SMC Corporation LECSB User manual

PRODUCT NAME
Electric Actuator /Slider Type
《
AC Servo Motor
》
MODEL / Series
LEF Series
Applicable models: LEFS/LEFB
Doc. no. LEF-OM00403
AC Servo Motor Driver
LECS Series
LECSB
(Pulse input)
LECSA
(Pulse input /
Positioning)
LECSC
(CC-Link)
LECSS
(SSCNETⅢ)

- 1 –
Contents
Safety Instructions............................................................................. 2
1. Procedure before operation .......................................................... 4
1.1 Preparation ................................................................................ 4
1.2 Startup ....................................................................................... 6
1.3 Gain tuning................................................................................ 7
2. Slider type LEFS series ................................................................. 8
2.1 Specification.............................................................................. 8
2.2 How to Order ............................................................................. 9
2.3 Construction ........................................................................... 10
3. Slider type LEFB series ............................................................... 12
3.1 Specification............................................................................ 12
3.2 How to Order ........................................................................... 13
3.3 Construction ........................................................................... 14
4. Product Outline ............................................................................ 16
4.1 System construction .............................................................. 16
4.2 Function/Configuration .......................................................... 18
5. Wiring of cables / Common precautions.................................... 19
6. Electric actuators / Common precautions ................................. 20
6.1 Design and selection .............................................................. 20
6.2 Mounting.................................................................................. 21
6.3 Handling .................................................................................. 22
6.4 Operating environment .......................................................... 23
6.5 Maintenance ............................................................................ 24
6.6 Precautions for actuator with lock ........................................ 24
7. Electric actuators / Slider type Common precautions .............. 25
7.1 Design and selection .............................................................. 25
7.2 Handling .................................................................................. 25
7.3 Mounting.................................................................................. 26
7.4 Precaution on maintenance ................................................... 27
7.5 How to detach and attach the dust seal band ...................... 28
7.6 Replacement of belt................................................................ 29
8.Troubleshooting ............................................................................ 30
8.1 Alarms and Warning ............................................................... 30

- 2 -
LEF Series / Slider type
Safety Instructions
These safety instructions are intended to prevent hazardous situations and /or equipment damage.
These instructions indicate the level of potential hazard with the labels of “Caution,” “Warning” or “Danger.”
They are all important notes for safety and must be followed in addition to International Standards (ISO
/IEC), Japan Industrial Standards (JIS)*1) and other safety regulations*2).
*1) ISO 4414: Pneumatic fluid power -- General rules relating to systems
ISO 4413: Hydraulic fluid power -- General rules relating to systems
IEC 60204-1: Safety of machinery -- Electrical equipment of machines (Part 1: General requirements)
ISO 10218-1992: Manipulating industrial robots -- Safety
JIS B 8370: General rules for pneumatic equipment.
JIS B 8361: General rules for hydraulic equipment.
JIS B 9960-1: Safety of machinery – Electrical equipment for machines. (Part 1: General requirements)
JIS B 8433-1993: Manipulating industrial robots - Safety. etc.
*2) Labor Safety and Sanitation Law, etc.
Caution Caution indicates a hazard with a low level of risk which, if not avoided, could result in minor or
moderate injury.
Warning Warning indicates a hazard with a medium level of risk which, if not avoided, could result in
death or serious injury.
Danger Danger indicates a hazard with a high level of risk which, if not avoided, will result in death or
serious injury.
Warning
1. The compatibility of the product is the responsibility of the person who designs the equipment or
decides its specifications.
Since the product specified here is used under various operating conditions, its compatibility with specific
equipment must be decided by the person who designs the equipment or decides its specifications based on
necessary analysis and test results.
The expected performance and safety assurance of the equipment will be the responsibility of the person who
has determined its compatibility with the product.
This person should also continuously review all specifications of the product referring to its latest catalog
information, with a view to giving due consideration to any possibility of equipment failure when configuring the
equipment.
2. Only personnel with appropriate training should operate machinery and equipment.
The product specified here may become unsafe if handled incorrectly.
The assembly, operation and maintenance of machines or equipment including our products must be
performed by an operator who is appropriately trained and experienced.
3. Do not service or attempt to remove product and machinery /equipment until safety is confirmed.
The inspection and maintenance of machinery /equipment should only be performed after measures to
prevent falling or runaway of the driven objects have been confirmed.
When the product is to be removed, confirm that the safety measures as mentioned above are implemented
and the power from any appropriate source is cut, and read and understand the specific product precautions
of all relevant products carefully.
Before machinery /equipment is restarted, take measures to prevent unexpected operation and malfunction.
4. Contact SMC beforehand and take special consideration of safety measures if the product is to
be used in any of the following conditions.
1) Conditions and environments outside of the given specifications, or use outdoors or in a place exposed to
direct sunlight.
2) Installation on equipment in conjunction with atomic energy, railways, air navigation, space, shipping,
vehicles, military, medical treatment, combustion and recreation, or equipment in contact with food and
beverages, emergency stop circuits, clutch and brake circuits in press applications, safety equipment or other
applications unsuitable for the standard specifications described in the product catalog.
3) An application which could have negative effects on people, property, or animals requiring special safety
analysis.
4) Use in an interlock circuit, which requires the provision of double interlock for possible failure by using a
mechanical protective function, and periodical checks to confirm proper operation.

