeSection7.5.3
QEA Query Error/Status String (ASCII Query) ........ SeeSection7.5.3
QC QueryLastCommand........................ SeeSection7.5.4
Artisan Technology Group - Quality Instrumentation ... Guaranteed | (888) 88-SOURCE | www.artisantg.com

18 C4 Manual Rev 7.5.2
1.5.22 Remote Mode Setup Parameter Commands
SC SetCorrection(Calibration)forProbe ........... SeeSection7.6.1
WP SetPIDConstants ........................... SeeSection7.6.2
BF TurnBlowersOff ............................ SeeSection7.6.3
BO TurnBlowersOn ............................ SeeSection7.6.3
SL SetUUTTemperatureLimits .................. SeeSection7.6.4
SD SetUUTTemperatureDifferentialLimits........ SeeSection7.6.5
UP WriteSRAMParameterstoEEPROM ........... SeeSection7.6.6
1.5.23 Remote Mode IEEE-488 (GPIB) Monitoring
The IEEE-488 bus controller is automatically reset if a problem is detected. No
message to the user is generated as no data is typically lost in the process.
1.5.24 Setup Mode Easier Parameter Access
Setup parameters may now be accessed directly by number rather than having to
scroll the entire list. If scrolling is used, there is now a backup key so the list can
be scrolled in either direction. Likewise, for parameters that are chosen from a
list, the list can be scrolled in either direction or the parameters can be keyed in
directly without scrolling the list. See Section 8.1.
Artisan Technology Group - Quality Instrumentation ... Guaranteed | (888) 88-SOURCE | www.artisantg.com

19
C4 Manual Rev 7.5.2
2. PHYSICAL DESCRIPTION
The SIGMA SYSTEMS Model C4 Controller fits into an area 3.5" x 5.5" x 9.5"
long. Connection to the chamber or platform is made through an umbilical cable
with a 12 pin connector that is standard for all SIGMA chambers and thermal
platforms. Controllers destined for use with SIGMA thermal platforms have an
additional 6 pin connector used for the sensor probe circuits. All C4 controllers
have a 3 pin “pigtail” connector at the back of the controller for control of
refrigeration via solid state relay. This feature was optional on CC-3 controllers
and is thus not a consistent feature of CC-3.5 controllers.
2.1 Front Panel
The front panel consists of four major parts: the LED digit display, the LED
indicators, the mode switch and the keypad. The numbers in circles on the front
panel guide the user through the steps for changing the temperature setting in
the LOCAL (manual) mode of operation. See Section 5.
2.1.1 Digital LED Display
The Digital LED Display is a 7 digit display arranged in the following
configuration:
***-****
The display is used for showing probe temperatures, setpoints, program steps,
fail-safe status and setup information.
2.1.2 LED Indicators
Below the Digital LED Display are four discrete LED Indicators. These indicators
are arranged in the following order:
REFER
COOL
HEAT
RUN
REFER indicator lights if power is applied to the refrigeration compressor
control port (not all units are equipped with compressors).
