Smittybilt Comp Series User manual

1
XRC GEN3INSTRUCTION MANUAL

2
#97695
XRC Gen3 9.5K
with 4-Way Roller Fairlead and Steel Cable
#97612
XRC Gen3 12K
with 4-Way Roller Fairlead and Steel Cable
#98695
XRC Gen3 9.5K COMP SERIES
with Aluminum Hawse Fairlead and Synthetic Rope
#98612
XRC Gen3 12K COMP SERIES
with Aluminum Hawse Fairlead and Synthetic Rope
XRC Gen3 Winches include:
• 9.5k or 12k XRC Gen3 Winch
• Steel Cable or Synthetic Rope
• 4-Way Roller or Hawse Fairlead
• Movable Control Box Mounting Bracket
• Remote Controller with Load Indicator
• Forged Winch Hook
New Remote Controller Features .......................3
New Control Box Features ..................................4
Safety Precautions ...............................................5
Operation Warnings .............................................6
Winch Operation ...................................................7
Winch Mounting ....................................................8
INSTALLATION INSTRUCTIONS
Electrical Connections .......................................10
Auxiliary 12v Power Post ................................... 11
Armor Plate Removal .........................................12
Control Box Mounting ........................................14
Wiring for DRL and Tie Bar Lighting ................. 16
Motor Wire Nuts Supplement ............................17
Product Specications .......................................18
Understanding IP Ratings ..................................19
Service Parts .......................................................20
Troubleshooting ..................................................22
Warranty ..............................................................23
Smittybilt 400 W. Artesia Blvd., Compton, CA 90220 • Customer Service: (310) 762-9944 • (888) 717-5797

3
Power switch
Direction switch (IN/OUT)
NEW! XRC Gen3 Winch
Remote Controller Features
Load Indicator
Power IN
switch
To power IN:
Press the power IN
switch. The switch
cover and IN indica-
tor will light up. Use
the power switch to
control the winch.
Note: If you press
the power IN switch
a second time, the
remote will go into
neutral and will not
power the winch.
Power IN
indicator light
Power OUT
switch
To power OUT:
Press the power OUT
switch. The switch
cover and IN indica-
tor will light up. Use
the power switch to
control the winch.
Note: If you press the
power OUT switch
a second time, the
remote will go into
neutral and will not
power the winch.
Power OUT
indicator light
What do the
colored lights
on the Load
Indicator mean?
COLOR: BLUE
READY
Winch is ready to start
COLOR: GREEN
LOADING
Winch is operating within
safe levels
COLOR: YELLOW
MAX LOAD
Winch is operating at
maximum load
COLOR: RED
OVERLOAD
STOP!!!
Time to use snatch
block or other assist
IMPORTANT: Load indicator lights will let you know approximately how much load is on your winch based on the
chart above. Maximum pulling power is only achieved when pulling from the rst layer of rope on the drum. Avoid
continuous winching at high load and always check motor temperature frequently. If motor is too hot to touch , allow
to cool before you continue your recovery. It is recommended to re-access your recovery and consider the use of a
snatch block when recovery exceeds full load and/or when red over load lights begin to light up.

4
Magnetic
Mounting Pads
Strong neodymium magnets
enable remote to be secured to
any ferromagnetic material
LED Flashlight
To use LED light in the
remote, ensure remote is
plugged in and then press
the LED light switch to
power the light on and o.
Control Box Socket
Connect the remote to the
Control Box by lining up
the arrow on top of the plug
with the extended Push Tab
on the control box. Push
plug straight into socket
until you feel the push tab
engage and lock the plug
into the socket. The three
blue indicator lights will turn
on, indicating the controller
is connected.
To remove the remote
controller, depress the
Push Tab, then pull out
the plug.
Auxiliary 12V
Accessory Power Post
For quick use of 12 volt accessories without
popping the hood. Perfect for powering
small items such as an air compressor.
The power post is protected with a 50-
Amp automatic circuit breaker. In case of
a ground short, or thermal overload, the
breaker will trip, it will automatically reset
itself after a short period of time after the
fault is removed.
To use, open the cover to expose power
post. Attach accessory POSITIVE lead to the
post. Attach accessory NEGATIVE lead to
a suitable ground location on your vehicle.
NOTE: you may remove the button head bolt
to connect a power wire with an eyelet.
NEVER operate winch with less than 10 wraps
of Synthetic rope around the drum. The terminal
end is to prevent the rope from unraveling, it is
NOT a load bearing attachment point. Improper
installation and/or spooling out to last layer will
put a load on the terminal end and the rope will
release from the terminal. Always re-spool winch
rope under minimum 1000lb. Load before each use.
*For more information see owners manual*
• Inspect rope before each use
• Protect the rope from coming in contact with
sharp or rough objects that may damage, cut or
weaken the rope
• Never use rope over a rough surface without
chafe protection
• Never shock load winch rope
• Never bend rope around unprotected, sharp
corners
• Always use an aluminum hawse fairlead with
synthetic ropes
• Never hook rope back onto itself
• Always wash rope after use
• Manufacturer is not responsible for the results
of misuse, misapplications, faulty installation,
abuse, vehicle condition or modication of the
product in any way.
NEW! XRC Gen3 Winch
Remote/Control Box Features