- 3 -
LEF Series / Slider type
Safety Instructions
Caution
The product is provided for use in manufacturing industries.
The product herein described is basically provided for peaceful use in manufacturing industries.
If considering using the product in other industries, consult SMC beforehand and exchange specifications
or a contract if necessary.
If anything is unclear, contact your nearest sales branch.
Limited warranty and Disclaimer /Compliance Requirements
The product used is subject to the following “Limited warranty and Disclaimer” and “Compliance
Requirements”.
Read and accept them before using the product.
Limited warranty and Disclaimer
The warranty period of the product is 1 year in service or 1.5 years after the product is
delivered,whichever is first.*3)
Also, the product may have specified durability, running distance or replacement parts. Please
consult your nearest sales branch.
For any failure or damage reported within the warranty period which is clearly our responsibility, a
replacement product or necessary parts will be provided.
This limited warranty applies only to our product independently, and not to any other damage
incurred due to the failure of the product.
Prior to using SMC products, please read and understand the warranty terms and disclaimers noted
in the specified catalog for the particular products.
*3)
Vacuum pads are excluded from this 1 year warranty.
A vacuum pad is a consumable part, so it is warranted for a year after it is delivered.
Also, even within the warranty period, the wear of a product due to the use of the vacuum pad or failure
due to the deterioration of rubber material are not covered by the limited warranty.
Compliance Requirements
When the product is exported, strictly follow the laws required by the Ministry of Economy, Trade and
Industry (Foreign Exchange and Foreign Trade Control Law).

- 4 -
1. Procedure before operation
1.1 Preparation
(1) Items to be prepared
Please check on the label, and the quantity of accessories, to confirm that it is the product that was
ordered.
Table 1. Componets
No. Part name Qty
(1) Electric Actuator / LEF Series 1
(2) Driver / LECS Series 1(in case with driver)
(3) Motor cable
(4)
Encoder cable
(5) Lock cable
Pre-installed (1)
(in case with cable)
(6) I/O Connector 1(in case with I/O connector)
LECSA(Pulse input / Positioning)
(2) Drive
r
(
3
)
Motor cable
(4) Encoder cable
(1) Electric Actuator
DC24V
(5) Lock cable
(2) Drive
r
(
3
)
Motor cable
(4) Encoder cable
(1) Electric Actuato
r
(5) Lock cable
LECSB(Pulse input)
DC24V
Host controller,
etc
(6) I/O Connector
Host controller,
etc
(6) I/O Connector

- 5 -
LECSC(CC-Link)
(2) Drive
r
(
3
)
Motor cable
(4) Encoder cable
(1) Electric Actuato
r
DC24V
(5) Lock cable
(2) Drive
r
(
3
)
Motor cable
(4) Encode
r
cable
(1) Electric Actuato
r
(5) Lock cable
LECSS(SSCNET III)
DC24V
Host controller,
etc
(6) I/O Connector
Host controller,
etc
(6) I/O Connector

- 6 -
1.2 Startup
When switching the power on for the first time, follow the startup procedure below.
The setting of the filter parameter might become necessary for LEFB25S, and confirm paragraph 7.6,
please.
Refer to the “Driver operation manual” for wiring method and detailed procedure.
1)CC-Link cable (LECSC), SSCNETIII cable (LECSS)
2)When using test operation mode (JOG operation), the LECSC and LECSS need the
MR-Configurator.
Wirin
g
check
Surrounding
environment check
Power-on of the
controlled circuit power
I/O signal wiring and
cables check
during power-on
Parameter setting
Power-on of the main
circuit power supply
Test operation
(JOG operation)
Actual operation
Stop
Confirm that the cables to the driver and the actuator are
connected correctly.
Check the surrounding environment (cable routing and
impurity such as wire off cuts or metallic dust) of the driver
and the servo motor.
Follow the procedure shown in the "Driver Operation
Manual" to supply power to the product.
Check the wiring of the input and output signals and
cables1) according to the procedure shown in the "Driver
Operation Manual".
Set the parameters as necessary, such as selecting the
control mode and each control value.
Follow the procedure shown in the "Driver Operation
Manual" to supply power to the product.
Operation with a vibration might be done according to the
condition. In that case, adjust gain. (Refer to section 1.3 &
7.6)
Gain tuning
Check if the cables to the driver and actuator are
connected correctly.
Stop command to stop the operation.
- - -
- - -
- - -
- - -
- - -
- - -
- - -
- - -
- - -
- - -
Use the test operation mode (JOG operation) at the
slowest speed and check whether the servo motor
rotates.2)