Artisan Technology Group - Quality Instrumentation ... Guaranteed | (888) 88-SOURCE | www.artisantg.com
This manual suits for next models
1
Table of contents
Other SIGMA SYSTEMS Temperature Controllers manuals
Popular Temperature Controllers manuals by other brands
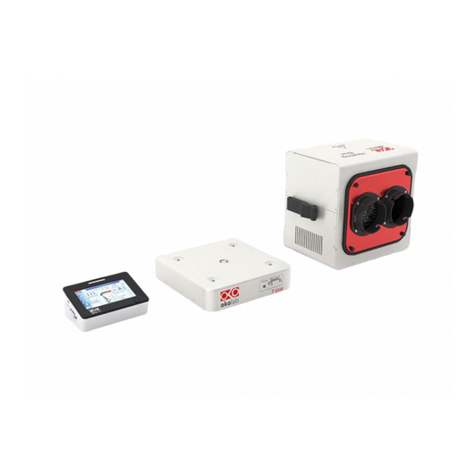
Okolab
Okolab H201-T-UNIT-BL manual
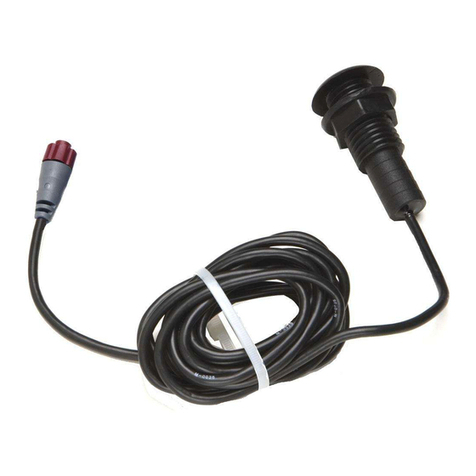
Lowrance
Lowrance EP-80R TH Installation and configuration instructions
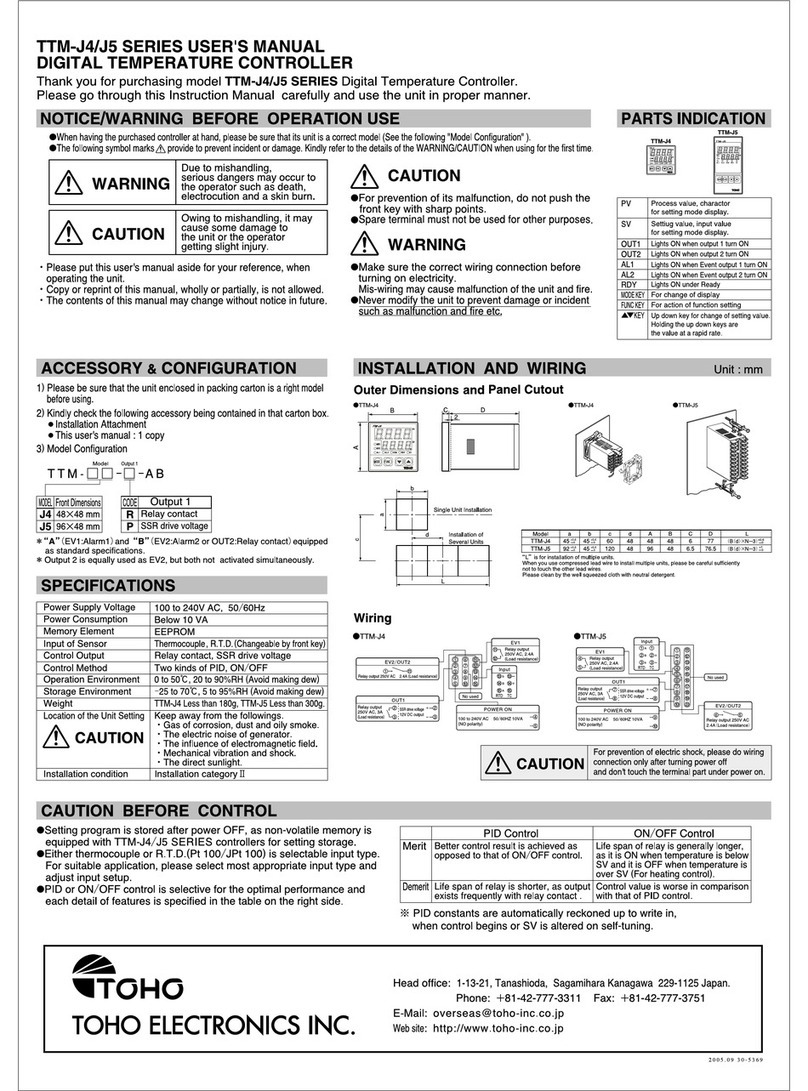
Toho Electronics
Toho Electronics TTM-J4 Series user manual