5
SAFETY PRECAUTIONS
Improper equipment operation may cause
damage to equipment. Observe all safety
precautions for personal safety and the safety
of others. Failure to comply may cause death or
serious personal injury.
Read the following carefully before attempting
to operate your winch. Keep the instructions for
future reference.
1. DRESS PROPERLY.
• DO NOT wear loose clothing or jewelry. They can be
caught in moving parts.
• Wear leather gloves when handling winch cable. Do
not handle cable with bare hands as broken wires can
cause injuries.
• Non-skid footwear is recommended.
2. KEEP A SAFE DISTANCE.
• Ensure that all persons stand well clear of winch
cable and load during winch operation, 1.5 times the
cable length recommended. If a cable pulls loose or
breaks under load, it can lash back and cause serious
personal injury or death.
DO NOT STEP OVER THE CABLE.
• All visitors and onlookers should be kept away from
the work area.
• Keep proper footing and balance at all times.
3. DO NOT ABUSE THE CORD.
• Never carry your winch by the cord or yank it to
disconnect it from the receptacle.
• Keep cord from heat, oil and sharp edges.
4. DO NOT OVERWORK THE WINCH.
• If the motor becomes uncomfortably hot to touch,
stop and let it cool for a few minutes.
• DO NOT maintain power to the winch if the motor
stalls.
• DO NOT exceed maximum line pull ratings shown in
tables. Shock loads must be avoided.
Safety Precautions
5. AVOID UNINTENTIONAL OPERATION.
• Winch clutch should be disengaged and the hook
secured when not in use and fully engaged when in
use.
6. CHECK DAMAGED PARTS.
• Before using, you should check your winch carefully.
Any part that is damaged should be properly repaired
or replaced by an authorized service center.
7. REPAIR YOUR WINCH.
• When repairing, use only identical replacement parts
or it may cause considerable danger for the user.
8. RE-SPOOL THE CABLE.
• Leather gloves must be worn while re-spooling. To
re-spool correctly, it is necessary to keep a slight load
on the cable. See item 16 of operational warnings
section.
• Do not allow the cable to slide through your hand
and do not approach the winch too closely.
• Turn o the winch and repeat the procedure until all
the cable except for approximately 1 meter (3 feet) is
in.
• Disconnect the remote control switch and nish
spooling in cable by rotating the drum by hand with
clutch disengaged.
• On hidden winches, spool in cable under power but
keep hands clear.

6
OPERATIONAL WARNINGS
Read the following carefully before attempting
to operate your winch and keep the instructions
for future reference. Smittybilt electric winches
are intended for recreational self-recovery usage
only.
1. The uneven spooling of cable, while pulling a load, is
not a problem, unless there is a cable pile up on one
end of the drum. If this happens reverse the winch to
relieve the load and move your anchor point further
to the center of the vehicle. After the job is done, you
can unspool and rewind for a neat lay of the cable.
2. Store the remote control switch inside your vehicle
where it will not become damaged, inspect it before
you plug it in.
3. When ready to begin spooling in, plug in remote
control switch with clutch disengaged, do not engage
clutch with motor running.
4. Never connect the hook back to the cable, this
causes cable damage. Always use a sling or chain of
suitable strength.
5. Observe your winch while winching, if possible
while standing at a safe distance. Stop the winching
process every meter or so to assure the cable is not
pulling up in one corner. Jamming the cable can
break your winch.
6. Do not attach tow hook to winch mounting plate, they
must be attached to vehicle frame.
7. The use of a snatch block will aid recovery operations
by providing a doubling of the winch capacity and
a halving of the winching speed, and the means to
maintain a direct line pull to the center of the rollers.
When double loading during stationary winching, the
winch hook should be attached to the chassis of the
vehicle.
8. Ensure "D" or bow shackles with adequate load rating
are used in conjunction with an approved tree trunk
protector to provide a safe anchor point.
9. When extending winch cable, ensure that at least ve
wraps of cable remain on drum at all times. Failure
to do this could result in the cable parting from the
drum under load. Serious personal injury or property
damage may result.
10. All winches are provided with a red cable marking to
identify that 5 cable wraps remain on the winch drum
when this mark appears at the rollers (10 wraps for
synthetic rope). No recovery should be attempted
beyond this marking (wire rope only).
11. Since the greatest pulling power is achieved on the
inner most layer of your winch, it is desirable to pull
o as much line as you can for heavy pulls (you must
leave at least 5 wraps minimum on the drum--red
cable). If this is not practical use a snatch block and
double line arrangement.
12. Draping a heavy blanket or similar object over the
extended winch cable is recommended as it will
dampen any back lash should a failure occur.
13. Neat, tight spooling avoids cable binding, which
is caused when a load is applied and the cable
is pinched between the others. If this happens,
alternatively power the winch in and out. Do not
attempt to work a bound cable under a load, free by
hand.
14. To prevent vehicle rollback, apply blocks behind
wheels when vehicles are on an incline.
15. Battery
• Be sure that the battery is in good condition. Avoid
contact with battery acid or other contaminants.
• Always wear eye protection when working around a
battery.
• Have the engine running when using the winch, to
avoid attening the battery.
16. Winch cable
• Be sure that the cable is in good condition and is
attached properly.
• Do not use the winch if cable is frayed.
• Do not move the vehicle to pull a load.
• Do not replace the cable with a cable of lesser
strength.
• The life of the cable is directly related to the use and
care it receives. Following its rst and subsequent
Operational Warnings

7
uses, a cable must be wound on to the drum under a
load of at least 500Ibs (230kgs) or the outer wraps will
draw into the inner wraps and severely damage the
cable during winching. The rst winch use should be
a familiarization run while in a relaxed, non recovery
situation. Spool out the cable until the red cable mark
appears(about 5 wraps on the drum),then rewind the
cable on the drum under a load of 500Ibs (230kgs)
or more. This will slightly tension and stretch the new
cable and create a tight cable wrap around the drum.
Failure to do so may result in cable damage and
reduced cable life.
• When the cable is replaced, be sure to apply Loctite,
or an equal compound, to the cable clamp thread.
Tighten the clamp screw properly but do not over
tighten. The Loctite will prevent loosening of the
screw in arduous conditions. Loctite 7471 primer and
222 threadlocker are recommended.
17. Do not attempt to exceed the pulling limits of this
winch.
18. Do not drive your vehicle to assist the winch in any
way. Vehicle movement in combination with winch
operation may overload the cable, the winch itself or
cause damaging shock loads.
19. Shock loads when winching are dangerous! A shock
load occurs when an increase force is suddenly
applied to the cable. A vehicle rolling back on a slack
cable may induce a damaging shock load.
20. The winches shown in this manual are solely
for vehicle and boat mounted, non-industrial
applications.
21. Do not use winch in hoisting applications due to
required hoist safety factors and features.
22. Do not use the winch to lift, support or otherwise
transport personnel.
WINCH OPERATION
The best way to get acquainted with how your
winch operates is to make a few test runs before
you actually need to use it. Plan your test in
advance.
Remember you can hear your winch as well as
you can see it operate. Get to recognize the
sound of a light steady pull, a heavy pull, and
sounds caused by load jerking or shifting. Soon
you will gain condence in operating your winch
and its use will become second nature to you.
STANDARD OPERATING
PROCEDURE
1. Ensure the vehicle is secure by applying the parking
brake or chocking the wheels.
2. Pull out the winch cable the desired length and
connect to an anchor point. The winch clutch allows
rapid uncoiling of the cable for hooking onto the load
or anchor point. The shifter tab located on the gear
housing of the winch operates the clutch as follows:
a. To disengage the clutch, move the clutch shifter
tab so that the "FREE SPOOL" text is facing
forward. Cable may now be free spooled o the
drum.
b. To engage the clutch, move the clutch shifter tab
into the "ENGAGED" position. The winch is now
ready for pulling.
c. Line the tab on the inside of the remote socket
end with the groove on the remote plug on the
control box.
You should always “Free spool” the winch outward.
d. Push the switch on the side of the remote to
select the direction you want the winch to
operate, then pull the trigger to operate the
winch.
e. The remote features a magnet on the front which
enables you to keep the remote o of the ground
by having it placed on your vehicle, bumper, etc.
Winch Operation