- 7 -
1.3 Gain tuning
Here are the steps for basic gain tuning.
Refer to the “Driver operation manual” for details and for tuning methods other than shown below.
●For LECSA (Pulse input / Positioning)
A. Adaptive filter II
Set filter parameter In LEFB25S2S. Refer the setting method of paragraph 7.6 driver's gain filter
parameter value to the setting method of filter parameter value.
B. One-touch tuning
During motor driving, push “AUTO” button on the front of the driver for three seconds.
When display panel becomes “ ”, push “AUTO” button again.
⇒The gain (including filter, etc) is adjusted automatically.
When the error occurs, refer to the “Driver operation manual”.
C. Auto tuning (Mode1)
Do this operation, if you are not satisfied with the result of “One-touch tuning”.
Set parameter No.PA08 “001”. Afterwards, do 1 and 2 alternately.
1. Reduce value of parameter No.PA09 to be less than present value.
2. Operate and ascertain the situation.
⇒The gain is adjusted automatically.
●For LECSB (Pulse input), LECSC (CC-Link), LECSS(SSCNETIII)
A. Auto tuning (Mode1)
Set parameter No.PA08 “0001”. Afterwards, do 1 and 2 alternately.
1. Reduce value of parameter No.PA09 to be less than present value.
2. Operate and ascertain the situation.
⇒The gain is adjusted automatically.
B. Auto tuning (Mode2)
Do this operation, if you are not satisfied with the result of “Auto tuning(Mode1)”.
Set parameter No.PA08 “0002”. Afterwards, do 1 and 2 alternately.
1. Reduce value of parameter No.PA09 to be less than present value.
2. Operate and ascertain the situation.
⇒The gain is adjusted automatically.
C. Adaptive filter II
Set parameter No.PB01 “0001” and drive the motor.
⇒The filter is adjusted automatically.
1)The auto tuning mode 1 may not be performed properly if the following conditions are not satisfied.
・Time to reach 2,000rpm is the acceleration/deceleration time constant of 5[s] or less.
・Speed is 150rpm or higher.
・Load to motor inertia is 100 times or less.
・The acceleration/deceleration is 10% or more of the rated torque.
2)In LECSA, load moment of inertia ratio doesn't become a fit but because the auto-tuning mode doesn't
operate when driving in low speed, operation might become unstable.
Please set increasing the speed until the auto-tuning mode operates or load moment of inertia ratio to a
proper value (About 50 times) manually. Whether to lighten the load in that case
3)Please set load moment of inertia ratio to about 50 times after it sets it to auto-tuning Mode 2 when you
drive in low speed in LECSB, LECSC, and LECSS (state that the auto-tuning mode doesn't operate).

- 8 -
2. Slider type LEFS series
2.1 Specification
LEFS25,32,40 AC servo motor (100W / 200W/400W/)
Model LEF25S* LEF32S* LEF40S*
Stroke [mm] Note 1) 100,200,300,(400),
500,(600) 100,200,300,(400),
500,(600),(700),(800)
200, 300, (400), 500,
(600),(700), 800, (900),
(1000)
Horizontal
Note 2) 20 20 40 45 50 60
Work load
[kg] Vertical 8 15 10 20 15 30
to 400
900 450
401 to 500
720 360
1000 500
501 to 600
540 270 800 400
1000 500
601 to 700
- - 620 310 940 470
701 to 800
- - 500 250 760 380
801 to 900
- - - - 620 310
Maximum
Speed
Note3)
[mm/s]
Range
of
stroke
901 to 1000
- - - - 520 260
Acceleration/deceleration [mm/s
2
]
5,000
Positioning repeatability [mm]
±0.02
Lead [mm] 12 6 16 8 20 10
Impact resistance/vibration
Resistance [m/s2]Note 4) 50 / 20
Drive method Ball screw
Guide type Liner guide
Operating temperature range [
℃
]
5 to 40
Actuator specification
Operating humidity range [%RH]
90 or less (No condensation)
Motor output/size 100W / ☐40 200W/☐60 400W/☐60
Type of Motor AC servo motor (100/200VAC)
Electric
s
p
ecification
Encoder
[Type of Motor: S2,S3,S4] : Incremental 17bit encoder
(Resolution: 131072 p/rev)
[Type of Motor: S6,S7,S8] : Absolute 18bit encoder
(Resolution: 262144 p/rev)
Type Note 5) No excitation operating type
Holding force [N] 131 255 197 385 330 660
Power consumption [W] at 20℃Note 6)
6.3 7.9 7.9
Lock
s
p
ecification
Rated voltage [VDC] 24 0
-10%
Note 1) The middle stroke other than the above are produced upon receipt of order.
Note 2) The maximum value of the horizontal workload. (An external guide is necessary).
The actual workload will depend on the type of external guide.
Note 3) The allowable speed changes by the stroke.
Note 4) Impact resistance:
No malfunction occurred when the actuator was tested with a drop tester in both an axial direction and perpendicular direction
to the lead screw. (The test was performed with the actuator in the initial state.)
Vibration resistance:
No malfunction occurred in a test ranging between 45 to 2000 Hz, when the actuator was tested in both an axial direction
and a perpendicular direction to the lead screw. (The test was performed with the actuator in the initial state.)
Note 5) Only when the motor option, "with lock", is selected.
Note 6) For an actuator with lock, add the power consumption for the lock.
Product Weight
Model LEFS 25S LEFS32S
Stroke [mm]
100 200 300 (400) 500 (600) 100 200 300 (400) 500 (600) (700) (800)
S2/S3
2.14 2.42 2.7 2.98 3.26 3.54 3.55 3.95 4.35 4.75 5.15 5.55 5.95 6.35
Weight
(kg)
Type of
motor
S6/S7
2.20 2.48 2.78 3.04 3.30 3.60 3.49 3.89 4.29 4.69 5.09 5.49 5.89 6.29
Model LEFS40S
Stroke[mm]
200 300 (400) 500 (600) (700) 800 (900) (1000)
S4
6.15 6.71 7.27 7.83 8.39 8.95 9.51 10.07 10.63
Weight
(kg)
Type of
motor
S8
6.25 6.81 7.37 7.93 8.49 9.05 9.61 10.17 10.73
S2/S3/S4
S2:0.2 / S3:0.4 / S4:0.4
Additional
weight for
lock(kg)
Type of
motor
S6/S7/S8
S6:0.3 / S7:0.7 / S8:0.7

- 9 -
2.2 How to Order
<Ball screw drive>

- 10 -
2.3 Construction
LEFS□S□S <Ball screw drive> In-line mouting type
Parts list