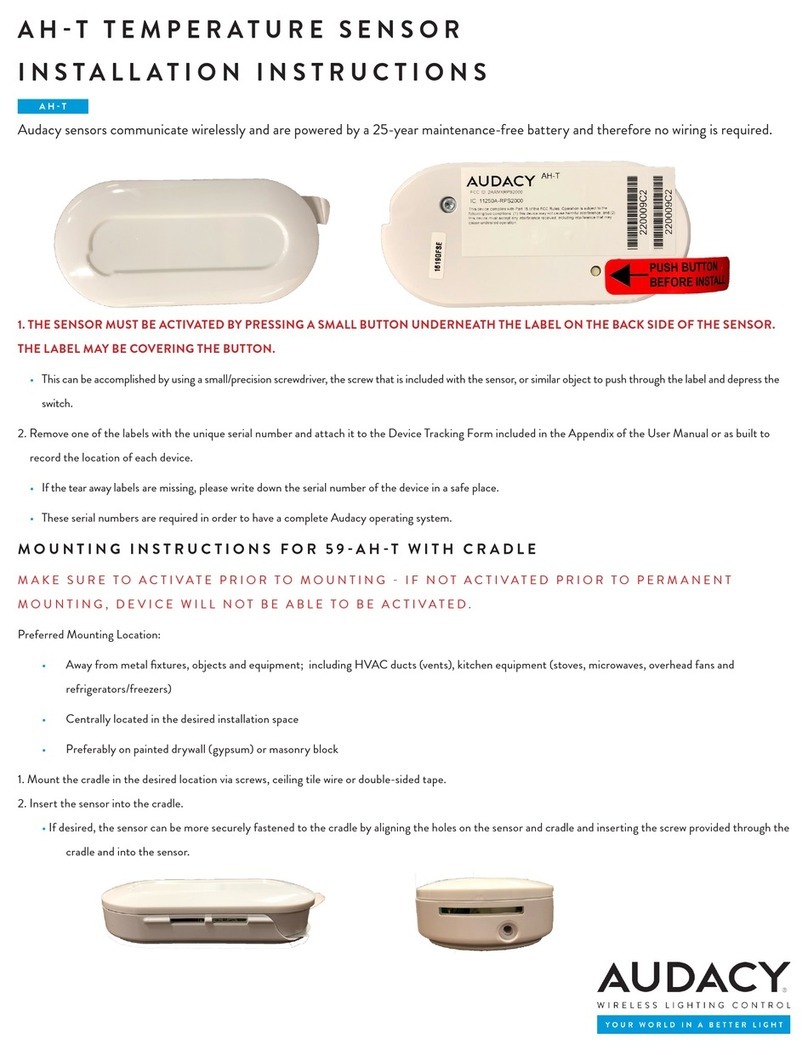
Audacy
Audacy AH-T Series installation instructions
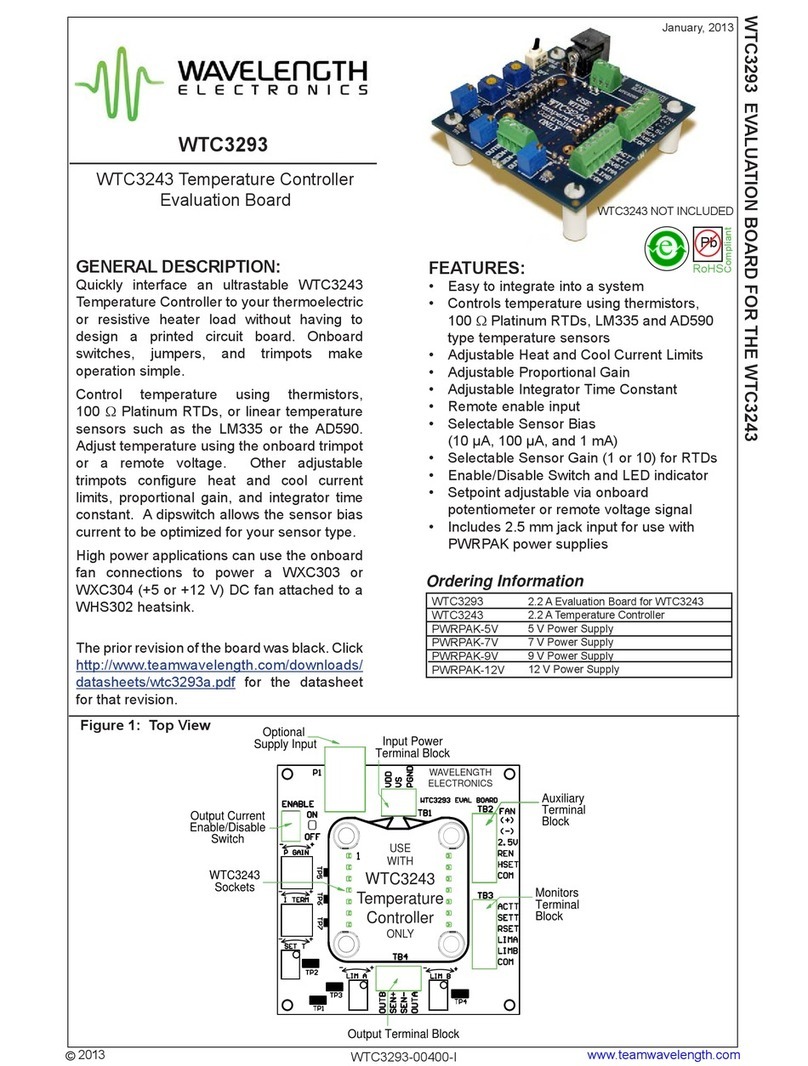
Wavelength Electronics
Wavelength Electronics WTC3293 manual
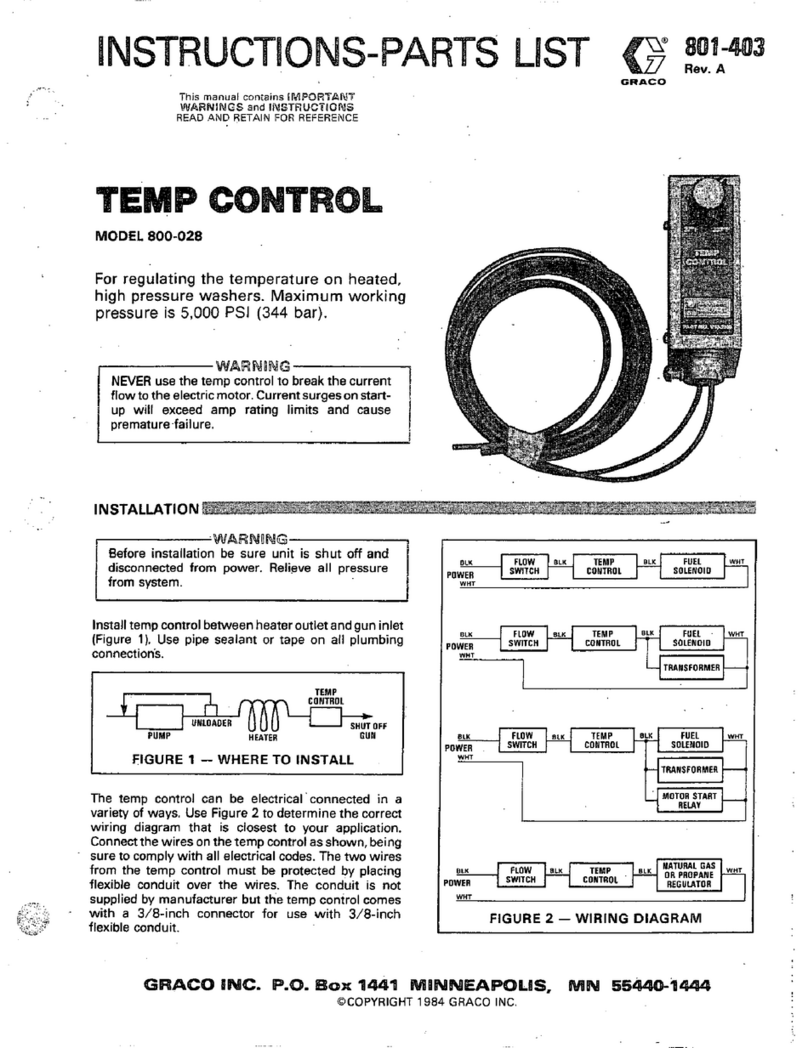
Graco