8
Winch Mounting
After turning on the winch or plugging in the
remote you must always select a direction in
order for the trigger to operate.
3. Recheck all cable rigging before proceeding.
4. Plug in the winch hand control. It is recommended
that the winching operation takes place from the
driver's position to ensure safe operation.
5. To commence winching operation, start vehicle
engine, select neutral in transmission, maintain engine
speed at idle.
6. Operate the remote control switch to the IN or OUT
position until the vehicle has been retrieved. Regularly
check the winch to ensure cable is winding onto the
drum evenly.
WINCH MOUNTING
The tment of winches and/or a frontal
protection system may aect the
triggering of SRS airbags. Check that the
mounting system has been tested and approved
for winch tment in the airbag-equipped vehicle.
Failure to comply may cause death or severe
personal injury.
The winch is to be mounted into a suitable steel
mounting frame using the 4-pont foot mounting system
either a horizontal or vertical plane. It is very important
that the winch be mounted on a at surface so that the
three sections (motor, cable drum and gear housing) are
properly aligned.
Winch mounting frames and/or frontal protection systems
are suggested to suit most popular vehicles. Winch
frames are packaged with detailed tting instructions.
The winch should be secured to the mounting with the
M10x 32mm bolts and spring washers provided. Winch
plate must be at least 6mm thick. Thicker winch plates
may require longer bolts (not included). Ensure winch
mounting bolts protrude past the top surface of the
square nut.
The roller fairlead is to be mounted so as to guide the
rope onto the drum evenly.
NOTE: The gear box and motor assembly are
not clockable. Attempting to do so can cause
damage to the winch and voids warranty.
DO NOT FORCE CLUTCH HANDLE.
Rotate drum to align gear in order to free spool if
needed.
ROPE IS NOT COVERED UNDER THE
MANUFACTURER WARRANTY. THIS IS A
NORMAL WEAR AND TEAR ITEM.
Inspect rope before rst use during the
mandatory pre-stretching. Any defects must be
noted before initial use.
Improper use, inadequate fairlead to bumper
clearances, abuse, neglect, chang damage are
not covered by any warranty.

9
INSTALLATION INSTRUCTIONS

10
WARNING: Do not alter,change or amend and winch wiring/connections. Doing so can cause property
or bodily injury and voids warranty.
Electrical Connections
WARNING: Do not alter, change or amend winch wiring/connections.
Doing so can cause property or bodily injury and voids warranty.

11
Auxiliary 12v Power Post
XRC Gen3 winches feature an auxiliary positive power post on the control box for quick use of 12 volt
accessories with out popping the hood. Perfect for powering small items such as an air compressor.
Power post is protected with a 50-Amp automatic circuit breaker. In case of a ground short, or thermal
overload, the breaker will trip, it will automatically reset itself after a short period of time after the fault
is removed.
Step 1: Open cover to expose power post. (Fig 1).
Step 2: Attach accessory positive lead to power post (Fig 2).
Step 3: Attach accessory negative lead to a suitable ground location on your vehicle.
Note: You may remove the button head bolt to connect a power wire with an eyelet.

12
XRC Gen3 winches feature removable high-impact plastic armor to protect the motor and gear box.
They can be permanently removed to better winch clearance, or they can be temporally removed so
they can be custom painted to add some contrasting color to the front of your vehicle. T-30 torx bit and
4mm Allen wrench are needed to remove the armor plates.
Note: Painting HDPE requires prep work for proper paint adhesion. Contact your local paint supplier
for the recommended adhesion promotors, primers and paint.
Armor Plate Removal
STEP 1: Remove button head bolts, holding down
the armor plates on to the motor (Fig. 1), then gently
slide the plate to the left to remove it (Fig 2).
Photos on following page...
STEP 2: Remove button head bolts, holding down
the armor plates on to the gear box (Fig. 3), remove
the Allen head bolt holding the gear lever in place
(Fig 4).
Use a 4mm Allen wrench and completely remove
screw. Not orientation of lever so it can be installed
in the same position, then pull straight up on the
gear lever. Gently slide the plate to the right to
remove it (Fig 5/6).
STEP 3: If you are planning on running no armor,
it is crucial to reinstall four of the short bolts you
removed in order to properly secure the tie bar/
rod. Re-install one button head bolt into each of the
empty tie rod mounting holes. Take care that you do
not over-tighten the bolts
(Fig 7).
STEP 4: To re-install, simply slide the plate back on
to the winch and secure with the button head bolts
you removed in prior steps. Do not over-tighten
bolts.

13
Armor Plate Removal

14
XRC Gen 3 control box can be mounted over the drum or over the motor with the included bracket
kits. Over-the-motor mounting will provide additional clearance for power wires when mounting the
winch close to a grille.
Step 1: Locate the control box brackets and hardware (Fig 1).
Step 2: Attach the control box mounting brackets to the bottom of the control box with button head bolts. Note front to
rear orientation (Fig 1 & 2).
Step 3: Attach the control box to the tie bars by placing front of bracket over the front tie bar, then line up the rear
mounting holes with the threaded holes in the rear tie bar. Secure with button head bolts. Ensure both bolts are started
before tightening. Note: you may loosen tie bars slightly to aid in alignment of control box mount (Fig 3 & 4).
Control Box Mounting (Over Drum)

15
Control Box Mounting (Over Motor)
XRC Gen 3 control box can be mounted over the drum or over the motor with the included bracket kits.
Over-the-motor mounting will provide additional clearance for power wires when mounting the winch
close to a grille or winch plate.
Step 1: Locate the control box bracket and hardware (Fig 1).
Step 2: Attach control box bracket to the threaded holes in the top and rear of the winch motor. The top will use the
countersunk head bolt along with the bracket spacer. The bracket spacer will be placed on the winch with the ange towards
the top. The rear will use the button head bolt and at washer. Ensure both bolts have been started into the threaded holes
before tightening.
Step 3: Loosen the side control box cover bolts just enough to allow them to connect onto the control box bracket (Fig 3).
Step 4: Slide the control box onto the control box bracket by placing the control box cover bolts into the keyway on the control
box bracket, slide forward and then tighten bolts.