- 11 -
LEFS□R/LS□S <Ball screw drive> Right / Left side parallel type
Parts list
No. Description Material Note
1 Body Aluminum alloy Anodized
2 Rall guide -
3 Ball screw (shaft) Alloy steel
4 Ball screw nut Resin/Alloy steel
5 Table Aluminum alloy Anodized
6 Blanking plate Aluminum alloy Anodized
7 Seal band stopper Synthetic resin
8 Housing A Aluminum die-casted Coating
9 Housing B Aluminum die-casted Coating
10 Bearing stopper Aluminum alloy
11 Return plate Aluminum alloy
12 Pulley Aluminum alloy
13 Pulley Aluminum alloy
14 Blet -
No. Description Material Note
15 Cover plate Aluminum alloy Anodized
16 Table spacer Aluminum alloy Only LEFS32
17 Motor -
18 Motor adaptor Aluminum alloy Anodized
19 Band stopper Stainless steel
20 Dust seal band Stainless steel
21 Bearing -
22 Bearing -

- 12 -
3. Slider type LEFB series
3.1 Specification
LEFB25,32,40 AC servo motor (100W / 200W/400W/)
Model LEFB25S* LEFB32S* LEFB40S*
Stroke [mm] Note 1)
300,400,500,600,
700,800,900,1000,
(1100),1200,
(1300,1400),
1500,(1600,1700),
(1800,1900),2000
300,400,500,600,
700,800,900,1000,
(1100),1200,(1300,1400),
1500,(1600,1700),
(1800,1900),2000,2500
300,400,500,600,
700,800,900,1000,
(1100),1200,(1300,1400),
1500,(1600,1700),
(1800,1900),2000
2500,3000
Work load
[kg]
Horizontal
Note 2) 5 15 25
MaximumSpeed
Note3)[mm/s]
2,000 2,000 2,000
Acceleration/deceleration [mm/s
2
]
20,000Note3)
Positioning repeatability [mm]
±0.02
Lead [mm] 54 54 54
Impact resistance/vibration
Resistance [m/s2]Note 4) 50 / 20
Drive method Belt
Guide type Liner guide
Operating temperature range [
℃
]
5 to 40
Actuator specification
Operating humidity range [%RH]
90 or less (No condensation)
Motor output/size 100W / ☐40 200W/☐60 400W/☐60
Type of Motor AC servo motor (100/200VAC)
Electric
s
p
ecification
Encoder
[Type of Motor: S2,S3,S4] : Incremental 17bit encoder
(Resolution: 131072 p/rev)
[Type of Motor: S6,S7,S8] : Absolute 18bit encoder
(Resolution: 262144 p/rev)
Type Note 5) No excitation operating type
Holding force [N] 27 54 110
Power consumption [W] at 20℃Note 6)
6.3 7.9 7.9
Lock
s
p
ecification
Rated voltage [VDC] 24 0
-10%
Note 1) The middle stroke other than the above are produced upon receipt of order.
Note 2) The maximum value of the horizontal workload. (An external guide is necessary).
The actual workload will depend on the type of external guide.
Note 3) The allowable speed changes by the stroke.
Note 4) Impact resistance:
No malfunction occurred when the actuator was tested with a drop tester in both an axial direction and perpendicular direction
to the lead screw. (The test was performed with the actuator in the initial state.)
Vibration resistance:
No malfunction occurred in a test ranging between 45 to 2000 Hz, when the actuator was tested in both an axial direction
and a perpendicular direction to the lead screw. (The test was performed with the actuator in the initial state.)
Note 5) Only when the motor option, "with lock", is selected.
Note 6) For an actuator with lock, add the power consumption for the lock.
Product Weight
Model LEFB25S*
Stroke [mm] 300 400 500 600 700 800 900 1000 (1100) 1200 (1300) (1400) 1500 (1600) (1700) (1800) (1900) 2000
S2 3 3.25 3.5 3.75 4 4.25 4.5 4.75 5 5.25 5.5 5.75 6 6.25 6.5 6.75 7 7.25
Weight
(kg) S6 3.06 3.31 3.56 3.81 4.06 4.31 4.56 4.81 5.06 5.31 5.56 5.81 6.06 6.31 6.56 6.81 7.06 7.31
Additional weight for
lock(kg)
0.35
Model LEFB32S*
Stroke [mm] 300 400 500 600 700 800 900 1000 (1100) 1200 (1300) (1400) 1500 (1600) (1700) (1800) (1900) 2000 2500
S3 4.9 5.25 5.6 5.95 6.3 6.65 7 7.35 7.7 8.05 8.4 8.75 9.1 9.45 9.8 10.15 10.5 10.85 12.6
Weight
(kg) S7 4.84 5.19 5.54 5.81 6.24 6.59 6.94 7.29 7.64 7.99 8.34 8.69 9.04 9.39 9.74 10.09 10.44 10.79 12.54
Additional weight for
lock(kg)
0.75
Model LEFB40S*
Stroke [mm] 300 400 500 600 700 800 900 1000 (1100) 1200 (1300) (1400) 1500 (1600) (1700) (1800) (1900) 2000 2500 3000
S4 7.1 7.55 8 8.45 8.9 9.35 9.8 10.25 10.7 11.15 11.6 12.05 12.5 12.95 13.4 13.85 14.3 14.75 17 19.25
Weight
(kg) S8 7.2 7.65 8.1 8.55 9 9.45 9.9 10.35 10.8 11.25 11.7 12.15 12.6 13.05 13.5 13.95 14.4 14.85 17.1 19.35
Additional weight for
lock(kg)
0.7