Graco 800-028 Instructions-parts list
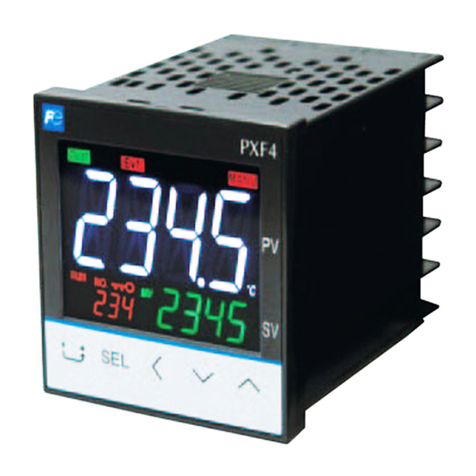
Fuji Electric
Fuji Electric PXF4 instruction manual
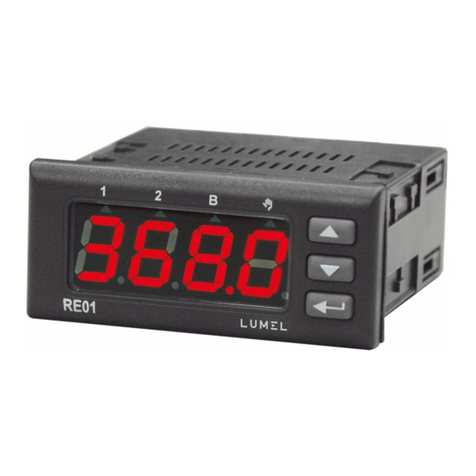
Lumel
Lumel RE01 User Manual & Quick Start
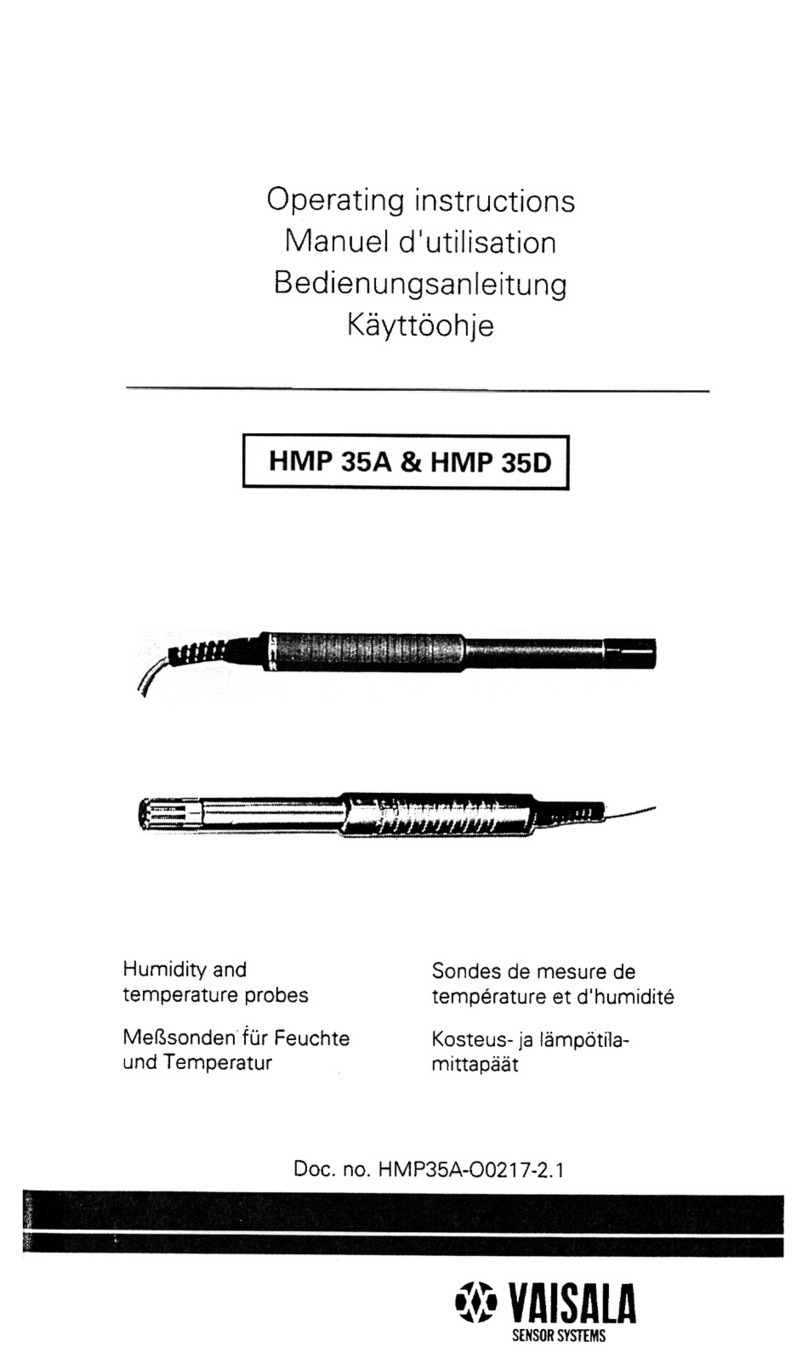
Vaisala
Vaisala HMP 35A operating instructions