16
Wiring for Lighting/DRL and Tie Bar
XRC Gen 3 control box features a light up
XRC logo. It is recommended to use as a
daytime running light or may be independently
switched.
To power XRC logo (Fig 1):
Step 1: Locate blue and white wire coming out of the
control box (Fig 2).
Step 2: Decide on power source. This could be an aux
switch, daytime running light, fog light, or headlight
circuit.
Step 3: Route wire ensuring it will not chafe along any
sharp edges or get caught in any moving parts. Then
connect to positive power source of your choice.
Note: An inline fuse or wiring to a fused circuit is
recommended. XRC logo light draws approximately 50
mAh.
XRC Gen 3 winches feature a lighted front tie bar
to light up the winch and drum during evening
recoveries. LED tie bar is illuminated only when
you have the remote control plugged in to the
control box.
Step 1: Locate the black wire coming out of the control
box and the black wire coming out of the tie rod on
the motor side. Each end of the wire has a small quick
connect plug (Fig 3).
Step 2: Locate the arrow on each of the plugs. With the
arrows facing each other, connect the quick connect
plugs to complete the circuit (Fig 4). DO NOT twist
connectors when making the connection.

17
MOTOR WIRE NUTS MOUNTING SUPPLEMENT
Motor Wire Nuts Mounting Supplement
Motor Wire Nuts Mounting Supplement
Step 1: Do NOT screw wire nuts too tight
Step 2: Put a wrench on bottom nut when installing wire nuts to prevent movement of terminal stud and hold down nut.
It’s helpful to avoid bolt broken during installation. See pictures below.

18
9500 SPECIFICATIONS 12000 SPECIFICATIONS
Single Rated Line Pull 9,500 lbs (4310 kgs) 12,000 lbs (5443 kgs)
Motor 7HP Series Wound 7HP Series Wound
Controller 12-foot Remote Switch 12-foot Remote Switch
Gear Train 3-Stage Planetary 3-Stage Planetary
Gear Reduction Ratio 173:1 173:1
Clutch Sliding Ring Gear Sliding Ring Gear
Braking Automatic in-The-Drum Automatic in-The-Drum
Drum Size Dia. 2.5" (63.5mm) x Length 9.6" (224mm) Dia. 2.5" (63.5mm) x Length 9.6" (224mm)
Steel Cable 5/16" x 94'(8.0mmx28.5m) 23/64" x 94'(9.2mmx28.5m)
Synthetic Rope (COMP Series) 3/8" x 94'(9.4mmx28m) 7/16" x 90'(11mmx27m)
Fairlead (w/Steel Cable) 4-Way Roller Fairlead 4-Way Roller Fairlead
Fairlead (COMP Series) Aluminum Hawse Fairlead Aluminum Hawse Fairlead
Remote Control Included Included
Battery Recommended 650 CCA Recommended 650 CCA
Battery Leads 25m2 72" L (1.83m) 25m2 72" L (1.83m)
Net Weight #97495 87lbs (39.5kgs) / #98495 66lbs (30kgs) #97612 94lbs (42.5kgs) / #98612 71lbs (32kgs)
Overall Dimensions (L x W x H) 21.7" x 6.7" x 8.3" (546x170x210mm) 21.7" x 6.7" x 8.3" (546x170x210mm)
Mounting Bolt Pattern 10" x 4.5" (254 x 114.3mm) 10" x 4.5" (254 x 114.3mm)
Line Pull - lbs 0 2000 4000 6000 8000 9,500 0 3000 6000 9000 12,000
Line Pull - Kg 0 910 1814 2720 3625 4536 0 1364 2727 4082 5433
Line Speed - Ft/min 27.3 18.3 15.4 12.8 10 7.5 25 14.7 12.8 85.2
Line Speed - M/min 10.8 6.30 4.35 3.45 2.90 2.25 7.6 4.5 3.9 2.4 1.6
Motor - AMPS 80 160 220 280 340 385 90 160 230 300 375
Specications
97495 87lbs(39.5kgs)
5/16”x94’(8.0mmx28.5m)
3/8”x94’(9.4mmx28m)
21.7"x6.7"x8.3" (546x170x210mm)
35.56
0
0
10.84
80
2000
910
20.66
6.3
160
1814
14.27
4.35
220
2720
11.32
3.45
280
3625
9.51
2.9
340
4536
7.38
2.25
385
4000 6000 8000 9500
Rope
/ 98495 66lbs(30kgs)