- 13 -
3.2 How to Order
<Belt drive>

- 14 -
3.3 Construction
LEFB25S□S <Belt drive (25)>
Parts list

- 15 -
LEFB32/40S□S <Belt drive (32/40)>
Parts list

- 16 -
4. Product Outline
4.1 System construction
Incremental Encoder
(Pulse input / Pisitioning)
Absolute Encoder
(Pulse input)
Prepared by user
Prepared by user
Prepared by user
Prepared by user
Prepared by user
Power supply
Control circuit power
supply
Regenerative option
Setup software
Electric actuator
PLC (Positioning unit)
LEC-MR-SETUP221
USB cable
LEC-MR-J3USB
Motor cable
Lock cable
1-phase 100 to 120VAC (50/60Hz)
200 to 230VAC (50/60Hz)
LEC-MR-RB-□
Power supply
DC24V
PC
Driver
Standard
Standard Robot
Robot
Encoder cable
Standard Robot
Slider type
LEF series
I/O connector
LE-CSNA
Control circuit
power connector
(accessory)
Main circuit
power connector
(accessory)
Power supply
Regenerative option
Setup software
Electric actuator
PLC (Positioning unit)
Slider type
LEF series
Power supply
DC24V
I/O connector
LE-CSNB
LEC-MR-SETUP221
PC
USB cable
LEC-MR-J3USB
◎o
p
tion
◎o
p
tion
1-phase 100 to 120VAC (50/60Hz)
200 to 230VAC (50/60Hz)
3-phase 200 to 230VAC (50/60Hz)
LEC-MR-RB-□
Motor cable
Lock cable
Encoder cable
Main circuit
power connector
(accessory)
Driver
Standard
Standard Robot
Robot
Standard Robot
Control
circuit power
connector
(accessory)
Motor
connector
(accessory)
◎o
p
tion
◎o
p
tion
◎o
p
tion
◎o
p
tion Analog
monitor
output
RS-422
interface
Battery
LE-MR-J3BAT
(accessory)
When using this software,
order USB cable separately.
When using this software,
order USB cable separately.

- 17 -
Absolute Encoder
(SSCNET III)
Absolute Encoder
(CC-Link)
Prepared by user
Prepared by user
Prepared by user
Prepared
b
y
use
r
Power supply
Regenerative option
Setup software
Electric actuator
PLC (CC-Link master unit)
Slider type
LEF series
Power supply
DC24V
I/O connector
LE-CSNB
LEC-MR-SETUP221
PC
USB cable
LEC-MR-J3USB
◎o
p
tion
1-phase 100 to 120VAC (50/60Hz)
200 to 230VAC (50/60Hz)
3-phase 200 to 230VAC (50/60Hz)
LEC-MR-RB-□
Motor cable
Lock cable
Main circuit
power
connector
(
accessor
y)
Driver
Standard
Standard Robot
Robot Control circuit
Power connector
(accessory)
Motor
connector
(accessory)
◎o
p
tion
◎o
p
tion
RS-422 interface
Battery
LE-MR-J3BAT
(accessory)
Power supply
Regenerative option
Setup software
Electric actuator
PLC (Positioning unit /
motion controller)
Slider type
LEF series
Power supply
DC24V
I/O connector
LE-CSNS
LEC-MR-SETUP221
PC
USB cable
LEC-MR-J3USB
◎o
p
tion
1-phase 100 to 120VAC (50/60Hz)
200 to 230VAC (50/60Hz)
3-phase 200 to 230VAC (50/60Hz)
LEC-MR-RB-□
Motor cable
Lock cable
Main circuit
power connector
(accessory)
Driver
Standard
Standard Robot
Robot
Control circuit
power connector
(accessory)
Motor
connector
(accessory)
◎o
p
tion
◎o
p
tion
Battery
LE-MR-J3BAT
(accessory)
Encoder cable
Standard Robot
Encoder cable
Standard Robot
CC-Link connector
(accessory)
SSCNET III
optical cable
LE-CSS-□
◎o
p
tion

- 18 -
4.2 Function/Configuration
The following control mode can be selected for applicable drivers.
Refer to the “Driver Operation Manual” about wiring and parameter setting.
Table4-1. Applicable control mode
Control modeNote1) Positioning
Driver Position control Encoder Point table method Program methodNote3)
Parameter
select
LECSA
(Pulse input /
positioning)
Pulse train Incremental
ON/OFF signal
3 points
(max. 7 points)Note2)
ON/OFF signal
4 programs
(max. 8 Programs)Note2)
PA01
LECSB
(Pulse input)
Pulse train Absolute - - PA01
LECSC
(CC-Link)
CC-Link
(When 2 stations
are occupied)
Absolute
CC-Link
31 points(When 1 station is occupied)
255 points(When 2 stations are occupied)
- PC30
LECSS
(SSCNET III)
SSCNET III Absolute - - Note4)
Operation
method Positioning operation - Positioning operation by
point table No. setting
Positioning operation by
program No. setting -
Note1) Only the position control can be used.
Note2) To set the maximum value for the each method, it is necessary to change the setting.
Please refer “Driver Operation Manual”.
Note3) The MR Configurator is necessary to control by the program method. Order separately.
-MR Configurator (Setup software Japanese version) / LEC-MR-STUP221
-MR Configurator (Setup software English version) / LEC-MR-SETUP221E
-USB cable for Setup software (3m) / LEC-MR-J3USB
Note4) The LECSS is set by upper positioning unit or motion controller.