Katranji
Katranji XH-M452 user manual
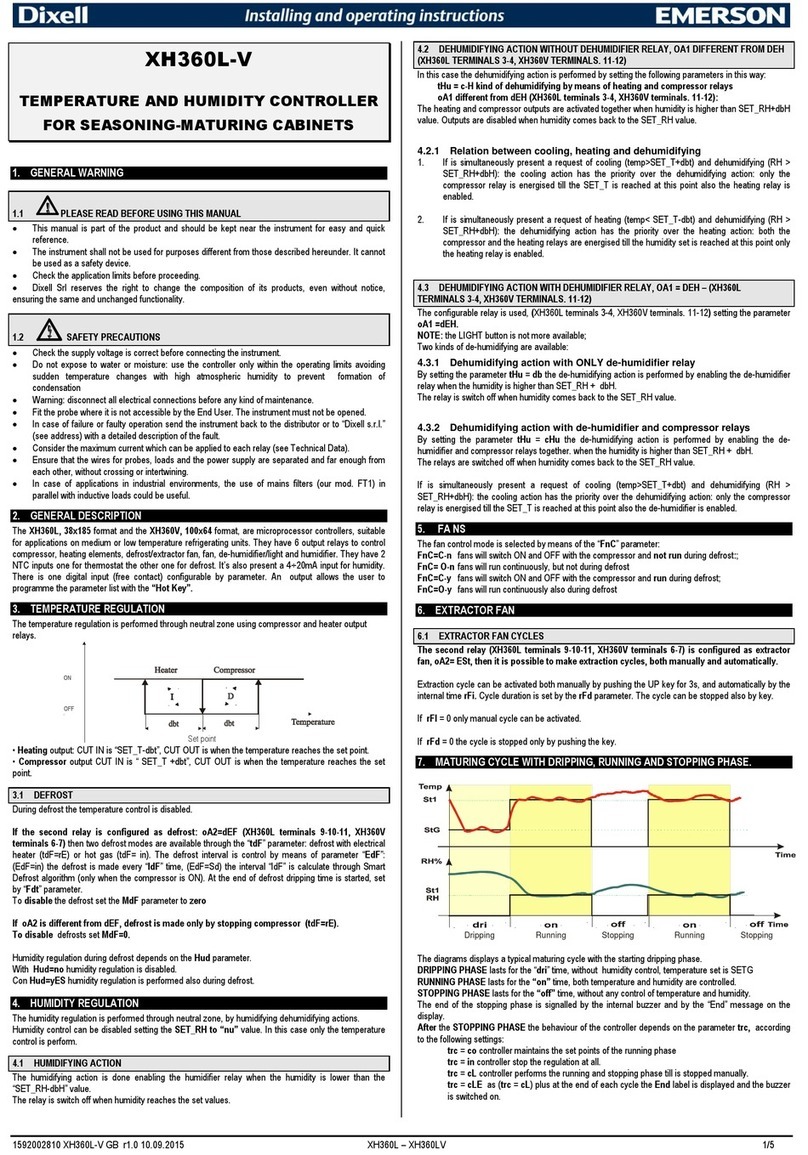
Emerson
Emerson Dixell XH360L-V Installing and operating instructions
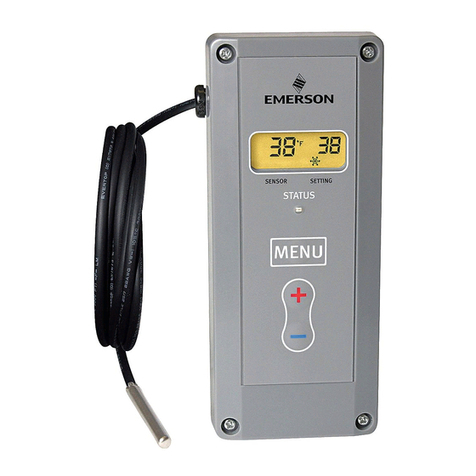
Emerson
Emerson 16E09-101 Installation and operation instructions