19
Understanding IP Ratings
THE FIRST DIGIT indicates the level of protection that the enclosure provides
against access to hazardous parts (e.g., electrical conductors, moving parts)
and the ingress of solid foreign objects.
THE SECOND DIGIT indicates protection of the equipment inside the enclosure
against harmful ingress of water.
LEVEL OBJECT SIZE
PROTECTED AGAINST EFFECTIVE AGAINST
0No protection against contact and ingress of objects
1>SO mm Any large surface of the body, such as the back of a hand, but no protection against deliberate contact
with a body part
2>12.5 mm Fingers or similar objects
3>2.Smm Tools, thick wires, etc.
4>1 mm Most wires, screws, etc.
5Dust Protected Ingress of dust is not entirely prevented, but it must not enter in sucient quantity to interfere with the
satisfactory operation of the equipment; complete protection against contact.
6Dust Tight No ingress of dust; complete protection against contact
LEVEL PROTECTED AGAINST TESTING FOR DETAILS
0Not Protected
1Dripping Water Dripping water (vertically falling drops) shall have no
harmful eect.
Test duration: 10 minutes - Water equivalent
to 1mm rainfall per minute
2
Dripping Water
When Tilted
Up To 15°
Vertically dripping water shall have no harmful eect
when the enclosure is tilted at an angle up to 15° from its
normal position.
Test duration: 10 minutes - Water equivalent
to 3mm rainfall per minute
3Spraying Water Water falling as a spray at any angle up to 60° from the
vertical shall have no harmful eect.
Test duration: 5 min. - Water volume: 0.7
liters per minute - Pressure: 80- 100 kN/m2
4Splashing Water Water splashing against the enclosure from any direction
shall have no harmful eect.
Test duration: 5 min.- Water volume: 10 liters
per minute - Pressure: 80- 100 kN/m2
5Water Jets Water projected by a nozzle (6.3mm) against enclosure
from any direction shall have no harmful eects.
Test duration: at least 3 min. - Water volume:
12.5 liters per minute - Pressure: 30 kN/m2 at
distance of 3m
6Powerful Water
Jets
Water projected in powerful jets (12.5mm nozzle) against
the enclosure from any direction shall have no harmful
eects.
Test duration: at least 3 minutes - Water vol-
ume: 100 litres per minute - Pressure:100 kN/
m2 at distance of 3m
7Immersion
Up To 1m
Ingress of water in harmful quantity shall not be
possible when the enclosure is immersed in water
under dened conditions of pressure and time (up to
1m of submersion).
Test duration: 30 minutes Immersion at
depth of Im
8Immersion
Beyond 1m
The equipment is suitable for continuous immersion in
water under conditions which shall be specied by the
manufacturer. Normally, this will mean that the equipment
is hermetically sealed. However, with certain types of
equipment, it can mean that the water can enter but only
in such a manner that it produces no harmful eects.
Test duration: continuous ummersion in
water.