- 19 -
5. Wiring of cables / Common precautions
Warning
1. Adjusting, mounting or wiring change should never be done before shutting off the power
supply to the product.
Electrical shock, malfunction and damaged can result.
2. Never disassemble the cable. Use only specified cables.
3. Never connect or disconnect the cable or connector with power on.
Caution
1. Wire the connector securely. Do not apply any voltage to the terminals other than those
specified in the product manual.
2. Wire the connector securely.
Check for correct connector wiring and polarity.
3. Take appropriate measures against noise.
Noise in a signal line may cause malfunction. As a countermeasure, separate high voltage and low
voltage cables, and shorten wiring lengths, etc.
4. Do not route wires and cables together with power or high voltage cables.
The product can malfunction due to interference of noise and surge voltage from power and high
voltage cables to the signal line. Route the wires of the product separately from power or high voltage
cables.
5. Take care that actuator movement does not catch cables.
6. Operate with cables secured. Avoid bending cables at sharp angles where they enter the
product.
7. Avoid twisting, folding, rotating or applying an external force to the cable.
Risk of electric shock, wire break, contact failure and loss of control for the product can happen.
8. Select “Robotic type cables” in case of inflecting cable(encoder/motor/rock) repeatedly.
Refer to the “Driver operation manual” for the bending life of the bending radius of the cable.
9. Confirm proper wiring of the product.
Poor insulation (interference with other circuits, poor insulation between terminals and etc.) can apply
excessive voltage or current to the product causing damage.
[Transportation]
Caution
1. Do not carry or swing the product by the cable.
This manual suits for next models
3
Table of contents
Other SMC Corporation Controllers manuals
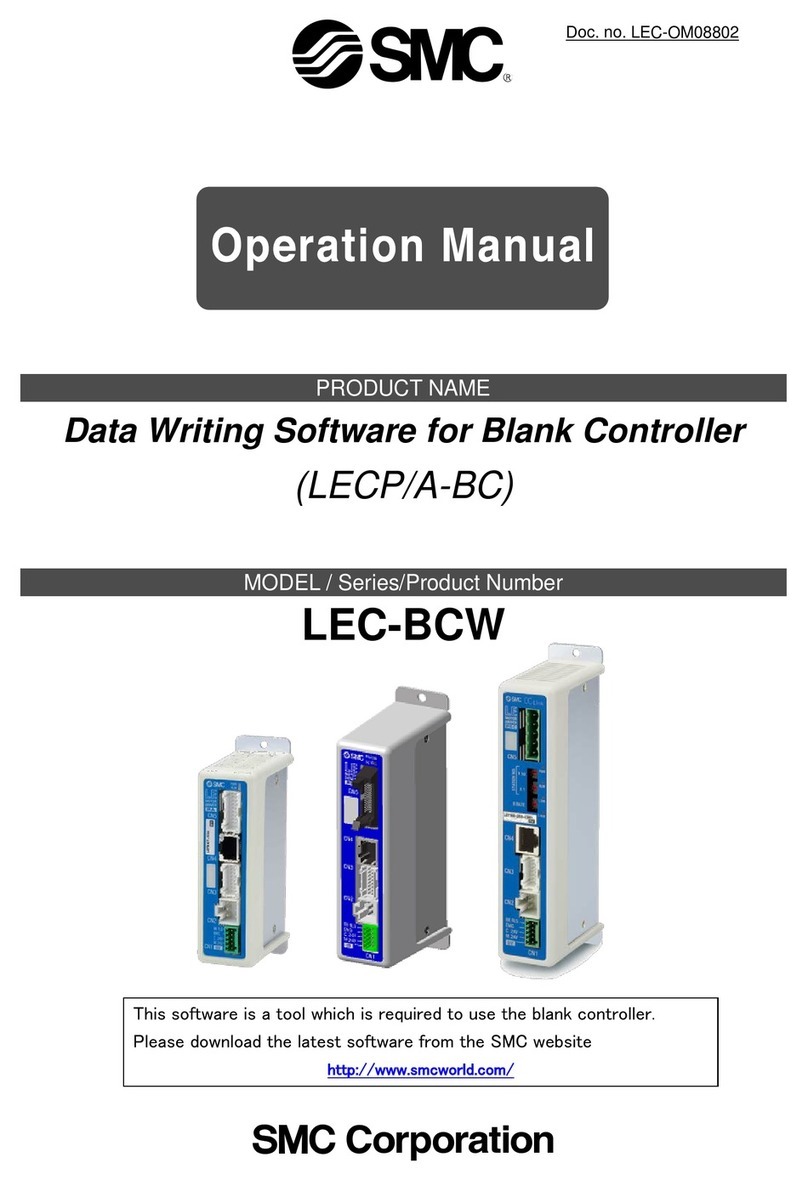
SMC Corporation
SMC Corporation LEC-BCW Series User manual
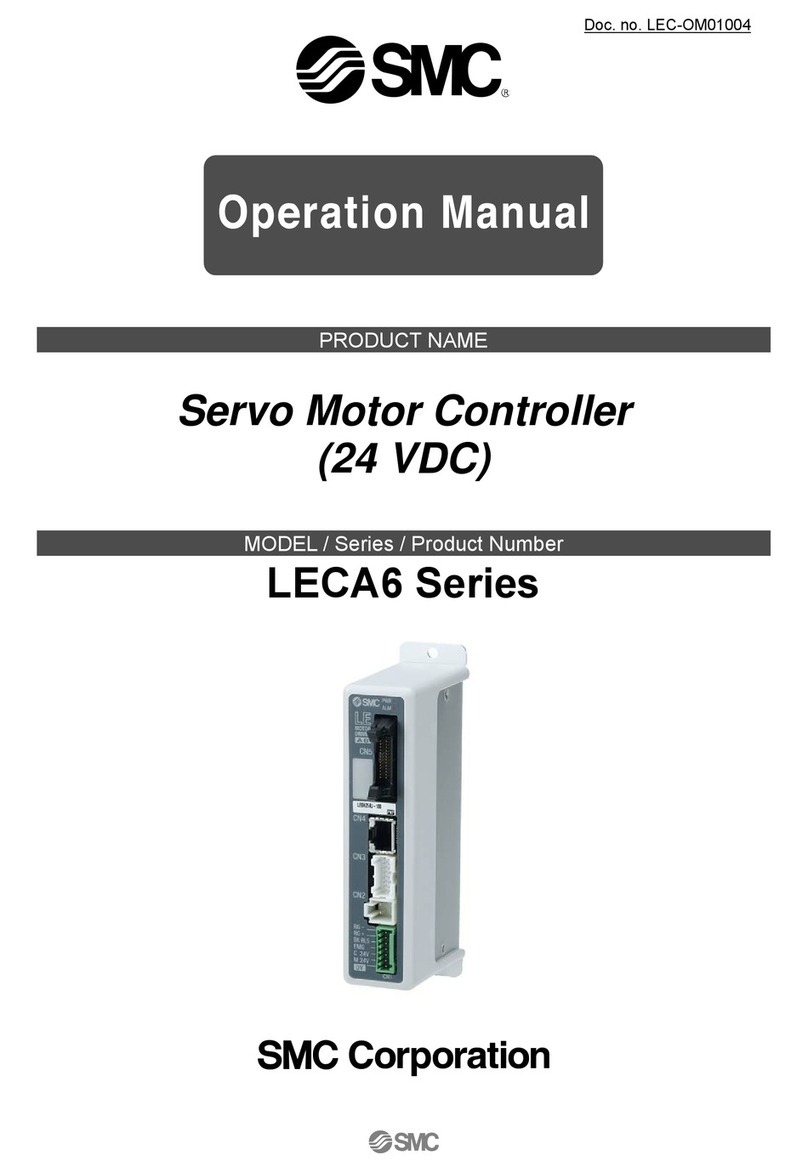
SMC Corporation
SMC Corporation LECA6 Series User manual
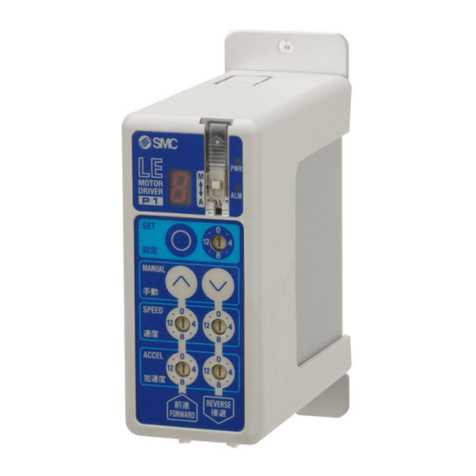
SMC Corporation
SMC Corporation LECP1 series User manual
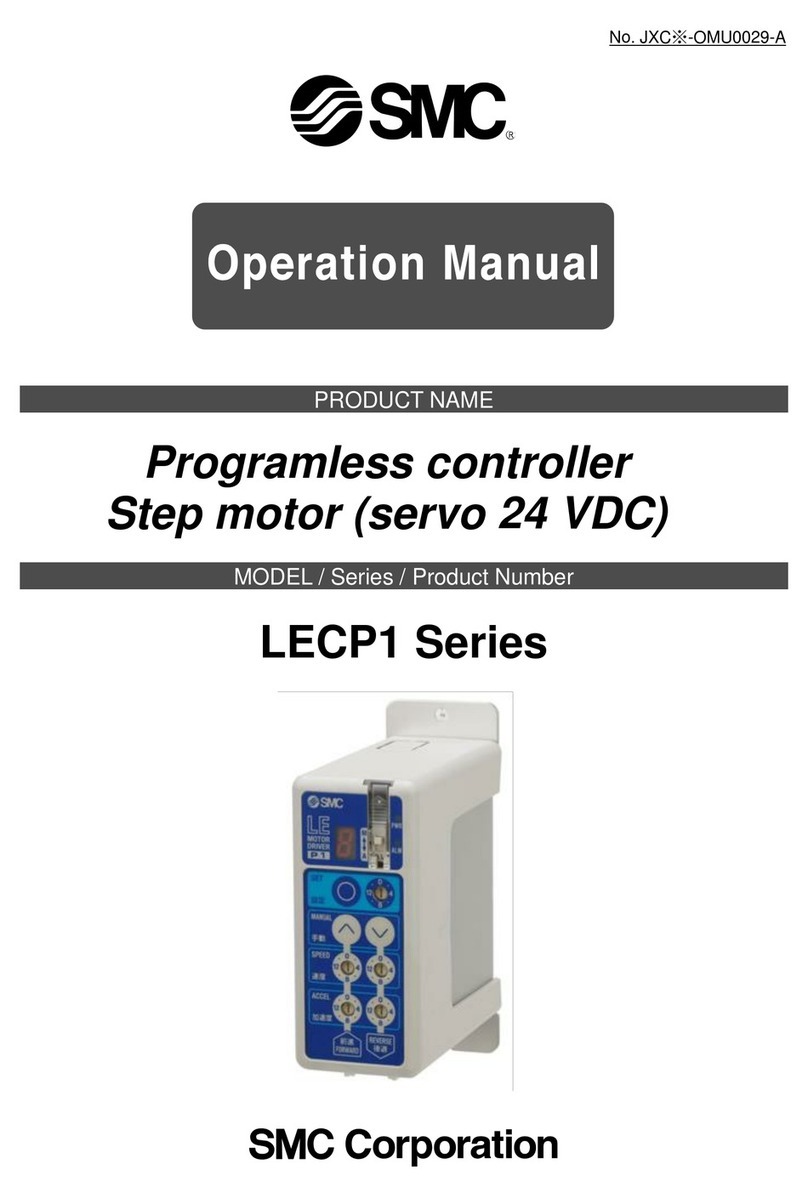
SMC Corporation
SMC Corporation LECP1 series User manual