20
Service Parts
WINCH PART NO. DESCRIPTION CONTAINS
XRC Gen3 9.5K 97695-57 7.0 hp motor asm 9.5K Winch 9.5k complete Motor assembly, motor side casting seal to drum
XRC Gen3 9.5K 97695-41 Cable 9.5k Appropriate cable and securing screw
XRC Gen3 9.5K/12k 97695-46 Hook 9.5K/12K hook, ag, pin, clip
XRC Gen3 9.5K/12k 97695-37 Free spool handle 9.5K/12K Handle, seal, and hardware
XRC Gen3 9.5K/12k 97695-42 Rope x bolt 9.5K/12K
XRC Gen3 9.5K 97695-55 9.5K gearbox asm 9.5k complete gear box
XRC Gen3 9.5K/12k 97695-47 Roller Fairlead 9.5K/12K with hardware
XRC Gen3 9.5K/12k 97695-77 Hawse Fairlead 9.5K/12K with hardware
XRC Gen3 9.5K/12k 97695-53 Control box cover 9.5K/12K
XRC Gen3 9.5K/12k 97695-58 Socket covers 9.5K/12K remote and 12v socket covers
XRC Gen3 9.5K/12k 97695-79 Armor set 9.5K/12K Both side armors and hardware
XRC Gen3 9.5K/12k 97695-50 Wired remote with LI 9.5K/12K Wired remote and cord
This manual suits for next models