SMC Corporation
SMC Corporation LECP6 Series User manual
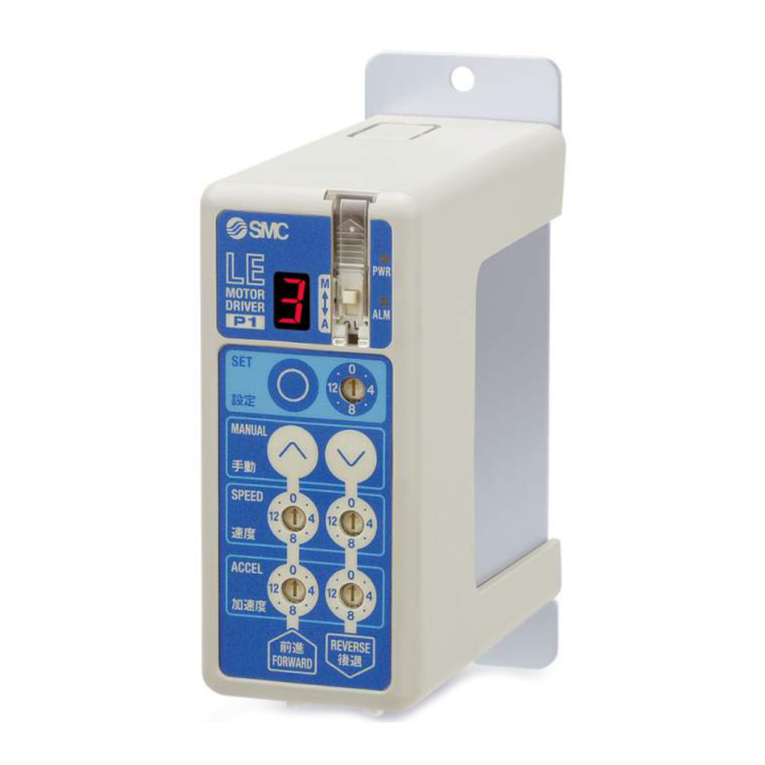
SMC Corporation
SMC Corporation LECP1 series User manual
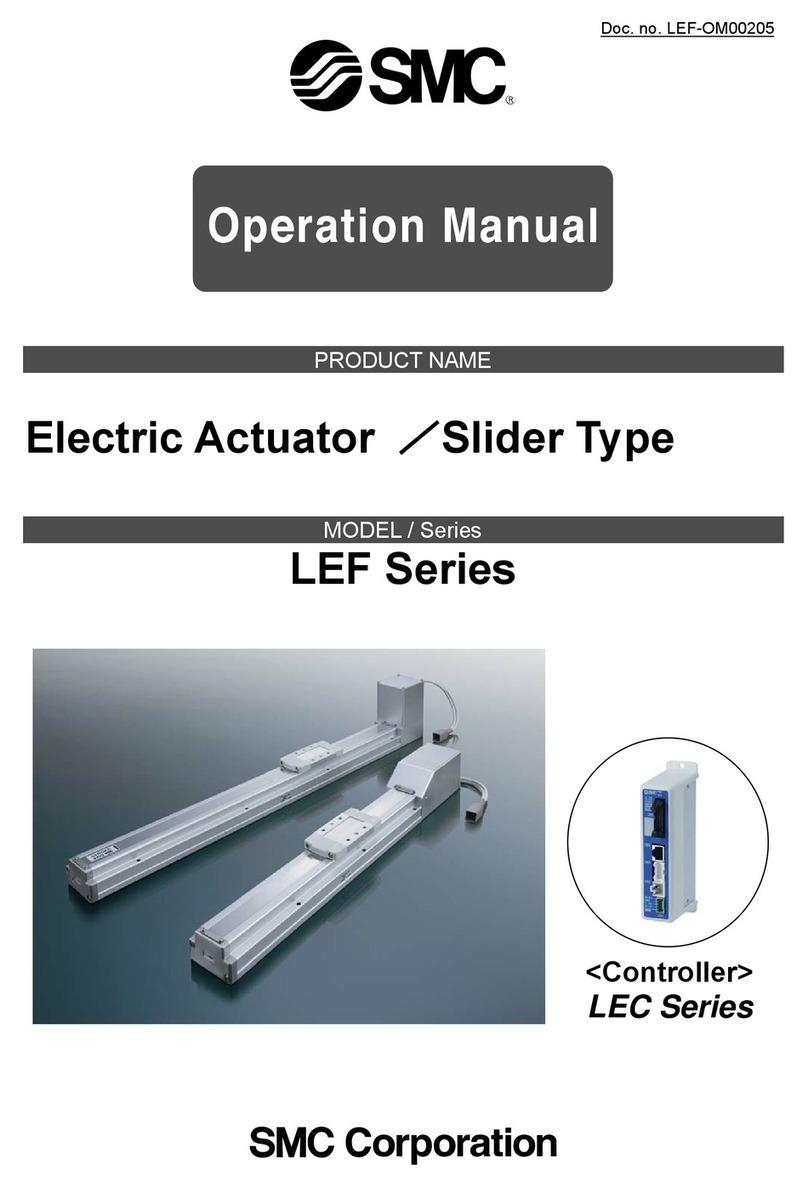
SMC Corporation
SMC Corporation LEF Series User manual