6
Table of contents
Other Smittybilt Winch manuals
Popular Winch manuals by other brands
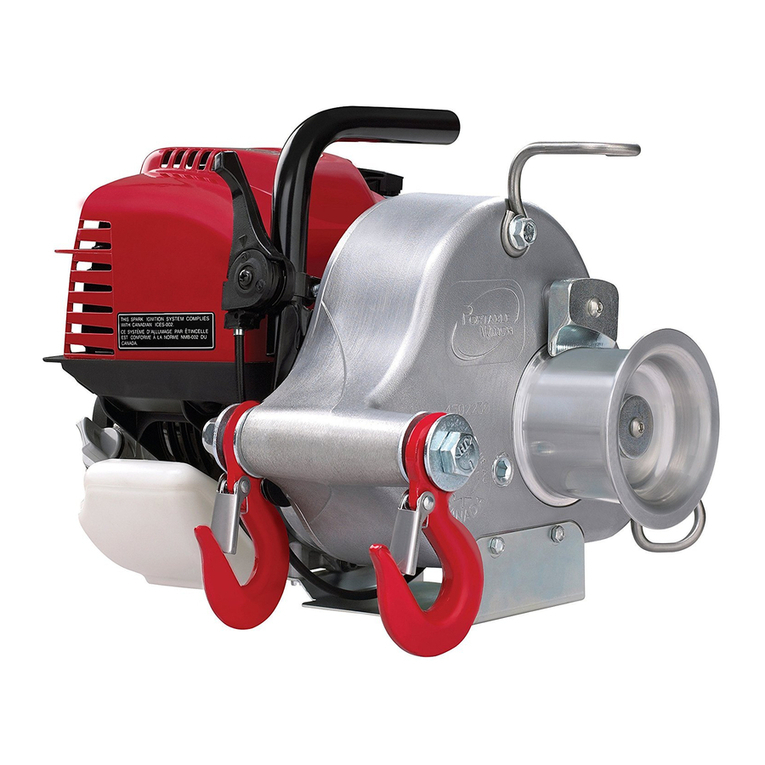
Portable Winch
Portable Winch PCW3000 user guide
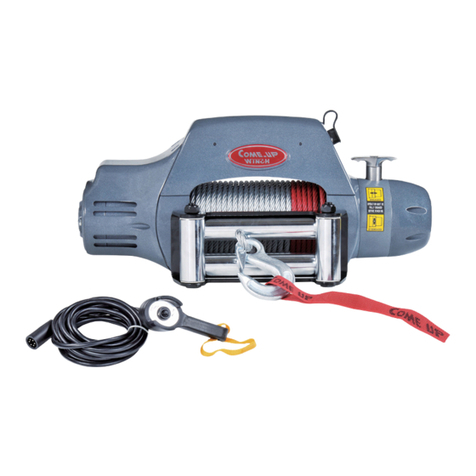
Comeup
Comeup DS-9.5 instruction manual
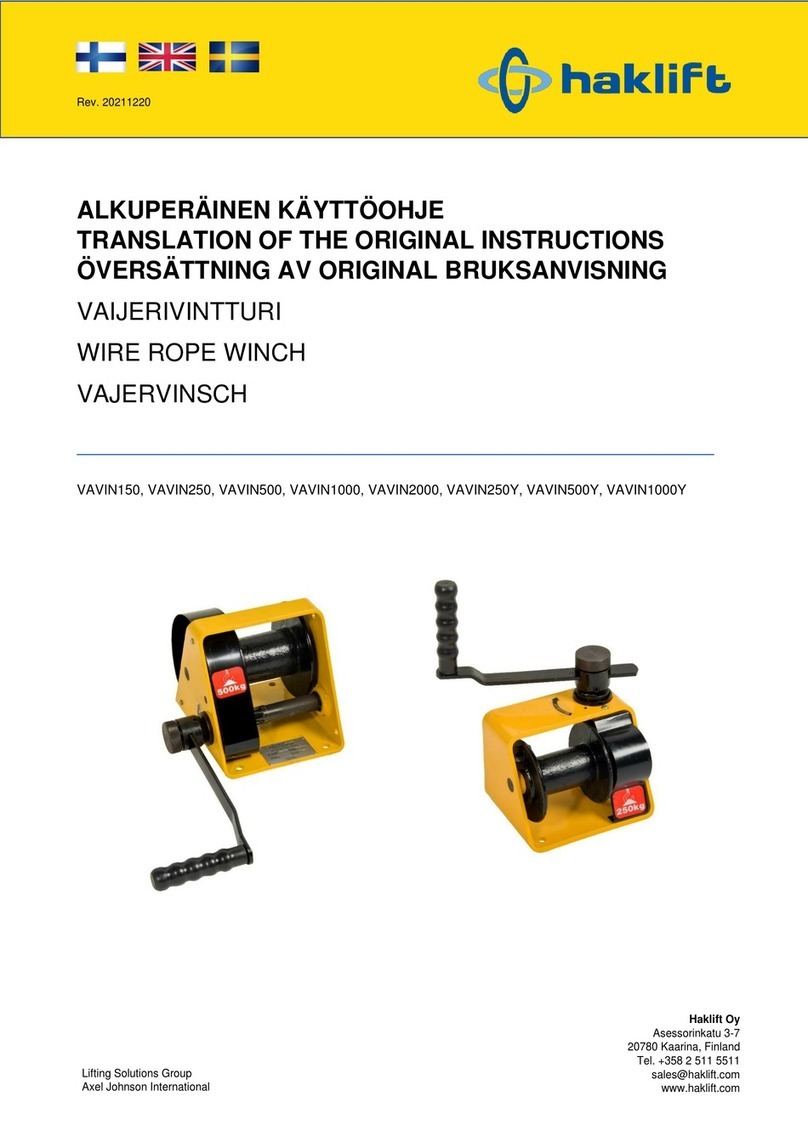
Haklift
Haklift VAVIN150 manual
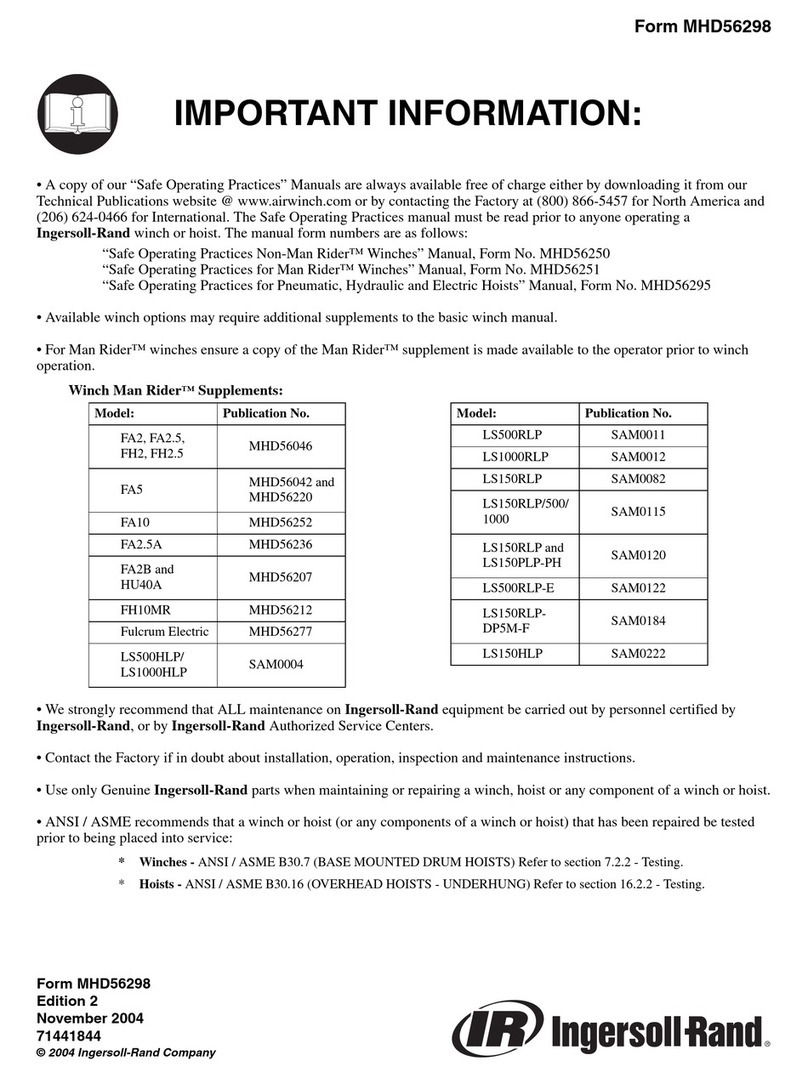
Ingersoll-Rand
Ingersoll-Rand Force 5 MANRIDER FA2MRA Installation and operation manual
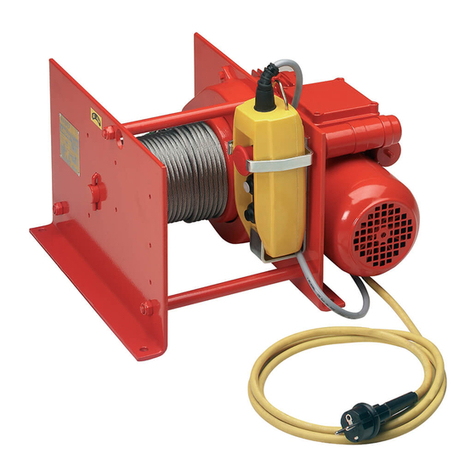
HADEF
HADEF 43/86E-Liftboy Installation, operating and maintenance instructions
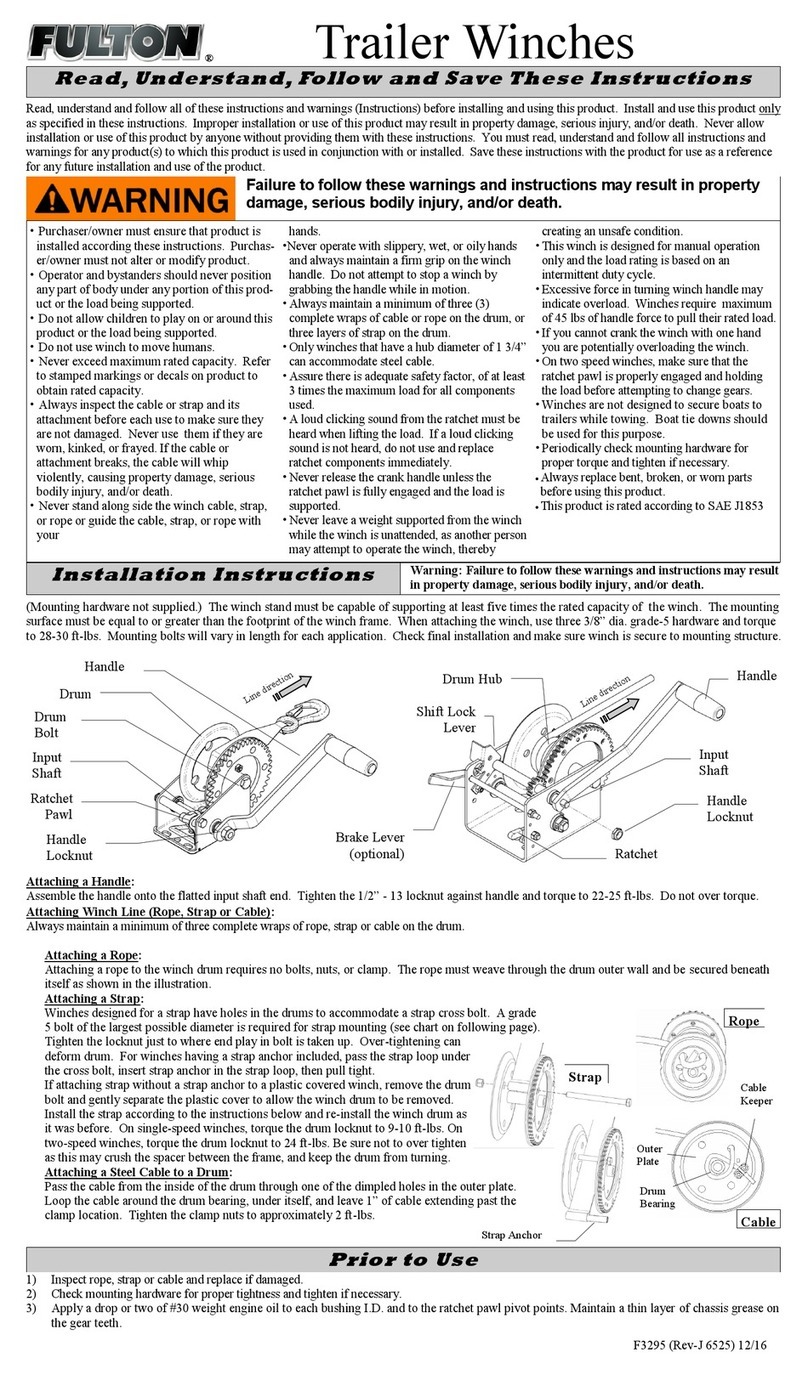
FULTON
FULTON 142401 installation instructions
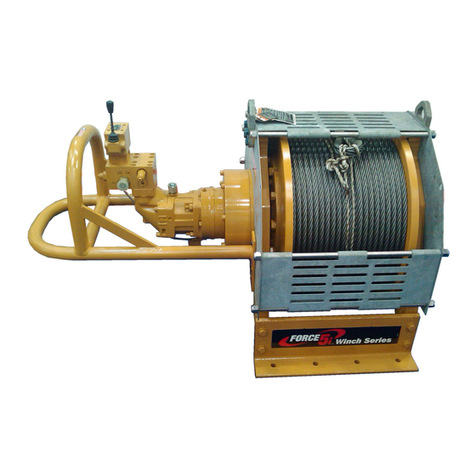
Ingersoll-Rand
Ingersoll-Rand Force 5 FH5 Parts, operation and maintenance manual
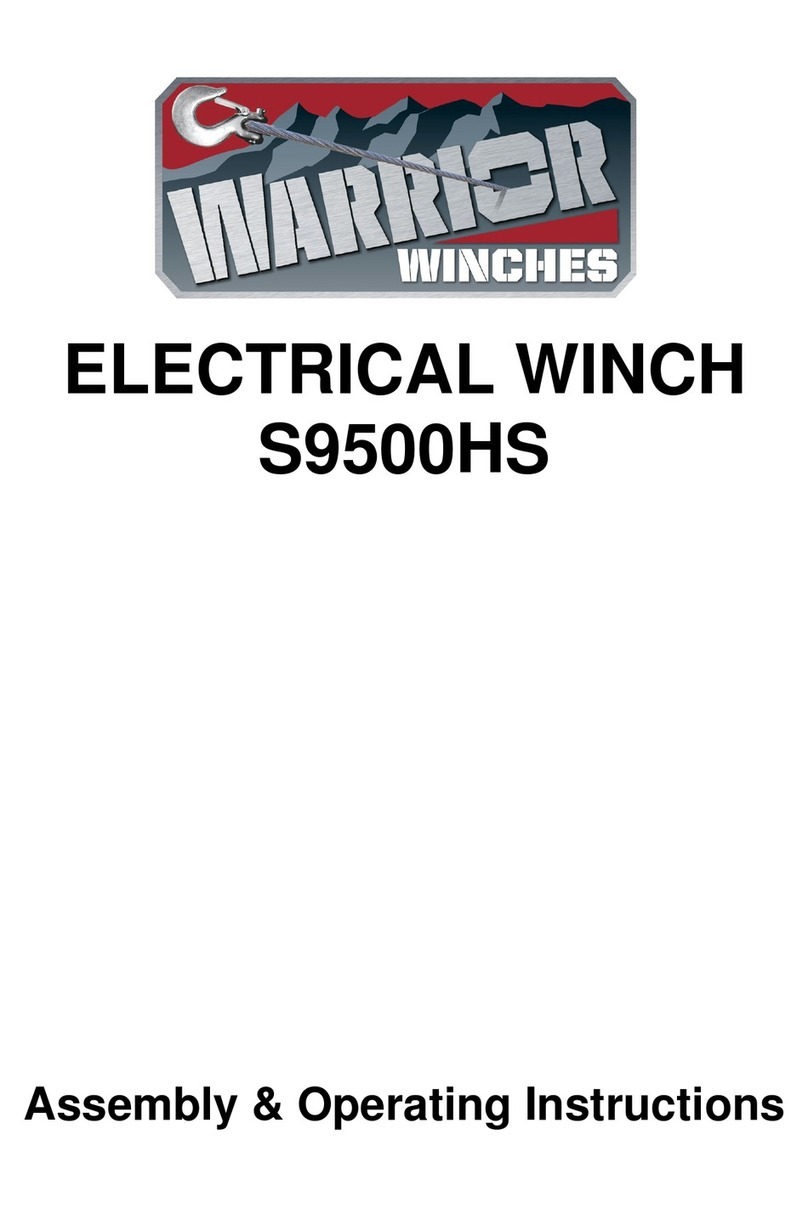
Warrior Winches
Warrior Winches S9500HS Assembly & operating instructions

TOHO
TOHO S Series instruction manual
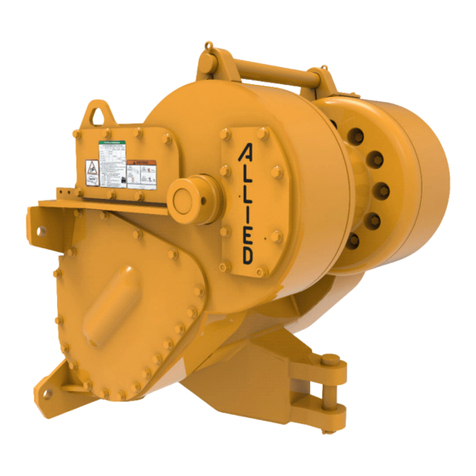
Allied Systems
Allied Systems W8L operating manual
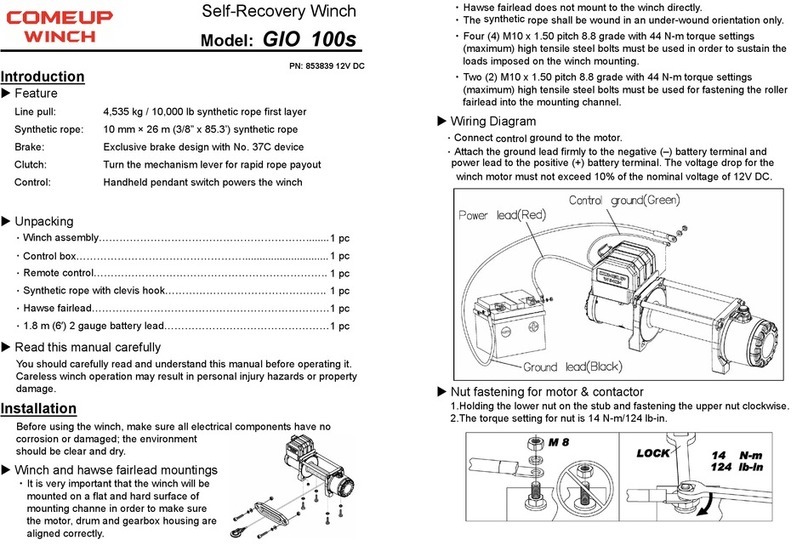
Comeup
Comeup GIO 100s manual
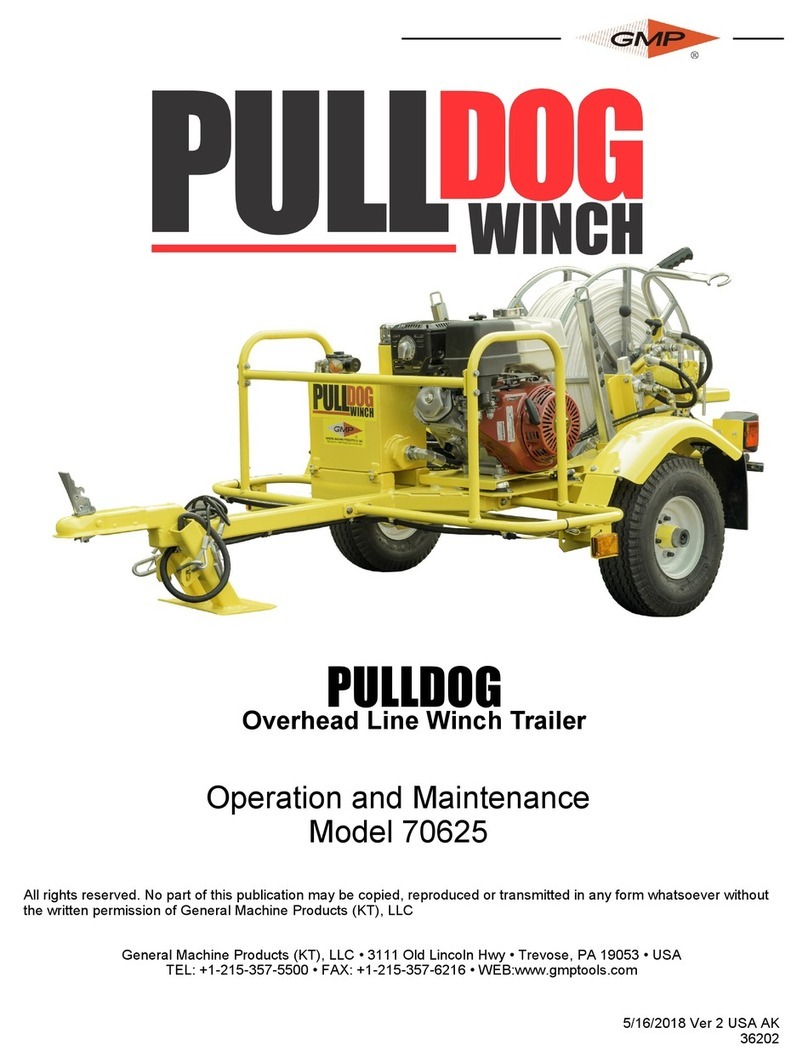
GMP
GMP PULLDOG 70625 Operation and maintenance